In detail: DIY repair of bosch piezo injectors from a real master for the site my.housecope.com.
Piezoelectric injectors are now increasingly used in common rail fuel systems in modern diesel engines. Designers receive a tool to fine-tune their engines, while car owners and mechanics receive a bunch of financial and technical nuances. So what are the advantages and disadvantages? The engine will deal with the issue.
The introduction of the Common Rail system, which took place in the late nineties, was a new milestone in the development of the Diesel engine. The in-line high pressure fuel pump (TNVD) replaced the main pump, and the hydraulic injectors gave way to injectors with electronically controlled solenoid valves.
Unlike the previous design, where the opening of the nozzle needle was only due to pressure, electro-hydraulic nozzles work in a slightly different way. At rest, the fuel pressure on the cone of the nozzle needle and in the chamber of the control valve located above the needle is the same, the spring-loaded needle closes the nozzles, and injection does not occur. When a signal from the control unit is received, the solenoid valve is triggered, the pressure above the needle is released, it rises, opening the nozzles, and injection is carried out.
Piezo injectors work in a similar way, in which instead of an electromagnet with a moving core, another performer is used - a piezoelectric element. It has the shape of a square column, consisting of a plurality of ceramic plates stacked on top of each other and sintered together. Under the influence of current, a piezoelectric effect arises in them, due to which the structure is able to quickly change its length, acting on the control valve. Compared to an electromagnet, the piezoelectric element provides faster response, the time of which is about 0.1 ms (versus 0.5 ms for a nozzle with an electromagnet), and is also capable of creating a greater force on the control valve and has a higher stroke accuracy for fast cut-off. fuel supply.
![]() |
Video (click to play). |
Piezoelectric nozzle design: 1 - piezoelectric element; 2 - hydraulic compensator; 3 - control valve; 4 - throttle washer; 5 - spray needle
The use of a piezoelectric element in the injector allowed the designers to implement up to ten injections per engine cycle - preliminary, main, post-injection. At the same time, the portions themselves, their volume and frequency can be flexibly adjusted here, based on the engine operating modes. Thus, the smoothness and completeness of fuel combustion is achieved in the engine, noise and toxicity are reduced. For modern diesel engines in passenger cars, piezoelectric injectors are becoming an integral element in the design of the fuel system. But high technology comes at a price.
From the point of view of service, the main feature of piezo injectors is the high complexity of repair, which requires special equipment. In some cases, repairs are completely impossible. At the same time, the piezo injectors themselves are very demanding on the quality of the fuel, its composition and the degree of purification, with a decrease in which they quickly fail.
Piezo injectors for passenger car engines are manufactured by companies such as Bosch, Delphi, Denso and Siemens. But they are in no hurry to give this market to third-party repair services, offering a replacement entirely. This component is quite expensive: depending on the brand and model, a piezo injector can cost from 16,000 to 40,000 rubles. Therefore, repairs, the average cost of which is half or less of the price of a new nozzle, is in demand. But not every service can handle it.
The control valve most often fails.In this case, the part is manufactured with high precision and dimension at the micron level.
Difficulties begin already from the moment of diagnostics, which cannot be carried out in a garage workshop. For example, a transfusion test, when pipes with glasses are connected to the drain fittings in the return line, in a system with piezo injectors it is simply impossible to do that, since there must be a back pressure in the return line.
As servicemen say, the most vulnerable is the control valve, which fails most often. Moreover, it is one of the most important components - its malfunction can lead to the failure of the entire nozzle. The valve is either replaced as a whole, or restored by grinding and lapping the working edge of the valve itself and the working edge of the valve seat. But this is not easy to do. The valve has a very high, precision manufacturing accuracy with micron-level measurement parameters.
For example, the shoulder at the top of the valve plug is about one hundred microns (one tenth of a millimeter) wide, and there must be a certain chamfer angle. And the more accurately the factory parameters are reproduced, the easier it will be to adjust the injector and the longer its service life will be.
Dmitry Efremenko, director of the company> - "Europrom":
- Rolling bearings in the units of domestic machine tools have greater tolerances for backlash and clearances than the valves of piezo injectors. Accordingly, it is impossible to achieve the required accuracy on such machines. Therefore, we had to design the equipment for the restoration ourselves, the individual units and elements of which had to be bought in Switzerland.
It is also possible to restore the sprayers, in which the needle and the saddle are processed and rubbed, the nozzles are blown out. If the atomizer is irreversibly damaged (for example, when the nozzle overheats), then a part from another nozzle is taken, where the atomizer can be restored. They do the same with valves, the varieties of which, in contrast to the types of sprayers, are ten times smaller, which greatly facilitates the selection. For example, Bosch piezo injectors can use the same valve in more than ten different injectors.
Recently, new Chinese-made spare parts (valves, hydraulic lifters, sprayers) have appeared on the market. But their quality "floats" a lot, it is difficult to figure out where the non-original, suitable for repair, and where the thrown away money is.
The Chinese offer in the form of a spare part and a piezoelectric element, which is also one of the weak points of the piezo injector. But, as servicemen say, replacing it does not justify itself in terms of labor costs. Part of the piezoelectric element is firmly soldered to the connector block, which, in turn, is pressed onto the body, which forms a non-separable structure. Therefore, it is easier to replace this part of the body entirely.
The piezo injector is a high-tech component, originally intended for replacement as a whole and difficult to repair. But life dictates its own rules - services appeared in which they learned how to restore these parts so that the client was satisfied. It remains to say their word to the manufacturers of the non-original and start producing analogs. And also to the manufacturers of original piezo injectors themselves, offering proprietary restoration technologies and spare parts for repairs.
Alexey Zubikov, Head of Network Development, Bosch Diesel Center / Service in Russia, Transcaucasia and Central Asia:
- For the repair of piezo injectors in Bosch Diesel Service workshops, the company does not yet have the technology, sets of special tools and spare parts are not ready. At the moment, we can only diagnose this type of injector. It is planned that we will start providing piezo injectors repair services from 2017–2018.
In our time, the rapid development of technology contributes to the discovery of more practical and environmentally friendly inventions. Diesel fuel system manufacturers are constantly improving their units.If earlier the injectors were controlled, let's say, mechanically, then then electrical elements appeared in the control of the fuel system. This made it possible to more accurately monitor and control the injection system. But the nozzles themselves still remained a purely mechanical product, and the speed of their operation depended on the parameters of the dynamism of the operation of these mechanical units.
In the electromagnetic injectors of the first generations, the fuel supplied to the cylinder was divided into a preliminary and main dose. But the injection system turned out to be more efficient, where, in one working stage of the injector, the fuel is divided into the maximum possible number of micro-portions.
For this, it was necessary to increase the response speed of the control and actuating mechanisms of the injector. For this purpose, a piezoceramic nozzle was designed, which works four times faster than a traditional electromagnetic one.
Considering the specifics of the design of this type of injectors, they add their own specific ones to all the "sores" of traditional electromagnetic nozzles.
Basically, they manifest themselves in this way: the car does not start well (it will not start at all); stalls in load; troite; stalls at idle; traction is lost under load; the appearance of gray smoke at idle and black in the load.
The reasons for such defects in the operation of the car can be varied, but quite often we observe the root cause in the injectors. Therefore, if such symptoms are found on your diesel engine, the first thing to do is go through computer diagnostics. It is inexpensive and will save you a good amount of money in your case.
If the diagnostics determine a loss (excess) of pressure in the system, a short circuit on the injectors or a significant imbalance in the operation of the cylinders, then first pay attention to the injectors. They are often the reason for these problems.
Piezo injector does not hold pressure - the precision part of the switching valve is damaged. As a result, the car will not start well. It can also stall under load.
Short circuit of the nozzle to ground - the insulating layer of the piezoelectric element is damaged. In this case, the car does not start at all, or it starts up and after a short period of time stalls right at idle speed. Sometimes, with such a breakdown, the car stalls only under load. Most often we see such a defect on Trafic 2.0, less often on cars of the Volkswagen and Audi group.
Failure of the sprayer... There are, in principle, two options: either the sprayer pours or wedges in the closed position. In the first case The low pouring nozzle produces light smoke at idle speed, which disappears completely under load. It manifests itself on non-working sprayers after removing the particulate filter. Cars of the Mercedes group, less often Audi, Crafter, love to be sick with such a light smoke.
If the sprayer pours heavily (open wedge), there will be more smoke. Also, black smoke appears in the load, which is accompanied by a knock. But such a defect has so far been observed very rarely.
At closed wedge of the sprayer, the car troit at idle (the wedge is more felt with a small pressure in the system).
Depressurization of the drain line - mechanical damage to the elements of the drain line, failure of the check valve of this line. With such a breakdown, the car starts up, works, but stalls with a small load. Quite often we see such damage on Trafic 2.0.
Ninsufficient capacitance of the piezoelectric element (or weak resistance) - the piezoceramic element is out of order. If this happened on one injector, then the machine is troit. If the piezoelectric element loses capacity across multiple injectors, then the vehicle may lose traction.
We successfully repair all the listed breakdowns of piezo injectors since 2014. A guarantee is given for the repair of piezo injectors, and a record of the repaired cars is kept. To date, more than two thousand injectors have been serviced for Trafic 2.0 only.
Cutaway piezoelectric nozzle:
1 - drain line; 2 - electrical connector; 3 - piezoelectric element; 4 - high pressure channel; 5 - hydraulic cylinder; 6 - coupled pistons; 7 - switching valve (multiplier); 8 - throttle plate; 9 - spray needle; 10 - nadigolny camera; 11 - outlet throttle.
Now let's take a closer look at these nodes.
It is assembled piezo crystal (30-40 mm long), which consists of ceramic plates welded together. When an electric pulse is applied to it, it is capable of expanding in 0.1 ms
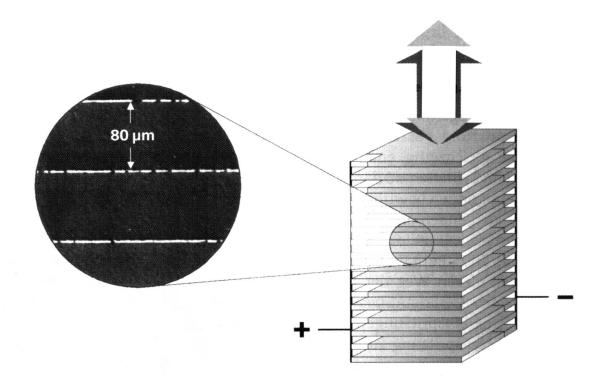
This is quite enough to act on the needle of the nozzle atomizer with a force of 6300 N. To increase the efficiency, palladium and zirconium are added to its structure. Interestingly, it consumes electricity only when voltage is applied. And when the electrical voltage is turned off, it regenerates this energy.
Frame hydraulic cylinder located inside the damping spring. There are two coupled (dependent on each other) pistons in the cylinder body. The space between them is filled with fuel, which, thanks to a valve in the drain line, is under pressure up to 10 bar. The fuel acts as a pressure shock absorber here. The hydraulic cylinder acts as an intermediary between the piezoelectric element and the switching valve.

Switching valve (multiplier) Is a valve that is a switch between the areas of low pressure (in the nozzle cavity around the hydraulic cylinder) and high pressure, which is located above the throttle plate and is connected to the cylinder chamber.
Spray slightly different from the classic version. But the principle of its operation is similar to the atomizer of an electromagnetic nozzle - high pressure fuel is pumped simultaneously from the upper and lower sides of the needle. This allows the nozzle to be kept closed.
Above the spray is located choke plate... It is equipped with holes through which the fuel flows between the high-pressure channel, the spray nozzle and the changeover valve chamber.
At rest, the spray needle, under the action of high pressure from both sides simultaneously, is in the closed position. When an electric pulse is applied to the piezoelectric element, it expands. The piezo crystal expands and pushes the elements of the hydraulic cylinder.
The hydraulic cylinder, in turn, acts on the changeover valve and opens the outlet throttle channel through which the pressurized fuel flows out of nadigolny cameras. In this case, the pressure above the needle drops, and the fuel in submissive chamber, which is under high pressure, raises the spray needle, and the injection is performed.
That's all. But the main trick is that this whole series of processes is happening at a very high speed. This is the main advantage of piezo injectors.
- response speed and frequency
- number of injections in one working cycle of the injector
- fuel dosage accuracy
- reduction of noisy engine operation
- operation of the nozzle at high pressures
- environmental friendliness
As mentioned above, the speed of the piezo injector makes it possible to divide the fuel supply into a large number of micro doses: first, several preparatory injections take place, then the main injection takes place, and after it the so-called post-injection.
Fuel injection occurs in such a way that a small amount of fuel enters the cylinder - pilot injection (about 1.5 ml). It enriches and warms up the fuel-air mixture, smoothly preparing the system for the main fuel supply. This achieves an even pressure distribution in the combustion chamber.The more such pre-injection, the softer the combustion proceeds, and, accordingly, the quieter the engine runs.
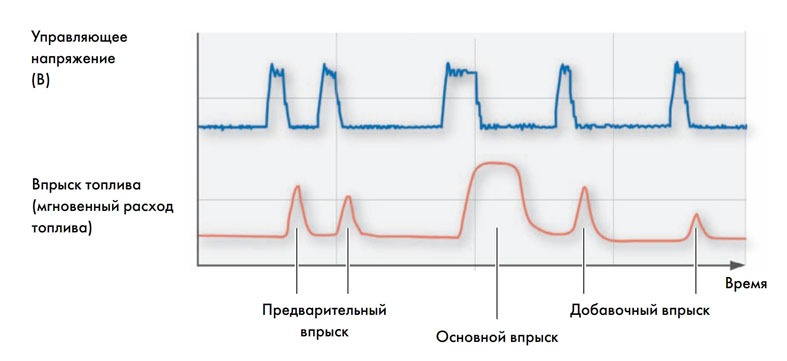
After that, a large dose of fuel is supplied, which plays the main role in creating the fuel-air mixture. At the end of the combustion cycle with post-injection residual fuel is burned out. This reduces the toxicity of the exhaust gases. Also, the fuel supplied in this way at the end of the injector cycle helps to clean and regenerate the particulate filter.
Thanks to the latest developments, it is possible to use up to seven injections per injector stroke. Due to this, new opportunities appear for increasing engine power, reducing its noise level and creating conditions for more accurate control of exhaust gases.
Today, manufacturers are developing common rail systems with operating pressures up to 2500 bar. The maximum pressure in such injectors is achieved not in the fuel rail, but in the injector itself. They are equipped with a small hydraulic pressure booster and two electromagnets for precise control of the torque and the amount of fuel supplied. This will increase the injection pressure and the efficiency of the fuel system.
We are looking forward to seeing these nozzles in our workshop ...
Diesel injector nozzles. Mechanical injectors, Common Rail injectors. Repair technology.
The analysis of wear of parts of common Rail BOSCH piezo injectors gives grounds to assert that these injectors can be repaired not by replacing their worn out parts, but by restoring the geometry of the worn surfaces of injector parts.
The main, most loaded and subject to maximum wear of the nozzle assembly is the control valve. Fig. 2 shows the valve stem (fungus) on the conical obturator surface of which traces of cavitation wear are visible (Fig. 2, a) and characteristic scours (Fig. 2, b).
Wears out (Fig. 5) and the end surface of the fungus closes and opens the fuel flow from the high pressure zone through the nozzle in the throttle plate.
The wear on the surface of the throttle plate itself from the side of the control valve is very significant (Fig. 6).
There is an annular wear surface on the orifice plate and on the side of the sprayer (Fig. 7).
Typically, wear marks are visible on the end of the sprayer sleeve (Figure 8).
All of the above defects (Fig. 5, Fig. 6, Fig. 7 and Fig. 8) can also be removed using the technological methods of finishing, finishing and abrasive processing.
In case of noticeable wear (Fig. 9) on the closure cone of the nozzle needle, which usually causes the formation of drops on the nozzle of the nozzle under static pressure and on the operating nozzle, i.e. when cavitation defects appear and the contact area between the surfaces of the locking cone of the needle and the conical surface in the sprayer body increases, it is necessary to restore the tightness of the contact of these surfaces and correct their profile.
I have been following your publications for several years. Very interesting, very interesting. It is also advisable to check the performance on the machine. And the atomizers in this nozzle play an important role.
Thank you for rating.
On the issue of sprayers. I heard that the sprayers are flowing on the named nozzles, and this, as I understand it, is at static pressure. So maybe these are design features? On the nozzles that I disassembled, the condition of the nozzle locking cones was excellent. It is known that the spring on the spray needle in CR nozzles is not necessary for the operation of the spray. It presses the needle to the atomizer body so that when the engine is off, diesel fuel does not flow into the combustion chamber, and the needle is lifted and lowered due to the energy of the compressed fuel. And the spring is not very impressive there.
It is at a low (200 bar) pressure in static that such an unpleasant thing is revealed - the well-known spitting of white smoke at idle.
If we assume that after removing and disassembling the injector, you will not find any noticeable wear on its parts, then these are probably failures (breakdowns) in the electro-hydraulic injection system at low pressure and low rpm.
It has been recovering for a long time, but what resource does your recovery have? And what are the results before and after. My best result is a return flow of 5 cubic meters more than the new valve, and the mileage is 50tyk. But this has to be fucked up pretty well, and the feed must be driven in and the code must be assigned.
Repairs for sale will do, I don’t put this under commerce like a sprintercraft ..
I will not be honest, there are no statistics on this issue yet. But the fact that the resource of your repair is small is your problem. I don’t know what you’re doing with them. I know that if the geometry of the worn surface is restored and its quality is no worse than that of a new product, and the working clearances, in particular the same distance from the end of the valve stem to the orifice plate, remains unchanged, then why should this unit work less than the new one? And there is not so much "f ... tsya" there.
In theory, of course, everything is so, but how are things really going with you, what are the indicators of the oratka at the maximum speed of 1600bar - 565u
Today I looked at the insides of the rejected DENSO piezo nozzle for a very long time and I think that bringing it back to life is a very real task. Wearing there and in a microscope is not easy to see.
So far, I will not say anything about the return flow of the 1600 bar piezo BOSCH injector.
Guys are all right. The return flow with such a repair is the same as that of a new one. And they go with the correct repair and correct adjustment over 100,000. We have a lot of these machines. the main thing that would not be Turkey metal was! And the new Turkish ones fly out after 10,000. There were precedents.
Alexey, good day. Please do not tell me the angles of the working chamfer on the control valve, which is in Figures 3a and 3b and the mating surface in the plate in Fig 4. I tried to measure the valve 84 degrees using BMI-1. Is it so? Thanks in advance for your reply
Oddly enough, but I did not measure the angle of the locking tapered surfaces or whatever you call it "the angle of the working chamfer on the control valve". For me, to create a method for restoring the hermetic density of the named conjugation, it was not needed. However, I want to say that the angle of this cone, even when visually assessed, is certainly not 84 degrees. This is very small, logically, it should be 120 degrees there.
Will you sell the recovery method?
If you want me to help you in this matter, write to me personally and first of all who are you, where are you from and what do you do? My email is here. True, so far, to be honest, I have no great desire to replicate my methods. Outwardly, it looks simple enough, but only outwardly. All this requires a head and hands.
In our time, the rapid development of technology contributes to the discovery of more practical and environmentally friendly inventions. Diesel fuel system manufacturers are constantly improving their units. If earlier the injectors were controlled, let's say, mechanically, then then electrical elements appeared in the control of the fuel system. This made it possible to more accurately monitor and control the injection system. But the nozzles themselves still remained a purely mechanical product, and the speed of their operation depended on the parameters of the dynamic operation of these mechanical units.
In the electromagnetic injectors of the first generations, the fuel supplied to the cylinder was divided into a preliminary and main dose. But the injection system turned out to be more efficient, where, in one working stage of the injector, the fuel is divided into the maximum possible number of micro-portions.
For this, it was necessary to increase the response speed of the control and actuating mechanisms of the injector. For this purpose, a piezoceramic nozzle was designed, which works four times faster than a traditional electromagnetic one.
Considering the specifics of the design of this type of injectors, they add their own specific ones to all the "sores" of traditional electromagnetic nozzles.
Basically, they manifest themselves in this way: the car does not start well (it will not start at all); stalls in load; troite; stalls at idle speed; traction is lost under load; the appearance of gray smoke at idle and black in the load.
The reasons for such defects in the operation of the car can be varied, but quite often we observe the root cause in the injectors. Therefore, if such symptoms are found on your diesel engine, the first thing to do is go through computer diagnostics. It is inexpensive and will save you a good amount of money in your case.
If the diagnostics determine a loss (excess) of pressure in the system, a short circuit on the injectors or a significant imbalance in the operation of the cylinders, then first pay attention to the injectors. They are often the reason for these problems.
Piezo injector does not hold pressure - the precision part of the switching valve is damaged. As a result, the car will not start well. It can also stall under load.
Short circuit of the nozzle to ground - the insulating layer of the piezoelectric element is damaged. In this case, the car does not start at all, or it starts up and after a short period of time stalls right at idle speed. Sometimes, with such a breakdown, the car stalls only under load. Most often we see such a defect on Trafic 2.0, less often on cars of the Volkswagen and Audi group.
Failure of the sprayer... There are, in principle, two options: either the sprayer pours or wedges in the closed position. In the first case The low pouring nozzle produces light smoke at idle speed, which disappears completely under load. It manifests itself on non-working sprayers after removing the particulate filter. Cars of the Mercedes group, less often Audi, Crafter, love to be sick with such a light smoke.
If the sprayer pours heavily (open wedge), there will be more smoke. Also, black smoke appears in the load, which is accompanied by a knock. But such a defect has so far been observed very rarely.
At closed wedge of the sprayer, the car troit at idle (the wedge is more felt with a small pressure in the system).
Depressurization of the drain line - mechanical damage to the elements of the drain line, failure of the check valve of this line. With such a breakdown, the car starts up, works, but stalls with a small load. Quite often we see such damage on Trafic 2.0.
Ninsufficient capacitance of the piezoelectric element (or weak resistance) - the piezoceramic element is out of order. If this happened on one injector, then the machine is troit. If the piezoelectric element loses capacity across multiple injectors, then the vehicle may lose traction.
We successfully repair all the listed breakdowns of piezo injectors since 2014. A guarantee is given for the repair of piezo injectors, and a record of the repaired cars is kept. To date, more than two thousand injectors have been serviced for Trafic 2.0 only.
Cutaway piezoelectric nozzle:
1 - drain line; 2 - electrical connector; 3 - piezoelectric element; 4 - high pressure channel; 5 - hydraulic cylinder; 6 - coupled pistons; 7 - switching valve (multiplier); 8 - throttle plate; 9 - spray needle; 10 - nadigolny camera; 11 - outlet throttle.
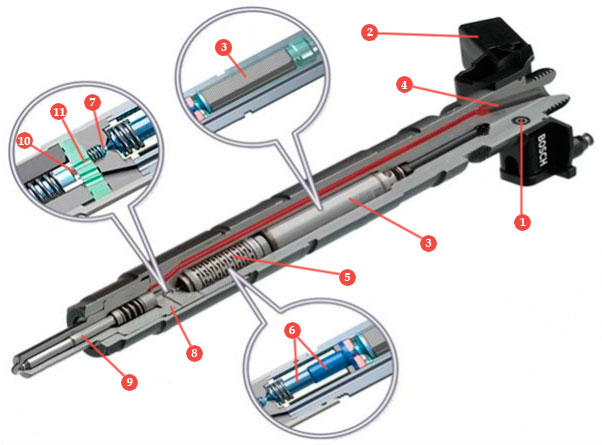
Now let's take a closer look at these nodes.
It is assembled piezo crystal (30-40 mm long), which consists of ceramic plates welded together. When an electric pulse is applied to it, it is capable of expanding in 0.1 ms
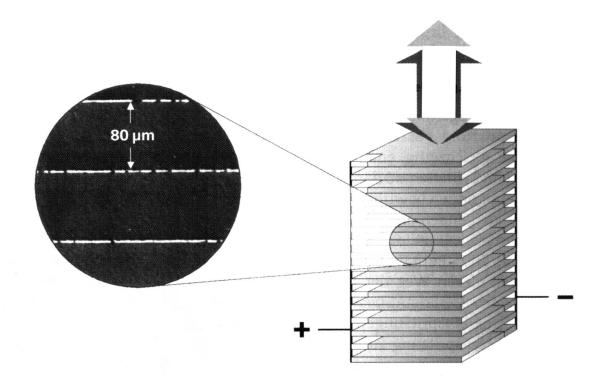
This is quite enough to act on the needle of the nozzle atomizer with a force of 6300 N. To increase the efficiency, palladium and zirconium are added to its structure. Interestingly, it consumes electricity only when voltage is applied. And when the electrical voltage is turned off, it regenerates this energy.
Frame hydraulic cylinder located inside the damping spring. There are two coupled (dependent on each other) pistons in the cylinder body.The space between them is filled with fuel, which, thanks to a valve in the drain line, is under pressure up to 10 bar. The fuel acts as a pressure shock absorber here. The hydraulic cylinder acts as an intermediary between the piezoelectric element and the switching valve.

Switching valve (multiplier) Is a valve that is a switch between the areas of low pressure (in the nozzle cavity around the hydraulic cylinder) and high pressure, which is located above the throttle plate and is connected to the cylinder chamber.
Spray slightly different from the classic version. But the principle of its operation is similar to the atomizer of an electromagnetic nozzle - high pressure fuel is pumped simultaneously from the upper and lower sides of the needle. This allows the nozzle to be kept closed.
Above the spray is located choke plate... It is equipped with holes through which the fuel flows between the high-pressure channel, the spray nozzle and the changeover valve chamber.
At rest, the spray needle, under the action of high pressure from both sides simultaneously, is in the closed position. When an electric pulse is applied to the piezoelectric element, it expands. The piezo crystal expands and pushes the elements of the hydraulic cylinder.
The hydraulic cylinder, in turn, acts on the changeover valve and opens the outlet throttle channel through which the pressurized fuel flows out of nadigolny cameras. In this case, the pressure above the needle drops, and the fuel in submissive chamber, which is under high pressure, raises the spray needle, and the injection is performed.
That's all. But the main trick is that this whole series of processes is happening at a very high speed. This is the main advantage of piezo injectors.
- response speed and frequency
- number of injections in one working cycle of the injector
- fuel dosage accuracy
- reduction of noisy engine operation
- operation of the nozzle at high pressures
- environmental friendliness
As mentioned above, the speed of the piezo injector makes it possible to divide the fuel supply into a large number of micro doses: first, several preparatory injections take place, then the main injection takes place, and after it the so-called post-injection.
Fuel injection occurs in such a way that a small amount of fuel enters the cylinder - pilot injection (about 1.5 ml). It enriches and warms up the fuel-air mixture, smoothly preparing the system for the main fuel supply. This achieves an even pressure distribution in the combustion chamber. The more such pre-injection, the softer the combustion proceeds, and, accordingly, the quieter the engine runs.
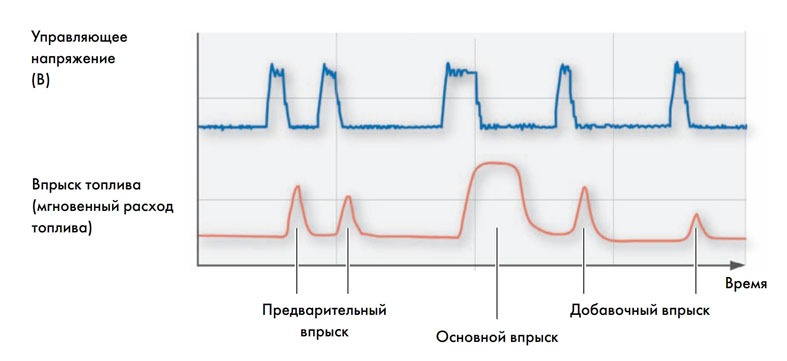
After that, a large dose of fuel is supplied, which plays the main role in creating the fuel-air mixture. At the end of the combustion cycle with post-injection residual fuel is burned out. This reduces the toxicity of the exhaust gases. Also, the fuel supplied in this way at the end of the injector cycle helps to clean and regenerate the particulate filter.
Thanks to the latest developments, it is possible to use up to seven injections per injector stroke. Due to this, new opportunities appear for increasing engine power, reducing its noise level and creating conditions for more accurate control of exhaust gases.
Today, manufacturers are developing common rail systems with operating pressures up to 2500 bar. The maximum pressure in such injectors is achieved not in the fuel rail, but in the injector itself. They are equipped with a small hydraulic pressure booster and two electromagnets for precise control of the torque and the amount of fuel supplied. This will increase the injection pressure and the efficiency of the fuel system.
We are looking forward to seeing these nozzles in our workshop ...
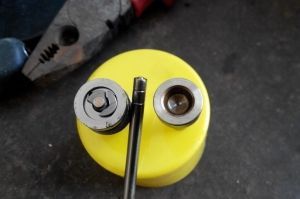
A breakdown can cause unpleasant consequences: a bluish exhaust, a tangible knock similar to that of a connecting rod, a loss of power - but somehow you can go. If the advanced nozzles fail, there is a chance not to leave the place where the unfortunate incident occurred.
DIY Common Rail injector repair seems very doubtful to many. The motorists unanimously assure that even disassembling it without special equipment leads to hopeless injury to the spare part. However, you need to know what is to be restored, at least theoretically, and what absolutely needs to be scrapped immediately.
Diesel engines with nozzles from Bosch, Delphi, Denso and a variety of Common rail the same Bosch company with a competitor in the person of Siemens (now it has a new name Continental) - Piezo. We will deal with each of the varieties separately.
Previously, they appeared only on cars from China and Japan, now they are used on individual Europeans, in particular, on Peugeot and Ford. Their attractiveness lies in their lower cost. They walk up to 150 thousand km, which is not a bad result at all. However, the disadvantage is that the manufacturer does not supply spare parts separately, only complete injectors. The part can only be restored in the hands of someone who has several nozzles and can assemble one workable one out of 2-3 broken ones. Again, the body, atomizer, and solenoid keep on track just like they do in Bosch or Delphi injectors. The stem and valve are worn out, in both cases only replacement will help.
![]() |
Video (click to play). |
Piezo injectors have 2 global disadvantages... The first is the price. For less than 16 thousand rubles, you will not find a part, and the average cost is considered to be 30-40 thousand. The second is low maintainability. Most crafters consider them not recoverable at all. And those who undertake the restoration warn about the temporary nature of the measures taken. Usually, people agree to repair a damaged nozzle only while waiting for a new one to be sent. Even if you are confident in yourself and decide to repair a Common Rail injector with your own hands, pay special attention to installing it back on board. Otherwise, you run the risk of finally ditching the repaired. Pumping fuel through the injection pump should be carried out up to the nozzles in order to remove all air bubbles.