In detail: do-it-yourself auto speaker repair from a real master for the site my.housecope.com.
The current state of the market with loudspeaker prices makes speaker repair virtually unnecessary, but if there are difficulties in purchasing a new speaker instead of a damaged or damaged one, then it makes sense to try to restore the damaged loudspeaker with your own hands. I came across several coaxial speaker systems from various cars. Unfortunately, 2/3 of the speakers produce a distorted signal during playback, and the rest simply do not work. Below will be presented material only on the restoration of "littered" coaxial-type car speakers for use in the future in the design or installation in multi-way stationary speaker systems. Before starting work, we will carry out diagnostics speaker states.
1. Check for "trash". Coaxial speakers are not fully protected from foreign objects falling into the magnetic gap, this is especially dangerous for old cars covered with rust or cars that have undergone body repairs. Checking is simple - gently with your fingers moving diffuser inside the magnetic system, if at the same time extraneous sounds are clearly audible: rustles, crackles, rattling, then this means that metal debris may have got into the magnetic gap.
2. We take a tester and in ohmmeter mode we check the resistance of the coil. If there is resistance, then this is our case. If there is no resistance, then it makes sense to check for an open circuit thick flexible copper conductors from the speaker terminals to the diffuser. If there is no break, then most likely there is a break in the speaker coil and this case of self-repair is not considered in this article. Instructions for self-repair are given below.
![]() |
Video (click to play). |
1. We unsolder the flexible leads of the coil from the contact lugs of the speaker connection and the contact lugs of the coaxial speaker.
2. Remove the coaxial speakers. Repairs of the speaker system are not provided by the manufacturer and coaxial speakers are installed tightly... The column with reinforced tweeters was removed by drilling an aluminum rivet. We work carefully, the main thing is not to tear or damage anything.
3. On the forums for repairing speakers, there are ways to dismantle the diffuser and centering washer. I also went along this path. We carry out work in the open air in the absence of open fire sources! After spending 100 ml of acetone, it was not possible to peel off the diffuser and the washer. The solvent evaporated quickly without softening the glue line. In order to save time and solvent, a cord made of cotton cloth was placed in place of gluing and moistened with acetone; if necessary, moistening as it evaporated continued until the glue softened. After softening with a thin screwdriver, he forged the edge of the centering washer and lifted it over the gluing point. With the corrugation of the diffuser made of thin rubber, you need to be more careful and delicate so as not to damage the rubber.
Pouring solvent onto the corrugation
4. Remove the diffuser. From trapped debris inside the magnetic system, damage-tearing of the speaker coil insulation is noticeable. It is useful under a magnifying glass to see the degree of damage for the presence of short-circuited turns (scratches to a depth of more than 40% of the coil wire diameter), if there is a suspicion of short-circuited turns, then it is better to reject the speaker. Using a damp cloth, I cleaned the diffuser, centering washer and coil inside and outside from dirt.Cleaning should be done carefully so as not to damage the coil.
There are scratches on the coil
5. The gap in the magnetic system is a sad sight. Strong magnet holds fine metal debris and dust firmly. I tried to clean it mechanically, but the small size of the gap and its curvature did not allow successfully removing debris. Decided to use a strong blast of air from an air compressor - it was not possible to clear the gap! Another remedy had to be used - a high-pressure jet of water from a car wash. The result is that I am all wet, but the gap is 100% cleaned, and at the same time the whole frame of the frame shone like new. I tried to do it carefully, since the pressure of the water jet is very high and I suppose with special zeal it is possible to destroy the gluing of the speaker magnet. To prevent rusting, you must immediately dry the frame and magnet. After drying, it is useful to check the cleanliness of the gap under a magnifying glass. And as experience has shown, it is good to seal the gap with tape to protect it from accidental metal debris.
1. After cleaning and drying the speaker components, we assemble the structure. It's important not to rush. The goal is to position the coil in the magnet system exactly in the center and to ensure there is clearance and no touching the coil. From a strip of A4 format office paper 10 cm wide and about 18 cm long, we roll up the cylinder and insert it into the diffuser coil. The cylinder must fit snugly against the spool and not have any protrusions or bulges inside.
2. Let's try to insert such a structure into the magnetic system. Do not hurry! Better to practice a few times. The cylinder should descend to the full depth of the magnetic gap and the coil should hardly move over the inserted cylinder. If the coil moves along the cylinder with great effort, then it is necessary to shorten the length of the paper strip, and if the coil moves freely, then it is necessary to increase the length of the paper strip.
Insert the cylinder into the gap
The coil runs tightly in the cylinder
The reel is centered
3. Holding the cylinder in the lower position, raise the diffuser and grease the area for gluing the centering washer with glue of the "Moment" type. We orient the washer according to the leads of the coil conductors and speaker terminals, as well as along the cutouts in the corrugation of the diffuser. We glue the centering washer.
4. We glue the corrugation of the diffuser.
5. After the glue has dried, we solder the coil conductors to the terminals.
6. Carefully remove the paper cylinder. Checking the diffuser travel. If everything is done correctly, then there should be no extraneous sounds.
7. To close the magnetic system from the ingress of debris, I sealed the coil hole on the side of the diffuser with black spunbond, and on the side of the magnet with tape.
Glue the centering washer
Sealing the diffuser hole
Seal the hole with tape
8. Finally, we check the result of the work by connecting the speaker to the sound source.
Using this technique, several speakers were independently restored for installation in stationary speaker systems and radios to replace old or torn speakers.
I tried to collect this way. It didn't always work out.
I did the assembly differently. After gluing the corrugation of the diffuser and the centering washer, until the glue has dried, I connected the dynamic head to a 6.3 volt transformer through a low-resistance variable wire resistor.
It was enough to slightly stir the diffuser.
In this case, the diffuser itself is centered. The noises disappeared immediately. In this position, he dried.
The disadvantage of this method: 50Hz is still hard to withstand for a long time.
The constant must be connected!
Professionals - a must, but amateurs can do so!
Hello everyone! My name is Mikhail, now I'll tell you a story about how I managed to exchange a dvenashka for a 2010 Camry. It all started with the fact that I was wildly annoyed by the breakdowns of the two, like nothing serious broke down, but the little things, damn it, so many things that really started to enrage. Here the idea was born that it was time to change the car to a foreign car. The choice fell on the tayet Camry of the tenths.
One day in my the car wheezed (ripelled) the speaker I decided to just replace it with a new one. After I found out that good speakers are not cheap, I decided to give it a try. repair the old speaker yourself... To repair and remove the wheezing of the speaker we need:
- Screwdriver
- Acetone
- Double-sided tape
- Camera roll
- Knife
- Battery 3v
- Rubber glue (for example, "Moment")
- Syringe
- Scissors
- Piece of Whatman paper
Soak the upper gum and the lower diffuser from the glue... For this we use a syringe filled with acetone.
Peel off the upper membrane with a sharp knife, while gradually moistening with acetone. We do the same with the lower diffuser.
We unsolder contacts using a soldering iron.
Unscrew the central bolt and carefully extract everything.
If the coil winding is not intact, then you need to turn to the rewinder.
Wipe the coil from metal droplets and debris.
Need to rub around the core... For this we use double-sided tape. We glue it on a piece of narrow cardboard and try to collect the dirt inside.
Need to check, so that the core is strictly centered... It is necessary to clearly center the coil during installation.
Therefore, during installation, the upper speaker will interfere with us, which also needs to be unsoldered.
My speaker rustled due to the fact that the inner part of the coil touched the core. (the trail is clearly visible in the photo).
Centering with photo film... The foil must be wrapped around the core so that it is no more and no less than it.
We carefully put it there so that later you can get it.
We clean the surfaces from glue and apply a new layer of glue... First, lower it to the lower part, where the membrane is located, and once again check the centering using a battery. When the contacts close, the diaphragm should retract.
Leave the glue to dry and check that the membrane is pressed. We do not touch the membrane so as not to knock off the centering.
Further glue the upper part. Apply glue and press for a day. For this I used a saucer, ideally matched in diameter, a paint can and my wife's flower 🙂
After drying take out a photo film and checkso that there is no rubbing when pressed.
After soldering everything back.
As a result, I saved on acoustics 2600 RUR
Loudspeaker repair video
Has the speaker wheezed or stopped sounding and want to bring it back to life? First, diagnostics. We remove the speaker, disconnect the wires from the terminals, having previously marked the polarity. In the future, we adhere to this rule: everything that we disassemble, draw or photograph will help a lot.
We check the winding resistance with the device. There are three options here.
1) Break.
2) Nominal resistance.
3) Reduced resistance.
Now the second check. We put the speaker on the magnet and gently move the diffuser up and down. If you hear a rustle or creak, or there is no movement, the speaker will have to be disassembled.
If there is no grinding, and the winding is open - you need to check the conductivity of the flexible wires from the terminals to the soldering of the winding. They are made of threads intertwined with copper veins that break over time. They can be replaced without disassembling the speaker with M.G. T.F. a suitable cross-section or braid tape to remove excess solder.
We solder the wires so that they do not stretch when the diffuser moves and do not touch it. We glue the place of soldering with Moment glue.
If the speaker needs to be disassembled, disconnect the wires from the terminals, put the speaker on the magnet and with a swab dipped in acetone, soften the glue around the protective cap and remove it, prying it off with a non-sharp scalpel. In the same way, peel off the outer edge of the diffuser and the outer edge of the centering washer. Carefully pull the diffuser straight up without skewing.
I do not recommend unsticking the coil frame from the diffuser and centering washer, so as not to disturb the centering of the speaker.
To rewind, you need to assemble a simple device, the device of which is clear from the figure. The hardest part is the spool holder. To make it, you need to contact a turner. Mandrel length 100-150 mm, material - any metal.
We measure the inner diameter of the coil (x). The mandrel for the spool should have a diameter of x + 0.5 mm at one end and x-0.5 mm at the other end.
On the large end, we drill a 3.2 mm hole and cut an M4 thread for attaching the handle.
We drill a 6.5 mm through hole for the stud. The surface of the mandrel must be sanded.
Now you can start winding. We need alcohol-based glue, for example, BF-2 or BF-6, paper from the MBM capacitor, wire and a lot of patience.
We dilute the glue with alcohol. We pierce the centering washer with a needle, thread the winding wire and solder it to the flexible wire. We fix the wire at the soldering point and at the beginning of the winding by gluing pieces of paper.
If the coil frame is made of metal, we glue it with a layer of paper from the capacitor without overlapping layers. We wind the wire coil to coil, gluing it before winding and over it. Remove excess glue with your finger. We try to wind not tightly, but tightly.
On the first layer we glue the paper from the capacitor without overlapping layers and perform the same actions in reverse order. When the winding is ready and soldered to the terminals, you need to connect them to a 4-5 Volt power source with a current of 1-2 Amperes to dry. The winding will heat up to 50-60 degrees, while the glue will dry and harden, the coil will expand slightly. This will help to easily remove it from the mandrel.
We check the free play of the coil in the speaker gap and start assembling.
We need to align the coil exactly to the center. There are 2 ways to do this.
1) Place a film or X-ray film gasket in the gap.
2) Apply a small constant voltage of 2-3 Volts to the coil so that it is slightly pulled inward.
Apply a layer of Moment glue to the outer edge of the diffuser and the outer edge of the centering washer and lower the diffuser vertically downward without skewing and without radial displacement, press. You can turn the speaker over onto a flat table and while the glue dries, solder the wires to the terminals.
After the glue dries, remove the gasket and check the free play of the coil in the speaker gap.
If everything is in order, we glue the protective cap in place and enjoy the result!
Are the speakers wheezing? Do not rush to throw them away, getting rid of the wheezing of the speakers is possible and not so difficult. Speaker wheezing, a fairly common phenomenon, is most often found in broadband acoustics, due to dust and all kinds of debris trapped between the core and the coil, which, when moving the speaker cone, causes an unpleasant sound in the form of a speaker wheezing. Speaker repair consists in disassembling the speaker and removing the source of the unpleasant sound.
A wheezing four-way coaxial speaker from Pioneer was repaired. The main tool for disassembling the speaker, a regular, flat screwdriver and a soldering iron.
First of all, I removed the buzzer module. In this model, the buzzer module was fastened with a long bolt, which was hidden under the magnet sticker. On other models, the tweeters can be simply glued, in which case they need to be ripped off, but before that, if possible, unsolder the wires going to the tweeters.
In the lower photo, if you look closely, you can see debris between the metal core and the sound winding.
After the tweeter module was unscrewed and the wires were soldered from it, armed with a screwdriver, he forged the plastic cover that presses the rubber suspension of the diffuser and carefully, slowly, was peeled off.
With the same tool, I peeled off the diffuser suspension. With a screwdriver, it is enough to pry it off a little, then you can peel it off with your hands.
I unsoldered the wiring to start peeling off the centering washer.
Peeling off the centering washer is a little more difficult than the previously peeled off parts, you cannot rush here, it is easy to damage the washer.
There was a lot of debris inside the speaker, no wonder it was constantly wheezing.
On the voice coil of the speaker, scratches are visible, proving the presence of foreign objects, the insulation of the winding is damaged. The protective layer of the winding, it is desirable to restore, for this you can open it with varnish or epoxy resin over the scratches, with a small layer.
We clean, wash, vacuum all parts of the speaker.
Well, now the most difficult thing that had to be faced with the repair of speakers is the removal of metal particles magnetized to the core. A vacuum cleaner cannot cope with them. Scotch came to the rescue, with the help of just such not cunning actions, everything that was superfluous in the dynamics was removed.
Then it was necessary to glue everything into place. I glued the speaker with ordinary, universal glue. Moment.
I did not remove the old traces of glue, since it is easy to navigate along them when gluing the speaker, which allows you to glue it correctly and without distortions. But all the same, you need to check if the winding clings to the core when the diffuser moves.
If everything went well, there is no extraneous noise when the diffuser moves, we add it, solder it, assemble the speaker.
Refurbished speaker, pictured on the right. The speaker repair was successful, everything works and does not wheeze.
There is absolutely nothing in disassembling the speaker, there is nothing complicated, everything is simple and easy, the main thing is not to rush. It took me about an hour to repair one speaker.
Today, the number of good sound lovers who just throw out a wheezing speaker is not decreasing! At the same time, the cost of an analogue can be a tangible amount. I think the following will help anyone who has hands that grow out of the right place to fix the speaker.
Available - a miracle of design thought, once the former column S-30 (10AC-222), now serving as one of the autosubs. A week later, after the mutation, the patient began to show signs of the disease - he emitted extraneous sounds when working out the bass parts, and wheezed a little. It was decided to conduct an autopsy.
After autopsy, a diseased organ was removed from the patient's body - woofer 25GDN-1-4, 86 of release. The organ clearly needed operation - when gently pressing the diffuser, an extraneous sound was heard (very similar to a quiet click), and when ringing in various tones (generated by the nchtoner program), a clearly audible rattling-crackling sound was heard with a large diffuser stroke and when ultra-low (5-15Hz) ) frequencies. It was decided to trepan this organ
First, the patient's flexible lead wires were sealed off (from the side of the contact pads)
Then a solvent (646 or any other capable of dissolving glue, such as "Moment") was moistened with a syringe with a needle to the place where the dust cap and the diffuser were glued (along the perimeter).
... the place where the centering washer is glued to the diffuser (around the perimeter).
... and the place where the diffuser itself is glued to the basket of the diffuser holder (again around the perimeter)
In this state, the speaker was left for 15 minutes with periodic repetition of the previous three points (as the solvent was absorbed / evaporated)
Attention! When working with a solvent, you should observe safety measures - avoid contact with skin (work with rubber gloves!) And mucous membranes! Do not eat or smoke! Work in a well ventilated area!
When wetting, use a small amount of solvent, avoiding getting it on the gluing area of the coil and the centering washer!
Depending on the type of solvent and air temperature, after 10-15 minutes of the above operations, using a sharp object, you can gently pry off the dust cap and remove it.The cap should either come off very easily or offer very little resistance. If you need to make significant effort, repeat the operations with wetting its edges with a solvent and waiting!
After peeling off the cap, carefully pour out the remaining solvent from the recess near the coil mandrel (by turning the patient over).
By this time, the centering washer has time to peel off. Carefully, without using any efforts, we separate it from the basket of the diffuser holder. if necessary, re-wet the gluing site with a solvent.
Wet the place where the diffuser is glued to the diffuser holder. We wait. Wet again and wait again. After about 10 minutes, you can try to peel off the diffuser. Ideally, it should detach from the diffuser holder (together with the coil and centering washer) without effort. But sometimes he needs a little help (the main thing is accuracy! Do not damage the rubber suspension.)
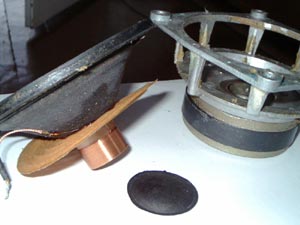
We clean the gluing points from the old glue and dry the disassembled speaker. We examine the disassembled patient for a malfunction. We look at the coil. If there are no scuffs and loose turns on it, we leave it alone. When peeling off the coil, glue it back with a thin layer of BF-2 glue.
We carefully inspect the place where the lead wires are attached to the diffuser. So it is - the patient has the most common malfunction in old speakers with a large diffuser travel. The lead wire at the attachment point is frayed / broken. What kind of contact can we talk about when everything hangs on a thread passed into the center of the wiring!
Gently bend back the copper "antennae".
... and solder the lead wires.
We repeat the operation for the second wiring (even if he is still alive - the disease is easier to prevent!)
We cut the supply wiring at the break point.
... and we serve the resulting ends (of course - first we use rosin). Here you need to be careful! Use a small amount of low-melting solder - the solder is absorbed into the wire like a sponge!
Gently solder the wiring into place, bend the copper "antennae" and glue (Moment, BF-2) the place where the wiring adheres to the diffuser. Remember - you cannot solder the wires to the fastening "antennae"! Otherwise, how can the wiring be changed again in ten years?
We collect the speaker. We put the diffuser with the entire “household” into the diffuser holder, orienting the wiring to the places of their attachment. Then we check the correctness of the polarity - when connecting a 1.5V AA battery to the terminals, when connecting the “+” battery to the “+” of the speaker, the diffuser will “jump out” of the basket. We put the diffuser so that its “+” lead wire is at the “+” mark on the speaker basket.
We solder the lead wires to the contact pads. Please note that the length of the wires has decreased by almost half a centimeter. Therefore, we solder them not as it was at the factory - to the hole in the plate, but with a minimum margin to maintain the length.
We center the diffuser in its basket using photographic film (or thick paper), which we place in the gap between the core and the coil. The main rule is to place the centering evenly around the perimeter, to maintain the same gap. The amount (or thickness) of the centering should be such that when the diffuser is slightly protruding outward, it freely rests on it and does not fall inward. For the 25GDN-1-4 speaker, 4 pieces of film are enough for this, placed in pairs in front of each other. The length of the film should be such that it does not interfere if you put the speaker on the diffuser. For what - read below. We glue the diffuser. We use the indication for the glue used (I recommend "Moment", the main selection criterion, so that the glue can be subsequently dissolved with a solvent).I usually stick out the diffuser 1-1.5 cm up so that the centering washer does not touch the basket of the diffuser holder, then I apply a thin layer of glue on it and the basket with a brush, wait and firmly push the diffuser inside, additionally press the washer against the basket around the perimeter with my fingers ... Then I glue the diffuser (in the retracted state, without skewing).
We leave the speaker upside down for several hours under load (this is why our film should not protrude beyond the plane of the diffuser!).
Then we check the speaker for correct assembly. We take out the centering and carefully check the diffuser travel with our fingers. It should walk easily, without emitting overtones (there should be no touching of the coil and core!). We connect the speaker to the amplifier and send low-frequency tones of low volume to it. Extraneous sounds should be absent. In case of improper gluing (misalignment, etc.), the speaker must be glued (see above) and reassembled, being careful! With a high-quality assembly, we get 99% of a fully working speaker.
We glue the edge of the dust cap with glue, wait and carefully glue it to the diffuser. Here you need accuracy and precision - a crookedly glued cap does not affect the sound quality, but it spoils the speaker's appearance very much. when gluing, do not press on the center of the cap. It can bend from this and you will have to peel it off, straighten it, coat it from the inside with a thin layer of epoxy for strength and stick it back.
We wait until all parts are completely glued together (about a day) and put the finished speaker in its place. We enjoy the sound, which is no worse than that of the new factory analogous speaker.
That's it, now you can see that fixing a speaker is an easy task. The main thing is slowness and accuracy! So in an hour, you can slowly repair almost any woofer or midrange speaker of domestic or foreign production (for gluing imported speakers, a more powerful solvent is often required, such as acetone or toluene, carefully - they are poisonous.) Having a similar defect.
Yes, after the operation, the former patient got a second wind and the cheerful yellow subs continue to do their hard bass work:
Speaker systems can be active or passive. Internally, they have different microcircuits used to process audio.
In order for the sound to be of high quality, many devices are used to reproduce it. But all these devices cannot be seen with the naked eye, since they are located inside.
But everyone who owns them should know how the repair of loudspeakers takes place. Repair of acoustic buttons and other elements can be done with your own hands, if you know the speaker device.
In our case, we will consider the situation when the speaker speakers stopped working. You need to purchase special glue in advance, which may be needed during the repair process.
In general, any quick-drying glue you can find will do. It may just happen that during dismantling you will have to disassemble the glued joints. After that, they will need to be collected back somehow.
Before you start repairing your loudspeakers, you should know how the system works. This is necessary in order not to harm her in the process of performing certain actions.
Despite the size of the speaker, it has two components: mechanical and electrical. The first includes an induced current coil.
The second contains a magnet and a special membrane. At first glance, this mechanism seems to be simple, but it is not.
For this, you may need a speaker classification:
- Reel to reel. Their principle of operation resembles the operation of a gas water heater (used to heat water). The ring of the magnet makes it move due to the formation of current in it.
Note: the device will work as long as all the turns of the coil are intact. Therefore, if the coil speaker does not work, then first of all you should pay attention to the integrity of the coil.
- Tape. In this case, the variable magnet is a narrow corrugation.
At the same time, there is no coil inside, as in the previous version. To use such a device, you must purchase matching transformers in advance, which must be connected to the circuit.
Most often, these transformers are already installed from the factory.
Note: it is their presence or absence that allows you to quickly find out the type of speaker.
- Isodynamic, which include a square or round spiral. It carries out circular movements together with the membrane, being under the influence of a magnetic field.
- Electrostatic speakers. Their main difference is that they work without any movement. The current is initially already in the circuit, so you do not need to take any action for it to be formed.
In this case, the membrane moves a little, but it does not perform any translational movements.
Note: They are ideal for high-frequency speakers.
- Capacitor, which includes two electrodes. One of them is quite massive, since it performs an important function - the supply of variable potential.
It acts as a support for the second electrode. By the way, instead of the second, you can use a foil twisted into a thin tube. - There are also other types of speakers, but only the most popular and common ones were considered.
The speakers work as follows:
- Thin wires go to the cap located on the membrane. The cap itself is attached with a diffuser.
So these wires pierce it so that they have access directly to the cap. - The coil should be light, as it is necessary to achieve low inertia in the system. After all, the frequency of oscillations in the dynamics is enormous, therefore, in order to move at such a speed, the moving part of the speaker does not have to be heavy.
- The magnet is stationary. Most often it is in the shape of a ring. A coil with an induced current is located in the hole.
As a rule, it moves back and forth. It also sets in motion a membrane with a cap.
The connecting wires are also in constant motion. So that the moving parts do not move from their place, in the center they are connected with a special washer, which helps to ensure that the axis of symmetry is not violated.
Speaker repair is a fairly straightforward process. The cap and membrane rarely break.
Most often, the coil fails. You should also check the soldering points of the wires, since it is possible that one of them has come off.
Coil repair is as follows:
- The old turns should be removed.
- Wrap inductance on the coil as it was on the old one.
- Each layer should be carefully greased with glue so that the turns are not moving.
Note: it is because of the high mobility that the turns can break. Therefore, you need to do everything possible to ensure that they are fixed in the best possible way.
- The wire can be wound in any convenient way. The simplest option is to take two racks.
Place them parallel to each other and connect with an axis. Place the core on one side and the store wire on the other. The wiring should be wound quickly until the glue is dry.
Note: the wire must be lacquered.
First, it will improve its quality, so it will not rip as quickly. And secondly, it will be less likely that a short circuit will occur in the system.
- The coils fall on top of each other. In this case, it is necessary to ensure that there is a sufficient number of revolutions.
In addition, you need to correctly place the conclusions.
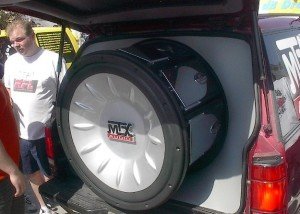
Acoustic speaker in the car
![]() |
Video (click to play). |
Quite often, in the process of repairing loudspeakers, you have to disassemble the speakers. Therefore, you should stock up on solvent before starting repairs.
All glued joints must be moistened with glue and wait a while. Particular attention is paid to cleaning the joints.
Thus, you can do the repair of speakers with your own hands, without leaving your home. Initially, you need to purchase glue, the price of which is scanty.
Before starting the repair yourself, you also need to review the photos and videos with this topic, of which there are a lot on the Internet. Instructions on this will also come in handy.