Details: nissan presage do-it-yourself automatic transmission repair from a real master for the site my.housecope.com.
By the way, as Tsefirovody wrote, there are adjusting screws on two solenoids, this can be seen in the photo.
The cogs, that is, but adjusting something will not work, they are very stuck, like double punching
And to remove the valve body, it is enough to actually unscrew 14 bolts, 2 on the filter, and almost in a circle 12, since the filter, with the main number of bolts, is screwed only to the valve body, but there is an option to pour oil on it, since after removing the filter, from the unit another 300 grams of oil is poured out
Story: Fishing trip, vydovy nissanchik, mud. They kneaded for a long time and thoughtfully. At some point, the box refused to quickly turn the wheels back. Attempts were made, but sluggish, and at increased engine speeds. As a result, the car was dug up and pulled out, but even after the box cooled down, the reverse gear did not appear. It was, but only on a flat road and it feels like the box is skidding a lot Everything was normal with the movement.
Theory: During the excavations and the subsequent trip, that just did not think. The most suitable option is overheating of the automatic transmission fluid. However, this option assumes, in the same way, the axle boxes of the box when moving forward. And of course, the thought came to me about the automatic transmission breaking down, well, you never know everything that can break down.
Repair Attempt 1: Replacing the automatic transmission fluid. It gave a result - the reverse gear became more pronounced, but again only on a flat surface and if you press the accelerator pedal. In general, replacing the slurry did not give anything.
Search in manuals and forums: All searches, as before, led to the conclusion that the reverse friction discs had become unusable as a result of oil overheating or other factors (looking ahead - others).
![]() |
Video (click to play). |
A decision was made to extract, disassemble, troubleshoot and repair the automatic transmission right in the garage.
Organized with a relative, and flooded, the car on a half-meter bakulka with a jack. The garage is equipped with a pit, so it rushed: there is no photo, but in short, everything is according to the manual, all the hoses, all the wires were disconnected, from below everything that could be disconnected, the cardan shaft and everything in general. There is no hook in the garage, so we thought that we would wake up and put the box with our hands, we thought that it weighs 50 kilograms, maximum 70, and together we can definitely remove and short-circuit it back. They intended to shoot on a jack and a board across the pit. Oh, I'll tell you, shooting without hanging is still a pleasure. They squirmed for a long time, hard, the box was lowered on a jack, initially it was held on pillows and a pair of engine bolts.
After they jacked up the engine and the box with two jacks, they began to unscrew the pillow and the box from the engine (the flywheel was unscrewed in advance, there are technological holes, in general - all according to the manual ). They unscrewed, but no, something prevents the box from sinking into them - according to the manual, it is simply taken out downward. as a result, they found 2 more bolts for the engine and 1 motor - gearbox. Unscrewed - somehow it is all the same bad, probably stuck - and indeed, and on the guides it sits to the engine. Tugged. the box is unstuck, removed from the guides, we tensed. We pulled ourselves together, compensated for the box with the weight of the jack and began to lower it. It was a huge mistake not to remove the drives from the hubs - although they were not in the boxes, they interfered and resisted a lot and did not allow the box to be lowered and there was nowhere to put them. We tried to unscrew the hub nut in the process, it did not work, one - not from the hand. As a result, one of us held the box on a jack, the second unscrewed the hub from the rack so that by tilting the steering knuckle we could remove the drive to the side so that it would not interfere.
The drive was removed only one, the second was supposed to be pulled out in the process.Yeah. They unscrewed one rack (the steering tips had already been dismantled), tilted the entire hub and removed the entire drive from the box, then again the descent and recess of the second drive, the second sat deep in the box and to take it out of the box, the entire box was also moved towards the arch. In general, they barely took out a long drive, a box on a piece of wood, and it weighs a lot together with a gearbox.
Then they carried the box to the street and, with the help of a mini-washer, washed it at least a little, plugging the holes with rags. Then a box on a specially prepared table for parsing.
The manual assumes 88 points for disassembling the box, but what we need is a large-knot disassembly to gears with clutches. At first, they did not start according to the manual, in the end it turned out to be the wrong side, only one bolt was broken off (I did not want to unscrew, then the wrong side was grabbed by a couple of bolts until the moment of collection)
Unscrewed the oil pan, photo from this moment. Some comments along the way of the photos:
4-speed automatic transmission RE4F04A A flawless front-wheel drive layout was developed by Jatco in 1993 for the 3-liter Maxima, using the experience of the JF403E gearbox made in 1990 for Isuzu.
Later they began to put it on other popular cars Nissan and Infiniti with engines up to 3 liters. At the same time, a modification was released for a lower torque from engines up to 2 liters - RE4F03A... Until 1995, the JF403E modification was produced for Isuzu and other manufacturers. (Read what the letters and numbers in the box name mean on the page RE4F03A.)
The JF403E modification adapted for Mazda Millenia was called in Mazda: LJ4A-EL and was installed in parallel with the "old lady" GF4A-EL from 1995 to 2003. This workhorse also met on rare "Americans" under the Ford name 4F20E.
This family of 4-speed automatic transmissions is used on front-wheel drive vehicles with engines from 2 to 3 liters. Masters call it "04th Nissan", which is rightfully considered a success Jatco by combination: reliability / price. Competitors - aisinovskaya A540, which could not hold out for a long time and gave way to 5 (and 6) speed automatic machines, Ford CD4E, and GM 4T65E... But these boxes lag significantly behind the Jatka bestseller in many ways.
2000 to 2003 several modifications were reissued with the letter "B" - RE4F04B, for more powerful engines (Infiniti, Murano up to 3.5 liters), and then “V” - RE4F04V, but the super-reliable and heavy 4-speed Jatko gearboxes were soon considered “morally obsolete” and from 2006 this family was gradually changed to variators.
Pick up repair kits - press the button on the left.
Filters are typically Dzhatkov for 4-speed automatic machines, metal with an open mesh, which do not require replacement for many years, if you do not allow accidentally burnt oil.
Until 2003, they had a 10 mm intake (No. 315010), and after 2003, a variant with a deep pan appeared - a 34 mm intake (# 315010A).
The filter is rarely changed, often washed, even when Jatko recommends changing it (burnt oil). Instead of replacing the coarse filter, an additional main external fine filter (below).
The clutches in boxes operated in burnt oil are also changed with the whole set - 315003. Friction kits are also different for boxes before and after 2000 according to the diameter of the Reverse clutch. Until 2002 (at some assembly plants) discs Ø139mm were produced, and since 2000 they switched to reinforced discs with an outer diameter of 147mm (the inner one is the same). It is determined only when disassembling the automatic transmission.
The Master Kit kit includes the entire set of gaskets, oil seals, clutches and steel discs (except for the brake band) - 315007.
The most popular Nissan box in repair, which is called “4th Nissan” in professional slang.
Typical repairs of age automatic transmissions RE4F04 LJ4A-EL:
In addition to the usual set of consumables for the age machine bulkhead, mentioned above, the torque converter lock-up friction lining must be replaced. With powerful engines, Jatko's torque converter eats up its clutch first. The blockage, eaten away to glue, clogs the valve body and gives strong vibrations to the pump shaft, killing both the pump oil seal and the pump itself. The first sign of a running torque converter is a leaking oil seal.
Torque converter repair (order) - 315001.
It changes with the replacement of the clutches of the High package - 315106A. Craftsmen prefer Original Ribbon - Borg Warner, on right.
For LJ4A-EL and JF403E - old brake band ( narrow, since 1990 ) No. 310020A and your filter No. 310010A.
All clutches are replaced with a set, if the machine came for repair with burnt oil: No. 315003.
The clutches of the second generation (since 2000) have been changed, the diameter (147 mm) of the clutches of the weak Reverse package has been increased - 315110.
It is rare when ordering a set of steel discs - 315004.
Then the vibrations break the rest of the bushings along the chain. Change the entire set of 10 bimetallic bushings - No. 315030.
If you continue to kill the pump further, then. see Reconditioned Oil Pump - No. 315500.
A typical problem node of this machine:
- Rear planetary row, (Rear Planet) - No. 315584.
the splines are cut off. Occurs at high mileage aggregated with an engine with maximum torque.
Another popular repair location is replacing the Solenoid Kit RE4F04 № 315420 .
For Maxima (. 04B) in 2000, a new block of solenoids was released. Like the valve body for powerful engines since 2000 - its own.
For Mazda LJ4A-EL - its own set of solenoids, as well as for JF403E.
Of the clutch packs, two are leading by a wide margin in terms of consumables burning: - High Clutch -No. 315106) and - package Forward Clutch (315108).
Steel disc High [28Tx1.4 × 91.7] - No. 315126A - the leader in replacements, burns out together with the thrust disc. If the oil smells like burnt, these discs have to be replaced.
Even thrifty owners change a pair of friction clutches of the Reverse package - No. 315110. The rest of the packages have a slightly larger resource. And they can hold out until they start turning on the jerk and bump packs.
But with burnt oil from the blue discs of the High package, the masters recommend changing the full set of clutches - 315003. If you start the problem, then you have to change the High drum - # 315555.
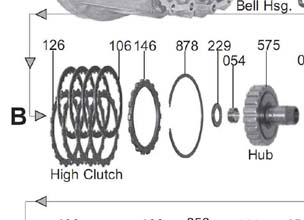
- Drum (Reverse) No. 315556, tears off the splines, especially in modifications RE4F04B since 2000.
In general, the "iron" of this box has a large supply, allows drivers a lot and breaks down only when the pallet already contains a lot of metal chips and shavings. With the timely repair of the torque converter and keeping the oil clean and unheated, this gearbox goes up to incredible mileage.
The inline filter helps keep the oil clean and reduces friction wear. This is recommended for all machines that have a standard filter with a metal mesh.
In addition to finely dispersed dust from the clutches, such a filter also retains the adhesive base of the clutches, in the case when the lining is erased to the very base. That protects the solenoids and valve body valves from hanging and wear.
Also, this filter has a magnet that retains iron dust from the planet's gears and a bypass valve, which is triggered if the filter has not been changed for many years and it is completely clogged with dirt. The outer filter should be checked and changed every year or every 10-20 tkm, depending on driving style. More details - here.
Leaving the oil out of the box through the oil seals can lead to big trouble.Therefore, if the craftsmen do not order a complete repair kit for gaskets and oil seals, then they always change the pump oil seals and axle shafts, if the box has come into overhaul for the second time with the same problem. (Replacing solenoids and not repairing the torque converter is a common mistake of economical owners).
- The valve body is often simply repaired and cleaned.
- One way clutch separator (No. 315642),
All these fairly reliable nodes develop their resource with the help of forgetful owners.
Manual for RE4R04A the tightening torques for the bolts can be found here.
The cost and availability of the items you need can be checked in the online store by clicking the number on an orange background to search for a part. A complete list of parts is below.
On which cars this automatic transmission family was installed:
Bulkhead box RE4F03B on Nissan Primera P12.
Bulkhead indications: almost complete absence of reverse gear. The car moved forward without comment.
Foreword.
The defect appeared gradually. Slippage appeared when moving back. At first, they were not very strong, then I could no longer move the 5 cm high tubercle.
The installation option is contractual, i.e. bu boxes: there were options from 10 tr (with Wingroad) to 40 tr with Examples. The state of the boxes is naturally unknown.
Repair option on the side: The amount is about 50 tr and there is no confidence in those who will do it.
As a result, I came to the conclusion that I have to do it myself. this is an acceptable budget and
the result will be a box that is almost new in terms of wearing parts.
The final straw for the decision was the ism report. those. Sergei.
Part 1. Removal.
Material support of the 1st stage:
Manual. Chapter REMOVAL AND INSTALLATION.
Tools: keys, heads, including heads for 18 and 16.
Lift, well, or a pit.
Part 2. Disassembly.
Material support of the 2nd stage:
- Manual. Chapter DISASSEMBLY.
- Tools: The collar is large, the collar is small. Heads 12 and 10, as well as wrenches for dismantling the oil cooling pipes. Flat-blade screwdrivers.
–The table is large on which oil can be poured. Rags, kerosene (5 l) and preferably a spray gun into which we pour kerosene and rinse everything.
-Compressor.
1. We measure the distance from the flange of the box to the torque converter. We write it down and compare it with the manual.
2. Remove the torque converter and put it with the hole down for a couple of days in a ditch.
3. Remove the mode switch (PNP-switch).
4. Close the connectors.
5. We wash the box from dirt, otherwise it will later serve as a source of dirt.
6. Unscrew the pallet bolts and put them in a separate box (the manual insists on replacing them, I did not change)
7. Remove the pallet.
The magnets are in sawdust, there are no pieces of iron in the pallet.
8. We wash the pallet and magnets, wipe and put in a clean bag.
View of the inside of a box without a pallet.
9. Remove the latch from the external connector and push it inward.
The picture shows the solenoids. The line pressure solenoid stands alone (left side of figure). A red wire with white stripes goes to it.
10. Remove the Control Valve Assembly or brains. The manual has a very good drawing of which bolts to unscrew. We put them separately. Having a specification is impossible to confuse. A = 40 mm (5 pcs.), B = 33 mm (6 pcs.), C = 43.5 mm (2 pcs.) See page AT-515.
It is slightly visible in the photo that the filter is clogged.
11. Remove the bell, take out the differential and remove it if there are no questions to it (as in my case).
12. Remove the oil pump. Then we will revise it.
13. Remove the brake band. I measured the distance of the adjustment bolt. 14mm. As it turned out later, the adjustment of this unit is made by tightening the bolt (Anchor end pin) with a torque of 3.5-5.8 Nm and then unscrewing it by 2.5 ± 0.125 turns. The nut is locked with a torque of 31-36 Nm. See page AT520. We insert a bracket into the holes of the brake band (there is a drawing in the manual) in order to prevent it from straightening.
Next, we sequentially disassemble the box. We add the nodes in the order of parsing. Be careful not to drop the thrust bearings.
Retaining rings are easy to remove.Pry off with a screwdriver and carefully take out.
So, we reach the very bottom of the box. And we see the hero of the occasion. The reverse brake package is worn out nowhere else. Only the last (closest to us) friction plate remained alive (if I may say so, since there are only traces of friction material). All other clutches and all the hardware are just in the trash.
Reverse brake piston. Wear is visible on one of the edges. The D-ring (inner) was destroyed, which was the cause of the breakdown.
Place of installation of the reverse gear brake (the very depths of the box).
Part 3. Troubleshooting / disassembly of units / assembly.
Material support of the 3rd stage:
- Manual. REPAIR FOR COMPONENT PARTS, ASSEMBLY, SERVICE DATA AND SPECIFICATIONS (SDS).
- Compressor.
- Tool see part 2.
- Torque wrench 5-25 Nm.
- Lint-free rags.
- ATF (any at this stage).
- Petroleum jelly (well, in our opinion - petroleum jelly).
We proceed to troubleshooting the box assemblies. We disassemble all the clutch assemblies one by one (or as they are called in the manual, the clutch, i.e. clutch). They are disassembled quite simply (remove the retaining rings).
The result of troubleshooting: All clutches except for the reverse gear are in satisfactory condition (wear of some 0.1 mm on the clutch) in the tolerance, of course, but if you add it up, it turns out not so little.
Solution: Replacing all clutches of all gears + iron on the reverse gear brake + a new piston.
Purchased spare parts:
1. Precision Gasket Kit.
2. Friction clutches (I didn't take the kit, didn't like it, pure China and, as it seemed to me, there were differences in size.) They were assembled separately.
3. Used piston.
4. Brake band (did not install later, because the native is better).
5. Iron (driven plate) brake reverse gear.
A little about the order of work. I started disassembling clutch packs after purchasing spare parts. I advise. You will definitely not confuse anything, and there are a lot of details.
By assembly. Large packages are easy to assemble, but small ones, for example High clutch, are difficult to assemble without tools. But you can.
We disassemble, wash, change all rubber bands and friction clutches and assemble.
I advise you to follow the manual clearly and point by point. Written and drawn clearly enough. Be careful with the installation of the spring rings (dish plate). Install incorrectly - will not reassemble the assembly. Be sure to control the clearances.
Oil pump. In admission. We wash, change the gaskets, collect.
Brake band drive. A compressor is needed for parsing. We wash, change the seals, collect. It was fun here. They were assembled by installing the box on a lathe with a retractable quill of the tailstock J. Otherwise, I did not succeed. The effort is good. The puller was slipping.
So. All packages are sorted out, the brake band drive is assembled.
We replace the oil seals of the drive shafts.
Brainwash J
Carefully according to the manual (p. АТ439-АТ453). Condition before flushing:
In general, quite satisfactory, but ... Pay attention to the filter. It is not so easy to rinse it, but it is necessary. Carefully, it is possible in several stages and it is better in the container.
Carefully with balls and springs. The above kit includes balls. The places of their installation in the manual are indicated exactly.
The gaskets were so well adhered to the metal plates that I decided not to change them, because it is very difficult to remove them from the plates, you can scratch the plates.
As for the valves. Maybe I was wrong, but I could not get everything. Accordingly, their performance and flushing of the spray gun with 6 atm kerosene were tested. Everything moves and works. Be sure to check the spring of the 1-2 switching accumulator.
Spring sizes are listed in the specifications on the last pages of the (SDS) section. We check carefully.
We collect.
There are several points here. It is necessary to pay attention to the installation of bolts F. They are installed in reverse. I rearranged it later. And it's good, because overtightened when installing the solenoid block.
Tighten the bolts only with a torque wrench to specification.
One more point.Check the line pressure solenoid for mesh cleanliness and condition.
Ring all solenoids. The resistance values are indicated in the specification. Put new rubber bands on the solenoids.
Brains are collected.
I did not remove the back cover. In my case, I did not see much sense. If there are doubts about the bearings, then it is better to dismantle and defect this unit.
The shift shaft (manual shaft) was not removed.
Let's start assembling the box.
We consistently and accurately assemble clutch packs, planetary gears, etc. The drawings in the manual are quite detailed.
[b] Take a close look at the top figure on page AT504. I remembered, probably, the mother of every Japanese and not very engineer who wrote the instructions, because by this moment everything is already assembled. [b]
We put on the brake band and adjust (see removal of item 13 and manual page AT520).
The last to be installed is the oil pump. Don't forget the seals.
We put the differential.
We put the body (bell) on the sealant. We tighten the bolts.
Install the N-D and servo pistons. Install 3 O-rings, install the solenoid connector in the box, install the brains.
We put a new gasket and install the pallet. We tighten the plug.
We put the torque converter and check the size from the end of the box (bell) to the torque converter.
Installing the box in the reverse order of removal.
After installation, fill in the oil. Gradually. First up to the level. We start the engine. We run the modes. Top up. We look at the leaks.
The first week - check the oil level every day on the hot box. Top up if necessary.
[b] Total for money: [b]
Gaskets 3600 r.
Clutches 3500 rub.
Used piston 1050 rub.
Reverse gear brake plates 5x180r / pc.
Brake band 1300 (not needed).
Total spare parts: 10350r.
Oil Nissan Matic D 2х4l = 4200r.
Torque wrench 5-25 Nm - 1200 rubles.
Add. expenses 2500 p.
Total with overhead costs and a tool of about 18 tr.
The report is rather modest in terms of technical details. The main thing is in the manual. Unfortunately, the photos are from the phone.
PS. While the box was removed, I replaced the steering rack oil seal. Very comfortably.
AlexVF thanks for the detailed report.
Moroz
4-speed automatic transmission RE4F04A A flawless front-wheel drive layout was developed by Jatco in 1993 for the 3-liter Maxima, using the experience of the JF403E gearbox made in 1990 for Isuzu.
Later they began to put it on other popular cars Nissan and Infiniti with engines up to 3 liters. At the same time, a modification was released for a lower torque from engines up to 2 liters - RE4F03A... Until 1995, the JF403E modification was produced for Isuzu and other manufacturers. (Read what the letters and numbers in the box name mean on the page RE4F03A.)
The JF403E modification adapted for Mazda Millenia was called in Mazda: LJ4A-EL and was installed in parallel with the "old lady" GF4A-EL from 1995 to 2003. This workhorse also met on rare "Americans" under the Ford name 4F20E.
This family of 4-speed automatic transmissions is used on front-wheel drive vehicles with engines from 2 to 3 liters. Masters call it "04th Nissan", which is rightfully considered a success Jatco by combination: reliability / price. Competitors - aisinovskaya A540, which could not hold out for a long time and gave way to 5 (and 6) speed automatic machines, Ford CD4E, and GM 4T65E... But these boxes lag significantly behind the Jatka bestseller in many ways.
2000 to 2003 several modifications were reissued with the letter "B" - RE4F04B, for more powerful engines (Infiniti, Murano up to 3.5 liters), and then “V” - RE4F04V, but the super-reliable and heavy 4-speed Jatko gearboxes were soon considered “morally obsolete” and from 2006 this family was gradually changed to variators.
Pick up repair kits - press the button on the left.
Filters are typically Dzhatkov for 4-speed automatic machines, metal with an open mesh, which do not require replacement for many years, if you do not allow accidentally burnt oil.
Until 2003, they had a 10 mm intake (No. 315010), and after 2003, a variant with a deep pan appeared - a 34 mm intake (# 315010A).
The filter is rarely changed, often washed, even when Jatko recommends changing it (burnt oil). Instead of replacing the coarse filter, an additional main external fine filter (below).
The clutches in boxes operated in burnt oil are also changed with the whole set - 315003. Friction kits are also different for boxes before and after 2000 according to the diameter of the Reverse clutch. Until 2002 (at some assembly plants) discs Ø139mm were produced, and since 2000 they switched to reinforced discs with an outer diameter of 147mm (the inner one is the same). It is determined only when disassembling the automatic transmission.
The Master Kit kit includes the entire set of gaskets, oil seals, clutches and steel discs (except for the brake band) - 315007.
The most popular Nissan box in repair, which is called “4th Nissan” in professional slang.
Typical repairs of age automatic transmissions RE4F04 LJ4A-EL:
In addition to the usual set of consumables for the age machine bulkhead, mentioned above, the torque converter lock-up friction lining must be replaced. With powerful engines, Jatko's torque converter eats up its clutch first. The blockage, eaten away to glue, clogs the valve body and gives strong vibrations to the pump shaft, killing both the pump oil seal and the pump itself. The first sign of a running torque converter is a leaking oil seal.
Torque converter repair (order) - 315001.
It changes with the replacement of the clutches of the High package - 315106A. Craftsmen prefer Original Ribbon - Borg Warner, on right.
For LJ4A-EL and JF403E - old brake band ( narrow, since 1990 ) No. 310020A and your filter No. 310010A.
All clutches are replaced with a set, if the machine came for repair with burnt oil: No. 315003.
The clutches of the second generation (since 2000) have been changed, the diameter (147 mm) of the clutches of the weak Reverse package has been increased - 315110.
It is rare when ordering a set of steel discs - 315004.
Then the vibrations break the rest of the bushings along the chain. Change the entire set of 10 bimetallic bushings - No. 315030.
If you continue to kill the pump further, then. see Reconditioned Oil Pump - No. 315500.
A typical problem node of this machine:
- Rear planetary row, (Rear Planet) - No. 315584.
the splines are cut off. Occurs at high mileage aggregated with an engine with maximum torque.
Another popular repair location is replacing the Solenoid Kit RE4F04 № 315420 .
For Maxima (. 04B) in 2000, a new block of solenoids was released. Like the valve body for powerful engines since 2000 - its own.
For Mazda LJ4A-EL - its own set of solenoids, as well as for JF403E.
Of the clutch packs, two are leading by a wide margin in terms of consumables burning: - High Clutch -No. 315106) and - package Forward Clutch (315108).
Steel disc High [28Tx1.4 × 91.7] - No. 315126A - the leader in replacements, burns out together with the thrust disc. If the oil smells like burnt, these discs have to be replaced.
Even thrifty owners change a pair of friction clutches of the Reverse package - No. 315110. The rest of the packages have a slightly larger resource. And they can hold out until they start turning on the jerk and bump packs.
But with burnt oil from the blue discs of the High package, the masters recommend changing the full set of clutches - 315003. If you start the problem, then you have to change the High drum - # 315555.
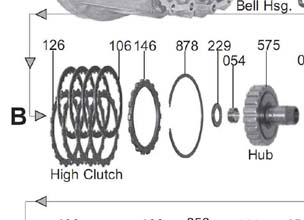
- Drum (Reverse) No. 315556, tears off the splines, especially in modifications RE4F04B since 2000.
In general, the "iron" of this box has a large supply, allows drivers a lot and breaks down only when the pallet already contains a lot of metal chips and shavings. With the timely repair of the torque converter and keeping the oil clean and unheated, this gearbox goes up to incredible mileage.
The inline filter helps keep the oil clean and reduces friction wear. This is recommended for all machines that have a standard filter with a metal mesh.
In addition to finely dispersed dust from the clutches, such a filter also retains the adhesive base of the clutches, in the case when the lining is erased to the very base. That protects the solenoids and valve body valves from hanging and wear.
Also, this filter has a magnet that retains iron dust from the planet's gears and a bypass valve, which is triggered if the filter has not been changed for many years and it is completely clogged with dirt. The outer filter should be checked and changed every year or every 10-20 tkm, depending on driving style. More details - here.
Leaving the oil out of the box through the oil seals can lead to big trouble. Therefore, if the craftsmen do not order a complete repair kit for gaskets and oil seals, then they always change the pump oil seals and axle shafts, if the box has come into overhaul for the second time with the same problem. (Replacing solenoids and not repairing the torque converter is a common mistake of economical owners).
- The valve body is often simply repaired and cleaned.
- One way clutch separator (No. 315642),
All these fairly reliable nodes develop their resource with the help of forgetful owners.
Manual for RE4R04A the tightening torques for the bolts can be found here.
The cost and availability of the items you need can be checked in the online store by clicking the number on an orange background to search for a part. A complete list of parts is below.
On which cars this automatic transmission family was installed:
Repair of any automatic transmission from 1 day
CVTs, DSG, torque converters, new and remanufactured automatic transmissions, spare parts
Well, here it is clear what the conversation is about.
# 1 Post miha Feb 14, 2008 2:16 pm
I have an automatic transmission from Presage of the RE4F04B brand (six months ago I shook mine by changing the oil in the Nissan SC.Yes, yes, they are goats)
when installing the boule, incompatibility problems (the solenoid connector did not fit, the output shaft speed sensor connector, and the torque converter bagel)
the solenoid wires matched the color, there were no problems with this, the bagel left the old one, but here's the problem:
I can’t combine the speed sensor, Presage has two wires, RNessa has three wires, I tried to stick my sensor into the press (it fits in the seat), one fig auto-computer swears at it (flashes when the ignition is turned on), I tried to connect the sensor from the press to the two wires of the Rneski connector (one remained superfluous), it seems that something has changed in motion, but the auto-computer continues to swear, but I would have resigned myself to this glitch, if not for a problem while driving
at a speed of 80 - 110 km / h at medium speeds, the torque converter lock-up starts to cycle on / off, and as a result, a slight twitching with a rhythm of 3 seconds is felt.
in general, I understand that such a question is for the specialists, for them and an offer, if anyone can help solve this glitch, I will be glad to pay for help (from 3000 rubles and above)
_________________
PNN30 / KA24 / RE4F04B / 4WD / 2000 / Project 170t.km / HBO LOVATO /
# 2 Post miha Feb 14, 2008 2:18 pm
# 3 Post yurik 09-03-07, 09:16
# 4 Post miha Feb 14, 2008 8:12 pm
Yurik thanks for the answer
I came to the conclusion about the nature of the malfunction after self-diagnosis of the automatic transmission according to the manual. & thiscat = 3
when I put my own sensor, the automatic transmission control unit of course perceived it and did not show errors, but now my sensor from the old automatic transmission seems to be faulty (I rang the manual, there is no set 500-600 ohm between 1 and the second contact)
and it looks like it burned down after installing it in a press box.
possibly a different exciter disc of the sensor, or a different gap between them.
now there are several options from inexpensive solutions
1.replacement of the automatic transmission control unit with PRESSAZHEVsky
2.replacement of the driven shaft speed sensor and the exciter disk located on the driven shaft with Rnesovsky
3.creation of a logical converter that will receive readings from the press sensor and convert them into suitable for the Rneskov automatic transmission unit
4.and of course, if you're lucky, then just installing a new native ERNESK sensor with adjusting the gap between it and the disk to the required signal level (but this is provided that the intestines in the area of the secondary shaft turn out to be the same in the boxes)
if anyone sees another solution to the problem, please tell me
and IF WHO HAS A SCHEME FOR INCLUDING THE AUTOMATIC TRANSMISSION CONTROL UNIT ON A / M PRESS, please give a scan of this page, see if it is possible to stick brains from the press.
# 5 Post yurik Feb 15, 2008 9:02 pm
# 6 Post miha Feb 15, 2008 9:46 pm
![]() |
Video (click to play). |
# 7 Post miha Sat Feb 16, 2008 11:34 am