In detail: DIY repair of generator brushes from a real master for the site my.housecope.com.
Hello dear motorists! Today I will tell you how to repair a generator with your own hands. You may have already encountered such a problem, when the battery discharge indicator suddenly came on on the dashboard, this means that your car has lost its charging, and you will not go long, the battery will last for a maximum of 1-2 hours.
Do not rush to throw away the generator. Try to repair it first. The most common generator malfunction is brush wear.
To check the brush assembly, you need to remove the rear plastic cover by bending the three plastic clips located in a circle.
Remove the cover, unscrew the two screws and remove the voltage regulator.
Check the wear of the brushes, if the residual length of the brushes is less than five millimeters, feel free to buy a new voltage regulator in the store. Sometimes it happens that the generator does not charge or recharges the battery, this is also a malfunction of the voltage regulator. The normal voltage of the generator is 13.5 to 14.5 volts, depending on the engine speed and the load on the generator.
The next generator malfunction is a breakdown of the diode bridge. To check the diodes, the diode bridge must be removed. We unscrew the bolts that hold the diode bridge.
Bend the wires to the side.
Remove the diode bridge. How to check a diode bridge. Read here: How to check a diode bridge?
After removing the diode bridge, be sure to check the stator windings. We do this, turn on the multimeter in dial mode and check all three stator windings for an open. All windings must ring among themselves.
![]() |
Video (click to play). |
Next, we check the short to ground. We connect one probe of the multimeter to ground, and the second is alternately connected to the terminals of the windings. There should be no short circuit to ground.
Similarly, we check the armature winding.
We check the anchor, there is no short circuit to ground.
Now I will show you how to disassemble the alternator to replace the bearings. We unscrew the four screws connecting the two halves of the generator together.
Unscrew the nut and remove the pulley.
Using a screwdriver, carefully split the generator in two so as not to damage the aluminum covers.
Replace defective bearings with new ones. Reassemble the generator in reverse order.
Friends, I wish you good luck! See you in new articles!
As the title of the post implies, I tried to extend the life of genadia by replacing bearings and brushes. Genes mileage 95 thousand miles across states and 53 thousand miles in the harsh conditions of Russia - mother. That is not enough. And for such a solid service life, the bearings began to squeal and the brushes were worn out so that they barely touched the rotor.
We removed the gene from under the hood and unscrewing the pulley, we begin to disassemble. 4 bolts are unscrewed by the head by 8, they hold the body and 4 bolts for a figured screwdriver around the pulley. They hold the bearing, and, as usual, turn them off and turn them off with a chisel.
Gently hit the body with a hammer because it sticks to the stator, be healthy. Our goal is to remove the front cover and pull out the rotor. If we could, then well done. No, we go on)))
To remove the back cover, you need to unscrew the nut on the back of the genes head by 12 and 3 bolts with a curly screwdriver inside. 2 bolts can be easily removed, and one stsuka will be under the stator winding. So the people here then you need to be careful, because you need to slightly pull the stator out of the back cover and bend it a little to the side, because the cross-eyed soldered the diode bridge to the winding. They bent back, crawled up and turned away. After all this, the back cover will fall off by itself.
After these manipulations, we see the following picture.
Mon 19 Oct 2015
Hello! Today I will show you how I repaired my generator, which, perhaps, someone else would have thrown into a landfill. When I drove home yesterday, everything was included - lights, stove and music. At some point, the on-board computer squeaked and the battery light on the panel came on. I immediately deduced the voltage of the on-board network on the BC and was surprised - it was 11.4 volts. I turned everything off immediately and drove home slowly.
After turning off the engine, the computer showed 8 volts. Having removed and disassembled the generator, it was revealed that one of the copper-graphite brushes of the relay-regulator simply fell off the wire. This one costs 510 rubles, but I thought it would be better to fix it myself.
This is how it looks.
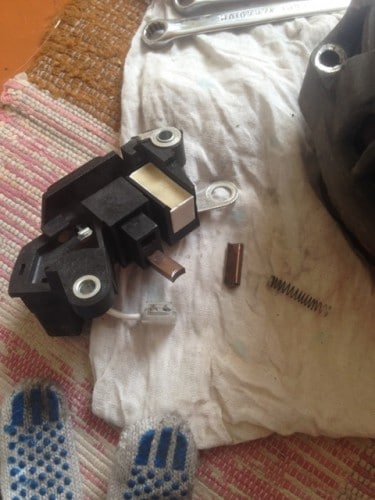
After rummaging through the warehouse, new drill brushes were found.
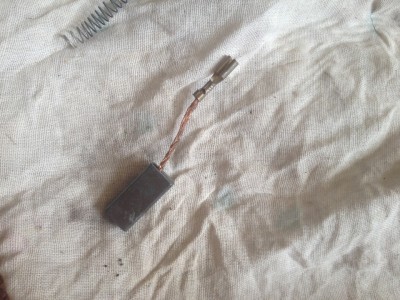
They varied in width and thickness, but the length was the same. Compare:
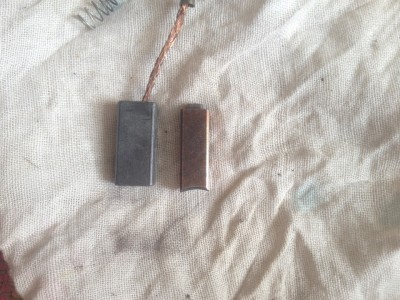
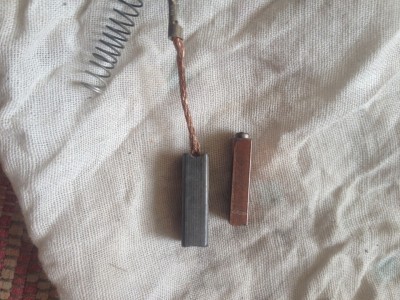
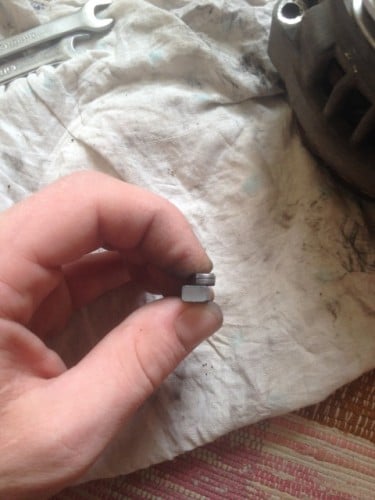
After a little processing on a sharpener, they became almost identical, only the color was different.
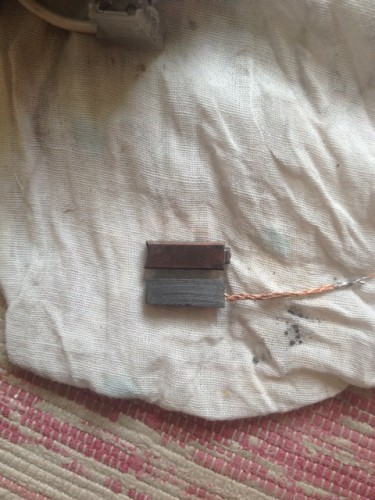
Then I soldered a thin copper wire to the brush pigtail, so that with it in the future I would not have any problems with how to tighten this same pigtail into the brush contact hole.
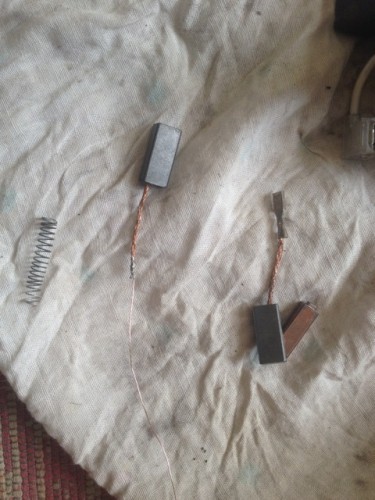
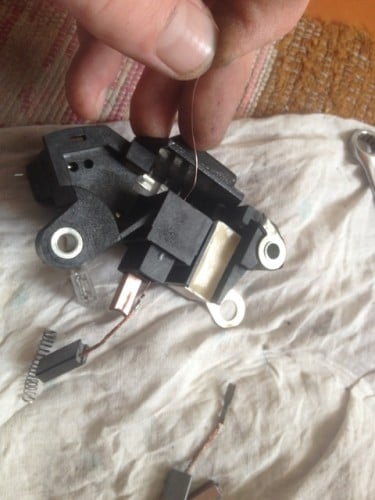
After the contact of the brush of the relay-regulator was cleaned, there are still remnants of the old scythe.
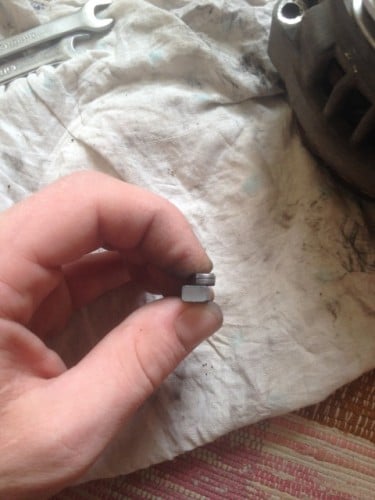
And he tinned the whole thing, using tin and soldering acid.
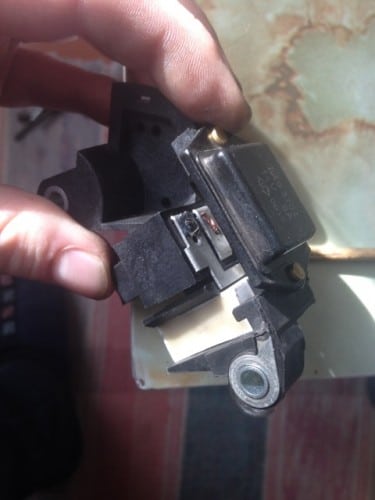
Then I put a spring on that very wire.
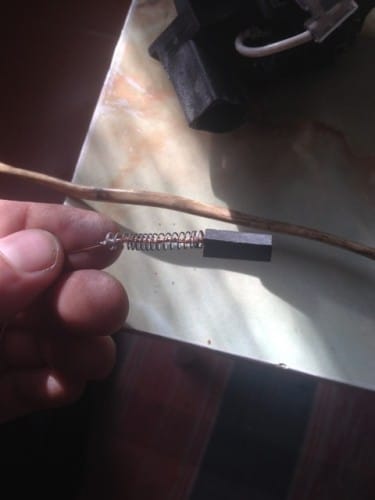
And put it into the contact hole of the brush of the relay controller.
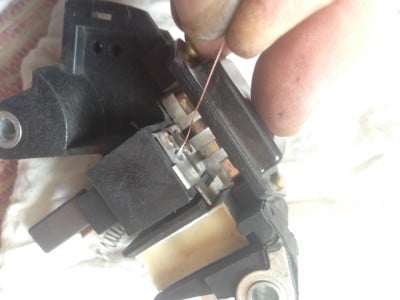
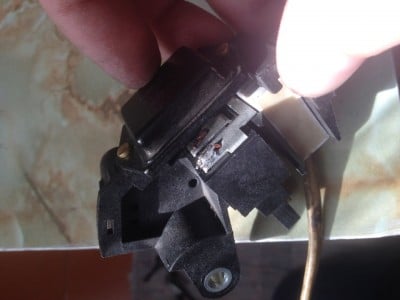
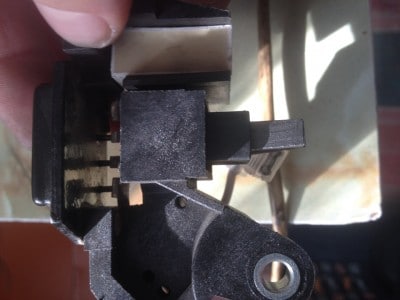
Then I saw that the contact sleeves of the generator rotor were rubbed with brushes, so much so that plastic was already visible in the grooves, that is, either the contact sleeves or the rotor had to be changed.
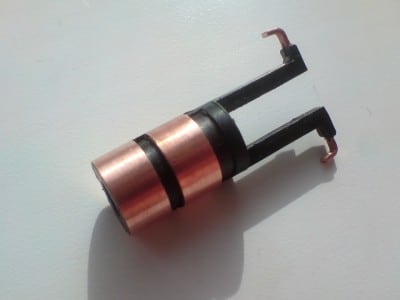
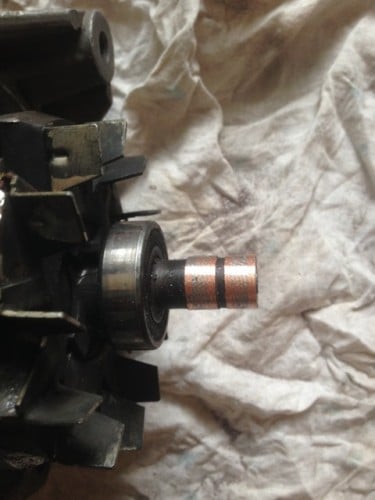
Well, this is how a repaired generator looks like.
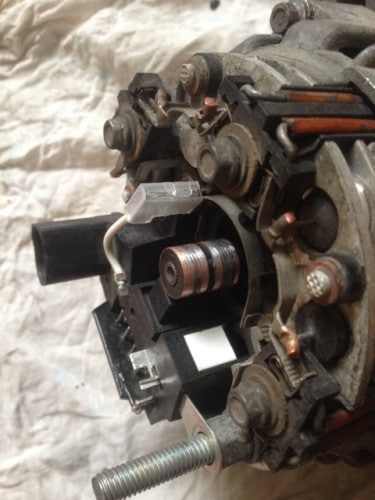
I installed it back in the car, started it and I see 14.1 volts. Of course, I could not sweat it and buy all this, incl. and a new generator. But why? 0 rubles and a minimum of effort were spent on repairs. Hope this is useful to someone. Good luck!
Generator brushes are an important part of an automotive electrical supply and drainage system. Without their participation, the car generator will not be able to generate voltage.
The brushes of interest to us are made of graphite, which is why they are often called carbon brushes. They are used not only on cars with an internal combustion engine, but also on a wide variety of mechanisms and machines equipped with an electric motor (machine tools, lifting equipment, urban public transport, and so on). The most common are brushes. EG-4.
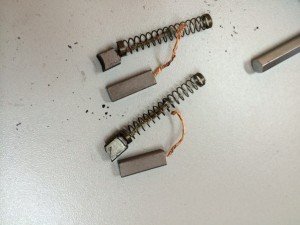
This brand is suitable for installation on many machines of different years of production, since it has standard operating parameters. Other products are used less often (for example, EG-61), which are characterized by a high margin of safety due to their impregnation with special compositions.
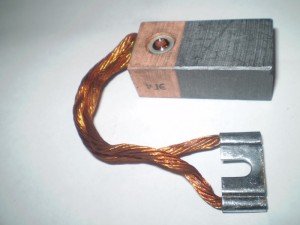
The generator and brushes for it on domestic cars are located under the right headlight of your "iron horse". Finding them is easy. It is enough to open the hood to see the generator - its winding and two lids, outwardly similar to cans, come to the surface.
With planned maintenance, of course, no one pays attention to the small elements of the generator. It is for this reason that the breakdown of his brushes always comes as a surprise to the driver. Experts advise after 50 thousand kilometers (or once every four years) to check their serviceability and functionality, and then there will be no problems with the operation of the generator.
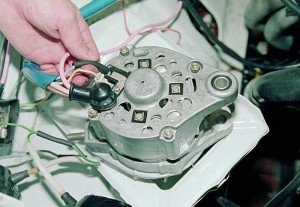
It is noteworthy that you can check the brushes (and change them if necessary) without dismantling a rather bulky generator. In addition, the following symptoms may signal the need to look under the hood of a car and check the graphite brushes:
- unpredictable disconnection of electronic devices in the vehicle, occurring for unknown reasons;
- reducing the illumination of the car interior and external light sources;
- voltage reduction;
- an unreasonably fast discharging car battery, which, moreover, is then very difficult (and sometimes impossible) to charge.
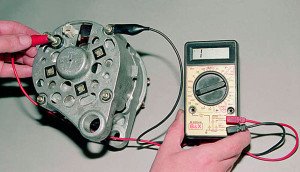
Any of these symptoms tells the motorist that he most likely needs to remove the old brushes and replace them with new ones. You can easily check old products for functionality. It is necessary to fold the "minus" away from the battery, remove the voltage regulator and visually evaluate to what height the graphite parts of interest to us protrude from their "shelter". The brushes need to be changed urgently when their height is less than five millimeters.
We must say right away that this operation is very simple and does not require special skills from the driver. First, as already mentioned, it is required to fold the "minus" from the battery, then dismantle the regulator (it is located in relation to the generator on the opposite side), and then do the following:
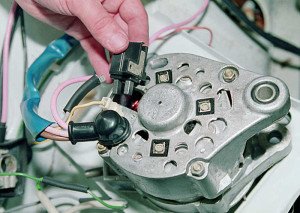
- Thoroughly remove soot and dust from the holder seat as well as the pressure springs and the slip ring. This operation is performed with a soft bristled brush. Sometimes it may be necessary to grind the graphite brushes to the collector using fine glass paper (its grain size should be about 100).
- Install new products and make sure they move freely in the brush holder.
- In the reverse order, assemble the unit, and then connect the previously wrapped wire to the battery.
If you bought a prefabricated structure (regulator plus brushes), its installation also does not cause any problems.
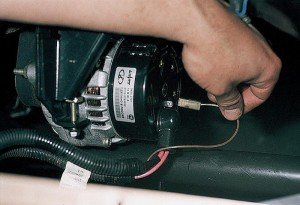
Disconnect the "minus", remove the cap made of rubber from the "plus" wire, and then dismantle the unit by unscrewing the fastener nut. Then you will need to remove the plastic casing and remove the three spring clips located around the perimeter of the block. Using a Phillips screwdriver, unscrew the brushes along with the voltage regulator, and disconnect all the wires leading to it. Mount the purchased prefabricated structure to the vacated space. Operation completed!
The generator is the main unit in the vehicle's electrical supply system. Sometimes it breaks down, but you shouldn't throw it away and rush to buy a new one. Often the problem is that the generator brushes have worn out and it is enough to replace them for the further uninterrupted operation of this unit. Replacing the generator brushes is a fairly simple procedure, but first it is worth finding out what signs may indicate brush wear.
Often, when carrying out a preventive inspection of a car, they do not pay attention to various trifles. Generator brushes are one of those little things, if they wear off, the generator will stop charging the battery. Experts recommend inspecting the brush assembly every 45-55 thousand kilometers. The brushes can be diagnosed without removing the generator, and in some cases it may even be possible to replace them without removing the main unit.
- The electrical devices of the car suddenly turn off (even while driving);
- Headlights, dimensions and even interior lighting dims and blinks;
- A sharp decrease in the voltage of the vehicle's on-board network;
- Sharp discharge of the battery, which will be very difficult to recharge in the future.
Each of these points may indicate wear on the generator brushes, which are located inside this unit. Many people wonder how to check the brushes. In order to check what the residual length of the generator brushes is, it is enough to disconnect the generator from the battery and remove the voltage regulator. After this procedure, you can determine by eye how worn out any of the generator brushes. If the length is less than 0.5 centimeters, you need to change the brushes unambiguously. Checking the brushes should be carried out during a routine inspection of the generator.
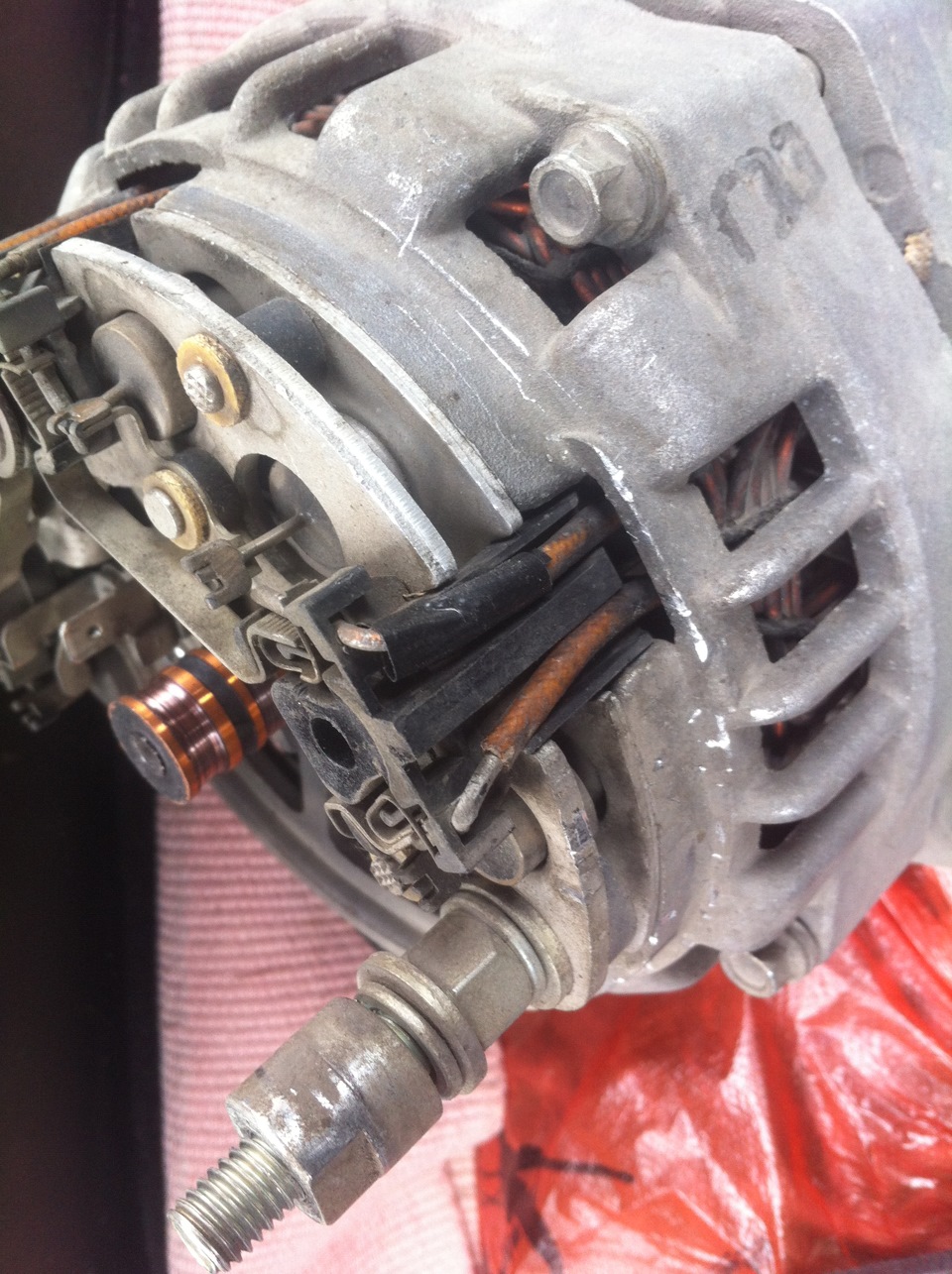
Changing the generator brushes is not difficult. They are located in the rear half of the device and are held in place by a single bolt.The brush assembly itself is located next to the slip rings and is connected to a voltage regulator. The brushes are held close to the rings by springs. Knowing the diagram of the generator device, it is easy to find the brushes. To replace, you need a standard set of tools:
- Several wrenches;
- A pair of screwdrivers;
- New brushes;
- WD-40 fluid (in order not to rip the threads of the bolts).
The brushes can be replaced in two ways, by removing or not removing the generator. Which method is best to use will be prompted by the design of the car, or rather the place in the engine compartment. If there is free space, it is not difficult to repair the generator brushes without removing the unit, and if the engine occupies the entire engine compartment space, you cannot do without removing the generator.
With the generator removed, the replacement of the brushes will be much easier. With access from all directions, it is easy to see the wear of the brushes and to replace them. The main problem in this option will be to remove the generator from the car. It is necessary to unscrew the generator mounting bolt, loosening the belt tension, remove it and unscrew the mounting bolts connecting the generator to the engine housing. If you can reach the generator from above, consider yourself lucky. There are often cases when, to remove the generator, you have to remove not only the air filter and pipes, but even remove the radiator.
First of all, you need to clean the mounting place of the brush holder from dirt and dust. It can be wiped clean with solvent and then blown out with compressed air. After that, you need to remove the brushes, for this they need to be unsoldered. Leaving the generator without brushes, be sure to clean all contacts and check the springs for elasticity. It is advisable to polish the slip ring after that.
The replacement itself consists in unsoldering the old wires from the worn out brushes and soldering them to a new set. Care must be taken when carrying out this operation, as the material of the brushes is very fragile. After installing the brushes in the seat, make sure that they are free to move.
The installation of new brushes should be carried out in the reverse order, after which the generator is assembled and installed on the vehicle. It is recommended to change the bearings of the generator during the procedure for replacing the brushes. When installing a generator on a car, the main thing is to correctly adjust the belt tension. If the tension is insufficient, the belt will slip on the rollers.
It so happens that the computer in the car begins to show a malfunction of the generator immediately after replacing the brushes. This is due to insufficient lapping of new parts. During operation, they will get used to it, and the error will disappear. If the error persists, the case is sticking due to excessive dirt. This problem can be easily eliminated by blowing compressed air through the parts. Before checking the operation of the generator, be sure to inspect the brushes for chips and cracks. New parts often have manufacturing defects.
It so happens that the brushes change together with the relay by the generator regulator. In this case, the replacement process is as follows:
- The negative terminal is disconnected from the battery;
- Remove the rubber tip from the positive wire;
- The generator is dismantled (if necessary, you need to remove the air filter housing);
- Get a block of brushes with a relay regulator;
- Retaining springs are removed;
- The brushes are unscrewed;
- All associated wiring is disconnected;
- A new block is being installed.
The generator is connected only after checking the absence of defects on the new brushes. After assembly, we put the generator in place, tighten the belt, connect the battery and start the car.
If the previous owner put a block of brushes with a relay regulator in the generator, then the question of how to change the brushes on the generator without removing it from the car is solved much easier than replacing individual brushes.With sufficient space in the engine compartment, it is also possible to replace the brushes separately without having to remove the generator.
All work with the car's electrical equipment should be started by disconnecting the battery.
- The voltage regulator is removed;
- The production of brushes is measured;
- Old brushes are soldered off;
- Contacts are cleaned;
- New brushes are soldered;
- The free movement of the generator brushes is checked;
- The regulator is installed in place;
- We connect the battery and start the car.
If everything went without errors, you will not have to suffer for a long time with the question of how to check the generator brushes. Now, knowing perfectly the generator device after disassembling it, it will not be difficult for you to repair another generator malfunction with your own hands.
A car generator is a device that takes mechanical energy from an engine and converts it into electric current, thus providing electricity to the rest of the car's units. The generator provides battery charging and power to the vehicle's engine. Therefore, the connection "engine-generator" should not be interrupted, because an inoperative generator is a battery that does not receive a charge and, accordingly, an inoperative main body of the car.
Replacing the generator will entail significant financial costs. Therefore, if you have at your fingertips all the necessary tools and knowledge of the devices of the engine compartment of the car, then you can fix the breakdown yourself (read about what to do if the car does not start - the starter turns, read in our other article).
So the generator is broken. What malfunctions can cause this device to malfunction? Let's consider them:
- The generator produces a very low voltage current.
- The generator does not generate electricity at all.
- A breakdown of the device is displayed on the dashboard in the form of a blinking light.
- The generator is charging in excess of the optimal rate.
- Generator operation is accompanied by extraneous noise.
Before you start doing generator repairs with your own hands, it is necessary to check its technical condition and disassemble the unit into parts. Before disassembling the generator, check the condition of the belt and its tension and make sure if you are expecting a replacement of the alternator belt in the near future (read also how the timing belt is replaced with a VAZ 2109). Checking consists in pressing your finger on the middle of this part of the generator. If the belt is in good condition, then it should not fall by more than half a centimeter when pressed. It should be noted that the new belt should not bend more than 2 mm. If the belt is not worn out, but the tension is weak, then the defect can be corrected by tightening the generator belt. Also scroll the generator tension roller, if it scrolls with difficulty and squeaks, then it will need to be oiled, or put a new roller instead.
The technical condition of the generator can be checked using the following measuring instruments:
The rotor speed is measured using a tachometer (usually located next to the speedometer on the dashboard). During normal operation of the generator, the indicators of this device should not be less than 2000 rpm, while the norm is 5000 rpm.
Let's consider the reasons that can cause generator breakdown. So, if the generator does not generate a charge, then the following phenomena may be the reasons for this:
- Fuse or contacts blown.
- Broken or worn out generator brushes.
- The regulator relay is out of order.
- Due to the short circuit of the winding, an open circuit occurred in the stator or rotor circuit.
In order to fix the first three malfunctions from the list, you just need to replace the worn out parts of the generator, having previously, of course, disassembled it.
- First of all, remove the brush holder along with the voltage regulator, carefully unscrewing all fasteners.
- Remove the tensioning bolts and then the cover with the stator.
- Remove the cover from the stator by first disconnecting the phase windings from the output wires on the rectifier unit.
- Next, remove the pulley from the shaft and the front cover of the generator using a special puller.
The assembly of the generator is carried out in reverse order.
In the event of a short circuit in the winding, you will need more serious action than a simple replacement of the part. So, a broken winding can either be repaired or replaced with new wires. Often the winding breaks off near the slip rings. In addition, breakdown can occur due to unsoldering of any of the ends of the winding. Such a malfunction can be repaired by rewinding the coil in the area of the gap back from the rotor winding. Further, the broken end of the winding must be removed (evaporated) from the slip ring and the previously unwound wire must be soldered there. The wiring is very easy to repair by re-soldering the wiring.
A weak or too strong generator charge is indicated by a damaged relay, which must be replaced when the generator is repaired.
If the generator voltage check showed that the device is working properly, but the indicator is flashing on the instrument panel, then, most likely, one of the diodes that are responsible for powering the light in the indicator has failed. These diodes are located in the generator itself, and replacement is carried out after disassembling the device.
Noise unusual for a generator may be indicated by wear of the rotor bearing. If an inspection reveals that the generator bearing is worn out, it will need to be replaced. If the incomprehensible sounds of the generator are associated with the absence of play in the bearing, then it can be simply filled with oil, having previously washed it in gasoline. Extraneous sounds will then disappear.
Thus, you can even repair the generator on your own in your garage (as well as overhaul of the engine, in fact). When checking and replacing parts of the device, observe safety precautions and be careful, because the electrical system should not be damaged in this case.
I have already talked about the device of electric current generators, which are arranged similarly to synchronous motors, only differ from them in the collector, therefore the process of troubleshooting and repairing electric current generators is in many ways similar to them.
In this article I will tell you in detail using the example of a do-it-yourself repair of an automobile generator, because it is it that most people most often encounter with repair. The principle of repairing a generator with your own hands as part of a power plant will be similar. Only a voltage rectifier will not be built into its case and the output voltage regulation will work differently.
Cars use a three-phase generator alternating current, but as is known in the on-board network, a constant voltage of 12 volts. To obtain direct current, a rectifier consisting of 6 diodes is used, and a voltage regulator is provided to keep the voltage of 12 volts within acceptable limits.
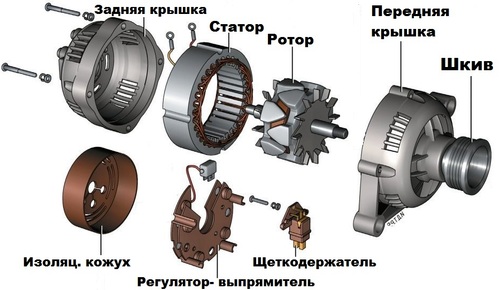
The generator is arranged quite simply. Voltage is applied to the rotor through graphite brushes and slip rings to excite it. It is driven by a pulley through a belt drive. The rotor rotates in bearings. Electric voltage is generated in the stator windings and converted into a constant voltage using six power semiconductor diodes, three of which are connected to the positive terminal of the generator, and the other three to the negative terminal and "vehicle ground".
- If on the dashboard of the car does not go out after starting control lamp, this indicates that the generator does not work and does not give current. But sometimes the cause of the alarm can be poor contact of the connector, wires, or a malfunction of the relay.
- Battery discharge. But keep in mind that sometimes the battery is discharged and does not have time to be charged by a working generator when moving over short distances and with the light and electrical devices of the car turned on as much as possible.
- Generator at engine speed 2000-2500 gives out voltage below the permissible limit of 13.2 Volts.
- If the generator generates a voltage above the permissible limit of 14-14.8 Volts (depending on the model), this indicates a faulty voltage regulator, which leads to a disastrous overcharge for the battery.
Before removing the generator for repair, check:
- Tensioning the drive belt and rotating the pulley, tightening its nut.
- Connection to the vehicle body of the battery and generator.
- The integrity of the fuses.
- Bearing play. It is checked in the same way as for electric motors according to this instruction.
- Before removing and disassembling power unit, if there is generator noise during operation, try disconnecting the wires. If the noise has disappeared, then this indicates a short circuit or interturn short circuit of the stator windings or a short circuit to ground. Repair is not advisable, replacing the generator with a new one will be cheaper. If the noise persists, this indicates bearing wear. They need to be replaced.
- Most often worn brushes are the cause of the malfunction... Check and replace them.
- Poor contact between brushes and slip rings. Check if the spring is not pressing well. It can be stretched or replaced if necessary. Inspect slip rings for scorching or dirt. Use the finest sandpaper for cleaning and a rag for dirt. If the slip ring is severely worn, the rotor must be replaced.
- Damage to the rotor winding can be checked with a multimeter. The windings should ring among themselves for a short circuit or show a small resistance. If the windings are intact, then it is necessary to ring for the lack of electrical connection between them and the case. A defective rotor cannot be repaired and must be replaced.
- Damage to the stator winding are checked in the same way. The multimeter should show a short circuit or very small resistance between the terminals. And there should be no electrical contact between the winding and the generator case. The defective stator must be replaced.
- Check all diodes in the rectifier. They must conduct electric current only in one direction, in the opposite direction (we swap the positive and negative probes) - the resistance is large enough. In the example in the picture, it is necessary to check each diode between points numbered 1 and number 2.
Recommend additionally will get acquainted with the instructions for repairing synchronous electric motors with their own hands, because they carry out troubleshooting in almost the same way as for generators.
The generator set belongs to a rather complex automotive electrical equipment, however, maintenance of the generator and DIY generator repair most motorists can handle.
From theory. A working generator must supply a voltage of the order of 13.7 - 14.5 V to the car's electrical circuit, sufficient for its normal operation.
There is a separate article on the possible causes of a generator failure, where the reasons for a generator failure are described in detail.
Reminder. Do not try to test the generator's functionality by disconnecting it from the battery while the engine is running. A voltage surge that occurs when the terminal is removed can damage the diode bridge of the generator.
If, after checking the integrity of the fuse, tensioning the alternator belt, checking the tightening of the pulley, the generator malfunction remains, then go ahead, namely:
- the brush assembly is removed and the generator brushes are checked, the ease of movement of the brushes in the brush holder and the height of their protrusion
- a faulty relay, the regulator is replaced with a working one or is regulated (VAZ, ZAZ, GAZ, etc.)
If the generator malfunction remains, then the generator must be disassembled, except for the generators, where the diode bridge (if, say, the problem is in it) is taken out, and it can be replaced without disassembling the generator.
Dismantling the generator
before disassembling the generator, you need to mark the relative position of the covers so as not to get confused during assembly
• The alternator pulley is removed
• remove the terminal on the output of the brush assembly (car generators vaz output -67) and remove the brush holder with a voltage regulator (if it is a combined unit). You need to act carefully so as not to damage the generator brushes.
• the ground wire is given (-)
• the power wire is given and removed, as well as the wire from the capacitor going to the same contact (on the VAZ this output is 30), if you perform DIY vaz generator repair.
• the nut that secures the voltage output is given (the contact bolt, where the (+) thick power wire was screwed). This must be done since this power lead is attached to the diode bridge inside the generator and it will be impossible to remove the back cover.
• It is checked again that there are no unused wires left, going either to the terminals of the generator, or to the inside of it.
Further, the bolts are given, tightening the covers and the stator winding. Then the back cover is carefully removed together with the stator winding (the stator winding can "stick" to the front cover and the leads of its windings connected to the diode bridge fixed on the back cover can be damaged). First, the stator winding must be separated from the front cover, for which you must walk carefully with a screwdriver's sting.
along the contour between the cover and the stator. Relevant for - VAZ car generators.
Remains in the disassembly of the generator, the front cover and the rotor are not removed. If the generator cover cannot be removed from the rotor by hand,
then you need to pick up two bars, put a cover with a rotor between them and knock it out of the front cover with light blows on the rotor shaft (through a soft metal or wooden block). In order not to damage the generator rotor, place a piece of rags between the bars.
Disconnect the ends of the windings from the diode block and remove the stator and diode bridge of the generator.
The generator has been disassembled and all components must be checked. The check can be performed both with the help of the device and with a test lamp.
- check for breakage
With the help of a test lamp and a battery, the terminals of the stator windings are checked. The lamp is alternately connected between the terminals of all windings. In this case, the lamp should be lit in all three cases. When the lamp does not light up in one of the connections, it means that there is an open circuit in the stator winding and it is necessary to replace the winding or stator.
When checking with the device, all the ends of the windings should "ring" among themselves.
If, in this case, we take into account the cost of replacing the stator winding from a professional electrician, and the cost of the stator itself, then it is more profitable to purchase a new stator, since an ordinary car enthusiast cannot independently replace the stator winding.
- checking the stator for a short circuit of the windings on the case.
To do this, connect one end of the test lamp to the output of the stator winding, and the wire from the battery to the stator housing. If the winding does not short to the body, then the lamp will not light. When the lamp is on, this indicates that there is a short circuit and the stator needs to be replaced.
If the check has shown that the stator winding is working properly, it must be carefully inspected for overheating (usually with breakdown of diodes) and if there are traces of overheating on the winding, then the stator must also be replaced.
Three diodes of the rectifier unit (bridge) are "positive", they have a "plus" on the body and are pressed into one plate of the bridge, and three diodes are "negative", they have a "minus" on the body and are pressed into another plate of the block or into the generator body.Between them is a non-conductive current plate that separates them.
A diode in good condition only passes current in one direction. When there is an open circuit in the diode, then it does not pass current at all, but when it passes current in both directions, then there is a short circuit in it. In both cases, replacement of the diode bridge is required.
- For a short circuit, the diodes in the rectifier unit (horseshoe) can be tested directly on the car without removing the generator. Disconnect alternator and battery leads before checking. The diode bridge can be checked using again a test lamp ((1 - 5 W, 12 V) and a battery, as seen in the figure.
where: a - checking "positive" and "negative" diodes at once - the lamp burning will mean that there is a short circuit in one of the diodes and it is required replacement of the diode bridge of the generator
b - checking the "negative" diodes - the lamp burning indicates a short circuit in the negative diodes / diode; в – checking "positive" diodes - lamp burning indicates a short circuit of positive diodes / diode.
1 – generator; 2 – control lamp; 3 – rechargeable battery
If, after checking, it turns out that the generator windings are in working order, and there is no short circuit in the diode bridge, then the cause of the malfunction (decrease in the charging current) is an open circuit in one of the diodes.
* rotor check
- the resistance of the generator excitation winding is checked between the two rings and it should be - 4.3 ± 0.2 Ohm.
- checking the winding for its closure to the rotor housing. The test lamp is connected to the body, and the battery wire is connected in turn to each ring. The lamp should not light up in both cases, otherwise the rotor must be replaced, since the winding is closed in it.
![]() |
Video (click to play). |
As you can see from the article, servicing the generator and repairing the generator with your own hands is not very difficult and is quite within your power.