In detail: do-it-yourself Bosch punch repair scheme from a real master for the site my.housecope.com.
The most widespread among professional builders in Russia are Bosch hammer drills, and among amateurs, household models Bosch 2–20, 2–24, 2–26.
Rock drills not only work well but are also easy to repair. You can easily find any broken part on them.
In the designs of the described perforators, the same principle is incorporated, to transmit the rotational moment from the rotor to the shaft of the barrel of the percussion unit with the simultaneous transmission of the translational impulse to the working tool.
Structurally, the perforators are made according to the same scheme, but individual units or parts have their own characteristics.
If you know the specific differences between the models of the described Bosch rotary hammers, then disassembly and repair with your own hands will not be difficult.
Along with the originals, there are a large number of counterfeit tools on the Russian market, including Bosch hammer drills.
The design features of the models and how to disassemble and repair them with your own hands are described below.
The principle of operation of perforators is the same, but the design features are different.
The main parts used in the listed models of Bosch rotary hammers are interchangeable. This applies to the mechanical and electrical assembly.
But there are knots and made that differ in the details used.
To repair a Bosch rotary hammer 2–20, 2–24, 2–26, you need to know these differences. Knowledge of the design features of each rotary hammer facilitates the repair process, finding breakdowns and eliminating them.
The designs of Bosch rotary hammers are so simple that they allow you to perform simple repairs, practically with your own hands, and replace any part without contacting service services. You need to have the skills of an assembler, have basic knowledge of electrical engineering and understand the principle of the hammer drill.
![]() |
Video (click to play). |
When repairing a Bosch hammer drill, you will not do without an electrical and disassembly diagram for the tool of the model you are going to repair.
The wiring diagrams of Bosch rotary hammers 2–20, 2–24, 2–26 are practically the same. Although there are some minor differences.
But the mechanical blocks are equipped with parts that differ structurally from each other. The main differences are collected in two nodes: in the intermediate shaft and the shaft of the barrel of the impact block.
The greatest differences are presented in the design of the intermediate shaft, in the assembly of the "drunken bearing", in the mode switch. Non-fundamental features are present in the designs of the barrel of the percussion block, striker, striker.
Let's start with the Bosch 2–20 rotary hammer.
Repair of a Bosch 2–20 rotary hammer is not possible without knowledge of the design of the tool being repaired.
The principle of operation of the Bosch 2–20 hammer drill is based on the transmission of torque from the rotor shaft, pos. 3, to the shaft of the impact unit, pos. 22, through the intermediate shaft, pos. 824, while simultaneously transmitting a longitudinal impulse to the working tool.
The rotor pos. 3 transmits the torque to the helical gear of the intermediate shaft pos. 824.
The helical gear is fixed on the intermediate shaft and transmits the torque to the shaft. A drunk bearing is fixed on the shaft, which receives the torque through the clutch. Due to its design, the drunk bearing transmits the translational motion to the barrel cylinder of the percussion mechanism.
The intermediate shaft of the Bosch 2–20 perforator consists of a rolling bearing assembly (drunk bearing), a clutch, a large helical gear, and a small spur gear.
Most often, breakdowns are manifested in the wear of the clutch splines, which leads to the loss of rotation of the drill chuck in the presence of a shock pulse.
It is corrected by replacing the clutch or restoring the teeth of the clutch parts.
It is best to start repairing a Bosch 2-24 hammer drill with an acquaintance with the diagram and design features of the tool being adjusted. The operating principle of the Bosch 2–24 rotary hammer is similar to that of the Bosch 2–20 rotary hammer.
The torque is transmitted to the tool holder shaft, simultaneously with the transmission of the shock impulse. The hammer drill has three operating modes: drilling with impact, drilling without impact, impact.
The helical gear wheel of the rotor, poz.803 transmits the torque to the helical gear of the intermediate shaft, pos. 826.
The intermediate shaft of the Bosch 2-24 perforator consists of a rolling bearing unit pos. 830, a clutch pos. 823, and shift parts pos. 44. Most often, the clutch fails. Teeth wear out in it. Clutch repair consists in correcting the tooth profile of the engagement in the clutch and on the intermediate shaft.
The barrel shaft of the striking unit is designed to transmit a rotational impulse with the simultaneous movement of the striker.
Rotation is transmitted from the spur gear of the intermediate shaft to the large spur gear pos. 22 of the barrel shaft pos. 821.
The reciprocating motion is transmitted through a drunk bearing, pos. 830, an impact piston, pos. 26, a firing pin, pos. 27, an impact bolt, pos. 28, to a drill fixed in a chuck, pos. 756.
The design is a hollow shaft on one side. Parts are installed on the shaft from both sides.
From the side of the chuck mounting, a spur gear, pos. 22, is installed on the shaft and fixed on the shaft by means of a roller, pos. 88, pressed against the shoulder of the shaft by a spring, pos. 80. The spring itself is fixed with a retaining ring, pos. 85.
In the cavity of the shaft of the barrel of the impact block is inserted: the assembled impact bolt pos. 28 and the impact piston. In the impact piston, pos. 26, is inserted the firing pin, pos. 27, with a new rubber ring, pos. 73, placed on it. All rubber products are lubricated with the recommended lubricant.
Due to the weakening of the spring force, falling out of the fixing roller, the gear can turn on the shaft. This is manifested in the disappearance of the angular momentum with the presence of a shock impulse.
When rubber products (O-rings) wear out, the perforator stops working in the "Chiseling" mode. This happens gradually. The impact force weakens as the rubber rings wear. The thing is that the movement is transmitted from the drunk bearing to the impact piston, pos. 26, in which the firing pin, pos. 27, creates air pressure and acts on the impact bolt, pos. 28.
If you apply a lot of force during the operation of the hammer drill, this can lead to the destruction of the impact bolt, jamming of the striker in the impact piston. Such malfunctions are eliminated only by complete replacement of the failed part. Learn more about troubleshooting a Bosch rotary hammer.
Repair of the Bosch 2-26 rotary hammer should begin with familiarizing yourself with the design features of the tool being adjusted. The operating principle of the Bosch 2–24 rotary hammer is similar to that of the Bosch 2–26 rotary hammer.
Rotation is transmitted from the rotor shaft, through the intermediate shaft, to the shock barrel shaft. At the same time, a drunk bearing attached to the intermediate shaft transmits a reciprocating motion to the impact piston.
The hammer drill has three operating modes: drilling with impact, drilling without impact, impact.
The helical gear wheel of the rotor, pos. 803, transmits the torque to the helical gear of the intermediate shaft, pos. 823.
The intermediate shaft is similar to the shaft in the design of the Bosch 2-24 rock drill and is interchangeable between itself and the parts that make up the intermediate shaft of the Bosch 2–24, 2–26 rock drills.Instructions for disassembling the Bosch rotary hammer.
The barrel shaft of the percussion block is similar in design to the barrel shaft of the Bosch 2-24 rock drill. Failures are caused by faults in the same parts as in the Bosch 2-24 rotary hammer.
Features of the shaft of the Bosch 2-26 perforator is that the driven large spur gear, pos. 22, is fixed on the shaft by three pins, pos. 37, in contrast to the fixing roller in the Bosch 2-26 puncher.
When disassembling the barrel shaft of the percussion block of the Bosch 2-26 perforator, pay attention to the method of fixing the gear. Before removing the gear, you must remove the three pins. The order of the correct assembly of the Bosch rotary hammer.
- Knowing the differences between the given models of Bosch rotary hammers will allow you to quickly disassemble the tool, replace defective parts. To do this, you do not need to contact the service department.
- Structurally, Bosch rotary hammers are so simple that they allow you to carry out repairs of almost any complexity.
- All that is required of you is desire and basic knowledge in mechanics.
It happens that fake models of Bosch rotary hammer come across in more detail about this.
The principle of operation of the Bosch 2-26 hammer drill is no different from the famous brands of hammer drills.
The rotating rotor transmits torque to the intermediate shaft of the mechanical unit of the rock drill, while transmitting the translational motion through the rolling bearing to the hammer mechanism of the rock drill and the impact impulse. A rotational moment with a translational shock impulse is transmitted to the working tool. This principle is implemented in all rotary hammers.
But different firms that produce rock drills have their own design features.
Bosch rotary hammers are considered the best in the power tool segment. But nothing is eternal.
If your Bosch 2-20, 2-24, 2-26 rotary hammer stops working, then you can restore it yourself. You need to have basic locksmith skills and a little knowledge of electrical engineering.
And another important detail, the design of Bosch rotary hammers is so simple that it does not cause difficulties during repair.
When repairing power tools, including repairing Bosch rotary hammers, strictly follow the safety precautions when working with electrical appliances.
To facilitate the repair of the Bosch rotary hammer, its disassembly and assembly, study the tool assembly diagram:
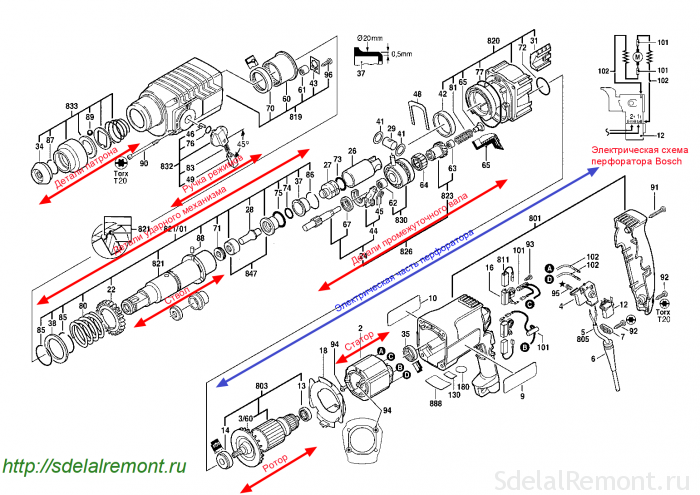
Any disassembly of the bosch 2-26 perforator begins after inspection, test switching and identifying the causes of the device malfunction.
Video disassembly of the Bosch rotary hammer 2-26
Since the order of disassembly of drills Bosch 2-20; 2-24; 2-26 is almost the same, consider the sequence of disassembly using the example of the Bosch 2-26 rotary hammer.
Dismantling the Bosch GBH 2-26 dre rotary hammer begins with the disassembly of the quick-release chuck.
Two types of chuck are most commonly used in Bosch rock drills: SDS-plus chucks and SDS-max chucks. The difference between them is in the principle of clamping the tail of the working organ.
The device of the Bosch hammer drill chuck differs in the design of the tool landing rods, depending on the SDS-plus or SDS-max model. In addition to the listed types of cartridges, there are SDS-top, SDS-quick cartridges.
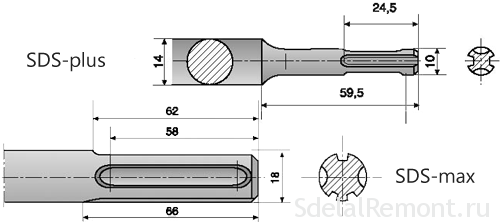
The procedure for disassembling the cartridge of the Bosch 2-26 perforator is simple:
- remove the rubber tip, pos. 34;
- take out the retaining ring, pos. 87;
- remove the steel washer pos. 833;
- remove the conical spring, pos. 833;
- carefully, so as not to lose it, using a magnet, remove the barrel balls pos. 89.
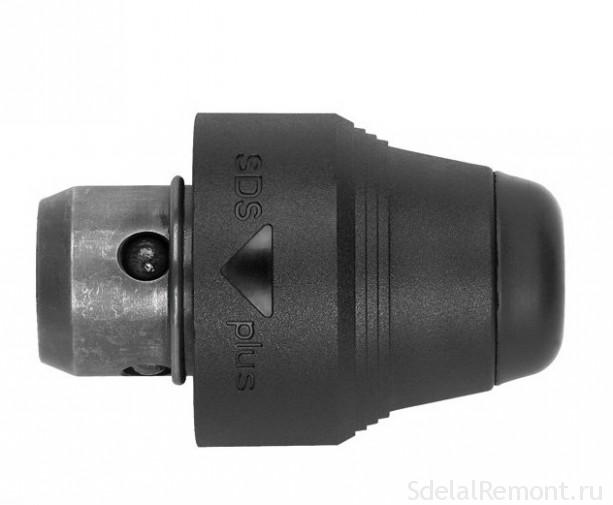
Inspect all parts of the cartridge carefully.
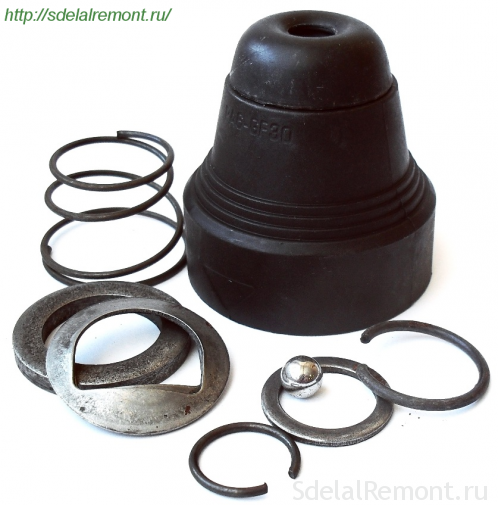
SDS-plus chucks have been specially developed for drilling tools. The diameter of the tool shanks is 10 mm, the length of the working tool is in the range of 110 ... 1000 mm. The diameter of the drills is in the range of 4 ... 26 mm.
Putting the puncher on its side, remove the mode switch pos. 832.
First, turn the switch to the “Drilling” position, press the screwdriver all the way into the end face of the switch button (it is red) and turn the switch counterclockwise through an angle of 70º.
While wiggling the switch handle, pull the switch handle out of the housing.
Putting the Bosch 2-26 rotary hammer vertically on the handle, unscrew the four screws, pos. 90, holding the housing cover of the mechanical assembly.
Press down on the end of the percussion shaft and remove the cover. Black plastic cover.
Now you need to remove the barrel poz.821 and the intermediate shaft poz.826. They are not fixed by anything.
Then, using a screwdriver, you need to remove the bracket pos. 48 of the rolling bearing pos. 830. By the way, in a simple way it is called "drunken bearing". Sequentially removed: sleeve poz.26 and "drunken bearing".
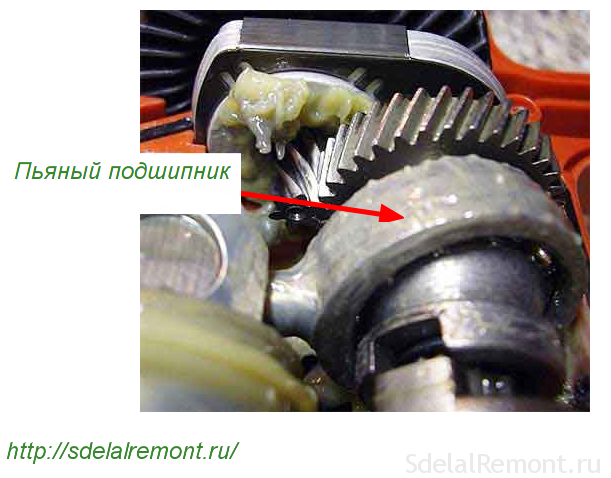
- disassembly of the Bosch perforator barrel assembly begins from the side of the cavity, taking out the cylinder poz.26 with the drummer poz.27;
- the firing pin assembly must be removed from the cavity;
- from the side of the chuck shaft, remove the retaining ring, pos. 85, the steel ring, pos. 38, and one more retaining ring, pos. 85;
- remove the spur gear, pos. 22.
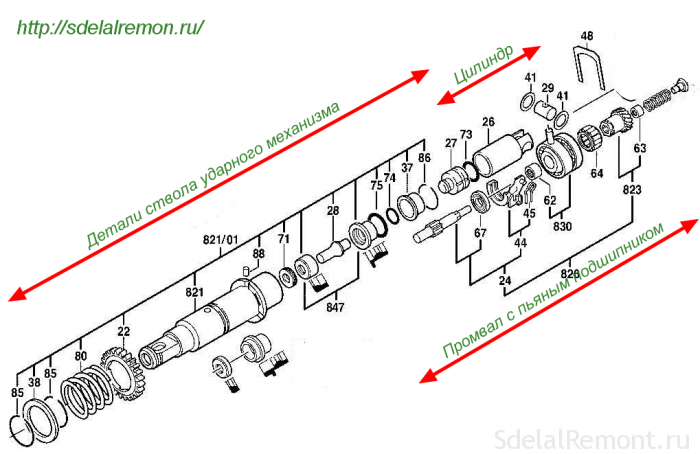
A striker, pos. 27, is inserted inside the cylinder, from which it is necessary to remove the rubber ring, pos. 73. For any disassembly, rubber parts must be replaced without fail.
At the opposite end of the cylinder, a hinge, pos. 29, and two flat washers, pos. 41, are inserted.
The intermediate shaft is disassembled by removing the shaft, pos. 24, and by pulling the "drunk bearing" out of the housing, pos. 77.
Bearings are removed with pullers or manually using a tool.
Bosch rotary hammers are very reliable. But there are malfunctions that practically do not occur in practice. Below is one of them.
If the hammer drill has stopped hammering, but still allows drilling, the most likely cause may be the destruction of the "drunken bearing". This malfunction is not common and it is not easy to find it.
You don't have to go to a repair shop to fix it. Any person who is more or less versed in mechanics will eliminate such a malfunction.
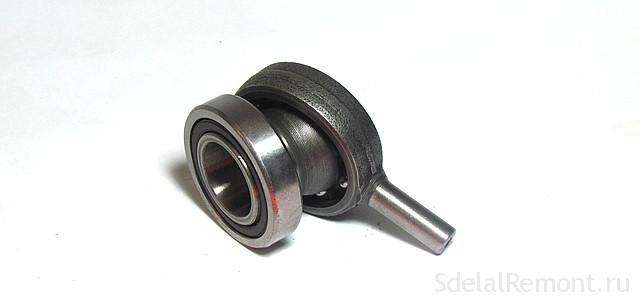
First you need to disassemble the Bosch hammer drill to the intermediate shaft. Disassembly procedure is shown above.
Removing the intermediate shaft, you get to the "drunk bearing". Broken cage, scattered balls, cage pieces indicate the destruction of the rolling bearing.
Take out the bearing, remove the dirt, all parts of the destroyed mechanism.
You buy a new "drunk bearing", and after lubricating all the parts with new grease, replace and reassemble in the reverse order of the disassembly steps.
Dismantling the Bosch 2-26 rotary hammer, its electrical part, begins by removing the back cover on the handle of the puncher by unscrewing three screws.
The next step is to remove the reverse switch.
Turn it to neutral and lift it towards you. The reverse switch is removed.
To remove the stator cover, it is necessary to hold the mechanical unit in your right hand, and to the left stator housing, pull them in different directions, shaking them.
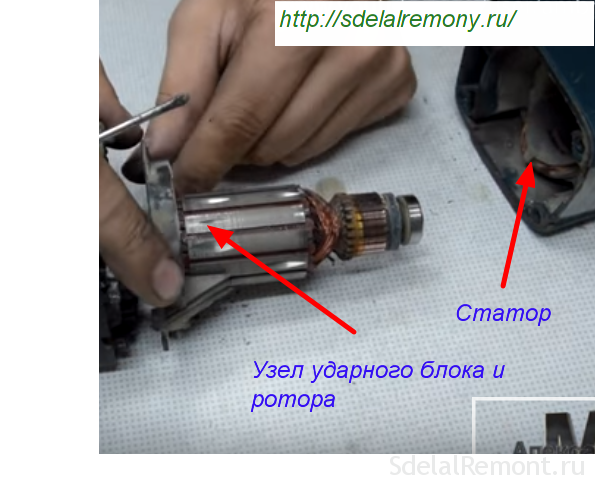
To separate the rotor from the mechanical unit, it is enough to drag these parts in different directions. The rotor is secured to the mechanical assembly by a small helical gear that is inserted into contact with the large helical gear of the mechanical assembly.
The rotor has been released and you can carefully inspect the condition of the collector and bearings.
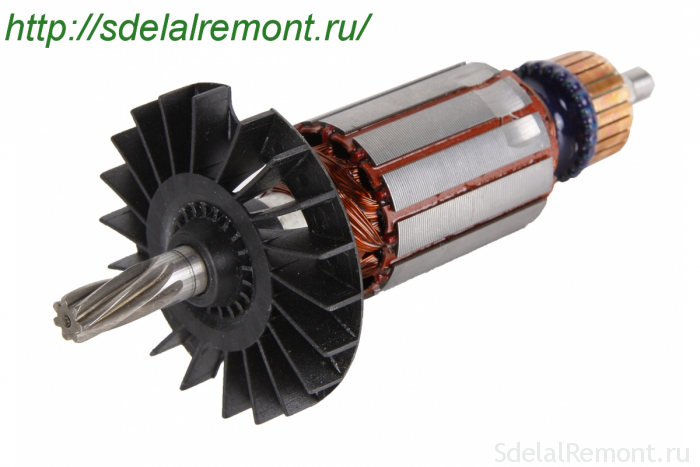
To remove the stator, it is enough to remove the protective plastic protective casing, and knock with a wooden blank or mallet on the end of the housing, into which the stator is inserted. Before doing this, do not forget to unscrew the two screws holding the stator in the housing.
The stator is removed, the rotor is taken out, you can proceed to their inspection and defect detection of all parts that make up the electrical part of the Bosch rotary hammer.
When inspecting the disassembled Bosch 2-26 hammer drill, pay special attention to the condition of the carbon brushes, the bloom on the brush holders and the reliability of their attachment, the integrity of the reverse switch contacts, and the state of the wire at the point of entry into the hammer drill.
The length of the brushes should not be shorter than 8 mm. There should be no traces of sparking and carbon dust from the brushes on the brush holders; there should be no burnouts or damage to the contacts on the contacts of the reverse switch of the Bosch 2-26 perforator.
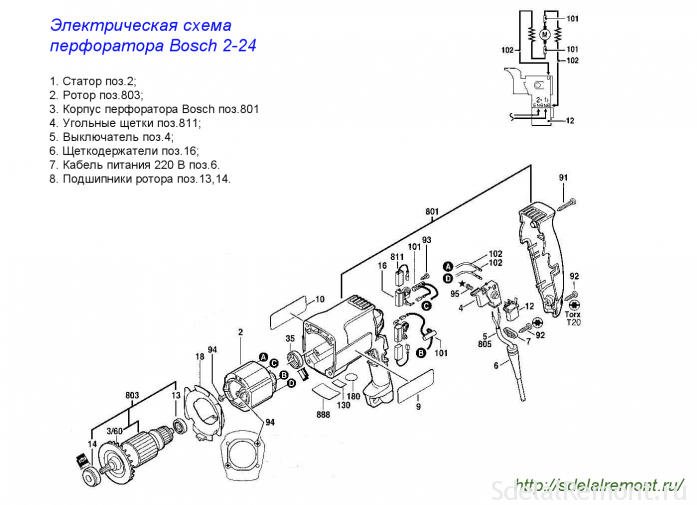
An electric rock drill is perhaps the most popular device that I use at construction sites, repairs, etc.
This tool is operated in rather harsh conditions - vibration, increased dustiness, power surges and others. All this, sooner or later, leads to the fact that the tool will fail and require repair.
An electric rock drill is a complex engineering product that consists of assemblies that ensure the movement of a chuck with a drill installed in it. Basically, a hammer drill is a device that converts electrical energy into mechanical energy.
Depending on the operating conditions, this device may have mechanical and electrical problems.
The hammer drill scheme is pretty close to that of an electric drill. One of the differences is that instead of an ordinary gear pair transmitting torque to the tool, a full-fledged gearbox is mounted in the hammer drill. It is designed to convert the torque generated by the electric motor into the reciprocating movement of the chuck.
Malfunctions requiring repair can occur in almost any part of the device. But before starting the repair, it is required to diagnose the breakdown and identify the reasons that led to its appearance.
It should be noted that detecting a breakdown is not difficult, but sometimes you have to disassemble the punch body for this.
Like any technical device, an electric rock drill has some weak points in its design. It is they who are the cause of breakdowns that require repair. It is not uncommon for a perforator to fail due to the fault of a worker who operates it at extreme modes and in violation of operating rules.
It must be understood that the main faults occur in the electrical or mechanical part. In the mechanical part, the following problems most often occur:
- the device does not perform its main functions - drilling and drilling;
- jamming of the drill in the chuck;
- the nozzle is not installed in the chuck;
- extraneous noise during the operation of the device.
In an electrician, the following defects are most often manifested:
- the engine does not work;
- excessive sparking of brushes;
- the appearance of burning or the smell of burnt insulation.
The beginning of the repair begins with cleaning the body of the device. This is necessary at least to prevent dirt from getting into the disassembled perforator.
When repairing an electric rock drill, there is often a need to disassemble it. But before you start it, you need to make sure once again that the problems have arisen precisely in the mechanical part of the device. We will analyze in detail what problems are encountered and how they can be eliminated
Untimely maintenance, poorly performed repairs, operation of the hammer drill in extreme modes can lead to the fact that any part that is part of this mechanism can fail. To identify defects in the gearbox, it is necessary to disassemble it, rinse the parts and then carry out a thorough inspection.
Revealed damaged parts must be replaced with new ones. Then assemble the gearbox, of course, you need to put grease into it. By the way, the brand of lubricant must be indicated in the operating manual.
If the nozzle does not enter the working position, then most likely the reason lies in the cartridge. To eliminate this defect, there is no need to disassemble the tool.As a rule, interference with the installation of the nozzle consists in the fact that any debris has got into the chuck.
To identify malfunctions in the mode switching device, the punch will still have to be disassembled. In principle, a defect can be identified by a careful examination of the switching mechanism.
Mode switch repair
In principle, the main components are listed, in which breakdowns most often occur and require repair. Meanwhile, there are several more types of defects that can arise for various reasons. For example, there is no impact hammer mode. That is, the drill rotates together with the chuck, but does not have an impact on the working surface. The most common cause, in this case, is a floating bearing. Damage to the steel striker may be another cause of this malfunction. In both cases, replacement of the defective part is required.
It is not uncommon for the engine to run when the tool is turned on, but the chuck does not rotate. This happens most often because the gearbox is stuck. By the way, it is unacceptable to keep the hammer turned on for a long time; it is unacceptable when the chuck is inoperative, the motor winding may burn out. The hammer drill will have to be disassembled and defects in the gearbox removed. They can be caused either by damage to the gears or by debris falling into it.
Another defect is that the chuck cannot fix the drill. This problem can arise with a tool that has been in use for a long time. The cause of this problem lies in the wear of the retainer housing mount.
Malfunctions associated with the electrical part of the hammer drill can also cause serious problems. By the way, a failure in work can be caused by a trivial lack of voltage in the outlet.
By the way, troubleshooting should start with less. That is, it is necessary to check the presence of power in the electrical network, the integrity of the wire and outlet.
By and large, if the instrument does not show any signs of life, it is likely that the electrical part of the instrument is out of order. The main electrical defects include the following:
Any electrical device can be connected for testing. If there is voltage in the network, then it is necessary to check the integrity of the cable.
To identify this defect, they inspect it, then, using a tester, ring it. To eliminate a cable break, you can either solder it or twist it. But it's best to replace it.
The cause of this defect may be elementary oxidation of the contacts in the button. To test this assumption, it is necessary to dismantle the rear casing cover. If there are no visible signs of oxidation, it is advisable to use a tester. To correct this malfunction, you can clean the contacts, but it is better to replace the power button.
With prolonged and intensive use of the perforator, the brushes wear out, through which electric current flows to the motor. With a lot of wear, they begin to spark and a burning smell appears. The brush must be at least 8 mm long.
Upon reaching this and smaller size, they are replaced. The replacement procedure is quite simple and anyone who is not even familiar with the basics of electrical engineering can handle it.
If this problem is identified, it is advisable to replace the entire assembly. But, in fairness, it should be noted that this defect is not common.
This is probably the worst defect that can occur with an electric tool. The user should understand that it is better not to repair the engine on his own. For this, there are specialized workshops equipped with all the necessary repair and diagnostic equipment.
When the engine is running, a certain layer of carbon deposits forms on the manifold. You can remove it yourself and then try to enable it. If this operation does not help, then it is necessary to ring the armature and stator. There are certain requirements for the resistance in the windings.
Repair of these units is permissible only in an electrical workshop. It is permissible to do this work at home, but only if you have special equipment and certain knowledge about the operation of the electric motor. This operation, performed at home, will significantly reduce the cost of repairing the hammer drill as a whole.
Important! Repair of the device is carried out with the tool disconnected from the electrical network.
To repair and restore the tool's functionality, you will need some keys, both ordinary open-end and hexagons, screwdrivers with different slots. A puller will be required to remove the bearings.
Disassembly and assembly of the perforator must be carried out using the kinematic and electrical circuits of the perforator.
To diagnose a faulty hammer drill, most often there is no need to use special equipment and tools, with the exception of a tester and a device for rewinding the motor.
You can establish the cause of the breakdown using an ordinary inspection.
And in order to identify problems in the mechanism of the tool, it is desirable to know and understand its structure and principle of operation.
To ensure long-term and efficient operation of an electric rock drill, it is enough to follow a few simple rules. In particular:
- When working, it is impractical to put strong pressure on the tool, at least there is no need for this, and moreover, with excessive pressure, the tool breaks down faster.
- The operation of the electric hammer drill in idle mode is inadmissible.
- When working with porous materials, it makes sense to turn off the impact mechanism. When working with particularly hard materials, it is advisable to use a lubricant.
- When working, especially for a long time, it is necessary to monitor the heating of the housing, especially in the place where the gearbox is installed. If there is noticeable heating, it is necessary to stop the work and wait until it cools down. Cooling water must not be used, its use may damage the gearbox parts.
- Work with the tool should be carried out in the following mode - at least 10 minutes break after half an hour of work.
Do-it-yourself punch repair can be done only partially. But, for example, such a unit as an electric motor is still better done in a special workshop.
It is best to make repairs in the warranty workshop of the company from which it was purchased.
To lubricate the hammer drill units, use only those materials recommended by the manufacturer.
The drum rock drill differs from the traditional one in that the electric motor is located vertically and it cannot work in the drilling mode.
Drum perforator SDS-plus Intertool DT-0182
Therefore, due to the design features, in order to get to certain nodes, additional operations will have to be performed, in particular, to inspect the electric motor, it is necessary to remove the lower part of the casing or the cover. And to replace the brushes, special technological holes are provided in the body.
To replace this button, you will have to disassemble the case, disconnect it and install a new one in its regular place.
To replace the brushes, it is necessary to provide access to the brush assembly. To replace, it is necessary to release the brushes from the lock, install new ones in their place.
If extraneous sounds are heard during the operation of the perforator, then there is a high probability that the bearing has reached a certain degree of wear. That is, it needs to be replaced.
For this, it is necessary to complete or partially disassemble the case and gain access to the unit in which it is installed. It may require a puller to remove it. By the way, some bearings can be secured with circlips.
To replace a cartridge that has exhausted its resource, first of all, it is necessary to take into account which company produced this product. The thing is that the schemes for fixing the cartridges from different manufacturers have their own characteristics.
Replacing the chuck on the hammer drill
For example, to dismantle a chuck in a Bosch hammer drill, you need to do the following manipulations - loosen the retaining ring, pull out the chuck and install a new one in its place.
In some models of this tool, the impact is provided by a drunken bearing. With intensive use, it can undergo destruction.
To repair it, you need a flat-head screwdriver. After disassembling the housing, the bearing must be removed from the housing, disassembled, replaced with worn parts and installed in place.
To repair the percussion mechanism of the punch, it is necessary to remove the raster sleeve; for this, it is necessary to release the spring and the retaining ring. After that, the impact bolt is replaced with a new one, or sent for restoration.
The sleeve fails quite rarely. To replace it, the old one must be removed from the aluminum housing and a new one must be installed instead.
If you find an error, please select a piece of text and press Ctrl + Enter.
The most widespread among professional builders in Russia are Bosch perforators, and among amateurs, household models Bosch 2-20, 2-24, 2-26. Rock drills not only work well but are also easy to repair. You can easily find any broken part on them.
In the designs of the described perforators, the same principle is incorporated, to transmit the rotational moment from the rotor to the shaft of the barrel of the percussion unit with the simultaneous transmission of the translational impulse to the working tool.
Structurally, the perforators are made according to the same scheme, but individual units or parts have their own characteristics.
If you know the specific differences between the models of the described Bosch rotary hammers, then disassembly and repair with your own hands will not be difficult.
Along with the originals, there are a large number of counterfeit tools on the Russian market, including Bosch hammer drills.
The design features of the models and how to disassemble and repair them with your own hands are described below.
The principle of operation of perforators is the same, but the design features are different.
The main parts used in the listed models of Bosch rotary hammers are interchangeable. This applies to the mechanical and electrical assembly.
But there are knots and made that differ in the details used.
To repair a Bosch 2-20, 2-24, 2-26 rotary hammer, you need to know these differences. Knowledge of the design features of each rotary hammer facilitates the repair process, finding breakdowns and eliminating them.
The designs of Bosch rotary hammers are so simple that they allow you to perform simple repairs, practically with your own hands, and replace any part without contacting service services. You need to have the skills of an assembler, have basic knowledge of electrical engineering and understand the principle of the hammer drill.
When repairing a Bosch hammer drill, you will not do without an electrical and disassembly diagram for the tool of the model you are going to repair.
The wiring diagrams of Bosch rotary hammers 2-20, 2-24, 2-26 are almost the same. Although there are some minor differences.
But the mechanical blocks are equipped with parts that differ structurally from each other. The main differences are collected in two nodes: in the intermediate shaft and the shaft of the barrel of the impact block.
The greatest differences are presented in the design of the intermediate shaft, in the assembly of the "drunken bearing", in the mode switch. Non-fundamental features are present in the designs of the barrel of the percussion block, striker, striker.
Let's start with the Bosch 2-20 rotary hammer.
Repair of the Bosch 2-20 perforator is not possible without knowledge of the design of the tool being repaired.
The principle of operation of the Bosch 2-20 perforator is based on the transfer of torque from the rotor shaft, pos. 3, to the shaft of the impact unit, pos. 22, through the intermediate shaft, pos. 824, while simultaneously transmitting a longitudinal impulse to the working tool.
The rotor pos. 3 transmits the torque to the helical gear of the intermediate shaft pos. 824.
The helical gear is fixed on the intermediate shaft and transmits the torque to the shaft.A drunk bearing is fixed on the shaft, which receives the torque through the clutch. Due to its design, the drunk bearing transmits the translational motion to the barrel cylinder of the percussion mechanism.
The intermediate shaft of the Bosch 2-20 perforator consists of a rolling bearing assembly (drunk bearing), a clutch, a large helical gear, and a small spur gear.
Most often, breakdowns are manifested in the wear of the clutch splines, which leads to the loss of rotation of the drill chuck in the presence of a shock pulse.
It is corrected by replacing the clutch or restoring the teeth of the clutch parts.
It is best to start repairing a Bosch 2-24 perforator with an acquaintance with the diagram and design features of the tool being adjusted. The principle of operation of the Bosch 2-24 rotary hammer is similar to that of the Bosch 2-20 rotary hammer.
The torque is transmitted to the tool holder shaft, simultaneously with the transmission of the shock impulse. The hammer drill has three operating modes: drilling with impact, drilling without impact, impact.
The helical gear wheel of the rotor, poz.803 transmits the torque to the helical gear of the intermediate shaft, pos. 826.
The intermediate shaft of the Bosch 2-24 perforator consists of a rolling bearing assembly pos. 830, a clutch pos.823, shift parts pos. 44 Most often, the clutch fails. Teeth wear out in it. Clutch repair consists in correcting the tooth profile of the engagement in the clutch and on the intermediate shaft.
The barrel shaft of the striking unit is designed to transmit a rotational impulse with the simultaneous movement of the striker.
Rotation is transmitted from the spur gear of the intermediate shaft to the large spur gear pos. 22 of the barrel shaft pos. 821.
The reciprocating motion is transmitted through a drunk bearing, pos. 830, an impact piston, pos. 26, a firing pin, pos. 27, an impact bolt, pos. 28, to a drill fixed in a chuck, pos. 756.
The design is a hollow shaft on one side. Parts are installed on the shaft from both sides.
From the side of the chuck mounting, a spur gear, pos. 22, is installed on the shaft and fixed on the shaft by means of a roller, pos. 88, pressed against the shoulder of the shaft by a spring, pos. 80. The spring itself is fixed with a retaining ring, pos. 85.
In the cavity of the shaft of the barrel of the impact block is inserted: the assembled impact bolt pos. 28 and the impact piston. In the impact piston, pos. 26, is inserted the firing pin, pos. 27, with a new rubber ring, pos. 73, placed on it. All rubber products are lubricated with the recommended lubricant.
Due to the weakening of the spring force, falling out of the fixing roller, the gear can turn on the shaft. This is manifested in the disappearance of the angular momentum with the presence of a shock impulse.
When rubber products (O-rings) wear out, the perforator stops working in the "Chiseling" mode. This happens gradually. The impact force weakens as the rubber rings wear. The thing is that the movement is transmitted from the drunk bearing to the impact piston, pos. 26, in which the firing pin, pos. 27, creates air pressure and acts on the impact bolt, pos. 28.
If you apply a lot of force during the operation of the hammer drill, this can lead to the destruction of the impact bolt, jamming of the striker in the impact piston. Such malfunctions are eliminated only by complete replacement of the failed part. Learn more about troubleshooting a Bosch punch.
Repair of the Bosch 2-26 rotary hammer should begin with an acquaintance with the features in the design of the tool being adjusted. The principle of operation of the Bosch 2-24 rotary hammer is similar to that of the Bosch 2-26 rotary hammer.
Rotation is transmitted from the rotor shaft, through the intermediate shaft, to the shock barrel shaft. At the same time, a drunk bearing attached to the intermediate shaft transmits a reciprocating motion to the impact piston.
The hammer drill has three operating modes: drilling with impact, drilling without impact, impact.
The helical gear wheel of the rotor, pos. 803, transmits the torque to the helical gear of the intermediate shaft, pos. 823.
The intermediate shaft is similar to the shaft in the design of the Bosch 2-24 rotary hammer and is interchangeable between itself and the parts that make up the intermediate shaft of the Bosch 2-24, 2-26 rotary hammers. Instructions for disassembling the Bosch rotary hammer.
The barrel shaft of the percussion block is similar in design to the barrel shaft of the Bosch 2-24 rock drill. Failures are caused by malfunctions of the same parts as in the Bosch 2-24 rotary hammer.
Features of the shaft of the Bosch 2-26 perforator is that the driven large spur gear, pos. 22, is fixed on the shaft with three pins, pos. 37, in contrast to the fixing roller in the Bosch 2-26 puncher.
When disassembling the barrel shaft of the impact unit of the Bosch 2-26 perforator, pay attention to the method of fixing the gear. Before removing the gear, you must remove the three pins. The order of the correct assembly of the Bosch rotary hammer.
• Knowing the differences between the given models of Bosch rotary hammers will allow you to quickly disassemble the tool, replace defective parts. To do this, you do not need to contact the service department.
• Structurally, Bosch rotary hammers are so simple that they allow you to carry out repairs of almost any complexity.
• You are only required to have desire and basic knowledge in mechanics.
It happens that fake models of Bosch perforator come across in more detail about this.
Video: How to fix a hammer drill / 2-24 / How to change an impact bolt / Drunken bearing / Service / Repair
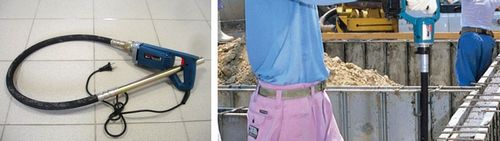
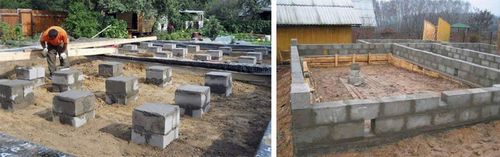
![]() |
Video (click to play). |
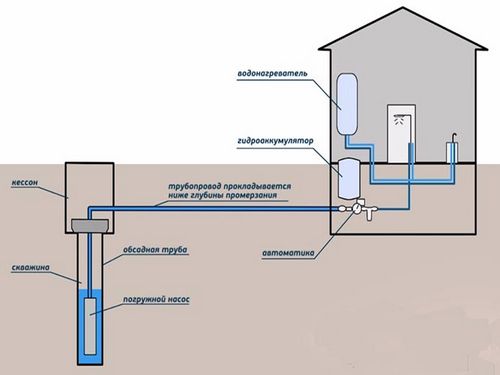