In detail: watch amber do-it-yourself repair from a real master for the site my.housecope.com.
What is OCHZ - this is a watch produced in the first quarter of 1961, manufactured at the Oryol watch factory in accordance with GOST - 58 years. The mechanism works on four stones, well, not the whole mechanism, but only the balance, or rather its axis.
Each trunnion has a pair of stones, one through acting as a bearing, the other is a flat thrust bearing. Each pair is pressed inside a screw-sleeve, which is screwed into the mechanism plate and allows you to adjust the balance axis gap between the support stones.
We can say that the design of this table clock to "disgrace" is simple and has a classic example of a watch mechanism. Everything is very simple, the alarm clock mechanism of the same manufacturer is used. The combat mechanism is excluded, and the rest of the structure is left.
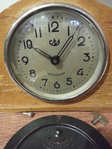
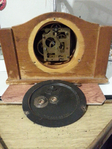
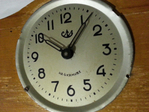
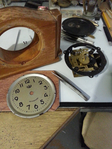
Spring-loaded winding wheel (motor), central, intermediate, second, escapement, four classic wheels (angrenage). The next node, an anchor fork, has a pin escapement and balance (pendulum).
I, of course, made out all this to the last nut., washed and cleaned every part of old grease, eliminated defects, in some holes in the plates there was an eleps-shaped working, where the axles of the wheels rotate.
Mechanism parts are ready for assemblywhich I did. When assembling, you need to carefully put the balance in its place, in the same screw-bushings, in which there are through and support stones without breaking the axle pins. And of course, during the assembly process, I do not forget to put the grease in the right places.
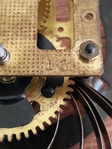
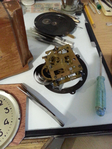
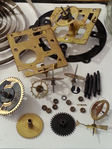
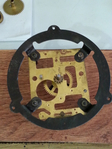
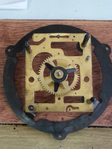
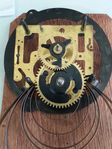
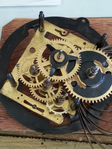
The mechanism is assembled, installed in the case, The watch is ready for use, but first, control for daily accuracy for 3-5 days with adjustment. What can be said about the watch itself, after more than 50 years of operation, it is old, but strong, the manufacturing technology is followed, judging by the state of the mechanism.
![]() |
Video (click to play). |
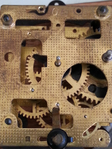
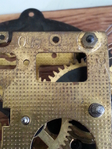
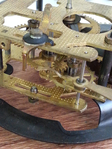
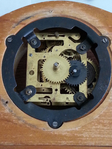
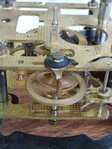
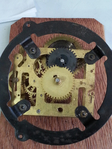
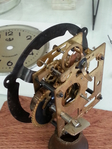
I want to say a few words about accuracy a mechanical watch, the example described above has a 2nd class of accuracy.
When the first mechanical watches first appeared, displacing solar and sand, they have become a symbol of high accuracy in measuring time, since then the image and symbol of time in general has taken root behind them.
Today is a mechanical watch are still used for timing, but their accuracy is poor. So, a watch of the first class of accuracy gives an error of +40 or -20 seconds every day, which is quite enough for everyday needs.
Inferior precision watches give a large error. The manufacturer is obliged to indicate the maximum deviations, both upward and downward. If the watch starts to lag too late, or vice versa, it is in a hurry, this is already a sufficient reason to contact a watchmaker for their repair.
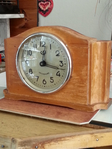
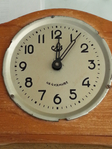
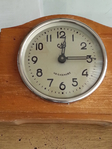
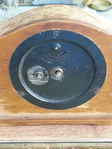
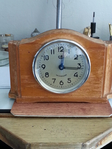
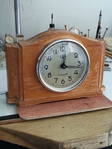
Common causes of clockwork malfunction is clogging, drying out of the lubricant, natural aging and wear, moisture ingress, irregular winding or excessive twisting of the winding mechanism.
Due to the decreasing accuracy of the movement of mechanical devices Compared to other watches available, mechanical watches are becoming a symbol of prestige and status rather than a truly necessary instrument for measuring time.
Mechanical watches require regular windingif they are not self-winding. Contrary to popular belief, such a system not only does not reduce the accuracy of the course, but on the contrary increases it, because the spring is always in a state close to fully wound, while there is no overvoltage in it.
Finally, permanent winding will wear down the crown of the watch., the formation of a gap between it and the case through which moisture, dust and dirt enter the mechanism. However, self-winding should not be counted on if you lead a sedentary lifestyle (important for office workers). Best regards, Nikolay, watch repair specialist.
The factory producing most of the large-sized watches in the USSR was the Oryol Watch Factory. On many watches on the dial was the abbreviated name of this plant "OCHZ". The factory began to produce watches Amber in the late 60s. The watch became very popular among the citizens of the Soviet Union. Nowadays, they still use this watch, this speaks of the good quality of the mechanism, because with proper operation and timely prevention, the Amber watch with a pendulum can last at least 100 years. A watch was brought to the Fullfix watch center for repair after a long stay in the attic. Corrosion has strongly eaten the chrome-plated elements of the case, we will carry out restoration and repair of watches. Let's start with the watch case.
As you can see, there are traces of paint on the body, most likely due to storage in the attic, corrosion has appeared on the chrome parts.
The condition of the case and chrome-plated parts leaves much to be desired, there is also corrosion on the dial elements.
The pendulum is covered with a layer of rust.
We will remove rust from the case and dial elements by polishing with abrasive wheels.
Let's pay attention to the striking strings of our clocks, as we can see the time also did not pass them by, we will carry out the restoration of the "voice", our clocks.
From the exterior of the watch, let's move on to the internal mechanism. Dust has adhered to the old watch oil and an unpleasant "mess" has formed, we will disassemble and clean everything.
In the process of parsing, we notice the absence of a pawl spring on the mechanism. Repairing antique pendulum clocks is not an easy task these days, you have to make some spare parts yourself, as new ones can no longer be found. We make the spring ourselves and solder the missing end to the old piece in platinum.
We disassemble the watch and wash everything in a special solution.
We assemble and lubricate the mechanism.
We insert the mechanism with the dial into the watch.
After restoration, the watch took its original appearance, the watchmaker №1 in Sokolniki Fullfix coped with its work perfectly.
The striking wall pendulum clock is a household clock. In terms of accuracy, they satisfy the need for measuring time in everyday life. The watch has a device for striking a clock and half an hour.
- After unpacking the watch, free the pendulum from the holders. It is not recommended to take the pendulum by the load with unprotected hands, in order to avoid corrosion and oxidation of it.
- Hang the clock on a wall away from windows and heating systems.
- Remove the shipping bar from the sound strings.
- Move the fight fence lever (if there is one).
5. Carefully place the pendulum on the hanger with the hanging hook.
6. Set the watch so that the pendulum rod is parallel to the back wall of the case. Parallelism can be achieved by rotating the set screws on the bottom of the case.
7. To wind the chime, insert the key into the left hole on the dial, winding is done clockwise. Move the key to the right hole and insert the travel spring as far as it will go. The watch must be wound every two weeks. For two weeks of operation of the watch, the power spring unwinds by 6 full revolutions, the striking spring unwinds by 5.65 revolutions. ! When winding the watch, be careful not to knock the case to the side.
8. To start the clock, take the pendulum to the side and release it smoothly, the movement should be rhythmic. If this is not observed, carefully move the lower part of the watch case to the right or left, achieve rhythmic strokes of the movement. ! If you cannot achieve the rhythm of the movement by moving the watch case, you should contact the watchmaker.
9. Set the exact time by turning the minute hand.If the hands diverge, set the minute hand to the “12” position, and adjust the hour hand by turning it to the left or right. ! When rotating the minute hand, it is advisable to stop it at the “6” and “12” positions, and enable the clock to strike the hours and half hours.
Adjusting the accuracy of the wall, grandfather clock
If the clock is inaccurate, it is adjusted by moving the weight of the pendulum. If the watch lags behind, the weight must be lifted up by turning the adjusting screw clockwise, if the watch is in a hurry, lower the weight in the same way, counterclockwise. One full turn of the adjusting screw corresponds to a change in stroke of one minute per day.
In order to prevent damage to the watch, when adjusting the stroke, the pendulum must be removed from the suspension.
- A dry, heated room is required to store or use wall clocks, floor clocks. It is not allowed to store watches in the same room with substances or materials causing their corrosion.
- A watch with a suspended pendulum should never be carried.
- The watch mechanism is lubricated with special watch oil of the MTs-3 and PS-4 brands. The service life of the oil is 3 years, during which time it is recommended to clean and lubricate the mechanism. Replacing the oil of the indicated brands with others is not permissible.
To avoid voiding the warranty, it is not recommended to lubricate, disassemble or repair the watch yourself.
What is OCHZ - this is a watch produced in the first quarter of 1961, manufactured at the Oryol watch factory in accordance with GOST - 58 years. The mechanism works on four stones, well, not the whole mechanism, but only the balance, or rather its axis.
Each trunnion has a pair of stones, one through acting as a bearing, the other is a flat thrust bearing. Each pair is pressed inside a screw-sleeve, which is screwed into the mechanism plate and allows you to adjust the balance axis gap between the support stones.
We can say that the design of this table clock to "disgrace" is simple and has a classic example of a watch mechanism. Everything is very simple, the alarm clock mechanism of the same manufacturer is used. The combat mechanism is excluded, and the rest of the structure is left.
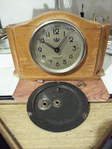
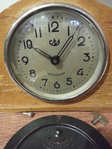
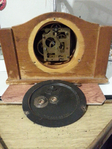
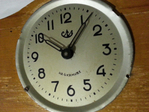
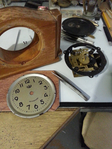
Spring-loaded winding wheel (motor), central, intermediate, second, escapement, four classic wheels (angrenage). The next node, an anchor fork, has a pin escapement and balance (pendulum).
I, of course, made out all this to the last nut., washed and cleaned every part of old grease, eliminated defects, in some holes in the plates there was an eleps-shaped working, where the axles of the wheels rotate.
Mechanism parts are ready for assemblywhich I did. When assembling, you need to carefully put the balance in its place, in the same screw-bushings, in which there are through and support stones without breaking the axle pins. And of course, during the assembly process, I do not forget to put the grease in the right places.
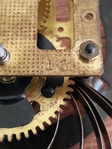
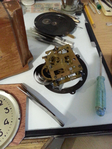
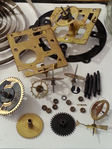
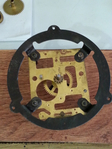
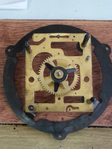
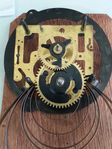
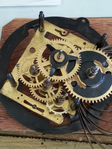
The mechanism is assembled, installed in the case, The watch is ready for use, but first, control for daily accuracy for 3-5 days with adjustment. What can be said about the watch itself, after more than 50 years of operation, it is old, but strong, the manufacturing technology is followed, judging by the state of the mechanism.
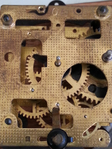
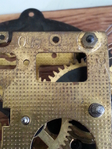
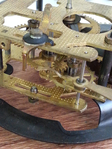
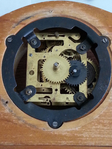
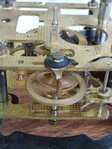
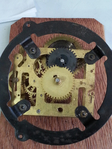
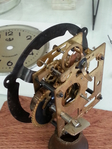
I want to say a few words about accuracy a mechanical watch, the example described above has a 2nd class of accuracy.
When the first mechanical watches first appeared, displacing solar and sand, they have become a symbol of high accuracy in measuring time, since then the image and symbol of time in general has taken root behind them.
Today is a mechanical watch are still used for timing, but their accuracy is poor. So, a watch of the first class of accuracy gives an error of +40 or -20 seconds every day, which is quite enough for everyday needs.
Inferior precision watches give a large error. The manufacturer is obliged to indicate the maximum deviations, both upward and downward.If the watch begins to lag too late, or vice versa, it is in a hurry, this is already a sufficient reason to contact a watchmaker for their repair.
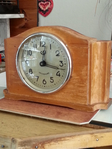
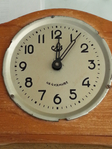
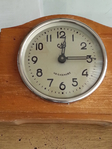
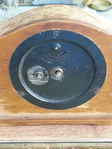
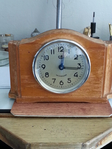
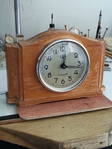
Common causes of clockwork malfunction is clogging, drying out of the lubricant, natural aging and wear processes, moisture ingress, irregular winding or excessive twisting of the winding mechanism.
Due to the decreasing accuracy of the movement of mechanical devices Compared to other watches available, mechanical watches are becoming a symbol of prestige and status rather than a truly necessary instrument for measuring time.
Mechanical watches require regular windingif they are not self-winding. Contrary to popular belief, such a system not only does not reduce the accuracy of the course, but on the contrary increases it, because the spring is always in a state close to fully wound, while there is no overvoltage in it.
Finally, permanent winding causes wear on the crown of the watch., the formation of a gap between it and the case through which moisture, dust and dirt enter the mechanism. However, self-winding should not be counted on if you lead a sedentary lifestyle (important for office workers). Best regards, Nikolay, watch repair specialist.
The novel is light, relaxing and without pretensions. >>>>>
A very strange novel. the heroes' feelings are described very poorly >>>>>
"OWN HAND REPAIR OF WATCHES"
A beginner's guide
Watchmaking devices can be classified in different ways: according to the principle of operation, according to the structure of the oscillatory system, and finally, according to their purpose.
According to the principle of operation, watch movements can be mechanical, electronic-mechanical or electronic. The oscillatory systems used in the watch device (balance, pendulum, quartz generator, tuning fork, etc.) depend on the way of use and purpose of the watch. So, for example, a pendulum clock can only work if the pendulum is suspended vertically, that is, the clock must be stationary. This is a floor clock, wall clock or (in rare cases) table clock. The balance oscillatory system, unlike the pendulum one, is not afraid of movement of the mechanism, therefore it is used mainly in wrist or pocket watches.
Mechanical watches, in addition, can be subdivided according to the type of motor used: kettlebell or spring. The simplest in design is a wall pendulum clock with a kettlebell motor, such as a cuckoo clock.
Mechanical watches, in addition to the main mechanism, can also have various additional devices. For example, in an oversized watch, it can be a battle, a calendar or signaling device; in wristwatches - automatic spring winding, stopwatch, signaling or calendar device, etc.
Electromechanical clocks can be either wrist or stationary (table or wall). Electronic and electronic-mechanical watches can also be equipped with additional devices.
The book is mainly devoted to the repair of the most common watches - wristwatches and alarm clocks.
In mechanical watches, these are: the engine, the main wheel system, the oscillating system or regulator, the escapement or stroke, the pointer mechanism, the mechanism for winding the spring and shifting the hands.
The watch is powered by the engine.
It can be spring or kettlebell. A running engine stores energy, and then transfers it to the regulator and the switch mechanism through the wheel system. The main wheel system consists of toothed wheels (second, intermediate, central) that transmit energy from the engine through the escapement to the regulator and switch mechanism. The regulator controls the unwinding of the spring (or the opening of the weight). The escapement, which is an intermediate unit, periodically releases the gear train in the wheel system and transfers the spring energy to the regulator.The pointer mechanism consists of a system of toothed wheels (transfer, bill, watch) and transfers movement to the arrows from the main wheel system.
The mechanism for winding the spring and shifting the hands consists of a winding shaft, a drum and winding wheel and a system of levers. The base of the movement is platinum, one of the sides of which is called the pavement, and the other - the dial. On the bridge side there are: the engine, the main wheel system (or angrenage), the escape wheel, the escapement fork, the balance-spring, the automatic winding mechanism for watches with such a system, and on the dial - the arrow mechanism, the mechanism for winding the spring and shifting the hands and the calendar mechanism if provided.
The crown is screwed onto the winding shaft.
When the crown rotates, that is, when the watch is wound, the shaft also rotates, transmitting the movement to the winding wheel and then to the drum wheel put on the drum shaft. The inner coil of the mainspring is attached to it, and when the wheel rotates, the spring is wound onto the shaft. When the wound spring begins to unwind, the rotation of the drum is transmitted to the central wheel. The central wheel, in turn, rotates the intermediate wheel, and it is the second wheel, which drives the second hand. Then, from the second wheel, the movement is transmitted to the escape wheel, which maintains the balance oscillations. Finally, through the bill wheel, the movement is transmitted to the hour wheel with an hour hand.
To repair watches at home, you will need: a magnifying glass, several screwdrivers with a blade diameter of 0.6 to 2 mm, 2-3 tweezers, a set of keys, pliers, wire cutters, files, a needle, a knife, a vernier caliper, cleaning and lubrication tools ( oiler, brushes, rubber bulb, etc.). Gasoline for lubrication can be poured into an ordinary teacup, only you need to tightly close it. You can use old toothbrushes as part brushes.
Electromechanical wall clock Amber comes from the 80s. In this case, this is the simplest option without a fight in a simple (although with a claim to design) plastic case.
The frequency setting element of the mechanism is a spring pendulum, and a generator with a pair of coils is engaged in swinging. This determines not the highest accuracy. Powered by one element 373 (aka type D).
Unfortunately, after 30+ years, the mechanisms of watches of this type and age are usually in a deplorable state - the accuracy of the watches is poor, the battery runs out quickly, they can just get up. This is due to the lack of maintenance and trivial wear and tear. Of course, you can slightly refresh the mechanism, but usually the parts require not only lubrication, but also cleaning, which is not suitable for everyone at home. Just pouring watch oil in different places usually does not save for a long time, if at all changes something. In addition, the abundance of Soviet plastic from the 80s in the mechanism raises some doubts about the outcome of this enterprise.
The radical remedy is replacing the mechanism. Modern movements are much more compact and are usually quartz-stabilized and powered by a single AA cell. Importantly, the replacement mechanism is usually virtually silent! True, now the mechanism will be almost completely plastic and not authentic Soviet, but Chinese.
First of all, it is necessary to dismantle the old mechanism - this must be done carefully. The dial with the old movement must be unscrewed from the outer case and removed from it, the hands are simply tightly mounted on the shafts - they must be removed. The mechanism is attracted to the dial by a brass nut - it is located on the front side under the hands. This nut does not always give in - if so, it is better to wield from the side of the mechanism (unless, of course, it is dear to you as a memory) - you can use a drill and cutting wheels. The new mechanism has a similar fastening, but its length is shorter, so the elastic band under the mechanism most likely will not work - I suggest damping the strips of electrical tape with a sticker.The mechanism should not turn, but do not get carried away especially with a tightening. We also lose our native fasteners on the wall (in the version where the fasteners are directly above the mechanism) - there are replacement mechanisms with a loop, but I don't really like this option - and the clock is not a fluff, and it is not known whether that loop will be enough for your nail in the wall. As an option, I propose to fix a wire between the screws for attaching to the outer casing and make a suspension from it.
There is a positive point - most likely it will be possible to preserve the native hands - for the minute and hour landings they coincide. Our second shaft is thinner, but if desired, the bore hole can be unclenched - it will hold. However, you can try to find a mechanism with similar openwork arrows, although their length will have to be clarified.
An important point in setting the hands is to synchronize them correctly, that is, when the minute looks at 30 minutes, the hour should show half of any hour.
For many years now, we have had a wall clock with a Soviet-made pendulum hanging in our houses. Hanging, but not walking. After winding the springs and starting the pendulum, they stop and do not move, so I decided to fix them. It took me a lot of time, I will try to briefly tell you about it.
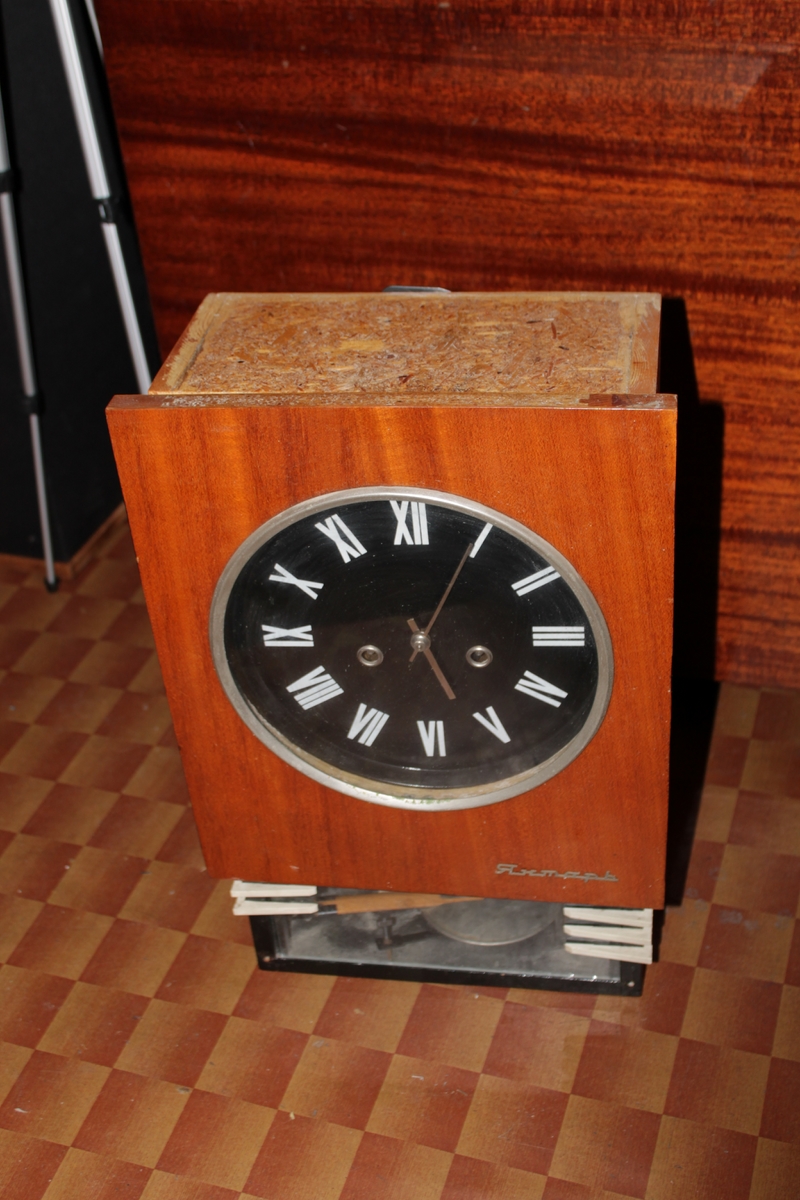
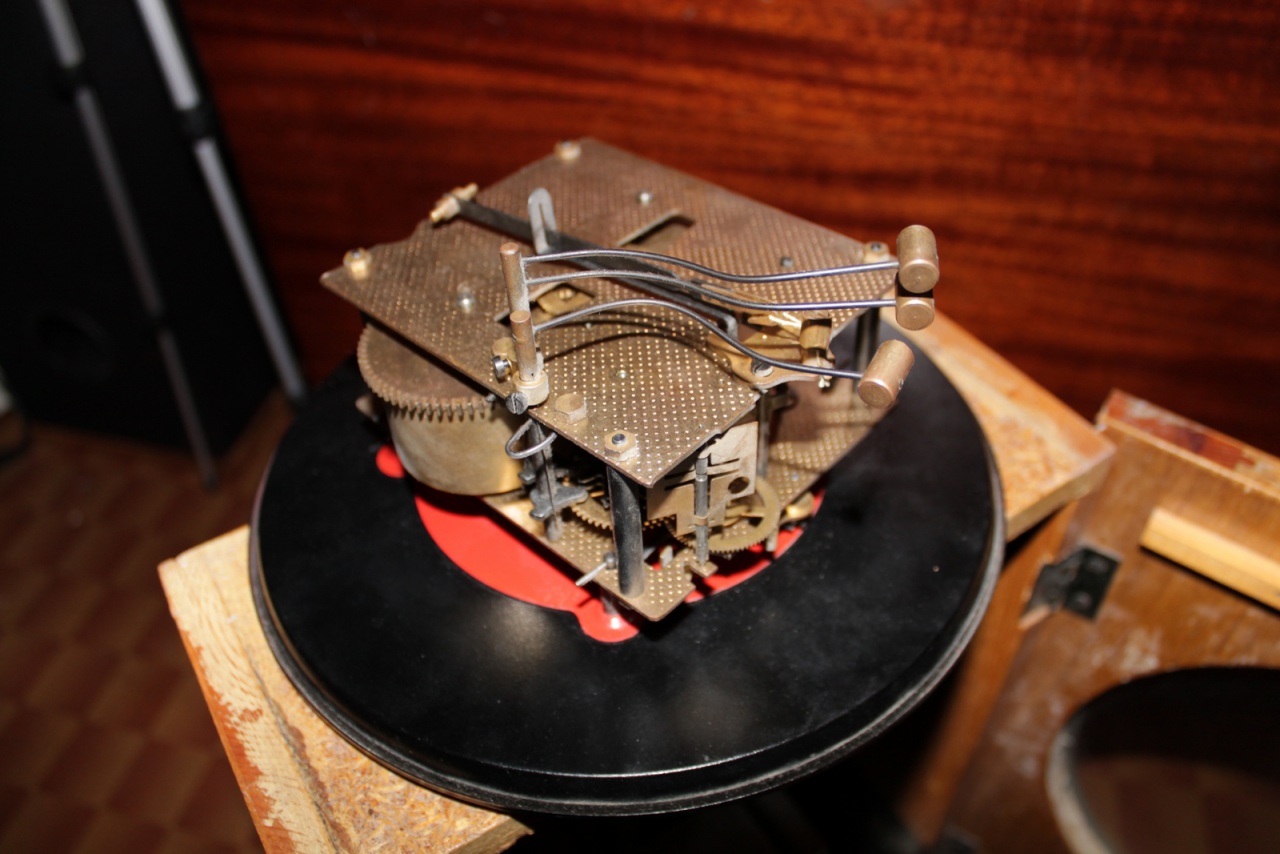
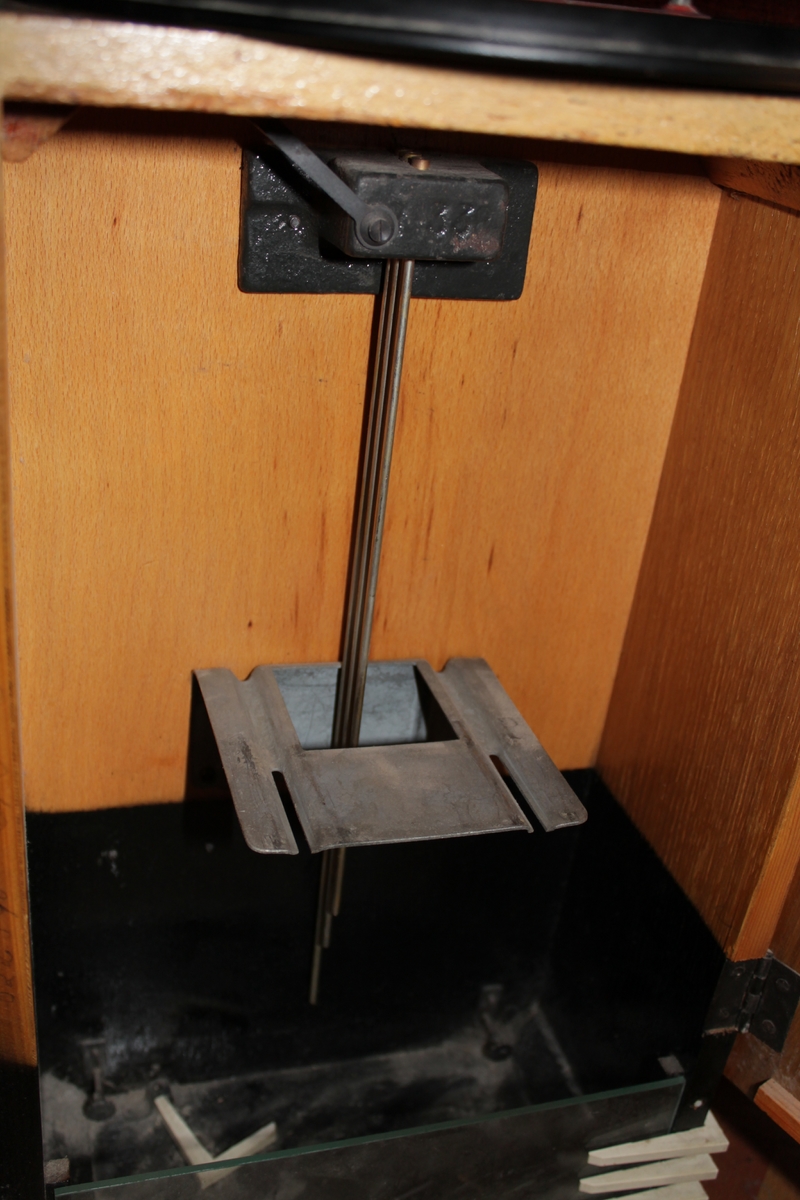
On the advice of dear members of the forum, I took off the dial and hands, unscrewed the anchor and set the mechanism to soak in Kalosha gasoline. After that, they had to go, but still something interfered with the move.
After repeated attempts to start the clock, I "hammered" a little on them. But the other day, passing through the courtyard, I saw a thrown out watch. Amber, also pendulum, but without a fight and the pendulum itself. But in them there was a detail on which the pendulum itself is attached, and the same one as in my watch. Naturally, I picked them up. I had doubts about this part for a long time, it was all wrinkled, loosened, in general, with signs of use.
So, having replaced the pendulum holder and the rope on which it is hung, I tried to start the mechanism. And lo and behold - the clock has gone. True, five minutes later they got up again. But it was 5 minutes!
After repeated advice with members of the forum, I aligned the clock not by a plumb line, as I had done earlier, but by ear, to a uniform "tick-tock". And the clock went on. Now it's okay, without stopping. Adjusted the hammers for the right fight, now they signal to me the new hour has arrived.
This is the name of a wrist electronic-mechanical watch with a quartz generator (Fig. 9).
Rice. 9. Kinematic diagram of a quartz watch KNCH 3050:
9 - central wheel with a tube;
10 - stepper motor rotor;
11 - stepper motor stator;
12 - stepper motor tribe;
14 - second wheel with tribe;
19 - transfer lever with a pin;
The crystal oscillator is a highly stable oscillation source located in the electronic unit.
The block of a quartz generator is a printed circuit board with a quartz resonator, an integrated microcircuit and passive elements placed on it. The block is connected to the plate with screws. The actuator in the watch is a stepper motor made in the form of an autonomous unit. The battery provides at least 12 months of continuous operation of the watch.
The principle of operation and the kinematic diagram of the clock are as follows: the electrical signal of the quartz generator is divided by its frequency and, after the formation of the pulse, is fed to the stepping motor. The pulse repetition rate is 1 Hz. The stepper motor, in turn, converts successive electrical impulses into intermittent rotation of the main wheel system.
Through the wheel system, the rotation of the engine shaft is transmitted to the arrows and the calendar device (if any).
The stepper motor arm (12) meshes with the transfer wheel (13), the arm of which drives the second wheel (14). From the tribe of the second wheel through the intermediate wheel (15) with the tribe, rotation is transferred to the central wheel (9).The pointer mechanism consists of a minute hand tribe (8), a bill wheel (6) with a tribe, an hour wheel (7).
The conversion shaft (2) with the head (1) can take two fixed positions. If the watch has a calendar device, then the conversion shaft will be designed for three positions.
In order to translate the arrows, it is necessary to put the conversion head in the second fixed position. In this case, the cam clutch (17) must engage with the shifting wheel (16). Further, the rotation is transferred to the switch mechanism.
During the translation of the arrows, a locking lever, mechanically connected to the translation shaft, locks the translation wheel and prevents the movement of the wheel system and the stepper motor when moving the arrows. After setting the arrows and returning the conversion head to the initial position, the lever returns to its normal position, allowing the stepper motor to start.
Unscrew the locking ring and remove the housing cover.
Unscrew the battery spring screw, remove the spring and carefully, preferably with tweezers, pull out the element, taking it only by the cylindrical part of the body.
Next, unscrew the screws connecting the stepper motor, be sure to hold the ends of the conductors with tweezers.
Insert the battery into the mechanism and use a tester to check the functionality of the electronic unit.
The positive probe of the tester is connected to the platinum of the clock mechanism, and the negative one is connected in turn to the connection pins of the stepper motor. In this case, the arrow of the device should deviate to 1.4–1.5 V and oscillate within 1–2 mm with an interval of 2 s. If there are no such fluctuations, replace the electronic unit.
Then determine if the stepper motor is working properly. To do this, set the tester switch to the resistance measurement position.
Connect the tester probes to the contacts (outputs) of the stepper motor and measure the resistance of the coils, which should be within 3-4 kOhm.
Connect one tester probe to the clock plate, and the other to one of the stepper motor leads.
In this case, the arrow of the device should be in the left extreme position of the scale of the device. Repeat the same with a different conclusion. If, when measuring, the arrow deviates to the right, it means that the stepper motor coil is closed to the case. Such an engine must be replaced.
Remove the electronic unit. To do this, unscrew the screw securing the current lead, remove the insulating washer, unscrew the two screws securing the block to the plate, carefully lift the block with tweezers, move it to the side and remove it from the speakers.
Press on the support of the transfer shaft, pull the shaft out of the housing, and then the entire mechanism.
Remove the screws securing the stepper motor bridge. Remove the bridge, then remove the two screws securing the stepper motor and carefully pull out using tweezers.
When removing and installing the stepper motor, use only brass tweezers and only plastic tweezers for the power supply.
Next, disassemble the switch mechanism. To do this, you need to remove the hands, two screws of the dial, the dial, three screws, the bridge, the hour, bill and transfer wheel and the tribe of the minute hand. Then remove the calendar device, if present.
Disassemble the main wheel system. To do this, unscrew the screws and remove the bridge.
After disassembling the mechanism, cleaning the parts follows. All parts are washed except for the power supply, stepper motor, dial, case glasses, inserts, quartz generator block and painted hands. All of these parts, except for the stepping motor, are cleaned with a soft hair brush.
Install the central wheel with tube (9), minute hand tribe (8).
Press the central tube into the hole of the minute hand tribe, then check the smooth rotation of the central wheel, as well as its axial and radial clearances. Lubricate all center tube seats.
Assemble the wheel system.This is done in the following order: install the intermediate wheel (15) with a pinion, the transmission (13) and second (14) wheels with tribes and the axle of the main wheel system so that the brake of the locking lever enters the axle groove, fasten the axle with screws. Check the clearances of the intermediate and second wheel with tribes and the smoothness of the rotation of the system.
Assemble the translation mechanism. To do this, you need to install the transfer lever (19), the clutch lever and the cam clutch itself (17), as well as the transfer shaft (2).
Check the smooth rotation of the shaft in the plate, install the locking lever and lubricate all parts.
Install the minute wheel with tribe, transfer wheel, axle and fix it with screws.
Install the clock wheel (7).
Install the spring washer and dial. Screw down the dial with the screws and then install the hour, minute and second hands. In this case, it is necessary to monitor the position of the transfer shaft; when installing the hour and minute hands, the shaft must be in the position of the transfer of the hands.
Using the transfer shaft, move the hands to number 12 and set the second hand, matching its position with the divisions of the dial.
The minute, second and hour hands should be set without applying great force so as not to violate the established vertical clearances in the main wheel system.
Insert the mechanism, the mechanism fastening ring, the transfer shaft into the housing.
Install crystal oscillator block, stepper motor and power supply. Do not overtighten the stepper motor mounting screw.
Close the housing cover. After completing the assembly, the stepper motor should immediately start its work, this will be seen by the movement of the second hand.
Oversized quartz watch
As an example, we will consider the mechanism of an electronic mechanical table clock with a quartz resonator (Fig. 10).
Rice. 10. Structural diagram of quartz watch "Yantar" 59206:
3 - gearbox mounting nuts;
6 - screws for fastening the stepper motor;
7 - stepper motor tribe;
8 - screws for fastening the coil;
17 and 19 - intermediate wheels first and second;
22 - screws for fastening the electronic unit
The mechanism consists of a stepper motor, a main wheel system, a battery and an electronic unit.
The quartz clock generator starts working when the batteries are connected to the electronic unit. A stepper motor (9) is used to convert electrical energy into mechanical energy. From the tribe (7) through the first intermediate wheel (17) rotation is transmitted to the second wheel (20). There is a second hand on the axis of the second wheel. In order to set the minute hand in motion, the rotation is transmitted further through the second intermediate wheel (19) and the central wheel (15), on the sleeve of which the minute hand is fixed.
The movement from the central wheel is transmitted to the bill wheel (10), and from there to the hour wheel (12). The center wheel assembly is equipped with a special device that allows the minute and hour hands to be coordinated. To set the exact time and translate the minute and hour hands, a conversion shaft (14) is used.
To set the second hand to the exact time, use the second hand stopper (5).
Remove the cover and pull out the battery and terminals.
Remove the electronic unit (21); to do this, firstly, unscrew the two screws (22) securing the electronic unit in order to disconnect it from the speakers of the panel (13) and the bridge (4); secondly, disconnect the electrical connector.
Remove the stepper motor (9); to do this, unscrew the two screws (6) securing the stepper motor to the panel columns.
Unscrew the two nuts (3) securing the gearbox.
Remove the rear axle (4), second wheel (20), first (17) and second (19) idler wheels.
Remove the second hand stopper (5), front axle (18), center wheel (15), bill wheel (10), hour wheel (12).
Remove the spring (16) and the transfer shaft (14).
Remove the speakers (11) by unscrewing the two nuts securing the speakers to the front side of the panel.
Disassemble the stepper motor if necessary. To do this, remove the stepper motor rotor assembly, unscrew the two screws securing the coil and remove it. After disassembly, all parts of the stepper motor and gearbox, except for the coil, must be rinsed in gasoline. To flush the rotor axis of the engine, you need to remove the coils and the rotor, and the flushing itself should be carried out with the assembled magnetic circuits.
The main malfunction of a stepper motor, as a rule, is a break in the coil wire. In this case, repair is possible only if the outer end of the wire is cut off. The repair procedure is as follows: dissolve the coil varnish with amyl acetate near the broken end so that there is enough length to stretch the wire. Then use a soldering iron to remove the remaining wire from the terminal. Make 2-3 turns around this terminal and re-solder the wire.
Soak the brush in a mixture of alcohol and gasoline and clean the soldered area, and then cover it with varnish.
The most common faults in the electronic clock unit are the failure of the integrated circuit and the quartz resonator. These nodes are best replaced.
Defects in the main wheel system are corrected in the same way as in a mechanical watch.
Assembling and adjusting the watch mechanism
Install two columns (11). Place the spring (16) on the right column and fix its position with the stand pin. Then put the front axle (18) on the same column; the bend of the spring must fit into the groove of the bridge.
Insert the first intermediate wheel (17) into the axle hole with the tribe up. Put a washer and a spherical spring on the second wheel axle (20) and also insert the second wheel into the hole in the bridge.
Raise the second wheel slightly and install the second intermediate wheel (19) and stopper.
Install the rear axle and tighten the two nuts.
Place the main wheel assembly on the rear axle. Place the minute wheel on the front axle tube, and fix the transfer shaft (14) in the holes of the front and rear axles.
Put the bill wheel on the axle of the front axle, and the hour wheel on the hub of the minute wheel.
Install the panel (13) on the top of the columns, tighten two nuts.
Place the coil on the base of the stepper motor assembly and secure with screws. Install the motor rotor on the axle.
Engage the rotor tribe with the first idler wheel. Install the stepper motor and secure it with two screws.
Place the electronic unit in the corresponding slots on the motor and secure it with two screws. Insert two terminals into the grooves of the panel, check the contact. If necessary, the terminal tabs can be folded.
![]() |
Video (click to play). |
To test the operation of the mechanism, connect it to a power source.