In detail: do-it-yourself Volkswagen pump nozzle repair from a real master for the site my.housecope.com.
Attention! Car service network of favorable prices. Camber check is FREE! No queues! Repair on the same day!
Download / Print topic
Download a theme in various formats, or view a printable version of the theme.
wimial - DMRV put new and no changes
USR - I will check today
———- The message was added at 13:53 ———- The previous message was at 13:51 ———-
wimial raves about the mass air flow sensor. USR, don't pay attention

look for where the hoses were removed, the gasket was squeezed out, the clamps were confused. how much pressure on vag?
———- The message was added on 03/06/2012 at 00:04 ———- The previous message was on 03/05/2012 at 23:54 ———-
He took off the USR of course, dreaming, washed it and put it back.
No change.
———- The message was added at 00:08 ———- The previous message was at 00:04 ———-
Guys, please tell me how much the lace costs and where you can buy it.
———- Message added at 00:11 ———- Previous message was at 00:08 ———-
wimial raves about the mass air flow sensor. USR, don't pay attention

look for where the hoses were removed, the gasket was squeezed out, the clamps were confused. how much pressure on vag?
as well as new bolts for fastening injectors and rocker arm axles
before starting work, we connected a VAG-com, we saw the spread so often discussed here in the parameters of the operation of the injectors. The first stage took place in my presence. They removed the valve cover. There is good news, there is bad news :-)
the good thing is that the first owner did not deceive me: the oil was really used of high quality and changed in a timely manner, there are no deposits
![]() |
Video (click to play). |
and then - incrementally. The nozzle pushers are worn out,
and worn very unevenly
and the adjusting bolts are worn unevenly, which is why it is impossible to restrict the adjustment of the clearances, only with the obligatory replacement
there are signs of the beginning of wear on the camshaft cam journals. If I am not mistaken - damage to the upper cemented layer (I am not responsible for the terminology)
the reason is faulty hydraulic pushers.
Next, take out the nozzles. Expected picture:
as already discussed in this topic - this is the price for the design feature of the nozzle attachment with one bolt, multiplied by the destruction from the gap leaving.
the preventive work, which my diesel operator spoke about, consists in the regular reinstallation of the injectors with subsequent adjustment. At least once every 100,000 km. In my case, this was not done on time, and we decided to change everything, that is, the camshaft, shaft liners, hydraulic pushers, timing belt and all the mounting bolts.
The Turan Club forum is incredibly full of useful information. True, over the years, each topic has grown so much that it can be difficult to find everything you need and useful in one place. Therefore, I will add a couple of notes on my own:
-my diesel operator not only took out the nozzle, replaced the seals and put it back in. In his words, the stubborn platform often suffers. And he certainly rules them. And on the surface, and in geometry, because they are also "trampled" with a slope.
With the help of these custom cutters:
if you have to remove a lot, picks up thicker washers to compensate for the immersion of the nozzle
- the injectors are placed in one position, determined by the stop and the bolt. But even at the same time, there is a small spread
but should be strictly parallel
ELSA has a distance plate:
He explained that if the injector is skewed, then the fastening bolt can loosen, which will lead to damage to the injector or the cylinder head, experimentally found that even the sound of the engine changes :-) This is determined by the fact that when the injector is deflected, the spray of the injected fuel also changes ... And he vividly portrayed “in faces” 🙂
and he also showed what driving with a cleared gap leads to:
and to this: (wetsuit not from my motor!)
As I already wrote, there were no warning signs in the operation of my motor. However, having removed the camshaft, my diesel operator assumed that this position would remain no more than 5000 km.
If the power of the tdi engine suddenly dropped, it began to make noise and smoke a lot during operation, the fuel consumption increased and there were problems with starting, then it’s time to pay attention to the condition of the injectors. Repair of pump injectors will help. Volkswagen will find new life!
Injectors are mechanical atomizers responsible for the smooth operation of a tdi diesel engine. Their task is to atomize the fuel. A huge load falls on this part, because the injectors supply fuel to the combustion chamber under high pressure, which inevitably leads to their wear.
Repair of diesel injectors is required at the moment when the first prerequisites for their wear began to appear. The condition of the atomizers is affected by low-quality fuel and corrosion.
Deviations in work requiring intervention:
- Uneven atomization and fuel injection;
- Carbon deposits on fuel holes;
- Violation of the tightness between the nozzle body, spacer and the sprayer body;
- Reduced fuel flow caused by coking;
- Drop in sprayer opening pressure.
The repair of this part can only be trusted by real professionals who know everything about tdi engines, who will be able to pinpoint the cause of the problem. To do this, at the TO station, they check the opening pressure, the mobility of the needle, the shape of the jet of injected fuel.
After discovering the cause, you may be offered the following services:
- Cleaning and adjustment;
- Replacing the atomizer and needle;
- Repair of springs;
- Replacing the washer between the spray gun and the nozzle.
- The first thing to do is to remove the head cover and soundproof cover.
- Now it is necessary to rotate the crankshaft until the pair of cams of the pump injectors evenly point upwards.
- The lock nuts are unscrewed at the adjusting screws, and the screws themselves are unscrewed so that the rocker arm rests on the pusher spring of the pump injector.
- Using the end cap, it is necessary to unscrew the securing bolts of the second axis of the roller levers.
- Remove the roller arm.
- Remove the spacer by first unscrewing the fastening bolt from it.
- Using a screwdriver, unplug the pump injector plug by slightly holding the reverse side of it.
- Install the puller into the side groove in place of the spacer and carefully remove the pump injector from its seat.
Attention. It is necessary to carry out repairs as carefully as possible so as not to damage the tdi engine parts.
After the nozzles are removed, you can proceed with the installation.
- Lubricate O-rings with grease.
- Install the pump nozzle into the socket on the head of the block, pressing it evenly until it reaches the end.
- Install a spacer in the side groove of the pump injector.
- The fastening bolts must be screwed into the spacer until the nozzle rotates easily.
- Install a new lever shaft and tighten the retaining bolts.
- Tighten the adjusting screw, which will compress the spring until it resists strongly.
- From the “screwed in” position, unscrew the adjusting screw by 180 °.
- Tighten the lock nut.
- Install the plug and cover for the cylinder head and soundproofing.
It is almost impossible to carry out this kind of repair work on a tdi engine on your own. But if you do decide on this, then you should carefully read the valuable advice.
First, when installing a new spray device, it is necessary to replace the corresponding rocker adjustment screw.
Secondly, it is necessary to install the O-rings without twisting.
Thirdly, a crooked pump injector will lead to loosening of the mounting bolt and damage to the block head. Therefore, it is worth installing it strictly at right angles to the spacer.
The pump injectors of the tdi engine are adjusted in the same way as when replacing them.
- The valve cover is removable.
- The crankshaft turns until the camshaft is pressed on one pump injector.In this case, the rocker arm should move upward as much as possible.
- The fixing nut is unscrewed a few turns.
- The adjusting screw is screwed in by hand until it stops until it pushes against the nozzle.
- The adjusting screw turns 180 degrees counterclockwise, relieving pressure on the nozzle.
- The fixing nut is tightened, and do not forget to hold the adjusting screw.
- The crankshaft turns until the camshaft is pressed against the injector.
If you notice a problem with the tdi engine, you should immediately contact a specialist. The less wear and tear on your spray equipment, the less expensive your repairs will be.
Sooner or later, diesel injectors have to be repaired, like other types of diesel engine systems, especially if it has already traveled several thousand kilometers. Fuel consumption begins to increase, and the power of the injector, and, accordingly, the operation of the engine deteriorates. At this moment, the driver realizes that something needs to be done with the injector. Some do not bother with repairs and buy a new one, but it will cost a lot of money.
Sometimes it is much cheaper to restore the working capacity of the nozzle that you removed, but this must be done correctly. In specialized services there is special equipment, with the help of which the shortcomings of work are determined, the device is disassembled and assembled. And then what should those who live far from such services do?
The device and malfunctions of diesel injectors
In most cases, diesel injectors for foreign cars have the same structure, which means that the malfunctions are about the same. When the diesel engine starts to work, the fuel pump rotates a pulley, which under high pressure and the plunger begins to compress the fuel to high pressure, after which it is distributed to each injector.
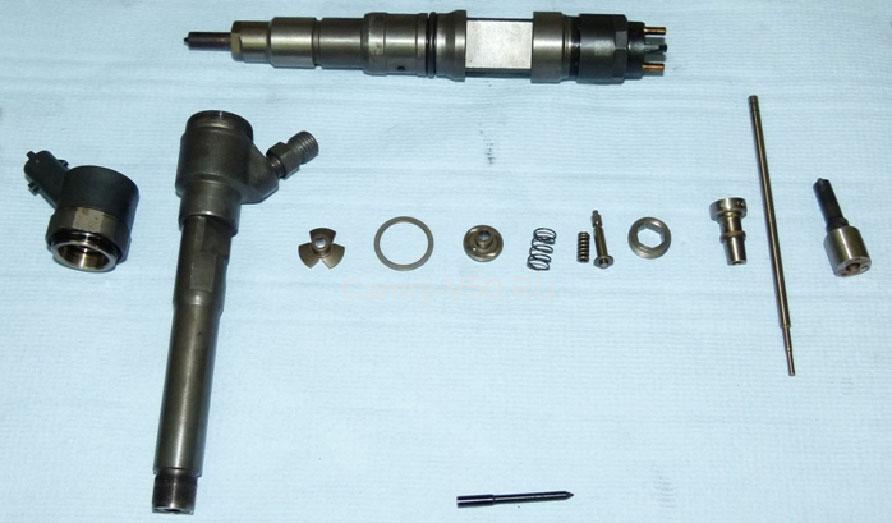
pump nozzle DIY repair
The fuel is squeezed out by the pump and transferred through pipes, which provide for its supply at high pressure to the nozzle, the nozzle expels the diesel through a special channel of the system. In this system, a special needle is installed, which is precisely attached and pressed from above by means of a spring. If the fuel is supplied under high pressure, it immediately reaches the needle. With the help of the plunger, the pressure builds up and increases, then the spring gives in and rises. When the needle is raised through the special holes, the fuel passes through and begins to spray.
Needle problems are the main problems with injector breakage as fuel stops flowing. The engine is in danger, and combustion products begin to enter the nozzle, and fumes accumulate inside, repair is inevitable. You can easily get rid of burns and other microparticles, but with a problem injector, the engine will not perform better. Repair operations with injectors are complex and the main guarantee of a positive result is cleanliness in everything: at work, in the injector and at the workplace. It is recommended to flush the engine before removing the injector. Having repaired a spare part, it will last a long time and will not require replacement with a new one.
In the fuel systems of modern diesel engines, pump injectors are one of the most important and complex elements. They are used for very precise fuel delivery in diesel engines at high pressure. If the fuel supply is disrupted, it may be necessary to repair the Volkswagen pump injectors, which requires high professionalism and modern equipment.
Installed injectors in the cylinder head on each separately. In order to carry out repairs, the first step is to remove the head cover. Next, you should turn the engine crankshaft until the cams with the help of which, the installation is made, will not look up. It will be necessary to unscrew the adjusting screws so that the rocker arm rests on the pump pusher spring.Next, you will need to perform many manipulations using various tools, including the use of special pullers.
In modern foreign-made cars, the repair of automatic transmissions, pump nozzles and many other equipment on Volkswagen cars is possible only in specially equipped car workshops, where experienced craftsmen work. At home or artisanal conditions, it is highly likely that it will not even be possible to remove a part or assembly that requires repair or complete replacement.
High-quality repair of Volkswagen pump injectors is impossible without the use of special high-precision machines, coordinate grinding and other types. After the work on the restoration of parts on special stands, the parameters are monitored, without which it is impossible to be sure of the normal operation of the pump nozzles and other equipment. Equally difficult is the repair and replacement of automatic transmissions on Volkswagen and other foreign cars. It also requires special equipment and a high level of professionalism. Any serious work on the repair and maintenance of foreign cars is possible at large car services, where modern automated and high-precision equipment is used. Therefore, in the event of malfunctions, it is best not to save money and contact only car services with extensive experience and good authority, which will guarantee a long service life of the car after repair work. The advice seems obvious, but it's worth reminding.
Before proceeding to the description of the method of how the pump injector is checked, we first figure out what it is and which parts of it are subject to the greatest wear.
The mechanically driven unit-injector, unlike Common Rail, has the combined functions of generating high pressure (single-plunger pump) and fuel injection. It includes a high pressure pump, a nozzle, a power actuator and a metering valve assembly in one housing. The pump injectors that make up the mechanical part of the control are distant relatives of the parts of the gas distribution mechanism with the fundamental difference that the working fluid in this case, instead of the air mixture, is diesel fuel under high pressure. This allows for increased engine power and torque. Briefly, her work process will look like this:
- The control electromagnet receives a command (electrical impulse) from the ECU to move the valve; the working chamber closes, cutting off the fuel from the line;
- The plunger creates pressure for fuel injection;
- Injection takes place through a "fuel cloud" atomizer, first a preliminary injection and then a main injection.
Such a scheme of work shows that the main mechanisms that are subject to the greatest loads and the most frequent failures are the valve assembly, which actually controls the fuel injection process in these systems and the atomizer that directly injects and the proper atomization for a given cylinder.
The owners of diesel vehicles with fuel injection pump nozzles and facing their failure can be divided into the following main groups:
- cannot start or have difficulty starting the engine;
- have excessive fuel consumption;
- complain about uneven engine operation or loss of power;
- observe an increased smoke of the exhaust.
The process of checking the unit injector
Typical malfunctions of the electronic unit injector:
- The valve assembly comes out in 63% of cases.
- Sprayer at 30%.
- The electromagnetic part will have a 5% chance of failure.
- Plunger, spring, body - 2%.
In an amicable way, the pump injector diagnostics and testing should be carried out in the same way as the common rail at a professional stand, where there will be an imitation of operation in different modes (idle, nominal and accelerated operation).But at home, checking the unit injectors will be limited. By the most elementary method find out one of the reasons when the unstable and hard operation of the engine is observed at full load with such fuel injectors - be careful pinch the return hose on the fuel filterif the work evens out, this indicates that air bubbles are most likely forming in the nozzle. In turn, this phenomenon occurs if the tandem pump does not develop the required pressure or does not reach the design capacity.
If the pressure increases during pinching, it is most likely that the rubber connection between the incoming channel and the return in the unit injector is leaking. If there are no changes, the tandem pump is faulty. Such a check will be more accurate if you connect a pressure gauge to check the fuel pressure. Confirmation of this diagnosis can also be obtained with the help of VAG-com, observing the dynamics in 13 (XX stabilization) and 23 (pump-injector activation time) blocks on a cold and warm engine. An increased variation in parameters with increasing load and temperature will indicate the formation of air locks.
Diagnostics of the main performance indicators of the unit injectors installed on VAG cars can be produce with VCDS software by taking readings on 13 and 14 channels in the section "Engine control unit". The spray correction numbers should tend to zero. By the way the correction indicates not topping up or overflowing, one can more or less accurately say whether the nozzle is clogged or there are problems in the actuation of the valve assembly. When the engine is unstable at idle, and after warming up, its operation is restored, while the balance on some cylinder will be more than 2.5 mg, then its pump nozzle is definitely for repair.
Connecting the pump injector connector
You can also check the resistance of the coil of the electro valvewhen there is a suspicion of its failure. If it does not work, the plunger will supply diesel fuel to the return line. Valve coil resistance should be about 0.5 ohm... Or make another test by applying 5V to the valve (it will click, which means it is okay). On the injector block at the end of the cylinder head, the 7th contact is a common "minus", and positive: the 5th of the first cylinder, the 3rd goes to the second, contact No. 2 is the "+" of the third cylinder, the 6th pin to the fourth. When there is a knock in the engine coming from the injectors, you can connect the connector to the gap with wires and remove the impulse from them at the moment when the knocking is clearly audible, such a test will help determine the knocking unit injector. It will not be superfluous as well check the breakdown of the injector to ground... But still, the most effective method for checking pump injectors at home and without removing is software. So we will dwell on the values of which groups in the "Vasya diagnostician" program to pay attention to.
In order to correctly and accurately determine the nature of the malfunction of the fuel injector of a diesel car, we will find out which groups in the vag com program we will check and what they should show us:
Vag-com diagnostics (groups 13,18,23)
- Group 13 shows corrections to stabilize idle speed and up to 1500 rpm. Reflects the work of the NF (very rarely the cylinder);
- Group 14 - spray difference between nozzles;
- Group 18 - valve status, must be zero;
- 23.24 groups - corrections for cyclic feed, shows how the solenoid valve and the closing spool are triggered. The most objective method for evaluating pump injectors;
- 72-77 groups - injection pressure correction, their values show values at different pressure levels, groups of trainees, due to the operation of the lambda probe, should show values as close to zero as possible.
Now let's take a closer look at what approximate values should be and what it says when the indicator goes in plus or minus.
When correction in 13 and 14 channels from 0 to 1 mg / stroke ideal operation of the injector, up to 2 mg / stroke - normal, and if more than two - very poor quality of the pump injector. That is, the data of these two groups should tend to zero, but when there is a big plus or a big minus, it indicates a performance violation. If in “-“, then NF is crammed, and when in “+”, then you need to additionally look at the data for 23 and 24 groups.
When viewing the readings of the 13th group, it is worth taking into account that the operation of the injector, first of all, changes depending on the degree of compression in the cylinder, and only then on its state, so you should first measure the compression with a pressure gauge in all cylinders, or it is also imperative to check the numerical indicators in the 23rd group. So even if the correction in the 13th group is permissible, it is recommended to take readings in 23.24 groups, because it contains the value that is used by the ECU to control the solenoid valve in the NF in order to ensure the exact moment of triggering.
The ECU, controlling the closing of the solenoid valve, determines:
- injection moment;
- the amount of cyclic feed;
- actual boundaries of changes in the moment of complete closure of the EMC.
The higher value in group 23-24the worse condition of the pump injector... A large number will indicate that the spool response time is too long. This is the time that elapses from the moment the control pulse is applied to the electromagnet until the spool lands on the seat. When on some cylinder, the value exceeds the number 100, an error will be written in the control unit - "The pump injector regulation limit has been exceeded" and the correction for the start of delivery disappears until the engine is restarted. But when we have “-100” on one cylinder, it indicates the presence of gases in the fuel (as a rule, the lower O-ring is to blame), for all cylinders, this is a problem with the fuel priming pump.
The adaptation values in measured value blocks 72 to 77 are also important for the correct operation of the motor, as they indicate the speed of injection learning. For each block of measured values, 3 values are output. These are the set values for the individual cylinders at different pressure levels (300, 600 and 1000 bar). If the value of the injection time correction is minus (for example, at the 1st position lower - 45 ms, and at the 2nd - minus 15 ms) - the needles and injector seats are worn out, as a result of which the control unit reduces the amount of injected fuel. And when the delay is a big plus - a sign of clogged nozzles.
Electromagnetic pump injectors are repairable when the sealing ring is worn, insignificant contamination, damage to the atomizer, but when the EMC and the locking valve are worn, they must only be replaced. Replacement of faulty unit injectors is carried out according to the indices in their designation!
diesel engines with pump nozzles differ from others in that they do not have a high-pressure pump in our usual sense, it (pressure) is created in the nozzle itself when the camshaft cam is pressed.
This design has both pros and cons, and the latter can be judged by the statistics of calls for repairs. Unfortunately, due to the rather high reliability of VAG-ov structures, and the peculiarities of the control system for such an engine, the owner learns about the malfunctions when the cost of refurbishment exceeds all reasonable limits.
Without plunging into lofty matters, let us consider “on our fingers” what happens most often.
Weak point can be safely called hydraulic lifters. Due to the high load, they quickly cease to fulfill their role, but it is very difficult to manage to cut off this moment in a diesel engine.
And then they break the seat in the head, stop rotating and wipe them corny
and sometimes to this state
if the faulty hydraulic lifter is not replaced in time, it starts to dangle in the seat, breaking even more
and can also damage the block head
the camshaft suffers next. A durable layer is erased from its surface
and then the cam is instantly grinded, literally a couple of thousand kilometers.
As a result, the valves stop opening, the motor loses power and stops starting.
It is treated only by replacing the camshaft and hydraulic pushers. It should be noted that you can not bet just that, great attention should be paid to manufacturers if it is not possible to buy the original
But this is not the whole list. As I already wrote, the cam of the camshaft pushes the rocker arm, otherwise it presses on the nozzle through the hinge joint.
As in any movable joint, there is both friction and losses from it.
a change in the gaps leads to an increase in the load on the nozzles, and they do not last forever
on 8 valve motors, the nozzle is fixed with one bolt. And with an increase in shock loads, it begins to gnaw through the block head
and all this again can lead to the need to replace the block head
How can you avoid this? VAG does not regulate any preventive work, but based on statistics that have been accumulated over the years of working with these engines, we can recommend the following: when computer diagnostics of a car, attention should be paid to the parameters of the injectors. By deviations from the tolerance, it is possible to draw indirect conclusions about the state of the drive.
It is also possible to recommend at least once every 100,000 km to adjust the injector drive, with the replacement of the pushers and the counterpart. And if large gaps are found, it would not be superfluous to reinstall the nozzles. That is, you need to remove them, change the seals, “fix” the working surface (restore the geometry) with special sweeps.
well, do not forget that the basis of the durability of the engine is a timely oil change
————————————————————–
I hope someone will come in handy
- Jacob
- Out of town
- Local
- Touran 2006 1.9 VKS
- Posts: 316
- Karma: 84
- Igor1
- Out of town
- Moderator
- golf option / 07
- Posts: 979
- Karma: 89
“Informed is armed” 🙂
I know that there are people who are interested in the long-term operation of their cars, for such such information will not be superfluous.
A diesel engine with a high-pressure fuel pump immediately showed itself as external signs for any deviations from the normal state. The plus and minus of the pump injectors is that as the wear and tear, the electronics will compensate for it so that the owner will not suspect anything. And when external manifestations begin, adjustments will not be enough.
For example, I bought a car on the go, without any complaints, but immediately went to my diesel operator, and here are the results - in the photographs. Another would be a maximum of 5000 km, and the engine would have stopped, and repairs could cost much more
As for the oil, I do not advertise LongLife at all. Moreover, I am an ardent opponent of such a system, and I sincerely believe that the maximum interval between oil changes on a diesel engine is 7500/10 000 km
But when I was looking for what exactly to fill in for myself, the same diesel operator said that so far there is nothing better than the original 506
as usual, the need for this article is inspired by the increasing frequency of appeals on this matter
diesel engines with pump nozzles differ from others in that they do not have a high pressure pump; it is created in the nozzle itself when the camshaft cam is pressed.
This design has both pros and cons, and the latter can be judged by the statistics of calls for repairs. Unfortunately, due to the rather high reliability of VAG-ov structures, and the peculiarities of the control system for such an engine, the owner learns about the malfunctions when the cost of refurbishment exceeds all reasonable limits.
Without plunging into lofty matters, let us consider “on our fingers” what happens most often.
Weak point can be safely called hydraulic lifters. Due to the high load, they quickly cease to fulfill their role, but it is very difficult to manage to cut off this moment in a diesel engine.
And then they break the seat in the head, stop rotating and wipe them corny
and sometimes to this state
if the faulty hydraulic lifter is not replaced in time, it starts to dangle in the seat, breaking even more
and can also damage the block head
the camshaft suffers next. A durable layer is erased from its surface
and then the cam is instantly grinded, literally a couple of thousand kilometers.
As a result, the valves stop opening, the motor loses power and stops starting.
It is treated only by replacing the camshaft and hydraulic pushers. It should be noted that it is impossible to bet just that, great attention should be paid to manufacturers if it is not possible to buy the original. And also always change the fastening bolts and camshaft beds, and the axles of the rocker arms and the nozzles themselves.
Even if the injectors are removed only for diagnostics, pre-stock with repair kits, all seals and adjusting bolts must be changed
If the mileage exceeds 100,000 km, during any work in the head, check the condition of the camshaft bearings.
Unlike gasoline versions, in case of problems with pressure or oil quality, replacing them can significantly reduce the cost of repairs.
But this is not the whole list. As I already wrote, the camshaft cam pushes the rocker arm, otherwise it presses on the nozzle through the pivot joint.
As in any movable joint, there is both friction and losses from it.
a change in the gaps leads to an increase in the load on the nozzles, and they do not last forever
on 8 valve motors, the nozzle is fixed with one bolt. And with an increase in shock loads, it begins to gnaw through the block head
on the traces of uneven wear, you can imagine how the nozzle is warped in the head
and all this again can lead to the need to replace the block head
How can you avoid this? VAG does not regulate any preventive work, but based on statistics that have been accumulated over the years of working with these engines, I can recommend the following: when computer diagnostics of a car, attention should be paid to the parameters of the injectors. By deviations from the tolerance, it is possible to draw indirect conclusions about the state of the drive.
Where and how to look? If on the fingers, then this system works like this: when the engine is started, the same amount of time is injected into each cylinder, and the time it takes for the piston to pass from TDC to BDC is recorded. The older the motor, the greater the difference. The ECU adjusts the amount of fuel injected to equalize the times. Somewhere more, somewhere less. And this correction can be seen in the 13th group. The greater the deviation from "0", the greater the wear. This can be both natural wear of the cylinder-piston group, and a problem with the drive (camshaft, pushers), or with the nozzles themselves. It is impossible to say exactly based on the results of computer diagnostics. But if the numbers in the windows are more than "1" / "- 1", then there is already a reason to remove the valve cover.
It is also possible to recommend at least once every 100,000 km to adjust the injector drive, with the replacement of the pushers and the counterpart. And if large gaps are found, it would not be superfluous to reinstall the nozzles. That is, you need to remove them, change the seals, "fix" the working surface (restore the geometry) with special sweeps.
well, do not forget that the basis of the durability of the engine is a timely oil change, and the use of only VAG approval for units with unit injectors
Reasons for the need to adjust the pump injectors on VW diesel engines
1 Wear of rubber seals for pump injectors on VW engines. Factory recommendation to replace the pump nozzle seal rings every 100 t.km.
2 A copper sealing washer installed on the pump injector passes blow-by gases into the return line. Often occurs with improper installation of the pump injectors. It manifests itself in the absence of thrust when the engine is hot. Diagnosed by computer diagnostics and installation of a transparent hose on the return line.When the engine heats up, blow-by gases enter through the copper plugs of the pump injector and we will see bubbles in the tube and a sharp deterioration in the operation of the pump injectors of the 4th group. the VAG COM program is out of parameters from - 2.8 to +2.8, but errors will not be recorded. Customer complaint about the deterioration of the dynamics of the VW engine with pump injectors during warm-up. It is necessary to replace all seals of the pump injector with subsequent adjustment.
3 Mechanical wear of the piston rod pusher pump injector of the VW engine
Sign up for a service in Kiev by phone. Please agree on the time of your visit to the service.
Kiev +380444015050 Vodafone +380950739377 KivStar +380672362921 +380980540055 Life +380734742669
I give an example of removing the log from group 4. VAG COM program
1 cylinder -0.54 mgH
2 cylinder -0.23 mgH
3 cylinder -0.23 mgH
4 cylinder 1.01 mgH
VAG stipulates an acceptable range for these parameters from - 2.8 to +2.8
The pump injector T5 1.9 T5 2.5 delivers a certain amount of fuel for a certain number of cycles, the response speed and depends on the response speed of the solenoid armature
(controlled by the 23rd group), as well as the speed of the pre-injection valve and the sprayer itself, is not directly controlled by anything, only indirectly.
The amount of fuel is group 13, this is a correction. it is incorrect to consider it in isolation from other parameters. for example, without the first group XX.
Example due to wear and tear. or high mileage, the feed on XX grows. and on all injectors.
You can see these changes in the parameters in the first group, the norm is 4-8 cubic meters
The more uncontrolled fuel the injector will inject into the cylinder, the lower these values will be.
As soon as the XX values fall below 3 cubic meters, the engine will start to work in jerks, twitch, along with this, the values of the first group from 0 to 10 will immediately start to jump and the values in the 13th group. up to overstepping the measuring range.
This will happen because the pump injector T5 1.9 T5 2.5 will grow physically, and the unit will cut it electrically, and he does this only by decreasing the injection time.
Accordingly, the moment will come - that in order to keep xx within the specified limits, the block will cut the injection time so much that the engine stops working normally, it will start.
The XX readings will start jumping and the correction or 13 group will take effect.
For example, in this case, rearranging N.F in places will give nothing or add even more problems.
If all of the above happens with the ode Pump injector T5 1.9 T5 2.5 then this is group 13 in its pure form. In this case, the permutation of N.F in places will give the result.
In general, it is very difficult to diagnose N.F without understanding what for what.
Diagnostics in Kiev at the service station
23 group or response speed. The injector response speed is the time that elapses from the moment the signal is given by the control unit until the moment the fuel is actually injected into the combustion chamber. It is divided into two parts. Electrical - this is the time that elapses from the moment the control unit sends a signal to the actual activation of the injector control solenoid armature or BIP signal. It may fluctuate slightly, depending on the operating mode of the nozzle, on average 950μs + - 100.
23 group + - 100 actually + -50.
How BIP violation affects engine performance. Violation of speed affects the actual start of delivery by each nozzle, earlier later,
a real beep can float away in 3000-4000 μs, while the car starts to triple, ring, or spit white smoke,
With less maintenance, this can only appear on a cold machine and even on a hot one.
You need to watch groups 13 and 23 at the same time. in this case XX will be all right. The malfunction of these injectors can be detected by repositioning.
At the initial stage, you can slightly correct the matter by mixing the camshaft gear at an earlier start of the supply if the engine is 1.9-2.0 liters.
The second part is a mechanical beep or the time that will be spent from the moment the control valve is fully lifted to the moment of the actual start of feeding. I will not consider the actions that occur at the same time in the injector, I will only note that if the mechanical part of the injector malfunctions, the pre-injection in both directions can actually disappear.
That is, to disappear altogether - the injection starts from the main feed.
Or option two - it starts on time but immediately goes into the main feed without delay, merges.
In the first and second case BIP electrical 23 group will be ok
but in the first variant, due to the complete absence of pre-injection, the main injection begins much later, and the total dose will be less. The general picture is that XX minus pre-injection is equal to dose reduction and late injection. As a result of the interruptions, white smoke disturbances are visible in only 13 groups.
In the second case, the picture will look like this: increased pre-injection + XX = earlier injection and an increase in the total dose. As a result, a huge pre-injection that will replace XX in volume, this will lead to a more hard work of the engine or to a knock.
All these violations will be visible in group 13 and only because the dose is changed in both cases.
All other parameters are visible only at specialized stands, and even then not at all. Not all fuel operators are thoroughly versed in the operation of the injectors, they can professionally check and adjust the Pump injector T5 1.9 T5 2.5 Usually, it does not go beyond setting the flow rate,
Full BIP including mechanical can only be controlled by a few stands of well-known manufacturers.
And it can be regulated even less, which is why the percentage of return after repair is so high.
Of course, I did not consider all the options for the scanner readings and the behavior of the T5 1.9 T5 2.5 injectors or the operation of the engine, I considered many more options to understand what was happening
only extreme values.
In addition to compression, this parameter is influenced by the correct adjustment of the levers that press the injectors.
When adjusting, you should change the adjusting screws and counterparts on the nozzles, as well as the bolts of the lever axle.
The problem is buried in the material of the adjusting screws, the wear of which leads to the destruction of the pump injector.
The reason for the adjustment is not exceeding the range of parameters in group 13, but changing these parameters during a standard service interval of 7500 km. mileage.
When installing a new unit injector, the corresponding rocker arm adjusting screw must be replaced.
For any work related to the adjustment of the unit injector, it is necessary to replace the adjusting screw in the rocker arm and the ball head screw of the unit injector.
On the older version of the unit injector drive, lubricate the contact surfaces between the ball screw and the adjusting screw with grease -G 000 100-.
New unit injectors are supplied complete with O-rings and heat seal.
When installing an old unit injector, it is necessary to replace the O-rings and the thermal insulation seal.
Before installing the unit injector, check that the three O-rings, heat seal and circlip are seated correctly. The O-rings must not be twisted.
Lubricate the O-rings and very carefully fit the unit injector into the seat on the cylinder head.
Pressing evenly, insert the unit injector as far as it will go into the socket on the cylinder head.
Install the spacer into the side groove of the unit injector.
If the unit injector is not at right angles to the spacer, the retaining bolt may come loose, causing damage to the unit injector or the cylinder head.
Align the unit injector as follows:
Screw the fastening screws into the spacer until the unit injector can be easily rotated.
Position the unit injector at right angles to the main bearing bed.
Using vernier calipers (measuring range at least 400 mm), check dimension “a” from the outer edge of the cylinder head to the cylindrical part of the unit injector.
![]() |
Video (click to play). |
The deviation values are given in the table for unit injectors with new and old fastening nuts.