In detail: do-it-yourself Honda Torneo steering rack repair from a real master for the site my.housecope.com.
Hello to all happy owners of Chords!
I would like to add some more information on the repair of our painful rails!)))) A lot of things were discussed about this, I also decided to share my experience.
The problem actually was like many - it's an annoying knock, first on the right and then on the left side. I endured all this until the right gland began to sweat. Winter is coming and I decided to fix this problem! I ordered a repair kit online, a bushing (lock nut), an adjusting bushing, an upper spool seal (it comes with a bearing), a right boot, a week of waiting and everything came. And another liter of fresh PSF.
From an unusual tool, you will need large keys (32, 40, 46), a wrench with an average square, a denometric key (it is possible without it), preferably an electric drill and a drill (4 or 5 mm), a tube wrench (17-19), a large syringe with a tube (remove the liquid from the tank).
Now the whole process is in order:
1. We drive the car onto a flyover (pit), hang out the front wheels.
2. pump out the liquid from the tank
3. Disassemble the top (in the cabin)
just pull the protection towards you, it is held on by clips.
4. unscrew the cardan of the steering column.
5. We pull the cardan from the slots to the top.
IMPORTANT: When the cardan is already removed, you need to fix the steering wheel so that no one turns the steering wheel.
Since you can break the train under the steering wheel.
6. Unscrew the three nuts by 10 and remove the boot.
removing this duster is problematic. interferes with insulation and rug, anther is under them. Okay, take it off, put it in its place, this is a hemorrhoid. So a couple of packs of sedatives will come in handy. )))
![]() |
Video (click to play). |
remove the retainer and rubber band. the gum is shifted to the bottom relative to the shaft.
7. Unscrew the steering tips. I didn’t have a puller at hand, I made it easier to unscrew the nuts not completely so that the nut was flush with the end of the thread of the tip. This is necessary so as not to spoil the thread with a blow. We hit everything from the bottom with a hammer and voila. the tip came off. unscrew the nut and everything. If the finger scrolls, then press the tip from the top with the mount and unscrew it to your health!) Unfortunately, I didn’t take a photo ((
8. unscrew the mount of the rail itself.
We twist the lower one from the bottom and the one that is higher is more convenient to twist from the top
9. unscrew the three bolts of the heat shield from the bottom.
They are tightened from the heart!) You will need such a key.
11. first unscrew the blue bolt of the bracket, holding the handset, then the rest.
for convenience, you will need such a set with a cardan.
12. to remove the rail, you need to lower the beam. you can replace the stabilizer bushings in one, I did just that.
so we lower the beam:
we lower it by 3-3.5 cm, this is quite enough, we leave the right bolt, the beam will be held on it, and the left one is completely unscrewed and the spacer is removed (it interferes with unscrewing the stub bushing)
13. remove the rail to the left
my carefully benzinchikom and carry it to a warm garage))
14. unscrew the tips, you will need two keys for 19 and one for 14
remove the anthers and unscrew the rods (do not spoil the plastic thrust rings, they will still come in handy), here you need keys for 22 and 32 (32 will need to be modified so that it is no wider than 10 mm, otherwise it will not fit)
15. unscrew the adjusting sleeve key 40 and a knob with a middle square.
production of teflon coating to metal
16. unscrew the two bolts, tubes and remove the spool.
17. knock out the spool shaft (it came out easily for me)
the ring is in the repair kit.
18. then unscrew the guide nut, it is locked. I didn’t drill much and it unscrewed without problems. (The nut is thick, don’t be afraid to drill))
IMPORTANT: do not clamp the case strongly in a vise, it can be deformed and that's it. the rail can be thrown out. Nut under
key for 46
19. Next, you need to knock out the gland that is under the nut. The difficulty is that the shaft will spring due to the air and oil of those left behind the outlet fitting.
I did this: I pulled the shaft out of the housing as much as possible and pressed the shaft to the side so that there was a gap between the shaft and the stuffing box, the main goal was to release air (it is very springy). Then we put something on the opposite side of the shaft and try to knock out the oil seal (it came out easily for me). I used the extension cord from the kit.
the second seal is knocked out in the same direction as the first.
you need to knock it out carefully with something softer than steel without damaging the inner working surface, I found some kind of stick in the garage and easily knocked out the oil seal.
we see that there is a washer under the gland
21. We wash the body thoroughly with gasoline and drive in a new oil seal (do not forget to put a washer in front of the oil seal)
a new washer can be taken from rep. kit
I pressed the new oil seal with a 27 head and two extensions
22. Now you need to replace the cuffs on the shaft, there are two of them: one ring is white, it looks like it is made of plastic, and under it the other is rubber (the plastic ring must be worn very carefully - it is difficult to stretch, you can tear it, for example, I have a little heated over the lamp-carrying.)
here's what happened in the end
23. We install the shaft into the housing, before installation, put a little electrical tape on the end of the shaft so as not to seal the gland.
IMPORTANT: Insert the shaft carefully, remember that the teeth of the shaft can also damage the oil seal!
24. We crush the second stuffing box with a new nut.
25. We lubricate the whole thing, I used violet grease, of course, you can use lithol, in general, whoever wants it!))
26. Now we change the stuffing box and spool bearing. I picked up the head from the set, I don’t remember exactly which one, and pressed the oil seal at the beginning, then the bearing (with the inscriptions outward, so that after installation they could be seen).
We put the spool shaft in place, check that the shaft rotates without much effort. Lubricate everything, especially the bearing and splines.
put it all on the rail (do not forget to change the ring, it is in the repair kit)
27. put the adjusting sleeve (do not forget to lubricate everything)
How I adjusted:
I twisted until it rested, then unscrewed it one turn and turned it again until it rested and let it go by about 20 degrees (all this is necessary for the spring to fall into place) If you need a denmetric wrench and do it all with some effort. I didn't have a key. After assembly, the steering wheel did not become tighter and the knock (if you move the steering wheel) on the turned off engine is a thing of the past!)))
28. Screw the tubes into place (I forgot to take a photo)
29. screwed steering rods, do not forget to put plastic thrust rings
we put new retaining rings (with a mustache in the shaft), they are in the repair kit
31. fasten the steering tips (bending in front)
Everything. now put on auto. I think it's not worth describing the order!)))
here are some pics of the bushings i replaced. I put myself polyurethane bushings of a smaller diameter instead of 26.5 mm, I put 25.4 mm, since the stabilizer itself turned out to be worn.
Good luck to everyone in the repair of your favorite car))).
Repair of the steering rack Honda Accord 7. Repair of the steering rack in St. Petersburg.
Honda srv steering rack repair
Repair steering rack Honda Accord. How to remove a knock in the steering rack Honda accord 8
Do-it-yourself power steering pump repair (hydraulic booster). Replacing seals and bearings. Acura Honda
What to do if the steering rack rattles?
Honda - steering rack knock.
Acura MDX steering rack repair. Acura MDX steering rack repair in St. Petersburg.
tightened the steering rack Honda Civic VII ep1
Steering rack ACURA RDX
Steering — one of the most important parts of the car. Its main purpose is to tie the front wheels and steering wheels together, to set the direction of movement for the car.It is thanks to her that the direction of movement of the car on the road is determined.
True, like any other part of the car, it is subject to wear and tear. They affect traffic safety, driving, wear and tear of other parts of the car. Tires wear out especially badly in such a situation. Therefore, it is important to monitor the serviceability of this part and troubleshoot in time.
By car "Honda» This part has a high level of reliability. As a rule, up to a run of 18 thousand km, there are no difficulties with its operation. She does not have typical breakdowns that are not typical for other car brands. Basic breakdowns happen for the same reasons as other cars.
In most cases, cars are hydraulic racks, but some Honda vehicles are equipped with electric steering parts. They wear out faster, in them the bushing of the right end of the shaft most often fails. In this case make repairs yourself steering rack honda civic impossiblebecause it requires a special tool and a lot of experience with parts.
The main signs that indicate the need for repair are knocking noise coming from front suspensionwhen the steering wheel is turned to the side. As a rule, this indicates the need to replace the broken bushings of the worm pair. The leakage of the working fluid requires the replacement of damaged seals and the cleaning of parts from corrosion.
Another problem that indicates the need to repair the Honda Fit steering rack is steering play. It usually occurs due to the development of the distributor rod or the teeth of the worm pair. Replacement of these parts is also required when biting the steering wheel. If the steering wheel is tight, most likely the problem is corrosion of the assembly. It can be eliminated only by its complete analysis and cleaning of every detail.
It must be understood that the repair of the Honda Accord 8 steering rack is an expensive pleasure. In addition, it takes a lot of time.
The difficulty also lies in the fact that it is difficult to find a complete assembly kit for some car models. Then you have to select parts from different cars, but in this case, the guarantee of the unit will not be high. Sometimes it will be more justified to completely replace the rail with a new original one.
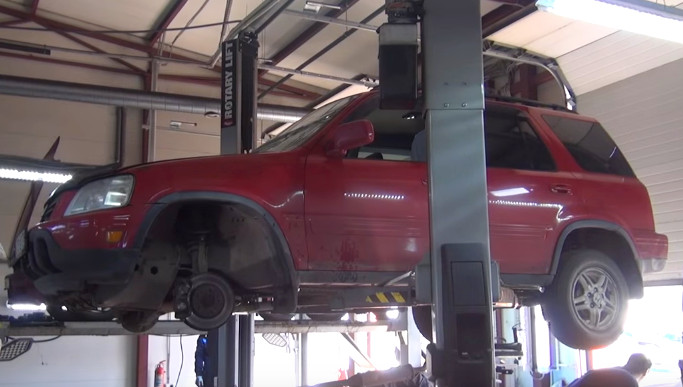
Now let's take a closer look at typical breakdowns and how to fix them.
In this case, you can try repairing the steering rack "Honda Accord 7" preventby adjusting the degree of tightening of the nut. But if the crankcase or steering rack shaft have mechanical damage or deformation, you will still have to carry out repair work. Their cost, as already mentioned, will be quite high.
This is one of the main causes of node breakdowns. This type of failure usually does not require major renovation. If you give the car to a car service to a good specialist, he can simply adjust the backlash, spending relatively little time on it.
If there is a leak in this part of the car, this indicates oil seal wear. Its damage leads to a violation of the tightness of the system. Through the resulting gaps, a process fluid flows out, which requires an urgent and mandatory replacement of the stuffing box. This is a complex and jewelry process that requires removing the bolts (almost always they are covered with corrosion), the cross beam, and in especially difficult cases it is necessary to hang the engine.
Knocking, as a rule, appears due to overcoming various obstacles at high speeds. He talks about wear and sometimes destruction of the bushings. In this case, they need replace. To do this, the assembly will have to be dismantled, the damaged parts replaced, installed back, and then adjusted for its operation. In this case, the repair of the Honda SRV 3 steering rack requires a special tool, so it is almost impossible to carry it out on your own without certain skills.
Any repair is a whole list of works aimed at restoring the operation of the mechanism in the mode provided by the manufacturer.In the process, it is necessary to identify and eliminate faults, replace parts, and adjust their operation.
Before making repairs, prepare the car to work. To do this, dismantle all nodes that block access to the node: air filter, resonator, battery. Its removal is also carried out according to a special procedure. When it is removed, it is disassembled and all parts are cleaned.
In order to carry out a correct and adequate repair of a part, it is necessary to carry out a clear diagnosis of it, as well as the components associated with it. Therefore, repair of the steering rack in St. Petersburg must be carried out at service stations only by qualified specialists.
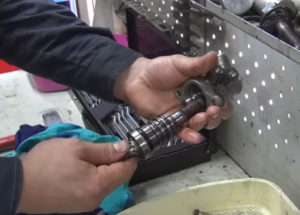
From tools you will need a serviceable power steering (if the previous one is broken), adjustable wrenches, heads and a reliable vice. For complex repairs that require hanging the engine, special equipment is required.
Depending on the type of breakdown, the repair of the unit is carried out in different ways.
In case of minor malfunctions or preventive maintenance, the system is flushed and cleaned. It takes a little time and does not require much money.
This type of repair requires the removal of the assembly. Then held such works, how:
- removal and disassembly of the assembly;
- flushing and cleaning the assembly and its parts;
- replacement of parts that cannot be restored;
- check and cleaning of the gear shaft;
- replacement of components (rings, seals, anthers, etc.);
Depending on the damage and wear of the parts, repairs can take from a couple of hours to a couple of days. At the end of the repair, several stages of its adjustment and testing for performance are carried out.
Since such repairs take a lot of time, not everyone is willing to wait a few days until it is completed. In this case, the spent node is replaced with an already assembled new one of the same configuration. This is also a long and laborious process.
- First you need to remove the battery terminal, unscrew the pain by 10 near the pedals and disconnect the steering shaft.
- Then raise the car, disconnect the wheels, unscrew the steering tips of the caliper. Sometimes at the same time they remove the anther without removing the tip.
- Then you need to remove the chips from the assembly and unscrew the bolts that hold the subframe.
The assembly of the assembly is carried out strictly in the reverse order. When the repaired or new rail is installed in place, it is necessary to repeatedly test the operation of the assembly, which will determine the accuracy of the work performed, indicate how ready the machine is for further operation.
The quality of work is indicated by the absence of noise and difficulties when turning the steering wheel, a stable level of power steering fluid, and the absence of its foaming. Preventive work in the area of the node should be carried out every six months.
As you can see, repairing a Honda steering rack is a difficult job that requires a lot of experience, knowledge, qualifications and special conditions, even for simply replacing a broken assembly with a new one. To do this in an ordinary garage is practically unreal.
The cost of a new node is high, work to repair or replace it takes a long time. So much wiser on time contact a car service specialist for the diagnosis and prevention of all its details.
Thanks for this report Mikhail199 for editing.
steering rack Honda Civic cannot be called a disease in the full sense of the word, but at 180,000 - 200,000 km of run, even it comes into a state of “fatigue”. Dirt gets inside the rack through cracked from time to time, torn anthers. Under the action of the abrasive, which is in the road dust and gets into the rack with dirt, the process of accelerated wear of the steering mechanism begins. Plus, without protection, the guide rails rust pretty quickly.Not the best way to repair is to clean the rust and fill the rack with new grease, especially if the grease is not designed to work specifically in the steering rack. If the rack does not work correctly, the load also goes to the power steering (GUR), as a result of which it wears out faster than with a working rack. A new OEM Honda rail costs about $1200-1500 or even more, which, you see, at a car price of $7000. becomes just a piece of gold. A contract rail, also repaired, costs a little less, but in the same price range, $500-1000. What to do? Of course, do not lose heart, but repair the rail on your own.
To get started, you will need the following things, general repair price 100-150$
- Steering rack repair kit - 06531-S04-J51 ($50)
- Anthers to the rail - 53534-ST0-013 and 53534-SR3-N52 ($ 30)
- Steering column bushing - 53416-S04-J51 ($ 15)
- Power steering fluid - Honda PSF 3 bottles or 1 liter
- good vise
- 10, 12, 14, 17 : heads and keys
- Adjustable wrench 34 or 36 approx.
- Live power steering if broken
First thing remove steering rack Honda Civic. Unscrew two hoses on the rail itself. The hoses go from the pump to the rail, and from the rail to the fluid reservoir. To make this easier, you need to unscrew the other fasteners first of these hoses, they are attached to the subframe with small bolts of 10.
First thing throw off the soft tube, which goes from the tank to the rail (fastening with a clamp), then unscrew with a split wrench a 14 hard high-pressure tube that goes from the pump to the steering rack itself.
You will also have to remove middle exhaust and a small metal protectioncovering the steering rack from below, remove the steering tips and rods, and in the cabin unscrew the two 10 bolts that hold the cardan between the steering column and the steering rack and pull the cardan up. Next, we put forward the steering rack guide in one direction (I moved to the right) and pull it out.
10mm bolts holding steering rack cardan
It is enough to simply loosen the upper bolt in the steering column and, by moving the steering cardan up, disconnect it from the rack.
IMPORTANT REMINDER! After you remove the gimbal, never turn the steering wheel! Without a rack, the steering wheel will not have a travel limit and, by rotating it in any direction, you can ruin the cable of contacts on the steering wheel. The steering wheel can be turned if necessary! But always return it to the position in which you took it off! Also, before disconnecting this cardan between the steering column and the rack, put the wheels in a level position and try to keep the steering wheel in the same position throughout the work.
By removing the rail, you will be very dissatisfied with her appearance dirt, rust, yes, yes, and most of the components on your car are in this condition, but for now forget about it. After some time, you will bring the rail into excellent condition with your own hands, and it will serve you for a very long time, the main thing is care and diligence. Unscrew absolutely everything that is on the rail, and try not to confuse or lose the removed parts!
Start with guide bushing. To do this, unscrew the locknut (size 34 or 36, I used an adjustable “gas” wrench), then unscrew the tensioner with a 14 wrench and pull out the spring and the bushing itself. Next, use a 12 wrench to unscrew the tubes that remain on the rail. In my case, there was horror:
Swamp and rust inside the steering rack.
With a key or head for 12, unscrew the two bolts distributor and pull it out.
Distributor bolts out
As you understand, all removed parts simply need to be cleaned of a layer of dirt and washed as best as possible. But the hardest part of the work is still ahead of you.
When assembling the rail at the factory, after tightening the main nut on the body of the rail with a core or press, a small point is pressed through, fixing the nut and preventing it from arbitrarily unscrewing under the influence of shocks and vibrations that occur when driving a car.
This point must be drilled with a drill with a diameter of 3 mm to a depth of approximately 2.5 - 3.0 mm. If you do not drill this point, then you risk unscrewing this nut, cut a thread on it. Initially, this is exactly what happened to me. I had to look for a new nut, or rather, buy a dead steering rack and carefully unscrew this nut from it.
And it was necessary to drill
If everything is drilled correctly, then the nut is easily unscrewed, and the thread remains in place. For your information, the original nut costs about $ 100 or 6000 r and wait for it for an order for about a month. Having unscrewed the restrictive nut, we pull out the rail guide as much as possible and then carefully press it out together with the stuffing box. Then we take a special mandrel and with its help press out the second seal. (According to the manual, the head seems to fit 17, but it wedged for me, so I didn’t take risks and carved a special mandrel). In principle, with the analysis of everything. Once again all washed and cleaned!
Before assembly, you should pay attention to a couple of points. The main reason why our reiki starts to die is our own carelessness. Namely - torn anthers of the steering rack. Do not think that if you wrap a bag around the steering rod, then dirt, sand and water will not seep into it. All this leads to the formation of rust rails on the working shaft, which, forming uneven growths or pits, just the same ruins the seal. In my case, everything was quite sad. The black stripe on the shaft and the dots are rust that has eaten quite deeply. And because of it, the rake flowed strongly.
In this case, there are several solutions:
- Give the shaft to the turner for grinding (but it is important to consider that you cannot remove too much)
- Buy a new shaft (To my surprise, its cost is noticeably lower than that of the rail assembly)
- Grind the shaft myself (which I actually did)
It turned out, of course, so-so. But, looking ahead, I will say that the result justified itself.
After you have prepared your old shaft or bought a new one, you can proceed to reassembly.
My ground shaft and rail
ATTENTION! Be sure to purchase the original steering rack repair kit in advance! (06531-S04-J51).
Original Honda repair kit
The kit includes everything you need
First of all, we change rubber and plastic rings on the guide rail. We remove the old rings and put on new ones from the repair kit, first rubber, and then plastic.
Be sure to level the plastic ring so that it is not twisted anywhere.
In the rail itself, in reverse order, we lay an iron washer from purchased repair kit. In fact, just throw it into the rack body.
Before installing the first oil seal, according to the manual, the teeth on the shaft must be wrapped with special tape. To be more precise, we are talking about the usual FUM tape, which can be bought at almost any hardware store where there is a plumbing department. It is necessary to wrap the shaft so that when you put on the extreme stuffing box, you do not damage its working surface on the teeth on the shaft.
Shaft wrapped with FUM tape
You need to wind the tape from the center of the shaft to the edge, in this case, when you put on the gland, it will not cling to the tape, but will slip along it. Then lightly lubricate the oil seal and put it on the shaft so that its flat side looks from the center to the teeth.
Then insert the rail guide into the housing. Because of the stuffing box, the shaft will not be easily inserted, it must be pressed in. Essentially, with the shaft you are pressing the oil seal into place.
Then put the second oil seal with the flat side towards you and tighten the restrictive nut.
Correct seal installation
After you have tightened the restrictive nut, you can fill the rail with a core with the same point as it was done at the factory so that the nut does not unwind. (Personally, I did not do this, but simply smeared the old place with sealant).
Next, we put the liquid distributor in place, changing the sealing rubber from the repair kit on it. But, before doing this, you will need to rotate the shaft with the teeth along the distributor. Then you need to fill a little new grease into the lower bearing. This is necessary so that the distributor turns easier and there is no extraneous noise. Please note that if your rail has been flowing for quite some time, then in this bearing no proper lubricant left. Therefore it definitely needs to be done. It is also desirable to lubricate the bearing on the distributor itself.
We fill new grease into the lower bearing
The teeth on the shaft are also lubricated with new grease. Just don't put too much on it.
Now the only thing left to install is the steering rack guide. There is also a small nuance which I think it would be nice to pay attention to. If your rail is rattling but not leaking, the rods and tips are not always the reason for this. In some cases, play in the rail appears due to wear on this guide. Since its part that is in contact with the shaft is made of plastic, it wears out, which leads to free play between the teeth on the shaft and the teeth on the liquid distributor. In its normal state, the spring and this guide press the shaft against the distributor, thereby removing the play between the teeth.
The photo shows an old worn bushing on the left, and a new original one on the right (by the way, it costs about $ 10 or 600 rubles.)
Left - worn, right - new steering rack guides
Sometimes it is enough just to change this guide, and all problems with backlash are solved.
But back to our rail:
Before installing the guide, it is necessary to apply some lubricant to its plastic part.
Before installation, the new guide must be lubricated.
Next, put the guide in place. Then we put the washer, if you had one, and put the spring in place. Before installing the spring, lubricate the back of the guide bushing or the spring itself and tighten the bolt in its place.
According to the rail bulkhead manual, in order to correctly set the pressure force of the guide, you need a bolt that fixes it first tighten with a torque of 25Nm, and then loosen it. This is done in order to trim the shaft and guide, as well as develop the spring a little. After loosening this bolt, it must be tightened, but with a smaller moment of only 3.9Nm. Then, holding the bolt with a 14 wrench, wind and tighten the thin locknut.
After that, we fasten all the pipes? who were on rails and EVERYTHING. The rack is ready.
Your steering rack is like new!
After repairing the rail itself, we install the removed parts back on the car. After you shove the rail into place, First of all, screw on the high pressure pipes (from the pump to the rail) and the return hose. After that, you can safely fasten the rail to the subframe. Then you screw on the tie rods, put on the anthers and screw on the tips. If you were able to remove the rail yourself, then you should also be able to assemble it back, there is a purely designer. To install the steering wheel, set the wheels approximately in a level position, then put on the steering column cardan shaft on the rail.
Next, fill the tank with power steering fluid, Original HONDA PSF. Since the fluid from the system has been drained completely, you will need almost a liter of new fluid.
Smoothly rotate the steering wheel from stop to stop, NOT starting the car! With such manipulations with the steering wheel, the liquid enters the rail, being distributed throughout the system. Only after the fluid from the tank has left even a little can you start the engine and repeat the rotation of the steering wheel in order to release air bubbles. Then turn off the car and add fluid to average mark. Between minimum and maximum!
If everything was done correctly, then the noise during the rotation of the steering wheel will disappear, the steering wheel itself will turn much easier, the knocks will disappear, and the power steering fluid will stop leaving and will not foam. Such repairs will save the family budget very well. And finally, since the tips were removed, you will have to make a collapse. The total cost of repairing the steering rack, with all the original consumables, will be approximately $ 100-150. P.S. do not pull with the repair of your cars. Change all consumables on time.
This article is relevant for 1992-2000 Honda vehicles such as Civic EJ9, Civic EK3, CIVIC EK2, CIVIC EK4 (partially). The information will be relevant for owners of Honda Integra in DB6, DC1 bodies, with ZC, D15B, D16A engines.
It's really more convenient than writing comments below.
How often do you hear a sad phrase from hondavods: “my steering rack rattled, I’ll have to change it, probably ... is it expensive?”. Questions like these are always answered with pleasure:Very expensive!At the same time, without deceiving a person at all. Indeed, the steering rack, or steering gear, is a very, very expensive part of a car. It so happened that the price offered by the supplier for this part reached a quarter of the real value of the car on the market. After announcing it to the client, often in his eyes there was an acute desire to do “self-depilation” of different points of the body, and no wonder - for example, for the Honda H-RV, the cost of the steering gear assembly is more than 50,000 rubles with a delivery time of more than a month!
And what then is our joy when such a question arises? Do you think in a thirst for profit? Wrong, dear ones! Now we will tell you how to get rid of knocking in the Honda steering rack at least on your own, and as a maximum, returning to the service that diagnosed you with the replacement of the rack, and victoriously poking them into this article, you will indicate the right course of action. Intrigued? Already good. Let's figure it out then. We will start, as we usually do, from the very beginning, that is, from the fact that we have a steering rack and where it comes from knocking in steering rack.
So, the steering rack, or the correct “power steering gearbox”, is the most important component of the power steering system, the one that helps to rotate the steering wheel with minimal effort. Those who studied in driving schools on Russian cars that are not equipped with a power steering system should perfectly remember how tight the steering wheel turns in them. The hydraulic booster is designed to facilitate this operation. And the key part of the power steering is the steering rack itself. In fact, the rail is the hydraulic booster. Let's take a look at this assembly first.
So, you see a picture from the official catalog. Let's take a look at what's on it. The most interesting elements for us are highlighted in red circles. So let's start from the end. Under the number "14»We see the power steering gearbox itself, which is also the steering rack assembly. On each side, steering rods are attached to it (in the figure under the number "1"). Steering tips are attached to the steering rods ("12"), which are eventually attached to the wheel. All this simple but very effective design allows you to control the turning of your car's wheels.
Knocking diagnostics should begin with this picture, since the first thing that can knock in this scheme, you already know, is the steering tips and tie rods. If the tips are extremely easy to diagnose - as a rule, a failed tip has a torn anther, which is why the ball joint of the finger has become unusable, then everything is a little more complicated with traction.
As a rule, the thrust also fails due to a torn anther (in the figure they are shown under the numbers "9" and "10"), but it also happens that the previous owner "killed" the thrust, but changed the anther by stuffing new grease into it. As a result, the thrust worked for some time and finally failed, starting to knock.Diagnosing it in this case is a little more difficult than the steering tip, it is necessary to remove the thrust boot and check the thrust itself for play in the horizontal plane. If there is play, cheers, the source of the knock is found, you can change and collect everything back.
There is one significant disadvantage in this whole scheme - to miss a knock in the steering rod, or tip, and only non-specialists can recommend replacing the steering rack. As a rule, a good master “catches” such a breakdown immediately, indicating the need to replace the part. Another thing is a knock inside the rack itself. Let's take a look at its design together, and figure out what can knock there.
You see a screenshot from the official Honda catalog, it shows the steering rack disassembled. Among all the details in this picture, we are most interested in the number "7″, «10″, and "11". Let's find out together what's special about them.
You should start with part number "10“, this is the steering rack shaft, a key element of the whole structure. It is the movement of the shaft inside the rack housing that turns the wheels - the working fluid presses on the shaft in a horizontal plane, and it already transfers power to the wheels of the car through rods and tips. The source of the knock inside the rail is it. But by itself, it cannot knock (on a new car, it doesn’t knock!), Accordingly, there must be other details that provoke this sound. And they really are.
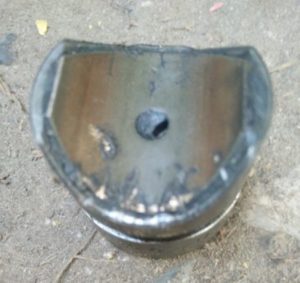
Please note that the sleeve itself is not fixed, but, on the contrary, is a movable part (with a rigid fixation, it would quickly deform the shaft), pushed forward by a powerful spring, regulated by a special bolt with a lock nut (in the figure, part No. "5«,»6«,»8"). As a rule, in most cases, it is this bushing that causes knocking in the steering rack, after diagnosing which, many “masters”, including official Honda dealers in some cities, issue a verdict on the need to replace the entire assembly. And this is where you need to stop and think.
The fact is that among the original Honda parts there are indeed parts that change only as an assembly, for example wheel bearings with a magnetic ring, but this is not the case. This bushing is quietly sold separately and often in specialized stores there can be a fairly wide selection for most models! Therefore, do not rush to change the rail! Look for the bushing first!
Although, in fact, there is an even simpler solution to the problem, although it requires preliminary diagnostics at a service specializing in Honda. Often, to completely eliminate knocking, a very simple operation is required - unscrewing the bolt fixed with a lock nut, and ... That's right! Cleaning the spring, covered with rust and deposits over the years. The spring simply ceases to fulfill its “clamping” properties due to accumulated dirt, and the sleeve itself is blocked by the same deposits.
To restore the working properties of this entire element (and, as a result, eliminate knocking), the following actions will be required:
- Loosen the lock nut8"and bolt"6". Sometimes it is not easy to get to them, but these are already technical issues. Reassure yourself that changing the rail is more expensive.
- Pull the spring and bushing out of the seat.
- Clean the spring with a brush and chemical cleaners such as "carburetor cleaner" or Profoam 1000, or with ordinary diesel fuel. After cleaning, lubricate the spring with any lubricant to protect it from water ingress.
- Carefully inspect the working (fluoroplast-coated) surface of the bushing. It should not have deep scratches, potholes, or places worn down to metal. If there are any, replace the bushing.
- Carefully wipe the bushing seat free of dirt.
- Lubricate the bushing with grease and install it in place.
- Assemble the knot in reverse order. It is also advisable to lubricate the bolt with the locknut.
- Adjust tightening torque. This operation is carried out with the help of a partner, who must sit behind the wheel of a car and swing the steering wheel left and right with short movements. The person below adjusts the spring tension with a bolt until the knock in the steering wheel disappears, then fixes the position of the bolt with a lock nut.
Attention! When performing this operation, it is necessary not to overdo it so as not to make the tension too strong. This will lead to the failure of the entire node! If everything is lubricated and cleaned well, it will not take much effort to adjust!
Voila! As a result, you get an almost perfectly working rail (there is still wear, but it is eliminated by reasonable tightening), practically for nothing!
We should dwell on the “improvement” of the process, which is sometimes suggested by the “masters”. For a long time, we could not understand why clients, referring to the forums, avoid this procedure. As it turned out, the reason is as follows.
Many masters understand the procedure of "lifting" literally. They loosen the lock nut and tighten the screw all the way until the knock stops, then fix the result with the lock nut. It turns out that all the dirt and rust that had to be cleaned out from under the bolt not only remain in place, but are also driven further into the assembly, and the sleeve itself, which, in general, should be movable, rests against the shaft with such force , which sometimes even arches it. Naturally, the operation of the rail with such a “fixation” quickly disables the entire mechanism, and the curved shaft breaks all the seals in its path, which is why the assembly also begins to leak. Repair after such a "lift" is no longer possible, so please be careful when choosing a service. To stand above the soul and follow the work of the master is incorrect. But asking how this procedure will be done is not superfluous.
We return to the figure with the disassembled node. If you have not forgotten, we still have one more detail circled - No. "11", - the output sleeve of the steering rack. It's also worth talking about. It happens that when diagnosing a rail, an obvious play of the shaft itself is noticed at the outlet of the housing. This happens when the output sleeve itself is worn, the central part of which (the liner) is made of a softer metal than the shaft itself. The play formed inside can also lead to the effect of knocking in the rail. Replacing this bushing is usually even easier than the clamping one - you unscrew the old one, screw in the new one, and that's it. Repair without replacement, in this case, is impossible, since the play appears as a result of natural wear.
In any case, until dirt gets into the rail and destroys the shaft itself and the seals, the rail is quite repairable.
By the way, knocking in the electric power steering (EUR) system is eliminated in the same way as in the hydraulic booster, with one exception - in the EUR there is no way to change the output sleeve. The manufacturer believes that there can be no problems with it. In fact, unfortunately, this is not the case. Often, owners of electric rails are offered to change the rail assembly, although there are technologies for restoring or replacing steering bushings.* The clamping sleeve is adjusted in the usual way.
So, now you have the knowledge of repairing steering racks. As you can see, there is no magic in that matter - the knock in the rail is removed simply and without problems, if you know where to look for it.
* There is actually a way out when replacement of the output sleeve of the electric rail is required. The sleeve itself can be unscrewed with a special tool, and despite all its protests, in most cases it succeeds. But then you can proceed in two directions.
The first is the manufacture of fluoroplastic inserts in an old, worn bushing. Quite a reliable way if the manufacturer has experience in this direction.
![]() |
Video (click to play). |
The second is the restoration of the original output sleeve. Very few services own this "Jedi" art, and as a rule, keep it a secret, since the final quality of the product is very close to the original performance, and lasts long enough, provided that the rail shaft is intact. Unfortunately (for the project, of course) we are bound by a promise to remain silent on the intricacies of this technology. But, we can help readers from Novosibirsk by suggesting, upon personal request, a service that you can contact regarding the recovery procedure. That is, with all our desire, we do not have the right to talk in detail about the technology, but we will tell you where to turn!