In detail: DIY guitar stand repair from a real master for my.housecope.com.
Musical instruments for beginners and intermediate
Tool selection. Availability in stores. Repair questions.
A year ago I bought a Madeira HC-09 guitar from you, in order to carry it on a hike. It is clear that it is not the most tenacious in this sense, but I liked the sound-price ratio.
As expected, recently, due to body deformations, the strings have begun to “lay down” on the neck. Such a situation was assumed even upon purchase - at the same time with the guitar I bought taller bones (to be honest, I am more accustomed to calling this thing a saddle) so that I could raise the strings. However, after replacing the saddle with a higher one (the highest one bought in the store), while pulling the strings, the stand burst: the part that was separated by the groove broke off from it.
I have two questions:
1. Considering that I do not live in Moscow, and the guitar is no longer in perfect condition, should I bother with a professional repair? Maybe it's easier to try to glue the breakaway part of the stand yourself, reinforcing it with “improvised means”? It is clear that the sound quality will deteriorate in this case - well, I do not expect something outstanding from an instrument that gets wet in the forest, shakes in a bicycle backpack, and so on.
2. The second question is this: maybe it would be more correct not to try to repair the old stand, but to replace it entirely? Do I understand correctly that for this it is enough just to glue it to the deck (of course, with the exact adherence to the location of the bone)?
I would be grateful for any advice.
If the guitar is dry and worn out to the point where the strings are on the neck, you will not save it by replacing the stand. The Madeira HC-09 is one of the toughest and most durable guitars in its class. The most that happened to her was that the ends of the frets had to be sharpened in the midst of frost. Of course, the bar can move from dryness, but not to a fatal outcome.
![]() |
Video (click to play). |
It is more likely that the belt spring was broken during the hiking exercise. At the same time, the deck sits down, and the strings fall on the neck. It is hardly possible to fix it without the guitar repair skill. Press down on the deck, if the spring is cracked, you will see the deck sag when pressed.
The part of the stand chipped off in layers can be glued together in this case. The safest way is to use epoxy, you can also use a reinforced tibond. Replacing the stand is much more difficult, you will need to remove the old one and completely clean the gluing surface from the old glue. And at the same time, do not shift the scale (since the supports are not identical in geometry).
The "walking guitar" is doomed to be disposable, there is nothing to be done.
Dear experts, tell me why this could happen? Would it be okay if I just take the strings off and just glue the nut back on?
This is one of the most common guitar breakdowns. I don't advise you to glue it yourself, it's better to take it to the master.
> Dear experts, tell me why this could happen? Would it be okay if I just take the strings off and just glue the nut back on?
> bug2,
> This is one of the most common guitar breakdowns. I don't advise you to glue it yourself, it's better to take it to the master.
It would be naive to hear another answer. For greater persuasiveness, one could add something like - In the absence of sufficient experience and certain skills in this operation, it is possible to disrupt the unhindered passage of sound waves, which in turn can lead to the appearance of tops and undesirable harmonics and various unpleasant overtones, which is further will entail an increase in the cost of repairs at least twice.
It is proposed to manufacture and install a new tailpiece holder for your instrument to replace the broken one.
Below you can see an example of repair to replace the tailpiece (stand) of an inexpensive Chinese-made guitar. The peculiarity of the breakdown was due to the fact that the top soundboard of the guitar was made of a 3-layer thin veneer of extremely low-quality, weak wood. There was practically no glue on the veneer, and the tailpiece was bolted to the deck with two screws. According to the customer, the guitar was purchased in a store, in a cardboard box, with metal strings deflected. And it's understandable why: after all, at the very first pull, the tailpiece was pulled out of its junction with the deck; the deck itself crumbled into layers of veneer.
The repair of the instrument consisted in layer-by-layer gluing of veneer, making a new tailpiece that significantly overlaps the place of the old one, replacing metal strings with nylon strings in order to avoid further delamination of this "problem" deck.
After a refurbishment repair, the deck surface was varnished and polished, after which it became possible to replace the tailpiece.
In the photo near the tailpiece, there are barely noticeable traces of the previous destruction of the deck (unfortunately, its condition before the repair was not recorded in the photo).
REPAIR OF CRACKS IN THE BASE (BRIDGE)
AFTER REPAIR: REPLACING THE BASE FOR A NEW
The main difficulty at home to glue the stand is the need to have special clamps. If you find it difficult to buy or make special metal, then there is a very original version from our members of the forum.
First you need to draw a frame on the deck. The stand is already positioned on studs. Using the tip to slightly lift the edges of the stand, scribble or use a sharp pencil to draw a frame on the deck.
You can close the window for the stand from applying varnish, just as you can scrape off the varnish within the window.
There is a technique for using a minifill for stripping. The cutter is exposed in such a way as to remove literally several dozen of varnish.
It often happens that after repair or tearing off the stand, there is an uneven surface of the deck, torn out with meat. You can choose 0.5 mm of the body of the deck, as if sinking the stand into it. With careful work, this is not at all visible, but there is no need to use epoxy resin or any complex inserts with additional glue seams. Again, with the help of a mini-milling cutter, you can make the window bed for the stand absolutely even.
If the surface of the deck and the stand are exactly adhered to each other, then you can glue it with high-quality wood glue or special adhesives such as Titbond, or epoxy. By joinery adhesives we mean skin, bone or fish adhesives. Reading an article about adhesives
It is impossible to glue with elastic adhesives, since this is the so-called permanently loaded gluing, and very strongly, and if the glue stretches, then the stand will come off soon.
If the deck surface has all sorts of defects and you have a bias against epoxy, then you can use intermediate inserts. If there is no bias, then epoxy is suitable, since it will fill in all the irregularities and will not shrink.
The rear of the stand must be fitted especially carefully. It is she who comes off. The front of the stand, on the other hand, is pressed into the deck. The shift can be ignored, since gluing resists it in the best way. The main problem is the back, which is trying to come off.
You need to press the stand with special clamps through the hole in the deck. Three clamps reaching from the voice box to the stand. Pinch the middle and edges.
From the side of the deck, from the inside of the body, it is necessary to ensure the uniformity of the pressure, capturing the entire area under the stand. A special piece-druka is attached to the clamp, which presses the deck, but allows the springs of the fan to pass through. It is advisable to press into the springs themselves, this can be achieved by thrusting something like foam into the gaps.
Pressing only into the springs is a bad option, since the deck will go in waves between the springs.
Our members of the forum came up with and made a very interesting device for pressing the stand, which is made from ordinary sticks with an F-shaped clamp.
And what for you, my friend, decided to use metal guitar for nylon strings? She is not adapted for this. It could bend the neck too, then just glue it back and put on the native strings.
here, too, I don’t understand what for .. I fucked up the seller in the store and looked through the internet before putting it to a friend.
Its directly went with the metal.
@ColpaQ, I advise you to put a stand with pegs (it can withstand metal strings if the guitar is not made of paper). They will hold not only due to glue, but also due to tuning pegs with strings. I had a similar situation - the norms went down.
What do you think it was attached there before?
The safest way is with two bolts and nuts. But you can see them. In general, metal should not be placed on classics - if not a nut, the neck bends into an arc.
Next time you google before doing.
The finishing of the tool begins with a wet cleaning of the workshop, since dust is the worst enemy of the wood polishing process. It is necessary to replace the apron or dressing gown and warm up the room to 24-27 ° C. Then make a close inspection of the outer surface of the instrument. The noticed cracks are putty with sawdust mixed with liquid skin glue. Putty is done carefully, trying not to stain the deck. If this does happen, remove the uncured putty from the polished deck with a damp cloth.
The dried body is cycled. In this case, the body of the tool lies on the knees, and the head of the neck is pressed against the rubber gasket of the workbench.
The sidewall is cycled along the entire plane, avoiding getting into the enthusiasm. Otherwise, the direction of cycling is reversed.
The bar is looped starting from the heel. In this case, the loop smoothly passes through the vein separating the heel from the body. When processing the handles, make sure that no edges are formed. They are eliminated by giving the cycle a spiraling direction. The headstock is cycled from head to body, also avoiding the resulting edges on oval surfaces.
The body and neck are sanded with fine-grained emery paper in the direction of the scraping. It is recommended to wipe the treated surface with alcohol after finishing sanding and sand the raised pile.
Before applying varnish to the body and neck, the surfaces to be coated are primed with nitrocellulose varnish NTs-222 or the like. The body and neck are primed using the same technology as the deck primer.
The body and parts of the neck are varnished with shellac varnish using a tampon in the same sequence as when processing the soundboard. The same technological sequence is adhered to when grinding and pumicing the lacquer coating, as well as during the subsequent polishing of the case.
Great care should be taken when sanding the lacquer coatings of the housing, as sanding down to wood is possible.
Quite often, the craftsman is not satisfied with the natural color of the wood of the case. In this case, the body is painted after the body is sanded. The dye is diluted in the right proportion and be sure to try it on a plate of the same breed as the shell. When good results are obtained, the dye is evenly applied with a swab along the shell without streaks or gaps. Do not wet the painted surface too much. After the dye dries, the painted surface is wiped with a piece of felt until a slight shine appears. Next, proceed to priming with nitro varnish and subsequent finishing of the tool. It should be remembered that when sanding a painted case, unpainted wood appears. This defect can be completely eliminated only by cycling and repeating all subsequent operations.
For the convenience of finishing work, a pin 100 mm long is inserted into the hole drilled in the arrow for the button instead of it.The guitar (like a cello) is held by the neck with the left hand and rests on the workbench with a pin. In this position, the parts of the guitar are painted over, varnished and polished.
The guitar stand, also called the saddle, serves as a second anchor point for the taut strings. The strings are attached to the stand with the help of small balls (in the case of a pop-type guitar) inserted into the grooves of the stand, or with a loop (in the classical one). The stand is made of several types, depending on the method of fixing the lower end of the strings. For the manufacture of this part, hornbeam, walnut and other hard wood are used. The support is well cleaned with a sanding cloth and covered 1-2 times with nitrocellulose varnish. Preliminarily, the ends of the fret wire are rounded off with a file.
fig. 1
It is possible to manufacture a stand with a so-called slide (Fig. 1). The musician-performer has the ability to adjust the length of the sounding string within insignificant limits by moving the slider along the surface of the stand. The figure shows the main dimensions of the cross-section of support 4 with a slide 2. In this case, the strings are attached with a loop to the buttons 3.
There are stands that are adjustable in height with screws. They are made from metal and wood parts. Stands of this type are not widely used.
fig. 2
The length of the stand depends on the distance between the strings, which in turn is determined by the width of the neck. Calculate the location of the stand and its dimensions according to the scheme shown in Fig. 2. The distance from the edge of the nut to the 12th fret (the line connecting the neck to the body of the guitar) is set aside twice. Thus, the axis of the support is obtained. The fret wire of the stand should be located along this axis. At a distance of 2-3 mm from the edge of the neck, lines are drawn and, continuing them to the axis of the support, the size A is obtained, which is divided into five parts and the distance between the holes or buttons on the support of a six-string guitar is obtained. For a seven-string guitar, size A is divided into six parts.
You should not get carried away with decorating the stand, make it pretentious and make it too heavy. Sometimes a wooden plate (2.5-3 mm thick) is glued from the inside of the deck under the place of gluing the future stand. This is believed to improve the performance of the stand and give it greater strength.
fig. 3
Before gluing the stand, they put it in its place and circle it with an awl along the contour. A thin line remains on the surface of a polished or lacquered deck. Inside this contour, with a scraper or knife, remove the varnish film to clean wood. When gluing, use fresh skin glue, which is applied to both the deck and the stand. It is recommended to slightly heat the stand before gluing. Pressing the glued stand is carried out with a clamp (Fig. 3). The protruding glue is carefully removed with a chip and a damp cloth.
The tuning machine is attached to the headstock using screws 5-6 mm long. The slots for the screws are marked with an awl.
Depressions are made on the sill equal to half the diameter of the string being applied. The grooves are spaced at equal distances from each other, departing from the edges of the nut 2-3 mm. The strings are pulled only when there is confidence in the high-quality gluing of the stand.
A button is inserted into the hole drilled in the arrow.
This guitar stand is interesting for its laconic design and ease of assembly. Its prime cost is low. You don't need fasteners or wood glue to make. Details of the process, how to make a guitar stand with your own hands, below.
Before starting work, check the presence of:
-
oak boards (0.25 x 22 x 38 cm);
a sander or sandpaper;
Step 1... The work begins with making a template. You can use the given one in your work or change its parameters based on the required height and dimensions of the guitar itself.
Step 2... Print the template on a standard sheet of paper, if you have not changed its dimensions, and using a pencil and a ruler, transfer it to the existing piece of board.
Step 3... Drill two holes with a diameter of 25 mm at the locations marked on the template.
Step 4... Carefully make grooves from the holes and cut the board along the marked lines into two parts. This work is painstaking and requires the utmost care from you due to the relatively complex shape of the blanks.
Step 5... Fold the two pieces of the stand together. In this case, the grooves must fit into each other. Check the stability of the product.
Step 6... If everything is in order and the parts do not need to be adjusted to each other, sand the edges of the sections. If you wish, you can cover the surface of the stand with varnish or stain, or you can leave the product as it is.
Everything in this world is not eternal, everything breaks down and falls into disrepair. This also applies to the guitar, which, by the way, is a rather fragile instrument that requires proper and careful care. But if suddenly the guitar is still a little damaged what to do?
The easiest way out is to contact a guitar master. This is such an uncle (very auntie) who makes these guitars to order and will be able to fix yours with maximum speed and quality. The problem is that the masters take money for their work, moreover, the money should be recognized as not small.
If the guitar is badly damaged (the neck is cracked, the spring inside the soundboard has fallen off), then it would still be wiser to pay money to a professional. But if the damage is not great then guitar repair it is quite possible to carry out at home using your own hands and simple tools:
Cause:
The strings are too close to the nut
Solution:
Strings get along because the strings touch the metal frets when they are tugged, resulting in such an unpleasant rattling sound. There are several options for elimination.
If your guitar has a truss rod, then you just need to adjust it to the height you want, that is, to the height where the strings sound normal, without rattling. But the truss rod is not available in all guitars, so the old grandfather's file comes to our rescue, but rather the skin of one. If you use a skin, then it is better to come to a flat bar and grind it as if you were working with a plane.
Our goal is to file the frets a little to increase the distance to the strings. This should be done carefully and evenly, while I would advise not to touch the first 2-3 frets at all, but to grind off the others. Sharpen gently and slowly. If suddenly it turned out that one fret was worn off very much - no need to compare everything for it. Better to have one fret lower than you ruin everything.
Solution:
And here, with the presence of an anchor rod, the problem is solved in a couple of minutes. But if it does not exist, the situation becomes more complicated, since we can grind off the frets, but we can not increase it.
There is only one way out - to make the cuts in the nut deeper. This is done using a thin - thin file. And again, you should act very carefully and slowly so that the strings do not sink too low.
If you have gone too far, then you can build up the nut back by dropping a little melted plastic into the slot under the strings, or by thrusting a little hard leather into the slot.
Cause:
Most likely one of the springs inside the case has come off.
Solution:
It is better to consult a specialist, but you can also glue it in place yourself using Moment glue. The difficulty is that you have to act blindly and with one hand. Even if you managed to pour glue where you need it, it is not a fact that you can attach this small board where you need it. However, the task is quite feasible, in front of my eyes, the fallen off spring was blindly glued into place and it held on for many many years.
Solution:
Again, it is better to contact the master. But if the crack is not deep and not long, then richly fill it with epoxy and press it with a clamp. 24 hours in a dry warm place and the problem should be eliminated.
In general, friends, if your guitar is expensive, run to the master, do not engage in amateur performances. If the cost of the guitar
what to do if the gears of a classical guitar are broken, how can they be repaired or replaced?
buy new mechanics for classical guitar and replace the old one
If the gears are tuners (tuning pegs), then they change simply. We take a screwdriver and twist, remembering to remove the strings from them. (On the classics, there are usually pegs of 3 pieces per ponel). If the legs at the gearwheel are bent on one side, and the string tension falls off at a certain level of tension (the gear does not hold much tension), you can remove the gear and turn it over with its whole legs, looking with a glance.
If you mean other gears? O_o then clarify
How do I fix my electric guitar?
Which keys to adjust the truss on Maria's bass guitar? It is clear that the original keys may no longer be found, but maybe there is some kind of replacement?
This DIY guitar stand was made from the remnants of plywood, painted with a small amount of paint.
DIY guitar stand
Step 1. Cut the vertical part
2 cm. Redraw the stand template onto a piece of plywood and cut with a jigsaw.
The base of the stand should be approximately 2 times the depth of the acoustic guitar body. The height of the stand should be sufficient so that the hanging guitar does not touch the floor.
The base is trapezoidal: the front is slightly wider than the back. The front edge of the stand is slightly less than the width of the guitar.
The distance from the leading edge to the trailing edge is approximately three times the depth of the guitar.
Step 4. Make a guitar holder
This piece needed to be wide enough to hold the tuning pegs.
Step 5. Install the retaining nuts
Drill holes in the bottom of the vertical section of the stand and insert the hex nuts there.
Step 6. Install the hardware at the top
Drill one hole for the nut and the other for the dowel.
Step 7. Drill holes in the base
Drill three holes in the center of the rear edge of the stand base to match the holes in the vertical piece (step 5). Play 4 more holes, in each corner of the base.
Sand the edges of all parts thoroughly. I decided to paint the ribs with dark paint.
Step 9. Painting and polishing
I painted the stand and the vertical section with honey-colored paint to match the color of the guitar itself. Finally, I covered the stand with 4 coats of varnish.
Screw the metal legs into the base.
When the whole structure is assembled, cut out two pieces of felt and glue on the top of the stand.
Best logic puzzles of all time: Roses (Answer) 576 views
Best logic puzzles of all time: ball and bat (answer) 230 views
Simple Tricks That Make Your Life Much Easier 222 views
The 25 Most Unusual Sports in the World 205 views
Relationships will be long-lasting if at least one of the partners has this trait 152 views
Best Logic Puzzles of All Time: Fruit Math 134 views
Best Logic Puzzles of All Time: Spy and Maple Syrup 132 views
This Faith Raises the IQ Level 109 views
22 Ways To Fold A Party Table Napkin 90 views
How long can a person survive without water, food and air 89 views
Electric guitarperhaps the most distressing instrument - it seems to have been created especially for expressive and aggressive playing. And where emotions run over the edge, there is always room for trouble - belts break, guitars fall, strings break, varnish cracks, neck deforms. Repair, in short, is inevitable sooner or later. (In addition, over time, guitarists have to change frets, re-solder electronics, shield tone bays, and so on.)
Note that not every guitar can be saved - some damage is incompatible with life. In this case, it is better to buy a new electric guitar. In the Muzline online store - hundreds modern electric guitars for every taste and wallet, from well-known brands and young companies. If the goal is to revive the instrument, it is important to know some of the features of home repair.
Not everything can be done at home. However, even a non-specialist can cope with such types of work:
- shielding of internal cavities for electronics;
- grinding of frets;
- inserting fret marks;
- fret scalping;
- adjusting the springs of the tremolo machine and floyd rose;
- replacement of tuning pegs;
- replacement of pickups;
- replacement of the cover on the body.
More serious procedures, such as anchor adjustment, complete replacement of electronics, body restoration, etc. Such work requires special knowledge, skills and conditions for correct execution and high-quality results.
Careful operation, proper storage and timely maintenance of the instrument is a guarantee that it will not need repairs for several years, or even decades.
- It is necessary to store the electric guitar in a case or case in a room with stable humidity and air temperature.
- On stage and in the studio, it is worth using guitar stands - instruments are guaranteed not to fall from them.
- Stretchers are much more reliable than traditional belt buttons, which, if broken, often damage the tool. Better to use them.
- Electric guitar body and neck should be thoroughly cleaned every few weeks and treated with polishes and conditioners that protect the varnish from environmental influences.
- Guitar should not be transported in the cargo hold of public transport unless the musician has a sturdy solid-state case with secure locks and internal tool holders at his disposal.
Repair Class - Forum about DIY repair, home improvement and house construction .: DIY guitar stand - Repair Class - Forum about DIY repair, home improvement and house construction.
#1
konoplyaninov
- Moderator
I did not make step-by-step pictures for the master-class, and I cannot imagine. But the idea of how to make a guitar stand with your own hands, I think, will be clear without them.
To make a guitar stand with your own hands, you need to find:
- A sheet of plywood is better than seven-layer plywood;
- 2 pine or spruce planks and a lath;
- Thick fabric, foam, thin felt or carpet trim;
- Regular furniture door hinge, screws, nails;
- wood glue;
- wood stain, furniture varnish.
From the boards, with a jigsaw, we cut out the lower side supports for the future guitar stand.
The stand for the guitar neck was made of a rail, to the end of which the neck holder was fixed.
The base of the guitar stand is made of three layers of plywood, to which I attached a stand with a neck support and lower side supports using a furniture loop. I installed the lower side supports on self-tapping screws and made them movable.
The front decorative panel is made of plywood and serves to fix the side supports from "creeping". To do this, I fixed two pins in its lower part (cut off 2 nails), and drilled two blind holes in the front part of the side supports.
After processing, I opened all the details with wood stain and furniture varnish. In the places where the guitar touches the stand I glued “pillows” made of felt and foam rubber, in the lower part I glued “blotches” from the carpet on the supports.
I hope you enjoy the idea of how to make a guitar stand with your own hands!
The message will be completely deleted.
Nowadays, the media widely cover interior themes. The most significant players on TV are the TV programs "Kvartirny Vopros", "Dachny Otvet" and "School of Repair".
Housing Question - has been on the NTV channel since 2001.
Dachny Answer - has been on the NTV channel since 2008.
School of repair - has been on the TNT channel since November 2003.
The leading players in the interior press are the magazines Ideas for Your Home, Apartment Answer to the Apartment Question, and Home.Interiors plus ideas ”,“ Salon Interior ”,“ Interior + Design ”.
“Ideas for Your Home”, “Apartment Answer to the Apartment Question” and “Salon Interior” are magazines of the leading interior publishing house “Salon-Press” in the Russian Federation. In our opinion, it is the Ideas of Your House magazine that is the best printed source on interior issues and has undoubtedly enjoyed the confidence of the readership for almost 15 years.
"Home. Interiors plus Ideas ”is undoubtedly an interesting publication, which is a direct competitor to the“ Ideas for Your House ”magazine, but due to the later entry into the market, the number of readership is much smaller. Published since 2007
"Interior + Design" is a long-liver in the interior press market. Published since 1996.
Each of the above sources is an undoubted helper for people who have started repairs, plan to change furniture or even build a house, but the obvious drawback of all these media is the inconvenience associated with a time limit. The KlassRemont team is trying to make a resource that will promptly respond to any tasks in the field of repair and planning of their homes.
We are interested in making a unique resource that will help people. Everyone in their life, one way or another, is faced with repairs and it would be great to get yourself an on-line assistant.
Installing a septic tank, gluing wallpaper, conducting electricity or selecting furniture, we will try to consider all these issues for you as soon as possible. Undoubtedly, we have a long way to go to work out all the questions about the repair, but our professionals will not keep you waiting long with an answer.
Playing the classical guitar also assumes an appropriate fit. Its peculiarity is that the guitar has 4 points of support: both legs, the forearm of the right hand and the chest. In a classic fit, the bar is raised at approximately a 45 degree angle to the floor. For such a fit, guitarists use stands of different designs.
First of all - the usual footrest for many people. This stand is the most common. It is with her that training in a music school begins. Foot stands can be wooden, plastic or metal, solid or folding, but it remains unchanged that this stand is used with a certain angle of inclination, which can vary depending on the individual characteristics and desires of the performer himself.
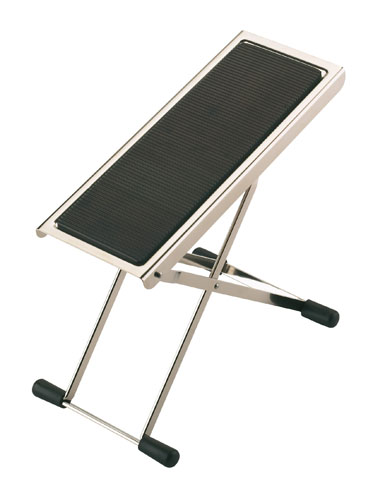
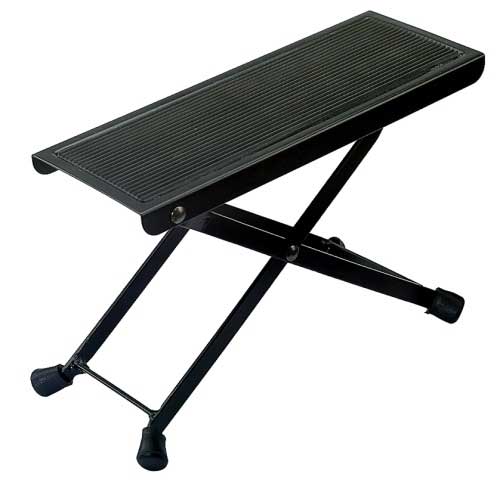
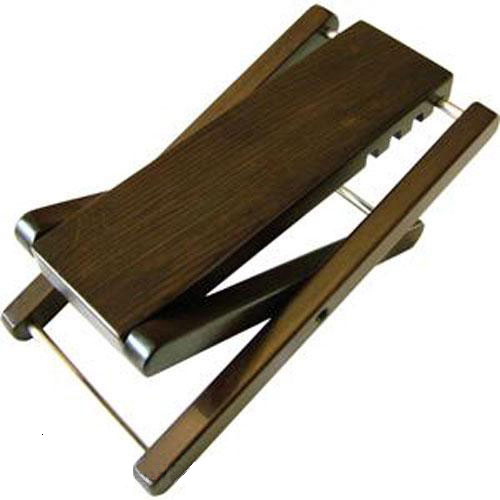
During many hours of practice, the guitarist has to sit asymmetrically at the instrument with a footrest: the left leg, being in a raised state relative to the right, helps to reduce the blood circulation of the internal organs, while the body is often turned towards the neck. This situation can be one of the causes of discomfort and even occupational diseases.
The transition to another stand, a stand for a guitar or, as it is also called, a support, depends not only on the individual characteristics of the performer, but is largely related to physiology.
When using a guitar stand, there is a better chance of achieving a flat landing, an even spine due to the fact that the legs are at the same level.
Of course, for those musicians who have been practicing with a footrest for many years, it will be unusual to use a caliper. Some, having tried once a guitar stand, again return to the usual stand, familiar from the music school. But those guitarists who understand the physiological significance of the caliper are trying to get used to the new sensations.
Guitar stands also come in several types. Today, the most common are arcuate calipers with a different number of fasteners, calipers with folding parts and in the form of a "pirate leg".
Arcuate stands differ in the number and quality of fasteners. Most often, these mounts are suction cups. Calipers with three suction cups are considered more stable, but there are also one and two.A stand that attaches to suction cups requires a perfectly smooth surface. If the body of the guitar is not varnished, then it is possible that such a stand will not be fixed. There are also fasteners in the form of special clamps, into which the tool itself is inserted.
Folding stands are more mobile. Once you have attached such a stand, you do not need to remove it, since it does not take up much space in a case or case.
The “pirate leg” support is so named because it resembles the wooden leg of a pirate from old Soviet cartoons.
Guitar stands are more difficult to obtain than foot stands and are more expensive. But there are cases when the calipers were made independently.
I saw calipers with three suction cups (1990) in the Moscow store of musical instruments “Rhonda Music”, by the way, there was also a “pirate leg” (990 rubles).
in fact, I was in the RONDO! store, which is 8/10 Neglinnaya Street, yesterday. A caliper with three suction cups cost 1,440 rubles there. Has the price really gone up so quickly?)
And do not write the address of the store, the "Pirate's leg" is of interest. Thanks in advance!
You cannot undo what has been done. What is done is done
I was born in the USSR with the ensuing consequences. That is, Leningrad guitars with a curved neck, and those in tallons, but there was no question of stands. Virtuosos often told in their master classes:
1) how to wash your strings to prolong their life
2) what kind of glue to drip onto the rubbed braid so that the string will last longer
3) how to put together a footrest from the available means. Some textbooks wrote that instead of a stand, as a last resort, you can use a stack of books. In general, when I was learning to play, I saw the stand only in pictures. Having moved to live in Germany, I once and for all solved the issue with the stand by going to the nearest store and buying it. Accordingly, without bothering to ask if the bourgeoisie had invented something new during this time. It turned out to be invented. And I like to test different new items. After playing with the footrest and comparing it to the guitar holder, I came to the conclusion that it is equally convenient for me to play with both the first and the second. But my choice settled on a footrest - compact, foldable, rectangular, fits in a denim jacket pocket. But.
Dear guest, so you hint in which region you are interested in the address.
![]() |
Video (click to play). |
The Moscow address is indicated in the comments, and it was at that address that the same “pirate leg” was noticed. And if it is completely sour with the search for such a thing in your region, then it is possible to simply order a stand. Write.