In detail: do-it-yourself rolling board for car repair from a real master for the site my.housecope.com.
Hello everyone, now the time has come when I decided to make myself a lounger to "drive in" under the car, before that I just used a piece of penoplex. The size of my roll-up lounger was 50 centimeters per meter.
The boards were taken from an old barn. I also used a 20mm x 20mm pipe and 50mm wheels. He collected and cooked slowly, though there is really nothing special to cook here.
I am satisfied with my creation, since now it has become much more convenient to drive under the car. But you just need to come up with something to do under your head, for example, a rise with adjustment. Well, that seems to be all, there is nothing special to describe, everything else is clearly visible from the photographs.
Hello everyone. The idea to make a rolling lounger for car repair crept into my head a long time ago. Since I do not have a viewing hole in the garage, I decided to make a sunbed for car repairs. Prices for sun loungers in the store are very high, it is better to do it yourself.
The main, if not the most important, are the wheels. Wheels can be bought in any construction market.
wheels for rolling lounger
rolling lounger wheel
In total, we will need 6 pieces. Next, you need a metal profile 20x20 mm, wall thickness 1.5 mm. In total, you need 4.5 meters of a square pipe. Cut like this:
square tube for lounger 20x20
2 segments of 1 meter 4 segments of 0.5 meters
The remaining profile was cut by fitting, relying on the height of the wheel, and, of course, drilled the holes.
movable repair lounger
After assembly, I cleaned up a little and covered everything with enamel for rust and primed the profile.
sliding lounger for car service
![]() |
Video (click to play). |
movable sunbed for car repair
trolley bed for car repair
It is still cold here, and therefore instead of days, as written in the instructions, it dried for a week.
Then I cut out 10 mm from plywood. sunbed, varnished (varnish-amber like):
sliding loungers for car repair shops
Marked the holes, drilled and screwed on.
movable sunbed + for car repair + do it yourself
do-it-yourself roll-up lounger for car repair
I tried to ride on my floor, but, as you can see, it is not very even, but it rolls quite easily, only a little harsh. It was decided to make it softer. He took the insulation, one can say what came to hand, and nailed it straight to the board with a stapler, only then I remembered that I have other material, but it’s fine with this, it turns out, it keeps warm, my back is not cold. Here's what happened =)
Sun loungers and repair seats irreplaceable when servicing a car in a garage, workshop or service station. They significantly simplify access to units and parts, allow the master to take a comfortable position and work for a long time without getting tired.
Sun beds are used when it is necessary to inspect and repair a car while under it, but there is no way to drive it into a pit or lift it on a car lift. Then the machine is jacked up and placed on supports. The repair lounger used by the master consists of a metal frame with a length of about the height of a person. The base is usually made of plastic, in some models it is covered with a soft material with oil-petrol-resistant casing. On one side of the roll-up bed there is a head-back, which can be adjusted for the most comfortable head position. Wheels (from 4 to 6 pieces) are fixed on the frame, so it is easy to roll under the car on a sunbed. There are products with a folding structure that can be transformed into a repair seat. This is a great option for garage use.
The seat is useful when straightening car body parts, when dismantling parts, when you need to unscrew a lot of fasteners and other work in which it is inconvenient to work while standing. The durable seat structure provides stability, while the soft padding adds comfort during extended periods of work. Also, the design of the repair seat can be provided with a drawer for tools and fasteners, as well as wheels for quick movement, for example, from a car service area to a workbench. The most convenient models are with a microlift, which allows you to change the height of the seat position, depending on the height of the user.
Timely and high-quality technical maintenance of fire fighting equipment is the most important element of its operation and must ensure: constant readiness of equipment for use; the safety of its use; elimination of the causes of premature wear, aging, destruction, malfunctions and breakdowns of components and mechanisms; reliable operation of equipment during the established overhaul resources and their service life before repair and write-off; minimum consumption of fuel, lubricants and other operating materials.
Car maintenance should be carried out according to the so-called scheduled preventive system. The peculiarity of this system lies in the fact that all cars undergo scheduled maintenance without fail. The main purpose of maintenance is to prevent failures and malfunctions, prevent premature wear of parts, timely repair damage that impedes the normal operation of the car. Thus, maintenance is a preventive measure.
As you know, repair is a set of specific operations to restore the working condition of vehicles and equipment to ensure their trouble-free operation. It can be performed on demand or after a certain mileage. Repairs associated with disassembly or replacement of units and assemblies are carried out according to the results of preliminary diagnostics.
To perform a number of maintenance work, special equipment and accessories are required to make the work more efficient.
One of these devices, included in the list of equipment for specialized enterprises and service stations for fire trucks, are movable sun loungers. With them, work on the repair of a fire engine becomes, if not easier, then at least more convenient.
Usually a repair lounger is made of a metal frame. Its length is about human height. The base is made of durable plastic, some models are covered with soft material. Additionally, oil-petrol-resistant casing is made to exclude fire in contact with gasoline and oil. In most cases, the rolling bed has six wheels, although there are models with four wheels. The chassis rotates in a circular manner, which gives more freedom of movement. Loungers are made with a comfortable headboard, which has adjustments to adjust the optimal comfortable head position, but models are also used that have a folding structure that transforms into a seat - this option is used for working in the garage. There are also repair seats that are used when straightening car body parts, when dismantling parts, when you have to unscrew a lot of fasteners, since it is extremely inconvenient to do this while standing. Wheels allow you to quickly move around the site without getting up from the seat.
The variety of designs offered on the market for sun loungers is very wide, the main ones are shown in Figures 1 - 3.

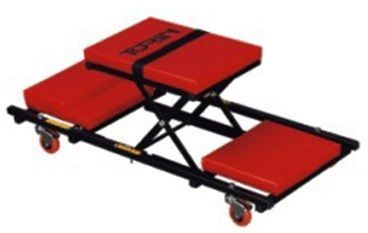
On the lounger, the specialist can diagnose and repair the car, located directly under the bottom of the car. The car mechanic's rolling bed is used when it is impossible to drive the car into a pit or lift it on a lift. The loungers are designed to provide comfort to all parts of the body during long-term work. On top of the roll-up bed is a soft headrest that can be adjusted for a more comfortable head position. The frame is equipped with wheels (from 4 to 6 pieces), which makes it easy for the master to work on the sunbed under the car.
Nevertheless, the disadvantage of existing sun lounger devices used for repair and maintenance of fire fighting equipment is that the loungers are not adjustable in height, which significantly reduces the list of repair operations that can be performed without using a viewing hole or a car lift.
The authors have developed the design of a sliding bed with adjustable lifting height (Fig. 4), and also performed the necessary calculations.
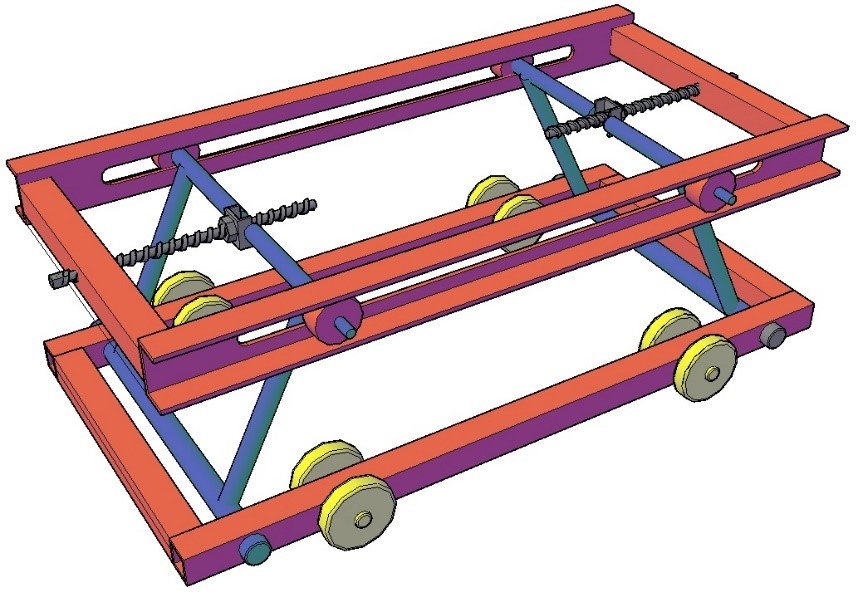
The lounger is a welded structure mounted on rollers that allow the locksmith to move under the car. The structural elements are square pipe 40x3 GOST 8639-68 and channel 5U GOST 8240-97. The upper and lower platforms of the power structure of the lounger are also connected by square pipes, but of a smaller section of 30x2. The lifting height adjustment mechanism is shown in fig. 5.
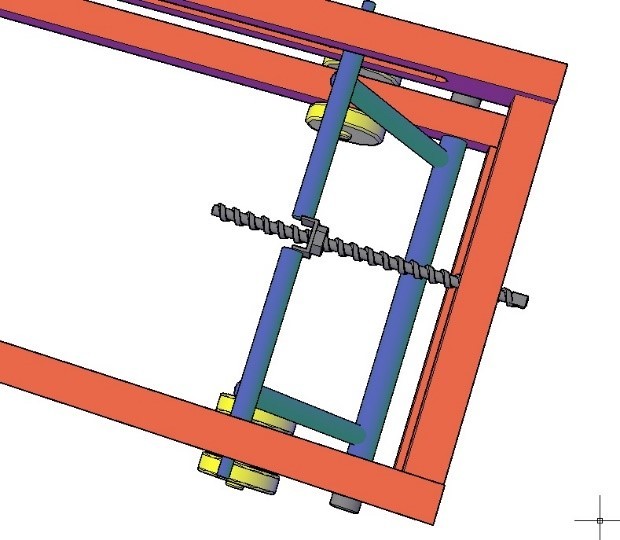
The lifting of the upper platform of the lounger can be adjusted on both sides by means of a screw-nut transfer. Rotation of the screw handle allows the rollers to move, installed in the inner cavities of the channels of the upper platform, thus providing an adjustment of the lifting height. The designed device can provide both horizontal lifting of the lounger and the lifting of one of its sides. This method of adjustment will provide better ergonomics and will facilitate better access to vehicle components and parts.
Timely and high-quality technical maintenance of fire fighting equipment is the most important element of its operation and must ensure: constant readiness of equipment for use; the safety of its use; elimination of the causes of premature wear, aging, destruction, malfunctions and breakdowns of components and mechanisms; reliable operation of equipment during the established overhaul resources and their service life before repair and write-off; minimum consumption of fuel, lubricants and other operating materials.
Car maintenance should be carried out according to the so-called scheduled preventive system. The peculiarity of this system lies in the fact that all cars undergo scheduled maintenance without fail. The main purpose of maintenance is to prevent failures and malfunctions, prevent premature wear of parts, timely repair damage that impedes the normal operation of the car. Thus, maintenance is a preventive measure.
As you know, repair is a set of specific operations to restore the working condition of vehicles and equipment to ensure their trouble-free operation. It can be performed on demand or after a certain mileage. Repairs associated with disassembly or replacement of units and assemblies are carried out according to the results of preliminary diagnostics.
To perform a number of maintenance work, special equipment and accessories are required to make the work more efficient.
One of these devices, included in the list of equipment for specialized enterprises and service stations for fire trucks, are movable sun loungers.With them, work on the repair of a fire engine becomes, if not easier, then at least more convenient.
Usually a repair lounger is made of a metal frame. Its length is about human height. The base is made of durable plastic, some models are covered with soft material. Additionally, oil-petrol-resistant casing is made to exclude fire in contact with gasoline and oil. In most cases, the rolling bed has six wheels, although there are models with four wheels. The chassis rotates in a circular manner, which gives more freedom of movement. Loungers are made with a comfortable headboard, which has adjustments to adjust the optimal comfortable head position, but models are also used that have a folding structure that transforms into a seat - this option is used for working in the garage. There are also repair seats that are used when straightening car body parts, when dismantling parts, when you have to unscrew a lot of fasteners, since it is extremely inconvenient to do this while standing. Wheels allow you to quickly move around the site without getting up from the seat.
The variety of designs offered on the market for sun loungers is very wide, the main ones are shown in Figures 1 - 3.
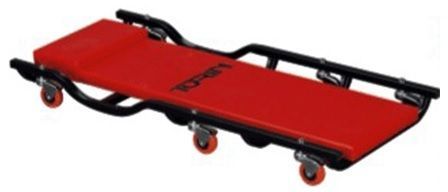

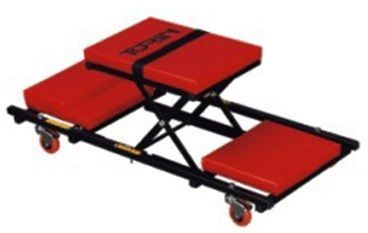
On the lounger, the specialist can diagnose and repair the car, located directly under the bottom of the car. The car mechanic's rolling bed is used when it is impossible to drive the car into a pit or lift it on a lift. The loungers are designed to provide comfort to all parts of the body during long-term work. On top of the roll-up bed is a soft headrest that can be adjusted for a more comfortable head position. The frame is equipped with wheels (from 4 to 6 pieces), which makes it easy for the master to work on the sunbed under the car.
Nevertheless, the disadvantage of existing devices of sun loungers used for repair and maintenance of fire fighting equipment is that the loungers are not adjustable in height, which significantly reduces the list of repair operations that can be performed without using a viewing hole or a car lift.
The authors have developed the design of a sliding bed with adjustable lifting height (Fig. 4), and also performed the necessary calculations.
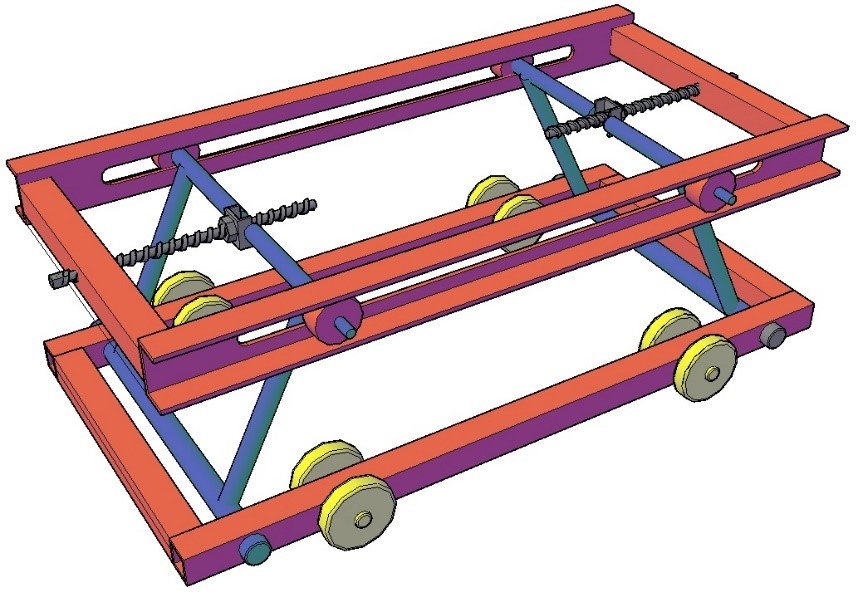
The lounger is a welded structure mounted on rollers that allow the locksmith to move under the car. The structural elements are square pipe 40x3 GOST 8639-68 and channel 5U GOST 8240-97. The upper and lower platforms of the power structure of the lounger are also connected by square pipes, but with a smaller section of 30x2. The lifting height adjustment mechanism is shown in fig. 5.
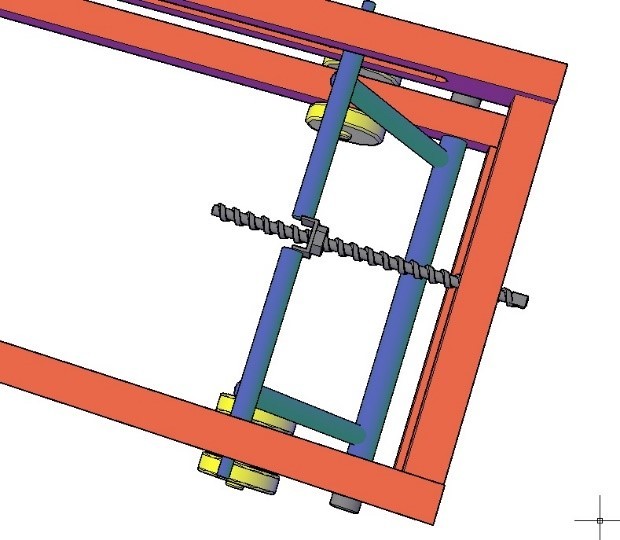
The lifting of the upper platform of the lounger can be adjusted on both sides by means of a screw-nut transfer. Rotation of the screw handle allows the rollers to move, installed in the inner cavities of the channels of the upper platform, thus providing an adjustment of the lifting height. The designed device can provide both horizontal lifting of the lounger and the lifting of one of its sides. This method of adjustment will provide better ergonomics and will facilitate better access to vehicle components and parts.
Homemade trolley jack with your own hands: blueprints, photo, video review of homemade products.
We bring to your attention a home-made hydraulic rolling jack for servicing a car.
For the manufacture of homemade products, a bottle jack with a pick-up height of 23 cm, a channel of 10 and 12 mm was used. A stand was made from the 12th channel, the base and the lifting arm were made from the 10th channel.The bottle jack swing is made from a 12th channel.
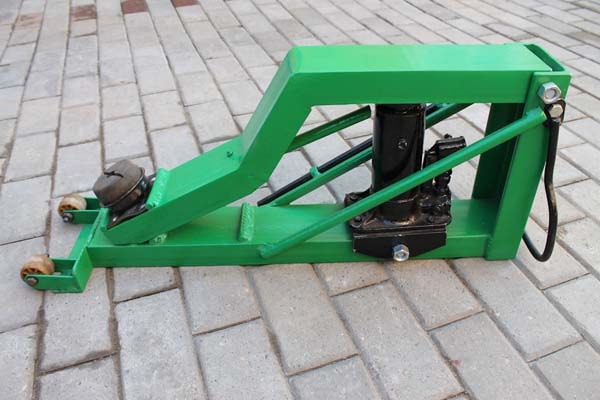
There are rollers from the washing machine in front. The cup is taken from a car bump stop.
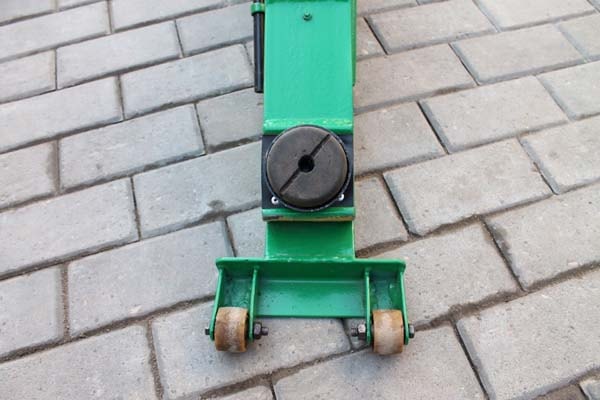
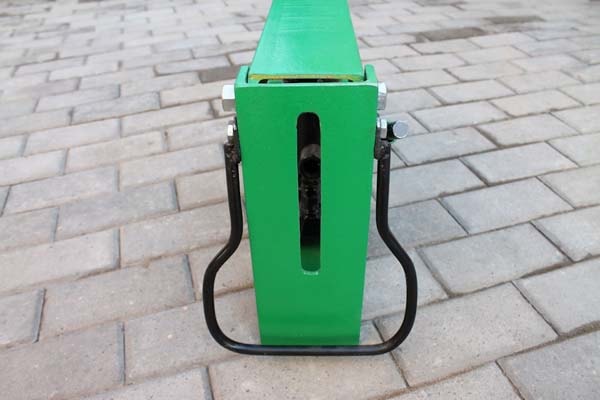
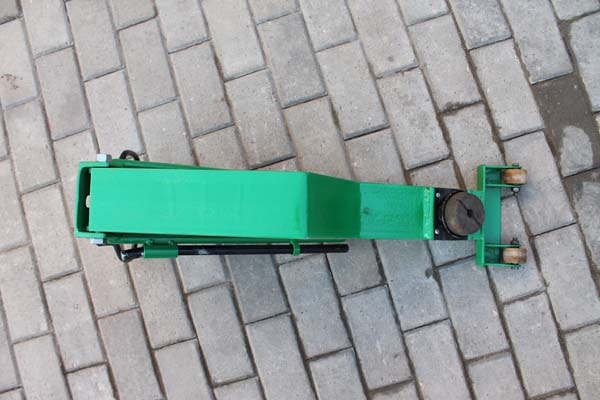
The braces are made from a 20 mm bar.
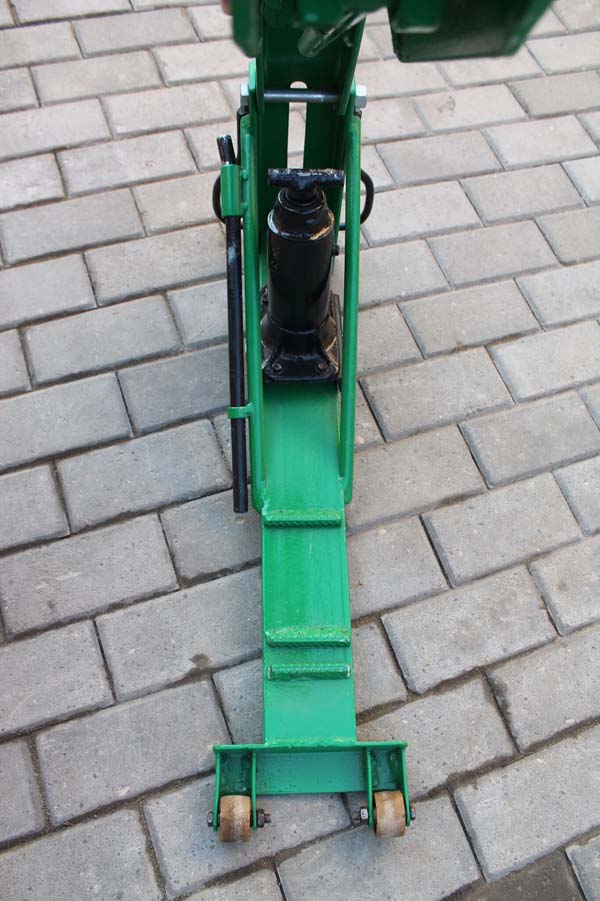
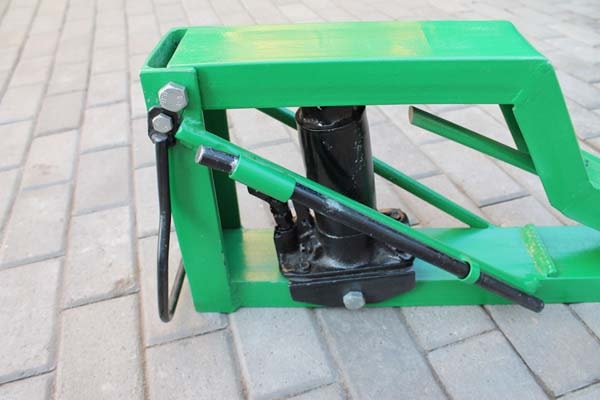
Drawings of a rolling jack for self-production.
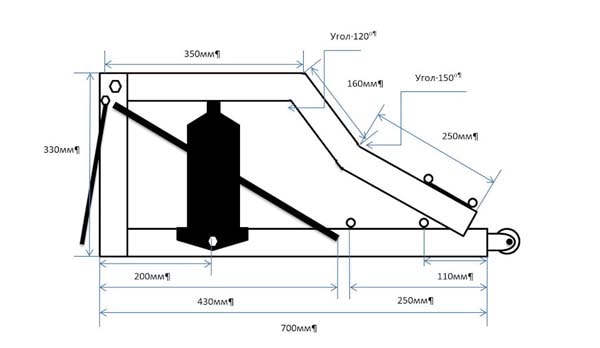
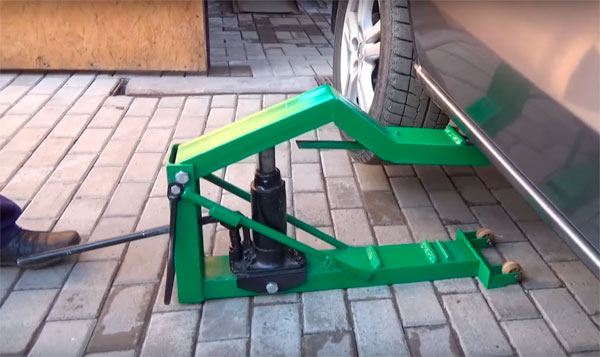
In this video, the author demonstrates the work of his homemade rolling jack.
Sometimes it is not possible to drive the car into a hole in order to start repairing or replacing parts located under the bottom. For such cases, it is good to have a tipper for a car in the garage, which is not at all difficult to do with your own hands. It is manufactured by welding, from sheet iron and a square metal profile. The design is very simple, both in installation and in operation. This article describes the mechanism, how to assemble and use it.
Automotive tipper for a car, a drawing, video and photo of which are presented below, it works by means of a jack:
You can take any lift that you can find in the garage. The maximum possible angle of safe lifting of the side of the machine is 45 degrees.
The heel for the jack should have as many stiffening ribs as possible, which will give it additional strength. This is an important point, since the part during the operation of the tipper moves along the rail, experiencing loads in the region of 2.5 tons. The heel is made of sheet metal (5 - 7 mm).
We make a tipper for a car with our own hands: a drawing of the structure described below
The same applies to the platform, which will rest against the bottom of the car - we make more stiffeners, we use metal with a thickness of 5 - 7 mm. Additionally, you will need a metal corner and a square profile. The bottom platform, support angle and support beam are made from the same profile.
The bottom platform is a fixed piece made of one metal profile that will lie on the ground. The support angle consists of two elements connected by short sections of the metal profile and moves up and down along the guide rail. The latter has a number of holes for fixing the tipper at the desired angle.
Bottom platform and support angle assembly
The row of holes that you see on the sides of the support angle serves to fix the platform on which the bottom of the machine will rest. During lifting / lowering of the car, it moves along the part in one direction or another. At the highest point, when the ascent is over, the platform is fixed with a bolt. The platform and the support corner are fastened with a bolt.
We stretch the support platform of the tipper for the car with our own hands under the bottom of the car. In this case, we place the place of fixing the heel for the jack on the side that should be raised. We introduce a support corner on top and fasten it to the platform with a bolt. Next, we assemble and insert the support beam into the device. First, remove the caps from the wheels to which it will fit.
The heel for the jack is inserted between the platform and the support corner, then a rail is vertically inserted through all three parts, which has a number of through holes. It serves as a guide and retainer for the top of the inverter. The lower end of the rail is screwed to the platform with a bolt. The sections of the profiles of the support angle, along which the platform will move, are lubricated with grease and only then we install it, moving it under the bottom of the car.
Next, attach a jack to the tipper and start lifting. After the desired height is reached, a cotter pin is inserted into the vertical rail through the hole located directly under the support angle. He will not let the car fall if something happens to the jack. The following video describes in detail how to install a homemade tipper for a car with your own hands.
Car repair is a serious and responsible job that requires certain knowledge and skills. There are operations that a beginner can handle as well.But many types of repairs require serious experience and some preparation.
However, any car repair specialist was once a beginner - each of us once did even the most familiar work for the first time.
Therefore, if you are determined to master the ability to repair a car with your own hands, do not be afraid to start. Learn, be attentive, pay attention to every little thing, and after a while you will acquire all the necessary skills.
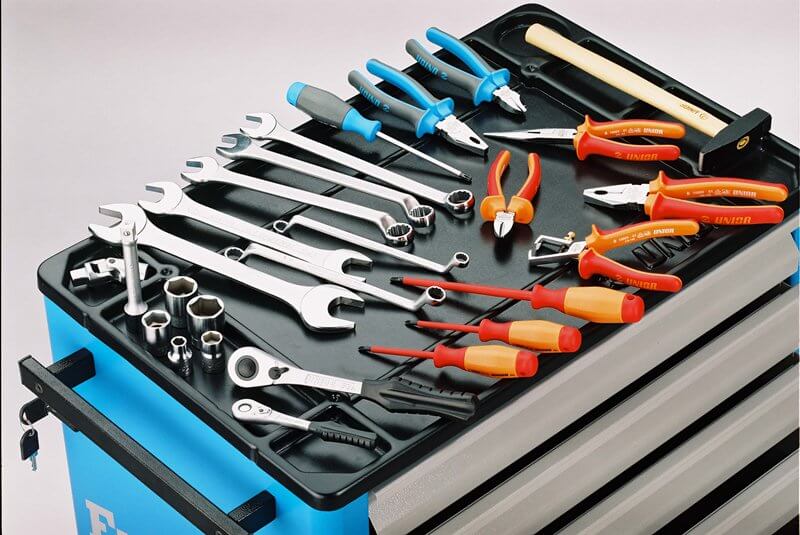
You will also need a special tool for auto repair - as you understand, it is impossible to do without it.
To do many work with your own hands, you will need various tools and materials - with their help, fixing of units, assembly and disassembly, operations to eliminate defects, etc. will be carried out.
Let's figure out what special tools and accessories you may need during do-it-yourself car repairs.
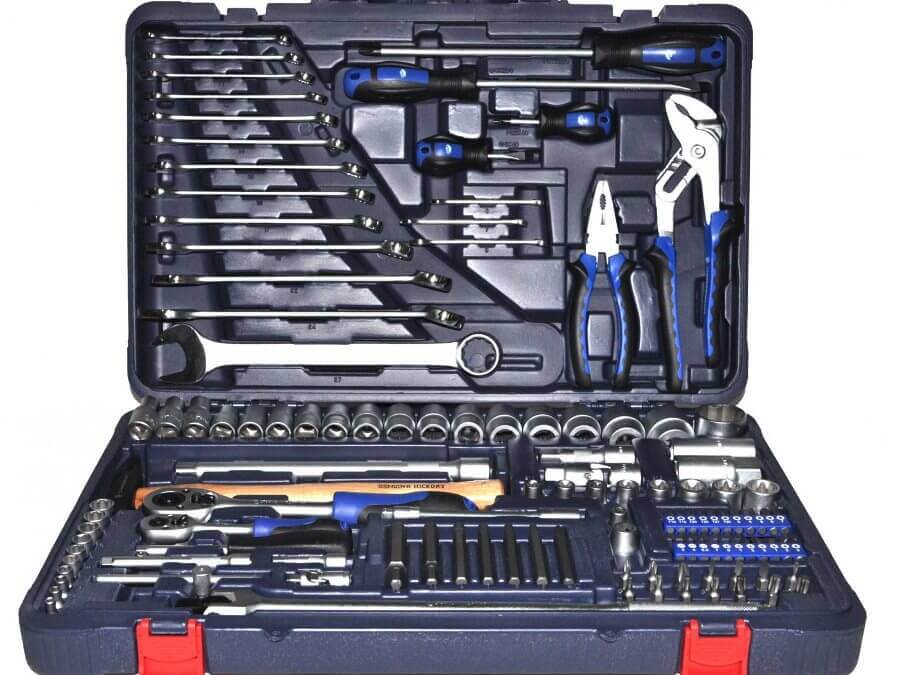
To begin with, consider the standard set of tools that you will need not only to have in the garage, but also to carry with you. Situations happen different - it happens that a breakdown forces you to work with your hands right on the spot, making it impossible to reach the garage. For this purpose, you must have the following special set with you:
- Screwdrivers - any work with the machine rarely does without them. You will need two flavors:
- with a slot;
- with a cruciform tip.
Since you may need different sizes, it is best to carry a universal screwdriver with different types of bits.
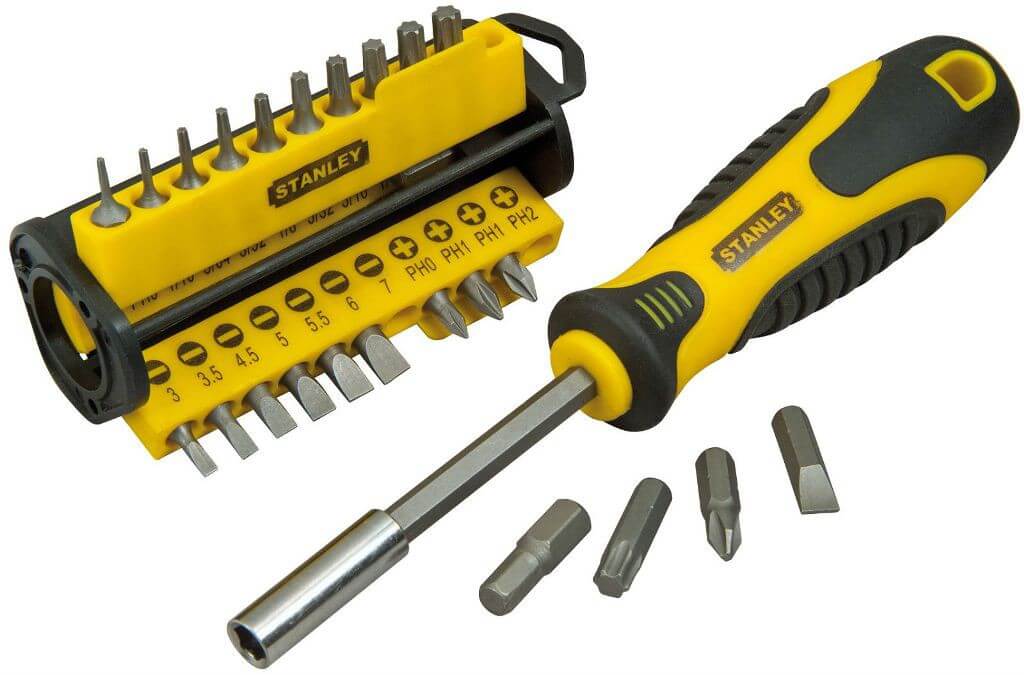
- Adjustable wrench - it may be needed when the force of the pliers is not enough to unscrew a stubborn bolt;
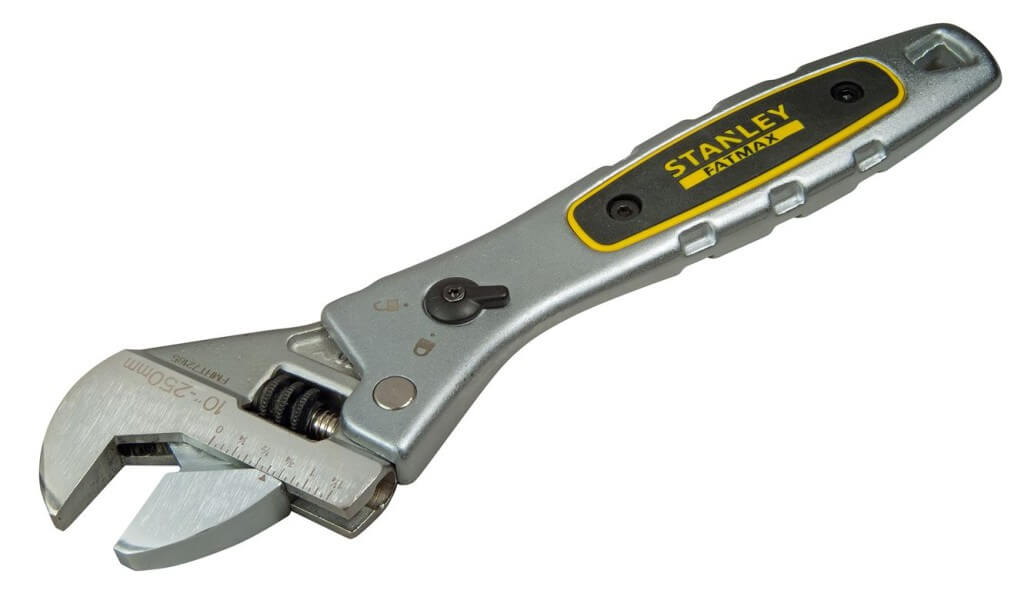
- Jack - will be needed in order to raise the car or hold it, for example, when changing a wheel. There are 3 popular jack types:
- screw;
- rack and pinion;
- pneumatic.
The screw jack is considered to be the most convenient - it is compact and efficient.
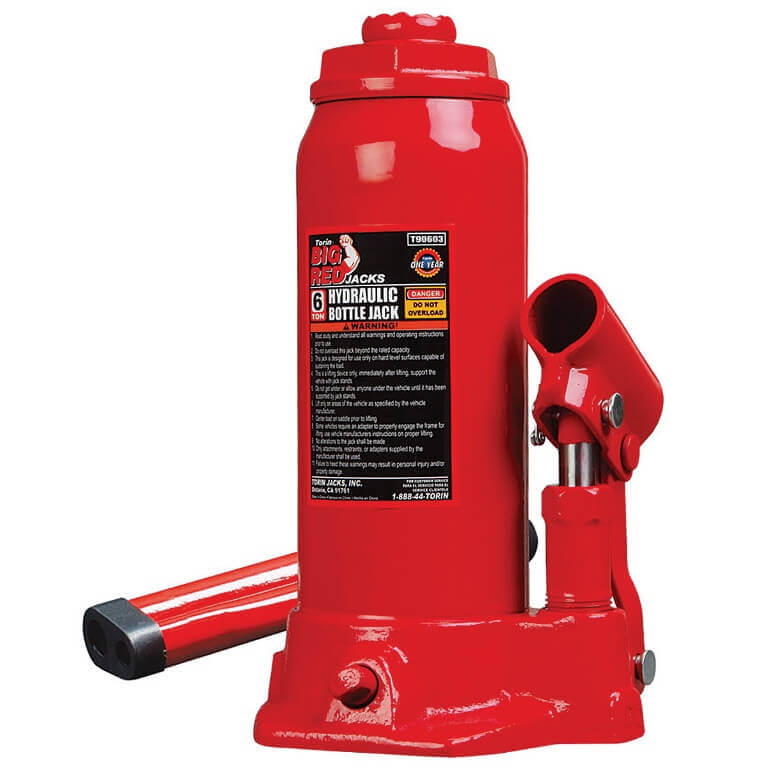
- Socket wrenches for unscrewing the heads. They can have 6-sided and 12-sided heads.
- A set of spanner wrenches. There should be as much as possible. The car has a huge number of different nuts, so such a set will be extremely necessary for you.
- Several hammers of different sizes. A light hammer is used to knock out bolts, nuts and studs. The heaviest one is needed for wheel replacement operations, door repairs and other heavy work.
- Pliers.
- Nippers.
- Rope for towing cars. It must be worn, reliable, non-slip and not damaged.
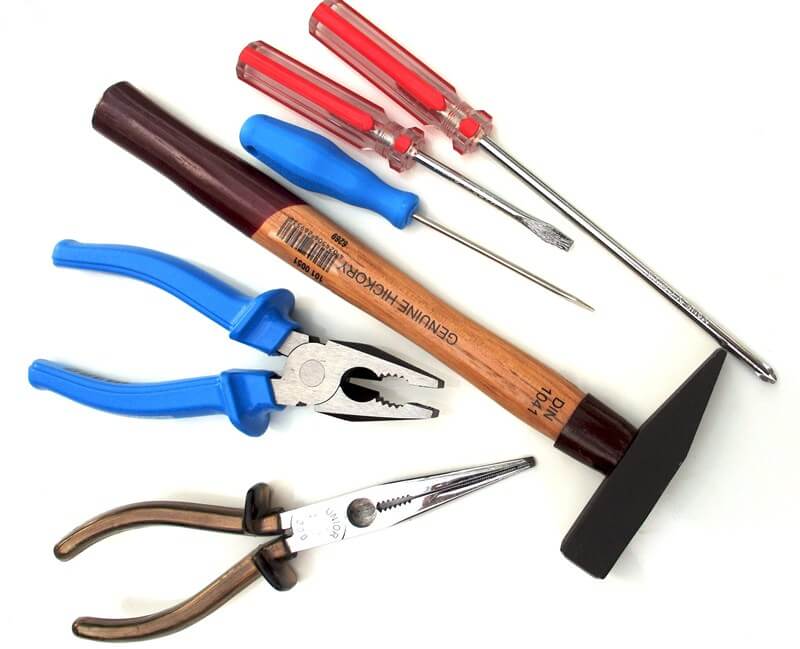
In addition to the standard set of tools, it is advisable for you to carry with you special devices and materials that you may need to work with your own hands at the breakdown site:
- spare parts - it is advisable to have small spare parts with you that may be needed during the repair. These can be bolts, nuts, gaskets, hoses, and the like;
- spare parts and components: belts, fuel pump, fuses and other little things that can let you down on the way;
- spare tire - if you have a punctured wheel, only the spare wheel will save you;
- cigarette lighter - it will come in handy if there is a need to charge the battery from another car;
- woolen gloves - useful so as not to injure your hands during hard work;
- clean dry rags and rags - they are used to wipe hands or car parts from dirt, dust and oil.
It makes sense that you don't need to carry an entire workshop with you. However, if you want to do all car repairs with your own hands, if possible, your garage should be part-time and a car repair shop.
There should be all the tools for auto repair and special equipment for a more serious event than troubleshooting on the spot.
You need to ensure that your garage has:
- high-quality lighting - as strange as it may sound, the light source plays a huge role in car care. Your eyes shouldn't get tired of bright light. At the same time, it is difficult to overestimate the importance of a full review of any work areas;
- welding machine - it is likely that you will have to perform operations for welding metal elements. Therefore, if possible, it is worth getting a welding machine;
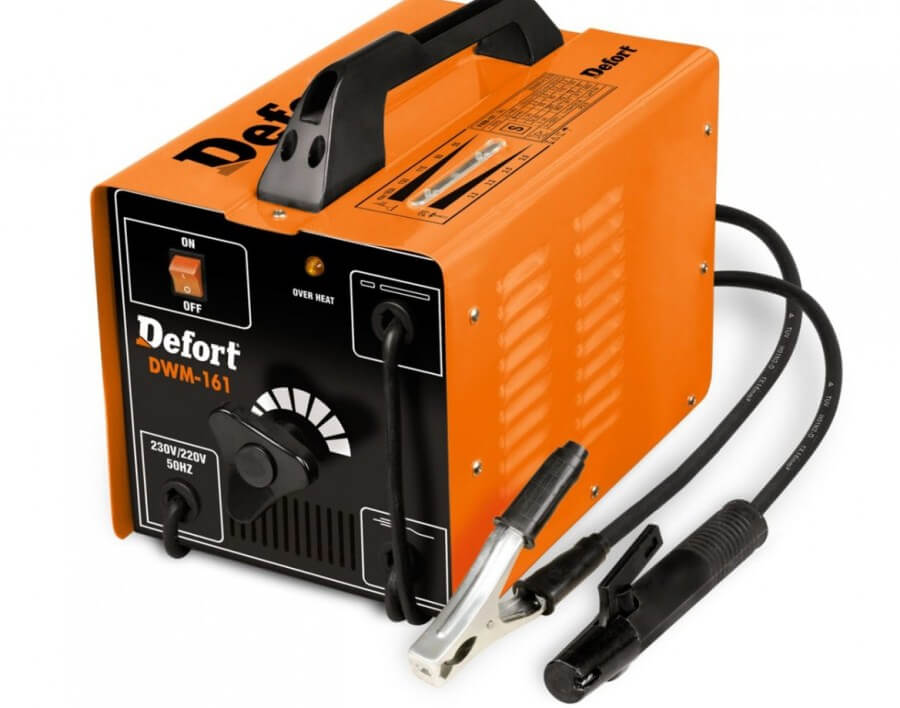
Please note that its operation will require certain skills from you. Practice well before starting work.
- straightening spotter with all complete set. It is used to straighten parts of the car body and for spot welding;
- sandblasting machine. Used for cleaning and degreasing various surfaces. Indispensable in the fight against emerging foci of corrosion, as well as when repainting car units;
- a set of tools for non-welding straightening: hammers, blades, mandrels, etc .;
- vice;
- Sander. It can also be a regular grinder that can grind and cut;
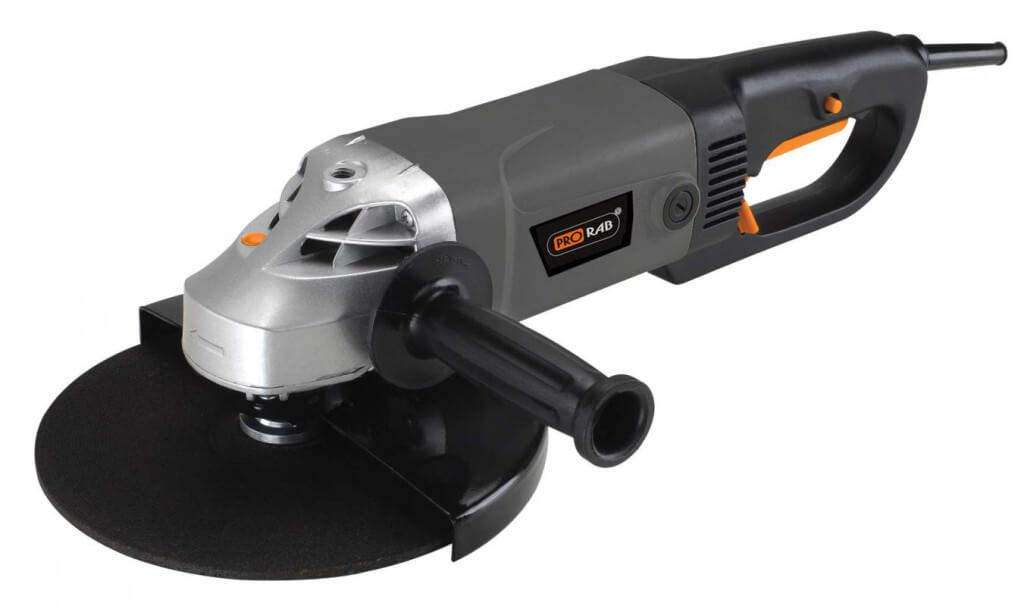
- electric drill;
- milling machine;
- pneumatic spray gun for surface painting;
- a set of hand-held locksmith tools: chisels, punches, barbs, etc .;
- measuring instruments: calipers, tape measures, etc.
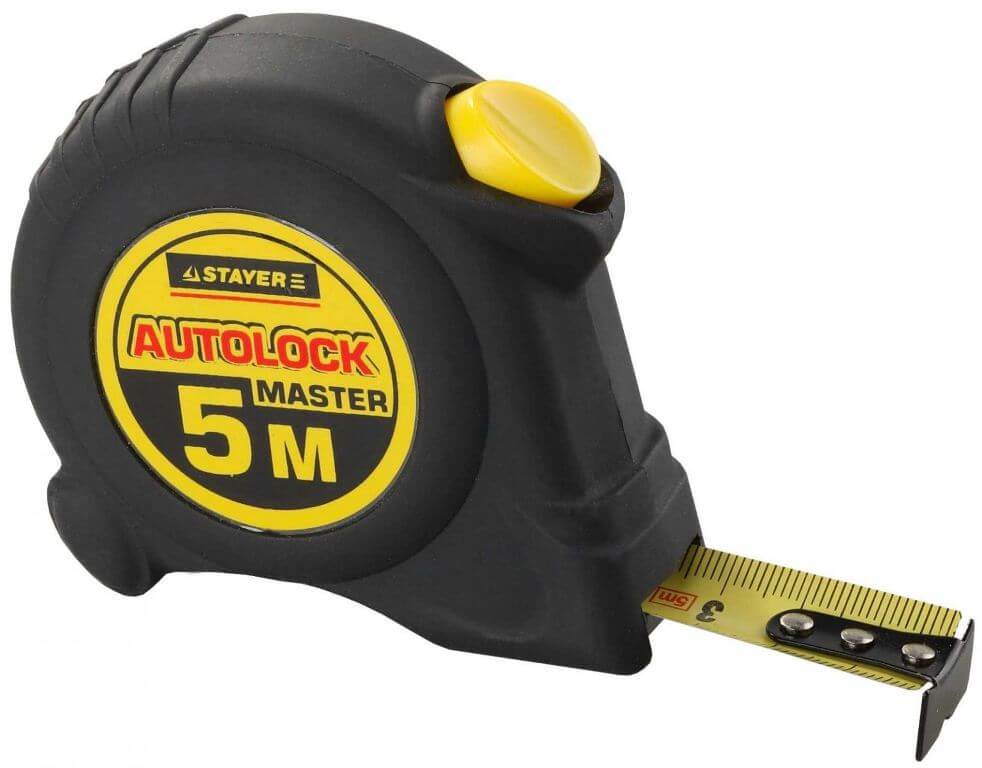
It is quite logical that this list can be continued indefinitely - its length depends on your knowledge, skills, financial capabilities and willingness to delve into the intricacies of the process.
It is likely that you will undertake only simple work with your own hands, and for more serious service - contact a car service station.
Any car repair specialist uses tools that can hardly be called standard, but they make your life a lot easier. Let's consider some of them:
- gate for places with difficult access. If you find it difficult to reach the bolt, the ratchet collar will help you handle it effortlessly;
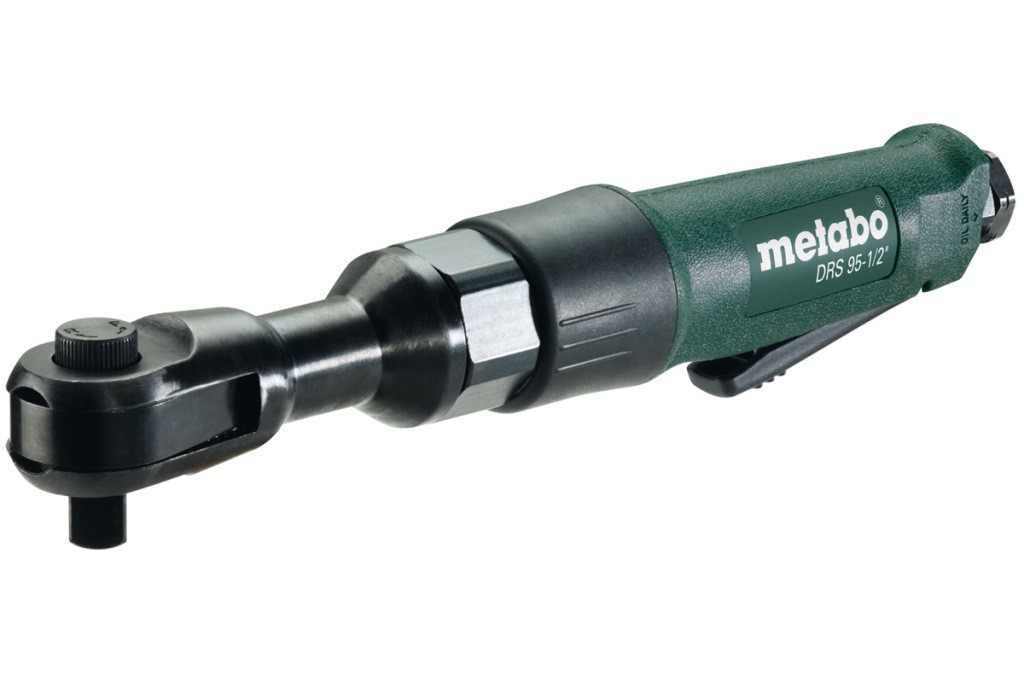
- needle hammer. Removes any scale, rust and paint no worse than a sandblaster. Needles (12 or 19 pcs.) Are located on the handle, which is attached to the compressor. With the help of pneumatics, this device very effectively taps and cleans the surface;
- gaikolom - a cap ring with a cutting tooth inside. If the corroded nut does not give way, put on the ring, press the cutting tooth and apply force until the nut breaks. At the same time, the bolt thread remains intact: put on a new nut, make a pass with lubricant - and the problem is solved;
Do-it-yourself car repair requires a serious base of tools, fixtures and materials. Without the presence of the obligatory standard tools, car repairs will simply be impossible.
Therefore, if you are planning to repair your car yourself, it will be very helpful to know what tools and fixtures are used for different operations. The success of the work, as well as the time spent, depends on how fully and competently your workshop is staffed.
Some motorists who have been using cars for a long time prefer to repair their cars on their own instead of contacting service centers. In the case of minor breakdowns, you can get rid of them in your own garage, but special equipment is required to repair the chassis or body. In a garage, a tipper may come in handy.
Such equipment is rarely used at service stations, and in the factory version it is quite expensive. At the same time, you can try to make a tipper for a car with your own hands according to the drawings - it is economical, and you can always choose the most suitable option.
There are a lot of copyright ideas on the Internet, and before making a device for a car, you should make sure that it meets all the technical requirements, namely:
- carrying capacity;
- safety;
- ascent angle.
So, we will consider in detail all the components of the tippers, and also tell you how to make and assemble them together.
It is made from metal 3-4 mm thick and a metal bar with a diameter of 12 mm. The latter is welded to fix the jack. In this case, it is necessary to maintain the internal size without narrowing it. This is important for the shoe's ability to move around the rack.
It can be made from a 32 mm corner with a length of 150 cm. In total, 4 pieces are required. We collect the corners in a square, using the clamps. Inside one of the squares, you need to insert a metal rod from a square 26x21 mm 35-36 cm long. You must first drill holes, make electric rivets and clean them.
To create it, you need sheet metal with a thickness of 3-4 mm. It should be 350x150 mm in size with curved sides. It is also possible to weld a 20 mm wide strip on the tacks with drilled holes to fix the inserted board. We fix the rubber strip on the board. We weld stiffeners and guides under the lower part of the platform, not forgetting about the jumper. The dimensions of the site are not critical. It is necessary to adhere to the size between the guides, putting the platform on the upper beam, along which it can move freely.
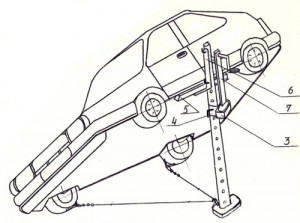
For this, you will need sheet metal 3-4 mm thick. Putting together an element of two halves with a metal strip between them. The front part should be left open, and a jumper is welded to the lower part.
We make it from a corner of 32 mm with a length of 1540 mm (4 pieces are needed in total). You will also need 4 corners of 36 mm of the same length. We assemble the corner into a square using welding seams with a length of 30-40 mm. When assembling, we use clamps. After connecting the corners, you need to drill 26 mm in diameter in the lower part of the hole, stepping back 31 mm from the edge. This leaves you 5mm left to weld the metal bar inside the structure. Next, we drill 13mm holes:
- one at a distance of 100 mm;
- the next after 80 mm;
- the third and all subsequent ones through 190 mm.
Tipper in action
Holes are needed for the metal pin, which are needed to secure the shoe and top beam. After assembling the square profile and drilling it, it must be connected with pieces of corners, also assembled into a square profile.
When assembling, you need to insert spacers of the same size between the profiles, that is, 36 m each or a finished upper beam. After welding, let the part cool down without removing the spacers. Check that the top beam fits easily between the square profiles.
To build it you will need:
- two inch pipes 30 cm long;
- corner 32 mm, length about 33 cm;
- rod from a rod with a diameter of 26 mm and a length of 42 cm.
At the corner we mark 6 cm from the center in both directions and keep the shelf at this distance. In the center of the corner, we drill a hole with a diameter of 16 mm, which is needed to connect the lower beam, taking into account the size of the bolt head. After that, we bend the corner into a U-shaped figure. It is better to connect the parts assembled with the rack.
Make sure that the pipe does not burn out during reconciliation. The entire front connecting unit is movable, that is, the U-shaped corner along the edges with pipes must rotate on a metal rod.
- two 32 mm corners 171 cm long;
- sheet metal strip 64 mm wide;
- several bushings.
We assemble the corner into a U-shaped profile, that is, a channel. On the one hand, in the middle, we weld a metal insert 3-4 mm thick and 16 cm long, which is needed to use different jacks. Weld the plate on top with tacks, sew it all into one piece and get a rectangular profile.
We weld the insert to the plate, and on the back side we muffle the profile with a metal plate 4-5 mm thick, scalding and cleaning around the perimeter. We weld a sleeve of the following dimensions to the end in the middle:
- length 35 mm;
- inner diameter 20 mm;
- outer 35 mm.
In front of the upper beam we weld two rails for the jack with holes for the jack stopper. They need to insert an M8 bolt with a nut. Also on the upper part we weld a sleeve with rollers and under a safety pin.
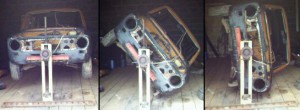
We make them from a 12 mm metal bar. Cut to size and fold, Preheating the fold. In total, you will need three such rods.
For it, we need an M16 nut and a 32 mm angle. We assemble the corners into a square profile using tack welding. We weld an M16 nut from one end - to connect to the front assembly. For the other end, we drill a hole, retreating 20 mm from the edge in the center. The hole diameter is 12 mm. It is needed to connect to the rear node.
![]() |
Video (click to play). |
When all the nodes and elements are ready, we put everything together according to the scheme.