In detail: do-it-yourself yamz 650 engine repair from a real master for the site my.housecope.com.
Repair manual YaMZ 650 (pdf, 14.3 Mb)
Operation manual for YaMZ 650 (pdf, 3.5 Mb)
Technical materials for YaMZ 650
- copies of certificates of conformity:
- dimensional drawing of the engine:
Advertising materials for YaMZ 650
- presentation of the YaMZ 650 engine part 1 part 2 part 3
YaMZ-650 engine. MR - Part 16
DISASSEMBLY AND ASSEMBLY OF ENGINE UNITS
Dismantling the fuel pump.
(cm. Rice. 91)
1. Unscrew the bolts (1).
2. Compress the fuel priming pump
(2) with a plastic hammer (3).
3. Remove the fuel priming pump (2).
4. Remove the fuel supply pump gasket.
5. Unscrew the bolt (1) (cm. Rice. 92a).
6. Remove the phase sensor (2) (cm. Rice. 92b).
7. Remove the phase sensor gasket (3).
Rice. 91. Removing the pump
fuel pump.
Rice. 92. Removing the fuel pump phase sensor.
Here is a link:.
It turns out that we have 2 liters of “loss” loaded and 1.25 liters empty, about 100 km of the way.
If we take into account that under a load of 20 tons + transport (about 15 tons minimum), we get from 35 to 40 tons of total cargo.
400 strong motor STE is quite on the float, but less than 1300 min-1 we will not go down, we will take the average value of 1350 rpm.
So, at an average speed of 50 km / h, we will cover 400 km in just 8 hours. Multiply 8 by 60 minutes = 480 minutes x 1350 = 648,000 rpm to the motor shaft. If in one revolution a 4T in-line 6 makes three working cycles, then in 648,000 it will make 1,944,000 working cycles. Those. if all cylinders are guilty of “missing” coolant, then divide 8 liters by 1944000 = 0.0041 ml (4.1 mm3 in volume) for each cylinder; or one culprit "eats" coolant, then 8 liters will disappear like this - 8/648000 = 0.0123 ml per cycle of one cylinder. may well be the case. one hundredth ml. in STE volume about 12.3 mm3. STE is just such a minuscule amount of the cylinder volume of this engine, which is only 6.6-1000000% of its volume.
![]() |
Video (click to play). |
In general, the motor eats everything and does not even chiHnetttt.
- thoroughly clean and check all parts;
- it is recommended to unpack the new bearing immediately before installation, do not remove the preservative grease from the new bearings;
- it is forbidden to reuse retaining rings and seals removed during disassembly;
- if the parts are tight, do not use a copper or brass hammer;
- all parts intended for pressing must be pre-lubricated;
- it is recommended to use a specially adapted mandrel every time in order to exclude the ingress of metal particles into the crankcases and bearings;
- some o-rings must have grease inside the flanges;
- parts mounted "hot" are heated by a stream of hot air in a heat chamber.
Before starting assembly, thoroughly clean all surfaces of the parts to which the sealants will be applied. Remains of the old funds must be removed. Threaded connections are cleaned with a brush and tapped if necessary.
1. Install the engine crankshaft (See the article "Installing the crankshaft YaMZ-650")
2. Install the connecting rod-piston group (See the article "Repair of the connecting rod-piston group YaMZ-650")
3. Install the end plate:
Apply Loctite 518 end sealant to the end of the cylinder block, as shown in Fig. one.
Install the two rails in the cylinder block.
Install the end sheet in place and screw on the bolts of its fastening to the cylinder block.
4. Install the axles of the intermediate gears.
Tighten the plate fastening bolts with an end torque of Mcr = 20 ± 4 Nm, and the bolts of the axles of the gear wheels with an intermediate torque Mcr = 90 ± 18 Nm according to the order in Fig. 2.
4. Install the flywheel housing:
Install the guide pin into the cylinder block.
Apply sealant to the end of the block to fit the flywheel housing (see Fig. 3).
Install the flywheel housing on the block and screw on the bolts of its fastening.
Tighten the crankcase mounting bolts to the following torque:
- for bolts М14 - Мкр = 150 ± З0 Nm;
- for bolts М8 - Мкр = 20 ± 4 Nm.Apply Loctite 542 sealant to the threaded part of the М8х1.25 -100 mm bolt
5. Install the flywheel housing seals (see Fig. 4):
Place special tool 2562 and protective ring (A) on it.
Install the crankshaft seal after lubricating the outer surface (Michelin-Tigre80 or Pneufix grease).
Remove special tool 2562.
The cuff comes with a protective ring that fits over the installation tool. The lip must remain on this ring until it is completely seated in the crankcase. Do not lubricate the flanges. Do not use the cuff that has been removed from the ring.
The cylinder block is installed on the stand (see Fig. 5), fixing it with fixing pins for the four holes of the block. Bolts with spring washers secure the starter bracket. Screw plugs and a square for oil drainage to the compressor are screwed into the holes of the block. The plugs and the square are placed on nitro putty, red lead or lead whitewash. Then, using a mandrel (Fig. 108, a), the oil seal of the fuel pump drive shaft is pressed in, maintaining a distance of 69 mm from the end of the socket for the front bearing to the oil seal. Using a safety mandrel (Fig. 108, b), install the driven gear wheel of the fuel pump drive assembly with the shaft and bearings. The bolts of the thrust flange are secured by bending the edges of the lock washers on the edge of the bolts. The pushers are mounted in the following order. In the bore of the rear partition of the cylinder block 8, the rear
bushing 6 (Fig. 109); in the rear bushing insert the extreme axis 7 with the pushers 2 and the spacer sleeve 3 put on it and put the intermediate bushing 5 of the pusher axes. Other axles assembled with pushers and their bushings are installed similarly. The pushers should rotate on the axles easily, without jamming. When installing the camshaft assembly with gears and a thrust flange, ensure that the marks on the drive 5 (see Fig. 54) and the driven gears of the fuel pump drive match. The thrust flange of the shaft is screwed in by placing lock washers under the bolt heads. The flange must cover the hole under
axle in the front pusher axle bush. The circumferential clearance and in the meshing of the gears should be 0.09-0.22 mm. After installation, it is necessary to bend the edges of the lock washers on the edge of the bolts.
After removing the crankshaft main bearing caps, wipe the connector planes and beds under the liners, put the liners and main bearing caps in place and, lubricating the liners with diesel oil, lay the crankshaft, ensuring that the marks on the crankshaft gear 3 and camshaft gear 4 are aligned. Bushings with holes and grooves are installed in the block slots. The repair size of the main bearing shells must match the repair size of the crankshaft main journals.
Then, thrust half rings of the crankshaft are installed in the grooves of the rear main support of the block so that the sides of the grooved rings adjoin the thrust ends of the shaft, check the protrusion of the pins above the mating plane of the thrust half rings in the rear cover (6.2-6.8 mm) and set the thrust half rings into the cover with grooves to the thrust ends of the crankshaft.
Having lubricated the liners placed in the main bearing caps with diesel oil, the caps are installed in accordance with the marking. The serial number of the cover must coincide with the number of the support on the block, while the branded side of the cover must face the left row of cylinders. The numbering of the supports on the block starts from the front end.
The bolts of the main bearing caps, except for the rear ones, starting from the middle and ending with the extreme ones, are tightened in two steps (moment 30-32 kgf-m). Before tightening the rear main bearing, it is necessary, by slightly tightening the cover with the bolts, move the crankshaft back and forth, aligning the position of the cover, and only then tighten the bolts. All bolts should be pinned in pairs, tightly, but without tears, pulling the cotter pin-wire. The ends of the wire must not protrude beyond the ends of the cover.After tightening the bolts, the total axial clearance between the shaft and the thrust half rings should be 0.08- - 0.23 mm, the circumferential clearance in engagement
crankshaft and camshaft gears in working position 0.09-0.22 mm (dimension a in Fig. 54). After tightening the main bearing bolts, the shaft should be able to turn easily by hand using the pins.
The oil seal is pressed into the cover of the distribution gears using a mandrel (Fig. 110, a). After pressing the oil seal, put in place the right and left gaskets and the cover of the distribution gears.To protect the oil seal from damage when installing the cover, use the mandrel shown in Fig. 110, b.
Next, having previously placed gaskets, the water pump is fixed on the studs of the distribution gear cover with nuts and spring washers, the fan drive and the upper cover of the block are fixed. The top cover hatch is closed with a plug. The pneumatic brake compressor is mounted after the engine acceptance tests.
Then the engine front support bracket is installed, four bolts are tightened (torque is 9-11 kgf-m), the crankshaft pulley key is pressed in, the pulley is pressed against the stop and secured with a bolt. Having unscrewed three nuts, remove the sidewall of the water pump pulley, put on the belt, put the sidewall of the pulley in place and check the belt tension. The deflection of the branch under the action of a force of 3 kgf applied to the middle of the branch should be 10-15 mm. If it is necessary to increase the belt tension, reduce the number of shims between the pulley sidewalls. The removed gaskets are placed under the nuts on the outside of the pulley sidewall.
Using a mandrel / (Fig. 111, a), press the oil seal 2 into the flywheel housing 3, put the gasket and the flywheel housing in place.
To protect the oil seal from damage during the installation of the flywheel housing, a special mandrel is put on the rear end of the crankshaft 4 (Fig. 111, b). The crankcase mounting bolts are tightened in two steps (the final tightening torque is 8-10 kgf-m). After tightening, check the ease of rotation of the pushers.
The flywheel is installed on the crankshaft pins. To facilitate the installation of the flywheel in the required position on the flywheel hub and on the end of the crankshaft, the numbers 2 are stamped (Fig. 112), which must be aligned during assembly. The flywheel is attached to the crankshaft with eight bolts, placing a lock plate under each two bolts. The bolts are tightened in two steps. The final tightening torque is 20-22 kgf-m. The locking plates are bent on the edge of the bolts, as shown in Fig. 112.
After that, the breather is fixed with two bolts with spring washers to the end of the block and a clamp to the flywheel housing, a centrifugal oil filter is installed, ensuring that the holes for the oil passage in the block and the gasket match (if necessary, the gasket should be turned on the other side), a coarse oil filter is attached and fine fuel filter. When installing a high-pressure fuel pump assembled with an automatic clutch and a regulator, a stand is placed under the protruding end of the shaft 4 (Fig. 113) of the pump drive and the key is pressed in, the half-coupling 7 is put on the shaft 4, aligning the marks a on the flange 5 and the half-coupling 7; install a high-pressure fuel pump with an automatic clutch and a regulator; put washer 8, ensuring the gaps between the cams of the driving half of the coupling and the end of the automatic clutch 9 within 0.7-1.0 mm (the marks on the leading half of the coupling must be aligned), tighten and cotter the nut 13 for securing the half of the coupling.
The low pressure fuel pipes are then secured. The fuel supply pipe to the injection pump should not touch the bolt of the injector drain pipe and the block top cover. Place sealing washers under the tube ends and hollow bolt heads.
After wiping the seats of the liners and the cylinder block, a selected set of liners is installed in the bore of the cylinder block.The protrusion of the sleeve collars above the plane of the block should be 0.07-0.16 mm; the difference in protrusion values within one cylinder bank should not exceed 0.08 mm. After measuring, the position of the sleeve in the block should be marked with a mark embossed on the upper non-working surface of the sleeve collar in the direction of the front part
engine; remove the sleeves from the block, put the O-rings and anti-cavitation rings lubricated with oil into the grooves, and install the sleeves into the block. The branded side of each liner should face the front of the engine. When assembling the connecting rod-piston set, on one side of the piston / insert the circlip 13 (Fig. 114) of the piston pin and, using the tool (see Fig. 15), put on successively the lower and upper oil scraper rings 4 (see Fig. 114), the third , the second 3 and the first 2 compression rings. The bevels at the ends of the compression rings should be directed upward to the piston bottom, and the locks of the adjacent rings should be turned in opposite directions. Next, the piston with rings should be kept in an oil bath for 10 minutes at an oil temperature of 80-100 ° C, the connecting rod 6 should be installed in the piston so that the axis of the upper connecting rod head coincides with the axis of the hole for the piston pin, and allowed). The combustion chamber of the piston in must be displaced towards the long bolt 9 of the connecting rod cover. Thereafter, a second retaining ring is installed. Having unscrewed the connecting rod bolts 9 and 10, remove the connecting rod cover 8 together with the bolts and put the liners 7, aligning the projections of the liners
with grooves in the beds. The size group of the set of connecting rod bearings installed on the engine must correspond to the repair (or nominal) size of the connecting rod journals of the crankshaft. Used inserts are recommended to be placed in the beds where they were installed earlier and always in pairs. Having lubricated the liners with diesel oil, using technological mandrels 14, the pistons, complete with connecting rods, are inserted into the liners // of the cylinders, pre-lubricated with oil. The combustion chambers in the pistons must be offset to the axis of the engine. The connecting rod caps are tightened with their fastening bolts (tightening torque 17-19 kgf-m), starting with a long bolt. The total axial clearance between the ends of the lower heads of the connecting rods and the cheeks of the crankshaft should be 0.15-0.57 mm. Measurements are made between the ends of the connecting rods and their caps. If the gap
The tightening procedure for the nuts is shown in fig. 116.

5-3-6; for the YaMZ-238 engine; 1-5-4-2-6-3-7-8. The cylinder numbering scheme is shown in Fig. 117.
Then a set of nozzles is installed, with which the injection pump was tested and adjusted. Place no more than one sealing washer under the spray nut. The fastening nut of the bracket is tightened with a torque of 5-6 kgf-m. Next, place the drain pipes of the injectors and the fuel outlet pipe and fix the latter with a clamp on the intake manifold stud. After that, it is necessary to install the cylinder head covers, the connecting pipe of the intake manifolds with the flange of the compressor pipe to the front of the engine, the air filter, assemble the connecting and bypass pipes of the water thermostats with hoses and clamps and install them on the engine, remove the engine from the stand, put it on a stand and install starter and transport seals.
The fan impeller, generator and compressor, as well as the clutch and gearbox, are assembled after the engine has been completed.
In-line diesel engine YaMZ-650 - this is the Russian version of the French DCi11 engine, the license for the production of which "GAZ Group" acquired from Renault Trucks in 2006. The engine has proven itself well on Renault trucks.It is planned to supply licensed engines to the Minsk Automobile Plant, to AvtoKrAZ and, in the future, to the Kharkov Tractor Plant. With the help of the new engine, GAZ Group intends to update Ural vehicles as well.
This power unit with a working volume of 11.12 liters and a maximum power of 412 hp. will supplement the existing model range of YaMZ engines and will be produced simultaneously with the home-grown V-shaped "eight" YaMZ-658.10 power of 400 hp, which also complies with Euro 3. By the way, if we carry out a brief comparative analysis, it turns out that the YaMZ 650.10 engine has a higher (37.7%) liter capacity, 5.5% more torque moment less by 280 kg in weight and slightly lower fuel consumption. In addition, the in-line "six" is almost ideal in terms of poise.
It is important to note that JSC Avtodiesel is engaged in the production of the DCi11 engine independently, using a French technological line and equipment, and is not an assembly plant. In accordance with the signed agreement, equipment was transported to the Yaroslavl region from the plant in Lyon, and a group of engineers and workers of YaMZ underwent an internship at Renault Trucks and at the enterprises of Bosch. Why did France refuse to manufacture this engine? Renault Trucks President Stefano Szmielewski explains it this way. After the conclusion of the alliance between Renault Truck and Volvo, it was decided to equip all truck models with Volvo engines. Replacing its predecessor "six" of the next generation, the 11-liter DXi11, although produced in France, was created with the participation of the same Volvo, on the basis of its 9-liter unit.
Before shipment to the customer, each engine is subjected to hot run-in at the stand. For this, a special laboratory is equipped at TERZ. The engine is filled with pre-heated engine oil and coolant, and then runs in different modes for about 20 minutes. By the end of 2007, 500 engines will roll off the assembly line in the commissioning mode, and the design capacity of production is 20,000 units per year. The engine resource before overhaul is 1,000,000 km.
So far, YaMZ-650 engines are manufactured from assembly kits supplied by Renault Trucks, but now the plant has two Russian suppliers. Knorr-Bremse two-cylinder air compressors come to the conveyor from Nizhniy Novgorod (the plant of the Knorr-Bremse group of companies operates there), and the wiring harnesses come from Saratov (from the Bosch Saratov enterprise). It is planned that further localization of production will begin only in the second half of next year. It will be carried out using a number of units and parts produced at the enterprises of the GAZ Group and other machine-building plants of the Russian Federation, which have modern technologies.
Using non-standard 518DLLA155P180 nozzles and air cleaning problems resulted in burnout.
The engine oil was not changed for MOT. In the interval between the second and.
The oil pump drive chain broke 77 thousand kilometers. Warranty.
The overhauled engine is out of order. After the repair of the engine c.
The reason for the failure of the Subaru engine. The recommendations of the car manufacturers should be followed.
The examination of the tanker for compliance with GOST R 50913-96 was presented to the Technical expert.
The owner of the warranty bus decided to save money on replacing the timing belt c.
Having bought a "new" tractor Kirovets K-700 through an intermediary, its new owner.
As a result of refueling with bad gasoline, the engine pistons burned out. Mazda CX-9 car.
Maintenance of the Komatsu tractor caused engine damage. The Komatsu tractor is out.
At the last maintenance service by the mechanics of the organization - the dealer was found.
3 three hundredths of a millimeter. it is also 0.03 mm.it is (For You to Represent) a millimeter Divided into 100 parts. and only 3 parts from that.
This is Very Little.
Because of this, pressure cannot appear or disappear with a difference of 2-3 values.
that it was different. They don't tell YOU.
Based on what I have read, I think that the heat exchanger is also crap on their part.
How sad it sounds.
But you have to take the Car From There. As soon as possible. and look for a new place of repair or YOURSELF!
The cylinder block is installed on the stand (see Fig. 5), fixing it with fixing pins for the four holes of the block. Bolts with spring washers secure the starter bracket. Screw plugs and a square for oil drainage to the compressor are screwed into the holes of the block. The plugs and the square are placed on nitro putty, red lead or lead whitewash. Then, using a mandrel (Fig. 108, a), the oil seal of the fuel pump drive shaft is pressed in, maintaining a distance of 69 mm from the end of the socket for the front bearing to the oil seal. Using a safety mandrel (Fig. 108, b), install the driven gear wheel of the fuel pump drive assembly with the shaft and bearings. The bolts of the thrust flange are secured by bending the edges of the lock washers on the edge of the bolts. The pushers are mounted in the following order. In the bore of the rear partition of the cylinder block 8, the rear
bushing 6 (Fig. 109); in the rear bushing insert the extreme axis 7 with the pushers 2 and the spacer sleeve 3 put on it and put the intermediate bushing 5 of the pusher axes. Other axles assembled with pushers and their bushings are installed similarly. The pushers should rotate on the axles easily, without jamming. When installing the camshaft assembly with gears and a thrust flange, ensure that the marks on the drive 5 (see Fig. 54) and the driven gears of the fuel pump drive match. The thrust flange of the shaft is screwed in by placing lock washers under the bolt heads. The flange must cover the hole under
axle in the front pusher axle bush. The circumferential clearance and in the meshing of the gears should be 0.09-0.22 mm. After installation, it is necessary to bend the edges of the lock washers on the edge of the bolts.
After removing the crankshaft main bearing caps, wipe the connector planes and beds under the liners, put the liners and main bearing caps in place and, lubricating the liners with diesel oil, lay the crankshaft, ensuring that the marks on the crankshaft gear 3 and camshaft gear 4 are aligned. Bushings with holes and grooves are installed in the block slots. The repair size of the main bearing shells must match the repair size of the crankshaft main journals.
Then, thrust half rings of the crankshaft are installed in the grooves of the rear main support of the block so that the sides of the grooved rings adjoin the thrust ends of the shaft, check the protrusion of the pins above the mating plane of the thrust half rings in the rear cover (6.2-6.8 mm) and set the thrust half rings into the cover with grooves to the thrust ends of the crankshaft.
Having lubricated the liners placed in the main bearing caps with diesel oil, the caps are installed in accordance with the marking. The serial number of the cover must coincide with the number of the support on the block, while the branded side of the cover must face the left row of cylinders. The numbering of the supports on the block starts from the front end.
The bolts of the main bearing caps, except for the rear ones, starting from the middle and ending with the extreme ones, are tightened in two steps (moment 30-32 kgf-m). Before tightening the rear main bearing, it is necessary, by slightly tightening the cover with the bolts, move the crankshaft back and forth, aligning the position of the cover, and only then tighten the bolts. All bolts should be pinned in pairs, tightly, but without tears, pulling the cotter pin-wire. The ends of the wire must not protrude beyond the ends of the cover. After tightening the bolts, the total axial clearance between the shaft and the thrust half rings should be 0.08- - 0.23 mm, the circumferential clearance in engagement
crankshaft and camshaft gears in working position 0.09-0.22 mm (dimension a in Fig. 54).After tightening the main bearing bolts, the shaft should be able to turn easily by hand using the pins.
The oil seal is pressed into the cover of the distribution gears using a mandrel (Fig. 110, a). After pressing the oil seal, put in place the right and left gaskets and the cover of the distribution gears.To protect the oil seal from damage when installing the cover, use the mandrel shown in Fig. 110, b.
Next, having previously placed gaskets, the water pump is fixed on the studs of the distribution gear cover with nuts and spring washers, the fan drive and the upper cover of the block are fixed. The top cover hatch is closed with a plug. The pneumatic brake compressor is mounted after the engine acceptance tests.
Then the engine front support bracket is installed, four bolts are tightened (torque is 9-11 kgf-m), the crankshaft pulley key is pressed in, the pulley is pressed against the stop and secured with a bolt. Having unscrewed three nuts, remove the sidewall of the water pump pulley, put on the belt, put the sidewall of the pulley in place and check the belt tension. The deflection of the branch under the action of a force of 3 kgf applied to the middle of the branch should be 10-15 mm. If it is necessary to increase the belt tension, reduce the number of shims between the pulley sidewalls. The removed gaskets are placed under the nuts on the outside of the pulley sidewall.
Using a mandrel / (Fig. 111, a), press the oil seal 2 into the flywheel housing 3, put the gasket and the flywheel housing in place.
To protect the oil seal from damage during the installation of the flywheel housing, a special mandrel is put on the rear end of the crankshaft 4 (Fig. 111, b). The crankcase mounting bolts are tightened in two steps (the final tightening torque is 8-10 kgf-m). After tightening, check the ease of rotation of the pushers.
The flywheel is installed on the crankshaft pins. To facilitate the installation of the flywheel in the required position on the flywheel hub and on the end of the crankshaft, the numbers 2 are stamped (Fig. 112), which must be aligned during assembly. The flywheel is attached to the crankshaft with eight bolts, placing a lock plate under each two bolts. The bolts are tightened in two steps. The final tightening torque is 20-22 kgf-m. The locking plates are bent on the edge of the bolts, as shown in Fig. 112.
After that, the breather is fixed with two bolts with spring washers to the end of the block and a clamp to the flywheel housing, a centrifugal oil filter is installed, ensuring that the holes for the oil passage in the block and the gasket match (if necessary, the gasket should be turned on the other side), a coarse oil filter is attached and fine fuel filter. When installing a high-pressure fuel pump assembled with an automatic clutch and a regulator, a stand is placed under the protruding end of the shaft 4 (Fig. 113) of the pump drive and the key is pressed in, the half-coupling 7 is put on the shaft 4, aligning the marks a on the flange 5 and the half-coupling 7; install a high-pressure fuel pump with an automatic clutch and a regulator; put washer 8, ensuring the gaps between the cams of the driving half of the coupling and the end of the automatic clutch 9 within 0.7-1.0 mm (the marks on the leading half of the coupling must be aligned), tighten and cotter the nut 13 for securing the half of the coupling.
The low pressure fuel pipes are then secured. The fuel supply pipe to the injection pump should not touch the bolt of the injector drain pipe and the block top cover. Place sealing washers under the tube ends and hollow bolt heads.
After wiping the seats of the liners and the cylinder block, a selected set of liners is installed in the bore of the cylinder block. The protrusion of the sleeve collars above the plane of the block should be 0.07-0.16 mm; the difference in protrusion values within one cylinder bank should not exceed 0.08 mm. After measuring, the position of the sleeve in the block should be marked with a mark embossed on the upper non-working surface of the sleeve collar in the direction of the front part
engine; remove the sleeves from the block, put the O-rings and anti-cavitation rings lubricated with oil into the grooves, and install the sleeves into the block. The branded side of each liner should face the front of the engine.When assembling the connecting rod-piston set, on one side of the piston / insert the circlip 13 (Fig. 114) of the piston pin and, using the tool (see Fig. 15), put on successively the lower and upper oil scraper rings 4 (see Fig. 114), the third , the second 3 and the first 2 compression rings. The bevels at the ends of the compression rings should be directed upward to the piston bottom, and the locks of the adjacent rings should be turned in opposite directions. Next, the piston with rings should be kept in an oil bath for 10 minutes at an oil temperature of 80-100 ° C, the connecting rod 6 should be installed in the piston so that the axis of the upper connecting rod head coincides with the axis of the hole for the piston pin, and allowed). The combustion chamber of the piston in must be displaced towards the long bolt 9 of the connecting rod cover. Thereafter, a second retaining ring is installed. Having unscrewed the connecting rod bolts 9 and 10, remove the connecting rod cover 8 together with the bolts and put the liners 7, aligning the projections of the liners
with grooves in the beds. The size group of the set of connecting rod bearings installed on the engine must correspond to the repair (or nominal) size of the connecting rod journals of the crankshaft. Used inserts are recommended to be placed in the beds where they were installed earlier and always in pairs. Having lubricated the liners with diesel oil, using technological mandrels 14, the pistons, complete with connecting rods, are inserted into the liners // of the cylinders, pre-lubricated with oil. The combustion chambers in the pistons must be offset to the axis of the engine. The connecting rod caps are tightened with their fastening bolts (tightening torque 17-19 kgf-m), starting with a long bolt. The total axial clearance between the ends of the lower heads of the connecting rods and the cheeks of the crankshaft should be 0.15-0.57 mm. Measurements are made between the ends of the connecting rods and their caps. If the gap
The tightening procedure for the nuts is shown in fig. 116.


5-3-6; for the YaMZ-238 engine; 1-5-4-2-6-3-7-8. The cylinder numbering scheme is shown in Fig. 117.
Then a set of nozzles is installed, with which the injection pump was tested and adjusted. Place no more than one sealing washer under the spray nut. The fastening nut of the bracket is tightened with a torque of 5-6 kgf-m. Next, place the drain pipes of the injectors and the fuel outlet pipe and fix the latter with a clamp on the intake manifold stud. After that, it is necessary to install the cylinder head covers, the connecting pipe of the intake manifolds with the flange of the compressor pipe to the front of the engine, the air filter, assemble the connecting and bypass pipes of the water thermostats with hoses and clamps and install them on the engine, remove the engine from the stand, put it on a stand and install starter and transport seals.
The fan impeller, generator and compressor, as well as the clutch and gearbox, are assembled after the engine has been completed.
Diagnostics of MAZ vehicles is not an easy task. The reason for this is that over the past 15-20 years, a lot of various models have been produced under this brand, which differ not only in the installed engines, but also in various other systems from different manufacturers. Therefore, there is still no such scanner model on the autoscanner market that would “take” all MAZs at once, regardless of the model and year of manufacture. Therefore, “novices” in the field of autodiagnostics, having 1-2 “universal” scanners, either do not take up MAZ diagnostics, or cannot provide the client with the whole picture.
One of the engines installed on MAZ trucks is the YaMZ-650 engine (Yaroslavl Motor Plant) and its modifications. It is an inline six-cylinder turbocharged diesel engine. Structurally, this family is based on the French Renault dCi 11 engines.The license acquired from Renault Trucks allowed the prototype to be first modified to Euro-3, and later to Euro-4. Improvements were achieved primarily through the introduction of the second generation CRS 2 fuel supply system by R. Bosch ".
This engine has several modifications, which differ from each other only by the parameters “hard-wired” into the electronic engine control unit, which allowed the manufacturer to change the characteristics of the used fuel equipment. Therefore, in computer diagnostics of such cars, a cargo electrician must understand not only the parameters of the ECU, but also determine a specific engine modification by external signs.
FixTruck24 specialists have not only extensive experience in diagnostics of electronic systems of MAZ trucks, but also a wide range of diagnostic equipment, which allows us to carry out diagnostics at the highest level with almost one hundred percent guarantee.
We can reliably find the causes of the malfunction: any engine ever installed on MAZ trucks, brake system, transmission, fuel supply systems, body electronics, AdBlue / SCR (urea) system operation, and the like.
Our company carries out diagnostics and repairs of electrical equipment of MAZ trucks on the road.
An electrician with a visit to MAZ trucks can diagnose the cause of the malfunction and, in many cases, arrange the operation of the truck at the place of call.
Calling prompt technical assistance is a reasonable solution if you are faced with a problem right on the track.
Why spend a lot of money on a tow truck if our auto electricians are able to provide the necessary assistance immediately at the breakdown site?
On-site auto electrician services: we will help you save time, nerves and money!
If an uncharacteristic noise, knocking, or any other abnormalities in the operation of the car appears while driving, you must stop and first visually assess the state of the transport. And if your Volvo does not start at all, then it is better not to try to fix the problem yourself.
Modern trucks have a built-in electronic control system. If a person intervenes in this system without the necessary knowledge and skills, the situation with a breakdown may worsen.
We provide prompt technical assistance to all those who are "stuck" on the track. For this we have everything you need: high-quality diagnostic equipment and qualified specialists, auto electricians for trucks, whose theoretical knowledge is backed up by many years of experience.
We diagnose and repair MAZ truck systems:
- EDC engine management system
- Braking system ABS, EBS
- Air suspension
- VIC drive control
- Immobilizer
etc.
We also produce:
- Repair of harnesses
- Immobilizer repair
- shutdown, repair of the AdBlue system (urea)
- Diagnostics before buying MAZ
- Pneumatic system repair
- Repair of the fuel system of the injection pump and Common Rail
- as well as other locksmith work.
Extensive work experience, and the corresponding qualifications of an auto electrician, allow on the spot and in a short time to eliminate faults that have arisen on the road.
Our company is ready to provide technical assistance 24 hours.
Unqualified repairs can damage many electronic components, as well as control units. Trust your car only to professionals!
You can order MAZ diagnostics right now by phone:
+7 495 294 15 19 or +7 917 542 30 23
Our work. Interesting and unusual cases.

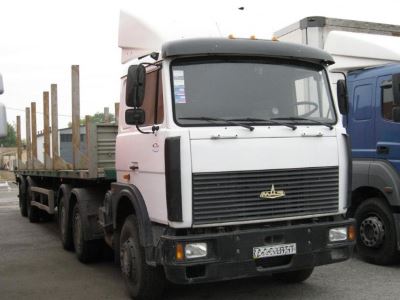
Useful files: wiring diagrams, repair manuals, error codes.
Manual for the operation and repair of MAZ vehicles with Mercedes engines of the Euro-6 ecological level. In Russian. 310 pages. File format: PDF.
The manual contains a brief description of the device of MAZ-437040, 437041,437043, 437141, 437143 vehicles, instructions for their operation, maintenance, adjustment of units and assemblies. In Russian. 288 pages. File format: PDF.
MAZ 555102, 5551A2, 5551A3, 555142, 555145, 555147, 533702, 5337A2, 533703, 533742, 533745, 533747, 543302, 5433A2, 543403. Operation manual
The manual contains a brief description of the device of MAZ vehicles, instructions for their operation, maintenance and adjustment of units and assemblies. In Russian. 312 pages. File format: PDF.
The manual contains a brief description of the device of cars, instructions for their operation, maintenance and adjustment of units and assemblies. In Russian. 320 pages. File format: PDF.
MAZ 642205, 6422A5, 642208, 6422A8, 630303, 6303A3, 630305, 6303A5, 630308, 6303A8, 651705, 6517A5, 543203, 5432A3, 543205,5432A5, 543208, 54323605338, 5335A , 5516A5, 551608, 5516A8. Manual.
The manual contains a brief description and technical characteristics of MAZ vehicles produced by the Minsk Automobile Plant. The basic rules for the operation of cars are stated, information is given on their adjustments and maintenance. In Russian. 320 pages. File format: PDF.
MAZ 643009, 6430A9, 643008, 6430A8, 643005, 6430A5, 6430A4, 631208, 6312A8, 544009, 5440A9, 544008, 5440A8, 544005, 5440A5, 544004, 5440A4, 544003, 5440A3, 534005, 5340A, 5340A, 534005, 5340A, 534005, 5340A ... Manual
The manual contains a brief description of the device of cars, instructions for their operation, maintenance and adjustment of units and assemblies. In Russian. 352 pages. File format: PDF.
The operating manual contains basic information on the design, maintenance and operation of trailers. In Russian. 111 pages. File format: PDF.
MAZ 650105, 650108, 6501A5, 6501A8, 6501A9 (dump trucks). Supplement to the manual for the operation and repair of MAZ-6430 vehicles
The manual is a supplement to the manual for MAZ-6430 vehicles and contains the main technical characteristics, information on the design, adjustments and maintenance of original components and assemblies of MAZ-650105, 650108, 6501A5, 6501A8, 6501A9 dump trucks. Information on the design, adjustments and maintenance of units and assemblies borrowed from vehicles of the MAZ-6430 family is set out in the main operating manual. In Russian. 68 pages. File format: PDF.
MAZ 651608, 6516A8, 6516A9, 6516V9, 651669, 6516V8. Supplement to the manual for the operation and repair of MAZ-6430 vehicles
The manual is a supplement to the manual for MAZ-6430 vehicles and contains the main technical characteristics, information on the design, adjustments and maintenance of original components and assemblies of vehicles - dump trucks and MAZ-6516XX chassis. Information on the design, adjustments and maintenance of units and assemblies borrowed from vehicles of the MAZ-6430 family is set out in the main operating manual. In Russian. 140 pages. File format: PDF.
MAZ 6430V7, 6430V9, 5440V3, 5440V5, 5440V7, 5440V9, 5340V2, 5340V3, 5340V5, 5340V7, 5340V9, 6312V3, 6312V5, 6312V7, 6312V9. Supplement to the manual for the operation and repair of MAZ-6430 vehicles.
This manual is a supplement to the operation manual for MAZ-6430 vehicles and contains technical specifications, information on the design, adjustments and maintenance of original components and assemblies of MAZ-6430VX, 5440VX, 5340VX, 6312VX vehicles. Information on the design, adjustments and maintenance of units and assemblies borrowed from vehicles of the MAZ-6430 family is set out in the main operating manual.In Russian. 67 pages. File format: PDF.
MAZ 6501B5, 6501B8, 6501B9 (dump trucks). Supplement to the manual for the operation and repair of MAZ-6430 vehicles
This manual is an addition to the operation manual for MAZ-6430 vehicles and contains technical specifications, information on the design, adjustments and maintenance of original components and assemblies of MAZ-5550V2, 5550V3, 5550V5 vehicles. Information on the design, adjustments and maintenance of units and assemblies borrowed from vehicles of the MAZ-6430 family is set out in the main operation manual. In Russian. 22 pages. File format: PDF.
The manual contains a description of the design, basic rules for the operation and maintenance of power units and engines YM3-650.10, YMZ-6501.10, YMZ6502.10, their configurations and versions. In Russian. 116 pages. File format: PDF.
Engines YaMZ-651, YaMZ-6511, YaMZ-6512 and their configuration. Supplement to the operation manual for YaMZ-650 engines
The device of the YaMZ-651, YaMZ-6511, YaMZ-6512 engines and their configuration is described. It is a supplement to the operation manual for YaMZ-650 engines. In Russian. 10 pages. File format: PDF.
The manual contains the information required to operate the clutch. For information on operating the clutch actuator, refer to the vehicle owner's manual. In Russian. 16 pages. File format: PDF.
The device of ZF gearboxes of models 9S109 and 16S109 is described. In Russian. 32 pages. File format: PDF.
Synchronized gearbox ZF 16S151, ZF 16S181, ZF 16S221, ZF 16S251. Manual
The device of ZF gearboxes of models 16S151, 16S181, 16S221 and 16S251 is described. In Russian. 31 pages. File format: PDF.
We work with a trip to the cities:
![]() |
Video (click to play). |