In detail: man tga turbine boost sensor DIY repair from a real master for the site my.housecope.com.
- Like
- I do not like
Good afternoon, this is not the first time I have come across that people turn off the boost sensor, and I myself have already traveled 100 thousand without it. maybe someone knows what it affects, and why the motor works better without it, the consumption decreases. what else is happening somewhere with this chain, or joint nodes. after all, at first, the motor worked well with the sensor, and the consumption was pleasant, and then the consumption increased sharply, and the thrust was gone. removing the chip everything becomes normal.
- Like
- I do not like
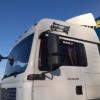
- Like
- I do not like

it was so. someone suggested to remove the sensor and spray it with liquid to clean the carburetor. helped. has been working for 3 months already.
on which part of the sensor was sprayed specifically, if not a secret?
- Like
- I do not like

I generally installed a new sensor, and no changes, then it’s not about it, but about the associated nodes
- Like
- I do not like
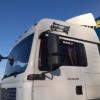
it was so. someone suggested to remove the sensor and spray it with liquid to clean the carburetor. helped. has been working for 3 months already.
on which part of the sensor was sprayed specifically, if not a secret? On the one inside the internal combustion engine. By the way, it also helps on the Volvos.
- Like
- I do not like
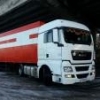
- Like
- I do not like
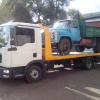
Disconnected the sensor but now the error 03088-06 is on!
The error will burn, do not pay attention to it, it does not bear any consequences. Pay attention to the consumption, I eat less in the city, and on the highway my appetite wakes up
- Like
- I do not like
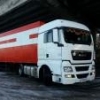
- Like
- I do not like

the turbine stops working on the move, so the engine does not pull. No errors
Then everything disappears and drives normally
- Like
- I do not like
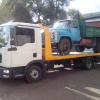
for a start, a car brand is needed, then some kind of drygatel, well, further requests. most likely AGR is riveting on your brain, mess up the forum, everything has been chewed for a long time ..
![]() |
Video (click to play). |
- Like
- I do not like

- Like
- I do not like

same as EGR 🙂. Exhaust gas recirculation system. (If you have a car with urea, then there is no AGR)
The topic has been discussed more than once.
If this happens after engine braking, then there may be a problem with the engine brake (the damper does not open)
- Like
- I do not like
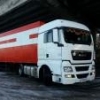
- Like
- I do not like
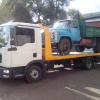
And what to do with the inflate sensor? Rinse, buy a new one or so and drive with a mistake. While it was turned off, the flow rate dropped to 37 liters, the turbine pulls better, the turbine runs quieter.
I’m thinking about pulling out the sensor and hanging it outside, and instead of it, put the plug in and there will be no error, and I think the car will go fine, but we need to experiment.
- Like
- I do not like
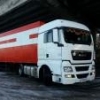
I’m thinking about pulling out the sensor and hanging it outside, and instead of it, put the plug in and there will be no error, and I think the car will go fine, but I need to experiment ..
The boost sensor measures the pressure and temperature (not always) of the incoming air. When it is turned off, the system goes into an emergency state and uses the ISA (international standard atmosphere) 760 mm Hg / st and +15 degrees, the closer to it, the better the engine works and vice versa. Therefore, in winter and in the heat, you are provided with a large flow when the sensor is turned off.
- Like
- I do not like
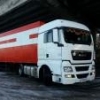
The boost sensor measures the pressure and temperature (not always) of the incoming air. When it is turned off, the system goes into an emergency state and uses the ISA (international standard atmosphere) 760 mm Hg / st and +15 degrees, the closer to it, the better the engine works and vice versa. Therefore, in winter and in the heat, you are provided with a large flow when the sensor is turned off.
Well, if it's not off and put a plug, let him measure himself on the street, so to speak?
- Like
- I do not like
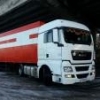
I took off the sensor! Visually, everything was normal, the only thing was an oily coating and the chip was a little in oil, washed everything out, blew it out and put it in place. Probably the problem in the sensor is due to the oily coating, it starts giving incorrect data from which, probably, there is a failure in flow!
- Like
- I do not like
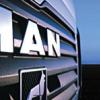
I took off the sensor! Visually, everything was normal, the only thing was an oily coating and the chip was a little in oil, washed everything out, blew it out and put it in place. Probably the problem in the sensor is due to the oily coating, it starts giving incorrect data from which, probably, there is a failure in flow!
For a long time I had the same assumptions that the sensor suffers from oil deposits, and it can be flushed.
- Like
- I do not like

Maybe a strange question, but where does the oil bloom come from?
Before talking about why a turbocharger sensor is needed, it is worth understanding what the very concept of turbocharging is. Automakers are constantly striving to improve the performance of powertrains. Every year, more and more technological innovations appear, but the essence and principle of operation of the motors remains the same.
The term "pressurization" itself characterizes the process of increasing the fresh charge of fuel in the cylinders of an internal combustion engine by artificially pressurizing. This technology is needed to increase the power of the motor. In the most favorable situations, the power can be increased by almost half of the nominal.
The most widespread is the so-called turbocharging, which is provided by a special turbocharger. The mechanical compressor, which was very common earlier, is gradually becoming a thing of the past.
In power units that are not equipped with a turbocharger, air enters naturally from the occurrence of vacuum when the piston is opened. Artificial air injection ensures that a much larger amount of the fuel-air mixture enters the cylinders. This leads to an increase in engine power. However, the turbocharger has its own significant disadvantages. With an increase in the volume of the combustion mixture, the temperature inside the cylinders rises very much. This can lead to detonation.
To prevent this phenomenon, it becomes necessary to install additional elements, such as:
- Turbocharger sensor;
- Intercooler;
- Compression ratio regulator.
Without the above, the coordinated operation of the entire turbocharging system is impossible. If any of these elements fail, an urgent replacement is required.
The boost pressure sensor is installed directly between the turbocharger and the intake manifold. It serves to control the boost pressure and, according to its readings, the electronic control unit draws conclusions about the needs of the power unit in the forced air.
Today the production of these sensors is carried out using two technologies: micromechanical and thick-film. The first is the most perfect and progressive. Most of these devices today are built using this technology. The main elements in this case are a chip made of silicon, a diaphragm, as well as four strain gauges located directly on it. When pressure is applied to this diaphragm, it bends. Due to its mechanical stretching, the strain gages begin to change their resistance. A change in voltage occurs in proportion to it. For greater sensitivity, the thermistors are interconnected using a special bridge circuit. The circuitry of the chip increases the bridge voltage, which at the output is between one and five volts. By analyzing the magnitude of this voltage, the ECM evaluates the pressure in the intake manifold. The higher the voltage, the higher the air pressure.
If the engine is not running, the intake manifold pressure is equal to the atmospheric pressure. At the time of starting the power unit, a vacuum or vacuum is formed in the intake manifold. When the engine is running at open throttle, the intake manifold pressure begins to equalize atmospheric pressure.
Failure of the sensor can lead to the shutdown of the turbocharging. However, for an accurate formulation of the correct diagnosis, it is necessary to conduct a competent diagnosis. It is possible that it is not the sensor that is faulty, but the turbine itself. In this case, it will need to be replaced.
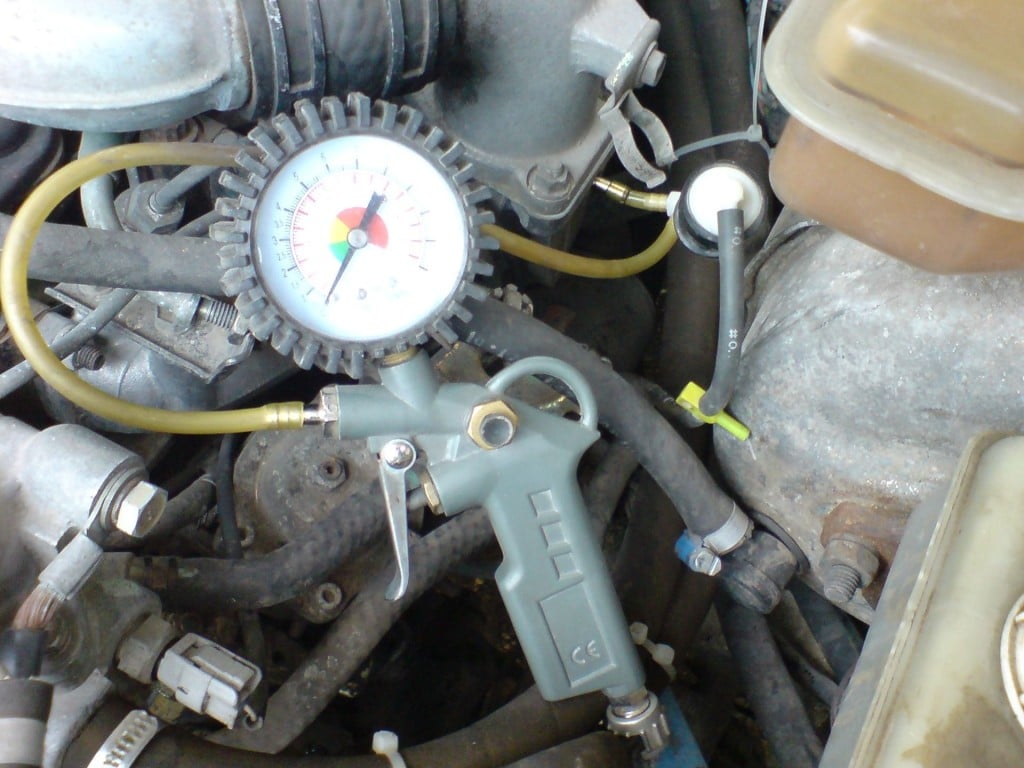
Turbocharging sensor check
Turbocharged powertrains must be equipped with a special sensor that monitors the boost pressure deviations. In order to limit this pressure at the right time, the electronic engine control unit activates a special solenoid valve, which is able to set the vacuum.
Turbine boost pressure deviation control is very similar to EGR deflection control. If the boost pressure goes beyond certain limits for a sufficiently long time, then this may indicate that there is a high probability of malfunction in the turbocharging system. If these deviations are short enough, then the presence of a malfunction is unlikely.
The boost pressure must be controlled in absolutely all turbocharged engines, since this indicator affects the correct filling of the cylinders, as well as the developed power, the amount of torque and the chemical composition of the exhaust gases. Checking the accuracy of the boost pressure sensor readings is performed on an uncooked power unit at the time between turning on the ignition and starting the engine. During the check, the values obtained from the turbo boost pressure sensor and the atmospheric pressure sensor are compared. As a result of comparing these indicators, the so-called differential pressure is obtained, which normally should not exceed a certain limit. If this limit is not exceeded, then the boost pressure sensor can be considered fully operational.
Time zone: UTC + 4 hours [Daylight Saving Time]
I have the same problem on Scania! I can’t figure it out, or rather there’s no time. You delete the error, the car seems to work fine, and then the same error pops up again and the car puffs like a tractor and does not drive.
The error appears to arise due to problems with the USR. Also there, that is, that is not. A question about the gas recirculation system. It is difficult to believe the turbine mechanics, it will not show without load.
What are you looking at? There should be turbo pressure. 950-1050 MBa at idle is normal.
If you suddenly decide the question, write how did it happen?
Message Sergei 1985 »02 Feb 2013, 15:30
Message Sergei 1985 »06 Feb 2013, 15:27
Message diagnostMAN »07 Feb 2013, 18:41
What are these numbers? and what does it mean “there are no more errors” and which one is? what does it mean “was 250 made 300” what was changed when repairing injectors? checked or repaired the injection pump? what kind of diagnostics did the car test by the dealership?
the presence of black smoke indicates certain malfunctions: 1. the boost or boost sensor is faulty 2. rich mixture, (the ignition is not set correctly, the injectors are faulty, the injection pump is faulty) 3. AGR valve is faulty
Added after 2 minutes 16 seconds:
Yes, I forgot to ask, what kind of fuel do you think is normal for your car?
Message Sergei 1985 »07 Feb 2013, 20:14
1.these figures 1.3-1.4 inflation pressure made diagnostics on the go loaded with mine tech
2. errors in abs, well, for little things, there was a couple of times the error of the first nozzle with the end (-02) but a noticeably high consumption disappeared with this error
3.I took all the nozzles to the master, all 6 lutes, they offered me to restore them, I agreed the pressure on them was 250. But the master said the mana tga should be 300, in short, he put 300-305 pressure on the forces
4.Recently they made diagnostics in the man's service in Pyatigorsk, they said that all the sensors are working, look for a jamb on the mechanical part
5 injection pumps were not touched at all, but they repaired the injection pump and changed the valves with rubber bands, ours crumbled.
6. do we have euro 2 in mine, d2866lf32 engine there is no AGR valve in the same place?
Added after 7 minutes 29 seconds:
we bought a car, we don’t carry a ref overload coupling, the driver of the cat used to work on this car 37 said, at least it’s okay.
Added after 2 hours 55 minutes 2 seconds:
wmah05zzz1m316263 can you completely decipher the wines
Message diagnostMAN »08 Feb 2013, 21:20
1. you still need to diagnose the dealer diagnostics there you can do a pump test.
2.if the nozzles were not changed on the nozzles, then I see no point in repairing
3.Agr on fault really did not find, probably one of the first models of tga (all of the tga euro3 I met)
4.Well, all the same, the fuel pump can fly with ignition when it was removed (although an error on EDC should appear)
Message Sergei 1985 »08 Feb 2013, 21:37
through the fault of all the information that is possible, where and what kind of kit, what would you advise to put new ones about the nozzles, and tell me which number goes,
and the first nozzle can increase the flow rate and add black smoke
Added after 5 minutes 12 seconds:
I forgot to ask in the muffler there is nothing that can get clogged to increase the consumption, just guys say from the parking lot
Welcome to the page of our site. The specialists of our company have accumulated considerable experience in diagnostics and repair of the multifunctional unit of the electronic pneumatic system of the MAN TGA - ECAM truck. The modulator or EKAM unit is designed to prepare air suitable for safe operation of the truck pneumatic system. The unit functions as a moisture separator and dehumidifier. With the help of sensors, it monitors the pressure in the air circuits and, with the help of solenoid valves, maintains it. All processes are controlled by an electronic control unit built into the modulator housing.
There is reason to believe that the air preparation system is out of order. If the truck exhibits the following characteristic features of the malfunction:
- Doesn't pump air
- Pads do not release
- No brakes on the tractor
- No brakes on the trailer
- Low pressure in the circuit
- High pressure in the circuit
- Venting air
To determine the cause of the above malfunctions, it is necessary to carry out diagnostics. Diagnostics will already accurately establish the cause of the equipment breakdown. Some of the possible causes are listed below:
- No power on the ECAM modulator unit
- Broken heating element
- Air pressure regulator malfunction
- Malfunction or open circuit of solenoid valves
- Software failure (faulty RAM; ROM)
- Open or short circuit of the CAN bus line (Kan)
- Clogged and oily air circuits
- Mechanical seizure of valves
We provide the following services for the elimination of malfunctions arising in the electronic blocks of EKAM trucks MAN TGA:
- Repair of the electronic control board
- Repair of electrical wiring connecting the ECAM to the vehicle environment
- Replacing a failed unit
- Electronic unit programming and firmware
- Restoration of the CAN bus to the control unit
- Bulkhead, lubrication and cleaning of mechanical valves and modulator air circuits
In the event of malfunctions in the operation of the MAN TGA air preparation unit, the indication lamps on the dashboard light up in red or yellow, and on the display the corresponding fault codes indicated below.
If any of the above codes is present in your situation, you can find more details here:
Also, more detailed information about the malfunction can be obtained after carrying out computer diagnostics.
Further from practice, one of such cases of diagnosis and repair. At the same time, 2 MAN vehicles are pulled up to the base at once. First born in 1987. Turning lamps and wipers do not work and close. Determine - the relay of turns and wipers does not withstand the load. We send the driver for a new relay. The second MAN TGA of the 2003 transitional model complains about the readings of the air pressure gauges of the primary and secondary circuits. The arrows point to the presence of air in the system. We diagnose with electronics and hands. The hero of the occasion is the old ECAM air preparation unit. Stands like a wing from a BOEING. We offer the owner 2 options for solving his problem - to find and buy the newest one for a lot - a lot of money, or make engineering solutions to change the principle of the components of the ECAM block. He agrees to the 2nd option, and with this he leaves, getting ready to buy everything necessary for this.
The first team leaves for yesterday's AKTROS, we need to finish the work and start the car. The MR block turned out to be in order, so it is already easier for us. With daylight hours, we find the main reason for not starting the engine. Someone, once, somewhere very strongly "artisan", when replacing the turbine gasket, considered it unnecessary to pull the clamp to the body of the electrical harness and it safely fell on a bump on the exhaust pipe, where the "annealing" of the wiring of the engine harness took place along with immobilizer. The reason is clear, we are repairing and the engine will start. The owner of the car is madly happy. At retirement age, he should not know what a car breakdown in our life is, however - if you like to ride - love to carry sledges, therefore we retire in a favorable mood.
By lunchtime, news came from the engineers of our company that they managed to restore the ECU of the IVECO STRALIS engine, which was idle under our repair. Tomorrow we are going to storm the car and wait for a positive result after the engine has started. The money for all this work is not small, but labor has been invested in order. We wait.
The third brigade goes to the amazing Russian-made equipment, among the common people - "golden hands" The machine designed for removing snow on the streets and highways does not want to go. The first glance at a car is disheartening and sad. People working on this technique apparently always and forever try to make changes in the wiring (as it seems to them) for the better. Hence all the troubles. In Russia, there are always and everywhere people who think that they know everything and are able to, and there, God forbid, what happens - it will carry over, it's okay, the main thing is to have time to complete the shift and hand over the tractor to the replacement as soon as possible. Smiled. "Snot" and the transfer turned out to be a sea and a small lake. Nevertheless, we figure it out - and after a short time the tractor starts up again. The driver is surprised - the tractor has never worked so well when changing. We hide our smiles modestly in the chipped beard. And really nice.
Turbocharger Man (Man) is a unit with a freely rotating turbine, the speed of which can exceed 80,000 rpm. At maximum speed, the linear speed of the sliding bearing sliding surface can exceed 30 m / s (100 ft / s), and the energy stored in the rotating assemblies can be equal to the power of the Man engine itself. These design features require almost perfect balancing of the Man turbine and the alignment of all rotating parts, as well as careful adherence to the rules of operation and maintenance of the Man turbine. In addition to failures of the Man turbocharger itself, most of its failures are usually associated with improper operation of the Man turbine, for example, blocking the intake air in the Man air filter.
In the event of a Man turbocharger failure, only the failed assembly or part is usually examined.However, in addition to this, it is also necessary to timely obtain information on the state of the Man turbine lubrication systems, air intake and exhaust gases before the Man turbocompressor fails, since these units directly affect its durability of the Man turbine and more often than others lead to its failure of the Man turbine. ... All Man turbine pressure data, leaks, interference, foreign material, high temperatures, loose connections in the Man engine timing system, or recent Man turbine repairs should be recorded.
In most cases, defects in the air intake and exhaust systems in the Man engine are the cause of a Man turbocharger failure. For example, if the intake air is severely blocked, the following can occur:
1. Excessive end load can cause accelerated wear of the thrust bearing in the Man turbine.
2. In addition, in this case, the speed of the turbocharger Man can increase significantly.
Excessively high exhaust gas temperatures can disrupt the operation of the MAN turbine lubrication system and destroy the metal structure in the Man engine. Foreign materials can enter the Man turbocharger through the air intake and exhaust systems of the Man turbine. Consequently, when analyzing the causes of failure of the turbocharger Man (Man), it is necessary to fix the main parameters of these systems of the Man turbine.
The condition of the Man turbine lubrication system also plays an important role in ensuring the trouble-free operation of the Man turbocharger, as it has three main functions: friction reduction, cooling and cleaning. Interruptions in the oil supply for just a few seconds can be disastrous. It is extremely important that during the operation of the Man turbine, a sufficient amount of oil passes through its lubrication system, which is capable of ensuring the operability of the fully unloaded suspension and stabilization system, as well as the removal of excess heat in the Man turbine. There are many reasons why the oil flow through a turbo compressor can be disturbed or blocked. The oil can contain large abrasive particles that can break the oil film and cause mechanical damage to the rotating parts of the Man turbine. Thus, in addition to a sufficient quantity of oil in the lubrication system, it is necessary to maintain its high quality. Before checking a failed Man turbocharger, it is necessary to determine the following main parameters of the Man turbine lubrication system, characterizing the quantity and quality of oil:
1. The type and viscosity of the oil used in the engine Man.
2. Engine oil level on dipstick Man.
3. Determination of the condition of the oil filter in the Man engine, as well as checking the paper filter element for the Man engine.
4. Scheduled oil sampling S • O • S. in the engine man
5. Information from the operator of the Man machine about deviations from the normal pressure readings in the lubrication system or other problems of the Man engine, preceding the failure of the Man turbine.
The turbine boost gauge on the dashboard does not display any boost at times. The thrust is not lost, there is no smoke, but the feeling of incorrect operation of the turbine
So see if there is a siphon at the outlet and inlet from the cylinder head to the turbine.
- EDC error 03076-09 in MAN TGA - 1 answer
- Antifreeze in a pallet MAN TGA - Stack overflow
- How to tighten the MAN TGA 26.413 cylinder head mounting bolts? - 0 replies
- What is the oil in the automatic transmission and the MAN TGA 26.410 bridge? - 1 answer
- Get started only with the air MAN TGA - Stack overflow
- What is the tightening torque of the MAN TGA injectors? - 1 answer
- What is the tightening force of the connecting rod bolts MAN TGA 18.460? - 0 replies
- What is the minimum and maximum height of the MAN TGA cylinder head - Stack overflow
- What is the diameter of the MAN TGA brake cylinder - 0 answers
- Is it necessary to hold out the cylinder head in the MAN TGA 2000 - Stack overflow
Subscribe to our channel in I am ndex.Dzene
Even more useful tips in an easy-to-use format
tightening torque of main and connecting rod bearings
Turbocharging today is one of the most common methods that allows you to significantly increase the power of a gasoline or diesel engine without increasing the displacement of the power unit. Installing a turbocharger is also a more efficient solution than mechanical superchargers.
The basis of turbocharging is the supply of air to the cylinders of the internal combustion engine under pressure. The more air can be supplied to the engine, the more fuel is burned. Civilian versions of turbo engines do not have too much boost, which is enough to achieve the required performance. It is quite obvious that in order to achieve maximum performance, turbines are installed on the engines, which are capable of providing high pressure. In this article we will talk about why you need an actuator on a turbine, what is the principle of operation of a turbine actuator, as well as how the turbine actuator is checked and this element is adjusted.
An actuator, also known as a wastegate or a vacuum regulator, is a valve for relieving excess air pressure at high engine speeds. The purpose of this solution is to provide a kind of protection for the turbocharger and engine. The specified regulator for protection against excessive loads is located in the exhaust manifold (in fact, on the turbine itself), the installation site is in the area in front of the turbine.
The wastegate works according to the following principle: if the engine speed is high, as a result of which the exhaust gas pressure and the charge air pressure increase, then the valve opens. Its opening redirects some of the exhaust gases bypassing the turbine wheel.
This is the case when the exhaust gas spins the turbine wheel to too high a speed, as a result of which the actuator triggers the bypass valve, that is, the exhaust gases pass by the turbine wheel. It turns out that the wastegate simply prevents the turbo from spinning to its maximum due to too much exhaust flow at high engine speeds.
We add that the turbo engines from the factory are initially fine-tuned. When tuning an internal combustion engine or installing a turbocharger on an atmospheric engine, the actuator must be tuned separately. Tuning and adjusting the turbine actuator is an important point, since the serviceability of the engine and turbocharger depends on the normal operation of the system. It is advisable to configure the Westgate using special equipment, but you can also do it yourself, which we will discuss below.
Now let's talk about frequent malfunctions in which the replacement of the turbine actuator is inevitable or the repair of this element is required. To begin with, there are several reasons for the failure of the specified part. First of all, electronic components break down, electric motor malfunctions are possible, and the teeth of the valve drive gears also break.
In some cases, the problem is eliminated after diagnostics in specialized turbine repair services. Experts check the controller's performance and perform a number of tests. A frequent malfunction that can be eliminated by repairing the turbine actuator without replacing is a failed cuff (turbine actuator membrane).
In the half of the last case, significant mileage and natural wear of parts leads to breakage, as a result of which the said cuff is often damaged. To eliminate it, it is necessary to remove the turbine actuator, after which the old membrane is removed from the housing. Next, the surfaces should be degreased, after which the new cuff is glued with glue to the body with two caps and additionally undergoes a circular rolling process. Then the turbine actuator is adjusted.
The need to adjust the wastegate is indicated by the appearance of a recognizable bounce at the place where the turbocharger is installed at the moment when the engine is turned off. Also, vibrations and rattling appear during gas changes, at the time of gas release. Such bounce appears as a result of the fact that the actuator stem begins to wobble, the rattling sound itself is created by the "gate" of the regulator. Insufficient air boost will also indicate problems with the actuator if no problems were found with the tightness at the intake and other elements of the turbocharging system.
I would also like to add that many drivers resort to manipulating the wastegate not only because of malfunctions, but also in order to increase performance and increase boost pressure, that is, they implement a kind of tuning of the system.
- In order to increase the pressure, there are several options available. The easiest is to replace the regulator spring. The more elastic the spring has, the more pressure the turbine will deliver until the valve is triggered.
- Another option is to tighten or loosen the end of the regulator, which directly affects the opening and closing of the damper. If the end is relaxed, then the valve rod is lengthened, tightening will shorten. The shorter the pull, the tighter the shutter will close. Accordingly, the opening will require a greater pressure and time interval. This allows the turbine to reach high revs, and this happens quite quickly.
- The third option for boosting boost is the boost controller. This mechanism is a solenoid that can replace real pressure data. Such a device is placed in front of an actuator, the main task is to reduce the pressure indicator, on which the wastegate operation depends. The boost controller actually bypasses part of the air, which prevents the actuator from evaluating the actual pressure.
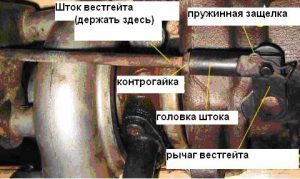
- at the very beginning, the bracket is removed from the stem, then the nut is loosened with a key;
- then use pliers to tighten the wastegate adjusting screw. This should be done counterclockwise;
- tightening occurs until the wicket is completely closed;
The completion of the adjustment process can be considered the tightening of the nut with a wrench of 10, as well as the installation of the bracket in place. As a result, after this adjustment, the actuator should have the maximum closing degree. After that, you can start the engine and check the operation of the device in different operating modes of the internal combustion engine. There should be no extraneous sounds from the wastegate on gas valves and when the engine is turned off, the boost pressure also predictably reaches the desired values.
Trucks only outwardly seem large, powerful and hardy. In fact, they just as need timely and high-quality care, like any foreign-made passenger car.
Car service MAN also requires carefulness, a certain leisurely and skilled approach and high quality of the required materials. Very often there are situations when MAN turbine repair is urgently needed. And this can happen much earlier than a complete overhaul of an automobile internal combustion engine.
The most common reason for repairs is poor quality lubricant. It's all about the design of the turbocharger. In some cases, its rotor part needs to rotate at a very high speed in bearings. This leads to the fact that in a car it is really difficult to find the same device that needs as effective lubrication as the aforementioned turbine.
Another fairly common cause is poor oil flow into the turbine bearing assembly. This breakdown can also occur with poorly cleaned oil that enters the turbine. Oil plays a really big role in a car's performance. And if it is of low quality, does not meet the factory requirements, then entering the engine, it clogs it. In a short period of time, the rotor part of the turbine and its bushings wear out greatly, and gaps appear that are inadmissible in the operation of the unit. Such clearances can have serious consequences for the vehicle, and in particular for the turbine of a commercial vehicle. Oil quickly seeps into these gaps, and semi-dry friction appears in the bearing blocks, which leads to complete deformation of the rotor shaft. In such a situation, not only does the wear increase, but also at high temperatures the lubricating properties are lost and the rotor part of the turbine is coked.
There are a number of reasons that can lead to rapid wear of the turbine, but they are due to improper car care.
- engine oil change;
- changing the oil in the engine; the price is included in the cost of removing and installing the turbocharger;
This operation must be performed by a qualified technician. If the repair MAN turbinesis made of poor quality, unprofessional, then in the near future this process will have to be repeated again, and this is an additional expenditure of time, effort and money. Only a specialist can know the conditions for performing a repair, for example, that the sealing of the system must strictly comply with the manufacturer's instructions. Removal, assembly and repair itself must be carried out strictly according to the rules. The specialist checks everything: the crankcase ventilation system, the absence of foreign objects in the system, the oil condenser is checked, the air intake paths are specially cleaned.
Our specialists have the appropriate specialization and qualifications, as well as extensive experience in servicing Man cars. We produce quality MAN turbine repairquickly, efficiently and reliably.
One of the design solutions for increasing engine power is a turbine (turbocharger). It is known that the quality and completeness of fuel combustion depends on the amount of air in the cylinder. The main purpose of the turbine is to increase the volume of air supplied to the cylinders. As a result, the gas pressure above the piston increases, therefore, the engine power increases. But such a picture is possible only with a working turbine. In some situations, the turbocharger will fail. If you do not take appropriate measures to restore it, the consequences can become very dire.
The service life of the turbocharger, declared by the manufacturer, is 200-250 thousand km. But this is possible when the operation is carried out according to its requirements. In the event of their violation, prerequisites are created for a significant reduction in the resource of work, and repairs will be required.
- use of contaminated or inappropriate brand of oil;
- its low level in the engine;
- refueling with low quality fuel;
- contamination of air and oil filters;
- malfunction of the catalyst;
- untimely maintenance;
- mechanical damage;
- overheat.
Butter. According to statistics, it is the main cause of breakdown. The main feature of the turbine is its high rotor speed.Hence, the loads on the bearing assembly are enormous, and if you do not provide it with high-quality lubrication in full, destruction is inevitable.
Poor quality fuel leads to the appearance of various deposits on the working parts of the turbocharger, which also disables it. This is also facilitated by various additives that increase the cetane number of the fuel.
Contamination of the air and oil filters will ultimately significantly reduce the purification of air and oil, which in turn will cause the prerequisites for the destruction of the turbine.
A defective catalyst can cause the turbocharger vanes to break apart with small pieces of burned-out internal packing.
Untimely maintenance means the operation of the machine with dirty filters, irregularities in the fuel supply system. We already know the results of this.
Mechanical damage. A particular danger is caused by various small objects falling on the blades of a rotating rotor. Their destruction in this case is inevitable.
Overheating leads to the formation of carbon deposits and coking of the internal elements of the turbine. In the worst case, cracks can form on the surfaces of parts with their subsequent destruction.
Common and frequent causes of turbocharger malfunctions are listed.
- the exhaust color changes to black or dark blue;
- oil consumption increases;
- engine thrust is sharply reduced;
- the backlash of the turbine rotor increases;
- traces of oil appear in the area of the turbocharger and on the pipelines.
With the appearance of such signs, the car must be presented to a specialized car service for diagnostics.
It is possible to determine the technical condition of the turbine only at a specialized car service. The possibility of further operation of the car will depend on the results.
- no oil leaks;
- no shaft backlash;
- rotation of the rotor.
Then the turbine is installed on a stand, where the degree of boost, vibration acceleration of the rotor and its imbalance, settings and valve operation are checked. Additionally, several more indicators are taken.
All results of inspection and measurements are recorded in the defect list. By analyzing the data obtained, the method of restoring the turbocharger is selected.
If a turbocharger fails, the question arises about the possibility of doing repairs yourself. Especially for professional drivers. Moreover, the unit does not represent great complexity, which contributes to the adoption of such a rash decision.
Yes, the design is simple. But it is not possible to carry out the adjustments and settings on your own. This requires special tools and equipment. There is no such set in any garage, whether it is a private or a reputable company, the car park of which includes more than a dozen cars.
- the cause of the malfunction is determined;
- selection of parts to replace faulty ones is carried out;
- primary assembly with testing is performed;
- balancing of moving parts;
- check on a test bench;
- final assembly and installation on the machine;
- computer diagnostics of the engine.
Determining the cause of the malfunction is the turbine diagnostics.
When selecting new parts, the entire unit goes through a complete sandblasting and chemical cleaning process.
Initial assembly with testing consists in adjusting the geometry change system and all clearances after assembly of the unit.
Balancing check is mandatory for the shaft-rotor wheel pair. The imbalance is corrected by the selection of these parts.
After the final assembly, the turbocharger is tested again at the bench and then installed on the machine.
Computer diagnostics of the engine is completing the repair.
As you can see, the process of restoring a turbine is a certain complexity. It is possible to repair the turbine in compliance with all technical specifications only in a specialized service station. This task is not feasible without special equipment. By the way, our car service is fully equipped with it. The turbines MAN TGS and MAN TGA restored by us did not cause any complaints in further operation.
And we produce them with high quality. This is clearly confirmed only by the positive feedback from our grateful customers.
Highly qualified specialists of our car service have ten years of experience in performing work on the restoration of turbochargers. The car service is equipped with the most modern certified equipment and tools. We give a guarantee for all work performed by us.
The constant availability of the necessary spare parts in the service station's warehouse can significantly reduce the time spent on the repair of the machine.
Flexible pricing policy, discounts and ongoing promotions make our car service more attractive for each client.
![]() |
Video (click to play). |