In detail: transfer box gazelle 4x4 do-it-yourself repair from a real master for the site my.housecope.com.
Transfer box drive
1 – fork of the interlock clutch
Details of the drive and intermediate shafts
1 - flange;
2 - stuffing box;
3 - thrust bearing ring;
4 - front bearing;
5 - drive shaft;
6 - gear wheel of the highest gear;
7 - hub;
8 - clutch;
9 - low gear;
10 - bushing;
11 - rear bearing;
12 - bearing adjusting ring;
13 - intermediate shaft bearings;
14 - intermediate shaft
Transfer Case Differential Parts
1 - retaining ring;
2 - spring washer;
3 – an adjusting ring of the bearing;
4 - bearings of the differential housing;
5 - driven gear;
6 - front differential case;
7 - front axle drive gear;
8 – a lock ring of an axis of satellites;
9 - satellite;
10 - rear differential case;
11 - support washer;
12 - rear axle drive gear;
13 - the axis of the satellites;
14 - spring washer of the axis of the satellites;
15 - support washer
Disassembly
PROCEDURE
1. Flush the transfer case and drain the oil.
2. Fix the transfer box on the stand for disassembly and loosen the fastening nuts
flanges on the drive shaft and on the drive shafts of the front and rear axles.
3. Turn away nuts of fastening and remove a crankcase
1 front axle drive assembly with cover
2, lever, fork, locking clutch
differential and with front drive shaft
bridge. Remove the housing 3 of the speedometer drive in
assembly with driven gear
speedometer.
10. Remove front cover 4 together with
differential, then install
bearing adjusting ring
differential 3 and remove from the front cover
bearing assembly with differential (1 -
intermediate shaft, 2 - drive shaft).
![]() |
Video (click to play). |
11. Remove the adjusting rings from the rear bearings of the drive and intermediate
shafts and remove both shafts from the transfer box housing: drive and intermediate.
12. Clamping the drive shaft in a vice, remove the thrust ring and rear bearing 11,
using a universal puller. Remove the lower gear 9 from the drive shaft
transmission together with sleeve 10, gear shift clutch 8, clutch hub 7,
gear 6 of the highest gear (see Fig. Details of the drive and intermediate shafts).
13. Disassemble the differential, for which remove the circlip 1 and the spring washer
2 front bearings (see Fig. Transfer case differential details).
14. Remove the rear and front bearings from
differential housing using
universal puller 1 - А.40005/1/6 and stop
67.7853.9559 - 2 (3 - bearing).
15. Turn away bolts of fastening of a conducted gear wheel of differential, note risks
on the differential housings, their mutual arrangement relative to each other and
separate the body.
16. Remove differential driven gear.
17. Remove retaining rings 8 and spring washer 14, then press out the axle
satellites and remove the satellites and drive axle drive gears with support
washers (see Fig. Details of the transfer case differential).
18. Press out worn or damaged oil seals from the crankcase
front axle, from the front bearing cover and from the rear cover.
19. Turn away nuts from axes of a pillow of a suspension bracket and remove arms in gathering.
Assembly
PROCEDURE
1. The assembly of the transfer case is carried out in the reverse order of disassembly.
2. Assemble the center differential by aligning the marks on its housings so as not to
unbalance this node.
3.Install the spring washer on the axis of the satellites from the side of the blind hole on
axle end.
4. The axial clearance of each axle drive gear should be 0-0.10 mm, and
the moment of resistance to rotation of the gears should not exceed 14.7 N m (1.5 kgf m).
5. If the gap is increased, replace the support washers with others of greater thickness; if
the specified clearance cannot be obtained when installing the support washers of the largest
thickness, replace the gears with new ones due to their excessive wear.
6. Leading 1 and intermediate 2 shafts
installed in the transfer housing
boxes at the same time.
7. Pressing the bearings onto the housing
differential swipe with mandrel
67.7853.9558 (1).
8. Lubricate the working surfaces of the seals before installing them in the covers and crankcases
grease Litol-24.
9. Tighten screw connections to the torque.
10. When compressing the nuts of the transfer case shafts
boxes use mandrel 67.7820.9520 (1)
(2 - flange retainer).
11. After assembly, fill the transfer case with oil up to the lower edge of the filler
holes.
- Like
- I do not like
Hello everyone! Tell me who knows, the blocking stopped turning on. When there was a new car, it was difficult to turn it on and off, but it was possible.
As they teach in a book, coasting back and forth, it didn’t stop working, it just rusted, I have the same garbage, it’s hard to turn on because I rarely use
- Like
- I do not like
As they teach in a book, coasting back and forth, it didn’t stop working, it just rusted, I have the same garbage, it’s hard to turn on because I rarely use
Thanks for the answer. I don’t use it often either, but at every opportunity I try to lubricate everything. The whole thing turned out to be in the switching rod.
- Like
- I do not like
I bought a new December gazelle 33027. and I don’t understand what should the downshift light turn on? because when I turn on the differential, I turn on orange. And the 4x4 gearbox is upgraded or a 1997 model?
No, it shouldn't, because there is NO such light bulb. Checkpoint own. Differences: there is no hole for the speedometer drive (on the RC) and there is a hatch instead of which you can put a PTO.
ZY Location indicate your location, please.
Post has been edited by den773: 17 January 2008 - 21:48
I bought a new December gazelle 33027. and I don’t understand what should the downshift light turn on? because when I turn on the differential, I turn on orange. And the 4x4 gearbox is upgraded or a 1997 model?
There is no reason for her to light up and there is no place for a light bulb, unless you start a reserve. The differential lock glows so that you don’t drive with it on the pavement and fly away, respectively. and lowering does not affect it. The checkpoint is the same, only the holes for mounting the levers of the differential and lowered are drilled, and on the other side of the hatches for attaching the KOM, it is milled and closed with a metal plate. the number of gears is unfortunately the same, in bridges 5.125
- Like
- I do not like
my gears are stuck with difficulty and constantly when driving there are two different sounds from under the gearbox. Is this how it should be for a 300km car?
About sounds in more detail, and “transfers with difficulty” - imported clutch (see related topics) and synthetic gearbox oil.
- Like
- I do not like
appear when driving from 20 km. the first cricket (rattles) trtr-trtrtrtrtrtrtrt. second buzz as if the wheels are unbalanced, vibration is felt.
The first is most likely from the levers of the pk. And the second is cardan shafts (I talked with the balancing master - it is necessary to balance because they don’t do this at the factory), although you need to start with balancing the wheels.
appear when driving from 20 km. the first cricket (rattles) trtr-trtrtrtrtrtrtrt.second buzz as if the wheels are unbalanced, vibration is felt.
The first cricket is most likely the washers at the ends of the lowered and locking levers and, respectively, at the ends of the rods from the pk side. It’s easy to check if, while driving, put your hand on these levers, the noise is less. From the side of the pk on the thrust for 35 tkm, the output was formed by 0.5 mm until I found it. It was cured very simply by putting rubber washers from a piece of hose, instead of native plastic ones. it is better to change everything at once. Native rubber k-139 at a speed of more than 90 km makes noise louder than the engine, with such a characteristic rumble due to the tread
- Like
- I do not like
- Like
- I do not like
- Like
- I do not like
- Like
- I do not like
- Like
- I do not like
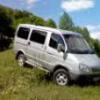
- Like
- I do not like
Today I have already successfully tested the electric drive for controlling the razdatka. For this, two wiper motors from a Muscovite were used. They are to the frame, and the movable levers on them are cut straight into the rods.
Everything, now a 4-hour trip to the country will not drill my brain with a ringing that drowns out the radio. Only two extra buttons on the panel https://my.housecope.com/wp-content/uploads/ext/3317/forum/public/s. )))))))
I saw a photo somewhere, they installed electric engines from the ESP. It also worked. Photo and description of the process in the studio!
Post edited by den773: 27 October 2008 – 16:58
A 4x4 transfer case for a gazelle is a unit that distributes torque from the engine to other drive mechanisms that also increase the number of gears in the transmission.
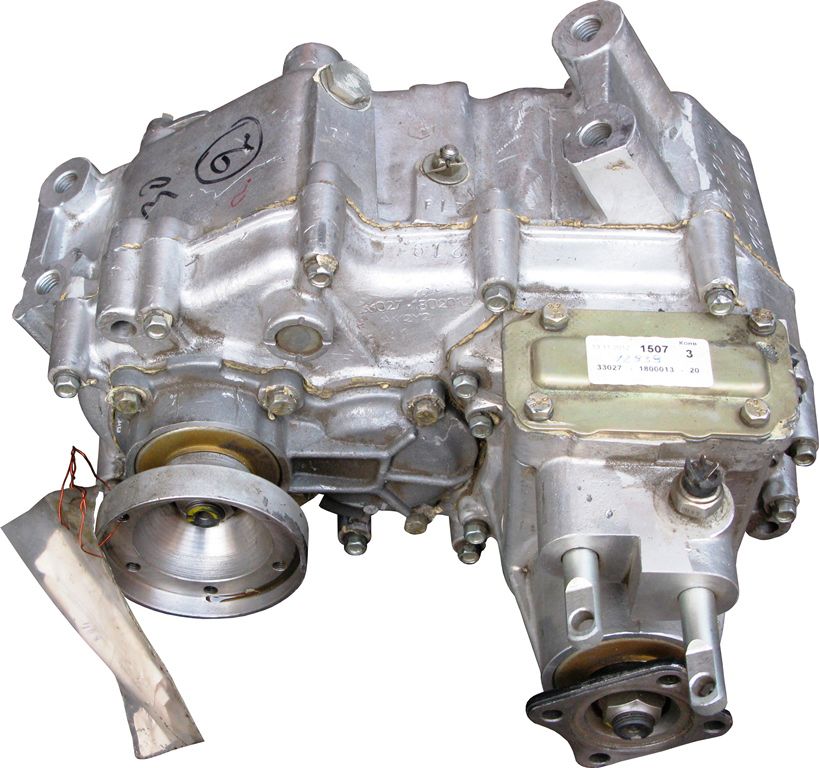
Transfer box 4x4 for gazelle
The transfer case is a unit that distributes torque from the engine to other drive mechanisms that also increase the number of gears in the transmission.
The device is an integral part of all-wheel drive vehicles. The first transport analogues appeared only at the beginning of the last century. They were intended only in racing competitions on the highway and off-road, and they looked like a passenger car. The public of that time considered the development to be mere pampering. After a series of manipulations, a transfer case was produced that performs the tasks of modern analogues.
Based on the method of power distribution between the bridges, the 4x4 transfer case for the gazelle of our time is diverse:
- With a differential type interaxle drive that does not provide for the possibility of forced shutdown of one of the drive axles. Cars with a similar box are characterized by the constant operation of the front axle. If it is necessary to increase the passage, the center differentials switch to forced blocking.
- With a differential type center drive, which provides for the possibility of forced shutdown of the front drive axle. Due to the use of a single main gear, this type has gained such popularity.
- With an interaxle locking type drive with a manually disconnected second drive axle or with the help of automation when the wheels slip. Cars with a similar box when driving on a hard surface provide for disabling the front axle. This condition helps to save fuel and reduce tire wear.
- With driven shafts of misaligned type. There is no intermediate shaft. Main advantages: compactness, noiselessness, high efficiency.
The 4x4 transfer case is responsible for the distribution of forces on all drive axles of the vehicle. Its additional application is the starting and stopping of the driving front axle. Basically, this type of gazelle is characterized by a two-stage gearbox. His work affects the gear ratio, as a result, the number of gears is doubled.
When starting a direct transmission to a 4x4 gazelle, the first row of gear ratios is introduced, and when lowering, the second. This factor determines the passage of the car in a variety of road conditions.
The cross-country gazelle is characterized by a design that blocks the possibility of downshifting when the front axle is engaged. A device of this type makes the rear axle insensitive to large torque overloads.
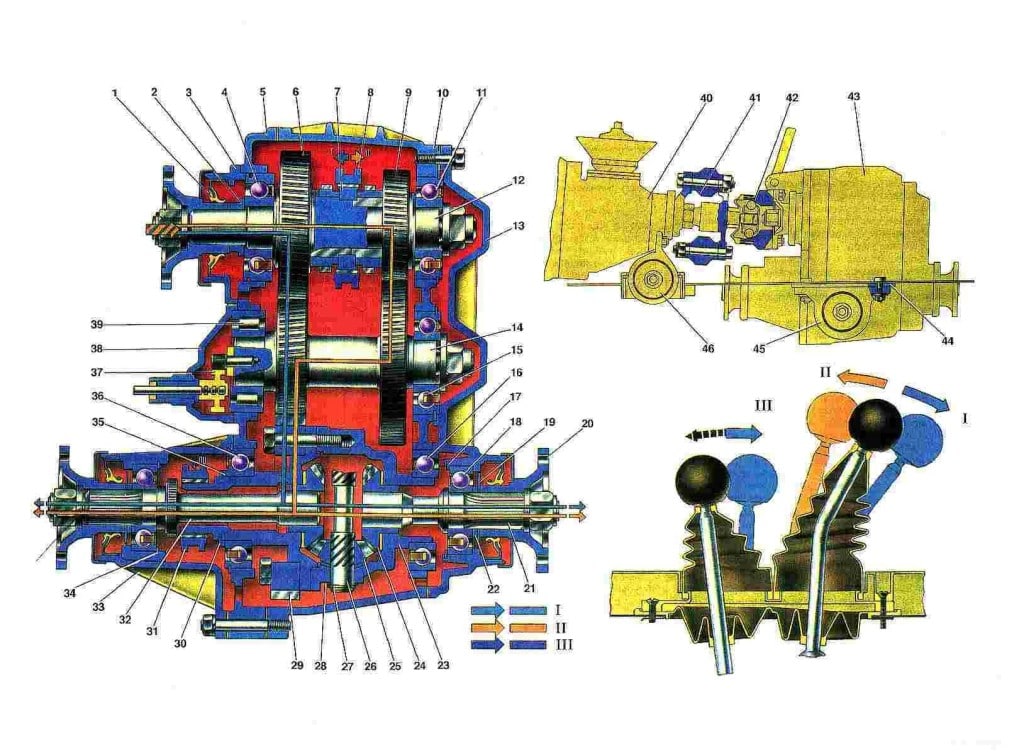
Transfer box device 4x4 for Gazelle
The 4x4 transfer case for a gazelle is characterized by the following main components:
- drive shaft;
- rear axle drive shaft;
- front axle drive shaft;
- center differential;
- a device that blocks the center differential;
- gear or chain transmission;
- downshift.
Torque, as the main acting force, passes from the transfer case from the gearbox through the drive shaft. The center differential is responsible for the distribution of torque between the axles. In turn, it causes rotation at speeds with different angular values.
A variety of center differential for a 4x4 gazelle includes two types:
- symmetrical, characterizing the uniform distribution of torque;
- asymmetrical, characterizing a different ratio of torque distribution.
In order to rigidly hitch the front and rear axles, a differential lock was provided for the 4x4 gazelle.
The task of the chain drive is to transmit torque to the front axle, which includes gears and drive chains.. It happens that the gear is replaced by a chain. And the all-wheel drive system with an automatically connected type of transfer case has the form of a bevel gear.
The downshift is assigned the role of increasing the torque when driving off-road. Here the design of the planetary gearbox is borrowed.
Movement on deformable soils usually does not imply the circulation of parasitic power, since the value of the total component of the movement resistance force is decent, and the adhesion force of the wheels to the supporting surface is insignificant.
The 4x4 transfer box for the gazelle is characterized by the regime operation:
Further modes are guided by the differential.
- Its unlocking with the condition of the included overdrive. The torque division is in the form of a ratio of 1:2.
- Blocking with the condition of the included upshift. The division of torque depends on the grip of the wheels and the surface.
- Unlock with downshift condition. The distribution of torque is represented by a ratio of 1:2.
- Blocking with downshift condition. The distribution of torque is carried out depending on the grip of the tires with the coating. The functioning of the front and rear axles is characterized inextricably. This mode has the highest degree of patency.
On 4 × 4 vehicles, a two-stage transfer case is installed with forced locking of the symmetrical center differential and manual control.
The transfer box device is shown in fig. 4.26 and fig. 4.27. In the crankcases 4 and 8 (Fig. 4.26) of the transfer case, cast from aluminum alloy, the primary 16, intermediate 45 shafts, shafts 37 and 23 of the drive of the front and rear axles with flanges, the box 41 of satellites and gear 33 of the differential are mounted on bearings. The axial clearance of the bearings 25 of the differential is adjusted during assembly by gaskets 35 installed in the cover 38 of the control mechanism.
- protective ring;
- cuff;
- gaskets;
- front crankcase;
- thrust washers;
- gaskets;
- downshift gear;
- rear crankcase;
- gear shift clutch;
- top gear;
- thrust washers;
- gaskets;
- back cover;
- rear input shaft bearing;
- retaining rings;
- primary shaft;
- intermediate shaft rear bearing;
- speedometer driven gear;
- speedometer drive gear;
- spring washer;
- fixing ball;
- retaining rings;
- rear axle drive shaft;
- bearings;
- differential bearing;
- support washer of the axle gear;
- bolt;
- satellite;
- axle gear;
- drain plug;
- satellite axis;
- satellite support washer;
- differential gear;
- gaskets;
- adjusting pads;
- differential lock clutch;
- front axle drive shaft;
- cover of the control mechanism;
- retaining rings;
- axle stopper;
- differential pinion box;
- retaining rings;
- front intermediate shaft bearing;
- front cover;
- intermediate shaft;
- retaining rings;
- screw;
- front input shaft bearing;
- flange
Gear shift and differential lock mechanism:
- intermediate rod;
- stem gland nut;
- sealing ring;
- washer;
- stem seal;
- fork of inclusion of blocking of differential;
- gear shift fork;
- gear shift rod;
- intermediate lever;
- stem head;
- Cork;
- bolt;
- axis of the intermediate lever;
- retainer ball;
- retainer spring;
- differential lock enable sensor;
- differential lock lever
Crankcases, to ensure the necessary alignment of the shaft supports and holes for the rods of the control mechanism, are centered on the dowel pins pressed into the rear crankcase 8, and are connected to each other by fourteen bolts.
All gears in the transfer case are helical. On the input shaft, gears of lower 7 and higher 10 gears freely rotate on bronze bushings, which are in constant engagement with the gears of the intermediate shaft, which is made in the form of a gear block. A sliding clutch 9 is installed on the input shaft on the splines. When the top gear is engaged, the gear shift clutch moves backward, and when the low gear is engaged, it moves forward. One of the rims of the block of gears of the intermediate shaft 45 is in constant engagement with the gear 33 of the differential, attached with bolts 27 to the satellite box.
Inside the satellite box, an axle 31 is installed with two satellites 28, which are in constant engagement with side gears 29, which are located at the splined ends of the drive shafts of the front and rear axles of the vehicle. On the drive shaft of the front axle, a clutch 36 for engaging the differential lock is installed on splines. When the differential is locked, the movable clutch rigidly connects the shaft 37 with the satellite box. In the grooves of the couplings 9 and 36 are the inclusion forks 7 and 6 (see Fig. 4.27), which are mounted on the rods with bolts and spring split washers.
The differential lock and gear shifting in the transfer case is carried out using levers 1 and 2 (Fig. 4.28) mounted on the axis 8, pressed into the bracket 9, which is fastened with two bolts to the gearbox.
Transfer case and its drive:
- gear lever;
- differential lock engagement lever;
- pillows;
- screw;
- sleeve;
- manhole cover;
- traction;
- axis of control levers;
- control arm bracket
The differential lock can be engaged both with the lowest gear in the transfer case, and with the highest one.
Link for those wishing to purchase this product.
razdatka gas 66 for a gazelle.
Not full video. I'll add later.
A small video about the SWAP of the Multimod dispenser in the Gazelle. Overview and cons of the Gazelle 4x4 Distribution turnkey multimode.
Consumption on a mountain road. Engine 405. Driver and 200-250 kg of cargo. I didn’t stand in traffic jams, the temperature was -3-5 C.
The famous “Red” Sable is equipped with 36th wheels and a new transfer case.
I gave the rear cardan for balancing and drove on the front axle (that is, the connected all-wheel drive.) What a horse.
Installation of the ZIL-131 transfer case on the GAZ66 frame with the front drive axle gear overturned.
Defects in the transfer case Sobol 4x4.
Moved the mount to the frame. Rods with ball ends.
Pneumatic control of the dispenser Gas-66.
The vehicle has been re-equipped to pass through hard-to-reach places. It stands on the bridges ZIL 157. Distribution box ZIL 157.
Delivery throughout Russia and the CIS!
Free shipping across Nizhny Novgorod, Moscow, Ulyanovsk and Vladimir!
The Avtohis company sells original components for GAZ vehicles, manufactured at the factory and passed multi-level quality control during the production process. The reliability of such parts is much higher than that of numerous handicraft analogues presented on the car market.
However, the price of a branded handout for «Sable» somewhat different from the products of Chinese masters. However, it is advisable to purchase a factory-made unit. The absence of problems when working in any road conditions and a long period of operation will more than pay for the additional costs in the first months after purchase.
The transfer box is one of the most reliable parts of a car. A complete replacement of the dispenser is usually carried out in the following cases:
- critical wear of most elements of the assembly;
- shock contact with the coating or damage resulting from an accident.
In other situations, it is enough to replace individual failed components. The dispenser promptly signals the appearance of problems: there is extraneous noise during the operation of the unit and difficulties appear when switching modes.
The Avtohis online store provides its customers with the opportunity to purchase original spare parts for domestically produced cars on favorable terms. Thanks to a direct supply channel directly from manufacturers, we offer to buy a dispenser for Sobol Gas at a factory price. Individual approach and meeting the needs of each client is the main principle of our company.
The transfer box is an integral part of any all-wheel drive vehicle. It is this device that is responsible for the distribution of the engine torque between the drive wheel axles of the machine.
Modern handouts provide for the possibility of turning on all-wheel drive or only one of the axles. The system of center differentials, similar to the design of the rear axle gearbox, makes it possible to ensure the movement of the car's wheels at different speeds, and the possibility of forced blocking of this device allows you to easily overcome difficult road sections.
The dispenser for the all-wheel drive GAZ Sobol 4x4 has a traditional functionality for cars of the Gorky Plant:
- three-position control lever: turning on all-wheel drive, activating only the rear axle and neutral position (both axles are off);
- low and high gear modes;
- center differential with the possibility of its manual blocking.
All elements of the dispenser are placed in a metal crankcase with a sealed lid. Maintenance of the unit is reduced to the control and replacement of oil. The box signals the occurrence of problems in advance: extraneous noise appears during the operation of the unit or difficulties arise when switching operating modes.
The Avtohis company offers its customers original spare parts and components for GAZ vehicles. You can buy a razdatka for a Gazelle 4x4 from us, made specifically for aggregation with the power plants of the Zavolzhsky Motor Plant. All products offered for sale are assembled from high-quality parts in compliance with the layout process and have passed mandatory testing in the form of finished products.
The Sobol 4×4 is good for everyone: it is inexpensive, the cross-country ability is good, and in comparison with the Ulyanovsk “loaf” it is simply luxurious. However, there is an element in its design that scares off a considerable part of consumers - permanent all-wheel drive, full-time ”(full-time). The transfer case along with the front gearbox and driveshafts howl and vibrate too much at high speed.
Two years ago, the designers decided to overcome the disease and began to grind the gear teeth of the transfer case. Introduced 100% control of vibration and noise characteristics of bearings. Handouts began to work quieter, but it was still far from ideal. And then the factory workers took drastic measures.In the joint engineering center of GAZ, work began on a new all-wheel drive transmission of the part-time type (part-time) with a connected front axle - instead of the full-time option, permanent all-wheel drive.
The new transfer case has retained the maximum unification from the previous one: the original elements (highlighted in red) can be counted on the fingers.
In order not to lose the main market trump card - low cost, the designers were asked to unify the new razdatka with the serial unit as much as possible. As a result, she retained a four-shaft scheme with constant meshing of gears, in which there is no direct transmission (the gear ratio of the first stage is 1.07, and the second stage increases the torque by 1.87 times).
Instead of a center differential housing with satellites, a special adapter sleeve is now screwed to the differential gear. With the rear axle drive shaft, this bushing is permanently splined, but the front axle shaft is connected to it through a toothed coupling. Even in razdatke had to replace the rods of both forks. Thus, in the new transfer case, it was possible to keep all the old body parts, except for the front cover of the control mechanism.
In addition to the part-time razdatka, they developed new cardan shafts with CV joints instead of crosses. They are better centered in the circuit and are almost free from noise and vibration.
Only the owners of "sables" with passenger and cargo-passenger bodies will be able to fully appreciate the advantages of the transmission with new cardan shafts. For flatbed trucks and three-seater vans, the hinges on the shafts leading to the bridges are the same. Their razdatka is located outside the cab, and therefore there is initially less noise in the cabin. The factory workers think so, but I do not agree with them.
The transfer case on the Sobol 4 × 4 is installed in the middle of the wheelbase and is connected to the gearbox by an intermediate cardan. The latter also received CV joints instead of crosses.
I jump into the brand new "Sobol" - "part time". Inside, nothing has changed: the same three levers in the floor, the familiar transmission control lamp on the instrument panel. But their functions are different. The lamp does not signal a locked differential, but the activation of the front axle. And the lever that included the lock now connects the front axle.
High-torque diesel "Cummins" cheerfully accelerates the car, and I listen to the noise of the transmission: 60, 80, 100 km / h - quietly. Previously, at this turn, I cut off conversations with fellow travelers: the noise drowned out the conversation. Now we can continue the debate about the advantages and disadvantages of the "full-" and "part-time" schemes. There is no hint of the former distributing itch even at one hundred and twenty.
We move down from the asphalt to the sandy hillock. Having quickly lost momentum, the car began to burrow, throwing fountains of sand from under the rear wheels. I push the left lever of the transfer case away from me. With unusual ease, the front end is connected - and the Sable easily climbs this hill, and all subsequent ones.
The shape and location of the transmission levers have not changed, only the content of the information sticker has been updated.
Only when the wheels sank into the sand almost to the hub, for the first time I decided to resort to a lower gear in the razdatka (it can only be used by connecting the front-wheel drive). But in stock there is still an Eaton rear wheel lock. For a year now, all all-wheel drive “sables” and “gazelles” have been equipped with it on a regular basis. Let's add here a large ground clearance and small overhangs - with such an arsenal, the Sable 4 × 4 will give odds to other venerable off-road vehicles!
The permanent all-wheel drive system has not gone away: the production of cars with full-time and part-time transmissions goes in parallel. And rightly so: every scheme has its admirers. The former is preferable for motorists who travel off-road more often than on asphalt. The plug-in all-wheel drive is addressed to those who mainly travel on asphalt, but sometimes they go where Makar did not drive calves. This option is just right for me.You need to comfortably drive a thousand and a half keme along the highway and then confidently overcome 500 meters of mud right to the water's edge.
Both types of all-wheel drive are priced the same: any Sobol 4 × 4 is more expensive than a rear-wheel drive counterpart with a similar body by exactly 52,000 rubles. In the segment of light commercial vehicles, this offer is still the most attractive.
The transfer case with a switchable front axle for minibuses and combi is equipped with flanges for cardan shafts with CV joints. Machines with permanent all-wheel drive are equipped with cardan shafts with crosses.
For several years now, GAZ has been experimenting with a new front drive axle - with CV joints instead of cardan joints of unequal angular velocities. Their introduction will help to completely get rid of the uneven movement of the wheels at large angles of rotation. On the Sobol 4×4, this small feature is clearly visible when turning around.
The new bridge, most likely, will mature by the time the Gazelle-Next 4 × 4 is put on the conveyor. But even earlier, “gazelles” and “sables” may receive transfer case control buttons instead of levers: tests of electrified transfer cases are in full swing.
The all-wheel drive engineering school at GAZ is already seven and a half decades old. What kind of all-terrain vehicles have not been designed here over the years! A whole magazine is not enough to tell about all of them. Let's go through only the lightest cars.
The first lightweight all-wheel drive - GAZ-61 - was created by designer Vitaly Grachev on the basis of the Emka in 1939. The torque of the inline "six" GAZ-11 was enough to get by with four gearbox steps from a lorry without an additional downshift in the razdatka. CV joints were used in the front wheel drive! The prototypes were assembled with bodies of a phaeton (model 61-40), a sedan (61-73) and a pickup truck with an all-metal cab (61-415). Only a sedan and a simplified pickup truck 61-416 with an open cab managed to get into small-scale production in 1941. In total, about 200 cars were made before the end of the war.
At the beginning of 1941, Vitaly Grachev developed the GAZ-64 compact army off-road vehicle with an original frame and a simplified open body. The car was equipped with a 4-cylinder M-1 engine and the same transmission as the GAZ-61. It lacked only an intermediate cardan shaft between the gearbox and the razdatka. From August 1941 to April 1943, 671 copies of the GAZ-64 were manufactured. The chassis of the "sixty-fourth" served as the basis for the BA-64 light armored car.
In 1943, the GAZ-64 was finalized: the track of the driving axles was expanded from 1206 to 1446 mm (bridges from the GAZ-61) and the body was adapted to them. The car under the GAZ-67 index lasted on the assembly line until August 1953. Circulation nearly 93,000 pieces. On the basis of the GAZ-67, the BA-64B armored car and the GAZ-011 amphibian were produced.
A new page in the history of Gorky all-terrain vehicles was opened by the GAZ-69, developed under the leadership of Grigory Wasserman in 1950 and mastered in 1953. He received a 52-horsepower engine and a 3-speed gearbox from Pobeda. A four-shaft transfer case with a built-in demultiplier and a front axle disconnect clutch was developed from scratch. Like today's "sables", it was mounted separately from the gearbox. Gear ratios - 1.15 and 2.78. Along with the base model, a more comfortable five-seat GAZ-69A and the GAZ-46 amphibian were produced. In 1956, the production of "sixty-ninths" was transferred completely to UAZ. They were made there until 1973. For two decades, 634,000 of these "gaziki" were produced by the forces of both plants.
In 1954, Grigory Wasserman tried on the transmission from the GAZ-69 to the reinforced body of the Pobeda. So the M-72 off-road vehicle was born. The car was mass-produced from 1955 to 1958, the total circulation is about 4700 pieces. In the GAZ-21 family, which replaced the Pobeda, there was no longer any place for an all-wheel drive.
Another light all-terrain vehicle designed by Wasserman - the M-73 model of 1955 - did not hit the conveyor, but served as a prototype for the all-wheel drive Moskvich of the 410th model.We made two prototypes - with pickup and coupe bodies. Both were equipped with a 35-horsepower engine and a 3-speed gearbox from Moskvich-402. The drive axles and transfer case are made according to the GAZ-69 model.
In 1974, according to a one-time Kremlin order, a batch of five GAZ-24-95 all-wheel drive Volga vehicles (lead designer Leopold Kalmanson) was manufactured at the plant; one of them was sent to the Zavidovo hunting estate to Leonid Ilyich Brezhnev. The razdatka, borrowed from the UAZ-469, was placed in the middle of the wheelbase, separate from the gearbox. The front axle was assembled from an inverted GAZ-24 rear gearbox with UAZ steering knuckles and CV joints. The main gears of both axles received cam differentials.
![]() |
Video (click to play). |
Volga GAZ-3105 (lead designer Sergei Batyanov) became the only GAZ car in which all-wheel drive was used not for the sake of increasing cross-country ability, but in order to provide decent handling parameters on slippery roads. The first prototype was built in 1987. A V-shaped petrol "eight" with a volume of 3.4 liters (170 hp) is installed in front of the front wheel axle. A two-shaft 5-speed gearbox is combined with a front gearbox and a lockable symmetrical center differential. Until 1996, 79 copies of the GAZ-3105 were assembled, including 24 prototypes.