In detail: do-it-yourself auto repair of a generator from a real master for the site my.housecope.com.
I have already talked about the device of electric current generators, which are arranged similarly to synchronous motors, only differ from them in the collector, therefore the process of troubleshooting and repairing electric current generators is in many ways similar to them.
In this article I will tell you in detail using the example of a do-it-yourself repair of an automobile generator, because it is it that most people most often encounter with repair. The principle of repairing a generator with your own hands as part of a power plant will be similar. Only a voltage rectifier will not be built into its case and the output voltage regulation will work differently.
Cars use a three-phase generator alternating current, but as is known in the on-board network, a constant voltage of 12 volts. To obtain direct current, a rectifier consisting of 6 diodes is used, and a voltage regulator is provided to keep the voltage of 12 volts within acceptable limits.
The generator is arranged quite simply. Voltage is applied to the rotor through graphite brushes and slip rings to excite it. It is driven by a pulley through a belt drive. The rotor rotates in bearings. Electric voltage is generated in the stator windings and converted into a constant voltage using six power semiconductor diodes, three of which are connected to the positive terminal of the generator, and the other three to the negative terminal and "vehicle ground".
- If on the dashboard of the car after starting it does not go out control lamp, this indicates that the generator does not work and does not give current. But sometimes the cause of the alarm can be poor contact of the connector, wires, or a malfunction of the relay.
- Battery discharge. But keep in mind that sometimes the battery is discharged and does not have time to be charged by a working generator when moving over short distances and with the light and electrical devices of the car turned on as much as possible.
- Generator at engine speed 2000-2500 gives a voltage below the permissible limit of 13.2 Volts.
- If the generator generates a voltage above the permissible limit of 14-14.8 Volts (depending on the model), this indicates a faulty voltage regulator, which leads to a disastrous overcharge for the battery.
![]() |
Video (click to play). |
Before removing the generator for repair, check:
- Tensioning the drive belt and rotating the pulley, tightening its nut.
- Connection to the vehicle body of the battery and generator.
- The integrity of the fuses.
- Bearing play. It is checked in the same way as for electric motors according to this instruction.
- Before removing and disassembling power unit, if there is generator noise during operation, try disconnecting the wires. If the noise has disappeared, then this indicates a short circuit or interturn short circuit of the stator windings or a short circuit to ground. Repair is not advisable, replacing the generator with a new one will be cheaper. If the noise persists, this indicates bearing wear. They need to be replaced.
- Most often worn brushes are the cause of the malfunction... Check and replace them.
- Poor contact between brushes and slip rings. Check if the spring is not pressing well. It can be stretched or replaced if necessary. Inspect slip rings for scorching or dirt. Use the finest sandpaper for cleaning and a rag for dirt. If the slip ring is severely worn, the rotor must be replaced.
- Damage to the rotor winding can be checked with a multimeter. The windings should ring among themselves for a short circuit or show a small resistance. If the windings are intact, then it is necessary to ring for the lack of electrical connection between them and the case. A defective rotor cannot be repaired and must be replaced.
- Damage to the stator winding are checked in the same way. The multimeter should show a short circuit or very small resistance between the terminals. And there should be no electrical contact between the winding and the generator case. The defective stator must be replaced.
- Check all diodes in the rectifier. They must conduct electric current only in one direction, in the opposite direction (we swap the positive and negative probes) - the resistance is large enough. In the example in the picture, it is necessary to check each diode between points numbered 1 and number 2.
Recommend additionally will get acquainted with the instructions for repairing synchronous electric motors with their own hands, because they carry out troubleshooting in almost the same way as for generators.
Hello dear motorists! Today I will tell you how to repair a generator with your own hands. You may have already encountered such a problem, when the battery discharge indicator suddenly came on on the dashboard, this means that your car has lost its charging, and you will not have long to drive, the battery will last for a maximum of 1-2 hours.
Do not rush to throw away the generator. Try to repair it first. The most common generator malfunction is brush wear.
To check the brush assembly, you need to remove the rear plastic cover by bending the three plastic clips located in a circle.
Remove the cover, unscrew the two screws and remove the voltage regulator.
Check the wear of the brushes, if the residual length of the brushes is less than five millimeters, feel free to buy a new voltage regulator in the store. Sometimes it happens that the generator does not charge or recharges the battery, this is also a malfunction of the voltage regulator. The normal voltage of the generator is 13.5 to 14.5 volts, depending on the engine speed and the load on the generator.
The next generator malfunction is a breakdown of the diode bridge. To test the diodes, the diode bridge must be removed. We unscrew the bolts that hold the diode bridge.
Bend the wires to the side.
Remove the diode bridge. How to check a diode bridge. Read here: How to check a diode bridge?
After removing the diode bridge, be sure to check the stator windings. We do this, turn on the multimeter in dial mode and check all three stator windings for an open. All windings must ring among themselves.
Next, we check the short to ground. We connect one probe of the multimeter to ground, and the second is alternately connected to the terminals of the windings. There should be no short circuit to ground.
Similarly, we check the armature winding.
We check the anchor, there is no short circuit to ground.
Now I will show you how to disassemble the alternator to replace the bearings. We unscrew the four screws connecting the two halves of the generator together.
Unscrew the nut and remove the pulley.
Using a screwdriver, carefully split the generator in two so as not to damage the aluminum covers.
Replace defective bearings with new ones. Reassemble the generator in reverse order.
Friends, I wish you good luck! See you in new articles!
Mon 19 Oct 2015
Hello! Today I will show you how I repaired my generator, which, perhaps, someone else would have thrown into a landfill. When I drove home yesterday, everything was included - lights, stove and music. At some point, the on-board computer squeaked and the battery light on the panel came on. I immediately deduced the voltage of the on-board network on the BC and was surprised - it was 11.4 volts. I turned everything off immediately and drove home slowly.
After turning off the engine, the computer showed 8 volts. Having removed and disassembled the generator, it was revealed that one of the copper-graphite brushes of the relay-regulator simply fell off the wire. This one costs 510 rubles, but I thought it would be better to fix it myself.
This is how it looks.
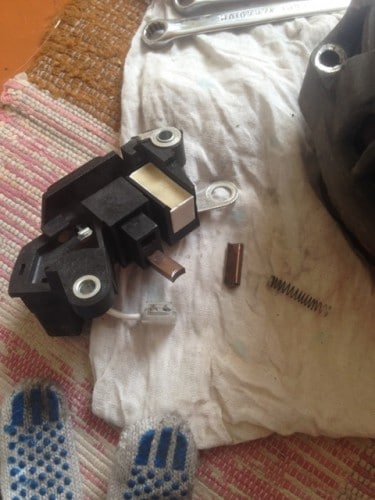
After rummaging through the warehouse, new drill brushes were found.
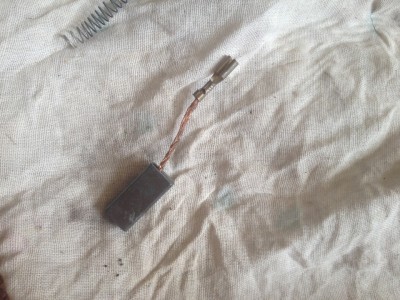
They varied in width and thickness, but the length was the same. Compare:
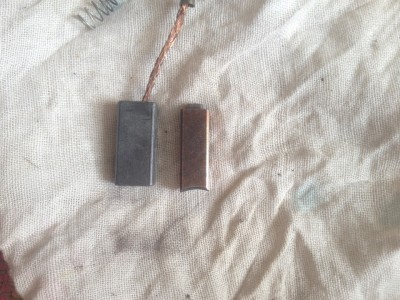
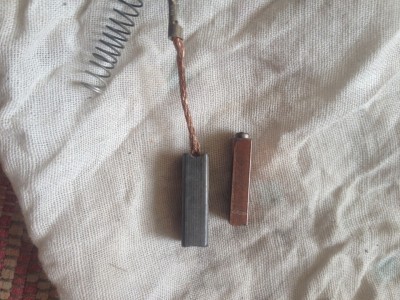
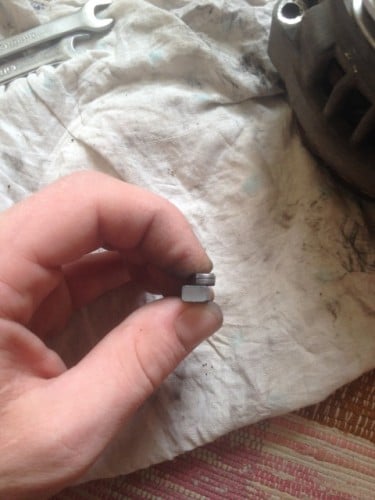
After a little processing on a sharpener, they became almost identical, only the color was different.
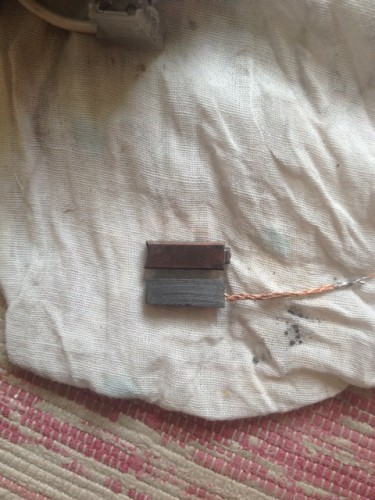
Then I soldered a thin copper wire to the brush pigtail, so that with it in the future I would not have any problems with how to tighten this same pigtail into the brush contact hole.
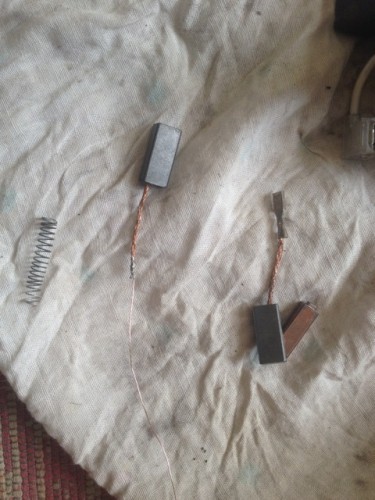
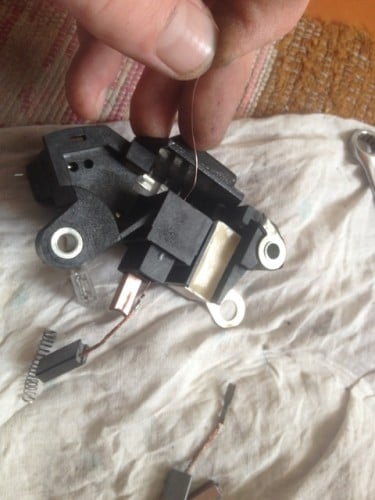
After the contact of the brush of the relay-regulator was cleaned, there are still remnants of the old scythe.
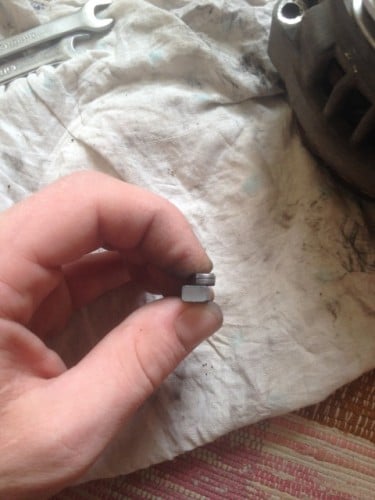
And he tinned the whole thing, using tin and soldering acid.
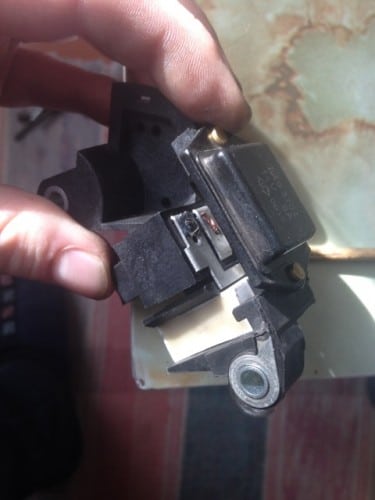
Then I put a spring on that very wire.
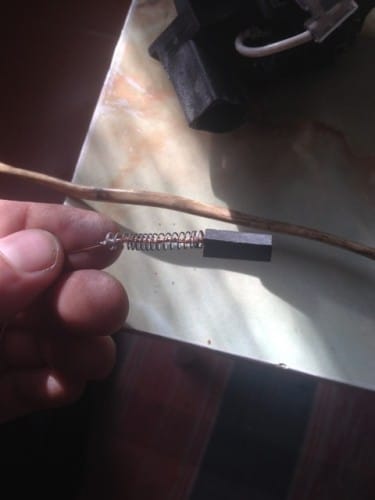
And put it into the contact hole of the brush of the relay controller.
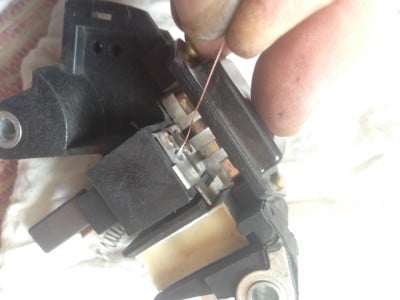
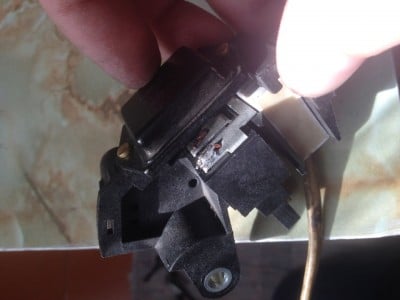
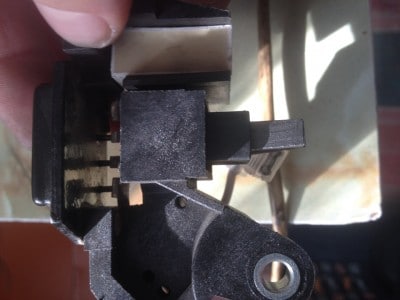
Then I saw that the contact sleeves of the generator rotor were rubbed with brushes, so much so that plastic was already visible in the grooves, that is, either the contact sleeves or the rotor had to be changed.
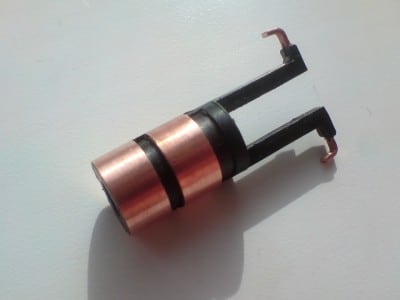
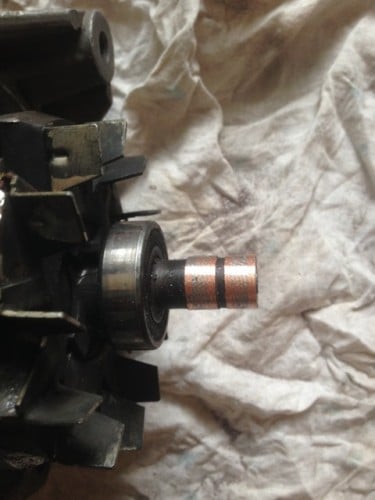
Well, this is how a repaired generator looks like.
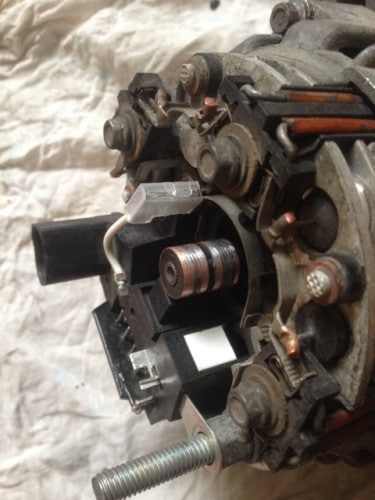
I installed it back in the car, started it and I see 14.1 volts. Of course, I could not sweat it and buy all this, incl. and a new generator. But why? 0 rubles and a minimum of effort were spent on repairs. Hope this is useful to someone. Good luck!
A car generator is a unit that is used to provide electricity to all energy consumers in a car. Failure of the generator device will lead to the fact that all equipment will be powered by the battery, and this will subsequently cause its rapid discharge. When do generators need to be repaired, and what malfunctions are typical for this device? You will find the answers below.
How much does the engine stall when the generator is loaded, what can be associated with current leakage problems, what should be the voltage, why the device does not work and how to repair the breakdown? Do-it-yourself repair of faults in automobile generators is a rather complicated matter, therefore, for a start, it recommends that you familiarize yourself with the main breakdowns of the device. Mechanical faults include damage to the mounting brackets, the unit housing, wear of the pulley and bearings, hold-down springs, etc. There can be many reasons for damage, but in any case, they have nothing to do with the electrical component.
If the car engine does not start and you think that it is the generator that has broken down, then it will be useful for you to find out about the main signs of malfunctions in the operation of the unit:
- A low battery indicator appears on the dashboard when the engine is running. The light can blink or stay on without interruption.
- In case of incorrect operation of the device, when a higher load is imposed on the unit than that for which it is designed, the battery comes into operation to support the power supply of the equipment. This can cause the battery electrolyte to boil off.
- The next symptom is that when you turn on the headlights, you can see how the optics began to burn more dimly. If you press the gas pedal, which will lead to an increase in the speed of the power unit, then the brightness of the optics will be restored to the required level.
- The device howls, hums, or whistles. If during the operation of the unit, extraneous sounds began to appear, this indicates a malfunction in its operation, which may be different. Also, the generator gets very hot.
- The car engine stalls from time to time for no apparent reason. A malfunction of this kind may indicate that there is a lack of voltage in the on-board network required to power electrical equipment. If at the same time the battery is fully charged, then most likely the reason lies precisely in the generator.
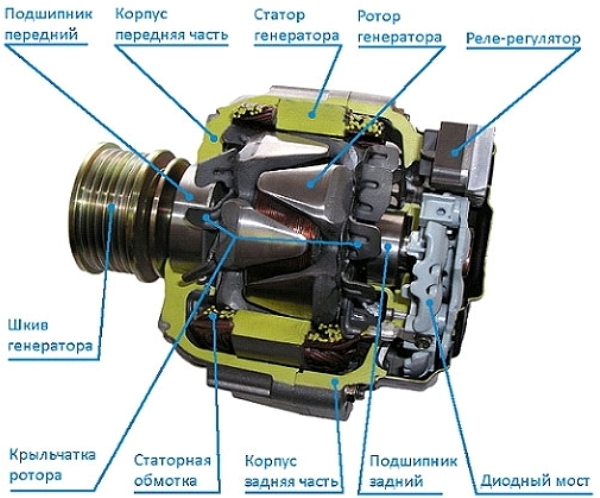
Now let's consider the possible causes of malfunctions, due to which it may be necessary to remove, disassemble and repair the generator device of the car:
- Pulley damage or wear. If we are talking about serious malfunctions and significant damage to the pulley, then it will be easier to replace it. In some cases, repair and refurbishment is allowed, but it is best to change the device.
- Damage or natural wear of slip rings, which can be damaged.
- Malfunction of the regulator. The voltage regulator is designed to equalize the operating value in the electrical network of a car, its breakdown will lead to voltage surges in the network.
- Breakdown of the diode bridge of the unit. If the diodes fail, the first symptom of a breakdown is the absence or too weak spark on the candles, and the battery capacity can also be reduced.
- Closing the turns of the stator winding. Sometimes the problem can be solved by rewinding the winding, but often it is easier to simply replace it.
- Bearing wear. If the bearing elements are worn out and broken, additional noise will appear in the operation of the unit.
- Damage to the power supply circuit.
How to disassemble and how to repair the device? Below are some basic troubleshooting tips.
These tips are relevant if you know the main causes and symptoms of breakdowns:
Sometimes self-repair of the unit is impractical, so car owners have to change the device. We will consider the replacement procedure using the example of a Lada Kalina car.
To successfully complete the replacement, prepare the following tool:
- wrenches for 8, 13 and 19, for more convenience, use ring and open-end;
- ratchets with heads of the same size;
- extension cord with a crank (video by AndRamons channel).
The replacement procedure should be carried out taking into account the recommendations and requirements of the manufacturer, which are indicated in the service book for operation. Before proceeding with the replacement, be sure to study the manual.
So, how to remove and replace the unit yourself:
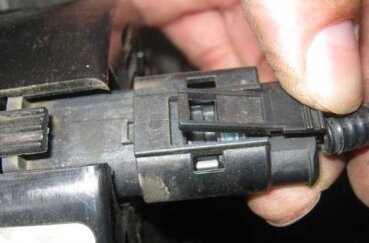

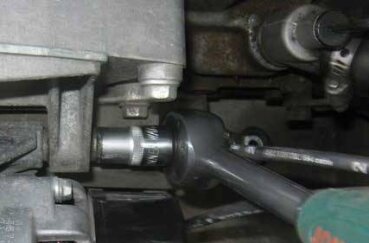
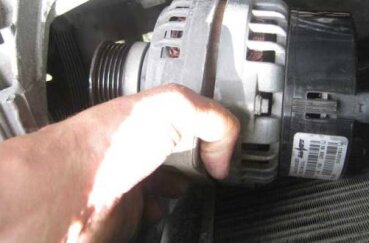
Timely repair and maintenance of the unit are the main aspects that will increase the service life of the device.
What nuances should be considered:
An illustrative lesson with a detailed description of all aspects on the principle of the unit's operation is shown in the video below (the video was published by Mikhail Nesterov).
Car generator - an electrical installation that converts the mechanical energy of the engine into electrical current. The car generator in the engine compartment of the car performs the function of charging the battery, and also powers the electrical equipment of the running engine. It is no secret that without proper operation of this device, normal engine operation is impossible. I propose to understand the design of the generator, as well as consider some possible breakdowns and options for their elimination.
The device itself belongs to the category of electrical equipment, which has a rather complex design. Failure of the generator will lead to the lack of charging the battery, as well as the failure of the car motor. Buying a new generator or repairing a generator in a service center is not cheap and most likely will cost you a pretty penny.
However, if you are not from the “timid ten”, but you have a soldering iron at your disposal, and you know how to use it purely by accident, then it makes sense to try to repair the car generator yourself.
I propose, for a start, to disassemble the main "diseases" that often arise in the generator:
1. The device has stopped charging.
2. The device outputs too little voltage.
3. The generator is overcharging.
4. During charging, a warning light on the dashboard flashes.
5. During the operation of the device, some extraneous noise is heard.
The next step will be to determine the nature of some of the problems and determine the "root of evil".
If the generator has ceased to provide a normal battery charge, this may mean the following:
1. The fuse has blown, or just moved a little (contacts).
2. Critical wear of the brushes, or the brushes are broken or jammed.
3. The regulator relay is damaged.
4. The winding may be short-circuited or the rotor or stator circuit broken.
In the first three cases, it is likely that the defective parts will need to be replaced. However, if you have all the signs of the latter, then you have to tinker a lot.
There are several solutions to the problem.
You can just buy a normal stator winding, or send a broken one for repair and replace it. If the winding breaks, it is necessary to repair the rotor. Often, a winding break occurs in the slip rings (it can also be unsoldering one end of the winding). In this case, you will need to rewind the turns of the damaged section to the point of rupture. The wire must be long enough to solder to the slip ring. Next, you need to solder the broken off end of the winding from the slip ring and then make a serviceable end from the same winding (broken back, wiring).
It is possible that there was a desoldering of the end of the winding, which is located on the rotor. If so, then you just need to solder it back. If there is a need to clean the slip rings, do so. If there is a deep defect, it is removed with a file.
At the same time, as they say, you can eliminate one more "headache" - the noise of the generator. If the problem is urgent, you should visually inspect the bearing that is located on the rotor and, if necessary, replace it. However, if the bearing has no backlash, then it must be carefully removed and washed, for example, in gasoline, and then lubricated. The lubrication should be approximately 30% of the volume of the bearing itself. Then reinstall the bearing.
Battery overcharged or poorly charged.
If you have this kind of problem, you will need to look for a solution in the battery relay, if necessary, replace it. As a variant of this breakdown, the breakdown of the diode, which is located in the diode bridge, can also be considered.
The signal lamp is on when the current is correct.
Most likely, the reason lies in the breakdown of one or several diodes at once, which are responsible for the power supply chain passing through this lamp. You should look for these diodes on the same diode bridge. Unscrew three nuts on the generator, using a key for 7, and remove the stator winding fastener, kick back the nut on the generator output mount with a "+" sign and remove the diode bridge. By performing this procedure, you can replace the stator winding.
That's all. I hope my article will help you repair your auto generator yourself. Remember that you need to have at least some knowledge of electrical engineering to undertake this kind of work.
A car generator is a device that takes mechanical energy from an engine and converts it into electric current, thus providing electricity to the rest of the car's units. The generator provides battery charging and power to the vehicle's engine. Therefore, the connection "engine-generator" should not be interrupted, because an inoperative generator is a battery that does not receive a charge and, accordingly, an inoperative main body of the car.
Replacing the generator will entail significant financial costs. Therefore, if you have at your fingertips all the necessary tools and knowledge of the devices of the engine compartment of the car, then you can fix the breakdown yourself (read about what to do if the car does not start - the starter turns, read in our other article).
So the generator is broken. What malfunctions can cause this device to malfunction? Let's consider them:
- The generator produces a very low voltage current.
- The generator does not generate electricity at all.
- A breakdown of the device is displayed on the dashboard in the form of a blinking light.
- The generator is charging in excess of the optimal rate.
- Generator operation is accompanied by extraneous noise.
Before you start doing generator repairs with your own hands, it is necessary to check its technical condition and disassemble the unit into parts. Before disassembling the generator, check the condition of the belt and its tension and make sure if you are expecting a replacement of the alternator belt in the near future (read also how the timing belt is replaced with a VAZ 2109). Checking consists in pressing your finger on the middle of this part of the generator. If the belt is in good condition, then it should not fall by more than half a centimeter when pressed. It should be noted that the new belt should not bend more than 2 mm. If the belt is not worn out, but the tension is weak, then the defect can be corrected by tightening the generator belt. Also scroll the generator tension roller, if it scrolls with difficulty and squeaks, then it will need to be oiled, or put a new roller instead.
The technical condition of the generator can be checked using the following measuring instruments:
The rotor speed is measured using a tachometer (usually located next to the speedometer on the dashboard). During normal operation of the generator, the indicators of this device should not be less than 2000 rpm, while the norm is 5000 rpm.
Let's consider the reasons that can cause generator breakdown. So, if the generator does not generate a charge, then the following phenomena may be the reasons for this:
- Fuse or contacts blown.
- Broken or worn out generator brushes.
- The regulator relay is out of order.
- Due to the short circuit of the winding, an open circuit occurred in the stator or rotor circuit.
In order to fix the first three malfunctions from the list, you just need to replace the worn out parts of the generator, having previously, of course, disassembled it.
- First of all, remove the brush holder along with the voltage regulator, carefully unscrewing all fasteners.
- Remove the tensioning bolts and then the cover with the stator.
- Remove the cover from the stator by first disconnecting the phase windings from the output wires on the rectifier unit.
- Next, remove the pulley from the shaft and the front cover of the generator using a special puller.
The assembly of the generator is carried out in reverse order.
In the event of a short circuit in the winding, you will need more serious action than a simple replacement of the part. So, a broken winding can either be repaired or replaced with new wires. Often the winding breaks off near the slip rings. In addition, breakdown can occur due to unsoldering of any of the ends of the winding. Such a malfunction can be repaired by rewinding the coil in the area of the gap back from the rotor winding. Further, the broken end of the winding must be removed (evaporated) from the slip ring and the previously unwound wire must be soldered there. The wiring is very easy to repair by re-soldering the wiring.
A weak or too strong generator charge is indicated by a damaged relay, which must be replaced when the generator is repaired.
If the generator voltage check showed that the device is working, but the indicator is flashing on the instrument panel, then, most likely, one of the diodes that are responsible for powering the light in the indicator has failed. These diodes are located in the generator itself, and replacement is carried out after disassembling the device.
Noise unusual for a generator may be indicated by wear of the rotor bearing. If an inspection reveals that the generator bearing is worn out, it will need to be replaced.If the incomprehensible sounds of the generator are associated with the absence of play in the bearing, then it can be simply filled with oil, having previously washed it in gasoline. Extraneous sounds will then disappear.
Thus, you can even repair the generator on your own in your garage (as well as overhaul of the engine, in fact). When checking and replacing parts of the device, observe safety precautions and be careful, because the electrical system should not be damaged in this case.
Electric generators are used to convert mechanical energy into electrical energy. All electrical gadgets are flexible enough and easily adapt to the needs of the person. Any engine can work both as a motor and as a generator. If you take an electric motor and apply voltage to it, the shaft will begin to rotate at a certain speed. If the shaft is rotated at a certain speed, then the electrical current can be removed from the terminals. Here, however, there are pitfalls - the rotational speed must be certain, and besides, the greater the load will hang, the harder it will be to turn the shaft.
All vehicles are equipped with a generator. The generator generates a constant electric current for the needs of the vehicle's on-board network and for charging the battery. The sum of all the power of the electrical equipment of the machine must be less than the power of the generator. The calculation is as follows:
- battery I = C * 0.1 = 60 Ah * 0.1 = 6 A;
- lamps I = P / U = ((21 +55 +10) * 2 + (21 +21 +5 + 10) * 2) / 12 = 24 A;
- cigarette lighter 10 A;
- trampler with a reel 5 A;
- etc.
Generators are made three-phase with rotor excitation. Excitation is needed to control the voltage generated by the generator. For example, if you close the contacts of the relay-regulator and spin the generator shaft to a speed of 1000 rpm, then the generator will generate 13 V, and already at 2000 rpm, the voltage will rise to 20 V and will continue to grow depending on the engine speed ... 20 V is an overvoltage for all power users of the machine and can ruin all electrical equipment. To prevent this, the generator is equipped with a device that controls the excitation on the rotor, called a relay-regulator. The relay regulator monitors the voltage that is supplied through it to the generator and stabilizes it at around 14.4 V or 2.4 V / bank. If it is not possible to stabilize and the voltage rises, then the relay-regulator closes and does not pass current through itself, which leads to the termination of the excitation of the rotor and the termination of generation.
The generator connection diagram is presented below. The usual connection of the generator from the Zhiguli. Generators are available with and without a built-in relay-regulator. The built-in relay-regulator is inconvenient in terms of diagnostics and installation in the case, so if it turned out that it was it that burned out - down with it and install only the brushes with the contact removed, since the fastening device allows you to do this simply. So, plus through the ignition switch and the fuse, it goes to the relay-regulator, which is connected to the excitation winding of the generator through copper-graphite brushes. The output to the brushes is bare and uncovered.
In contrast to the input to the brushes, the output from the middle point of the motor windings, connected in a star, is covered with a plastic insulator. The output is needed to indicate the operation of the generator. As soon as generation begins, a potential of 6 V appears at the midpoint. This potential turns on an auxiliary relay, which extinguishes the charging lamp on the instrument panel.
Diodes are needed to rectify three-phase current. It is interesting that an alternating voltage is generated at the midpoint of the windings, so you can turn on the relay with both a minus and a plus.
In foreign generators, the relay-regulator is built into the generator itself, but this does not mean that it cannot be thrown out and put in an external relay-regulator and auxiliary relay. The built-in gadget is sometimes quite a lot, and ours - a penny.So you have to do some magic to save the kids on ice cream. The light is switched on by a minus, which gives the relay-regulator. When generating, a plus is also supplied to the light bulb from the side of the relay-regulator and the light goes out. Otherwise, everything is the same.
A standard generator from a foreign car produces 360 W or 30 A. This is quite enough for all electrical receivers, naturally in the factory configuration. The generator is located next to the cooling pump and is connected via a belt to the crankshaft and pump pulleys. The generator must be in constant tension, otherwise electricity will not be generated. However, if the belt is pulled too tight, the pump bearings will fly out, so here you need a middle ground. It is believed that with average finger pressure on a tensioned belt, the belt should bend by 15 mm. With this tension, the belt will be tensioned, the generator will produce the required current, and the pump bearings will work for a long time. The generator is bolted through the ears on the generator itself and the mounting plate on the engine. To fix it in a given position, a second bolt passes through the upper ear and the guide. On modern machines, an automatic tensioning of the alternator belt is installed using an additional pulley with a spring tensioner.
The pulley on the alternator is secured with a nut. Unscrew the nut simply with an impact wrench, or you need to fix the pulley and unscrew the nut.
All leads are located on the side opposite to the pulley. Here there is a connector for connecting excitation from the battery through a fuse and a contact for connecting an indication lamp. It is important that foreign generators do not want to start being excited without an indicator light. So if the light bulb burns out and you don't pay attention to it when you turn on the ignition, you can put the battery somewhere far from home. Also here a wire is brought out from the midpoint of the transformer windings to bypass the function of the relay-regulator. A bolt and nut for connecting the main power plus is seen from the side. The relay-regulator is covered with a radiator, which is closed with a lid.
The cover is secured with three screws. Under the cover there are a relay-regulator with a radiator, a horseshoe-shaped three-phase rectifier and a brush assembly, covered with rubber protection.
The brush assembly is mounted on two screws that are not in the same plane. One brush rings with one contact, and the second brush with another. In the removed state, the brushes should not ring among themselves. The brushes fit against two slip rings on the rotor. The rings ring among themselves and do not ring out to the body.
The brushes are spring loaded and run in the holder. Brushes need to be replaced when worn. The gap between the body of the brush assembly and the rotor is a couple of millimeters. The brushes protrude by about 6 mm, which means a reserve of 4 mm. This is not enough, so it would be better to replace the brushes. The brushes should be installed as recommended by the manufacturer of this generator. If you put any others, then over time, the slip rings will eat up and the current will not be strong enough.
The horseshoe-shaped rectifier consists of six diodes. With a generator current of 30 A, each diode withstands 15 A in theory, but the manufacturer puts diodes with a margin, so each holds about 25 A. The bridge rings from the negative output to the positive output like two diodes connected in series. The generator winding leads are attached to the rectifier with four screws - three windings and a midpoint. You can ring each diode separately.
On the back of the rectifier, you can see the leads of the diodes. The diodes are divided into groups. On the outside of the rectifier there are insulators passing through the rectifier and going into the winding leads.
The relay-regulator is fixed by three screws, and the rectifier by four. After removing the relay and rectifier, you need to unbend the ends of the windings and remove the cover. The ends of the windings and the lead from the midpoint stick out upward.
The back cover has a protrusion for the alignment of the two covers for the fasteners. In the center there is a bearing seat. When repairing the cover, you need to clean it well.
There is a bearing under the pulley. To get to it, you need to completely disassemble the generator and remove the cover.
After removing the relay-regulator and rectifier unit, the rotor is removed from the front bearing. The excited rotor is an armored coil with a transformer steel core. The rotor leads are connected to two copper current collectors.
The front bearing sits in the cover and is closed by a steel plate with screws. The bearing is easily knocked out of the cover using a wooden hammer handle, after unscrewing all the screws securing the cover. The windings are also removed from the generator cover.
![]() |
Video (click to play). |
Problems in the operation of the car generator and methods for their elimination: