In detail: do-it-yourself aeg screwdriver button repair from a real master for the site my.housecope.com.
Using the Skil 2007 screwdriver as an example, let's consider the repair of its power button.
How to eliminate its main common disease - self-propelled?
Let's take a closer look in the article below.
By purchasing the Skil 2007 screwdriver, you are more likely to get this disease, which, in principle, can be solved. My spontaneous rotation on the screwdriver appeared after 3 weeks and since it was under warranty, I naturally did not think long and gave it for repair under warranty. They made it quickly in a few days, in the service I learned that these screwdrivers often have a start button out of order, and as a result, self-propelled things appear. After the repair, the screwdriver worked normally for about the same time, and then everything happened again. When the breakdown happened, I was on my business in Orenburg and therefore turned to a service center for repair there. This time, the repair of the screwdriver turned out to be of better quality, or it seems to me that I just got a better start button, because then the screwdriver worked for more than a year without problems, and at the same time I worked with it a lot.
The next time, when everything happened again, the screwdriver was no longer under warranty and I decided for myself that I would do the repair myself. Yes, and I'll take a look at one thing, what is the reason for the self-propelled.
Disassembling the screwdriver itself does not cause any problems, we just unscrew the screws around the perimeter with a Phillips screwdriver. Inside you will not see something complicated. There is a motor with a gearbox, a button and two wires that go from the contacts, where a battery is inserted that goes to the button and two wires go from the button to the engine.
If you want to go the simpler way, then just buy a new button, which costs about 300 rubles. and simply re-solder the wires from the engine to the button, and the wires from the button to the connector are included. Well, after that you check the button by connecting the battery, if everything works, then assemble the screwdriver in the reverse order. And the Skil 2007 screwdriver is ready to go.
![]() |
Video (click to play). |
But there is a second option for repairing a screwdriver - this is the repair of the button itself. Why did I start talking about such a development of an event as button repair? Yes, because when I turned to the service center with a request to sell me a button, I received an answer that they were over and would be no sooner than in a week. And the screwdriver, as luck would have it, was really needed for work not in a week, but tomorrow. Searches in other stores and other places were unsuccessful and I decided to disassemble and try to make the button myself.
In order to disassemble the button body, you need to remove the red push mechanism, this must be done carefully so as not to damage the base on which it is worn. It is best to shoot by rotating around the axis and at the same time pulling slightly towards yourself.
Now you need to remove the protective cover of the button, for this you need a knife and a flat screwdriver. Prying in turn and pushing out the latches, in those places where the arrows in the photo indicate, we remove the cover and the reverse compartment appears to our eyes, but the mechanism for turning on the screwdriver is not yet available.

Now you have to use a soldering iron and unsolder the two elements from each other, as shown in the figure. And now, slowly, we take out the element at number 1, which is located on top, after which you can safely remove the cover that covers the screwdriver activation compartment.


Now, neatly, we take out the switching mechanism from the case, holding the return spring.
Looking inside, you can visually see that the pads are erased.The reason that the contact pads are erased is the low quality of the metal. As a result of the fact that the metal dust is in an enclosed space, it settles between the contacts, as a result, a conductive surface is formed on the dielectric surface and a current begins to flow through it, as a result of which spontaneous rotation occurs.
And since the reason for this phenomenon is clear, that is, the way and solutions to this problem.

In order for the self-propelled to stop, you need to remove the metal dust between the contacts, cotton wool, or if you can't scrape it off easily with a knife.
After such a simple procedure, we assemble the button in the reverse order. We install it in place in the screwdriver body and assemble the body. After such a repair, the button will serve for some time, but you still have to buy a new one!
The site "I do it myself - I'll tell you how to do it for you!"

Look at the proposed crafts, perhaps you will want to do something for yourself.
In the process of rather short-term operation (about 3 months), a popular tool (especially among women) for cleaning floors - a PVA mop with a folding handle began to "malfunction", and then completely broke ... More ...
Such a coil water heater produces hot water very quickly. The coil is made of 1/2 diameter galvanized pipe. Pipe length - 8 m, coil diameter - 170 mm, height - 300 mm. It is best to wind the coil on a post dug into the ground. More details ...
One of the most "popular" tools of the home craftsman is a screwdriver. But, like any product, it breaks down. What to do in this case? In some types of work, an electric drill can save the situation, but only in some. You can take the tool to a service center and wait for it to be repaired. But this will take time and money, which will have to be paid to repair the instrument. But, as a rule, the third option is also available - the repair of the Makit screwdriver, and the device of the screwdriver is not so complicated.
Let's look at the main symptoms of screwdriver malfunctions and how you can fix them at home on your own.
Before proceeding directly to the malfunctions of this tool, it would be nice to briefly get acquainted with the device of the screwdriver and the purpose of its main units. Let's start with this. The photo below shows a disassembled screwdriver, on its basis and consider the purpose of the parts.
We'll start with the start button. The button has two functions: turning on the power supply circuit of the electric motor and its speed regulator. When the button is pressed all the way, the motor power circuit is closed by the button contacts to a straight line, providing maximum power and number of revolutions. The speed controller is electronic, it consists of a PWM generator located on the board. Depending on the force of pressing the button, the contact located on the button moves along the board. The degree of the generated pulse per key depends on its location along the board, the role of the key is played by a field-effect transistor (in the photo above it is designated as a "rotation speed regulator"). That is, the dependence is as follows: the harder the user presses the button, the higher the value of the pulse on the transistor and the more it opens, thereby increasing the voltage on the electric motor.
Motor rotation is reversed by reversing the polarity at the terminals. Reversal of polarity is carried out by means of changeover contacts, which are flipped by the user using the reverse handle.
Electric motor. In this tool, as a rule, single-phase DC collector motors are used. They are characterized by reliability, ease of production and maintenance.The design of such a motor is as follows: a body on which magnets, an anchor and brushes are located.
Reducer. Its purpose is to convert a large number of revolutions of the motor shaft into significantly lower revolutions of the chuck shaft. There are two types of screwdriver gearboxes: planetary and classic. The latter is very rarely used, so we will pay attention to the planetary type gearbox. The planetary gearbox consists of:
- ring gear;
- sun gear, which is attached to the shaft of the electric motor;
- satellites and a carrier (their number depends on the number of steps, there are two or three steps).
Without going into subtleties, let's consider the principle of operation of such a gearbox. The sun gear is driven by the armature shaft, in turn, its teeth drive the satellites, which transmit the rotation of the carrier. With a two-stage gearbox, the chuck shaft is connected to the second carrier, with a three-stage gearbox - with the third.
The force regulator is designed to adjust the force that is applied to the screw. As a rule, 16 adjustment positions are used. Thus, there is a wide range of screw tightening levels, which allows you to work with very fragile materials (drywall, etc.). Its principle of operation is well illustrated in the video below.
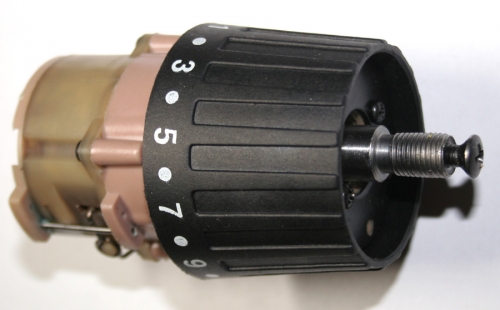
The chuck is attached to the output shaft of the gearbox and has three cams that securely hold the part in the chuck.
Having considered the main elements of the screwdriver, let's move on to possible malfunctions and possible ways to repair the AEG screwdriver. And we'll start with the electrical part. The main signs of a malfunction of the electrical component of the screwdriver are:
- the instrument does not turn on;
- no reverse mode switching;
- there is no adjustment of the number of revolutions.
The instrument does not turn on. The first thing to look out for when repairing a Skil screwdriver is the battery. If we put it on charging, and it did not help, then we arm ourselves with a multimeter and proceed to troubleshooting. To begin with, we measure the voltage on the battery, it should more or less correspond to the one indicated on the battery case. If the voltage is too low, it is necessary to identify the faulty element: a battery or a charger.
You can determine the health of the charger with a multimeter, for this we plug it into the network and measure the voltage at idle at the terminals. It should be a couple of volts more from the nominal indicated on the device. If there is no voltage, the charging unit is faulty. For such a repair of the Interskol screwdriver, knowledge of electronics will be required, otherwise it is easier to buy a new one.
If there is a problem with the battery, then to repair the Makit screwdriver with your own hands, you need to open the block with the elements. After the unit has been disassembled, it is necessary to carefully examine all the wire connections and check the quality of the soldering, whether any one has come off. If all connections are intact, we take a multimeter and measure the voltage across each element. Each element must have at least 0.9 - 1V voltage. If an element with a lower voltage is found, it must be replaced. The main thing is that the capacity and type of the cell correspond to the rest (i.e. if NiCd, then NiCd is also needed). You can learn more about the repair of batteries from the article: "Do-it-yourself screwdriver battery repair."
If the charger and the battery are in good order, and the screwdriver does not turn on, it is necessary to disassemble the screwdriver. Two wires go from the battery terminals to the button, we take a multimeter and measure the voltage at the input of the button (the battery is inserted in this case). If there is voltage at the input, then we take out the battery and with the help of the crocodile clips we short-circuit the wires from the battery. We put the device to measure resistance in ohms. Press the button all the way and measure at the exit from the button.The device should show the value of resistance tending to zero, if it is - the button is working properly, the problem is either in the brushes or in other elements of the electric motor. If the tester shows an open circuit, the button needs to be replaced or repaired. You can try to repair it yourself, as it often happens that there is no contact at the terminals due to burning, it will be enough to clean it with sandpaper and assemble it. The main thing when parsing a button is not to rush and act carefully, otherwise all the parts will fly apart, and you will have to puzzle for more than one hour how to assemble it.
Similar actions will need to be taken in the absence of reverse. We put one probe of the device on the input wire of the button, the second on the contact of the electric motor or the output of the button, this is more convenient. We switch the reverse handle. If everything is working properly, the device will fix a certain amount of resistance, if it is “silent”, the conductivity of the reverse contacts is broken. The procedure for disassembling and cleaning the contacts is the same as described above, as when repairing the Caliber screwdriver.
Is the engine running at maximum rpm and there is no rpm control? The cause of the malfunction can be both in the button itself and in the regulating transistor.
If all circuits to the electric motor are in good order, but the tool does not work, the malfunction may be associated with the brushes. Ideally, brushes should be changed when they are long, worn 40% of their original length. If the brushes are worn, replace them with new ones; if the brushes are in order, the problem is with the rest of the motor elements. To check the electric motor, you must disconnect the wires that go from the button. After disconnecting the wires, using a multimeter, we measure the resistance value at the wires fastening contacts. If the resistance value is small and tends to zero, most likely a winding break has occurred, either rewinding or a new motor is needed.

You can check the integrity of the armature windings, since the armature can be bought and changed on your own. To check the armature, it is necessary to measure the resistance on two adjacent collector plates, along the entire circumference. In this case, the normal value is "0". If during the check you find two adjacent plates, with a value other than zero, the anchor needs repair or replacement.
Signs of a malfunction of the mechanical part of the screwdriver may be the following:
- during operation, the instrument emits extraneous sounds that were not previously observed;
- strong vibration of the tool and chuck breakage;
- the screwdriver turns on, but its further work is impossible due to jamming.
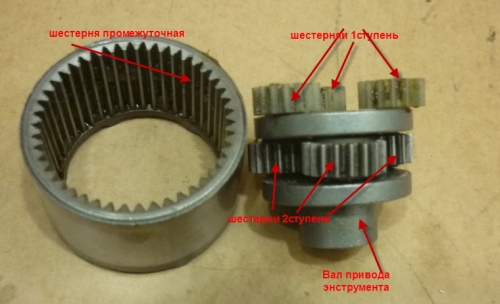
The reasons for "extraneous" sounds during the operation of the tool may be the wear of the bushings or the armature bearing. To do this, it is necessary to disassemble the electric motor and examine it for bearing integrity and the degree of bushing wear. The anchor should rotate easily, without friction and distortion. If necessary, these items can be purchased at the store and replaced by yourself.
The most common gearbox malfunctions are:
- bending of the gearbox shaft;
- wear of the working surface of the gears;
- wear of the bearing and / or bearing sleeve of the gearbox shaft;
- break in the pin on which the satellite is attached.
In all cases, it is necessary to replace defective gearbox parts. All described actions require attention and sequence in disassembling and assembling the screwdriver. Having shown these qualities, you can independently repair the Interskol screwdriver with your own hands, or any other, and only in some cases resort to the help of a service center.
The screwdriver is a mobile tool that makes it easier to work with fasteners and screw connections. Until recently, cordless screwdrivers could only be found in the arsenal of professionals, but with the advent of inexpensive household models on the wide sale, their popularity has increased dramatically.
Unlike an expensive professional tool, budget counterparts have a smaller resource, which is why they often fail.
One of the weakest points of a household screwdriver is the start button and reverse switch. As practice shows, it is they that break most often.
As a rule, it all starts with the fact that the soft start function stops working, then a stronger pull on the "trigger" is required to start the electric motor.
Over time, the tool ceases to respond to any manipulation altogether. Often there is a problem of the opposite nature, when the motor starts to work spontaneously.
In some cases, to eliminate the defect, it is enough to disassemble the tool and clean it, although more often a complete screwdriver button replacement... In both the first and second cases, you can fix the problem yourself. Everything in order.
The screwdriver button is the main control element that performs several functions at once:
- Turn on / turn on the instrument;
- Switching the direction of rotation;
- Smooth engine start;
- Speed control.
However, each of the controls built into the button block cannot work correctly by itself. Except for the direction of rotation switch, which is usually a separate function block.
In most cases, the body consists of three conventional compartments, in which the working units and mechanisms are located.
- In the lower part of the body there is an on / off control unit and an electric motor speed control unit.
- In the middle part there is the "trigger" of the smooth start (the deeper you press it, the higher the rotation speed of the cartridge). When pressed, the button slides in a special block along the guides, a variable resistor is responsible for adjusting the speed.
- In the upper part there is a reverse button - a switch for the direction of rotation of the cartridge. The direction is reversed by reversing the polarity of the voltage applied to the switch.
This is approximately how all control units of screwdrivers of different brands are arranged. To familiarize yourself with the device of a button of a specific instrument model in more detail, we recommend that you study screwdriver button diagram (it is in the instructions).
To diagnose and repair a screwdriver, you will need the following tools:
As a result of active use of any power tool, dirt inevitably accumulates inside its body.
Once in the control unit, it prevents the full movement of the "trigger" and blocks it.
Therefore, before going to the store for a new block, you should try to clean the old one. The carbon deposits formed on the contacts should also be cleaned with fine sandpaper. If the button is non-separable, the entire unit will have to be replaced.
Diagnostic steps:
- We disassemble the tool body. To do this, we disconnect the battery, unscrew all the screws (they can be hidden behind decorative overlays that will have to be removed).
- We check the serviceability of the electric motor. To do this, disconnect two power wires from the control unit and connect them to the battery contacts (the engine should start working).
- We disassemble the screwdriver button. To do this, squeeze the plastic latches and separate the two parts of the button housing.
- We make a visual inspection of the state of the button for dirt and damage.
- Next, you need to carefully assemble the screwdriver button, install it in place and test.
VIDEO INSTRUCTION
If the cleaning of the control unit did not work, it is necessary to replace the entire button unit.
- Disassemble the screwdriver (the process is described above);
- Install the new button in place of the old one;
- Connect the motor to the button terminals (polarity is not necessary in this case);
- Assemble the screwdriver by carefully placing the wires in the case.
It is very important to choose a button for a specific model of a screwdriver, since with all the external similarity and visual correspondence, the part may not fit into the grooves. Typically, new buttons are sold complete with battery terminals and a transistor.
A screwdriver is one of the most essential tools for a modern person. With its help, you can perform a lot of different household chores. It is indispensable for both global construction and local repairs. However, many parts of the device may fail sooner or later. This is most often due to improper use of the power tool. Sometimes you may need to repair a screwdriver with your own hands.
Diagram of a cordless screwdriver device.
Yes, of course, in most cases it is easier to contact a specialized workshop, but it can take a lot of time, and repairs can cost a pretty penny. In any case, minor breakdowns can be eliminated on your own. For example, the start button can be repaired. She often breaks down. How to repair a screwdriver button with your own hands will be discussed further.
Wiring diagram of the screwdriver button and the power transistor.
To begin with, you should think about how easy it is to make repairs by spending a minimum of money. Of course, a complete replacement of a structural element, and in this case a button, will save money and bring the device to its original level.
The screwdriver itself is quite easy to disassemble. To do this, you just need to take a Phillips screwdriver and unscrew all the screws around the perimeter, which are located here as fastening material. Having disassembled the device, you can find that it has a fairly simple structure. There is a motor, a gearbox, a button with two wires that connect it to the battery, as well as 2 wires that connect it to the engine.
So, the simplest repair method is to replace the button; it is simply soldered off from the motor. Then the connector is removed that connects it to the battery. Such a structural element is quite inexpensive. It can be purchased today for about 300-500 rubles. Further, the wires from the engine to the button are soldered in place, and those that go to the battery are installed together with the connector. The battery can now be reinserted and the instrument can be checked for functionality. If everything is in order, then we can safely state the fact that all the repair work was carried out correctly and competently. Now you can assemble the screwdriver. There is an even less expensive repair method, in which the button does not change, but is restored.
Electric diagram of the screwdriver button.
Of course, before proceeding directly to the repair work, it is imperative to select all the most necessary tools and materials. These include:
- knife;
- flat screwdriver;
- Phillips screwdriver
- soldering iron with rosin and solder;
- cotton wool.
Basically, these are all the tools and materials that you may need to carry out the work. The list is not that long. All this can be at home with any man.
Diagram of the gearbox of the cordless screwdriver.
Well, now let's go directly to the recovery process. Generally, the button is not easy to acquire. Often you have to make a pre-order at a service center and then wait several weeks for it to arrive. That is why DIY screwdriver button repair is relevant.
It can be noted right away that there is no need to unsolder the wires that come from the button. They will not interfere with the process of assembling and disassembling a structural element. So, the screwdriver was disassembled using the same technology that was mentioned above, which means that the button is in close proximity, that is, various repair work can be carried out with it. To begin with, it is worth removing the pressure mechanism.This must be done very carefully so that the base is not damaged.
The clamping mechanism is often red, but this all directly depends on the specific model of the power tool.
Electrical components of the screwdriver.
It is not necessary to remove the clamping mechanism with a sharp jerk. It is best to use slow rotational movements clockwise or counterclockwise. Here, too, it all depends on the specific model of the screwdriver. Now you can proceed directly to the repair, or rather, to identify the problems that led to the malfunction.
Any push-button product of this kind has a protective mechanism. It needs to be removed too. To do this, you will have to use the tools at hand, namely a flat screwdriver and a knife. Moving in a circle, you need to release the latches. This is done very simply, so it should not cause any problems in the work. Now you can remove the button cover, under which the reverse mechanism is located. In fact, the inclusion element itself is not yet visible. You still have to get to it.
To do this, you need to pick up a soldering iron and rosin. It contributes to the heating of the soldering point, which leads to the separation of the parts. In this case, you need to divide the two compartments between each other. First, the soldering iron is immersed in the rosin, and then leans against the separation. As a result of these manipulations, the mechanism from a single whole is divided into two parts. Only now you can try to get close to the switch. For this, the cover is removed from the corresponding compartment. Now the compartment for turning on the screwdriver becomes completely open to the human eye.
Stages of disassembling a screwdriver button.
Next, you need to carefully remove the mechanism from its rightful place, while holding the return spring, which is installed here without fail. Now you can look inside. Each person at this moment with the naked eye is able to see that all contact pads have worn out during operation. The main reason for this is most often the poor quality of the metal used to create these sites. As a result of the fact that the material is destroyed, its dust gradually settles between the contacts. This leads to the fact that those surfaces that were once dielectrics become electrical conductors. This is often the reason for the spontaneous switching on of the power tool.
Since the cause has been identified, accordingly, it remains only to eliminate it. This is done quite simply. With the help of the most primitive and simple materials, it is worth removing dust from the surface of dielectrics. For this, you can use the most ordinary cotton wool. It is advisable to pre-moisten it in alcohol. If this method does not help to remove the remaining dust, then you will have to use a knife. With it, you can try to scrape contacts. Some people use sandpaper for these purposes, but this is not recommended, since irreparable damage can be caused to the contact surfaces. That is, in this case, it turns out that the repair is not for the good, but reduces the entire result to a negative value.
Now we can state the fact that the button repair work has been completely completed. It remains only to collect the entire mechanism and tool. This is done in the reverse order. To begin with, two structural elements are soldered together. Then they are installed in their rightful place.
Comparative table of characteristics of screwdrivers from different manufacturers.
Now it is important to correctly install the return spring together with the pressure mechanism. It is worth immediately checking how the button is pressed. If it sinks, then it is possible that the technology was violated during its assembly. This leads to the fact that it simply will not work. We'll have to disassemble everything again. That is why you should be guided by the saying - measure seven times, and cut one off. This is the only way to return the original appearance to the push-button mechanism.
Then you can proceed to testing the functionality of the button. To do this, a battery is installed in its rightful place, and the power button is pressed. If everything is done correctly, the screwdriver should start. This suggests that the tool can be assembled. Previously, all structural elements are installed in their rightful places, and only after that the two halves of the tool can be connected together. Everything is returned to its place and connected with the same screws that were removed when the screwdriver was disassembled.
So, all the work has been completed, which means that we can summarize some of the results of all that was discussed above. As you can see, there are two main methods of restoring the functionality of the screwdriver button. The master himself must choose one of them. Of course, you can always contact the service center, but this is at least unprofitable. It's always best to do it yourself.
Is your TV, radio, mobile phone or kettle broken? And you want to create a new topic about this in this forum?
First of all, think about this: imagine that your father / son / brother has an appendicitis pain and you know from the symptoms that it is just appendicitis, but there is no experience of cutting it out, as well as the tool. And you turn on your computer, access the Internet on a medical site with the question: "Help to cut out appendicitis." Do you understand the absurdity of the whole situation? Even if they answer you, it is worth considering factors such as the patient's diabetes, allergies to anesthesia and other medical nuances. I think no one does this in real life and will risk trusting the life of their loved ones with advice from the Internet.
The same is in the repair of radio equipment, although of course these are all the material benefits of modern civilization and in case of unsuccessful repairs, you can always buy a new LCD TV, cell phone, iPAD or computer. And for the repair of such equipment, at least it is necessary to have the appropriate measuring (oscilloscope, multimeter, generator, etc.) and soldering equipment (hairdryer, SMD-hot tweezers, etc.), a schematic diagram, not to mention the necessary knowledge and repair experience.
Let's consider a situation if you are a beginner / advanced radio amateur soldering all sorts of electronic gizmos and having some of the necessary tools. You create an appropriate thread on the repair forum with a short description of “patient symptoms”, ie. for example “Samsung LE40R81B TV does not turn on”. So what? Yes, there can be a lot of reasons for not switching on - from malfunctions in the power system, problems with the processor or flashing firmware in the EEPROM memory.
More advanced users can find the blackened element on the board and attach a photo to the post. However, keep in mind that you are replacing this radio element with the same one - it is not yet a fact that your equipment will work. As a rule, something caused the combustion of this element and it could “pull” a couple of other elements along with it, not to mention the fact that it is quite difficult for a non-professional to find a burned-out m / s. Plus, in modern equipment, SMD radio elements are almost universally used, soldering which with an ESPN-40 soldering iron or a Chinese 60-Watt soldering iron you risk overheating the board, peeling tracks, etc. The subsequent restoration of which will be very, very problematic.
The purpose of this post is not any PR of repair shops, but I want to convey to you that sometimes self-repair can be more expensive than taking it to a professional workshop. Although, of course, this is your money and what is better or more risky is up to you.
If you nevertheless decide that you are able to independently repair the radio equipment, then when creating a post, be sure to indicate the full name of the device, modification, year of manufacture, country of origin and other detailed information. If there is a diagram, then attach it to the post or give a link to the source.Write down how long the symptoms have been manifesting, whether there were surges in the supply voltage network, whether there was a repair before that, what was done, what was checked, voltage measurements, oscillograms, etc. From a photo of a motherboard, as a rule, there is little sense, from a photo of a motherboard taken on a mobile phone there is no sense at all. Telepaths live in other forums.
Before creating a post, be sure to use the search on the forum and on the Internet. Read the relevant topics in the subsections, perhaps your problem is typical and has already been discussed. Be sure to read the article Repair strategy
The format of your post should be as follows:
Topics with the title “Help fix the Sony TV” with the content “broken” and a couple of blurred photos of the unscrewed back cover, taken with the 7th iPhone, at night, with a resolution of 8000x6000 pixels are immediately deleted. The more information you post about the breakdown, the more chances you will get a competent answer. Understand that the forum is a system of gratuitous mutual assistance in solving problems and if you are dismissive of writing your post and do not follow the above tips, then the answers to it will be appropriate, if anyone wants to answer at all. Also note that no one should answer instantly or within a day, say, no need to write after 2 hours “That no one can help”, etc. In this case, the topic will be deleted immediately.
You should make every effort to find a breakdown on your own before you get stumped and decide to go to the forum. If you outline the entire process of finding a breakdown in your topic, then the chance of getting help from a highly qualified specialist will be very great.
If you decide to take your broken equipment to the nearest workshop, but do not know where, then perhaps our online cartographic service will help you: workshops on the map (on the left, press all buttons except “Workshops”). You can leave and view user reviews for workshops.
For repairmen and workshops: you can add your services to the map. Find your object on the map from the satellite and click on it with the left mouse button. In the field “Object type:” do not forget to change to “Equipment repair”. Adding is absolutely free! All objects are checked and moderated. A discussion of the service is here.
Using the Skil 2007 screwdriver as an example, let's consider the repair of its power button.
How to eliminate its main common disease - self-propelled?
Let's take a closer look in the article below.
By purchasing the Skil 2007 screwdriver, you are more likely to get this disease, which, in principle, can be solved. My spontaneous rotation on the screwdriver appeared after 3 weeks and since it was under warranty, I naturally did not think long and gave it for repair under warranty. They made it quickly in a few days, in the service I learned that these screwdrivers often have a start button out of order, and as a result, self-propelled things appear. After the repair, the screwdriver worked normally for about the same time, and then everything happened again. When the breakdown happened, I was on my business in Orenburg and therefore turned to a service center for repair there. This time, the repair of the screwdriver turned out to be of better quality, or it seems to me that I just got a better start button, because then the screwdriver worked for more than a year without problems, and at the same time I worked with it a lot.
The next time, when everything happened again, the screwdriver was no longer under warranty and I decided for myself that I would do the repair myself. Yes, and I'll take a look at one thing, what is the reason for the self-propelled.
Disassembling the screwdriver itself does not cause any problems, we just unscrew the screws around the perimeter with a Phillips screwdriver. Inside you will not see something complicated. There is a motor with a gearbox, a button and two wires that go from the contacts, where a battery is inserted that goes to the button and two wires go from the button to the engine.
If you want to go the simpler way, then just buy a new button, which costs about 300 rubles. and simply re-solder the wires from the engine to the button, and the wires from the button to the connector are included. Well, after that you check the button by connecting the battery, if everything works, then assemble the screwdriver in the reverse order. And the Skil 2007 screwdriver is ready to go.
But there is a second option for repairing a screwdriver - this is the repair of the button itself. Why did I start talking about such a development of an event as button repair? Yes, because when I turned to the service center with a request to sell me a button, I received an answer that they were over and would be no sooner than in a week. And the screwdriver, as luck would have it, was really needed for work not in a week, but tomorrow. Searches in other stores and other places were unsuccessful and I decided to disassemble and try to make the button myself.
In order to disassemble the button body, you need to remove the red push mechanism, this must be done carefully so as not to damage the base on which it is worn. It is best to shoot by rotating around the axis and at the same time pulling slightly towards yourself.

Now you need to remove the protective cover of the button, for this you need a knife and a flat screwdriver. Prying in turn and pushing out the latches, in those places where the arrows in the photo indicate, we remove the cover and the reverse compartment appears to our eyes, but the mechanism for turning on the screwdriver is not yet available.

Now you have to use a soldering iron and unsolder the two elements from each other, as shown in the figure. And now, slowly, we take out the element at number 1, which is located on top, after which you can safely remove the cover that covers the screwdriver activation compartment.


Now, neatly, we take out the switching mechanism from the case, holding the return spring.
Looking inside, you can visually see that the pads are erased. The reason that the contact pads are erased is the low quality of the metal. As a result of the fact that the metal dust is in an enclosed space, it settles between the contacts, as a result, a conductive surface is formed on the dielectric surface and a current begins to flow through it, as a result of which spontaneous rotation occurs.
And since the reason for this phenomenon is clear, that is, the way and solutions to this problem.

In order for the self-propelled to stop, you need to remove the metal dust between the contacts, cotton wool, or if you can't scrape it off easily with a knife.
After such a simple procedure, we assemble the button in the reverse order. We install it in place in the screwdriver body and assemble the body. After such a repair, the button will serve for some time, but you still have to buy a new one!
The site "I do it myself - I'll tell you how to do it for you!"

Look at the proposed crafts, perhaps you will want to do something for yourself.
In the process of rather short-term operation (about 3 months), a popular tool (especially among women) for cleaning floors - a PVA mop with a folding handle began to "malfunction", and then completely broke ... More ...
![]() |
Video (click to play). |
Such a coil water heater produces hot water very quickly. The coil is made of 1/2 diameter galvanized pipe. Pipe length - 8 m, coil diameter - 170 mm, height - 300 mm. It is best to wind the coil on a post dug into the ground. More details ...