In detail: do-it-yourself repair with 7b from a real master for the site my.housecope.com.
Message # 1 Doc »29 Nov 2016, 19:04
Message # 2 korben dallas »29 Nov 2016, 20:46
Message # 3 Denis# »29 Nov 2016, 20:56
Oh familiar beast
nimble, strong, I liked it. Now look for a normal receiver for him, because he pumps up his own at the moment, and then farts into the atmosphere.
Sent after 2 hours 14 minutes 40 seconds:
Message # 4 Doc »29 Nov 2016, 23:49
Message # 6 Doc »29 Nov 2016, 23:54
engine will be 3 or 4kw 3000 rpm for picky 2800 rpm


Sent after 4 minutes 8 seconds:
or make a knight's move, replace the vulture 2 wires with 4 wires, leave the meter as it is, just stick 2 phases into the garage

Hello, Happy New Year to all of you!
And so the essence of the question is that there is a hammered compressor so7b, but due to its constructive simplicity and rather good performance, I think that it makes sense to do it.
If anyone has used such a unit, then I would like to hear reviews about it, whether it is worth using it as a painting unit or not.
I also wanted to find out what to do if the liner, or rather the babite filling, is worn out, are there any repair liners, or do you have to completely change the connecting rod?
I would also like to know what to pour into the crankcase? There is not a lot of information on this topic ..
Honestly, if it is not planned to carry out painting work on an industrial scale, this compressor is fucking unnecessary. Painfully, he is ugly and heavy. Relevant when you need a very high air flow and at minimal cost.
You can get spare parts for it, they are cheap. As a last resort, order online.
Oil - KS-19.
Thanks, at least something!
On an industrial scale, no, of course, painting is possible, and I want to make an anticorrosive underside of the car.
![]() |
Video (click to play). |
Special thanks to the oil brand!
And not vkurse what to do with the connecting rod, the babit is almost all melted .. The connecting rod is in the trash?
In principle, any compressor oil can be poured, preferably not the most expensive (passport oil consumption - 30 grams per hour), and KS-19 according to the passport it is supposed to.
Most likely, it will be easier to change the entire connecting rod, it costs about 500 rubles.
I also tend to this, but I'm afraid that it will not be successful in 500r, according to the price list in St. Petersburg, the connecting rod for the compressor costs around 1500 - 1900r somehow unjustifiably expensive IMHO
Previously, spare parts for it cost a penny, now - alas! It may turn out to be an economy. it is more expedient to take its motor as a basis, to buy a NORMAL MODERN (and small. at the same time) compressor. the head (here - who will like something, or maybe it will break off "on occasion"), "make them related" with a belt on a suitable channel, and throw out the rest. For this unit is extremely inconvenient (heavy and cumbersome).
Anyway - the receiver is normal with moisture separation and precise pressure control, a start relay (preferably with a decompressor to start), or even an “oil additive” (I don’t remember how this crap, adding oil to the air for lubricating pneumatic tool, scientifically called) - NECESSARY.
For at the construction site (where he always had a place, if you think about it) - all these nishtyaki - clearly "from the evil one."
Repeatedly came across broken pistons and valve plates (with remnants of plates). Works monstrously loud, vibrations, etc. "discomfort" - beyond any reasonable limits. These valves are unreliable. Spare parts are very expensive.
Dealing with it will protect. and regul. valves I did not succeed to the end (the first for some reason had a frenzied hysteresis loop and if they worked, then they dumped too much, the second - from time to time changed the mouth level).
They wanted accuracy - they installed large (by the diameter of the scale) pressure gauges on adapters. So they generally "seem to" the dollar rate on the Tokyo Stock Exchange - the arrow jumps SO that you understand the hell, you had to return the regular ones (and you can see the hell from afar).
As noted above, only a decent air outlet makes this venture at least somehow justified, but the pressure at the same time is still not enough for sand.
Paint brushes and so on. Nice little things - yes, but maybe it's worth looking at something else more decently?
Shl. And although my soul does not lie for China, there are some of them. Apparatus in general from 4 sput go.
ZZY. An idea about an upgrade: the power of the old 3.5 kW - the motor is quite enough even for a modern 3-cylinder head, we leave only the wheel from the healthy flywheel-propeller (it's easier to put a separate motor-fan on the side for cooling and not be fooled) and the casing.
We mount it on a suitable channel, without forgetting about the wheels and "transport" handles. The structure is taken out into the street, the receiver with ave. Pneumatic crap - in the garage against the wall.
If you need a "highly compact" arrangement - a vertical scheme in a cube frame, a motor on the bottom of the swinging frame (to adjust the tension), a head with a flywheel - on top, and a fan on the side.
And yet - air. the filter there just sucks. Take the time to familiarize yourself with the design 🙂 🙁
I heard - they were putting a "Zaporizhzhya" pan on the side. You can try something simpler, of course (for example, a VAZ “classic” “frying pan” with a dry replaceable filter ring inside), but only there, on the head, the air supply is EXTREMELY inconvenient and is designed for a standard cast (made of alloy) manifold.
Yes, I don’t want to fence in a special garden, I want it to at least somehow work, I’ve studied its design for a long time, as simple as five kopecks, but the idea with a cast sliding bearing from a babit is the dumbest in my mind ..
In my case, this liner is gobbled up, or melted, well, in general, it’s not the point, the point is that apparently you have to change the connecting rod, as well as the inlet valve that is on the side of the cylinder, since the frame holding the petal, apparently due to vibration, has weakened and deviated, in as a result, it was flattened by a piston ..
There is no other head, perhaps the Zilov compressor, but it also needs to be modified to run from the electric motor ..
ZIL-ovsky can be started from a conventional motor (1-phase), and then - buzzing!
In our 3-phase garages, an unprecedented luxury.
Only WHY it is needed - unspecified. CO-7 is a typical "general use" design, it is easy to pump up tires with it. Whether on a motorcycle, even on a jeep. Blowing is also not a problem. Pour Movil (this is already auto). Paint the fence with a HOLIDAY (not to be confused with AUTO) spray gun.
And in the garage, the tasks are different: painting is one thing, sand glass is another. There is also a specific specificity in the form of a pneumatic tool.
And then the costly part for the unit itself is already lost against the background of the connections-transitions-nozzles-spray guns (and mooring to them), oil separators and oil “additives”, manometers-thermometers (viscometers), again, the receiver needs a normal ...
One travel spray gun (without spare parts) costs like a whole compressor.
Plus the noise, dustiness and so on. The discomfort from this monster is an oil painting.
Complete restoration of the co7b compressor, in the first part we disassemble it and make troubleshooting.
Compressor SO-243 aka SO-7B produced by the Vilnius plant SOS 1991. I bought a compressor without checking it.
Compressor SO-7B, connecting rod repair.
replacement of a burst valve.
Compressor head troubleshooting.
The compressor went without a valve plate and. it's easier to say the electric motor and the compressor head.
I decided to assemble the co-7b compressor, I will make the state as close as possible to the factory one, we will see and check.
I bought a SO-7A compressor for spare parts and found it inside in a terrible state.
Repair of the SO-7B compressor. Replacing a burnt out motor.
Modification of the SO-7b compressor Help channel: Visa card Sberbank - 4276 8600 1052 8400 QIWI card QIWI - 4890 4943 8824 7595 Email.
Compressor СО7b, cylinder block wear, oil consumption.
To order a piston compressor repair or buy, go to our website or call +380672929472 +380502227123
Review and troubleshooting of the Soviet compressor SO-7B. 1983 onwards Repair, restoration, revision.
disassembly of the CO7B compressor, review and repair of parts.
VK group Connecting the affiliate program Channel remo.
self-repair of a piston compressor.
Compressor СО-7 is fully remanufactured, rebuilt, renewed, improved. Installed on the compressor.
SO-7A 1975 SO-7B 1982 ((SO-243 1991))
Alteration of the SO-7b compressor for long-term operation. Water cooling and performance check. Resive.
Compressor SO-7B TANDEM Electric motor 7.5 kW 1500 rpm Receiver 450 liters RPM on the compressor 740 rpm.
To order a piston compressor repair or buy, go to our website or call +380672929472 +380502227123
"Sold" many thanks to all.
To order a piston compressor repair or buy, go to our website or call +380672929472 +380502227123
Preparation of the connecting rod for pouring babbitt, and of the process itself.
Homemade compressor based on two SO-7B heads, electric motor power 7.5 kW.
Pins, pistons and rings SO-7B and SO-243
Electrics body 12 * 12 * 14 STL:
Garage 56: Casing for the SO-7B compressor.
Asynchronous motor 7.5 kW 1500 rpm Receiver air tank volume 450 liters Soviet compressor SO-7B manuf.
The SO 7B compressor for the workshop. Video review A short video review of the SO-7B compressor. Characteristics: Proizvo.
To order a piston compressor repair or buy, go to our website or call +380672929472 +380502227123
How I put the automation and the check valve (compressor valve)
8.4. Brief repair instructions
Repair of compressor installations is subdivided into: current (T) - carried out every 1500 hours; capital (K) - carried out after 7500 hours. During routine repairs, the compressor is partially disassembled, malfunctions in units and parts that arise during operation are eliminated, and individual parts are replaced with new ones from the set of spare parts. For current repairs, you should:
clean the compressor valves from carbon deposits. To do this, you need to disassemble the valve plate; Carefully clean each valve plate and their seats of carbon deposits and rinse with gasoline, and then dry them thoroughly. Lubricate the plates and sealing surfaces of the valve plate with a thin layer of compressor oil, and then collect it. If the working surface is damaged, replace the valve plates with new ones;
clean the bottom of the pistons, the discharge cavity of the compressor head and the discharge pipe from carbon deposits. Rinse cleaned surfaces with gasoline and dry them thoroughly;
clean the discharge line from carbon deposits. To do this, remove the pipeline, rinse it with 5% caustic soda solution until it is completely softened and remove carbon deposits, rinse with water and dry. Flush the receiver and oil-moisture separator in the same way;
clean and rinse the cooling fins of the cylinder block and head.
During the overhaul, the compressor is completely disassembled, all initial landings and interfaces are restored in accordance with the requirements of the technical specifications for the overhaul of SO-7B UK.
If a malfunction is detected, the compressor must be stopped. The compressor can only be started up after the fault has been eliminated.
Pages: 1 2 3 4 5 6 7 8 9 10 11 12 13 14 15 16 17 18 19 20 21 22 23 24 25 26 27 28 29 30 31
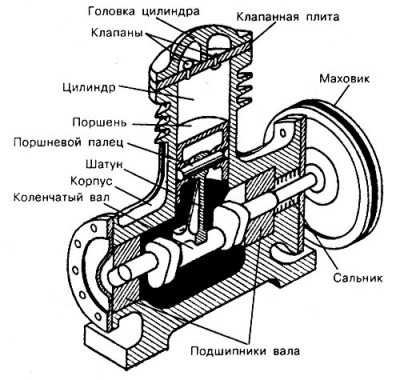
There are situations when the air compressor, peacefully rattling by the engine in the corner of the garage, starts to malfunction, or even turns off altogether. And at this moment, as luck would have it, there is a need for it. Do not be afraid, after studying theoretical information, repairing a compressor with your own hands will not seem like something unattainable.
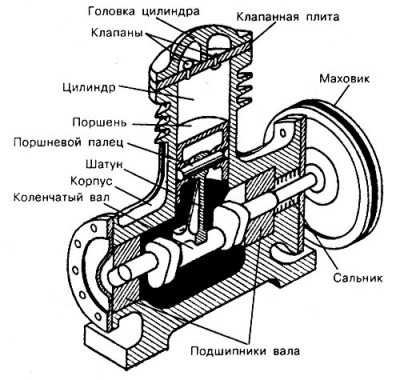
Compressors with a piston system electric motor have found the greatest application in car repair shops. In the supercharger crankcase, the transfer rod moves along the axis back and forth, giving the oscillatory moment to the reciprocating movement of the piston with O-rings. The bypass valve system located in the cylinder head works in such a way that when the piston moves downward, air is taken from the inlet pipe, and upward - it is returned to the outlet pipe.
The gas flow is directed to the receiver, where it is compacted. Due to its design, the blower produces an uneven air stream. Which is not applicable to spray gun use. A kind of condenser (receiver) saves the situation, which smooths out the pressure pulsations, giving out a uniform flow at the outlet.
A more complex design of the compressor unit implies the attachment of additional equipment designed to provide automatic operation, dehumidification and humidification. And if in the case of a simple execution it is easy to localize a malfunction, then the complication of the equipment execution complicates the search. The following are the most common faults and remedies for the most common piston-type compressed gas systems.
To make it easier to find the problem, all defects can be classified by the nature of the malfunction:
- Compressor unit blower does not start
- Compressor motor hums but does not pump air or fills air reservoir too slowly
- At start-up, the thermal protection circuit breaker is triggered or the mains fuse is blown out.
- When the blower is turned off, the pressure in the compressed air tank drops
- Thermal protection circuit breaker periodically trips
- Exhaust air contains a lot of moisture
- Engine vibrates violently
- Compressor runs intermittently
- Air flow is consumed below normal
Let's consider all the causes of the problems and how to fix them.
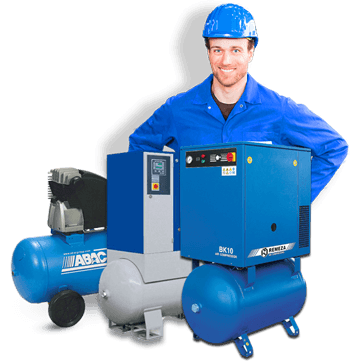
Failed ones are replaced by passive protection devices of the same rating as defective ones. In no case are hot-melt inserts designed for a higher electric current allowed. If the fuse blows again, you should find out the cause of the failure - probably a short circuit at the input of the circuit.
The second reason why the unit does not start is that the pressure control relay in the receiver is faulty or the level settings are out of order. To check, gas is released from the cylinder and the supercharger is tested. If the engine is running, the relay is reset. Otherwise, the defective part is replaced.
Also, the engine will not start when the thermal overload circuit breaker is triggered. This device turns off the power supply circuit of the winding of the electrical device in case of overheating of the piston system, fraught with seizure of the motor. Let the blower cool down for at least 15 minutes. After this time has elapsed, restart it.
With an underestimated mains voltage, the electric motor does not master the scrolling of the axis, while it will hum. With this malfunction, first of all, we check the voltage level in the network using a multimeter (it must be at least 220 V).
If the voltage is normal, then the pressure in the receiver is probably too high, and the piston does not overpower the pushing of air.In this case, manufacturers recommend setting the “AUTO-OFF” automatic switch to the “OFF” position for 15 seconds and then moving it to the “AUTO” position. If this does not help, then the pressure control switch in the receiver is faulty or the bypass (check) valve is clogged.
You can try to eliminate the last drawback by removing the cylinder head and cleaning the channels. Replace the defective relay or send it to a specialized center for repair.
Compressor start-up is accompanied by blown fuse or activation of automatic thermal protection
This malfunction occurs if the installed fuse is below the recommended rated power or the supply network is overloaded. In the first case, we check the compliance of the permissible currents, in the second, we disconnect part of the consumers from the electric main.
A more serious cause of the malfunction is incorrect operation of the voltage relay or breakdown of the bypass valve. We bypass the relay contacts according to the scheme, if the engine is running, then the actuator is faulty. In this case, it is more advisable to contact an official service center for technical support or replace the relay yourself.
A drop in compressed air pressure indicates that there is a leak somewhere in the system. Risk areas are: high pressure air line, piston head check valve or receiver outlet cock. We check the entire pipeline with a soapy solution for air leaks. We wrap the detected defects with sealing tape.
The drain cock may leak if not properly closed or defective. If it is closed all the way, and the soapy solution is bubbling on the spout, then we change this part. When screwing in a new one, do not forget to wind up the fum tape on the thread.
In the case of tightness of the air line and the exhaust valve, we conclude that the compressor control valve is not working correctly. For further work, be sure to bleed all the compressed air from the receiver! Next, we continue to repair the compressor with our own hands, disassembling the cylinder head.
If there is dirt or mechanical damage to the bypass valve, we clean it and try to fix the defects. If the malfunction is not eliminated, then we replace the control valve.
This defect occurs when the power supply voltage is too low, the air flow is poor, or the room temperature is too high. We measure the voltage in the network using a multimeter; it must be at least the lower limit of the range recommended by the manufacturer.
Poor air flow into the discharge system is due to a clogged inlet filter. The filter should be replaced or washed according to the unit's maintenance manual. The piston engine is air-cooled and often overheats when in a poorly ventilated area. The problem is solved by moving the compressor unit to a room with good ventilation.
This situation occurs under the following conditions:
- Large accumulation of moisture in the receiver
- Air intake filter dirty
- The humidity in the room of the compressor unit is increased
Moisture in the output stream of compressed air is fought by the following methods:
- Drain excess fluid from the cylinder regularly
- Clean or replace the filter element
- Move the compressor unit to a room with drier air or install additional filter-moisture separators
In general, piston engines are prone to high vibration. But, if the previously relatively quiet compressor unit begins to rumble, there is a high probability that the engine mounting screws are loosened or the material of the vibration cushions is worn out. This malfunction is eliminated by pulling all fasteners in a circle and replacing the polymer vibration isolators.
Interruptions in the operation of the engine can be caused by incorrect operation of the pressure control switch or too intensive extraction of compressed air.
Excessive gas consumption occurs due to a discrepancy between the compressor capacity and the power consumption. Therefore, before buying a new pneumatic tool, carefully study its characteristics and air consumption per unit of time.
Consumers should not take more than 70% of the compressor capacity. If the power of the blower with a margin overlaps the requests of the pneumatic tools, then the pressure switch is faulty. We either repair it or replace it with a new one.
This malfunction occurs as a result of a gas leak in the high pressure system or a clogged air intake filter. Air leakage can be minimized by pulling all butt joints and wrapping them with sealing tape.
Sometimes it happens that when draining condensate from the receiver, they forget to completely close the drain valve, which also leads to a gas leak. This problem is easy to solve - by tightly closing the valve. If the dust filter is clogged, clean it or, even better, replace it with a new one.
Most of the above malfunctions can be avoided by correctly carrying out the first start-up and running-in of the mechanisms, as well as performing regular routine maintenance.
In order for the device to function properly for a long time, the recommended maintenance should be started at the initial stages of operation. Experts recommend the following actions from the date of purchase:
Timely observance of these simple requirements will keep the mechanism in good condition. Such a time-consuming procedure as repairing a compressor with your own hands will be required extremely rarely. Proper grounding will avoid problems with the electrical part of the device. Regular replacement of oil and cleaning filters will prevent premature wear of rubbing parts.
Start-up of the SO-7b compressor and check the actual performance. Help channel: Visa card Sberbank - 4276 8600.
To order a piston compressor repair or buy, go to our website or call +380672929472.
Repair of the SO-7B compressor. Replacing a burnt out motor.
Alteration of the SO-7b compressor for long-term operation. Water cooling and performance check. Resive.
Compressor head troubleshooting.
Modification of the SO-7b compressor Help channel: Visa card Sberbank - 4276 8600 1052 8400 QIWI card QIWI - 4890 4943.
I apologize in advance for the negligence of this video. Don't get me wrong, I'm not showing off ☺.
Complete restoration of the co7b compressor, in the first part we disassemble it and make troubleshooting.
Review and troubleshooting of the Soviet compressor SO-7B. 1983 onwards Repair, restoration, revision.
Compressor head troubleshooting.
started the Bezhetsk compressor with a st16m starter from a semiautomatic device! but in the near future I will connect to a powerful transformer! and I will blow the starter motor assembly with a small snail! pleasant viewing! pumped up the receiver in 3 minutes to 3 bar! receiver with a volume of 325 liters! if anyone is strong in calculations and can calculate the performance I will be grateful! but the continuation already from 5.5 kV from a single-phase network from capacitors
unloading valve from the converted plumbing valve 12. We disassemble it in hit, move the spring to the opposite side. by rotating the spring along the coils, the closing pressure of the valve can be adjusted.
VISA 4320 3700 2763 3389 valid until 09.21 .. help the channel. ONE OF THE POSSIBLE CAUSES OF A COMPRESSOR BREAKDOWN
Start-up of the SO-7b compressor and check the actual performance. Help channel: Visa card Sberbank - 4276 8600.
To order a piston compressor repair or buy, go to our website or call +380672929472.
Repair of the SO-7B compressor. Replacing a burnt out motor.
Alteration of the SO-7b compressor for long-term operation. Water cooling and performance check. Resive.
Compressor head troubleshooting.
Modification of the SO-7b compressor Help channel: Visa card Sberbank - 4276 8600 1052 8400 QIWI card QIWI - 4890 4943.
I apologize in advance for the negligence of this video. Don't get me wrong, I'm not showing off ☺.
Homemade casing for the SO 7B compressor.
Complete restoration of the co7b compressor, in the first part we disassemble it and make troubleshooting.
Spacer Drawings Before printing, see what the page would be in.
Compressor SO-7B TANDEM Electric motor 7.5 kW 1500 rpm Receiver 450 liters Revolutions on the compressor 740.
replacement of a burst valve.
Compressor SO-243 aka SO-7B produced by the Vilnius plant SOS 1991. I bought a compressor without checking it.
Compressor SO-7B, connecting rod repair.
The compressor went without a valve plate and. it's easier to say the electric motor and the compressor head.
I bought a SO-7A compressor for spare parts and found it inside in a terrible state.
replacement of a burst valve.
The compressor went without a valve plate and. it's easier to say the electric motor and the compressor head.
Compressor SO-7B, connecting rod repair.
Complete restoration of the co7b compressor, in the first part we disassemble it and make troubleshooting.
Compressor SO-243 aka SO-7B produced by the Vilnius plant SOS 1991. I bought a compressor without checking it.
Alteration of the SO-7b compressor for long-term operation. Water cooling and performance check. Resive.
Compressor head troubleshooting.
Drawings of spacers Before printing, see what page would be set in landscape.
Modification of the SO-7b compressor Help channel: Visa card Sberbank - 4276 8600 1052 8400 QIWI card QIWI - 4890 4943 8824 7595 Email.
Repair of the SO-7B compressor. Replacing a burnt out motor.
DIY repair of a compressor from 416 m.
I bought a SO-7A compressor for spare parts and found it inside in a terrible state.
Compressor SO-7B TANDEM Electric motor 7.5 kW 1500 rpm Receiver 450 liters RPM on the compressor 740 rpm.
Start-up of the SO-7b compressor and check the actual performance. Help channel: Visa card Sberbank - 4276 8600.
To order a piston compressor repair or buy, go to our website or call +380672929472.
Repair of the SO-7B compressor. Replacing a burnt out motor.
Alteration of the SO-7b compressor for long-term operation. Water cooling and performance check. Resive.
Compressor head troubleshooting.
Modification of the SO-7b compressor Help channel: Visa card Sberbank - 4276 8600 1052 8400 QIWI card QIWI - 4890 4943.
I apologize in advance for the negligence of this video. Don't get me wrong, I'm not showing off ☺.
Homemade casing for the SO 7B compressor.
Complete restoration of the co7b compressor, in the first part we disassemble it and make troubleshooting.
Spacer Drawings Before printing, see what the page would be in.
I decided to assemble the co-7b compressor, I will make the state as close as possible to the factory one, we will see and check.
Compressor SO-7B TANDEM Electric motor 7.5 kW 1500 rpm Receiver 450 liters Revolutions on the compressor 740.
replacement of a burst valve.
Compressor SO-243 aka SO-7B produced by the Vilnius plant SOS 1991. I bought a compressor without checking it.
Compressor SO-7B, connecting rod repair.
The compressor went without a valve plate and. it's easier to say the electric motor and the compressor head.
I bought a SO-7A compressor for spare parts and found it inside in a terrible state.
The compressor went without a valve plate and. it's easier to say the electric motor and the compressor head.
Compressor SO-243 aka SO-7B produced by the Vilnius plant SOS 1991. I bought a compressor without checking it.
Complete restoration of the co7b compressor, in the first part we disassemble it and make troubleshooting.
replacement of a burst valve.
Compressor head troubleshooting.
Compressor SO-7B, connecting rod repair.
To order a piston compressor repair or buy, go to our website or call +380672929472 +380502227123
Alteration of the SO-7b compressor for long-term operation. Water cooling and performance check. Resive.
Modification of the SO-7b compressor Help channel: Visa card Sberbank - 4276 8600 1052 8400 QIWI card QIWI - 4890 4943 8824 7595 Email.
I bought a SO-7A compressor for spare parts and found it inside in a terrible state.
Repair of the SO-7B compressor. Replacing a burnt out motor.
start-up of the СО-7b compressor and check the actual performance.
Visa card Sberbank - 4276 8600 1052 8400
QIWI card Kiwi - 4890 4943 8824 7595

you need to put your own casing, it will pump air to the head. Should solve the overheating problem. You can also make an intercooler as done in industrial compressors.

Alim Rizaev, excuse the stupid question, what is the yellow boss at the compressor outlet, why and how is it arranged?

yes, they warm up for a long time, put additional blowing on the casing, only the dust blows, just like fans on electric motors, because of the valve, the softness of the compressor is not audible, the duc shakes and will shake, all the weight is on the top, the bed must be good, or it must be done separately from the cylinder , the same thing happened to me, for a long work like sandblasting it is with a large interference, you can burn it, that is, overheat the compressor, look how much its operating temperature I myself do not remember, I have a working temperature of 150g on bv o7-720, when I read it I was a little shocked, but this is a completely different compressor, this is just a note.


Wet rag to help you

He cannot pump 680 l / min, especially if the gaskets are piss


Hello, what kind of check valve to put on this compressor?

Good afternoon, it is possible to clarify one question from you. The SO-7B compressor has a side cover for the dipstick and a breather in it there is a metal plate that protects against oil splashes. The question is how is it correctly positioned with slots up or down?

Alim, register on the website Drive2 dot ru. it is possible without a wheelbarrow. join the “kulibin club” and “do it yourself” groups and place your compressors there. 1000-1500 views will come from there
Restoration and repair of SO-243 (SO-7B) after 5 years of downtime (compressor repair SO 7B)
Compressor SO-7B, connecting rod repair.
Repair and restoration of the SO-7B compressor. Part 2
Compressor Co7b repair, troubleshooting, part 1
Compressor SO 7B valve repair
Compressor SO-7B, revival from the ashes
Compressor SO-7B from Scrap metal
Abrupt revision of SO-7b. Water-cooled for continuous work
Compressor co7b. Overhaul, assembly.
SO-7B compressor after revision, like new with a check valve that works
Repair and restoration of the SO-7B compressor. Part 1
Repair of the SO-7B compressor. Replacing a burnt out motor.
Compressor SO-243 aka SO-7B produced by the Vilnius plant SOS 1991. I bought a compressor without checking, the owner said they had not started it for more than 5 years. I decided to restore and repair what was included to keep the budget as low as possible. ((I wish everyone a pleasant viewing))
Compressor SO-7B, connecting rod repair.
Compressor head troubleshooting.
Complete restoration of the co7b compressor, in the first part we disassemble it and make troubleshooting
replacement of a burst valve.
Modification of the SO-7b compressor Help channel: Visa card Sberbank - 4276 8600 1052 8400 QIWI card QIWI - 4890 4943 8824 7595 Email:
The compressor went without a valve plate and. it's easier to say the electric motor and the compressor head. I will reanimate.
I bought a SO-7A compressor for spare parts and found it inside in a terrible state.
Alteration of the SO-7b compressor for long-term operation. Water cooling and performance check. Receiver total volume 150 liters. Engine 4kv 3000rb, three phases. Productivity up to 6 atmospheres 750 liters per minute, pumping time 72 seconds. Help channel: Visa card Sberbank - 4276 8600 1052 8400 QIWI card QIWI - 4890 4943 8824 7595 Email:
I decided to assemble the co-7b compressor, I will make the condition as close as possible to the factory one, let's see and check what happens.
Compressor СО-7 is fully remanufactured, rebuilt, renewed, improved. The compressor is equipped with a non-return valve, an explosive valve, a quick release for a pneumatic hose (pistol), automation with the ability to regulate the pressure of the lower and upper. ———————————————————————————————————– We sell electric motors, gearboxes, gear motors, pumps (for water , for dirty water, fuels and lubricants, chemistry, oil), hydraulic pushers, various electric drives and much more in the range. For purchase, order, delivery and contact. +38 (096) 5001300 Dmitry
Review and troubleshooting of the Soviet compressor SO-7B. 1983 onwards Repair, restoration, revision.
Repair of the SO-7B compressor. Replacing a burnt out motor.
DIY piston compressor repair
Is a child growing up in your family? Naturally, the kid enjoys decorating the flowers on the wallpaper, tearing them off the wall. You have to periodically wash the wall covering, glue the wallpaper. When the child grows up, you can repair the compressor with 7b with your own hands, which will return the apartment to its original appearance. Modern materials make it possible to bring to life the most interesting solutions, to completely renovate the home.
Life goes by rapidly, one day is similar to another. Do you want variety, a change of scenery? The continuous work schedule provides for constant employment in the service, you have to be at home only in the evenings. An excellent solution would be to repair the shoes of the Kostroma beyond the Volga of the apartment, which allows you to bring a new note of pleasure into your life. You can contact a specialized company that offers a turnkey service.
How to renovate your apartment or house if there is no time at all? At the moment, the opportunity to contact professionals who are ready to completely revitalize your premises is quite popular. Qualified designers develop projects, companies offer the opportunity to carry out turnkey repairs of subaru engines. You do not have to buy materials yourself, hire workers, control the process.
Profile
Group:
Posts:
User no .:
Registration: -
I sell 9900r (cell 89201070964)
Compressors of the SO-7B series are a reliable source of compressed air for repair, painting, construction work in industrial and civil construction, car service enterprises and garages, for working with pneumatic tools: grinding machines, hand wrenches, percussion, reversible, hammers, drilling and threading machines and etc.
In July 1999, the following were introduced into the compressor unit:
1. a new suction filter with a synthetic filter element - this is a more thorough air purification, which means a longer service life of the piston group parts;
2. a balanced crankshaft (due to counterweights), which means that the noise and vibration factor is minimized, less than 85dB;
3. ribbed valve plate with stainless steel plates (Sandvik steel, Sweden) is:
long-term preservation of the mirror in the cylinder block, elimination of the cause of plate breakage;
increased cooling area of the valve plate (due to fins), lowering the temperature of the supplied air, which gives increased performance and reduces oil consumption.
4.Automatic switch to idle with reduced air consumption ensures
energy savings by 10-15%.
They are produced in three modifications: with a receiver volume of 25 liters, 80 liters. and 135 liters.
Unified compressors SO-7B / U - Magnitogorsk development (compressor unit U-43102A). Easy to maintain.
![]() |
Video (click to play). |
This post has been edited Made in USSR – 7.06.2013 – 11:27