In detail: do-it-yourself repair of the bottom of a VAZ 2105 from a real master for the site my.housecope.com.
I propose a way to restore the bottom of a car without overcooking and in normal garage conditions. I do not pretend to be the author of the idea, although the idea was born myself 🙂 If we compare the costs of capital welding, then this method is incomparably cheaper. It is certainly not perfect and is unlikely to suit those whose body has already rotted into "dust". And so - think for yourself, decide for yourself - to have or not to have.
For this we need:
Materials:
- galvanized iron in sheets (2 sq.m.);
- antinoise bitumen mastic (2 cans);
- bolts, nuts, washers M5;
- self-tapping screws 15-20mm long
Equipment:
- angle grinder (in common people, a grinder);
- drill
- screwdriver
- scissors for metal;
- roulette;
- brush 100mm wide;
- permanent marker;
- metal brush;
- cutting and grinding wheels.
Details:
- Small front side members right and left
And so, let's get started.
First you need to understand the interior: remove the seats, floor mats, remove the noise insulation. I have only one name left from Shumka :).
Next, you need to remove the old bituminous mastic from the floor in the cabin. this is necessary for a more detailed assessment of damage and marking of sheets. it is also necessary to remove the exfoliated mastic from the bottom of the bottom.
The rot is already cut off in the photo.
Due to the presence of a "grinder" I cleaned the "live" part of the floor to metal. The only jamb - after a couple of passes through the uncleaned mastic, the petal circle clogged and no longer cleaned it, but polished the rust, it had to be replaced.
In the end, it turned out something like this:
After sanding and trimming everything that is superfluous, we begin to cut the tin. Here, everyone has their own injuries. I covered the entire half from the inside, right down to the transverse spar, although the floor was intact there. The fact that there is a stamping in the floor does not really matter, later it will be possible to pour mastic there and everything will be a bunch. In any case, the tin did not work for me from this.
After cutting the material for the inner part, we cut the tin for the bottom. Here, again, your personal wishes, the amount of galvanizing available and the nature of the damage play a role.
After cutting the metal, coat the floor with bituminous mastic (from all sides). It is advisable to let the mastic dry so that the layer of mastic will eventually be larger. I had to dry for a week due to working days.
Galvanizing installation.
Before installing galvanized sheets, we generously smear them with mastic (by the way, it is better to make the mastic thicker, otherwise it flows strongly) only from the installation side, otherwise then all the mastic will be smeared on hands and clothes.
It is better to fix galvanized sheets intended for installation from below with self-tapping screws to the bottom, especially if you do not have an assistant. The protruding parts in the cabin must be cut down. Then we climb into the salon, put the galvanized steel (again, oiled with mastic) on the floor and begin to fasten it with bolts. In principle, M5x15 bolts are enough for the eyes with the obligatory use of washers on both sides. When using self-locking nuts, the lock washers can be omitted (only regular ones). If the nuts are common, then the growers must be installed. The drill must be taken with the same diameter as the bolts.
It is better to fasten it to start from one end, since the possibility of metal bending is excluded. I didn't do that right away and had to rebuild the structure.
How many bolts and location to choose according to the situation. If you have to replace the front spar ("jack"), then in this place the sheet is not yet fixed.
![]() |
Video (click to play). |
Installing the front side member
Preparation of side members:
I removed the hinges for the standard jack, I think very few people use a regular screw jack.
Drill six holes on the long crown attachment petals (three on one side and three on the other).
We apply the spar to his place of permanent residence and squeeze it from below. Better jack.
We drill holes in the floor through the spar. Then we remove the spar, coat the inside of the spar with mastic and the section of the bottom that will be closed by the spar and put the spar. We fasten again with bolts.
As a result, we got something like this:
the protruding parts of the bolts can be cut off.
In conclusion, we cover the galvanized sheets with mastic, trying to push the mastic into the cracks, if any, the spars and all places not covered with mastic.
I think this design will last longer than a digested bottom.
Now let's summarize the financial result of this venture (the repair was carried out in the winter of 2009-2010):
- galvanized iron 2 sq. M (350 rub.)
- bituminous mastic 2 large cans (360 rub.)
- side members 2 pcs. (200 rub.)
- bolts, nuts, washers, screws (about 80r.)
- cutting disc 1 pc. (15-20r)
- grinding wheel (60 rubles)
Total: approximately 1070r.
Plus an invaluable feeling of what I did myself :). The service asked 15 thousand rubles for overcooking the bottom.
I hope that this manual and idea will be useful to someone.
Masters at car services most often thicken the paint and tell the owner of the car that a rotten bottom requires long painstaking work, the cost of many materials. It is from this that such a high price is formed. At the same time, they try to prevent the owner from being examined or show problem areas in low light. In this case, ordinary dirt can be mistaken for an oxidized rotten metal, which you just touch and it crumbles. With the help of such little tricks, the colors are thickened, which allows to inflate the price.
If the car owner wants to save money, he needs to do a preliminary inspection of the bottom on his own. For this you will need:
- Lift, observation pit, overpass.
- Good lighting: a torch or a carrier with a powerful lamp.
- Hammer.
With the help of a hammer, it is necessary to tap all suspicious areas of the bottom and determine the degree of their damage, in order to approximately know the amount of required materials.
If all of the above is not at hand or there is simply not enough time for a thorough inspection, then a special mirror will come to the rescue for inspecting the underside of the car. It will allow you to assess in general terms the condition of the metal and get an approximate idea of the scope of work. But the situation will become fully clear only after a thorough examination.
The welding process itself is simple, everyone can master it in the shortest possible time. Sometimes it takes longer to connect and set up equipment. The easiest way to over-weld the underside of a car is with a semi-automatic welding machine. But often such repairs are simply impossible without the involvement of gas welding. Best of all, when these two units are used, they complement each other and enhance the quality of underbody repairs.
As the saying goes: "If you want to do something well, do it yourself." Car underbody repair is no exception. To implement it, you will need the following equipment:
- Semi-automatic welding machine.
- Gas welding.
- Conventional metal or electric scissors.
- Bulgarian (angle grinder).
- Hammers of various sizes and configurations.
- Good lighting.
You also need to stock up on the following materials:
- Oxygen and calcium carbide (for gas welding).
- Carbon dioxide and copper wire (for semi-automatic welding machine).
- Grinding and cutting wheels for metal grinders.
- Metal for patches.
To repair the underside of a car with your own hands went without problems, you need to choose the metal of the optimal thickness. Its recommended thickness varies from 1 to 2 mm. But here the qualifications of the one who will carry out the welding work should be taken into account.When working with thinner metal, it is necessary to strictly observe the temperature requirements during welding. Which, in turn, depends on the debugging of the equipment and the quality of consumables.
Thicker metal is more difficult to process, but at the same time it is more difficult to damage and spoil it. Therefore, before purchasing consumables, you need to really assess your qualifications as a welder.
Now you can start preparatory work. There is nothing difficult in this, and it will not be difficult to do them with your own hands. You just need to clean all problem areas of the bottom from rust. This can be done in two ways.
With the help of a grinder. In this case, it is necessary to use both cutting and grinding wheels. During work, be sure to follow all safety rules. It is better to clean hard-to-reach places from rust by gas welding.
After hitting rusty metal and corrosion, the edges of the surface to which the patches will be attached must be well cleaned. It is advisable to do this work with a grinder. Now you can cut out patches from metal and start welding. Cutting metal is best done with hand or electric metal shears. This will allow you to make your workpieces to the exact size and keep the edges straight. Cutting metal, especially thin metal, by welding requires high qualifications.
It is advisable to weld the bottom together. It will be difficult for one person to simultaneously fix the patch and scald it. If the metal is applied to a flat surface, then fix it faster with a semi-automatic welding machine.
If it is necessary to make a bend, you should resort to gas welding. When heated, the metal becomes soft and it can be bent and shaped with a hammer. At the same time, do not forget that high temperatures reduce the properties of the metal. Another option in this case can be a special device designed to create bends on metal workpieces.
After completing the welding work, all seams must be cleaned with a grinder and covered with anti-corrosion compounds.
This method will save time, money and hassle of the car owner. You will not need to pay huge sums to the masters at the service station or to comprehend the profession of a welder.
Hello members of the forum! In general, the problem is this:
A friend gave me his 83-year-old five as unnecessary. Although rather only a body with wheels. It probably had a year, if not more, now I have it for a month, since there is a carriage. In general, there is no interior, no engine, no gearbox. But The most interesting thing is that the iron in a circle is absolutely everything new, only the front fenders are missing. It is already painted in metallic. But it is already cleaned in places, it is necessary to putty. But this is not the point. The bottom and sills are in a very poor condition.
She stood and then I turned around to buy from a neighbor a shape-shifting seven in 2002 for a penny. The body is not about anything, but everything else is in good condition and on the move itself. That is, there is absolutely everything that this five needs. In general, the hands want restore this top five, but in my head doubts - will this 83 year remain with me forever, even if I completely restore it and fill it with it? Experience in this is not great, but there is. Can it then be sold at least a thousand for 35-40? If yes , then in the future I hope for your advice on recovery.
to Vllad: sell. We will help you with advice, please contact)
I changed the thresholds, but I didn’t deal with the bottom as a whole. Hence the question: How to put the car correctly, so that later the screw is not there and diagonally does not go away and what is done first of all, change the rotten thresholds or start from the bottom?
to Vllad: first you need to change the thresholds, and then the bottom
The fact is that the threshold with the amplifier is welded to the internal threshold, and it is most likely also for replacement. And accordingly, it is already welded to the bottom, and the bottom for replacement. I would like to learn more about the procedure, let's say step by step.
to Vllad: I will describe the step-by-step replacement of the sills and the replacement of the bottom separately.
How to replace thresholds with your own hands?
This question is of interest to many motorists.
Such repairs, of course, can be done at the maintenance station, financially, it is not so expensive, but it will take a lot of time. Therefore, many car enthusiasts decide on such repairs as a do-it-yourself replacement of thresholds.
Below is an approximate technology for replacing the threshold with your own hands on a VAZ car.
It is necessary to start this type of repair, such as replacing thresholds with your own hands on a VAZ car, in two cases, after an accident, if the threshold amplifier has received serious deformation, or the threshold has begun to collapse due to corrosion that occurs after water gets inside.
The threshold consists of three parts - the outer panel, the connector and the amplifier. All these elements are connected to each other by spot welding. This type of repair, such as replacing the threshold with your own hands on a VAZ car, begins with dismantling the rear and front doors.
To clear space for work, to do this, remove the aluminum sill, installed at the bottom of the over-door seals, and partially raise the mat. Old sills are easier to remove piece by piece, first at the front door, then at the rear, and finally at the B-pillar.
The thresholds can be removed in two ways: in the first method, it is necessary to mark all the spot welds with a marker and drill them with a thin drill. In the second method, the thresholds can be removed with a grinder. If it is necessary to replace the entire threshold, you need to drill holes from the rear, from the side of the jack amplifier, in the front - in the place where the old connector was left.
In addition, when removing the outer panel, it is necessary to leave 50-60mm sections of the old panel on the side of both the rear and front fenders, since the new panel will be butt welded to them. In addition, on the front side of the wing, a small section of the connector must be left. Next, we dismantle the threshold amplifier, taking into account that we leave not most of it under the middle rack - an amplifier will be welded to it a little later, but already a new one. After removing the threshold, all rust remaining on the metal should be cleaned. We also cut out the rusted areas of the body bottom, clean the places for future welding from rust and paint.
At the next stage, technologists do-it-yourself threshold replacement begins with the installation of a new threshold.
Adjusting the threshold begins with the connector, in front it should dock with the remaining old connector, not the large section that we left, but at the back we overlap on the jack amplifier. After this installation, you can weld on. We shorten the amplifier and make a cutout in the B-pillar area. This is done so that when installing it, the remnant of the old that was left there does not interfere.
Next, aligning the amplifier along the lower edge and the connector, we attach the amplifier to the connector by welding. It is desirable to adjust the outer sill panel more precisely, after which the sill is adjusted in place, the adjustment starts from the upper part, preferably the gaps remain minimal. After carrying out the above steps, it is necessary to clean the welding places from the transport soil, and drill holes for welding. Next, we mount the outer panel and fix it at the top with clamps or self-tapping screws.
Next, through the holes that were drilled in advance, we weld the panel in the lower part to the amplifier, and the connector to the bottom of the body. Now it is necessary to weld the remaining metal to the upper sections of the threshold, and from the bottom side, we weld the patches. And the final touch of this type of repair, such as replacing thresholds with our own hands - we clean it, putty and seal the welded seams along the entire outer panel.After that, the threshold must be primed and painted, and the front and rear doors must be installed back.
Do-it-yourself floor restoration without welding
I propose a way to restore the bottom of a car without overcooking and in normal garage conditions.
If we compare the costs of capital welding, then this method is incomparably cheaper.
It is certainly not ideal and is unlikely to suit those whose body has already rotted into "dust". And so - think for yourself, decide for yourself - to have or not to have.
For this we need:
- galvanized iron in sheets (2 sq.m.);
- antinoise bitumen mastic (2 cans);
- angle grinder (in common people, a grinder);
- drill - screwdriver - scissors for metal;
- roulette; - brush 100mm wide;
Due to the presence of a "grinder" I cleaned the "live" part of the floor to metal.
The only jamb - after a couple of passes through the uncleaned mastic, the petal circle clogged and no longer cleaned it, but polished the rust, it had to be replaced.
- permanent marker; - metal brush;
- cutting and grinding wheels.
- Small front spars right and left And so, let's get started.
First you need to understand the interior: remove the seats, floor mats, remove the noise insulation. I have only one name left from Shumka :).
Next, you need to remove the old bituminous mastic from the floor in the cabin. this is necessary for a more detailed assessment of damage and marking of sheets. it is also necessary to remove the exfoliated mastic from the bottom of the bottom. After sanding and trimming everything that is superfluous, we begin to cut the tin.
Here, everyone has their own injuries. I covered the entire half from the inside, right down to the transverse spar, although the floor was intact there. The fact that there is stamping in the floor does not really matter, later it will be possible to pour mastic there and everything will be a bunch. In any case, the tin did not work for me from this. After cutting the material for the inner part, we cut the tin for the bottom.
Here, again, your personal wishes, the amount of galvanizing available and the nature of the damage play a role. After cutting the metal, coat the floor with bituminous mastic (from all sides). It is advisable to let the mastic dry so that the layer of mastic will eventually be larger.
I had to dry for a week due to working days. Galvanizing installation. Before installing galvanized sheets, we generously smear them with mastic (by the way, it is better to make the mastic thicker, otherwise it flows strongly) only from the installation side, otherwise then all the mastic will be smeared on hands and clothes.
It is better to fix galvanized sheets intended for installation from below with self-tapping screws to the bottom, especially if you do not have an assistant. The protruding parts in the cabin must be cut down. Then we climb into the salon, put the galvanized steel (again, oiled with mastic) on the floor and begin to fasten with bolts. In principle, M5x15 bolts are enough for the eyes with the obligatory use of washers on both sides. When using self-locking nuts, the lock washers can be omitted (only regular ones).
If the nuts are common, then the growers must be installed. The drill must be taken with the same diameter as the bolts. It is better to fasten it to start from one end, since the possibility of metal bending is excluded. I didn't do that right away and had to rebuild the structure. How many bolts and location to choose according to the situation. If you have to replace the front spar ("jack"), then in this place the sheet is not yet fixed. Installing the front side member Preparation of side members: I removed the hinges for the standard jack, I think very few people use a regular screw jack.
Drill six holes on the long crown attachment petals (three on one side and three on the other). We apply the spar to his place of permanent residence and squeeze it from below. Better jack. We drill holes in the floor through the spar. Then we remove the spar, coat the inside of the spar with mastic and the section of the bottom that will be closed by the spar and put the spar. We fasten again with bolts. the protruding parts of the bolts can be cut off.
In conclusion, we cover the galvanized sheets with mastic, trying to push the mastic into the cracks, if any, the spars and all places not covered with mastic. I think this design will last longer than a digested bottom. Now let's summarize the financial result of this venture (the repair was carried out in the winter of 2009-2010): - galvanized iron 2 sq. M (350 rubles) - bitumen mastic 2 large cans (360 rubles) - spars 2 pcs. (200 rubles) - bolts, nuts, washers, self-tapping screws (about 80 rubles) - cutting disc 1 pc. (15-20r) - grinding wheel (60r.) Total: about 1070r. Plus an invaluable feeling of what I did myself :). The service asked 15 thousand rubles for overcooking the bottom. I hope that this manual and idea will be useful to someone.
The underbody of a car is more susceptible to aggressive environmental influences and mechanical damage more than other parts of it. If the bottom can be protected from corrosion, then this is unlikely to work from various kinds of damage. The reason for this is often the poor condition of the road surface. In general, sooner or later the car owner will have to face the need to repair the bottom of his iron horse, especially if he has been serving his owner with faith and truth for many years.
Overcooking of the bottom - this diagnosis is often made to car owners at a service station. It sounds very serious and from these words smells of a hopeless situation and the high cost of resolving it. Is it really? Situations are different, but often things are not as deplorable as the specialists of car services imagine them. If you wish, you can do everything yourself.
ATTENTION! Found a completely simple way to reduce fuel consumption! Don't believe me? An auto mechanic with 15 years of experience also did not believe until he tried it. And now he saves 35,000 rubles a year on gasoline! Read more"
Masters at car services most often thicken the paint and tell the owner of the car that a rotten bottom requires long painstaking work, the cost of many materials. It is from this that such a high price is formed. At the same time, they try to prevent the owner from being examined or show problem areas in low light. In this case, ordinary dirt can be mistaken for an oxidized rotten metal, which you just touch and it will crumble. With the help of such little tricks, the colors are thickened, which allows to inflate the price.
If the car owner wants to save money, he needs to do a preliminary inspection of the bottom on his own. For this you will need:
- Lift, observation pit, overpass.
- Good lighting: a torch or a carrier with a powerful lamp.
- Hammer.
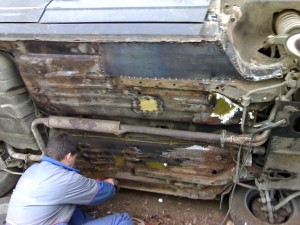
If all of the above is not at hand or there is simply not enough time for a thorough inspection, then a special mirror will come to the rescue for inspecting the underside of the car. It will allow you to assess in general terms the condition of the metal and get an approximate idea of the scope of work. But the situation will become fully clear only after a thorough examination.
The welding process itself is simple, everyone can master it in the shortest possible time. Sometimes it takes longer to connect and set up equipment. The easiest way to over-weld the underside of a car is with a semi-automatic welding machine. But often such repairs are simply impossible without the involvement of gas welding. Best of all, when these two units are used, they complement each other and enhance the quality of underbody repairs.
As the saying goes: "If you want to do something well, do it yourself." Car underbody repair is no exception. To implement it, you will need the following equipment:
- Semi-automatic welding machine.
- Gas welding.
- Conventional metal or electric scissors.
- Bulgarian (angle grinder).
- Hammers of various sizes and configurations.
- Good lighting.
You also need to stock up on the following materials:
- Oxygen and calcium carbide (for gas welding).
- Carbon dioxide and copper wire (for semi-automatic welding machine).
- Grinding and cutting wheels for metal grinders.
- Metal for patches.
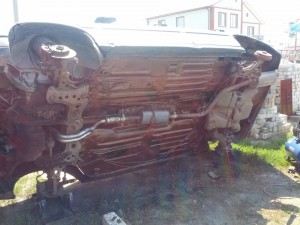
Thicker metal is more difficult to process, but at the same time it is more difficult to damage and spoil it. Therefore, before purchasing consumables, you need to really assess your qualifications as a welder.
Now you can start preparatory work. There is nothing difficult in this, and it will not be difficult to do them with your own hands. You just need to clean all problem areas of the bottom from rust. This can be done in two ways.
With the help of a grinder. In this case, it is necessary to use both cutting and grinding wheels. During work, be sure to follow all safety rules. It is better to clean hard-to-reach places from rust by gas welding.
After hitting rusty metal and corrosion, the edges of the surface to which the patches will be attached must be well cleaned. It is advisable to do this work with a grinder. Now you can cut out patches from metal and start welding. Cutting metal is best done with hand or electric metal shears. This will allow you to make your workpieces to the exact size and keep the edges straight. Cutting metal, especially thin metal, by welding requires high qualifications.
It is advisable to weld the bottom together. It will be difficult for one person to simultaneously fix the patch and scald it. If the metal is applied to a flat surface, then fix it faster with a semi-automatic welding machine.
If it is necessary to make a bend, you should resort to gas welding. When heated, the metal becomes soft and it can be bent and shaped with a hammer. At the same time, do not forget that high temperatures reduce the properties of the metal. Another option in this case can be a special device designed to create bends on metal workpieces.
After completing the welding work, all seams must be cleaned with a grinder and covered with anti-corrosion compounds.
And this option is possible. It is enough just to periodically inspect the bottom, if necessary, clean out the places where rust has appeared, and cover them with special compounds.
This method will save time, money and hassle of the car owner. You will not need to pay huge sums to the masters at the service station or to comprehend the profession of a welder.
Forget about fines from cameras! An absolutely legal novelty - NANOFLENKA, which hides your numbers from IR cameras (which are in all cities). Read more about this at the link.
- Absolutely legal (Article 12.2.4).
- Hides from photo and video recording.
- Installs independently in 2 minutes.
- Not visible to the human eye, does not deteriorate due to the weather.
- 2 year warranty,
Replacing the thresholds of the VAZ 2107 is an operation that sooner or later has to be carried out with most cars. The reasons for this may be:
- poor quality anti-corrosion treatment;
- humid climate;
- road chemistry;
- condition of roads.
Self-replacement of the VAZ 2107 thresholds requires certain qualifications in welding and the availability of the appropriate tool.
The following tools and materials are required:
- Electric drill.
- Bulgarian.
- Semi-automatic welding.
- Primer.
- Dye.
- New thresholds for the VAZ 2107.
[tip] In addition, in the process of work, you will have to use standard tools available from any craftsman: pliers, tape measure, metal cheek, and so on. If the threshold amplifier is rotten, you will have to buy a new one. [/ Tip]
Old rotten thresholds have to be cut off with a grinder. To provide access to the entire surface of the threshold, the doors must be removed. If the body is decrepit, spacers must be installed before removing the sills. Further operations are performed in the following sequence:
- Instead of paint, you can use an anti-corrosion coating such as "Gravitex".
- After replacing the thresholds, they must be subjected to anti-corrosion treatment, "blowing" the inner surface of the boxes with "Movil". If this is not done, the thresholds will have to be replaced again in the near future.
- The lower part of the thresholds (at the same time the bottom of the machine) should be treated with anti-corrosion bitumen mastic, which prevents corrosion and improves the protection of the paintwork from damage.
[/ tip]
Now you know how to independently replace the thresholds of the VAZ 2107. If you do not have the necessary qualifications of a welder or there is no welding machine, it will not be possible to replace the thresholds. In this case, it is better to seek help from professionals who can replace thresholds quickly and efficiently.
Sometimes there are cases when it is much more profitable, both financially and in terms of saving time, to repair your car with your own hands. In this regard, we will consider today how you can easily and quickly restore the front floor of a VAZ 21099 car. As you can see in the photo below, you will have to change the entire square, which is completely rotten, entirely, patches in this case will not help.
- firstly, it is necessary to put the car so that it is convenient to work, that is, so that there is comfortable access to it both from below and from the side of the door;
-It is also recommended to cover the dashboard and seats with foil so that dust does not get on them when you need to cut a piece of the floor. After that, you will need to purchase or, if possible, get a piece of iron for free in order to cut out of it "a piece of the required size for the floor."
You will also need a front jack and a sill connector for repairs. What materials are suitable for processing? The bottom will need to be coated with Body 930, and the floor, after welding, will need to be filled with Body 992 anti-corrosion primer.
What else awaits the masters during their work? You will have to raise the support (pictured below), under which, most likely, you can find rust. The new metal joint will go underneath it.
How to lift it? It is necessary to drill out points, which will then help to orientate, or you can put yourself other marks.
It is imperative to get to the very place where she stood, otherwise there will be problems with the installation of the seat. In the upper part of the threshold, you need to focus on the area where the paint has been preserved and it is along the edge of this area that you need to cut out a rusted piece of the floor.
As for the door, it is better to remove it. This will help create a more comfortable working environment. Of course, it will take a little longer for repairs, but in the future it will not interfere with the restoration work.
If you look at the threshold, you can see that it itself is quite suitable, only the edge has jammed.
What can be done is to replace the amplifier, put a thick plate in the appropriate place (in the photo below) and weld it together in the right places.
What to look for: before starting work, you need to cover the interior (so that dust does not get on the seats and the dashboard, disconnect the battery terminals).
In this particular case, a semiautomatic device and CO2 gas will be used for welding.
At the initial stage of work, you need to drill out the base. The points are marked, then it will need to be put in place.
As you can see, the support was not removed for nothing, there is a lot of rust under it, which must be removed, as well as mark the boundaries of the new plank.
Now let's move on to the spar.If it is in good condition, you can leave it as in our case. The floor is welded to it with dots. They hold the sill joint and the floor itself.
The photo shows the side member and the threshold connection.
It will also be necessary to change the subjack.
You should also take into account one more important nuance: welding will be carried out in the places indicated in the photo.
As a result, the anticorrosive will burn under the arch. To apply a new one, you will need to remove the wheel and wheel arch liner. However, first, when these elements are removed, you need to cut out the rusted section of the floor. In places where you can find points, you just need to drill them, where it will be impossible to find them, you will need to cut off the metal. As one of the options for reducing dust in the cabin, you can water the treatment area with water and cut on an already wetted surface. After the section of the rusted floor has been cut out, you can proceed to the next stage.
Do not forget that under the section, which is shown in the photo, brake pipes and gas lines pass. Therefore, you need to disconnect them, make a spacer so that they are as far from the metal as possible.
Then you can cut off the old floor. Where you can see the points, it is a little easier, in these places you can drill them and separate the metal.
In places where they are not visible (as on a spar), you can cut off the edges or even make an incision in the middle and, prying the incised area, find these points. The main idea is to leave the spar, which will be in good working order after cleaning.
In addition, as you can see from the photo, in the place of the base plank, where there used to be quite a lot of rust, now it is practically a clean place. All that is needed for this is to clean this area with sandpaper, treat it with a rust converter, cover the area with soil and it does not need to be cut off.
The next step is to cut out the front jack, as it is rather rusty, and we also have a new one. As for the sill connector, it is still in good condition and there is no need to do the extra work by cutting it out and replacing it with a new one.
What should be done next? Everything is very simple: the piece of floor that we managed to get out is put into place, the excess parts are cut off, a careful fitting and welding is performed.
When the floor is welded, you will need to weld the cross member on top.
It is necessary to weld the front jack, install the sill joints, cover a new piece of floor with a primer on top, and coat with grease from below, Body 930 will do.
The structure of the car body is shown in Figure 1.
A significant part of body repair work falls on emergency vehicles, which in most cases require checking the geometry, attachment points of the components and assemblies of the vehicle chassis.
To control the geometry of the attachment points of the chassis assemblies shown in Figures 2 and 3, as well as to perform complex repairs with simultaneous control, the installation (Fig. 4) is used for repair and control of bodies in combination with straightening devices.
The straightening device is fixed to the frame from the side of the deformed part of the car body.
Body damage can be very varied. Therefore, the repair rules in each individual case should be their own, most suitable for these damages.
In almost all cases of damage, it is necessary to remove some parts from the body in order to detect damage, straighten and align the skeleton. In case of serious damage, the easily removable interior upholstery parts are removed to facilitate measurement, control and installation of hydraulic or screw jacks to eliminate distortions and deflections.
By editing it is necessary to restore the original linear dimensions of the car body skeleton.
The diagonal dimensions of the window openings should be 1375 ± 4 mm for the wind window (Figure 5), and 1322 + 4 mm for the rear window. The distances between the flanges of the window openings along the vehicle axis must be equal, respectively, for the wind window 537 + 3-2 mm, for the rear window - 509 + 3 mm.
The difference in the diagonal dimensions of the opening of the wind window, as well as the openings of the rear window, hood, trunk lid of one body should not exceed 2 mm.
Most often, when repairing remains, replacement of fenders, roof panels, front and rear is required. The methods of replacing and repairing these parts can be taken as a basis for the repair of other frame parts. It is also necessary to know the location of the body welds.
In case of minor damage to the wing (small dents, scratches, etc.), do without removing the wing, straightening and painting work. After straightening, it is necessary to check the condition of the internal anti-corrosion coating. If defects are found, you must restore it.
In case of significant deformation of the wing, if there are gaps, it is necessary to replace the wing.
Remove the bumper (see the chapter “Hood, trunk lid, bumpers”), antenna, hood, front door, remove the lights from the fender.
Use a 6-7 mm diameter drill to drill out the contact weld points of the gutter with the bodywork and detach the groove with a thin flat chisel with a bent end.
Use a fine sharp chisel to cut or grind off the wing joints with a grinder (Figure 6):
- with the front panel from the headlamp down, stepping back 2-3 mm from the connection line;
- with the front pillar of the sidewall, stepping back 5 mm from the bending line.
Detach the fender, use a chisel to remove the remaining fender strips. Straighten out the deformed edges and clean the body and new wing seats.
Dirt and rust must be removed from the cavity covered by the wing. After cleaning, rinsing and drying, apply GF-073 zinc-chromate primer.
Replace the hood and door. Fit the new wing to the landing site and secure with grips.
Weld the wing with gas welding at the points shown in Figure 7. For gas welding, use a brass rod L 62 or L 68.
After checking the wing landing, weld it by contact welding with a pitch of 40-50 mm or electric welding in carbon dioxide with Sv-08G1S or Sv-08G2S wire 0.8 mm in diameter with an intermittent seam 10 mm long every 30-40 mm. Electric current strength 50-90A.
When replacing the rear wing, the rear light and bumper must be removed. Free the trunk, remove the trunk lid rubber seal and the fuel tank (if changing the right fender) and disconnect the electrical wiring.
Chop off with a fine, sharp chisel or grind along the joint wing:
- with the arch of the rear wheel along the bend (Figure 8), stepping back from the edge of the wing 12-15 mm;
- with the floor of the spare wheel (or fuel tank) along the bend, stepping back from the edge of the wing 12-15 mm;
- with a rear panel, departing from the connection line 2 mm;
- with a panel of the rear window cross member, departing from the bend edge by 2-3 mm;
- with the rear part of the sidewall along the bend, departing from the edge of the wing 15-20 mm.
Cut off the corner of the wing-to-rear panel connection, departing 15 mm from the edge of the corner.
Using a 6-7 mm drill, drill out the contact welding points at the junction of the wing with the side roof panel and disconnect the wing. Remove the remaining fender strips, trim off the deformed edges and clean the body and new wing seats.
Fit the new wing to the landing site, grab it with grips and weld it with gas welding rods L 62 or L 68 in the months indicated in the fragments of Figure 9.
Check the fit of the wing and weld it with contact welding in 40-50 mm increments. In the absence of a contact welding machine, gas welding is allowed by flashing the edges with an intermittent seam 20 mm long every 30 mm with a bar L 68. In the door opening, electric welding is allowed by a semiautomatic device in a carbon dioxide environment.
In most emergencies with damaged roofs, it will need to be replaced.
Remove the windscreen, rear glass, headliner and accessories.
Place the new panel on the roof and locate the cut points for the side panels and A-pillars.
Stepping back 8 mm from the edge of the roof panel, cut (Figure 10) along the bends of the connections with the panels of the wind window frame, with the cross member of the rear window frame, gutters and side roof panels. At the side roof panels, cut the roof panel 10-15 mm above the markings.
Detach the roof panel, remove the remaining panel strips and clean the seats of the vehicle body and the new panel.
Align the body elements at the panel joints and fit the new roof panel in place.
At the points indicated by arrows in Figure 11, gas-weld the roof panel to the windshield panel and side roof panel.
Carefully check the fit of the panel and weld around the perimeter by resistance welding at a pitch of 40-50 mm. Weld the roof to the side panels with gas welding.
In the absence of a contact welding machine, gas welding or electric welding in a carbon dioxide environment is allowed.
Using a thin sharpened chisel, cut off the tailgate panel (Figure 12) from the floor of the fuel tank, the floor of the spare wheel, the side members of the panel amplifier and remove the remaining strips of metal.
Straighten and grind the deformed edges with a sander.
Install the new panel and grip it in the locations indicated by the arrows in the figure. Check the correct installation of the panel by pre-installing the rear bumper.
Weld the tailgate panel by resistance welding or electric welding in the atmosphere of carbon dioxide with an intermittent seam 10 mm long every 30 mm in length.
Gas welding by points every 30-40 mm with brass rods L 62 or L 68 is allowed.
Replacements are made with the rear fenders, rear panel and rear panel amplifier removed.
Chop off the tail floor with a thin chisel (in Figure 13, the felling places are marked with a dotted line, arrows on the fragments). Use nippers to remove the remaining strips of metal, trim and clean the deformed edges with an electric or pneumatic grinder.
Cut off the floor of the fuel tank (spare wheel) from the side members and inner arches of the rear wheels (Figure 14), remove the metal strips and trim the edges.
Use a chisel to cut off the inner arches of the rear wheels and cross members with a side member (Figure 14), remove the remaining strips of metal and clean the seats.
Install the new side members in place and tack them with gas welding with rods L 62, L 68 in the places marked in the figure.
To the bottom of the tailgate floor, weld the central amplifier, the holder with the asbestos gasket underneath it, and the main muffler mounting brackets. Perform electric welding in carbon dioxide with dots through 40-50 mm with wire Sv-08G1S or Sv-08G2S with a diameter of 0.8 mm. Gas welding is allowed.
Refit the tailgate floor and gas-weld in the corners at the points marked in the figure.
Install the amplifier to the rear panel and weld with electric welding in an environment of carbon dioxide, with dots every 40 mm. Reinstall the tailgate panel and fasten it to the body elements by gas welding (see replacing the tailgate panel).
Figure 14. Replacing the fuel tank floor (spare wheel) and tail floor side members. Dotted lines indicate felling lines, dots of resistance welding seams. In the main view, arrows show the places of gas welding, arrows on the fragments - the places of felling
Gas-weld the floor of the fuel tank (spare wheel) at the points marked in Figure 14.
Be sure to carry out a preliminary check of all stuck parts with the attachment of the rear fenders and the trunk lid. Eliminate assembly flaws and finally weld the parts by electric welding in carbon dioxide with Sv-08G1S or Sv-08G2S wire with an intermittent seam 10 mm long every 30 mm. Electric current strength 50-90A.
Gas welding is allowed with brass rods L 62 or L 68 points every 30-40 mm.
Replace with front and rear fenders removed. Replace amplifier 2 (Figure 15) only in the presence of deformation or through corrosion.
Use a fine chisel to cut the sill panel 3, remove the remaining metal strips and grind the edges with a grinder.
Mark the new sill panel for the B-pillar, adjust the panel in place and secure with the clamps.
Gas-weld the panel at the extremes, install the doors and carefully check the panel installation. The protrusion and retraction of the threshold relative to the door should not be more than 3 mm.
Remove the doors and weld the sill panel to the mating parts by contact welding with a pitch of 50-60 mm. Electric welding in a carbon dioxide environment with a current strength of 50-90 A or gas welding is allowed.
Gas weld the panel to the B-pillar and strip the welds.
Drill out the butt weld points in the frame and air box joints with a 6 mm drill.
If replacing the window frame panel and the roof panel at the same time, mark the drain grooves on both sides of the roof joint with the windshield frame panel.
Use a chisel to chop off the frame panel (in Figure 16, the felling lines are marked with a dotted line) from the struts, gutters and reinforcements. Use nippers to remove the remaining metal strips and trim the edges.
Be sure to burn with a torch and carefully clean the paint on the parts along the fit of the windshield frame, as well as on both sides of the edge of the frame panel.
Install new frame panel and secure with clamps. When installing the panel, align the markings on the gutters with the roof joints. Using gas welding, grip the frame panel at the locations marked in the figure.
Replace the hood and check the fit of the panel. Check the dimensions of the opening of the wind window and weld the panel with gas welding with brass wire L 62, L 68 by reflowing 10 mm long shreds every 50 mm. Sand the joints on the frame panel with a sander.
Partial replacement of the windshield frame panel is allowed when the roof panel is installed.
Deformed surfaces are repaired by mechanical or thermal action on the metal, as well as by filling dents with fast-hardening plastics or solder.
The dented plumage is straightened, as a rule, by hand using a special tool (plastic, metal, wooden hammers and various mandrels) and devices.
Heat straightening is used to shrink highly stretched panel surfaces. To prevent sudden swelling and deterioration of mechanical properties, the panels are heated to 600-650 ° C (cherry-red color). The diameter of the heated spot should be no more than 20-30 mm.
Shrink the surface as follows:
- heat the metal with a gas burner from the periphery to the center of the defective area and use a flat support or anvil to upset the heated places with a wooden mallet and hammer;
- repeat the heating and settling operations until a flat surface is obtained.
Irregularities in panels can be leveled with polyester fillers, thermoplastics, cold curing epoxy mastics and solder.
Polyester putties form a secure bond with panels that have been brushed to metal. They are two-component materials: unsaturated polyester resin and a hardener, which catalyzes the quick hardening of the mixture, regardless of the thickness of the putty layer. Drying time at 20 ° C 15-20 minutes. Therefore, there is no need to apply it in several layers and the duration of the putty application is reduced.
Thermoplastic is available in powder form. It acquires the elastic properties required for its application to the metal surface of the panel at 150-160 ° C.
The surface to be filled must be very thoroughly cleaned of rust, scale, old paint and other contaminants. For better adhesion, it is recommended to create roughness on the metal surface with an abrasive tool. To apply thermoplastic, the area to be leveled is heated to 170-180 ° C and the first thin layer of powder is applied, which is rolled with a metal roller, then the second layer is applied, and so on until the unevenness is filled.
Each layer is carefully rolled until a monolithic layer of plastic mass is obtained. After hardening, the layer is cleaned and leveled with a grinder.
Corroded areas of car body panels can be repaired with cold curing epoxy mastics, which have high adhesion, sufficient strength and are easily applied to damaged areas.
![]() |
Video (click to play). |
Solders POSSu-18, POSSu-20 are used for leveling areas previously filled with solder, for building up the edges of parts and for eliminating gaps. To prevent corrosion of the metal, it is better to use an acid-free method of applying solder.