In detail: do-it-yourself aeg perforator repair from a real master for the site my.housecope.com.
Even very reliable Makita rotary hammers break down over time.
Any breakage is eliminated, you just need to have straight arms and perseverance.
In addition to electrical malfunctions, rotary hammers are also susceptible to mechanical damage.
Operation of rock drills with hard materials in dusty environments will shorten the service life and require user intervention to perform preventive maintenance.
Any tool repair begins with determining the nature of the malfunction and disassembling.
The Makita 2450 and 2470 hammer drill can be repaired by a user who has basic locksmith skills and is familiar with electrical safety requirements.
This article discusses the mechanical part of the Makita rotary hammer, the main malfunctions and how to fix them.
Dismantling the mechanical part of the Makita 2470 rotary hammer
To get to the mechanical part of the hammer drill, you need to remove or disassemble the cartridge.
Dismantling the quick-release chuck
Place the punch on the rear case cover on a tabletop covered with a clean cloth or paper. Using tweezers or a screwdriver, remove the rubber tip 35, item 1.
Carefully loosen the annular spring, pos. 2, the coupling cover, pos. 3, and the steel ring, pos. 4. You will reach a steel ball with a diameter of 7 mm pos. 20.
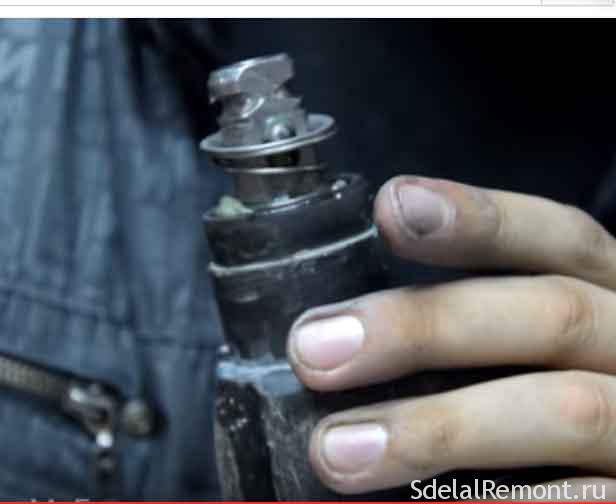
Now you can remove the housing of the mechanical part
It is black.
Using a screwdriver, unscrew the four screws at the end of the case.
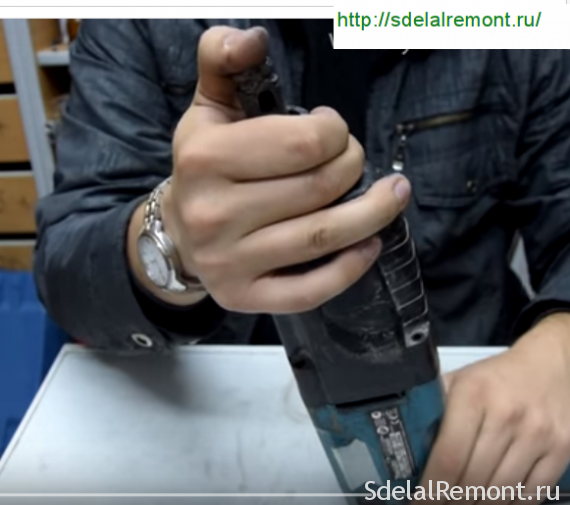
Holding the black case with your right hand, press your thumb on the end of the shaft from which the cartridge was disassembled. The plastic housing can be easily removed.
Next, you need to remove the gearbox shaft.
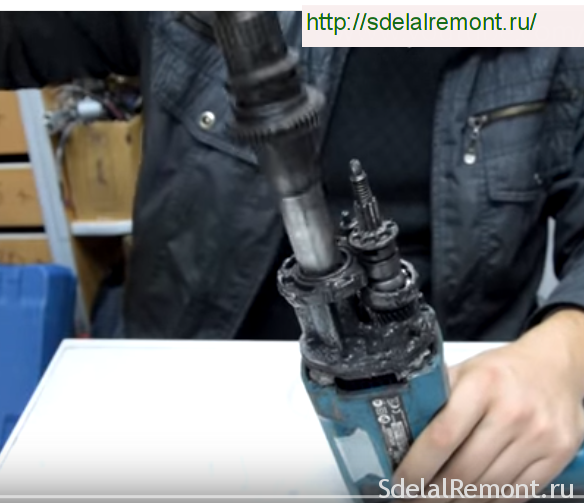
To disconnect the mechanical part from the electrical one, you must first remove the electric brushes.
Remember! In the lower part of the housing, the rotor is held by electric brushes, which must be removed.
After checking that the electric brushes are disconnected from the rotor lamellas, use a screwdriver to pry the metal housing of the hammer drill at the border of the green plastic housing.
![]() |
Video (click to play). |
Now we turn to disconnecting the rotor from the mechanical part of the perforated
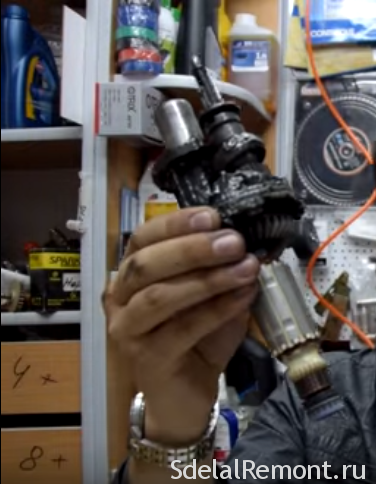
If you take the rotor housing in one hand and the mechanical housing in the other and pull in different directions, swinging, you will separate these two units.
You will get such a unit in the old grease.
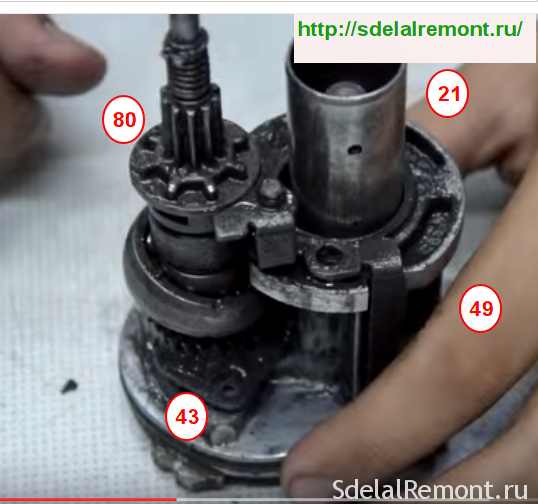
Then unscrew with a hexagon two bolts M4 × 12, pos. 43., art. 266273-7 with an internal hex head.
Pull out the shaft with the intermediate spur gear 10 pos. 80, art. 226399-7.
from the inner case, pos. 49, art. 153687-8. Remove old grease from parts.
You will get such a mountain of clean details.
Now carefully look through the details, discard the rubber rings immediately after picking up new ones.
Replace the defective parts with new ones.
Frequent mechanical failures of Makit punchers include:
- destruction of the quick-release chuck;
- failure of bearings;
- breakage of the striking mechanism;
- drill barrel wear;
- wear of striker and striker rubber bands;
- breakage of gears.
The hammer drill chuck is repaired to replace the boot and rubber ring, as well as the conical spring and the steel ball, which secures the working tool (drill). This is indicated by what is a working tool? namely, the drill does not hold well in the chuck.
The main reason is the wear of the steel ball 7.0, item 20, art. 216022-2. The wear of the ball occurs from contamination of the bore of the cartridge due to the ingress of dust and dirt.
The general view and device of the Makit perforator cartridge is shown in the photo below.
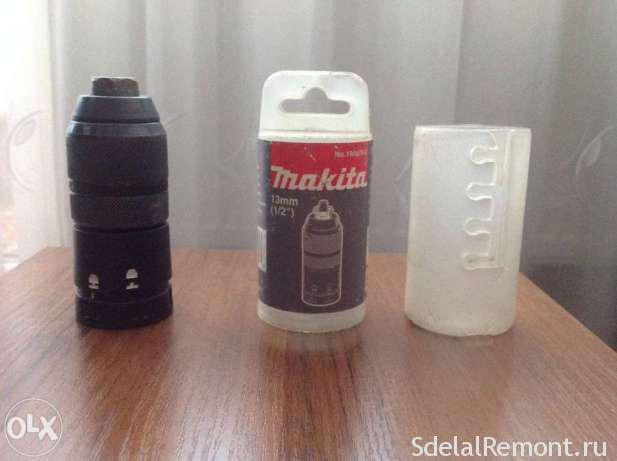
Do-it-yourself repair of the makita 2450 perforator cartridge is easy.The cartridge must be disassembled, freed from old grease, discarded rubber parts, replaced defective.
More complex malfunctions require knowledge of the mechanical part of the Makita 2450 perforator.
Having determined the nature of the malfunction of the Makita perforator, proceed to disassemble the mechanical part, called the gearbox.
Disassemble the mechanical part according to the attached video.
Free it from old grease.
Carefully inspect all parts, their integrity, level of wear. All rubber products require replacement during any disassembly.
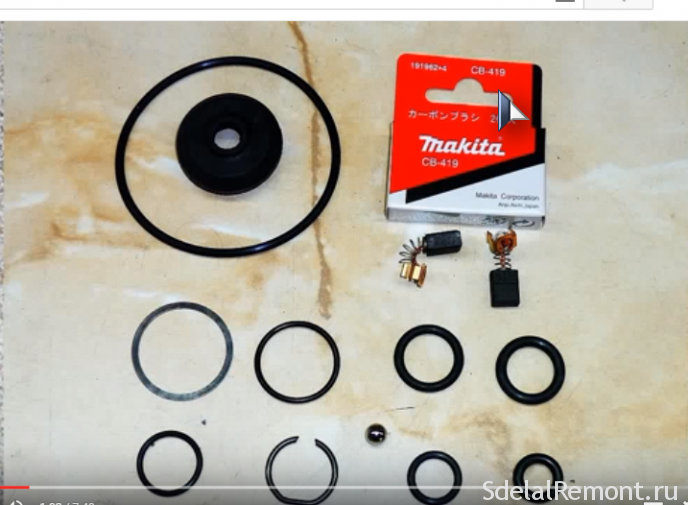
Consider repairing the barrel of a rock drill. Let's analyze the mechanism completely.
Video of disassembly, lubrication and assembly of the Makita perforator
Remember! In the lower part of the housing, the rotor is held by electric brushes, which must be removed.
The next step is to disconnect the rotor from the removed mechanism. The rotor is simply disconnected from the mechanism by pulling it out, since it is held by the friction of two helical gears.
The result is such a dirty knot.
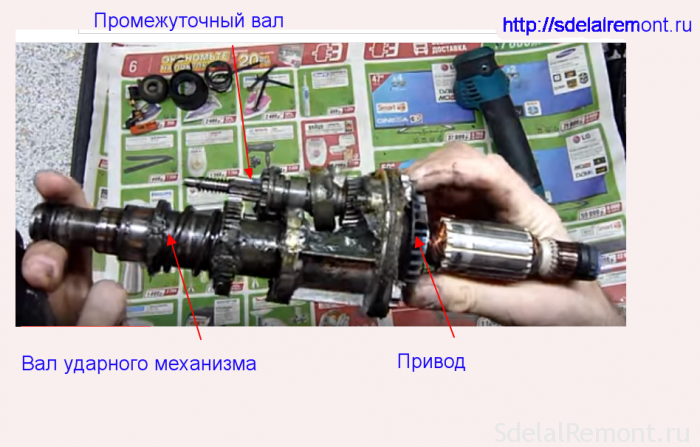
Now we need to separate the percussion shaft.
Most often, the rubber rings wear out, the firing pin pos. 24, compressor spring pos. 18. and cylinder parts.
This is how barrel parts wear out and break down when the tool is misused.
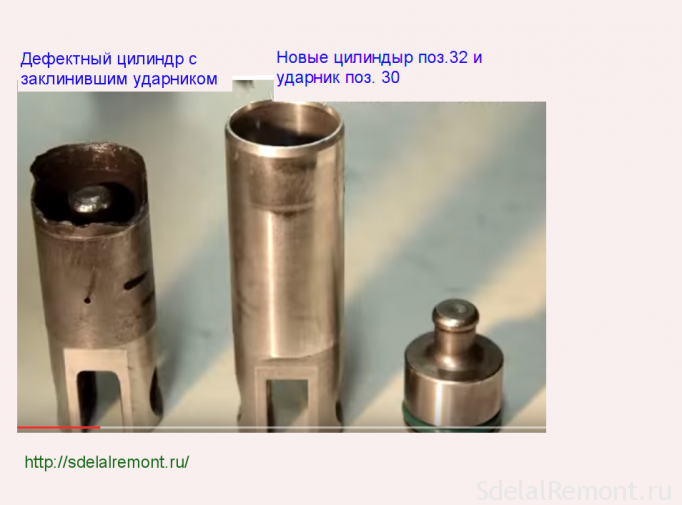
Consider the most difficult malfunction - the failure of the percussion mechanism.
The characteristic signs of a breakdown of the percussion mechanism are the absence of a blow and the unpleasant noise of a working perforator in the "Blow" mode.
Such a malfunction is typical for those rotary hammers that, during operation, were strongly pressed against the surface to be treated.
Having disassembled the gearbox, we remove debris and pieces of foreign objects. We find the faulty part and clean everything from the old grease.
Very often, the firing pin pos. 24, art. 324396-8, which is part of the barrel.
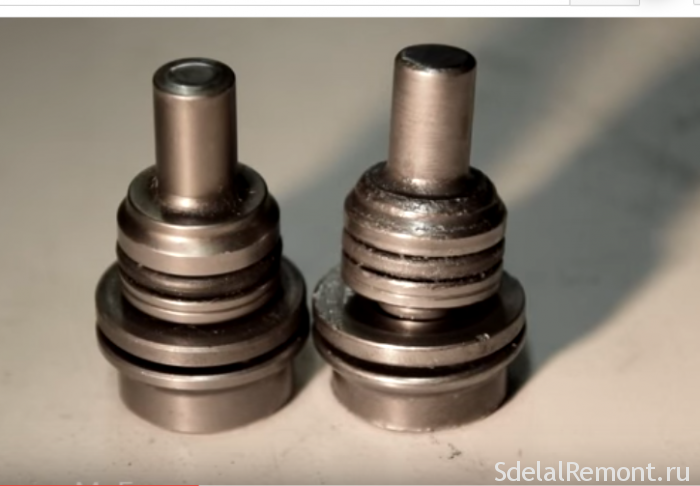
metal ring pos. 27. art. 324216-6.
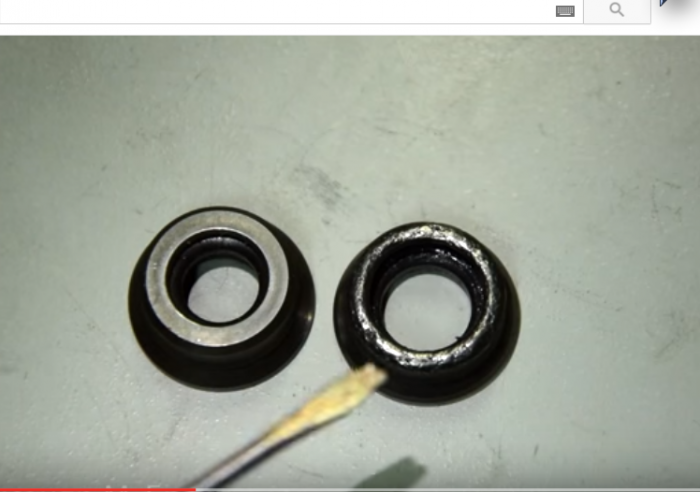
Discard damaged parts, replace with new ones, cover with a thin layer of grease. The parts are ready for assembly. But more on that in the next article.
They threw out at work the perf, seemingly killed in the trash, all in fuel oil, sand and with a cord cut off at the root. Another screwdriver is the same, but about him later. I pulled it home, the stator windings rang, both 2.7 Ohm each, only the plastic insulation was slightly melted. Well - I think if the same resistance means whole ... The anchor didn’t even ring the bell. everything looks OK with him, clean without darkening the insulation ... In general, I decided to build up the wires and plugged it into the outlet ... WORKS!
Dick if he was thrown out, I thought)))) I decided to disassemble it completely and clean it ... How I started at home, in the bathroom ...) I immediately cleaned all the plastics from the case, then began to half it, I could not make it out for about 40 minutes. all the bolts were under a centimeter layer of black fuel oil ... I downloaded the diagram for it:
And I found a couple of bindings hidden under a layer of mud. I cut it in half and oh ... ate ... I did it like half the case, and the bathtub is already dirty))) I thought I wouldn’t play with my wife’s nerves, I’ll wash the gearbox in the garage. And he began to scrub the tub of powder.
The next day I drove to the garage with an armyinby
He chopped his car, and I cleaned everything of coke in a hammer drill and helped him along the way: he hung in the garage
In general, how I cleaned everything up. I got to collect it) I came home and let's pick everything up according to the scheme)) Here is a photo:
Audi A4 Avant 2004, diesel engine 1.9 l., 130 hp sec., front-wheel drive, variator - DIY repair
my AEG is 14 years old (he killed so that 5-7 perfs fell from competitors, and I just bought new cartridges). And here the other day the blow disappeared (that is, when the button is pressed weakly, it hollows, and when completely it disappears). I decided to figure it out and got into a dead end (I can not remove the lower switch). rummaged through net, did not advance a single step until I came across your Oleg schemes (I'm sure they will come in handy). If it doesn't make it difficult, tell me how to remove it (I don't want to break it, because in our LPR I only think of such a device) When I drove a car from Szczecin (Poland), I bought this German there. By the way, there are three more differences to the schemes 261 262 276 ...
Honestly, I don’t remember how I ripped it out, but I remember that I suffered with it. But I didn't seem to break it) The recordings have been for almost a year, but the perf works as it should.
why are these entries in the BZ car?
Why in BZ cars of chicks with naked asses are photographed?
there at least in the background of the car
Soon people will start writing cake recipes in the BZ))
Why do you have in the BZ: Photoset at a gas station, Club card Volkswagen Technical Site (VWTS), Reviews about ZIC 5w30 oil, Summer PhotoSeason_2015, "Teaser" and most importantly: Help with answers (temporary entry) which has been hanging for 2 years)) ) Keep track of your BZ. If you don't like mine, just don't litter comments, no one asks you to climb here)
How easy it is to hook you!
Calm, and again calm! And it was not too lazy to watch my BZ.
If you don't want to read other people's comments, turn off the ability to write them.
So I'm calm) As they say, you can reach the post. It's just that it's more interesting for me to describe an independent repair here, even if it is a washing machine, a puncher or something else, than hammering the BZ with the same type of assemblies of pictures of the car in different places and taking pictures of friends with naked asses)) In reality, at least this would like to diversify your BZ, especially in the garage it was spinning. And with recipes you go too far 😉
May be )))
In any case, honor and praise to you for the work done 👍🏻
Anyone who has ever had to work with a hammer drill knows how difficult its operating conditions are. That is why do-it-yourself punch repair is such a popular request on the Internet. And today we will tell you absolutely everything regarding the repair of this tool.
Undoubtedly, the owners of such expensive equipment want their devices to be of high quality, to do their job 100%. First of all, correct use of the tool will save you from serious damage, which we will talk about a little later. And, of course, the device was repaired on time. At the same time, any small failure should already become a cause for concern and preparation for repair.
So, such "beacons" can be:
- Unstable work of the punch in the working mode;
- The appearance of strange sounds when turning on the punch;
- The smell of burning;
- The hammer drill does not hammer, although there is no apparent reason for this.
As soon as something like this happens to your equipment, it means it's time to repair. Like any such work, it requires care, understanding the cause of the breakdown and knowledge of how to cope with it. And your very first step in repairing is disassembling the tool into its components. For many, even this stage causes difficulties, and therefore it is necessary to know everything down to the nuances - how, what and why!





Just imagine that your tool suddenly stops working or you urgently need to replace any defective part. The easiest way is to take the hammer drill to a service center for repair, but this takes time, which means it will stop your work for a while. But if you know how the device is disassembled, it will be much easier for you to carry out the rest of the work. In addition, this will lead to significant cost savings, because there will be no need to spend money on paying for the services of repair centers.
Instructions for parsing the tool:
- We start work, starting from the upper unit: first, the rubber tip is removed, then the washer, the spring, the ball finishes working.
- After you have removed the ball, we unscrew the screws that hold the case, remove the cover on the handle, if available, and lastly disconnect the stator wires.
- We remove the brush holder.
- The next step is to separate the gearbox and housing until a gap forms. It is through it that we will retrieve the switch.
- After that, the punch body is placed vertically, with the help of a vise, it is fixed, and all its parts are carefully removed from the device.
Whatever breakdown awaits you, clean the case - sometimes it is dirt and dust that prevent the device from working normally.
You should be as prepared as possible to repair a device such as a hammer drill, which will keep financial and labor costs to a minimum. It's not bad if you are more or less familiar with the construction of a punch, you know what parts and assemblies it consists of, which will allow you to quickly replace a broken part. Most often, the repair of a perforator is reduced to a banal replacement of the "flying" elements, which include:
- Anchor;
- Brushes;
- Gears;
- Starters;
- Bearings;
- Network cables;
- Switches.
It is worth noting that the easiest way to repair light tools, given the fact that such a hammer drill is perfect for construction work at home.... But breakdowns of more serious equipment are much more difficult, and only professional craftsmen can handle them. In any case, no matter what class of tool you are interested in, find a model with a vacuum cleaner - this device will save you time for cleaning, and also make your work safer, as it reduces the amount of dust.
Another problem is the breakdown of the windings, rewinding of the armature and starter, which also arise from dust. Repair consists in thorough cleaning and replacement of those parts that cannot be repaired. However, "prevention" is a more reliable method. To do this, you need to clean the device every two weeks, soak it with varnish or grease. By the way, the choice of a lubricant must be carefully considered. So, there are several rules. First, it is better to purchase a solution from the same manufacturer (Bosch, Makita, Enkor), as the perforator itself, in this case, in terms of its composition, oil or varnish will be ideal. If such a composition is not at hand, a diesel engine oil is perfect for you.
The second most popular cause of breakage is brush wear, no matter how much your tool costs - even the most expensive models are prone to this problem. It is very easy to replace them: we disassemble the perforator according to the above described scheme, find worn brushes and put new ones in their place. You just need to correctly determine which of them is best used: coal, graphite or carbon-graphite. So, graphite ones have a long service life, however, due to the hardness of the material, the collector may suffer. Carbon elements have a short life, but they have high-quality contact with other parts of the hammer drill. The purchase of the third option is considered optimal and inexpensive.
There are also problems with the mechanical elements of the device. Each model is equipped with switching modes, and they often fail, especially on cheap devices. The algorithm of work is the same - we disassemble the puncher, find the broken parts, replace them. The main thing is to purchase items suitable for this model. A similar problem often "haunts" cartridges that are exposed to maximum stress. First of all, protect them from dust and dirt by rinsing the elements with grease. But if the cartridge is still broken, we will have nothing to do but change it.
Now you know how to fix a hammer drill and see that most of the breakdowns come down to simple cleaning or replacing defective parts. But if you disassembled the tool, and there are no apparent reasons, it is better to take the device to a service center - specialists will quickly find the cause and eliminate it.
A hammer drill is a tool without which it is impossible to imagine most of the construction and repair work today. Therefore, today every person associated with such works aspires to have this tool. A video about the repair of a hammer drill will be interesting to everyone who wants to be able to independently repair the breakdown of this tool.
To know what exactly needs to be repaired, it is worth understanding the reasons for the breakdown of the hammer drill. This video will help you to do this.
If you hear an uncharacteristic "rustle" or feel that the drill "slips" while working with the hammer drill, it is time to replace the bearing. This video will tell you how to do this.
The rotary hammer reducer is designed to transmit rotary motion to the chuck from the engine. This is what drives the impact mechanism. The gearbox must be disassembled to replace or lubricate parts. You will learn how to do this in the video.
Another story about the disassembly of the gearbox.
For. To prevent the perforator from breaking and failing, you need to properly care for it. Regular lubrication of the rock drill is one of the prerequisites for proper tool care. To lubricate the hammer drill, it must first be disassembled. You will learn how to do this by watching this video.
Protecting the rock drill from dust is wasting its service life. If you want to know how you can make a dust protection for your instrument with your own hands, watch this video.
One of the indispensable tools for installers of all stripes on a construction site since the beginning of the 20th century has been and will be a perforator. This tool is essential for punching technological holes in concrete and monolithic structures.
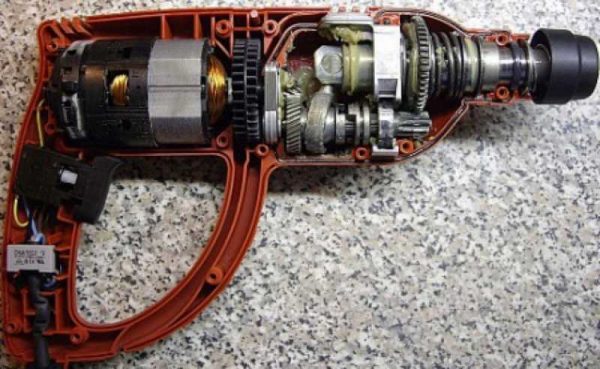
The most common malfunctions in machine components are:
- wear of brushes;
- breakage of the start / stop button.
In this case, the above problems may be accompanied by:
- unstable work;
- extraneous noises and sounds;
- the smell of burned wiring;
- inability to work in a given mode - crushing / drilling.
The reason for disassembling the tool is the dilapidated state of the boot of the cartridge. To avoid this, you only need to work with long drills in the future. However, the problem is not always in these details, and so that you can understand the nuances of repairing this device, in the article we will tell you what can be useful to you in this matter.
Cleaning and lubricating the rubbing parts of the mechanism is possible only when the device is completely disassembled, which, in order to avoid major breakdowns, should be carried out regularly. It is necessary to disassemble the device from the upper assembly of parts. First you need to remove the rubber tip. When you do this, you will see the lock washer. After removing it, the head and spring are removed. Take out the ball. The disassembled parts are best folded into a separate container prepared in advance so as not to get lost. The procedure for opening the case must be carried out after opening the gap in the case by at least five millimeters. The switch handle should be in the hammer drilling position, then it can be safely removed. Then you can remove the case.
One of the most expensive and costly parts in the repair of a hammer drill is the so-called anchor. These are copper coils interconnected and bonded by lamellas. In the event of a violation of the insulation of copper wires, a short circuit and a breakdown of the wiring occurs, therefore, the entire part of the engine must be replaced.
Complete disassembly of the gearbox is a necessary procedure to diagnose problems with this assembly. After dismantling the plastic housing, removing the remnants of the old grease, you will have to disconnect the following parts:
- floating bearing;
- drive gear shaft;
- raster sleeve;
- sleeve with a piston.
The floating bearing is fixed in the aluminum housing with a metal bracket. It should be wrung out with a flat screwdriver. Then you need to take out the bearing and replace it if necessary. In the design of the floating bearing there is also a needle bearing, which is necessary for the rotation of the drive gear. He has to experience great overload, and, as a result, he often breaks down. You can buy it either as a set or separately from the shaft.
An impact bolt is fixed in the grid sleeve by means of a metal impact ring. The ring is accessed through two side holes. A steel striker is located inside the bolt. It is advisable to replace the sealing rubber bushings, which are necessary for the tightness of the mechanism. In the process of replacing the parts of the striker, it is necessary to grease abundantly.
This model is famous for its short-lived collector. Often overheats, a pungent plastic smell appears. Breakdowns are common. Strong vibrations, noise. Differs in a large mass.
Brushes need to be changed frequently. The design has some minor usability flaws. The on / off button burns out easily when it gets jammed. Bearings need to be changed frequently. The gearbox fails occasionally. The lubricant is constantly flowing, there is a strong overheating in the "jackhammer" mode, especially during intensive work.
Overheating of the tool in the "drill" mode. There are malfunctions in the speed regulator. Large tool mass. There is a high probability of chuck jamming due to dust ingress. Demanding tension.
Differs in a large mass. Convenient design. Reliable, but sometimes the bearing sinks in the chuck.
Short-lived in work. Rapid heating during operation. High probability of breakage of the mode switch.
Differs in a large mass. Overheats during constant operation. Intensive wear of the conductive track in the controller board, low speed often disappears.
Very high probability of breakdowns. Poor shifting of the side handle, frequent overheating of the tool even at negative temperatures. The fragility of the brushes. Sometimes grease starts to flow. Poor chuck clamping - the presence of play in the fastening of the drills.
Poor tool lubrication. Occasionally, there is a malfunction in the "crushing" mode. Unstable handle attachment. Uneven engine operation after a short period of time. Rapid wear of brushes.
Unreliable reverse mechanism. Motor breakdowns occur. The mode switch is stuck.
Brushes fail. The gear unit is not securely attached to the tool. There is a radial runout of the flare sleeve. Spins a peak when crushing. Frequent overheating.
Sometimes the stator fails.
This model is characterized by poor lubrication of rubbing elements. The rubber protective cover of the start button often breaks.
For a long service life of the tool, before work, you should always carry out its technical inspection so as not to miss any defect. Always keep the tool clean after finishing work. You can clean it from dust with a vacuum cleaner. It is imperative that you familiarize yourself with the operating standards of the device recorded in its technical passport. Store in a warm and dry place. If you do not use the puncher for a long time, it is advisable to place it in a sealed package. Avoid getting moisture and condensation on the body of the device.
Even very reliable Makita rotary hammers break down over time.
Any breakage is eliminated, you just need to have straight arms and perseverance.
In addition to electrical malfunctions, rotary hammers are also susceptible to mechanical damage.
Operation of rock drills with hard materials in dusty environments will shorten the service life and require user intervention to perform preventive maintenance.
Any tool repair begins with determining the nature of the malfunction and disassembling.
The Makita 2450 and 2470 hammer drill can be repaired by a user who has basic locksmith skills and is familiar with electrical safety requirements.
This article discusses the mechanical part of the Makita rotary hammer, the main malfunctions and how to fix them.
Dismantling the mechanical part of the Makita 2470 rotary hammer
To get to the mechanical part of the hammer drill, you need to remove or disassemble the cartridge.
Dismantling the quick-release chuck
Place the punch on the rear case cover on a tabletop covered with a clean cloth or paper. Using tweezers or a screwdriver, remove the rubber tip 35, item 1.
Carefully loosen the annular spring, pos. 2, the coupling cover, pos. 3, and the steel ring, pos. 4. You will reach a steel ball with a diameter of 7 mm pos. 20.
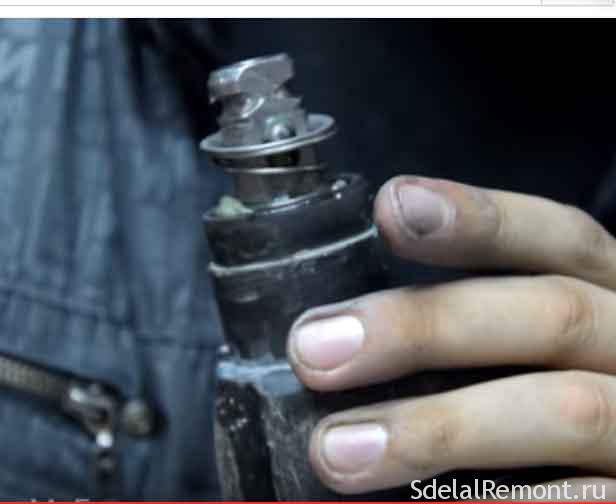
Now you can remove the housing of the mechanical part
It is black.
Using a screwdriver, unscrew the four screws at the end of the case.
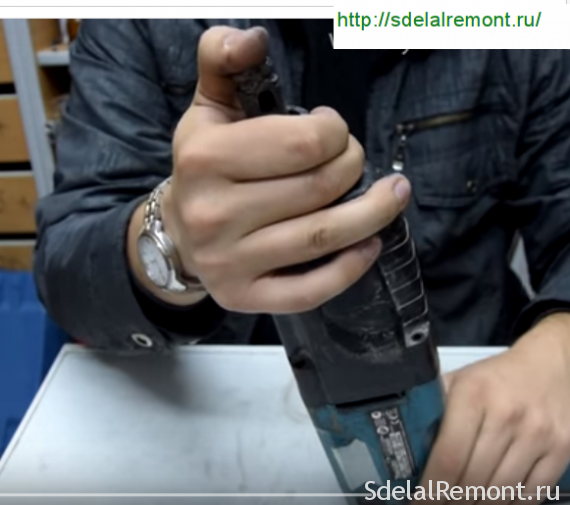
Holding the black case with your right hand, press your thumb on the end of the shaft from which the cartridge was disassembled. The plastic housing can be easily removed.
Next, you need to remove the gearbox shaft.
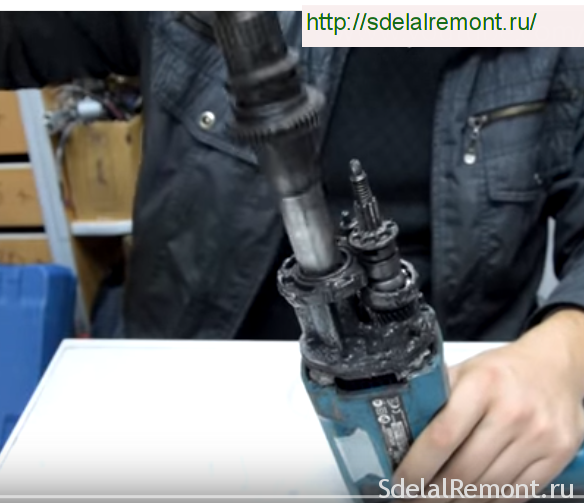
To disconnect the mechanical part from the electrical one, you must first remove the electric brushes.
Remember! In the lower part of the housing, the rotor is held by electric brushes, which must be removed.
After checking that the electric brushes are disconnected from the rotor lamellas, use a screwdriver to pry the metal housing of the hammer drill at the border of the green plastic housing.
Now we turn to disconnecting the rotor from the mechanical part of the perforated
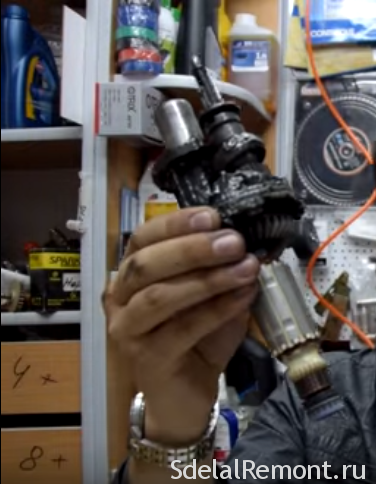
If you take the rotor housing in one hand and the mechanical housing in the other and pull in different directions, swinging, you will separate these two units.
You will get such a unit in the old grease.
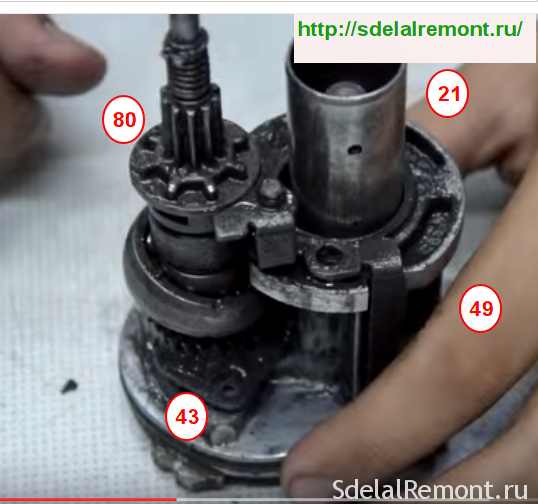
Then unscrew with a hexagon two bolts M4 × 12, pos. 43., art. 266273-7 with an internal hex head.
Pull out the shaft with the intermediate spur gear 10 pos. 80, art. 226399-7.
from the inner case, pos. 49, art. 153687-8. Remove old grease from parts.
You will get such a mountain of clean details.
Now carefully look through the details, discard the rubber rings immediately after picking up new ones.
Replace the defective parts with new ones.
Frequent mechanical failures of Makit punchers include:
- destruction of the quick-release chuck;
- failure of bearings;
- breakage of the striking mechanism;
- drill barrel wear;
- wear of striker and striker rubber bands;
- breakage of gears.
The hammer drill chuck is repaired to replace the boot and rubber ring, as well as the conical spring and the steel ball, which secures the working tool (drill). This is indicated by what is a working tool? namely, the drill does not hold well in the chuck.
The main reason is the wear of the steel ball 7.0, item 20, art. 216022-2. The wear of the ball occurs from contamination of the bore of the cartridge due to the ingress of dust and dirt.
The general view and device of the Makit perforator cartridge is shown in the photo below.
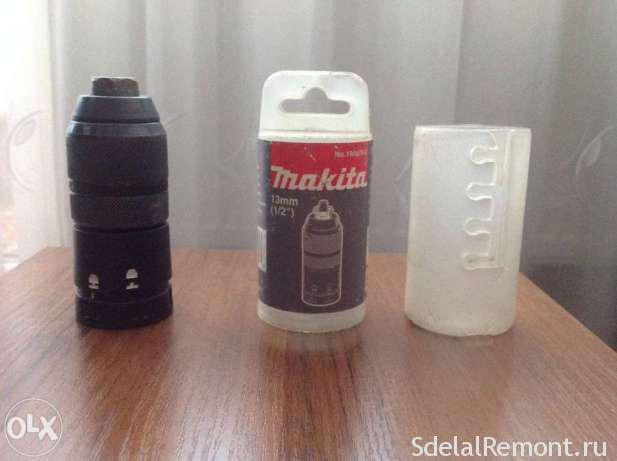
Do-it-yourself repair of the makita 2450 perforator cartridge is easy. The cartridge must be disassembled, freed from old grease, discarded rubber parts, replaced defective.
More complex malfunctions require knowledge of the mechanical part of the Makita 2450 perforator.
Having determined the nature of the malfunction of the Makita perforator, proceed to disassemble the mechanical part, called the gearbox.
Disassemble the mechanical part according to the attached video.
Free it from old grease.
Carefully inspect all parts, their integrity, level of wear. All rubber products require replacement during any disassembly.
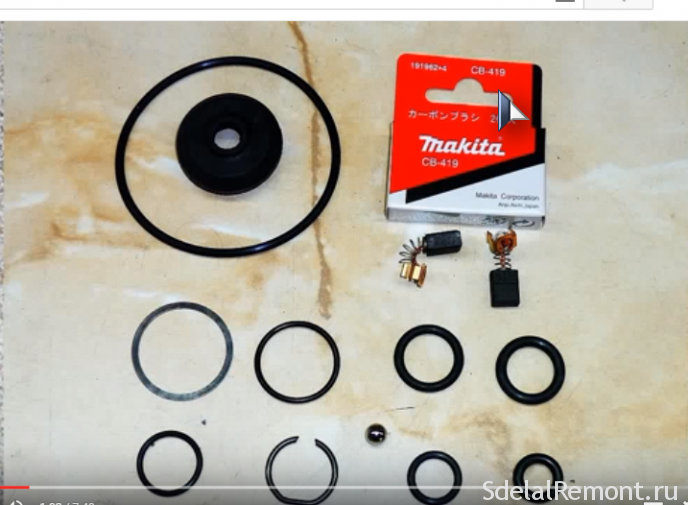
Consider repairing the barrel of a rock drill. Let's analyze the mechanism completely.
Video of disassembly, lubrication and assembly of the Makita perforator
Remember! In the lower part of the housing, the rotor is held by electric brushes, which must be removed.
The next step is to disconnect the rotor from the removed mechanism. The rotor is simply disconnected from the mechanism by pulling it out, since it is held by the friction of two helical gears.
The result is such a dirty knot.
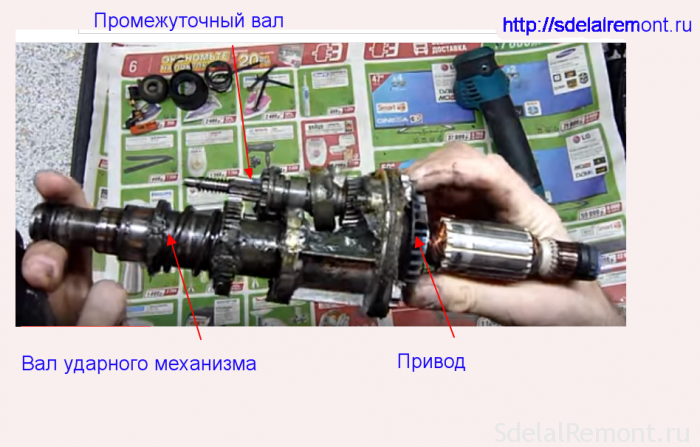
Now we need to separate the percussion shaft.
Most often, the rubber rings wear out, the firing pin pos. 24, compressor spring pos. 18. and cylinder parts.
This is how barrel parts wear out and break down when the tool is misused.
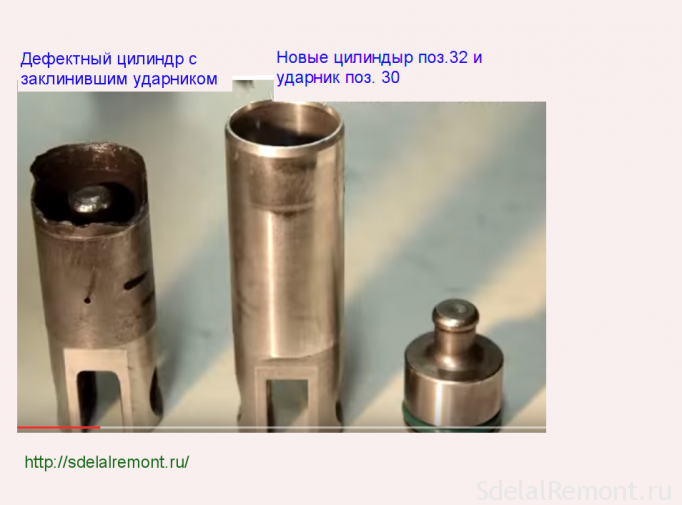
Consider the most difficult malfunction - the failure of the percussion mechanism.
The characteristic signs of a breakdown of the percussion mechanism are the absence of a blow and the unpleasant noise of a working perforator in the "Blow" mode.
Such a malfunction is typical for those rotary hammers that, during operation, were strongly pressed against the surface to be treated.
Having disassembled the gearbox, we remove debris and pieces of foreign objects. We find the faulty part and clean everything from the old grease.
Very often, the firing pin pos. 24, art. 324396-8, which is part of the barrel.
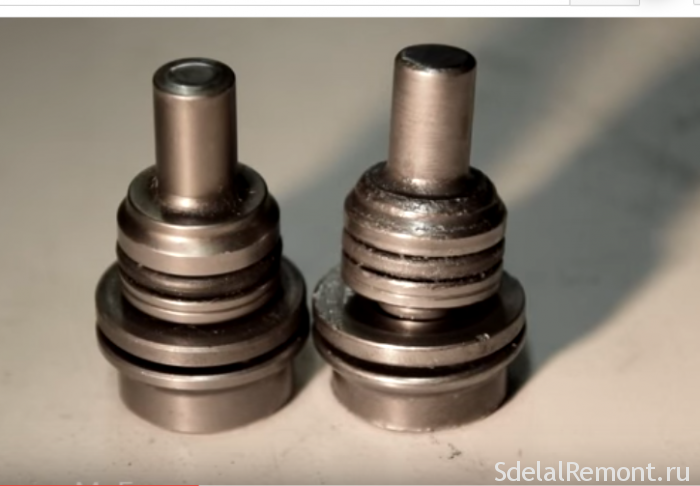
metal ring pos. 27. art. 324216-6.
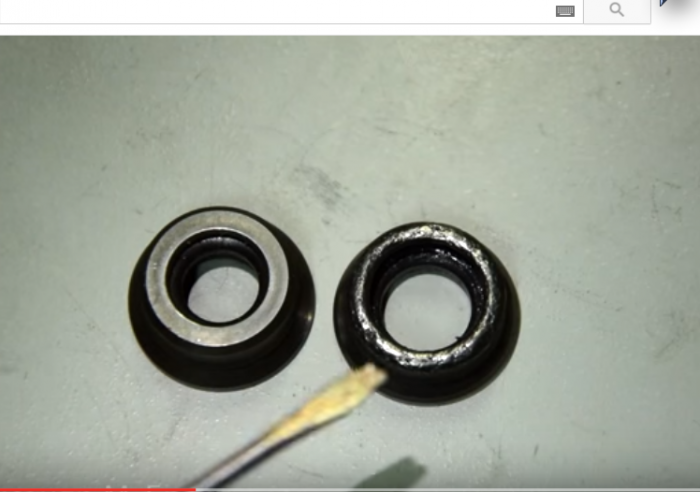
Discard damaged parts, replace with new ones, cover with a thin layer of grease. The parts are ready for assembly. But more on that in the next article.
Hello everyone! Today, when chiseling, I began to throw oil out of the AEG reducer (something there) superX, which has a capacity of 1024 watts. , do not bother with repairs (I gave it once, on Sladochnaya Street, repairs cost money), but buy instead? I really want a really reliable perf.
PS: in some branch, someone argued, they say, AEG-unkillable, so I have a Kress 750 with 97g. is still alive and has never been repaired, and after a year the AEG was repaired - it began to work in slotting mode with simple drilling).
Pablont wrote:
Should I fix the AEG hammer drill again, or buy another one?
Buy ANOTHER AEG, new
My AEG stopped a month after the purchase. The guarantee was refused - replacement of the brushes. Rhetorical question: How did the brushes in the expanded AEG in normal operation run out of service in a month? True, they took money only for the brushes, the replacement work is free. After that (t-t-t) everything is all right. So the AEG label means nothing at all, lottery, mlyn.
Hilti 12S has more than twenty years of experience and even without changing brushes.
By the way, on the punch, on the body, you can see numbers to know the depth of the hole. I don't remember if there is such a feature in other models.
In general, the AEG instrument has deteriorated. I have a parquet floor and two shura

Now I looked at the analogue AEG-Milwaukee, the protection against vibration, it vibrates strongly, the fix-stack cartridge is also not very good, the cartridge began to fall out of this fixture. Probably, I will buy Divolt D 25113 K, cheap and angry

PS: I wanted Makitka, but something went down with the quality.
Pablont wrote:
the chuck with the chisel just fell out of the quickfix several times
Strange and highly doubtful. This cartridge is as simple as a felt boot. Very reliable.
vik wrote:
Hilti 12S has more than twenty years of experience and even without changing brushes.
Well, this is generally a megadevice. By the way, you can buy on Ibei, ideally for ridiculous money.
vik wrote:
I don't remember if there is such a feature in other models.
Kvost wrote:
By the way, you can buy on Ibei, ideally for ridiculous money.
Quote:
there are a lot of good things you can buy, the question is how to deliver it, for a hundred bucks the delivery will pass, then who can be sure that you will not get a faulty one, and there have been no spare parts for them for a hundred years, well, there is still our mail, it is quite likely that is not perforated, but a brick is waiting for you in the package.
therefore it is better to buy here and not necessarily Hilty and work, work and work

Kvost wrote:
Not on mine.
something he looks suspiciously good

Pablont wrote:
Today, while chiseling,
vik wrote:
there are a lot of good things you can buy, the question is how to deliver it, for a hundred bucks the delivery will pass, then who can be sure that you will not get a faulty one, and there have been no spare parts for them for a hundred years, well, there is still our mail, it is quite likely that is not perforated, but a brick is waiting for you in the package.
As for the brick, there is a point criterion for evaluating the seller, reviews again. The question about the delivery price is complicated.
vik wrote:
something he looks suspiciously good
vik wrote:
not a toy?
Buzzing like real
Kvost wrote:
Strange and highly doubtful. This cartridge is as simple as a felt boot. Very reliable.
But I'm not in any way doubtful, but bitter and insulting! Placed an order for DeWalt D25113K
Pablont wrote:
I really want a really reliable perf.
Once DW is killed, fork out for the DUSS P-26C.
Pablont wrote:
What is it?
Kvost wrote:
Once DW is killed, fork out for the DUSS P-26C.
Pablont wrote:
What is it?
... well, now it will begin! The congregation held its breath in anticipation

... in case of. if ah dont undestand ">
Pablont wrote:
What is it?
DUSS? Producer of the best perfs in general. The P-26C is a lightweight tri-mode perforated vertical.
” >
FINN-UGR wrote:
... well, now it will begin! The congregation held its breath in anticipation
Of course! What marks the entrance went!
Well, well, well, they didn't say before that such a perf happens?
And who knows what the price is> Rotary hammer Р 26 С - three-mode station wagon
Drilling, hammering and chiselling.
Ideal for medium-duty slotting work and overhead work when installing door frames and window frames.
Indispensable for demanding precise slotting work,
when beating off plaster and tiles. Great helper
when installing ventilation and heating systems,
laying an electric cable.
Drills plug sockets and recesses for junction boxes with a diameter of up to 80 mm.
Pablont wrote:
And who knows what the price is
Those who saw her look like this.




Kvost wrote:
As for the brick, there is a point criterion for evaluating the seller, reviews again.
Yes, I'm talking about our mail, not the seller.
and the seller. Maybe before that he was selling only tights
Pablont wrote:
And who knows what the price is
on Juno in St. Petersburg two years ago I saw a duss for 27 thousand max.
Pablont wrote:
And who knows what the price is
The price is appropriate. For the P26C they ask for 1000 Euro.
Kvost wrote:
For the P26C they ask for 1000 Euro.
Someone uses such a machine.
Pablont wrote:
Someone uses such a machine.
you recently, apparently, on the forum

vik wrote:
Maybe he only traded in pantyhose before that.
vik wrote:
on Juno in St. Petersburg two years ago I saw a duss for 27 thousand max.
Stolen. The cheapest "max" РХ46 costs about 50t.r.
no, hung on the stand. talked to the seller. he said that they took it for a test, but they wouldn’t take it anymore - in six months, not a single person who wants to buy. There is no service, but how to serve?
vik wrote:
no, hung on the stand.
In a regular tool shop or in the market? I haven't seen it in stores, I've seen it a couple of times on the market. All are gray.
vik wrote:
There is no service, but how to serve it?
Their service is a separate conversation. Our local brushes won't even sell if the equipment is not bought from them. Strange approach.
Kvost wrote:
Their service is a separate conversation. Our local brushes won't even sell if the equipment is not bought from them. Strange approach.
what for is such a tool? well what for?
any brand's policy is accessibility. Of course. Hilty also sells the instrument only in his store, but maybe only in St. Petersburg? but you can repair any and not only the instrument purchased from them, only if it is not stolen.
well, yes, and this is not DUSS, but dust

Something like that
Three-mode rotary hammer SDS-plus PLH 30 E 30 mm Power consumption 750 W Max. drilling diameter in concrete / stone / wood / core bits 30/30/40/82 mm Impact energy 3.4 J Perforation frequency 0-4200 bpm Full load speed 0-740 rpm Weight 3.4 kg Electronic speed control or frequency Overload clutch AVS anti-vibration system Metal gearbox cover Rotation stop Softgrip - elastic grip
![]() |
Video (click to play). |
And here is not a very heavy perf, here I read about them, they are still different from AEG, can I take it?
