In detail: do-it-yourself repair of a lithium-ion battery of a screwdriver from a real master for the site my.housecope.com.
Lithium batteries are increasingly used in everyday life. Nowadays, they are increasingly found as replacement batteries for screwdrivers and other power tools. Despite their merits, lithium batteries also have their drawbacks.
So, after 1.5 years of operation, the batteries from the DeWalt screwdriver began to discharge quickly, it became impossible to work. The batteries were charged up to a maximum of 14.4 volts, although a standard DCB-107 charger was used for this. In addition, charging took place very quickly, instead of the prescribed 60 minutes, at most 15 minutes.
Before talking about how we managed to solve this problem, I would like to acquaint the reader with the device of a lithium battery from a screwdriver.
This is how the standard DeWalt DCB-145 battery looks like.
To open such a battery, you need a TORX hex screwdriver. The rechargeable battery consists of 4 lithium (Li-ion) "cans" SAMSUNG SDI INR18650-13B with a capacity of 1300 mA / h each. All four "cans" are installed in a plastic box and connected in series using current-carrying plates. The plates are spot welded to the battery contacts. It can be seen that this is a high-quality factory assembly.
I do not advise separating the "cans" of a composite battery by cutting off the connecting current-carrying plates. I did so and regretted it. Next, I'll tell you why you shouldn't.
Batteries SAMSUNG SDI INR18650-13B do not have a built-in charge / discharge controller. Unfortunately, to find documentation for batteries of this particular model (with the index 13B) I did not succeed. But, judging by the parameters of the batteries of this line, the maximum continuous discharge current (Max Continuous Discharge Current) can be from 18 (INR18650-13L) to 23 (INR18650-13M) ampere! Not surprisingly, they don't have a built-in controller.
![]() |
Video (click to play). |
Also in the battery case is a 5-pin connector and a small printed circuit board.
The multi-pin connector is necessary so that when charging, it is possible to control the charge of each of the four INR18650-13B batteries separately. As you know, the voltage is more than 4.1
4.2V for lithium batteries is dangerous and may cause damage or even fire. Therefore, the charger equalizes (balances) the current through each "cell" of the composite battery so that the voltage on each of them does not exceed 4.1V.
Also on the printed circuit board is a temperature sensor, which is adjacent to one of the lithium "cans".
Thanks to the sensor, the standard charging DeWalt DCB-107 measures the temperature of the battery and turns off the charging mode if the battery is overheated or has a temperature below +4 0 C. In addition to the temperature sensor, some kind of circuit is mounted on the board, but it is filled with sealant.
This battery assembly is called “Pack for Power Tool“, That is,“ Package ”or battery assembly for the power tool. This is how it looks.
Large companies like Samsung supply these assemblies for custom-made power tool manufacturers. Perhaps that is why I could not find the exact specifications for INR18650-13B batteries.
We got acquainted with the device of the Li-ion battery for the power tool. Let's go back to our "dead" batteries.
Before the batteries "died" they were very badly discharged. We used a screwdriver until the battery was discharged, and then, after taking a break, we worked with it for a while. After that, the batteries began to charge poorly and did not hold the capacity.
After measuring the voltage on each "bank" of the battery, it turned out that 3 "banks" out of 4 were not fully charged - up to 3.5 volts. Only one was charged to the required 4.1 volts (for Li-ion).
If we add up the voltage of all the cans, we get exactly the same 14.4V.Let me remind you that the standard charger very quickly charged the battery and turned off.
The first thing that came to mind was to replace those lithium "cans" that were not fully charged. But, search for original INR18650-13B returned no results. Perhaps due to the fact that such assemblies are supplied only on order and are not available at retail. And the cost of four new batteries, for example, INR18650-22R practically equal to the price of one DeWalt DCB-145 battery. Therefore, I decided to refuse to replace the batteries at that time.
And, then a sensible idea came to my mind, but it, as always, is late. What if the standard charging failed to properly balance the composite lithium battery after a deep discharge? That is, the standard DeVolt's charger charged one “can” to the required 4.1V and turned off. In this case, the remaining 3 lithium "banks" were not fully charged, but only up to 3.5V.
It was decided to check the standard DCB-107 charger for any malfunction, but it turned out to be in good order. And the new batteries were charged perfectly.
Thus, I came to the conclusion that the stock charger failed to properly balance the composite lithium battery after deep discharge.
It was decided to discharge / charge each 18650 lithium cell separately using a third party charger. For this, a charger was used. Turnigy Accucell 6 (analogue of IMAX B6), which I already talked about.
I discharged each 18650 cell to 3V with a current of 0.3A. Then he charged up to 4.1V with a current of 0.5A. Then he again discharged in order to determine how much current is poured into each specific "jar". This is necessary in order to assess their capacity. As it turned out, the batteries are in good order and each of them was filled with 1164 before 1186 mA... Which is not so far from the declared capacity of 1300 mA / h. Thus, I made sure that the batteries are in good working order and should not be replaced.
After the test (charge-discharge) of each battery, we measure the voltage on each lithium "bank". It should be within 3.1
3.3V each. Thus, the composite accumulator will discharged up to 12.4
Then I collected all the "cans" in a box, soldered the board with a connector and installed it in the case. Set completely discharged the DeWalt DCB-145 battery is already in the standard DeVolt's charging and has registered the time of the beginning of the charging process. As I expected, after 1 hour (60 minutes, as indicated in the instructions), the charging was completed.
As a "test shot" I measured the voltage at the terminals B + and B-... It amounted to 16.4Vas it should be for a fully charged battery.
Thus, it was possible to restore two DeWalt DCB-145 batteries and avoid wasting money on the purchase of new batteries, the total cost of which is almost equal to the cost of an inexpensive screwdriver.
Now I'll tell you about the "rake" that I stepped on.
Attention! The assembly must be done very carefully and not to allow a short circuit between the terminals of the "cans" and those conclusions that go to the balancing connector. If you close something with pliers or tweezers, then fireworks from sparks are provided! I was convinced of this in practice. The currents are such that a wire with a cross section of 0.5 mm. melt like it's the thinnest fuse wire.
I also strongly advise against separating lithium cans by cutting or biting the connecting conductive plates that are welded.
First, there is no need for this. You can charge each "can" simply by connecting the leads of the charger to the poles of the required battery. The only thing that may be required is to unsolder the balancing connector leads and temporarily remove the connector itself from the assembly.
Secondly, you can damage the insulation of lithium batteries and, because of this, short-circuit them.
Third, after the lithium "banks" are tested, the question of connecting them together will arise. And even if the plates can be soldered together, then putting such an assembly back into the case will be a very time-consuming task. The battery case is very tightly fitted to the dimensions of the assembly.
This went on for a long time, until in 1907 the Canadian inventor Peter Robertson patented the Robertson screw with a standard square hole, into which a screwdriver tip was inserted. Since that time, screws began to be produced on an industrial scale and used in households. Later, in 1934, inventor Henry Phillips redesigned the head of the screw and a Phillips screw was introduced into which the corresponding screwdriver was inserted. By that time, the engine had already been invented and the idea of creating a "screw and screw rotator" was in the air. However, there were big problems with the batteries - their weight and dimensions. The problem was solved only in the 1980s, when the first nickel-cadmium Ni-Cd and lithium-ion Li-Ion rechargeable batteries appeared.
The USA and Japan were the first to master the production of household and professional cordless drills and screwdrivers. All this happened thanks to the emergence of new energy-intensive batteries of electricity. We will urgently change them inside the Interskol DA-10 / 10.8 ER cordless drill-screwdriver that fell into my hands. The malfunction was like this - when the button was pressed, the engine simply did not spin, but the LED lit up, though the light was weak.
Let's start repairing the screwdriver battery. We remove the battery from the handle of the screwdriver and unscrew the three self-tapping screws that are located under the sticker at the bottom.
After unscrewing the screws, carefully push back the hooks of the latches, as in the photo. And remove the bottom of the plastic battery case.
Inside we see lithium-ion cans Chinese company HighStar model ISR18650-1300 Li-Ion. This means that the batteries have never been changed. Because it is known that Interskol purchases batteries from this company and inserts them into almost all of its cordless tools.
The photo below shows the insides of the screwdriver battery in all its glory with three cans, which were produced already in 2011. These batteries lasted five years during active use at a construction site. So the result is very decent. Usually they die earlier, probably in cold weather they were not exploited.
To replace the battery cells, you need to disassemble it even more. I advise you to remember the location of the plus, minus and charging contacts so as not to confuse the wires when reassembling.
Pay attention to the voltage control board on the batteries - especially often stabilizers and protective diodes fail on it. It is imperative to ring suspicious radioelements on this board with a multimeter.
We check the voltage at the output of the battery - it turned out 4.4 volts, and it should be 3.7 x 3 = 11.1 volts in the norm and 10.8 volts with the minimum charge of the batteries. In general, the banks are dead - they need to be changed unambiguously.
This can be done in several ways - you can unsolder the wires that go to the board.
You can also simply remove the contacts from the top battery cover. The photo shows the shape of the curved contacts, so you can easily remove them yourself.
Under the plastic cover, we see how the batteries are connected to each other. Their spot welded... This solution is used in almost any battery of another tool. This is a safe and gentle battery connection. At the same time, the destructive heating of the lithium batteries themselves is minimal.
Gently tear off or bite off the metal tape with pliers to disconnect the cans from each other. From the side of the board, they were also connected with a tape and glued to a cardboard gasket. This is done so as not to short-circuit anything on the board. Remember to put it back in place when reassembling the battery.
Due to the lack of a spot welding device, new lithium-ion batteries will be soldered very quickly with a well-heated powerful soldering iron. We remember that heating lithium-ion batteries reduces their service life and is generally explosive.
Pay particular attention to the condition of the wires inside the battery. They can be broken or frayed. They need to be qualitatively isolated or replaced with fresh ones. Since I was repairing a screwdriver battery on the road in the field, I had to apply a brilliant invention of the engineering mind. He took out a blue radio-technical electrical tape.
When disassembling the battery of the Interskol DA-10 / 10.8 ER screwdriver, I was pleasantly surprised - a thermal sensor was installed in the budget screwdriver to control the temperature of the batteries. It turns out that when the lithium cans overheat, the protection circuit turns off the power until the temperature returns to normal. True, the owner never managed to drive him into such a regime. We carefully tear off this thermal sensor so as not to break it - then we will place it in the same place on new cans.
can be done in different ways, for example with thick wires. I decided to solder a torn-off metal strip taken from old cans. First, I tinned the tapes in the places of future contacts on both sides. Later I tinned the battery contacts with a well-heated soldering iron with a drop of solder. But so that they do not get too hot - let them cool down. Then he pressed the tape to the contacts of the cans and soldered the tape again without severe overheating of the battery cans.
The minus leads are the hardest to solder, but with a good flux, things go very quickly. True, then it is better to wash the flux afterwards to clean the insides of the battery.
Now comes the most important thing. What batteries were used when repairing the battery of the Interskol DA-10 / 10.8 ER screwdriver, you ask? Well, I won't hide. These were the most Chinese of the cheap cans that the owner of the device honestly bought in the store. Batteries of standard size 18650 firm Bailong with a fictitious capacity of 8800 mAh. This is of course a laugh and God forbid that they have a 2200 mAh battery. Judging by how long the screwdriver worked after repair on a full charge. I would reduce this figure by a factor of two. But nevertheless, the screwdriver was urgently repaired and it pleases the owner.
When assembling, do not forget to replace the cardboard gasket between the banks and the board. This is so that the fresh soldering does not short-circuit anything on the board.
This completes the repair and restoration of the lithium-ion battery of the Interskol DA-10 / 10.8 ER screwdriver. Almost all batteries are repaired in much the same way. popular manufacturers of screwdrivers: Bosch, Makita, DeWALT, Metabo, Hitachi, Elitech, Skil and my favorite Bison. This concludes my story about repairing a screwdriver battery. Ask questions in the comments. Better yet, in the appropriate thread on our forum or write to the Solder Master personally by mail.
Best regards, Solder Master. Happy repairs!
solar panels novosibirsk do it yourself, reviews of solar controllers, review of solar panels, testing, electric transport, LEDs, motor wheel, do it yourself, solar panels
To begin with, there are a lot of videos on the Internet on recovering batteries from screwdrivers, and they are all the same as a mirror, a brief description of the recovery process that these people offer is that we take the battery, push it with a power supply or another battery, then charge and we use it, and it’s strange that someone doesn’t look, but what kind of stress will be on him when he lies down for a week or two. I propose a completely different way to restore
Which does not just charge and use until the battery dies again. And the one that you did and use as a new battery until the need arises.This method was filmed in draft about a month ago, but I never dared to post it on the site, I just didn't want to reshoot it for a more correct explanation. And frankly speaking, I have very little free time lately.
But now the time has passed which has shown that the recovery option that many people on the network offer to use are not destined to live for more than a certain period of time. And my version, even after 2-1 month of inactivity, as if nothing had happened quietly works and charges, I still tried to shoot a new video clip, where I will try to tell everything.
In fact, everything turned out to be very simple, and in this I was helped by the NI-CAD 1.2V battery I disassembled, which showed me that even with all the zeros on the outside of the device, the patient inside is rather alive than dead and feels very good.
An attempt to regenerate the bus relative to the collector plate was done using distilled water, and the process was quite successful, as a result of which I came up with the easiest way to restore them even without disassembling the batteries!
It is enough to drill a hole in the accumulator in the place behind the rollers +, and pour 20-40 ml of distilled water into it. after a couple of cycles, the hole is slightly covered with silicone.
Before repeating, I recommend watching the video, where I tried to describe the process in more detail.
If you are not sure or afraid of ruining a damaged battery, for example, you can do this with one battery.
If your batteries have voltage and are within the operating range, then you may have a problem with the following:
- faulty charger
- the thermal protection of the battery pack has worked
- there is one battery in the battery pack that has dropped to 0 Volts.
Also, if you notice that the drill began to work somehow sluggishly and at the same time it works as long in time after charging, then you most likely have a problem in one or more batteries that are at zero!
A very interesting effect on the battery capacity, it was equal to or slightly more than the indicated battery capacity after restoration by this method.
Or sign in with these services
Your post must be verified by a moderator
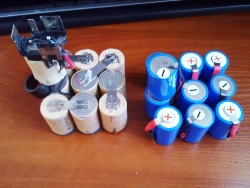
The cost of a new screwdriver is approximately 70% of the cost of the battery for it. Therefore, it is not surprising when, faced with a battery failure, we ask ourselves the question - what's next? Buy a new battery or screwdriver, or maybe it is possible to repair the screwdriver battery with your own hands and continue working with an already familiar tool?
In this article, which we conditionally divide into three parts, we will consider: the types of batteries that are used in screwdrivers (part 1), their possible causes of failure (part 2) and available repair methods (part 3).
It should be noted that regardless of the brand of the screwdriver and the country of the manufacturer, the batteries have an identical structure. The assembled battery pack looks like this.
If we disassemble it, we will see that it is assembled from small elements that are assembled sequentially. And from the school physics course, we know that elements that have a serial connection harmonize their potentials.
Note. The sum of each battery gives us the total voltage at the contacts of the battery.
Typesetting parts or "cans", as a rule, have a standard size and voltage, they differ only in capacity. Battery capacity is measured in Ah and is indicated on the cell (shown below).
For the arrangement of screwdriver batteries, the following types of elements are used:
- nickel - cadmium (Ni - Cd) batteries, with a nominal voltage on the "banks" of 1.2V;
- nickel-metal hydride (Ni-MH), voltage across elements - 1.2V;
- lithium-ion (Li-Ion), with a voltage of 3.6V.
Let's consider in more detail the advantages and disadvantages of each type.
- The most common type due to its low cost;
- Low temperatures, such as Li-Ion batteries, are not scary;
- It is stored in a discharged state, while retaining its characteristics.
- Produced only in third world countries, due to toxicity during production;
- Memory effect;
- Self-discharge;
- Small capacity;
- A small number of charge / discharge cycles, which means that they do not "live" for a long time with intensive use.
- Environmentally friendly production, there is an opportunity to purchase a high-quality branded battery;
- Low memory effect;
- Low self-discharge;
- High capacity compared to Ni - Cd;
- More charge / discharge cycles.
- Price;
- Loses some of its characteristics during long-term storage in a discharged state;
- It does not "live" for a long time at low temperatures.
- No memory effect;
- Self-discharge is almost absent;
- High battery capacity;
- The number of charge / discharge cycles is several times greater than that of previous types of batteries;
- To set the required voltage, a smaller number of "cans" are required, which significantly reduces the weight and dimensions of the battery.
- High price, almost 3 times in comparison with nickel - cadmium;
- After three years, there is a significant loss of capacity, because Li decomposes.
We got acquainted with the elements, let's move on to the rest of the elements of the screwdriver's battery pack. Disassembling the unit, for example, for repairing the battery of a Hitachi screwdriver (pictured below), is very simple - we unscrew the screws around the perimeter and disconnect the case.
The housing has four contacts:
- Two power ones, "+" and "-", for charge / discharge;
- Upper control, it is switched on through a thermal sensor (thermistor). A thermistor is necessary to protect batteries, it cuts off or limits the charge current when a certain temperature of the cells is exceeded (usually in the range of 50 - 600C). Heating occurs due to high currents during forced charging, the so-called "fast" charging;
- The so-called "service" contact, which is connected through a 9K ohm resistance. It is used for complex charging stations that equalize the charge on all battery cells. In everyday life, such stations are useless, due to their high cost.
That's actually the whole design of the battery. Below is a video on how to disassemble a block.
We figured out the purpose of the battery structure elements, now we will consider how to determine the malfunction, this is part 2 of the screwdriver battery repair. Immediately, we note that all the elements cannot fail at once, and since our circuit is sequential, when one element fails, the whole circuit does not work. Hence, our task is to determine where we have the weakest link in the chain.
For this, we will need a multimeter, and for the second method of troubleshooting a 12V lamp, if your battery for a screwdriver is also 12 volt. The procedure is as follows:
- We put the battery on charge, wait for the signal of a full charge.
- We disassemble the case and measure it on each battery bank. For Ni - Cd, we should have 1.2 - 1.4V, in lithium - 3.6 / 3.8V.
- Check all "banks" in which the voltage is less than the nominal one. For example, most Ni - Cd cells have a voltage of 1.3V, and one or more - 1.2 / 1.1V.
- We collect the battery and work until a noticeable loss of power.
- We remove, disassemble and measure the voltage drop across the "banks" of the battery. On the marked elements, the voltage "sag" will be greater than on others. For example, they are no longer 1.2V, but 1.0V or even lower.
Note. The difference between the cells in the battery of 0.5 - 0.7V is considered significant, which means that the cell becomes unusable.
Thus, we have found candidates for "resuscitation" or "amputation" and replacement with new elements.
If your screwdriver operates on a voltage of 12 or 13V, you can search with a simpler method.We disassemble the fully charged battery and connect a 12 volt lamp to the contacts "+" and "-". The lamp will be a load and will drain the battery. Next, we take measurements on the battery cells, where the voltage drop is strongest, there is also a weak link.
There are other ways, instead of a lamp, you can choose a resistance, but for this you already need the basics of electrical engineering, and it is doubtful that a resistor with the necessary resistance would be at hand.
Other faults are very rare. For example, loss of contact at the soldering points of the batteries or the power contacts of the unit, failure of the thermistor. This problem is more inherent in fakes. Due to the rarity, we will not focus on the battery elements.
We have dealt with the "problem" elements, they need to be repaired. How to repair a screwdriver battery? In general, 2 methods are available for repair, so to speak. This is the restoration and replacement of elements that have become unusable.
Let's proceed to part 3 of repairing a screwdriver battery and immediately make a reservation that the concept of "resuscitation" for lithium - ion batteries is not applicable. There is no memory effect in them, most likely, lithium decomposition has occurred, and nothing can be done about it. In such batteries, it is necessary to find out what the cause of the malfunction is: the element itself or the control circuit. There are two options here:
- we change the control scheme from another, but similar to ours, battery, if it helps, we find a replacement and change it;
- apply 4V to a cell with a current of about 200mA, this requires an adjustable charger. If the voltage on the element rises to 3.6V, the element is working properly, the problem is in other elements, or in the control circuit.
Screwdriver battery refurbishment is available primarily for Ni - Cd batteries, but these are usually the most common in household screwdrivers.
So how to reanimate a screwdriver battery? There are two types of "resuscitation" for these types of batteries:
- The method of compaction or compression (it will work in cases where the electrolyte is still present, but the volume is lost);
- "Firmware" voltage and current greater than the nominal. This method allows you to eliminate the memory effect, and although not completely, but restore the lost capacity.
This method is shown below in the video.
Note. As a rule, in a nickel - cadmium battery, the main reason for the loss of capacity is the boiling off of the electrolyte, and if it is critically small, no "firmware" will help.
This method, if its result is positive, will not solve the problem of failure of elements. Rather, it will only postpone the replacement of those that have become unusable and in the future you will still need to repair the battery of the Makit screwdriver or any other.
A more effective way to repair batteries for a screwdriver is to replace elements that we have identified as faulty.
To carry out repairs, we need either a "donor" battery, in which some of the elements are in good order, or new "banks". It will not be difficult to purchase them, even on the Internet you can easily find a dozen stores that are ready to send these items by mail. The price does not bite too much, for example, a nickel-cadmium cell with a capacity of 2000 mAh costs around 100 rubles.
Note. When purchasing a new element, make sure that its capacity and dimensions coincide with the native elements.
We also need a soldering iron, a low-corrosion flux (preferably an alcohol flux for rosin) and tin. We are not talking about spot welding, since there is hardly a need to purchase or assemble it for a one-time battery repair ...
There is nothing complicated in the replacement itself, especially if you have at least some experience in soldering. In the photographs, everything is shown in sufficient detail, we cut off the faulty element, instead of it we solder a new one.
Several nuances should be noted:
- when soldering with a soldering iron, try to solder quickly, so that the battery does not heat up, because risk spoiling it;
- if possible, implement the connection using native plates, or use the same copper plates, this is important because the charging currents are large and if the cross-section of the connecting wires is incorrect, they will heat up, respectively, the thermistor protection will be triggered;
- in any case, do not confuse the plus of the battery with the minus - the connection is sequential, which means that the minus of the previous can goes to the plus of the new can, and the minus of the new one goes to the plus of the next one.
After the new elements have been soldered, it is necessary to equalize the potentials on the "banks", since they are different. We carry out a charge / discharge cycle: we set it to charge overnight, give it a day to cool down and measure the voltage on the elements. If we did everything correctly, the picture will be something like this: on all elements the same indicator of the multimeter, within 1.3V.
Next, we proceed to discharge the battery, insert the battery into the screwdriver and load it "in full". The main thing is to spare the screwdriver itself, otherwise you will have to repair it too. We bring it to full discharge. We repeat this procedure two more times, i.e. charge and discharge completely.
It should be noted that the procedure for erasing the "memory effect" should be carried out every three months. It is carried out by analogy with the above-described training.
Such a not very tricky procedure will prolong the operation of your screwdriver, at least until you have to replace it with a new one.
Screwdrivers are used in different conditions and the degree of stress they have is different. Therefore, they differ in their power, which directly depends on the battery. If an element breaks down, you need to be able to carry out prompt repairs with your own hands.
By their design features, batteries are distinguished in the form of sliders and clips.
But these are insignificant differences compared to the types of batteries. Both the slider and the clip are used in different types of batteries.
There are three types of cordless screwdriver batteries:
- Nickel - cadmium (Ni-Cd).
- Nickel - metal hydride (Ni-Mh).
- Lithium - ionic (Li-Ion).
Lithium polymer batteries (Li-Pol) are not available for screwdrivers. Their main areas of application: smartphones, cell phones, tablets, laptops, radio-controlled devices, electric vehicles.
Nickel - cadmium batteries the cheapest, fast charging, have more than a thousand charging cycles. The batteries are resistant to use in low temperatures. But they have a memory effect. That is, they can be charged only after a complete discharge, otherwise the capacity will fall. They have a high self-discharge current. They are made from toxic materials and are difficult to dispose of. These batteries are in the highest demand.
Nickel - metal hydride batteries more expensive, non-toxic, have a low memory effect. Self-discharge current is higher than nickel - cadmium. The capacity is higher, the charge cycle is more than five hundred. These batteries do not tolerate high discharge rates worse. They are less suited to making the most of the power of the tool. They need to be constantly recharged.
Lithium Ion Batteries more expensive, more powerful, fast charging. They have no memory effect. Low self-discharge current. The voltage of the battery cells is higher, therefore their number is lower. Consequently, the dimensions and weight of such batteries are less than that of nickel ones. But they cannot be completely discharged, otherwise after several such cycles you will have to buy a new one. To improve the quality of lithium-ion batteries, manufacturers install a microcircuit in the battery or screwdriver case that monitors battery performance. A multi-level multi-stage protection is formed:
- From high fever.
- From full discharge. These batteries are afraid of full discharge and cannot recover if the discharge is below the permissible rate.
- From short circuit.
- Overcharge, as an explosion may occur.
- From overload currents.
The control board installed in the battery case is more efficient. When the battery lies separately from the screwdriver and is not used, the microcircuit monitors its condition and opens the circuit in case of any problems. The battery is fully protected.
What can be the problem with the batteries:
- flows;
- not removable;
- decreased capacity;
- not charging;
- the charging and discharging times are reduced.
Nickel batteries can be recovered. And lithium is not allowed, since lithium decomposes in them. Here you can only replace the unusable batteries.
Please be patient and proceed with the repair.
Disassemble the battery carefully. Do not use force to avoid damaging the case.
- Remove the battery from the screwdriver. If the buttons are stuck and it does not come off, unscrew the screws on the tool body and remove the top half. One of the buttons was released. Pull the battery towards you, slightly wiggling it in different directions, and it will also come off. When you disassemble the battery, position the buttons so that they easily press into their grooves.
- The battery case consists of two parts and can be collapsible and non-collapsible. In the first case, unscrew all the screws and separate both parts.
Several sequentially welded elements are located inside. This cassette provides the required voltage and current characteristics for the battery. Some nickel batteries have a thermal sensor attached to the cells.
Things get more complicated with lithium-ion batteries. There is a control board, and the elements are wrapped in a protective case or film.
A new battery must be fully charged before use. The average ambient temperature is from 10 to 40 degrees. The chargers have indication lights. When they show that the battery is charged, you must immediately turn off the process.
- New nickel-cadmium batteries must be rocked before first use. Fully discharge and charge three times. The capacity will become maximum. If the instructions for the device say that the buildup should include a larger number of charge cycles, then follow these recommendations. During operation, completely discharge the battery before charging.
- Nickel-Metal Hydride batteries have less memory effect, so they can be swung once before using for the first time.
- Lithium ion batteries do not need to be rocked. Simply charge them up to full power.
A 12 volt lamp load is used to discharge the battery. It is connected by crocodiles to the terminals. If the battery is disassembled, then to the terminals of the serial circuit of the batteries. The discharge process will take less than an hour.
The second way to properly discharge is to use a "smart" charger such as imax b6, which is very convenient to swing the batteries. In it, you can adjust the parameters of the current and voltage for charging and discharging the battery. Set the automatic cycling mode to swing the battery. That is, you do not need to constantly monitor the capacity and voltage. The device will do it for you. Up to 5 cycles are provided. And at the end you can see the current and voltage values after each cycle and analyze the result.
After fully charged, disassemble the battery. Examine elements for bulging and oxidation. Measure the voltage of all elements with a multimeter or tester. Voltage limits for different batteries:
- For nickel - cadmium 1.2 - 1.4 volts.
- For nickel - metal hydride 1.2 - 1.4 volts.
- For lithium - ion 3.6 - 3.8 volts.
The battery cans are paper wrapped. The voltage is applied to each element. If all cells have normal voltage, discharge the battery to half the capacity. Measure the voltage again. Those elements in which the voltage has dropped by 0.5 - 0.7 volts compared to the average must be restored or replaced. They say about such banks "flows".
If the charger is ok, check the contacts between the battery and the charger. The contacts of the charger could be straightened. This prevents the battery from charging. Disassemble the device and bend the terminals. The second reason may be a faulty or sealed temperature sensor. It needs to be soldered or replaced with a new one.
If the contacts of the battery, charger and tool become oxidized or dirty, the battery will quickly charge and discharge. Wipe the contacts periodically.
Boil-off of electrolyte occurs due to accelerated charging and overcharging. If the cells are not swollen and after a full charge show the operating voltage, they can be restored without replacement. It is necessary to replenish the empty volume with distilled water.
- After identifying the defective cans, cut the connecting metal tape. Unsolder the elements.
- Take a punch no more than 1 millimeter thick. Where the can has a minus, make a hole in the body.
- Pump out air up to 1 cubic centimeter and pour in the same amount of water.
- Seal the elements with epoxy and connect them to the circuit.
If this method did not help, then replace the cans with new ones.
When you have diagnosed and identified defective jars, you need to purchase a replacement. New elements must be completely the same in size and technical characteristics.
- Cut or unsolder old elements from the plates.
- Put new ones in their place. Use the same plates or copper conductors of the same cross-section for the connection.
- So that the cans do not overheat, do the soldering quickly. Observe the polarity of the series circuit. Connect plus with minus, and minus with plus.
Many owners of a screwdriver with a nickel-cadmium battery have faced such a problem that when you need to use it, the battery is always discharged. And constant charging kills her due to the memory effect. Therefore, such a battery is converted to a lithium-ion one.
![]() |
Video (click to play). |
Lithium batteries can be sourced from an old laptop battery, or you can buy new ones. Laptop and new banks are unprotected. You cannot use them without protection, because you will not be able to charge them and control the discharge. And when overcharged, they will die safely. It is allowed to connect in parallel exactly the same batteries, then they will work as a whole. Purchase a battery protection module for series-connected batteries that monitors and takes care of each cell individually. Monitors voltage and current, provides short circuit protection. Such modules are available for one, two, three and four batteries.