In detail: do-it-yourself repair of the Makita 2470 perforator from a real master for the site my.housecope.com.
Makita power tools have long established themselves as professional, reliable and easy to maintain. In addition, it has good maintainability and a relatively low price.
Of all the lines of punchers, I want to dwell on the model Makita HR 2450... The tool is very easy to use, has three modes of operation and can withstand very long loads. For the author of these lines, the perforator has worked faithfully for more than six years without breakdowns. Moreover, it was used in the mode of intensive loads. But at one fine moment ...
As you know, nothing is eternal. And reliable technology breaks down. Somehow, in the midst of work, he stopped hammering. In rotation mode, the machine worked, but the blow suddenly disappeared.
The gearbox was disassembled and the cause of the breakdown was identified. A bushing was broken in the barrel body, in which the striker (striker) directly carries out impact work. As a result, the drummer got stuck in the fragments of the collapsed bushing.
The service center advised to replace the barrel completely. It turned out that the bushing is pressed into the barrel at the factory and is not supplied separately. I had to buy an entirely new barrel.
In this article, we will tell you how to bring the hammer drill into working order yourself after this, in general, simple breakdown. If you have the skills to repair power tools and a desire not to pay someone your hard-earned money, then we take the tool and start disassembling the machine.
You will need two regular flat-head screwdrivers and one cross-head. One of the flat screwdrivers should be thin and narrow, no more than 4 mm wide. You will also need a wire hook to remove the retaining ring. It can be made from a bicycle spoke, the main thing is that the wire is rigid and does not easily unbend. You will also need a rubber mallet or wooden mallet.
![]() |
Video (click to play). |
Disassembly of the punch should be started by removing the protective rubber cap - boot. It can be easily removed, just take it with your fingers and pull it off the barrel.
Then, pushing on the plastic cover and squeezing the spring of the SDS + mechanism lock, remove the retaining ring with a screwdriver.
Remove the stopper using a screwdriver
The cover is removed from the barrel, and behind it, again squeezing the spring, we take out the retaining ball together with the spring and the figured washer.
Then the mode switch is disassembled. There is a special slot for a screwdriver under the cover holding the red release button. By inserting a screwdriver into this groove and prying the cover slightly, first from one edge, and then from the second, carefully remove it. You should not make significant efforts here, the lid is still plastic and may break. The red button together with the spring is removed from the switch body, and it is moved to the left until it stops, a little further than the drilling mode. It is from this position that it is removed from the gearbox. For this operation, the switch must be lightly picked up with thin screwdrivers on both sides and removed together with the rubber O-ring.
Remove the punch mode switch
Now the gearbox is removed. Using a Phillips screwdriver, unscrew the four bolts connecting the box to the stator housing. Then, holding it with your hand, you need to lightly hit the end of the barrel with a mallet in order for the box to come off the gearbox.
Remove the gearbox
After removing the box, we take out the barrel from the gearbox. It comes off easily.
We take out the barrel from the gearbox
Remove the old grease with a rag, and rinse the barrel with gasoline or kerosene and wipe it dry.
So, as mentioned above, it was required to completely change the entire barrel.However, this item, bought in a service center, turned out to be "naked as a falcon." That is, there was absolutely nothing on it and it was necessary to rearrange all the details from the old barrel to a new "blank".
The most difficult operation was the extraction of the striker from the barrel body. There are special holes in the barrel body through which the retaining ring is visible. This ring holds the firing pin with rings and rubber dampers in the body seat. Insert a thin screwdriver into the hole and slightly bend the ring. We do this first on one side, and then on the other. The stopper should come out of the groove.
Use two screwdrivers to squeeze the stopper
Then, from the inside, with a homemade wire hook, we pull out the stopper into the light of day.
With a wire hook, remove the stopper from the inside
Next, we remove the firing pin with washers and rubber rings. It is necessary for the assembly to remember or sketch the location of all rings and washers. If something goes wrong, the photos and drawings from the article will help.
Now you need to remove the gear from the shaft. Pressing on the washer and squeezing the spring, use a thin screwdriver to remove the retaining ring from the groove. After removing it, remove the washer, spring and gear from the barrel.
The toothed wheel is pushed onto the new barrel and meshed with the splines. Next, a spring with a washer and a stopper are installed on it. It is necessary to insert the retaining ring and fix the mechanism in the working position.
To do this, take the barrel in both hands and, resting it in your palms, with your fingers squeeze the spring with force, while simultaneously moving the washer and stopper down. It is necessary to squeeze until the stopper enters the groove.
Then a firing pin with washers and rubber rings is installed inside the barrel in the order in which it was sorted out. But first you need to pay attention to the condition of the drummer, his appearance.
If the firing pin has dents and pits after a long period of work or because it was scratched on a broken bushing, then it should be sanded down a little. To do this, it is clamped into a drill chuck and processed with fine-grained emery cloth. But if the irregularities are too large, then the drummer will be easier to replace.
It is necessary to lubricate the firing pin with special grease before installation and then use the grease during operation. When inserting the drill into the hammer drill, you need to apply a little grease to its shank. This extends the service life of the machine.
Having installed the striker mechanism in the barrel, we fix it with a retaining ring. Using a screwdriver, we try to move the striker on both sides inside the barrel. It should walk easily in the canal and not jam.
The assembled barrel is installed in the gearbox housing. Putting it on a cylinder with a piston, we put it into mesh with the drive gear and insert it into the body. All parts should be well lubricated during assembly.
Installing the barrel into the gearbox
Then we install the gearbox, after having lubricated the needle bearing. With four bolts, we pull the box to the stator housing and install the operating mode switch in place. To do this, set it to a position slightly to the left of the drilling mode.
Insert the red spring button and move the switch to the drilling mode. We snap on the plastic cover and check the operation of the switch.
Reinstall the mode switch
Snap the cover of the punch mode switch
Then, in a final chord, the SDS + mechanism is assembled. Having installed the spring of the mechanism, we put on a curly washer and insert the ball. Then, with a plastic cover, we squeeze the spring of the mechanism and insert the retaining ring. Putting on a rubber boot is no longer difficult.
Squeezing the spring with a washer, install the retainer ball
Installing the SDS mechanism
Trying the hammer drill under load. When the machine is operating, there should be no extraneous noise in the gearbox, the mode switch should be easily moved without jamming. In general, everything should work as before the breakdown.
The author of this article hopes that it will help dear readers to understand the repair of a hammer drill. Any breakdown can be simple if you find its cause.And then it all depends on your skill and diligence.
The author is fine, he described everything in detail, the only thing I forgot to write is that when you put the mode switch, you need to turn it counterclockwise so that it snaps into place.
In general, thanks, I repaired my perf in half an hour, it turns out that the firing pin just jammed. As a result, I cleaned it, greased everything, everything works.
The article is kind, but I can't understand how the striker repair kit gum is located.
I have not seen a better description, thanks to the author.
instead of replacing the barrel, he replaced the bushing (broken), but on BOSH 1610290029 they call it a scraper. Assembled checked (drilled two holes for fasteners F8 works), let's see how it goes next. Cost 120R. and lubricants.
Please tell me how to remove the drill from the cartridge if it turns out to be defective and so as not to harm the cartridge
How long did you work with a drill jammed in a chuck? It can be assumed that the shank was riveted due to poor quality drill material. There is also a possibility of cranking in the chuck. You can try to pull out the stuck drill by holding it in a vice and, shaking it, pull the drill towards you. You can use any lubricating fluids. But in the case of a very strong deformation, this method is unlikely to help. Then it is better, if possible, to contact a workshop. An attempt to disassemble the hammer drill and knock out the drill yourself without appropriate experience can lead to the failure of the hammer drill itself.
Even very reliable Makita rotary hammers break down over time.
Any breakage is eliminated, you just need to have straight arms and perseverance.
In addition to electrical malfunctions, rotary hammers are also susceptible to mechanical damage.
Operation of rock drills with hard materials in dusty environments will shorten the service life and require user intervention to perform preventive maintenance.
Any tool repair begins with determining the nature of the malfunction and disassembling.
The Makita 2450 and 2470 hammer drill can be repaired by a user who has basic locksmith skills and is familiar with electrical safety requirements.
This article discusses the mechanical part of the Makita rotary hammer, the main malfunctions and how to fix them.
Dismantling the mechanical part of the Makita 2470 rotary hammer
To get to the mechanical part of the hammer drill, you need to remove or disassemble the cartridge.
Dismantling the quick-release chuck
Place the punch on the rear case cover on a tabletop covered with a clean cloth or paper. Using tweezers or a screwdriver, remove the rubber tip 35, item 1.
Carefully loosen the annular spring, pos. 2, the coupling cover, pos. 3, and the steel ring, pos. 4. You will reach a steel ball with a diameter of 7 mm pos. 20.
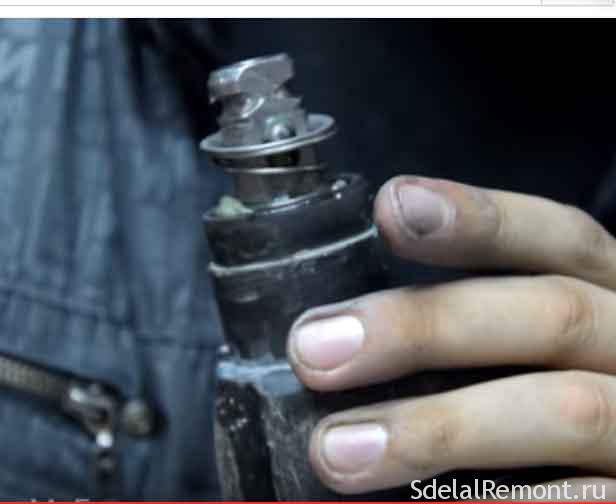
Now you can remove the housing of the mechanical part
It is black.
Using a screwdriver, unscrew the four screws at the end of the case.
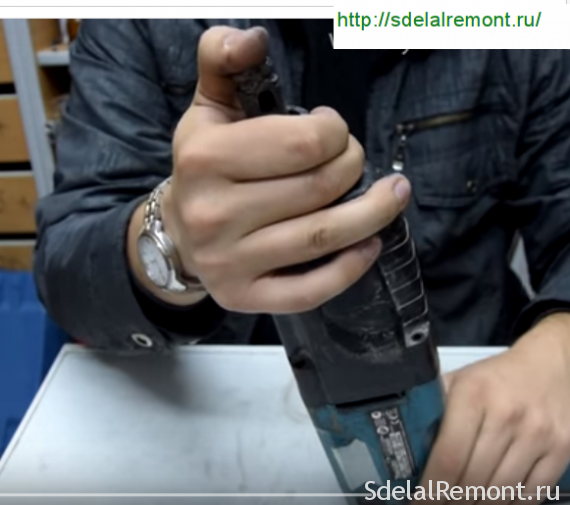
Holding the black case with your right hand, press your thumb on the end of the shaft from which the cartridge was disassembled. The plastic housing can be easily removed.
Next, you need to remove the gearbox shaft.
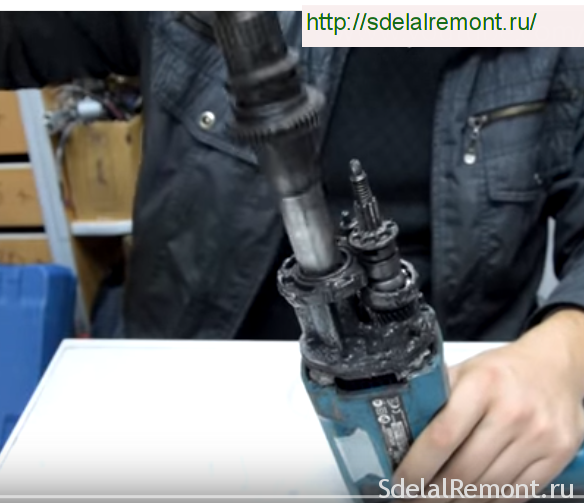
To disconnect the mechanical part from the electrical one, you must first remove the electric brushes.
Remember! In the lower part of the housing, the rotor is held by electric brushes, which must be removed.
After checking that the electric brushes are disconnected from the rotor lamellas, use a screwdriver to pry the metal housing of the hammer drill at the border of the green plastic housing.
Now we turn to disconnecting the rotor from the mechanical part of the perforated
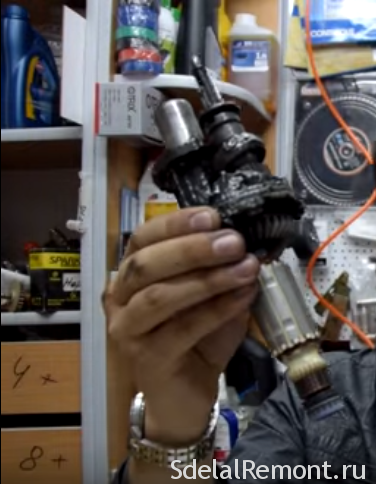
If you take the rotor housing in one hand and the mechanical housing in the other and pull in different directions, swinging, you will separate these two units.
You will get such a unit in the old grease.
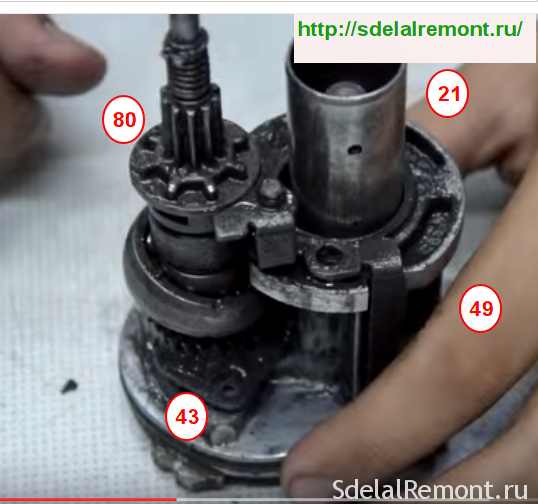
Then unscrew with a hexagon two bolts M4 × 12, pos. 43., art. 266273-7 with an internal hex head.
Pull out the shaft with the intermediate spur gear 10 pos. 80, art. 226399-7.
from the inner case, pos. 49, art. 153687-8.Remove old grease from parts.
You will get such a mountain of clean details.
Now carefully look through the details, discard the rubber rings immediately after picking up new ones.
Replace the defective parts with new ones.
Frequent mechanical failures of Makit punchers include:
- destruction of the quick-release chuck;
- failure of bearings;
- breakage of the striking mechanism;
- drill barrel wear;
- wear of striker and striker rubber bands;
- breakage of gears.
The hammer drill chuck is repaired to replace the boot and rubber ring, as well as the conical spring and the steel ball, which secures the working tool (drill). This is indicated by what is a working tool? namely, the drill does not hold well in the chuck.
The main reason is the wear of the steel ball 7.0, item 20, art. 216022-2. The wear of the ball occurs from contamination of the bore of the cartridge due to the ingress of dust and dirt.
The general view and device of the Makit perforator cartridge is shown in the photo below.
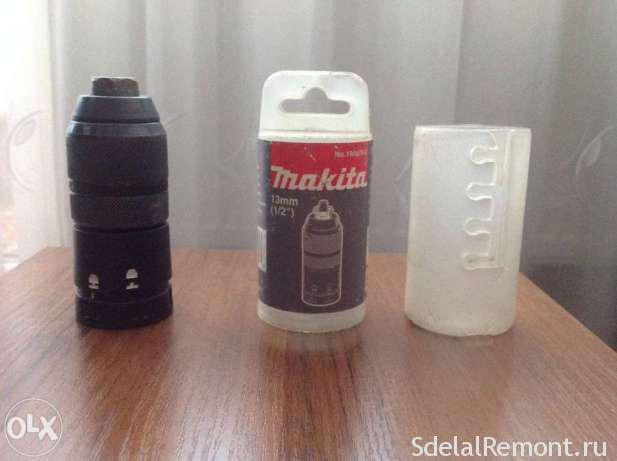
Do-it-yourself repair of the makita 2450 perforator cartridge is easy. The cartridge must be disassembled, freed from old grease, discarded rubber parts, replaced defective.
More complex malfunctions require knowledge of the mechanical part of the Makita 2450 perforator.
Having determined the nature of the malfunction of the Makita perforator, proceed to disassemble the mechanical part, called the gearbox.
Disassemble the mechanical part according to the attached video.
Free it from old grease.
Carefully inspect all parts, their integrity, level of wear. All rubber products require replacement during any disassembly.
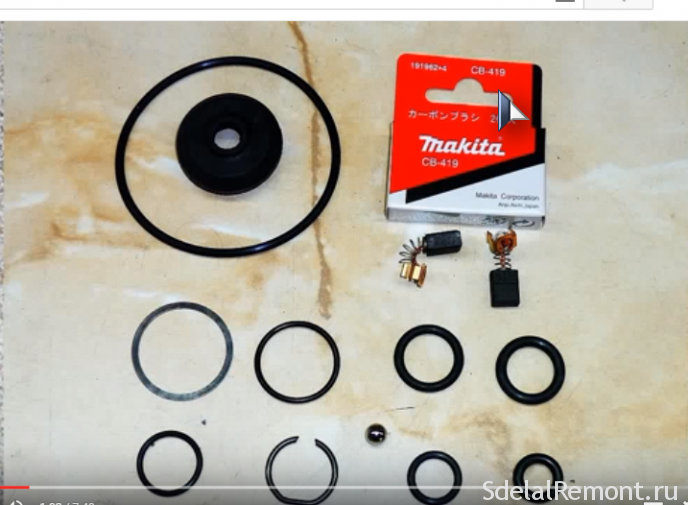
Consider repairing the barrel of a rock drill. Let's analyze the mechanism completely.
Video of disassembly, lubrication and assembly of the Makita perforator
Remember! In the lower part of the housing, the rotor is held by electric brushes, which must be removed.
The next step is to disconnect the rotor from the removed mechanism. The rotor is simply disconnected from the mechanism by pulling it out, since it is held by the friction of two helical gears.
The result is such a dirty knot.
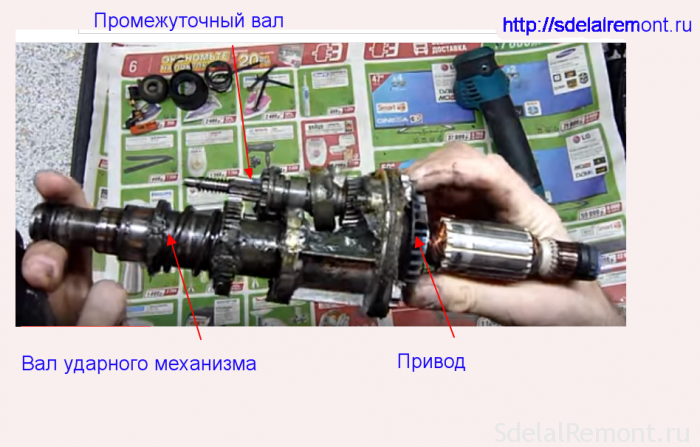
Now we need to separate the percussion shaft.
Most often, the rubber rings wear out, the firing pin pos. 24, compressor spring pos. 18. and cylinder parts.
This is how barrel parts wear out and break down when the tool is misused.
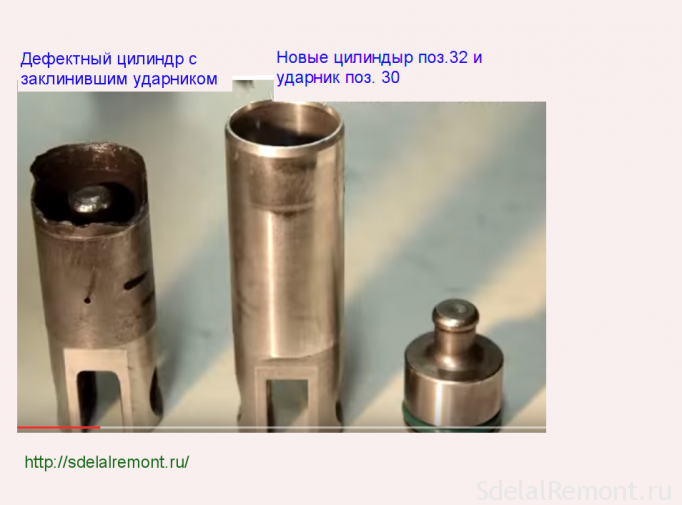
Consider the most difficult malfunction - the failure of the percussion mechanism.
The characteristic signs of a breakdown of the percussion mechanism are the absence of a blow and the unpleasant noise of a working perforator in the "Blow" mode.
Such a malfunction is typical for those rotary hammers that, during operation, were strongly pressed against the surface to be treated.
Having disassembled the gearbox, we remove debris and pieces of foreign objects. We find the faulty part and clean everything from the old grease.
Very often, the firing pin pos. 24, art. 324396-8, which is part of the barrel.
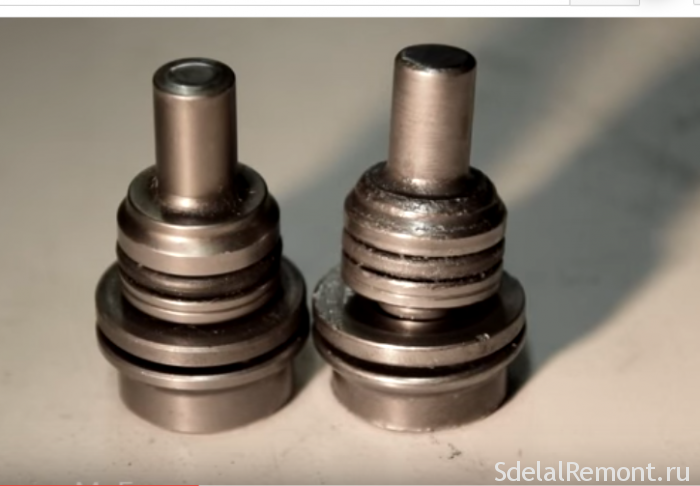
metal ring pos. 27. art. 324216-6.
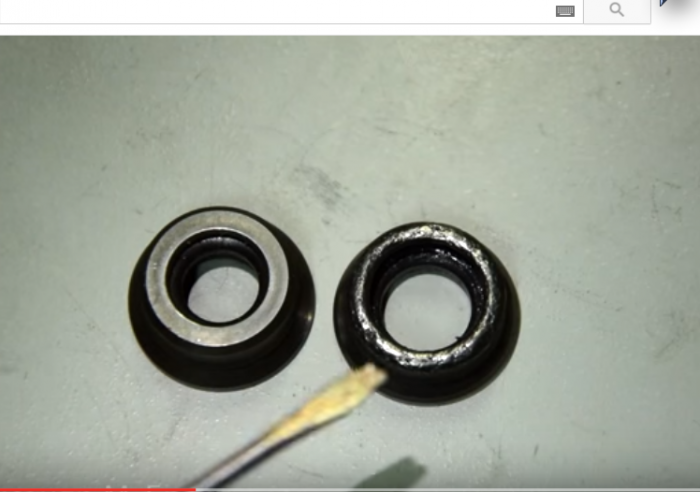
Discard damaged parts, replace with new ones, cover with a thin layer of grease. The parts are ready for assembly. But more on that in the next article.
Please help me if you can. I tell the whole prehistory.
On June 9, 2008, I finally made up my mind and bought a hammer drill for my birthday for small household needs, which I had two days before. Since there are a lot of punchers on the market, I studied for a long time, read reviews on the Internet, and finally, after painful choices, I settled on a dummy, tk. many people said great reviews about it, especially about the HR2450 - an indestructible device. I have a lot of different power tools, I like to tinker with my own hands in my free time from work, my hands are inserted in the right place. And therefore, right away, I initially wanted to buy a professional reliable hammer drill for life and save myself from smut and any problems with it. That is why I did not buy inexpensive Chinese and Russian perforators, such as stern, interskol and others. Apparently in vain.
In short, they promoted me in the store to a new version of HR 2450 only with a rubberized case and a convenient brush switch, as a result I bought myself another professional tool - HR2470. At home I read the instructions, twisted the punch in my hands, sniffed fresh grease, tried on different borax, and happily got down to work. Of the works, during the three days that I did from time to time at home, there were several holes in the puncher mode, and beating off the old tiles in the bathroom in the jackhammer mode. At some point, I noticed that he began to crunch, crackle incomprehensibly inside, it was worth adding momentum. Began to hammer worse. In punch mode, the drill began to wedge. And this is just a few days, having worked in total for 2-3 hours.
Contacting the service department brought amazing news - they said that some kind of spare part had broken down, that it could only break from improper operation, and they billed 800 rubles for a part, and for a used part (similar to 2450, since new they were out of stock, and a new one would have cost even more). Only after several threatening letters to Moscow official dealers, a couple of days later they called me from the Makita service center in Ufa and, reluctantly, with a favor, told me that my puncher had been repaired and I could pick it up for free. Immediately, a new part came from somewhere (although I doubt it must have been used, but how can you prove it?). Anyway. Renovated, so renovated. I spent a huge heap of nerves and energy, not counting the time and gasoline on trips to the other side of the city. I did not dare to give back and take the money - I no longer had the strength and patience to fight again, to prove my innocence, and so on. I decided, okay, they repaired it - now it's new again!
In short, two weeks after that, fearing to touch him once again, I decided to resume working with him - in vain did I buy it? But after some time of work with a 10 mm drill, it again began to crack and slip at high speeds!
The guarantee at that time was valid for another 11 months, but I already spent so much effort and nerves to get it repaired, and as it turned out, this did not give results.
Since that day, it has been in my suitcase. Sometimes, you need to drill something at home, I take it out and work only at a speed of 1/3 of the maximum speed, and if you increase the speed a little, it starts to slip. As a result, in a year and a half I could have worked for them for at most 1 hour of pure time.
In short, I understand the tools, and their structure is also more or less. Disappointed with the quality of Makita's service center, I now want to repair the hammer drill myself. On the Internet, I found a service manual for disassembling / assembling the Makita HR 2470 rotary hammer in English. After carefully studying manul, I have two assumptions:
1) either the 34th piston gets stuck in the 36th part (maybe from an abundance of lubricant, the effect of a suction cup, or vice versa from a lack of lubrication and a seizure, which is unlikely)
2) either the 90th part is out of engagement with the 44th. Most of all I sin on the knot starting from the 41st part to the 46th.
If there are knowledgeable people on the forum, tell me what exactly is faulty in the hammer drill, maybe some part is out of order, in your opinion? and how much will this part cost?
Due to the ingress of dust, dirt and moisture, the internal lubricant hardens over time and does not fulfill its intended purpose. The hammer drill starts to work with abnormal noise. When starting to repair a hammer drill, be sure to read the attached instructions for disassembling, lubricating, assembling the Makita 2450, 2470 hammer drill assemblies. We will also tell you how to disassemble the Makita 2450 perforator.
Disassembly of the Makita 2470 perforator begins with the removal of the mode switch knob.
Place the hammer drill on a clean surface.
When disassembling the mechanical part of the Makita 2450 or Makita 2470 hammer drill, you should always remove the mode switch knob.
At the beginning of work, the knob is set to the "Impact" mode (extreme right position clockwise).
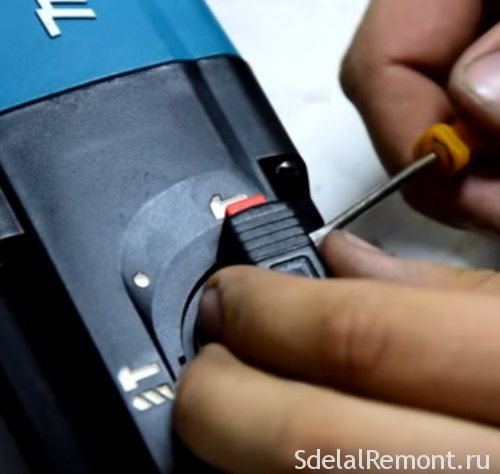

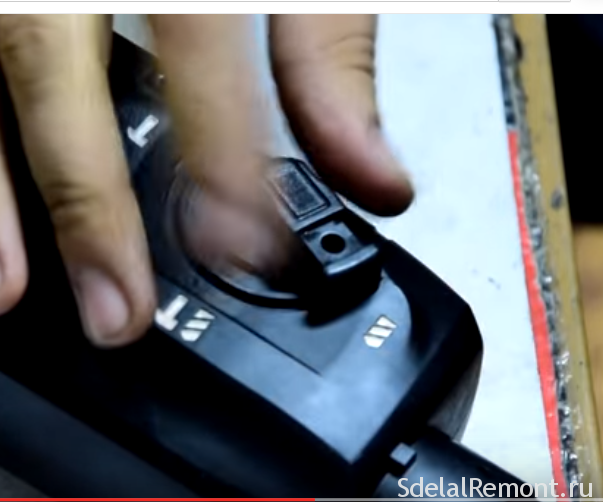
The grip clamped with fingers is removed from the grooves of the case.
Mode Knob Setting Procedure
To install the mode switch in the case, you need to perform some actions:
• insert the switch to the “drilling” position into the seat until it clicks;
• move the switch counterclockwise to the “impact” position;
• move the switch with a click counterclockwise to the "drilling" position;
• insert the spring and the red button;
• insert the cover from above until it engages.
The mode switch is assembled.
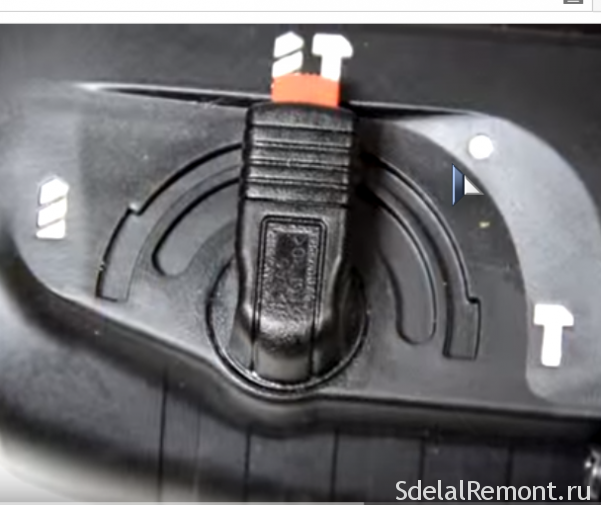
At the second stage, you should disassemble the quick-release chuck and repair the hammer drill chuck with your own hands. By the way, the cartridge requires disassembly only for Makita 2470 models. The cartridge device is quite simple, and any person who has a little bit of locksmith skills can handle its repair.
Punch chuck repair begins with installing the punch vertically on the rear housing cover. The diagram of the h-makita perforator will help to correctly perform the disassembly work.
Is it necessary to replace the cartridge of the Makit 2470 perforator? The answer can be obtained only after complete disassembly of the cartridge with your own hands.
Using a screwdriver or a puller, the boot is removed, the cartridge is freed from the retaining ring, the coupling casing, the metal ring 20 pos. 4. Next, you need to carefully get out the ball, pos. 20, remove the guide washer, pos. 5, and the conical spring, pos. 6, which supports it. The cartridge is disassembled.
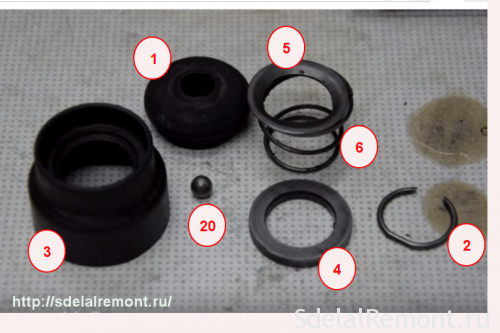
The diagram below shows the device of the punch chuck.
The main malfunctions of the makita 2450 rock drill that cause defects in the chuck are:
- wear of the protective rubber boot pos. 1;
- relaxation of the retaining ring pos. 2 or its partial wear;
- ball wear, pos. 20;
- loss of elasticity of the conical spring pos. 6 or its extension.
Repairing a hammer drill chuck is not a complicated procedure and is usually easily done by anyone who can handle a screwdriver.
If replacing a rubber boot, retaining ring, conical spring is not difficult, then replacing a new ball requires attention. The new ball should be 7mm ± 1 µm in diameter.
As a lubricant, it is recommended to use a special lubricant developed for the Makita perforator.
The grease has the index Makita P-08361, Makita 183477-5 SDS-PLUS 30g for the gearbox. It is recommended to use Makita 196804-7 grease for drill shanks.
When assembling the chuck, install the conical spring with the narrow side to the hammer drill.
Do not forget, repairing a hammer drill chuck with your own hands requires care from the collector.
The assembly is done on a clean surface. Parts are pre-washed, dried and lubricated with a thin layer of the recommended grease.
The gearbox shaft is lubricated with Makita 183477-5 SDS-PLUS grease. All incoming parts of the chuck are assembled on the shaft in a certain sequence.
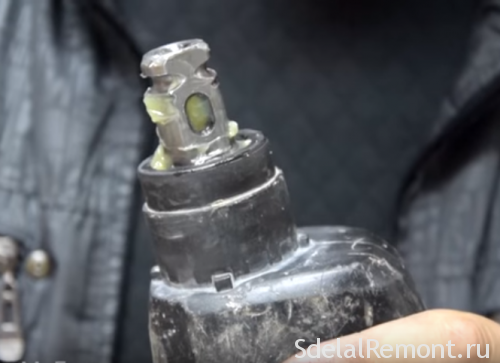
Having installed the conical spring, pos. 6, put on the guide washer, pos. 5, and fix it with the ball, pos. 20, by inserting it into the groove of the gearbox shaft.
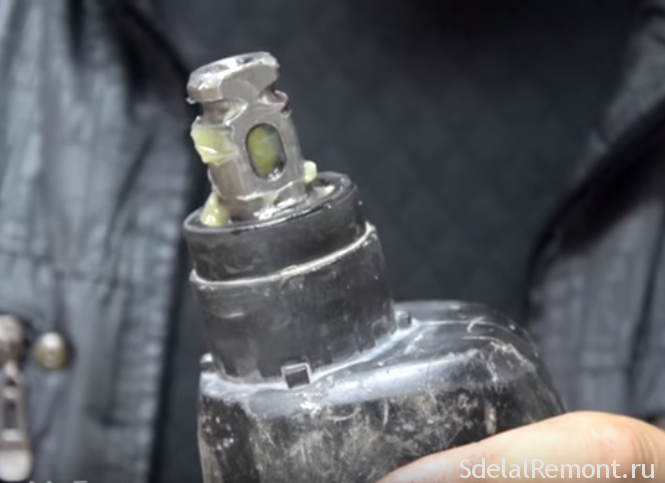
It remains to put on the ring (pos. 4), the coupling casing (pos. 3), fix the parts with the retaining ring (pos. 2). At the last stage, insert the protective tip pos. 1 into the end of the cartridge.
the repair of the Makita 2450 perforator cartridge is over. It remains to check its quality by inserting a drill into the chuck. When properly assembled, the chuck keeps the drill from falling out spontaneously.
The cartridge is assembled.
To get to the mechanical part, you will need to remove the plastic case.
The procedure for disassembling the mechanical part of the Makita perforator
First, the protective black plastic case is removed. The case is removed after you unscrew the four screws securing the case from the end.
Pressing on the end of the shaft, you push the gearbox out of the housing.
After removing the housing, it is necessary to separate the rotor from the gearbox.The general mechanical part is called a reducer.
It is easy to separate the rotor from the mechanical part (gearbox).
Clamp the gearbox with your right hand, clamp the rotor with your left.
Swinging, pull both sides in opposite directions. The rotor is held in the gearbox by the friction of the helical gears.
The main malfunctions of the Makita perforator occur in the mechanical part of the tool.
The most typical malfunction for the mechanical part is the failure of the percussion mechanism.
Disassembly of the striking mechanism
The percussion mechanism is assembled on the inner casing and consists of a gearbox shaft and an intermediate shaft.
The rotary motion is transmitted via helical gears to the countershaft.
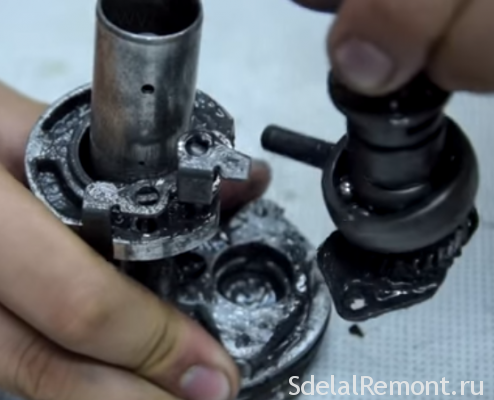
The gearbox shaft is a hollow barrel in which the cylinder moves freely.
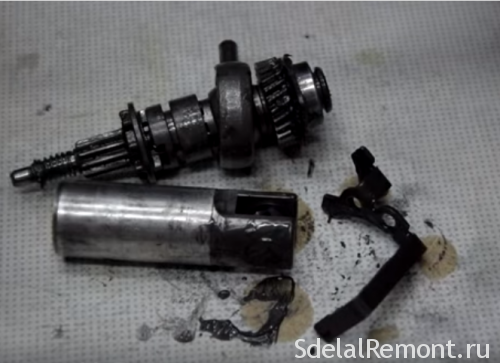
A small spur gear mounted on the intermediate shaft transmits rotation to the large spur gear of the gearbox shaft, in which the percussion mechanism is mounted.
And the translational movements on the shaft of the percussion gear reducer are simultaneously transmitted due to the transmission from the rolling bearing of the intermediate shaft to the cylinder moving in the gearbox shaft.
We proceed to disassembling the intermediate shaft.
Dismantling the intermediate shaft
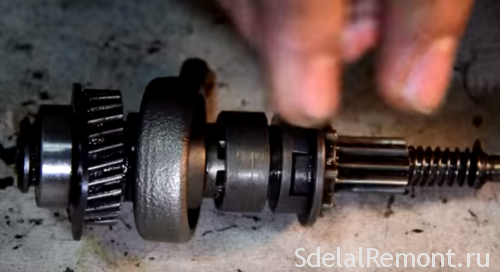
On the shaft poz.40 mounted helical gear poz.42, which is transmitted rotation from the rotor gear, rolling bearing 608zz poz.41, which transmits translational motion to the hinge poz.34 piston poz.32.
On the other side of the shaft, a clutch is installed pos. 39, spur gear 10 pos. 80, compression spring pos. 38, circlip S-7 pos. 37, bearing 606zz pos. 36
Pay particular attention to the condition of the rolling bearings.
Imported bearings are installed in the hammer drill. Installation of domestic bearings is allowed.
Bearing 606zz can be changed to 80016, bearing 609zz is changed to 80019.
Moving on to disassembling the shock mechanic's shaft
Disassembly of the percussion shaft
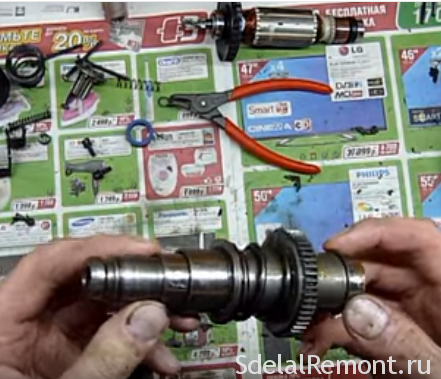
Disassembling the barrel of the Makita 2470 perforator is a simple process if you use the diagram of the Makita perforator.
The shaft is a barrel poz.21, in which the impact mechanism is assembled.
A gear, pos. 19, is attached to the barrel, which is pressed down by a spring, pos. 18, through a washer, pos. 17, and is fixed with a retaining ring, pos. 16.
The cylinder, pos. 32, moves in the barrel, acting on the firing pin, pos. 24. On the reverse side of the striker, a metal ring pos. 27 is fixed, which transfers the blow to the drill.
And when do you need to replace the drill barrel?
Most often, the metal ring fails.
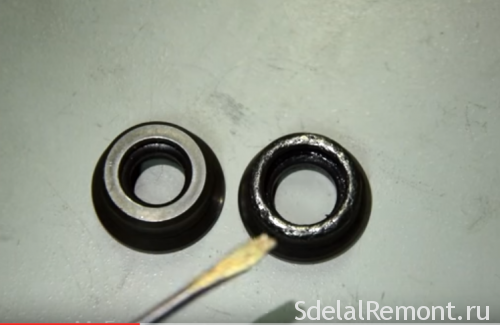
Striker
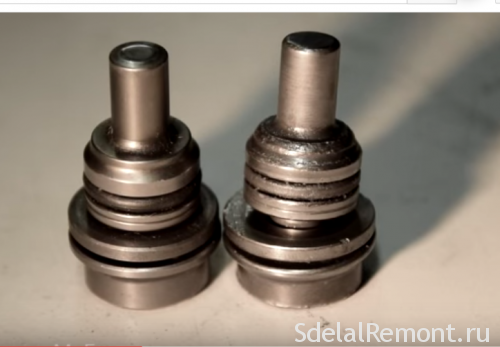
Cylinder with drummer
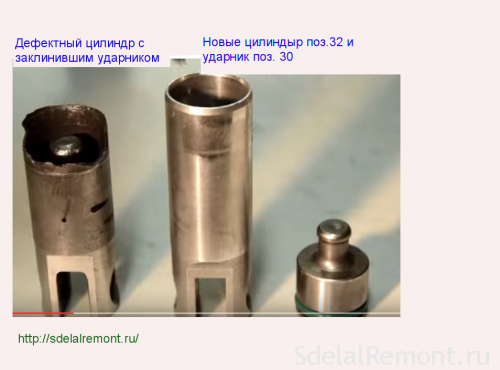
We figured out the disassembly.
We change the parts for serviceable ones and get ready to assemble. Learn more about the lubrication and assembly of the rock drill.
A hammer drill is a percussion drilling tool that simultaneously performs the function of percussion and drilling equipment when working with particularly durable materials.
The device uses two ideas at the same time: the tool rotates and moves in the longitudinal direction, transmitting the impact impulse to a hard surface.
Rock drills always work in an extreme environment with a high degree of dust.
The duration of trouble-free operation is influenced not only by the operating conditions, but also by the quality of the components included in the tool.
Perforators Makita 2450, 2470 are reliable high quality tools. But even the most reliable tool requires proper care and timely maintenance.
To perform maintenance on Makita 2450, 2470 hammer drills, it is imperative that you familiarize yourself with the internal contents of the tools that make up the assemblies. This instruction will help you find out the weak points of the Makit puncher.
To repair a hammer drill Makita 2450, 2470 with your own hands, a person who has locksmith skills and knowledge of electrical engineering is allowed.
Remember! When repairing a rotary hammer, you must follow the safety rules when working with electrical appliances.
Hammer drills Makita 2450 and 2470 are assembled practically according to the same scheme and, practically, from the same, interchangeable parts.Repairing them is no different.
General view of the Makita 2450 rotary hammer
For the convenience of repair, below is an assembly diagram and a catalog of parts for Makita perforators.
Makita 2450 hammer assembly diagram
The Makita hammer drill conventionally consists of electrical and mechanical parts. Moreover, in a black plastic case, there is a mechanical unit of the perforator, and under the green plastic case, the electrical part of the perforator is hidden.
The mechanical unit is designed to transmit the rotational moment of the shaft to the tool, creating not only torque and translational shock impulse.
The task of the mechanical unit is to transfer rotation from the rotor to the tool, while providing the tool with longitudinal movement.
Disassembly of the rock drill begins with the removal of the quick-release chuck.
Quick Release Chuck Parts
Having disassembled the chuck, unscrew the four screws, pos. 10, securing the gear housing cover, pos. 14, of the mechanical block and the puncher body, and, pressing on the end of the puncher shaft, remove the black plastic cover.
Remove the cover of the mechanical block
To remove the mechanical block from the green stator housing:
-
1. Unscrew the three screws, pos. 70,75,76, holding the cover, pos. 69, in the handle of the perforator;
-
2. Remove the cover;
-
3. Having released the springs of the brush holders pos.63.66, take out the carbon brushes pos.65.
The mechanical block can now be pulled out of the stator housing.
Having released the mechanical block, it is necessary to disconnect the rotor from it. Rotor pos. is fixed in the mechanical block due to the friction of the gear teeth and is pulled out by staggering and disengaging at the same time.
The mechanical assembly is assembled on the inner case, pos. 49. To remove the intermediate shaft, it is necessary to unscrew two bolts pos. 43 at the base of the housing. The intermediate shaft is also fixed with the mode switch lever.
Two words about the mode switch
The Makita 2450, 2470 hammer drills have a lever that provides the tool with three operating modes. The hammer drill can simply drill, just chisel, and chisel with simultaneous drilling. The switch lever is put on the axis of the inner case and is fixed with a compression spring, pos. 85, a washer, pos. 87, and a retaining ring, pos. 86.
It's time to remove the intermediate shaft.
To disassemble the intermediate shaft, use the diagram attached to this manual.
Photo of the intermediate shaft diagram showing the order of disassembly
Remove from the shaft pos. 40 in order:
- a). bearing pos. 46 and ring pos. 47;
- b). spur gear pos. 42;
- v). rolling bearing pos. 41;
And on the other side of the shaft, remove:
- G). flat washer 12 pos. 35;
- e). bearing 606 pos. 36;
- e). retaining ring S-7 pos. 37;
- g). compression spring 7 pos. 38;
- h). clutch, pos. 39.
To disassemble the percussion shaft, pull it out of the inner housing.
From the shaft it is necessary to pull out the cylinder, pos. 32, inserted into the inner cavity of the shaft.
The cylinder is very easy to disassemble:
-
1. From it you need to get the drummer pos.30;
-
2. Knock out the hinge of the piston poz.34;
-
3. Remove two flat washers poz.33,35.
To disassemble the shaft itself, pos. 21 of the percussion mechanism, it is necessary to remove from the side of the cartridge installation shaft:
- - ring spring 28 pos.16;
- - washer 30 pos. 17;
- - compression spring 31 pos. 18;
- - spur gear 51 pos. 19;
- - steel ball 7.0 item 20.
And from the side of the inner cavity of the shaft it is necessary to remove:
- - annular spring 28 pos. 29;
- - rubber ring, pos. 28;
- - metal ring pos. 27;
- - rubber ring 15 pos. 26;
- - ring 9 pos. 25;
- - flat metal washer 28, pos. 22.
Barrel shaft disassembled
The electrical part of the Makita 2450.2470 rotary hammer includes:
-
rotor pos. 54;
-
stator pos. 59;
-
circuit breaker TG813TLB-1 pos. 68;
-
carbon brushes SV-419 pos. 65;
-
brush holder pos. 63.66.
To remove the stator, it is enough to knock on the end of the green plastic housing from the stator side with a wooden mallet or block.
But first you need to unscrew the two self-tapping screws 4 × 60 mm pos. 57.
With frequent tapping on the body, the stator spontaneously protrudes beyond the edges of the body, and then is pulled out by hand.
![]() |
Video (click to play). |
The remaining elements of the electrical part of the Makita 2450 or 2470 perforator can be easily dismantled, since they are not attached to anything.