In detail: do-it-yourself repair of Cummins diesel injectors from a real master for the site my.housecope.com.
- Like
- I do not like
And I just cut out holes in the protection in front of the drain plug and in front of the oil filter with a grinder. Vieste with a sound vibration damper was cut with a bang.
- Like
- I do not like
Good afternoon, I have cummins of 2012, the nozzles are covered, I understood from the forum that you are repairing. If so, how can you ship them, how much will it cost to restore (4 pcs.)? I am in Voronezh.
guys, tell me my mileage is 180 thousand (cummins 2.)
- Like
- I do not like
guys, tell me my mileage is 180 thousand (cummins 2.)
guys, tell me my mileage is 180 thousand (cummins 2.)
empty less than 14 never happens and loaded up to 16 reaches
guys, do not scold me with the GAZ-560 pump injectors, 10 pieces gathered, tell me who does it in early April, is ready to take it away. or send me.
Contact Albert, he will prompt the topic Repair from Albert
- Like
- I do not like
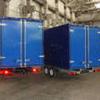
guys here on the site newbie. help (only in a personal). TODAY CHECKED 2 FARSUNKI LYUT AT THE STAND. REPAIR NEEDED. FOR ONE ASKING 6 TR IN YOSHKAR OLE. TE 12T.R. + FLUSHING FUEL SUPPLY SYSTEM. IS IT WORTH REPAIR? About the engines they said that woof. oh he. resource 300 t.km, on native farces more than 190 t.km did not go, at least they did not bring for repairs. What to do?? who will tell you? I decided to take it for repairs, since you can buy a pig in a poke (I'm talking about new farces)
![]() |
Video (click to play). |
passed 152 t.km Lil exclusively lukoil, did not overload, did not heat. I drive myself, it's a shame the car is not 2 years old
- Like
- I do not like
Leha Yurich will help you, he has a phone number in his profile. people checked. fireplaces, of course, shit is excellent, you need to run for umz))) or to another service
- Like
- I do not like
guys here on the site newbie. help (only in a personal). TODAY CHECKED 2 FARSUNKI LYUT AT THE STAND. REPAIR NEEDED. FOR ONE ASKING 6 TR IN YOSHKAR OLE. TE 12T.R. + FLUSHING FUEL SUPPLY SYSTEM. IS IT WORTH REPAIR? About the engines they said that woof. oh he. resource 300 t.km, on native farces more than 190 t.km did not go, at least they did not bring for repairs. What to do?? who will tell you? I decided to take it for repairs, since you can buy a pig in a poke (I'm talking about new farces)
passed 152 t.km Lil exclusively lukoil, did not overload, did not heat. I drive myself, it's a shame the car is not 2 years old
You wrote that it works fine. Buy new nozzles (and do not forget to register them), and repair the old ones in stock. Put, after your filter, a filter that will filter 2 microns (when you called me, I managed to tell you, after which the connection was cut off) .When you install new forces, flush the entire system, fuel. You also wrote that you can share information in a personal on the repair of a stone, it is not accepted here and they communicate on the forum, if I am wrong, the forum will correct me.
Leha Yurich will help you, he has a phone number in his profile. people checked. fireplaces, of course, shit is excellent, you need to run for umz))) or to another service
YOU look what he wrote, just yesterday and from his post, carried such confidence. Today the cry of the hero.
- Like
- I do not like
guys here on the site newbie. help (only in a personal). TODAY CHECKED 2 FARSUNKI LYUT AT THE STAND. REPAIR NEEDED. FOR ONE ASKING 6 TR IN YOSHKAR OLE. TE 12T.R. + FLUSHING FUEL SUPPLY SYSTEM. IS IT WORTH REPAIR? About the engines they said that woof. oh he. resource 300 t.km, on native farces more than 190 t.km did not go, at least they did not bring for repairs.What to do?? who will tell you? I decided to take it for repairs, since you can buy a pig in a poke (I'm talking about new farces)
passed 152 t.km Lil exclusively lukoil, did not overload, did not heat. I drive myself, it's a shame the car is not 2 years old
Are you sure that you will be repaired normally and it will not be a pig in a poke? Ask, will they give you the code for registering the injectors after the repair? So on which car of the three did the injectors fly?
Post has been edited RA3QBJ: 12 March 2013 - 00:16
- Like
- I do not like
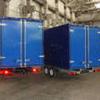
Are you sure that you will be repaired normally and it will not be a pig in a poke? Ask, will they give you the code for registering the injectors after the repair? So on which car of the three did the injectors fly?
flew on mine! in some places changed the sinkers in order as they were only put on a car that has almost no run. on a new troit only at the first start then it works smoothly. We drove literally 10 km as we also heard uneven work. We decided not to tempt fate and put everything in its place. My car's mileage is 153 t km. Teperb which is the third car everything works there. On it, at 75 t.km, the engine was approximately taken off. Threw out the oil. As it turned out, the marriage of the ring! () In one of the cities. We made two. in Yoshkar Ola. After the run, I walked 50 t km. Works smoothly quietly softly. But as it turned out with an electrician, he could not! I was wrong about the registration of the farsocks. (why asked) t. I didn’t know, and the third car didn’t tell me what they prescribed, although I personally saw that I had mixed up the badges.
About the code. Apparently it won't give the code, at least it didn't say anything. I heard out of my ear that they are being repaired when they are coded close to the central parameters. I don't understand anything about this.
- Like
- I do not like
do not encode. and "repair" so that the nozzle fits into the middle of the test plan .. frankly. not sure about the masters. - money down the drain. We have a lot of craftsmen in NN. I did it all the same with Leha Yurich. since not the first year with diesel engines, and only from a conversation with local craftsmen I understood. what they won't do well ..
Post has been editedRed001: 12 March 2013 - 08:58
The fuel system uses electro-hydraulic injectors, which are controlled by an electronic control module. High pressure fuel is supplied to the injector from the rail.
A solenoid valve located at the top of the injector activates a needle that delivers the required amount of fuel through a nozzle to each cylinder.
Multiple fuel injection is carried out by the command of the electronic module (ECM), which controls the operation of the solenoid valves of the injectors. The gaps in the nozzle nozzle openings are too small and any debris entering them will clog the nozzle. Therefore, it is important to remove dirt around all fittings in the fuel system before servicing.
The high pressure fuel line fitting has a slotted filter that crushes small dirt particles that enter the fuel system. It uses high-frequency fluctuations in fuel pressure to break down most of the particles to a size that matches the flow area of the injector.
All injectors are connected to a common low pressure fuel return line. All excess fuel from the injectors, rail, and fuel pump is returned to the fuel tank through the low pressure fuel line. A low pressure check valve is installed in the low pressure line, which prevents fuel from returning to the injectors along this circuit. The drain lines are provided with push-type fittings with lynch clips on each nozzle.
If the injector is faulty or partially faulty, the engine will work unstable, consume more fuel, and the engine will "shake". Fuel leakage through the drain line, as a result of a malfunction of any injector, can be checked as follows:
Disconnect the fuel drain line from each injector
Press on the latch fixing the drain pipe union
Disconnect the return line from the nozzle
We connect the separate drain hoses included in the nozzle leak test kit (catalog number 4918899). If this kit is not available, suitable sized hoses can be used.
We lower all four hoses into separate measuring containers.
We start the engine and measure the amount of fuel collected per minute. We compare the results for each injector.
The maximum fuel consumption for each injector should be 20 ml / min.
Do not remove the injectors unnecessarily!
Disconnect the negative terminal of the battery
We clean the area where the nozzle is located with compressed air or steam.
Press the latch and disconnect the wiring block from the injector
Press on the lock fastening the drain pipe fitting to the nozzle
Disconnect the pipeline from the nozzle
Unscrew the nut securing the high pressure pipe to the rail
Holding the nozzle fitting from turning, unscrew the nut securing the high pressure pipe to the nozzle
Engines of the cummins series, and in particular the cummins isf 2.8, are currently installed on such cars as Gazelle, Gazelle NEXT, GAZ 2752 Sable and are an excellent diesel engine. The cylinder block is cast from cast iron, the cylinder liners are milled into the block. Thanks to milling, significant block strength and material savings are achieved. When the liner wears out, then during a major overhaul, it can be very simply replaced or it can be sharpened to the first repair size.
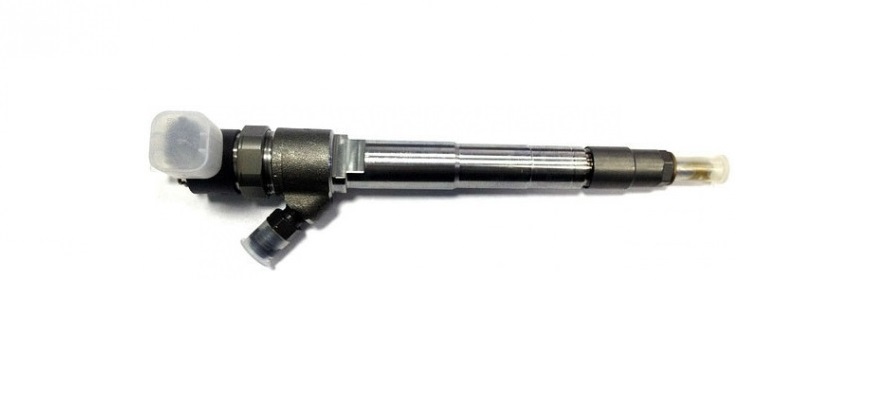
The block head is made in one piece, with four valves per cylinder. The valves are driven via rocker arms from the camshaft. The nozzle of the cummins isf 2.8 engine is located clearly in the center of the cylinder... All valves are made of high temperature resistant material and the valve stem is chrome plated to prevent scoring and chipping. If you have to buy the whole set, as the valves are not interchangeable. The crankshaft of the cummins isf 2.8 engine is made of gray cast iron, the pulley with the shaft is one-piece. The camshaft is driven by a chain and is carried out through an intermediate gear. The chain drive of the cummins isf 2.8 engine, although it adds a little noise, is quite tolerable for a truck.
Well, having figured out the minimum device of the cummins isf 2.8 engine, you can go to one of the main questions: how the injector is cleaned. And we are interested in how to do it on our own, for example, on a long journey or when it is often not cost-effective to contact the service. For example, when a GAZelle participates in a small business, and its driver is "handy" enough not to go to the service.
The first symptoms in order to start thinking about cleaning the injectors can be the twitching of the car when the accelerator pedal is pressed sharply, dips when picking up speed, and if the air is humid, then the car does not drive at all.
At the service station, the nozzle is cleaned using special equipment - ultrasound. After visiting the service and carrying out cleaning, the efficiency of the power supply system is restored almost completely, that is, the fuel mixture is much better distributed over the cylinders and is sprayed better. We will pay attention to the methods of self-cleaning of the nozzles, we will have two of them. We need these things:
- Injector and carburetor cleaning kit.
- Special rubber seals.
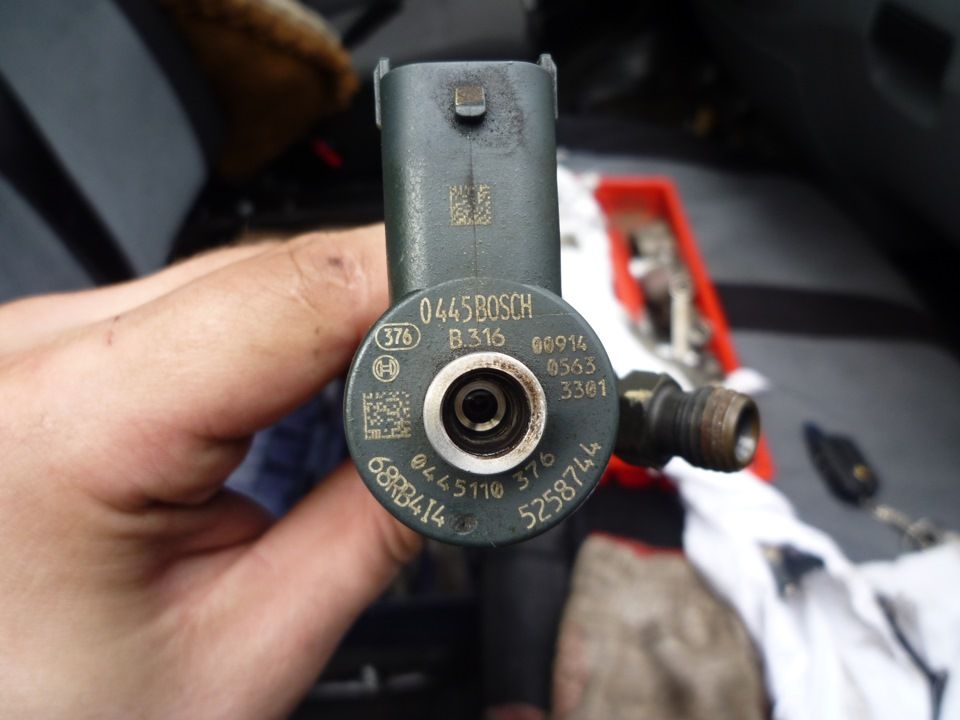
Cleaning the injectors of the cummins isf 2.8 engine
Now let's start parsing. First, carefully remove the barrel with the idle speed regulator (IAC) pipes, then disconnect the wires from the injectors and remove their clips. Now you need to carefully remove the nozzle bar, everything must be done carefully so as not to break anything.After removing the nozzles from their seats, you need to soak them in some unnecessary container in the liquid for the injector cleaner. While the injector of the cummins isf 2.8 engine is “turning off”, we will prepare the following tools: a foot pump with a pressure gauge and an accumulator. Also, in order not to waste time, you can clean the IAC with a carburetor cleaner. Next, we remove carbon deposits with a needle, we must clean everything around the nozzle. To completely clean the nozzles we have to flush them. To do this, we remove the hose from the pump and fill it with a cleaner, then we connect the hose to the nozzle and apply voltage to it. We repeat with each nozzle, after which we put everything back. The second method is longer, but cheaper. We do everything in the same way, but it will be necessary to pour a carburetor cleaner into the hose from the pump, and we remove the external carbon deposits with a cloth moistened with the same cleaner. The carbon deposits will slowly dissolve. That is why this method is longer. Next, put the nozzles in place in the same way.
The injection mechanics is the main difference between a diesel engine and a gasoline engine. In a diesel internal combustion engine, fuel is supplied to the combustion chamber using a nozzle. The device injects fuel in a metered manner into a chamber with a high temperature and pressure, after which the diesel fuel ignites. The nozzle is subjected to the greatest load: the part is constantly in an aggressive environment and works at high intensity. Any negative factor can disable the part or significantly reduce its resource, after which the diesel engine nozzles will need to be repaired.
To understand the mechanics of the injector, we will describe the injection cycle schematically:
- The injection pump takes fuel from the tank;
- then the pump saturates the fuel rail with diesel fuel;
- fuel enters the channels that lead to the nozzle;
- inside the nozzle, fuel flows to the sprayer;
- when the pressure on the atomizer reaches the set threshold, the nozzle opens and diesel fuel enters the combustion chamber.
Let us describe the design of the part using the example of a primitive mechanical nozzle with 1 spring. In the lateral part there is a channel that provides a continuous supply of diesel fuel. Inside the nozzle chamber there is a movable barrier with a spring and a needle, which drops when the pressure rises. The needle rises, clearing the path of fuel to the sprayer.
Additionally, more advanced types of nozzles can be noted:
- Piezoelectric: The spring pusher is lowered by a piezoelectric element. This technology provides a high intensity of opening of the atomizer: fuel economy is achieved, while the internal combustion engine operates more smoothly.
- Electro-hydraulic: The design includes an inlet and outlet choke and an electromechanical valve. The operating mode of the components is controlled by the engine control unit.
- Unit injectors: used in engines that do not have a high-pressure fuel pump. The fuel is supplied directly to the nozzle. These spraying devices have their own plunger pair inside, which generates the pressure required for injection.
Due to excessive loads, the injector may fail due to a violation of the operating mode of the motor. Manufacturers declare the resource of parts to be up to 200,000 km, but due to negative operating factors, wear of parts appears much earlier.
Repair of diesel injectors may be required for the following reasons:
- Low quality diesel fuel: the scourge of all "diesel operators". Due to impurities in the fuel, the sprayer becomes clogged; the dosage and the fuel supply mode are violated.
- Poor assembly quality of the injection component or factory defect: the injector does not withstand the operating conditions, the part as a whole or individual components fail.
- Mechanical damage caused by incorrect operation of adjacent ICE systems.
Usually, breakdowns are of the following nature: the spray angle and the amount of supplied fuel change, the integrity of the body is violated, and the needle travel deteriorates.
Let's briefly describe the "symptomatic series":
- jerks and jerks are felt when moving;
- The internal combustion engine is unstable at idle, stalls;
- when the engine is running, an excessive amount of exhaust is emitted;
- tangible loss of traction;
- failure of individual cylinders;
- gray or black smoke from the exhaust pipe.
It is preferable to entrust the routine maintenance or overhaul of diesel engine injectors to qualified specialists - they will be able to restore and adjust the part on high-precision automated stands. However, a certain set of repair procedures can be carried out in artisanal conditions without the use of complex equipment.
To carry out self-service of diesel engine sprayers, the car owner will need:
- a set of open-end or spanner wrenches;
- screwdrivers for straight and Phillips head;
- clean dry rags;
- maximeter;
- flushing fluid for internal combustion engines.
It is recommended to carry out work in a dry and lighted, dust-free garage.
Diagnostics of diesel injectors and their maintenance involves removing the nozzles from the internal combustion engine. Before starting work, it is recommended to thoroughly wash the engine and engine compartment to avoid the ingress of debris and foreign particles. With particular fondness, you need to rinse the cylinder head. High pressure tubing should be marked with markings to avoid confusion during reassembly.
Before removing it is necessary to close the nozzle fittings (use plastic caps) to avoid contamination. It is not recommended to use ordinary open-end wrenches to dismantle the nozzles - an inexperienced repairman can strip the threads from the nozzles. If the required qualifications are not available, use spanners and a long-handled head tool.
After removing the nozzles from the holes, dry them and remove external dirt with a rag. O-rings are placed in the holes of the nozzles. When repairing injection parts, they are replaced with new ones without fail. Do not allow dirt from the rings to get into the injection system during removal.
There are several methods to check if the sprayer is working properly. The easiest way is to check the injector while the engine is running:
- Start the "engine" at idle speed.
- Begin to unscrew the nozzles one by one in turn.
- If, after removal, the operation of the motor has deteriorated, then the remote nozzle is operational and must be returned to its place.
- By the method of elimination, you will find an injector, the dismantling of which will not change the operating mode of the internal combustion engine. This will be the broken device.
You can use a multimeter for diagnostics. In advance, it is necessary to throw off the battery terminals and disconnect the wiring of the injectors, and then "check" every detail with the device. On high resistance injectors, the device values will be in the range of 11 - 17 ohms; at low impedance, the multimeter will show up to 5 ohms.
The defective injector must be inspected. First, we look for leaks in the body of the part. If there are none, proceed to disassembling the part. We fasten the part in a vise and knock out the sprayer with a gentle tap. Next, you need a thorough cleaning: we soak the parts of the nozzle in diesel fuel or solvent to remove carbon deposits. Remove fumes and deposits with a fine steel grater. After completing the cleaning, you need to check the nozzle at the maximum meter. If the optimal injection parameters have been achieved, the device is ready to be installed in the engine.
In other cases, it is necessary to completely replace the atomizer on the defective nozzle. When installing a new part, carefully remove all factory grease, otherwise the device will not work.
Before disassembling the device, mark all parts with a marker to avoid confusion. Be especially careful when marking high pressure hoses.The nozzle is screwed in by hand as far as possible. Further tightening is done with a dynamometer wrench. For tightening values, refer to the motor manual. After installing the injector, evacuate air from the fuel system. On modern cars, for this it is enough to turn the starter several times; or use a manual priming pump (if equipped).
Let's list the main features:
- the resource declared by the manufacturer has been developed;
- there are breakdowns on the case, other leaks;
- burnt out spray nut: if the problem is not eliminated early, the spray itself will become unusable.
Please note that on some engines, after installing a new injector, it is necessary to "tie" it to the engine: make changes to the settings of the control unit.
Self-repair of injectors is a rather forced measure. Such a service in artisanal conditions can bring success only in the case of the highest qualifications of the master. The main problem of garage repairs is the lack of high-precision bench equipment for diagnostics. The repairman cannot objectively assess the effectiveness of the service measures.
If there is an opportunity to contact a service station, do not neglect it: computer equipment and cleaning stands will extend the life of the injectors and save them from potential expensive repairs. The same ultrasonic cleaning can save a motorist from engine problems for several seasons. It is not possible to repair modern Common Rail injection systems in a garage: you need a mandatory fine-tuning of the part by computer.
Use a cleaning fuel additive to avoid costly repairs and replacement parts. They prevent the formation of carbon deposits and the settling of deposits. The use of additives should be systematic, not one-off. Remember, additives are about preventing breakdowns, not fixing them.
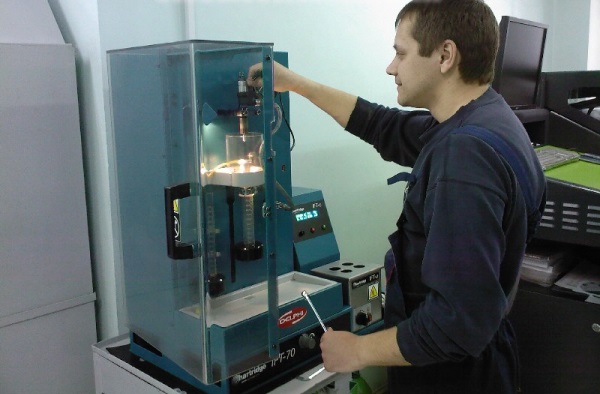
Their differences are due to the types of fuel systems that are used in diesel engines. Therefore, in order to understand the design and repair features of the injector, it is necessary to understand the principle of operation of a particular system for supplying fuel.
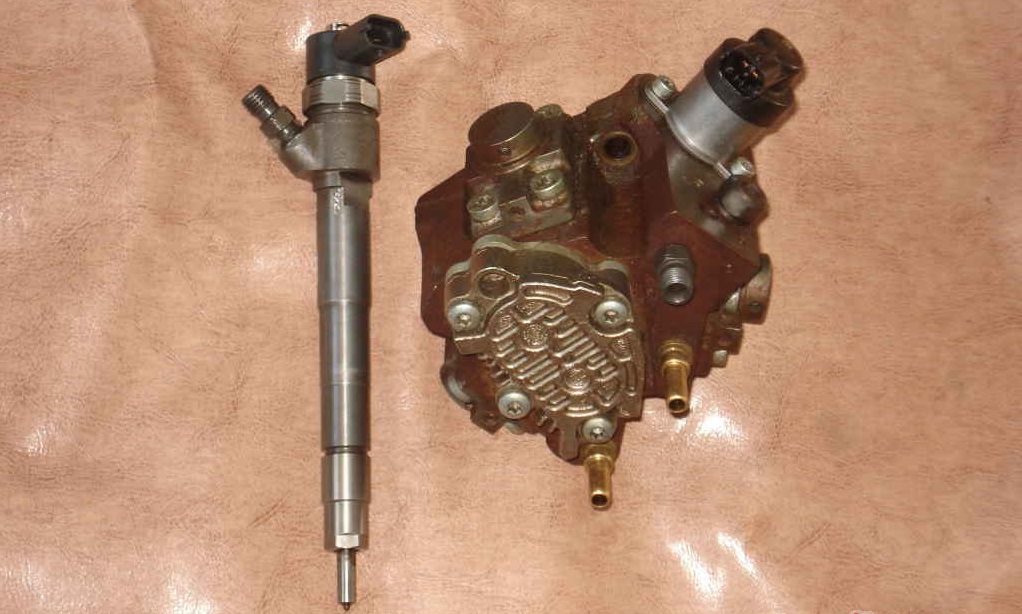
Due to the high pressure, a portion of the fuel is atomized into small fractions. This promotes its rapid evaporation and mixing with air, and, consequently, improves the quality of the resulting air-fuel mixture.
In order for the fuel system to clearly perform its functions, its design is constantly being improved, electronic control of the injection system is used, and various technologies are used to ensure optimal fuel injection. There are three types of fuel systems used in a diesel internal combustion engine:
- classic system using a high-pressure fuel pump (high pressure fuel pump);
- a battery-type fuel system with a common fuel line (Common Rail);
- system in which pump-nozzles are used (Pumpe-Duse).
Cummins engines use a variety of fuel delivery systems to accommodate different injectors. However, each of them meets international requirements for reliability and environmental friendliness. In addition, Cummins injectors can be repaired, which reduces the cost of operating the engine. Next, we will consider methods for troubleshooting and repairing Kamens injectors.
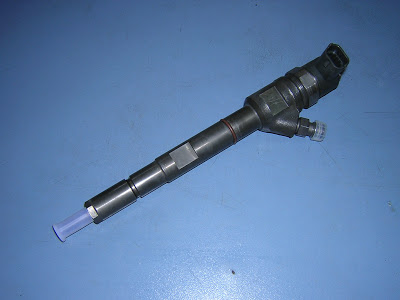
In this case, the most common failure of a nozzle is a failure of the atomizer. In addition, subject to wear: the nozzle nut, the nozzle body and fungus, and the spacer. Wear is manifested in mechanical damage and deformation of the nozzle parts, as well as a change in the linear dimensions of its parts.
There are external signs by which you can determine the need to check the condition of the injectors. These features include gaps and loose fit between the body and other parts of the nozzle, resulting from linear distortions or wear of the atomizer mounting nut.
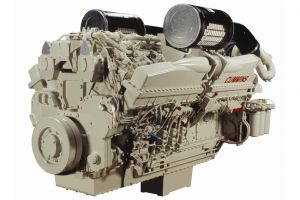
The peculiarity of the assembly of the gas distribution mechanism of the Kamins engine is that during it, parts made of heat-resistant steel are used, and the exhaust valves installed in the engines are made of chrome-silicon alloy. Engine assembly details are here.
Another alarm is a drop in pressure that causes the nebulizer to open. In normal operation, over the entire period of operation of the nozzle, the opening pressure should not decrease by more than 10% from the nominal value set by the manufacturer. Excessive pressure drop can be caused by wear on the spring or on the nozzle surfaces.
A worrying factor is reduced fuel delivery to the atomizer and improper injection. All this affects the quality of the engine's operation and leads to a loss of power or an increase in the opacity of work.

Checking for leaks with the cylinders shutting off in turn will not help determine the location of the leak, since it is located before the needle valve of the injector.
Since all injectors receive fuel from a common fuel line, losses will be distributed evenly across all cylinders.
There are a number of operations, individual for each engine model, focused on separating the fuel streams and measuring the fuel consumption from the injectors.
Initial check
After the preparatory operations have been carried out, you can start measuring the level of fuel consumption, but first, remember the important rules.
So, we start checking and first of all we start the engine. Next, enable the Fuel Leak Test available with the INSITE ™ Diagnostic Kit. It is necessary to wait at least a minute for the nozzles to warm up to operating temperature, as this will provide more accurate measurements.
Install the drain hose into a graduated cylinder and measure the amount of fuel flowing out per minute.
Fuel consumption rating with INSITE ™ check enabled
- 4-cylinder - no more than 200 ml,
- 6 cylinder - no more than 300 ml
Standard fuel consumption in idle mode
- 4-cylinder - no more than 120 ml,
- 6-cylinder - no more than 180 ml.
It should be borne in mind that in this mode, it is possible not to detect a fuel leak.
If fuel consumption is higher than the specified limits, it makes sense to carry out a check with insulation of the injectors.
Having found out that the problem of excessive fuel consumption in the injectors, they should be removed and checked for the possibility of further operation.
It should be noted that the removal of the injectors should be resorted to only if the malfunction was confirmed by diagnostic procedures.The injector can only be dismantled with the ignition off after preliminary cleaning of all connections of the fuel system with stiff brushes, rinsing and drying with compressed air.
Training: remove the fuel line, the fuel line fitting, the rocker arm cover and the exhaust rocker itself.
Removing the injectors. First, disconnect the wiring leading to the solenoid valve, and then remove the two bolts of the nozzle holder, and then the holder itself. Remember, the injector holder is not removable on all engine models. Use a special nozzle puller, or you can use a small pry bar to pry the nozzle by the pressure flange.
Use a piece of cloth soaked in solvent to clean the nozzle body and tip. Check tip for corrosion or carbon deposits. Check all terminals of the solenoid valve for damage.
Check the end of the fuel line fitting and the injector inlet for damage. If overheating took place during the operation of the injectors, then blue or dark yellow spots will appear on it (depending on the overheating temperature).
Check the injector O-rings for damage and replace if necessary.
After a general inspection, repair of the cummins injector pump and, if necessary, replacing defective parts, we proceed to installation.
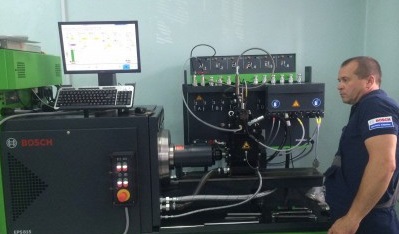
Lubricate the O-ring with engine oil and align the injector in the correct position on the cylinder head (inlet facing the fuel line fitting). Check that the nozzle fits snugly in the hole.
If the nozzle is installed without the solenoid valve packing cover, try to avoid applying force to the terminals, as they may break if pressure is applied to them when installing the nozzle.
Without tightening the bolts, install the nozzle holder. Check the fuel line fitting for burrs or deformation around the ends of the fitting, and inspect the slotted filter for clogging.
If all of the above signs are found, the parts must be replaced.
Install the fuel line fitting so that the end fits into the inlet of the injector. Screw on the nut of the high pressure fuel line fitting and tighten loosely. First, tighten the holder bolts evenly and make sure that the gap between the nozzle and the holder is even. But then you can tighten the fitting nut.
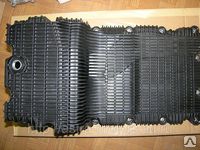
The Cummins ISF 2.8 engine is a great engine for medium-sized businesses. You can study the characteristics of an economical and efficient engine in this article.
Using a torque wrench, connect the electrical wiring to the valve and tighten the terminals and make sure that when installing the wires do not come into contact with the rocker arms.
Final operations: install the rocker arm and adjust the exhaust valve clearances, install the rocker arm cover, start the engine fuel line to make sure there are no leaks.
In conclusion, it must be said that all types of maintenance and repair of Kamens injectors should be carried out under the conditions of a specialized service center. This is due to the high requirements for cleanliness and accuracy of injector adjustment, as well as the importance of matching the injector parameters to the engine manufacturer's requirements.
Only then will the Cummins diesel engine operate in accordance with the factory parameters for reliability, durability and economy.
The fuel system uses electro-hydraulic injectors, which are controlled by an electronic control module. High pressure fuel is supplied to the injector from the rail.
A solenoid valve located at the top of the injector activates a needle that delivers the required amount of fuel through a nozzle to each cylinder.
Multiple fuel injection is carried out by the command of the electronic module (ECM), which controls the operation of the solenoid valves of the injectors. The gaps in the nozzle nozzle openings are too small and any debris entering them will clog the nozzle. Therefore, it is important to remove dirt around all fittings in the fuel system before servicing.
The high pressure fuel line fitting has a slotted filter that crushes small dirt particles that enter the fuel system. It uses high-frequency fluctuations in fuel pressure to break down most of the particles to a size that matches the flow area of the injector.
All injectors are connected to a common low pressure fuel return line. All excess fuel from the injectors, rail, and fuel pump is returned to the fuel tank through the low pressure fuel line. A low pressure check valve is installed in the low pressure line, which prevents fuel from returning to the injectors along this circuit. The drain lines are provided with push-type fittings with lynch clips on each nozzle.
If the injector is faulty or partially faulty, the engine will work unstable, consume more fuel, and the engine will "shake". Fuel leakage through the drain line, as a result of a malfunction of any injector, can be checked as follows:
Disconnect the fuel drain line from each injector
Press on the latch fixing the drain pipe union
Disconnect the return line from the nozzle
We connect the separate drain hoses included in the nozzle leak test kit (catalog number 4918899). If this kit is not available, suitable sized hoses can be used.
We lower all four hoses into separate measuring containers.
We start the engine and measure the amount of fuel collected per minute. We compare the results for each injector.
The maximum fuel consumption for each injector should be 20 ml / min.
Do not remove the injectors unnecessarily!
Disconnect the negative terminal of the battery
We clean the area where the nozzle is located with compressed air or steam.
Press the latch and disconnect the wiring block from the injector
Press on the lock fastening the drain pipe fitting to the nozzle
Disconnect the pipeline from the nozzle
Unscrew the nut securing the high pressure pipe to the rail
Holding the nozzle fitting from turning, unscrew the nut securing the high pressure pipe to the nozzle
Tell me how you can remove the injector from the engine.
I tried to loosen it by the fitting, but three people did not move it by a millimeter in an hour.
there is a pneumatic hammer for licota injectors
the right thing for diesel service
This is actually a difficult question. We coped with a homemade reverse hammer.
And so in the place of seeing, maybe the replacement of the nozzle will be required.
on sanyeng, the aktion could not be pulled out in two weeks until they cut it off.
Filmed with a partner once with a reverse hammer and a mounting. The reverse hammer does not quite work in the right direction. The knocking out produces upward and to the side, t to the nozzle on the nozzle at an angle. Therefore, they gave a stretch on the back side with a fitting. The method was certainly not humane, but after 3 hours of torment they pulled out!
Tell me how you can remove the injector from the engine.
Hydraulic puller Licota ATA-3502
on sanyeng, the aktion could not be pulled out in two weeks until they cut it off.
Share how you can do this using the drilling method?
The hole in the nozzle is not centered and the drill is pulling away, i.e. unreal.
We make in such difficult cases on a milling machine, well, or a new head.
- Like
- I do not like
The reverse hammer does not quite work in the right direction. Knocking out produces upward and to the side, t to the nozzle on the nozzle at an angle
Nothing that you need to cling to the fitting? :)
The reverse hammer does not quite work in the right direction. Knocking out produces upward and to the side, t to the nozzle on the nozzle at an angle
Nothing that you need to cling to the fitting? :)
I think everyone understood what I mean! Sorry, I put it wrong in panting!
on sanyeng, the aktion could not be pulled out in two weeks until they cut it off.
Share how you can do this using the drilling method?
The hole in the nozzle is not centered and the drill is pulling away, i.e. unreal.
We make in such difficult cases on a milling machine, well, or a new head.
I don’t know how they drilled it and gave it to the turners in the airlock area. Maybe they coped with the milling nozzle, but they didn’t know with the glow plug that it was at an angle. drilled at the wrong angle.
- Like
- I do not like
I think everyone understood what I mean
We understood, of course. this is not the way to do it.
I think everyone understood what I mean
We understood, of course. this is not the way to do it.
Is it unnecessary to write like this? Or to get the nozzle like that? Of course, it's better to take off your head. And for money it is more profitable and less hemorrhoids! :)
somehow they tried to remove the sporttezh 1.7 on Kia, but they could not, and the valve cover did not open until you remove the nozzles. The injectors were serviceable, it was necessary to remove the injection pump, the owner did not agree to break the injectors. As a result, I sold it.
- Like
- I do not like
Is it unnecessary to write like this? Or to get the nozzle like that? Of course, it's better to take off your head. And for money it is more profitable and less hemorrhoids! :)
Please do not write anything to me. With experience you will understand everything. And how to properly hook the nozzles under the reverse hammer and everything else.
I xs where you could read about the removal of the cylinder head in my posts.
Please do not write anything to me.
In no time did I want to offend you, and even more so to question your experience. Sorry if offended!
Perhaps experience and not enough in some issues, but the cases are different and they have to be solved according to the situation, and not according to the template!
- Like
- I do not like
What offended? I just ask a person with no experience not to mislead colleagues.
on one gazelle they could not take it off - they broke the valve cover - they took off the cylinder head and carried it to the press .. I don't know how they pressed it there - as a result, they broke my head in half. but the owners did it themselves - I only saw the result.
![]() |
Video (click to play). |
And I zakolhoz such pribluda. Looked at in the manual for UAZ Hunter
