In detail: do-it-yourself repair of the m16a engine from a real master for the site my.housecope.com.
We got to Berlin, we’ll get to Washington.
The soldier was getting drunk, a tear was rolling down, a trophy googlephone wheezing and a medal "For the city of Washington" sparkled on his chest
The author thanks the alphabet for the letters kindly provided.
All of the above is just my personal opinion. If you disagree with him, well, that's your right. For example, I never remember evil, but I can burn a hut.
And an earnest request: do not let your children go to the Internet, they spoil it.
We got to Berlin, we’ll get to Washington.
The soldier was getting drunk, a tear was rolling down, a trophy googlephone wheezing and a medal "For the city of Washington" sparkled on his chest
The author thanks the alphabet for the letters kindly provided.
All of the above is just my personal opinion. If you disagree with him, well, that's your right. For example, I never remember evil, but I can burn a hut.
And an earnest request: do not let your children go to the Internet, they spoil it.
The Suzuki M16A engine is a 1.6-liter naturally aspirated gasoline engine with in-line four cylinders.
Like all motors from the Suzuki company, the M16A is distinguished by good reliability.
ATTENTION! Tired of paying fines from cameras? A simple and reliable, and most importantly 100% legal, way has been found not to receive more “letters of happiness”. Read more"
This power unit was developed specifically for a small five-door hatchback, therefore it has little power. The main task of the designers was to create an economical and at the same time reliable engine, which, without serious intervention, could serve more than 200 thousand kilometers.
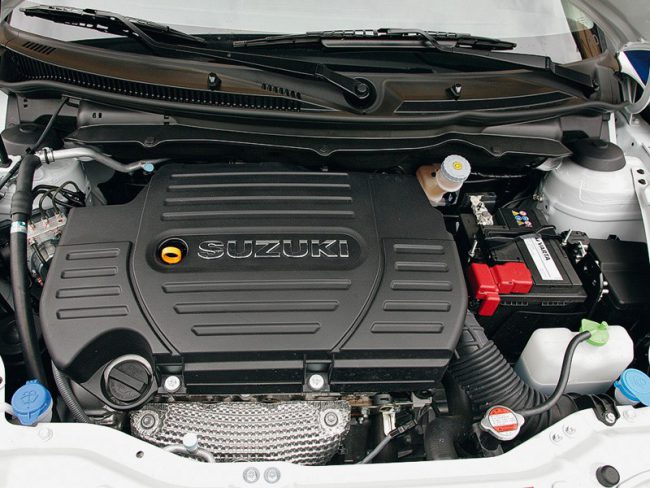
The M16A motor is characterized as a quiet driving power unit and is installed on city cars. Therefore, the technical parameters given below do not differ in any tuning potential:
Due to the fact that this power unit is considered extremely reliable, some tips for its operation will be given below that will help to extend its uptime.
In order for the engine to work flawlessly and serve for many years, it is necessary first of all to carry out timely maintenance. The oil should be changed every 7,500 - 10,000 km and only of good quality. Recommended viscosity 0W-20 - 5W-30. Spark plugs are an important factor in the stable operation of the engine. They should be replaced every 30,000 - 40,000 km, provided they are of high quality. The quality of the fuel also affects engine performance, albeit to a lesser extent. For the M16A engine, the optimal gasoline is 95th.
![]() |
Video (click to play). |
In addition, it is very important to check the technical condition. One of its main stages is to measure the compression in the engine cylinders. To do this, warm up the engine to operating temperature, disconnect the ignition coil and high-voltage wires, and then unscrew all spark plugs. After that, turn off the fuel injectors by disconnecting them from the connectors and connect the compressor to the connector for the spark plug. Next, you need to squeeze the clutch and press the gas pedal all the way, then start the starter and watch the readings of the device.
For reference! In order to obtain the necessary compression data, the engine must be cranked up to at least 250 rpm. To do this, the battery must be fully charged!
If values were obtained below normal (1100 kPa), this indicates that the piston rings and valves are worn out and require replacement.
In addition, it is recommended to check the thermal clearance of the valves (in the lower photo). This is to prevent the engine from running noisily over time. Violation of the thermal clearance of the valves also leads to increased wear of the elements of the gas distribution mechanism and valves in particular. For the M16A power unit, the thermal clearance of the intake valves is 0.18 - 0.22 mm, of the exhaust valves - 0.28 - 0.32 mm (for a cold engine) and 0.21 - 0.27 mm, 0.30 - 0.36 mm - at the operating temperature of the motor. If any of the valves does not correspond to the specified ranges, it must be adjusted using special washers.
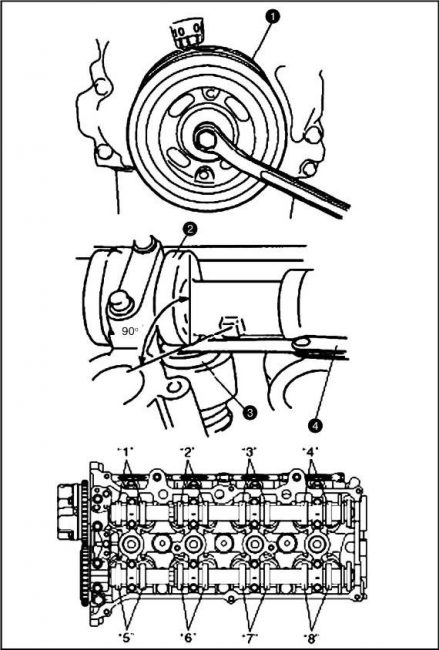
A huge number of car owners who are equipped with the M16A power plant agree that this is a very reliable and economical unit. However, you should pay attention to the chain of the gas distribution mechanism, because it tends to stretch (closer to 100 thousand kilometers). The chain must be replaced together with the drive sprockets. In addition, the owners note increased noise when the engine warms up, especially in the cold season. It is all the fault of the generator drive belt, which, after heating, ceases to make dubious sounds.
Since the Suzuki M16A engine is designed for budget cars, it has good maintainability. All engine parts are changed individually, and it will not be difficult to find spare parts for it. In addition, this motor does not have a complex design and high-tech systems, so you can repair or maintain it yourself.
And in conclusion of this article, it should be added that this engine was installed on only two car models from Suzuki:
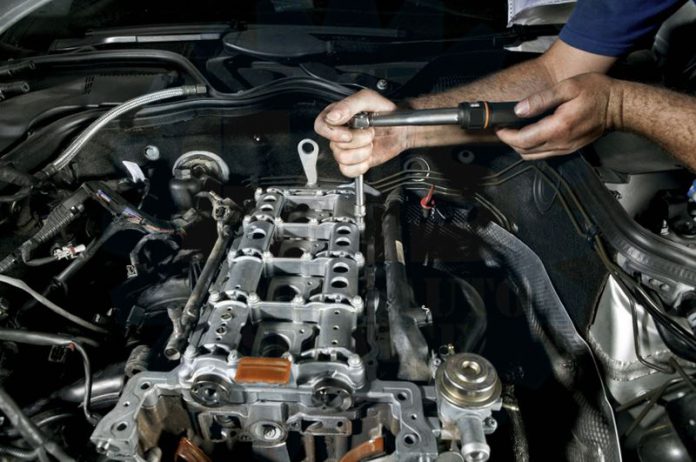
Some motorists, for various reasons, prefer to repair a car with their own hands. In these cases, it is important to know how to disassemble and assemble the engine. To begin with, it is worthwhile to understand that it will not be possible to do without costs at all. Even if it is not planned to replace parts, new gaskets will have to be installed during assembly (unless the gaskets are not damaged or punctured).
You may also need an engine sealant that can be used in place of gaskets, a torque wrench (needed during assembly), and a set of wrenches of different sizes. Moreover, you will need not only open-end and spanner keys, but also end keys (preferably with replaceable heads, long and short cranks). In addition, you will need a lot of free time, since disassembly takes from several hours to two to three days, depending on the make and condition of the car. Let's look at the procedure for disassembling and assembling the motor in more detail.
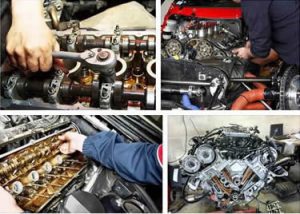
For complete disassembly, the engine will have to be removed. You can do this right away, or you can do it after the cylinder head has been removed. Removal requires a hand winch and a sturdy support (such as a beam) from which to hang it. Shooting a motor also takes several hours.
Disassembling and reassembling an engine is, in general terms, almost always the same. There might be some discrepancy in details depending on the brand and model. Further, the procedure for the removed power unit is proposed.
To remove the belt (chain), you must first loosen the chain itself by removing the tensioner. Next, you have to dismantle the camshaft gear. This part is fixed with a bolt. But besides a key of a suitable size, here you will need (at least on domestic engines) a powerful flat screwdriver or chisel, as well as a hammer.With the help of these tools, the lock plate is bent, which does not allow the bolt to spontaneously unwind.
When the gear is removed, the chain is removed and you can start removing the crankshaft gear. It is better to have a special puller here, as without it, you may have to tinker. This part is fixed on the shaft with a key, which can sit quite tightly in the groove. If, in the process of cutting the keys, its edges were somewhat deformed, then they can be corrected with a file. The last procedure in this step is to remove the chain tensioner shoe. There shouldn't be any problems with this.
6. Dismantling the camshaft. To do this, unscrew the nuts (they are on the studs) that fix the camshaft cover and remove the shaft itself.
7. Remove the cylinder head. It is fixed either with bolts or nuts on studs.
Now you can turn the engine over and unscrew its pan. There will be a gasket under the pallet. It will most likely have to be changed, but you can get by with a sealant.
8. Remove the oil pump. Unscrew the rear oil seal cover (from the end of the engine). The oil pump shaft and its drive gear on the back of the engine are removed. To do this, unscrew the bolts and remove the retaining bracket, after which the shaft is removed with a screwdriver, and then the gear. It must be handled carefully, as it plays an important role in the operation of the engine.
9. The next important step is the dismantling of the KShM. Complete disassembly and assembly of the engine is not complete without this process. Here attention and accuracy are required, since the parts are not interchangeable, but individual.
10. Removing the connecting rods. First you need to turn the crankshaft so that the two connecting rods are in the upper position. Next, the nuts are unscrewed from the connecting rod cover and the cover itself (yoke) is removed. The yoke will fit snugly, so gentle hammering on the sides will be required. The connecting rod can now be removed. It is pushed out together with the piston by hands or the handle of a hammer.
On the inside, the connecting rods and caps have metal inserts. If their replacement is not provided, then it is worth scribbling the corresponding number on the non-working side. The same procedure is carried out with the other two connecting rods.
11. Removing the main covers. They are also fixed with nuts and are strictly in place. On their inner side there are also inserts - root inserts.
12. The crankshaft is removed, the old liners and retaining half rings are removed from under it.
The engine disassembly process can be considered complete.
The assembly of the engine is carried out in the reverse order. When installing the connecting rods, it should be borne in mind that each of them has factory marks on the body, which must coincide with such marks on the cylinder block body.
Relatively speaking, you need to observe the left and right sides during installation. In addition, as mentioned above, the connecting rod and the connecting rod cover are individually matched to each other at the factory. More precisely, the parts are made from one single piece. They cannot be replaced.
The connecting rod and main bearings are installed so that the locks on them and the seats match. Before installation, they must be lubricated with machine oil, wiped with a clean cloth so that there are no dust particles. The main and connecting rod covers are tightened with a torque wrench. The tightening torque is different for different vehicles. It is written in the passport, as well as in special reference books.
Finally, we note that if the disassembly and assembly of the engine is done independently, then it is better to have with you special reference literature on a specific car model.
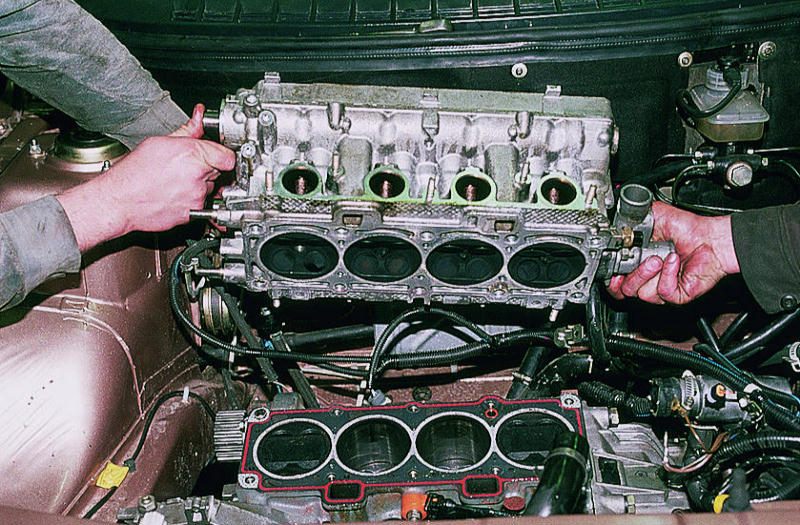
Do-it-yourself engine cylinder head removal in a garage: preparation and removal of the cylinder head. How to remove the head if it has become attached. Helpful hints.
Main and connecting rod bearings: purpose, structure and features of the plain bearings. How to properly tighten the liners, tightening torque.
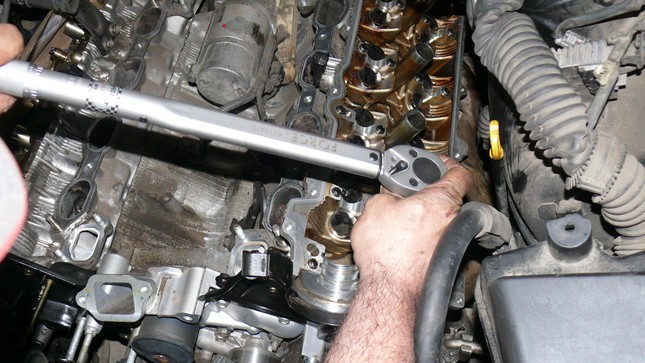
Features of the tightening of the cylinder head of an internal combustion engine. Tightening the cylinder head mounting bolts with a torque wrench: force and order of tightening.
Why and when the cylinder head needs to be ground. How to check the attachment plane of the block head with your own hands. Cylinder head milling and grinding.
How to remove a broken hairpin or broken bolt from the engine block and other components. Ways to unscrew a broken bolt, useful tips.
Purpose of internal combustion engine gaskets. Types of gaskets, materials of their manufacture: cylinder head gasket and valve covers, oil seals, cuffs and others.
We are exploring the possibility of swaping the engine or Jimny. The idea is this. The man has a Jimny with a 0.6 turbo author, he wants to sell it. I didn’t see the car myself, but it says something about the engine, but the car moves on its own. Does it make sense to acquire it with a swap sight on the M13A or M16A from Escudo. Instead of М13А, М16А is installed without problems, he smokes. To order the M13A or M16A engine as a contract.
Questions for a respected audience
1. Are the bodies of the 0.6 and 1.3 engines the same ?;
2. Will automatic transmission from 0.6 withstand М13А or М16А?
3. What about the engine mount cushions?
4. What are the nuances of such an operation? Interested in technical nuances, we will omit the legal side.
5. Is the game worth the candle?
in general a subject, where to make it cheaper?)) ask for 25k.
This is an approximate average price. In fact, there may be more, maybe less. And what about the engine, do you know?
or another question - is it possible in the E34 (1989) to shove the capacity of the E38 750I 95? after the accident, there is simply E38, in the village it is rotting))
It is possible, but the volume of work is not childish. Although the result is worth it.
25 for the capital of a 6-cylinder engine is very cheap. In our city they charge so much for Gazelevsky.
But plugging in a 5 liter engine can get even more expensive and definitely hemorrhoid. But it's worth it!
ps Let me have that choice. I would not even consider the option of capital - I immediately took up the issue of installing 5.0.
I changed it to sable, they said it was necessary to change the cylinder head gasket, it turned out that the reason was not in it. Half of the bolts are missing, etc.)) they say a thorough repair is needed.
So can put the missing bolts and the problem will be solved by itself? Although if the state is unknown, it is better to throw off your head and pallet and see what is there
Maybe for this money you can shove an engine from a 750i in there?)) Before the exchange they started up, only the radiator cap was opened.
To begin with, I advise you to download the cartest program and use it to calculate this option. and compare it with at least M5, 540 or E31. But it will cost _significantly_ more than even a major overhaul of the M20 in the conditions of advanced service, if only because a bunch of original parts will be required, which will have to be redone or, as an option, altered from existing ones (cardan, exhaust, reinforced front suspension, etc. .). If you are interested - there is a company Hartge, which at one time shoved the M70 into the E34, they still squandered it to a volume of 6 liters and boosted it to 480 hp, so half of the car had to be redrawn there, the brakes were generally put on racing and a lot more. , but such a car cost about 150 thousand dollars
Most drivers, giving their car engine to some service station for overhaul, know in advance that the repaired engine will still be somewhat worse than the new one, and its resource will naturally be less. After all, many argue like this - "the new is new." But very few drivers know what to do CORRECT overhaul engine, it will "run" much more than the new serial factory engine.
And what does the correct overhaul mean and what should it be? Most of the drivers do not even suspect about this and calmly give their engine to the service, hoping that the masters there supposedly know everything themselves. Only later on, drivers are surprised at the small resource of the repaired engine, and sin on low-quality spare parts.In this article, we will take a closer look at what the correct engine overhaul means, and perhaps after reading this article, many drivers will start choosing repairmen and a repair shop more carefully, or they will start to repair the engine on their own.
I already wrote about engine repair in this, this one, and this article, in which I described the basics of the usual overhaul of car and Japanese motorcycle engines and those who wish can click and read. But who wants to SIGNIFICANTLY increase the post-repair mileage (resource) of the engine of his motorcycle or car, then I advise you to read further.
So how can you carry out such a major overhaul of your old engine so that it becomes better than the new factory one? It’s not so difficult, if we take into account the fact that the serial production of engines is an ordinary conveyor flow, in which the serial engine parts are not given due attention, it’s simply not realistic.
Well, engine repair, even when put on stream, in some well-equipped workshop, is an art, because each engine needs an individual approach. For example, when troubleshooting parts, in which every detail is carefully studied, almost under a microscope, and sometimes it is being finalized by specialists and it becomes better than a new part.
In some competent foreign workshops, overhaul of any engine smoothly goes into its tuning, that is, finishing the serial parts to perfection. And despite the fact that such repairs are more expensive than usual (after all, manual labor is always more expensive), the demand for it is always great and customers are queuing up.
Because an engine repaired in this way is, firstly, much more powerful and more durable than a new serial motor, and secondly, it is also cheaper than a new serial motor. After all, most of the most expensive and time-consuming operations are done only at the factory, when the engine is manufactured from scratch.
And even if foreign factory (serial) engines need fine-tuning and improvement during repair, what can we say about our domestic factories, which operate in conditions of low wages for workers and a constant lack of funds for improving serial production. Where even the seat mounting bolts are hammered.
And in order to save time (and time, as you know, is money) at most domestic car factories, some important operations are deliberately neglected. For example, every engineer or metal expert knows that after casting a cylinder block, it must rest on the shelf for a certain time.
And thanks to this endurance (aging), the internal stress of each part gradually decreases, and at the same time it may even lose its shape a little (warp). And only after the part takes its final shape, only after that it can begin to be machined (select all holes and planes with a cutter).
So, in some factories, blocks and heads are not held, and as a result, after processing the holes and planes, over time the part changes shape, and already all the planes are not parallel, the holes too (for example, the bed of the shaft bearings). And the planes of the block and head connector, after assembly, will not be parallel to the crankshaft, camshaft and other engine shafts. It is not hard to guess what the engine will end up with and what its resource will be.
From the foregoing, it should be concluded that the domestic used cylinder block or head, which have worked for more than one hundred kilometers, is no worse, and even better than new parts, since over time there was a running-in of mates, sediment and parts do not need aging. And this is a big plus so that after repairs such parts become better than new factory ones.
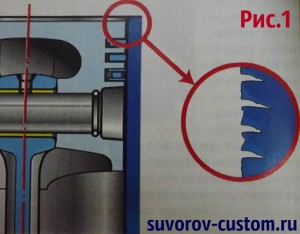
That is, it is necessary to process the walls of all cylinders with a special tool called a hone, which, after processing, will turn the surface of the cylinder walls into a rough one, with very small grooves and protrusions (when viewed under a microscope, as in Figure 1). Most drivers know that the smallest grooves on the cylinder surface keep the engine oil better (for lubricating pistons and rings).
So, for comparison and for further reflection, I will give another example that explains why domestic engines (and foreign ones too - after our repair) have such a low mileage (for new engines) and post-repair mileage too. And the thing is that at our domestic automobile factories, and in 95% of all repair shops, diamond abrasive stones are used for honing cylinders.
At foreign factories and repair shops, they never use such bars and use ugly bars, which should be changed several tens of times more often than diamond abrasives. And what is the main thing for our factories and workshops? Yes, the fact that an abrasive stone remains suitable for work even after a thousand honed blocks, because what kind of savings is obtained ?! And do not care that the engine resource will decrease dozens of times, but the production is cheap.
But why are abrasive stones for honing not used abroad and from this the resource of their engines is much longer? Yes, because when processing the surface of the cylinder with such a bar, abrasive particles are introduced (caricatured) into the metal surface of the cylinder walls, and then, when the engine is running, its pistons with rings are "eaten", and as a result, the piston wear quickly occurs.
And the ugly bars, which are used abroad, and which wear out much faster than the abrasive ones, are made of sufficiently soft alloys, and during operation they seem to not so much cut off the surface of the cylinder wall, but how much they press and smooth it. As a result, a very thin layer forms on the metal surface of the cylinder wall, which does not work as an abrasive, but rather as a solid lubricant, which significantly reduces the wear of cylinders and pistons (and reduces friction).
By the way, if anyone does not know, abroad have long forgotten what repair rings are and do not use them. Why, when on modern foreign cars (for example, fresh Mercedes), with the correct manufacture of the engine block (and some of them have a nickel coating) and a modern method of manufacturing piston rings, there is no need to change the rings, and the engine "passes" without replacing the rings a million kilometers! Who wants to know about this in detail, then click here and read on health.
Above, we examined one of the important points of correct cylinder honing, which if you use it when repairing your engine, then significantly increase its resource. But there are other important points as well. Not all drivers and even repairmen know that after installing the block on the engine and tightening its head, the geometric shape of the cylinders changes slightly, since metal is metal. That is, during compression, the cylinder (or cylinders) ceases to be strictly cylindrical, even if it was made very accurately and before compression it was so.
Correct cylinder honing.
1 - cylinder block, 2 - aluminum plate with holes instead of a head, 3 - hon with non-abrasive blocks.
And this means that to process any cylinder during repair, you need to COMPRESSED in about the same way as it will be compressed on the engine after repair. Simply put, you need to make a plate from a thick plate (or from an old head - see Figure 2), with holes for hone and for fastening bolts, which will compress the cylinders in the same way as on the engine (with the same prescribed torque).After boring the cylinders and releasing the bolts (and removing the plate and block), the geometric shape of the repaired cylinders will immediately be slightly disturbed.
But now all that remains is to assemble and install the standard engine head on the unit repaired in this way and squeeze the entire sandwich with the right moment, and the geometry of the bored cylinders will become ideal! The cylinders of the engine repaired in this way will become better than the new factory ones! Indeed, in the serial production of engines at factories, the above the right technology boring and honing are hardly used (and if they are used, then only on foreign prestigious cars).
By the way, and in most repair shops, so right motors are not repaired either, and if one of the rare repairmen does this, then you still need to look for him, which I highly recommend to you. And finally, one more nuance of the correct repair.
Most repair shops, when boring cylinders, consider the main (base) plane to be the lower plane of the crankcase (where the engine sump is). Simply put, they take and put the block of cylinders on the fixing table of the machine, then clamp the block and start processing. But none of the borers ever thinks (and if they do, then only when they make their engine), is the lower plane of the crankshaft or camshaft axis exactly parallel?
And even if this important condition was fulfilled even during mass production, especially domestic production (which is hard to believe), then from everyday loads during operation, this condition was violated over time. And maybe even just a fraction of a degree, and maybe more, but who knows and who checks? Yes, just some units of really competent minders.
By the way, there will be a layer of oil in the form of a wedge between the journal and the crankshaft liner (see Figure 3). The result of all this is accelerated wear and a naturally short engine life.
From the above, it should be concluded that before starting the processing of the block cylinders, it is very important to check the beds of the main liners (and any beds) for their exact cylindricality and alignment (the exact perpendicularity of the bed holes to the cylinder holes). And already based on this, it is correct to fix the block in the machine and process the surface of the cylinders.
If necessary, it is better not to put plates under the lower plane of the block, if this plane is not perpendicular to the axes of the cylinders, but it is better to grind this plane on a machine to correct the defect. And after that, you can already calmly lay the block on the boring machine table and grind, or honing the cylinders (again, the correct one - non-abrasive honing). Real minder professionals (unfortunately more often abroad) do just that.
And even if someone is not all able to do the correct overhaul of the engine on their own (not everyone has a machine park in their own workshop), then at least after reading this article, you will be able to adequately control the minders to whom you entrust the repair of your engine, and is it important.
I hope that if, after reading this article, you make an overhaul of your engine, taking into account all the nuances described here, then in the end you will see very interesting results of such repairs, namely: waste and oil consumption will be much reduced, as well as the exhaust of harmful substances in atmosphere (maybe it doesn't matter to someone, but yes to me),fuel consumption will slightly decrease (after all, friction losses will decrease), and the wear rate of cylinders, rings and pistons will significantly decrease.
Well, the main trick of such a correct overhaul of the engine is that the resource of your repaired engine will almost double the resource of an absolutely new factory serial engine; success to all!
The familiar machine operators asked to repair the engine of the BMW 525i car. Car 1989 year release (27 years old !!), in the back E34... After washing the engine, the car somehow limped to the workshop - the thin wiring was hostile to the water in the engine compartment.
The car was originally equipped with an engine M20B25 - inline six, volume 2.5 liters, with a capacity of 170 hp. But the engine suffered a well-known "disease" - the head moved from overheating, it burst. The owner bought an engine for analysis a few years ago M20B20 - the same in-line six, but with a smaller volume (2 liters) and less power - 129 forces. After leaving for several years, he wished to restore his own engine. Moreover, it became possible to "mend" a crack in the head using a new technology - Seal-Lock.
For a complete understanding of what kind of retro car we came across, I will only note that the mileage on the odometer is 545 thousand km! Those. the native 2.5-liter engine passed the order half a million kilometers, and survived one “capital” with block boring in the first repair size 84.25 mm.
To get started, we were given the “remains” of the native M20B25 engine - an assembled block and a bunch of spare parts from the engine in bulk. It was necessary to carry out troubleshooting and start work on the restoration of the motor. The owner of the car had to do the darning of the burst head of the block. First, remove the pallet from the engine.
Crankshaft bearings in extremely poor condition. On the surface - smeared bronze from the liners of the oil pump flush. Its inserts were made by the client himself from pieces of bronze. As he said, after the manufacture and replacement of the liners, the motor worked for 5 minutes, then jammed the washer and cut the teeth on the timing belt. After increasing the mounting gap, the motor worked for some time (obviously, until the head was cracked).
The connecting rods have a bronze bushing and a floating pin. The pistons are heavy, similar to VAZ pistons from tens or Niva. The block was sharpened to 84.25 mm, there is no hone on the cylinders, there are traces of sticks on the pistons.
The crankshaft has a lot of wear on the journals and deep wear under the oil seals. Neck in nominal size.
It looks like the motor was collected with dirt or was poorly washed before assembly - there is strong abrasive wear on all rubbing surfaces.
The design of the block is extremely simple - it is a “big classic” with a timing belt drive. The last photo shows the condition of the cylinders - we will re-grind the block to the repair size. By the way, the block does not have any oil cooling nozzles for the pistons. You can argue for a long time about their necessity or uselessness, the author will retain his opinion. It is possible to embed injectors into this block without any problems, but will the oil pump cope? Since the presence of injectors does not play any role for the client, we will leave everything as it is (i.e. in the standard version).
In general, the bottom of the motor left the impression of "simplicity to horror." However, what to expect from an ancient motor from the 80s? Everything is heavy, cast iron, simple.
Let's think, is there any point in repairing the engine of such a machine at all? While the client was mending the head, we started examining the machine hanging on the lift.
The condition of the body is very mediocre. Numerous foci of corrosion, body painted and with a lot of defects. Mufflers and resonators rotted long ago - they were completely scalded with sheets of metal. Now they are mufflers.
The car is quite popular with young people, thanks to the unforgettable films from the 90s, which made it an icon for the fans.But let's turn to the facts - the car has a long body, but according to the passport it weighs only 1200 kg (according to other sources 1360 kg), what is the car made of? The salon is crowding, the author with not very tall stature at the wheel beats his head against the lintel.
In general, let's leave the admiration for this model to the circle of fans and move on to what the client asked us about - to work with the motor.
Let's see under the hood. There is a two-liter M20B20 - it needs to be dismantled. It works fine in general, except for the current oil seals, but the owner wants to return to its place a more powerful 2.5-liter. There is a lot of space under the hood. Get in at least with your feet. We remove attachments, drain oil, antifreeze, remove the radiator.
There are no problems with timing marks - everything is visible and accessible. The motor is very simple, quick and easy to disassemble.
It was planned to remove the complete engine, tk. we didn't need to disassemble the two-liter engine. However, while we were fiddling with the attachment, the killer news came - the client could not "mend" the head from the 2.5 liter engine! A few words should be said about technology Seal-Lock... The author has heard about it more than once, but until now it was not possible to face it personally. They drill into the crack, cut a thread and screw the tapered pins onto the glue, which are then riveted. Frankly, the author never had any confidence in this strange technology. Advertising brochures are full of catchy slogans that literally everything is “darned” - both blocks and heads. But the engineering mind immediately sees a bunch of limitations and hidden problems. Physically, the integrity of the casting has already been broken and the pins will not restore it.
In the confusion, they forgot to take a photo of the crack - it is huge and goes through a pair of camshaft bearings. Vaunted Seal-Lock turned out to be a bad decision and the head, in the process of darning, continued to burst in new places and siphon on pressure testing like a sieve.
In general, we found ourselves at a broken trough - a 2.5-liter engine, for which we had already ordered repair rings and pistons, was not equipped with a head, and we almost got the 2.0 engine out of the engine compartment. It should be noted that the heads of 2.5 and 2.0 liters non-interchangeable between themselves. The head of the 2.52.7 liter engine has a diameter of the intake and exhaust valves increased by 2 mm, the intake ports are also increased in diameter (the manifolds are the same), and most importantly, the pistons and combustion chamber in the head differ.
The client pulls the hair out on his head and is completely at a loss. We are asked to “do something”. In general, everything is as usual, and the ghost of HondoVaz hovered over their heads.
We need to compare the hardware live. We remove the head from the two-liter engine. Along the way, it should be noted that the motors of the series M20 have SOHC layout (one camshaft and 2 valves per cylinder). Valve drive - through rockers with mechanical clearance adjustment. According to the manual, the adjustment is every 10-20 thousand km, the client never adjusted the valve.
The procedure for installing a Single VANOS system repair kit on M50TU and M52 engines is not very complicated and does not require special skills in engine repair. For installation, it is desirable to have some special tools to facilitate the procedure, but in the absence of them, repair is quite possible. The three most important points in this procedure: be sure to adjust the bearing to achieve the desired preload in the bearing, correctly set the timing phases and correctly install the VANOS system on the motor after repair. How to do all this is described below. If you doubt your abilities, we recommend that you contact the service station, which will be able to perform this procedure using this manual.
The VANOS itself is located at the front of the cylinder head (cylinder head). In order to get to it and dismantle it to install the repair kit, you need to remove the valve cover, remove the thermal coupling. Please note that if the valve cover profile gasket has changed more than 40,000 km ago, you better replace it to avoid oil leakage.
Special tool
To install a VANOS system repair kit on M50TU and M52 motors, it is advisable to have special dealer tools, as in the photo above: a camshaft lock (11-3-240), a flywheel lock (11-2-300), a sprocket scrolling tool (11-5- 490), a chain tensioner retainer (11-3-292) or just a nail of a suitable diameter.
But even in their absence, the installation of a repair kit is quite possible, but you have to sweat when installing the vanos in place in order to correctly set the timing phase (see TIS BMW).
Removing Vanos
Having removed the valve cover, we need to set the piston of the 1st cylinder to TDC, so that the marks on the crankshaft pulley and the timing cover match.
The motor can be scrolled with a wrench or head 22 clockwise.
The camshaft cams will be approximately in this position.
The top plane of the exhaust camshaft square will be parallel to the plane of the cylinder head.
Check the alignment of the labels.
After the marks have coincided, you need to fix the handwheel in this position using a special tool (you can use a conventional drill of a suitable diameter and length).
The latch hole is located on the left side of the engine under the starter motor. First remove the plastic cap with a screwdriver.
Install the camshaft retainer.
Unscrew the valve on the vanos hydraulic hose (key 19). Note: Replace the two sealing washers when reassembling.
Remove the lifting eye of the motor by unscrewing it from the head of the block.
Disconnect the vanos solenoid electrical connector. To do this, press down on the metal clip and pull on the connector.
Remove the retaining washers with fine nose pliers. Pull out the cable cover.
M52 only: Unscrew the vacuum pipe.
Lower the tube so that it does not interfere with the removal of the vanos.
Unscrew the two plugs in the vanos body to access the bolts securing the timing sprocket (key 19).
Place a rag or paper towel between the sprocket and the vanos body to avoid accidentally dropping the bolts.
Unscrew the 4 screws securing the sprocket (Torx E-10).
Press the chain tensioner pad in order to press it in, insert the retainer into the hole (you can use a nail of a suitable diameter).
Unscrew the 6 nuts securing the vanos to the motor head.
Cover the A / C and alternator belts with a paper towel to avoid getting oil on them. We remove the vanos from the engine. To do this, install the special tool (11-5-490) on the exhaust camshaft sprocket, pull the vanos forward towards the radiator while turning the sprocket clockwise with the tool. Please note that the sprocket must be unscrewed from the camshaft as indicated above for the instructions. In the absence of a special tool, you can gently turn the sprocket using a screwdriver inserted into the timing chain.
We disassemble vanos and diagnose it:
Remove the bolts securing the vanos cylinder cover to the body.
Remove the cover together with the piston and helical gear from the body.
Now you can diagnose and inspect the unit. First, visually inspect the piston for cracks or chips. Next, you can diagnose the tightness of the assembly. To do this, insert the piston into the cylinder and move it along the working stroke. Remember how easily the piston moves in the cylinder with the old O-rings.
Next, let's proceed to diagnostics of the bearing in the vanos piston.
Check for backlash, as shown in the photo above: wiggle the helical gear in different planes. Only the presence of a radial play is allowed, which is necessary for the correct functioning of the unit. Axial play is not allowed and means that the bearing is loose and needs to be repaired.
Install the anti-backlash washer from the repair kit
Attention! Washer installation must be done prior to installing new O-rings.
Fix the piston in a vise as shown in the photo above. Use special soft sponges or wooden spacers.Be extremely careful not to damage the piston surface or overtighten the vice, as the piston is very fragile.
We unscrew the vanos piston cover with a head of 18 (in some motors there may be a head of 17). The thread is ordinary, you need to unscrew it counterclockwise.
Attention. The slots on the cover are very low and a normal head will have a small hook, which will lead to licking of the slots and it will be impossible to unscrew this cover in the future. To do this, you need to specially modify the head by grinding off the chamfer from the end, so that the head fits more tightly to the lid and there is good engagement. You can grind both on a lathe and on a regular grindstone. It is important that the head is hex. The photo below shows a sample of the modified head.
Having unscrewed the cover, we put the piston in an upright position and fix it in a vice.
Next, take out the needle bearing.
We unscrew the bearing bolt. Attention. There is a left-hand thread. Unscrew clockwise (Use Torx T30 sprocket).
We take out the central bearing race.
Remove the piston from the gear axis.
Then remove the outer bearing washer.
Thoroughly clean the bearing parts with a brake disc cleaner (thinner or benzine).
Insert the bottom washer into the piston.
Reinstall the anti-play washer from the repair kit.
Reassemble the bearing parts in reverse order. Install the bolt with the Torx T30 sprocket. Attention! Left hand thread! Screw the bolt counterclockwise! (tightening force 8Nm).
Replace the upper bearing and washer.
Replace the piston cover.
Secure the piston body in a vise.
Tighten the piston cover. Do not tighten it to the final torque, as you will most likely have to disassemble the bearing again to fit it.
Now we need to check for the presence of the required radial play. Then rotate the piston axially, thereby checking the rolling resistance of the bearing. After installing a new washer, the piston should rotate on the bearing without much resistance. If the bearing is very “tightened”, then it is imperative that the bearing center race be adjusted (see “Tightening Tightened Bearing” below). If the piston still has an axial play and it is very easy to spin on the bearing, then you need to adjust the installed washer from the repair kit (see below “Fitting a loose bearing”).
Fitting a Tightened Bearing:
Disassemble the bearing again and remove the center race (washer that is between the two needle bearings).
Place a sheet of sandpaper (P400) on a hard and level surface and sand the washer on both sides. Grind the washer evenly for a couple of minutes on sandpaper, clean it, assemble the bearing and again check how the bearing turns. Repeat the trimming procedure as necessary until the bearing spins without much resistance.
Loose bearing fit:
Disassemble the bearing again and remove the outer washer (the washer that was installed from the repair kit).
Place a sheet of sandpaper (P250-P400) on a hard and level surface and sand the washer on both sides. Grind the washer evenly on sandpaper for a couple of minutes, clean it, reassemble the bearing and again check the axial play and whether the bearing is pinched during torsion. If necessary, repeat the adjustment procedure until the axial play disappears, but the bearing should rotate without much resistance.
When the fit is achieved, tighten the bearing cap to 40 Nm.
Replacing the O-rings from the repair kit
Having eliminated the vanos bearing play, you can start installing new sealing rings.
Carefully cut the old o-rings with a suitable cutting tool. Be extremely careful not to damage the working surface of the piston!
After you have cut and removed all the o-rings, wipe the piston with a paper towel and clean the ring groove well.
Install the rubber ring into the groove first.
Check that the rubber ring (it has a circular cross-section) is not twisted in its place.
If the installation is carried out at an air temperature below 20 degrees Celsius, then it is necessary to put the Teflon ring in warm water (40-50C) for a couple of minutes to make it elastic. Then wipe the ring dry and install.
Pull the Teflon ring gently and slowly from one end of the piston to the other.
Lubricate the housing cylinder and the piston itself with new rings well with engine oil. Insert the piston into the cylinder at an angle of approximately 30 degrees and rotate it into the cylinder.
Rotate the piston in the cylinder several times and move it up and down so that the ring takes the shape of a cylinder. Repeat this operation until the Teflon ring stops turning in its groove.
Press the piston to its lowest position and let it stand for 2-3 minutes.
Then remove the piston. The ring has acquired the desired shape.
Reinstall the piston. Press the plunger in completely. Tighten 5 screws (torque 10 Nm).
Installing Vanos
Clean all parts and surfaces from oil and dirt residues. Install a new gasket.
Install the special tool onto the sprocket. Scroll the sprockets clockwise until they stop. Attention! This operation is indispensable for the correct installation of the vanos.
Attention! The next installation step is very important: before installing the vanos on the motor, press the splined shaft with the piston into the housing. Install the vanos body onto the pins of the block head. Insert the splined shaft into the intake sprocket by twisting it slightly.
In order for the spline shaft to fully enter the sprocket, it is necessary to turn the exhaust sprocket counterclockwise and at the same time press the vanos against the motor. Very important! So that the splined shaft goes into the sprocket in the extreme right position of the sprocket. This will give the correct range to adjust the phases while the vanos is running.
Screw the vanos to the motor. Tightening torque for nuts 8 Nm.
Remove the upper timing chain tensioner retainer.
Reinstall the 4 bolts securing the exhaust sprocket to the camshaft. Tighten the bolts crosswise (Torx E-10) with a torque of 20 Nm.
Replace the plugs on the vanos body.
Reinstall the wiring cover and install the clips with fine nose pliers.
For M52 engines: Install the vacuum pipe.
Connect the electrical connector of the vanos solenoid.
Screw on the motor loop.
Screw on the hydraulic hose using new sealing washers (19mm wrench).
Remove the tool for fixing the camshafts, remove the flywheel retainer, reassemble everything in reverse order using BMW TIS. Be sure to check that there are no oil residues on the belts and rubber hoses.
Be sure to check the oil level after assembly!
It is important to know that the O-rings should be run in approximately 300 km in the urban cycle. Try not to load the engine with high revs and active driving during the break-in period.
![]() |
Video (click to play). |
Enjoy the smooth running of your motor.