In detail: do-it-yourself repair of the gur nissan almera n16 pump from a real master for the site my.housecope.com.
You will need keys "12", "14", socket "24", pliers, a container for draining the working fluid from the tank.
1. Remove the drive belt for the water pump and the power steering pump (see "Replacing the drive belts for the generator, air conditioning compressor, water pump and power steering pump").
2. Squeeze the bent ears of the hose clamp for the return line to the pump nozzle, slide the clamp along the hose.
3.. remove the hose of the return line from the branch pipe of the power steering pump and drain into a suitable container the working fluid from the power steering reservoir and the hose.
4. Unscrew the bolt-union securing the pressure line pipeline to the power steering pump union.
5. . and disconnect the pipeline.
WARNING: Take measures to prevent the leakage of hydraulic fluid from the lines by plugging them, for example, with wooden plugs.
Replace the copper O-rings in the connection of the pressure line hose with the power steering pump during assembly with new ones.
6. Unscrew the nut securing the tensioner slider to the power steering pump bar.
7. Remove the three bolts securing the power steering pump bracket to the engine block.
eight. . and remove the pump assembly with bracket.
9. Unscrew the nut that secures the pump to the bracket, remove the bolt through the hole in the pump pulley.
10. . and remove the pump.
11. Install the power steering pump in the reverse order of removal.
12. Adjust the tension of the drive belt for the water pump and the power steering pump (see "Checking and adjusting the tension of the belts for the drive of the generator, air conditioning compressor, water pump and power steering pump").
13. Fill the fluid into the power-assisted steering system and remove the air from it (see "Bleeding the power-assisted steering system").
![]() |
Video (click to play). |
Announcement on the Club-NISSAN or Nissan Primera Club (NPC) forum: Good afternoon. I am the owner of a Nissan Primera P12 car (I used to have an Almera N16). The car is great. For that kind of money, I didn't expect to get a comfortable and reliable car. But why, but why both Almera and Examples have steering racks leaking? How to prevent the rail from leaking, how to sort out the rail with your own hands? Where to buy oil seals and how to replace them? Is it possible to replace the steering rack oil seal on a Nissan without removing the rail from the car?
Forums and conferences are full of such messages, as well as responses to them. But still, there is no consensus on the Internet about the steering racks of the Nissan Almera and Primera. Many, having replaced only one oil seal on the Almera rail, which is very loose under the hood, report that everything is very simple. It is not necessary to remove the rail for this, and the oil seal can be supplied from a Soviet car, undercutting it slightly along the outer diameter. It is possible and so 🙂 The company Gidrolab has nothing against 🙂 But if you approach this issue professionally, then this method is not suitable.
Firstly, only one upper distributor oil seal can be replaced this way (some call it the steering shaft oil seal or the regulator oil seal) (pictured)
because to replace the lower distributor seal (which is installed on the same shaft, made of the same material, works in the same conditions and will also flow soon) (pictured)
you need to remove the entire spool, which then cannot be inserted back.In addition, the lower oil seal of the distributor on Nissan Almera and Primera rails is removed with the destruction of a disposable compression ring, which can only be put back using special equipment.
Secondly, when repairing a steering rack, absolute cleanliness is required. If you add dirt or sand to the valve spool, you can lose the power steering pump. Even a few grains of sand caught in the pump will scuff the polished mating surfaces and the rotor. After which it will have to be changed. The pump is expensive. More expensive than repairing the rail, even by professionals.
Thirdly, how to eliminate backlash, crackle knock and crack casing wear, rod wear, side oil seal leaks and much more without removing the rail?
For all of the above reasons, steering racks must be removed for repair.
But the power seals (shaft-rail oil seals, i.e. rod moving left-right) (pictured)
often not necessary to change. Their quality is not satisfactory. And at the same time, to replace them, you need to have a special tool to remove the inner power seal from the very depth of the rack cylinder.
How to repair a steering rack Nissan Almera and Primera yourself.
And yet, the Almera and Examples steering rack can be repaired on your own, but on condition that only the upper distributor oil seal is leaking and the rest of the oil seals are in excellent condition. Those. no need to get involved with a complex procedure for replacing them using a special tool.
For this, the rail still has to be removed. The wheels do not need to be removed. It is necessary to put the wheels straight and from the pit disconnect the ends of the steering rods from the swivel levers. Next, remove the cardan, disconnect the supply and return oil lines and unscrew the bolts securing the rack to the body.
The rack is removed through the hood past the battery along with the rods, after it is strongly shifted towards the right wheel. Installation is in reverse order, except that you first need to screw the steering rods to the wheels, put the wheels straight, and only then install the steering shaft cardan.
The removed rail must first be cleaned of dirt, washed with kerosene and blown off with compressed air. DO NOT wash the rail with a Karcher, as water gets inside. Next, unscrew the tubes from the distributor (they must be screwed back with care, since the fittings are screwed into aluminum), remove the distributor housing.
The oil seal must be purchased in advance in the size 19x29x4.5 mm. You can buy it from our company Hydrolab or just on the market. The procedure for replacing the oil seal itself is simple. Knock out the oil seal together with the bearing using a mandrel (a 16 high head will do).
Then drive the new oil seal back together with the bearing using a drift (a 22 high head will do).
Apply special grease to the oil seal and bearing and reassemble carefully. The bolts of the distributor housing must not be tightened to the end, but only to the moment they stop in the bearing.
Eliminating slack and knocking of the rail is a special topic for a separate article. We can only say that by a run of 100 thousand kilometers, they appear in any rail, and especially in racks with a plastic cracker, like in Almera and Examples.
So why are the steering racks of the Nissan Almera and Primera leaking?
For more than 10 years, Gidrolab has been successfully repairing steering racks of Nissan Almera and Primera cars and has accumulated solid statistics. 90% of these steering racks begin to leak at runs from 90 to 140 thousand kilometers and 98% of them flow through the upper and lower distributor oil seal.
Please note that there are two oil seals in the distributor - an upper and a lower one. The flow through the upper one is always noticeable, but through the lower one is not. When the lower oil seal of the distributor leaks, fluid enters and accumulates imperceptibly inside the steering rack. Therefore, if it flows from above, then both distributor oil seals must be changed.But the leaks of the power (side) oil seals are very rare and are associated with various defects introduced into the rail later - for example, when replacing the steering rods, the anthers were poorly installed and corrosion appeared. Or scratched and banged the polished parts of the shaft-rack.
So why does one pair of oil seals work perfectly, while the other is constantly flowing, although they work in the same oil, temperature, etc.? All our studies have shown that corrosion on the parts of these rails is extremely rare. Although for others it is a scourge. There is also no catastrophic wear on the working lip of the oil seals. But if you look at the oil seals, you will see that although they are made of a particularly heat-resistant material SNBR, they still look different. The power seals are made of slippery material, and the distributor seal material is similar to regular rubber. They are too soft and the spring is weak. It has long been noticed that if the stuffing box material is soft, then it not only quickly wears out, but also quickly loses its elasticity when working in oil. In other words, it quickly "dubs". And besides, that the spring on the distributor seals is weak, when they become tanned, leaks begin.
It turns out that the discrepancy came out precisely with the material of the oil seals at the factory. In the meantime, it was found out, a huge number of cars have already been produced in three years. And even now, the new original steering racks sold in the store do not nurse even 40 thousand kilometers, because they have been lying in a warehouse all these years somewhere, and the oil seals have already become stiff.
All that remains is to replace the hardened oil seals with new, high-quality ones. It's good that the rest of the steering racks of the Nissan Almera and Primera are very reliable. Gidrolab will quickly and efficiently repair the steering rack and give 13 months warranty no mileage limitation.
We remove the power steering pump to replace it or when dismantling the engine.
Remove the accessory drive belt (see "Replacing the accessory drive belt of the 1.6 (16V) engine").
Remove the left headlamp unit (see "Removing the headlamp unit").
We pump out the fluid from the power steering reservoir with a pear.
Using the "10" head, unscrew the bolt fastening the holder of the discharge line tube
Holding the pump union with the "22" wrench, with the "17" wrench, unscrew the union of the discharge line tube
We take out the tube fitting from the hole of the pump fitting and remove the tube from the pump body
Squeezing the filler pipe clamp with pliers, slide the clamp along the hose
Remove the hose from the pump connection
We insert plugs of a suitable diameter into the holes of the tube, hose and union of the pump body.
Turning the pump pulley, we align the hole in the pulley with the head of one of the two bolts securing the pump to the engine bracket
Using the "10" head, unscrew the bolt securing the pump to the engine bracket. Similarly, turn away
second bolt.
With the same tool, unscrew the two pump mounting bolts on the opposite side of the bracket
Insert a screwdriver between the pump casing and the motor bracket and squeeze the pump casing from the bracket ...
Install the power steering pump in reverse order.
We adjust the tension of the accessory drive belt (see "Replacing the accessory drive belt of the 1.6 (16V) engine").
Fill the power steering reservoir with working fluid and remove air from the system (see "Bleeding the power steering system").
It will not be difficult to change the fluid in the power steering Nissan Almera H16. First of all, do the preparatory work and cover the hinged belt so that oil does not get on it and remove the tank with washer fluid. Then start pumping out the old power steering fluid from the barrel with a large medical syringe. Before you start pouring fresh liquid into the tank, it will not be bad if you rinse it thoroughly.
Further, the algorithm for replacing the power steering fluid on the Nissan Almera N16 will consist in removing the return hose and installing it in a separate bottle and close the return pipe in the barrel with a plug and filling the tank we begin turn the steering wheel when the engine is not running (it is advisable to hang out the front of the car).
We repeat this procedure until fresh clean liquid runs out of the return hose.
Vovan1123
Drives: Nissan almera
With us from 27.12.10
Total Posts: 2
The rail leaked, the liquid in the tank is normal, but the power steering pump began to buzz. On the cold, everything is quiet, but warms up it makes a noise. Change the pump? Tell me please.

RomAlm
With us from 04.04.10
Total Posts: 668
to Vovan1123: It is very interesting how the rail flowed, and the liquid in the tank is the norm? There are two marks on the power steering reservoir, for a cold engine and for a hot one. The fact that the pump is buzzing indicates that it was scorched, that is, it worked without oil or the steering wheel was twisted all the way and someone gasped well, or maybe even twisted pennies on the ice) If the steering wheel is spinning normally and the noise does not bother, then it seems to me that you can ride like that. If you have money or obvious problems with taxiing, you need to change. Although first you need to change the power steering fluid. On a cold car, pump out the liquid from the tank with a syringe, as much as you can. Then add fresh slurry and ride for a day or two. Then you repeat. If you upload a couple of liters and a half of new slurry, you can count on changing it completely. You can, of course, call in at the station, they will do everything at once. Good luck!

Vovan1123
Drives: Nissan almera
With us from 27.12.10
Total Posts: 2

RomAlm
With us from 04.04.10
Total Posts: 668
Our local experts will appear and will definitely comment)

Messir
With us from 05.12.10
Total Posts: 3872
to Vovan1123: If the pump hums, then this is a reason to replace the fluid. This is the very first and least expensive job compared to repairing a pump or rack. But the fact that the leak points have been identified is not good. It is better to immediately replace both the oil seals and the fluid. Save yourself the double cost in the future.

vlad m
Moderator Drives on: Mitsubishi colt
With us from 12.06.10
Total Posts: 833
to Vovan1123: Change the fluid (I support Messire) and add a XADO tube for power steering there.

norddron
Drives: Nissan almera
With us from 28.12.10
Total Posts: 1
The Gora pump began to hum when turning the steering wheel on an unheated car. After warming up, there is no noise. The fluid is normal. Tell me what's the matter?
Rain
Chief newsmaker
With us since 26.09.07
Total Posts: 2360
to norddron: Check the pump itself, the motor.

Ruslan M
Drives: Nissan almera
With us from 04.12.10
Total Posts: 6
Bought N16 2006. mileage 46 t.km. During the initial examination, nothing excited, except for the power steering tank - it is covered in oil. What is it for? The car drives fine, but you still need to know
Dimon-811
Drives: Opel zafira
With us from 09.12.10
Total Posts: 2397
Ruslan_M: Bought N16 2006. mileage 46 t.km. During the initial examination, nothing excited, except for the power steering tank - it is covered in oil. What is it for? The car drives fine, but you still need to know #
the lid does not fit snugly, so it is in oil
Dimon-811
Drives: Opel zafira
With us from 09.12.10
Total Posts: 2397
RomAlm: to Vovan1123: The fact that the pump is buzzing indicates that it was scorched, that is, it worked without oil or the steering wheel was twisted all the way and someone gasped well, or maybe even twisted pennies on the ice) If the steering wheel is spinning normally and the noise does not bother, then it seems to me that you can ride like that. If you have money or obvious problems with taxiing, you need to change. Although first you need to change the power steering fluid. On a cold car, pump out the liquid from the tank with a syringe, as much as you can. Then add fresh slurry and ride for a day or two. Then you repeat. If you upload a couple of liters and a half of new slurry, you can count on changing it completely. You can, of course, call in at the station, they will do everything at once. Good luck! #
but even if you wrap yourself around dimes and get gazed, nothing will happen at a normal oil level.
The replacement procedure described above is stupid and costly, read the manual, everything is very simple.

Messir
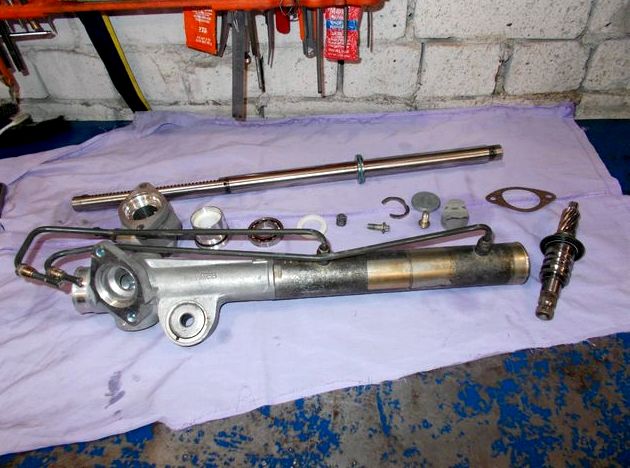
It began with the fact that the power steering fluid began to go by leaps and bounds in the literal sense (1 liter went for a day to top up), at first glance it was clear that the steering rack oil seal had broken through, but not the top one, but the side one. We must change!
The price of 12k for a bulkhead in a car service is too high for my student pocket, I decided to sort it out myself. Keep in mind that in car services they sort out "on the dump" and if the bulkhead is unsuccessful, you will be returned no more than half of your money, because 6k for dismantling / installation, still no one will file the teeth (they will tear the oil seal - the oil seal is bad), they will not lubricate with lithol and will not wash each a detail (this needs to be done only with a liquid for cleaning the carburetor, an awesome thing), well, what can I say, because they do it for strangers, otherwise they are for themselves conscientiously.
To do this, you will need to completely remove and disassemble the steering rack and more on this in more detail.
You will need: 2 gas wrenches (or a vice instead of one), an E8 head (asterisk), keys and heads for 12,13,15,17 with a cardan, an extension cord and a ratchet, a hammer, a 19-bar (for unscrewing the wheels), round-nose pliers (for unscrewing the "washer" from the rail), a hacksaw for metal, a file, 2 jacks (for hanging the wheels), screwdrivers, clamps for anthers and preferably an assistant.
Upper 485.HD484 (spool)
Side 495.HD448 2pcs (it is better to take one more spare)
Additional materials (found in the article, but did not purchase it myself):
Steering rack boot Toyota 45535-08010 2pcs
Clamp Toyota 90080-46340 2pcs
Clamp Toyota 90467-19021 2pcs
I removed the rail through the left wheel arch already without a spool (the upper part where the upper and lower oil seals are located), I removed it under the hood because I thought that the upper oil seal had broken through, but it turned out that the rail would not work with the spool in my experience, but: I was unsubscribed that it is possible to pull out the rail assembly through the driver's wheel arch (of course, the wheel is removed) by twisting it in different positions; if you succeed, then jump with happiness, because you will be lucky enough to disconnect the tubes and the spool not under the hood, but in a comfortable position.
Step 1 Prepare and remove the spool
We set the wheels, the steering wheel straight and fix the steering wheel with tape or electrical tape.
This is done in order not to break the train of the pillow. under the brake pedal in the cabin, unscrew the bolt with a 17 key, remove the bolt and move the steering column cardan aside.
Now let's move on to the engine compartment. We remove the air filter housing there as it hinders access. We drain the power steering fluid from the barrel as far as possible and go to the spool. There are 4 tubes on the spool. Unscrew the hose and the adjacent tube with keys 13 and 15. Unscrew 2 iron pipes with a 12 key or a special key if you are afraid to break the edges, it is important that these pipes do not come out of the grooves completely, do not break. Then, with the head 13, unscrew the lower hinge from the rack shaft and set it aside. There remain 2 “favorite” bolts for which you need the E8 head, the front one will not be difficult to unscrew, but you will have to tinker with the rear one. It is necessary to put a mark on the position of the spool to the cardan, so that then everything can be put evenly.
Make this mark fatter with something visible right along the spool, along the casing, along the splines and along the cardan shaft, otherwise I was stupidly on the slots and the casing and the sense of 0, the body itself could be in any position and the cardan was put on the splines randomly from that I had to tinker with adjusting the steering wheel and wheels (otherwise the steering wheel is straight - wheels to the side).
After that, turn the spool clockwise so that 2 iron tubes come out, and then the spool can be easily removed from its seat and set aside.
The rail itself sits on 3 bolts (head 17), which are not difficult to find and of course you have to disconnect the tips.
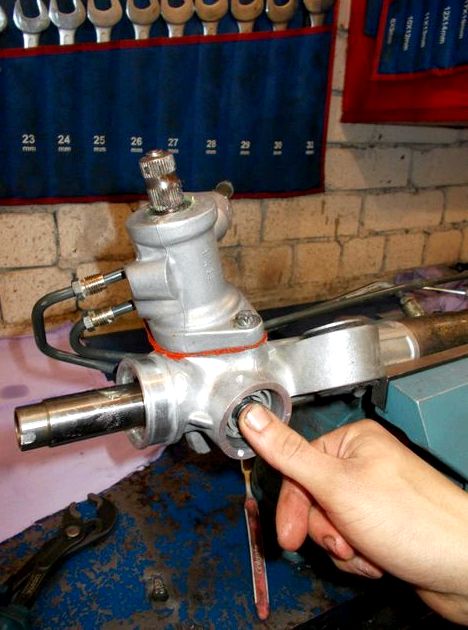
Jack up the right (passenger) front wheel and remove it. (This does not require additional instruction, only a balonnik) Using a 17 spanner wrench, unscrew the nut from the tip and knock it out with a hammer. There should be no problems with this, and I did not have to jack the tip separately for pressure on it (if you have a different situation, then it says here how to create pressure on the tip). We carry out the same procedure with the driver's wheel and pull out the rail through the arch of the driver's wheel.
P.S. Everyone complains about the distant bolt of the spool sprocket, to make it easier to crawl up to it without any problems, I first unscrewed the rail (3 bolts) and knocked out the tips, which allowed me to twist the rail under the hood for convenience.
When shooting wheels, I cleaned the bolt threads with a wire brush and processed them with graphite. This is my personal problem so that the thread does not rust and the bolts can be removed more easily in the future.
To begin with, I washed the rail from the dirt in the basin with a brush and gasoline, wiped it dry and started disassembling it. It is necessary to remove the anthers, or rather to expose the traction.We remove the collars (you need to buy new ones) on the anthers and expose what they were hiding (if the anthers are in good condition, then the clamps should be removed carefully without damaging the anthers, and if the boot is torn, then it should be replaced). Now we need to unscrew the rods. I did this using two gas keys, one clung to the traction head, and the other to the silver shaft and unscrewed it (the thread there is ordinary and unscrews counterclockwise like everything in this world))), I had a little problem at this stage, which I quickly solved it with a flat screwdriver and a hammer see photo.
both rods are removed and this is good, on the right side (where the spool socket is) it is necessary to unscrew the aluminum “washer”, I specified its material for a reason, since this must be done carefully without damaging it, I unscrewed it with round nose pliers.
There will be the first side oil seal. On the same side (on the right where the washer was located) we take out the rack shaft and find inside everything on the same side of the second side oil seal, it is not difficult to knock it out with something long and an incomprehensible ring will fly out with it, this is a caprolon bushing, which should also be replaced. It is useless to search for it on the Internet, you need to order a thickness of 5mm from a turner, an outer diameter of 37mm, and an inner diameter of 0.05-0.1mm larger than its shaft (some put it with an inner diameter flush with the shaft of 25mm).
some, in order not to pay the turner 150 times and not run, make three rings at once with inner diameters of 25mm, 25.05mm and 25.1mm
First, we throw in the sleeve, with the help of a suitable size of the head and extension cord, it is not difficult, but you will have to tinker with the oil seal ... The edges of the rack teeth are sharp and can easily break the oil seal, so you will have to process their edges with a file (it will not affect the operation of the rack). We throw the oil seal inside the rail, the main thing is to lie on the right side (with a spring towards you so that you can see it). Then, with light tapping, we hammer the oil seal - it sits easily. Then you can insert the rack shaft, machined from
sharp edges. We insert with the teeth up, and slightly push the shaft down so that the teeth touch the inside of the gland less. We twist the right washer with the changed right oil seal. With this part, everything.
We find the spool that we put aside at the end of the first stage and start working with it. There is a lot of information on how to change the upper oil seal, but in the process you need to knock out the shaft, then knock out the oil seal with the bearing using a suitable head, but be careful because you can damage the bearing. The upper oil seal is ready, now we will tinker with the lower one. We turn the spool shaft with the bearing up. The bearing is held in place by a lock washer that is flattened on four sides. We carefully cut it off with a hacksaw for metal. We remove the bearing and then remove the oil seal. Putting it up in the reverse order. The lock washer must also be ordered
for a turner made of stainless steel 3mm thick, inner diameter 25mm, outer 32mm. When installing a new lock washer, you will have to flatten it. Putting everything together (rail, spool) in the reverse order, install it in its original places. But that's not all, you need to pour NEW fluid into the power steering and pump the rail. It is not necessary to fill in original liquid KLF5000001.
P.S. When assembling the thrust under the anthers (where the ball is) and the “sting” of the spool shaft, I lubricated it with lithol as advised in various articles.
It is VERY IMPORTANT that the side seals are in the correct position, otherwise they will not hold, but this is correct with the other side, so that when the oil seals are clogged, you see the spring inside the oil seal and for convenience, so as not to jam the oil seal, I put the old bushing over the oil seal.
We hang the wheels (we jack up completely in front of the front wheels so that the front wheels do not touch the ground), pour new fluid into the power steering tank, which needed to be washed, to the top and start the car, the fluid leaves - we fill it. It is NOT NECESSARY to turn the wheels! We are waiting until the liquid stops leaving the tank. Then we turn the steering wheel slowly to one side until it stops. At this time, the second person pours liquid into the tank. Then we twist in the other direction until it stops.We top up to the level, and turn the steering wheel from side to side until it stops, until small bubbles stop appearing in the tank.
We go to the camber and set the wheels and steering wheel straight.
That's all, we rejoice at saving on the steering rack bulkheads and sleep peacefully knowing that the oil seals have been replaced with good ones.
I took some of the information and instructions from sources, combining them for more detailed instructions, I also collected some of the photos from articles and supplemented them with my own for details. I hope that I described everything clearly inside and out.
P.S. It's already been half a year on 03/20/15 - 09/17/15 and over 7.000 km and the flight is normal, the fluid does not go away and the steering wheel is spinning as it should.
10/12/15 (8,000 km) - the gur buzzed a little, I had to top up about a cap of 1.5 (in my opinion, no more than 50 ml) and silence again. Nothing leaks, the steering wheel does not “harden”, I sin for the first frost after the bulkhead.
Watch an interesting video on this topic
Finally, the hands reached their GUR. I did everything according to numerous instructions - there were no special problems, except for an accidentally broken off plastic tube from some kind of tank - but this is not the point - it is removable. The main question arose as follows: when they took Corteko's oil seal, grinded from 30 to 29, put it on, he turned out to be much thicker than his own. At the same time, the shaft did not enter the same level and the large bearing was the same. They cut the edge of the rubber from the bottom - it became even better, but the bearing did not enter the housing to the previous level by 2 mm. How fraught is it and what did those who put Corteko do about it?
Hi. I also have a problem with the gidrach. I found in St. Petersburg a company that manufactures oil seals of such dimensions, they also do not make them, but in return they offered a completely rubber ring without a spring, they are made in exchange if such oil seals do not exist for 300 rubles. On Friday it will be ready the next I plan to change weeks.
In general, we made the power steering ourselves today. This is my first serious experience in car repair. He did it with his brother, since he is very experienced in these matters. Well, I already told him the specifics in controversial issues. Many wonderful reports have already been published here, I will only add a little, it will suddenly be useful to someone.
In general, the problem was immediately with the purchase, the former owner honestly said about it and threw it off well. Tek the upper oil seal of the power steering gearbox, which is why the whole part was black with oil and dirt. It didn't flow much. Approximately once a week I topped up with a thin stream of 50 grams. The puddle was constantly under the car after the night. Barely passed the inspection because of the wet beam. So the problem was small but annoying.
In our city there are no offices specialized for power steering, I did not want to give to specialists of a wide profile, since there are a lot of dangerous nuances in this repair.
Having read the reports with photos on different forums, I decided to do it myself. I think that many already know about the problem of having a native oil seal - it simply cannot be found. In Moscow, I have no one to order to buy. So I had to try non-native oil seals, with sizes different from the native ones.
I took two types of oil seals - one from the MAP2507K repair kit, the other from Toyota in general - Corteco 01026490. The dimensions of the first turned out to be 30 mm outer diameter, 18 - inner. People suggested that it would be very tight on the shaft. I had to try the second one, with dimensions 30x19. The native oil seal has an outer diameter of 29 mm, so Corteco had to grind down first with coarse sandpaper, then grind it with 2000th. I sharpened it like this: I inserted a short mandrel from a set of heads into the drill, winding electrical tape to the required diameter so that the gland entered with little difficulty. I pulled the spring out of it beforehand. The main thing is not to forget to return it to its place. And then, holding a piece of sandpaper in his hands, he grabbed the oil seal in a circle and, at low speeds of the drill, grinded off the entire rubber layer. I had to wash it down to the metal frame of the oil seal. Then, when the size turned out to be 29.1, I polished the oil seal about "zero" to a mirror finish. Here a nuance was revealed - the thickness of the Corteco oil seal turned out to be much larger than the original one. There were fears that the shaft would not go into place and would block the oil channels.For reinsurance, the lower rubber edge of the oil seal was cut to metal. But all the same, its thickness remained greater. Concerns about this remain.
The parsing process has already been described in detail along and across. The most difficult stages for me turned out to be unscrewing the nut from the steering shaft cardan in the cabin, near the brake pedal. The 17 key was not useful - it was needed for the bolt head, and it was on the other side of the gimbal. The nut of this bolt turned out to be closer - by 14. I barely unscrewed it, spoiled it a bit. It is very inconvenient there and you need to immediately stock up on a flashlight - it is very dark there. We shone the phone.
They removed the air filter box and air duct, up to the throttle valve. The main thing is to remember which pipe goes where. There are 2 pipes that do not go anywhere - you can see the ventilation of something.
After that, they unscrewed the lower mount of the cardan - near the gearbox itself. Here everything is done with a ratchet wrench with mandrels. The bolt unscrewed easily, even without the WD. He removed the cardan mount from the shaft splines, threw it aside. There is one caveat - do not pull the gimbal too much - it flew out of the hole completely, and then the hole plug fell off in the cabin. But they did everything.
Then he drained the power steering fluid. I did not drain it from the tube, and removed most of the slurry from the tank with a syringe. By the way, I reused this liquid, so if I changed it recently, drain it into a clean container, it will come in handy. Then he removed the clamp from the rubber tube and removed it from the fitting. It turned out to be quite difficult. It takes a lot of effort - the tube fits snugly on the long fitting. It flowed from two places at once - from the fitting and the rubber tube. More from the tube. So prepare a small container here as well. I used the top of a plastic bottle - that was enough. The rest of the stack is in the bottle at the bottom - put something there in advance.
Then I twisted 3 metal tubes going to the gearbox. One is unscrewed with an ordinary open-end wrench for 14, the other two I did not dare to turn with open-end wrenches - I strangled the toad and bought a set of brake pipe wrenches. I was looking for such a key for a long time at 11 - nowhere was it. In our markets it was possible to find only 10, 12. Found in one expensive set. But he didn’t come in handy either — he didn’t climb. He unscrewed it with a key 12 from the same set. It has wide splines and a larger nut girth. So you could buy a cheap wrench with a 12 tightening screw and tighten it. Fortunately, my nuts were unscrewed without effort - I did not rip anything off. The steel tubes themselves are pulled out of the unit, too, with considerable effort. When I unscrewed the tube by 14, I made a problem for myself - my hand fell off and broke some kind of plastic fitting of a tube that goes into a black plastic bottle. There was an inscription like “FUEL TANK. ”Or whatever. Then I glued it with cyanoacrylate glue. The tube does not seem to carry loads, gasoline does not flow through it. So you have to be very careful - there are a lot of weak points around, you can easily destroy something.
Then he unscrewed the head 8 two bolts that secure the gearbox to the rack housing. The head of the bolts is a 6-point sprocket, so either turn with the sprocket or with the universal heads. It is better not to climb with a conventional hex head (without special grooves under the star) - it is fraught with breakdown. The bolts moved almost immediately - lucky.
I took the gearbox with the shaft out of the rail - sway a little and apply a little force - it comes out fine.
Then, hitting the upper part of the shaft with a hammer not very hard, they removed the shaft from the housing together with a large bearing. A small bearing with an oil seal remained in the housing. A head suitable for the diameter of the hole was pressed out in a vice and they came out too easily. Examined the old oil seal. Outwardly, it was undamaged, but it was severely hardened - the edge was no longer so tightly seated on the shaft. And then a rupture was found in this edge - apparently it flowed into it.
I washed all the parts with a WD-brush and a toothbrush - there was no gasoline at hand. Next, the oil seal was pressed in together with the bearing with a spark plug head - it came up to the diameter of the bearing and was of sufficient length.They were afraid to press in the oil seal separately - it is soft. The inner surface of the gearbox was pre-lubricated with dextron (power steering fluid). Everything stood up without distortions. They inserted a shaft with a bearing and slightly hammered it into the housing with a hammer - we went with a mandrel along the entire diameter of the bearing. The bearing did not reach the previous level by 2 mm - the large thickness of the stuffing box affected. Lubricated a large bearing with lithol.
They put everything together in the reverse order, fiddling with two steel pipes. At this stage, you can align the steering wheel, if it is not level - just turn the cardan to the slot to the left and right. By the way, before the whole operation, the steering wheel was screwed to the column with electrical tape - you can't turn it without a cardan - the train from the SRS is torn.
After assembling the air system, he poured slurry into the power steering tank to the eyeballs. He unscrewed the electrical tape from the steering wheel and started it for 5 seconds - the pump sucked in the liquid instantly! Here you need to watch out - the pump should not work at idle without slurry - it will burn out. After muffling, we added more slurry to the MAX level. Started up, the liquid left a little. I turned the wheel many times from end to end - bubbles came out - everything froth. When the bubbles stopped going, I muffled and refilled for the last time to the mark. Everything! The steering wheel turns even a little easier than before. Whether the repair helped - time will tell.
I didn’t take pictures - there are so many of them on the forums. It is recommended to print all the repair tips and photos - it helps not to forget anything. And it's better to do this repair together - it would be difficult for one.
My symptoms are a tight steering wheel and a leaking oil seal on the power steering pump.
There is very little information on the internet about the repair of power steering pumps. Basically, they write that it is easier to buy a new one, or on parsing, tk. hydraulic pumps are a very delicate thing, and improper operation, and the slightest wear, can lead to the failure of the entire pump. Therefore, in this article, I will try to collect as much information as possible about the repair of power steering pumps. I will draw conclusions about whether it is worth repairing or whether it is really easier to buy on analysis. (We have a cost of 4500 rubles.)
The pumps can be slightly different. I ended up without a ball bearing (rolling bearing), just an aluminum sleeve, i.e. sleeve bearing. But there are modifications of pumps, with a rolling bearing, and the size of the bearing is 35x15x11mm. And the pump is arranged a little differently, but in general the principle is the same. The only difference is in the fastening of the pulley to the axle (it is there on the nut), and in the place of the plain bearing, there is a rolling bearing.
At the end of the article, I will give links to articles on power steering repair that I found on the internet. After all, the more information the better ...
Repair requires:
- Repair pit, highly desirable. Although there are craftsmen, the pump was removed without a pit;
- A set of wrenches is better than ring wrenches (I do not recommend open-end wrenches, you can tear off all the bolts);
- A set of heads + a knob with a ratchet (it is possible without a ratchet);
- A screwdriver for picking out the old oil seal;
- Rem. kit No. 49591-6С925, price about 500 rubles;
(The repair kit contains o-rings, one large ring, a retaining ring, and an oil seal.)
- Power steering fluid (Nissan PSF or analogue DIII), for refilling. If you immediately change it completely, then you need somewhere 1l;
- WD-40;
- Daddy of plastic bottles with a capacity of 1 liter;
So let's get started
Next, we start the engine, immediately liquid will pour into the bottle, then turn the steering wheel back and forth, and turn off. Do not leave the engine running for a long time, otherwise the pump runs almost dry, this is bad for it. It takes about 20 seconds to drain to drain. In general, somewhere around 500-600 grams have merged, which is enough. In total in the system, somewhere between 800-900 grams.
Now the tank can be removed altogether, so that it does not interfere, for which we pull off the second suction hose from it by loosening the clamp.
Before removing the pump, while it is firmly fixed in its place, the outgoing high pressure line must be disconnected from it. (See photo 3) It is screwed on with a special, hollow bolt 22 or 24 (I don't remember exactly). It is better to unscrew the head from the pit.
Under the bolt and under the high pressure pipe fitting, there are two copper sealing washers, do not lose them when you unscrew the hollow bolt 24.These washers seem to be disposable, I bought washers of this size (16x22x2mm) in advance, I wanted to change them right away, but those that were my relatives turned out to be better than the new ones. I took new ones in the store of Russian auto parts. Later I put the old ones and nothing flows.
We unscrew it, take it to the side, so that it does not interfere.
Now you can remove the power steering belt and pump. (See photo 4)
Tighten the tension screw and release the belt tension. The pump itself does not move when the tensioning screw is loosened by moving the pump with your hands to the right, if you look at photo 4. Next, we completely unscrew the tensioning screw, the 12 nut fixing the bolt, in general, we remove three parts.
Next, we remove the pump itself. The pump is held on a bracket by a long stud bolt. But it will not be possible to completely unscrew this stud bolt, because the body wall interferes. You will have to remove the pump together with the bracket (bracket - see photo 8). To separate the bracket together with the pump from the engine, you need to unscrew the following bolts and nuts, watering them abundantly with WD-40, see photos 5, 6, 7.
Attention: Use spanners or sockets.
We unscrew the nut. It is better to use a spanner wrench, because do not crawl with the head.
You also need to loosen the bolt 12 from the engine compartment, which holds the reinforcement pipe (see photo 6). It is not necessary to completely unscrew it; it is enough to unscrew it by half.
Now we move under the car and work out of the pit. We unscrew everything that the pump holds, see photo 7.
Two long bolts 12 and a nut 14, under it a washer-engraver, do not lose.
The pump itself doesn't hold anything else. Now you can try to pull out the pump along with the bracket. But I could not do this, then we will pull out separately, first the bracket, then the pump. To separate the bracket from the pump, take out the long hairpin, which was screwed on with a nut by 14 (see photo 7). We pull out the hairpin through the hole in the pulley. Disconnect the pump from the bracket, the bracket can now be pulled out of the pit.
Next, you can remove the pump itself. The easiest way to get it out is here. (see photo 9) We take it out together with the suction hose.
By the way, the bracket is pulled out in the same place.
They've taken everything out! Here he is darling.
Let's start disassembling the pump
If possible, then the pump, it is better to rinse it well in gasoline, so that during disassembly the dirt does not get into the inner cavity of the pump.
I didn't have gasoline at hand, I didn't wash anything, I just wiped everything with a rag as I could.
Disassembling the pump does not require any special knowledge. Photo 11 shows that everything is simple ...
When disassembling, remember how the tensioning bracket stood, into which holes these two bolts for 12 were handed. Otherwise, the first time I put it wrong. There it turns out you can screw it into the nearby holes. They are the same with carvings. I realized this when the pump began to be installed. I had to remove the pump again and twist the tension bracket. Photo 19 shows in red, in which holes you need to attach the tension bracket.
I did not unscrew the suction pipe, because it is screwed on special. bolt under the inner sprocket, somewhere by 4 - 4.5mm. (see photo 12) I didn't find one, I had to go to buy. And they only sell sets, for h.z. what money. I didn’t have a leak at the point of attachment of the pipe, so I didn’t start screwing in and unscrewing this bolt.
Although, if it is possible to unscrew it, then it is advisable to change the sealing ring, which is in rem. included.
In general, we disassemble everything, remember how it stood, in order to collect everything the same way.
Next is a photo, in the sequence of disassembly. (nothing complicated)
Photo 13. The back cover is removed.
Photo 14. The part under the cover is separated. It is not attached in any way, it just takes root with the back cover.
Photo 15. Seizures are visible on the working surface. Apparently this is a consequence of working without a working fluid.
To remove the rotor, you need to remove the retaining ring. I did it with a screwdriver.
Photo 16. There are also seizure marks on the end of the rotor.
When removing the rotor, be careful not to let the blades fall out. It is advisable not to touch them or hang out.Let them stand in their places.
You can pull out one at a time and check their condition. I have them in perfect, polished condition.
Photo 17. Everything is filmed. Two holes are visible, throttling valves are inserted there (see photo 20).
The pulley on the axle sits firmly, set on hot. There is no need to remove it.
The axis is simply smooth, the working surface of the plain bearing.
Photo 18. Pulley and axle.
Photo 19. Front of the pump. The oil seal is removed.
The sleeve of the plain bearing is visible, with channels for bearing lubrication.
The holes are marked in red where the belt tensioner bracket is attached.
The new stuffing box is hammered all the way into it, using a socket head, slightly smaller in diameter than the stuffing box itself.
Unfortunately, I did not take a photo with the oil seal installed. But there is nothing complicated there.
Photo 20. Throttle valves.
Throttle valves are the same in perfect condition. Apparently they are all right.
Next, we assemble the pump in the reverse order. Installing a new large o-ring and retaining ring.
The rest of the rings are made of rem. no kits were needed, apparently for another version of the pump with a rolling bearing.
The assembly did not cause any difficulties, everything is good and simple, this is how it should be in a Japanese car ... ;-)
Only when installing the pump to the machine, do not tighten the nut by 14mm, see photo 7. If you tighten it tightly, then when the belt is tensioned, the pump will move very badly. It is necessary to tighten so that the pump moves with a slight interference.
As the pump is installed, the belt is tensioned, we fill in the slurry and start the engine. We turn the steering wheel in all directions, top up the rest. The level will at least be less than it was before the repair, because a little spill, something will remain on the walls of the plastic bottle. My level turned out to be at MIN, in principle, you can ride, but it is advisable to top up to MAX. I topped up somewhere about 60 grams.
Conclusions:
Well, what conclusion to draw. And the conclusion is that you need to change the pump, because those seizures that are visible cannot be eliminated, they apparently disrupt the operation of the pump. As I understand it, where there are seizures, there should be a perfect smooth surface. If this surface is absent, then there is a kind of bypass, from one working chamber to another, i.e. recirculation inside the pump, and it does not create the required pressure. This is especially evident when you drive 10-15 kilometers, and the working fluid heats up and becomes liquid like water, and then the pump stops creating pressure. Because of this, the steering wheel is taut if you turn it while standing still. And in the morning I started the car, the steering wheel is light, as if the wheels do not touch the ground, because cold working fluid is more viscous.
I read it in the internet. That a tight steering wheel, they say, is a consequence of a dying cardan, which is at the steering rack itself. He is constantly in the dust, so he stings him. But then it would wedge, even in the morning, but I have wedges only when the working fluid warms up. In general, it is advised to spray on the WD-40 cardan and, like, if the steering wheel becomes lighter, then this is the cardan. I sprayed, it gave nothing. Although, in theory, the cross in the cardan would not hurt to change. I will change, but then ...
I also think. I have Castrol TQ DIII working fluid. And the original should be filled with Nissan PSF. Maybe you need to fill in PSF? If it is thicker, then how will it behave in our frosts (-35)?
But it seems to me that PSF will not help, they are bad guys ...
But in general it suits me, even if it is, the main thing does not flow anywhere. The main goal was to change the oil seal. And you can still drive with a tight steering wheel, especially since it is not quite tight. And it is taut only when you stand in place, not so of course if you drown out the engine at all, there generally cannot be cranked on the spot, but the work of the power steering should not depend on the heating of the working fluid. If on the go, it does not bother you too much, I'm used to it already.
![]() |
Video (click to play). |
Useful links to resources:
Information about pump repair, everything that could be found on the internet: