In detail: do-it-yourself repair of edgebanding machines from a real master for the site my.housecope.com.
Services for the repair, maintenance and commissioning of industrial equipment
Compressors and compressor stations:
Abac, Aerzen, Airpol, Alup, Atlas Copco, Atmos, Bauer, Gardner Denver, Betico, Boge, Bottarini, CompAir, Ceccato, Chicago Pneumatic, Dalgakiran, Demag, Durr-technik, Ekomak, Fiac, Fini, Hitachi, Hertz Kompressoren, Irmair, Ingersoll Rand, Kaeser, Renner-Kompressoren, Sullair, Tamrotor, Worthington, Remeza, Akron, Arsenal (ZIF, MZA), Borets (Storm), Ilkom (RVK), Chita Mashzavod (PV, NV), Remeza (VK) , ChKZ (DEN);
Woodworking machinery:
Robland, Altendorf, Biesse, Casadei, Vitap, Griggio, Tecnoma, Orma, Kaindl, Osama, Holzher, Mida, Futura, Weinig, Filato + many noname;
Refrigeration compressors:
Bitzer, Copeland, Frascold, Danfoss, Alco, Bock, Hanbell, York.
Edgebanding machines are designed for the application of various types (PVC, ABS, melamine and veneer) of edges on straight and curved parts.
All work is done regardless of who the manufacturer of the machine is.
There are several schematic diagrams of the arrangement of the edges of the edging units, otherwise the differences are present in small nuances associated with the coordination of machine parts and edge feed.
Edgebanding machines for pasting curved and straight parts, production Vitap.
- repair of glue knots.
- replacement of graphite liners of glue rolls.
- repair of pneumatic parts and assemblies.
- repair and restoration of electrical parts and components.
Automatic edgebanding machines such as: Lato, Tecnoma, Griggio, Holtzher, Casadei, Akron, Filato and any others.
![]() |
Video (click to play). |
- repair of glue knots (especially for machines of the Lato and Tecnoma series).
- replacement of transformer tapes and drive rollers of the workpiece feeding mechanism of Kasadei machines.
- setting up milling and trimming units.
Repair of glue unit drive gearboxes and edge pressing unit for Lato machines.
Repair and adjustment of pneumatic and electrical equipment included in the machine tools.
Video uploaded by Nikolay Volkov
Search Nikolay Volkov 4 years ago
Edge cutter, edge banding machine, homemade, do it yourself

This video is about a homemade edge trimmer. You can even make a hot air gun like this. A homemade edging machine is made from scrap materials, this video shows how you can make a homemade edging machine. And here is a channel about aircraft models, construction and flights, very interesting
Video on how to glue a 0.4mm PVC edge on a manual edge banding machine.
Those who make furniture with their own hands and use materials such as chipboard and MDF are familiar when protection is required at the ends of the sheets after cutting. Due to this, the products both last longer and have a more beautiful appearance. The PVC edge for furniture is often used as protection, but there can be other options as well. In this article we will look at how to make a special edging machine, as well as how to glue the protective edge with our own hands.
As the basis of the machine, I used my universal platform, which was made for my old homemade drill stand. In addition, I prepared a polypropylene pipe, a clamp for sewer pipes 50 mm, and an aluminum profile from a mosquito net.
For the manufacture of the guide rollers, I used pieces of polypropylene pipe with a diameter of 20 mm and a height of 20 mm.
Inside, on both sides, I soldered nuts 8 mm, and on top I secured it with an enlarged washer with a countersunk bolt 6 mm. The bolts were not tight enough to allow the rollers to rotate freely.
In addition, he assembled a "third hand" to secure the industrial hair dryer. The hair dryer can be installed at various convenient angles, at the desired distance from the edge band.
An edging tape is taken, turned outward with an adhesive surface, and pulled along the rollers to the guide.After setting the desired distance and temperature of the hair dryer, we begin to glue.
We remove the excess tape with a knife, go through with sandpaper. Now we see a neat and durable edge, which outwardly is not inferior to the factory one.
Modern CNC edgebander
Edging machines are among the woodworking equipment, without which no furniture production can do. Machines of this type allow you to veneer the edges of panel board products, protecting them from negative external influences and giving a finished look. Repair of the edging machine is one of the areas of work of our company in Kolomna.
Depending on the purpose, some edging machines are designed for processing the ends of rectangular blanks, while others are designed for facing curly products of complex shapes. Straight edge trimming models are usually designed to automatically feed the facing material, so these machines are more difficult to repair than hand-fed curved trimming machines (see “Repairing Edgebanding Machines”).
Currently, on the market of industrial resources, there is a fairly impressive amount of woodworking equipment of the edgebanding type with a different number of processing units that make up the structure. The number of processing units determines the quality and accuracy of the application of edging materials, and, consequently, the aesthetic component of the workflow. Meanwhile, the larger their number, the more difficult the recovery actions when it is necessary to carry out repairs.
In the course of operation, any technique invariably wears out, which cannot but affect the quality of work. Of course, you can simply replace an outdated machine with a modern analogue, but the most correct solution to the problem will be a complete revision of all parts of the machine and the removal of worn-out components and parts that are on the verge of wear. This method will allow you to very significantly save the financial resources of production, having received equipment with characteristics that are in no way inferior to those of new technology.
The overhaul of the edge machine in relation to the economic part is not a cheap procedure, but it is extremely important, allowing you to eliminate the traces of wear on the machine. The result of the restoration work will be a completely updated and technically improved machine with accuracy indicators identical to the factory ones. The price of the issue depends on the type of equipment and the degree of its modernization. According to experimental calculations, even in the most difficult case, the cost of repairs will cost half the price of a new machine with similar capabilities.
If the equipment of your enterprise is outdated physically and morally, which is typical for most domestic production organizations, do not rush to get rid of the idle or unprofitable unit in operation. It is worth remembering that any, even the oldest machine, is of physical value, having an iron frame, and the larger the equipment, the more metal it contains, and, therefore, the more expedient the restoration.
Our trading and manufacturing company is ready to carry out the repair of any machine tool of the woodworking or metal-cutting series, having an excellent resource base and our own equipment for the manufacture of parts for machine tools. Contact +7 (916) 166-73-04, +7 (496) 613-20-02.
The "Instrument-Plus" company offers you prompt repair of edge banding machines WITH GUARANTEE ... We are also ready to provide services for setting up edge banding machines and launching their production (commissioning of edgebanding machines).
We have extensive experience in the repair and adjustment of edgebanding machines of the following brands:
Our advantages:
- more than 10 years of experience;
- own warehouse of spare parts;
- operational terms for the repair of edge banding machines;
- Repair work warranty;
- Prompt repair and departure of specialists throughout Russia;
- The quality of the renovation work has been checked by 100 of our clients.
For service and repair of edgebanding machines, you can call us by phone: +7 (831) 213-58-48
Or send an application to our specialists by e-mail:
Our advantages in the repair of edgebanding machines:
- more than 10 years of experience;
- own warehouse of spare parts;
- operational terms for the repair of edge banding machines;
- Repair work warranty;
- Prompt repair and departure of specialists throughout Russia;
- The quality of the renovation work has been checked by 100 of our clients.
Our services:
- prompt repair;
- setting up machine tools;
- launch of equipment into production.
Call us: +7 (831) 213-58-48
Video uploaded by Nikolay Volkov
Search Nikolay Volkov 4 years ago
Edge cutter, edge banding machine, homemade, do it yourself

This video is about a homemade edge trimmer. You can even make a hot air gun like this. A homemade edging machine is made from scrap materials, this video shows how you can make a homemade edging machine. And here is a channel about aircraft models, construction and flights, very interesting
Video on how to glue a 0.4mm PVC edge on a manual edge banding machine.
This machine is an equipment, the main purpose of which is cutting unedged boards, as well as longitudinal edge trimming to obtain unedged sawn timber. Edge-trimming machines can also be used for cutting slab boards to obtain wagon, pallet blanks, container boards, furniture board blanks, rails.
Very often, the edge trimmer is used in the sawmill and furniture industries, which have high and medium power. Among the areas of application, the edge trimmer can often be found in mechanized sawing lines behind the machines of the first row, as well as in areas where the slab is being finalized. In addition, edging machines are used on sorting lines to increase the grade of sawn timber (on the revision of the wane board).
To process the edges of MDF, chipboard or other similar types of modern sheet materials, you need to use special edging equipment. It is very difficult to do such work manually, without the use of special mechanisms. To get an excellent result, you need to do everything very painstakingly and subtly.
You can buy such equipment, but it is very expensive. As a result of this, a more economical option would be a homemade edgebander, which everyone can make, having drawings.
The simplest machine for edging modern sheet materials consists of the following elements:
- feed mechanism to the edge of the material from the roll;
- pressure roller;
- adhesive heater;
- adhesive application system.
To make a homemade edgebanding machine with your own hands, you can use separate spare parts for various power tools or immediately ready-made household electrical appliances.
For example, a conventional hair dryer can be used as a heater; a hand-held electric drill successfully performs the functions of a pressure roller drive.
To make the drawing and design of such a device simpler, when working, you can use materials on which glue has already been applied. In this case, not only will the process of processing the edges of the material be simplified, but also the dimensions of the entire machine will be reduced.
To advance the workpiece along the pressure roller, you can use some kind of special guiding mechanism, or you can do it manually, which, again, will simplify its design.
If it is not possible to use the material with the applied glue, it is additionally necessary to equip the machine with a container in which the glue will be constantly heated during operation.
For the convenience of performing all work with the machine, it must have a separate mechanism that cuts off excess material for facing edges, which necessarily arise during such work. Any guillotine device can be used for this. The most convenient option would be such a longitudinal device, which cuts off all excess directly when the workpiece moves.
Thus, making an edgebander with your own hands is not difficult at all, and you will not need to buy any expensive parts. Therefore, using it to repair furniture will be a very simple and not at all costly process.
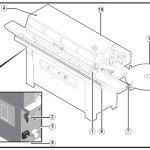
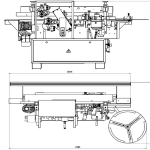
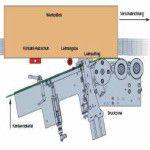
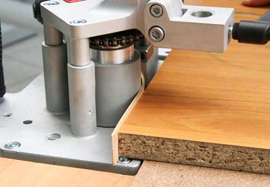
DIY edgebander (photo)
To process products made of fiberboard, MDF and other sheet materials, special equipment is required for processing the ends of the panels - this is a delicate and painstaking work, manual execution is unlikely to be convenient. Therefore, you need to purchase special equipment or, even better, make a homemade edgebander with your own hands. Firstly, making the equipment yourself saves money, and secondly, it is valuable experience and practice in engineering, which is necessary for every homeworker. Moreover, the principle of operation and the device of the edge banding machine are quite simple.
The main area of application of such equipment is furniture production, here this type of machine is one of the mandatory elements of technical equipment. For industrial needs, numerous machine models are offered, differing in performance, functions, price and other characteristics and are suitable for working with both straight and curved surfaces. This group of units has a common characteristic - their performance is too high for private use, so it makes no sense to spend money on purchasing a professional model.
The principle of operation of both factory and home-made machines is approximately the same - a decorative strip of material is glued to the raw end of the panel, which not only covers the raw material, but also protects the structure of the panels.
Edgebanding equipment can handle a variety of materials, including:
The layer of material can be very thin - from 0.4 mm, the width of the strip, as a rule, from 2 to 6 cm. For gluing, a special glue is used, which firmly fixes the decorative edge.
Immediately it is necessary to make a reservation that without sufficient experience in working with the tool and materials and understanding the principle of operation of this equipment, it is unlikely that an excellent result will be achieved. If you have enough confidence in your abilities, then you can safely begin to study the available circuits and assembly tips.
In order to properly design a machine, you need to decide on the following parameters:
- type of facing material;
- the thickness of the material used for the edge;
- necessary equipment functions.
The most important thing at the manufacturing stage is to correctly assemble the base. It consists of an edge feed mechanism, a pressure roller, a heating element and an adhesive application system. For their manufacture, you can use spare parts for power tools and whole appliances. For example, a hair dryer is suitable for heating, and an electric drill can be used to drive the pressure roller.
To simplify the machine layout, you can use materials with glue already applied to them. This will not only simplify the manufacturing process, but also reduce the size of the machine. To advance the workpiece along the pressure roller, a guide mechanism must be provided.
If it is not possible to use strips with pre-applied glue, it is necessary to provide for the presence in the design of a special container for glue, where it will be preheated. You also need to equip the device with a mechanism for trimming excess material for the edges, this can be any guillotine type device.
As you can see from the above, it is not so difficult to make a homemade edgebander with your own hands; this does not require complex and expensive elements. Therefore, subsequent repairs will be quite simple. And if you don't want to get involved with repairs, buy branded equipment, and let the service center specialists deal with it in the event of a breakdown.
This video was created in order to recognize the malfunctions of the main components of the edgebanding machine. So.
Supplier in Russia: LLC NOVA Mechanics Engineering Phone: +7 (343) 329-31-30 Email. mail: .
Edge machine. Overview. You can buy it here:.
The KDT edgebander setup and maintenance guide will help you get the most out of it.
Positional edgebander MF350A for straight and curved parts.
Bonding pvc edges when special equipment is not available.
Kromochnik was acquired by Leroy Marlene for a new hypermarket in Kiev on Bolshaya Okruzhnaya.
Association "KAMI" every Thursday goes live on Instagram to tell the features and benefits.
We continue to repair the 6P81 milling machine.
Edge banding machine, self-made, do it yourself.
Video on how to glue a 0.4mm PVC edge on a manual edge banding machine.
Repair of industrial equipment in Tomsk. 89061999883.
Edgebander GRIGGIO 4.3. Repair of the pneumatic cylinder of the trimming block.
2 HIGHLY Qualified Specialists (We have been repairing machines for 30 years.). Qualification: Locksmith-Repairman, 6th grade.
Video about training courses for the ship turner program.
Repair of the TV-4 lathe. Restoration of the bore of the spindle bearings in the headstock.
Tool shop CNC machine repair Renovated by CNC Electronics West Inc 1445 Tidelands Avenue.
Width of the processed material, mm. 10 - 50
The volume of the container for glue, dm.cub. 200
Glue temperature adjustment range, deg. 50 - 300
Installed power, kW. 1.6
Overall dimensions, mm., No more:
Additionally, on request, the machine is equipped with an imported drive "MOTOVARIO" and frequency control of the glue roll speed from 3 to 15 m / min.
The machine is manufactured with both a lower and an upper bath.
1. Machine assembled according to specification
2. Electric control box ESHU.KOS.4.000. (mounted on
3. Set of technical documentation - passport.
DEVICE AND PRINCIPLE OF OPERATION
The machine consists of a welded frame on which the main units and mechanisms are mounted, an electrical control box, a heating element temperature control panel.
1. The edge, pre-cut with an allowance for the entire length of the workpiece, is manually fed by means of a slide onto the glue roll, on which hot melt glue is applied. From the glue roller, the edge, with the applied hot melt glue, is fed to the rubberized roller, where gluing occurs when the workpiece is manually fed.
2. The temperature control of the heating element is carried out using a thermostat.
3. The electric motor is controlled from the ESHU console using the START and STOP buttons.
Edge banding is the process of gluing a special material onto it in order to give it a new look. In the furniture industry, where the narrow edges of panel board parts and plates are subject to refinement, this finishing method has become widespread. A huge choice of decor and color solutions opens up endless possibilities for creativity of furniture designers, and also stimulates designers to improve edgebanding machines.
The operation of any edge banding machine is based on the principle of creating a system "part - glue - facing material" (Fig. 1).Due to mechanical compression and physicochemical transformations, such a system is ultimately stabilized: the lining must be firmly fixed on the edge of the workpiece. Most edgebanding machines are geared towards the use of hot melt adhesives. Such thermoplastic glue (hot melt glue), when heated, passes from a solid state to a liquid, it has good adhesion. When it cools, a thin layer of hot melt glue quickly hardens, forming a strong adhesive seam. This technology requires strict adherence to temperature conditions, pressing the components to be glued to each other with a certain force, as well as holding the finished product. If this is not done, the system will become unstable and the cladding may simply fall off.
Depending on the version, the edgebander in the basic configuration is supplemented with various functional modules designed to increase its productivity, automate a number of auxiliary processes, prepare and bring the edge to an ideal state. These modules are focused on a certain size and type of workpiece, type of facing material. The main options for indicators that determine the performance of the edge-facing machine are presented in table. one.
To implement the basic cycle in edge banding machines, a combined module is used (Fig. 2), which includes systems for supplying the facing material, applying and heating glue, and pressing.
Facing material supply system consists of a magazine for a roll, rollers and a guillotine.
First, a roll of tape is installed in the store for wrapping, from the store, the tape is pulled by rollers into the gluing zone. The drive for the feed rollers is usually variable speed for adjusting the feed speed of the tape. The guillotine cuts the tape so that it is long enough to cover the entire edge of the part plus an allowance of 5-25 mm.
The guillotine drive is electromechanical or pneumatic, with automatic control. The trigger point of the guillotine is determined using a workpiece position sensor. Trimming the tape in the guillotine is preliminary.
Glue application and heating system. The machine can be equipped with a system for applying and heating glue in two fundamentally different versions: for edging with and without an adhesive layer as delivered. In the first version, since the glue has already been applied to the surface of the tape, it is only heated using an industrial hair dryer with hot air. In the second, the glue is heated in a glue pot and, in the molten state, is applied to the surface of the tape with a drive roller. Some models have two rollers, the second is used to apply glue to the edge of the part. The glue bath is an important element of the edgebander. The glue in it should be heated to a temperature of about 150-200 ° C, circulate and not burn, have a uniform consistency. To ensure this, teflon-coated trays, temperature sensors, heating elements of a special design are used. In some models, a cartridge is installed to apply glue to the glued surfaces.
In this scheme, a hairdryer or an infrared lamp can also be present, their function is to preheat the facing material with hot air in order to give it elasticity and high adhesion with glue.
Clamping system. It is depicted conventionally, in the form of a support roller. At the moment of contact of the tape of the facing material with the edge of the part through the layer of molten glue, a certain stable compressive force of these three components should occur (Fig. 1). On edge banding machines with a mechanized feed, the tape is pressed against the edge of the part by one or more consecutive rollers. On manual feed models, this function is performed by the machine operator.It simultaneously feeds the part and presses it against the outgoing belt, using one or more rollers as support. This technique requires appropriate work skills: in addition to uniform clamping, it is necessary to constantly synchronize the feed rate of the part and the belt in order to avoid rupture or "assembly" of the latter.
Of course, the design of the basic module depends on the machine class. First of all, this concerns the glue application and heating system. More sophisticated equipment is equipped with additional sensors and drives that allow controlling the module and the machine in automatic mode, using electronics.
For gluing the cladding on the edge of the part, a tape or strip is used, the width of which is 2-5 mm wider than the height of the part (edge). This is necessary in order for the facing material to be guaranteed to cover the edge. After gluing, so-called overhangs are formed - material protruding from both sides of the edge. To remove it, apply milling module (fig. 3). Its principle of operation is as follows. The cutter cuts off all facing material protruding from the part. As a rule, such a tool has a high-speed drive - 10,000-12,000 rpm, in order not to damage the surfaces. In addition, for the correct positioning of the workpiece, the module is equipped with limiting rollers. A module with two cutters, each with an individual drive, is adjusted to a specific workpiece height. For fine-tuning the module and its subsequent fixation, a movement mechanism with a "screw-nut" transmission can be used.
After the tape is pre-cut with a guillotine, it is glued to the edge with an allowance. To remove such an allowance, use trimming module (fig. 4). The design of the module can be different. In the simplest version, it is a circular saw with vertical movement, equipped with an individual low-power (0.2-1 kW) drive. At the command of the operator, it enters the working area of the edgebander and cuts off the protruding part of the facing material. This principle is realized only on machines with manual feed.
For models with mechanized part feeding, the trimming module is more complex. As a rule, the saw with a drive is mounted on a carriage. The carriage has two short strokes: one - to feed the saw, - to cut the band allowance, the second - to equalize the feed speed of the part and the saw. The work cycle looks like this. The part moves along the edge banding machine. At a certain moment, the carriage with the saw begins to move at a feed rate in the same direction as the part. For a short time (1-5 s) the saw becomes stationary relative to the workpiece. At this point, the carriage makes one more movement, and the saw cuts off the protruding part of the band. To prevent the tool from damaging the part during sawing, a limiter roller is provided.
The carriage can be moved using linear guides or levers, the drive - using pneumatic cylinders with automatic cycle control. Such control is carried out using part position sensors and a carriage with a saw. A branch of the aspiration system must be connected to the trimming module for disposal of sawing waste.
The required capacity plays a key role in the selection of the type of edgebander. To calculate it, you need information about the production program in terms of the sum of the perimeters of all parts produced in a month or more. This figure - the approximate length of the facing material that must be glued to the edges during the specified period - is then divided by the number of working hours in minutes in this period. The conditional veneering speed is obtained. To calculate the required feed rate, this figure must be multiplied by a factor of 1.5-3, taking into account downtime, equipment loading and unloading, etc.Let's give an example of a conditional calculation. Let's say a furniture shop produces 6,500 pieces of 1 x 1 m in a month, which is equivalent to 6,500 (1 + 1 + 1 +1) = 26,000 m of edging. We divide the result by the working time fund in a single-shift operation (10 560 min): 26 000: 10 560 = 2.46 m / min, then multiply by a factor of 2 and obtain the requirement for the feed speed of the edge banding machine - about 5 m / min. This means that production will need a model manual edge banding machine, where the feed speed of the tape of facing material varies in the range of 6-8 m / min.
This model should be chosen when there are parts with curved edges in the production program, since if automated machines exist for such purposes, they are very expensive. The minimum radius of curvature of the part, taking into account the particular design of the equipment, is usually 20 mm.
The hand-fed edgebander (Fig. 5) has a relatively simple layout. A table made of PCB or similar material is installed on the bed, which allows not to damage the surface of the workpiece. The base unit is mounted on the table. Downstream of this module, in the course of feeding the workpiece, a milling module can be installed to remove overhangs. Such a scheme is also acceptable, in which the facing material is glued on one machine, and the overhangs are removed on another.
In addition, machines of this type are optionally equipped with a simple trimming module for fine trimming of facing material (Fig. 4). Some models have such a useful function as a 45 ° tilt of a part of the table - for wrapping an edge made at an oblique angle to the face of the part. The advantages of such equipment are its mobility (when the weight and dimensions allow the equipment to be moved to the location of the edge), as well as design features (supporting roller support for large-sized parts, replaceable guides for working with solid strip facing materials, etc.).
A manual edgebander works with edging material typically up to 3 mm thick, covers an area of up to 2-3 m 2, maintains a feed rate of 3-6 m / min, consumes about 2 kW of electricity and is operated by one operator. For the functioning of all systems of the machine, it is required to connect a compressed air supply system at a pressure of 0.6 MPa.
Such equipment does not require complex setup. In practice, these edgebanding machines are serviced by an operator. The adjustment consists in the optimal setting of the heating temperature of the glue and tape (if any), setting the rotation speed of the glue rollers and the feed speed. It is important that the amount of glue applied to the edge and / or tape optimally matches the specifications: an insufficient amount of glue will most likely lead to a loss of bond strength between the facing material and the part, and excess will cause the excess to be squeezed out onto the surface of the product and, accordingly , pollution. The machine is tested in operating modes, after which the degree of adhesion of the glue and the reliability of the glue seam are monitored. A special transparent PVC film is used as a test facing material, which allows you to see how the adhesive is distributed on the surface after compression and polymerization. Such tests will not be superfluous during the work shift, they will serve to prevent the occurrence of hidden defects. It is necessary to properly sharpen all cutting tools - guillotine knives and cutters. The glue tray and glue circulation system must be cleaned regularly in accordance with the manufacturer's instructions.
To ensure safe operation, the edgebander must be equipped with a guard and marked in accordance with standards for surfaces subject to heating.The machine bed must be grounded. The equipment must be connected to the aspiration system - some types of adhesives, when heated, emit toxic substances that pose a threat to the health of the operating personnel.
Hand-fed edgebanding machines are not only used in artisan workshops. Large furniture factories have in their arsenal such equipment for the prompt repair of semi-finished products (edge delamination, chips, etc.), facing exclusive, curved workpieces, as well as small batches of parts that do not go through the main technological cycle. The presence of processors, controllers and process control systems in machines with manual workpiece feed makes them flexible and easy to prepare for work and control. Automatic control of temperature, length of facing material, feed rate - this is not a complete list of service functions that help the operator to focus on the main functional processes during work.
In the next publication, we will look at automated equipment for edge banding with mechanized workpiece feeding.
Andrey MOROZOV,
the company "MediaTechnology",
by order of the magazine "LesPromInform"
Characteristics of one of the hot melt adhesives (base - EVA copolymer)
Bonding: polyester materials, PVC, PP and ABS, unconsolidated impregnated paper, solid wood and veneer.
The density is about 1.4 g / cm 3.
Melt index according to DIN 53 735 (MFI 150 / 2.16): 50 ± 15 g / 10 min.
Softening point along the "ring and ball" DIN 1995: about 100 ± 5 ° C.
Glue processing temperature: 200-210 ° C.
Optimum moisture content of glued wood materials: 8-10%. Room temperature: not lower than 18 ° С in the absence of drafts.
The specialists of our company have vast experience in the repair and adjustment of edgebanding machines, so we can guarantee high quality repairs and short terms. As a rule, routine repair and adjustment of the machine takes one day, in severe cases, when it is necessary to order spare parts or repair defective electronics, the repair time may increase. Our experts will not only repair your equipment, but also advise on how to properly operate and maintain the machine in order to avoid future breakdowns.
If you and your customers are not satisfied with the quality of the glued edge, then our specialists will adjust all the units of the edge banding machine and train the operators to work on it.
The main reasons for the failure of edgebanding machines are:
- voltage drops in the network
- poor quality air preparation
- untimely lubrication of machine components
- large dustiness of the workshop
- negligence of operators to work on the machine.
Modern equipment has a large number of voltage-sensitive electronic components. As a result of drops, heating elements, controllers, inverters very often fail. In most cases, it is better to repair all electronics, since replacement is associated with a large investment and long delivery times.
With low-quality air (presence of water, lack of oil), pneumatic valves and pneumatic cylinders fail, as a result of which individual units begin to work poorly, which affects the quality of edge processing. Our specialists will check all pneumatics and eliminate any malfunctions.
It is very important to keep the machine clean as a lot of breakdowns are caused by dust. Very important - do not blow dust from electronic components, I use a vacuum cleaner to collect it.
One of the important units of the edge banding machine is the gluing unit. The glue tray and feed roller must be kept clean and free of carbon deposits at least once a year.
If your edgebander breaks down - call us and we will identify the malfunction as soon as possible and repair it.
The equipment should work, not stand idle for repair!
Edge cladding of furniture parts is an important step in furniture production. High-quality edges help protect the material, be it wood or plywood, from various negative influences, and also give it a beautiful and finished look.
Any normal furniture manufacturing business is required to have edgebanding equipment. For this, there is a special unit, which is called an edgebander.
If you have your own small production or you are just a lone craftsman making various wood products, then you do not have to waste your time and buy such a device. It is relatively easy to do it with your own hands, spending a little time and effort. A homemade edge banding machine will perform its task no worse than a factory unit, but it will cost the owner significantly less.
This device is widely used both in private workshops and on an industrial scale. As a working material for decorating wooden products, you can use:
Typical liner widths are approximately 2-5 centimeters, and thickness can vary from 0.4-3 millimeters.
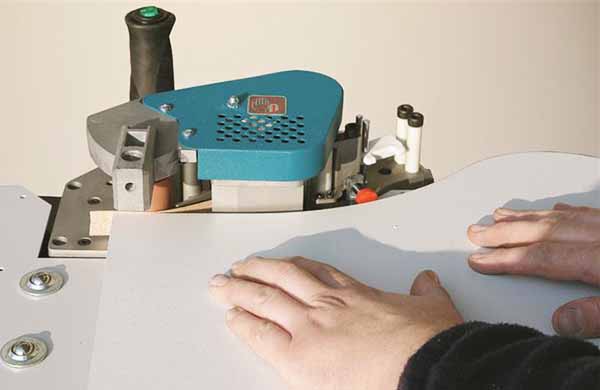
Next, the desired wooden part is brought to the device and a prepared tape is glued along its edge. It happens very simply - you just need to hold the apparatus along the tree, pressing it slightly.
Of course, if we are talking about making an edgebander with our own hands, then it is unlikely to be some advanced functions of a factory product, for example, heating the glue. Although it is quite easy to organize even this mechanism - it just takes a little more patience and time.
As for the varieties of the apparatus under consideration, the following options are distinguished:
- For working with curved edges. Usually, manual material feed is used here, since the master needs to adjust in time to the next bend on the part and it will definitely not work to rush for the automatic tape.
- For straight-line machining. Such products, as a rule, have an automatic feed. They are most often used in the mass production of furniture or other things made of wood.
In order to make a do-it-yourself edge trimmer successfully, you need to familiarize yourself with the typical design of such a unit.
The liner feeding system consists of a roll, a guillotine and special rollers. There is also a special store where the beginning of the tape is fed. It is pulled by rollers to the very part that needs to be processed, along the way, covered with a layer of suitable glue, heated to the desired temperature.
There are some types of cladding materials that come immediately with glue applied to them. In this case, it is enough to warm them up before use. If this is not the case, then the glue is contained separately in a special tray. Its temperature takes on typical values of 150-200 degrees Celsius.
The clamp between the wooden part and the cladding is performed by a special support roller, although there may be several of them. When making a homemade edgebander, you can completely get by with one such element, adding the necessary force with your physical strength.
Video: Homemade edgebanding machine.
Since the units in question are quite expensive on the market, many craftsmen are ready to spend some time making them with their own hands. In principle, this option will also be quite enough for normal operation, but here you will have to pay more attention to safety measures and use the device very carefully.
First, you need to get the necessary components. The standard package includes:
- Node for automatic trimming of cladding.
- Speed control unit The rotation of the rollers that feed the tape is good if it is equipped with a special indicator.
- A place for heating glue, some kind of thermostat.
- Adhesive tape supply unit.
- Guides that will help to properly fix the workpiece.
If you have stocked up with everything you need, then you can start assembling. Of course, nothing prevents you from slightly deviating from the accepted configuration and adding some additional unit of your own, which will help make the device more convenient and functional.
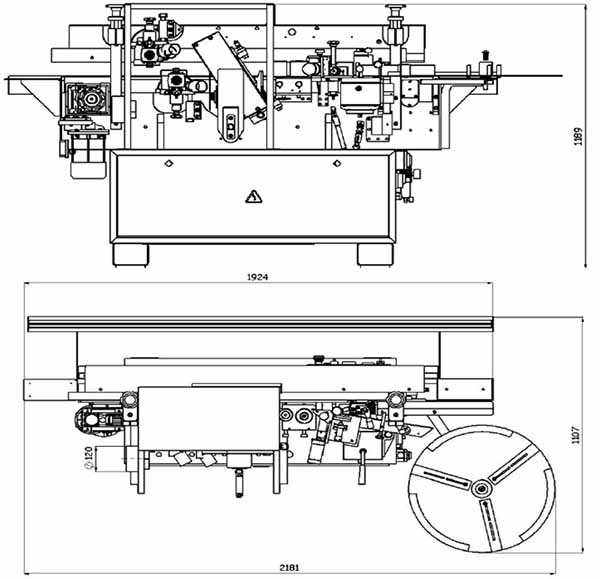
![]() |
Video (click to play). |
As a conclusion, it is worth noting that making an edgebander with his own hands will be within the power of any person who has experience with mechanisms, elementary electronics and tools. A little imagination - and you will get what you want.