In detail: do-it-yourself spring repair from a real master for the site my.housecope.com.
Springs, like all other parts, are an important element of the car device, which must be monitored and any malfunctions prevented in time. Without them, driving a car would not be relatively smooth, especially on our roads. You don't need to think that the parts of your car cannot be killed. Each of them requires certain attention and prophylaxis in order to avoid rapid wear, the necessary repair of the springs must be carried out on time.
The necessary inspection and repairs can always be done in the workshop, but it is not too difficult to do it with your own hands. If, for example, there is a drawdown, then you can install another rooted sheet with buffers-bumpers of the lower arm of the front suspension, for this it is enough to unscrew the nuts of the central bolt and stepladders.
Every 10,000 km, it is recommended to remove the springs to clean them of dirt, rust and for deep lubrication (first washed in kerosene, then a mixture of graphite grease and grease is applied), it is also recommended to regularly lubricate the sheets and tighten the ladders. In order to avoid the appearance of rust, it should be painted before reinstalling the suspension element.
To extend the life of the part under heavy loads on the car, you should protect the springs by wrapping them with twine soaked in resin and putting on a tarpaulin cover filled with grease.
Most often, the front suspension elements fail, since they are more loaded due to uneven road surfaces. Sheets or fingers of the spring can break, there is a subsidence, a breakdown of the bolts of the ladders. If the spring has burst, it must be replaced; if it bent, then the car body deviates to one side, which should not be allowed, the deformation is eliminated by editing according to the template. To know how to repair a spring, you first need to inspect it, which will give you an idea of which part is out of order.
![]() |
Video (click to play). |
Maintenance and repair of suspension springs for cars of the carriage layout of the UAZ-452 family consists in periodic checking of their condition and elimination of identified malfunctions. When servicing, check the tightness of the ladders of the springs, the bolts of the bracket covers, the riveted fastening of the brackets to the frame side members, as well as the condition of the springs themselves.
The springs should be systematically cleaned of dirt. When examining them, it is necessary to pay attention to the longitudinal displacement of the sheets, which may indicate a shear of the center bolt and the appearance of cracks in the sheets. Broken sheets must be replaced by removing and disassembling the spring. Settled springs that have whole sheets can be restored by straightening (straightening).
The deflection arrow (curvature) of the sheets is checked with a template. With a slight decrease in the deflection arrow, the sheets are straightened in the cold state by blows of a hammer on the inner surface of the sheet. Strong blows start from the middle of the sheet, moving towards the ends. As you get closer to the ends, the blows should be weaker.
The cups of the root leafs of the springs, which are not suitable for further exploitation, are replaced with new ones. On the UAZ-452 springs, the cups are riveted with an 8x16 rivet with a countersunk head. It is necessary to ensure that the countersunk head of the rivet does not protrude above the surface of the sheet. Clean it if necessary.
As needed, but at least once a year, or if the springs have been repaired, they should be lubricated. The lubricant prevents sheet corrosion, which is one of the main causes of spring breakage, increases suspension softness and eliminates friction between the sheets.For lubrication, it is necessary to remove the spring from the car, disassemble it, rinse it in kerosene, dry it with compressed air and thoroughly lubricate each sheet with graphite grease or a mixture consisting of 30% USS oil (grease), 30% graphite P and 40% transformer oil.
If it is not possible to remove the springs from the car, then in order to lubricate it is necessary to raise the front or rear end of the frame with a jack so that the wheels do not touch the surface. Then, pressing the ends of the leaf springs with a screwdriver, put grease in them.
It is necessary to periodically check the condition of the rubber cushions of the springs in the brackets. To do this, with a loaded car, unscrew the bolts securing the bracket covers, remove the covers and inspect the rubber cushions. The upper rubber pads usually wear out the side tabs, which are notched by the sides of the cups. These pillows do not need to be changed. The cushions do not require replacement, in which the jumper is cut at the point of its connection with the upper part of the cushion.
If significant wear or destruction of the spring cushions is found, they must be replaced with new ones. It is especially necessary to monitor the condition of the cushions of the front springs, since significant wear on the bearing surface of the cushions causes the wheels to wobble and impairs the vehicle's handling.
Install the spring bracket covers and tighten the bolts with the spring straightened, otherwise the pillows may take the wrong position and quickly fail. You can use a special device to straighten the spring.
Failure to replace worn-out rubber pads also causes destruction of the spring brackets attached to the frame. Loose rivets of the spring brackets must be replaced with new rivets of larger diameter or bolts.
To repair the springs, it is necessary to remove them from the car and disassemble. To remove the spring, place the car on the inspection pit and perform the following operations:
- set the front or rear part of the car on stands, crush the wheel, disconnect and swing up the shock absorber lever,
- raise the front or rear axle with a jack,
- unscrew the fastening nuts and remove the ladders,
- unscrew the bolts securing the covers of the supports of the front and rear ends of the spring and remove the covers,
- remove the spring together with the rubber cushions.
After disassembling, cleaning and washing the springs, it is necessary to check their condition and determine their suitability for further work. The springs of the UAZ-452 vehicle must be sorted according to the size of the deflection boom under a load of 600 kg into two groups: Group I - deflection boom 15-25 mm, Group II - deflection boom 15-5 mm. The assembled spring is upset with a test load from its free state to the deflection value indicated in the table below.
Back to the car, the springs are installed in the reverse order of removal. Before installing the springs in the support bodies, they must be straightened. To do this, use a jack or a special device. When installing the springs, attention should be paid to the position of the cups riveted to the ends of the root sheets. Fully enclosed cups at the front spring should be located at the front movable end and at the rear spring at the rear movable end.
After disassembling and changing defective sheets, before assembling the spring, its sheets must be lubricated. Punch out the threaded end of the spring center bolt or crush it off the end with hammer blows. The rivet end of the clamp after riveting to the leaf of the spring should not protrude above the surface of the leaf.
Spring clamps after compression should not impede free movement of sheets during spring operation. After assembly, paint the spring with enamel. Tighten the bolts of the covers of the spring brackets and the nuts of the ladders after the springs settle from the weight of the car.
- Major malfunctions, removal and replacement of springs in the car
- Vehicle springs malfunctions
- DIY spring repair
- Bulkhead spring
• cracks and breakage of the suspension plate;
Settlement of springs occurs due to loss of elasticity or sheet fractures. In this case, you can make a temporary repair: take two wrenches, one will be on top of the sheet, the second on the bottom, wrap them tightly with wire - the tire is ready.
Temporary repair in case of broken finger: you need to install any iron rod (screwdriver), wind it with wire. This will allow you to remove the breakdown and drive to the place of major repair. For self-repair on the road, use special bridges. They consist of a forged part and two tension springs. This kit allows you to make a part yourself.
Disassembly and installation:
1. The suspension is clamped in a vice, the clamp is removed;
2. Take out the center bolt;
3. Disconnect the sheets.
All small parts are carefully examined, cleaned of dirt and rust, lubricated, replaced. Let's figure out how to lubricate the spring parts. To do this, the car body is lifted on a jack, the lower ends of the shock absorbers are disconnected from the suspension linings and the sheets are lubricated with thick oil.
Unique cars for unique people
Message Andrews6666 "15 Dec 2015, 18:24
I have long had a desire to do something with the springs of my IZH. Because when landing on the back seat of 2 passengers, the stern fell indecently. I was looking for information, someone adds sheets to a package of springs, someone inserts springs. Someone just buys new springs in the store. But I doubted something about these methods and continued to search. And almost by accident I came across the page of one owner of Moskvich 2140 “Messer”On Here it is - And there the author outlined the whole essence of the process, as it seems to me, in extremely detailed and understandable way. I decided to restore the springs of my IZH in the same way. Basically, I did everything as the author describes, but with minor digressions, which I will discuss below. With the permission of the author of that page, Roman Polina, I will describe his method here. I will use the text and photos of the author. My personal add-ons will be highlighted.
Traveling across the vast expanses of the Community, I have repeatedly encountered a problem that prevents respected Moskvichevods from using their favorites normally! We are talking about "sagging" springs and how to solve this important issue. Many try to raise the "stern" by installing additional sheets in the springs, or springs. The effect is partly there, but at what cost ?! Our "tired" bodies are tearing alive! Everyone has heard stories about the springs that have fallen into the salon, the torn off "ears" and even the spars that have burst! I myself have never put any sheets or springs and I think this is absolutely unpromising! My way is to return the working capacity of the standard springs, by the method of “cold” forging (in the people, “coil”).
Two springs stood on Messer, butt lay on the floor.
The resulting sharp tip grinded off a bit and rounded the edges to make it look a bit like the edge of a ball. I must say for the entire time of work on the springs, this tip did not flatten at all. And this hammer didn't even fly off the handle, it just moved a little and that's it.
Sent after 15 minutes 38 seconds:
Preparing the battlefield! I take out a poplar stump into the street (he lives in my garage), put yews on it (I was so strong and broke them long ago ... now I don’t mind ...), next to a chair and a “soloist”,dragging the root sheet onto the operating table and - and applying secret signs on the patient's body (with the help of a matchbox and chalk) Box-50mm. (it was not at hand), we mark the sectors of "shelling" On the mounting hole, do not pound! (and in general ... no fanaticism!) "Vaccinations" (from fatigue), we begin to put from the center to the edges. 5 pieces per sector, measured, calm (not with all the foolishness!) Blows. By the end of the execution, all the neighbors will fall in love with the song "Evening Bells ..."
Here you can adapt a lot of things, screw any thick pieces of iron with even edges with long large (200 mm) self-tapping screws to the stump. I do not advise screwing on with small screws, the caps fly off from shocks and vibrations.
Sent after 18 minutes 56 seconds:
The first layer of grafts is delivered. By time 5-7 minutes.
INSTRUCTIONS: between the root sheet and sheet-2, the gap (center) is 35mm. Since each subsequent sheet is shorter than the previous one and we need to “catch” the exact gaps. Changing the style of applying "vaccinations!" Namely! We do not hit 5 (in the sector), but once, exactly along the entire length, after about 1 cm (of course, from the center to the edges) This style is preserved until the end of the process!
We continue the conversation. We “pull back” sheet N-2 to the state of damask steel. Forged, insufficient clearance. Let's continue!
The first, root leaf came to the required size in 1 pass and with relatively weak blows. Each subsequent sheet was “forged” more and more difficult. And you need more force, and make more passes, and the obstinate spring rewards the hand with an amazing impact. On this occasion, advice from my experience. Winding up a ton of rags has little effect. It is better to take a piece of sponge from the old seat, cut out a “brick” with dimensions of about 150x200x100 mm. And at the end, make a through cut with a knife, string this brick onto the spring and hold it through it. I also noticed that if you hold the sheet not by the edge, but closer to the place of impact, as much as possible, the recoil is less.
It's time to put the mounting bolt back in place. Long (m-8) stud and workshop clamp (center stud)
Yes! The result is obvious! And the result is excellent! There is nothing left to grab and set in place! And the "steepness" and-and-and ... will not rise! Precisely because it is “cool”, it is impossible to stretch from “ears” to stepladders! To solve the problem, we take out an easy-to-make device from the shelf.
Brief description of the design: 2 40 corners, length - 1215mm. "Gripped" by welding (at the edges) with 15mm spacers. Holes 15 - 16mm. Distances between holes (centers) - 1130mm .; 2 "ladders" (long) rod - 14th, total length - 335mm. Of these, the threads are 160mm m14. Distance between threads - 50mm .; 2 "cock", between the threads - 50mm. The total length is 85mm. Of these, the threads are 50mm, the rest of the lintel is 5mm steel. Washers plate steel-5mm.
We put the spring in a tied state on the car, and after all the fasteners are installed, we will remove it.
Of course, I didn't have such a device, and there was no welding to make it. I used a less technologically advanced method, but it worked nonetheless. The finished assembled spring was fixed in the attachment eyelet, in the one that is closer to the front of the car. Raised the spring until it touched the second eyelet of the side member under the boot floor. Under the bottom of the spring, in the area of the central mounting bolt, I put a rhombic jack. And he began to slowly raise, the spring straightened and the free eye crawled along the spar to meet the “earring”.
When I crawled close enough, I simply inserted the earring, screwed its mount and lowered the jack.
Sent after 12 minutes 6 seconds:
And now some tips and tricks. I "beat off" the root sheet by 230mm. Forget about it! (beat for his own purposes) The exact dimensions are as follows: root 180-200 mm. other dimensions in force: 35-25-15-5 mm. And the last (short) leaf is tight!
I beat off the root sheet by 230 mm, as did the author.Because I often go with passengers in the back and a load in the trunk.
IMPORTANT! The edges of the springs (where the holes for the gaskets are not “pounded!”), When the second spring is ready, it turns out that one of the two will definitely be “higher!” This is fine! (the hand of the blacksmith is not an “automatic”) We put the “high” one on the driver's side! (everything will be fine.) After installing the springs on the car, do not try to “put on” the amorts. Will not work! Tie them up with a string and quietly ride around the garages, on the very first bump of feed it will "sit"
I did so, loaded about 40 bricks into the trunk, and jumped on the towbar, the feed sat down. The rear spring lugs are “unstuck” from the side members and take a more natural position. I unloaded the bricks immediately, I didn't go with them.
You will see that the amorts are stretched out and dress close to each other. What to do? We don't put any sandbags in the trunk! We immediately take the 50th corner, cut 4 pieces (the reference point is the upper ears of the shock absorbers) We take (by welding) the pieces into a “square” and prepare the spacers (between the ears and the body) That's it! Enjoying the view of the road (and not looking at the pulled-up hood) And one last request. Guys! Each additional leaf is a terrible force! And she needs to “play” somewhere, the body of a Muscovite is strong, but there is a limit to everything - it will RAP! (a matter of time) And an additional spring (on the rear axle), it's like bending a stick over the knee, two spring attachment points + a spring in the middle. Well, where to go to the bridge ?!
Thank you all for your attention, Good luck!
Sent after 6 minutes 51 seconds:
And here is a photo of my car before the springs were restored
The angle is a little different, but I think the difference is noticeable.
In this position, the spring earrings on an empty car
Repair of springs should be carried out if necessary. To avoid this, it is necessary to disassemble them every 10,000 km and thoroughly clean them from dirt and rust. They clean the springs of the car with emery cloth and rinse them in kerosene. Before putting them back together, grease them with a mixture of grease and graphite.
Springs, like other car parts, need care
To protect the springs from rust, paint them with a quick-drying paint before reinstalling.
Spring pins and earring pins should be lubricated every 2 days using a grease pump. In this case, you need to carefully work with the spring pin and tighten the nuts with care to avoid breakage of the fingers due to their fragility. In particular, hammer blows do not need to be used.
To avoid breakdowns and accidents, the maintenance of the springs assumes that every 2 days it is necessary to check and tighten the ladders of the springs, with which the springs are attached to the front axle and the rear axle. In this case, the ladders should always be tightly tightened.
A little about the springs:
If the car works in difficult conditions, then to protect the springs, they are wrapped in tarred twine, and a canvas cover is put on them, which is stuffed with grease.
Most of the malfunctions occur on the front springs, as they are more often loaded due to jolts and uneven roads.
These malfunctions often take the form of a leaf spring breakage, their settling, breakage of the spring fingers and a breakdown of the stepladder bolt.
In the event of a burst spring, it is necessary to replace the springs. When the spring deflects, the car body tilts to one side, which, of course, is considered unacceptable. This deflection is eliminated by template straightening.
Springs do not last forever - they also have malfunctions
Due to the rather thick padding, the tapered head of the spring center bolt is very difficult to fit into the axle groove that is intended for it. As a result, the spring slides back and forth along the axis. Stepladder nuts with not very thick spacers are not suitable for screwing on locknuts.
A further and great advantage of springs with sliding ends is that their effective working length is reduced in the event of an increase in the load, due to which they are better able to resist shocks.Sliding springs are not capable of receiving and transmitting push forces from the rear axle to the frame. Such springs act only as an elastic suspension for the car. Komnik places the ends of the root and root leaf springs in the bracket. Here the springs slide on the roller. Due to such a device, the tension of the springs is greatly weakened.
In springs with ears, the load is distributed over the cross-section of the sheet. In the above-described spring suspension, the load is perceived simultaneously by two sheets, due to which it is distributed over a larger section. This, in turn, increases the safety margin.
Spring shackles and pins are usually provided with nipples. Through them, they are periodically lubricated with a grease gun. In case of changing the spring pins, coat them with grease. In addition, the springs must be protected from rust.
Springs repair:
The color of the sheets should be renewed periodically if it is damaged. It is also necessary to lubricate the surfaces of some sheets that are in contact with each other. To perform this procedure, you need to put the car on a box or raise it on jacks not under the axle, but under the frame. In this case, the springs will be unloaded, and some sheets will disperse a little, thus, it will be possible to introduce a certain amount of grease or thick oil between them.
The leaf spring can break if it is not properly lubricated. Of course, such a spring pin will show signs of significant wear.
In the event that such a breakdown occurs on the way, then for the time required to get to the nearest workshop, you can put a rod, key, screwdriver or something like that in its place, and then tie it up with wire.
If there is a squeak or squeak of the spring fingers or sheets, we can talk about their insufficient lubrication. In case of breakage of the leaf spring on the way, you need to put 2 long wrenches on top and bottom of the broken leaf. The resulting structure must be tightly tied with wire. In this case, you need to go further very carefully.
Service the springs - they will serve you for a long time
Repair bridges are very practical, with the help of which you can quickly make and repair springs on the way. Such bridges contain a solid forged part and two spring tensioners.
Thus, the maintenance of the springs implies the periodic tightening of the ladder nuts and the lubrication of the leaf springs, which can be lubricated without removing them from the car. This is done by disconnecting the lower ends of the shock absorbers from the spring pads and raising the body so that the wheels are off the floor.
In addition, the springs must be removed once a year and disassembled for lubrication and cleaning.
You can safely leave your feedback and comments on our website.
V. Zhibutko's advice on how to manage sagging springs, published in the February issue of the magazine last year, aroused the interest of the owners of "Muscovites". The head of the AZLK design group S. LIPGART and the car enthusiast V. ANKUDINOV from Izhevsk responded with stories about other, more perfect ways to restore the shape and elasticity of springs.
We bring them to your attention.
The author of the mentioned note recommended bending the straightened leaf springs by placing them on the channel and striking them with a pitch of about 50 mm with a sledgehammer through a chisel-like mandrel. This method is fraught with unpleasant consequences. First, the strong deformation of the sheet at the impact sites noticeably reduces its fatigue strength. Secondly, dents in the sheet, remaining in the form of thin stripes, become stress concentrators and can cause cracks. This danger is intensified, since the previously flat surface of the sheet acquires a faceted shape. Finally, the author recommends increasing the deflection boom to 50 mm without specifying the shape of the sheet before straightening.
The method adopted in auto repair practice to restore sagging springs by auto-fretting is devoid of these shortcomings.
The sheet is placed on a slab or flat anvil, and a heavy hammer with a smooth, slightly convex striker strikes the concave side of the sheet, starting from the central hole. The area located at a distance of 40 to 70 mm on both sides of it is especially carefully forged. The more uniformly the impacts follow and the less each of them deforms the surface layer in relation to the adjacent area, the less the risk of sheet breakage.
As a result, the sheet will bend evenly, approaching in shape to an arc of constant radius.
Arrows of sheet deflection (their "height") should be within the limits established by the factory, since they are determined taking into account the required spring shape under load and ensuring fatigue strength. For spring sheets of "Moskvich", subjected to straightening, the following deflection arrows should be provided: the first (main) - 100 ... 130 mm on an arc with a length of 1150 mm, the second - 130 ... 150, the third - 100 ... 115, the fourth - 70 ... 80, the fifth - 35 ... 40, the sixth (bottom, rectangular section) - 5 ... 7 mm. In this case, the curvature of each subsequent sheet after the root must be greater than that of the one above it. To unload the sheet located above, it is necessary that the parts, before being pulled together by the center bolt, touch only at their ends through anti-squeak gaskets.
After straightening the sheets, assembling the spring and even a small mileage of the car, some spring settlement is natural, since the residual stresses are removed.
Taking this into account, one should not be afraid that the spring will be too “high” immediately after installation on the car. If it remains this way even after a run of several tens of kilometers, it will be unnecessarily rigid and may break prematurely due to an increase in real deformations.
Thus, the nature of the work and the durability of the restored spring largely depend on the correct work hardening of the sheets (the quality of the resulting surface) and the mutual coordination of the radii of curvature, and therefore, on the qualifications of the performer.
Restoring the original shape of the springs by simply bending the sheets does not give the desired result. From experience I know that after two or three months such a spring will sag again.
I restore the springs by forging the sheets. I must say right away that this requires certain skills, since the blows must be delivered accurate and of equal strength. The result is remarkable - the springs serve no worse, if not better than new ones, without losing their shape and rigidity for a long time. I have been driving the last restored springs of the Izhevsk "Moskvich" for four years with a heavy load and on bad roads, without complaining about the suspension.
How do I restore the spring?
I disassemble it, I clean all the sheets of rust and dirt. I lay each sheet with its concave side on an anvil, which is a steel blank with a diameter of 100-120 mm. I use a hammer to strike with a step of 5 ... 6 mm across the sheet, as shown in fig. 1. The force of impact must be such that a noticeable dent remains on the surface.
First, I forge the root sheet until the distance between its ends reaches 1150 mm (the deflection arrow is about 260 mm). I adjust the rest of the sheets in order to the one on top. At first I assembled a spring from all seven sheets, but its rigidity was excessive. I removed the two lower ones - it turned out what we needed.
A few words about the tool. This is a light sledgehammer (weight about 1.5 kg), on the firing pin of which a piece of steel (steel 45) rod 30 mm long and 18 mm in diameter, previously hardened, is welded. To prevent it from letting go during welding, it should be cooled with water. First, I forge the root sheet from the ends to the middle. I check the quality of work as follows. Having secured one end of the sheet, I press on the other to straighten the sheet. I let go and check how much its shape has changed (deflection arrow). If it is significant, I forge it again. And so on until I am convinced that the sheet retains the required curvature after unbending.
When assembling the spring, a simple device will come in handy - a hook with a crowbar (Fig. 2).Putting the hook on the ear of the spring, pass the crowbar through the hole in it and, resting the end on the leaf of the spring, press the other down, while lowering the jack. And one more piece of advice. To drown out the piercing, annoying ringing during operation, wrap the free ends of the anvil with a thick, damp cloth or place sandbags on them.
If you do everything right, the springs will not remind you of themselves for a long time.
From the editor. Comparing the described methods of straightening the springs, readers probably noted that S. Lipgart advises striking with a hammer on the inner (concave) side of the sheet, and V. Ankudinov - on the outer one. And the result is the same - the sheet is bent inward. There is no mistake here. When hitting with a convex striker on the inner side of a sheet lying on a flat plate, the surface layer is hardened (compacted), as a result of which the fibers here are reduced, and on the outer side they are lengthened. In the second case, under the impacts of the cylindrical striker, the fibers are lengthened, and the fibers lying on the anvil contract. The sheet bends inward.
Rice. I. Sheet editing: 1 - a hammer with a welded rod; 2 - anvil; 3 - leaf spring.
The spring may have the following defects:
- change in boom deflection (draft)
- breakage of sheets
- breakage and thread stripping of ladders, clamps and center bolt
- wear of bushings and pins
To eliminate these defects, the removed spring is disassembled. To this end, the spring is clamped in a vice or in special clamps, then the clamps and the center bolt are released and the vice or clamps are carefully unclenched.
The deflection arrow (curvature) of the sheets is checked with a template. With a slight decrease in the deflection arrow compared to normal, the sheets are straightened in the cold state with hammer blows on the inner surface of the sheet (straightening). The blows are applied from the middle of the sheet, at first strong, and when approaching the ends, weak. If the decrease in the deflection arrow is more than half of its value, then the sheets are straightened with heating to a temperature of 700-800 °. After straightening, the sheets are heated to a temperature of 800 °, quenched in oil and then tempered with heating to a temperature of 400-500 °.
The worn out bushings of the main sheet are deployed under the enlarged spring pin or replaced with new ones. Smooth spring pins are restored to the nominal size by chrome plating or ground to a smaller size for repair bushings.
Before assembling the springs, the sheets are thoroughly cleaned, greased with graphite ointment, put on a special rod (instead of the center bolt) and compressed in a vice or clamping clamps. After that, the rod is removed, a center bolt is inserted instead, its nut is tightened to failure and the clamps are installed.
If a center bolt is not provided in the design of the spring, then when assembling it, it is necessary to combine the protrusions of the upper sheets with the recesses of the lower sheets and tighten the sheets with clamps.
After assembly, the spring is tested under pressure. Press the spindle of the press on the middle of the spring until it is completely straightened (the deflection arrow is zero); then the spring is gradually released, the deflection arrow is measured and pressed again. If, after the second push, the deflection arrow remains, the spring is suitable, but if the deflection arrow decreases (the spring sits down), then the spring is rejected.
We work together on a viewing ditch.
We jack up the beam and remove the front wheel (see Removing the front wheel).
Under the front end of the frame, we substitute a reliable factory-made stand with a lifting capacity of at least 2 tons and a height of 700 mm. We lower the jack and leave it under the beam or, for convenience, we rearrange it under the hub. To avoid damaging the brake hose, we recommend removing the front brake caliper and tying it to the frame.
Using the "24" head, unscrew the four bolts of the ladders.
Holding the bolt of the front spring lug with the key "22", with the head "24" unscrew the nut.
We knock out the bolt with a beard or a suitable rod.
Similarly, we unscrew the nut and knock out the bolt of the rear fastening of the spring (to the shackle).
We insert the bolts into the spring hinges.We pull the cord between them and measure the spring deflection arrow.
It should be 147 ± 10 mm for a two-leaf spring, and 135 ± 5 mm for a four-leaf spring. If this value is less, we replace the entire spring.
We unbend the clamp, striking with a hammer through another hammer.
Having clamped the spring in a vice, with two keys "17" we unscrew the nut of the centering bolt and take out the bolt.
Disconnect the leaf spring.
We clean the inner surfaces of the leaf springs from dirt and rust.
To replace the rubber-metal hinges, put the spring eyelet under the press.
To make it easier to press in a new hinge with a file or an emery wheel, we make a lead-in chamfer at the edges of the metal plates from the end of the hinge.
We squeeze the hinge with a band clamp. Lubricate the hinge with soapy water and, using a mandrel, press it in on the same press.
Mandrel for pressing out (pressing in) the rubber-metal hinge of the spring ears.
Material - steel
Having lubricated the sides of the sheets facing each other with graphite grease, we assemble the spring. When doing this, pay attention to the difference in design ...
We unscrew the nut and take out the spring earring mounting bolt.
Remove the spring earring plates.
Holding the bolts of the shackle bracket with a key "14", ...
... with the "17" head, unscrew the four nuts ...
We replace the rubber-metal hinge of the bracket as described above.
Install the removed parts in reverse order, evenly tightening the ladder nuts.
ATTENTION
The vertical lip on the spring pad must face the longitudinal axis of the vehicle. The final tightening of the nuts of the bolts of the rubber-metal hinges should be carried out on a loaded car with straightened springs. This is necessary for the hinges to work properly.
Similarly, we disassemble the spring and replace the rubber-metal hinges on the other side of the car.
Salam, lads.
I bought a GAZelle. She has noticeably sagging rear springs. Replacement with new ones disappears (the question is in the price) 😉
The father says nothing terrible - wave a sledgehammer for a day, forge them and they are like new. I was looking in the workshop for how to do it and in useful advice I read that you can not forge but replace the earrings with 30-40mm elongated earrings. The spring will rise from the springs and will still serve.
That's the question. It will serve, but it will probably bend in the opposite direction almost certainly. Maybe someone tried it. Tell me which is better - forging or lengthening. And in general what such lengthening is fraught with in the future.
The car will not need to be heavily loaded, but you will have to travel relatively a lot.
I haven’t heard about the extended earrings. But I’ve heard about the fact that the spring leaves have been retracted. They say it’s possible, but not for long, and you’ll put off your hands. ...
Salam, lads.
I bought a GAZelle. She has noticeably sagging rear springs. Replacement with new ones disappears (the question is in the price) 😉
The father says nothing terrible - wave a sledgehammer for a day, forge them and they are like new. I was looking in the workshop for how to do it and in useful advice I read that you can not forge but replace the earrings with 30-40mm elongated earrings. The spring will rise from the springs and will still serve.
That's the question. It will serve, but it will probably bend in the opposite direction almost certainly. Maybe someone tried it. Tell me which is better - forging or lengthening. And in general what such lengthening is fraught with in the future.
The car will not need to be heavily loaded, but you will have to travel relatively a lot.
I put on earrings extended by 50 mm two years ago, the car on them has already covered about 150 thousand km, everything is in order, it became even softer, but I have a minibus and a maximum load of 800 kilograms (13 people).
I put on earrings extended by 50 mm two years ago, the car on them has already covered about 150 thousand km, everything is in order, it became even softer, but I have a minibus and a maximum load of 800 kilograms (13 people).
And here, if possible, more popular.Where did you get the sizes of earrings? They measured their own, but how to measure the diameter of the holes without removing the earrings, there seems to be a tight fit?
Load also max up to 1t. So I think this method will do.
I put on earrings extended by 50 mm two years ago, the car on them has already covered about 150 thousand km, everything is in order, it became even softer, but I have a minibus and a maximum load of 800 kilograms (13 people).
And here, if possible, more popular. Where did you get the sizes of earrings? They measured their own, but how to measure the diameter of the holes without removing the earrings, there seems to be a tight fit?
Load also max up to 1t. So I think this method will do.
- Like
- I do not like
And here, if possible, more popular. Where did you get the sizes of earrings? They measured their own, but how to measure the diameter of the holes without removing the earrings, there seems to be a tight fit?
Load also max up to 1t. So I think this method will do.
[/ quote]
Measure the diameter of the hole at the tip of the bolt protruding from the nut, the hole is not tight, the usual one for a bolt for the passage, or 16 or 18, I don’t remember exactly, drill 0.5 mm more, 2nd: measure the distance between the centers of two holes and increase it is 40-50 mm (as you want), 3rd: you make new earrings from metal no thinner than 6 mm (I did not count, but I have such). And yet (it has nothing to do with your question), if you put a stabilizer and gas-oil shock absorbers, then it will finally be buzzing.
[quote name = ’Nomad’ date = ’6.4.2010, 10:27 ′ post =’ 347918 ′]
Salam, lads.
I bought a GAZelle. She has noticeably sagging rear springs. Replacement with new ones disappears (the question is in the price) 😉
The father says nothing terrible - wave a sledgehammer for a day, forge them and they are like new. I was looking in the workshop for how to do it and in useful advice I read that you can not forge but replace the earrings with 30-40mm elongated earrings. The spring will rise from the springs and will still serve.
That's the question. It will serve, but it will probably bend in the opposite direction almost certainly. Maybe someone tried it. Tell me which is better - forging or lengthening. And in general what such lengthening is fraught with in the future.
The car will not need to be heavily loaded, but you will have to travel relatively a lot.
[/ quote
if you don’t find a machine with three rollers
the sledgehammer will help you
I fly so regularly
and hands will go away
- Like
- I do not like

Salam, lads.
I bought a GAZelle. She has noticeably sagging rear springs. Replacement with new ones disappears (the question is in the price) 😉
The father says nothing terrible - wave a sledgehammer for a day, forge them and they are like new. I was looking in the workshop for how to do it and in useful advice I read that you can not forge but replace the earrings with 30-40mm elongated earrings. The spring will rise from the springs and will still serve.
That's the question. It will serve, but it will probably bend in the opposite direction almost certainly. Maybe someone tried it. Tell me which is better - forging or lengthening. And in general what such lengthening is fraught with in the future.
The car will not need to be heavily loaded, but you will have to travel relatively a lot.
I turned over the brackets and earrings - rose 12-15cm.
I turned over the brackets and earrings - rose 12-15cm.
Yes, indeed, you can turn the rear brackets of the rear springs, due to which the car will rise, this is done from the factory on all-wheel drive GAZelles. I also made spacers from 40mm steel between the spring and the bridge, respectively changing the ladders to longer ones.
- Like
- I do not like
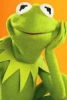
All clear. Forging only. Everything else only slightly improves the situation, but in the future it only aggravates everything.
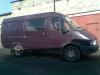
correct. lengthening of earrings - interference in the design of the vehicle: removal of numbers and a fine. and I read about the straightening of the springs in the old (where they wrote about the case, and did not shout about the advantages of expensive foreign cars) magazine "at the wheel", the meaning of the article is that on the convex side, it is necessary to form a work hardening, for this the spring is placed with the concave side on the anvil (the rail for the steam locomotive is the very thing), and on the convex side we hit with a special hammer (the firing pin is rounded, the rounding axis during impacts is perpendicular to the spring and is parallel to the rounding axis of the top of the rail) during impacts work hardening and it, expanding, increases the deflection and stiffness of the spring. I would also advise you to check the wear of the main sheets (uneven thickness), I would not straighten the main sheets.
- Like
- I do not like
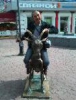
heats up with a belt lamp and gnes as much as necessary
all resors have been repaired with current repair. on two cars. so no problem.
And how long will such a repair last?
- Like
- I do not like
I rolled my springs, there are machines, three rollers, enough for three years and again I have to roll.
And how long will such a repair last?
with a sledgehammer, good physical development! and the head begins to think that it is necessary to buy new two leaflets are not so expensive
need to buy new two sheets are not so expensive
How can I say it is not so expensive.
It's still expensive, one in the collection is $ 110. And you need two, and you also need glushak, and also tires, and also change the oil, and more. and also a radio tape recorder. In general, I don’t save money on the car, but since I don’t know how to draw money, I try to do my best to make repairs on my own.
Of course, the ideal option is to replace it with new ones, or even better, a new GAZelle. Today I also made the second side. Zae *** is not childish. The fingers do not bend or unbend, the back aches, the hands hurt. But the result is PLEASANT! And if such repairs are enough for at least a year of intensive use, I will forge every year, I will not break. But the car will be in good condition.
THIS IS NOT I HAVE A GAZEL, THIS GAZELLE HAS ME! 😉
Wait a photo I'll post.
Salam, lads.
I bought a GAZelle. She has noticeably sagging rear springs. Replacement with new ones disappears (the question is in the price) 😉
The father says nothing terrible - wave a sledgehammer for a day, forge them and they are like new. I was looking in the workshop for how to do it and in useful advice I read that you can not forge but replace the earrings with 30-40mm elongated earrings. The spring will rise from the springs and will still serve.
That's the question. It will serve, but it will probably bend in the opposite direction almost certainly. Maybe someone tried it. Tell me which is better - forging or lengthening. And in general what such lengthening is fraught with in the future.
The car will not need to be heavily loaded, but you will have to travel relatively a lot.
I set myself earrings elongated by 3 cm. To take the measurements I bought an earring (40 rubles). from a strip 6mm thick cut out what nada. And the holes were drilled for me by a turner. while walking (about 20 thousand km). I'm satisfied. I read about elongated earrings in a book on Gazelle
- Like
- I do not like
How can I say it is not so expensive.
It's still expensive, one in the collection is $ 110. And you need two, and you also need glushak, and also tires, and also change the oil, and more. and also a radio tape recorder. In general, I don’t save money on the car, but since I don’t know how to draw money, I try to do my best to make repairs on my own.
Of course, the ideal option is to replace it with new ones, or even better, a new GAZelle. Today I also made the second side. Zae *** is not childish. The fingers do not bend or unbend, the back aches, the hands hurt. But the result is PLEASANT! And if such repairs are enough for at least a year of intensive use, I will forge every year, I will not break. But the car will be in good condition.
THIS IS NOT I HAVE A GAZEL, THIS GAZELLE HAS ME! 😉
Wait a photo I'll post.
![]() |
Video (click to play). |
like metal science I once rode, so there is metal fatigue and heat treatment is needed to remove it. and the spring works constantly and it has a number of times it will work. plus the shock absorbers must work so that the springs do not break earlier.