In detail: do-it-yourself candy washing machine repair from a real master for the site my.housecope.com.
Breakdowns can range from simple to complex ones that can lead to costly repairs. To determine the reasons for the failure, it is necessary to diagnose, which is quite possible to carry out on your own. Experienced craftsmen put the following faults in the first place:
- Blockage or technical malfunction in the drain system. The machine stops draining water, stops after washing, without going to spin. If the tightness is broken, then a leak may occur during the wringing of things. A signal to a problem that has arisen may be a characteristic noise during the descent of water. It is usually audible if the pump is clogged.
- Wear of the moving parts of the washing machine. Oil seals, engine, shock-absorbing elements, bearings - all this is under constant load. If any of the elements fails, vibration appears in the machine, especially during the spinning process. If you listen, you can distinguish light tapping or grinding in the drum.
- Failure of the water heating element. This problem is typical for older models. The water stops heating up, or the machine doesn't wash at all.
- Problems with electrical and electronics. The wiring and the points of its connection to the sensors cause the washing machine to stop working. In most cases, due to high humidity, oxidation appears on the terminals, but sometimes the wiring "burns". Voltage drops cause the failure of the sensors and the control module. The failure of the pressure switch is accompanied by problems with draining and drawing water, poor spinning indicates that the tachometer has broken.
![]() |
Video (click to play). |
To fix the problem with your own hands, careful preparation is necessary. You will need a spacious workplace, tools and accessories.
- Eliminate blockage and drain problems.
This breakdown can be easily repaired on its own. The problem, as a rule, manifests itself in those situations when the rules for operating the machine and caring for it are violated. Cleaning the drain begins with checking the filter. In Kandy, it is located on the lower left side, hidden by a small door or panel. To clean it, carefully unscrew it counterclockwise, pull it towards you. First, spread a rag on the floor to collect the flowing water. The removed filter is washed with water, cleaned of debris, and installed in place.
To clean the hose, pipe and pump, you will have to raise the washer or lay it on its side. The power supply is disconnected beforehand, the drain hose is disconnected from the sewer system. You will have to get to the pump in cars of this brand through the bottom, which is either not there, or there is a special pallet.
After loosening the clamps, it is necessary to disconnect the hose and branch pipe. The latter is washed with water, wiped dry. The hose is cleaned with a cable with a brush and inspected for damage. After that, the sensors are disconnected from the pump intended for draining the water, the fasteners are unscrewed. Having taken out the pump, it is necessary to check the impeller located under the cover. As a rule, hair, wool, villi are wound around it, so everything will have to be removed. It is recommended to replace the burnt out pump with a new one.
Now all that remains is to assemble the machine and test it in operation.
Such work is considered more serious. The difficulty in replacing bearings is that the sleeve that holds them is thermally pressed in, and the bearings themselves are difficult to remove. For repairs, you will have to disassemble the washer by removing the top cover and back panel. First, remove the detergent tray. Next, the front panel is detached. Now it is the turn of the tank, which is removed carefully so as not to damage the wiring and hoses that were previously disconnected.
The peculiarity is that you cannot cope with such work yourself - you will need an assistant. To remove the bearings, the tank will have to be disassembled, the pulley removed from the shaft, the shaft removed, and the two bearings will have to be removed. For such work, you will need a special removable device, but you can also use a regular hammer. Now it remains to install new bearings and assemble the machine. It will not be superfluous if you pre-lubricate the cleaned seats with grease.
Another problem is shock absorbers wear. Strong vibration during washing or wringing out things will remind you of this. These elements are located under the tank. Remember that shock absorbers are non-separable structures, so they will have to be completely replaced. To do this, first unscrew the lower, and then the upper mounts. Sometimes there are plastic latches that you just need to press down to pull out the locking pin. The removed old shock absorber is replaced with a new one.

- Procedure for replacing the heating element.
Most often, this element fails during prolonged use of the machine. The reason is the hardness of the water, which is deposited on the heating element with a dense bloom. In case of such a failure, a special error code will be displayed on the screen. There is no need to worry here - the work is simple, it is quite possible to do it yourself. It should only be remembered that the heating element is located behind the rear panel, under the tank.
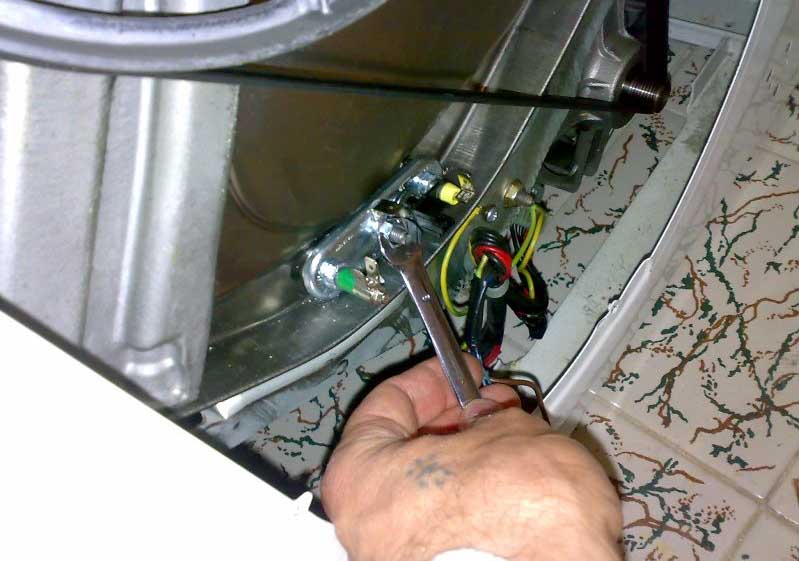
To replace it, it is necessary to carry out a number of operations:
- remove the panel;
- unscrew the bolt securing the failed water heating element;
- disable all sensors, having previously memorized or marked their connection;
- using a flat screwdriver, you can begin to remove the heating element by gently pulling it towards you;
- using a multimeter, it is checked for operability;
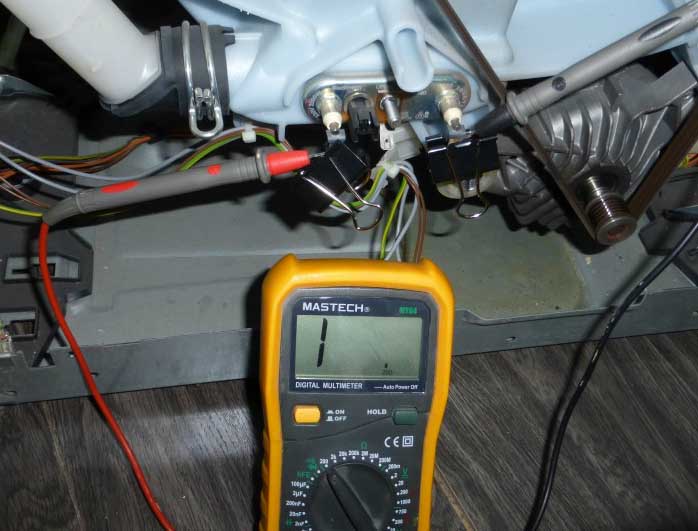
- a serviceable element is simply cleaned of scale, and a new analogue is acquired instead of a burned-out one;
- we carry out the installation, connect the wiring and sensors, screw in the mounting bolt, install the back panel in its place.
- Problems with electrical and electronics.
Electrical failure is another common problem, involving not only electrical wiring, but sensors as well. Most often, the tachometer and the pressure switch, which is responsible for the liquid level, fail. Checking the wiring for operability is a rather complicated process, which implies the presence of a multimeter and the ability to use it. Sometimes a visual inspection is sufficient to identify oxidized wires or terminals.
The water level gauge is easy to change. It is located in the upper corner, under the cover. The wiring leading from the pump and the electrical board is disconnected from it, the tube connecting the device to the tank is disconnected.
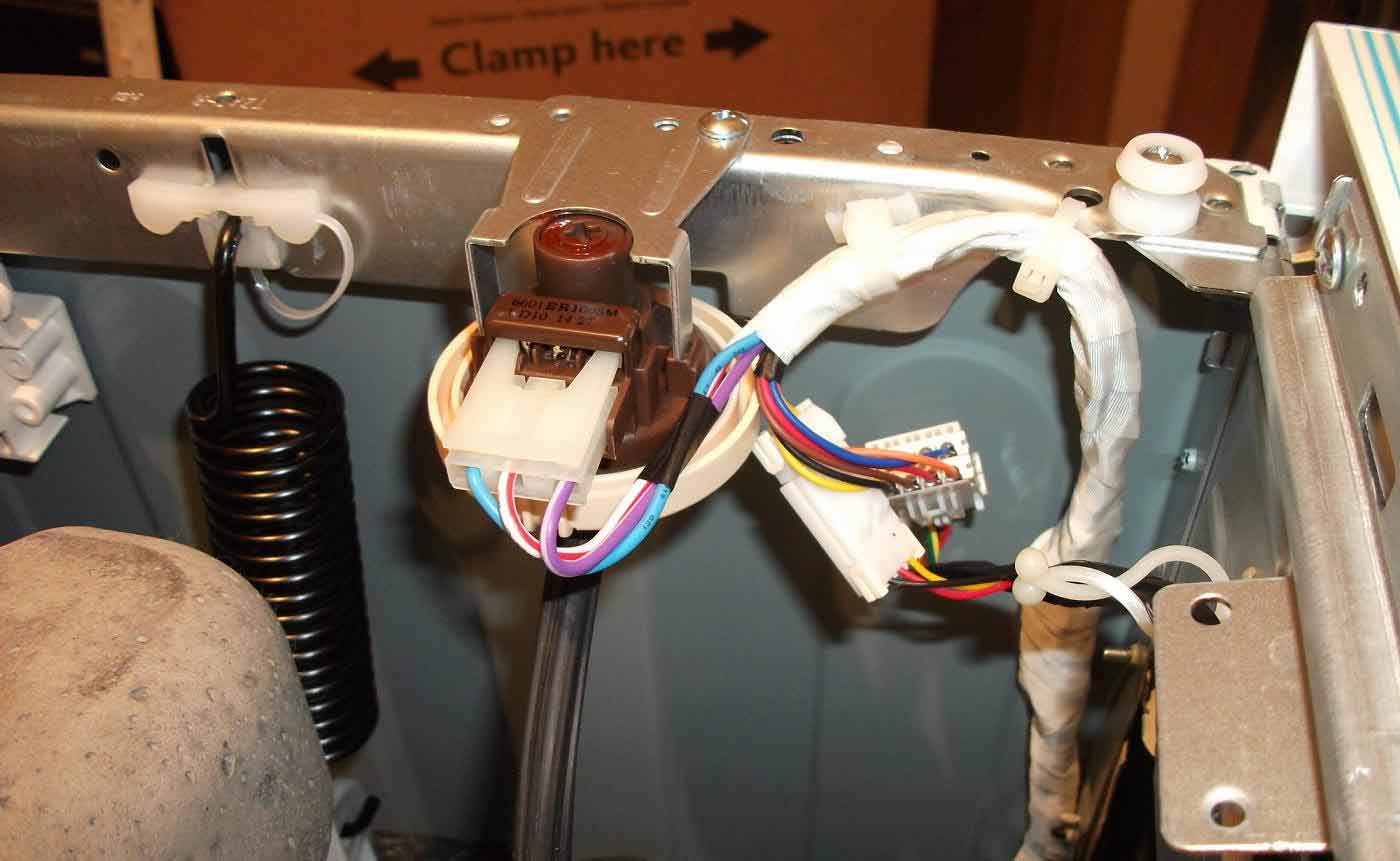
In place of the removed pressure switch, a new one is installed. But the tachometer needs to be changed by an experienced craftsman, because the washing machine will have to be disassembled to get to the electric motor.
If the surge protection is not installed, or there is no ground, the control module may fail. The machine will stop turning on, programming will fail, the washing machine will freeze. The control board is quite expensive, so it is recommended to have it checked and repaired by an experienced technician. Most often, all work ends with its complete replacement.
It happens that the machine does not turn on during startup.There may be several reasons for this:
- burned out or kinked network cable. It must be checked and, if necessary, replaced. It happens that the problem is hidden in the extension cord used, so it is recommended to start checking with it;
- there is no voltage in the network. Also, it may simply not be enough to start the washing machine. To check, you will have to use any electrical device. If the "diagnosis" is confirmed, invite an electrician;
- contacts on the start button have oxidized. Remove the top cover, remove the powder container, remove the panel, disconnect the wiring to the control module, inspect the contacts. They will either have to be protected or changed;
- the management module has failed.
Noticing a puddle on the floor, it is recommended to urgently look for a leak. But before starting all the actions, the machine must be de-energized so as not to get an electric shock.
There may be several reasons for the leak:
- the dispensing tray is clogged with detergents, clogging the branch pipe;
- the water drain pipe is damaged;
- from prolonged use, the cuff is worn out or damaged by small objects, having lost its tightness.
It is recommended to regularly clean the outside of the SMA Candy, without using products containing solvents, alcohols or abrasives. It is enough to use a damp cloth for such work.
Check the detergent drawer regularly to remove any powder residues. If necessary, remove the container and rinse it thoroughly with water.
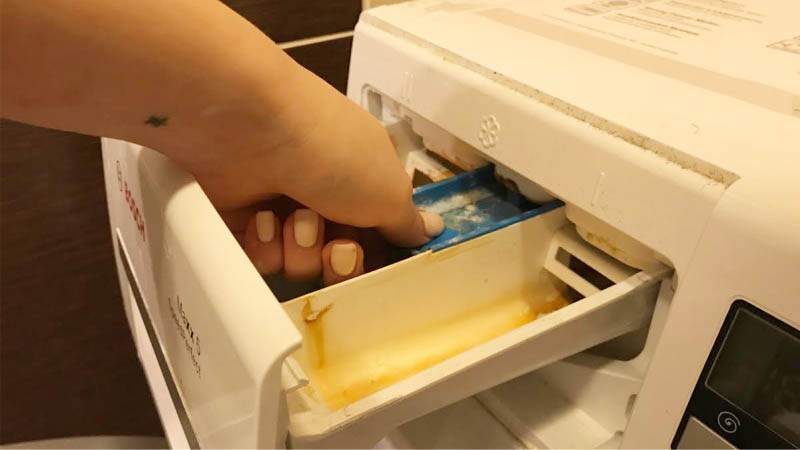
The drainage system should be checked and cleaned twice a year.
If the device is moved to another place and it has not been used for a long time, all water must be drained from the system.
Remember that all repair work must begin with the diagnosis of the washing machine in order to identify the malfunction as accurately as possible. Having estimated the complexity of the failure and your own strength, you can decide on an independent repair or call an experienced specialist. Working on your own without the necessary skills can lead to more costly repairs. But if you act on your own, then change the failed elements with their exact counterparts.
It is not so difficult to repair a Kandy washing machine with your own hands. To do this, you need to know its common malfunctions and have some knowledge of electrical engineering. It is enough to watch the video on this topic (presented below) and a lot will become simple and clear.
In order to independently repair the washing machine, you need to carefully prepare for the repair. The tool, accessories and the workplace are prepared first. For disassembly you will need:
- Screwdriver Set;
- wrenches for 8, 10, 17 and 19;
- pliers and side cutters;
- pliers for self-clamping clamps;
- awl and small hammer.
The best place to disassemble is the garage. The main thing is to have space and good lighting. At the workplace, you need to carefully lay out the tool, clean rags, sealant, WD-40 liquid, and a brush. It remains to prepare a soldering iron and an electrical measuring device, for example, a tester.
For those who will be doing repairs for the first time, it is advisable to have a camera for photographing the disassembly sequence. Pictures will be of great help when assembling the machine.
Before you start repairing the washing machine, you need to find the malfunction due to which the appliance does not work. There are not many of them. The most time consuming of these is bearing replacement... It is immediately necessary to determine which tank is installed in the machine. If it is non-separable, it is better to postpone self-repair. Of course, you can rely on your experience, but it is better to entrust this work to specialists from the service. You will have to saw the tank to get to the bearings, and then you will need to glue it back together. It is much easier to carry out repairs on a typewriter with a collapsible tank.
To replace the bearing, the machine must be disassembled. For this purpose, the top and rear panels are removed first.The detergent dispenser is immediately removed along with the tray holder. Now nothing prevents the detachment of the front decorative panel. It remains to carefully pull out the tank. You need to be extremely careful here. The fact is that a mass of hoses, wires and other parts are attached to the tank. All of them must be carefully disconnected, secured, the loading hatch removed, and only then the tank must be removed. Moreover, it is almost impossible to perform this operation alone, you will need a second pair of hands.
To remove the bearings, we disassemble the tank, remove the pulley from the shaft, take out the shaft and carefully begin to remove the bearings (there are two of them in the car). The best thing to do is special puller... As a last resort, you can knock out with a hammer.
The next step is to install new bearings. As a rule, there are no difficulties here. We assemble the car in reverse order using photographs.
Important. Before installing new bearings, their seats must be well cleaned and lubricated with grease, for example, "Litol-24".
The next common problem is shock absorbers wear... This is a fairly simple operation. If the machine vibrates very strongly during washing or spinning, then it's time to replace the shock absorbers. They are located at the bottom of the tank. Considering their design feature - non-separability, it must be remembered that shock absorbers are not repaired, but replaced.
To remove them, you must first unscrew the lower mounting bolt (in the place where the shock absorber is attached to the machine body), and then the upper one. Instead of bolts, depending on the model, there may be plastic pins with latches. In this case, you must press the latch and push the pin out of its seat. For example, a screwdriver. After disconnecting the mountings, the shock absorber is removed and replaced with a new one.
Advice. When buying new shock absorbers, the seller must be sure to show a sample of the old one.
Sometimes, in order to fix Kandy's car, it is enough replace the heating element in it (heating element). It can be accessed with the rear cover of the machine removed. The removal process itself is not difficult. First of all, all wires are disconnected from the heating element. Then the fastening nut is loosened and the screw is pressed inward. After these operations, the heating element is carefully removed from its seat with a slotted screwdriver. When installing a new heating element, it is very important to avoid distortions and not to use brute force. Immediately after installation, without assembling the machine completely, it is necessary to check its operation by heating water to 60ᵒ. If this wash takes place without water leaking, you can assemble the machine to the end and put it in its place.
Important. When disassembling, try to remember the places of connection of the wires so that during assembly do not confuse them.
Complete disassembly of the Candy washing machine will be needed in case replacement of electric motor brushes... Repair in itself is not difficult, but without its implementation, the device will not work. The brush assembly of the electric motor is quite stable in operation. Without replacing it, the machine usually works for 5 years. There were cases when this period was more than doubled. It all depends on the intensity of the load on the machine. Replacing the brush assembly is very easy. The only problem is getting to the electric motor. When this is done, there will be no barriers to repair.
Repair of all washing machines, including Kandy, is not very difficult. Especially when you have knowledge in electrical engineering and plumbing. And, of course, the experience in repair work.
Due to the adequate ratio of quality and cost, Candy brand washing machines have found many fans among our consumers.
But, as you know, there is no perfection in the world: wonderful Italian devices sometimes break down.
Fortunately, most of the faults are repairable and it is quite possible that you yourself will cope with the problem after reading this article. So, Kandy is a washing machine: DIY repair.
If the Kandy washing machine has a malfunction, you can try to do it yourself. Of all the many elements that make up the washing machine, probably only the frame and decorative trim cannot break. All others, with varying probability, may fail.
The most common problems you have to solve are:
- The machine cannot be turned on.
- The water in the tank remains cold.
- The hatch does not want to open.
- Water is not collected well or is not drained.
- There is increased vibration and unusual noise during machine operation.
The self-diagnosis function is of great help to the repairman.
If something goes wrong, the built-in controller detects the fault itself and reports it in some way. If there is a display, such as in the ActivaSmart model, an alphanumeric code is displayed on it. Owners of machines without a display (Aquamatic model) can guess the nature of the malfunction by the number of flashes of the LED on the control panel.
For repairs at an amateur level, you will need the simplest tools - keys, screwdrivers, pliers, etc.
You can find out the condition of the electrical part using a multimeter and a phase indicator screwdriver.
A special tool has to be used only when replacing bearings - they are pressed with an interference fit, so a puller will be needed.
We strongly recommend that you take a photo of the wires connected to it before dismantling a unit, so that there are no connection problems during assembly.
Well, now let's see how you can return this most useful device to working condition.
In this regard, the repair manual contains the following recommendations:
- Unplug the power cord from the socket, plug it in again and try to start the device again.
- If the machine does not turn on again, check that the outlet is working with some other known working electrical appliance.
- The most common reason for this failure is oxidation or burnout of the contacts on the power button. This element is checked using a special tester and, if necessary, replaced with a new one.
The reason for the "strike" may be a faulty control module (the indicator blinks 14, 15 or 18 times in a row). To repair or replace it, you need to contact a workshop.
The reason that the washing machine began to treat its duties "with coolness", in most cases, is the breakdown of the heating element (error code "E05" or the indicator flashes 16 times every 5 seconds).
It can simply burn out from the development of a resource, like a light bulb, or it can "order a long life" prematurely - because of a thick layer of scale.
The heater is manipulated in the following order:
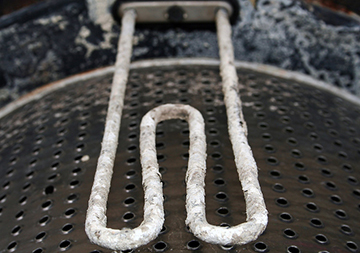
- Remove the back panel by unscrewing the corresponding screws.
- Locate the heater shank protruding from the bottom of the tank (two wires are connected to it).
- Determine the resistance of the heating element with a multimeter. If it is suitable, the device will show 20 - 30 Ohm, if it is burnt out - "infinity".
- If the heating element is faulty, unscrew the nut holding it (between the contacts) and carefully remove it from the tank. If you get stuck, hit it gently a couple of times with a rubberized hammer (or with a regular one - on the attached wooden block).
- Before installing a new heating element, the inner surface of the tank around the hole must be descaled.
To make sure that the heating element is working, it is enough to turn on the machine for heating and look at the electric meter - the rotation speed of the disk or the blinking frequency of the indicator should increase sharply.
A less common reason is the failure of the temperature sensor (E05 or 5 flashes). To check, first measure its resistance at room temperature, then after heating with hot water. In a non-working element, the resistance will remain constant.
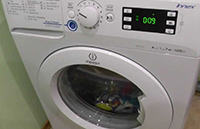
We will consider the main problems associated with connecting a washing machine here.
If there is not enough space in the bathroom, then the washing machine has to be installed in the kitchen. In this thread https://my.housecope.com/wp-content/uploads/ext/740/cancliz/mnogokvartirnyie-doma/santehnika/kak-podklyuchit-stiralnuyu-mashinku-na-kuhne.html you will find tips for connecting the device for beginners and experienced.
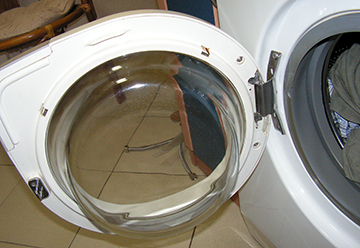
If its appearance is not expected in the near future, the lock can be opened by yourself. This will be possible if the front cover is removed from the de-energized machine and slightly tilted back.
It happens that the lock itself requires replacement. To dismantle it, you first need to carefully remove the hatch seal by prying the clamp holding it with a screwdriver. After that, two screws that secure the lock will become available.
If the machine cannot get rid of the waste water (error "E03" or 3 blinks), it is most likely a clogged filter. A pump breakdown could also have occurred. Do the following:
- After removing the front lower panel, locate the drain filter on the left side of the machine.
- Place a container under the machine, unscrew the filter and free it from accumulated dirt.
- Also inspect the tank connection to which the filter is attached. It is often clogged with muddy deposits, which must be carefully removed with a screwdriver.
- After plugging in the machine, start it in drain mode and look at the pump impeller (you can see it through the hole in the filter plug). If the pump is working properly, it will rotate. It happens that the impeller rotates, but the operation of the pump is accompanied by a strong hum, and when the impeller is swinging from side to side in the direction perpendicular to the axis (the machine, of course, must be turned off), you can feel that it is very loose. In this case, the impeller can jam from time to time, which is the cause of the problems with the drain. Such a pump must be replaced, for which the rear wall will have to be removed.
It will also be helpful to clean the inlet filter, for which you need to disconnect the inlet hose. It is also often clogged with sand and rust, as a result of which water begins to flow into the machine very slowly (error "E02" or 2 blinks).
The reason for the lack of a normal drain can also be a malfunction of the level sensor, also called a pressure switch (located under the top cover). If the tube attached to it becomes clogged with dirt, the sensor will not function. After removing the dirt, you can check the performance of the pressure switch by blowing into the tube. A working device should respond with a click.
If the machine starts to work with a loud hum, it is most likely that one of the bearings needs to be replaced. To do this, you need to remove the tank, which is done through the top in Candy machines. In some models, the tank is one-piece and needs to be cut and welded to replace the bearings. This can only be done correctly in the workshop. At home, replacement of bearings is possible only for machines with a collecting tank. To get to it, you need to remove the panels - top and back.
It is also better to dismantle the front panel so as not to accidentally scratch it when removing the tank.
Before you get the tank, you need to do the following:
- disconnect all the hoses connected to it (the clamps are unclenched with pliers);
- remove the powder distribution hopper;
- unscrew the counterweight;
- remove the belt from the drum pulley;
- disconnect the wires from the heating element;
- unscrewing the bolts and disconnecting the wires, remove the engine (extends along the guides);
- remove the hatch by unscrewing the screws under the sealing collar (the clamp fixing the collar is pushed off with a screwdriver).
Having disassembled the tank into two parts, the pulley is removed from the drum shaft, and then by careful knocking the shaft is knocked out of the bearing.You cannot hit directly on the shaft - you need to put a wooden block. Next, you need to knock the bearing out of the tank with careful uniform blows around the perimeter.
The new bearing is installed in place using a simple device consisting of a pressure washer, a threaded rod and a pair of nuts. One nut is screwed onto the rod from one side - it will press on the pressure washer pressing the bearing. The second nut is screwed onto the rod from the other side (abuts against the tank) - it must be rotated slowly.
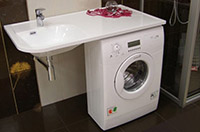
This information will help you decide on the choice of a kitchen faucet. Characteristics of devices by manufacturer, material and mechanics.
Any washing machine can break down. The reasons may be different, banal or, on the contrary, too serious, which will lead to expensive equipment repairs. Professional diagnostics will help to determine exactly what is broken. But in most cases, such diagnostics can be carried out independently, the main thing is to listen well, take a closer look, and have tools at hand.
What goes wrong in Kandy typewriters most often? The wizards note the following malfunctions:
- blockage of the drain system or its malfunction. If a blockage occurs, the machine does not drain the water and stops after the wash cycle, the laundry is not wrung out. If the tightness of the connection of the nozzles, hose or drain pump is broken, then water may leak during spinning. In addition, a characteristic hum during draining of water indicates a malfunction of the drain system, most often this is due to a blockage in the pump.
- wear of the moving parts of the washing machine. Parts that are subjected to more stress during washing are subject to faster wear than those that do not. These elements include oil seals, bearings, shock absorbers, engine.
The average service life of bearings is about 7 years; they are replaced together with the replacement of the oil seals.
The malfunction of these parts manifests itself as follows: strong vibration of the machine during spinning, knocking or rattling of the drum even when the machine is not working, the drum stops, the machine does not start for washing after filling with water.
A blockage in the drain system is a malfunction that can be easily eliminated by hand. In service centers, it belongs to the first category of complexity. A similar problem usually arises in cases where the rules for the operation and maintenance of the washing machine are not followed. Cleaning the drain system begins with cleaning the drain filter.
In Kandy machines, the drain filter is located at the bottom, on the left behind a small door or behind the bottom panel.To clean it, you need to carefully unscrew it counterclockwise and pull it towards you. Be sure to use a large cloth to prevent any remaining water in the tank from spilling out onto the floor. After removing the filter, rinse it in water and remove lint and other dirt, then slide it back into place.
To clean the hose, drain and pump, you need to lift the machine or lay it on its side. Before doing this, be sure to turn off the power supply, as well as the drain hose from the sewer. You can get to the pump in the Kandy machine through the bottom, which is either missing or there is a pallet. It can be easily unscrewed.
So, we loosen the clamps and disconnect the pipe and hose. We rinse the branch pipe in water and wipe it with a dry cloth. We clean the hose with a cable with a brush and inspect for damage. Next, we disconnect the sensors from the drain pump, unscrew the self-tapping screws holding the pump, and take it out. In the pump, you need to inspect the impeller, which is located under the cover.
Pile, hair, wool can be wound on it, so we clean everything carefully. Using a multimeter, we check its performance. If the pump burns out, then in this case it is better to replace it with a new one; repair in this case is not advisable.
After cleaning, we assemble the machine and run the wash in idle mode.
The silent operation of the washing machine is ensured by shock absorbers. And if one day you hear a roar, then, most likely, the problem is precisely in the shock absorbers, in rare cases in loose counterweights. It is not worth operating a machine with faulty shock absorbers, because this can lead to even more complex breakdowns. It is best to delegate their replacement to the master, but if you wish, if you have time and space to disassemble the machine, you can do this work yourself, step-by-step instructions that will allow you to do the work are in the article on replacing shock absorbers and dampers.
- unscrew the back wall;
- we unscrew the bolt holding the heating element;
- we disconnect the sensors from the heating element, after taking a photo of their correct connection;
- using a flat screwdriver, carefully pull out the heating element towards us;
- we inspect it, if outwardly it is not possible to determine the serviceability, we take a multimeter and check its performance;
- if the heating element is serviceable, then we clean it from scale, if not, we buy a new one;
- insert the heating element into place;
- we connect wires and sensors;
- we fix the heating element with a bolt;
- we put the back cover of the machine body.
Another of the typical breakdowns of a washing machine is an electrician, by which in this case we mean not only electrical wiring, but also sensors. The tachometer and pressure switch (water level sensor) fail more often. Checking that the wiring is working is a process that requires patience and skill in using a multimeter. In some cases, a visual inspection of the wires and terminals is enough to understand that they need to be stripped or replaced.
You can easily replace the water level sensor with your own hands. It is located under the top cover in the corner. It is necessary to disconnect the chips with the wires coming from the electronic board and the pump, and also disconnect the pipe coming from the tank. And in place of the faulty one, a new pressure switch is connected. It is better to entrust the replacement of the tachometer to a specialist, because you will have to disassemble the washing machine and get to the electric motor.
With poor protection against power surges and lack of grounding in the electrical network, the control module of the washing machine may fail. This can lead to the fact that the machine does not turn on, wash programs get lost, the machine "freezes". The control board is quite expensive, so it is best to entrust diagnostics and repairs to a master. In some cases, repair is actually possible, not replacement.
There are amateurs who are easily versed in electronics, if you consider yourself one of those, then go for it. But remember, mistakes can be costly.
So, the repair of Candy washing machines should begin with a high-quality diagnosis, determination of the malfunction. Only after assessing the complexity of the work ahead and your capabilities, make a decision whether to do the repair yourself or it is better to entrust everything to the master. And there is nothing wrong with everyone doing their own thing.
Automatic washing machines Kandy are affordable and compact. Convenient control system and a wide range of programs have made the technique popular among users.
However, over time, even reliable equipment can fail. Is it possible to repair the Kandy washing machine with your own hands? Quite!
You just need to find out what the error codes on the control panel mean, and then find and fix the malfunction.
Let's analyze the main problems that are typical for machines of this brand. We will also find out how you can repair Candy washing machines with your own hands.
Have you noticed that the Kandy washing machine does not drain water. The program can stop right in the middle of a wash. Due to the fact that the water does not leave completely, you take out wet things after spinning.
What are the reasons for such a breakdown:
- The drain system is clogged. If debris gets into the drain filter or hose, it will block. It is necessary to check the pump and the branch pipe from the tank to the pump.
- Breakdown of the drain pump (pump). Often, small objects entering the pump cause damage to the pump.
Why isn't the Candy washing machine working? You start the washing machine as usual, but it does not respond to your actions. Let's figure out the reasons for this problem:
- Defective mains cable or extension cord. He could burn out, twist.
- Lack of voltage in the network, or it is not enough to start SM Kandy. This can happen if repair work is being carried out on your site, a powerful tool is involved, and so on.
- The contacts on the start button are oxidized, so the machine does not respond to switching on.
- Malfunction of the control module of the Kandy washing machine. The module is responsible for all programs in the CMA, therefore, if it breaks down, the technician refuses to work.
If you notice a puddle of water under the washing machine, you need to urgently look for a leak.
Attention! Do not step into the water, you may be electrocuted. If possible, disconnect the CM from the network or turn off the electricity supply on the switchboard.
- Dispensing tray. If the tray is not periodically cleaned, powder accumulates in it, which clogs the pipe. As a result, leakage comes out of the tray.
- Drain connection of the Candy washing machine. If it is damaged, water flows out through the bottom of the CM.
- Rubber cuff of the hatch. With prolonged use, the cuff could leak and lose its tightness. Or it is damaged by small items during washing.
The washer does not start the washing process or washes things in cold water. The reason for this is a malfunction of the heating element (heating element). Basically, the element fails due to scale or damaged contacts.
Wear of bearings, oil seals, motor electric brushes leads to various malfunctions in the Kandy washing machine. For example, you may notice knocking and rumbling when the washer is running, or the drum stops rotating.
These include problems with closing the sunroof door, faulty wiring between parts and the control module, and a faulty Candy washing machine control board.
How to figure out what kind of breakdown happened in your car? The error codes will help you.
Thanks to the self-diagnosis system, a malfunction code is displayed on the Kandy washing machine display. After decrypting it, the user understands which detail needs to be checked. This makes it possible to independently repair Candy washing machines.
Depending on the type of model, CM can show an error in different ways:
- Electronically controlled Activa models show an error on the display.
- Models Candy Aquamatic (Kandy Akvamatik), signal about a malfunction by blinking the bottom light on the left. The number of flashes after a pause means the error code.
![]() |
Video (click to play). |
For washing machines Candy Holiday, Aquamatic, Activa and other models, the following error codes are characteristic: E01, E02, E03, E04, E05, E09.