In detail: do-it-yourself power supply for phone repair from a real master for the site my.housecope.com.
Greetings radio amateurs.
Going through old boards, I came across a couple of switching power supplies from mobile phones and I wanted to restore them and at the same time tell you about their most frequent breakdowns and troubleshooting. The photo shows two universal schemes for such charges, which are most often found:
In my case, the board was similar to the first circuit, but without the LED at the output, which only plays the role of an indicator of the presence of voltage at the output of the block. First of all, you need to deal with the breakdown, below in the photo I outline the details that most often fail:
And we will check all the necessary details using a conventional DT9208A multimeter.
It has everything you need for this. The continuity mode of diodes and transistor junctions, as well as an ohmmeter and a capacitor capacitance meter up to 200 microfarads. This set of functions is more than enough.
When checking radio components, you need to know the base of all parts of transistors and diodes, especially:
Now we are completely ready to check and repair the switching power supply. Let's start checking the block for visible damage, in my case there were two burnt resistors with cracks on the case. I did not reveal more obvious shortcomings, in other power supplies I met swollen capacitors, which also need to be paid attention first of all. Some details can be checked without desoldering, but if in doubt, it is better to desolder and check separately from the circuit. Be careful when soldering so as not to damage the tracks. It is convenient to use a third hand during the soldering process:
![]() |
Video (click to play). |
After checking and replacing all faulty parts, do the first switch-on through a light bulb, I made a special stand for this:
We turn on the charger through the light bulb, if everything works, then we twist it into the case and rejoice at the work done, if it doesn’t work, we look for other shortcomings, and after soldering, do not forget to wash off the flux, for example, with alcohol. If all else fails and the nerves are on the line, throw away the board or unsolder it and take away the living parts as a reserve. Good mood everyone. I also suggest watching the video.
JLCPCB is the largest prototype PCB factory in China. For more than 200,000 customers around the world, we place over 8,000 online orders for prototypes and small batches of printed circuit boards every day!
This article was born due to the fact that I had to deal with the frequent repair of cell phone chargers. Even though the price of a Chinese charger does not exceed 100 rubles (new), they are carried to me regularly. And for all their uniformity, there are slight differences in the construction of the charger circuitry.
This article will combine chargers that I copied myself and found on the Internet.
LG phone charger circuit
Another version of the charger is the so-called Frog
And finally, the scheme for obtaining from 12-24V at the output 4.5V 0.8A. Car adapter Panasonic Pulse, stabilized on 4 transistors.
In the radio industry, to check or repair a cell phone, a simple power supply from a suitable charger, with an output of 6-8V 0.5-0.7A, may come in handy. To do this, we need a suitable charger from a cell phone and an LM1117 stabilizer, or similar. You can find these stabilizers on motherboards, video cards and various Chinese devices. And you can get hold of the boards themselves in computer repair shops, where they are simply thrown away.
Previously, I already laid out a similar alteration of the memory, you can see it here:
https://my.housecope.com/wp-content/uploads/ext/2533/forum/3-3792-2 post 16.
We assemble a voltage regulator on a miniature seal and set the 4V output with a resistor R1.
If space in the memory allows, you can solder a small heat sink, it will not hurt. Then we build the scarf into any free place in the memory, and for greater safety it can be put on heat shrink.
We remove the old cord and drill out the adapter block and insert a suitable one with thicker wires. We solder mini crocodiles or mini clips like mine, if any, to them.
As a result, we get a simple power supply for checking or repairing cell phones. Moreover, the block can be useful for the initial charge of completely dead lithium batteries (their rise), for the subsequent full charge. For this, a small heat sink is useful in the block, because. the stabilizer in this application will warm up a little ..
Good luck with the repair..
In most cases, breakdowns of cell phones are quite easy to fix and come down to replacing the display, speaker, all kinds of cables and body elements. In the vast majority of cases, complex soldering of any elements is not required. The repair process is limited to replacing the display or a cable that connects to the cell phone circuit board via a connector. It is also quite often required to clean the cell phone circuit board from corrosion and oxides. At the same time, time-consuming soldering of microcircuits and other elements is not required.
But there are breakdowns that require the replacement of a microcircuit or the soldering of an element on the printed circuit board of a cell phone (SIM card holder, battery connector, power connector, etc.).
For successful repair of cell phones, a special tool is naturally needed. In addition, consumables are also needed, which should be on hand during the repair process.
When equipping one workplace for the service repair of cell phones, you will need several devices. Let's list them. Devices required for software repair of cell phones will not be considered.
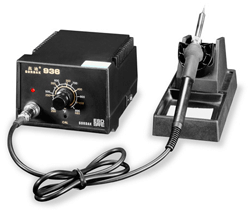
The soldering station has all the necessary functions for working with small parts. This includes adjusting the temperature of the soldering iron tip within 200 0 - 480 0 C, digital indication of the temperature of the tip, the ability to use all kinds of tips for any work. It is also worth noting that a conventional electric soldering iron is not galvanically isolated from the mains, which increases the likelihood of damage to sensitive electronic elements on the mobile phone board. Therefore, a conventional electric soldering iron is not suitable for repairing cell phones.

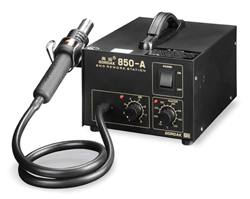
The motherboards of computers and laptops use microcircuits that have larger linear dimensions than the microcircuits on the circuit board of cell phones, and during dismantling, uniform and larger heating of the microcircuits is required. Infrared soldering stations just have such qualities as uniform heating.
Unlike infrared soldering stations, hot air soldering stations heat the soldered element less evenly. In addition, when working with a hot air soldering station, it is necessary to monitor the flow rate of hot air. If you set too high an air flow rate, then when soldering it is easy to “blow off” neighboring elements and the heating of the element will be uneven due to the presence of hot air swirls. If you reduce the air flow rate, then the heating of the soldered part will be slower due to the fact that the still air is a heat insulator.
Despite the negative qualities of hot air soldering, hot air soldering stations are actively used in the repair of cell phones. The small dimensions of the printed circuit boards of cell phones and electronic components on them allow for high-quality assembly and disassembly of microcircuits and small-sized elements. Of course, during the repair process, it is worthwhile to correctly set the speed of hot air supply through the nozzle of the hair dryer and the air heating temperature.

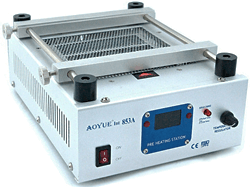
If it is necessary to dismantle any part from the printed circuit board of the device, it is necessary to heat the element to the solder reflow temperature. Since SMT elements and BGA microcircuits are very widely used in portable electronics, when soldering with hot air, you have to warm up the microcircuit case first, and only then the contacts themselves. Naturally, heat transfer occurs from the heated microcircuit to the printed circuit board. This leads to the fact that it takes a long time to heat the soldered element, which can lead to its overheating.
In addition to overheating of electronic components, there is also the possibility of damage to the printed circuit board. With uneven heating, it begins to warp, deformation, delamination occurs. If you sharply heat the printed circuit board to a temperature of more than 280 0 C, then it will swell. In the future, it will not be possible to eliminate such deformation of the printed circuit board. For smooth and uniform heating of the printed circuit board, the bottom heating station is used.
When replacing elements such as, for example, the SIM card holder, the lower heating of the board is very convenient. Before soldering the defective latch, the printed circuit board is heated using the bottom heating station of the boards to a temperature of 120 0 - 140 0 C. In this case, the solder at the place of soldering the contacts warms up and for its final reflow, short-term soldering with hot air using a hot air gun is required. If you solder the latch only using a hot air soldering station, then prolonged exposure to hot air will deform the plastic base of the SIM card latch. It is clear that when replacing joysticks, the bottom heating station will also facilitate the work and allow it to be done more efficiently.


For convenience, you can use a regular serviceable battery from any cell phone.Conductors with crocodile clips are soldered to its conclusions (there are three of them). Such a universal rechargeable battery can be used in the repair of any cell phone. The main thing is to be able to correctly connect the clamps to the power connector of the cell phone being repaired and from time to time charge such a universal battery.
In many cases, a universal power battery is enough to diagnose a malfunction of a cell phone and check its health. In this case, a stationary power supply may not be required at all.


For deeper cleaning from corrosion and restoration of telephone boards - “drowned” are used ultrasonic baths (USW). Cleaning agent is poured into the ultrasonic bath. Under the action of ultrasonic waves, microbubbles appear in the liquid, which, collapsing and moving randomly, effectively clean all elements damaged by corrosion. Ultrasound accelerates chemical and physical processes, and the use of a special cleaning fluid contributes to high-quality cleaning. Using an ultrasonic bath, you can restore the operation of a seemingly hopeless cell phone.

This is only a tentative answer to the question of what equipment you need to have in a cell phone repair shop. Many of the listed devices will not be required immediately, but as you grow professionally and develop your business. It is also worth noting that the devices necessary for software repair are not considered here.
Do not forget that in the process of hardware repair, consumables are needed: flux, solder paste, cleaner, etc.
Perhaps the most "sick" part of a cell phone is its charger. A compact DC source with an unstable voltage of 5-6V often fails for various reasons, from the actual malfunction to mechanical failure as a result of careless handling.
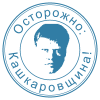
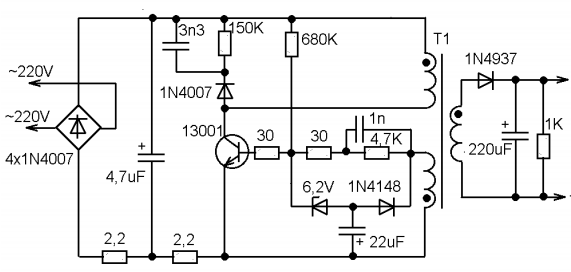
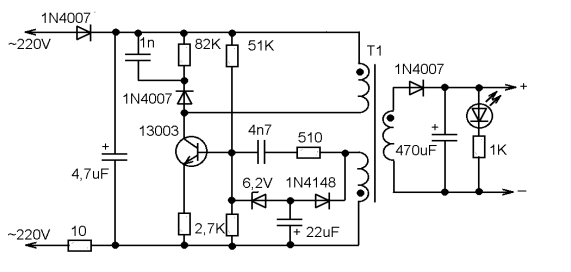
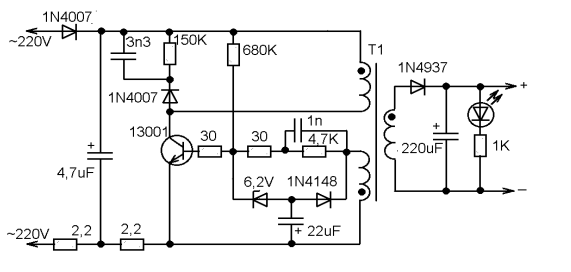
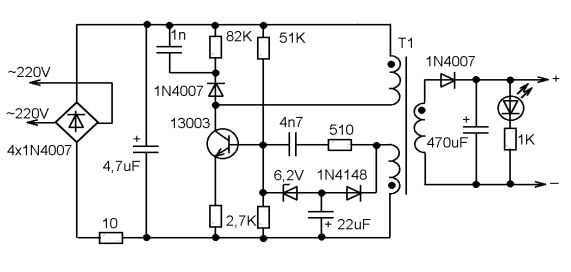
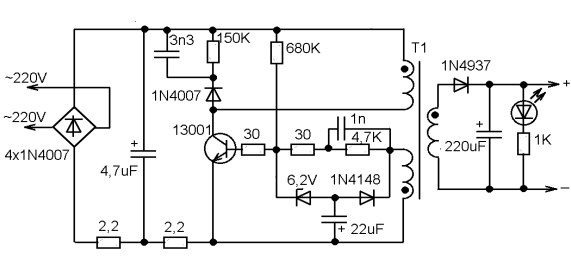
And so, what are the "typical" malfunctions? First of all, you should pay attention to the capacitors. The breakdown of the capacitor connected after the mains rectifier is very likely, and leads both to damage to the rectifier and to the burnout of a low-resistance constant resistor connected between the rectifier and the negative plate of this capacitor. This resistor, by the way, works almost like a fuse.
Often the transistor itself fails. Usually there is a high-voltage power transistor, designated "13001" or "13003". As practice shows, in the absence of such a replacement, you can use the domestic KT940A, which was widely used in the output stages of video amplifiers of old domestic TVs.
The breakdown of the 22 uF capacitor leads to the absence of generation start. And damage to the 6.2V zener diode leads to unpredictable output voltage and even failure of the transistor due to overvoltage at the base.
Damage to the capacitor at the output of the secondary rectifier is the least common.
The design of the charger case is non-separable. You need to saw, break: and then somehow glue it all together, wrap it with electrical tape. There is a question about the feasibility of repair. Indeed, in order to charge a cell phone battery, almost any source of direct current with a voltage of 5-6V, with a maximum current of at least 300mA, is sufficient. Take such a power supply, and connect it to the cable from the faulty charger through a 10-20 ohm resistor. And that's it. The main thing is not to reverse the polarity. If the connector is USB or universal 4-pin, turn on the resistance of about 10-100 kilo-ohms between the middle contacts (choose it so that the phone “recognizes” the charger).
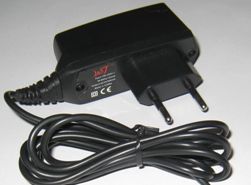
– failure of the charger unit;
- violation of the contact connection of the wire with the plug or charger unit.
Very often, the reason for the failure of the charger is a wire break or a violation of the contact of the wire with the structural elements of the charger - the plug and the block. In this case, you can repair the charger yourself. Consider the principle of repairing damage to the charger wire using a specific example of repairing a Nokia mobile phone charger (with a thin plug).
To repair the charger, we need:
- a soldering iron and everything you need for soldering;
- insulating tape and heat shrink tube (if available);
– a small piece of thin wire to make contact with the inner contact part of the charger plug (for the slim Nokia charger plug).
The first stage is the search for damage to the wire or contact connection. Damage to the wire can be determined visually. The place where the conductive wire broke, as a rule, is of a different color and slightly smaller in diameter.
If a visual inspection failed to determine the location of the damage to the wire, then most likely the charger does not work due to the wire being torn off at the point of its attachment to the block or plug. The wire may also be damaged, we will find out in the process of further finding the damage.
We take the wire and cut it off 7-10 centimeters further than the plug. If there is no contact failure at the point of connection to the plug, we will connect the wire at the cut point. Therefore, you cannot cut the wire at the point of attachment to the plug, that is, you must leave a small piece to be able to connect the wires by soldering.
Strip the wires on the part of the wire that goes to the charger. Take a multimeter and select a DC voltage measurement limit of 20 volts.Connect the charger to the network and measure the voltage value at the output of the charger, that is, at the stripped ends of the cord.
We measure the voltage at the output of the memory
If the device shows a voltage value, then this indicates that the charger unit and the wire are not damaged. In this case, the device showed 7 volts - this is the nominal output voltage of this charger. At this stage, we can conclude that the memory does not work due to a violation of the contact of the conductors at the point of their attachment to the plug. You can verify this by ringing the plug with the device.
To do this, we clean the wires that come from the plug, insert a thin wire into the inside of the plug (this is necessary for contact with the internal contact part of the plug).
We take a multimeter and select the dialing mode. With one probe we touch one of the stripped conductors, and with the other, first to the outer contact part of the plug, and then to the inserted wire. If the device showed contact (the presence of a sound signal), then this indicates that the contact between this wire and the plug is not broken.
We rearrange the probe of the device to another stripped conductor, with the other we alternately touch the outer part of the plug, and then the wire. If, when touching both contact parts of the plug, the device did not emit a signal, then there is no contact. That is, one of the wires is torn off from the plug.
In this case, there are two ways: you can purchase a new plug, or you can repair the old one. The first way is easier and more reliable. A new plug can be purchased from mobile phone repair shops or the radio market. You may have an old charger with an intact plug.
In this case, it is enough to solder a new plug to the charger, while observing the polarity. How to check the correct connection of wires (polarity)? As a rule, each cord has a color-coded wire. If it does not match, then you need to make sure that the wires are connected correctly.
To do this, plug the charger into a power outlet and the new plug into your mobile phone. Connect the plug wires to the charger cord. If the charging went, then you connected the conductors correctly. If the phone does not charge, swap the conductors. The check must be carried out in any case, even if the color coding of the connected cords is the same, as there may be discrepancies in the marking of the cords.
The next step is to connect the two cords by soldering. If you have heat shrink tubing, then before soldering, put a part of it on one of the cords to be soldered. Solder the conductors, observing the polarity. Insulate both wires with insulating tape, put on heat shrink tubing. Check the functionality of the charger.
If you do not have the opportunity to purchase a new plug, but you still want to reanimate the charger, then the second way to repair the damage is suitable for you - repairing the plug.
We remove the rubber (plastic) coating from the plug with a knife. In this case, be careful, do not rush, as you can damage the plug itself.
Remove the rubber cover from the plug
The next step is to solder the charging cord to the plug.
Soldered cord to plug
Check the performance of the charger. If everything is normal, we isolate the conductors, and put a heat shrink tube on the plug. The charger is ready for use.
Heat shrink tube on plug
We considered the case of contact failure at the point of connection of the cord to the plug. There may also be another reason. Let's consider one more case.
You cut the wire, checked for voltage at the output of the charger, it is missing. We cut the wire near the charger, stepping back from the charger unit 7-10 cm. We clean the wire that comes out of the charger unit and check for voltage at the output.The presence of voltage at the output indicates that the memory is working properly. We call the plug according to the above method. In this case, there is no contact failure.
The continuity of the charging cord showed that one of the conductors was broken. No visual damage is visible. The best option is to purchase a new wire. Then solder it to the plug and charger unit, observing the polarity.
In order not to be mistaken (especially if the wires have the same color marking), before soldering the wires, connect them and plug the charger plug into the phone. If charging has started, connect the conductors by soldering. Insulate the wires at the soldering point and put on a heat shrink tube (it must be put on the wire before soldering). The damage has been repaired.
If the wire is intact, the contact connection of the plug is not broken, then the charger unit is damaged or one of the wires inside the unit is torn off.
Unscrew the charger block and look at the wire connections. If all the wires are connected normally, then the memory unit itself is damaged.
If your charger unit is damaged, then, without having skills in the field of electrical engineering, you will not be able to find the cause of its failure, much less fix it yourself. Repairing a charger at a specialized service will cost you more than a new charger.
The article talks about a typical malfunction of mobile phone chargers. A diagram of one of these blocks, compiled according to a "live" model, is given, recommendations are given for changing the output parameters and using the repaired block in amateur radio practice.
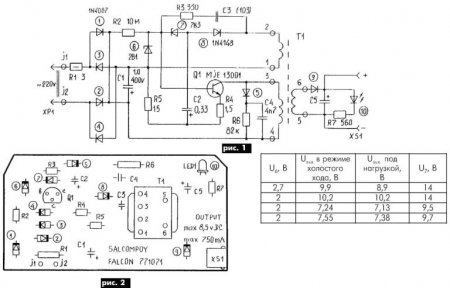
The culprit was the zener diode, conditionally indicated in the diagram of Fig. 1 by the number 7. It had a leak and “floating” parameters.
The free space in the power supply housing made it possible to use a chain of several series-connected domestic zener diodes instead. At the same time, it was easy to obtain other, except for the passport, values of the output voltage (see table).
This will probably be of interest to radio amateurs, since they will always find use for such a powerful and small-sized power supply. The location of the elements on the board is shown in Fig.2.
First, the block must be disassembled. Judging by the seams on the case, this block is not intended for disassembly, therefore, the thing is disposable and you can not pin high hopes in case of a breakdown.
I had to literally unravel the case of the charger, it consists of two tightly glued parts.
Inside is a primitive board and a few details. It is interesting that the board is not soldered to the 220v plug, but is attached to it using a pair of contacts. In rare cases, these contacts can oxidize and lose contact, making you think the block is broken. But the thickness of the wires going to the connector on the mobile phone was pleasantly pleased, you don’t often see a normal wire in disposable devices, usually it’s so thin that it’s even scary to touch it).
There were several parts on the back of the board, the circuit turned out to be not so simple, but still it is not so complicated as not to fix it yourself.
Below in the photo are the contacts of the inside of the case.
There is no step-down transformer in the charger circuit, its role is played by an ordinary resistor. Then, as usual, a couple of rectifying diodes, a couple of capacitors for rectifying the current, then a choke and finally a zener diode with a capacitor complete the chain and output a reduced voltage to a wire with a connector to a mobile phone.
There are only two pins in the connector.
When such a charger breaks down, first of all, pay attention to the appearance of the parts, often only by appearance you can determine which part is out of order. Carefully inspect the throttle, it has a very thin wire and it can simply burst.If nothing can be revealed by eye, and you yourself do not understand anything in electronics, ask those who know to check the details with a tester. If the power supply is completely unrepairable, then you can assemble your circuit much easier, and if you use a step-down transformer in the circuit, as is done in branded chargers from Nokia mobile phones, then problems with breakdowns will disappear for a long time. And finally, the easiest way to fix this charger is to buy a new one 🙂
Siemens has chargers with a pulse-type power supply, in the article the board is described as a parametric power supply. This is fundamentally not true. Written by a non-professional. The price of the article is zero.
Charging is originally expensive to the same Chinese 50 rubles and 20 in the purchase!
buy a cheap phone buy a cheap charger
I disassemble glued chargers, power supplies by gently tapping on the case at the points of gluing with a rubber mallet. The body rests on an anvil.
I completely agree with Alexander about the incorrect description, but photos of the disassembled charge may be interesting for those who understand.
. as Kuravlyov said in the famous film. “well, fool.”
It would be nice to write the values \u200b\u200bof all resistors, or even R13 and R16
Thank you for the article. Presented in an accessible and understandable way. Repaired charger. It turns out that some kind of piece of iron fell off, I inserted it and OK!
As a rule, the repair of such an inexpensive device is not economically viable.
Especially in non-poor countries. The average price is 5 dollars.
But it happens that there is no extra money, but there is time and spare parts.
There is no shop nearby. Circumstances do not allow. Then it's not about the price.
In my case, everything was simple - one of my two chargers broke Nokia AC-3E, friends brought a bag of broken chargers. Among them there were about a dozen branded Nokia chargers. It was a sin not to take it.
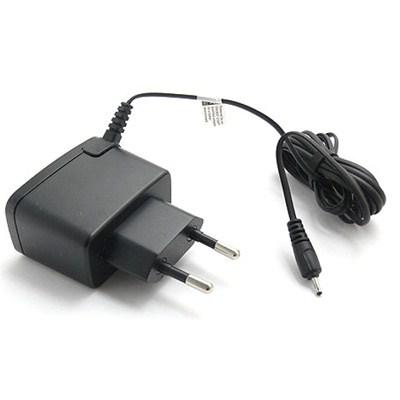
The search for the circuit did not lead to anything, so I took a similar one and remade it for AC-3E. A lot of chargers for mobile phones have been made according to a similar scheme. As a rule, the difference is not significant. Sometimes the ratings are changed, a little more or a little less elements, sometimes a charge indication is added. But basically the same thing.
Therefore, this description and diagram will be useful for repairing not only AC-3E.
The repair manual is simple and written for non-experts.
The scheme is clickable and of good quality.
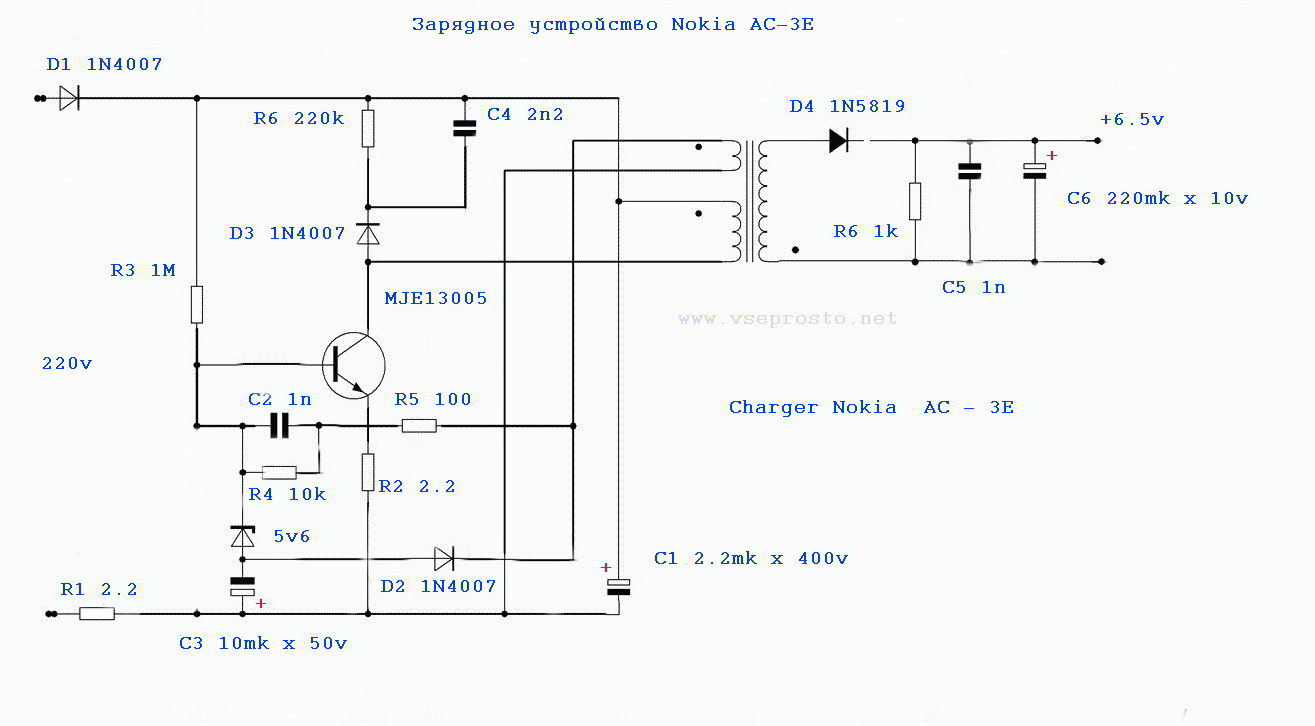
The device is a blocking generator operating in self-oscillating mode. It is powered by a half-wave rectifier (D1, C1) with a voltage of approximately +300 V. Resistor R1, R2 limits the starting current of the device and acts as a fuse. The blocking oscillator is based on a transistor MJE13005 and pulse transformer. A necessary element of a blocking generator is a positive feedback circuit formed by winding 2 of the transformer, elements R5, R4 C2.
The 5v6 zener diode limits the voltage at the base of the MJE13005 transistor to within five volts.
Snubber chain D3, C4, R6 limit voltage surges on winding 1 of the transformer. At the moment the transistor turns off, these surges can exceed the supply voltage by several times, so the minimum allowable voltage of the capacitor C4 and diode D3 must be at least 1 kV.
1. Disassembly. The self-tapping screws holding the charger cover in this device look like a triangular star. As a rule, there is no special screwdriver at hand, so you have to get out as best you can. I unscrewed it with a screwdriver, which, during the operation, sharpened itself for all sorts of crosses.
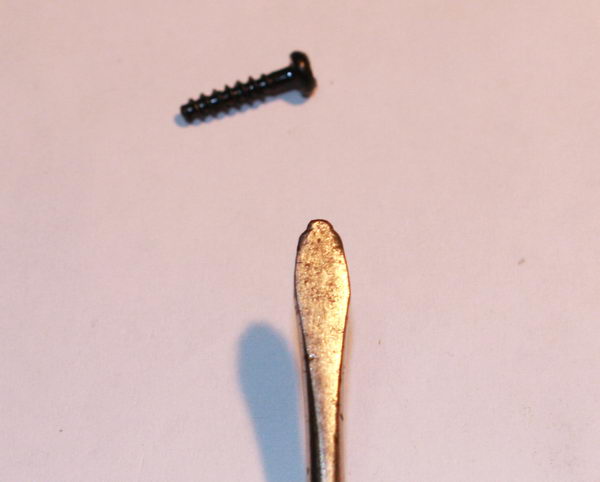
Sometimes chargers are assembled without bolts. In this case, the body halves are glued together. This indicates the low cost and quality of the device. Disassembling such a memory is a little more difficult. It is necessary to split the body with a non-sharp screwdriver, gently pressing on the junction of the halves.
2. External inspection of the board. More than 50% of defects can be detected precisely due to external examination. Burnt resistors, a darkened board will show you the location of the defect.A burst case, cracks on the board will indicate that the device was dropped. Chargers are operated in extreme conditions, so falls from everywhere are a common cause of failure.
In five out of a dozen memories that I had a chance to do, they were trite contacts are bent through which 220 volts are supplied to the board.
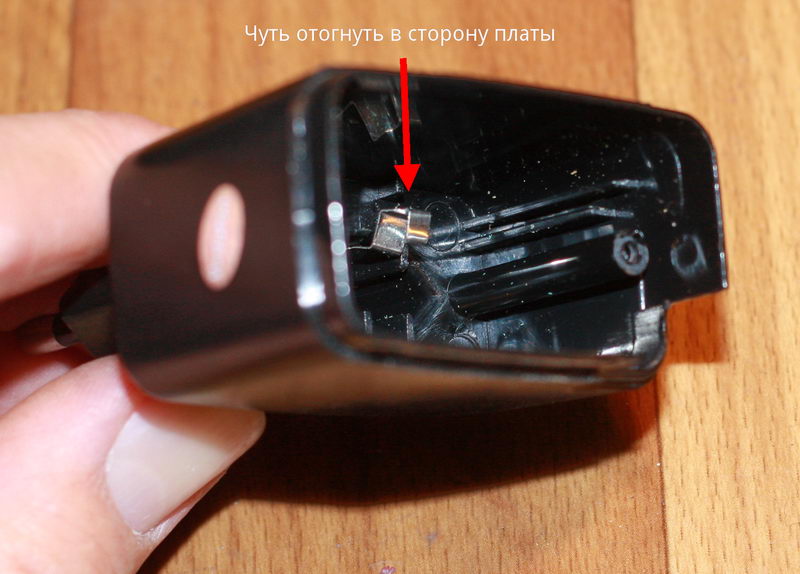
To fix it, just bend the contacts slightly towards the board.
To check the contacts are to blame or not, you can solder the power cord to the board and measure the output voltage - red and black wires.
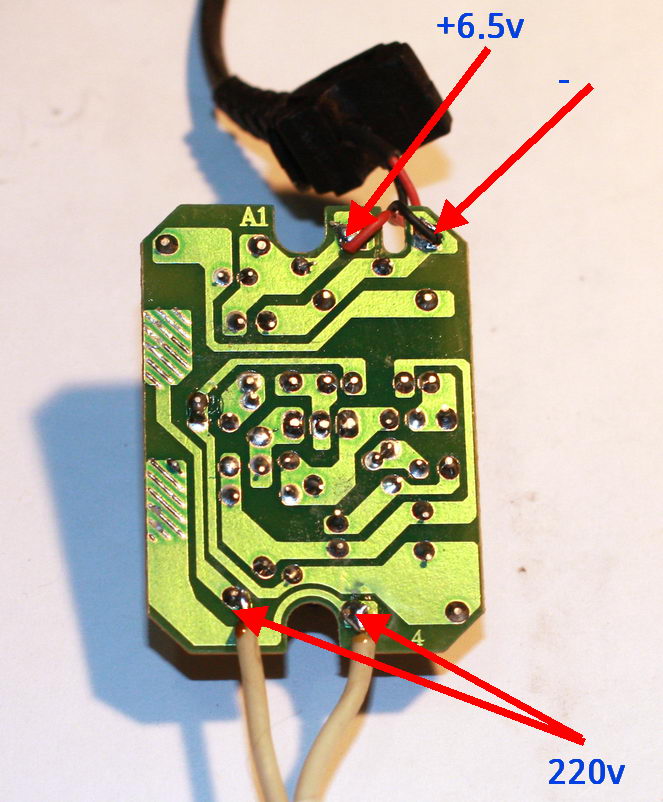

3. Broken cord at the output of the memory. It breaks as a rule at the plug itself or at the base of the charger. Especially for those who like to talk while charging the phone.
Called by the device. Insert the lead of a thin part into the center of the connector and measure the resistance of the wires.
4. Transistor + resistors. If there is no visible damage, first of all you need to unsolder the transistor and ring it. It must be borne in mind that the transistor
MJE13005 base is on the right, but it happens the other way around. The transistor may be of a different type, in a different case. Let's say MJE13001 looks like a Soviet kt209 with a base on the left.
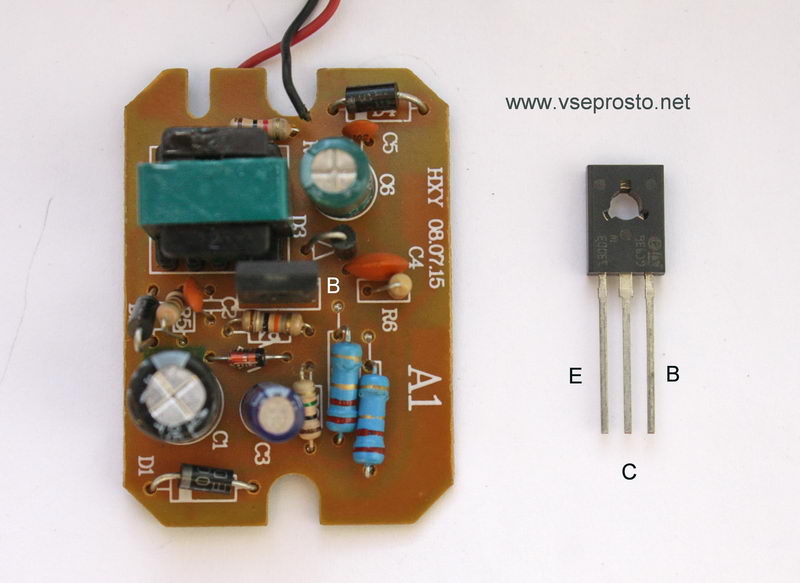
Instead, I put MJE13003. You can put a transistor from any burnt lamp - the housekeeper. In them, as a rule, the filament of the bulb itself burns out, and two high-voltage transistors remain intact.
5. The consequences of overvoltage. In the simplest case, they are expressed in short-circuited diode D1 and a broken resistor R1. In more complex cases, the MJE13005 transistor burns out and inflates the capacitor C1. All this elementary changes to the same or similar details.
In the last two cases, in addition to replacing burnt conductors, it will be necessary to check the resistors around the transistor. With a diagram, this will be easy to do.
The phone is not charging. The power supply is not working. Charging adapter does not work. All these problems can be caused by elementary breakdowns, which are easily fixed with:
- Ohmmeter or multimeter;
- Phillips small screwdriver;
- Low power soldering iron with a thin tip;
- Spare parts and parts that can be borrowed from another, not working, adapter or phone charger.
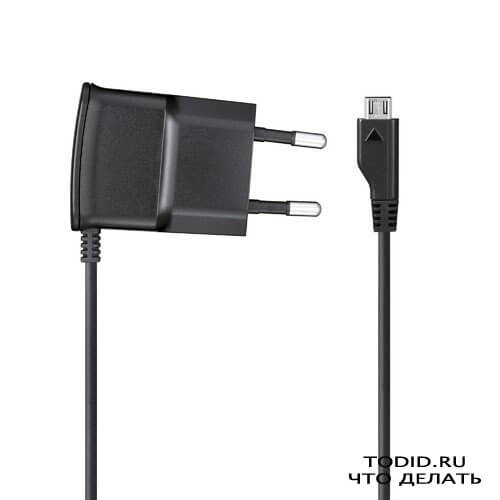
First of all, the site my.housecope.com/wp-content/uploads/ext/2985 emphasizes that there are two types of power adapters:
In any case, the methods described in the article will help test the device for performance, make easy repairs. This means that the failed device will work again, and you won’t have to go to the store for a new power supply or phone charger.
How to check the charger for performance and repair the power adapter
1. Pay attention to the indicator, which is located on the body of each adapter. The LED should be on. If this is not so, then:
A) the LED burned out;
b) no electricity is supplied to it.
1.1. We call the wiring using a multimeter or ohmmeter. Important: when measuring the resistance of each wire, pay attention to the multimeter display indicators. A broken wire will have an infinite resistance value. If such a wire is detected, then it is because of it that the adapter (charger, power supply) broke. Most often, the adapter for the power supply does not work for this reason.
Note: in order not to break the insulation, you can use sewing needles, stuck wires, as outlet contacts.
Accordingly, the adapter broke down precisely for this reason, which means that you need to replace the bad wire or eliminate the gap with a soldering iron.
2. If the wiring is good, and the indicator does not light up or the adapter does not charge, disassemble the adapter case by unscrewing the mounting bolts with a suitable screwdriver.
What do we see? Two main blocks:
- A transformer that reduces the voltage to the required value from standard 220V;
- An electronic circuit that converts alternating current into direct current, brings it to exactly the required values.
Accordingly, the breakdown is hidden either in the circuit or in the transformer. Of course, if there are no noticeable breaks in contacts between these elements inside the adapter case.
3. Breakdown of the transformer is a break or burnout of a low-quality (probably Chinese) winding.
3.1. You can identify the problem by ringing the primary and secondary windings with a multimeter. It is done like this:
A normal working adapter on the plug contacts (which is for a socket) has a resistance of several thousand ohms (kilo-ohms, kOhm). If your check reveals this fact, then the primary winding is working properly. And so we keep looking
3.2. When checking the transformer, it is important:
- disconnect the adapter plug from the power outlet beforehand;
- do not touch the contacts with your hands (this is not dangerous, but it violates the accuracy of objective measurements);
- unsolder the contacts of the electrical circuit from it (if it is faulty, it will affect the readings of the ohmmeter, introducing confusion).
4. We check the secondary winding to find out why the power supply does not work.
To do this, we measure the resistance of individual diodes from the diode bridge. This bridge is responsible for the electric current flowing through the secondary winding and may interfere with its normal movement, contribute to the breakdown of the adapter (charger, power supply).
There is no need to solder anything from the circuit here. A faulty diode will show zero or too low a resistance value. The working diode, accordingly, will show too high, almost infinite resistance values.
5. Let's move on to checking the electronic circuit. This element of the adapter (power supply, charger) breaks quite rarely, but still it happens.
Malfunctions and breakdowns are detected visually. If the power supply does not work for this reason, then:
- darkening is noticeable on the diagram (places of burnout);
- capacitors may be swollen, resembling overflowing barrels;
- chips, cracks, and any other signs of malfunction will appear on the cases of radio components.
To fix this type of breakdown (if the adapter for the power supply does not work), it is necessary to replace the failed parts with new and working ones. By the way, you can unsolder some work items from another broken adapter or mobile phone charger.
When soldering, it is important to observe:
- polarity of transformers;
- correct inclusion of radio components in the electrical circuit.
6. A rare case of adapter failure is a malfunction of the stabilizer. If the charger breaks down precisely for this reason, then the stabilizer will be replaced with a new one, and the work will return to normal.
![]() |
Video (click to play). |
Important: in order not to confuse the location of the stabilizer pins, it is recommended to take a preliminary photograph or draw circuit elements and connection paths on the sheet. And if the adapter for the power supply does not work, it will not hurt you to prepare the camera before work. In particular, a photograph taken from a disassembled device will help, without going into details, to solder a working stabilizer and eliminate the cause of the adapter's malfunction.