In detail: do-it-yourself repair of diesel engine injectors from a real master for the site my.housecope.com.
Attention! Car service network of favorable prices. Camber check is FREE! No queues! Repair on the same day!
Download / Print topic
Download a theme in various formats, or view a printable version of the theme.
The injection mechanics is the main difference between a diesel engine and a gasoline engine. In a diesel internal combustion engine, fuel is supplied to the combustion chamber using a nozzle. The device injects fuel in a metered manner into a chamber with a high temperature and pressure, after which the diesel fuel ignites. The nozzle is subjected to the greatest load: the part is constantly in an aggressive environment and works at high intensity. Any negative factor can disable the part or significantly reduce its resource, after which the diesel engine nozzles will need to be repaired.
To understand the mechanics of the injector, we will describe the injection cycle schematically:
- The injection pump takes fuel from the tank;
- then the pump saturates the fuel rail with diesel fuel;
- fuel enters the channels that lead to the nozzle;
- inside the nozzle, fuel flows to the sprayer;
- when the pressure on the atomizer reaches the set threshold, the nozzle opens and diesel fuel enters the combustion chamber.
Let us describe the design of the part using the example of a primitive mechanical nozzle with 1 spring. In the lateral part there is a channel that provides a continuous supply of diesel fuel. Inside the nozzle chamber there is a movable barrier with a spring and a needle, which drops when the pressure rises. The needle rises, clearing the path of fuel to the sprayer.
![]() |
Video (click to play). |
Additionally, more advanced types of nozzles can be noted:
- Piezoelectric: The spring pusher is lowered by a piezoelectric element. This technology provides a high intensity of opening of the atomizer: fuel economy is achieved, while the internal combustion engine operates more smoothly.
- Electro-hydraulic: The design includes an inlet and outlet choke and an electromechanical valve. The operating mode of the components is controlled by the engine control unit.
- Unit injectors: used in engines that do not have a high-pressure fuel pump. The fuel is supplied directly to the nozzle. These spraying devices have their own plunger pair inside, which generates the pressure required for injection.
Due to excessive loads, the injector may fail due to a violation of the operating mode of the motor. Manufacturers declare the resource of parts to be up to 200,000 km, but due to negative operating factors, wear of parts appears much earlier.
Repair of diesel injectors may be required for the following reasons:
- Low quality diesel fuel: the scourge of all "diesel operators". Due to impurities in the fuel, the sprayer becomes clogged; the dosage and the fuel supply mode are violated.
- Poor assembly quality of the injection component or factory defect: the injector does not withstand the operating conditions, the part as a whole or individual components fail.
- Mechanical damage caused by incorrect operation of adjacent ICE systems.
Usually, breakdowns are of the following nature: the spray angle and the amount of supplied fuel change, the integrity of the body is violated, and the needle travel deteriorates.
Let's briefly describe the "symptomatic series":
- jerks and jerks are felt when moving;
- The internal combustion engine is unstable at idle, stalls;
- when the engine is running, an excessive amount of exhaust is emitted;
- tangible loss of traction;
- failure of individual cylinders;
- gray or black smoke from the exhaust pipe.
It is preferable to entrust the routine maintenance or overhaul of diesel engine injectors to qualified specialists - they will be able to restore and adjust the part on high-precision automated stands. However, a certain set of repair procedures can be carried out in artisanal conditions without the use of complex equipment.
To carry out self-service of diesel engine sprayers, the car owner will need:
- a set of open-end or spanner wrenches;
- screwdrivers for straight and Phillips head;
- clean dry rags;
- maximeter;
- flushing fluid for internal combustion engines.
It is recommended to carry out work in a dry and lighted, dust-free garage.
Diagnostics of diesel injectors and their maintenance involves removing the nozzles from the internal combustion engine. Before starting work, it is recommended to thoroughly wash the engine and engine compartment to avoid the ingress of debris and foreign particles. With particular fondness, you need to rinse the cylinder head. High pressure tubing should be marked with markings to avoid confusion during reassembly.
Before removing it is necessary to close the nozzle fittings (use plastic caps) to avoid contamination. It is not recommended to use ordinary open-end wrenches to dismantle the nozzles - an inexperienced repairman can strip the threads from the nozzles. If the required qualifications are not available, use spanners and a long-handled head tool.
After removing the nozzles from the holes, dry them and remove external dirt with a rag. O-rings are placed in the holes of the nozzles. When repairing injection parts, they are replaced with new ones without fail. Do not allow dirt from the rings to get into the injection system during removal.
There are several methods to check if the sprayer is working properly. The easiest way is to check the injector while the engine is running:
- Start the "engine" at idle speed.
- Begin to unscrew the nozzles one by one in turn.
- If, after removal, the operation of the motor has deteriorated, then the remote nozzle is operational and must be returned to its place.
- By the method of elimination, you will find an injector, the dismantling of which will not change the operating mode of the internal combustion engine. This will be the broken device.
You can use a multimeter for diagnostics. In advance, it is necessary to throw off the battery terminals and disconnect the wiring of the injectors, and then "check" every detail with the device. On high resistance injectors, the device values will be in the range of 11 - 17 ohms; at low impedance, the multimeter will show up to 5 ohms.
The defective injector must be inspected. First, we look for leaks in the body of the part. If there are none, proceed to disassembling the part. We fasten the part in a vise and knock out the sprayer with a gentle tap. Next, you need a thorough cleaning: we soak the parts of the nozzle in diesel fuel or solvent to remove carbon deposits. Remove fumes and deposits with a fine steel grater. After completing the cleaning, you need to check the nozzle at the maximum meter. If the optimal injection parameters have been achieved, the device is ready to be installed in the engine.
In other cases, it is necessary to completely replace the atomizer on the defective nozzle. When installing a new part, carefully remove all factory grease, otherwise the device will not work.
Before disassembling the device, mark all parts with a marker to avoid confusion. Be especially careful when marking high pressure hoses. The nozzle is screwed in by hand as far as possible. Further tightening is done with a dynamometer wrench. For tightening values, refer to the motor manual. After installing the injector, evacuate air from the fuel system. On modern cars, it is enough to turn the starter several times for this; or use a manual priming pump (if equipped).
Let's list the main features:
- the resource declared by the manufacturer has been developed;
- there are breakdowns on the case, other leaks;
- burnt out spray nut: if the problem is not eliminated early, the spray itself will become unusable.
Please note that on some engines, after installing a new injector, it is necessary to "tie" it to the engine: make changes to the settings of the control unit.
Self-repair of injectors is a rather forced measure. Such a service in artisanal conditions can bring success only in the case of the highest qualifications of the master. The main problem of garage repairs is the lack of high-precision bench equipment for diagnostics. The repairman cannot objectively assess the effectiveness of the service measures.
If there is an opportunity to contact a service station, do not neglect it: computer equipment and cleaning stands will extend the life of the injectors and save them from potential expensive repairs. The same ultrasonic cleaning can save a motorist from engine problems for several seasons. It is not possible to repair modern Common Rail injection systems in a garage: you need a mandatory fine-tuning of the part by computer.
Use a cleaning fuel additive to avoid costly repairs and replacement parts. They prevent the formation of carbon deposits and the settling of deposits. The use of additives should be systematic, not one-off. Remember, additives are about preventing breakdowns, not fixing them.
The injectors of a diesel engine, as well as an injection engine, are periodically contaminated. Therefore, many owners of cars with a diesel engine are wondering how to check injectors on a diesel engine? As a rule, in the event of their clogging, fuel is not supplied to the cylinders in a timely manner, and there is an increased fuel consumption, as well as overheating and destruction of the piston. In addition, the valves can burn out and the particulate filter can fail.
Diesel injectors
In modern diesel engines, one of two well-known fuel systems can be used universally. Common rail (with a common ramp) and unit injectors (where a separate injector is supplied to each cylinder).
Both of them are capable of providing high environmental friendliness and engine efficiency. Since these diesel systems function and are arranged in a similar way, but Common Reil is more progressive in terms of efficiency and noise of work, although it loses in power, it has become increasingly used on passenger cars, then we will talk about it further. And we will tell you about the operation, malfunctions and testing of the pump injectors separately, because this is an equally interesting topic, especially for owners of VAG group cars, since software diagnostics are not difficult to perform there.
The simplest method for calculating a clogged nozzle of such a system can be carried out according to the following algorithm:
- at idle speed, bring the engine speed to the level when problems in engine operation are heard most clearly;
- each of the nozzles is turned off by loosening the union nut at the attachment point of the high pressure line;
- when you turn off the normal working injector, the engine operation changes, if the injector is problematic, the engine will continue to work in the same mode and further.
In addition, you can check the injectors with your own hands on a diesel engine by probing the fuel line for jolts. They will be the result of the high pressure fuel pump trying to pump fuel under pressure, however, due to the clogged nozzle, it becomes difficult to pass it. A problem fitting can also be identified by an overestimated operating temperature.
Checking the volume of discharge to the return
As the diesel injectors wear out over time, the problem arises that the fuel from them flows back into the system, due to which the pump cannot build up the required working pressure. This can result in problems with starting and operating the diesel engine.
Before checking, you will need to buy a 20 ml medical syringe and a dropper system (you need a 45 cm tubing to connect the syringe). To find a nozzle that throws more fuel into the return line than it should, you must use the following algorithm of actions:
- remove the plunger from the syringe;
- on a running engine, using the system, connect the syringe to the “return” of the injector (insert the tube into the neck of the syringe);
- hold the syringe for two minutes so that fuel is collected into it (provided that it will be collected);
- repeat the procedure one by one for all injectors or build a system for all at once.
Based on the information on the amount of fuel in the syringe, the following conclusions can be drawn:
Checking the overflow to the return
- if the syringe is empty, then the nozzle is fully functional;
- the amount of fuel in a syringe with a volume of 2 to 4 ml is also within the normal range;
- if the volume of fuel in the syringe exceeds 10.15 ml, this means that the nozzle is partially or completely out of order, and it must be replaced / repaired (if it pours 20 ml, then it is useless to repair, since this indicates wear of the nozzle valve seat ), since it does not hold the fuel pressure.
However, such a simple check without a hydrostand and test plan does not give the complete picture. Indeed, in fact, when the engine is running, the amount of discharged fuel depends on many factors, it can be clogged and needs to be cleaned, or it hangs and needs to be repaired or replaced. Therefore, this method of checking diesel injectors at home allows only to judge only about their throughput. Ideally, the amount of fuel they pass through should be the same and be in the range of up to 4 ml in 2 minutes.
In order to keep the injectors in operation for as long as possible, fill up with high-quality diesel fuel. After all, it directly depends on the operation of the entire system. In addition, install original fuel filters and do not forget to change them in time.
A more serious check of diesel injectors is carried out using a device called maximeter... This name refers to the special reference nozzle with spring and scale. With their help, the pressure of the start of injection of diesel fuel is set.
Another verification method is to use control model working nozzlewith which the devices operated in the engine are compared. All diagnostics are performed with the engine running. The algorithm of actions is as follows:
- dismantle the injector and the fuel line from the engine;
- a tee is connected to the free union of the high pressure fuel pump;
- loosen the union nuts on other high pressure fuel pump fittings (this will allow the fuel to flow to only one injector);
- the control and test nozzles are connected to the tee;
- activates the decompression mechanism;
- rotate the crankshaft.
Ideally, the reference and test injectors should show the same results in terms of starting fuel injection at the same time. If there are deviations, then it is necessary to adjust the injector.
The control sample method usually takes longer than the maximeter method. However, it is more accurate and reliable. You can also check the operation of the engine and injectors of the diesel engine and high-pressure fuel pump on a special control stand. However, they are available only at specialized service stations.
You can clean the injectors of a diesel engine yourself. Work must be done clean and well lit. For this, the nozzles are removed and washed either in kerosene or in diesel fuel without impurities. Before reassembling, blow out the nozzle with compressed air.
It is also important to check the quality of the fuel atomization, that is, the shape of the “flame” of the nozzle. There are special techniques for this. First of all, you need a test bench.There they connect a nozzle, supply fuel to it and look at the shape and force of the jet. Often a blank sheet of paper is used for testing, which is placed underneath it. Traces of fuel ingress, torch shape and other parameters will be clearly visible on the sheet. In accordance with this information, it will be possible to make the necessary adjustments in the future. A thin steel wire is sometimes used to clean the nozzle. Its diameter should be at least 0.1 mm less than the diameter of the nozzle itself.
The most common cause of a malfunction is a violation of the tightness of the seating of the needle in the nozzle guide sleeve. If its value is reduced, then a large amount of fuel flows through the new gap. In particular, for a new injector, a leak of not more than 4% of the working fuel that enters the cylinder is allowed. In general, the amount of fuel from the injectors should be the same. You can detect a fuel leak at the injector as follows:
- find information about what pressure should be when opening the needle in the nozzle (it will be different for each engine);
- remove the nozzle and install it on the test bench;
- create a knowingly high pressure at the nozzle;
- using a stopwatch, measure the time after which the pressure will drop by 50 kgf / cm2 (50 atmospheres) from the recommended one.
Checking the injector at the stand
This time is also spelled out in the technical documentation for the engine. Typically, for new injectors, it is 15 seconds or more. If the nozzle is worn, this time can be reduced to 5 seconds. If the time is less than 5 seconds, then the injector is already inoperative. You can read additional information on how to repair diesel injectors (replace nozzles) in the additional material.
If the valve seat of the injector is worn out (it does not hold the required pressure and excessive draining occurs), the repair is useless, it will cost more than half the cost of a new one (which is about 10 thousand rubles).
Occasionally, the diesel injector will ooze lightly or profusely. And if in the second case only repair and complete replacement of the nozzle is needed, then in the first case you can do it yourself. In particular, it is necessary to grind the needle to the saddle. After all, the main reason for leakage is a violation of the seal at the end of the needle (another name is the sealing cone).
To remove the leakage of a diesel injector, a fine grinding paste GOI is often used, which is diluted with kerosene. During lapping, care must be taken that no paste gets into the gap between the needle and the bushing. At the end of the work, all elements are washed in kerosene or diesel fuel without impurities. After that, you need to blow them with compressed air from the compressor. Recheck for leaks after assembly.
Partially defective injectors are not critical, but very unpleasant breakdown... After all, their improper operation leads to a significant load on other components of the power unit. In general, the machine can be operated with clogged or unadjusted injectors, but it is advisable to carry out repairs as soon as possible. This will keep the car's engine in good working order, which will save you even more money costs. So when the first symptoms of unstable operation of injectors on your diesel car appear, we recommend at least an elementary way to check the performance of the injector, which, as you can see, everyone can do at home.
Undoubtedly, the best tool for this is an injector test stand, which can be the most complicated electronic one for thousands of dollars and very simple, even primitive in the spirit of the fifties (Fig. 7) or even home-made (Fig. 8).
Any of them, with a greater or lesser degree of convenience, can be used for work.There are many diesel garages and stands in the country, although they have the simplest ones. And we know how to negotiate. But what if your diesel is the only one in the area? Not very scary efforts need to be made to make a homemade stand from a decommissioned tractor-KAMAZ or marine pump or to adapt the injection pump of your engine to check the injectors. Certainly not the most beautiful way, but without fish.
To do this, you need to make a tube - a tee, which at one end will be connected to one of the high-pressure fittings of your high-pressure fuel pump, on the other end we will attach the nozzle, and on the third - a 200-300 atmosphere pressure gauge (maybe more). First, we turn the engine with a starter until the nozzle starts firing, and then, remembering to leave the ignition on, manually. It is agonizing of course, but if there is no other way out, it is quite possible.
About injector opening pressure
During the compression stroke, the air charge from the cylinder flows into the combustion chamber at a very high speed. At the same time, due to its shape, a directed vortex appears in the combustion chamber, into which fuel is injected. Depending on the design of the combustion chamber and the compression ratio, the speed and shape of the vortex is different, therefore, there are different types of atomizers and different values of fuel injection pressure. Designers set recommended as well as allowable injection pressures for each engine. As a rule, these values must be observed with an accuracy of 5-10 kg.cm2 within a set of nozzles. When the nozzle is overhauled, it makes sense to set the injection pressure by 10-15 kg.cm2 more than the required one, in the expectation that in the very first minutes of the nozzle operation there will be some shrinkage of the moving parts and, accordingly, a decrease in the set pressure.
It is especially necessary to note the specific property of the rotary-type distribution fuel pumps of the LUCAS company - very strict requirements for the accuracy of the injection pressure regulation within the set of injectors. For reference, in engines with such fuel pumps, it is often impossible to find a faulty injector using the shutdown method. The engine will immediately stall due to the cessation of fuel supply to the remaining injectors.
How to adjust the opening pressure of the nozzle at home
In the overwhelming majority of modern injectors, the opening pressure is regulated by adjusting the thickness of the spacer washer between the spring and the body. Decent workshops have sets of these washers to solve any adjustment problem. For amateurs, it should be borne in mind that washers exist of various diameters (for different nozzle bodies), and are available with or without a hole. Washers with a hole can always be used instead of washers without a hole, but replacement is not allowed. It is also unacceptable to use washers of "non-native" diameter.
As a rule, injectors are designed in such a way that an increase in the washer thickness by 0.1 mm leads to an increase in the injection pressure by 10 kg.cm2. It is very common to see when repairing injectors that, during previous interventions, the injection pressure was regulated using pieces of razor blades placed under a spring. This method of adjustment is completely unacceptable. First, with an uncontrolled backing, you create uncertainty in the spring support and thus non-uniform spring production and provoke lateral force. And secondly, there is a risk of chipping a piece of the blade and no one knows what he will do inside the nozzle. Therefore, the only qualitative solution to the problem is the manufacture of new shims of the calculated thickness. And only in those cases when the lathe, heat treatment and grinding are absolutely inaccessible, it is permissible to regulate the pressure with steel foil washers, placing them only between the body and the standard washer.If your spring rests on an unhardened lining, then after a short time, little will remain of it.
A typical problem with Japanese injectors
A distinctive feature of the injectors of Japanese engines is the return flow through the end face of the injector into a special ramp. Careless disassembly often results in deformation of the nozzle sealing end, which is why it is not possible to achieve a hermetic “return” seal. "Experiments" begin with tightening the ramp nuts, with the setting of sealing washers under the nuts, etc. However, the only way to solve this problem is only to undercut the sealing end of the nozzle on a lathe. However, it should be borne in mind that only one surface of the nozzle is corrected by facing, and the shape of the groove at the end may be deformed so much that the sealing washer can no longer overlap it. This nozzle must be replaced.
Indefatigable attempts to tighten sweating or flowing return lines often lead to deformation of the return rail flanges. Seals cannot be achieved with such flanges and must be refurbished. It is not difficult to do this by hand on a small sanded tile with sandpaper on top.
Internal combustion engines, built according to the scheme of fuel injection into the combustion chamber using nozzles, are most widely represented in the secondary market of automotive equipment, and the development trend of the modern automotive industry, in general, adheres to the concept of completing the fuel supply systems of all new automobile engines exclusively with nozzles.
A technically complex device called an injector is one of the most important functional elements of the systems for supplying fuel directly to the combustion chamber of the engine, doing it under high pressure. And also the nozzles are responsible for the timely formation of the fuel mixture and for the strict dosage of the fuel portion.
At the same time, they constantly work in an intensive mode with large overloads and because of this, over time, they lose part of their technical characteristics, which, as a result, leads to engine malfunctions. Therefore, the repair of diesel engine injectors is one of the most demanded types of car maintenance.
The main problem is that any car engine performs its daily work in conditions that are far from ideal. Therefore, it is possible to determine a number of main factors leading to the failure of the injectors of the fuel supply systems of diesel engines, namely:
Regardless of the negative factors or various reasons leading to malfunctions, it is necessary to clearly know and understand the consequences of this in the operation of fuel injectors. So, a failure in the operation of the injector will manifest itself in the following external signs during the operation of the car:
- well perceptible weakening of power, with a warm engine;
- various difficulties when starting the motor;
- uneven engine idling;
- jerks when accelerating;
- a noticeable increase in fuel consumption,
- the presence of constant vibration in the area of the engine,
- the appearance of peculiar clattering sounds;
- the appearance of smoke (black or gray) from the exhaust pipe,
- slow achievement of high engine speed;
- exceeding the permissible level of engine oil in the engine sump;
- the check engine icon on the instrument panel lights up.
If such symptoms appear, it is necessary to immediately make a technical diagnosis in a specialized auto repair shop in order to understand and identify the exact reasons that led to the engine failure.
The main malfunctions arising during the operation of diesel engine injectors include:
- deformation over time of the O-rings;
- the presence of residues of combustion products on the parts of the sprayer;
- significant wear of the sprayer;
- reflowing the tip of the spray;
- the presence of mechanical scratches on the surface of the nozzle;
- significant narrowing of the injector nozzle diameter;
- various mechanical damage to injector parts;
- one-sided mechanical wear of the spray needle;
- wear of the piston surface along the periphery of the valve;
- Reduction of valve piston stroke or spray rod;
- the presence of rust in the fine filter;
- the presence of rust granules on the needle and spray rod;
- erosion of the high pressure seal;
- a blue spot on the spray pin due to overheating;
- burnout of the electric coil of the magnet.
The presence of one or more malfunctions in the operation of the injector does not necessarily require an expensive complete replacement, since even the elimination of the most serious damage will cost no more than a third of the price of a new injector.
It is worth knowing that if the motorist did not repair the injectors on his own, then it is better to contact a specialized car service, but overestimating his own strength, as a rule, leads, at best, to a loss of time and the purchase of a new injector. In the worst case, it can result in more serious engine damage.
Depending on the type and degree of malfunction of the diesel engine, the technology for repairing modern fuel systems is carried out in the following sequence:
As a rule, the repair of a set of diesel fuel injectors at a specialized auto repair center takes no more than two days, and the total cost of repair work will be in the region of 30% of the price of a new injector set.
Equipment for the repair of diesel engine injectors existing on the market today can be divided into several categories in terms of technological complexity and functionality, namely:
- professional stations for checking and diagnosing all types of malfunctions of fuel systems, as a rule, large service centers can afford it;
- specialized stands for testing injectors, which are quite affordable even for small car services;
- individual testers for diagnosing injectors should at least be present in every auto repair shop that specializes in the repair of diesel engines;
- electronic devices and measuring instruments for making nozzle adjustments;
- tools for disassembly and service of injectors
- ultrasonic baths for cleaning nozzles.
Only the presence of diagnostic equipment and a specialized tool in the car service will be a prerequisite for carrying out high-quality work on the repair of diesel engine injectors.
Attention! Car service network of favorable prices. Camber check is FREE! No queues! Repair on the same day!
Download / Print topic
Download a theme in various formats, or view a printable version of the theme.
The reliable operation of the engine depends on the correct functioning of the injectors. Their condition is largely influenced by the quality of the fuel used. High-quality fuel significantly increases the life of the injectors. During normal operation, they are replaced every 100 thousand kilometers.
The main reasons that negatively affect the performance of the injectors are their clogging, as well as wear or breakage of some parts that make up their design. For prophylaxis, various additives should be added to the fuel tank, and every 30-40 thousand kilometers, check the filter elements and clean clogged nozzles from dirt and debris. You can do this work yourself or contact the professionals of specialized firms, one of the proven ones is
Malfunctioning injectors signal such symptoms:
✔ the engine is unstable at idle;
✔ increased fuel consumption;
✔ Difficulty starting the engine;
✔ poor response when pressing the gas pedal;
✔ exhaust with smoke and increased toxicity.
Lower ambient temperatures will exacerbate these symptoms as the volatility of the mixture decreases. Timely flushing will prevent coking of the nozzle spray. For this, special cleaning fluids are used, and the procedure itself can be carried out even at home. This should be done regularly as smaller fuel outlets will reduce engine power and performance.
A spanner wrench is used to remove and further disassemble the injectors. This is, firstly, convenient, and secondly, an open-end wrench can damage the union nuts of the injector bodies, and they can crack during disassembly and assembly. On examination, worn parts are identified and replaced.
Repairs to the sprayer must be carried out with absolute cleanliness. Before removing injectors from diesel engines and during their disassembly, it is necessary to thoroughly rinse everything. The smallest particles of sand or dust trapped in the channel can damage the threads and impair a reliable seal. After disconnecting the high-pressure tube from the nozzle, it is necessary to close the fitting with a tight and clean cap, this will protect its cavity from dirt.
After removing the injector from the gasoline engine, it is imperative to close the holes where they are inserted with clean plugs. There is also a non-disassembly cleaning method using a temporary power system. It consists of an additional fuel pump, a plastic bottle with cleaner and a hose. The fluid is pumped in two stages with a break to dissolve the deposits. The first time the device turns on for 5 minutes, and then for another half hour. The advantage of this method is flushing the entire fuel system, and its simplicity allows you to perform actions in a garage. Of course, not every driver can do it on their own, in this case, you should contact a car repair company.
For a long time, the carburetor engine was the most common power unit installed in passenger cars. The natural way of delivering the working mixture to the combustion chamber made it possible not only to produce relatively inexpensive engine models, but also to restore the car's power system in a garage.
Modern engine manufacturers abandon this design and use forced fuel injection. The complication of the design entailed not only an increase in the cost of such units, but also significantly complicated the engine repair. Adjusting and repairing injectors has become an especially difficult task for motorists. The main symptoms of a malfunction in which one can suspect that the engine injectors are the cause of unstable operation will be described below.
Injectors can be faulty not only on a gasoline injection engine, but also on diesel units. The main symptoms of inoperability of these parts are identical, therefore, regardless of the type of fuel on which the engine is running, the following symptoms may indicate a malfunction of this part:
- Increased fuel consumption;
- Unstable engine operation in idle mode;
- Difficult starting, reminiscent of the "overflow" of a carburetor engine;
- Jerks with steady motion, and dips with sharp acceleration.
These are the main symptoms of a malfunction, but the injectors should be checked only after other possible causes of such manifestations have been completely excluded. The engine may run unstable if the fuel pump malfunctions, when hoses are leaking or the lumen of the pipe is clogged with various deposits. A clogged fuel filter can also adversely affect engine throttle response. A faulty ignition system can also cause jerking on a gasoline engine.All of the above options for engine breakdowns must be completely excluded before proceeding with a full-fledged diagnosis of engine injectors.
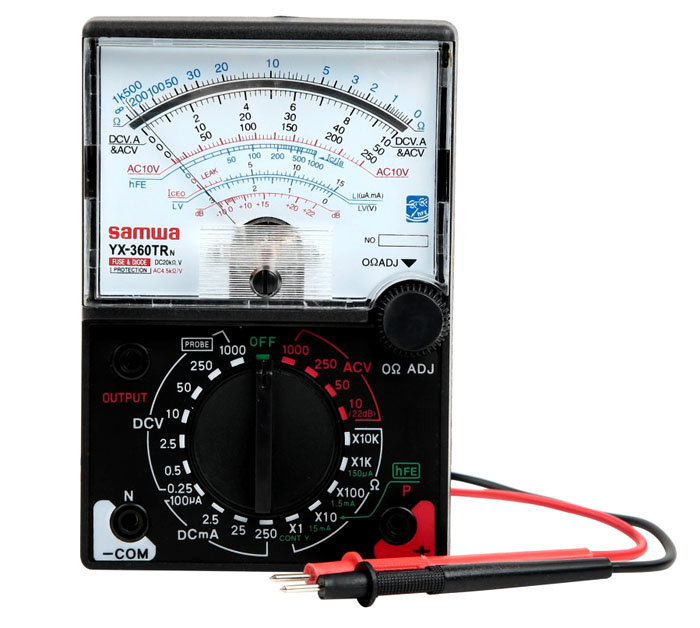
The injector diagnosis depends on the type of this part. Currently, injection and diesel engines use two types of injectors - electromagnetic and mechanical.
- Electromagnetic - injection is controlled by an electrical impulse emanating from the control unit;
- Mechanical - driven from the engine crankshaft using a transmission mechanism.
Many novice car enthusiasts are interested in the question: "How to check the injectors without removing them from the engine?"
There is a way of detecting a malfunction of this part by the sound that is detected in the cylinder, where the malfunctioning injector cannot provide normal fuel atomization.
With even a little experience, you can quite accurately determine the knock of the nozzle. If fuel overflow occurs due to incomplete closure of the needle valve, then in this case detonation and increased engine noise are also possible. A muffled high-frequency noise can also be observed in such a cylinder.
Faults in electronic injectors can be determined with a multimeter, a pointer injector tester is also suitable for this operation. Diagnostics using an electrical measuring device is carried out in the following sequence:
- In the documentation for the car or for the installed injectors, it is necessary to find the resistance value of this part;
- Turn off the ignition and remove the negative terminal of the battery;
- Using a thin screwdriver, disconnect the electrical connector of the injector;
- The multimeter or tester is switched to the resistance measurement mode, and this parameter is measured between the contacts.
If the resistance values differ significantly from those indicated in the documentation, then the injector must be removed from the engine and must be adjusted or replaced.
The process of dismantling the injectors from the injection engine will not take much time, but in order to carry out this operation, it is necessary to locate these parts on the engine, as well as prepare the tools for work.
To remove the nozzles, you will need to prepare:
- Screwdriver Set;
- A set of keys;
- Pliers;
- Rags.
As a rule, the injectors on an injection engine are located on a special fuel rail, so it will not be difficult to find them. To access these parts, it is necessary to remove the air filter and various pipes, which can significantly complicate the removal process. Care should also be taken when carrying out dismantling work. The fuel supplied to the injectors is under high pressure, which must be reduced without fail. For this purpose, the design of the injection engine has a safety valve, by pressing it, you can reduce the fuel pressure to a safe value.
Then it is necessary to disconnect the wires from each engine injector. These wires connect the control unit to the injector contacts. The injector terminals have reliable spring clips that can be bent with a thin screwdriver, after which the control wire can be easily removed. Next, unscrew the 2 bolts that fix the fuel rail to the engine and use a pry bar to carefully separate the fuel rail from the intake manifold. When the injectors are removed together with the fuel rail, they should be carefully inspected.
If there are no O-rings, they must be carefully removed from the manifold and installed back on the nozzles, otherwise the performance of this unit will be lost. At this point, the process of removing the injectors from the injection engine can be considered complete.
The process for removing a diesel injector can be significantly different from the process described above.The main difficulty of this operation lies in the more severe temperature conditions of the diesel engine, from which the injector can stick to the cylinder head. In order to prevent thread stripping, it is necessary to use special pullers, which will avoid many troubles. Improper actions can lead to damage to the cylinder head, the repair of which will cost a very serious amount. Damage to the injector itself is also undesirable, this engine element is expensive, so replacing the injector will also lead to unnecessary financial costs.
Injector malfunctions are not numerous, but any of the failures can lead to unstable operation of the cylinder in which this part is installed. After removing the injector, it is necessary to carefully check and, if necessary, clean or replace a part that does not meet the conditions for uninterrupted fuel delivery to the cylinders. Correction of injectors of an injection engine consists, first of all, in the elimination of tarry deposits in the area of fuel atomization. Diagnostics and repair of parts installed on a diesel engine is carried out in a similar way. The cylinder injector of the diesel engine is designed so that only the atomizer can be replaced. If the injector is not dirty, but there is no fuel combustion in this cylinder, then the injector winding may have burned out. An open injector is a rather rare malfunction, but in the absence of other damage, it is necessary to measure the resistance between the contacts of this part with a multimeter. If there is no resistance at all, then the defective part must be replaced.
The removed injectors can be checked directly on the fuel rail. To do this, connect the control unit by connecting the wires in the sequence in which they were connected to the running vehicle. The fuel rail must be secured in such a way that containers of the same volume can be placed directly below them.
Plastic cups are ideal for this purpose and are placed under the sprayer of each nozzle.
Then you need to turn on the ignition and start the engine starter for 7 - 10 seconds. When performing diagnostics, you should pay attention to the quality of the atomization of the fuel flowing out of the nozzle. If fuel flows from a nozzle in a straight stream, then this nozzle must be replaced or cleaned from carbon deposits formed on its sprayer. You should also pay attention to the amount of fuel in the containers, which were placed under the nozzles. If, when performing diagnostics, in any container there is no fuel at all, then there may be no power supply to the injectors. This problem can be caused by the lack of contact between the cable and the terminal, as well as a banal break in the electrical wiring. If the wiring is intact, and there is good contact between the wire and the injector winding terminal, then the vehicle power system control unit may be faulty. If the electronic control unit is faulty, then in order to continue the diagnostic measures, it must be replaced with a known good part.
Checking the injectors with your own hands in this way allows you to fairly accurately determine the faulty parts of the car's power system. When performing such diagnostics, one should remember about the heavy load on the battery when the starter is turned on, as well as the harmfulness of crankshaft rotation without sufficient oil flow into the engine line, therefore it is advisable to carry out the diagnostics in one step. When the problem injector is found, you can start repairing it.
Repairing and adjusting injectors is a snap.Most of the problems that arise with the performance of injectors are solved by cleaning them from carbon deposits and oily deposits.
Restoration of injectors is carried out in the following sequence:
- The battery is removed from the car and an adjustable adapter with a switch for autonomous control of injectors is made from the unnecessary wires and parts available;
- Any spray for cleaning the carburetor is purchased, and an adapter is made from the fuel hose from the nozzle of the cartridge to the inlet of the nozzle.
To clean the internal capacity of the injector, electricity is supplied through the control switch from the battery to the injector terminals to open the needle valve. Simultaneously with the opening of the nozzle, the button of the spray can with the cleaning liquid is pressed. Adjusting the injectors in this way allows you to save a lot of money, as well as gain invaluable experience in repairing an injection engine. During the nozzle cleaning procedure, you should pay attention to how the spray device passed the fuel. If fuel escaped from the nozzle in a direct stream, then this part will need to be disassembled and repaired. How to disassemble the nozzle for repair will be described below.
In most cases, the repair of injectors can be carried out by replacing the filter, which is installed in the upper part of the injector, where it is connected to the fuel hose. To remove the filter, a self-tapping screw is used as the main tool, which is screwed into the mesh filter by 2 - 3 turns and removed from the nozzle body.
Then, in place of the removed filter, a new strainer and an O-ring are installed. Thus, it will be possible to ensure a stable filling of the nozzle with clean fuel, which will have a positive effect on the operation of the injection engine.
Adjusting nozzles at home is a feasible task, with minimal experience with tools. For home craftsmen, who at least once disassembled the carburetor and eliminated the engine overflow, it will not be difficult to clean the injectors.
![]() |
Video (click to play). |
Remanufactured injectors can last for a long time, and if all cleaning and repairs were performed according to the rules, then the car will be operated without serious deviations in the fuel supply system.