In detail: do-it-yourself repair of the fiolent milling cutter from a real master for the site my.housecope.com.
Here. Actually two modifications "in one bottle". Copy sleeves + offset pad with additional handle. I wanted to add a pair of compasses, but decided not to get rid of it. I will make a compass separately, on the same rods as for the parallel stop. I am also going to modify the emphasis. But more on that later.
In the meantime: here is a 6 mm thick plexiglass sole. It can be used simply as a sole with an additional handle, including as an offset. And you can also install copying sleeves.
The bushings themselves are made of bronze. Made a familiar turner, according to drawings such as the Enkorovsky. Actually, they differ only in the diameter of the neck.
The seat for the bushings in the sole is chosen with a play of about 1 mm. For precise fit, a centering pin is used - it is clamped into the chuck and “catches” the sleeve with a taper.
Pardon me: reveal the manufacturing technology of the plexiglass lining! according to the cleanliness of the edge, there is an opinion about sawing in machine conditions.
All the work, except for turning the copy sleeves, was done by himself, at home.
I sawed out the sole with an electric jigsaw on a "butt" - a folding workbench. Then he grinded the ends on a tape machine (I forgot a tape with an abrasive either 120 or 240).
Drilled holes for screws with a drill in a drill stand, pulling a pair of clamps a new sole with a "native". Then he countersinked.
I made the central hole like this: I fixed a pointed cutter into the chuck and pressed the cutter a little. So the central hole was screwed. I made a 40 mm deep sample for copying sleeves with a “percock”. I drilled it with a crown with a centering drill (30 mm or so) - already through and through.
Well, fixing the handle is not a problem. I picked up the old handle from the door to the pantry, cut off the pin a little, drilled a hole, cut the M8 thread and screwed it in with glue.
And about the drawings: I took them either on this site, or on a friendly woodtools. In addition, there are a lot of implementation options - I advise you to rummage around in search engines.
![]() |
Video (click to play). |

Nikolay Borisyuk
You can install any router on the table, and this one is no exception.

Fiolentovtsy to you that in the bastard you answer the improvement right now in Simferopol and you add novelty there in Simferopol there and really can't write three words a. FIOLENTOVTSY. ==== WHO WORKS THERE .. == AT LEAST TWO YEARS YOU CAN ANSWER .. == OR IT'S ALL IN YOUR PADLA. = ANSWER. A. RESPOND .. SIMFEROPOL. WHERE ARE YOU??

Probably they don't see us - again the light in Crimea was turned off.

What is Fiolent 4. Che, how is he. You have not heard, you do not know. )

Fiolent has Festula roots (it was ripped off from Festula, but later “modified” by our engineers, which obviously did not benefit%))).
Makita and the Blue Bosch have a "one-handed" router with a "copy base" and a removable head.
But mostly these models are popular in North America, and it is rather difficult to find them here.

This I will ask. With such a milling cutter, it is convenient to perform some operations when one hand is needed and the other is busy! I only know TWO Large Routers with this arrangement: - these are all these Fiolents and. FESTULA. Which are each, like a whole pallet-pallet loaded with these Violets !! Gyyy :))))))). Well, maybe there are other brands, but I don't know them! :)))

Held in the hands of the market. Seems OK. But didn't work.

Tell me, is it possible to install a button with a speed regulator on this router? Or how else to make a regulator?

1. Disassemble (carefully).
2. Remove debris and burrs
3. Possibly lubricated with dry grease / powdered graphite.
4.Collect and enjoy your work.

I bought it, put it on, twists it. True, the quality of the button is not very clicky, crunches.

Either the foreman is not competent, or he is trying to "dilute" an additional amount of unnecessary work.
– –
See how the hold button works on the same drill.
The wheel is exactly for this and is * intended * to adjust the speed in the * fixed position *, otherwise it would be possible to do just the trigger without the wheel and the lock button (as was done in old drills).
– –
Need * original * Fiolent button. It works “as expected”, but you may need to adjust the footprint as the “no adjustment” button may be different.
– –
I went to the workshop, turned on my Fiolent: * the wheel adjusts the revolutions when the button is fixed *, though not from “zero”, but approximately from the middle and above.

I was completely confused. On the market I found a button with a regulator and a lock. But the seller, who is also a repairman, said that if I use the button lock, then the rpm will be at maximum speed, no matter how much I set the wheel, that the wheel will not work when using the button lock. Proposed a separate block of the speed regulator. I have a boshsh jigsaw, where I set the revolutions with the wheel, then the same revolutions were fixed with the fixing button.

Replacing the native button with a * adjustable button * will solve the problem.
– –
The manufacturer Fiolent took the easiest route,
and unlike other milling cutter manufacturers that install * a separate speed control unit *, they installed a button usually used on drills.
The button includes the actual * start button * with a built-in triac power regulator and * a wheel for presetting * the adjustment level, as well as * a fixing button * of the start button.
Of course, this is not the best option, but the cheapest one.
For example * the lock button *, in contrast to the * safety button * used on most modern carpentry tools,
* does not prevent accidental pressing of the start button *, but only fixes it * in the pressed position *,
and this is fraught with injury if you accidentally press (carry) the tool by the main handle.

Can't remove the spring case without damaging it. Probably if this is done then he will not hold on. How to remove it, what if necessary, install it back?

Feed - opened, but PM - no 🙁
To do this, click on the gear on the main page (near the subscriber counter) and go to the “channel settings” tab to turn on the 4 and 5 switches.

Changed in channel settings as you explained.
To choose the right milling cutter, you need to decide on the tasks that he has to perform. If you need to make paneled doors for furniture, you need either a machine immediately or a manual tool with a power of 1500-1800 W with speed control installed in the table.
Of course, you can do other work with such a powerful milling cutter, but does it make sense? For processing furniture edges, the power will be clearly excessive (add more power of the vacuum cleaner working in conjunction with the router!), And the significant weight of the tool will quickly lead to fatigue. Well, for chamfering, in general, the most low-power milling cutter is enough.
Hence the conclusion suggests itself: you need to purchase another milling cutter (or even several). I have got accustomed to three Fiolent cutters, and for the following reasons. Low price and, on the contrary, high reliability, light weight and ease of use. Milling, holding the tool with one hand, is convenient when you need to profile an edge or chamfer a whole batch of parts: you guide the tool with one hand, and throw off the finished parts with the other. This is how productivity is ensured. I especially like the speed control at the push of a button, like a drill.
When guiding the tool, you can increase / decrease the speed, and a smooth start is ensured (1).
I bought a new "Fiolent" every 5 years, but not because of wear and tear: all milling cutters are in service (2, 3, 4). The goal was this - each milling cutter should perform one operation, but "excellently".
The first "Fiolent" - with a power of 500 W - was purchased in 1997 and was initially used in various jobs. The tool turned out to be very "tenacious", I still actively use it. The only "repair" is the replacement of a fully functional button with the same one, but with speed control. Now it performs only one task - it removes a chamfer, for which a guide with a recess for the milling cutter bearing is fixed on it from below. (5, 6). You don't need to set up anything - just go and work! The beech guide provides dust extraction and makes it easier to guide the tool along the workpiece. When milling a chamfer, the volume of material to be cut is very small, there is enough power in abundance.
5 years have passed, and in 2002 I purchased another "Fiolent", but with a power of 1100 watts. At first I also used it in a variety of ways, but now I am milling an edge. And not only for canopies with countertops, but also for furniture fronts. And the cutter is the same, only the bearing changes (7). If the doors are in operation, then we put a bearing with a diameter of 12.7 mm, or Ѕ ’ (8), if the visors are 9.5 mm in diameter, or 3/8 '' (9). Since the cutter itself has a radius of 6.35 mm (ј ’’), and its outer diameter is 25.4 mm (1 ’’), in the first case a shoulder is not formed, but in the second it is. (All sizes of cutters are tied to inches - this is the specificity.) Set the guide along the bearing (10, 11). It significantly improves the removal of cut products (nothing flies to the side) and makes it easier to move in a straight line. On curved sections, it has to be pushed back or removed, basing occurs along the bearing - and immediately the amount of dust and sawdust around increases sharply (see the master class on making a hallway, published in the same issue).
Another 5 years passed, and in 2007 the Fiolent milling cutter with a power of 1100 W was purchased. His tasks are certainly the most diverse. This instrument has the inscription "Professional", this is true and verified by practice. (By the way, among artisans there is an opinion that this inscription can scare away those who are not familiar with the products of this or that manufacturer. It's all the fault of the fly-by-night "brands" that compromise such an inscription.)
As you can see, my use of Fiolent milling cutters has a long (by modern Russian standards) history. Naturally, it was not without refinement. Its goal is to make a convenient and "environmentally friendly" tool, ideally suited to the performance of its task. But everything is in order.
First, the "extra" revolving stop was sawn off. Then a cover was made to prevent chips and dust from escaping through the top. On the first two milling cutters, I cut it out of fiberglass, but then I decided to just cut it out of the canister with scissors - it's easier this way.
The situation is similar with the base plate. Previously, I also made it from fiberglass, instead of the standard plastic one, but now the quality of the plate from the kit has become much better and suits me perfectly, it remains only to round the edges a little with sandpaper (12).
You ask: "What is this plywood box, sewer pipes and hoses?" This is because brushes produce carbon dust when the brushes are worn out. If you work on the street, it doesn't matter at all, but when a lot of all kinds of power tools are gathered in one small room, there is something to think about. It is in this box that warm dusty air enters, which cools the engine. Then he goes to the vacuum cleaner, and there, depending on the time of year, to the street or for additional cleaning.
The box is glued together from plywood scraps and thin strips. From a cut of a sewer pipe with a diameter of 40 mm, I made an air duct.To do this, I had to cut out a rectangular cutout with a jigsaw with a short file so that the duct was put on the box.
At the back, the air duct is closed with a stopper, and a tee is put on it in front - the air duct "flows" at an angle into the main air line, through which cutting products fly into the vacuum cleaner. Now you need to coordinate the air consumption, otherwise the dust suction from the cutter will deteriorate, the vacuum cleaner will drive air through the cutter motor. For this, the cross-section of the cooling duct is reduced using a streamlined piece of wood. The air duct is fixed to the box with electrical clamps. After that, all connections are sealed with silicone. A tee is put on the air duct.
The "park" of modernized milling cutters can be seen in the photo at the end of the article. Each one performs only his task, By the way, all these milling cutters are involved in a master class on making a hallway.
Practice has shown that the time spent on improving the tools was not wasted. All of the materials used were either very cheap or taken from scrap materials altogether.
It's nice to know that your instrument is not simple, but the most environmentally friendly. And besides, as I already said, you don't need to set up the router and change the equipment every time: take it from the shelf and work. So you can save the most important resource for a craftsman - time.
NOTE. Having looked at the catalog of cutters of some large specialized company, we can conclude that the variety of cutting tools is quite large. But in practice, for the formation of the edge, it is really possible to do with three cutters - profile, "chamfer" and cylindrical. The purpose of the first is to process the edges of furniture fronts, as well as countertops or canopies (after changing the bearing and changing the position of the guide). With the "chamfer", everything is clear from its name, and the cylindrical one is useful for various tasks, for example, for the manufacture of accessories and the installation of door hinges.
I added a little to my arsenal of tools for woodworking. I think every beekeeper has one, because you have to work with a tree - either make frames, or some kind of plank. I'm going to make bee removers the other day, figured out what would be needed for this and decided to do two things.
First, I bought a router. Supported by the domestic manufacturer - Fiolent. Power - 1.1 kW, 30,000 rpm. I gave 650 hryvnia for it. I wanted to immediately take a table for a milling cutter - it is convenient to work, the processing accuracy is higher. The table was not available, they can bring it on order. I looked at the price - 900 hryvnia - more expensive than the milling cutter itself. No, - I think, - I'd rather make such a table myself, the main thing in it is an even plate.
I went to the guys who sell rolled metal products, took from them for 230 hryvnia a piece of metal plate 90x50 cm in size, 8 mm thick. I drew with chalk where there should be a hole with a diameter of about 40 mm, and the guys with an oxygen cutter immediately cut it out on the spot.
In the village, I sanded the edges of the slab and the holes with a grinder (sagging after the cutter), removed a small chamfer. I screwed on a frame made of bars from below and attached legs - it turned out to be a completely tolerable table.
To the plate, from below, I attached the router itself with three screws - it has special threaded holes for fastening.
I planted a massive bar - I will push the workpieces into it during processing. In the center of the bar, I made a recess for the cutter.
The beam itself will be fixed to the table with clamps. Put the cutter - you can work.
The milling cutter, by the way, is not included in the kit, you have to buy it separately. The depth of the cut will be adjusted by lowering and raising the cutter, and the width - by shifting the stop bar. Now I can choose a quarter in one go, make a groove, easily make side strips of frames with permanent Hoffmann dividers, and not suffer with knives, as before. In addition, one operation can now be performed on the circular, and another on the milling cutter, which also saves time and effort.
And the second thing I did was a sliding table on my father's circular.I described this in detail here, and here there are still working photos. I found a plastic plate in the barn for the entire length of the circular, screwed it to the table with screws, as a result, closed the shaft with a jointer. I welded two brackets from the 70's corner to the machine bed. On the brackets - a guiding corner.
Made a sliding table from a duralumin plate. Below is a groove for the guide corner.
Above - an emphasis for workpieces.
With such a device, I can trim boards, bars, making a rectangular even cut.
I can cut workpieces of the same length. I will work - I will show you.
To receive new blog articles to your e-mail, subscribe.
I would be grateful if you share the article on social networks:
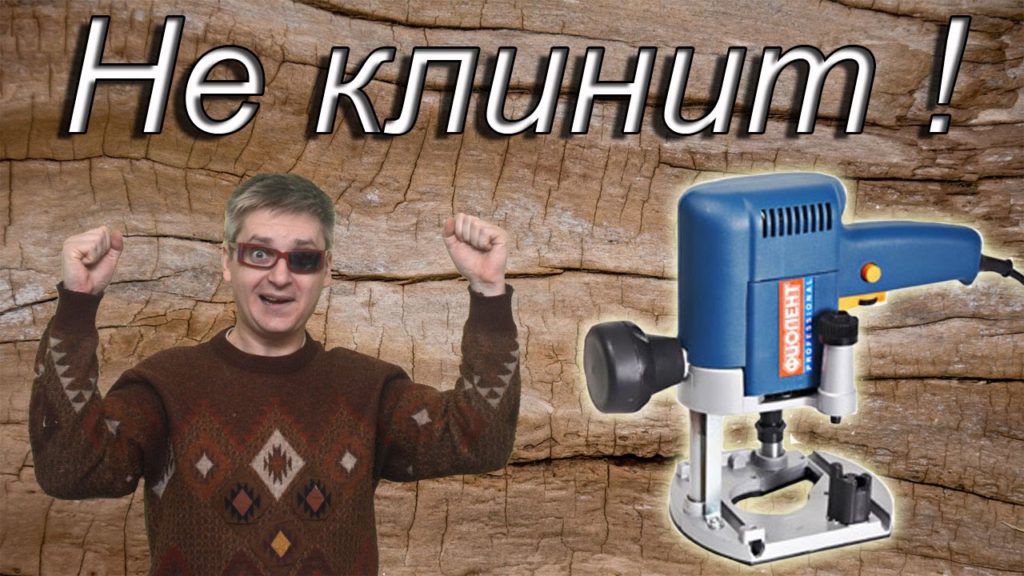
In this video I share the secret of how to use the Fiolent MFZ-1100e milling cutter so that it does not wedge. At the end of the video anecdote about artisans
——————————————————————————————————–
This is a channel about carpentry - how to make wood with your own hands.
Watch my other videos:
*** Carpentry projects (furniture, etc.) *** <>
*** Tools and Workshop *** <>
*** Clamps, clamps and vices ***
*** Circular saws. Homemade and store-bought ***
*** Self-made planer (planer) do it yourself ***
*** Useful carpentry tricks *** <>
*** Turning projects ***
*** How to cover the tree? ***
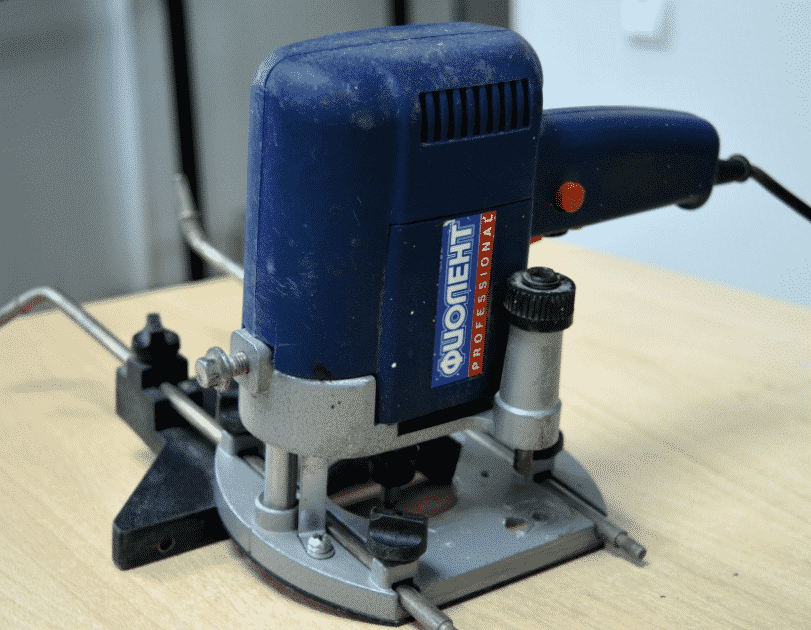
Routers are special equipment used in the woodworking industry. Manufacturers produce a wide range of models, ranging from small hand tools to sophisticated automatic machines.
Fiolent milling cutters are presented by household and professional models, differ in performance, reliability, practicality and an affordable price. They are produced in a durable and reliable aluminum alloy housing. They have a comfortable pistol grip, as well as an additional support for one or two hands.
Extending the service life and postponing the repair of milling equipment will allow regular preventive maintenance in our workshop. It includes the following works:
- bench test of the performance of the main units;
- cleaning from contamination;
- replacement of worn out parts;
- lubrication of moving parts.
Most often, our service receives equipment with a burned-out winding, worn brushes, a jammed shaft or bearing. Before the restoration of the instrument, the specialists of our service carry out diagnostics.
- We guarantee the high quality of the work performed and the service life of the refurbished equipment.
- Own warehouse, always in stock original spare parts and components.
- We issue a 1-year warranty for all types of work.
Leave a request on our website and get advice from our specialists.
Precise adjustment of the cutter overhang on the Fiolent MFZ-1100 router
By unscrewing the screw securing the ruler, we separate the motor from the sole with the struts.
Insert the M8 pin flush with the sole into the hole of the unsprung stand (the plastic sole plate must be removed). We drill a hole, cut the M3 thread and fix the M8 stud with an M3 countersunk screw.
We disassemble the case. Saw off the tides for the self-tapping screw that interfere with the hairpin.
We drill holes for studs and self-tapping screws in the body.
We twist the self-tapping screws holding the triangular plate into the tides with holes located at the end of the electric motor. Self-tapping screws on emery grind off the edge, and their length is selected depending on the thickness of the plate.
We assemble the body, fix the plate.
We put on washers on the hairpin, screw the adjusting, wing and cap nuts.
First, we set the cutter overhang to be larger than necessary. We fix this position by turning the handle. Then we tighten the adjusting nut until it touches the plate. Loosen the fixing handle. We measure the size of the cutter overhang and, by unscrewing the adjusting nut, set the desired one. We fix this position by turning the handle.The adjusting nut is counter-winged.
Adjustment by tightening the nut is problematic due to the skewing of the guides.
Feedback: Milling machine Fiolent MF3-1100E - Does not pull on a professional tool, but suitable for homemade homemade products
The milling cutter itself is quite compact in size.
The technical parameters of the tool are indicated on the side.
The cutter speed regulator is built into the start button, but I rarely use it, I work at speeds close to maximum.
There is a plastic pad on the working surface of the router so as not to scratch the workpiece being processed.
The level of the cutter exit above the working surface (the depth of "immersion" of the cutter into the wood) is set by a step stop and a smooth adjustment knob.
A ruler is provided in the design of the router, which should help set the level of the cutter output, but it is inconvenient to use it and it is rather difficult to accurately set the size. Therefore, I usually expose the dimensions "by eye" and try on an unnecessary piece of wood, and if the result suits me, I start working.
The same applies to the side limit bar, on which there is no ruler either. Of course, with such a limited number of measuring and adjusting devices, this router can hardly be called a professional tool. The inscription “Professional” on the router is perceived only as a publicity stunt.
There is another retractable plastic ruler on the side of the work surface, but I never used it.
Someone may have a question: what is this tool for, what can they do? It all depends on what kind of cutter you insert into it. In general, we can designate two types of work - edge processing and cutting all kinds of grooves. There are quite a lot of different milling cutters on sale, I now have only four, which are still enough.
The cutter is installed in a collet chuck. To fix the cutter, you need two open-end wrenches, 14 and 19 (no wrenches included). The clamp is designed for cutters with 8 mm shank. I heard that some milling cutters have adapters for different diameters of cutter shanks, but this model of the economy version does not apply to it either.
Well, a few examples of using the router.
Rounded edge cutter (before and after processing).
In the last photo, one side of the groove turned out to be not quite even, the hand trembled.
The advantages of this model include its low weight. If the work piece is small or difficult to hold, you can easily grip the router with one hand and the other with the other.
As a disadvantage, it is possible to note the lack of a device for fixing the router on the table, so that you can hold the workpiece being processed with two hands and reduce the "effect of trembling hands".
I can't say that I use a router all the time, but sometimes there is a desire to make something, for example, such a folding stool.
And then the router is useful, so friends can recommend it. Considering that now Simferopol is Russia, there may be difficulties with the promised 2-year warranty in Ukraine, but the milling cutter itself has not given reason to think about warranty repairs yet, it has been working for 9 months without comment.
Fraser FIOLENT MFZ-1100E. Alteration of the locking handle (revision). ELSA online store | LZA
Video instruction for replacing the front bearing on the Fiolent mill.
In this video, I showed how easy it is to * become a star * Without noticing your * jambs *, to teach others.
In the video I will tell you how to get rid of the stuck uprights on the Fiolent router.
In this video I am trying to understand the reasons for the wedge of the Fiolent MFZ 1100 E.
Replacement of bearings on the Fiolent MF3-1100E mill.
High-quality anchors for the Fiolent router (Simferopol) produced by the Rostov plant "Electroinstrument"
Many of you have encountered such a problem, some buy spare parts, and some even completely new cutters.
In the review, I personally expressed my opinion about this router. Why buy a tool that you then need to finish.
My youtube affiliate program: Epn affiliate program: Link for ePN Cashback:.
I eliminate the jambs in the work of the Chinese instrument, change the button, brushes, assembly, disassembly.
In this video, you will be presented with a brief overview of the fiolent pmz-600 e jigsaw.
In this video, I disassemble the mechanism for fixing the height of the Fiolent router and compare it with the Fest mechanism.
Other videos about improvements: 1. 2. 4.
Review of my first router Fiolent R2 620 E.
Anyone who is seriously involved in woodworking knows how important it is to have a good router. However, it is not at all necessary to pay exorbitant sums for this instrument - it is quite possible to make it with your own hands. How to do this will be discussed in this article.
A well-made milling table greatly improves the efficiency of working with a hand router. However, their purchase can cost a pretty penny, so it will be much easier to make such a table yourself, using special drawings for this. This will save a lot of money and, moreover, the process will not take too much time. There are several types of milling tables: stationary, adaptive and portable. This article will focus on the stationary version, because it is the most difficult to execute. And, therefore, having learned how to make it, other types of milling cutters can be made without difficulty.
Before starting any work, you should decide what kind of result you need to get. The easiest way would be to make a milling table on the basis of a regular workbench, but it is still better to make a separate structure. And if for this purpose an ordinary table is nevertheless taken, then it must be very strong and stable. It is also important to choose the right dimensions: for example, the optimal height is about 90-100 cm. An even better solution would be a table with an adjustable height, because this will allow you to adjust the milling machine to the needs of the master. A general view of the elements of the milling table can be seen below.
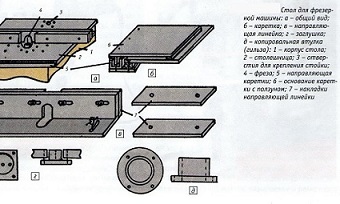
As for the materials, there are also subtleties here. Often, covers for such a table are made of MDF board. In general, this is justified: they are inexpensive, lightweight and easy to use. Phenolic plastic is also a popular material - it is stronger and more durable than MDF. But also more expensive - by about 20%. You can make a tabletop from a sheet of metal. One thing is important - the surface must be absolutely smooth, since the workpieces must easily move along the surface of the table, without clinging anywhere or getting stuck. The thickness of the cover must not exceed 35 mm.
Of the tools for work you will need:
- Electric drill.
- Chisel.
- Sander. In principle, sanding can be done manually with sandpaper, but this will take much longer.
- Plane.
- Screwdriver.
- Jigsaw.
As you can see, both the materials and tools for making a milling table are not so difficult to get. But it is extremely important that everything is of high quality, because the durability and reliability of the product directly depends on this.
When all the preparatory work is completed, you can proceed directly to the manufacture of the product. Everything is done in several stages. They will be listed below.
There are some nuances associated with the implementation of each of the points. However, anyone who has experience working with wood products will be able to make a milling table. It is only important to be attentive to the task at hand.
Most people prefer to buy ready-made tools, but some of them can be made by hand. Refers to those and hand-held milling cutter. Of course, we are not talking about assembling from scratch - it takes a lot of time. But the router can be made from another, simpler and cheaper tool. For example, from a drill. You can also make this tool from a grinder or hammer drill.It is optimal to take a device with a power of 600 to 1000 W (it can be "Fiolent" or something like that). The whole structure will consist of a motor (that is, the drill itself) and a frame in which it will be fixed. How exactly the process will take place will be discussed below.
The first step is to make a frame, into which you will then need to install a drill. It is cut from a chipboard plate, then a special iron clamp is installed on top for additional fixation. Parts of the structure are fastened together with self-tapping screws. A cutter is clamped into the drill chuck. To make the structure stable enough, the frame is attached to the tabletop using self-tapping screws. Of course, even with a seemingly good fixation, the drill can stagger in the frame, which will lead to the fact that wooden parts processed on such a router will look sloppy. A good solution would be to place the rotary lever on the side, and not on top - the motor will then be less loose during operation.
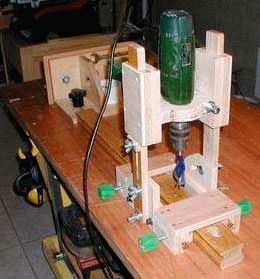
Of course, this solution also has certain disadvantages. For example, such a home-made device is not suitable for long-term work: with constant use, it will quickly fail. And because of the low power with the help of such a tool, it is difficult to process hardwood. But a router made from a drill will be inexpensive, easy to use, and even a beginner can assemble it. Therefore, this design is used quite often.
In conclusion, it is worth noting that you should not be afraid to make tools for woodworking yourself: expensive factory equipment will undoubtedly be better in some way, but sometimes availability and low price play a much larger role. Especially when it comes to products where it is not necessary to adhere to high precision. Such a self-assembled product is ideal for those who are just learning to work with wood, but sometimes it can help out more experienced craftsmen.
Many of you have encountered such a problem, some buy spare parts, and some even completely new cutters.
Many of you have encountered such a problem, some buy spare parts, and some even completely new cutters.
Replacement of bearings on the Fiolent MF3-1100E mill.
Replacement of bearings on the Fiolent MF3-1100E mill.
In this video, I showed how easy it is to * become a star * Without noticing your * jambs *, to teach others.
In this video, I showed how easy it is to * become a star * Without noticing your * jambs *, to teach others.
Video instruction for replacing the front bearing on the Fiolent mill.
Video instruction for replacing the front bearing on the Fiolent mill.
Fraser has already worked for more time than before the repair and does not heat up.
Fraser has already worked for more time than before the repair and does not heat up.
High-quality anchors for the Fiolent router (Simferopol) produced by the Rostov plant "Electroinstrument"
High-quality anchors for the Fiolent router (Simferopol) produced by the Rostov plant "Electroinstrument"
We give the video if we want to show how to know the view of the situation and repair the tool.
We give the video if we want to show how to know the view of the situation and repair the tool.
I eliminate the jambs in the work of the Chinese instrument, change the button, brushes, assembly, disassembly.
I eliminate the jambs in the work of the Chinese instrument, change the button, brushes, assembly, disassembly.
Many of you have encountered such a problem, some buy spare parts, and some even completely new cutters.
Replacement of bearings on the Fiolent MF3-1100E mill.
In this video, I showed how easy it is to * become a star * Without noticing your * jambs *, to teach others.
Video instruction for replacing the front bearing on the Fiolent mill.
Fraser has already worked for more time than before the repair and does not heat up.
High-quality anchors for the Fiolent router (Simferopol) produced by the Rostov plant "Electroinstrument"
We give the video if we want to show how to know the view of the situation and repair the tool.
I eliminate the jambs in the work of the Chinese instrument, change the button, brushes, assembly, disassembly.
Other videos about improvements:
1. /> 2. /> 4. />
Homemade elevator for the Fiolent router.
The base of the lift is a threaded rod М6х1, length 215 mm. Router stroke 54 mm.
When using a standard spring casing, the length of the stud must be 205 mm.
I would recommend starting a router upgrade with a stepless feed lift. Then the revision of the adjustable stop paired with a stepped revolving stop (on new models) may not be necessary.
As a last resort, it will be enough to repeat my scheme without the "microscrew"
Subscribe to my channel:
More videos in playlists
Wood lathe:
A method of making a copying sleeve without the use of special machines and devices. Only the tool that every novice master has. The sleeve is made literally “on the knee” within an hour. The video also shows some very useful tips and tricks.
![]() |
Video (click to play). |
I make a unique homemade product, one might say a tool for fixing thoughts, ideas, drawings, diagrams. The tool is made entirely by hand from available materials.