In detail: do-it-yourself roof rack repair from a real master for the site my.housecope.com.
Initially, I was looking for a car with roof rails, but there was nothing suitable for the state, when I found this instance, I had to put up with the lack of rails.
I thought to buy universal ones, which are placed on doorways - I was afraid that the roof was bent.
I went to the Spasio-club, read it, everywhere it was written that “do not put”, “accept”, “use universal”, although there were people who screwed the stock ones stupidly on bolts - put them as an element of decor. God forbid getting on such a specimen - load something, and your roof will bend. In general, this did not suit me and I climbed into the existential, looked at the factory diagrams and realized that all you need is the factory rails themselves and amplifiers for them, which are installed from the inside under the ceiling.
In the open spaces of the Internet railing from Spasio AE111115 the sea, but they are all without fasteners, unfortunately. I monitored disassembly resources for about 2 months, even found complete sets, but did not have time to buy. As a result, I scored on the search and ordered just the used roof rails (2000 rubles) and NEW mounting plates in Exist (
Issue price: 5 500 rubles
All rights belong to the author of the publication: = MityA =
1) Kiryukha without roof rails, but with Tulev crossbars. Thule SlideBar 892
2) the rails themselves - move apart
3) what broke in the railing
4) what broke (installed BU railing)
5-6) to the question of 8 years of standing such happiness on the car and rubber bands
1) Kiryukha without roof rails, but with Tulev crossbars. Thule SlideBar 892
2) the rails themselves - move apart
3) what broke in the railing
4) what broke (installed BU railing)
5-6) to the question of 8 years of standing such happiness on the car and rubber bands
do not buy roof rails. better: set of bows with sliding function 144 cm. for author. trunk Thule SlideBar 892 (2 pcs.) -Set of locks for auto. Thule 544 roof rack (4 pcs.) - 1.00 pcs. Thule supports 754 for cars without gutter (4 pcs.) - 1.00 pcs. Thule trunk - 1.00 pieces I've bought a bibik with a railing, so this miracle of technology burst under a box of 30 kg. Brother Bibik without them - there is a set described above - do not transport cast iron, and nothing will burst
![]() |
Video (click to play). |
The idea is good.
Dear, do you have any information about staples? Because after contacting the Tulev managers on this topic, they said that all this is not a problem, but they need the article number of a suitable bracket for attaching to the roof of the kai. They will not pick up the bracket themselves. They say it's like looking for a needle in a haystack.
everything that was bought:
Set of bars with sliding function 144 cm. For bus. Thule SlideBar 892 (2 pcs.)
Set of locks for auto. roof rack Thule 544 (4pcs.)
Thule stops 754 for cars without gutter (4 pcs)
Installation kit for auto. roof rack Thule 1448
bought in
complete set: id = 8 & carid = 4975, only there are 127 arcs, and my brother and I have 144
Post has been edited by ziabr on 15 March 2014 - 11:50
Hello to all! With such wonderful instructions and photos, even I, a blonde, could install roof rails on my kiryusha. In just 4 hours. Thanks a lot. And then the officials refused to put it. I had to go around a bunch of services, agreed on one thing. At the same time, they requested 5000r. Fiends. So, thanks again, tremendous.
Officials don't like trying new things.
And who will advise the trunk (original car), or is there a ready-made theme?
Trunk or crossbars for roof rails?
There are no rails, you need a trunk.
In Ulan-Ude we saw only China, but different.
Finally I installed the roof rails for myself. I took it here https://my.housecope.com/wp-content/uploads/ext/2109. _fromsearch__а1 According to the advice in the topic, I did not completely remove the ceiling (it remained hanging on the eyeglass case and the central plafond). The points where you need to drill are clearly visible when you bend the skin. The author of the topic is a big plus for the cap puller, only I grinded it off a little in order to better crawl up to them.
Good day! And the question is - should you start drilling from the bottom or from the top?
It so happened that I broke the front left support of the roof railing. I go - knocks. Until I bought it, I decided to repair it as soon as possible.
It so happened that I broke the front left support of the roof railing. I go - knocks. Until I bought it, I decided to repair it as soon as possible.
remove the rubber seal
unscrew the nuts "by 10" with a tubular wrench
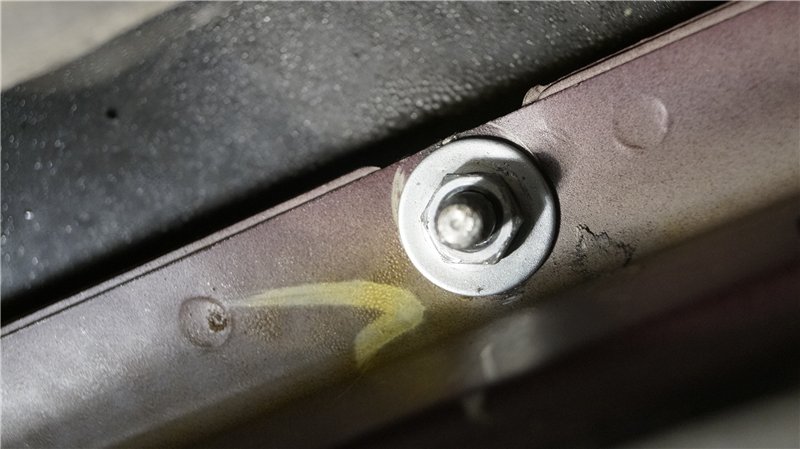
remove the support. the breakdown looks like this.
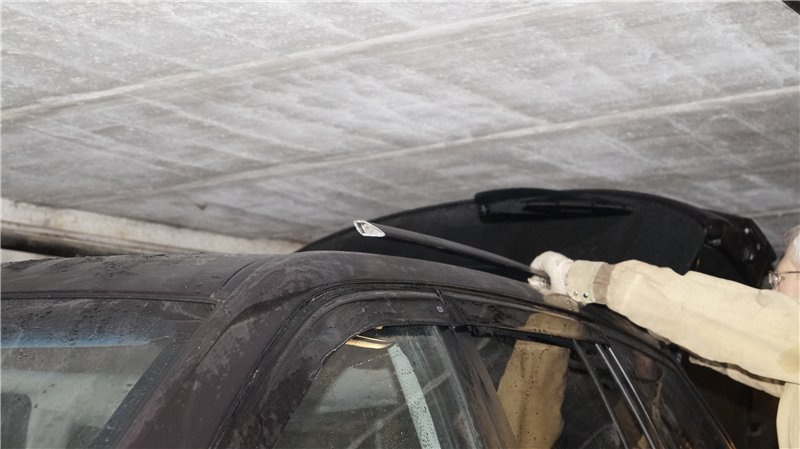
remove the railing itself. broken off support inside the pipe.
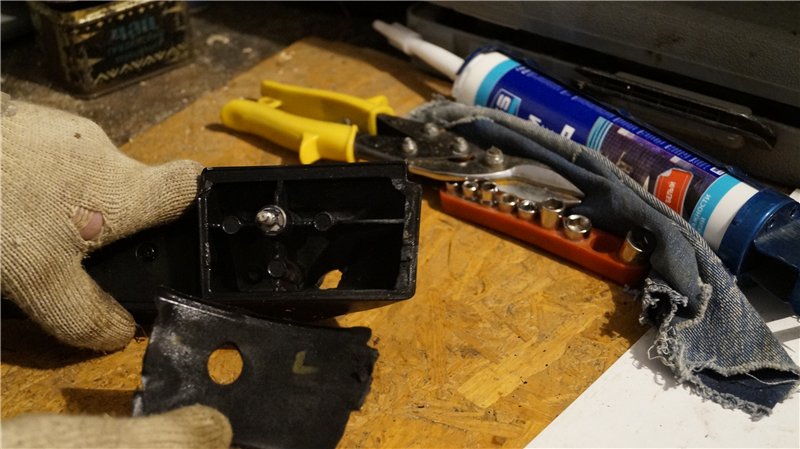
remove the rubber seal
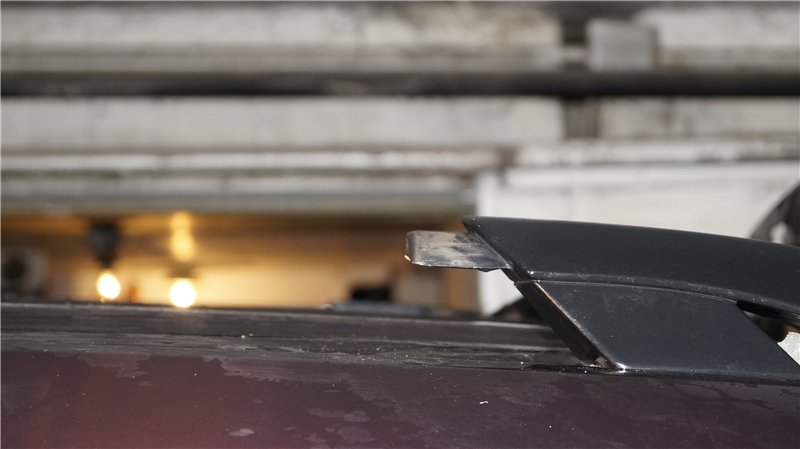
this is how a “healthy” support looks like. (back)
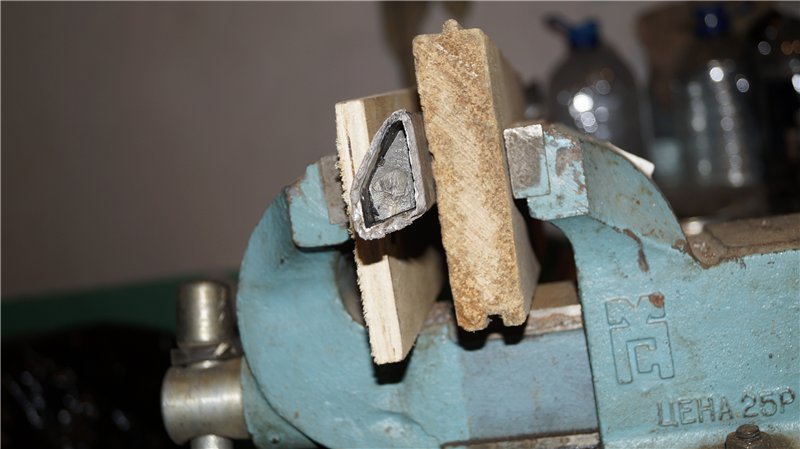
clamp in yews. Carefully, through the pieces of wood.
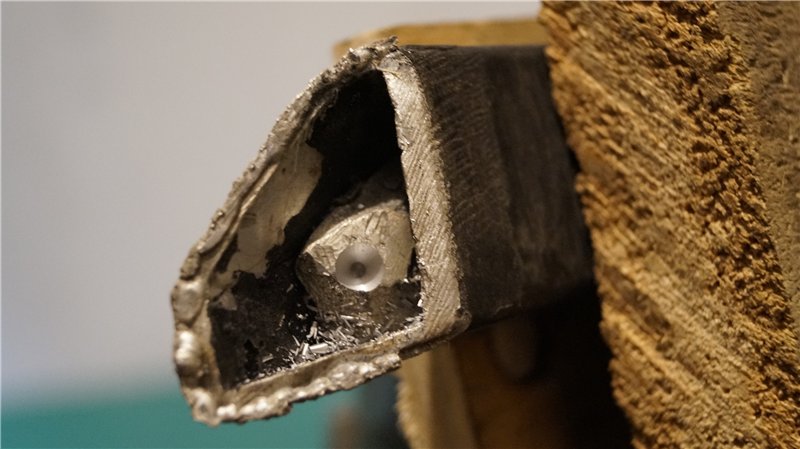
like that. you need to drill at an angle, as the rail bends (of course, by eye)

then I drill with a drill for thread m8. This drill has a diameter of 6.5 mm. Drilling depth mm 40.
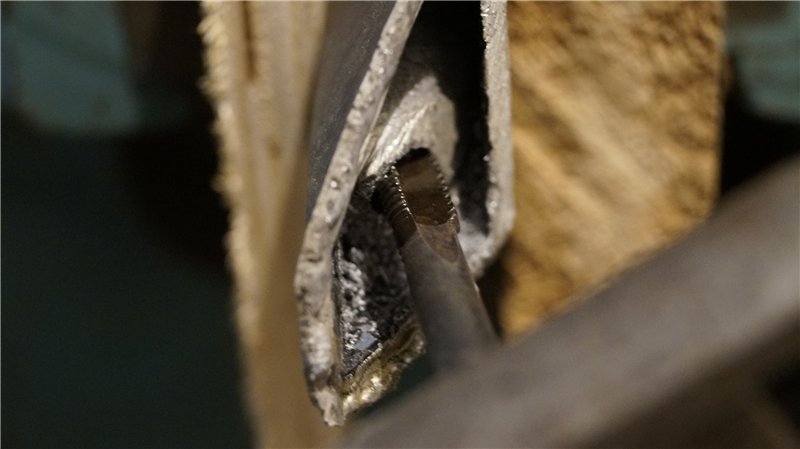
cut the thread. Can be used with one tap, if machine tap, but better with 2
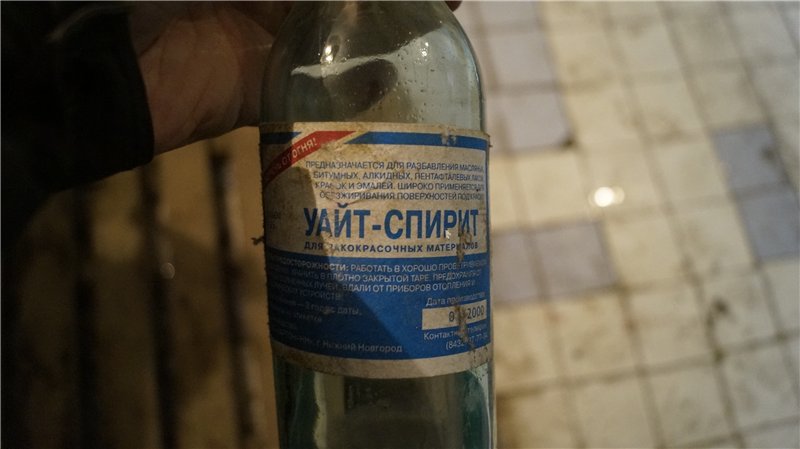
we wash or blow off the thread from shavings
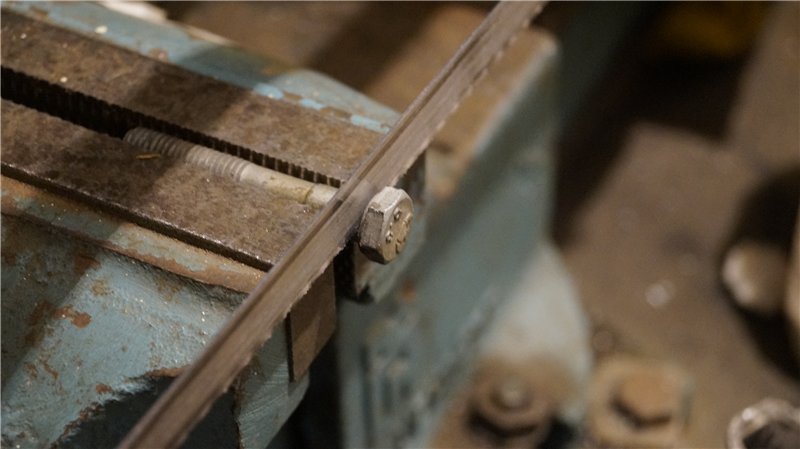
we make a hairpin from the bolt by cutting off the head
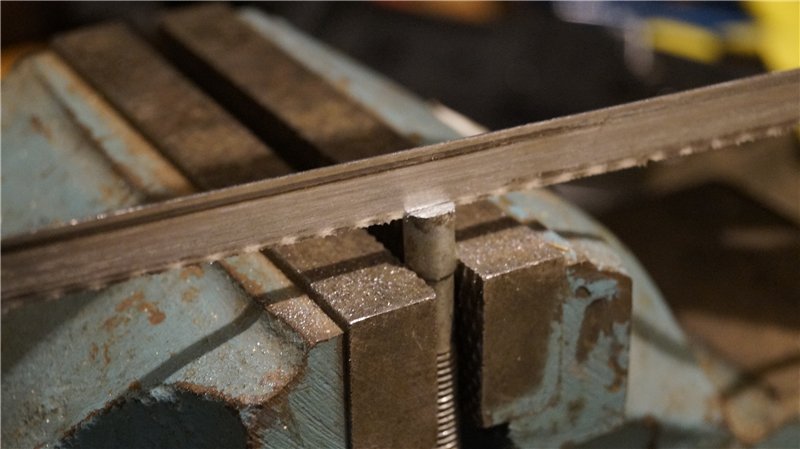
make a cut for a screwdriver
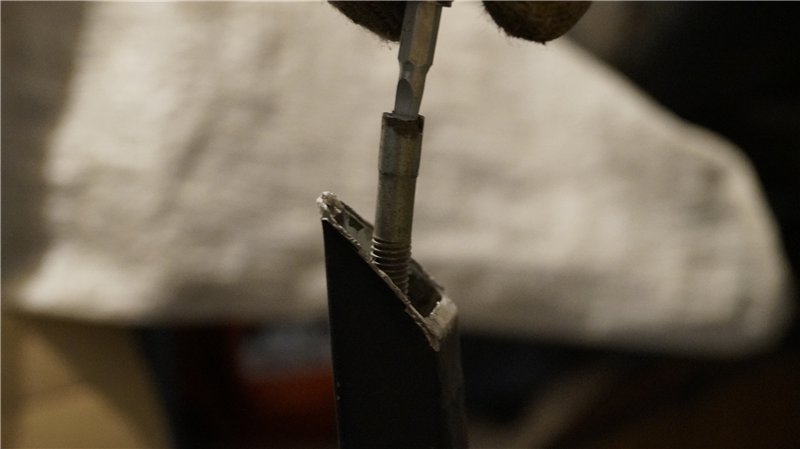
screw the hairpin into the rail
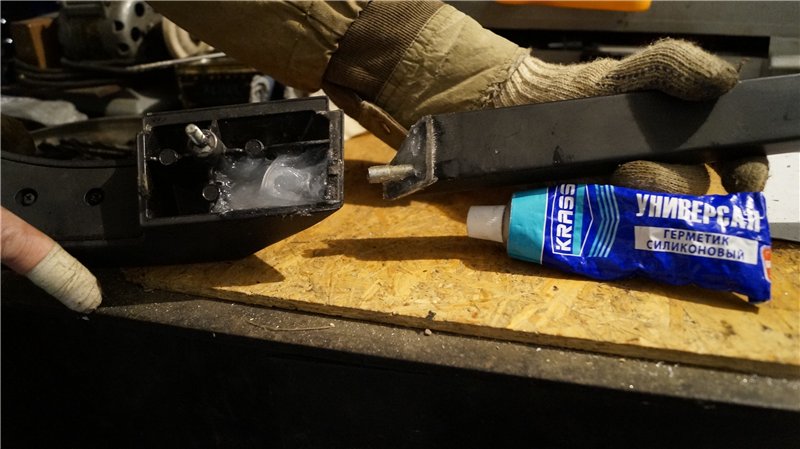
in the support and on the hairpin silicone sealant. so as not to dangle. and we assemble everything in the reverse order without waiting for the sealant to harden. Everything fell into place perfectly. Of course I will not carry heavy things, but something like skis will withstand it. I will find a rail, maybe used, I will put it in the summer. Good luck to all.
Why didn't the broken end come out?
Didn't even try. It turned out faster with him
Didn't even try. It turned out faster with him
if I got out, I just drill a piece of the katsa, and then attach it to the support and drill there, well, put it on the bolt.
if I got out, I just drill a piece of the katsa, and then attach it to the support and drill there, well, put it on the bolt.
Unlikely. The shape of the support is too tricky
Here's another photo
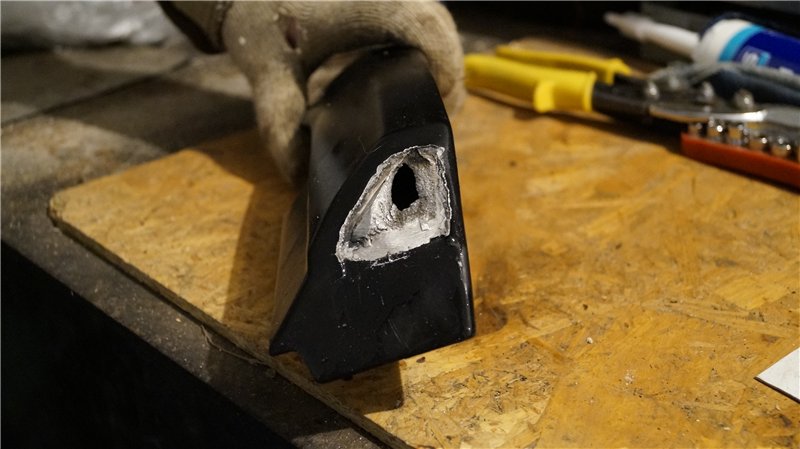
Roof rails are an attachment to the roof of a car that gives it a unique appearance and improves its performance. These accessories are used to mount additional luggage equipment. It can be:
- specialized box;
- basket on the roof of the car;
- mounts for bicycles, skis, snowboards, and other tourist equipment for recreation.
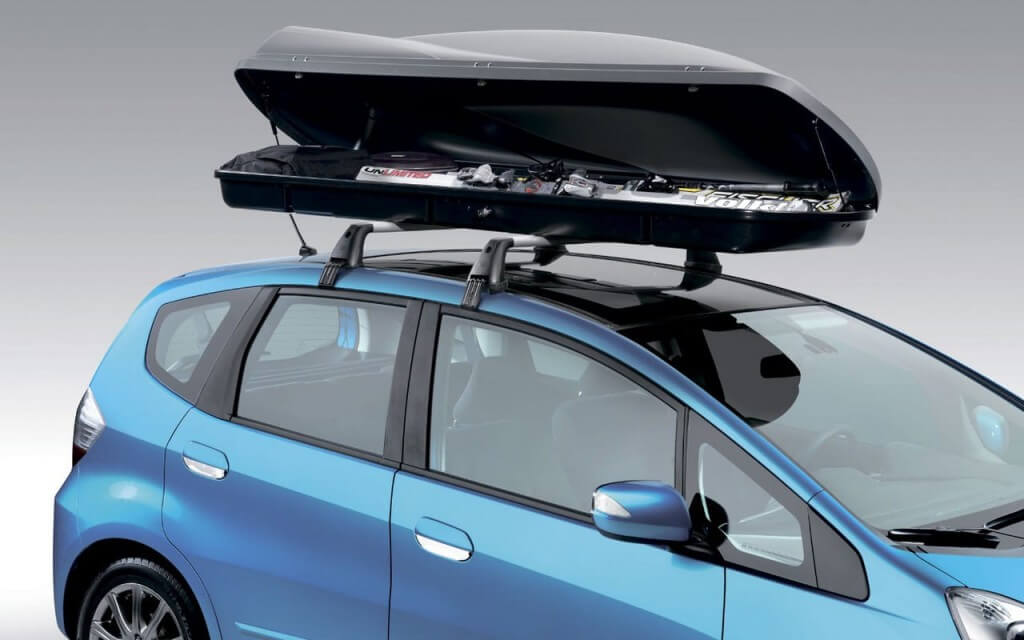
But before installing the trunk, box, or specialized mounts, you need to install additional cross members. They will be securely attached to the rails, and to them, respectively, the transported equipment. These crossbars for the trunk can be either purchased at specialized car dealerships or made yourself. Next, we will describe several ways to make do-it-yourself crossbars for roof rails.
Making crossbars for roof rails with your own hands will not be difficult. For their manufacture, it is necessary to take into account the features of each car, as well as the individual wishes of the motorist. The main "plus" of creating fasteners with your own hands is the price, since the purchased crossbars will cost several times more.
Also, do not forget about the strength characteristics. When transporting cargo, the main thing is that it does not fall and create an emergency. Therefore, it is also not worth saving on the quality of materials for the manufacture of crossbars for the trunk. Today, the cargo transported on the roof of a car can range from 60 to 110 kg.
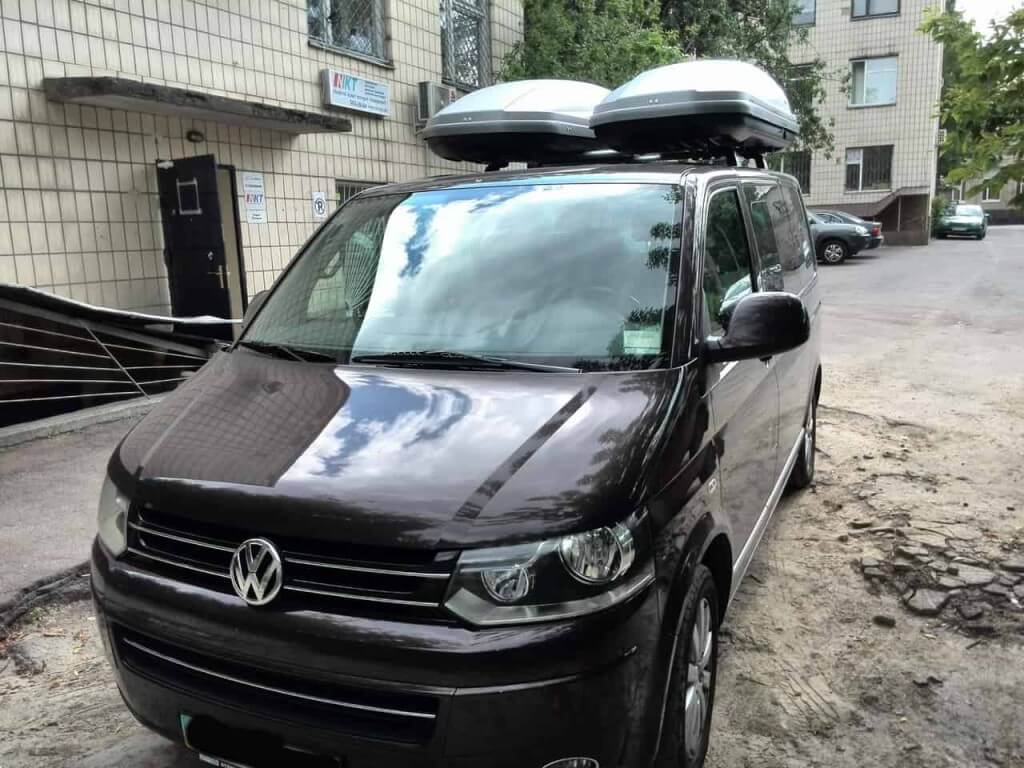
To create crossbars for roof rails, we need:
- metallic profile;
- grinder, drill, welding;
- fixing material (bolts, nuts, washers);
- polyurethane foam;
- heat shrinkage;
- construction hair dryer;
- paint, brush.
Typically, the roof rails for installing the rack are two parallel straight lines that are fixed to the rails. During their manufacture, you need to take into account the shape of the roof, as well as its width. The material for them can be a metal profile made of light-alloy materials, or a square tube (metal thickness - up to 3 mm).
The cargo is fixed by means of:
- belt fasteners (if the cargo is transported directly on the crossbars);
- nets (if a basket is used);
- support or pressure clamps (for transporting skis, snowboards, bicycles).
Also, during the installation and removal of the cross members, it is necessary to provide rubberized gaskets to prevent damage to the paintwork of the car body. Below we will consider several options for creating crossbars with our own hands.
Option number 1... Such creation of crossbars will be the easiest and will not take much time. In this case, we need:
- clamps for fastening in the amount of 4 pieces;
- profile pipe 20 * 40 (you can also use 20 * 30).
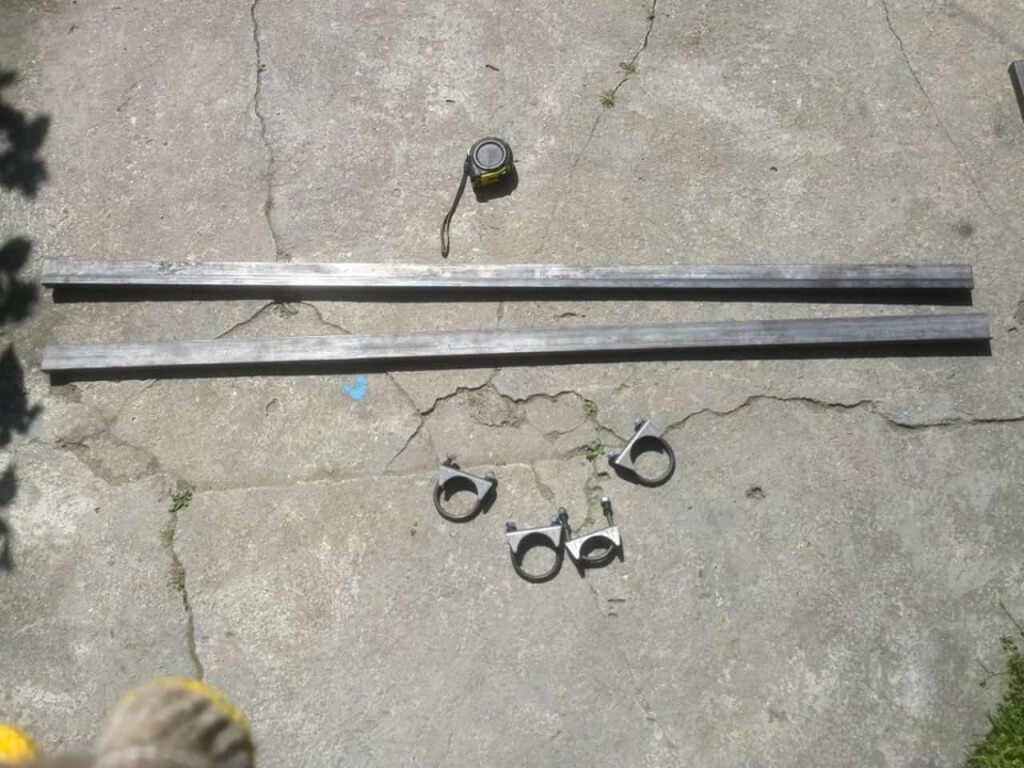
Manufacturing process:
- Decide on the size of the crossbars (in our case - 140 cm). In order not to be mistaken in further dimensions, after creating the first blank, we recommend that you double-check all the measurements taken in advance.
- Next, you need to drill holes for the clamps, which will be used to attach the cross member.
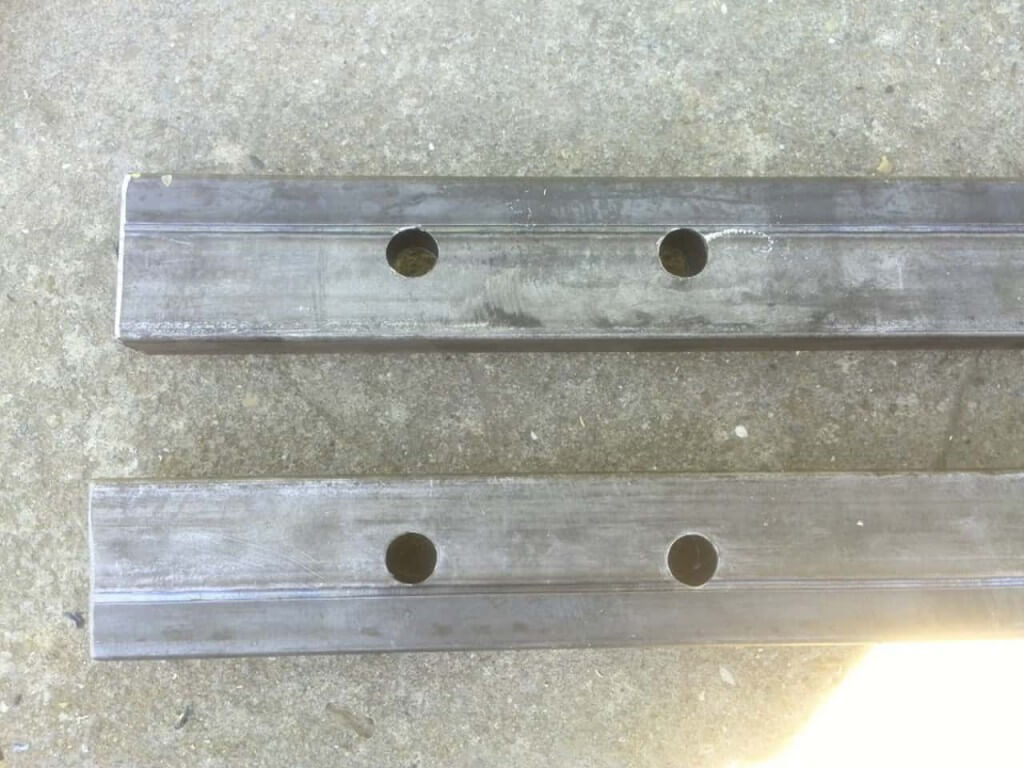
The next stage is the preparation of metal plates, with the help of which we will fix the crossbars for the trunk made by us.
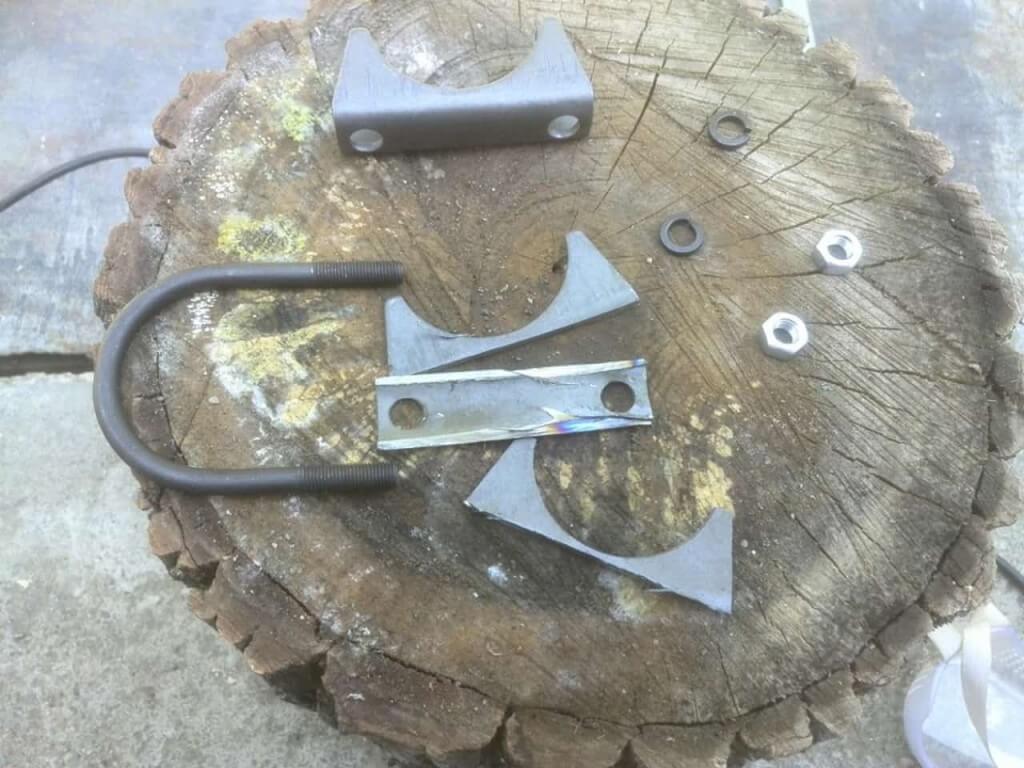
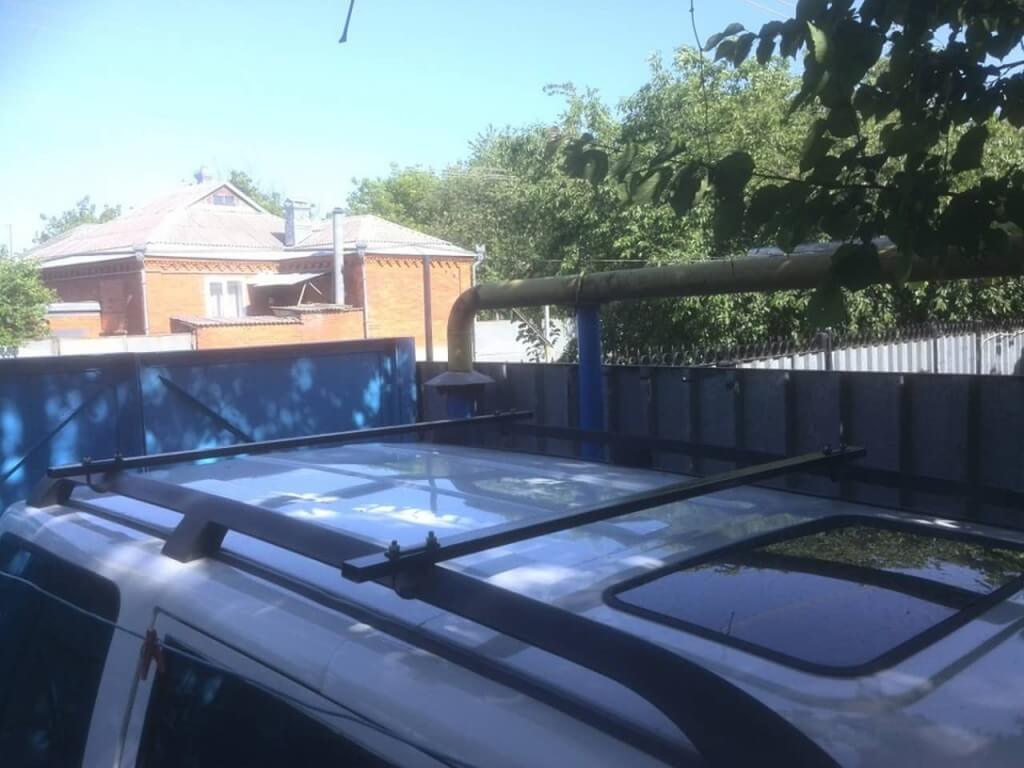
This type of rack is recommended to be used only during the carriage of luggage, because, due to its poor aerodynamic properties, it is possible that extraneous noise will be generated while driving.
Option number 2... This option will not be as practical as the first, and will require breaking the integrity of the car's roof rails. So, we need:
- shaped tube made of aluminum;
- anchors, with hooks at the end;
- screws M6 (M8).
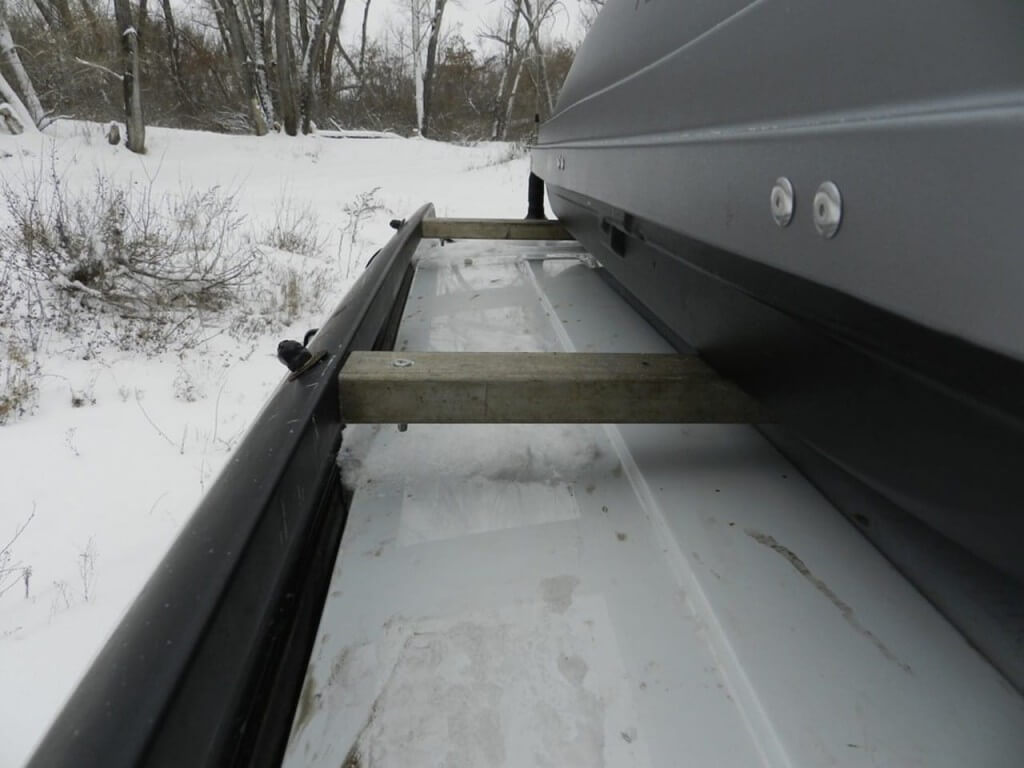
The process of making crossbars with your own hands will be as follows:
- An aluminum profile (50 * 25mm, wall thickness - 3 mm) is cut to the length we need (the distance between the rails).
- Drill holes in the profile for M6 screws and take into account the length of the anchor bolt.
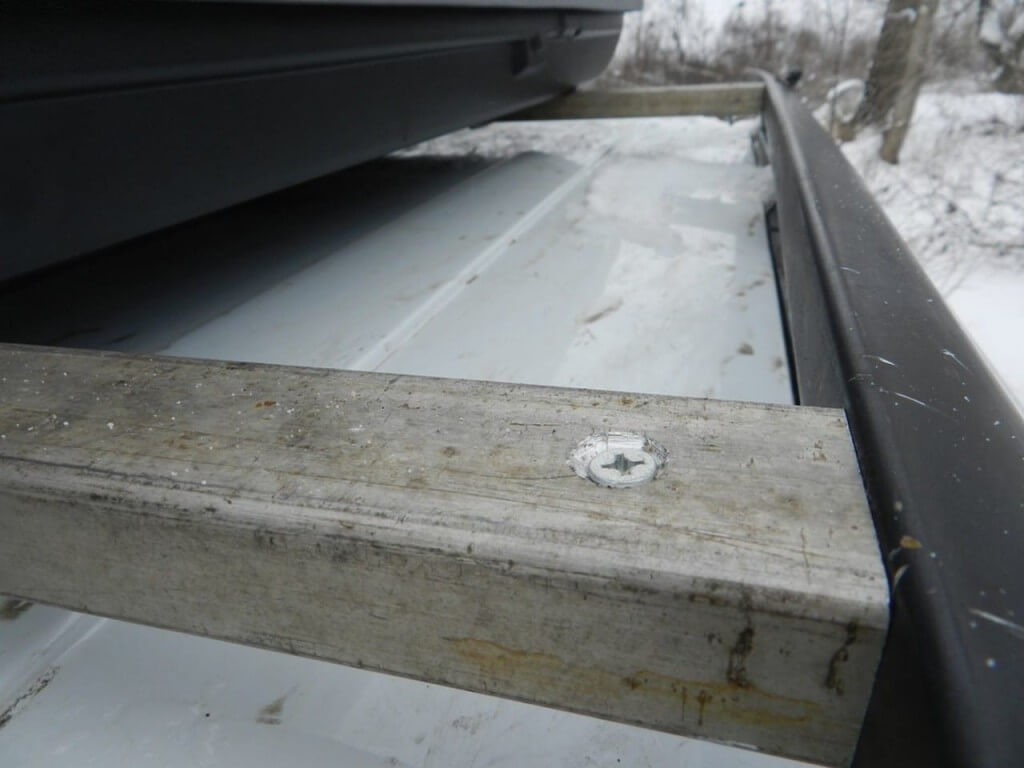
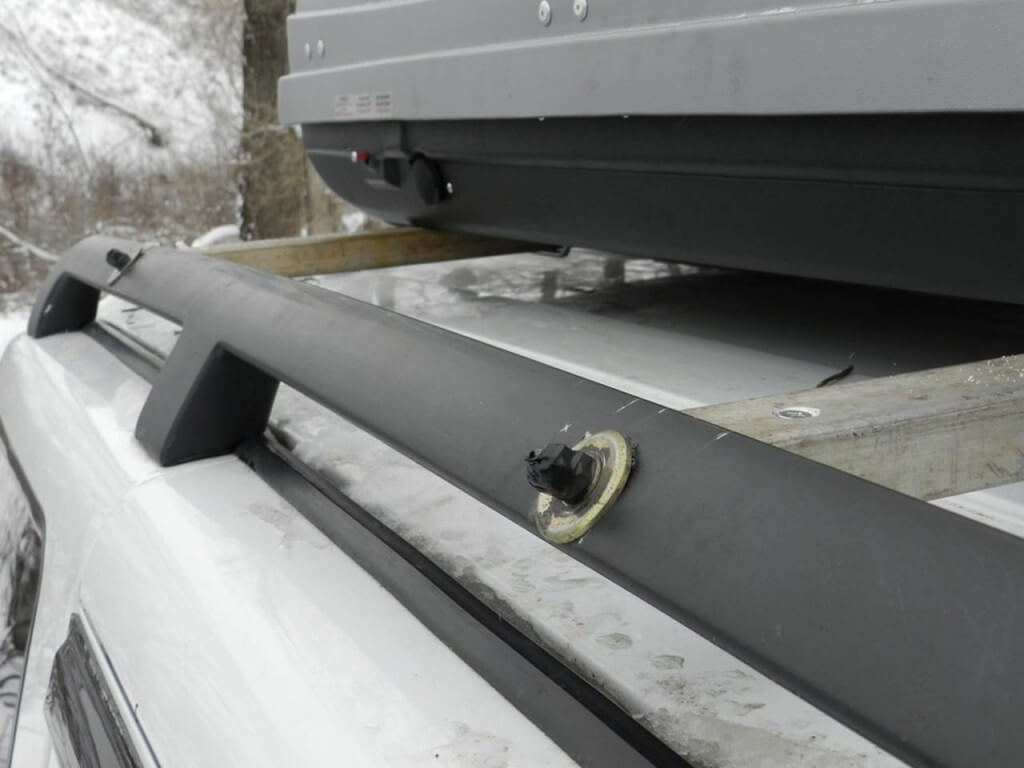
The next step is tightening the M6 bolts, and only then - the M8 anchors. In advance, you need to put enlarged washers under them in order to increase the pressure area at the attachment points. For insurance, so that the bolts do not loosen while driving, it is recommended to counter them.
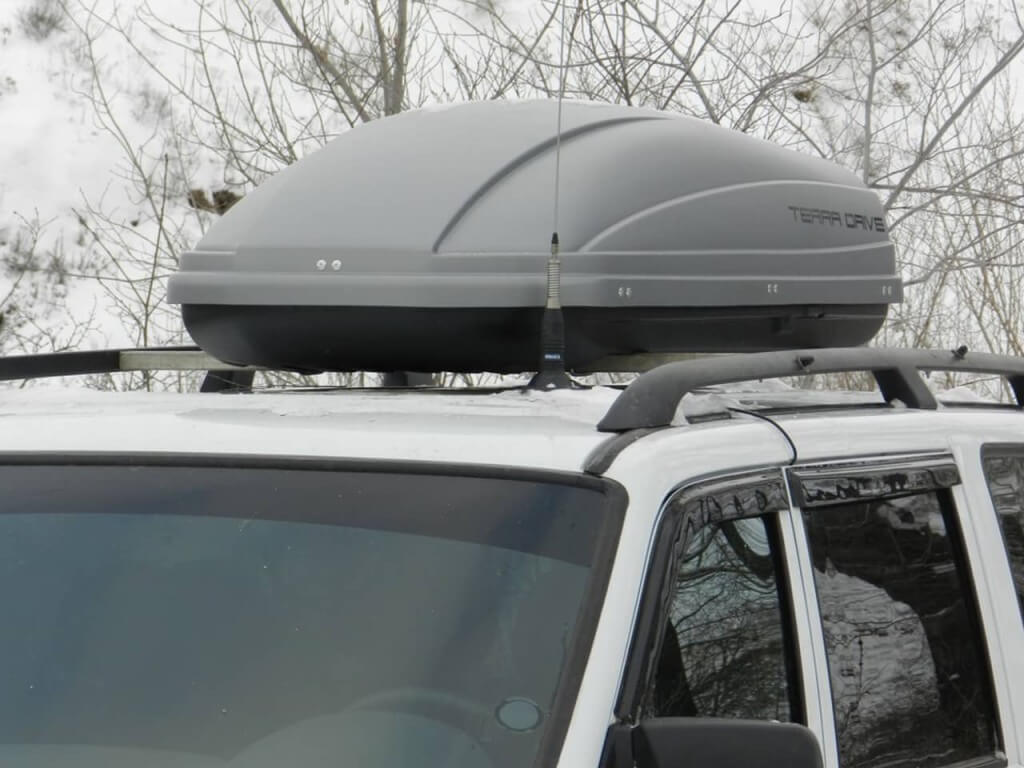
This process of making and installing the cross members is recommended in case of continuous use. After dismantling the crossbars, the appearance of the car deteriorates due to the drilled rails.
Option number 3... This option will be more practical, since the materials used in it have a more streamlined shape. Therefore, virtually no noise is generated when the vehicle is moving. But the maximum carrying capacity of these cross members does not exceed 60 kg.By slightly strengthening the method presented below, it will be possible to load up to 90 kg. But this will require additional costs. To make crossbars, we need:
-
furniture profile, wall thickness - at least 1 mm;
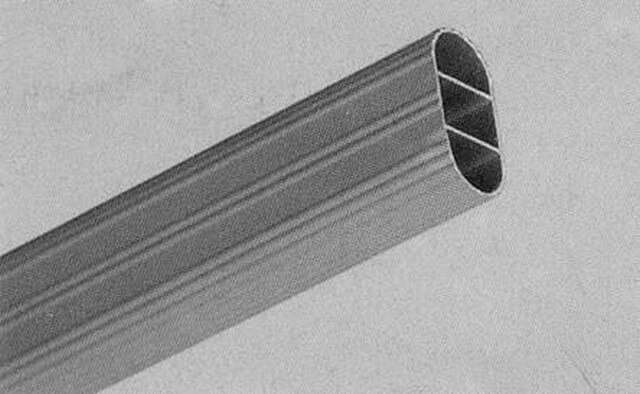
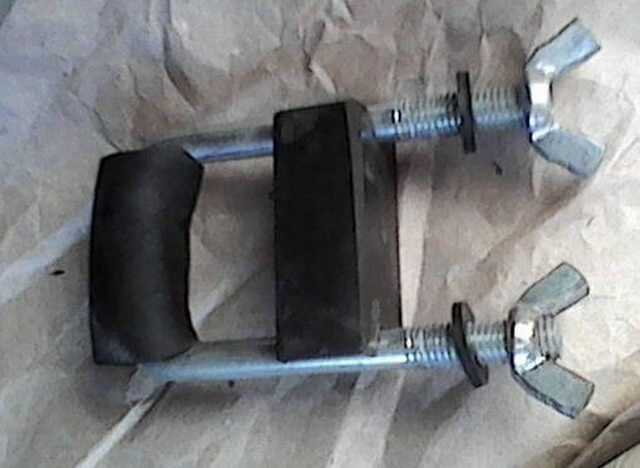
The very process of making crossbars for roof rails will be quite simple. The main thing is to make the correct measurements and not be mistaken:
-
Drill holes in the profile taking into account the profile width and the diameter of the U-shaped mount.
![]() |
Video (click to play). |
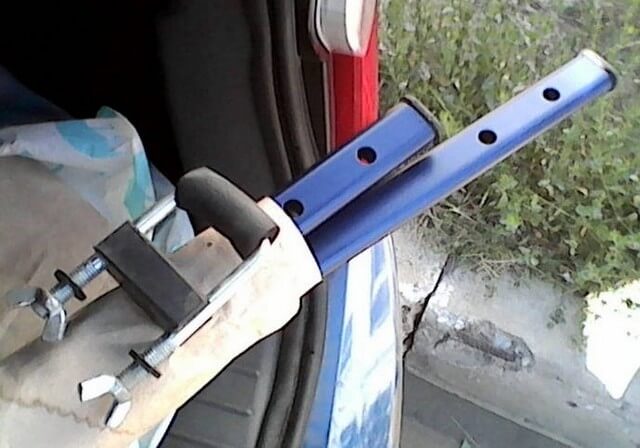
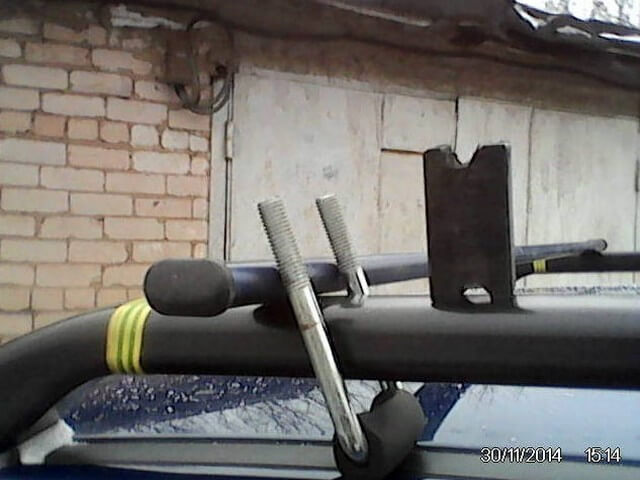
The next step is the process of assembling the entire structure and installing it on the car rails. For this, the fasteners are installed under the car rails. The cross member is put on the holes drilled in advance. A sealing, insulating material - rubber - is placed between the rails and crossbeams. After that, everything is clamped.
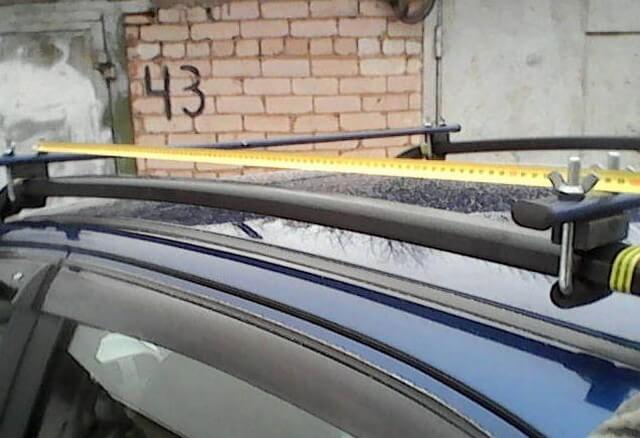
This crossbeam manufacturing process is fairly straightforward and does not require any special skills. Also, the advantages of these crossbars for installing the luggage rack are that they can be installed at different distances, depending on the transported goods and the make of the car.
Option number 4... In this case, it is necessary that there are specially designed mounting holes in the car rails. For the manufacture of crossbars for the trunk, we need experience in welding. We list the materials required to create crossbars:
- aerodynamic profile;
- metal corner 50 * 50 * 4 mm;
- consumables: bolts, nuts, washers;
- paint, gloves, brush;
- protective equipment for eyes and respiratory organs.
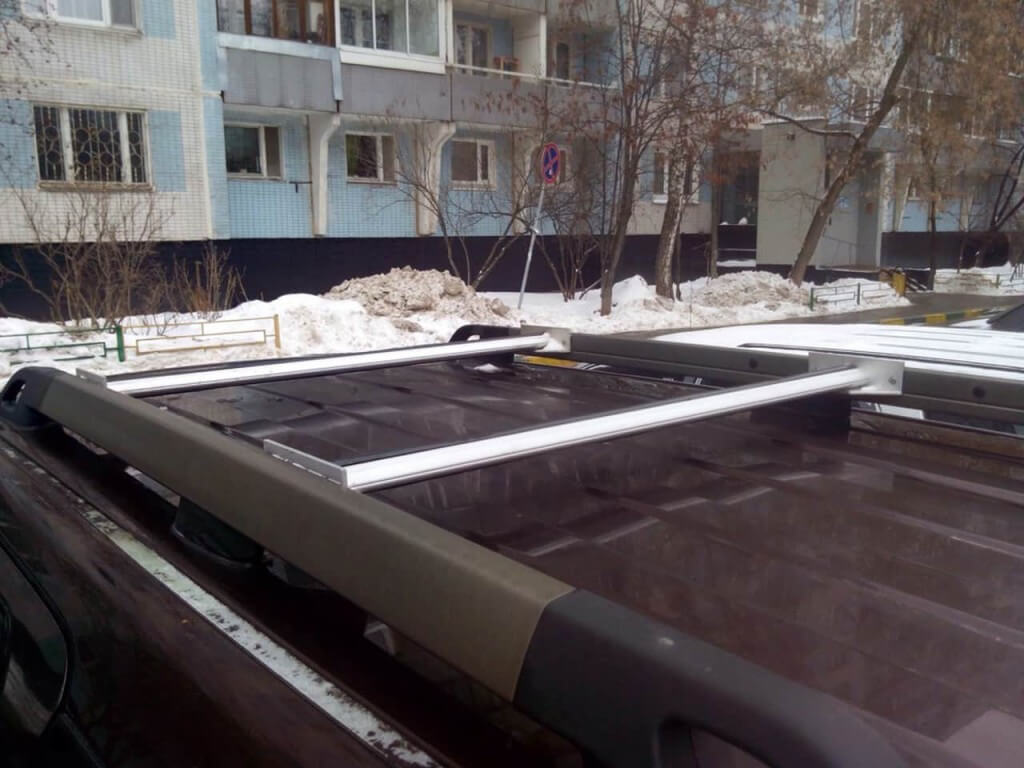
The manufacturing process itself will be as follows:
- The profile is cut to a measured length, taking into account the corners welded on the sides.
- The corner is cut to a length of 20-25 cm. Holes for the fastening bolts are immediately marked on it. It is also recommended to drill them out before welding.
- Next, you need to weld the profile and prepared corners. All welded seams are cleaned and bounced off the slag, and the drilled holes are treated with anticorrosive material.
- It is advisable to paint the finished structure. Do not paint the freshly welded surface, as this will lead to its rapid peeling.
- After complete drying, you can mount everything in its place.
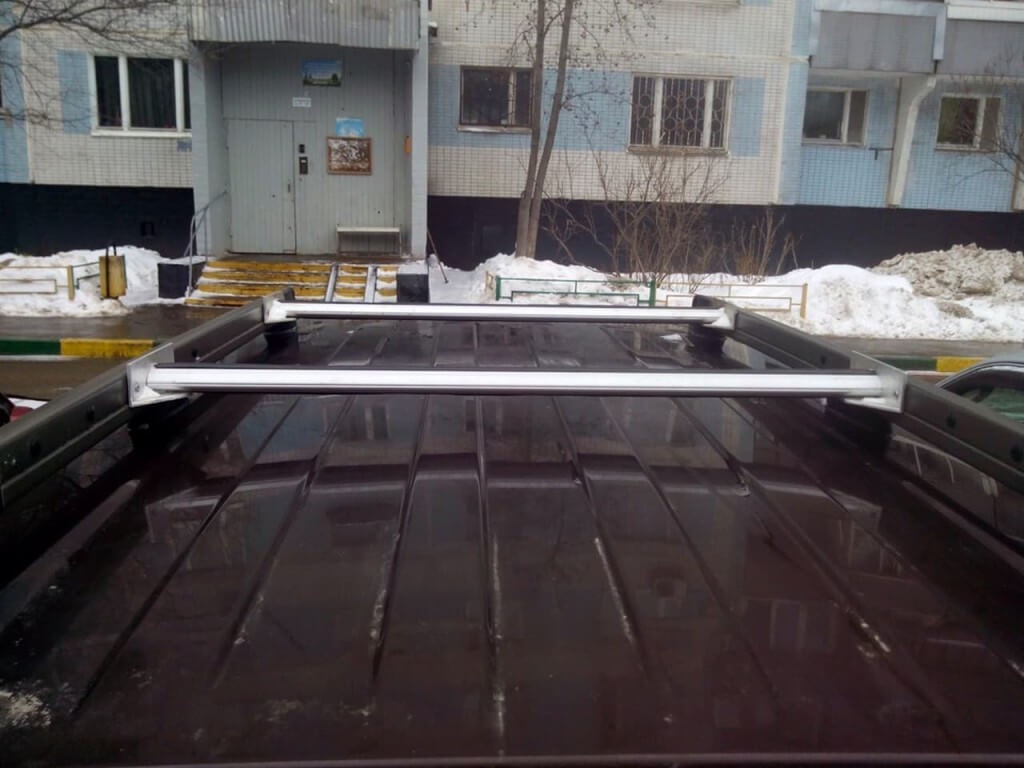
As can be noted from the experience of drivers, such a fastening of the crossbars does not create additional noise when the car is moving at a speed of more than 100 km / h. Also, the manufacturing process itself will not take you more than 2 hours. And installation and dismantling, if necessary, can be done within 10 minutes.
As you can see, making roof crossbars with your own hands is quite simple. This process requires the ability to work with a power tool, precision, a little time (no more than 2-3 hours), and skillful hands. Making your own crossbars will cost you 2 or even 3 times cheaper than buying them in specialized stores.
Friends,
In general, ripe for homemade roof rails, here are the primary thoughts.
First, I removed the cover that covers the groove of the rails. Strange, but it turned out to be rubber, without a metal skeleton.
Measured the required distance between the bolts. Another point - on the roof, in two places, films are glued that start from the edge and close these covers.They interfere with shooting, you will have to cut it off. Why is this done? The only explanation in my head is to fasten the crossbars, and not to scratch the paintwork, right?
Sketched a drawing of the roof railing. There may be a millimeter or two difference in size, all this must be corrected during assembly. The idea is this - a 3/4 ″ pipe is welded on three bases, the bases are hidden in a groove, only a hole for the pipe is cut off on the lid, so it looks like the pipe is coming out of the roof. The fasteners are hidden under the cover.
Material - stainless steel. Here is the question in my head spinning - to polish to a shine, matte, paint or cover with a film? 🙂
And another question is spinning - is it worth it to immediately make the crossbars and weld? In principle, rigidity will be added, and there is no need to buy additional left cross members. Like this:
I would be glad to have ideas and constructive criticism.
Yes, the reason for this whole collective farm is either the absolute lack of a subject within a radius of several hundred kilometers, or the exorbitant price of a couple of copies. According to preliminary estimates, the collective farm will require about 6-7m of stainless steel, at a price of something like $ 6 per meter. Work (pipe bender, welding) is almost free.
Every person at least once in his life has seen a car on the roof of which roof rails are installed, i.e. special slats (skids), with the help of which the transportation of bulky household goods is carried out. In addition, roof rails allow you to transport sports equipment and camping equipment at various distances. Often, such additional elements are used as the basis for a car box. It should be noted that the installation of roof rails on the vehicle gives the interior a sporty look and makes the vehicle more individual.
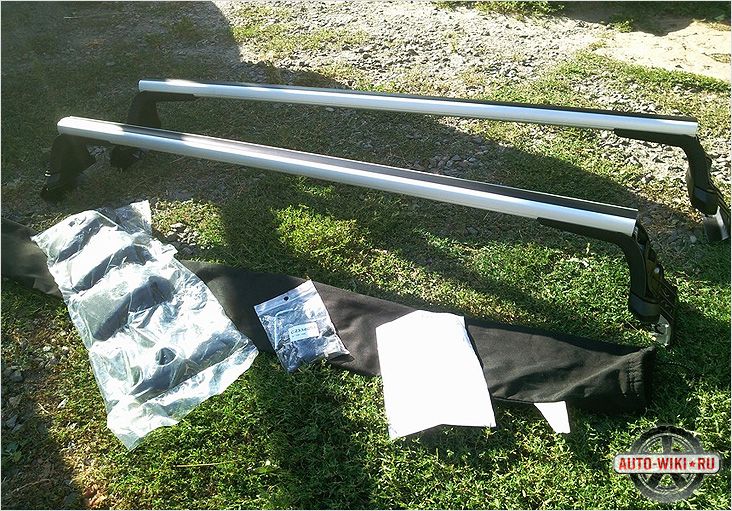
Today, in numerous specialized stores, a variety of both model and universal roof rails are presented. Their difference lies in the fact that model fixing elements are made for a specific brand of car, so it is not possible to mount them on other cars. Universal fastening elements are designed for installation on most modern vehicles of domestic and foreign manufacturers. There are two types of roof rails placement: transverse and longitudinal.
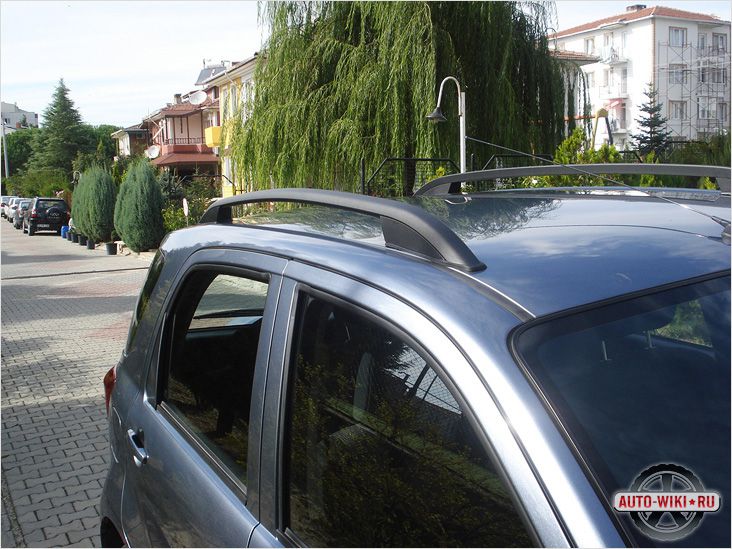
A standard rail consists of the following elements:
- The main pipe, the diameter of which most often varies from 25 to 51 mm.
- Holders (2 pcs.).
- Plugs (2pcs).
Anchoring elements can be made of plastic, steel or a combination of these materials. A layer of specialized powder paint is applied to their surface, which minimizes the negative effects of high humidity, ultraviolet radiation and changes in ambient temperature.
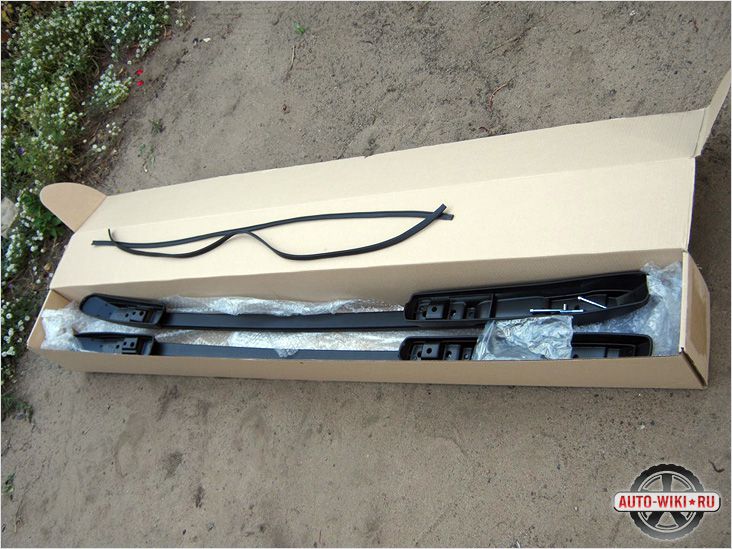
Practice shows that it is best to entrust the installation of roof rails to specialists who have professional knowledge and a sufficient amount of experience in this matter. In addition, service station workers are responsible for the quality of the work performed, therefore, if any defects are identified, their elimination will be carried out at their expense.
If for some reason it is not possible to contact the specialists, then you can try to install the roof rails yourself. The first thing to do in the case of installing fastening elements with your own hands is to find out if there are seats for them on the roof of the car. If such holes are provided in the car structure, then they are hidden under protective plugs, which are quite easy to remove. To do this, pull the plugs in the direction indicated by the arrows on them and pull them up. Further, regular holes must be cleaned of dust particles and degreased, after which a layer of silicone sealant used for outdoor work is applied to the seats.If the holes are not carefully sealed, there is a high probability that moisture will get into the interior of the car over time. At the final stage, the roof rails are attached to the prepared surface of the car body.
It is much more difficult to install roof rails on a car, the design of which does not provide for the presence of standard holes for fastening elements on the roof.
It is recommended to install roof rails only on condition that they will be on the car all the time, because for their installation in the roof of the vehicle, several holes must be drilled.
Immediately before installation, it is necessary to carry out preparatory work, namely:
- Thoroughly clean the roof of the car from dirt and dust;
- Degrease the body surface to which the roof rails will be attached;
- Remove the headliner.
After completing the preparatory work, you can start drilling holes in the body. In order not to have to drill extra holes, it is necessary to carefully calculate the places of future seats for the roof rails. To protect the body paint from hot chips that form during drilling, you can use masking tape, which must be glued to the roof surface around future holes.
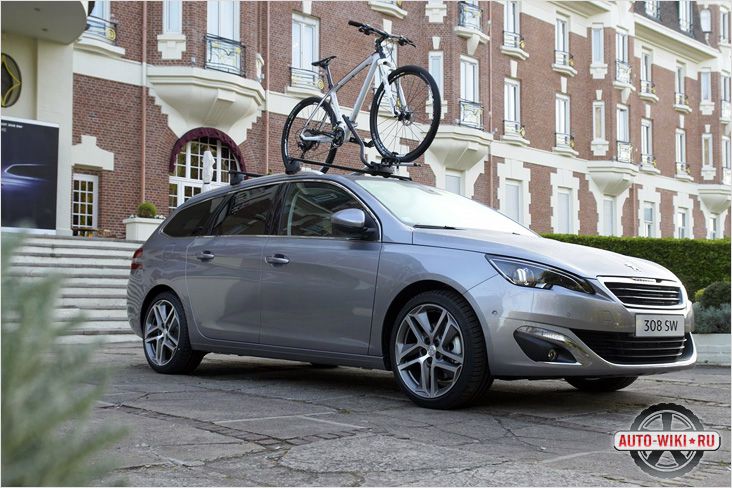
In order for car rails to serve as long as possible, motorists must follow simple rules:
- It is recommended to transport the first load on the fastening elements no earlier than 24 hours after their installation;
- Before each trip, you need to check how firmly the roof rails are attached to the car body;
- Cargo transported on rails must be evenly distributed over them and carefully secured;
- The maximum carrying capacity of the roof rails must not be exceeded.
Compliance with the last paragraph of the rules is most important.
Experts do not recommend transporting cargo on rails, the weight of which exceeds 70-80 kg, because overloading can cause the most negative consequences, from a skewed vehicle roof to deformation of doorways.
If any difficulties arise during the installation of roof rails, then there are at least two ways to solve any problems:
- seek help from third-party specialists;
- study step-by-step photos and videos on self-installation of fastening elements on the roof of a car.
Installation of Voyager roof rails on TOYOTA Land Cruiser Prado 150:
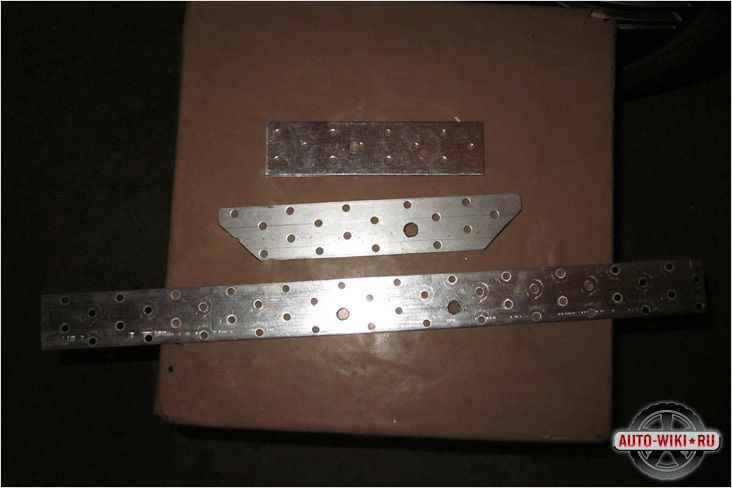
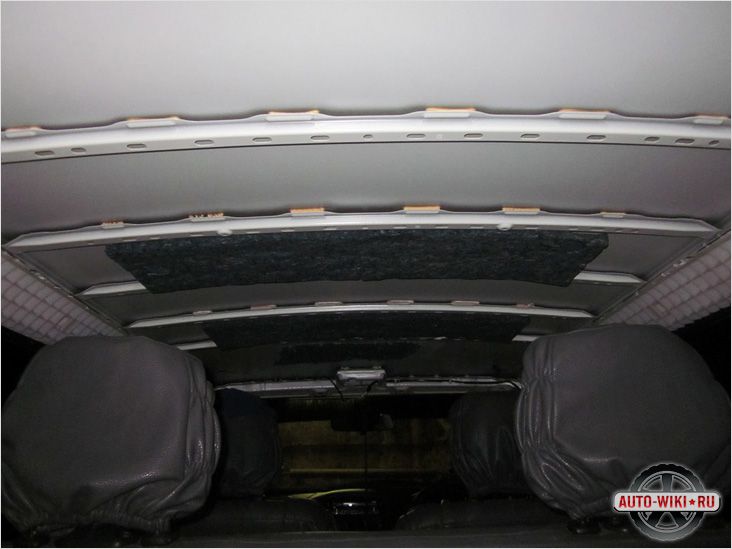
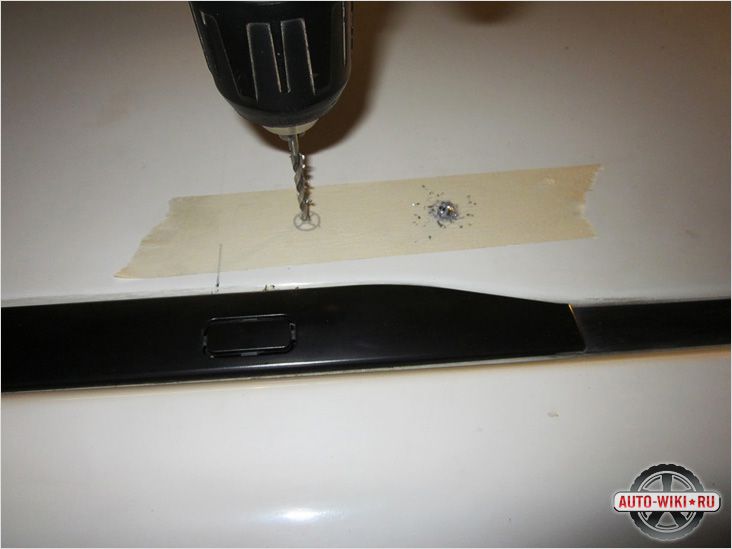
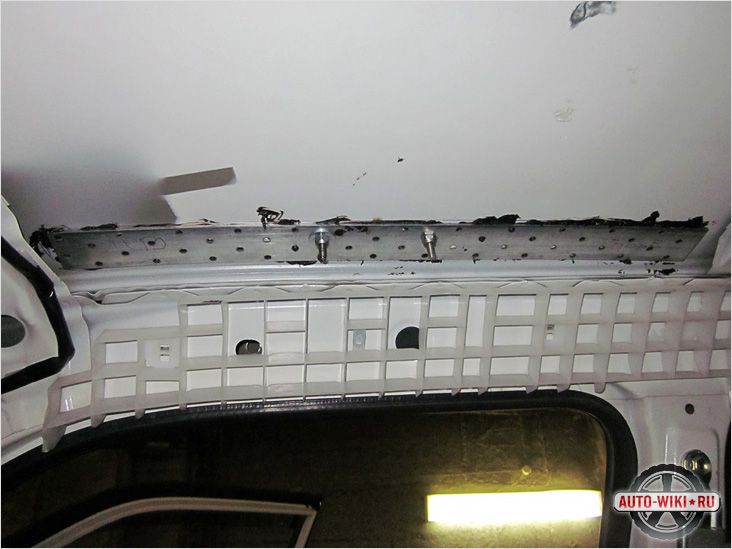
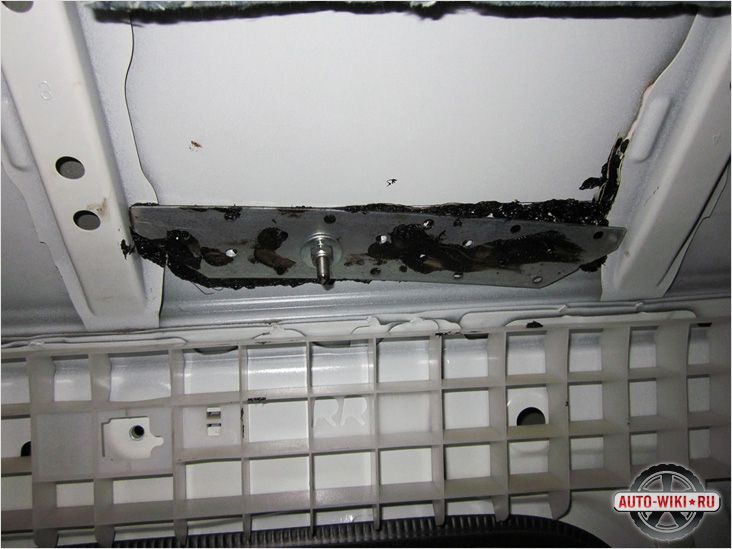
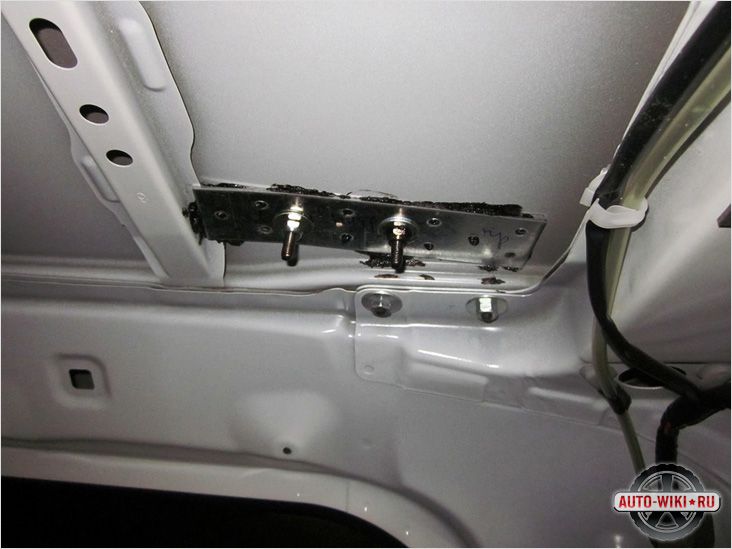
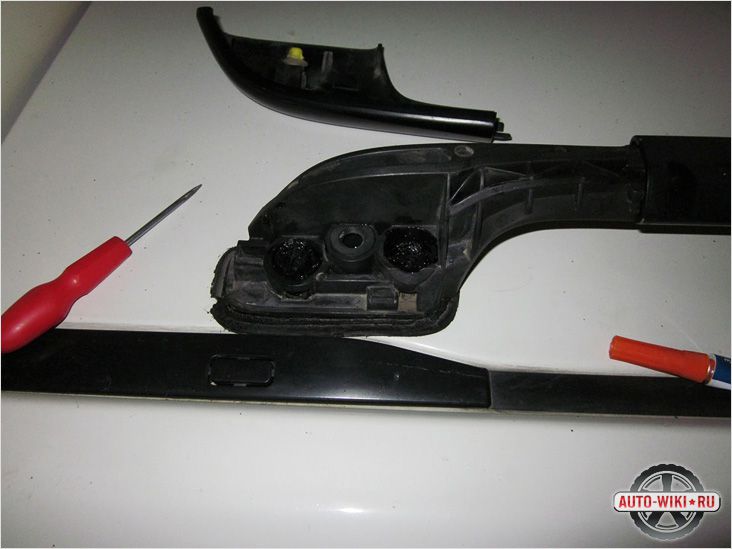
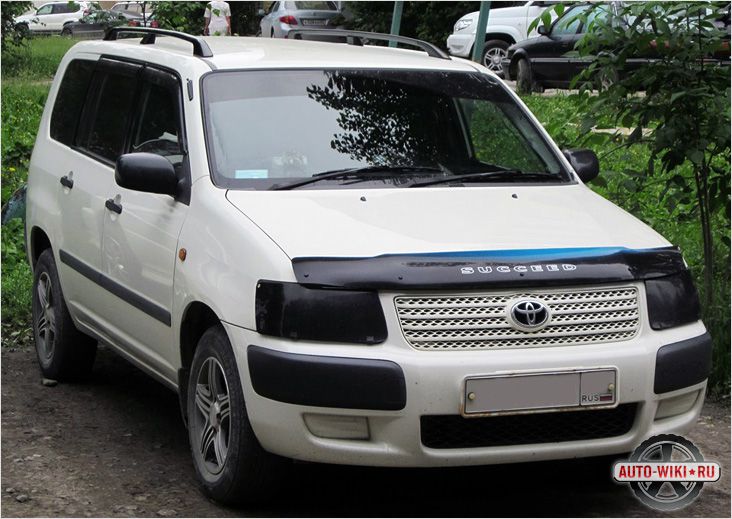
Indeed, the designers could make the VAZ 2111 roof rails more attractive, and when the station wagon is not at all suburban, then these horns only start to spoil the view.
Hello everyone! My name is Mikhail, now I'll tell you a story about how I managed to exchange a dvenashka for a 2010 Camry. It all started with the fact that I was wildly annoyed by the breakdowns of the two, like nothing serious broke, but on little things, damn it, so many things that really started to enrage. Here the idea was born that it was time to change the car to a foreign car. The choice fell on the tayet Camry of the tenths.
Station wagon roof rack fixed with M10 bolts.
To remove the roof rails VAZ 2111 you will need to partially remove the headliner (bend it) and unscrew the fastening bolts.
If, nevertheless, you decide to remove the entire headlining, then you can immediately perform the soundproofing of the roof.
Close the holes from the roof rails in different ways:
The easiest way close the holes in the roof using rubber plugs for 10mm holes (found in any auto shop). Naturally, a car sealant should be used. Special thanks for providing a photo of Kir-kuk.
Or use ordinary plastic covers, according to the author, they do not allow water to pass through even without a sealant, and the holes in the center of the plugs are not through.
It's okay but rubber roof plug will stand out because it cannot be painted over.
Another way cover openings in the roof looks more secretive. It is necessary to cover the holes from the passenger compartment with rubber, and then cover it with sealant from above. Once dry, this area can be painted in body color.
You will need 4 furniture bolts with a semicircular head no more than 30mm long. We insert the bolts into the roof using automotive sealant, and fix it with nuts from the inside. Paint the bolt surfaces with a brush. Everything is reliable and tidy.
All three methods have been tested for 3 years and have shown their reliability, rust on the roof didn’t appear, and it’s not the underbody of a car to rust so quickly. 🙂
Close the holes from the roof rails VAZ 2111 after removing the roof rails, it is possible in a more complex way, for example, degreasing, priming and painting, this is everyone's business.
VAZ 2111 without roof rails quite another matter!
In order to get rid of constant fines from cameras, many of our readers successfully use Special Nano Film for numbers. Legal and 100% reliable way to protect yourself from fines. Having familiarized ourselves and carefully studying this method, we decided to offer it to you as well.
In order to get rid of constant fines from cameras, many of our readers successfully use Special Nano Film for numbers. Legal and 100% reliable way to protect yourself from fines. Having familiarized ourselves and carefully studying this method, we decided to offer it to you as well.