In detail: do-it-yourself aquario asp pump repair from a real master for the site my.housecope.com.
Hello! The circulating pump Aquario AC 324 ”> in the heating system is broken. The device worked for about 3 years. According to the residents of the house, the “medical history” is as follows. After one year of operation, the pump stopped working in the “1” mode (this is, as far as I remember, the weakest operating mode), namely, the device hummed but did not work. But in other modes, the device worked, and the residents switched the mode of its operation to position “2” (medium). After about a year of operation, this regime also “ordered to live long”. Mode “3” worked. The owners have moved the handle to position “3”. About a year later, the situation repeated itself with this regime. And friends asked to see this pump.
I tried to check it manually - the shaft turns easily. Usually, when the engine is humming but not spinning, the problem may be in the capacitor. I did not find any schemes on the Internet on the model of this company and others like it. But I heard that the stator consists of two windings, one of which is connected through a capacitor. Unfortunately, I did not find a spare capacitor in my bins. Yes, to be honest, I doubt that the case is in the capacitor, tk. the pump alternately worked in different modes until it failed. And when I opened the terminal cover, I smelled burning from the stator winding. Since there is no diagram, namely, how the performance of this pump is regulated, I could not fully ring the terminal box; or rather, it rang like this: one end of the tester on the neutral wire, the other closed the other terminals. There are 8 contacts in total. And the device showed a break. But I'm not completely sure. And really, how does the speed control work? I can assume that the turns of one of the stator windings are short-circuited, and thus the magnetic flux is regulated.
![]() |
Video (click to play). |
Well, okay, I drove on. He began to disassemble. He unscrewed the four hexagons connecting the stator housing to the rest. Here, as I understand it, the rotor is enclosed in a stainless steel sleeve. Well, God bless him, I don't need him, because I have no complaints about him yet. The purpose of my disassembly was to remove the stator winding. And then I came to a dead end. It is very difficult to see, but it seems that the stator winding is wound on a metal screen and this screen is pressed into a steel case. The distance between this screen and the body is small, and the screen is deeply recessed, so it is unrealistic to put any instrument in there. The body itself is deaf, i.e. on the reverse side there is only a hole designed to unscrew the air bleed screw with a screwdriver during the start-up and installation of the pump. Through this hole I tried to knock out this very screen, even the petals were bent, you can see this in the photo, but to no avail.
Help, how can I remove the stator winding? I understand, of course, that most of the Chinese pumps are not repairable, and the only way out is to put a new one, but I'm used to repairing things, I can already do a lot, but I've never dealt with pumps. Yes, and a friend works at the company as a wrapper for electric motors, if anything, he is always happy to help. Attaching photo.
Continuation of the article - Submersible pump Aquario ASP series.
For free lowering of the pump into the well, its diameter must be appropriate. The pump connections to the pipe line must be tight. To prevent a decrease in pump head loss, the diameter of the supply pipe to the pump must be no less than the diameter of the pump outlet. It is necessary to lower the pump using a special cable protected from moisture, the cable is attached to the lugs located on the pump.It is FORBIDDEN to lower the pump using the electric cable of the pump! Never pull on the cable. It is recommended to fasten the electrical cable to the supply pipe at a distance of 2-3 meters, using moisture-resistant clamps.
The installation of a check valve is recommended, especially when installing an autonomous water supply system. The valve prevents the backflow of water from the system into the well and prevents the head pressure on the pump from the water column.
- a check valve is installed on the pump;
- by installing the pump close to the water surface (up to 3 meters), in this case the valve is installed at a distance of 1-5 meters from the pump outlet.
- An additional check valve is installed for every 50 meters of the pipe to protect the pump from the water column.
An incorrectly positioned pump in the well is exposed to dry running, clogging and overheating.
The pump is installed so that at the lowest water level, at least 1 meter remains from the pump surface. It is necessary to submerge the pump at a distance of at least 1 meter from the bottom. The pump is always positioned above the well screen. This is necessary to create a cooling water flow along the engine.
Installation of the pump in the well, the main elements.
When installing a submersible pump in a well, reservoir, container, the following requirements must be met:
- take measures to prevent air from entering the pump and working without water;
- Installing a shroud around the submersible pump to create fluid flow around the pump to cool the engine. The maximum diameter of the casing for the ASP series pump is not more than 120 mm.
Installation of the pump in the cooling jacket.
Switching on the pump without water and even for a short time is prohibited!
- Open the valve on the discharge pipe 1/3.
- Switch on the pump.
- Before opening the valve fully, make sure that there is no sand in the supply water. After the clean water flows, you can open the valve completely and you cannot turn off the pump at this time. This is required to avoid seizure of the pump.
- It is not allowed to operate the pump with closed taps, no more than 3 minutes. As it runs, the pump is cooled by the water around it, when there is no flow, the water heats up and the pump overheats. For the same reason, water consumption of less than 5 l / min is not allowed.
- The pump can only be used within the limits of its flow-pressure characteristics.
- The frequency of switching on the pump is no more than 30 times per hour.
A built-in thermostat protects the pump from overheating by opening the pump. When the engine cools down, the thermal relay turns on the pump automatically, closing the network circuit.
The pump is maintenance-free under normal operating conditions. If the flow rate and pressure drop, it is necessary to dismantle the pump and contact the service center.
Good day. Tell the aquarium borehole pump with a remote unit, how to connect an electrician to a pressure switch. There are four wires to connect to a pressure switch?
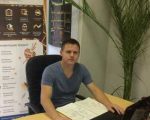
Everything is very simple. Open the control box. in my opinion there is a diagram on the lid on the back side. Or if you explain it on your fingers. Most often, in borehole pumps, be it Aquario, Belamos, Vilo or grundfos, there is a 4-core wire. 1-phase, 2-zero, 3-ground, 4-start relay (usually black). The pump connection diagram is as follows: first, there is a cable from the pump to the control unit, let's say you put the unit in the house, then you pull a 4-core cable from the pump to the block, if the standard is not enough, you also build up a 4-core cable. Next, the 4-core cable enters the control unit, the 4th core remains there, you will see a relay there, this is just this starting relay. After that, the control unit switches to a standard 3-core plug. You twist this plug with a short cable that comes out of the unit, put it in the same place, say VVG 3 * 1.5, you lead it to the pressure switch and the hydrostop relay, how to connect the relay there should also be a circuit, but it's easier to say, there is the inscriptions MOTOR and LINE and so here is the cable that goes from the control unit to the MOTOR, and remove it from the relay with LINE and put it into another relay if there is, if not, then connect the TOT cable with the plug that you unscrewed from the control unit and that's it, into the socket. But better in the stabilizer and only then into the outlet.
Without submersible pumps, not a single well will function properly.This very robust-looking device really is, and is distinguished by its reliability and duration of operation without emergencies.
Connected submersible pump ready to be lowered into the well
Failure of submersible pumps is an extremely rare occurrence (of course - with proper operation). But if it happens, then timely repair of deep-well pumps is necessary in order to avoid additional, sometimes more serious, problems in the water supply system from the well. Fortunately, you can make such repairs yourself.
Due to the fact that the pumping device constantly interacts with water, it is constantly influenced by various negative factors. Fortunately, such negative factors rarely lead to lightning-fast breakdowns, usually the pump's performance is disrupted gradually, gradually and noticeably for the exploiters.
And this means that if small defects are found, it is not necessary to radically replace the deep-well pump, since you can do the repair yourself. By the way, replacing a submersible pump with minor breakdowns is practically never carried out at all. Submersible pumps are even easier to repair, including by hand, than submersible pumps.
In the overwhelming majority of cases of breakdowns of deep-well pumps, it is the magnet of the pumping device that fails. Such a breakdown is most often observed in submersible pumps of the "Sprut" and "Aquarius" brands. Unfortunately, in this case, do-it-yourself repairs will not work, since the equipment for repairing the pump magnet is available only at specialized enterprises. In such a situation, the pump must immediately be taken for repair to specialists..
Another thing is extraneous noise when the pumping device is running. Here we are already talking about a breakdown of a mechanical nature. In the overwhelming majority of cases, mechanical damage can be eliminated by hand.
The first step in case of extraneous noise is to disassemble the pumping device for parts. In cases where noises are heard from pumps of the "Sprut" or "Aquarius" brand, it is necessary first of all to check the electrical system of the pump, which includes both the engine itself and the automation system.
Subsurface pump with connected hose
Pumps of the brand "Sprut" and "Aquarius" have breakdowns most often in these systems, which, however, can be repaired quite simply with your own hands. Among other problems that often arise with pumps of the brand "Sprut" and "Aquarius" are breakdowns of the time relay and the protection system against short circuits or dry running.
The reasons for such breakdowns can be the gradual blockages of the internal pumping system with foreign objects from the well soil. In addition, the operation of the pump in dry mode can also become a serious problem, since at such a "stroke" the oil quickly runs out, which leads to uneven and uneven operation of the internal mechanisms of the pump.
In such a situation, over time, the parts undergo deformation, up to the impossibility of repairing in principle. That is why any pumping device, especially popular in the CIS brands "Aquarius" and "Sprut", must undergo constant diagnostics for internal problems, preferably by specialists.
The rarest reasons for the failure of a pumping system are the following:
- overheating of the working fluid when its temperature exceeds 40 degrees Celsius;
- improper fastening of the submarine cable.
These problems are typical not only for pumps of the brands "Aquarius" and "Sprut", but in general for everyone, since the reasons that led to such problems are in no way connected with the quality of the pump, but directly depend on the professionalism of the pump installer.
to the menu ↑
If you find that the device is not working properly, you should not immediately try to fix it, even if the reason is obvious.Initially, you need to check the device for the presence of either minor problems that are not so obvious at the first inspection, or for the presence of a major problem, when it is initially not clear at all why the device does not work.
Submersible pump with accumulated deposits on the casing
On the submersible pumps of the brands "Sprut" and "Aquarius", as, indeed, on any others, the first thing we do is to check whether there was a banal overload, due to which the automatic device and the entire pumping system as a whole could turn off.
- disassemble the junction box;
- make a visual inspection of the inside - a burnt-out part will be immediately noticeable (a burning smell can also be felt).
If the cause of the breakdown is not clear, then you need to remove the impeller from the pump motor and check whether the motor itself rotates directly in a free state or not.
It is important to know that most modern pumping devices are manufactured in single phase. A so-called "smoothing capacitor" is connected to them, thanks to which the engine starts up more smoothly and smoothly. There is a special winding around it.
In such pumps, the engine most often burns out. Actually for this reason, it is necessary to remove the impeller. And after removing the impeller, you must try to scroll the shaft manually. Thanks to the pre-vacated space, due to the removal of the impeller, this is not difficult to do.
But if the shaft is not spinning, then you need to think about mechanical failure. To be more precise, you should think about engine jamming.
This can happen for the reason that small or, in other cases, large particles of soil constantly get into the engine.
This only happens if the engine does not have an additional protective filter. Actually, these particles can be the cause of such problems. It is noteworthy that if they are not promptly removed from the motor of the pumping device, then this will gradually lead to the fact that the entire stator winding will completely burn out. She, obviously, cannot be repaired, only replaced. However, if the shaft has no problems with rotation, then the lower part of the motor can be assembled.
to the menu ↑
to the menu ↑
Before starting to disassemble the upper part of the electric motor, be sure to place it in an upright position. This is really necessary, as installing the electric motor in the wrong position can lead to oil leakage, which is the working fluid in pumping systems..
After installing the electric motor in the required vertical position, it is imperative to remove the cover through which the power wires of the installed electric motor pass. Actually, when you remove the cover, you can immediately diagnose the starting capacitor for problems. To do this, it will be necessary to use an ohmmeter in order to check the resistance of both the starting and its own working winding.
Therefore, further you need to take the ohmmeter terminals and connect them directly to the winding itself. Next, you need to rotate the handle, which will then create the required voltage of 200 - 300 volts. When the resistance readings on the device do not reach infinity, and this has a certain value, it can be assumed that the condition of the winding is satisfactory or even ideal.
But in cases where the device detects resistance reaching infinity, we can safely say that there is a problem in the form of an interruption in the operating phase of the motor.
Blockage of the inside of the submersible pump
When the device detects too little resistance, we can say that there is a so-called turn-to-turn circuit. Unfortunately, if one of the above possible problems occurs, then an attempt to fix everything with your own hands will not be crowned with success, and the unit will need to be taken to specialists who have the equipment necessary for repairing.
However, in most cases, the problems described above require not so much a partial or complete repair as a complete replacement of all defective parts. Especially when it comes to winding.
If the device says that all the checked elements of the pumping system are in perfect working order, it is necessary to carefully examine the starting capacitor. Under such circumstances, most often the cause of a malfunction of the entire system is precisely its breakdown. In addition, it can be in a state of the so-called breakage.
Unfortunately, at first glance, this problem may not be striking, but when diagnosed with a special device, an ohmmeter, the malfunction will surely come out. And already in these cases, it will be possible to repair the starting capacitor on its own. However, most often, the repair of a starting capacitor can only be called a complete replacement, since its breakdown, and most often it is overheating and combustion of the capacitor, is a fatal breakdown.
And where to get spare parts for it!
It’s easier to buy a new one and doesn’t get steamed!
I already have two lying around!
There were new ones working well.
Literally enough for the winter, then they start howling. make noise.
The vibration is unhealthy - common turd, not pumps.
One octopus. the other is good, Italy or something. worked a little longer!
And there are no spare parts for either.! - this is a specialist so that new ones take,
and the price, mind you, is not small!
Convenient - but hemorrhoids!
Uv. comrade, your pump sighed from the increased amount of abrasive particles. The repair consists in replacing the bushings. The sleeve is pressed tightly into a stainless steel sleeve. A car puller is required to remove the sleeve, and heating is possible.
Recently I asked for a non-working pump for spare parts, disassembled, checked. The coils are intact, the snail is intact, only it did not turn on the axis. A drop of synthetic detergent, moved, stirred, washed in water, again in detergent. I twisted it for about ten minutes - I washed my face and started to rotate easily. The bushings of my pump are ceramic, the axle is also ceramic.
The second option is to pour in diluted sulfuric acid, then rinse with water.
If a screeching or hum wakes up, the bushings are broken, they are only replaced.
Uv. comrade, your pump sighed from the increased amount of abrasive particles. The repair consists in replacing the bushings. The sleeve is pressed tightly into a stainless steel sleeve. A car puller is required to remove the sleeve, and heating is possible.
Recently I asked for a non-working pump for spare parts, disassembled, checked. The coils are intact, the snail is intact, only it did not turn on the axis. A drop of synthetic detergent, moved, stirred, washed in water, again in detergent. I twisted it for about ten minutes - I washed my face and started to rotate easily. The bushings of my pump are ceramic, the axle is also ceramic.
The second option is to pour in diluted sulfuric acid, then rinse with water.
If a screeching or hum wakes up, the bushings are broken, they are only replaced.
Submersible pumps have to work in difficult conditions. They are constantly exposed to water, vibration, low temperature, abrasive particles, etc. But despite the fact that the units are made from parts with a large margin of safety, various malfunctions appear in them over time. To repair water pumps with your own hands, you need to familiarize yourself with the main symptoms that indicate certain breakdowns in the equipment.
If malfunctions are noticed in the operation of a submersible pump, then it does not always need to be removed from the well for inspection. This recommendation only applies to pumping stations where pressure switch installed... It is because of him that the device may not turn on, not turn off or create a poor water pressure. Therefore, first the operability of the pressure sensor is checked, and only after that, if necessary, the pump is removed from the well.
Important! In the case of submersible pumps that operate without accumulators, they should always be removed from the mine at the slightest sign of failure.
It will be easier to diagnose water pump malfunctions if you first familiarize yourself with the most common failures of this unit.
The reasons that the pump does not work may be the following.
- Electrical protection tripped... In this case, disconnect the machine from the mains and turn the machine back on. If it knocks out again, then the problem should not be looked for in the pumping equipment. But when the machine is turned on normally, do not plug the pump into the network anymore, you must first find the reason why the protection worked.
- Blown fuses... If, after replacing, they burn out again, then you need to look for the cause in the power cable of the unit or in the place where it is connected to the mains.
- Cable damage has occurredunder water. Remove the device and check the cord.
- Dry-running protection of the pump has tripped”. Before starting the machine, make sure it is immersed in liquid to the required depth.
Also, the reason that the device does not turn on may lie in the improper operation of the pressure switch installed in the pumping station. It is necessary to adjust the starting pressure of the pump motor.
There may also be several reasons that the device does not pump water.
- Shut-off valve closed... Turn off the device and slowly open the tap. In the future, you should not start the pumping equipment with a closed valve, otherwise it will fail.
- The water level in the well has dropped below the pump... It is necessary to calculate the dynamic water level and immerse the device to the required depth.
- Stuck check valve... In this case, it is required to disassemble the valve and clean it, if necessary replace it with a new one.
- Clogged intake filter... To clean the filter, the hydraulic machine is removed and the filter mesh is cleaned and washed.
Also, the decrease in performance causes:
- partial clogging of valves and gates installed in the water supply system;
- partially clogged riser pipe of the apparatus;
- depressurization of the pipeline;
- incorrect adjustment of the pressure switch (applies to pumping stations).
This problem occurs if the submersible pump works in tandem with a hydraulic accumulator... In this case, frequent starts and stops of the unit can be provoked by the following factors:
- the pressure in the hydraulic tank has dropped below the minimum (by default it should be 1.5 bar);
- there was a rupture of the rubber bulb or diaphragm in the tank;
- the pressure switch is not working properly.
If you notice that the water from the tap does not flow in a constant stream, then this is a sign of a decrease in the water level in the well below the dynamic... It is necessary to lower the pump deeper if the distance to the bottom of the shaft allows this.
If the pump is humming, and water is not pumped out of the well, then there may be several reasons:
- there was a "sticking" of the impeller of the apparatus with its body due to long-term storage of the apparatus without water;
- defective motor start capacitor;
- the voltage in the network sank;
- the impeller of the pump is stuck due to dirt collected in the housing of the apparatus.
If the automation does not work, the pump will work without stopping, even if excessive pressure is created in the hydraulic tank (seen from the pressure gauge readings). It's all the fault pressure switchout of order or incorrectly adjusted.
During the operation of pumps from different manufacturers, it was noticed that some brands of devices are often subject to the same breakdowns. It follows from this that these models of units have their own distinctive features in terms of the occurrence of malfunctions.
Pumps "Aquarius" have overheating predisposition, especially if they work in shallow wells. If a cheap model breaks down, its repair costs about 50% of the cost of a new device.If the device is out of order, it is easier to throw it away than to repair it.
Most of the models of this manufacturer have valve system... There is also a special thermal insulation around the engine. Sometimes pump malfunctions occur due to the failure of the listed parts. Since the thermal insulator is located around the engine, it will need to be removed from the housing for repairs.
Devices "Malysh" are products of domestic manufacturers. The cost of repairing units of this brand is not high, and the owners of the devices eliminate most of the breakdowns with their own hands. The main failure often found in this pump is loud noise when operating the hydraulic machine without pumping out the liquid. This behavior of the apparatus means that there has been a rupture of the central axis holding the armature and the membrane.
The engine in pumps of vortex and rotary type "Dzhileks" is oil-filled. Therefore, a frequent breakdown of these units is leaking oil from the engine... It can only be refilled at a service center.
Important! Many on the Internet advise using transformer oil or ordinary glycerin instead of the original oil filler. Doing this is highly discouraged, of course, unless you have set yourself a goal to spoil the technique in an unusual way.
There is an opinion that the operation of the trickle drainage pumps can continue without interruption for 7 hours or more. This is explained by the peculiarity of their design, which meets all European standards. But despite this, the apparatus exposed to overheating as well as pumps from other manufacturers. Therefore, it is recommended to give it time to “rest” after every 2-3 hours of operation.
The owners of the pump for the "Markus" well sometimes notice that the device turns on only after a slight blow either on the pipe going to it, or after hitting the hydraulic machine itself. This malfunction is explained by “souring "impeller, which will have to be cleaned by disassembling the unit.
In the event of pump breakdowns requiring replacement of parts located inside its housing, disassembly of the unit will be required. The submersible pump consists of a compartment for the engine and a compartment with one or more impellers, the purpose of which is to capture water... Below is a diagram of the device of that part of the centrifugal pump where the impellers are installed.
As you can see from the figure, the impellers are mounted on the unit shaft. The more there are, the higher the pressure generated by the pump. In the second compartment of the hydraulic machine is located rotary engine. It is located in a sealed case, and in order to open it, you need to know some of the nuances.
So, to go from theory to practice and disassemble the pump, follow these steps (depending on the manufacturer, the design of the unit may differ).
-
Unscrew the 2 screws holding the mesh of the device.
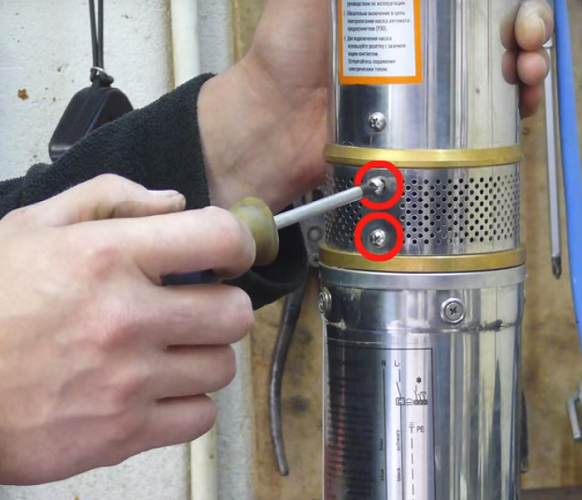
![]() |
Video (click to play). |
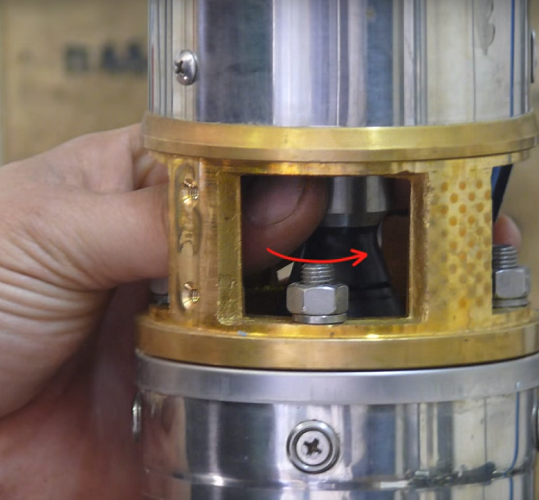
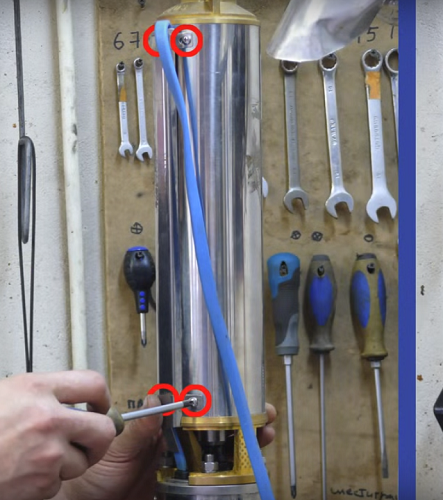
Next, unscrew the 4 nuts holding the pump flange.
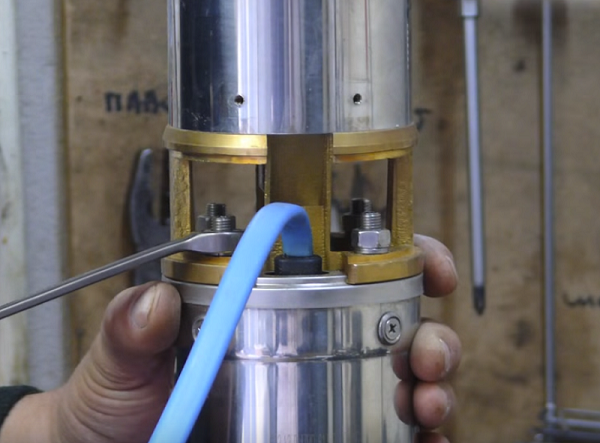
Now that you know how the hydraulic machine is disassembled, you can try to repair the submersible pump with your own hands.
Mostly impeller blocking occurs due to clogging them with sand or dirt deposits on them. In addition, the impellers can be soldered together when a high temperature occurs in the unit, when the pump is idling (dry running). To repair this section of the unit, it is necessary to remove the impeller (s) and remove the accumulated dirt. If the impellers are damaged, they will need to be replaced with new ones.
It is not recommended to repair the pump motor on your own, since it requires special knowledge and the necessary equipment to diagnose this unit and subsequent repairs.
On some pump models, removing the motor will require pressing it out using special equipment. Replacing the oil seal and bearing also carried out at the service center.
If engine hums and won't startthen the capacitor should be checked. It is located in the pump block in which the motor is mounted.
But when the shaft with the impellers rotates without problems, then in order to remove the hum in the water pump, you should disconnect the condenser and replace it with a new one. Better of course check this part with a multimeter, since similar symptoms can be caused by a short circuit in the motor windings.
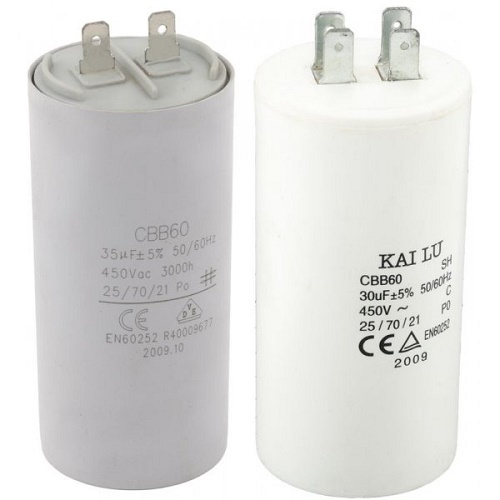
The water pump motor is located in a special glass filled with oil, and by its condition it is possible to determine some breakdowns in the electric motor block.
- The oil has a characteristic, unpleasant odor... This means that the engine is still in working order, but it has been working with great overloads.
- Turbid oil - water has entered the engine housing due to a crack in the housing or failure of the oil seal (cuff).
- Black oil with an unpleasant odor... In this case, we can say with great confidence that the varnish burned on the engine coils.
Important! Normally, the oil should be clear. Its quantity is determined by the unit model. On average, the volume of oil poured into the chamber is at the level of 0.5 liters.
If, when opening the engine, the above changes in the quality of oil were noticed, then first you need to repair this unit, and only after that fill in new grease.
Everyone knows what is dissolved in water some gas... When a liquid moves at a certain speed, rarefaction zones are sometimes formed in it. In these zones of reduced pressure, gas bubbles begin to emerge from the water. After the bubbles hit the high-pressure zone, they collapse. This process occurs with the release of a large amount of energy, from which the impellers and the pump volute are destroyed. The next photo shows the unit impeller destroyed by cavitation.
The energy of the collapsing bubbles is capable of creating shock wavescausing vibration. It spreads throughout the entire unit and affects not only the impeller, but also the bearings, shaft and seals, from which these parts quickly become unusable.
The cavitation effect can most often be observed in pumping stations that work for suction.... In such systems, the impeller creates a vacuum, due to which water rises through the hose from the well. But if there is a lack of liquid at the pump inlet, then an excessive vacuum occurs in the impeller zone, provoking cavitation.
Important! The most obvious signs of cavitation are vibration of pipes and the pump itself, as well as increased noise during its operation. If you do not take any measures to eliminate this process, then it can completely destroy the station.
To prevent cavitation in the pumps, you should adhere to the rule: there must be more water at the inlet than at the outlet. This can be achieved in several ways:
- move the device a little closer to the source;
- the diameter of the suction pipe (hose) can be increased;
- to reduce the resistance in the suction section, the suction pipe can be replaced with a pipe made of smoother material;
- if there are many turns on the suction pipe, then, if possible, their number should be reduced;
- it is desirable that all bends have large turning radii.
We repair a borehole pump
If you have a well or a well at your summer cottage, then they will never work correctly without a deep pump. A device such as a submersible pump is seemingly durable and does not always work properly.
In our time, breakdowns of submersible pumps are very rare.But suddenly you have a pump failure, you need to pay attention to it in a timely manner and bring it into normal operation.
So that in the future there are no more serious consequences. You can also fix a deep pump with your own hands, if you do not want to call a special master.
The submersible pump is constantly in the water and is constantly influenced by negative factors. In most cases, submersible pumps do not break down instantly, but gradually fail. If you still have a small breakdown, then it is not necessary to replace the pump, you can do a little DIY repairs.
And it is not necessary to change a completely submersible pump with a small defect and it is not advisable. If we compare a submersible pump with a submersible pump, then a submersible pump is easily repaired by oneself than a deep one. Most often, the magnet of the pumping device breaks at a deep pump.
Such a defect is exposed in such pumps as "Aquarius" or "Octopus". If your pump magnet is out of order, then you will not be able to make repairs with your own hands, but only a replacement is provided in special services. There are such breakdowns as extraneous noise during the operation of pumps. And these are mechanical breakdowns that can be easily eliminated by hand.
Deep water pump device
First you need to put the pump upright and disassemble it for parts. If the pump makes noise during operation ("Octopus" and "Aquarius"), then first the electrical system of the pump is checked, which is responsible for the automation system and the operation of the engine.
The most vulnerable pumps of the brand "Sprut" and "Vodoley" in which noises are heard during operation. In this case, you can fix the breakage with your own hands. Breakdowns also occur in pumps such as "Sprut" and "Aquarius"; this is a relay malfunction, as well as dry running failure. Such breakdowns occur most often from clogging of the internal pump system.
Also, if you turn on the pump in dry mode, this can also lead to serious damage. And most often the submersible pump works in dry mode, it quickly runs out of oil, while the mechanism starts to work tightly and not smoothly. If the pump runs in dry mode for a long time, deformation of the internal parts occurs, as a result of which it becomes impossible to repair the pump with your own hands.
That is why pumps such as Aquarius or Octopus must undergo constant diagnostics and, preferably, by qualified specialists.
But infrequent breakdowns of the pumping system are pump overheating, this is when the unit heats up over 40 degrees Celsius, or you have incorrectly strengthened the connection cable. These infrequent breakdowns not only occur with such pumps of the Vodoley and Sprut brands, and other manufacturers.
to the menu ↑
If during operation you notice that the pump does not work as it should, extraneous noises are heard, then you need to take action immediately. We recommend checking the devices for minor problems first. On such brands of pumps as "Sprut" and "Aquarius", initially it is necessary to check whether a reboot took place, because of which the machine most often turns off, and then the pumping system.
Pump Aquarius and its repair.
To check this, you must first unscrew and disassemble the junction box. Inside this box, you can see a breakdown, and this is blackening or a burning smell. If everything is in order in this area, the smell is not felt, then proceed to removing the impeller from the pump motor.
First, it is checked whether the engine is spinning. A smoothing capacitor is connected to the engine, through which the engine is started. We also look at the winding around it, which should not be broken or torn. Most often, in these pumps, a breakdown is a burnout of the engine. That is why the impeller is removed to see this.
After removing the impeller, we begin to manually scroll the engine (shaft). If the shaft does not rotate, then mechanical failure is evident. In other words, the pump motor has jammed.Most often this happens due to the fact that small debris and soil can get into the engine. And this happens due to the fact that there is no protective filter on it. If in the future you do not clean the special filter and remove particles on it, then the stator winding in the engine may soon burn out.
ATTENTION! The stator winding cannot be repaired - only replacement.
Before you decide to repair the electric motor, you must put it vertically. If you do not, when disassembling the electric motor, oil will leak, without which the pumping system will not work. Further, in a vertical position, the cover is removed through which the 220 W power wire passes.
Immediately after removing the cover, it is advisable to diagnose the starting capacitor. To diagnose a starting capacitor, you need an ohmmeter. This is checked by connecting the terminals to the motor winding. Then we rotate the handle, and it creates a voltage of 250-300 volts.
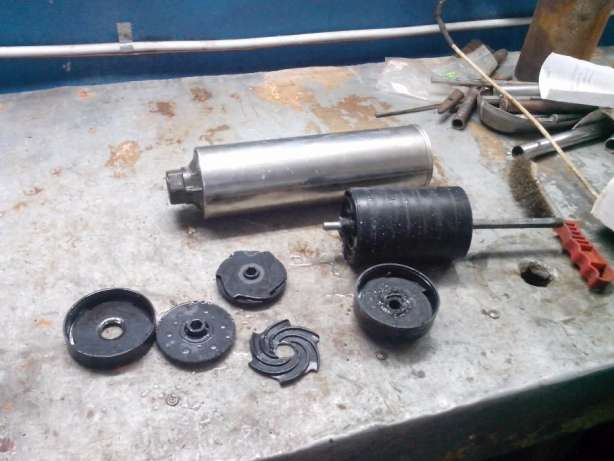
If the device shows resistance at the same time, then it is considered that the condition of the winding is ideal. But if the ohmmeter device detects infinite resistance, then there is a problem in the form of a break. Conclusion: the working phase of the motor is not working, there is an open circuit.
If the device shows a small resistance, then we can talk about an inter-turn circuit. Conclusion from the above - on your own, if it happened, it is not possible to fix it. It is better in such cases to contact a specialist. Since in most cases, replacing parts will not help, but only replacing all successive parts will help. Especially if the pump winding has not been fixed.
When viewed further, we look at the pump further. The device shows that everything is in order, we proceed to inspect the starting capacitor. Most often, a breakdown occurs in it. In other words, there is a cliff in it. When the pump is operating, such a problem does not immediately catch the eye, but upon a detailed examination with such a device as an ohmmeter, the breakdown will come out.
At the same time, do-it-yourself repairs of the starting capacitor can be done independently, without resorting to the help of a master. But if this does not work out for you, then it is better to replace the starting condensate with a new one. Since starting condensate is a fatal breakdown.
to the menu ↑