In detail: do-it-yourself grundfos pump from a real master for the site my.housecope.com.
Equipment Grundfos (Grundfos) due to their reliability, performance and ease of use are widely used in all industries.
They are used in the field of housing and communal services in the construction of centralized heating, water supply, sewage disposal, servicing agricultural and forestry enterprises, as well as in equipping industrial complexes.
Timely maintenance of a pump or pumping station for any purpose is a guarantee of its correct operation and the durability of the system as a whole. Repairing pumps in a specialized service center, for example, in Sergiev Posad, is initially an expensive pleasure. However, if you are familiar with the device of the unit and understand the principles of its operation, it is quite possible to eliminate the malfunctions on your own.
to the menu ↑
The Grundfos range is represented by all the main categories of pumping equipment:
- downhole;
- sewer;
- centrifugal;
- circulating;
- multi-stage self-priming units.
Range of pumping equipment Grundfos
Borehole pumps are used in the water supply system and in the arrangement of wells with artesian water, for filling tanks and other water distribution systems. As a rule, these are downhole installations operating in continuous or short-term mode, regulated by a pressure switch and a hydraulic tank. The product package includes three main elements - the engine, the built-in filter and the upper or lower water intake system. Products are represented by the series of equipment SP, SQ and SQE.
![]() |
Video (click to play). |
Consider the device of Sololift sewage pumps, using the example of a typical Sololift 2 WC 3 unit. The unit consists of a tank equipped with inlet / outlet openings, into which waste water enters. After the pre-cleaning provided by the filtration system and upon reaching a certain level, which is monitored by the Grundfos level sensor, the pump switches on automatically. Thus, the process of pumping out liquid into a centralized line, septic tank or other disposal tank is started. The unit is also equipped with a shredder that recycles large household waste and prevents clogging of sewer pipes. The simplest installation is capable of raising water to a height of 5-7 m and transporting it 100 m in a horizontal plane.
Monoblock centrifugal pumps of the NB series are distinguished by a one-way suction system and are used in water supply, heating, ventilation, air conditioning and irrigation systems. The torque from the engine is transmitted to the rotor impeller, and fluid enters the central part of the unit. As the blades rotate, water or another carrier of thermal energy, in the case of a heating system, is thrown towards the outer elements of the housing and redirected to the outlet pipe under the influence of centrifugal force. The pressure values inside the system are regulated by a Grundfos level sensor.
Circulation pumps, presented by the series of equipment UP, UPS, UPSD, Alpha 2, are equipped with a wet rotor and are intended mainly for completing a heating system with a closed loop. Its operation is based on the centrifugal force generated by the impeller placed on the shaft. When water enters the central part of the rotating wheel from the suction pipe, it is thrown into the peripheral sections of the unit.The advantage of the equipment of this series is the automatic cooling of the rotor, which rotates directly in the pumped medium. Repair of a circular heating pump with a wet rotor is still recommended to be entrusted to professionals.
In the segment of self-priming equipment, the leader is Grundfos MQ 3-35, which is used in a pumping station with a diaphragm expansion tank. The circulation of water is stimulated by an increase in pressure due to the centrifugal force arising from the rotation of the impeller. When it is displaced from the peripheral compartments of the unit into the pressure pipeline, the pressure in the central part of the impeller decreases and the liquid enters the pump casing. Such models are used to increase pressure and as part of pure water supply systems (drinking or technical).
Circulation pump device Grundfos
As a rule, pump breakdown occurs suddenly and is mainly caused by incorrect operation, which also needs to be given a little attention. Installation of Sololifts, for example, and similar high-performance equipment and the first start-up should preferably be entrusted to specialists.
Before connecting a submersible or surface pump to the power grid or to a hydraulic accumulator, it is necessary to check whether there is liquid in the area of the intake device and in all pipelines of the system - with a "dry" start, the pumping station will fail with almost 100% guarantee. The volume and temperature of the water to be pumped must comply with the performance specifications and the manufacturer's recommendations.
When the pump is idle for a long time, for example, when used in a country house or in a non-residential country house, once a month it must be turned on for 15-30 minutes to prevent oxidation of moving parts.
Despite the differences in design and principle of operation, most types of pumps are characterized by the following types of problems:
- lack of torque;
- premature spontaneous stop of work;
- increased noise level;
- increased vibration;
- insufficient pressure;
- stop after the start.
The lack of torque, despite the fact that the unit is humming, indicates shaft oxidation as a result of prolonged downtime of the equipment or contamination of the system with foreign insoluble or coarse-grained elements in the composition of the pumped liquid. In both cases, cleaning can eliminate the malfunction; less often, measurement of the rotor shaft or the entire engine is required. If the pump does not rotate and does not make noise when switched on, it is necessary to check the parameters of the power supply and voltage.
When the pump shuts down arbitrarily shortly after starting, the problem is most likely caused by excess lime and salt mass in the space between the rotor and the starter. The problem is also solved by cleaning, which requires prior shutdown of the system and dismantling the engine.
A high noise level when switched on indicates the presence of an excess amount of air in the pipelines, which is sufficient to release with a simultaneous increase in the inlet pressure. Sololift repair is not required in this case.
The increased vibration level is due to the fact that the bearing, which the pump is equipped with in some models, has become unusable and needs to be replaced.
Pressure defects occur when the viscosity of the pumped liquid is higher than the capacity of the pumping station, which is eliminated by replacing the clogged filter. Another reason is an incorrectly implemented three-phase connection. This is also the reason for the shutdown of the equipment almost immediately after its start-up.
The device of the pumping station Grundfos
The causes of breakdowns also include uncontrollable external factors - freezing of liquid in pipelines in the event of insufficient insulation or abnormal climatic phenomena and water hammer during a "dry" start.
to the menu ↑
Repair of the Sololift pump, as well as the repair of a Grundfos pumping station for any purpose, can be done independently, having previously identified the source of the problem.
Equipment diagnostics involves several stages:
- start the pumping station, evaluate the level of noise and vibration;
- check the pressure indicators;
- make sure that the motor does not overheat during operation;
- check the presence and quality of lubrication of the nodal joints;
- make sure the integrity of the structure and the absence of leaks;
- inspect the box to ensure that the terminals are securely seated.
If you are confident that the malfunctions are not caused by lime deposits and contamination, overloading or operating at maximum capacity, the pump can be disassembled. When planning to repair the Grundfos pump with your own hands, make sure that the water is drained from the pipelines and turn off the system. Disassembly begins with the junction box and a visual assessment of the components. As a rule, such an inspection makes it possible to immediately detect a burned out or worn out part. If not, we will continue to disassemble the installation.
The engine must be in an upright position during disassembly.... This will prevent the risk of oil leakage. To diagnose the trigger, an ohmmeter must be connected to the engine. This tool, when the handle is rotated, generates a voltage in the range of 200-300 V, sufficient to take readings on a resistance tester. Too high diagnostic data reaching infinity indicates an interruption in the operating phase, too low - an interturn short circuit. Self-adjustment of the operating parameters with such deviations is impossible.
to the menu ↑
Any pump is susceptible to damage. It is necessary to take into account their constant contact with various kinds of liquids. Therefore, even pumps from the well-known Danish company Grundfos are not insured against stopping due to failure. It is the water that causes the loss of performance. Depressurization due to worn out glands or seals can create a breakdown in the insulating components of the pump. To avoid trouble, you should periodically inspect the pump.
It is better to entrust the repair to professionals. However, no one says that in some cases, some types of restoration work can be carried out at home. More on this later.
Before providing first aid to the pump, you should familiarize yourself with the most common causes of pump failure:
- The use of the pump for purposes not foreseen by the manufacturer.
- Incorrect installation of the unit.
- Voltage surges - from low to above required.
- Pumping liquids containing large solids.
- Ignoring the correct fixation of the cable.
The grundfos pump can also fail due to the failure of its pump. In this case, the only correct solution would be to completely replace the broken part of the device. Do not forget that in the process of replacing any parts of the pump, it is almost completely disassembled. The main task will be not only to assemble everything in the reverse order, but also during the assembly process not to harm the pump with anything else.
The best repair option would be to contact a service center, where the restoration of the device's performance and maintenance is always at a high level. With the help of the necessary tests and stands, the following will be carried out in a quality manner:
- breakdown diagnostics;
- replace broken components with original ones;
- will carry out post repair tests.
Test benches provide the ability to:
- check hydraulics indicators;
- measure the resistance level of the insulating material of the electric motor;
- test the cable supplying power to the motor.
Using a variety of tools of the service center, it is easy to:
- replace the rotor of the electric motor;
- change worn-out bearings that require pressing out;
- change the top cover of the engine;
- clean the pumping part of the pump from contaminants.
The pumps are taken out of working condition, various deposits settling on the walls. It is they who prevent the device from starting. Your hands will always help to get rid of the problem, even if they are not golden.
Getting down to the crucial moment, prepare the necessary working tool. You will need:
- hex key;
- wooden scraper;
- polishing paste;
- polishing wheel;
- cross and flat screwdrivers;
- hammer (medium and small).
The primary repair task will be to clean the rotor and shaft from deposits accumulated on them. Armed with a hex wrench, unscrew the screws on the pump. This brings us to the threaded connection holding the pump and its motor. Such repair of grundfos pumps is not the pinnacle of genius. After opening, you will be convinced that there is an impressive amount of rust.
It can be easily removed with a scraper or strong cloth. A small, flat screwdriver will help to get to the rotor and its impeller. It must be positioned in the grooves along the diameter of the support washer. The surface that has opened will need to be carefully sanded, which will eliminate the possibility of new dirt adhering. To do this, use a previously prepared grinding wheel.
At this stage, you can proceed to inspect the stator itself. Its main enemy is oxidation. The working tool here will be a hammer, with which it is necessary to tap the surface and knock down the deposits by vibration.
Rust in tandem with dirt is favored by a controlled pressure sensor. In this context, the maintenance of grundfos pumps is extremely important for stabilizing the functioning of the device and its operation in general. To do this, you will need to disassemble the pump into two parts by removing the cover of the unit.
The sensor can be removed by hand using the keys specially made at the factory, which are included in the standard package of the product. In some cases, it is required to lightly pry it off with a screwdriver, when the accumulated dirt impedes the removal process. The manufacturer requires it to be cleaned with soft tissues without undue effort. The best option would be to use an ordinary toothbrush.
Danish pumps are always efficient if they are repaired and serviced in a timely manner. Therefore, special attention should be paid to polishing the inner walls. To eliminate the laboriousness of the process, the work is facilitated by the use of polishing tools, which are most convenient to use fixed in the drill chuck.
Bearing wedging is also possible. To break it, sometimes it is enough just to turn the impeller. Limestone deposits are no less annoying. Cleaning takes place by means of preparing a vinegar bath. You will need to mix this acid with water in equal proportions. Try to pay attention to the threaded connections as well. Seal them if possible using a bicycle tube to create spacers.
Other breakdowns are not excluded. Stopping the pump is possible due to:
- seized bearing;
- inoperative sensor for the presence of a water flow;
- lowering the pressure.
In such cases, you should not disassemble the pump to the smallest detail. Just put it in manual control mode. To do this, remove the switch, which is locked and located on the pump distribution box. Such actions can make the pump work even if the drain valve is closed.Otherwise, you will have to turn the impeller manually. If you fail to rip it out of place, then a complete replacement of the element will be required.
Functionality is guaranteed by regular servicing of grundfos pumps. Sometimes there are exceptions to the rule. If the device fails to operate in the process automation mode, but works on manual control, try replacing the sensor for fixing the movement of water. The unit may have stopped listening to commands through the accumulated air in the system. Bleed it off by turning the center screw.
Problems are possible in any pumps, even circulation ones. Once you have decided to personally eliminate any potential problems, always try to assemble the pump in such a way that after the assembly is complete, there are no unnecessary parts left on the workbench. Stick to the reverse order of assembly.
Pump manufacturers such as Grundfos produce quality pumps that are characterized by high performance and long service life. But even high-quality equipment is susceptible to breakdowns in the event of non-compliance with the norms of use or when periodic maintenance is not carried out. As a result - partial or complete cessation of the functioning of the apparatus.
Grundfos pumps are usually repaired by specialized workshops, which charge a substantial fee for their services. Moreover, the problem itself is not always worth the money spent. The solution may be to repair the Grundfos pump with your own hands, which is quite possible with certain knowledge.
The repair of Grundfos pumps depends largely on the type of pumping device. Depending on the type of device, the design, the most probable malfunctions and the way of their elimination differ. Among the main series of pumping devices manufactured by Grundfoss, the following stand out:
- borehole pumps of the SQ, SQE, SP series;
- drainage and well devices Unilift KP, cattle;
- circulating devices for heating UPS, UPSD, ALPHA2, ALPHA3;
- sewerage system Sololift and Sololift 2 WC 3;
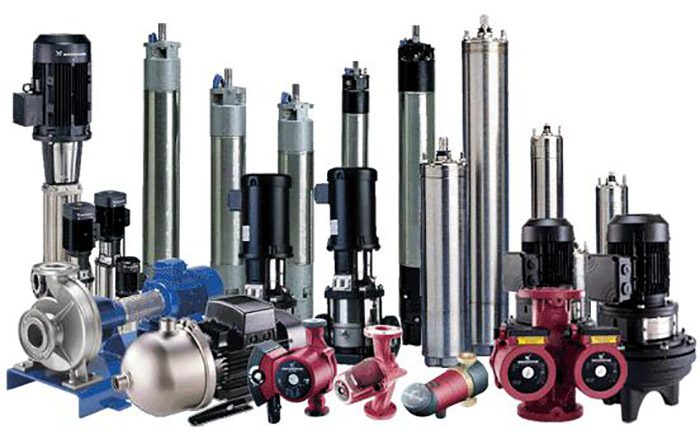
Range of pumping equipment Grundfos
Each individual device implies its own peculiarities of repair and maintenance.
to the menu ↑
Downhole tools such as SQ and SQE operate at great depths, where the bottom water can contain a high percentage of abrasives and silt. Therefore, the most common failure in such devices is contamination of the impeller and failure of the check valve. As a result, the device may not turn off after the end of work, or there is no pressure in the line. The solution to the problem will be to disassemble the pump and replace the check valve. In this case, it will not be superfluous to clean the entire working chamber.
Another common problem with the SQE series is air ingress into the system. As a result, the pressure level is disturbed, and the device turns on and off by itself. In this case, the power is turned off, the filters and the impeller are checked for contamination, then air is released from the line.
Also, a rather serious malfunction of a pumping device of the SQE type is increased vibration during operation. Such a problem can lead to too much silting of the source, which can make it unusable. Vibration occurs when the impeller is not centered. This happens when the fastenings on the housing are unevenly tightened, or the shaft bearing has become unusable. The solution is to replace the bearing and adjust the rotor inside the chamber using a ruler.
To solve any of the above problems, it is necessary to disassemble the apparatus. The procedure is carried out in the following stages:
- The device is firmly clamped in a vice. It is advisable to clamp with pipe halves so as not to deform the body.
- Further, VD-40 is injected into the thread area, after which you can gently turn it. The thread is often clogged with clay and sand, which greatly complicates the unwinding process.
- The rotor is removed from the working chamber.
Such disassembly is sufficient for cleaning the pump chamber and replacing the main components. The motor chamber is designed in such a way that it is not possible to disassemble it. Therefore, in case of damage to the motor winding, control electronics or electrical cable, the pump must be returned for repair.
After the device is disassembled, it is necessary to clean the impeller, bearing, valves in running water, and if necessary with a brush. You should also carefully inspect the mechanical seal between the working chamber and the engine compartment. There should be no obvious damage or tears on it. After the cleaning and replacement of components is done, the device is assembled and connected to the mains.
The device of the pumping station Grundfos
Assembly is carried out upside-down. In this case, the important points are the uniform fixation of both mounts on the body, correct thread adjustment, centering of the rotor and its fixation in the socket. If the filter at the suction ports is damaged, it must be replaced to prevent further contamination.
to the menu ↑
The Unilift KP and KRS series are designed for pumping melt water, sewage, septic tank contents, and drainage of swimming pools. At the same time, the simple design of such devices makes it easy to repair the Grundfos pump with your own hands.
Initially, drainage options are designed for difficult working conditions, therefore, breakdowns in such devices are quite rare. The main malfunctions that occur include:
- decrease in pressure;
- engine problems.
In the first case, there can be many reasons, but the main one is the presence of a leak. You should carefully inspect all joints for tightness, check on the outside and inside of the case wall for deformation. If no obvious problems are found, the piping, suction port and impeller should be checked for blockage. Blockages occur as a result of stagnation of dirty liquid inside the canal and its drying out. Cleaning is carried out under a strong pressure of water from a hose, and if necessary, a stiff brush is used.
In the second case, first of all, you should check the correct connection of the electric motor. Three-phase models have three working phases, and switching to another phase can solve the problem. If the problem is not resolved, the pump is disassembled further and the quality of the winding and wires is checked.
Before disassembling the device, it is imperative to turn off the device and check it for the ability to connect independently to the network. When disconnected from the mains, you can gradually remove the mesh filter of the device with a screwdriver. It is removed by uniform pressure along the entire groove at the junction with the body. Then, using a screwdriver, the case is rotated 90 degrees in the direction indicated on it and removed. This disassembly is sufficient to clean the impeller, filter and working chamber.
If after that the problem is not found, further disassembly takes place. Using a 13 key, the impeller retainer is unscrewed and it is removed. Further, the rotor nut is loosened. After completely loosening, the rotor is removed from the groove, and after it the stator can already be removed. After checking and cleaning all components, the device is assembled in reverse order. In this case, it is necessary to check the free wheel travel and the correct centering of the rotor. After complete assembly, it is necessary to connect the pump to the network and carry out a test run.
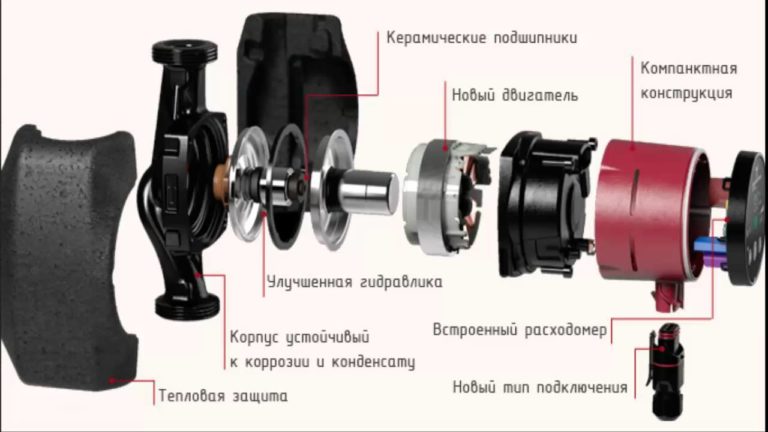
Circulation pump device Grundfos
It is possible to prevent the repair of the circulation pump, but for this it is necessary to carry out a monthly check of the device. For this, the device is turned on, and the inspector notes the following criteria:
- lack of strong vibration and extraneous noise during operation;
- lack of "punching" on the pipeline or the body of the apparatus;
- all nuts and bolts are tightened as much as possible and do not wobble;
- the engine operates in the optimal temperature range stated in the technical passport;
- there are no leaks between the units of the apparatus, and at the joints with the pipeline;
- all rubbing parts have grease.
If there is at least one of the problems, the device is turned off, dismantled, an internal inspection is carried out, and, if necessary, the main components are replaced.
The main problems that arise during the operation of circulation devices are:
- Running noise and the impeller does not move. The cause of this problem can be the ingress of solid particles into the rotor or oxidation of the mechanism. In this case, the water in the line is blocked, the accumulated air is released from it. Further, the fastening screws are loosened, and the motor with the rotor is removed. All hard parts are removed, and the rotor is turned for a while by hand or a screwdriver until the rust is removed. To prevent re-breakage, a filter is installed on the pipeline.
- Lack of noise and rotor rotation. In this case, the problem lies in the correct connection to the network, or in the weak voltage. It is necessary to check the condition of the power supply with a tester, it is also necessary to inspect the correct connection of the contacts and the functionality of the fuse.
- The pump turns on normally, but turns off after a certain period. Repair of the heating circulation pump in this case requires a complete disassembly of the rotor and stator. The reason for this phenomenon is deposits (lime, scale) on the connection between the rotor and the engine. Both mechanisms must be removed and cleaned thoroughly.
- High vibration level. The cause of this problem is a worn-out bearing at the connection of the rotor to the motor. In this case, a replacement is required.
to the menu ↑
The peculiarity of using Sololift pumps is that they are installed in places that are below the main sewer line. Therefore, the pumping station pumps the effluents under pressure forcibly. But, despite such serious tasks set for Sololifts, there is nothing difficult in the installation of a sololift and it can be done independently. And the correct installation of the device is the key to long-term operation and excludes the prompt repair of Sololift. Correct installation of the unit includes the following points:
- the device is installed exclusively on anti-vibration material;
- only those elements that come with the model are used as fasteners;
- the minimum distance to walls and other plumbing fixtures must be at least 10 mm;
- when connecting to a sink, a filter must be installed on the inlet pipe, and in the case of using on other plumbing, a check valve is required.
Cleaning of the Grundfos Sololift installation
As for the repair of the Sololift pump, there are many service options, depending on the specific problem. Most often, the following malfunctions occur:
- The engine does not start when the water reaches the start level. If there is such a problem, first of all, you need to check the presence of power in the network and the correctness of the connection. The fuse may also blow. This is caused by damage to the cable or motor. In this case, the main components are inspected, after which the fuse is replaced. If none of the above helps, you need to check the operation of the pressure switch.
- The motor is noisy but does not turn the impeller. There can be two reasons for this: the wheel is too jammed, or the engine is faulty. In the first case, the repair of the Sololift pump consists in restoring the mobility of the working body. The second option can be corrected exclusively at the service center. There are such centers in Moscow, Sergiev Posad, Orel, Tula, Kaluga, as well as in other regions of the country.
- The engine does not shut off by itself. The reason is a leak in the pipeline, an inoperative check valve, or a faulty pressure switch. Replacement of the corresponding part is required.
- Slow pumping out of fluid when all units are operational. First of all, it is necessary to check the tightness of the case and the absence of leaks on it, replace if necessary. Clearing a blockage in the system can also help.
Circulation pumps of various types are often used today in country houses and summer cottages, which makes it possible to make the operation of autonomous heating systems more efficient and at the same time save on energy resources. Meanwhile, if such a hydraulic machine fails, the entire heating system ceases to function, which puts its user with a choice: use the services of qualified specialists or repair the heating circulation pump with his own hands.
Dismantling the circulation pump
The reasons for the breakdown of circulation pumps, the types of which differ from each other in certain design features, are associated both with non-compliance with the rules for operating such equipment, and with the quality of the coolant, drops in the power supply network, as well as with a number of other factors. Before deciding on an independent repair of the circulation pump, you should understand well the design and principle of operation of such a device, which will allow you to establish the exact cause of its failure and eliminate it.
Without knowing the design of the circulation pump, you will not only be able to repair such a hydraulic machine, if necessary, but also engage in regular maintenance. The design of circulation pumps is:
- a body made of stainless steel or non-ferrous alloys;
- an electric motor, the shaft of which is connected to the rotor;
- directly the rotor itself, on which the wheel with blades is installed - the impeller (its blades, which are constantly in contact with the pumped medium, can be made of metal or polymer materials).
Circulation pump design
The circulation pump operates, regardless of its design, according to the following principle.
- After the electric current is supplied, the shaft of the drive motor begins to rotate the rotor on which the impeller is installed.
- The heat-transfer fluid entering the inner part of the pump through the suction branch pipe is thrown by the impeller and centrifugal force to the walls of the working chamber.
- The liquid, which is subject to centrifugal force, is pushed into the discharge pipe.
As mentioned above, depending on the design features, the circulation pump for heating can be of different types. So, devices with a rotor are distinguished:
In private houses, the most commonly used circulation pumps are "wet" type
For circulation pumps of the first type, which are used mainly for equipping domestic heating systems, the rotor is constantly in a liquid medium. This not only contributes to the lubrication of the moving parts, but also to their efficient cooling. The main advantages of this type of equipment include:
- low noise level during operation, since the water, in which all the moving elements of such a device are located, perfectly absorbs vibrations;
- ease of installation (such pumps simply cut into the pipeline), maintenance and repair.
Meanwhile, pumps with a "wet" rotor, if we talk about their shortcomings, are not very efficient, can be installed only in a horizontal position and are very critical of the lack of liquid in the heating system.
Pumps with "dry" rotor are installed in separate boiler rooms and are used in systems that heat large areas
The drive motor of pumps with a "dry" rotor is placed in a separate unit. Rotation from the motor shaft is transmitted to the impeller by means of a special coupling. Unlike devices with a "wet" rotor, pumps of this type are characterized by a higher efficiency (up to 80%), but also by a more complex design, which somewhat complicates the procedures for their maintenance and repair. Circulation pumps with a "dry" rotor are cut into the pipeline and their body is fixed to the wall, for which a special console is used.
In order not to face situations in which the circulation pump installed in the heating system will require repair, it is necessary to strictly follow the rules for operating such equipment, which are as follows.
- If there is no water in the pipeline, it is impossible to start the circulation pump.
- The value of the generated water pressure must be within the characteristics specified in the technical passport of the circulation pump. If the device produces a reduced or, conversely, increased water pressure, this can lead to its rapid wear and, accordingly, failure.
- During the period in which the heating system is not used, the pump must be turned on for circulation at least once a month for a quarter of an hour, which will prevent oxidation and blockage of its moving parts.
- It is very important to ensure that the water temperature in the heating system does not exceed 65 °. In water heated to a higher temperature, a precipitate begins to actively form, which, interacting with the moving parts of the hydraulic machine, contributes to their active wear and, accordingly, the failure of the entire device.
It is necessary to inspect the circulation pump and check the correctness of its operation on a monthly basis. Such measures make it possible to identify malfunctions in the operation of equipment at the initial stage and promptly take appropriate measures.
Periodic inspection of the circulation pump will significantly reduce the likelihood of its failure during the heating season.
Checking the circulation pump for correct operation includes such actions as:
- switching on the hydraulic machine to the operating mode and checking the level of noise and vibration generated by it;
- checking the pressure (pressure level) of the coolant created in the discharge pipe (as mentioned above, the pressure of the liquid must be within the values given in the technical data sheet);
- control of the degree of heating of the engine, which should not be too high;
- checking for the presence of grease on the threaded connecting elements of the pump and applying it if it is absent;
- checking the presence and correctness of the grounding of the body of the hydraulic machine;
- checking for leaks both on the pump casing and in the places where it is connected to the pipeline (if leaks are present in such places, it is necessary to tighten the threaded connections and check the integrity of the installed gaskets);
- Inspection of the terminal box and check if the wire is fixed in it (in addition, it is necessary to check whether moisture gets into the terminal box, which is unacceptable).
The main reason for the rapid wear of friction bearings in pumps is considered to be the increased contamination of the coolant.
It is possible to single out several of the most typical malfunctions for circulation pumps, which are quite realistic to eliminate with your own hands. Such malfunctions can be identified by their characteristic signs, without even disassembling the pump and without using complex diagnostic equipment.
A situation where the pump is noisy but the impeller is stationary is often caused by oxidation of the drive motor shaft. This can happen due to the fact that the hydraulic machine has not been used for a long time. To repair the heating pump with your own hands with such a malfunction, you must perform the following steps:
- disconnect the power supply;
- drain all water from the pump and the adjacent pipeline;
- by unscrewing the corresponding screws, dismantle the drive motor together with the rotor;
- resting on the working notch of the rotor with a hand or a screwdriver, turn it by force, moving it off the dead center.
Disassembled circulation pump
The pump will make noise, but it will not work even if a foreign object gets into its inner part, which blocks the rotation of the impeller. To repair the circulation pump in such a situation, do the following:
- turn off the power supply;
- drain water from the pump and the adjacent pipeline;
- disassemble the pump according to the above scheme;
- remove a foreign object;
- a strainer is installed on the inlet pipe.
This is how the body of the circulation pump looks from the inside.
If the switched on circulation pump does not make noise, but also does not work, there may be problems with the power supply. To identify the cause and eliminate such a malfunction, disassembling the circulation pump may not be required: using a tester, they check the level and presence of voltage at the device terminals. In many cases, to eliminate such a malfunction, it is enough to correctly connect the pump to the power supply.
If there is a fuse in the design of the circulating pump, then it could burn out during a voltage drop in the mains, which can also be the reason why the heating pump does not work and does not make noise when it is turned on. To restore pump operation, simply replace the blown fuse.
Armed with a tester and a schematic diagram, you can find more serious breakdowns in the electrical part of the pump, for example, burned out windings
In the event that a layer of lime deposits has formed on the inner surface of the stator, the running pump will periodically stop. To solve this problem, it is necessary to disassemble the pump and clean all its internal parts from lime deposits.
The reason for the loud noise of the equipment when pumping liquid can be the presence of a large amount of air in the pipeline. To eliminate such a problem, it is enough to bleed air from the pipes. In order not to face this in the future, you can install a special unit in the upper part of the heating system circuit, which will automatically release air from the pipeline.
If the housing of the hydraulic machine vibrates strongly when pumping the coolant, this may indicate that the bearing, which ensures the rotation of the impeller, is severely worn out. Repair of a circulation pump for heating in this case consists in replacing a worn bearing.
End graphite bearing of the "Grundfos" pump
Among the reasons for the discrepancy between the fluid pressure and the standard values at the outlet of the centrifugal pump are the following.
- The impeller is rotating in the wrong direction.
- The phase conductors in the terminal box are incorrectly connected (with three-phase connection).
- The viscosity of the heating medium used is too high.
- The filter installed on the suction line is clogged.
The specified issue is corrected according to the cause that caused the issue.
The causes of such a malfunction may be incorrect connection of the phase wires in the terminal box, bad or oxidized contacts in the safety assembly of the device.
To repair the electronic component of the pump, you will need basic knowledge of electrical engineering.
This is another nuisance that occurs quite often during the operation of such equipment. Why is the circulation pump heating up? The reasons may be different, but such a situation always indicates that your equipment is operating under increased load.
Thus, many situations in which the circulation pump does not work or does not work correctly can be dealt with on your own, without resorting to the services of qualified specialists and without purchasing expensive spare parts and components for repair.
Before the start of the heating season, in order not to subsequently face the failure of the circulation pump and its repair, it is necessary to properly prepare the device for a long period of intensive work.
- It is necessary to check the correctness of the pump insertion into the pipeline, referring to the arrow on the housing and the impeller rotation indicator. When installing a new pipeline for installing a circulating hydraulic machine, it is better to choose a section directly in front of the boiler, where the risk of air congestion is minimized.
- Grease must be present on gaskets and pump nozzles to prevent drying out.
- Check the condition of the suction strainer and, if clogged, thoroughly clean it.
- It is also required to evaluate the correct connection of the pump to the power supply, for which a tester is used.
- Check the tightness and reliability of the hydraulic machine connections.
- It is necessary to perform a test run, the results of which will show whether your equipment is ready for the heating season.
Before disassembling the circulation pump, if it becomes necessary (for example, during repairs), it is necessary to disconnect it from the power supply and remove it from the pipeline by unscrewing all fastening threaded elements.
After the pump has been dismantled from the heating system, you can start disassembling it:
- The cover is removed, which is fixed to the pump body with special bolts.
- After removing the cover, the impeller is removed from the inside of the pump.
After that, access to all internal parts of the pump will be provided, they can be inspected, cleaned or replaced with new ones, if necessary.
The sequence of disassembling circulation pumps of various models for repair is very well demonstrated by videos that are easy to find on the net.
![]() |
Video (click to play). |