In detail: do-it-yourself oki body repair from a real master for the site my.housecope.com.
Oka's car passed 150 thousand km in the most severe conditions. On a run of 140 tkm, the cage nut of the subframe was torn out - a washer was welded in at the service. After some time, it was discovered that the floor amplifier burst in half and began to “breathe”. The car stood for several months until hands reached it - the work is rather dreary - to replace the floor amplifier, you need to remove the entire power unit and disconnect the subframe.
Further, the photo shows the engine compartment of the car (the power unit is dismantled), the red arrow shows the place of the break of the body amplifier - it can be seen that the part has begun to move away from the engine shield panel. The salon has to be disassembled, otherwise everything will burn out during welding.
The new floor amplifier is shown below. Cage nuts and reinforcement plates are clearly visible.
Since the machine is noise and vibration insulated, this created some difficulties. I had to dismantle all the noise insulation from the floor area where the welding work was carried out. To dismantle the vibroplast, a thermal gun was used - only after warming up, the vibroplast can be peeled off.
Next on the photo is an old floor amplifier. It burst in half. A welded washer is visible (welded from below, without cutting the floor in the cabin). The second nut is in a deplorable state - cracks have appeared around it, it is not known how long it would have lasted.
After welding, we again glue the floor in the cabin with vibroplastic, put isolon and noise-insulating mats. The internal cavity of the amplifier is filled with anticorrosive material (Movil) through the technological holes.
Since the mileage is already quite large (150 tkm), the brakes and the steering rack have undergone a general revision. The rail was overhauled, the rail shaft was ground. After the repair, the steering turned out to be simply amazing.
The brake machines were also shaken up - they put new calipers, new brake discs, hoses. The hubs were replaced with new ones. The wheel bearings were also changed - the old ones went through a lot (only one bearing was changed) and although they did not hum, after opening they found that all the treadmills were covered with dents. New bearings were treated with XADO repair and restoration grease.
The new amplifier was welded on, having previously welded the reinforcing plates of the nuts.
![]() |
Video (click to play). |
Hello to all! As promised saw the 2nd part completely. In this post, the actions are already taking place in 2014. How long did I wait for the warming to get busy with the car, and now it has come.
I began my renovation with the continuation of cosmetic and welding works.
To begin with, I decided to make her evil eyes, so to speak, Bad boy hood) It turned out excellent metal took 1.5mm. Cut out a stencil from a sheet of iron and grinded on emery, then welded them to the hood.
The bottom of the doors is a little rotten, I had to cook.
I cut a corner out of the tin and tried it on.
I welded it to the door, everything turned out pretty neatly. Drops from welding grind off with a grinder. The same operation was performed with the other door, and he also welded all the holes on the rear firecracker except for the lock. Now there will be no rear wiper and OKA emblem too.
I cleaned all the mushrooms on the back.
Disassembly began. During the evening, my friend and I scattered it all.
Here is actually the best friend as an assistant)
After dismantling, putty began. I started with the wings. The first layer was an aluminum filler to build strength and the like. How I was tortured to rub it, but the result was worth it)
Here is the end result. The second layer was soft putty. This is where I finished with the wings.
Then he began to putty all the doors.
I was overwhelmed with the roof, but in 2 days it was ready)
Hood. The highlight of the car.I also filmed it, it took a day to work with it.
With the putty, it seems finished) We turn to the painting work. The car was washed with four hundred sandpaper, it was washed inside too, since the color will be different. Then there is the ground, unfortunately there is no photo of the car in the ground. The wash-out begins again, only not of the old paint, but of the soil. And finally, what I have been waiting for so long begins, painting)
The first photos after painting :) I was happy, but it was not me who painted it, but my stepfather. I got such a skill later when I painted a car for a friend) The color is called “Medeo 428” I wanted something unusual that would stand out among the gray mice.
And of course an autograph without it)
Further assembly of the car, unfortunately there is no photo either.
Fully assembled from the outside. New bumpers and every little thing. The salon is still empty. Photo at 2.5 megapixels) Sorry for the quality.
Covering the sidewalls. Dermantin got it from his grandmother in the closet, he put everything on staples and glue.
The finished version also wrapped around the torpedo and rear pieces.
The structure of the body frame and its sections are shown in Fig. 8-1, 8-2
Rice. 8-2. Main body sections (side view)
Damaged body straightening
A significant part of the repair work on cars, especially after road accidents, falls on the repair of bodies. In most cases, this requires checking the geometry of the attachment points, components and assemblies of the vehicle chassis. The main reference dimensions for checking the geometry are shown in Fig. 8-3.
Rice. 8-3. The main reference dimensions of the attachment points of the units: Χ, Υ, Ζ - αphase lines; О - four base holes with a diameter of 15 mm; 1 - lower radiator supports; 2 - upper support of the radiator; 3 - fastening of the power unit subframe; 4 - centers of the upper hinges of the struts; 5 - fastening the steering bracket; 6 - fastening the gear lever; 7 - fastening the parking brake lever bracket; 8 - fastening the bracket for the left arm of the rear suspension; 9 - center of attachment of the right arm of the rear suspension; 10 - centers of the upper supports of the rear suspension shock absorbers; 11 - centers of attachment of compression buffers
Damage to the car body can be very different. Therefore, the repair rules in each individual case should be different, the most suitable for these damages. However, there are general requirements as well. For example, it is necessary to maximize the ability to straighten damaged panels. It is advisable to avoid excessive thermal effects on the metal, so as not to interfere with the factory welding and anti-corrosion protection of the body. Body faceplates should only be removed in extreme cases to locate damage, straighten or align the body. In cases of significant damage to the body, it is recommended to remove all interior upholstery parts to facilitate the measurement, control and installation of hydraulic and screw jacks to eliminate distortion and damage. By editing, the original linear dimensions and locations of the power units, the dimensions of the openings of the wind window, hood, and tailgate are restored. The protrusion of front surfaces and removable parts relative to adjacent panels is eliminated by their fitting and adjustment.
Repair of deformed surfaces of parts
Repair of damaged body parts is carried out by drawing, straightening, straightening with metal shrinkage, cutting out sections (not amenable to repair), making repair inserts from rejected body parts or sheet metal, giving them the shape of a restored part.
The deformed places of the panels are straightened, as a rule, manually using a special tool (metal, plastic, wooden hammers, mandrels of various shapes) and fixtures.
Straightening with heat is used to settle (tighten) highly stretched surfaces. To prevent sudden swelling and deterioration of the mechanical properties, the panels are heated only to 600-650 ° C (cherry red).The diameter of the heated spot should be no more than 20-30 mm.
The contraction of the surfaces is carried out with a carbon electrode of a semiautomatic welding machine or a gas torch. The metal is heated from the periphery to the center of the defective area, upsetting the heated areas with blows of a wooden mallet or hammer using a flat support or anvil.
The heating and settling operations are repeated until the desired panel surface is obtained.
Irregularities in the panels are leveled with polyester fillers, thermoplastics, cold curing epoxy mastics or solder.
Polyester putties such as "Hempropol-P" or PE-0085 form reliable joints with panels cleaned to metal. These putties are two-component materials consisting of an unsaturated polyester resin and a hardener that catalyzes the quick hardening of the mixture. The temperature in the working room should not be lower than 18 ° C. The prepared putty must be used within 10 minutes. Final hardening - 60 minutes after application. The thickness of the putty layer should not exceed 2 mm.
Thermoplastic is available in powder form. Thermoplastic acquires the elastic properties required for application to the metal surface of the panel at a temperature of 150-160 ° C. The surface to be filled must be thoroughly cleaned of rust, scale, old paint and other contaminants. Thermoplastic adhesion is better on rough metal surfaces. To apply thermoplastic, the area to be leveled is heated to 170-180 ° C, after which the first layer of powder is applied, which is rolled with a metal roller. Then a second layer is applied and so on until the unevenness is filled. Each layer is rolled until a monolithic layer of plastic mass is obtained, and after hardening it can be processed using conventional methods.
Solders such as POSSu 18-2 or POSSu 25-2 are used to level areas previously filled with solder, as well as to build up the edges of parts and eliminate gaps.
In case of significant damage, the panels are replaced with new ones using gas-shielded electric welding.
Removal and installation of the front wing
To remove the wing, remove the socket with the direction indicator lamp. Remove the self-tapping screws securing the wing to the body: three screws 2 (Fig. 8-4) on the upper flange, one screw 1 at the bottom of the front of the wing and at the bottom of the rear, and one screw 3 for fastening to the front stack, which can be accessed through the gap between the strut and open door.
Rice. 8-4. Removing the front wing: 1, 2, 3 - points of attachment of the wing with screws
Carefully detach the fender and remove the insulating gaskets from where the fender contacts the mudguard.
Install the wing in reverse order. It is recommended to replace the insulating gaskets with new ones. Before the final tightening of the screws using the enlarged holes, adjust the wing for clearances and protrusion with other body elements.
After replacing the fender, pay attention to the condition of the anti-corrosion coating under the front fender. If necessary, restore the coating by applying D-11A plastisol or BPM-1 mastic.
So. I cook a wonderful Oka car. I want to ask who has already cooked it? I am interested in the Rear Panel, I live in the city. Orel and nowhere else can I find such a detail.
What is a ”tailgate” ?? Top, bottom, opening of the tailgate, the place of attachment of the beam. Misunderstanding, in more detail pliz (desirably with a photo).
- Posts: 217
- Location: Tomsk region
- Oka 11113
In Serpukhov, it seems. Article 1111-5601080
This page is searched for by queries: Oka body repair, Oka forum, Oka discussion.
- Our pets (photos) emo I'm not a man, don't follow me with your estrus
- Humor - Vladimir Vladimirovich, but what about those who will not live to retire?
- Humor - Here the other day Tony Robbins spoke, those who watched gave 30 thousand
- Humor I'm not against Putin being president.but why again Russia? Poo
- Humor Government meeting. Putin: - What a disgrace - a ruble oopya
- Humor -German Oskarovich, why do you think that mathematical schools are not needed
- On the GAZ-3309, with 4 gears, the check point knocks. When the gruzhonny is in general trouble. I am going home from Karachay-Cherkessk to Mordovia. I am going home from Cherkessk to Mordovia. I will be loaded with 4 tons. I'm afraid they will tear
- On the GAZ-3309, with 4 gears, the check point knocks. When the gruzhonny is in general trouble. Coming from Karachay-Cherkessk home to Mordovia
- On the GAZ-3309, with 4 gears, the check point knocks. When the gruzhonny is in general trouble. I am going from Karachay-Cherkessk home to Mordovia, these are guys for money, there are no questions, maybe there will be a varia along the way
- On the GAZ-3309, with 4 gears, the check point knocks. When the gruzhonny is in general trouble. I'm going from Karachay-Cherkessk home to Mordovia. Is there someone who can sell me 5 mortar for my lawnich snake?
- Smell in the car interior I use automatic air freshener sprays in my cars.
- The smell in the car interior After washing, I always treat my swallow with odorgon av
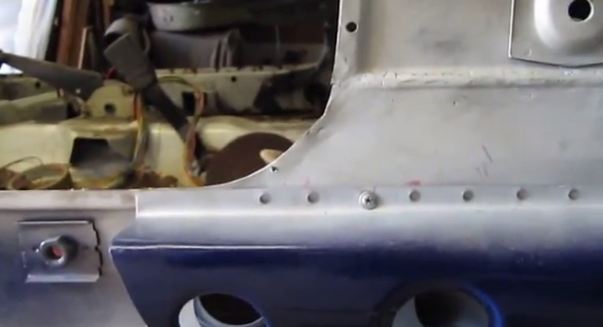
Preparation of the body for welding VAZ-11113 Oka. Internal sidewall repair.
The place where you will paint must be dry, draft-free, warm and free of dust.
Initially, you need to wash the body well. Before washing, it is advisable to remove all plastic parts from the body. This will eliminate the presence of moisture in crevices and gaps. It is best to wash the car with a strong water pressure.
Next, you need to inspect the car and find the right paint. In the case of a complete painting of a car, you can choose any paint similar to the previous one (shades are still not indicated in the data sheet). If the painting is partial, then you need to contact a special laboratory, where they can choose the required color.
Former students of technical universities, and now, as a rule, successful leading engineers, are well acquainted with the subject of "strength of materials". For many students, this subject was not a bastion that was not taken, followed, at best, by retaking the exam, at worst, expulsion from the university and replenishment of the ranks of the invincible Russian army. For those who have forgotten this subject a bit. Due to the fact that it was not useful in future labor activity or was not studied at all, since the chosen profile of the specialty did not require strong knowledge of this subject. Therefore, it is not a sin to remind. It will be about the ability of any material to withstand the external influence of any other bodies on it. Under the body, we will take the material in the form of the body of our car. Under “other bodies” we consider the Russian road with all its “charms”, as well as inertial forces and other side objects, including various bodies of oncoming and passing vehicles. Having considered the actions of all these factors and opposing forces in a single complex, the selection committee may have the right to give an assessment "unsatisfactory" to the designers of an automobile model that has not passed the necessary tests.
Why do you need to strengthen the body.
For the perception of the narrated material, we will give an illustrative example with a packaging cardboard box for household appliances, where the inner perimeter of the boxes has foam inserts. In the case of using physical force, twisting the box, we will be able to do this very easily. Having finished gluing the wings of such a box with tape, with a new physical impact it will wrinkle, but more physical effort will be required. Having inserted the longitudinal and transverse struts tightly abutting the sidewalls of the box, it will withstand many strong physical influences, even if it will be played with football instead of a ball. At the same time, it will maintain the integrity of its original design.
Returning to our cars, we are well aware that in the presence of the toughest car body, we will be faced with obtaining deformation of vulnerabilities.Perhaps it will be microscopic damage, but it will be. Another vivid example can be cited when a domestic car with five years of service experience is lifted to a certain height using a jack. Then we will make sure that in eighty percent of such cases, the doors will be jammed in the openings. This will indicate the deformation of the body. One of the main strength characteristics of an automobile body is its torsional rigidity. In the case when the body stiffness is insignificant, then the turns of the car will occur with some delay, due to a slowdown in the reaction of the car structure. The metal in the areas where the levers are attached will introduce a mismatch in the operation of the rear and front suspensions. Due to constant twisting, premature aging of the body occurs, welded seams diverge, and metal corrosion occurs intensively. If we consider cars only in this aspect, then the strongest in terms of body rigidity are three-door coupes and hatchbacks, which resist bending as much as possible. The worst indicators in this regard are station wagons and minivans.
Strengthening the car body depends on the specialization of the vehicle and the financial capabilities of the car owner. There are many options for this, ranging from the installation of stretch marks and spacers.
From all this abundance of various modifications, we choose: rods, kerchiefs, rear, lower, front spacers.
Front struts
A popular way to reinforce the body is with the front struts. The advantages of this design include ease of installation, reasonable price, increased rigidity in the front of the car, and finally, visual aesthetics. The use of such a mount depends on the purpose of the vehicle. Its advantages are obvious - ease of installation, low price, visual appeal and a fairly strong increase in the rigidity of the front of the car. This method of strengthening the body for VAZs of the "tenth" family is not suitable. Since on these modifications of the models not only the racks are "dancing", but the entire front shield is subject to deformation.
Spacers are offered by the trade in a wide range, but their main difference from each other is in the material from which they are made and the method of fastening. The gussets are usually used to strengthen wheel arches, stiffeners throughout the body and suspension struts. Such auto body reinforcement is usually used on sports car models.
Bottom struts
The lower struts have an effect on improving the car's handling, increasing stability, increasing the life of the body, but the installation itself is very laborious.
The rear struts have an effect on improving the maneuverability and stability of the vehicle. Installing and removing the rear struts is straightforward. The rear strut is also quite easy to install and dismantle.
There is the existence and application of folk methods of strengthening the body, when the holes of the side members and thresholds are filled with polyurethane foam. In terms of value, it is cheap. An advantage of this design is an increase in rigidity, a disadvantage is an increase in the activation of corrosion, the lack of ventilation. The risk of fire increases during welding. The choice is up to car owners.
3-09-2011, 06:30 | Zinchenko Vladimir Alexandrovich
There are a number of simple rules, the adherence to which allows you to maximize the resource of the automatic transmission.
Alexy59 »20 Mar 2014, 18:52
Homa »20 Mar 2014, 19:53
Hello Alexy!
This means that among the rotten people - Okovodov - replenishment!
I did not expect that there is something more rotten than my Akushka! And it looks like they drove it to the last?
In general, the sight of such devastation + repairs with foam and self-tapping screws causes cruel despondency.
I will say banality - without new spare parts, repairs will become more complicated.
What is your task in terms of repairs?
And what kind of piece of iron is on her doorstep?
Dear Alexy!
I have for you:
Two requests:
Complete your profile so we know where you are from.
If not difficult, go here viewtopic.php? F = 21 & t = 112
And one message:
Our strict but fair moderator is Yuri
even if you do something bad, do it well
Yuri »20 Mar 2014, 22:40
Alexy59 »21 Mar 2014, 10:24
mmlevin »21 Mar 2014, 11:05
Yuri »21 Mar 2014, 11:44
Alexy59 »21 Mar 2014, 11:56 am
started by repairing the left threshold. put a new threshold on top of the old one and circled around the contour, cut off with a grinder
it turned out to be an uncomfortable diagonal cut, and even with steps.
and here is a photo of the rear sidewall with lining
Alexy59 »21 Mar 2014, 12:02
Alexy59 »21 Mar 2014, 12:44
In the process of repairing the threshold, first it was necessary to cut out the old one, or rather its remnants, which go under the middle bottom. I simply cut the corner where the middle bottom meets the inner sidewall with a grinder, and then uprooted the remnants of the threshold connector. After that, he brought in a new sill connector, which he grabbed to the inner sidewall. At first I wanted to do it like an “adult”. drilled holes in the connector and tried to honestly weld through them to the inner sidewall. But it was not there. In some places there was a gap and the metal did not fit very tightly to the sidewall. In addition, the iron of the sidewall was corroded, although I cleaned it. Well, and most of all, these first welded points were my first ones and I had no experience yet. And it turned out not a beautiful welding ala an electric rivet, but some kind of garbage. and so then I just started to grab to the edge of the iron. Thus, today the rear of the sill connector is attached only to the inner sidewall and that is not so hot. then the truth on the other side of the inner threshold will be connected to the middle bottom. besides these compounds there are no more others. maybe Homa will tell you how it should be in that place CORRECT. I will be very grateful.
Here is a photo of that place, which I talked about during the fitting process.
Oka's car began to be produced a long time ago and has earned considerable popularity among domestic motorists. Of course, the technical characteristics of the car in question are far from the requirements of a modern motorist. Despite this, at one time Oka enjoyed great popularity due to its inherent economy. Owners of an Oka car of the early years of production often encounter malfunctions of the engine system. This is easily explained by the service life and operating conditions of the vehicle. One of the most effective ways to return the vehicle to work is to overhaul the Oka or VAZ 11113 engine. It is quite difficult to carry out repairs yourself, since many processes will require expensive equipment. In order to save money, you can prepare the Oka for a major overhaul with your own hands.
The benefits of the overhaul are clear. Large-scale repair of the engine will allow: to increase the service life of the vehicle, to increase the resource of the engine and to increase its performance.
The first stage of the overhaul is a detailed diagnosis of the internal combustion engine. It is quite difficult to carry out a check in a garage. In order to determine the productivity of an engine, you will need computer equipment and related skills.
To perform a complete restoration of the engine, it is necessary to dismantle the vehicle device. It is not so easy to carry out this procedure with your own hands, despite the small dimensions of the motor. To avoid damage to the engine, it is necessary to use a number of specialized equipment: support frames, hydraulic puller, engine hanging device.
After the engine has been successfully dismantled, it is necessary to start disassembling it. It is necessary to disassemble the engine strictly in a certain order in order to prevent damage to its individual parts.
After disassembly, it is necessary to proceed to the most important stage of the overhaul, which consists in troubleshooting individual components of the internal combustion engine. The main purpose of the overhaul is to restore the original parameters of the vehicle elements. Therefore, the only correct manual for repairing the Oka is the original instructions of the manufacturer.
In the course of a large-scale restoration of the VAZ 11113 engine, the following procedures are mandatory:
- Restoring the parameters of the cylinder block VAZ 11113.
- Repair of crankshaft and camshaft inlets.
- Restoration of the bearing part of the crankshaft.
- Processing the head of the VAZ 11113 cylinder block.
- Restoring the tightness of the unit by welding.
- Correction of the connecting rod geometry.
- Replacement of all consumables and rubber seals.
Large-scale car repair requires appropriate skills and expensive equipment. Therefore, in order to perform the restoration, you will have to turn to professionals.
One of the most important stages of engine restoration is cylinder head processing. The vehicle manufacturer specifies the permissible head processing limit, which must be strictly adhered to when carrying out repairs. Before proceeding with a large-scale repair, it is necessary to study in detail the accompanying instructions of the manufacturer's plant. Also, it is imperative to check with the master to what depth the cylinder head will be processed. If the element is worn out above the permissible limit, further operation of the block head is prohibited. If processing and restoration of the cylinder head is possible, the work is accompanied by the obligatory replacement of the cylinder head gasket. In this case, it is also necessary to take into account the processing depth of the element in order to give the block its original tightness.
To restore the VAZ 11113 internal combustion engine to the factory parameters, it is recommended to use the services of proven workshops. Overhaul is a rather complicated and time-consuming procedure that must be carried out by qualified craftsmen. Before carrying out repairs, it is necessary to assess the cost of the restoration soundly. Some car enthusiasts forget to appreciate the difference between restoring an element and replacing it. With critical engine wear, repair costs may well exceed the primary cost of the internal combustion engine. If it is necessary to replace individual elements of the vehicle, it is worth using only original spare parts from the manufacturer.
After carrying out the repairs, it is worth starting to break in the car. During the running-in period, it is necessary to prevent an increased load on the propulsion system. Otherwise, the costs of restoring the engine will not pay off and the VAZ 11113 vehicle will again lose its performance.
Successful restoration of the VAZ 11113 car!
Oka Vaz 11113 is a small-sized Russian hatchback, the production of which began in 1988 and ended quite recently, in 2008. The car was initially produced at the Volga AvtoVAZ plant, after which production was transferred to the SeAZ and ZMA plants.
The very first Oka was the cheapest Russian car, which included a 29 horsepower engine with a volume of 0.6 liters.
After that, an improved version of the Oka 11113 appeared, with a two-cylinder engine with a volume of 0.7 liters and a power of 33 horsepower. The car came with a 4-speed gearbox. But you can make something worthwhile out of such a car if you make OKA tuning.
The maximum speed that a car can reach is 140 km / h. Further, the car was modernized by a Chinese concern, with a 1-liter engine and a power of 53 horsepower, the car brand began to be called Seaz11116, the equipment was equipped with a 5-speed mechanics.
The maximum speed that the car could develop was 150 km / h.The car has a spare wheel on the rear door, "kenguryatnik", tubular sills, looking at such attributes, we can say that Oka's car is a real compact SUV.
The OKA jeep all-terrain vehicle is designed for off-road driving. The car borrowed many parts to increase its cross-country ability, the car body, lighting equipment, seat and interior upholstery remained from the native parts.
The front panel is borrowed from the figure eight, and the armrest and stove are from the five. Kengurin from the Ssang Young Musso model, which is very necessary for off-road conditions. The car demonstrates ease of movement, maneuverability on the road and good cross-country ability.
Under the hood of the car there is an injector and an engine from the well-known company Rover Mini, with a volume of 1.3 liters, with a capacity of 63 horsepower. To show the capabilities of a machine, you cannot stand still and discuss details. You need to feel the car and start moving.
The performance indicators of the Oka model are well demonstrated by the 14-inch wheels, which added significant weight to the car, and thus the car became even more like a jeep. To increase the cross-country ability of the car, the chassis and suspension were borrowed from the front-wheel drive VAZ.
Further video about tuning OKA Lambo:
Many car enthusiasts like to ride on spread wheels, so VAZ 11113 Oka tuning widens the car's track by 150 mm, increases the arches for installing larger wheels. Over the arches, you can install plastic overlays that will decorate the appearance of the car and create individuality.
Tuning Oka can be done indefinitely, it all depends, as a rule, on the owner's imagination. Oka's external tuning is considered one of the most important and noticeable elements of car modernization. It has become fashionable to do tuning of aerodynamic body kits, which can also change the look of the car and improve its technical characteristics.
If, slightly raise the car body, you will immediately feel the glance past the passing envious people. Install good bumpers in place of the plastic ones, push them out and make the trim with overlays, so you will noticeably expand the car body, and the Oka itself will look even more powerful.
Install the steering shaft from a figure eight, with a modified driver's position, so you get the long-awaited comfort. And here is the long-awaited Oka tuning photo, with the listed upgrades.
The first impression of the interior may seem scarce and insufficient for such a powerful car. Oka's interior tuning includes interior firmware, modern upholstery with high-quality material, installation of glass electric lifters and high-quality vibration and noise insulation. Head units, midbass, amplifiers and a subwoofer are being updated.
The dashboard is also equipped with noise isolation, and the electric lifters can move the windows at the touch of a button. The pedals are equipped with aluminum pads, which are often found in sports cars. A loud rectangular muffler can emphasize the spirit of sport.
The car has a low degree of passive safety, so this feature needs to be urgently corrected. For the safety of passengers and the driver, install a crash panel and additional airbags. Plus, you can install disc brakes and dynamic stabilization system.
Sometimes, as Oka tuning, motorists purchase starting-chargers. Such devices are necessary on the road when the battery is accidentally low. In addition, interesting multicolor airbrushing and painting with vinyl decoration will be able to decorate the car.
Here, give free rein to a professional artist, and he will create a "car" that will amaze and stun everyone on the road. The most popular fantasy-style body murals, gloomy castles, unexplored planets, stars, or the sky.
Many people think that if the car is small, there is no point in tuning the Oka for a jeep.It really consumes little gasoline, however, all the factory parameters of the propulsion system were not ideally provided, therefore, it is necessary to refine some of the characteristics.
To increase the power of the car, you need to do the tuning of the engine. The modernization begins with replacing all major components, namely the air filter, camshaft, carburetor and cylinder head.
The exhaust and fuel intake system will also have to be replaced, while the cylinder engine changes to a Rover engine, which has a volume of 1.3 liters. With such an engine, the car accelerates evenly.
If a gas unit is installed in the car, it can also imply the installation of a camshaft, with a lift level of 10.3 mm, and with significantly increased compression ratios. When the engine of the gas unit is forcing, the power increases accordingly and the traction at the bottom improves.
Now it is very popular to carry out chip tuning of the engine in cars, which significantly affects the increase in engine efficiency. This modernization method differs from others in that there is a software change in the motor control unit.
The program can be adjusted taking into account the concealment of reserves and other characteristics. This method is considered to be the simplest and most powerful. In the event that the car stops working, you can return the original engine characteristics back.
Chip tuning is able to reduce fuel consumption, reduce the emission of fuel into the atmosphere with harmful toxic substances. Chip tuning is now applicable to most Russian cars, including the famous VAZ 2106.
Be sure to make Oka tuning, it is necessary to replace the camshaft, pusher and grind the manifold. The grinding procedure means fitting the manifold channels to the head channels. Pushers of a special profile, with a lightweight valve and a new camshaft can significantly increase the power of the Oka engine.
For the new engine, it will be important to install a high-quality air filter, thereby allowing wheel speed up to 7000 rpm, and aggressive notes of the engine will be felt on the road.
To reduce fuel loss at high speeds, the exhaust and intake ports are being finalized, the valve seats and the shape of the combustion chamber are changed. This type of tuning is considered one of the most expensive, since the master does all the work by hand.
For a compact car, the increase in power will be a compelling argument. By installing the main pair with a good gear ratio, you can increase the maximum speed of the Oka, and also improve the acceleration characteristics, which even the driver himself can appreciate. The reserve of traction will be felt while driving, it will add confidence and agility on the road.
In the process of tuning the engine, you can get the following results:
- the maximum engine speed will increase from 119 to 127 km / h;
- acceleration time to 100 km / h will increase from 36 to 25 seconds.
Surely everyone is tormented by the question: "How to make Oka tuning with your own hands?" Since the car is considered the cheapest and most economical, it is possible to emphasize the following advantages: the car consumes only 3-4 liters of fuel per 100 kilometers, but at the same time it loses its dynamics.
Let's try to improve the technical part of such a powerful unit, for this it is necessary:
- any repairs to begin with the purchase of the necessary material;
- buy all tools, devices and devices from an authorized dealer in order to avoid possible counterfeiting;
- choose only high-quality materials, metallic.
Next, we turn to the purchase of equipment: a gas shock absorber, mirrors that match the body color, luxurious upholstery with armrests, a towbar, a cigarette lighter with an ashtray, noise insulation material, an engine protection device, an anti-corrosion treatment device, lockers (fenders), inertial seat belts ...
Additionally, you can purchase a new dashboard with a clock, tachometer and a special place for a radio. Looking at the car, you can see how the designers bent the cables of the car, thereby reducing its longevity.
You can see how one cable presses the filler pipe of the gas tank, which adversely affects the propulsion system, so some redevelopment is required. Then we move on to adjusting the carburetor, tensioning belts and replacing the heating tap.
Let's start by changing the look with changing wheels, the purchased kit should consist of light alloy wheels and tires of the required diameter, usually from 14 to 16 inches. The first impression that you will get is how much the sensation of movement has changed, there is a softness of the stroke along the bumps.
To replace the torpedo, you can use the console from the "Niva", for this you need to cut off the lower part of the device, fix it on four self-tapping screws for the heater and the lower part of the torpedo.
You can install a radio tape recorder in the torpedo, and mount speakers on the lower front of the door. The rest of the speakers must be installed in the luggage compartment niche. If all the work is done correctly, you can get quality music.
In the dashboard, you can also install buttons for controlling the head light, rear and front fog lamps, an emergency light button, a heating button for the rear window and rear wiper, and a fan switch.
Where the cigarette lighter is located, you can also install a door ashtray. Don't forget to install a glove compartment, which you can buy at any car dealership.
A special Oka tuning photo with your own hands will help to make the modernization of the car yourself, which shows where all the devices should be located. The photo can be used as a guide or as a diagram of the occupancy of the salon.
To improve the quality of interior lighting, you can embed two lamps of the required color into the rear of the door trim, another lamp can be installed in the lower part of the dash above the glove compartment. It will not be superfluous to install a lamp in the luggage compartment.
Next is a video with a do-it-yourself Oka tuning option:
VAZ 1111, better known as Oka, due to its compact size and simple design, has become the subject of ridicule. Meanwhile, this car heralded the era of frugal, compact cars. Today, almost every global automotive brand develops its own "baby", so a serious competition has unfolded in the class of compact cars. The domestic auto industry, along with the Italian one, can be considered a pioneer in the development of the production of compact cars. Another question is that the VAZ 1111 has not received sufficient development in the form of the development of restyling and new generations. But Oka provides fans with their own car tuning and ample opportunities for modernization.
There are many options for transformation, restyling of the VAZ 1111:
- SUV
- Rally car
- Retro car - design concepts of the late 60s and early 70s of the XX century are due to the angularity of the body shapes, the use of bright colors in the design
- Cabriolet
- Roadster
The simplest and most affordable is tuning of the Oka for off-road, since the car looks similar to this class of cars. To enhance this effect, it is enough to lift the suspension, install discs with a larger diameter and rubber with a powerful tread. But tuning the Oka for a jeep is not limited only to the above changes, they can be considered only the first stage in creating an exclusive baby all-terrain vehicle.
Oka's external tuning can be styled to resemble the popular Grand Cherokee SUV model. This is facilitated by the similarity of the headlights and grille. In both cars, they are oblong, rectangular in shape. It is enough to install a body kit, wheels with a large diameter and a tractor rubber tread, as well as to give an appropriate configuration to the hood and the nondescript OKA will turn into a miniature clone of the SUV popular in the 90s.
Tuning Oka cars with your own hands is quite easy to do.This is due to the simplicity of the technical device of the car and the unassuming appearance, which, on the one hand, makes modernization simple and cheap, and on the other hand, it allows all kinds of experiments to be carried out on the car.
From all of the above, we can conclude that tuning the VAZ 1111 is the best school for a beginner and a kind of creative studio for an experienced craftsman.
The process of improving engine performance can be conditionally divided into 2 directions:
- A radical change in characteristics - a complete replacement of the motor
- Improvement of the standard power unit
In the first case, the ideal option would be a Rover Mini injection engine with a volume of 1.3 liters. The advantage of this type of tuning is a significant increase in technical indicators, the disadvantages will be the high cost of implementation and the need to recycle most of the car systems for a new engine. It is expensive and time consuming.
The second option is the modernization of the standard power unit, which is cheaper and simpler, but it will not allow obtaining such an increase in power as in the first case.
Do-it-yourself tuning of the Oka engine must start with the carburetor. The first step is to increase the diameter of the throttle valve to 52–54 cm. This will allow the engine to receive more air, which will facilitate its operation, increase performance and increase the service life. You can immediately install a tuning modification of the carburetor.
Installing a new camshaft allows you to increase the revs to 7000 units. In this case, it is imperative to tighten the engine power, which is done using the following operations:
- Replacing standard valves with lightweight
- Valve seat modernization
- Modification of the inlet and outlet ports of the valves
- Valve sealing
- Installing bronze guides
- Changing the shape of the combustion chambers
Additionally, it is necessary to replace the intake and exhaust manifolds with sports modifications, as well as the air filter for the K&N model with zero resistance. This set of measures will significantly improve the technical characteristics of the engine and optimize its operation, that is, the power loss will be minimal.
The muffler cap can be used to give the engine a sporty growl. Backlit models will create the effect of a flame bursting from a jet nozzle.
Improving the driving characteristics of the VAZ 1111 is the primary task of the owner, since in the basic version of the suspension they are useless and cause a lot of complaints. To remedy the situation, it is necessary to install gas-oil shock absorbers. This is enough to give the vehicle stability and improve its handling.
Experts do not recommend changing the standard springs to advanced modifications, since the latter quickly fail.
If it is planned to make an SUV from the Oka, then it is necessary to lift the suspension. This can be done with a dedicated kit or by adding spring spacers. The result is a kicked-up rear of the car. But at the same time, you will have to modify the shock absorber mountings. Actually, this is all that is needed to improve the VAZ 1111 suspension with your own hands.
There are more than enough options for modernization:
- Complete replacement of the interior trim. For this, they use their own materials or buy a special set. You can try the author's technique for processing the interior, for example, finalizing the standard trim
- Partial decoration - installation of curly inserts and elements in the trim
- Refinement of standard armchairs - installation of comfortable headrests; purchase or manufacture of stylish covers. At the same time, the general design concept of interior processing in terms of color matching should be taken into account.
- Replacement of regular seats for sports or executive class chairs
- Installing a new steering wheel
- Fitting Stylish Pedal Pads
- Installation of additional equipment: automatic drive of glass and side mirrors
- The roof can be made panoramic or a hatch can be cut
These are far from all the options that can be implemented by doing the tuning of the Oka salon with your own hands. In fact, there are no dogmas and prohibitions here, it all depends on the imagination of the master. This is a great option for creative experiments, the invention of author's decoration techniques.
Tuning the Oka torpedo is associated with the difficulty - the compact dimensions of the car. In this regard, it is unlikely that it will be possible to install a torpedo from other models. Or you will have to look for suitable sizes for a long time. Here the best helpers will be imagination and improvised means.
You can resort to the standard, proven option - to cover the torpedo with leather or carbon film. If you want to create an exclusive, then mounting foam, epoxy resin, a grinding tool will help with this. With their help, you can change the design of the torpedo as you like. It is also a good method for redesigning the dashboard bore.
Tuning the Oka panel with your own hands also provides 2 options:
- Factory panel upgrade
- Installing a new panel from other car models
The first option involves replacing standard backlight lamps with LED ones. Installing a new backing or revision of the standard one will create a non-standard look. A complete replacement of the instrument panel will require revision of the torpedo.
Do not forget about high-quality sealing, a new or modified torpedo should not emit squeaks. This requirement can be considered an integral part of tuning.
Standard bumpers VAZ 1111 do not lend themselves well to modernization, since they have a limited tuning resource. The reason is the small surface area, where fog lights and a place for a license plate are located close to each other. But if you wish, you can also swing the regular bumpers. This is done using polyurethane foam, epoxy and a sander. For example, you can enlarge the bumper at the bottom by adding diffusers like rally cars. But this technology is impractical and time consuming.
The main difficulty in modernizing a standard bumper is to create a symmetrical surface and clear lines. Also, a certain difficulty can be caused by the development of design. In order not to suffer for a long time, it is worth taking some advanced example of a sports bumper as a basis.
Do-it-yourself optimal bumper tuning for Oka - replacing native samples with advanced modifications. It's simple and fast. The only difficulty will be the installation of the rear bumper. The reason for the difficulties is the hitch.
It should be remembered that voluminous bumpers visually increase the size of the body. The effect can be increased by pushing the bumpers forward.
Oka optics tuning is one of the important elements affecting the appearance of the car. An effective method of transforming headlights is to install overlays. You can buy them or make them yourself. Before you need to install LED bulbs and polish the headlights. There is a possibility of complete replacement of optical devices. To install an advanced model, bodywork will be required.
What other techniques can be used to change the appearance of headlights:
- Headlamp rim redesign - high-gloss chrome finish
- Refinement of the headlight substrate
- Decoration with LED strips, most often they resemble eyelashes, but you can place them at the bottom and give the car an aggressive look
![]() |
Video (click to play). |
Tuning of the taillights of the Oka is carried out mainly through the installation of overlays. At the same time, it is worth remembering that they should not harm safety - the lights remain clearly visible in any case.