In detail: do-it-yourself repair of a pneumohydraulic pump from a real master for the site my.housecope.com.
Pneumohydraulic pump AIST 67913325 (10t) pedal for slipway
Pneumohydraulic pump Nordberg N3P (10t) pedal for slipway (reservoir 1690ml)
Pneumohydraulic pump Nordberg N3P1 (10t) pedal for slipway (reservoir 690ml) NEW

Pneumohydraulic jacks are certainly very convenient and effective equipment for lifting large loads (20-50 tons) to a certain height. During the operation of equipment, especially experimental equipment, certain problems arise with it related to design features and internal structure - we will figure out how to fix them as quickly and efficiently as possible.
Pneumohydraulic jacks, despite widespread public opinion, are very simple - the main elements can literally be counted on the fingers of one hand.
- The body is made of high strength "stainless steel". It exhibits a kind of "duality": it is both a cylinder for a piston and a container for oil.
- The retractable piston (also called the "rod") is the second main part of pneumohydraulic jacks, the efficiency of the device directly depends on its condition.
- Well, the third "integral component" is the working fluid, in this case - oil.
The mechanism of operation of a pneumohydraulic jack is very simple: with the help of a pump (foot, hand or air drive), the oil is moved into the cylinder, where the valve moves - this is how the load rises. In simple words, these are just vessels communicating under high pressure.
![]() |
Video (click to play). |
We have already said that pneumohydraulic jacks, like any other specialized equipment, are not without drawbacks - only in the case of them, they are very easy to fix. In fact, the foremen call this kind of malfunction "working moments", now we will consider them in more detail.
You can solve the three listed problems with pneumohydraulic jacks yourself at home - this will require a little free time and a few of the simplest tools.
We will now list three main symptoms of malfunctions and tell you what each of them says. They can be seen with the naked eye, especially if you work with the jack frequently.
- Having raised the load to the required height, the device begins to lower it slowly, that is, in simple words, it cannot fix it. In most such cases, the cause of the malfunction should be looked for in the valve and cuffs.
- The reduced functionality of the device also manifests itself in the inability to lift the load to the height to which it could have been lifted before. In this case, it is necessary to clean the stem from dirt and possible corrosion, if it is bent (for example, a pneumohydraulic jack was used to lift unacceptable weights), then even replace it.
- If the device does not fully return to its original position (discrepancies, gaps are observed), this indicates that the springs are worn out - they will also need to be replaced.
From these "symptoms" you can easily tell when the air hydraulic jack needs repair. If the problem is corrected quickly, it is very unlikely that it will reoccur.
The decision to buy a pneumohydraulic jack is mainly taken by specialized workshops and service stations, because this is quite expensive equipment that requires special handling.However, advanced motorists also like to use really high-quality and convenient equipment, which means that owners of pneumohydraulic jacks meet among them.
Of all the problems we have listed, as a rule, you can solve everything at home - unscrew the fasteners, remove the valves, the piston, then drain the used oil and follow the prescribed instructions. If you cannot solve the problem on your own, then do not delay contacting a specialized workshop - the sooner you do this, the higher the likelihood of a "complete recovery" of the technique.
Do not skimp on your safety and comfort, use only proven products from well-known manufacturers!
Message # 1 Denis# »28 Jan 2016, 16:28
Hello everyone, I never thought about what and how is implemented inside a conventional hydraulic jack, but I just can't buy in St. Petersburg (!) A pneumohydraulic bottle for 50 tons. The epic is already a month. As I understand it, PNEUMATIC hydraulic is obtained from conventional hydraulic by adding air supply from the compressor.
How to organize it correctly? What needs to be piled and where to stick in order to press not only with a handle, but also with air? Who did the thread like that, are there pictures?
Thank you all in advance

Message # 2 vovasm »29 Jan 2016, 00:32
Message # 3 Denis# »29 Jan 2016, 01:25
And now it's the same, only for the dumb one

Today I saw a similar jack alive, it turns out that a certain cylinder is stuck to an ordinary jack, into which air is supplied from the compressor. As I understand it, this is a kind of pneumatic cylinder in which air is supplied from one side of the piston, and on the other side of the piston there is oil in the cylinder itself?
It turns out that I need to disassemble the pneumatic cylinder, instead of the rod, use a hydraulic hose for it and insert it into the jack somewhere. Moreover, it should be introduced so that it does not interfere with the manual plunger, and when the bypass valve is opened, the oil returns to the pneumatic cylinder.
How to do it?
Pneumohydraulic pump AIST 67913325 (10t) pedal for slipway
Pneumohydraulic pump Nordberg N3P (10t) pedal for slipway (reservoir 1690ml)
Pneumohydraulic pump Nordberg N3P1 (10t) pedal for slipway (reservoir 690ml) NEW

Published by admin in Auto 26.01.2018 0 281 Views
In order to increase physical efforts in the process of car repair, body repair hydraulics are used. To correct various dents and defects in places where it is impossible to use straightening hammers or other hand tools, a hydraulic set of stretch marks is used. Hydraulics help speed up the elimination process and can be used for straightening.
For bodywork, hydraulic equipment is used: pumps, lifting devices, cylinders, presses. Slipways for body straightening are completed with hydraulic power devices, pumps, cylinders.
A set containing stretchers on hydraulics is used to force impact on the composite structures of a car during body repair to correct various mechanical damages:
A set of stretch marks for straightening has a standard look and complete set:
- nozzles of various configurations;
- hydraulic pump;
- hydraulic cylinder;
- equipment such as grips and stops;
- extension cords.
If desired, this set can be increased by adding other parts and equipment. The set containing straightening braces is sold in a convenient special box, which makes it easy to transport and store. Stretch marks may include a pump.
The standard body repair kit usually does not have it, but this powerful tool allows you to significantly increase the tensile forces. The stretch marks themselves are divided according to the mechanism of action on the structure in this way:
- tensile equipment required, for example, to straighten a door arch;
- a tension tool (tie) that is used to tighten vehicle elements, such as a collision-damaged wing.
This equipment can carry out work on straightening the body, trunk, roof and hood of the car.
When carrying out such work, the equipment is capable of reaching an effort of 5 tons. Also, the equipment can be used for straightening various metal assemblies and parts, correcting distortions of vehicle elements, replacing thresholds.
When performing body repairs using a stretch, you must do the following.
- Step 1. A visual inspection is required to assess the degree of damage to the structure, the distance between the deformed areas, material and surface quality.
- Step 2. Take a set of guy wires and perform the assembly: connecting the hydraulic cylinder and the hose. Use an extension cord if necessary.
- Step 3. The assembled structure must be secured in a stable position so that it does not slip. To do this, use the appropriate attachments provided in the repair kit.
- Step 4. After installing the structure, press on the pump to firmly fix and stop the unit.
- Step 5. To straighten the element, use a pump to create forces that will straighten it.
If the part is badly damaged, the dressing procedure should be repeated. Stretching must be applied carefully so as not to further damage the car body.
To straighten the frame and body geometry, special equipment is used - a slipway. Stacking is the most difficult and time-consuming process in the field of car repair. With the help of the slipway, both minor damage and rather complex ones associated with the restoration of the body geometry are corrected. Not a single auto repair shop and service station can do without a slipway. Many car enthusiasts have in their garage a homemade slipway for body repair.
The construction of the slipway for car repair has a pneumohydraulic pump. This tool is used not only during the work of the slipway, but also with other garage tools: presses, stretch marks, etc. The design features of the pneumohydraulic pump ensure its advantages during operation:
- high productivity;
- lightness and ease of use;
- simple mechanism for checking and replenishing the oil level;
- a fuse protects the tool against overload during operation.
Many models are equipped with mufflers that provide a low-noise operation of the mechanism. The use of a pneumohydraulic pump in body repairs greatly speeds up and facilitates the process.
A tool that is indispensable when carrying out repair work in the garage and on the road - a jack. It is used in cases when it is necessary to raise the car during repairs. The jack is indispensable as a luggage tool, without which it is impossible to replace a wheel in case of a puncture on the road. When choosing a jack, you should pay attention to its main characteristics.
- Lifting capacity - shows the maximum weight that this equipment can lift. Buy a jack based on the weight of your vehicle.
- Lift height - the distance between the support and the pick-up at the maximum stem exit.
- The dimensions and weight of the unit matter, as it will have to be carried in the trunk.
Increasingly, a pneumohydraulic jack is used for work in the garage associated with straightening vehicle elements. This is a hybrid unit in which pneumatic and hydraulic mechanisms are connected. These jacks lift the load by supplying a special oil, which is pumped into the system using air.
This type of lifting device is designed for stationary use. A pneumohydraulic jack allows you to eliminate some of the disadvantages of hydraulic devices - slowness and high pickup height.The advantages of such units also include:
- high carrying capacity;
- little effort;
- can be used on any soil (uneven, loose, etc.);
- ease of use.
In order not to get injured when working with the jack, do not damage your car or break the tool itself, follow simple rules.
- First of all, read the instructions for use of the air hydraulic jack.
- Before each use of the unit, check for oil leaks, damaged or loose parts.
- Bleed air from the hydraulic system before starting work.
- Do not use the unit to move the vehicle.
- Do not exceed the carrying capacity.
- Do not use the jack as the only support.
- When replacing parts, it is advisable to use original spare parts.
Following these recommendations will ensure your safety during repair work and will increase the duration of use of the lifting equipment.
Rating of the most stolen cars. A list was drawn up by Russian automotive experts.
Reliable alarm? 4 ways to steal your car quickly and with impunity
Submersible pumps have to work in difficult conditions. They are constantly exposed to water, vibration, low temperature, abrasive particles, etc. But despite the fact that the units are made from parts with a large margin of safety, various malfunctions appear in them over time. To repair water pumps with your own hands, you need to familiarize yourself with the main symptoms that indicate certain breakdowns in the equipment.
If malfunctions are noticed in the operation of a submersible pump, then it does not always need to be removed from the well for inspection. This recommendation only applies to pumping stations where pressure switch installed... It is because of him that the device may not turn on, not turn off or create a poor water pressure. Therefore, first the operability of the pressure sensor is checked, and only after that, if necessary, the pump is removed from the well.
Important! In the case of submersible pumps that operate without accumulators, they should always be removed from the mine at the slightest sign of failure.
It will be easier to diagnose water pump malfunctions if you first familiarize yourself with the most common failures of this unit.
The reasons that the pump does not work may be the following.
- Electrical protection tripped... In this case, disconnect the machine from the mains and turn the machine back on. If it knocks out again, then the problem should not be looked for in the pumping equipment. But with the normal switching on of the machine, do not plug the pump into the network anymore, you must first find the reason why the protection worked.
- Blown fuses... If, after replacing, they burn out again, then you need to look for the cause in the power cable of the unit or in the place where it is connected to the mains.
- Cable damage has occurredunder water. Remove the device and check the cord.
- Dry-running protection of the pump has tripped”. Before starting the machine, make sure it is immersed in liquid to the required depth.
Also, the reason that the device does not turn on may lie in the improper operation of the pressure switch installed in the pumping station. It is necessary to adjust the starting pressure of the pump motor.
There can also be several reasons that the device does not pump water.
- Shut-off valve closed... Turn off the device and slowly open the tap. In the future, you should not start the pumping equipment with a closed valve, otherwise it will fail.
- The water level in the well has dropped below the pump... It is necessary to calculate the dynamic water level and immerse the device to the required depth.
- Stuck check valve... In this case, it is required to disassemble the valve and clean it, if necessary replace it with a new one.
- Clogged intake filter... To clean the filter, the hydraulic machine is removed and the filter mesh is cleaned and washed.
Also, the decrease in performance causes:
- partial clogging of valves and gates installed in the water supply system;
- partially clogged riser pipe of the apparatus;
- depressurization of the pipeline;
- incorrect adjustment of the pressure switch (applies to pumping stations).
This problem occurs if the submersible pump works in tandem with a hydraulic accumulator... In this case, frequent starts and stops of the unit can be provoked by the following factors:
- the pressure in the hydraulic tank has dropped below the minimum (by default it should be 1.5 bar);
- there was a rupture of the rubber bulb or diaphragm in the tank;
- the pressure switch is not working properly.
If you notice that the water from the tap does not flow in a constant stream, then this is a sign of a decrease in the water level in the well below the dynamic... It is necessary to lower the pump deeper if the distance to the bottom of the shaft allows this.
If the pump is humming, and water is not pumped out of the well, then there may be several reasons:
- there was a "sticking" of the impeller of the apparatus with its body due to long-term storage of the apparatus without water;
- defective motor start capacitor;
- the voltage in the network sank;
- the impeller of the pump is stuck due to dirt collected in the housing of the apparatus.
If the automation does not work, the pump will work without stopping, even if excessive pressure is created in the hydraulic tank (seen from the pressure gauge readings). It's all the fault pressure switchout of order or incorrectly adjusted.
During the operation of pumps from different manufacturers, it was noticed that some brands of devices are often subject to the same breakdowns. It follows from this that these models of units have their own distinctive features in terms of the occurrence of malfunctions.
Pumps "Aquarius" have overheating predisposition, especially if they work in shallow wells. If a cheap model breaks down, its repair costs about 50% of the cost of a new device. If the device is out of order, it is easier to throw it away than to repair it.
Most of the models of this manufacturer have valve system... There is also a special thermal insulation around the engine. Sometimes pump malfunctions occur due to the failure of the listed parts. Since the thermal insulator is located around the engine, it will need to be removed from the housing for repairs.
Devices "Malysh" are products of domestic manufacturers. The cost of repairing units of this brand is not high, and the owners of the devices eliminate most of the breakdowns with their own hands. The main failure often encountered in this pump is loud noise when operating the hydraulic machine without pumping out the liquid. This behavior of the apparatus means that there has been a rupture of the central axis holding the armature and the membrane.
The engine in pumps of vortex and rotary type "Dzhileks" is oil-filled. Therefore, a frequent breakdown of these units is leaking oil from the engine... It can only be refilled at a service center.
Important! Many on the Internet advise using transformer oil or ordinary glycerin instead of the original oil filler. Doing this is highly discouraged, of course, unless you have set yourself a goal to spoil the technique in an unusual way.
There is an opinion that the operation of the trickle drainage pumps can continue without interruption for 7 hours or more. This is explained by the peculiarity of their design, which meets all European standards. But despite this, the apparatus exposed to overheating as well as pumps from other manufacturers. Therefore, it is recommended to give it time to “rest” after every 2-3 hours of operation.
Owners of the pump for the "Markus" well sometimes notice that the device turns on only after a slight blow either on the pipe going to it, or after hitting the hydraulic machine itself. This malfunction is explained by “souring "impeller, which will have to be cleaned by disassembling the unit.
In the event of pump breakdowns requiring replacement of parts located inside its housing, disassembly of the unit will be required. The submersible pump consists of a compartment for the engine and a compartment with one or more impellers, the purpose of which is to capture water... Below is a diagram of the device of that part of the centrifugal pump where the impellers are installed.
As you can see from the figure, the impellers are mounted on the unit shaft. The more there are, the higher the pressure generated by the pump. In the second compartment of the hydraulic machine is located rotary engine. It is located in a sealed case, and in order to open it, you need to know some of the nuances.
So, to go from theory to practice and disassemble the pump, follow these steps (depending on the manufacturer, the design of the unit may differ).
-
Unscrew the 2 screws holding the mesh of the device.
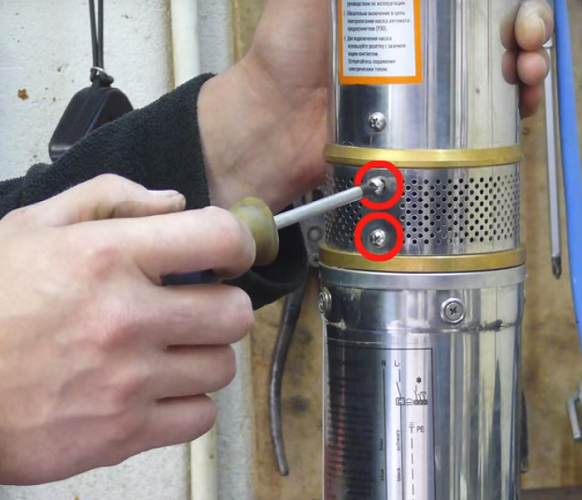
![]() |
Video (click to play). |
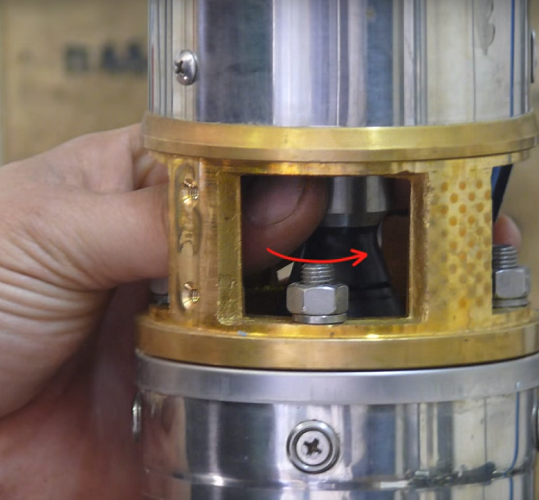
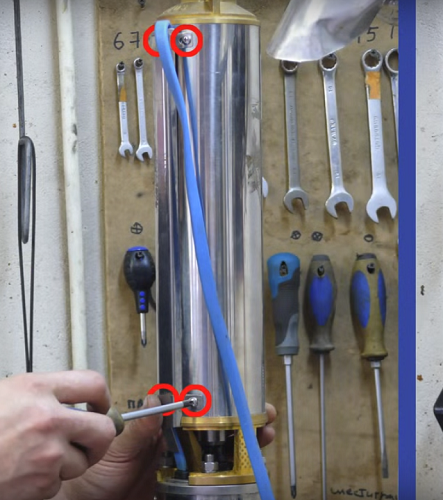
Next, unscrew the 4 nuts holding the pump flange.
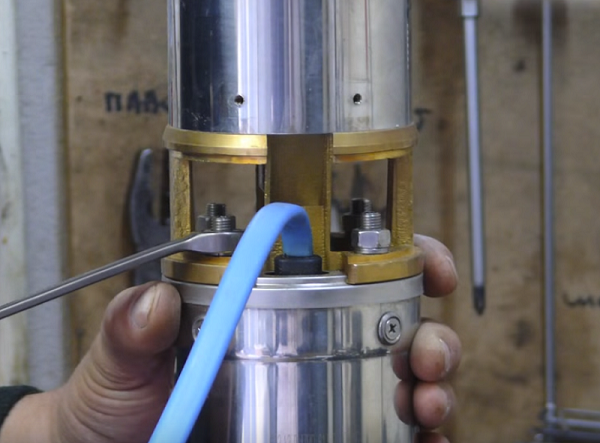
Now that you know how the hydraulic machine is disassembled, you can try to repair the submersible pump with your own hands.
Mostly impeller blocking occurs due to clogging them with sand or dirt deposits on them. In addition, the impellers can be soldered together when a high temperature occurs in the unit, when the pump is idling (dry running). To repair this section of the unit, it is necessary to remove the impeller (s) and remove the accumulated dirt. If the impellers are damaged, they will need to be replaced with new ones.
It is not recommended to repair the pump motor on your own, since it requires special knowledge and the necessary equipment to diagnose this unit and subsequent repairs.
On some pump models, removing the motor will require pressing it out using special equipment. Replacing the oil seal and bearing also carried out at the service center.
If engine hums and won't startthen the capacitor should be checked. It is located in the pump block in which the motor is mounted.
But when the shaft with the impellers rotates without problems, then in order to remove the hum in the water pump, you should disconnect the condenser and replace it with a new one. Better of course check this part with a multimeter, since similar symptoms can be caused by a short circuit in the motor windings.
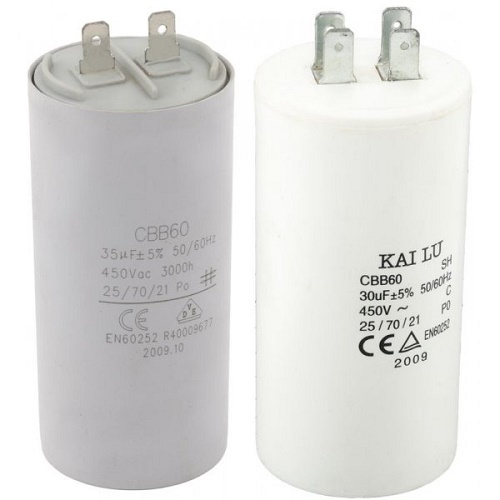
The water pump motor is located in a special glass filled with oil, and by its condition it is possible to determine some breakdowns in the electric motor block.
- The oil has a characteristic, unpleasant odor... This means that the engine is still in working order, but it has been working with great overloads.
- Turbid oil - water has entered the engine housing due to a crack in the housing or failure of the oil seal (cuff).
- Black oil with an unpleasant odor... In this case, we can say with great confidence that the varnish burned on the engine coils.
Important! Normally, the oil should be clear. Its quantity is determined by the unit model. On average, the volume of oil poured into the chamber is at the level of 0.5 liters.
If, when opening the engine, the above changes in the quality of oil were noticed, then first you need to repair this unit, and only after that fill in new grease.
Everyone knows what is dissolved in water some gas... When a liquid moves at a certain speed, rarefaction zones are sometimes formed in it. In these zones of reduced pressure, gas bubbles begin to emerge from the water. After the bubbles hit the high-pressure zone, they collapse. This process occurs with the release of a large amount of energy, from which the impellers and the pump volute are destroyed. The next photo shows the unit impeller destroyed by cavitation.
The energy of the collapsing bubbles is capable of creating shock wavescausing vibration. It spreads throughout the entire unit and affects not only the impeller, but also the bearings, shaft and seals, from which these parts quickly become unusable.
The cavitation effect can most often be observed in pumping stations that work for suction.... In such systems, the impeller creates a vacuum, due to which water rises through the hose from the well. But if there is a lack of liquid at the pump inlet, then an excessive vacuum occurs in the impeller zone, provoking cavitation.
Important! The most obvious signs of cavitation are vibration of pipes and the pump itself, as well as increased noise during its operation. If you do not take any measures to eliminate this process, then it can completely destroy the station.
To prevent cavitation in the pumps, you should adhere to the rule: there must be more water at the inlet than at the outlet. This can be achieved in several ways:
- move the device a little closer to the source;
- the diameter of the suction pipe (hose) can be increased;
- to reduce the resistance in the suction section, the suction pipe can be replaced with a pipe made of smoother material;
- if there are many turns on the suction pipe, then, if possible, their number should be reduced;
- it is desirable that all bends have large turning radii.
The drainage pump in a suburban area is a kind of magic wand in case of unforeseen situations. By design, it resembles equipment for the supply of drinking water, but it has the ability to move contaminated media with large inclusions.
Let's try to understand the weaknesses of the unit and find out if it is possible to repair the drain pump with our own hands, if necessary.
The ability to pump water with fine gravel, large inclusions of sand, organic debris is a very useful quality when you need to pump out water after flooding or drain a pond. Drainage units are designed to work in such conditions, but exceeding the load often leads to breakdowns.
It is better to get acquainted with the internal filling of the device immediately after purchase in order to imagine which parts may fail in case of clogging or breakdown. To do this, it is not necessary to open the case or disassemble - it is enough to study the diagram that is attached to the instructions for connecting and maintaining the device.
Apparatuses for private use in summer cottages do not differ in high power or complex filling. Unlike heavy industrial equipment, they are compact, relatively light (average weight - 3-7 kg), consist of steel or plastic parts, although cast iron is still used for the production of industrial models and some household ones.
The main components of the submersible mechanism are a pump unit that pumps water and an electric motor that rotates a shaft with blades. The motor is housed inside a robust casing, which is made of stainless steel or reinforced polypropylene and is double. Water circulates between the outer and inner walls, preventing cooling.
Modern models are equipped with thermal protection that is triggered when the device is overloaded. An impeller is attached to the axial shaft - a screw device that supplies liquid to the inside of the housing.When the unit is turned on, the impeller begins to rotate, pick up water from the outside and push it along the walls to the outlet. The first portion of water is replaced by the next - and so on until the mechanism stops.
The float switch regulates the frequency of operation. It monitors the level of liquid in a reservoir or natural reservoir, when it drops sharply, it turns off the device in automatic mode.
As you can see, the device of the drainage pump is quite simple, and if you have ever disassembled and cleaned a submersible well pump, then you can handle this category of equipment as well. The faecal aggregate, which has an additional unit for crushing too large particles, is slightly different.
The submersible is useful for cleaning deep tanks, for example, a well that has just been commissioned. The first liquid that has accumulated in it cannot be called drinking, since there are many large inclusions of sand and clay. During the day, it is necessary to pump out the contaminated liquid so that clean, usable water comes in its place.
Unlike a submersible pump, a surface pump is not used for deep tanks; it is more suitable for pumping water from a pool or basement when it is flooded. A hose for receiving dirty water is placed at the bottom of the container, the second hose is used to drain the drains.
If the pump is used in an emergency, it is appropriate to use a float device that will control the critical level of water rise. The plus is that the design of the mechanism allows you to pump liquid with large pieces of dirt - up to 5 cm (less often - 10 cm).
It is clear that the surface type aggregate differs in its structure. A working shaft and a wheel are fixed inside the metal case, and the motor can be different: for centrifugal products - single-phase with external ventilation, for self-priming products - asynchronous two-pole.
Despite the contamination of the pumping medium, do not allow the pump to operate with a liquid in which gasoline, kerosene or other oil products and chemicals are dissolved.
Both new equipment and those that have served for more than one year can break down. A newly purchased device may fail due to a manufacturing defect made during assembly: a damaged piston or an incorrectly connected valve. Often breakdowns occur due to inept installation, if:
- lowered the unit to an insufficient depth;
- allowed air to enter the water intake compartment;
- the water inlet is above the water and is not covered with liquid.
These flaws are easy to fix with a simple check, but it is better not to allow them.
Most often, problems arise during the operation of the equipment. The manufacturer sets the control parameters within which it is necessary to act (they are declared in the technical passport of the product). If the equipment is used incorrectly, not for its intended purpose, it simply will not withstand the load.
For example, it is normal for a drainage device to pump dirty water. This means that problems can arise if you start moving clean drinking water (for which borehole and well models are designed). On the contrary, too coarse dirt clogs the filters, as a result of which the pump stops working.
Also, troubles await if the equipment is idle, in "dry" mode - overheating will surely happen, which cannot always be corrected on your own. As a result of an oversight, the matter can end up in expensive service repairs.
Lack of prevention, rare technical inspections can also cause breakdown. Many troubles can be avoided by preventing them by replacing one of the parts or by elementary cleaning.
There are a number of possibilities to repair the equipment with your own hands, provided that the broken part can be replaced with a new one or a simple technical procedure (for example, cleaning) can be performed. To do this, you will have to disassemble the case, make diagnostics, identify the problem and select an identical part.
Available actions include replacing a capacitor, impeller or float, repairing an electrical cable, fixing a shock absorber, removing large pieces of clay and sand stuck inside the housing.
If the cast-iron body is cracked, the valve is out of order, or the winding has stopped functioning, you should contact the service center or think about buying a new pump. Inexpensive Chinese-made drainage devices are inexpensive, so ordering serious professional repairs is impractical.
The flexible element - the cable - is always at risk, since due to regular twists and kinks (which often happens during transportation and reinstallation of equipment), the wires under the layer of plastic or rubberized protection break, as a result of which the pump power is cut off.
It is necessary to find the break point and make the connection. This operation is easy to carry out if a break occurs near the plug - you just need to strip and connect the wires, finally carefully insulating the place of work.
A broken cable in the area where the pump is connected will take longer to repair. First you need to remove the equipment from the water, wipe and dry it, then disassemble it to get to the internal connection block. Get ready for the fact that instead of hexagonal holes you will encounter triple ones, which will make it difficult to select a screwdriver.
The cover should be removed carefully, without jerking or force. By unscrewing the bolts holding the tension member, you will be able to see the cable and identify the area of the break. We remove the worn-out piece, mount the cable in its original place, fasten the tensioning element, fix the bolts.
The engine is working properly, but the fluid has either stopped flowing altogether, or comes in in small, uneven jerks. There may be several reasons for the strange phenomenon:
- Part of the supply line is clogged. This is a branch pipe or supply pipe. There is a kind of blockage from bundles of algae and pieces of clay. It is necessary to disconnect the pipes and clean them. It is possible that the pipe length is longer than the manufacturer's recommended length, and therefore there is not enough pressure to deliver the required power.
- The impeller is worn out. Blades are bent or damaged. It is necessary to disassemble the device, replace parts, to begin with visually (as far as possible) determining the cause of the malfunction.
- The fluid is saturated with dirt and debris. Therefore, the water has a thick consistency and is difficult to pump. We solve the problem by raising the suction hole a certain distance from the bottom, where sediment accumulates.
- Engine power has noticeably decreased. That can be determined even by the sound. Possible malfunctions in the supply of electricity, failure of bearings, depressurization of the oil compartment. It is necessary to disassemble the case to clarify the cause of the breakdown and replace worn parts.
The most common problem is filter clogging. You can try running some clean water through the pump to clean the sieve and suction port. If this procedure does not help, disassemble the case and clean all chambers, removing pebbles, algae and chips.
When disassembling the unit, be sure to follow the manufacturer's diagrams or instructions. They will help to consistently remove parts, quickly find bolt attachment points. In some cases, wear on fasteners or loose nuts will cause parts to move, which will also affect the performance of the machine.
You connect the power supply - and the pump does not work, does not make noise and does not pump water. Prepare to inspect all equipment.The most common causes of engine failure are:
- Disruption to the electricity supply due to broken wires. We check the cable by touch and find the break point. If the emergency area is in the area of connection to the pump, proceed as described above.
- The stator winding is out of order. Happens due to dry running. If you cannot replace it yourself, contact a specialist.
- Seized bearing... We check the part for suitability, according to the results of diagnostics, we clean or replace it.
- The suction device is clogged with debris. We clean the blades and grate, check the integrity of the operating elements and the mesh.
- The float switch has broken. To check its performance, you need to close the relay. The problem may be in the wire connecting the float to the pump.
If the capacitor is out of order, replacement is required. In some models, special access is provided to it, which is a separate hole in the case.
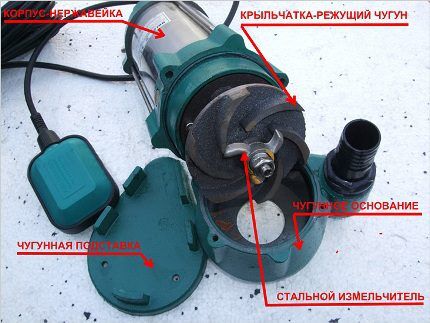
When the pump is switched on to the network, it starts to work, however, after a while, it stops spontaneously. Most likely, a protective mechanism is triggered due to engine overheating.
A heating cable may be the cause. It is worth checking the correspondence of the mains voltage and the parameters set by the manufacturer. If the data does not match, you need to purchase a stabilizer.
Shutdown can also occur due to clogging of the blades with debris. In this case, we recommend that you carry out a complete cleaning procedure, that is, open the housing, clean the inner chambers and impeller, and check the filter.
If blockages occur frequently, re-read the instructions for the product to determine the size of the fractions. Perhaps the pump is not designed for pumping liquid with large particles of debris - only a fecal pump is suitable for grinding
When the pump is turned on, plugs fly out or wires burn out. The reason should be sought in the details directly responsible for the wiring of electricity - the cable or the stator winding. The serviceability of the wires can be checked using a tester; if a worn-out area is found, the entire cable should be replaced or (if the gap is near the end) shorten it.
Winding repair is a laborious task and requires special knowledge. Even with a neatly drawn secondary winding, a short circuit cannot be ruled out. If you have no time to fiddle with a burned-out part, take the device to a service center - perhaps, after diagnostics, they will advise you to buy a new pump.
As you can see, the cause of wear of parts can be both inevitable wear and a violation of the rules for operating the equipment. To make the device last longer, try to follow the manufacturer's recommendations. For example, position the body so that the suction device is at a certain distance from the base of the tank and does not pick up coarse particles.
At least once a year, check the integrity of the cable and internal parts by disassembling the case as much as possible. Perform preventive cleaning, which will increase the life of the parts by several times. Do not confuse a drainage device with a faecal one - it does not have a special grinder and cannot cope with the movement of large inclusions.
Videos from craftsmen will help you properly organize the disassembly of pumps of various brands and troubleshoot yourself.
Overheating of the stator due to violation of the interval operation mode:
Features of Pedrollo pump repair:
How to Repair the Whirlwind Sump Pump:
Dismantling the Praktika DNG-400 pump:
Do-it-yourself repair of the drain pump is quite possible and desirable if it is enough to clean it or change a spare part to fix it. Difficult accidents - rupture of a housing or a rotating shaft - cannot be repaired by yourself. Elimination of serious problems must be entrusted to specialists, and if replacement is impractical, then buy a new pump.