In detail: do-it-yourself high-pressure hose repair for Karcher from a real master for the site my.housecope.com.
There is an equipment base in the tourist club Korbita. There is a well and a Karcher pressure washer. For three years the whole system worked without failures. And now, the Karcher hose broke. Many questions immediately arose. Where to buy a new hose? Where to run if Karcher is urgently needed?
We found out everything and share our experience! First, the Karcher hose is a high pressure hose and can be repaired. Secondly, Karcher high-pressure hoses can be repaired with your own hands, or you can do it in a specialized organization.
Do-it-yourself Karcher hose repair technology is very simple. First, cut the hose along the edges of the gap. Then we make the cuts even - either with special scissors, or with a machine, or with a cutting tool.
After that, we go to a special store for a fitting (a connecting tube along the inner diameter of the hose) and special power clamps. Ideally, put a pair of clamps on each side. Attention, simple clamps will not work!
Such a do-it-yourself hose repair has disadvantages. If the hose is used in the washing area, then the repair unit (clamps) will constantly cling to something, this is inconvenient.
Another minus. If you don’t have a fitting and a power clamp in your garage (in your warehouse), you still spend time looking for and buying a fitting of the desired diameter and clamps.
But there are also pluses. Such a repair of Karcher high pressure hoses will not be expensive. Especially if you need to lengthen the hose or make a few repair connections.
If you have little free time, you should turn to professionals. Pros . Repair the Karcher hose on site in 10 minutes. Repair carefully, the repair unit will not interfere with the work with the sink. Repaired on professional equipment and reliably.
![]() |
Video (click to play). |
Minuses . The cost of repair is 500-800 rubles for each node. That is, at a market value of a non-original, but acceptable in quality, Karcher hose of 2000-2500 rubles (autumn 2018), it makes sense to make repairs if you have a relatively new hose and no more than 2 damage. In other cases, it is worth thinking about a new hose.
Subscribe to the news of the tourist club "Korbita"!
Don't miss cool events and important information!
We have compiled a list of organizations in major cities of the Central Federal District where you can repair the Karcher hose:
If your city is not listed, try clicking here.
At least in a nutshell, but we need to talk about the reasons for the repair. In our case, the reason is this - the sink itself “shudders” at startup. The hose coming from the sink gradually rubbed against a sharp corner. But there may be other reasons - poor-quality hose material, mismatch of the operating pressure of the hose with the washing pressure, obsolescence of the hose, and others. Of course, all these reasons must be eliminated.
That's all! Keep your tool in good working order, keep enjoying your hands! Have a good day!
P.S. If you have up-to-date information or want to add an organization, write about it in the comments.
NB! Dear visitors! Please note! Only articles where the author declares the tourist club "Korbita" are the position of the leadership of the tourist club "Korbita" on the topics expressed in the article at the time of publication.
If the hose is torn off the flange, then you need to cut off the damaged section of the hose evenly, to the point where there are no extensions, cracks and undamaged cord.
Next, purchase the necessary flange and install it - fortunately, a large number of them are sold in auto stores and there is also a choice.The flange is inserted into the hose and simply crimped well with the help of a stop in the vise jaws and hammer blows from the third upper side.
If the damage is somewhere along the length of the hose, for example, a cut, a rupture, or something else, then we do exactly the same as in the first case, cut the hose and cut it to a whole, but here a connector of the desired diameter and a pair of clamps will help - just buy clamps not cheap, but good ones like those in the photo!
Repairing a high-pressure hose at Karcher is an almost hopeless business. If it is damaged in a straight section, crushed, chopped, and so on, then finding a double-sided Christmas tree branch pipe and compressing it at home on a hose is very problematic. You can do without buying a new (very expensive) hose only if it has begun to be torn off the outlet metal pipe. That is, the thread on the union coupling was torn off, and I don’t want to buy a new hose. Russian artisans do this:
A section of a rectangular pipe is taken, in my opinion, 45x25, the “CLIP” grip is carefully and thoughtfully cut out of it. With slots for the hose itself and for the pipe. I think it looks better in a photo. I repeat - if you don’t want to buy a new hose at all.
The design of the product, of course, is not a museum one, but it works properly. The connection may slightly dig, but this is not critical.
High-pressure hoses, more commonly referred to as high-pressure hoses (HPHs), are designed to create or absorb the working force that is transmitted under high pressure by liquids or gases pumped into them.
The main field of application of high pressure hoses is hydraulic and pneumatic systems of various devices and mechanisms. Outside of industrial production, motor vehicle owners most often deal with high-pressure hoses, these are power steering hoses (Power Steering), and those who use high-pressure pumps, for example, the most common Karcher brand in our country.
The design of the high pressure hose is due to the need to withstand internal pressure, which can reach up to several hundred atmospheres.
In addition, the inner surface of the high-pressure hose must be impervious to the media being transported. Therefore, its lower layer is made of oil and petrol resistant rubber or synthetic rubber.
For the manufacture of the upper, thicker layer of the high-pressure hose, wear-resistant rubber is used, which, if necessary, is supplemented with thermal protection in the form of a corrugated coating, metal or polymer.
A metal wire is wound in several layers between the upper and lower layers of rubber, thanks to which the hose receives the necessary rigidity and strength. Layers of wire are interspersed with thin rubber films.
Depending on the method of winding the wire, there are two types of high-pressure hoses:
- Coiled. In the production of this type of hose, the coils of wire are wound in even rows.
- Braided. In this case, the coils are wound at an angle to the axis of the hose so that the coils of the previous layer cross with the coils of the next layer of wire. Braided hoses are more durable and able to withstand more pressure than winding hoses.
In addition to the wire, textiles can act as an internal rigid frame.
The number of wire layers and the thickness of the rubber layers are set by standards that determine the scope of one or another type of high pressure hoses.
To fix the hoses in place, fittings (tips) are mounted at their ends, which are of the following types:
Fittings are fastened to the ends of the hose using compression couplings, which are pressed on special machines.
Depending on the type of shank, fittings are classified into series:
- Universal. This series can be used in all high pressure hoses except coil type hoses.
- Interlock. The series is used for winding sleeves.
When installing fittings of this type, it is imperative to remove both layers of rubber, inner and outer.
Fittings for high pressure hoses
The operation to remove layers of rubber is called hose debarking.
Fitting failure is the most common cause of high pressure hose failure. This is due to the magnitude and intensity of the loads they experience.
The causes of damage can be divided into the following types:
- Manufacturing defects. Most often, this is poor-quality crimping of the joint of the fitting with the hose, due to the use of handicraft or non-adjusted equipment.
- Damage received during the operation of the main mechanism. They appear as cuts and ruptures in the hose. The most common cause of them is the sagging of the high pressure hose due to the wrong length.
- Damage caused due to inconsistency of the HPH parameters with the operating conditions. This could be a hose rupture or a fitting failure, due to which the pressure turned out to be higher than that for which the hose was designed.
- In the same row, damage to the outer layer of the high pressure hose should be mentioned when it is used in a different temperature regime for which it is designed.
Important! In order to protect as much as possible from possible damage to the high pressure hoses, when choosing them, it is necessary to carefully check the compliance of their characteristics and parameters with the operating conditions.
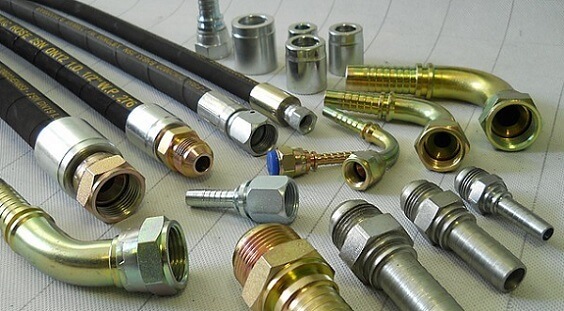
High pressure hoses with fittings
First of all, we are talking about the calculated value of the maximum allowable value of pressure, temperature and the minimum bending radius of the hose.
Among the damage to high pressure hoses, the most common are the following:
- Fittings corroded.
- Broken sleeve.
- Abrasion and wear of the top layer of the hose.
- Sleeve blockage.
- Violation of the tightness of the fitting connection.
- Hose fitting torn off.
- Fitting joint leak.
- Thermal damage to the inner layer of rubber.
Back to content ↑
From the foregoing, we can conclude that the repair of high pressure hoses consists either in replacing the damaged area or in replacing fittings that have become unusable.
When replacing a damaged area, as well as when replacing fittings, it will be necessary to crimp the couplings, that is, technologically these two actions are very similar.
The sequence of operations in this case looks like this:
- The damaged sleeve is disconnected from the main mechanism.
- On a cutting machine, a new sleeve is cut to the size of the old one. Moreover, for measurement, the distance between the ends of the nipples at its ends is taken. It is better to choose a high pressure hose designed for more pressure than that for which the old high pressure hose was designed.
- The markings that are placed on the sleeves will help you choose the right diameter.
Factory marking DN indicates the diameter of the internal channel of the hose.
In case of difficulty, it is easiest to measure the old fitting with a caliper and thread gauge, which will allow you to accurately set the desired diameter and thread pitch and then select the desired parameters of the new fitting from the tables.
If a non-standard connection is found, then the repair is carried out using a repair fitting.For this, the head of the old fitting is taken, to which the part to be crimped is soldered.
This method is often used by motorists for emergency repair of power steering hoses, as well as owners of pumps and Kircher mini-washers.
The reason for the occurrence of damage to the power steering hoses most often is that when the steering wheel is rotated due to friction, a serious effort occurs. This force causes deformation of the elastic element, which changes the size of the holes in the distribution mechanism that regulates the pressure drop in the hydraulic cylinder.
As a result, the power steering sleeve, connected to the restrictive valve, wears out. This power steering sleeve is designed for pressure, depending on the brand of car, from 70 to 130 kgf / cm2.
At such a high pressure, repairing a damaged power steering hose with clamps or wire is almost impossible.
There are two options left: either replace the entire power steering tube, or replace only the damaged part of it by moving the fittings to a new hose.
Moreover, it is better to rearrange the fittings in a special workshop.
Replacing and installing the power steering hose is as follows:
- The front of the car is raised on jacks.
- The steering wheel turns all the way to the left.
- A syringe with a tube attached to a needle is pumped out of the hydraulic booster reservoir.
- After that, the hose is disconnected, the working openings of the hydraulic system are closed with plugs.
Power Steering Hoses
The selection of a new hose is carried out with exact observance of the diameter, otherwise the performance of the hydraulic booster may change.
Back to content ↑
People with professional skills are able to repair high pressure hoses for hydraulic systems of a car or a Karcher pump manually using the simplest equipment and fixtures. But the quality of such repairs will remain in doubt, which is highly undesirable.
It must be understood that high pressure creates a zone of increased risk, when a breakdown or abnormal operation of the high pressure hose can lead to serious consequences. Especially when it comes not to the Karcher pump, but to the hydraulic systems of heavy equipment. A far from complete list of such consequences looks like this:
- Shooting of fittings and dangerous outflow of torn hoses;
- Fire or explosion of the working fluid;
- Loss of vehicle control;
- Poisoning and burns due to liquid spilled from the hoses.
Accurate observance of instructions, attentiveness and accuracy during installation work, as well as contacting specialists if necessary, will help to avoid this and ensure long-term and high-quality operation of the repaired pipeline.
I am a crocodile, I am a crocodile, and I will be a crocodile!
Sibgidravlika, LLC, repair company
[COLOR=rgb(164, 124, 39)]Operations of the organization:[/COLOR]
Repair of special vehicles, Rubber products, Repair of industrial equipment, Spare parts for agricultural machinery
Knitted, 52/2
just take the hose with you, they will make a new hose for the old fittings.
10 meters about 1500 rubles.
oops, plastic.
By the way, they machined the fitting for me according to the model themselves.
Repairing a high-pressure hose at Karcher is an almost hopeless business. If it is damaged in a straight section, crushed, chopped, and so on, then finding a double-sided Christmas tree branch pipe and compressing it at home on a hose is very problematic. You can do without buying a new (very expensive) hose only if it has begun to be torn off the outlet metal pipe. That is, the thread on the union coupling was torn off, and I don’t want to buy a new hose. Russian artisans do this:
A section of a rectangular pipe is taken, in my opinion, 45x25, the “CLIP” grip is carefully and thoughtfully cut out of it. With slots for the hose itself and for the pipe. I think it looks better in a photo.I repeat - if you don’t want to buy a new hose at all.
The design of the product, of course, is not a museum one, but it works properly. The connection may slightly dig, but this is not critical.
High-pressure hoses, more commonly referred to as high-pressure hoses (HPHs), are designed to create or absorb the working force that is transmitted under high pressure by liquids or gases pumped into them.
The main field of application of high pressure hoses is hydraulic and pneumatic systems of various devices and mechanisms. Outside of industrial production, motor vehicle owners most often deal with high-pressure hoses, these are power steering hoses (Power Steering), and those who use high-pressure pumps, for example, the most common Karcher brand in our country.
The design of the high pressure hose is due to the need to withstand internal pressure, which can reach up to several hundred atmospheres.
In addition, the inner surface of the high-pressure hose must be impervious to the media being transported. Therefore, its lower layer is made of oil and petrol resistant rubber or synthetic rubber.
For the manufacture of the upper, thicker layer of the high-pressure hose, wear-resistant rubber is used, which, if necessary, is supplemented with thermal protection in the form of a corrugated coating, metal or polymer.
A metal wire is wound in several layers between the upper and lower layers of rubber, thanks to which the hose receives the necessary rigidity and strength. Layers of wire are interspersed with thin rubber films.
Depending on the method of winding the wire, there are two types of high-pressure hoses:
- Coiled. In the production of this type of hose, the coils of wire are wound in even rows.
- Braided. In this case, the coils are wound at an angle to the axis of the hose so that the coils of the previous layer cross with the coils of the next layer of wire. Braided hoses are more durable and able to withstand more pressure than winding hoses.
In addition to the wire, textiles can act as an internal rigid frame.
The number of wire layers and the thickness of the rubber layers are set by standards that determine the scope of one or another type of high pressure hoses.
To fix the hoses in place, fittings (tips) are mounted at their ends, which are of the following types:
Fittings are fastened to the ends of the hose using compression couplings, which are pressed on special machines.
Depending on the type of shank, fittings are classified into series:
- Universal. This series can be used in all high pressure hoses except coil type hoses.
- Interlock. The series is used for winding sleeves.
When installing fittings of this type, it is imperative to remove both layers of rubber, inner and outer.
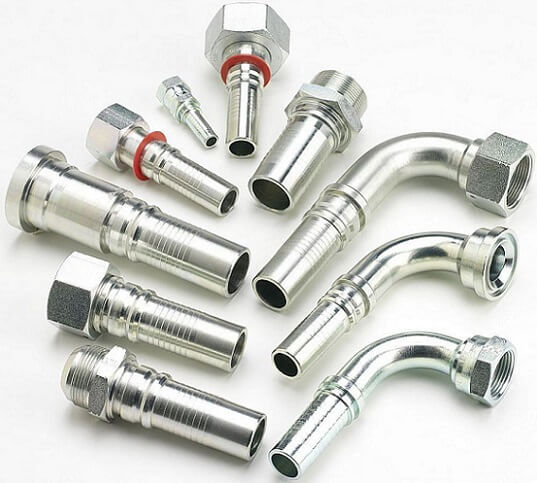
Fittings for high pressure hoses
The operation to remove layers of rubber is called hose debarking.
Fitting failure is the most common cause of high pressure hose failure. This is due to the magnitude and intensity of the loads they experience.
The causes of damage can be divided into the following types:
- Manufacturing defects. Most often, this is poor-quality crimping of the joint of the fitting with the hose, due to the use of handicraft or non-adjusted equipment.
- Damage received during the operation of the main mechanism. They appear as cuts and ruptures in the hose. The most common cause of them is the sagging of the high pressure hose due to the wrong length.
- Damage caused due to inconsistency of the HPH parameters with the operating conditions. This could be a hose rupture or a fitting failure, due to which the pressure turned out to be higher than that for which the hose was designed.
- In the same row, damage to the outer layer of the high pressure hose should be mentioned when it is used in a different temperature regime for which it is designed.
Important! In order to protect as much as possible from possible damage to the high pressure hoses, when choosing them, it is necessary to carefully check the compliance of their characteristics and parameters with the operating conditions.
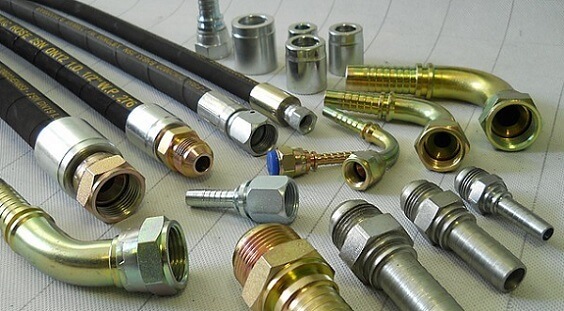
High pressure hoses with fittings
First of all, we are talking about the calculated value of the maximum allowable value of pressure, temperature and the minimum bending radius of the hose.
Among the damage to high pressure hoses, the most common are the following:
- Fittings corroded.
- Broken sleeve.
- Abrasion and wear of the top layer of the hose.
- Sleeve blockage.
- Violation of the tightness of the fitting connection.
- Hose fitting torn off.
- Fitting joint leak.
- Thermal damage to the inner layer of rubber.
Back to content ↑
From the foregoing, we can conclude that the repair of high pressure hoses consists either in replacing the damaged area or in replacing fittings that have become unusable.
When replacing a damaged area, as well as when replacing fittings, it will be necessary to crimp the couplings, that is, technologically these two actions are very similar.
The sequence of operations in this case looks like this:
- The damaged sleeve is disconnected from the main mechanism.
- On a cutting machine, a new sleeve is cut to the size of the old one. Moreover, for measurement, the distance between the ends of the nipples at its ends is taken. It is better to choose a high pressure hose designed for more pressure than that for which the old high pressure hose was designed.
- The markings that are placed on the sleeves will help you choose the right diameter.
Factory marking DN indicates the diameter of the internal channel of the hose.
In case of difficulty, it is easiest to measure the old fitting with a caliper and thread gauge, which will allow you to accurately set the desired diameter and thread pitch and then select the desired parameters of the new fitting from the tables.
If a non-standard connection is found, then the repair is carried out using a repair fitting. For this, the head of the old fitting is taken, to which the part to be crimped is soldered.
This method is often used by motorists for emergency repair of power steering hoses, as well as owners of pumps and Kircher mini-washers.
The reason for the occurrence of damage to the power steering hoses most often is that when the steering wheel is rotated due to friction, a serious effort occurs. This force causes deformation of the elastic element, which changes the size of the holes in the distribution mechanism that regulates the pressure drop in the hydraulic cylinder.
As a result, the power steering sleeve, connected to the restrictive valve, wears out. This power steering sleeve is designed for pressure, depending on the brand of car, from 70 to 130 kgf / cm2.
At such a high pressure, repairing a damaged power steering hose with clamps or wire is almost impossible.
There are two options left: either replace the entire power steering tube, or replace only the damaged part of it by moving the fittings to a new hose.
Moreover, it is better to rearrange the fittings in a special workshop.
Replacing and installing the power steering hose is as follows:
- The front of the car is raised on jacks.
- The steering wheel turns all the way to the left.
- A syringe with a tube attached to a needle is pumped out of the hydraulic booster reservoir.
- After that, the hose is disconnected, the working openings of the hydraulic system are closed with plugs.
Power Steering Hoses
The selection of a new hose is carried out with exact observance of the diameter, otherwise the performance of the hydraulic booster may change.
Back to content ↑
People with professional skills are able to repair high pressure hoses for hydraulic systems of a car or a Karcher pump manually using the simplest equipment and fixtures. But the quality of such repairs will remain in doubt, which is highly undesirable.
It must be understood that high pressure creates a zone of increased risk, when a breakdown or abnormal operation of the high pressure hose can lead to serious consequences. Especially when it comes not to the Karcher pump, but to the hydraulic systems of heavy equipment. A far from complete list of such consequences looks like this:
- Shooting of fittings and dangerous outflow of torn hoses;
- Fire or explosion of the working fluid;
- Loss of vehicle control;
- Poisoning and burns due to liquid spilled from the hoses.
Accurate observance of instructions, attentiveness and accuracy during installation work, as well as contacting specialists if necessary, will help to avoid this and ensure long-term and high-quality operation of the repaired pipeline.
Do-it-yourself high-pressure washing hose crimping without special crimping tools. (well, almost without 🙂)
ps. The hose has been tested and works great.

Look at Yegorov's lawyer collar

but did not try to compress with a simple clamp
of which there are many on the internet.

Thanks for the advice - the clamp turned out to be a very interesting thing. I would try them, but I didn’t know about the existence of such a device. I'm thinking of doing one now - it looks like it will be a very good help. Thanks!

No, I haven't. Simple clamps twisting even in two fly off literally after 10 minutes of work, wire puffs (I hung them a few and tightened them in a row) a little longer. This method made it possible to use a really thick nail as a crimp - it works without problems. (very tight and holds up very well)
=Repair of high pressure hoses=
I decided to make a series of projects on the topic = WE DO IT OWN =. I want to show some devices that can be used to make various repairs with high quality and for a long time, sometimes even those that seem to be impossible to do at home. But everything is done by human hands, one has only to want to do it. In my works, I will show the equipment and devices that I made myself for my work, although it may not be so beautiful aesthetically, but in terms of the parameters of work, it has completely satisfied me for many years now.
Video Do it yourself Repair high pressure hoses channel Petr Zhurba
Sign up for an account. It's simple!
Already registered? Sign in here.
Karcher car wash repair (connector tube replacement)
In this article, we will look at how to do a do-it-yourself car wash repair and how to get to the outlet at the Karcher sink and replace it.
First you need to unscrew the screws (for a Phillips screwdriver) that are located on top of the handle
Then unscrew the screws securing the back cover
Now lay the sink and remove the top cover
Access to the internal components is opened and we can already remove the connector
Removing the metal bracket
Raise the pump and pull out the tube. We give a new spare part and install in the reverse order. Carefully remove the rubber sealing ring and rearrange it in a new connector. Next, install back and insert the fixing bracket.
Good day! They gave away a STIHL RE 108 sink for free. We need to change the high pressure hose.I can’t unscrew the nut near the pump with a gas wrench ((I’m afraid I won’t tear it off. How can I do it? I also have a native hose that costs 1000 UAH on some site. Maybe it’s cheaper from some other model? Thank you!
New information with article numbers and detailed photos has been added to the file on repair kits for Makita sinks.
Added kits for HW110/130/131/140/151 models
Attached is a complete file with repair kits for Makita sinks.
High pressure hydro cleaners(new).ppt
On karcher sinks, depending on the year of manufacture, there were two fastenings of a high-pressure hose, this is a hose that goes from the washer to the washing gun.
The threaded connection is used on later production sinks and is replaced by a quick coupling.
To unscrew the hose from the sink, if you have just used the sink, release the water pressure in the hose by pressing the gun button, and unscrew the hose from the sink in a counterclockwise direction.
Often, the original threads are plastic inside and this caused problems during prolonged use, the high pressure hoses sold in our store have brass threads. hose link.
The quick coupling replaces the threaded connection.
If you have just used the washer, pull the trigger on the washer gun and relieve the water pressure inside the hose.
Grasp the hose at the entrance to the sink and press with your finger or the second hand on the plastic black circle towards the sink, pull the hose away from the sink.
It is advisable to periodically, once or twice a season, disconnect the hose from the washer and from the gun, clean and lubricate the thread or quick connector.
Of course, a garden hose isn't that expensive, but I personally can't bring myself to go out and buy a new one if I can repair the existing one myself. The hose can be repaired no matter what part of it is leaking, whether it is for a high pressure washer, such as Karcher or it is a regular garden hose. Here I will tell you how to repair the end of the watering hose.
This will require:
- defective 5/8 inch (16 mm) watering hose;
- replaceable tip (in our case, a 5/8-inch sleeve);
- hose clamp;
- utility knife (anything will do, as long as you can cut the hose with it);
- screwdriver.
Having found damage, the first step is to either make sure that it is the only one, or find all and evaluate their location. In my case, only the end of the hose is damaged, the rest is quite usable. If the damaged sections are scattered along the entire length, it will be easier not to repair the hose, but to throw it away and buy a new one.
We cut off the entire damaged part of the hose with a small margin, since we need an absolutely serviceable end for repair.
Having cut off the damaged part, we put the clamp on the remaining fragment of the hose, but do not tighten it.
Carefully insert the sleeve into the tip of the hose, this should not require any extra effort. The tip should hold on its own without additional fixation. If this is not the case, then either the size of the sleeve is not selected correctly, or the structure of the hose is completely damaged. If everything is correct, the sleeve can be secured by tightening the clamp first with your hands, and then with a screwdriver.
Repair successfully completed, you can proceed to watering.
The two most commonly used hose sizes are 5/8 and 1/2 inch. Long hoses are usually slightly wider (5/8"), 1/2" (12.5 mm) hoses are usually shorter. If the exact diameter cannot be established, repair parts for both sizes can be purchased. Those that don't fit can be returned.
If the defective section of the hose is located in the middle, the procedure will be the same, only two clamps and a double-sided sleeve are required.
How to repair the high pressure hose of the Karcher mini washer. Karcher high pressure hose repair: how to do it yourself
Washers "Karcher" are different in themselves, different outlet pressure, different sleeves (hoses).
A hose rupture can be anywhere, the most “unpleasant” one can be considered a gust somewhere in the middle, such a repair is difficult.
As an option for a Karcher household sink, use a herringbone fitting
And compress it with clamps, but it is better to take reinforced steel clamps.
We buy here such a bolt with a flat head for a screwdriver.
We drill a hole in it to the full depth, as a result we have a tube with an external (external) thread.
You can buy these bushings with internal threads for the bolt,
You can simply cut threads in steel tubes.
The inner thread of the sleeve corresponds to the outer thread of the bolt (the pitch is the same).
Cut off the problem area.
We insert the bushings into the hose tightly.
We take a thick-walled copper pipe and cut it in length, slightly more than the length of the bolt.
We twist the bolt (drilled) into one sleeve, then we wind the second part of the hose with the sleeve.
We push the copper pipe onto the connection and slightly clamp it in a vice.
If someone does not understand, here is a video, only in the video a person repairs a sleeve from improvised materials.
Pay attention to how he drills the bolt, the drill is clamped in a vise, and the bolt is in the screwdriver.
Instead of a vibrating cutter, you can use a grinder.
At the finish we get a “picture”, the thread does not allow the hose to break, and the outer tube does not allow the sleeve to swell.
In my opinion, the whole “genius” of such a solution is in the simplicity of execution, and the tools used are ordinary (many have them) drill, screwdriver, tap, grinder.
Due to intensive use, the service life of high-pressure hoses in automatic car washes is short. They can be attributed to the number of car wash consumables that need fairly frequent repair or replacement. At the same time, high-pressure hoses are an important part of the smooth operation of car washes.
We carry out all types of repair work on high pressure hoses (repair connections, replacement of worn fittings) on site (directly at the sink) or replace them when repair is no longer possible. We carry out all types of work in the shortest possible time to minimize downtime. If repair is not possible in the shortest possible time, we replace the hose of any length and diameter. We make prompt delivery and installation of Karcher brand high-pressure hoses. Their distinguishing features:
- increased safety margin against corrosion of hose fittings;
- abrasion resistance.
Karcher is the world's leading manufacturer of car wash equipment. The operating temperature range for Karcher high-pressure hoses is from -40 to +130 degrees Celsius. All products of the brand for equipment of sinks are guaranteed to justify their price.
For optimal use of the working area of the car wash, the length of the Karcher high-pressure hose varies from 10 to 30 meters or more.
The costs of any emergency situation can be reduced if you are prepared for it in advance and entrust its solution to professionals. During the operation of the sink, contacts of proven specialists who carry out prompt repairs are necessary. This will be the key to its impeccable functioning and a guarantee of quality for customers.
Popular with homeowners. With this compact device, you can clean almost any surface from dirt. In addition, the use of a mini-sink allows you to reduce water costs. Therefore, such devices are often used in car washes and cleaning companies.
It is quite logical that the continuous operation of the mini-wash can lead to equipment failure. The most common problem should be considered a breakdown of the high pressure hose that provides water supply under pressure. Below are solutions for some common problems.
Diagnostics, maintenance (TO), minor repairs is 2-3 days.
Repair average 5-7 days
The repair is complex with a complete overhaul of 7-15 days.
Repair with bulkhead - 30 days.
Maintenance (TO) of all types of equipment - 20 days.
All adjustments: carburetors, cables, belt and chain drives - 10 days.
Departure for diagnostics, maintenance and minor repairs or equipment collection is possible. The cost is calculated based on the amount of work and distance.
Quite often, the cause of a hose breakdown lies in the damage to the flange, that is, the fastener that connects the hose to the minisink. In this case, it is necessary to purchase a flange that is suitable for its parameters and install it in the base of the hose. The installation procedure may require the use of pliers and a hammer, with which the fasteners are adjusted to the diameter of the hose.
Karcher hoses are often subjected to mechanical stress, which leads to the appearance of holes, tears and cuts in them. It would seem that in any other case, an overlay glued at the place where the gap appeared would be an ideal solution to this problem.
However, the pressure inside such a hose is so great that no adhesive will be able to hold the patch. The ideal option in this case is to replace this part. If, for one reason or another, a spare hose cannot be obtained, you can resort to using clamps and a connector.
The connector is an elongated piece of metal that is attached at the point of rupture. To hold it, clamps are used that “tighten” the connector, preventing it from moving.
High pressure hose repair - implies pressing a torn high-pressure hose at the ends (pressing in a new end fitting), pressing the hose at a break approximately “in the middle” - inserting a special repair fitting and its subsequent pressing, pressing the fitting for the required high pressure apparatus.
Our service center for high pressure hoses also offers you such services as:
- pressing high-pressure hoses of the required length (from 1 meter or more)
- pressing with the required fitting (for example: M22x1.5 nut; 3/8″ nut or fitting; 1/2″ nut or fitting; 1/4″ nut or fitting - check the availability of the fitting you need)
- production of a high-pressure hose for the most popular high-pressure cleaners: Karcher (Karcher) with an 8 mm fitting (a new mount for Karcher mini-washers since 2008), 10 mm, 11 mm and a M22x1.5 union nut
- pressing a high-pressure hose for connecting ceiling consoles (rods) both from the device to the console, and a hose from the console to the high-pressure gun
- production of hoses for high pressure pulling through the washing box (car wash)
Please note that we can offer you a replacement for the original plastic hose (as a rule, household mini-sinks are completed) with a more durable and professional high-pressure hose. If you just want to repair the old hose - contact us. Also, our sleeves are made or repaired from various high-pressure apparatuses: in addition to Karcher, also Kranzle, Portotecnica, Faip, Bosch, Lavor, IPC, Poseidon, WAP, Alto, etc.
![]() |
Video (click to play). |
If you have a household high-pressure apparatus that needs to be repaired, and we do not have the required fitting (household car washes), we offer the following repair option: we UNPRESSURE your original high-pressure hose, that is, remove the tips from the original hose, and subsequently press them into a new high-pressure hose of the required length, the cost of such a repair service varies depending on the complexity of the hose.
More and more new high-pressure apparatuses are being imported into our country, and as a rule, trouble is with the service center. But do not worry - we will help you: we will repair your high pressure hose or extend it to a longer length.
Also, high-pressure hoses are used when installing (pulling) a high-pressure line on a future or already operating car wash of the required length for their subsequent installation on walls and ceilings. etc. In this embodiment, a high-pressure hose is used as an analogue of high-pressure pipes. Connect from machine to gun, console or simply distribute high water pressure. We can also repair an already installed high pressure hose.