In detail: do-it-yourself speaker repair broke from a real master for the site my.housecope.com.
In general, the story is this: I drive myself and am glad, there was a bad rattling. A cursory examination of the rear of the passenger compartment did not give any result. Traveled like this for probably a month, from time to time trying to find a source of irritating sound. Interestingly, the more you focus on this, the louder and more irritable it seems. In general, on the next outing into nature, I accidentally climbed into the trunk and discovered the cause of emotional disorders.
More about breakage: Clarion speaker rated 15W (maximum 30). Produced, oddly enough, in china. The membrane has a rubber suspension, it was she who came off the edge along the circumference. The size of the gap is approximately 5-7 cm.
If someone had to reanimate such speakers, share your experience. I will try to remove and glue it myself with rubber glue, you may have to glue a reinforcing pad (also rubber). If it does not work, then you will have to buy a new one, but I am afraid that one may not be sold to me and, perhaps, the size will not fit (or the mounting holes will not match).
The current state of the market with loudspeaker prices makes speaker repair virtually unnecessary, but if there are difficulties in purchasing a new speaker instead of a damaged or damaged one, then it makes sense to try to restore the damaged loudspeaker with your own hands. I got a few coaxial speaker systems from various cars. Unfortunately, 2/3 of the speakers produce a distorted signal during playback, and the rest simply do not work. Below will be presented material only on the restoration of "littered" coaxial-type car speakers for use in the future in the design or installation in multi-way stationary speaker systems. Before starting work, we will carry out diagnostics speaker states.
![]() |
Video (click to play). |
1. Check for "trash". Coaxial speakers are not fully protected from foreign objects falling into the magnetic gap, this is especially dangerous for old cars covered with rust or cars that have undergone body repairs. Checking is simple - gently with your fingers moving diffuser inside the magnetic system, if at the same time extraneous sounds are clearly audible: rustles, crackles, rattling, then this means that metal debris may have got into the magnetic gap.
2. We take a tester and in ohmmeter mode we check the resistance of the coil. If there is resistance, then this is our case. If there is no resistance, then it makes sense to check the thick flexible copper conductors from the speaker terminals to the diffuser for an open circuit. If there is no break, then most likely there is a break in the speaker coil and this case of self-repair is not considered in this article. Instructions for self-repair are given below.
1. We unsolder the flexible leads of the coil from the contact lugs of the speaker connection and the contact lugs of the coaxial speaker.
2. Remove the coaxial speakers. Repair of the speaker system is not provided by the manufacturer and coaxial speakers are installed tightly... The column with reinforced tweeters was removed by drilling an aluminum rivet. We work carefully, the main thing is not to tear or damage anything.
3. On the forums for repairing speakers, there are ways to dismantle the diffuser and centering washer. I also went along this path. We carry out work in the open air in the absence of open fire sources! After spending 100 ml of acetone, it was not possible to peel off the diffuser and the washer. The solvent evaporated quickly without softening the glue line.In order to save time and solvent, a cord made of cotton cloth was placed in place of gluing and moistened with acetone; if necessary, moistening as it evaporated continued until the glue softened. After softening with a thin screwdriver, he forged the edge of the centering washer and lifted it over the gluing point. With the corrugation of the diffuser made of thin rubber, you need to be more careful and delicate so as not to damage the rubber.
Pouring solvent onto the corrugation
4. Remove the diffuser. From debris that got inside the magnetic system, damage-scuffing of the insulation of the speaker coil is noticeable. It is useful under a magnifying glass to see the degree of damage for the presence of short-circuited turns (scratches to a depth of more than 40% of the coil wire diameter), if there is a suspicion of short-circuited turns, then it is better to reject the speaker. Using a damp cloth, I cleaned the diffuser, centering washer and coil inside and outside from dirt. Cleaning should be done carefully so as not to damage the coil.
There are scratches on the coil
5. The gap in the magnetic system is a sad sight. Strong magnet holds fine metal debris and dust firmly. I tried to clean it mechanically, but the small size of the gap and its curvature did not allow successfully removing debris. Decided to use a strong blast of air from an air compressor - it was not possible to clear the gap! Another remedy had to be used - a high-pressure jet of water from a car wash. The result is that I am all wet, but the gap is 100% cleared, and at the same time the whole frame of the frame shone like new. I tried to do it carefully, since the pressure of the water jet is very high and I suppose with special zeal it is possible to destroy the gluing of the speaker magnet. To prevent rusting, you must immediately dry the frame and magnet. After drying, it is useful to check the cleanliness of the gap under a magnifying glass. And as experience has shown, it is good to seal the gap with tape to protect it from accidental metal debris.
1. After cleaning and drying the speaker components, we assemble the structure. It's important not to rush. The goal is to position the coil in the magnet system exactly in the center and to ensure there is clearance and no touching the coil. From a strip of A4 format office paper 10 cm wide and about 18 cm long, we roll up the cylinder and insert it into the diffuser coil. The cylinder must fit snugly against the spool and not have any protrusions or bulges inside.
2. Let's try to insert such a structure into the magnetic system. Do not hurry! Better to practice a few times. The cylinder should sink to the full depth of the magnetic gap, and the coil should hardly move over the inserted cylinder. If the coil moves along the cylinder with great effort, then it is necessary to shorten the length of the paper strip, and if the coil moves freely, then it is necessary to increase the length of the paper strip.
Insert the cylinder into the gap
The coil runs tightly in the cylinder
The reel is centered
3. Holding the cylinder in the lower position, raise the diffuser and grease the area for gluing the centering washer with glue of the "Moment" type. We orient the washer according to the leads of the coil conductors and speaker terminals, as well as along the cutouts in the corrugation of the diffuser. We glue the centering washer.
4. We glue the corrugation of the diffuser.
5. After the glue has dried, we solder the coil conductors to the terminals.
6. Carefully remove the paper cylinder. Checking the diffuser travel. If everything is done correctly, then there should be no extraneous sounds.
7. To close the magnetic system from the ingress of debris, I sealed the coil hole on the side of the diffuser with black spunbond, and on the side of the magnet with tape.
Glue the centering washer
Sealing the diffuser hole
Seal the hole with tape
8. Finally, we check the result of the work by connecting the speaker to the sound source.
Using this technique, several speakers were independently restored for installation in stationary speaker systems and radio receivers to replace old or torn speakers.
I tried to collect this way. It didn't always work out.
I did the assembly differently. After gluing the corrugation of the diffuser and the centering washer, until the glue has dried, I connected the dynamic head to a 6.3 volt transformer through a low-resistance variable wire resistor.
It was enough to slightly stir the diffuser.
In this case, the diffuser itself is centered. The noises disappeared immediately. In this position, he dried.
The disadvantage of this method: 50Hz is still hard to withstand for a long time.
The constant must be connected!
Professionals - a must, but amateurs can do so!
Today, the number of good sound lovers who just throw out a wheezing speaker is not decreasing! At the same time, the cost of an analogue can be a tangible amount. I think the following will help anyone who has hands that grow out of the right place to fix the speaker.
Available - a miracle of design thought, once the former column S-30 (10AC-222), now serving as one of the autosubs. A week later, after the mutation, the patient began to show signs of the disease - he emitted extraneous sounds when working out the bass parts, and wheezed a little. It was decided to conduct an autopsy.
After autopsy, a diseased organ was removed from the patient's body - woofer 25GDN-1-4, 86 of release. The organ clearly needed operation - when gently pressing the diffuser, an extraneous sound was heard (very similar to a quiet click), and when ringing in various tones (generated by the nchtoner program), a clearly audible rattling-crackling sound was heard with a large diffuser stroke and when ultra-low (5-15Hz) ) frequencies. It was decided to trepan this organ
First, the patient's flexible lead wires were sealed off (from the side of the contact pads)
Then a solvent (646 or any other capable of dissolving glue, such as "Moment") was moistened with a syringe with a needle, the place where the dust cap and the diffuser were glued (along the perimeter).
... the place where the centering washer is glued to the diffuser (around the perimeter).
... and the place where the diffuser itself is glued to the basket of the diffuser holder (again around the perimeter)
In this state, the speaker was left for 15 minutes with periodic repetition of the previous three points (as the solvent was absorbed / evaporated)
Attention! When working with a solvent, you should observe safety measures - avoid contact with skin (work with rubber gloves!) And mucous membranes! Do not eat or smoke! Work in a well ventilated area!
When wetting, use a small amount of solvent, avoiding getting it on the gluing area of the coil and the centering washer!
Depending on the type of solvent and air temperature, after 10-15 minutes of the above operations, using a sharp object, you can gently pry off the dust cap and remove it. The cap should either come off very easily or offer very little resistance. If you need to make significant effort, repeat the operations with wetting its edges with a solvent and waiting!
After peeling off the cap, carefully pour out the remaining solvent from the recess near the coil mandrel (by turning the patient over).
By this time, the centering washer has time to peel off. Carefully, without using any efforts, we separate it from the basket of the diffuser holder. if necessary, re-wet the gluing site with a solvent.
Wet the place where the diffuser is glued to the diffuser holder. We wait. We wet again and wait again. After about 10 minutes, you can try to peel off the diffuser. Ideally, it should detach from the diffuser holder (together with the coil and centering washer) without effort. But sometimes he needs a little help (the main thing is accuracy! Do not damage the rubber suspension.)
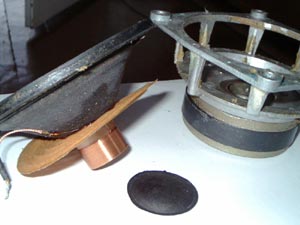
We clean the gluing points from the old glue and dry the disassembled speaker. We examine the disassembled patient for a malfunction. We look at the coil. If there are no scuffs and loose turns on it, we leave it alone. When peeling off the coil, glue it back with a thin layer of BF-2 glue.
We carefully inspect the place where the lead wires are attached to the diffuser. So it is - the patient has the most common malfunction in old speakers with a large diffuser travel. The lead wire at the attachment point is frayed / broken. What kind of contact can we talk about when everything hangs on a thread passed into the center of the wiring!
Gently bend back the copper antennae.
... and unsolder the lead wires.
We repeat the operation for the second wiring (even if he is still alive - the disease is easier to prevent!)
We cut the supply wiring at the break point.
... and we serve the resulting ends (of course - first we use rosin). Here you need to be careful! Use a small amount of low-melting solder - the solder is absorbed into the wire like a sponge!
Gently solder the wiring into place, bend the copper "antennae" and glue (Moment, BF-2) the place where the wiring adheres to the diffuser. Remember - you cannot solder the wires to the fastening "antennae"! Otherwise, how can the wiring be changed again in ten years?
We collect the speaker. We put the diffuser with the entire “household” into the diffuser holder, orienting the wiring to the places of their attachment. Then we check the correctness of the polarity - when connecting a 1.5V AA battery to the terminals, when connecting the “+” battery to the “+” of the speaker, the diffuser will “jump out” of the basket. We put the diffuser so that its “+” lead wire is at the “+” mark on the speaker basket.
We solder the lead wires to the contact pads. Please note that the length of the wires has decreased by almost half a centimeter. Therefore, we solder them not as it was at the factory - to the hole in the plate, but with a minimum margin to maintain the length.
We center the diffuser in its basket using film (or thick paper), which we place in the gap between the core and the coil. The main rule is to place the centering evenly around the perimeter, to maintain the same gap. The amount (or thickness) of the centering should be such that when the diffuser is slightly protruding outward, it freely rests on it and does not fall inward. For the 25GDN-1-4 speaker, 4 pieces of film are enough for this, placed in pairs in front of each other. The length of the film should be such that it does not interfere if you put the speaker on the diffuser. For what - read below. We glue the diffuser. We use the indication for the glue used (I recommend "Moment", the main selection criterion, so that the glue can be subsequently dissolved with a solvent). I usually stick out the diffuser 1-1.5 cm up so that the centering washer does not touch the basket of the diffuser holder, then I apply a thin layer of glue on it and the basket with a brush, wait and firmly push the diffuser inside, additionally press the washer against the basket around the perimeter with my fingers ... Then I glue the diffuser (in the retracted state, without skewing).
We leave the speaker upside down for several hours under load (this is why our photographic film should not protrude beyond the plane of the diffuser!).
Then we check the speaker for correct assembly. We take out the centering and carefully check the diffuser travel with our fingers. It should walk easily, without emitting overtones (there should be no touching of the coil and core!). We connect the speaker to the amplifier and send low-frequency tones of low volume to it. Extraneous sounds should be absent. In case of improper gluing (misalignment, etc.), the speaker must be glued (see above) and reassembled, being careful! With a high-quality assembly, we get 99% of a fully working speaker.
We glue the edge of the dust cap with glue, wait and carefully glue it to the diffuser. Here you need accuracy and precision - a crookedly glued cap does not affect the sound quality, but it spoils the speaker's appearance very much. when gluing, do not press on the center of the cap. It can bend from this and you will have to peel it off, straighten it, coat it from the inside with a thin layer of epoxy for strength and stick it back.
We wait until all parts are completely glued together (about a day) and put the finished speaker in its place. We enjoy the sound, which is no worse than that of the new factory analogous speaker.
That's it, now you can see that fixing a speaker is an easy task. The main thing is slowness and accuracy! So in an hour, you can slowly repair almost any woofer or midrange speaker of domestic or foreign production (for gluing imported speakers, a more powerful solvent is often required, such as acetone or toluene, carefully - they are poisonous.) Having a similar defect.
Yes, after the operation, the former patient got a second wind and the cheerful yellow subs continue to do their hard bass work:
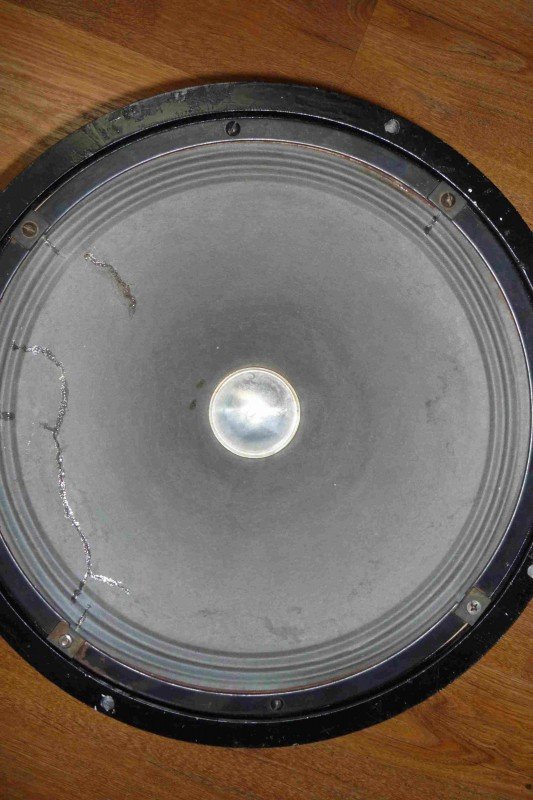
Bonding the subwoofer is possible, do not throw it away right away
How to glue the speaker of a subwoofer, if you find a hole in its diffuser (there are many reasons and carelessness and the children played pranks and more), do not rush, throw out the old one, look for a new speaker to replace it. Such damage can be easily and successfully repaired without the consequences and noticeable changes in the subwoofer speaker operation.
How to glue the subwoofer if there is a problem, now we will help.
The first question in this case is what to do - to glue, how to glue, what kind of glue is needed for the subwoofer - rubber, elastic, for example, "88th" or "Moment". Without panic, everything is fixable, you can save money, without losing sound quality, let's do everything in order.
To carry out a simple repair, you only need the following tools:
- A tube of glue "Moment"
- Thin cardboard (ideally electric cardboard, it is stronger)
- Matching screwdriver
- Sharp comfortable scissors
- Regular hair dryer
Note: Use rubber glue to glue the subwoofer, no quick dry moments are recommended.
Having assembled a simple repair kit, let's get down to business:
- Disconnect the subwoofer from the amplifier, remove the grill from the speaker with a screwdriver and unscrew the fixing screws from the speaker, carefully remove the speaker from the case, disconnect the acoustic wires
- We inspect the condition of the speaker diffuser, we immediately make sure that the leads from the voice coil were not damaged
- Using scissors, cut out a patch from thin cardboard, such that it blocks this hole by a centimeter in either direction
- You don't have to look for electric cardboard, almost any will do, you can even use a cardboard box for sweets
- It often happens that the shape of the diffuser is formed by the so-called double curvature surface
- Then you need to make two or three patches that need to overlap one to the other.
- Align the edges of the damaged part on the diffuser, impregnate the back side with Moment glue, diffuser material, wait a little for the glue to dry
- Prepare cardboard patches in advance, then liberally moisten the damaged area on the diffuser on the reverse side with glue, then immediately apply patches, our goal is to saturate the parts to be joined with glue
- Then we immediately remove the patches from the diffuser, without removing them, you need to wait 20-30 seconds, then attach both patches back
- On the reverse side, press them against the diffuser, placing a roller of cotton wool or padding polyester inside the speaker basket
- It is necessary to ensure that the diffuser does not immediately bulge in the place of gluing, which means that you need to select the optimal pressure for pressing the patches in order to maintain the initial shape of its diffuser
- After a day, we remove the supported support roller from the speaker basket, inspect how well the connection is glued
- If you notice areas that are not glued, then bring the tube of glue to the gap, and gently press on the tube and squeeze a drop of glue into it.
- The main goal is to disappear bounce when the speaker is working
- With a hairdryer, carefully heat the glue seam until the glue boils, remove the hair dryer and squeeze the gluing place with your fingers
- Hold for at least a minute, after which the glue will set tightly and will hold the patch
- Gently move the diffuser in and out to make sure that it does not hit the magnet on the coil when it moves.
- If necessary, replace the sealing gum, connect the speaker cables to the speaker back and install the speaker in place
- As you can see, the subwoofer is not so difficult to glue.
- Then you need to do a test switch-on at a low volume to make sure that there is no bounce during operation.
- Then we smoothly increase the volume to the maximum, listen carefully for the appearance or absence of any extraneous overtones
- If no extraneous sounds are found, you can return the grill to its place.
That's all, in my opinion, everything is clear without video.
As a rule, there are more speakers in the audio system, so the instructions for gluing them will come in handy:
- If your speaker starts to give out extraneous noise, it means that it could leak from time to time.
- To glue the speaker, it is enough to purchase Moment glue (“subwoofer glue” and “speaker glue” does not exist) and take a piece of cloth or bandage
- And if its damage is significant, then you cannot do without a soldering iron
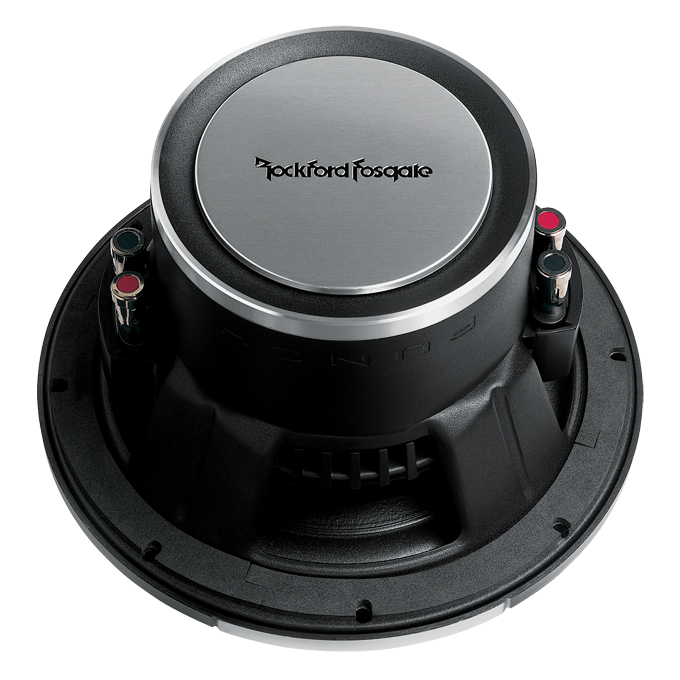
To repair a speaker with your own hands, you need:
- The same glue "Moment"
- A couple of pieces of thin tissue (possibly a bandage) as a last resort toilet paper
- Sharp knife or scalpel
- Tweezers
- Acetone
The procedure for repairing the speaker, photo above:
That's all, you can of course buy a new one if the price is not important to you.
Composite A.Vorobyov. At the same time, soak.
What is there in his line-up, so that the dynamics do not completely change. I was also advised by guerlain, what is the difference?
.There, and the paper is completely different and the sound is also not equal to any 4gd. ,
But the price of your problem is 500 times higher, I buy 4gd35 for 5-10 UAH maximum. And whether the sound is better than your royal speaker, at least 100 times, is the question.
And as soon as you intervene, with treatment, in the construction of the diffuser, it will sound 100 times worse, and then its price will be 5 UAH.
So a big ship has a great voyage, if you want “the sound is also not equal to any 4gd. "- this one, throw it away as a" match ", and buy another" not equal ".
Otherwise, horror you will equal and become "equal to everyone 4gd. "
Of course 4gd-35 (4gd-36) is not Klangfilm, Telefunken or Fosteks: D, but quite a good, self-sufficient shirik deserving the respect of an audiophile, despite its humped frequency response: D Anyway, it will surpass many modern bookshelf speakers in sound! And as for the Chinese consumer goods, I just do not say anything at all: beer:
Of the impregnations, I used only guerlain - the result is good, but the most important thing is not to overdo it! To soften suspensions - vodka combined with a sinusoid of 50-60 Hz (below it will kill him!) From the bass generator, naturally at a moderate volume: D
Regarding the gluing of torn diffusers, I cannot say for sure myself until I was involved in this process. Although one friend of mine - advises to seal the "vomit" with a strip of tissue (cigarette paper) on PVA - it seems to be light and strong! I haven't tried it myself - I can't say that I can ((Maybe someone has heard about this method.
Guys tell me: there is a 100GDN speaker, completely new, but the problem is that the diffuser is torn in two places And it is also half-torn in diameter from the rubber on which it vibrates, can it be glued and how will the sound become worse or not after its repair? but with a defect. How to be ??

can be glued with latex, but it will not become new
Sound change or not.

The doctor said to the morgue means to the morgue.

Wherever possible, there is glue. Moment, but not super, in other cases a good adhesive plaster on both sides, or a wide cloth tape "under the mettalik"
BF-2 alcohol glue (not on acetone). Describe in more detail how the torn is torn off? Is the edge left intact or part of it remains on the rubber? Are the gaps big? If it is carefully glued and the coil is not deformed, then the sound quality will not change (for this speaker).
SergdeParchi, It was torn like this: the edge of the diffuser on the rubber did not remain completely flat (completely intact), and the paper thickness is acceptable, on the diffuser there are breaks (in the direction of the radii) by about 50-60 millimeters, like everything, is it worth taking it or not ?? All the same - this is 100 watts (all my life I dreamed of having it).
FreddyWhy is it so abruptly impudent to shoot, or do you think there is no other way out?
Seal BF-2 with alcohol produced by ANLES JSC, glue small pieces of thin soft paper underneath the gaps. Of course, BF-2 is a harsh glue, but it will not stick to vibrations and the rigidity will be sufficient, besides, tears and repairs will not be noticeable (if the diffuser is light, you can paint it with a marker). When comparing the sound of the repaired speaker (rewinding the coil, sealing the gap) with another whole, I did not notice any difference in sound, since the 100GDN is a rather rough speaker. No extraneous resonances and overtones were observed either.
SergdeParchi, Thank you for the consultation I will glue.
I will say about the result, but the current is in a week.
The materials are simple:
1. gauze, paper.
2. glue moment, quintol. (required elastic)
.. stick on both sides! .. there is only one problem - the appearance.
I took a photo of him, tell me what kind of model it is

I did this: I took the Moment glue, which I didn’t superimpose with pieces of a diffuser from a broken speaker or black paper and glued it. The quality of course will not be named, but as a new one it will not be, but of course you can listen to me during transportation I drove two speakers 35 W 16 Ohm brought them to the right place they broke there were small cracks I glued them two years ago and they are currently working for I'm cool. Good luck.


KaSer, Ay cha something like that were torn or even worse ??
Guys, thanks for the advice, I will certainly seal it. But I would like to know what kind of head brand it is, what power, etc., can anyone come across it ?? ).
LIKE IT'S NOT 100 GDN, it's a shame
telestudent, Something like this on one dimanik and on the second less. Good luck.

PEOPLE WHO WILL TELL WHAT THIS BEAST IS.
Diffuser diameter 270mm,
Speaker diameter 310mm
Ah, handsome! ... it looks like it's not 100GDN. Rather 50GDSH. The diffuser is being treated.

As I understand it is 4A32-6, or I'm wrong.
anything but 4a-32
I would like to do something better, and more power.
So we will determine what kind of model it is. or no ??

rummaging in old reference books on kinap and lomo
if i find anything i will give an answer on monday-tuesday
Certainly not 100gdn, that will be bigger, what is the resistance of the coil? And look approximately the diameter of the wire.
People !! help. I have a 75 gdn speaker, and such a problem: the suspension spilled out

telestudent Is this a laboratory task? The first pancake is lumpy. Would you have about five maybe
Like a broadband 30 watts (small pads for attaching flexible wires)
telestudent Is this a laboratory task? The first pancake is lumpy. Would you have about five maybe
Like a broadband 30 watts (small pads for attaching flexible wires)
I don’t know the brand, clearly not a sub. I had these in the repair, the diffuser is relatively thin and with a large amplitude it breaks in a circle around the ZK. The suspension can be glued with BF-88 glue, and I would not recommend just gluing the diffuser, it must be reinforced with longitudinal strips cut from diff. for example 75GDN-3.
Speakers 75GDN with polyurethane suspension (usually AS Amfiton) quickly lose their suspension in the sun, in a car, in general outside the living room 😥 There is usually almost nothing to restore, and it is not worth it! The simplest way of rescue is a suspension from 35GDN-1 (10GD-30.25GD-26), it is true of a smaller caliber (200mm), so we add an insert. We save three 75GDN with 4 suspensions. Many speakers have already been redone, no complaints!
if the suspension is slightly torn, you can just glue it up and soak it with glue in a moment, and if it's really bad, change the address where the suspensions are made



Hey! maybe it's too late, but I recently saw this forum and I can give a very qualified advice, since I have been repairing speakers for 15 years.
for this speaker is a bass Bulgarian.
The dynamics are the most difficult to repair. Firstly, do not put any latoks - the diffuser hardness changes (and it is very soft), the centering will fly away, it will wheeze.
Glue breaks into the joint and only glue "phoenix" or "urethane".
After drying, iron the seams with something hot, for example, a belt. If you cannot smooth the wrinkled edges, wet them with water,
align, let's dry.
The rest, if it is interesting and necessary, I can write later.
about 75gdn - you can do it but you need experience
anything but 4a-32
this is a speaker from the Bulgarian sound-amplifying equipment "Druzhba"
and in the reference books they are not. Power-40 watts.
igogochik, the speaker still lies in such a state in which it was, listen, as I understood, after looking at the previous link (my corrugation from the diffuser is almost completely unsticked), I need to completely disassemble it and start gluing from scratch ?? Duck is this broadband?
Hello telestudent!
First, it's pure bass.
And secondly, I looked at the photo, and I think that a complete analysis is not necessary. First, check if the coil is intact! Then do the rest.
First, align the crumpled diffuser in some places. To do this, moisten the crumpled places with hot water (about 70 g) with a brush. Just do not flood everything, especially the magnet. When the paper becomes soft, smooth it out carefully with your hands and iron the crumpled seams with something hot. Once dry, glue the tears into the joint with Phoenix or Urethane glue. Never use another.
After the glue dries, it must also be ironed.
I can tell you the rest of the procedure later if I have not lost interest yet.
By the way, I forgot to warn you!
In no case put patches in place of breaks, because. kill the speaker.
Only in the joint, and then impregnate all the crumpled places, then let it dry for a couple of hours and then warm it up again.
After putting the diffuser in order, you can start gluing the corrugation (if I am not mistaken, it is made of molded vinyl)
Here the corrugation can be glued "Moment" only slowly and in sectors, so as not to knock down the centering.
And I glued it with hot glue with a very thin layer. Well, the sound. You want to use it all under the bass?
I have not tried it with hot melt glue, just for a decent period of speaker repair on my own experience
chose several adhesives and could not find replacements for them yet.
BF-2 and Epoxy exclusive 1 for repair and manufacture of coils.
Epoxy exclusive 1-for gluing magnets.
Phoenix, Urethane and can be different if it is based on Dismakol - for repairing diffusers, corrugations and centering washers. The rest of the adhesives either poorly penetrate into the structure of the diffuser, or dunn and burst from strong vibration.
As for the bass driver, it has a very long stroke and if the stiffness of the diffuser changes on one side, then at a power close to maximum it will lose centering and break the coil.
So think.
I forgot, but the Moment glue (not super) is great for gluing the diffuser to the frame.
How good it is sometimes in the summer on the street in a cool gazebo to listen to your favorite tracks ... We got together like that in the summer with a friend sat listening to some drummer on his old S30 Radiotehnika. Surprisingly, the columns, in spite of their already advanced age, were always hollowed out very well. But after a couple of tracks at full power of this ULF, one of the speakers began to wheeze strangely ...
Thinking about what happened, I started looking for the reason in the ULF, disassembled the amplifier and measured all the voltages. Everything turned out to be normal. After that I decided to swap the channels and turned on the sound for the whole ... All the same column with the same effect.I had to repair, by the way, this is not the first speaker repair, I already had experience in repairing the Chinese speaker of the Sven speaker
After the autopsy, it turned out that the inside was GDN 25, which I had previously seen only in pictures on the Internet.
Here is a photo of the speaker of the GDN 25
Having twisted the speaker and examined it from all sides, no defects were found. But then I slightly pressed down the diffuser, I found that the diffuser was torn off from the centering washer, which can be clearly seen in the photo
Rub the diffuser against the core of the magnet and if this nuisance is not eliminated, then in addition to the grinding, which presses on the ear, the sleeve will fray and close the coil, which can lead to the destruction of the ULF. Fortunately, such repairs are carried out very quickly and will not take much effort.
To repair the speaker, we need:
Glue. I used regular rubber, liquid 88 glue
Acetone. I used regular nail polish thinner.
Syringe. For easy bonding of the diffuser
When everything is ready, you can start repairing
You need to remove the dust cap to get to the speaker coil. To do this, you need to slowly soak the edges of the cap with acetone to soak the glue. It is convenient to do this using the same syringe. The photo clearly shows what needs to be done! The photo shows how the solvent has not yet been absorbed.
After the cap is soaked, it is literally 5 minutes, we carefully try to pry it by the edges, only very carefully because the diffuser can be damaged. If the cap does not slip, add more acetone. It should slide easily.
Here is the cap removed
As you can see, the speaker is still damp. He needs to be allowed to dry, literally half an hour is enough for this, this is in the summer and just not in the sun. Drying should be done in the shade and in a well-ventilated place ..
When the speaker is dry, we need to center the speaker. To put it simply, it is necessary to align the sleeve so that it does not touch the core at full speed. This is done using regular film from a camera. If it is not there, you can use an old X-ray photograph, or at worst, as I did, take an ordinary thick thin cover from a notebook.
So you need to twist the film into a tube and insert it between the core and the sleeve
And press down tightly so that the diffuser is well pressed against the washer. Then we collect the syringe with glue, so the thinner the glue, the better
And now we carefully glue the washer with a good layer of glue. Be careful. Hold the needle, because under the pressure of the piston, it sometimes flies out and can get injured.
Stretch out with glue as seen in the photo
After you have stretched it once, look carefully, perhaps there is not enough glue and you need to walk again .. Remember that the quality of your work depends on the quality of the sound and the absence of alterations.
This completes the repair. Once again, check if the washer is pressed tightly and leave the speaker to dry for a day until the glue completely solidifies.
After a day, we carefully take out the centering film and try to connect the speaker for testing. Drive it well and test its strength. If everything is normal, glue the cap back in place and put the speaker in the speaker. This completes the repair
Here are a couple more photos of the speakers Radiotehnika S-30
![]() |
Video (click to play). |
The repair is over. A year has already passed since this speaker works and it still pleases with its sound. Therefore, do not be afraid to repair the speakers and do it with high quality so that you do not have to repeat the repair. And just good luck to you
From SW. Admin check