In detail: gearbox gaz 3302 DIY repair from a real master for the site my.housecope.com.
- Like
- I do not like
I bring to your attention a video tutorial on repairing a Gazelle gearbox.
The video tutorial tells in detail about the sequence of disassembling and assembling the box, and troubleshooting parts.
Cool video report! Well done!
- Like
- I do not like
along the way when you disassembled the prom shaft box, you also need to legalize the free wheeling in the case, but you didn’t do that, and so it’s all good
- Like
- I do not like
I bring to your attention a video tutorial on repairing a Gazelle gearbox.
The video tutorial tells in detail about the sequence of disassembling and assembling the box, and troubleshooting parts.
- Like
- I do not like
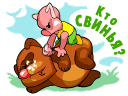
With a hammer on the primary, and then on the secondary. Wasn't a piece of copper or aluminum lying around.
And then also the shaft in a vice for the teeth
Synchronizer couplings are practically not described (in terms of what, how, where, components)
The bearing seats in the gearbox covers were not checked.
It is not shown how to adjust the intermediate shaft, and this is one of the most important components.
Not a word about oil seals and breather.
And for the rest: an excellent manual for repairing gearboxes
All of the above is not offensive to the author, but in order to see a more complete video with additions to the ones presented.
- Like
- I do not like
I join! Just perfect! Such a manual for each unit and unit and no books are needed, and much of the books do not specify. That rare moment when I spent a little over an hour of my life watching videos on YouTube, and I don't regret it a bit
- Like
- I do not like
Such would be a manual for each unit and unit, and no books are needed.
There is still an order for the repair of the rear axle, so there will be a new video tutorial soon
![]() |
Video (click to play). |
also thanks to shurhen80 for the comments. and in response, they post the third part of the video tutorial on repairing the checkpoint
- Like
- I do not like
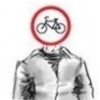
13.43 fifth and back
- Like
- I do not like
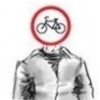
but at 29.00 it is better to change the ring, otherwise it will break the groove on the shaft and fly out, after which the fifth will disappear and the speedometer will be silent.
it is then treated by replacing the shaft, which is on sale only like raw
- Like
- I do not like
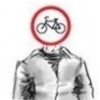
bearings need to look for shells.
the shaft must be checked at least the fifth "treadmill" with a vernier caliper, it looks like it is squashed a lot (it sits down all forward) and breaks the gear, having worn out the teeth.
It is better to put the 5th gear washer “from below”, the bearing will then have a more uniform load, although this is a trifle.
the gears can be half, that is, the clutch engagement is separated from the gear and dangles.
wear of the cage of the clutch and gear engagement, which leads to the flying out of the gears.
Post has been editedusgg on: 20 March 2014 - 07:06
We remove the gearbox. We look at the article - "Removing and installing the checkpoint."
We wrap the filler and drain plugs in place.
Remove the power unit support.
Remove the reversing light switch.
We remove the speedometer drive.
We remove the clutch with the bearing and the foam rubber rings of the front cover.
Using a 12 key, unscrew the three bolts securing the bearing cover (the bolts are installed on the sealant).
Remove the cover with the gasket.
When installing it later, pay attention to the coincidence of the oil drainage channel in the cover and the holes in the crankcase.
Prying off with a screwdriver, remove the input shaft seal from the cover (when disassembling the gearbox, we replace all the cuffs, regardless of their condition).
Press in a new cuff with a mandrel or a head of a suitable diameter.
With the key "13" we unscrew and remove the bolt securing the bushing of the reverse gear axle to the front crankcase
Use a thin screwdriver to pry on and remove the retaining ring of the input shaft bearing
Turn the key "12" and remove the breather.
Using a 12 key, unscrew ten bolts connecting the front and rear crankcases (two bolts passing through the dowel sleeves are longer than the others).
11. Gently tapping with a hammer through the brass mandrel, undo the front and rear crankcases.
In this case, do not strike at the end of the input shaft, as the synchronizers will be damaged.
Disconnect the gearbox housings
Carefully, trying not to damage, remove the gasket
We take out the adjusting shims from the bore under the intermediate shaft bearing in the front crankcase (they may not be there). In this case, the axial clearance in the bearings is set only by the crankcase seal.
Noise in the gearbox is usually the result of bearing wear, chipping of the working surface of the gear teeth, and even their breakage. Disassembly of the gearbox and replacement of damaged parts is required.
Another reason even a new gearbox can make noise is the low oil level in the crankcase. This malfunction is a consequence of an oil leak from the gearbox.
A misalignment of the crankshaft and clutch housing is also possible. Using an indicator mounted on a stand attached to the rear end of the engine crankshaft (gearbox and clutch removed), while rotating the shaft, check the runout of the bore for the gearbox in the clutch housing (db 0.3 max) and the non-perpendicularity of the rear end clutch housing (d. b. 0.15 max).
How to remove the gearbox can be read in many printed and electronic publications, such as the repair and maintenance manual, so this operation will not be described in this article.
The next step is to thoroughly wash and rinse all parts of the gearbox, including the crankcase of the gearbox itself. Next, conduct a close inspection of all gearbox parts for damage and excessive wear.
- chipping of the working surface of the inner ring of the input shaft bearing (for clarity, the bearing is cut)
- slight wear of the secondary shaft roller bearing,
- output shaft bearing play,
- play in the bearing of the toe of the input shaft of the gearbox (pressed into the crankshaft),
- the absence of one of the contacts of the reverse sensor (broke off when dismantling the gearbox)
- input shaft bearing V6-50307АКШ1,
- secondary shaft roller bearing 20-1701182,
- bearing of the secondary shaft V6-50706USH1,
- primary toe bearing 402.1701031,
- reverse gear sensor LSH.609.016,
- gearbox shank oil seal (2 pcs.) 24-1701210-07,
- set of paronite gaskets.
I will not describe the assembly itself either, but I will point out its subtleties.
For ease of assembly, it is better to screw the rear part of the gearbox housing with self-tapping screws to the bar (see below in the photo). In this state, it is easier to insert the shafts, the crankcase does not fall anywhere and does not collapse.
For this, a similar block is taken as for the rear of the crankcase and a hole is drilled with an 18 mm feather drill, then the output shaft is inserted into the drilled hole (see photo). Now the work on pressing will be much easier, and will not spoil the shaft itself when it stops.
In the same block, next to the previously drilled hole, a new hole is drilled with a 16 mm nib drill. Then the input shaft is inserted into the drilled hole (see photo) and 14 rollers are installed. Without removing the shaft from the bar, we connect the primary and secondary shafts. Now this node is ready for further assembly.
The resulting device in the course of work.
We install the primary, secondary and intermediate shafts in the gearbox housing. If the plunger jumped out during the parsing of the checkpoint, then questions may arise: how did they still stand? Schematically it looks like this:
If all the parts located inside the crankcase are installed, then you can connect the two halves of the gearbox housing and tighten 10 bolts.
It remains to install the gear lever and check the engagement of each of the gears, scrolling the input shaft, controlling the speed and direction of rotation of the output shaft. We unscrew the block previously screwed to the rear half of the gearbox housing. Screw in the reverse sensor after installing the gearbox on the vehicle.
Lubricate with paste (included in the kit with the ZMZ clutch disc): the seat on the input shaft for the crankshaft bearing, the input shaft splines and the sliding surface of the release bearing of the gearbox front cover.
... installation of the reverse sensor in the gearbox.
The oil should still be poured through the hole for the gear lever, because in this case, it will partially lubricate the gearbox elements, and conduct additional control through the filler hole.
Hang up the rear wheels of the car (jack up and place the rear axle of the car on the stops), start the engine and slowly turn on the gears one by one (create an imitation of the car's movement). Performance test of each transmission for about one minute. WHAT WILL IT GIVE!? Firstly, since the gearbox parts have been thoroughly washed, then the initial operation of the gearbox will be dry, despite the fact that the oil is already filled in As a result, the operation of the primary and secondary shafts goes dry, although where the gears and bearings were lubricated during the assembly process), and when the vehicle is operating without load, it will painlessly distribute the oil inside the gearbox system, and secondly, in case of unforeseen circumstances (sudden exit failure of any element, breakdown, etc.) the operation of components and assemblies will be without load, which will avoid more serious breakdowns.
Repair of the Gazelle checkpoint is a difficult event for which you need to prepare in advance. The gearbox functions by transmitting torque to the wheels from the motor shaft. It should be understood that the slightest failure in the functioning of the transfer case can threaten your safety. If there is no service station nearby, you can repair the malfunction yourself. If you strictly follow the step-by-step instructions, even a novice motorist can carry out this procedure without any problems.
The Gazelle checkpoint is rightfully considered one of the most reliable and durable, but even they can become unusable due to high loads. In order for the replacement of the Gazelle gearbox to go without a hitch, you must know the materiel of the car, study the diagrams, be careful and patient, and also follow the safety rules and understand the principle of operation in the Gazelle 4x4 gearbox.
Repair of the Gazelle may be required in some cases:
- Difficulty shifting gears. Such a snag occurs due to the lack of fluid in the cylinder or due to the presence of air in the hydraulic actuator. In addition, you can check the locking bolts, which often require additional tightening, as well as the intermediate shaft of the gearbox. You can observe how the device jerks in neutral and the box howls. Another sign - in 4th gear, the fifth or second device makes a howl, a lot of noise;
- the inclusion of the gearbox occurs with noise and crackling at startup. In this case, the synchronizer block ring on the transfer case could be worn out or deformed. Also check the power take-off. It is advisable to replace the locking ring or the power take-off, and in order for the new element to rub in without problems, use lapping paste. In addition, check the condition of the input shaft, how the mortar works, whether the car was noisy in neutral;
- arbitrary shutdown of the manual transmission. If you noticed such a problem, first of all check the fastening nuts to the clutch housing, as well as in what condition the gearbox gazelle is in.In addition, the couplings (worn out teeth), as well as the retaining springs (they can both wear out and weaken), could wear out. You may also need to adjust the intermediate shaft and input shaft;
- the appearance of extraneous noise. In order to get rid of them, it is necessary to replace the bearings or damaged gears, add oil to the crankcase or check its alignment with the crankshaft.
To repair a gearbox on a Gazelle, you should know everything about the transfer case, because disassembling the gearbox is not an easy task. It is also necessary to determine the type of breakdown. The most popular reason for replacing the gearbox with Gazelle owners is oil leakage. It occurs due to worn out gaskets or bushings, worn out gaskets, as well as a violation of the tightness of the plugs. In this case, you will need to add or change the oil on the car, as well as replace the bushing.
How to remove the box? Replacement of the checkpoint is carried out on an overpass or inspection pit. First, drain the oil from the crankcase. Now we remove the gimbal. To do this, arm yourself with a file and put a notch on the connecting unit and the continuation of the gearbox on the gazelle. Now remove the support hardware using the thirteen and twelve wrenches. With the keys for seventeen and fourteen, we remove the fixing of the cardan to the flange of the main gear gear. We remove the shank and push the rags into the hole. Now we need to get the lever to install the gearbox. To do this, we get rid of the cover and the top of the lever inside the cab, unclench the bushing, remove the rubber cushion, the floor seal and the cover, the cap and the lever itself.
Next, we disconnect the speedometer from the transmission together with the rear light switch. Now you can remove the transfer box. How to disassemble the gearbox housing? To do this, get rid of the fixing of the receiving pipes and the bracket, disconnect the transmission from the clutch housing, create a protection from a wooden block for the block head. We proceed to remove the transverse fixation of the transfer case and remove the device. Be careful as it can weigh up to 30 kg. Install a new item. Be careful not to damage or miss the stepped transfer case.
Now we start assembling the Gazelle checkpoint. The assembly of the box is carried out in the reverse order. Please note that the shafts must be installed at the same time, for this, tie them up in advance. Inspect the input shaft, shank, bushing, crankcase, output shaft and all gears. Wash them in kerosene or diesel. If there are traces of rust, sand. The fasteners are coated with sealant and the elements are coated with gear oil.
Before installing the splines, lubricate them with SHRUS-4, and during the assembly of the universal joint, follow the correspondence of the marks and pay attention to the gear ratio. It is an important indicator of the adequate performance of a mechanical device. After repairing the Gazelle gearbox, replenish the amount of oil in the crankcase.
We remove the gearbox.
We wrap the filler and drain plugs in place.
We remove the clutch with the bearing and the foam rubber rings of the front cover.
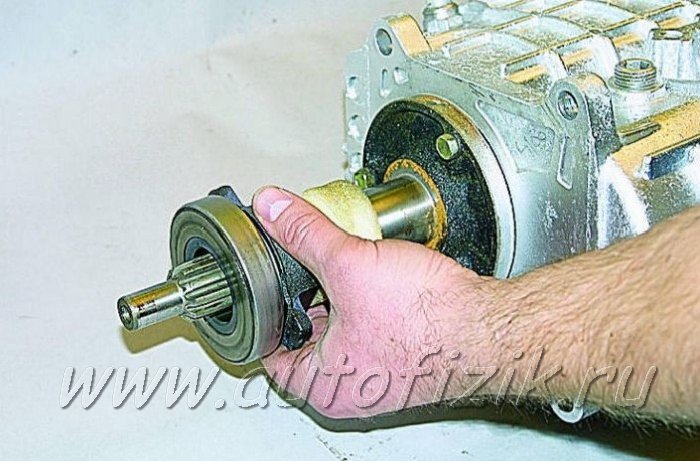
Remove the power unit support.
Remove the reversing light switch (see Replacing the reversing light switch).
Remove the speedometer drive (see Replacing the speedometer drive).
Using a 12 key, unscrew the three bolts securing the bearing cover (the bolts are installed on the sealant).
Remove the cover with the gasket.
When installing it later, pay attention to the coincidence of the oil drainage channel in the cover and the holes in the crankcase.
Prying off with a screwdriver, remove the input shaft seal from the cover (when disassembling the gearbox, we replace all the cuffs, regardless of their condition).
Press in a new cuff with a mandrel or a head of a suitable diameter.
Using the "13" key, unscrew and remove the bolt securing the bushing of the reverse gear axle to the front crankcase.
Use a thin screwdriver to pry and remove the input shaft bearing retaining ring.
Turn the key "12" and remove the breather.
Using a 12 key, unscrew ten bolts connecting the front and rear crankcases (two bolts passing through the dowel sleeves are longer than the others).
By gently tapping the brass mandrel with a hammer, undo the front and rear crankcases.
ATTENTION
In this case, do not strike at the end of the input shaft, as the synchronizers will be damaged.
Disconnect the gearbox housings.
Carefully, trying not to damage, remove the gasket.
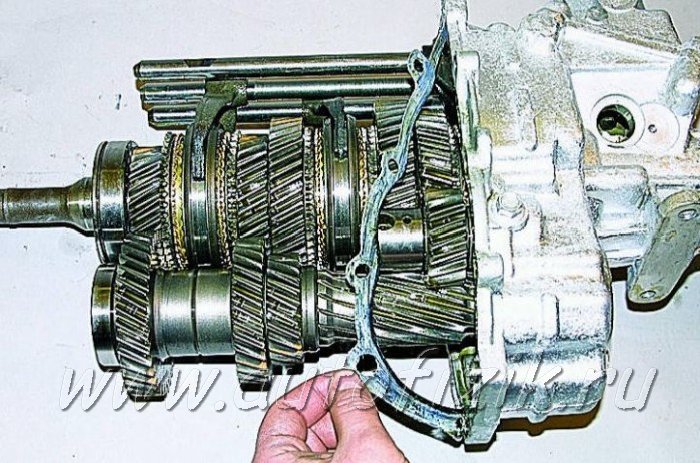
We take out the adjusting shims from the bore under the intermediate shaft bearing in the front crankcase (they may not be there). In this case, the axial clearance in the bearings is set only by the crankcase seal.
Turning the input shaft, we turn on the reverse gear (we move the V gear and reverse gear forward).
Using the "10" key, unscrew the bolts of the three gear shift forks.
Using the "12" key, unscrew the four bolts securing the gear lever housing.
Remove the lever housing with a gasket.
Using the "12" wrench, unscrew the bolts of the rod retainer plate.
Remove the plate with the gasket.
We take out three springs and three balls of the gearshift clamps (they can be removed with a magnetized screwdriver or by turning the box over).
We take out the rod of the 1st – 2nd gear (so as not to confuse it during assembly, we immediately put the plug on the rod and fasten it with a bolt).
We take out the rod of the V gear and reverse gear by putting the appropriate plug on it.
We take out the rod of III-IV gears. Remove the blocker pin from the stem.
To prevent the plungers of the blocker from falling out, we insert tubes rolled from thick paper into the holes of the rods.
Using the "13" key, unscrew the bolt securing the reverse gear axle to the rear crankcase.
Using pliers, we push apart the tendrils of the circlip of the rear bearing of the secondary shaft and, tapping with a copper hammer on the rear end of the secondary shaft, ...
… We take out the set of shafts together with the axle and reverse gear.
Disconnect the primary and secondary shafts.

We remove the IV gear synchronizer and take out 14 rollers of the front support of the secondary shaft.
Gears, synchronizers and other parts located on the input and output shafts are similar to each other, therefore, to facilitate subsequent assembly, they should be carefully laid out in the order of removal.
Using two thin screwdrivers or special pliers, we unclench and remove the locking ...
With a beard (with two mounting blades or a special puller) we press the input shaft bearing.
Similarly, remove both intermediate shaft bearings.
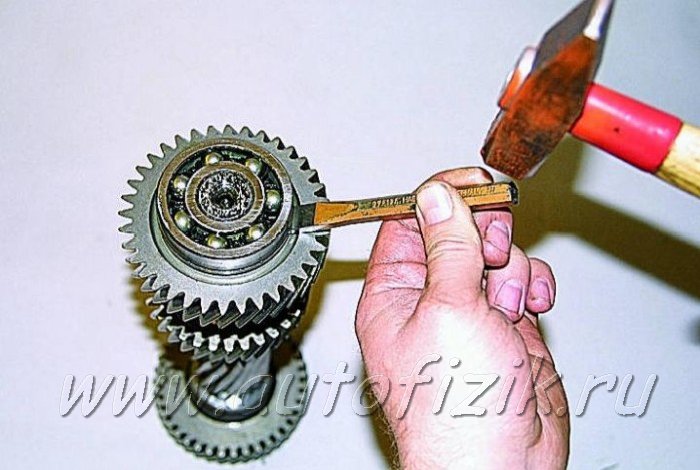
Installing the output shaft vertically in a vice through soft shims.
… And a snap ring of the III – IV clutch hub.
Remove the clutch assembly with breadcrumbs and synchronizer springs.
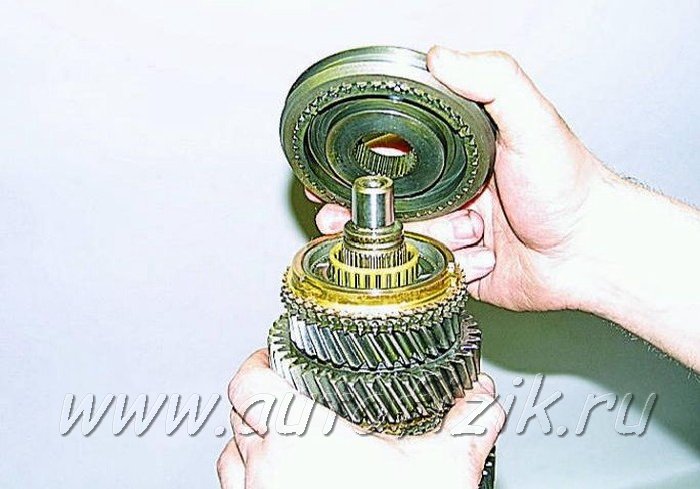
It is better not to disassemble this kit, but if such a need arises, mark the relative position of the parts.
ATTENTION
The gear clutches are not symmetrical, so they only fit in one position.
Removing the synchronizer ring ...
... and a gear wheel for 3rd gear with a plastic cage and rollers.
Use a screwdriver to pry on and remove the retaining ring ...
With a magnetized screwdriver, take out the locking ball of the half rings.
We remove the gear wheel of the 2nd gear with the bearing.
Remove the 2nd gear synchronizer ring.
Removing the clutch for engaging 1st-2nd gears ...
... and the 1st gear synchronizer ring.
Remove the 1st gear with the bearing.
We carry out further disassembly of the secondary shaft from the other end.
Prying off with a thin screwdriver, remove the locking ...
We remove the drive gear of the speedometer drive ...
... and take out its locking ball.
Using two mounting blades or a special puller, we remove the rear bearing of the secondary shaft.
We take out the pin with pliers.
Remove the V gear with bearing ...
Remove the spacer ring.
We remove the spring ring with special pliers and screwdrivers and then ...
… The clutch for engaging the 5th gear and reverse gear.
Remove the synchronizer ring.
Remove the reverse gear with bearing.
ATTENTION
The thickness of the spacer between the gearbox housings determines the axial clearance in the intermediate shaft bearings. Therefore, we must install it, lubricating it with a thin layer of sealant for reliability. Sealant should also be applied to all other cardboard gaskets of the transmission.
When assembling, the bolts connecting the crankcase parts should be degreased and the threads covered with sealant. After installing the unit on the car, do not forget to fill the box with 1.2 liters of transmission oil (up to the level of the filler hole).
- Features of the repair of the gearbox "Gazelle"
- Features of Gazelle gearbox repair
- How the gearbox is arranged on the Gazelle
- When a gearbox repair is needed
- The main malfunctions of the gearbox on GAZ 3307 cars
- How to repair a Gazelle checkpoint
- Essential tool for removing and disassembling the box
- Step-by-step instructions on how to remove the box
- Disassembly and assembly of the Gazelle gearbox
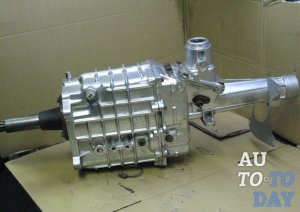
The Gazelle checkpoint is reliable and durable. But constant loads sometimes lead to its breakdown. Repair of the Gazelle gearbox will require from the driver:
- knowledge of the materiel of the car;
- the ability to remove the checkpoint, disassemble, and then assemble and put in place;
- strict adherence to safety regulations;
- attention, accuracy and patience.
Transmission - mechanical, five-speed. Consists of:
- two aluminum crankcases (connected with 10 bolts);
- primary and secondary shafts (connected to the crankshaft and cardan);
- an intermediate shaft with cut teeth of the 1st gear and reverse gear, a pressed gear block and a speedometer drive gear;
- inertial synchronizers;
- spring balls for gear fixing;
- blocking the inclusion of gears at the same time;
- a damper lever device;
The signal for urgent repair of the Gazelle gearbox is:
- Inability to change gear or if it is difficult to do so.
- When you try to turn on the gear while driving, a loud crack is heard.
- Self-inclusion of the transfer (threatens the danger of an accident).
- Any extraneous noise, crunching, tapping at the checkpoint.
- Scheduled diagnostics of the Gazelle checkpoint should be carried out every 300,000 km.
Long-term operation of Gazelle cars made it possible to make a list of the main faults of the Gazelle gearbox and their possible reasons:
- Cause of humming noise during operation - destruction of worn parts or loosening of fastening bolts;
- Crunch at the checkpoint - destruction of bearings;
- Crackle when switching - the synchronizer rings are worn out;
- Difficulty shifting speeds - jamming in the gearbox drive, wear of gears, burrs, etc. (you need to disassemble and look);
- Self-switching off speeds - misalignment of gear teeth, wear of rods and forks, loosening of gearbox and driven shaft fasteners;
- Oil loss - a crack in the crankcases, loosening of fasteners, wear of the gasket, oil seal, etc.
A breakdown was found, the reasons were found out - it remains to start repairing. To do this, it is necessary to remove and disassemble the checkpoint.
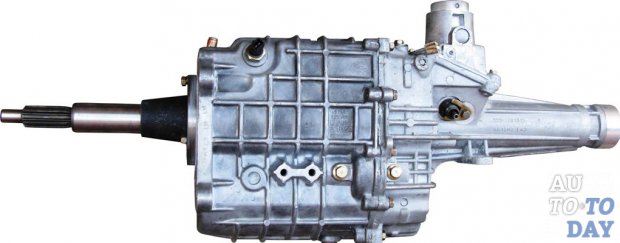
For repairs, you will need an inspection pit or overpass, as well as tools:
- a set of keys (for 10, 12, 13, 14, 17, 19);
- Screwdriver Set;
- beard;
- wooden blocks;
- pliers (pliers);
- mount;
- strippers;
- hammer;
- file, sandpaper;
- brass lining or copper hammer;
- mandrel for old oil seals.
- container for draining oil;
- rags;
- SHRUS-4, gear oil, GOI paste.
When repairing a Gazelle checkpoint with your own hands, first of all, you need to drive the car onto an overpass or inspection pit. After that, proceed to remove the box:
Step 1 - free the crankcase from oil;
Step 2 - remove the gimbal:
- using a file, mark the position of the cardan joint and the gearbox extension, as well as the cardan and rear axle flanges;
- using keys 12 and 13, remove the fasteners for the intermediate support;
- using keys 14 and 17, remove the cardan fasteners to the flange of the main gear drive gear;
- remove the shank from the gearbox (pull it back and pull it out);
- Plug the hole with a rag.
Step 3 - get the lever:
- from inside the cab, remove the cover and the upper part of the lever;
- unclench the spacer sleeve, remove the rubber pad and locking sleeve;
- remove the floor seal and the protective cover, unscrew the cover and remove the lever.
Step 4 - disconnect the speedometer and reversing light switch from the checkpoint.
Step 5 - remove the checkpoint:
- unscrew the fasteners of the intake pipes and the bracket to the gearbox (keys 12 and 14);
- disconnect the gearbox from the clutch housing (4 nuts);
- protect the block head with a wooden block;
- remove the cross member of the gearbox mounting and shaking, giving back the box itself.
Troubleshooting requires overhauling the Gazelle gearbox. Disassembly of the checkpoint must be done in stages:
- Remove the bearing cover, change the oil seal (key 12, screwdriver, mandrel).
- Remove the reversing axle bushing fasteners (spanner 13).
- Remove the input shaft bearing circlip (thin screwdriver).
- Remove breather.
- Disconnect the crankcases (12 wrench, hammer and brass mandrel).
- Engage reverse gear (by turning the input shaft).
- Remove the gear fork mount (spanner 10).
- Remove the lever bodies and the plate with the gasket (key 12).
- Remove the springs and balls (3 each) of the retainers (magnetic screwdriver).
- Remove the rods in order - 1, 2, 5, reverse, 3 and 4 gears and the locking pin.
- Using a wrench 13, unscrew the fastening of the reverse gear axle and remove the circlip of the rear bearing of the output shaft.
- Remove the shafts (using a copper hammer) and disassemble them. When disassembling, carefully lay out the parts in order, mark their relative position.
Assembling the Gazelle gearbox after repair is carried out in the reverse order. The shafts should be installed at the same time (tie with twine). Before assembly, you should carefully inspect the crankcase (for cracks, notches, bumps). Wash all parts (in kerosene, diesel fuel), inspect (bearings, shafts, gaskets, gear teeth, etc.). Any traces of corrosion, grind the faces. Replace all broken or suspicious parts with new ones, lubricate with transmission oil, SHRUS-4 (cuffs, splines, etc.). Treat the crankcase fasteners with sealant. Do-it-yourself Gazelle gearbox bearings should be replaced every 100,000 km.
Installing the gearbox The gearbox is installed in the reverse order. The slots must be lubricated with SHRUS-4. Next, a cardan is placed (you need to make sure that the marks match). After installing the gearbox, pour in 1.2 liters. oil into the crankcase (up to the filler hole). As you have seen, the work on the checkpoint repair is large and preparation for it must be serious.
Noise in the gearbox is usually the result of bearing wear, chipping of the working surface of the gear teeth, and even their breakage. Disassembly of the gearbox and replacement of damaged parts is required.
Another reason even a new gearbox can make noise is the low oil level in the crankcase. This malfunction is a consequence of an oil leak from the gearbox.
A misalignment of the crankshaft and clutch housing is also possible. Using an indicator mounted on a stand attached to the rear end of the engine crankshaft (gearbox and clutch removed), while rotating the shaft, check the runout of the bore for the gearbox in the clutch housing (db 0.3 max) and the non-perpendicularity of the rear end clutch housing (d. b. 0.15 max).
How to remove the gearbox can be read in many printed and electronic publications, such as the repair and maintenance manual, so this operation will not be described in this article.
The next step is to thoroughly wash and rinse all parts of the gearbox, including the crankcase of the gearbox itself. Next, conduct a close inspection of all gearbox parts for damage and excessive wear.
- chipping of the working surface of the inner ring of the input shaft bearing (for clarity, the bearing is cut)
- slight wear of the secondary shaft roller bearing,
- output shaft bearing play,
- play in the bearing of the toe of the input shaft of the gearbox (pressed into the crankshaft),
- the absence of one of the contacts of the reverse sensor (broke off when dismantling the gearbox)
- input shaft bearing V6-50307АКШ1,
- secondary shaft roller bearing 20-1701182,
- bearing of the secondary shaft V6-50706USH1,
- primary toe bearing 402.1701031,
- reverse gear sensor LSH.609.016,
- gearbox shank oil seal (2 pcs.) 24-1701210-07,
- set of paronite gaskets.
I will not describe the assembly itself either, but I will point out its subtleties.
For ease of assembly, it is better to screw the rear part of the gearbox housing with self-tapping screws to the bar (see below in the photo). In this state, it is easier to insert the shafts, the crankcase does not fall anywhere and does not collapse.
For this, a similar block is taken as for the rear of the crankcase and a hole is drilled with an 18 mm feather drill, then the output shaft is inserted into the drilled hole (see photo). Now the work on pressing will be much easier, and will not spoil the shaft itself when it stops.
In the same block, next to the previously drilled hole, a new hole is drilled with a 16 mm nib drill. Then the input shaft is inserted into the drilled hole (see photo) and 14 rollers are installed. Without removing the shaft from the bar, we connect the primary and secondary shafts. Now this node is ready for further assembly.
The resulting device in the course of work.
We install the primary, secondary and intermediate shafts in the gearbox housing. If the plunger jumped out during the parsing of the checkpoint, then questions may arise: how did they still stand? Schematically it looks like this:
If all the parts located inside the crankcase are installed, then you can connect the two halves of the gearbox housing and tighten 10 bolts.
It remains to install the gear lever and check the engagement of each of the gears, scrolling the input shaft, controlling the speed and direction of rotation of the output shaft. We unscrew the block previously screwed to the rear half of the gearbox housing. Screw in the reverse sensor after installing the gearbox on the vehicle.
Lubricate with paste (included in the kit with the ZMZ clutch disc): the seat on the input shaft for the crankshaft bearing, the input shaft splines and the sliding surface of the release bearing of the gearbox front cover.
... installation of the reverse sensor in the gearbox.
The oil should still be poured through the hole for the gear lever, because in this case, it will partially lubricate the gearbox elements, and conduct additional control through the filler hole.
![]() |
Video (click to play). |
Hang up the rear wheels of the car (jack up and place the rear axle of the car on the stops), start the engine and slowly turn on the gears one by one (create an imitation of the car's movement). Performance test of each transmission for about one minute. WHAT WILL IT GIVE!? Firstly, since the gearbox parts have been thoroughly washed, then the initial operation of the gearbox will be dry, despite the fact that the oil is already filled in As a result, the operation of the primary and secondary shafts goes dry, although where the gears and bearings were lubricated during the assembly process), and when the vehicle is operating without load, it will painlessly distribute the oil inside the gearbox system, and secondly, in case of unforeseen circumstances (sudden exit failure of any element, breakdown, etc.) the operation of components and assemblies will be without load, which will avoid more serious breakdowns.