In detail: do-it-yourself Tuareg pneumatic compressor repair from a real master for the site my.housecope.com.
Perhaps, many motorists, and just those who are simply interested, know all the advantages of the air suspension of the Volkswagen Tuareg car. But, in addition to these pluses, there are also minuses, this is natural. The disadvantages, of course, include the problem of leaking air bellows. Unfortunately, this sometimes happens, albeit on high runs. Fortunately, the factory supplies special repair kits with which this problem is solved.
Usually, the problem starts to manifest itself gradually. After a long parking (several days) - You may find that the car has dropped on one wheel. Or on one axis, thus forming an unnatural roll. After you start the engine, the level of the body will be leveled and everything will work normally, until you leave the car again for a long time. If the situation repeats, then there is an air leak from the system. The tightness is lost. We strongly recommend not to delay contacting the service as soon as you notice similar symptoms. This is due to the fact that in the absence of tightness, oxidative processes inside the air spring can intensify, the amount of condensate can increase, which will further enhance corrosion. Moisture will accumulate in the places where the rubber seals and the aluminum frame of the rack mate. In these places, violation of the working surface is not permissible. If oxides and corrosion appear on the working surface, a repair kit consisting of rubber seals and ensuring proper tightness will not perform its functions. Tuareg air suspension repair
![]() |
Video (click to play). |
If the leak persists even after replacing the repair kit, the only way to solve the problem is to replace the air spring. That is why it is not worth delaying the repair, because you can do just by replacing the "rubber bands". For clarity, we post a photo and a couple of drawings of the air suspension device.
What parts the air strut consists of - you can see in this diagram: Tuareg air suspension repair
On the left parts of the picture (parts that we are changing are highlighted in bold): Tuareg air suspension repair
1 - Bushing
2 - the Bolt
3 - the Cover
4 - Nut
5 - Support
6 - the Valve for maintaining pressure
7 - a pneumocylinder of a suspension
8 - Latch preventing pulling off (must be replaced)
9 - Cover
10 - the O-ring
11 - Lip seal (to be replaced)
12 - Shock absorber air suspension repair Tuareg
On the right parts of the figure (also, the replaceable is highlighted):
1 - Support
2 - the O-ring (it is obligatory to replace)
3 - the Valve for maintaining pressure
4 - the Cover
5 - the outer guide
6 - Cover in the form of a sleeve element
7 - the Piston
8 - Cover
9 - Latch preventing pulling off (must be replaced)
10 - the O-ring (it is obligatory to replace)
11 - the Shock absorber
As you already understood, the repair kit consists of 2x supports, 2x clamps (preventing pulling off), 2x O-rings and 2x lip seals. In order to change this entire kit, you need to do the following:
- Remove both front wheels
- For right-hand pneumatic strut of diesel vehicles
- Remove the fuel filter above the pneumatic strut - Disconnect the shock absorber control cables
- Unscrew the upper struts fastening nuts to the body
- Remove air from pneumatic struts
- Unscrew and disconnect the rod of the body position sensor
- Unscrew the air line from each air strut
- Unscrew the ball of each upper arm from the steering knuckle
- Unscrew the stabilizer struts at the point of attachment to the stabilizer
- Remove the brake pipe mount from the steering knuckle
- Unscrew the steering knuckles from the lower arms
- Remove the air suspension strut
- Disassemble the pneumatic struts using a special tool
- Replace O-rings and bearings
- Assemble the air struts and check the tightness by applying a small amount of air to the cylinders using a soap solution
- Assembly is carried out in reverse order, taking into account the requirements of the manufacturer.
Below you can see other photos of the repair process: Tuareg air suspension repair




Reason: Multiple registration Nth time





IMHO, all rubber bands, gaskets must be changed, not only on the compressor, but for all types of work.
Added after 40 seconds
Bolts optional.
Reason: Multiple registration Nth time
IMHO, all rubber bands, gaskets must be changed, not only on the compressor, but for all types of work.
Added after 40 seconds
Bolts optional.





There may be a leak in the check valve in the dryer housing due to moisture.
Added after 1 hour 2 minutes 25 seconds
With the permission of the author of the topic, I will insert my five cents into a sore problem.
With the onset of winter (well, of course, high humidity), problems began with the compressor (error on the pressure sensor, well, in general, like everyone else). Inspired by the successes of his comrades from the forum, he bought one of the repair kit options on Avito, namely a Chinese head and a ring.
After removing the compressor, I was very surprised not to find critical seizures on the mirror of the original head. Well, okay, maybe general wear and tear, I thought, and assembled the compressor. The car in the garage jumped briskly from sport to extra leveled, and my joy had no limit, but. the next day I saw a familiar inscription.

Having gained time and energy, I decided to get to the bottom of this problem and also share with my comrades

We completely disassemble for parts:
We pay close attention to the check valve:
I suspect many further, assessing the condition of the rubber bands and springs, collect everything back. But in vain.
We remove the plastic sleeve, and there.
And there are two rubber rings that seal nothing at all!
It should probably be recalled that the released air goes through the dehumidifier (carrying moisture along with it), bringing it to its original state (the regeneration process takes place), and so in the absence of compaction, the air will bypass the dehumidifier through a leak and the poor fellow only accumulates moisture without drying anything.
As a result, the pressure relief valve rusts and fails:
Added after 42 minutes 25 seconds
Since it would not have been possible to find such rings quickly, I went the beaten path to Avito, and was surprised to find a new (.) Dehumidifier body there for a song, but without the dehumidifier itself.
After examining his desiccant, he saw that he was covered in water and rusty:
This silica gel is no longer good for anything, even keep it in the oven for a month

Such a weighty thing

We open the cartridge and rejoice at the stocks of silica gel (for 10 of our cartridges, there will be enough for sure!):
Next, we proceed to the electrical part, clean and polish the collector:
When disassembling the compressor, I found another common jamb, the insulation of the wires at the entrance to the case burst, wrapped the latsar with tape and filled it with sealant:
When assembling the compressor, I drew attention to one more subtlety, the air supply tube is also connected with a quick-detachable connection, in which there is a rubber ring.I assembled the compressor and blew it into the air supply hose. Well, in general, there was a siphon from there, Mom, don't worry, and I went to look for the ring. I traveled around all the shops, I didn't find a nifiga, and by chance my eyes fell on the old rings of the fuel injectors (the old ring on the right):
Put the ring on and voila! Nothing siphon anywhere, everything is hermetically sealed!
Unit ready for installation:
Epilogue: happiness is in the little things, only with completely serviceable components will the compressor delight you with flawless operation. Even because of one ring or the slightest leak, it will swing and swing, causing increased wear of the elements of the piston group and accumulating moisture in the desiccant, which ultimately will completely disable it.
So my conclusion: still, a complete repair kit is preferable, we eliminate all possible and impossible problems with the dryer, valves and fittings (in the end, the price is approximately the same).
No offense to those who sell only heads: I don't know about the author of the topic, but characteristic scratches appeared on my head, which indirectly speaks of the quality of these products, I gave the original head to the sleeve (they will put a sleeve with a ceramic coating), let's see which of it will come out.
First, let's figure out what the purpose of the air suspension is. This equipment will allow you to adjust the ride height in any situation on the road. When the desired mode is selected from four possible on both sides of the car, the height is constantly maintained, which is monitored by sensors. The main task of this equipment is to increase comfort and safety while driving.
The air suspension consists of the following elements: a compressor, a receiver, a switch-on and control relay, a repair kit, and so on. Proper care and timely troubleshooting will help you avoid troubles such as repairing or replacing parts. The compressor and the receiver are responsible for the supply of compressed air, the relay protects the pneumatic system from overheating, and the repair kit allows you to perform maintenance, diagnostics and repairs.
Air suspension height adjustment is carried out by pressing one button. Set the StraKen mode to travel on city roads and wait until the indicator on the panel stops flashing. This will mean that the clearance height has reached the desired value. It is also possible to activate the lifting mode of the car for changing tires or for pumping them up.
Under normal conditions, the compressed air is supplied from the receiver and the suspension is lifted in a few seconds. In the absence of air, the compressor takes over and performs its work a little slower. In order to avoid overheating, the device is equipped with a special turn-on relay.
You can choose one of the available air suspension modes:
- Lade is the minimum ride height. It is installed when the car is stationary or its speed is comparable to the speed of pedestrian movement. In this mode, it becomes necessary when you need to load or unload the trunk.
- StraKen is the standard level for driving on normal roads at speeds over 5 km / h. Switching occurs automatically. The clearance height can be higher or lower depending on the speed of movement. This mode will allow you to increase the stability of the car, its maneuverability and reduce aerodynamic resistance.
- Offroad is a mode with maximum clearance for off-road driving. In this case, the speed should not exceed 70 km / h, otherwise the level will automatically switch to StraKen. To prevent this from happening, it is better to install a speed limiter. The ground clearance will then maintain the optimum ride height for poor road travel.
- X'tra is a temporary mode that cannot be set for a long time. Designed for driving over obstacles or freeing the car from the ground. The speed does not exceed 20 km / h.When leaving an obstacle and increasing the speed, the mode switches automatically.
The Tuareg air suspension compressor is located in the front part of the body at the bottom of the right side of the car and is fixed to the bracket. Under normal operating conditions, there are no unnecessary rattling sounds. Automatic start-up at engine start activates the compressor. The compressed air is fed into a special cylinder, the so-called air receiver, which can be found in the trunk of your car. Together with it, there is usually a hose that allows you to pump up the wheels.
Stable and long-term operation of the compressor is ensured by the switching relay. Its main advantages include:
- small dimensions of the relay;
- reliability and durability of the product;
- the absence of a large number of current wires, which significantly increases safety.
It often happens that during the operation of a vehicle, you can hear a rumble from under the hood, uncharacteristic for the normal operation of the system. This indicates that the compressor needs repair or replacement.
Most air-suspended cars are equipped with a compressor that regulates the pressure in the wheels and provides them with pumping. After some time of operation, this equipment fails, which it informs the owner about through rattling. This signal indicates that the piston system is in a critical condition and the pump may stop working at any time. This, in turn, will lead to "deflation" of the tires and upsetting the car "on the belly." Naturally, there will be no question of further operation of the vehicle, and repairing the car will become a problem. After all, the minimum clearance of a deflated car will not make it possible to load it onto a tow truck. To avoid such troubles, carry out timely equipment diagnostics, use a repair kit to eliminate minor problems.
Every driver should be aware that an air suspension compressor cannot be a complete replacement for a conventional wheel pump. It cannot be used permanently for this purpose.
If you've heard the rumble under the hood of your Volkswagen Touareg, it's most likely the compressor. In this case, he needs a major overhaul, if possible, or a complete replacement. If the cylinder is not too worn out and the situation is not running, it will be enough to carry out repairs. Be prepared to replace all defective parts: guide bushings, seals, switching relays, and so on. For these purposes, you will definitely need a repair kit, without which repairs are impossible. You can cope with this on your own if you have the proper experience, or you can entrust the implementation to specialists, the cost of such a service will not hit your pocket hard.
Otherwise, when the compressor cannot be repaired and even the repair kit cannot help you, the compressor must be replaced. At the same time, keep in mind that the cost of a new part will cost you a round sum, so you can limit yourself to a used spare part. This will save you money by performing minor repairs and installing the product. A feature of this equipment is the need to replace the control relay when replacing the compressor itself.
When repairing or replacing the compressor, as well as regardless of its condition, the switching relay must be replaced every five years. After all, it is the failure of this element that most often leads to engine combustion.
If possible, replace the compressor with a more efficient one. This will avoid problems with overheating of the closing relay and, as a result, will increase the service life of the unit.
Do you still think that car diagnostics is difficult?
If you are reading these lines, then you have an interest in doing something yourself in the car and really savebecause you already know that:
- STO lomat big money for simple computer diagnostics
- To find out the error, you need to go to the specialists
- Simple wrenches work in the services, but you can't find a good specialist
And of course you are tired of throwing money away, and there is no question of driving around the service station all the time, then you need a simple ELM327 AUTOSSCANER that connects to any car and through a regular smartphone you will always find a problem, pay off CHECK and save a lot.
We have tested this scanner ourselves on different machines. and it showed excellent results, now we recommend it to EVERYONE! So that you do not fall for the Chinese counterfeit, we publish here a link to the official website of the AutoScanner.
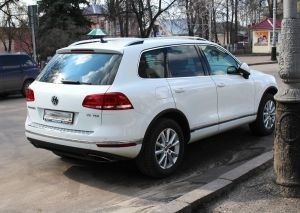
The car was released back in the early 2000s, during this period it experienced only one restyling, which indirectly indicates the perfection of the car.
In addition, this is a child of the German giant Volkswagen, it makes no sense to talk about its products, since one word "German" is enough and the quality is not discussed. It would seem that there is nothing to complain about the drivers of the Touareg? Yes, perhaps not for anything. It turns out that everything is far from the case, we will consider the sins of the concern below.
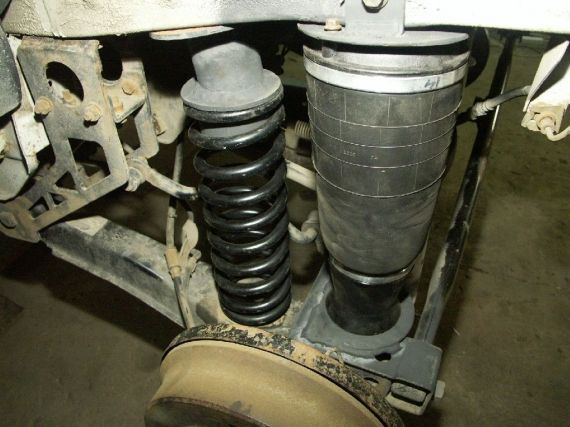
Therefore, those who were going to buy a car of this brand were warned about such diseases and recommended not to purchase a 2003 model year. Throwing a stain on the German in the running system of the pumping cylinder, due to the strong wear of the rubber seal. But even despite the repeated improvement of the mechanism, it was not possible to completely eradicate it.
Although in fact the suspension in the car is simply amazing, it inherited from the Volkswagen Phaeton, the truth was modified a little for its weight. Without leaving the salon, you can safely change the ground clearance from 160 to 300 mm. ground clearance. The ride is soft and smooth, like a ship on the waves. The suspension has three modes: standard, soft and hard.
- The start of the engine is marked by arbitrary lifting of the front or rear of the body;
- The back of the car drops when the engine is off;
- Systematic arbitrary change in ground clearance;
- Drawdown of one of the racks, no matter which one;
- The service mode in the electronic control unit blocks access to data on wheel alignment in the car.
Average service life of the pneumocylinder reaches 100,000 km. mileage, the figure may vary depending on the operating conditions of the vehicle. The next reason for failure is often a chemical reagent, which is sprinkled on roads in winter against icy conditions. It simply eats away at the rubber vacuum, causing air to leak over time.
Recently, would-be drivers have been using a compressor installed in a car to inflate tires, but it is actually intended by the manufacturer to inflate air into the suspension system. Frequent use leads to the fact that the fittings quickly wear out and begin to poison the air in the opposite direction. The car just lies on its belly, so much so that more than one tow truck will not crawl.
The ground clearance will be less than 5.0cm... in such situations, mobile jacks are used, with which the entire car is evenly lifted, wooden blocks are placed under the support points and the pneumatic system is replaced. There are simply no other options for resuscitation and delivery to a car service.
The way out of such an unfortunate situation is as follows: change the brains of the driver and read the operating instructions for the car, or very often change the fitting, working proactively.I don’t know which option each owner of such a legendary SUV will choose to repair the air suspension on the Volkswagen Touareg.
With proper maintenance and moderate driving style, the number of such problems can be reduced to a negligible minimum.
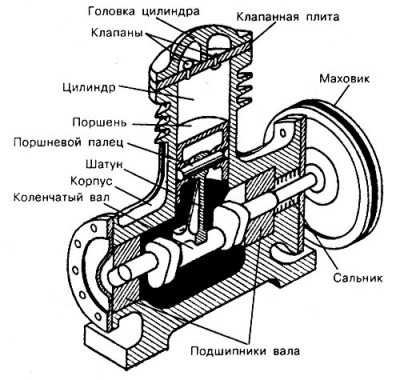
There are situations when the air compressor, peacefully rattling the engine in the corner of the garage, starts to malfunction, or even turns off altogether. And at this moment, as luck would have it, there is a need for it. Do not be afraid, after studying theoretical information, repairing a compressor with your own hands will not seem like something unattainable.
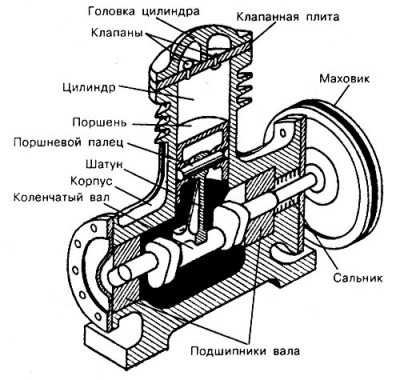
Compressors with a piston system electric motor have found the greatest application in car repair shops. In the supercharger crankcase, the transfer rod moves along the axis back and forth, giving the oscillatory moment to the reciprocating movement of the piston with O-rings. The bypass valve system located in the cylinder head works in such a way that when the piston moves downward, air is taken from the inlet pipe, and upward - it is returned to the outlet.
The gas flow is directed to the receiver, where it is compacted. Due to its design, the blower produces an uneven air stream. Which is not applicable to spray gun use. A kind of condenser (receiver) saves the situation, which smooths out the pressure pulsations, giving out a uniform flow at the outlet.
A more complex design of the compressor unit implies the attachment of additional equipment designed to provide automatic operation, dehumidification and humidification. And if in the case of a simple execution it is easy to localize a malfunction, then the complication of the equipment execution complicates the search. The following are the most common faults and remedies for the most common piston-type compressed gas systems.
To make it easier to find the problem, all defects can be classified by the nature of the malfunction:
- Compressor unit blower does not start
- Compressor motor hums but does not pump air or fills air reservoir too slowly
- At start-up, the thermal protection circuit breaker is triggered or the mains fuse is blown out.
- When the blower is turned off, the pressure in the compressed air tank drops
- Thermal protection circuit breaker periodically trips
- Exhaust air contains a lot of moisture
- Engine vibrates violently
- Compressor runs intermittently
- Air flow is consumed below normal
Let's consider all the causes of the problems and how to fix them.
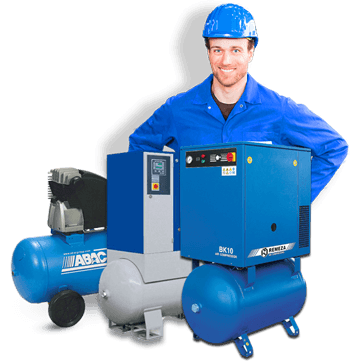
Failed ones are replaced by passive protection devices of the same rating as defective ones. In no case are hot melt inserts designed for a higher electric current allowed. If the fuse blows again, you should find out the cause of the failure - probably a short circuit at the input of the circuit.
The second reason why the unit does not start is that the pressure control relay in the receiver is faulty or the level settings are out of order. To check, gas is released from the cylinder and the supercharger is tested. If the engine is running, the relay is reset. Otherwise, the defective part is replaced.
Also, the engine will not start when the thermal overload circuit breaker is triggered. This device turns off the power supply circuit of the winding of the electrical device in case of overheating of the piston system, fraught with seizure of the motor. Let the blower cool down for at least 15 minutes. After this time has elapsed, restart it.
With an underestimated mains voltage, the electric motor does not master the scrolling of the axis, while it will hum. With this malfunction, first of all, we check the voltage level in the network using a multimeter (it must be at least 220 V).
If the voltage is normal, then the pressure in the receiver is probably too high, and the piston does not overpower the pushing of air. In this case, manufacturers recommend setting the “AUTO-OFF” automatic switch to the “OFF” position for 15 seconds and then moving it to the “AUTO” position. If this does not help, then the pressure control switch in the receiver is faulty or the bypass (check) valve is clogged.
You can try to eliminate the last drawback by removing the cylinder head and cleaning the channels. Replace the defective relay or send it to a specialized center for repair.
Compressor start-up is accompanied by blown fuse or activation of automatic thermal protection
This malfunction occurs if the installed fuse is below the recommended rated power or the supply network is overloaded. In the first case, we check the compliance of the permissible currents, in the second, we disconnect part of the consumers from the electric main.
A more serious cause of the malfunction is incorrect operation of the voltage relay or breakdown of the bypass valve. We bypass the relay contacts according to the scheme, if the engine is running, then the actuator is faulty. In this case, it is more advisable to contact an official service center for technical support or replace the relay yourself.
A drop in compressed air pressure indicates that there is a leak somewhere in the system. Risk areas are: high pressure air line, piston head check valve or receiver outlet cock. We check the entire pipeline with a soapy solution for air leaks. We wrap the detected defects with sealing tape.
The drain cock may leak if not properly closed or defective. If it is closed all the way, and the soapy solution is bubbling on the spout, then we change this part. When screwing in a new one, do not forget to wind up the fum tape on the thread.
In the case of tightness of the air line and the exhaust valve, we conclude that the compressor control valve is not working correctly. For further work, be sure to bleed all the compressed air from the receiver! Next, we continue to repair the compressor with our own hands, disassembling the cylinder head.
If there is dirt or mechanical damage to the bypass valve, we clean it and try to fix the defects. If the malfunction is not eliminated, then we replace the control valve.
This defect occurs when the power supply voltage is too low, the air flow is poor, or the room temperature is too high. We measure the voltage in the network using a multimeter; it must be at least the lower limit of the range recommended by the manufacturer.
Poor air flow into the discharge system is due to a clogged inlet filter. The filter should be replaced or washed according to the unit's maintenance manual.The piston engine is air-cooled and often overheats when in a poorly ventilated area. The problem is solved by moving the compressor unit to a room with good ventilation.
This situation occurs under the following conditions:
- Large accumulation of moisture in the receiver
- Air intake filter dirty
- The humidity in the room of the compressor unit is increased
Moisture in the output stream of compressed air is fought by the following methods:
- Drain excess fluid from the cylinder regularly
- Clean or replace the filter element
- Move the compressor unit to a room with drier air or install additional filter-moisture separators
In general, piston engines are prone to high vibration. But, if the previously relatively quiet compressor unit begins to rumble, there is a high probability that the engine mounting screws are loosened or the material of the vibration cushions is worn out. This malfunction is eliminated by pulling all fasteners in a circle and replacing the polymer vibration isolators.
Interruptions in the operation of the engine can be caused by incorrect operation of the pressure control switch or too intensive extraction of compressed air.
Excessive gas consumption occurs due to a discrepancy between the compressor capacity and the power consumption. Therefore, before buying a new pneumatic tool, carefully study its characteristics and air consumption per unit of time.
Consumers should not take more than 70% of the compressor capacity. If the power of the blower with a margin overlaps the requests of the pneumatic tools, then the pressure switch is faulty. We either repair it or replace it with a new one.
This malfunction occurs as a result of a gas leak in the high pressure system or a clogged air intake filter. Air leakage can be minimized by pulling all butt joints and wrapping them with sealing tape.
Sometimes it happens that when draining condensate from the receiver, they forget to completely close the drain valve, which also leads to a gas leak. This problem is easy to solve - by tightly closing the valve. If the dust filter is clogged, clean it or, even better, replace it with a new one.
Most of the above malfunctions can be avoided by correctly carrying out the first start-up and running-in of the mechanisms, as well as performing regular routine maintenance.
In order for the device to function properly for a long time, the recommended maintenance should be started at the initial stages of operation. Experts recommend the following actions from the date of purchase:
Timely observance of these simple requirements will keep the mechanism in good condition. Such a time-consuming procedure as repairing a compressor with your own hands will be required extremely rarely. Proper grounding will avoid problems with the electrical part of the device. Regular replacement of oil and cleaning filters will prevent premature wear of rubbing parts.
If your air suspension compressor flatly refuses to work and by a happy coincidence you have a few hours of free time, then I suggest you get out the dusty tools and give your compressor a new life. And now we will consider how to do this as quickly and efficiently as possible.
So, the defective compressor is lying on the table, you are already angry and tired (it is not so easy to remove the compressor from the car, especially without breaking anything), but still full of determination? Wonderful! Let's start then.
What we definitely need:
- Torx T30 key. I strongly recommend using a high-quality wrench with a good wrench - you can break a lot of poor-quality ones, but you still can't achieve the goal, because the bolts we need sit on thread glue and, moreover, often "sour"
- Slotted screwdriver
- Soap solution
- Rags or cotton wool
You may also need a drill, a thin drill (3-4 mm), side cutters, a file, a 10mm head and many other useful tools, depending on the condition of your compressor.
Before repairing the air suspension compressor, it is advisable to wash it well in order to prevent dirt from entering the pneumatic system, which can make all our work in vain. For washing, you can use soapy water and a stiff brush, such as an old toothbrush. It is highly undesirable to use a wire brush or pressure washer. It is also best to set organic solvents aside to avoid damaging the plastic and rubber parts of the pneumatic fittings.
Next, we begin to disassemble. The first step is to remove the cylinder assembly with the dryer block and dump valve. To do this, we are trying to unscrew the two T30 bolts that we mentioned earlier.
After the bolts are unscrewed, we remove the temperature sensor and put it aside. On some air suspension compressors, for example on the VW Touareg and Range Rover Vogue, in order to remove the temperature sensor, it is necessary to additionally unscrew the fixing bolt on the back of the cylinder. After that, we can remove the cylinder and look inside.
Inside we see a piston on which the piston ring is worn. The piston itself rotates on the connecting rod. We are interested in three things here.
The first is the ease of rotation of the rotor of the electric motor. To do this, we try, by pulling or pushing on the piston, to scroll it. The rotor should rotate easily and without biting. If it rotates heavily and unevenly, or does not rotate at all, then with a greater degree of probability we can say that the cause of the compressor malfunction was the melting of the rotor windings, which led to its sticking. In this case, we recommend replacing the compressor with a new one.
Next, we check the condition of the bearing on which the piston is rotating. It is checked by staggering the piston along the axis of rotation of the bearing. If the backlash is 1-2 mm in each direction, then everything is in order with the bearing, if the backlash is greater, then it is recommended to replace the bearing.
To replace it, it is necessary to drill out rivets on the end flange, remove it and unscrew the bolt securing the bearing. Note that the thread of this bolt is LEFT! Then it is necessary to remove the piston and bearing assembly. The bearing must be pressed out of the piston. To do this, you must use a specialized puller. DO NOT use a hammer, etc. to press out the bearing. The piston is aluminum and can crack easily. Then we carefully press in the new bearing.
The next thing we pay attention to is the cleanliness inside the cavity in which the piston moves. If there is a slight plaque on the inner walls, then we have nothing to worry about. To remove it, use a soapy solution. In extreme cases, weak organic solvents (such as gasoline) may be used, but under no circumstances should the solvent come into contact with the plastic and rubber parts of the compressor.
If we find a large amount of dirt (and this dirt is not a debris from the cylinder and piston ring), or, even worse, this dirt is oily, then everything is a little worse. The only way this dirt could get inside is the air supply lines. They must be carefully checked and, if necessary, repaired or replaced.
The last thing we are interested in is the state of the piston ring and cylinder walls. If we are going to install the air suspension compressor repair kit, then this item can be skipped. If we hope for a miracle (and miracles do happen), then it is necessary to carefully examine the cylinder walls for the absence of scratches and wear. Small scratches are allowed on the cylinder walls, which are not perceptible by touching with a finger.If the cylinder has deep scratches or grooves (especially deep in the cylinder where maximum compression should be achieved), the cylinder must be replaced. If the cylinder has no signs of wear, then we next check the condition of the piston ring.
If the cylinder does not have scratches, then most likely you will not find them on the piston ring either. Use a vernier caliper to check the condition of the ring. The ring width should be 4.75 mm. Wear up to 0.05 mm is allowed, and then it is recommended to replace it.
If during the check it turned out that the engine, cylinder and piston ring are in order, then either we disassembled the compressor in vain, or for its further verification we need a specialized stand where we can accurately determine the correct operation of the electric motor and the air discharge system, as well as the places of possible leaks air. To do this, we recommend that you contact a specialist (for example, us) or replace the compressor with a new one (in case you are sure that it is faulty).
If we do not replace the desiccant unit with a new one, then it is also recommended to recycle it. We will consider the features of the bulkhead of the dryer block in another article.
Compressor assembly is carried out in reverse order. All worn out and broken parts are replaced with new ones whenever possible. If the quick-release couplings were damaged during the repair, they must also be replaced! All pneumatic tubing must be fully inserted into the connections.
When installing the piston ring, pay attention to the correct installation. There is only one position on the piston in which it will work correctly.
![]() |
Video (click to play). |
Please also note that unnecessary details MUST NOT be left behind.