In detail: do-it-yourself plow share repair from a real master for the site my.housecope.com.
The main working parts of the plow (Fig. 123) are the body, consisting of a share 6, a blade 1, a field board 7 and a rack 2, a draft 3, a skimmer 5, a knife 4 and a soil-dredging share 8.
Dullness of the plowshare, as well as wear or deformation of the blade, skimmer, knife or field board, increases the traction resistance of the plow, leads to excessive consumption of fuel, worsens the quality of the seam turnover, its crumbling and incorporation of plant residues.
Rice. 123. Working bodies of the plow installed on its frame
Two types of plowshares are used in plows:
trapezoidal - with a straight cutting edge (Fig. 124, a) and chisel - with a thickened and downward curved toe (Fig. 124, b).
Plowshares are made of durable and wear-resistant steel grade L65 and thermally treated to increase wear resistance. However, the working conditions in the soil are so difficult that the plowshares wear out quickly. When the ploughshare is worn, the blade becomes dull and the shape of the nose changes. In fig. 125 cross lines mark the edges of the worn-out trapezoidal and chisel-shaped blades. When the blade becomes dull, its thickness increases, and a faoca (back of the head) forms on its reverse side. When the plowshares are worn out, the plow performance deteriorates, i.e. the plowshares lose their ability to go deep into the soil, and the plow's stroke stability is disturbed. The plow share must be repaired when its width is reduced by 10 mm compared to the width of the new trapezoidal share, or when the length of the nose is reduced by 25 mm compared to the length of the nose of the new chisel share.
![]() |
Video (click to play). |
Repair of plowshares is reduced to blade retraction, sharpening and heat treatment. Repair of plowshares is carried out in order to restore their size and shape, as well as to give them durability.
The ploughshare section has a thickening - a stock of metal, which is called a "store". When repairing a worn ploughshare, its shape is restored by a blacksmith's guy at the expense of a stock of metal in the "store". The ploughshare pulling is done manually, usually in several heats, since the blacksmith does not have time to pull off the entire ploughshare in one heating. When pulling the share manually, it is necessary to always strive to reduce the amount of heating, as with repeated heating, cases of metal burnout are possible.
The drawback of the share on a lever or some other mechanical forging hammer is usually done in two steps. In this case, the length of the heated part of the share must each time slightly exceed half of the share.
To reduce heat loss and prevent carbon from burning out of the surface layer of the metal, the part of the share that is not heated is covered with fresh coal.
The forging guy of a worn out share is made in the following order. The ploughshare is placed flat in the forge so that it is heated from the side of the blade to a width of 60-80 mm; the rest of it, which does not require heating, is covered with fresh coal. It is necessary to heat the share for the quickdraw at first slowly, until
luminescence, ie, up to 500-600 °. It is impossible to heat the share directly to the forging temperature in order to avoid the formation of cracks. As soon as the ploughshare is heated to 500-600 °, the heating rate is increased and the temperature is brought to 850-1200 ° (up to light red and orange heat).
Rice. 124. Plowshares: a - trapezoidal, b - chisel
Rice. 125. The shape of worn out plowshares: a - trapezoidal, b - chisel
The heated ploughshare is taken out of the forge, placed with the front side on the anvil, and from the back side, the stock of metal is dispersed from the "store" with frequent blows from the parking brake or hammer.A ploughshare made of steel grade L65 can be pulled (forged) only at temperatures above 800 °. The drawing is stopped when the plowshare cools below 800 ° (with a cherry-red heat) and is resumed after reheating. The drawn part of the ploughshare is ironed on the anvil with a trowel along the entire length of the cutting part so that the thickness of the blade is 1–2 mm, then the irregularities formed from hammer blows are removed.
When pulling, the shape and size of the plowshare is checked with a template (Fig. 121, a). For the drawn share, deviations in size are allowed against the new: in length by ± 15 mm, in width by + 4 mm.
The ploughshare, after drawing and ironing, when it is still in a heated state, is clamped in a locksmith's vice and its blade is sharpened with a file. Then the cooled ploughshare is sharpened from the front side on a naphtha sharpener. After sharpening, the width of the edge of the blade should be no more than 5-6 mm, and the thickness of the blade should be within 0.5-1 mm. The share blade should not be sharpened thinner than 0.3 mm, otherwise it will wear out quickly during operation.
Heat treatment of the drawn share consists of hardening and tempering. During hardening, the plowshares are heated along the blade by about one third of its width. Heating in the furnace to a temperature of 780-820 ° should be uniform (light cherry-red heat). The heated ploughshare is quickly cooled in a water bath. The water temperature in the quenching bath should be 30-40 °. The ploughshare is lowered into the bath with its back down. If the share is dipped into the hardening bath with the blade, it can crack. Do not lower the ploughshare flat, as in this case it usually warps. The ploughshare is kept in a quenching bath until the water stops boiling, after which it is taken out of the bath and slowly cooled in air.
When the chisel share is hardened, cracks may appear on the blade. To avoid this, it is necessary to pre-cool the place of transition from the tip to the blade at the heated ploughshare by applying to it for 2-3 sec. a wet rag, only after that the ploughshare is quickly lowered into the hardening bath.
To reduce the fragility of the ploughshare, which occurs during hardening, it is tempered. For this, the ploughshare is reheated to 350 ° (discolored gray) and then slowly cooled in air.
During hardening, the ploughshare often warps. The warped ploughshare is ruled over the anvil by the blows of a hammer. The blows on the share should be applied carefully and not hard.
The hardness of the hardened part of the share is checked with a personal file. The file must not leave any marks on the hardened part of the share.
In RTS repair shops, plowshares during repair are welded with high-quality electrodes or a charge of V-9 hard alloy. This method of repairing plowshares increases their durability. An increase in the wear resistance of the plowshares is also achieved by hardening their outer layer with high-frequency currents.
Holders of the patent RU 2344913:
The invention relates to agricultural engineering, in particular to methods for restoring plowshares, and can be used for restoration with hardening of plowshares of agricultural machinery. The method consists in the fact that a groove is made on the surface of the share blade, the groove is filled with solder, cermet plates are installed on the solder, an additional layer of solder and flux is applied at the junction of the plates with the vertical edge of the groove. Then the plates are heated until the solder melts and the ploughshare with plates in a heat-insulating collector is cooled to room temperature at a rate of 4 ° C / min. In this case, L63 grade solder is used as a solder, and FK-250 flux is used as a flux. The plates are heated with a hydrogen-oxygen flame of the burner at a gas mixture pressure of 0.5 MPa and a distance from the burner nozzle exit to the plate surface - 50 mm. The technical result is to increase the adhesion strength of the cermet plates with the plow share. 1 tab.
The invention relates to agricultural engineering, mainly to machines for soil cultivation, and can be used to restore and strengthen plowshares of agricultural machinery.
There is a known method of obtaining wear-resistant blades of working bodies of soil-cultivating tools by strengthening their blades, which consists in the fact that in order to form waviness of the blades leading to their self-sharpening, a harder metal is placed on the smooth surface of the blades intermittently and parallel to the cutting edge, followed by limiting the surfacing zone (see AS USSR No. 461721, class А01В 15/04, publ. 1975).
However, when using this method, the share has a relatively low wear resistance, since the non-melted part of the share wears out much faster than the welded areas, as a result of which the hard alloy being welded is exposed and crumbled, which worsens the conditions for self-sharpening of the share.
The closest to the proposed method in technical essence and the achieved result is a method for restoring plow shares by applying hard alloys to their cutting bodies. Its essence is as follows: in order to increase the service life of plowshares and cultivator paws, the application of hard alloys to their cutting bodies is carried out in two stages: the first is welding of a steel lining on a worn out nose, followed by its surfacing with hard alloy; in the second stage, after intermediate operation, the worn out is pulled the straight part of the blade of the cutting bodies with its subsequent hard-facing (see AS USSR No. 241959, class А01В 15/04, publ. 1969).
However, the working surfaces of the plowshares, restored by this method, have a low adhesion strength between the hard alloy and the base metal, as a result of which the restored plows are short-lived during operation.
The objective of the invention is to increase the breakout force and, as a consequence, the adhesion strength of the sintered plates with the plow share, as well as to reduce the consumption of sintered plates and to increase the plowing performance by increasing the working speed of the plowing unit.
The task is achieved by the fact that in the known method of restoring plowshares on the surface of the plowshare blade, a groove is made, the groove is filled with solder, cermet plates are installed on the solder, an additional layer of solder and flux is applied at the junction of the plates with the vertical edge of the groove, the plates are heated until the solder melts, and the ploughshare with the plates in the heat-insulating collector is cooled to room temperature at a rate of 4 ° C / min, while the L63 grade solder is used as the solder, the FK-250 flux is used as the flux, and the plates are heated with a hydrogen-oxygen flame of the burner at a gas pressure mixture of 0.5 MPa and a distance from the nozzle exit of the burner to the surface of the plates - 50 mm.
The method is carried out as follows.
Plowshares of plows, taken for restoration, must meet the following requirements: they must be cleaned of contamination to a state that allows inspection and detection of defects; the thickness of the base of the worn share in the area of the bolt holes is at least 8 mm; the width of the worn share, determined from the back (non-working) side as the distance from the back to the occipital chamfer - not less than 100 mm.
A groove with a depth of 1.5 is made on the surface of the plowshare blade. 2.0 mm. This operation is performed on a vertical milling machine.
Then, L63 solder is placed in a previously prepared groove at regular intervals, after which metal-ceramic plates TN-20 or T15K6 are installed on the solder. After that, an additional layer of solder and flux of the FK-250 brand is applied to the junction of each plate with the vertical edge of the groove.
Next, the plates and the restored plow share are heated using a portable gas welding apparatus MBV-500 with a hydrogen-oxygen torch flame. Process modes: the distance from the burner nozzle exit to the surface to be restored is 50 mm, the oxygen consumption is 400 l / h, the hydrogen consumption is 375 l / h at a gas mixture pressure of 0.5 MPa. In this case, the burner is alternately stopped over each plate, trying to ensure its uniform heating. Heating is continued until complete melting of the solder occurs. In this way, each plate is soldered. Exposure to a hydrogen-oxygen flame does not adversely affect the used solder, flux, cermet plates and share metal.
Then the recovered ploughshare with the brazed metal-ceramic plates is placed in a heat-insulating collector heated to a temperature of 620.630 ° C, together with which it is cooled to room temperature, the cooling rate being 4 ° C / min.
The results of comparative tests of the proposed method and prototype are shown in the table.
The following malfunctions and wear are possible in plow bodies: the share blade becomes dull, a chamfer appears on the back side, the toe is rounded, the share narrows in width. There are frequent cases of breakage of the ploughshare and the mowing of its working part as a result of striking the roots and stones when plowing high-speed plows when the pile of the dump is worn out, the shape of the field cut changes, its edge is rounded, the working surface is worn out and the toe breaks off, at the wing it wears out
The blade of the share when blunt is sharpened by the working side to the thickness
Ploughshare a-self-cleaning; b-composite welded; 1-strip; 2-back
The shape of the worn-out working surface of the blade is checked with a template. Deviation from the template is permissible no more than 6 mm. If the toe of the chest breaks, the blade can be restored. To do this, the broken off part is made from an old dump, according to a template, adjusted at the junction and electrically welded from the back to the worn dump. Before welding, the workpiece is thermally treated to obtain a hardness of NKS 62. 50. To remove heat during welding, the areas near the seam are coated with a solution of clay with asbestos, a 5 mm thick red copper lining is placed under the seam, and a rag soaked in water is placed under the lining. After welding, the seam is cleaned. When the field edge of the blade is worn out, it is deposited by sequential overlay. rollers with T-590 electrodes and sharpened at an angle of 45. 50 ° to the work surface.
With slight wear, field boards are restored with hard surfacing, followed by sharpening, or use the unworn side of the board, turning it over. For this, holes are made in it and hardened.
Crumpling of the knife blade is allowed in no more than three places with a depth of up to 1.5. 2.0 mm and length up to 15 mm. Disc warping is allowed no more than 3 mm. Warped discs run cold on the stove. They are sharpened to a blade thickness of 0.5 mm on an OR-6112 device for sharpening circular knives and on accessories for a lathe with cutters with plates made of hard alloys T15K6, etc. Axial and radial runout of the disc is allowed no more than 3 mm.
The wear of the ends of the disc hubs up to 8 mm is compensated by setting washers in such a way that the gap between the spurs of adjacent discs is at least 4 mm. Cast iron parts with cracks are welded with PANCH-I flux-cored wire by electric welding or hot gas welding with cast iron rods.
Limit display of worn-out cutting bodies of tillage machines
You can ask questions only after registration. Login or register, please.
Look at the plow, what needs to be replaced in it, so that it plows and does not cut furrows. I'll try to post a photo, it seems to me that the first dump is mowing to the right, I will be very grateful for your help.
Well, yes, the first building is crooked. Does the second body also leave a furrow?
Firstly, you need to set all the bodies in one plane, and secondly, adjust the plow. Your dump does not work completely, hence the ridges.
In my opinion, there can be two reasons:
1 The plow is blocked in the furrow
2 low speed
In other cases, the ridges would be different, but you have all the same ridges
The moldboard of the first body differs from the 2nd and 3rd, and what is the rear wheel track of the tractor?
Adjust the plow.
do you drive a tractor along a furrow or across a field? the first body does not throw a lot to the previous track. the dumps are normally sanded, which means there is a turnover of the seam. the trail from the pukary is even and clean, it goes exactly judging by the fact that all the dumps have the same grinding height . well, almost a plowshare and breast

Make a harrow after a plow and you will be happy.
- something knocks in the engine.
- make the radio louder and you will be happy

Economic policy is above all the art of implementation, not the art of making plans. (A.V. Chayanov)
We create conditions for development:. support of agricultural producers in terms of not hindering them. P.N. Cherkasov, Natalinskoe Moscow Region.
It is a fact that the plow must be regulated, but in addition, it is necessary to regulate the way the plow is mounted on the tractor. then the arable land will be beautiful.
Economic policy is above all the art of implementation, not the art of making plans. (A.V. Chayanov)
We create conditions for development:. support of agricultural producers in terms of not hindering them. P.N. Cherkasov, Natalinskoe Moscow Region.
How not to adjust the plow, but the grooves and lumps will still remain. Especially on hard ground. With the harrow, it turns out perfectly even.
And what, so exactly what can you sow without leveling with a cultivator?
do you drive a tractor along a furrow or across a field? the first body does not throw a lot to the previous track. the dumps are normally sanded, which means there is a turnover of the seam. the trail from the pukary is even and clean, it goes exactly judging by the fact that all the dumps have the same grinding height . well, almost a plowshare and breast

The plow plows normally, the track from one pass is even

1) Pull the plow with chain ties closer to the right side (the plow is far away from the furrow, maybe
also field boards can compost brains)
2) Just digest the plow attachment point (automatic coupler triangle).
Specifically, it's up to you to decide.
Do not rush to do good. Good should be done slowly so that it is noticed and appreciated.
An equestrian plow, a tractor plow or for a walk-behind tractor is an indispensable thing in a backyard farm. The plow plows the soil, turning the top layer of the soil, which reduces the amount of weeds, makes the soil softer and more pliable. You can not only buy a plow, but also make it yourself. To do this, in addition to tools and materials, you need to have an idea of \ u200b \ u200bthe structure of the plow and its geometry.
It is possible to make a plow correctly only when there is an understanding of the plowing process, as well as the purpose of each of the parts of the plow.
When plowing, the plow wedge cuts into the soil at a specific angle, depending on the softness and moisture of the soil. The wedge separates the reservoir, lifts and compresses it, while simultaneously dividing the reservoir into several parts. The angle of entry depends on how many parts the earth layer will be split: the larger the angle, the larger the split. But if the angle of entry is more than forty-five degrees, then the soil stops sliding on the working surface of the plowing device, and begins to accumulate in front of it, making further work difficult.The vertical plow, that is, with a sharper leading angle, separates the soil from the edge of the furrow and compresses it horizontally. A plow with a horizontal steering angle works differently: it deflects and turns the soil layer.
A typical working plow consists of:
- A ploughshare that cuts the soil
- Dump,
- Knife,
- Field board,
- Racks,
- Skimmer.
Additionally, the plow can be equipped with:
- Stronger metal frame
- Wheels
- A mechanism that corrects the work of the plow relative to the tractor,
- Hydromechanisms,
- Pneumatic hydraulic system.
The dump can have several types of working surface:
- Screw,
- Cylindrical,
- Cylindroid.
The cylindrical one perfectly grinds the soil, but the formation forms poorly. This is not always convenient. The cylindrical working surface is usually used for working in soft soil. The most convenient and practical to work with is a cylindrical surface, which crumbles and turns the soil well, and also copes with both dry and wet soil.
To make a plow at home with your own hands, you must have:
- Rollers,
- Grinder,
- Gas cutter,
- Fasteners,
- Measuring tool,
- Hammer,
- Welding machine,
- Scissors for cutting metal.
Before starting work, it is recommended to draw up a drawing or diagram, or find a ready-made version on the Internet. This will allow you to visually represent the progress of work, the location of all parts and fasteners.
The easiest option to manufacture. One-sided device can be made as one-piece, in the form of a single body, and collapsible. The collapsible version is convenient in that it allows you to remove the ploughshare for sharpening. The ploughshare can be replaced with a disc from a circular plate. The dump is usually done in two ways. The first of them requires the use of a pipe cut, about five millimeters thick and fifty centimeters in diameter.
A workpiece is cut out of the cut, and using an angle grinder, it is brought to the desired size. The second method of making a dump involves the presence of a steel sheet, four millimeters thick, or a cylinder with the same wall thickness, but with a section of about 50 cm.Using a welding machine or metal scissors, a shape is cut out and bent in the form of a cylinder. If there are deviations from the required dimensions, you can use a hammer for rework.
Any drawings provide six constituent elements:
- Metal disc or ploughshare,
- The foundation,
- Spacer plate,
- Side flap,
- Pipe cut for the flap,
- Field work board.
The ploughshare is usually installed using a sheet of metal and several wedges, beveled at an angle of twenty-five degrees. Fastened by two-point welding, and it also connects the rack and the side shield. It is advisable to make the shield a centimeter higher than the lower edge of the share, while the edges of the shield should overlap the edge of the blade by five or six millimeters.
The ploughshare with the blade is fastened by welding so that they are a single whole, without gaps and irregularities. The angle formed between them should not exceed seven degrees. A welded share and a blade are attached to the side stand, and the stand itself is welded first to the base, and then to the spacer plate. Finally, the corners of the share are welded to the base. All traces of welding and seams are cleaned, and the blade with a share is sanded.
This type is more efficient for plowing large tracts of land. For manufacturing, a solid steel frame is required, made of a round or rectangular profile, at least two millimeters thick. The size of the frame depends on the number of work pieces required and the control element. In the working body, the share must be placed from below, since its role is to move a layer of earth to the dump. The dump turns over the soil, cuts and shifts, forming a furrow.
The stand is necessary for attaching working tools to the frame and holding the knife. Several adjustable holes are made in it, which will allow you to change the plowing depth.Usually the rack is welded from a metal plate, at least a centimeter thick, and attached to the frame with bolts.
The frame with all the working tools is attached to the mini-tractor or walk-behind tractor with a home-made drawbar or hitch. The drawbar must necessarily have a handle, and have a straight or V-shape. The second form is more efficient as it makes the plow much more stable. Also, for greater stability and straightness of movement, you can install field wheels. They are attached to the frame with an adjustable bracket.
To assemble a plow with your own hands, you need to adhere to one very important rule: all the parts of the device are welded first by spot welding, and only when all the parts are in their places and fastened correctly - the final one. The quality of workmanship is easy to check - for this, the blade with the share must be removed, and the plow itself must be placed on the table. Pressing the plow tightly, check the coincidence of the table surface with the horizontal surface of the runner. If there are no deviations, everything is done correctly.
You can also determine a good build by the following criteria:
- The sharp edge of the share is located two centimeters below the runner,
- The share with the blade does not protrude beyond the vertical edge of the runner by more than a centimeter,
- There is no gap between the skid and the blade.
A home-made device is mounted on a walk-behind tractor next to the plowing area. They start with the installation of steel wheels - they prevent the walk-behind tractor from slipping in the soil. The next step is to attach the plow, but do not completely tighten all the fastening nuts. With their help, the device will be adjusted, which begins on a special stand. The height of the stand should be equal to the depth of plowing. After mounting and checking the fastening of all units, the plow is placed on the ground.
The performance test is carried out on three-furrow plowing.
This is sufficient for measuring depth and checking overturned formations. If the furrows run over one another, or the distance between them is more than ten centimeters, all components must be adjusted again.
Restoration of a ploughshare, with your own hands, at home, the easiest way
subscribe to my channel
Share the video with your friends
Like and leave a comment
See more of my videos
Universal fixtures. Cool homemade product Make yourself this necessary and simple device
/>
The simplest and most useful homemade product! Universal self-clamping pliers that are useful for everyone
/>
Useful homemade product that will definitely come in handy, a tool to help the welder
/>
What Can Be Made From Broken Keys! homemade tool that is useful to everyone
/>
A useful homemade product that will definitely come in handy! Make yourself this simple fixture
/>
Cool homemade product! The universal key that unscrews everything! DIY
/>
The simplest homemade tool that is useful to everyone, try to make one for yourself
/>
The homemade tool that conquered the internet! The simplest clamp, do it yourself
/>
The simplest screw wood splitter, do it yourself
/>
Subscribe to our channel and together with us you can experiment, learn something new and interesting.
Learn from our mistakes, not yours!
Agriculture, dacha, repair, equipment. in general it will be interesting!
Play top games at maximum speed: Hello friends. Today I am sharing with you the design of a simple and mega useful device with which you can easily sharpen drills of any diameter with the correct sharpening angle. This is perhaps the simplest and most effective device with which you can get sharpening the drills correctly even for those who have never done this before. Well, making this device is very simple.
Hard surfacing of plowshares with sarmite. Plowshares reinforced or increased 7.5 kg
Unrealistically cool homemade product from the usual old and unnecessary flexible hose for a shower head / Make yourself this simple and necessary device for the workshop.
Plow for plowing cultivated soils. Not suitable for virgin lands. Arable layer on red clay. There is not a single gram of sand! The earth must be done. Plowing is carried out in one direction. While I am idling, the assistant lays out the organic matter in the furrow, as well as for leveling the plot.
video on how you can harden and make a part stronger, even if it does not lend itself to the usual hardening method.
This model, new or used, due to its technical characteristics, is used for arable work on soils of various types: light, smooth, as well as medium-heavy, in which all types of grain are planted. The land must be cleared of weeds and stone beforehand. There are a lot of videos on this topic on the Internet.
LN-3-35 housings can be screw, cultural and semi-screw. Cultivated are the weakest and are suitable only for the cultivation of old arable soils. The screw is able to plow the land heavily overgrown with weeds and virgin lands.
The semi-screw housing is a medium-power unit that allows plowing stagnant soils. An elongated feather is mounted to it, with the help of which the power of the half-screw body becomes higher than that of the cultural one.
The hull structure directly depends on the type of soil that is supposed to be cultivated. If, for example, it is necessary to plow the soil of a heavy type with grinding for planting root crops, you will have to resort to using a combined housing. In it, the dump and share are shortened, but there is a rotor driven by the PTO of the traction unit and which, with its blades, crushes heavy soil.
PLN-3-35, new or used, is quite easy to adjust and operate, thanks to which one person can handle it.
The attachment consists of the following elements shown in the drawing:
- hitch;
- coulter;
- support wheels;
- frame;
- harrow hitch;
- frame.
The support wheels are provided with a special screw, with which it is possible to adjust the plowing depth. There are many videos that describe in detail the device of the plow and its coupling to the tractor. Depending on the calculated working depth, a skimmer can be installed, which has several positions;
- for a plowing depth of 200 mm;
- plowing depth 220 mm;
- processing depth 250 mm;
- cultivation depth 270 mm
- plowing to a depth of 300 mm.
The plow stand in LN-3-35 is made in one piece and has the main shares, a blade and a field board on it. The skimmer has a plow blade with a small surface area and a function for removing plant residues. The wheels are used to adjust the depth of soil cultivation. There is also a device due to which the tractor is connected to the LN-3-35.
Before removing the equipment for direct work, you need to adjust it on a special site. It is required to take special stands, as shown in the drawing, corresponding to the depth of the intended processing, minus 2-5 cm, and install them under the tractor left wheels and the supporting plow wheel. Further, the unit with plowshares must be lowered onto the platform. With the help of a screw, the support wheel is twisted until the shares touch the surface of the platform.
After that, it is necessary to align the LN-3-35 with the help of the central link and the brace of the tractor hitch. The main thing that needs to be done when setting up the unit is to adjust the position of the equipment parallel to the site. In addition, the adjustment must be carried out both in the longitudinal and transverse planes. Plow braces are attached to the longitudinal rods to the front holes. Fastening the frame with the top link through a special hole must only be carried out using an automatic coupler.If fastening is carried out through a recess, this can lead to the fact that the machine will be unstable during plowing.
Between the hinge axles, it is required to install the left brace of the towing unit with a distance of 515 mm.
Before paving the initial furrow, it is necessary, according to the marks on the support wheel stand, to set the working depth, which is 2/3 of the specified one. When laying the first lane, make sure that the rear body of the device plows to the depth specified by the support wheel, the front one only half this value. After 2-3 furrows have been driven, the final adjustment must be made.
The mounted plow must be stable and move smoothly along the furrows, as seen in the video
It is required to control so that the frame does not skew, and it is constantly parallel to the ground. You also need to check if the width and the uniformity of the working depth are satisfactory.
In the event that the right side of the frame is higher or lower than the left, then the right brace of the canopy of the traction unit should be lengthened or shortened. If the rear body is plowing the ground deeper or shallower than the front, then the top link should be increased or decreased.
After setting up the entire system, you can start plowing. In this case, you cannot change the settings throughout the entire processing of the site. After processing one area, and the need to move to another field, the system must be configured again, adhering to the same scheme.
During plowing with PLN-3-35, due to its technical characteristics and in order to avoid unscheduled repairs, the following rules should be adhered to:
- you can turn the tractor to lay the next furrow only with the machine in the transport position, as shown in the video below;
- circular plowing is prohibited;
- making sharp turns is strongly discouraged;
- in order to avoid an accident, it is necessary to control the ground clearance.
- when plowing with power adjustment, it is necessary to remove the support wheel in advance. In this case, the required depth is maintained automatically by means of a power regulator.
It is advisable to purchase LN-3-35 directly from the manufacturer. In this case, its price may be 50-60,000 rubles. You can also buy a used device at a fairly low price. If it is decided to buy a PLN-3-35 plow from agricultural machinery dealers, then its price can go up to 80,000 rubles. This largely depends on the region and the margin set by the seller.
The PLN 3-35 plow is adjusted on the adjusting platform before use when plowing the field. First, you need to install spacers for the support wheel of the plow under the left wheels of the tractor, on which we attach the plow. The spacers are installed 20-50 mm less than the depth that we are going to plow.
After that, lower the plow so that all plowshares touch the surface. Then use the plow wheel screw mechanism to place the support wheel on the spacer. Now you need to adjust the plow in the longitudinal and transverse planes.
To do this, align it in the longitudinal plane with the tractor's hitch, and in the lateral plane with the central link. The main thing is that the plow is parallel to the surface in both planes. On the front holes of the plow's upper link, we need to install the braces of the tractor's hitch.
We connect the frame and the top link using the CA-1 automatic coupler through the openings and nothing else.
Under no circumstances use the grooves to hold them together, otherwise the plow will then walk with a shaker during operation.
Adjust the skimmers on the plow depending on how deep you want to plow the soil. Place the socks of the skimmer shares 25 centimeters from the body. The holder has a cylindrical protrusion. Insert this tab into one of the blind holes in the skimmer strut.
Attachment chains tractors serve as plow restraints.They are secured with screws. In this case, the chains should hang slightly. All this is required so that when transporting to the ground the plow does not stagger by more than 2 cm. Now pull up the field edge of the skimmer so that its field edge of the body is covered by the edge of the skimmer.
Now we need to place the left brace of the tractor canopy between the pivot pins. The distance between them should be 51.5 cm.
Before working on the ground, do not under any circumstances change the length of the brace that has already been adjusted by us.
Before starting work, we need to set the plowing depth in front of 2/3 of the previously set on the support wheel. After we have passed the first furrow, we complete the setting of the PLN 3-35. Make sure the frame remains parallel to the surface. Make sure that all plow bodies plow the soil to the same depth.
Make sure that all plant residues are properly milled. If the left side is lower than the right, reduce the brace of the attachment. If the left side is higher than the right, instead, increase the canopy brace.
In the event that the rear plow body plows deeper or shallower than the front, it means that the upper link must be lengthened or shortened.
And lastly: if you plow the land with a power regulator, you do not have to use the support wheel, since the plowing depth control during work will be automatic.
PLN 5-35 is a five-furrow mounted plow, the task of which is to plow the soil, not littered with flagstone, stones and other debris for grain and industrial varieties. The second figure in the name - "35" means the width of the soil plowing with one body. With a single body coverage of 350 mm, the plow plows to a depth of 300 mm.
The plow is rated for resistivity up to 0.12 MPa and earth hardness up to 4 MPa with absolute humidity up to 25 percent or so. Works at an incline of 8 degrees. The depth of entry into the ground is set with a screw on the support wheel. The support wheel forms part of the plow together with bodies, frame, skimmers and braces.
The productivity of such a unit is up to 1.57 hectares / h for 1 hour of main time. Plows of this brand are endowed by manufacturers with high-speed hulls. Working speed - from 8 to 12 km / h. PLN 3-35 is aggregated in tractors with a capacity of 30 kN, such as T-150K and T-150.
As an option, we can consider the image and description of the PLN 5-35 plow manufactured by the Almaz company.
The plow frame consists of a main and additional (longitudinal) beams, cut in the form of a pipe. Plow body holders are attached to these beams. The working body of the plow is bodies and skimmers.
The principle of operation: the coulters bite into the ground, lift the soil, overturn it and throw it on the bottom of the previously plowed furrow. A variant is possible when the client can agree on the manufacture of skimmers to order.
If the bodies of the plow work with the help of skimmers, and not with skimmers, as in the previous version, the skimmers cut off the ball of earth, which raises the body, and drops it to the bottom of the previous furrow. On the formed layer, the body imposes a layer of soil from itself, and therefore, thanks to the use of coal removal, weeds are completely removed, plant residues are sealed and there is the necessary crushing of the soil.
During operation, it is necessary to reduce the central rod, so that the gap under the first body is not less than 250 mm. After that, adjust the length of the attachment chains-stop so that the ends of the lower links dangle no more than 20 mm to the right and left sides.
The design of plows differs in purpose, type of grip and pulling force. A very popular option is a semi-mounted plow, which we considered earlier. This type of plow is attached to the tractor with a canopy and rests on a support wheel. There are other types of clutch as well. So, for example, the mounted attachment is completely attached to the tractor with a canopy (without using a wheel), and the trailed ones are connected to the tractor using a trailed shackle and have three wheels.
The plow consists of a frame, body, skimmers, disc or cutter knife. The body, knife, skimmers are attached to the frame. Of course, the body can also be attached to a so-called beam. The beam is attached to the front end with two chains.
A furrow wheel is installed to the front through the right (major) semiaxis, and a field wheel of the corresponding size through the minor semiaxis on the left. In turn, the body consists of a ploughshare, a blade, a rack and a field board. The principle of operation is that the ploughshare cuts off the soil level we need and thereby digs the bottom of a new furrow, and the blade turns it over, loosens it and throws it aside.
In the process of work, lateral pressure is created on the plow. This pressure arises from the action of the share and blade and is taken over by the field board. Skimmers also have a stand, plowshares and a blade, although they are somewhat smaller than the body skimmers. Depending on the number of bodies on the plow, the units are divided into single-body, double-body, and multi-body. Earlier we looked at three and five furrow semi-mounted plows.
There are also combined plows. Their power is several times higher than that of those described earlier. They are capable of moving at speeds up to 15 km / h. Such mechanisms are equipped with rotors and in their work are guided more by them than by the share and the blade.
You can see below the plow body with its components:
The body can be divided into cultural, screw and semi-screw, depending on what difficulty the earth is capable of plowing. The cultural one is the weakest. He can cultivate old arable soils. The screw is capable of plowing the land, where everything has been overgrown with weeds for years. It is suitable for plowing virgin lands.
To fulfill its functions, it is endowed with excellent revolving power. Between them, a semi-screw hull was wedged in - an aggregate of medium strength, which can cultivate stale, heavily turfed lands. An elongated feather is attached to it, due to which its power is higher than the cultural body.
The design of the bodies is directly related to the soil you have to plow. So, if you need to work on heavy soil with active crushing of the layer under the root of the tuber crops, you need to use the combo box.
The design of such bodies has a shortened blade and a share, but there is a rotor, which receives its drive from the tractor power take-off shaft and with its blades actively crushes difficult-to-work soil. At the same time, the load on the share and dump is reduced by 25-30%, and the efficiency of formation crushing increases by 10-20%. The consumption of wasted energy is more by 13-26%, but it's worth it.
Also, we will consider the device of a horse plow. This device is the most primitive of the ones we are considering. The factories produce one- and two-body horse plows, leading and non-leading. Horse plows consist of a ploughshare, a knife, a blade, a skimmer and a field board.
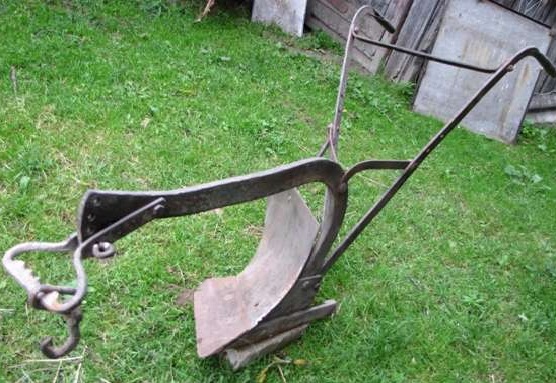
The most common horse plow brand is PV-23, a hanging plow. "Hanging" means a plow that either has no front wheels or has one wheel and a small one. In the process of work, the plowman supports such a plow with his hands. The PV-23 case belongs to the cultural type devices.
Table of contents: naveska na mtz belorus Why do you need a hitch for MTZ, installation and examples of use Trailer for the MTZ tractor and their types MTZ power take-off shaft - purpose and characteristics [...]
Table of contents: Diagram of the MTZ 82 tractor Diagram of the electrical equipment of the MTZ 82 tractor Transmission of the MTZ 82 tractor description, photo Diagram of the suspension on the MTZ 82 Diagram of the MTZ 82 tractor The MTZ 82 tractor is made according to the usual, standard scheme, as well as [...]
Table of contents: Plow share and general purpose plows General purpose plow. Use and adjustment Plow frame - device, description Moldboard plow: pros and cons A suitable plow for the T-40 Plow share and [...]
Table of contents: Plow diagram.Diagrams of different plows and their purpose Plow stand: purpose and design Plow blade description and types Plow plow: device, working bodies and auxiliary parts of the plow Wheeled [...]
Table of contents: The design and operation of the plow Plow diagram How to adjust the plow for plowing The plow blade and its application Working bodies of the plow Plow photo Design and operation of the plow The main working bodies of the plow [...]
Thanks for the article, very instructive. Adjustment of the mounted plow during work.
![]() |
Video (click to play). |
The plow bodies during work must maintain the correct position and go at a given depth. The plow frame (beams) must be horizontal. When the frame is tilted forward, the front plow body plows deeper, the rear shallower; the bodies rest on the toes of the plowshares. When the frame is tilted back, the front body plows shallower, the rear one deeper; the bodies rest on the heels. The correct position of the bodies in the longitudinal direction is achieved by changing the length of the upper link of the tractor hitch. In the first case, it is necessary to lengthen the upper link of the tractor hitch, in the second - to shorten it. The position of the support wheel adjusting screw rod can serve as an indicator of the correct position of the housings. It should be located vertically to the supporting surface; its position is checked with a plumb line (a weight on the thread); the plumb line must touch the propeller shaft along its entire length.