In detail: do-it-yourself oka body repair from a real master for the site my.housecope.com.
Oka's car passed 150 thousand kilometers in the most severe conditions. On a run of 140 tkm, the subframe fastening nut was torn out - a washer was welded in at the service. After some time, they discovered that the floor reinforcement burst in half and began to “breathe”. The car stood for several months, until her hands reached her - the work is rather dreary - to replace the floor amplifier, you need to remove the entire power unit and disconnect the subframe.
Further, the photo shows the engine compartment of the car (the power unit was dismantled), the red arrow shows the place where the body amplifier was broken - it can be seen that the part began to move away from the engine shield panel. The salon has to be disassembled, otherwise everything will burn out during welding.
The new floor reinforcement is shown below. Cage nuts and reinforcing plates are clearly visible.
Since the machine is noise and vibration isolated, this created some difficulties. I had to dismantle all the sound insulation from the floor area where the welding work was carried out. To dismantle the vibroplast, a thermal gun was used - only after warming up the vibroplast can be peeled off.
Next in the photo is the old floor amplifier. It cracked in half. A welded washer is visible (welded from below, without cutting the floor in the cabin). The second nut is in a deplorable state - cracks appeared around it, it is not known how long it would have lasted.
After welding, we again glue the floor in the cabin with vibroplast, put isolon and noise-insulating mats. We fill the internal cavity of the amplifier with anticorrosive (movil) through technological holes.
Since the mileage is already quite large (150 tkm), the brakes and the steering rack have undergone a general revision. The rail was overhauled, the rail shaft was polished. After the repair, the steering turned out just amazing.
Brake machines also shook up - put new calipers, new brake discs, hoses. The hubs were replaced with new ones. The wheel bearings were also changed - the old ones went through a lot (only one bearing changed) and although they did not buzz, after opening they found that all the treadmills were covered with dents. New bearings were treated with XADO repair and restoration grease.
The new amplifier was welded, having previously welded the reinforcing plates of the nuts.
![]() |
Video (click to play). |
Hello to all! As promised, I'm posting Part 2 in full. In this post, the actions are already taking place in 2014. How long have I been waiting for warming, that would take the car, and now it has come.
I began my repair with the continuation of cosmetic and welding work.
To begin with, I decided to make her evil eyes, so to speak Bad boy hood) It turned out great metal took 1.5mm. Stenciled out of a sheet of iron and turned on emery, then welded them to the hood.
The bottom of the door is a little rotten, I had to cook.
I cut a corner out of a tin and tried it on.
I welded it to the door, everything turned out pretty neat. Drops from welding grind grinder. The same operation was carried out with the other door, and all the holes on the rear cracker except for the lock were also welded. Now there will be no rear wiper and the OKA emblem too.
Cleaned up all the mushrooms on the body.
Disassembly has begun. During the evening, my friend and I scattered it all.
Here is actually the best friend as an assistant)
After disassembly, puttying began. Started with wings. The first layer was aluminum putty to create a fortress, etc. How I was tortured to rub it, but the result was worth it)
Here is the end result. The second layer was soft putty. This is where I finished with the wings.
Then he began to putty all the doors.
I ended up with the roof, but it was ready in 2 days)
Hood. The highlight of the car.I also filmed it, it took a day to work with it.
With putty like finished) Let's move on to paint work. The washing of the car with four hundredth sandpaper began, I also washed it inside, since the color would be different. Next is the ground, unfortunately there is no photo of the car in the ground. Washing begins again, only not the old paint, but the soil. And finally begins what I've been waiting for so long, painting)
The first photos after painting :) I was happy, but it was not me who painted, but my stepfather. I got such a skill later when I painted a car for a friend) The color is called “Medeo 428” I wanted something unusual that would stand out among the gray mice.
And of course the autograph as without it)
Further assembly of the car, unfortunately there is no photo either.
Completely assembled from the outside. New bumpers and every little thing. The salon is still empty. Fotkal at 2.5 megapiskel) Sorry for the quality.
Side lining. Dermantin got from my grandmother in the closet, put everything on staples and glue.
The finished version also covered the torpedo and rear pieces.
The structure of the body frame and its sections are shown in Fig. 8-1, 8-2
Rice. 8-2. Main sections of the body (side view)
Repairing a damaged body
A significant part of the repair work on cars, especially after traffic accidents, falls on the repair of bodies. In most cases, this requires checking the geometry of the attachment points, components and assemblies of the vehicle chassis. The main reference dimensions for checking the geometry are shown in fig. 8-3.
Rice. 8-3. The main reference dimensions of the attachment points of the units: Χ, Υ, Ζ - α basic lines; O - four base holes with a diameter of 15 mm; 1 - lower radiator supports; 2 – the top support of a radiator; 3 - fastenings of the subframe of the power unit; 4 - centers of the upper hinges of the racks; 5 – fastenings of an arm of a steering; 6 – fastenings of the lever of a gear change; 7 – fastenings of an arm of the lever of a parking brake; 8 - fastening the bracket of the left arm of the rear suspension; 9 – the center of fastening of the right arm of a back suspension bracket; 10 - the centers of the upper supports of the rear suspension shock absorbers; 11 - centers of attachment of compression buffers
Damage to the car body can be very different. Therefore, the repair rules in each individual case should be their own, most suitable for these damages. However, there are also general requirements. For example, it is necessary to use the possibilities of straightening damaged panels to the maximum. It is desirable to avoid excessive thermal impact on the metal, so as not to disturb the factory welding and anti-corrosion protection of the body. The front panels of the body can only be removed in extreme cases to determine the location of damage, straighten or align the body. In cases of significant damage to the body, it is recommended to remove all interior upholstery parts in order to facilitate the measurement, control and installation of hydraulic and screw jacks to eliminate distortions and damage. Editing restores the original linear dimensions and locations of the power units, the dimensions of the openings of the wind window, hood, tailgate. The protrusion of the front surfaces and removable parts relative to adjacent panels is eliminated by their fitting and adjustment.
Repair of deformed surfaces of parts
Repair of damaged body parts is carried out by drawing, straightening, straightening with metal shrinkage, cutting out sections (not repairable), manufacturing repair inserts from rejected body parts or sheet metal, giving them the shape of a restored part.
The deformed places of the panels are straightened, as a rule, manually using a special tool (metal, plastic, wooden hammers, mandrels of various shapes) and fixtures.
Editing with heating is used for upsetting (pulling) highly stretched surfaces. To prevent sudden swelling and deterioration of the mechanical properties, the panels are only heated to 600-650°C (cherry red color).The diameter of the heated spot should be no more than 20-30 mm.
The surfaces are tightened with a carbon electrode of a semi-automatic welding machine or a gas burner. The metal is heated from the periphery to the center of the defective area, upsetting the heated places with blows of a wooden mallet or hammer using a flat support or anvil.
The heating and upsetting operations are repeated until the desired panel surface is obtained.
Irregularities on the panels are leveled with polyester putties, thermoplastics, cold curing epoxy putties or solder.
Polyester fillers of the Chempropol-P or PE-0085 type form reliable joints with panels cleaned to metal. These putties are two-component materials consisting of an unsaturated polyester resin and a hardener, which catalyzes the rapid curing of the mixture. The temperature in the working room should not be below 18°C. The prepared putty must be used within 10 minutes. Final hardening - 60 minutes after application. The thickness of the putty layer should not exceed 2 mm.
The thermoplastic is available in powder form. The elastic properties necessary for application to the metal surface of the panel, thermoplastic acquires at a temperature of 150-160°C. The surface to be filled must be thoroughly cleaned of rust, scale, old paint and other contaminants. Thermoplastic adhesion is better to rough metal surfaces. To apply thermoplastic, the area to be leveled is heated to 170-180°C, after which the first layer of powder is applied, which is rolled with a metal roller. Then a second layer is applied and so on until the roughness is filled. Each layer is rolled to form a monolithic layer of plastic mass, and after hardening it can be processed by conventional methods.
Solders such as POSSu 18-2 or POSSu 25-2 are used for leveling areas previously filled with solder, as well as building up the edges of parts and eliminating gaps.
In case of significant damage, the panels are replaced with new ones using electric welding in a protective gas environment.
Removal and installation of a forward wing
To remove the wing, remove the cartridge with the turn signal lamp. Unscrew the self-tapping screws securing the wing to the body: three screws 2 (Fig. 8-4) on the upper flange, one screw 1 each at the bottom in front of the wing and at the bottom rear and one screw 3 for attaching to the front stack, which can be accessed through the gap between the pillar and open door.
Rice. 8-4. Removing the front wing: 1, 2, 3 - wing attachment points with screws
Carefully detach the wing and remove the insulating gaskets from the places where the wing contacts the mudguard.
Install the wing in reverse order. It is recommended to replace the insulating gaskets with new ones. Before finally tightening the screws, use the enlarged holes to match the gaps and protrusions of the fender with other body parts.
After replacing the fender, pay attention to the condition of the anti-corrosion coating under the front fender. If necessary, restore the coating by applying D-11A plastisol or BPM-1 mastic.
So. I cook a wonderful car Oka. I want to ask, maybe someone already cooked? exactly interested in the Back Panel, I live vg. Orla, and I can’t find such a detail anywhere.
What is a "rear panel" ?? Top, bottom, tailgate opening, beam attachment point. Neponyatka, more details pliz (please with a photo).
- Posts: 217
- Location: Tomsk region
- Oka 11113
In Serpukhov there is, sort of. Article 1111-5601080
This page is searched for by queries: Oka body repair, Oka forum, Oka discussion.
- Our pets (photo) emo I'm not a man, don't follow me with your heat
- Humor - Vladimir Vladimirovich, but what about those who will not live to see retirement?
- Humor - Here the other day Tony Robbins performed, those who watched gave 30 thousand each
- Humor I'm not opposed to Putin being president.but why Russia again? Pu
- Humor Meeting of the government. Putin: - What a disgrace - the ruble again
- Humor - German Oskarovich, why do you think that mathematical schools are not needed
- On the GAZ-3309, with 4 gears, the knock of the gearbox. When the cargo is generally a disaster. I'm going home from Karachay-Cherkessk to Mordovia I'm going home from Cherkessk to Mordovia. I'll be loaded with 4 tons. I'm afraid they will tear
- On the GAZ-3309, with 4 gears, the knock of the gearbox. When the cargo is generally a disaster. I'm going from Karachay-Cherkessk home to Mordovia
- On the GAZ-3309, with 4 gears, the knock of the gearbox. When the cargo is generally a disaster. I’m going from Karachay-Cherkessk home to Mordovia, these guys don’t have any questions for money, maybe there will be a varia along the way
- On the GAZ-3309, with 4 gears, the knock of the gearbox. When the cargo is generally a disaster. I'm going home from Karachay-Cherkessk to Mordovia Is there anyone who can sell me a 5 mortar bu for my lawn snake?
- The smell in the car interior I use automatic air freshener sprayers in my cars
- The smell in the car interior After washing, I always treat my swallow with odorgon av
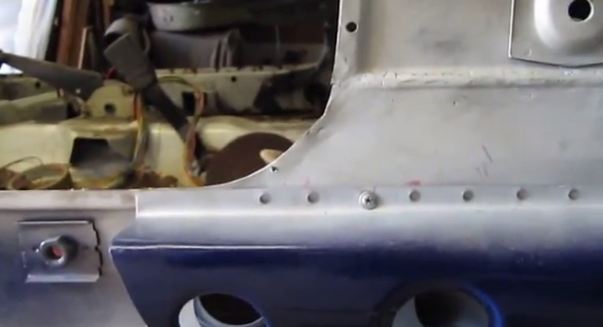
Preparing the body for welding VAZ-11113 Oka. Repair of the inner side.
The place where you will paint should be dry, draft-free, warm and dust-free.
First you need to wash the body well. Before washing, it is advisable to remove all plastic parts from the body. This eliminates the presence of moisture in cracks and gaps. It is best to wash the car with strong water pressure.
Next, you need to inspect the car and choose the right paint. In the case of a complete painting of a car, you can choose any paint similar to the previous one (the shades are not indicated in the data sheet anyway). If the painting is partial, then you need to contact a special laboratory where they can choose the desired color.
Former students of technical universities, and now, as a rule, successful leading engineers, are well acquainted with the subject of “sopromat”. The mentioned subject for many students was not taken bastion, which was followed, at best, by retaking the exam, at worst, expulsion from the university and replenishment of the ranks of the invincible Russian army. For those who forgot about this subject. Due to the fact that it was not useful in future work or was not studied at all, since the chosen profile of the specialty did not require strong knowledge in this subject. Therefore, it is not a sin to remind. We will talk about the ability of any material to resist the external influence of any other bodies on it. Under the body, we will take the material in the form of the body of our car. Under "other bodies" we consider the Russian road with all its "charms", as well as inertial forces and other secondary objects, including various bodies of oncoming and passing cars. Having considered the action of all these factors and opposing forces in a single complex, the selection committee may have the right to give an “unsatisfactory” rating to the designers of an automobile model that did not pass the necessary tests.
Why do you need to strengthen the body.
For the perception of the narrated material, let's give a clear example of a packaging cardboard box from under household appliances, where the inner perimeter of the boxes has foam inserts. In the case of applying physical impact, twisting the box, we can do this very easily. Having completed gluing the wings of such a box with adhesive tape, with a new physical impact it will wrinkle, but more physical effort will be required. By embedding longitudinal and transverse struts tightly resting on the sides of the box, it will withstand many strong physical impacts, even if they play football with it instead of the ball. At the same time, it will retain the integrity of its original design.
Returning to our cars, we are well aware that in the presence of the most rigid car body, we will be faced with getting the deformation of vulnerabilities.Perhaps it will be microscopic damage, but they will be. One more vivid example can be given when we raise a domestic car with a five-year operating experience with a jack to a certain height. Then we will make sure that in eighty percent of such cases the doors will be wedged in the openings. This will talk about the deformation of the body. One of the main characteristics of the strength of an automobile body is its torsional rigidity. In the case when the body rigidity has an insignificant value, then the turns of the car will occur with some delay, due to the slowdown in the response of the car structure. Metal in the areas of attachment of the levers will introduce a mismatch in the operation of the rear and front suspensions. Due to constant twisting, premature aging of the body occurs, welds diverge, metal corrosion occurs intensively. If we consider cars only in this aspect, then the three-door coupes and hatchbacks, which resist bending as much as possible, are considered the strongest in body rigidity. Wagons and minivans have the worst indicator in this regard.
Strengthening the car body depends on the specialization of the vehicle and the financial capabilities of the car owner. There are many options for this, starting from the installation of stretch marks and spacers.
From all this abundance of various modifications, we choose: rods, scarves, rear, lower, front struts.
Front struts
A popular way to strengthen the body is the front struts. The advantages of this design include ease of installation, reasonable price, increased rigidity in the front of the car, and finally, visual aesthetics. The use of such a mount depends on the purpose of the vehicle. Its advantages are obvious - ease of installation, low price, visual appeal and a fairly strong increase in the rigidity of the front of the car. This method of strengthening the body for VAZs of the "tenth" family is not suitable. Since on these modifications of the models not only the racks “dance”, but the entire front shield is subject to deformation.
Spacers are offered by trade in a wide range, but their main difference from each other is in the material from which they are made and the method of fastening. Kerchiefs usually strengthen wheel arches, stiffeners throughout the body and suspension struts. Such reinforcement of the auto body is usually used on sports car models.
Bottom struts
The lower struts have an impact on improving the car's handling, increase stability, increase the life of the body, but the installation itself is very laborious.
The rear struts have an effect on improving the maneuverability and stability of the vehicle. Installing and removing the rear struts is easy. The rear strut is also quite easy to install and dismantle.
There is an existence and use of folk methods of strengthening the body, when the holes of the spars and thresholds are filled with mounting foam. In value terms, it's cheap. The advantage of this design is an increase in rigidity, the disadvantage is an increase in the activation of corrosion, the lack of ventilation. Increases the risk of fire during welding. The choice is up to car owners.
3-09-2011, 06:30 | Zinchenko Vladimir Alexandrovich
There are a number of simple rules, following which allows you to maximize the life of the automatic transmission.
Alexy59 » Mar 20, 2014, 06:52 pm
homa » Mar 20, 2014 19:53
Hey Alexy!
So, among the rotten people - Okovodov - replenishment!
I did not expect that there is something more rotten than my Akushka! And it looks like they drove it to the last?
In general, the sight of such devastation + repair with foam and self-tapping screws causes severe discouragement.
I’ll say a banality - without new spare parts, repairs will become more complicated
What is your goal in terms of repair?
And what kind of piece of iron is in her doorstep?
Dear Alexy!
I have for you:
Two requests:
Complete your profile so we know where you are from.
If not difficult, go here viewtopic.php?f=21&t=112
And one message:
Our strict but fair moderator - Yuri
even if you do something bad, do it well
Yuri » Mar 20, 2014, 10:40 pm
Alexy59 » Mar 21, 2014, 10:24 am
mmlevin » Mar 21, 2014, 11:05 am
Yuri » Mar 21, 2014 11:44 am
Alexy59 » Mar 21, 2014 11:56 am
started with the repair of the left threshold. put a new threshold on top of the old one and circled it along the contour, cut it off with a grinder
it turned out to be an uncomfortable diagonal cut, and even with steps.
and here is a photo of the backside with lining
Alexy59 » Mar 21, 2014, 12:02 pm
Alexy59 » Mar 21, 2014, 12:44 pm
In the process of repairing the threshold, it was first necessary to cut out the old one, or rather its remnants that go under the middle bottom. I just cut the corner with a grinder where the middle bottom meets the inner sidewall, and then I uprooted the remnants of the threshold connector. After that, he brought in a new threshold connector, which he grabbed to the inner sidewall. At first I wanted to do it like an “adult”. I drilled holes in the connector and through them tried to honestly weld to the inner sidewall. But it was not there. In some places there was a gap and the metal did not fit snugly to the sidewall. In addition, the iron of the sidewall was corroded, although I cleaned it. Well, the most important thing is that these first weld points were one of my first and there was no experience yet. And it turned out not a beautiful welding ala electric rivet, but some kind of garbage. and so I then just started to grab the iron to the edge. so today the back of the sill connector is attached only to the inner sidewall, and that's not so hot. then the truth, on the other hand, the inner threshold will be connected to the middle bottom. besides these connections, there are no others. maybe Homa will tell you how it should be in that place CORRECTLY. I will be very grateful.
Here is a photo of the place that I talked about during the fitting process
The Oka car began to be produced a long time ago and has earned considerable popularity among domestic motorists. Of course, the technical characteristics of the car in question are far from the requirements of a modern motorist. Despite this, at one time the Oka was very popular due to its inherent economy. Owners of an Oka car from early years of production often encounter malfunctions of the propulsion system. This is easily explained by the service life and operating conditions of the vehicle. One of the most effective ways to restore the vehicle to working capacity is to overhaul the Oka or VAZ 11113 engine. Doing repairs yourself is quite difficult, since many processes will require expensive equipment. In order to save money, you can prepare the Eye for a major overhaul with your own hands.
The benefits of overhaul are clear. Large-scale repair of the engine will allow: to increase the life of the vehicle, increase the resource of the motor and increase its performance.
The first stage of the overhaul is a detailed diagnosis of the internal combustion engine. It is quite difficult to perform a check in a garage. In order to determine the productivity of the engine, you will need computer equipment and appropriate skills.
To perform a complete restoration of the engine, it is necessary to dismantle the car device. Performing this procedure with your own hands is not so simple, despite the small dimensions of the motor. In order to avoid damage to the engine, it is necessary to use a number of specialized equipment: support frames, a hydraulic puller, a device for hanging the engine.
After the dismantling of the engine has been successfully completed, it is necessary to proceed with its disassembly. It is necessary to disassemble the engine strictly in a certain order in order to prevent damage to its individual parts.
After disassembly, it is necessary to proceed to the most important stage of the overhaul, which consists in troubleshooting individual components of the internal combustion engine. The main goal of the overhaul is to return the vehicle elements to factory settings. Therefore, the only correct Oka repair manual is the original manufacturer's instructions.
During the large-scale restoration of the VAZ 11113 engine, the following procedures are mandatory:
- Restoration of the parameters of the cylinder block VAZ 11113.
- Repair of crankshaft and camshaft inlets.
- Restoration of the bearing part of the crankshaft.
- Processing of the head of the cylinder block VAZ 11113.
- Return tightness block by welding.
- Editing the geometry of the connecting rod.
- Replacement of all consumables and rubber seals.
Large-scale car repairs require appropriate skills and expensive equipment. Therefore, in order to perform the restoration, you will have to turn to professionals.
One of the most important stages in the restoration of the engine is the processing of the cylinder head. The vehicle manufacturer indicates the permissible head treatment limit, which must be strictly adhered to when carrying out repairs. Before proceeding with a large-scale repair, it is necessary to study in detail the manufacturer's instructions. Also, it is imperative to check with the master at what depth the cylinder head will be processed. If the element is worn out above the permissible limit, further operation of the block head is prohibited. If the processing and restoration of the cylinder head is possible, the work is accompanied by the mandatory replacement of the cylinder head gasket. In this case, it is also necessary to take into account the depth of processing of the element in order to give the block its original tightness.
To restore the VAZ 11113 internal combustion engine to factory settings, it is recommended to use the services of trusted workshops. Overhaul is a rather complicated and time-consuming procedure, which must be carried out by qualified craftsmen. Before carrying out repairs, it is necessary to sensibly assess the costs of restoration. Some car enthusiasts forget to appreciate the difference between restoring an element and replacing it. With critical engine wear, repair costs may well exceed the primary cost of the internal combustion engine. If it is necessary to replace individual elements of the vehicle, it is worth using only original spare parts from the manufacturer.
After the repair, it is worth starting to run the car. During the break-in period, it is necessary to prevent an increased load on the propulsion system. Otherwise, the cost of restoring the engine will not justify itself and the VAZ 11113 vehicle will again lose its performance.
Successful restoration of the VAZ 11113 car!
Oka Vaz 11113 is a small-sized Russian hatchback, the release of which began in 1988 and ended as recently as 2008. The car was initially produced at the Volga AvtoVAZ plant, after which production was transferred to the SeAZ and ZMA plants.
The very first Oka was the cheapest Russian car, which included an engine for 29 “horses” of power, and the volume was 0.6 liters.
After that, an improved version of the Oka 11113 appeared, with a two-cylinder engine with a volume of 0.7 liters and a power of 33 horsepower. The car came with a 4-speed gearbox. But something worthwhile can be made from such a car if you do OKA tuning.
The maximum speed that the car can develop is 140 km / h. Further, the car was modernized by a Chinese concern, with a 1 liter engine and a power of 53 horsepower, the brand of the car began to be called Seaz11116, the equipment is equipped with a 5-speed manual.
The maximum speed that the car could develop was 150 km / h. The car has a spare tire on the back door, a “kenguryatnik”, tubular thresholds, looking at such paraphernalia, we can say that Oka’s car is a real compact SUV.
Jeep all-terrain vehicle "OKA" is designed for off-road driving. The car borrowed a lot of parts to increase its cross-country ability, the car body, lighting equipment, seat and upholstery remained from the native parts.
The front panel is borrowed from the figure eight, and the armrest and stove from the five. Kengurin from the Ssang Young Musso model, which is very necessary for off-road. The car demonstrates ease of movement, maneuverability on the road and good cross-country ability.
Under the hood of the car there is an injector and an engine from the well-known company Rover Mini, with a volume of 1.3 liters, with a capacity of 63 horsepower. To show the capabilities of the machine, you can not stand still and discuss the details. You need to feel the car and start moving.
The performance of the Oka model is well demonstrated by the 14-inch wheels, which added significant weight to the car, and thus the car became even more like a jeep. To increase the cross-country ability of the car, the chassis and suspension were borrowed from the front-wheel drive VAZ.
Further video about tuning OKA Lambo:
Many car enthusiasts like to drive on splayed wheels, so the VAZ 11113 Oka tuning expands the car's track by 150 mm, increases the arches to install larger diameter wheels. On top of the arches, you can install plastic lining that will decorate the appearance of the car and create an individuality.
Tuning the Eye can be done indefinitely, it all depends, as a rule, on the owner's imagination. External tuning of the Oka is considered one of the most important and noticeable elements of the modernization of the car. It has become fashionable to do tuning aerodynamic body kits, which can also change the look of the car and improve its technical characteristics.
If you slightly raise the body of the car, you will immediately feel the look past the passing envious people. Install good bumpers in place of plastic ones, slide them out and trim with overlays, so you will noticeably expand the body of the car, and the Oka itself will look even more powerful.
Install the steering shaft from the eight, with a modified driver's seat, so you get the long-awaited comfort. And here is the long-awaited Oka tuning photo, with the upgrades listed.
The first impression of the cabin may seem poor and insufficient for such a powerful machine. Oka interior tuning includes interior firmware, modern upholstery with high-quality material, installation of electric glass lifts and high-quality vibration and noise insulation. Updated head units, midbass, amplifiers and subwoofer.
The torpedo is also equipped with soundproofing, and electric lifts can move the windows with the push of a button. On the pedals are aluminum pads, which are often found in sports cars. A loud muffler of a rectangular shape can emphasize the spirit of sports.
The car has a low degree of passive safety, so this feature needs to be urgently corrected. For the safety of passengers and the driver, install a safety panel and additional airbags. Plus, you can install disc brakes and a dynamic stabilization system.
Sometimes, as a tuning for the Oka, motorists purchase start-up chargers. Such devices are necessary on the road when the battery randomly runs out. Additionally, interesting multi-color airbrushing and vinyl decoration can decorate the car.
Here, unleash a professional artist, and he will create a "car" that will surprise and stun everyone on the road. The most popular fantasy-style body paintings, gloomy castles, unknown planets, stars, or the sky.
Many people think that if the car is small, it makes no sense to do Oka tuning for a jeep. It really consumes little gasoline, however, all the factory parameters of the propulsion system were not provided ideally, so some characteristics need to be finalized.
To increase the power of the car, you need to do engine tuning. Modernization begins with the replacement of all major components, namely the air filter, camshaft, carburetor and cylinder head.
The fuel exhaust and intake system will also have to be replaced, while the cylinder engine changes to a Rover one, which has a volume of 1.3 liters. With such an engine, the car accelerates evenly.
If a gas unit is installed in the car, it may also involve the installation of a camshaft, with a lift level of 10.3 mm, and with significantly increased compression ratios. When the engine of the gas unit is boosted, the power increases accordingly and the traction on the bottoms improves.
Now it is very popular to carry out chip tuning of the motor in cars, which significantly affects the increase in engine efficiency. This method of modernization differs from others in that there is a software change in the motor control unit.
The program can be adjusted taking into account the concealment of reserves and other characteristics. This method is considered the simplest and most powerful. In the event that the car stops working, you can return the engine to factory specifications.
Chip tuning is able to reduce fuel consumption, reduces the emission of fuel into the atmosphere with harmful toxic substances. Chip tuning is now applicable to most Russian cars, including the famous VAZ 2106.
Be sure to do Oka tuning, it is necessary to replace the camshaft, pusher and grind the manifold. The grinding procedure means fitting the channels of the manifold to the channels of the head. Tappets of a special profile, with a lighter valve and a new camshaft can significantly increase the power of the Oka engine.
For a new engine, it will be important to install a high-quality air filter, thereby allowing the wheels to rev up to 7000 rpm, and the aggressive notes of the engine will be felt on the road.
To reduce fuel loss at high speeds, exhaust and intake channels are being finalized, valve seats and the shape of the combustion chamber are changing. This type of tuning is considered one of the most expensive, as the master does all the work manually.
For a compact car, the increase in power will be a weighty argument. By installing the main pair with a good gear ratio, you can increase the maximum speed of the Oka, as well as improve acceleration characteristics, which even the driver himself can appreciate. The traction reserve will be felt while driving, it will add confidence and maneuverability on the road.
In the process of tuning the engine, you can get the following results:
- the maximum engine speed will increase from 119 to 127 km/h;
- acceleration time to 100 km / h will increase from 36 to 25 seconds.
Surely everyone is tormented by the question: “How to make Oka tuning with your own hands?”. Since the car is considered the cheapest and most economical, the following advantages can be emphasized: a car consumes only 3-4 liters of fuel per 100 km, but at the same time it loses its dynamics.
Let's try to improve the technical part of such a powerful unit, for this you need:
- any repair begins with the purchase of the necessary material;
- buy all tools, devices and devices from an authorized dealer to avoid possible counterfeiting;
- choose only high-quality materials, metallic.
Next, we turn to the purchase of equipment: a gas shock absorber, mirrors that match the color of the body, luxurious upholstery with armrests, a towbar, a cigarette lighter with an ashtray, soundproofing material, an engine crankcase protection device, an anti-corrosion treatment device, lockers (fender fenders), inertial seat belts .
Additionally, you can purchase a new dashboard with a clock, a tachometer and a special place for the radio. Looking at the car, you can see how the designers have bent the cables of the car, thereby reducing its longevity.
You can see how one cable presses the filler pipe of the gas tank, which adversely affects the propulsion system, so some redevelopment is required. Then we move on to adjusting the carburetor, tension belts and replacing the heating tap.
Let's start with changing the appearance of the wheels, the purchased set should consist of alloy wheels and tires of the required diameter, usually from 14 to 16 inches. The first impression you get is how much the sensations from the movement have changed, the softness of the ride over bumps has appeared.
In replacing the torpedo, you can use the console from the Niva, for this you need to cut off the lower part of the device, fix it on four self-tapping screws for the heater and the lower part of the torpedo.
A radio can be installed in the torpedo, and speakers can be mounted on the front lower part of the door. The remaining speakers must be installed in the niche of the luggage compartment. If all the work is done correctly, you can get high-quality music.
In the dashboard, you can also install control buttons for the head light, rear and front fog lights, an emergency light button, a heating button for the rear window and rear wiper, and a fan switch.
Where the cigarette lighter is located, you can also install a door ashtray. Do not forget to install a glove box, which can be bought at any car dealership.
It will help to make the modernization of the car yourself with a special Oka tuning photo with your own hands, which shows where all the devices should be. The photo can be used as a guide or as a diagram of the occupancy of the cabin.
To improve the quality of interior lighting, you can embed two lamps of the desired color into the rear of the door trim, another lamp can be installed at the bottom of the dashboard above the glove compartment. It will not be superfluous to install a lamp in the luggage compartment.
Next is a video with a do-it-yourself Oka tuning option:
VAZ 1111, better known as Oka, has become the subject of ridicule due to its compact size and simple design. Meanwhile, this car foreshadowed the era of economical, small cars. Today, almost every global automotive brand is developing its own “baby”, so a serious competition has unfolded in the compact car class. The domestic auto industry, along with the Italian one, can be considered a pioneer in the development of the production of compact cars. Another question is that the VAZ 1111 has not received sufficient development in the form of the development of restyling and new generations. But Oka provides fans with car tuning with their own hands and ample opportunities for modernization.
There are many options for transformation, restyling VAZ 1111:
- SUV
- rally car
- Retro car - design concepts of the late 60s and early 70s of the XX century are due to the angular shape of the body, the use of bright colors in the design
- Cabriolet
- Roadster
The simplest and most affordable is off-road Oka tuning, since the car looks similar to this class of cars. To enhance this effect, it is enough to lift the suspension, install larger diameter discs and rubber with a powerful tread. But tuning Oka for a jeep is not limited to the above changes, they can only be considered the first step in creating an exclusive little all-terrain vehicle.
Oka's external tuning can be stylized as the popular Grand Cherokee SUV model. This is facilitated by the similarity of the headlights and grille. In both cars, they are oblong, rectangular in shape. It is enough to install a body kit, wheels with a large diameter and a tractor rubber tread, as well as give the appropriate configuration to the hood and the nondescript OKA will turn into a miniature clone of an SUV popular in the 90s.
Do-it-yourself tuning of Oka cars is quite easy to do.This is due to the simplicity of the technical device of the car and the unpretentious appearance, which, on the one hand, makes modernization simple and cheap, and on the other hand, allows all kinds of experiments to be carried out on the car.
From all of the above, we can conclude that tuning the VAZ 1111 is the best school for a beginner and a kind of creative studio for an experienced master.
The process of improving engine performance can be conditionally divided into 2 areas:
- A fundamental change in performance - a complete replacement of the motor
- Improvement of the regular power unit
In the first case, an injection engine from Rover Mini with a volume of 1.3 liters would be an ideal option. The advantage of this type of tuning is a significant increase in technical indicators, the disadvantages will be the high cost of implementation and the need to recycle most car systems for a new engine. This is expensive and takes a lot of time.
The second option is the modernization of a regular power unit, which is cheaper and simpler, but will not allow you to get such an increase in power as in the first case.
Do-it-yourself tuning of the Oka engine must begin with a carburetor. The first step is to increase the throttle diameter to 52–54 cm. This will allow the engine to receive more air, which will facilitate its operation, increase performance and increase engine life. You can immediately install a tuning modification of the carburetor.
Installing a new camshaft allows you to increase the speed to 7000 units. In this case, it is imperative to tighten the engine power, which is done using the following operations:
- Replacing standard valves with lightweight ones
- Valve seat upgrades
- Modification of inlet and outlet valve channels
- Valve sealing
- Installation of bronze guides
- Changing the shape of combustion chambers
Additionally, you need to replace the intake and exhaust manifolds, as well as the air filter with a K&N model with zero resistance, for sports modifications. This set of measures will significantly improve the technical characteristics of the engine and optimize its operation, that is, the loss of power will be minimal.
With the muffler attachment, you can give the engine a sporty growl. Models with backlight will create the effect of a flame escaping from a jet nozzle.
Improving the driving characteristics of the VAZ 1111 is the owner's first priority, since in the basic version of the suspension they are useless and cause a lot of complaints. To remedy the situation, it is necessary to install gas-oil shock absorbers. This is enough to give the car stability and improve its handling.
Experts do not recommend changing standard springs to advanced modifications, since the latter quickly fail.
If it is planned to make an SUV out of the Oka, then it is necessary to lift the suspension. This can be done using a specialized kit or by adding spacers under the springs. The result is a bulging rear end of the car. But at the same time, it will be necessary to modify the shock absorber mounts. Actually, this is all that is needed to improve the suspension of the VAZ 1111 with your own hands.
There are more than enough options for upgrading:
- Complete upholstery replacement. To do this, use your own materials or buy a special kit. You can try the author's method of processing the interior, for example, finalizing the standard trim
- Partial decoration - installation of curly inserts and elements in the skin
- Refinement of regular chairs - installation of comfortable headrests, purchase or manufacture of stylish covers. At the same time, the general design concept of interior processing in terms of color matching should be taken into account.
- Replacing regular seats with sports or executive class seats
- Installing a new steering wheel
- Fitting stylish pedal covers
- Installation of additional equipment: automatic drive of windows and side mirrors
- The roof can be made panoramic or cut out the hatch
These are far from all the options that can be implemented by doing the tuning of the Oka's interior with your own hands. In fact, there are no dogmas and prohibitions, it all depends on the imagination of the master. This is a great option for creative experiments, the invention of author's decoration techniques.
Tuning the Oka torpedo is associated with a difficulty - the compact dimensions of the car. In this regard, it is unlikely that it will be possible to install a torpedo from other models. Or it will take a long time to find the right size. Here the best assistants will be imagination and improvised means.
You can resort to the standard, proven option - to cover the torpedo with leather or carbon film. If you want to create an exclusive, then polyurethane foam, epoxy resin, and a grinding tool will help in this. With their help, you can change the design of the torpedo as you like. This is also a good method for reworking the mounting hole for the dashboard.
Tuning the Oka panel with your own hands also provides 2 options:
- Factory Panel Upgrade
- Installing a new panel, from other car models
The first option involves replacing standard backlight lamps with LED ones. Installing a new substrate or modifying the standard one will allow you to create a non-standard look. Complete replacement of the instrument panel will require revision of the torpedo.
Do not forget about high-quality sealing, a new or modified torpedo should not make squeaks. This requirement can be considered an integral part of tuning.
Standard VAZ 1111 bumpers are difficult to upgrade, as they have a limited tuning resource. The reason is a small surface area where fog lights and a place for a license plate are located close to each other. But if you want, you can also swing regular bumpers. This is done with mounting foam, epoxy resin and a grinding tool. For example, you can increase the bumper at the bottom by adding diffusers in the style of rally cars. But such technology is impractical and time-consuming.
The main difficulty in upgrading a standard bumper is the creation of a symmetrical surface and a clear drawing of lines. Also, the development of design can cause a certain difficulty. In order not to suffer for a long time, it is worth taking some advanced sample of a sports bumper as a basis.
Do-it-yourself optimal bumper tuning for Oka is the replacement of native samples with advanced modifications. It's simple and fast. Difficulty will cause only the installation of the rear bumper. The reason for the difficulties is the hitch.
It should be remembered that voluminous bumpers visually increase the size of the body. The effect can be increased by pushing the bumpers forward.
Tuning Oka optics is one of the important elements that affect the appearance of the car. An effective method of transforming headlights is to install overlays. You can buy them or make your own. Before that, you need to put LED lamps and polish the headlights. It is possible to completely replace optical devices. To install an advanced model, body modification will be required.
What other tricks can be used to change the appearance of the headlights:
- Redesign of the headlight rim - application of a shiny coating, stylized as chrome
- Finalization of the headlight substrate
- Decoration with LED strips, most often they resemble eyelashes, but you can place them at the bottom and give the car an aggressive look
![]() |
Video (click to play). |
Tuning the rear lights of the Oka is carried out mainly by installing overlays. At the same time, it is worth remembering that they should not compromise safety - the lights remain clearly visible in any case.