In detail: do-it-yourself gugma161 welding repair from a real master for the site my.housecope.com.
The weakest element of welding transformers is the terminal block to which the welding cables are connected. Poor contact together with a high welding current leads to strong heating of the connection and the wires connected to it. As a result, the connection itself is destroyed, the insulation at the ends of the windings burns out, as a result of which a short circuit occurs.
Repair of a welding transformer in this case is reduced to sorting out the heating joint, cleaning the contact surfaces and clamping them, ensuring tight contact of all elements.
Among others, the following malfunctions occur.
Spontaneous shutdown of the welding machine... When the transformer is connected to the network, its protection is triggered, as a result of which the device is turned off. This can occur due to short circuits in the high voltage circuit - between the wires and the case, or wires between themselves. A short circuit between the turns of the coils or sheets of the magnetic circuit, as well as the breakdown of capacitors, can also trigger the protection. When repairing, it is necessary to disconnect the transformer from the network, find the defective place and eliminate the malfunction - restore the insulation, replace the capacitor, etc.
Strong hum of the transformer, often accompanied by overheating. The reason may be loosening of the bolts tightening the sheet elements of the magnetic circuit, malfunctions in the fastening of the core or the mechanism for moving the coils, overloading of the transformer (excessively long operation, high value of the welding current, large diameter of the electrode). A short circuit between welding cables or sheets of a magnetic circuit also leads to a strong hum. It is necessary to check and tighten all screws and bolts, eliminate irregularities in the mechanisms for fixing the core and moving the coils, check and restore the insulation in the welding cables.
![]() |
Video (click to play). |
Excessive heating of the welding machine... The most common reasons for this include a violation of the operating rules in the form of setting the welding current above the permissible value, using a large diameter electrode or too long work without interruption. It is necessary to observe the standard operating mode - set moderate current values, use electrodes of small diameters, take breaks in work to cool the device.
Strong heating can lead to a short circuit between the turns of the coil winding due to combustion of the insulation, usually accompanied by smoke. This is the most serious case, about which they say that the apparatus "burned out". If this happened, then the repair of the welding machine will require, at best, a local restoration of the coil wire insulation, at worst - its complete rewinding. In the latter version, in order to preserve the characteristics of the apparatus, it is necessary to rewind with a wire of the original section - with the same number of turns as it was.
Low welding current... The phenomenon can be observed with undervoltage in the supply network or a malfunction of the welding current regulator.
Poor welding current adjustment... This can be caused by various faults in the current control mechanisms, which differ in different designs of welding transformers. Namely, malfunctions in the screw of the current regulator, a short circuit between the terminals of the regulator, a violation of the mobility of the secondary coils due to the ingress of foreign objects or other reasons, a short circuit in the choke coil, etc. It is necessary to remove the casing from the apparatus and investigate the specific current control mechanism in order to detect a malfunction.The simplicity of the device of the welding machine and the accessibility of all its components for inspection make it easier to troubleshoot.
Sudden interruption of the welding arc and inability to ignite it again... Instead of an arc, only small sparks are observed. This can be caused by a breakdown of the high voltage winding to the welding circuit, a short circuit between the welding wires or a disruption in their connection to the terminals of the machine.
Consumption of large current from the network at no load... This can be caused by a short circuit of the winding turns, which is eliminated by a local restoration of insulation or a complete rewinding of the coil.
The available electronic part - a diode rectifier and a control module - makes the welding rectifier akin to an inverter. Therefore, troubleshooting involves checking the diode bridge and elements of the control board. A diode bridge is a reliable component in electronic circuits, but sometimes it fails. In general, the causes of the malfunction can be very different: the tracks on the boards burn out, the control circuit transformers fail. The photo below shows a case when repairing a welding machine with your own hands, which consisted of replacing a non-working part of a control board with a Russian analogue, allowed the user to save a considerable amount on repairs (70% of the cost of the welding machine).
Unlike a welding transformer, which is more of an electrical product, a welding inverter is an electronic device. This means that diagnostics and repair of welding inverters involves checking the performance of transistors, diodes, resistors, zener diodes and other elements that make up electronic circuits. You need to be able to work with an oscilloscope, not to mention multimeters, voltmeters and other ordinary measuring equipment.
A feature of inverter repair is the fact that in many cases it is difficult or even impossible to determine by the nature of the malfunction a failed component, you have to check all the elements of the circuit sequentially.
From the foregoing, it follows that the successful repair of a welding inverter with your own hands is possible only if you have at least basic knowledge of electronics and little experience with electrical circuits. Otherwise, self-repair can only result in a waste of time and effort.
As you know, the principle of operation of a welding inverter is a step-by-step conversion of an electrical signal:
- Rectifying the mains current - using an input rectifier.
- Converting the rectified current into high-frequency alternating current - in the inverter module.
- Lowering the high-frequency voltage to the welding voltage - with a power transformer (very small in size due to the high frequency of the voltage).
- Rectification of alternating high-frequency current into constant welding - by an output rectifier.
In accordance with the operations performed, the inverter structurally consists of several electronic modules, the main ones of which are the input rectifier module, the output rectifier module and the control board with keys (transistors).
While the main components in inverters of different designs remain unchanged, their layout in devices from different manufacturers can vary greatly.
Checking transistors... The weakest point of inverters is the transistors, so the repair of inverter welding machines usually begins with their inspection. A faulty transistor is usually visible immediately - a cracked or cracked case, burned-out leads. If such is found, you can start repairing the inverter by replacing it. This is what a burnt key looks like.
And this is how it was installed instead of the burnt one. The transistor is installed on thermal paste (KPT-8), which provides good heat dissipation to the aluminum radiator.
Sometimes there are no external signs of malfunction, all keys appear to be intact.Then, to determine the faulty transistor, a multimeter is used to dial them.
It is very good to identify faulty items, but not all. Repair of inverter welding machines also involves the search, instead of burnt out elements, suitable analogues. For this, the characteristic of the failed elements is determined (according to the datasheet) and, based on it, analogues are selected for replacement.
Checking Driver Items... Power transistors usually do not fail by themselves, most often this is preceded by the failure of the elements of the "swinging" their driver. Below is a photo of the board with the elements of the Telwin Tecnica 164 inverter driver. The check is carried out using an ohmmeter. All defective parts are soldered out and replaced with suitable analogs.
Rectifier test... Input and output rectifiers, which are diode bridges mounted on a radiator, are considered reliable elements of inverters. However, sometimes they also fail. This does not apply to those shown in the photo below, they are serviceable.
The diode bridge is most conveniently checked by unsoldering the wires from it and removing it from the board. This makes work easier and does not deceive when there is a short circuit in the circuit. The verification algorithm is simple, if the entire group is short-circuited, you need to look for a faulty (punctured) diode.
It is convenient to use a soldering iron with a suction for desoldering parts.
Control board monitoring... The key control board is the most complex module of the welding inverter; the reliability of the functioning of all components of the device depends on its operation. A qualified repair of welding inverters should end with a check for the presence of control signals coming to the busbars of the gates of the key module. This check is carried out using an oscilloscope.
Inverter welding machines are gaining more and more popularity among master welders due to their compact size, low weight and reasonable prices. Like any other equipment, these devices can fail due to improper operation or due to design flaws. In some cases, the repair of inverter welding machines can be carried out independently by examining the inverter device, but there are breakdowns that are eliminated only at the service center.
Welding inverters, depending on the models, operate both from a household electrical network (220 V) and from a three-phase (380 V). The only thing to consider when connecting the device to a household network is its power consumption. If it exceeds the capabilities of the wiring, then the unit will not work with a sagging network.
So, the following main modules are included in the device of an inverter welding machine.
Just like diodes, transistors are installed on radiators for better heat dissipation from them. To protect the transistor unit from voltage surges, an RC filter is installed in front of it.
Below is a diagram that clearly shows the principle of operation of the welding inverter.
So, the principle of operation of this module of the welding machine is as follows. The primary rectifier of the inverter is supplied with voltage from the household electrical network or from generators, gasoline or diesel. The incoming current is alternating, but passing through the diode block, becomes permanent... The rectified current is fed to the inverter, where it is converted back to alternating current, but with changed frequency characteristics, that is, it becomes high-frequency. Further, the high-frequency voltage is reduced by a transformer to 60-70 V with a simultaneous increase in the current strength. At the next stage, the current again enters the rectifier, where it is converted to DC, after which it is supplied to the output terminals of the unit. All current conversions controlled by a microprocessor control unit.
Modern inverters, especially those based on the IGBT module, are quite demanding on the rules of operation. This is explained by the fact that when the unit is operating, its internal modules give off a lot of heat... Although both radiators and a fan are used to remove heat from power units and electronic boards, these measures are sometimes not enough, especially in inexpensive units. Therefore, you need to strictly follow the rules that are indicated in the instructions for the device, implying periodic shutdown of the installation for cooling.
This rule is usually referred to as the “Duty Cycle” (Duty Cycle), which is measured as a percentage. Not observing the PV, overheating of the main units of the apparatus occurs and their failure occurs. If this happens with a new unit, then this breakdown is not subject to warranty repair.
Also, if the inverter welding machine is working in dusty rooms, dust settles on its radiators and interferes with normal heat transfer, which inevitably leads to overheating and breakdown of electrical components. If it is impossible to get rid of the presence of dust in the air, it is necessary to open the inverter case more often and clean all the components of the device from accumulated dirt.
But most often inverters fail when they work at low temperatures. Breakdowns occur due to the appearance of condensation on the heated control board, as a result of which a short circuit occurs between the parts of this electronic module.
A distinctive feature of inverters is the presence of an electronic control board, therefore, only a qualified specialist can diagnose and eliminate a malfunction in this unit.... In addition, diode bridges, transistor blocks, transformers and other parts of the electrical circuit of the apparatus can fail. To carry out diagnostics with your own hands, you need to have certain knowledge and skills in working with measuring instruments such as an oscilloscope and a multimeter.
From the above, it becomes clear that, without the necessary skills and knowledge, it is not recommended to start repairing the device, especially electronics. Otherwise, it can be completely disabled, and repairing the welding inverter will cost half the cost of a new unit.
As already mentioned, inverters fail due to external factors affecting the “vital” units of the apparatus. Also, malfunctions of the welding inverter can occur due to improper operation of the equipment or errors in its settings. The most common malfunctions or interruptions in inverter operation are as follows.
Very often, this breakdown is caused by faulty network cable apparatus. Therefore, first you need to remove the cover from the unit and ring each wire of the cable with a tester. But if everything is in order with the cable, then more serious diagnostics of the inverter will be required. Perhaps the problem lies in the standby power source of the device. The repair technique for the “duty room” using the example of a Resant brand inverter is shown in this video.
This malfunction can be caused by an incorrect setting of the amperage for a certain diameter of the electrode.
You should also consider and welding speed... The smaller it is, the lower the current value must be set on the control panel of the unit. In addition, to match the current strength to the diameter of the additive, you can use the table below.
If the welding current is not regulated, the cause may be breakdown of the regulator or violation of the contacts of the wires connected to it. It is necessary to remove the cover of the unit and check the reliability of the connection of the conductors, and, if necessary, ring the regulator with a multimeter. If everything is in order with him, then this breakdown can be caused by a short circuit in the inductor or a malfunction of the secondary transformer, which will need to be checked with a multimeter.If a malfunction is found in these modules, they must be replaced or rewound to a specialist.
Excessive power consumption, even when the device is not loaded, most often causes turn-to-turn closure in one of the transformers. In this case, you will not be able to repair them yourself. It is necessary to take the transformer to the master for rewinding.
This happens if the voltage drops in the network... To get rid of the sticking of the electrode to the parts to be welded, you will need to correctly select and set up the welding mode (according to the instructions for the device). Also, the voltage in the network may sag if the device is connected to an extension cord with a small wire cross-section (less than 2.5 mm 2).
It is not uncommon for a voltage drop that causes the electrode to stick when using a power strip that is too long. In this case, the problem is solved by connecting the inverter to the generator.
If the indicator is on, this indicates overheating of the main modules of the unit. Also, the device can turn off spontaneously, which indicates tripping of thermal protection... So that these interruptions in the operation of the unit do not occur in the future, again, it is necessary to adhere to the correct mode of the duration of the on (DC). For example, if duty cycle = 70%, then the device should work in the following mode: after 7 minutes of operation, the unit will have 3 minutes to cool down.
In fact, there can be a lot of various breakdowns and the reasons that cause them, and it is difficult to list them all. Therefore, it is better to immediately understand what algorithm is used to diagnose the welding inverter in search of faults. You can find out how the device is diagnosed by watching the following training video.
Register to get an account. It's simple!
Already Registered? Sign in here.
PT Devolt702 ku, s, type 1 was brought in for repair. I looked at Dyatko in detail, there it is, but type 2, the question arises, are their anchors interchangeable? If anyone knows, please tell me.
Replacing the keyless chuck on a Panasonic screwdriver
If the chuck of your screwdriver began to hold the bits poorly or jam, then you need to disassemble it,
clean and replace locating balls or replace completely with sleeve and spring
If you do not have a special tool (spreader) at hand, then you can do with two small slotted screwdrivers
We lower the cartridge sleeve down and insert the screwdriver on both sides, hook the retaining ring with one screwdriver
Remove the retaining ring, then remove the spring and take out the sleeve
And carefully take out the balls
Then you can clean everything and put new parts
Bosch jigsaw repair (replacement of the base plate)
Over time, the sole of your jigsaw may break, consider how to quickly replace it with your own hands and without going to a service.
We unscrew the hex bolt at the bottom of the sole, which is attached through a spacer
The screws fixing the plate opened in front of us
There is nothing complicated here, we select a slotted screwdriver and unscrew all the screws
Then we take out the plate and replace it with a new one.
Next, we collect everything in the reverse order.
Repair of welding inverters, despite its complexity, in most cases can be done independently. And if you are well versed in the design of such devices and have an idea of what is more likely to fail in them, you can successfully optimize the costs of professional service.
Replacement of radio components in the process of repairing a welding inverter
The main purpose of any inverter is to generate a constant welding current, which is obtained by rectifying a high-frequency alternating current. The use of a high-frequency alternating current, converted by means of a special inverter module from a rectified mains supply, is due to the fact thatthat the strength of such a current can be effectively increased to the required value using a compact transformer. It is this principle underlying the operation of the inverter that allows such equipment to have compact dimensions with high efficiency.
Functional diagram of the welding inverter
The welding inverter circuit, which determines its technical characteristics, includes the following main elements:
- a primary rectifier unit, the basis of which is a diode bridge (the task of such a unit is to rectify an alternating current supplied from a standard electrical network);
- an inverter unit, the main element of which is a transistor assembly (it is with the help of this unit that the direct current supplied to its input is converted into an alternating current, the frequency of which is 50–100 kHz);
- a high-frequency step-down transformer, on which, due to a decrease in the input voltage, the output current is significantly increased (due to the principle of high-frequency transformation, a current can be generated at the output of such a device, the strength of which reaches 200–250 A);
- output rectifier, assembled on the basis of power diodes (the task of this block of the inverter includes rectifying an alternating high-frequency current, which is necessary for performing welding work).
The welding inverter circuit contains a number of other elements that improve its operation and functionality, but the main ones are the ones listed above.
Repair of an inverter-type welding machine has a number of features, which is explained by the complexity of the design of such a device. Any inverter, unlike other types of welding machines, is electronic, which requires specialists involved in its maintenance and repair to have at least basic radio engineering knowledge, as well as skills in handling various measuring instruments - a voltmeter, digital multimeter, oscilloscope, etc. ...
In the process of maintenance and repair, the elements that make up the welding inverter circuit are checked. This includes transistors, diodes, resistors, zener diodes, transformer and choke devices. The peculiarity of the design of the inverter is that very often during its repair it is impossible or very difficult to determine the failure of which particular element was the cause of the malfunction.
A sign of a burnt out resistor may be a small carbon deposit on the board, which is difficult to distinguish with an inexperienced eye.
In such situations, all the details are checked sequentially. To successfully solve such a problem, it is necessary not only to be able to use measuring instruments, but also to be quite familiar with electronic circuits. If you do not have such skills and knowledge at least at the initial level, then repairing a welding inverter with your own hands can lead to even more serious damage.
Realistically assessing their strengths, knowledge and experience and deciding to undertake independent repair of inverter-type equipment, it is important not only to watch a training video on this topic, but also to carefully study the instructions, in which manufacturers list the most typical malfunctions of welding inverters, as well as ways to eliminate them.
Situations that can cause the inverter to fail or lead to malfunctions can be divided into two main types:
- associated with the wrong choice of welding mode;
- caused by the failure of parts of the device or their incorrect operation.
The technique for detecting an inverter malfunction for subsequent repair is reduced to the sequential execution of technological operations, from the simplest to the most complex. The modes in which such checks are performed and what their essence is, is usually specified in the equipment instructions.
Common inverter malfunctions, their causes and remedies
If the recommended actions did not lead to the desired results and the operation of the device has not been restored, most often this means that the cause of the malfunction should be looked for in the electronic circuit. The reasons for the failure of its blocks and individual elements may be different. Let's list the most common ones.
- Moisture has penetrated into the interior of the device, which can happen if precipitation falls on the body of the device.
- Dust has accumulated on the elements of the electronic circuit, which leads to a violation of their full cooling. The maximum amount of dust gets into inverters when they are used in highly dusty rooms or on construction sites. In order not to bring the equipment to such a state, its interior must be regularly cleaned.
- Overheating of the elements of the electronic circuit of the inverter and, as a consequence, their failure can lead to non-observance of the duration of the switch (DC). This parameter, which must be strictly observed, is indicated in the technical passport of the equipment.
Liquid traces inside the inverter housing
The most common problems encountered when operating inverters are as follows.
Unstable arc burning or active metal spatter
This situation may indicate that the wrong amperage has been selected for welding. As you know, this parameter is selected depending on the type and diameter of the electrode, as well as on the speed of welding. If the packaging of the electrodes that you are using does not contain recommendations on the optimal value of the current strength, you can calculate it using a simple formula: 1 mm of the electrode diameter should account for 20–40 A of welding current. It should also be borne in mind that the lower the welding speed, the lower the current should be.
Dependence of the diameter of the electrodes on the strength of the welding current
This problem can be associated with a number of reasons, and most of them are based on undervoltage. Modern models of inverter devices also operate at reduced voltage, but when its value drops below the minimum value for which the equipment is designed, the electrode begins to stick. A drop in the voltage value at the output of the equipment can occur if the device blocks do not contact the panel sockets poorly.
This reason can be eliminated very simply: by cleaning the contact sockets and fixing the electronic boards in them more tightly. If the wire through which the inverter is connected to the mains has a cross-section of less than 2.5 mm2, this can also lead to a voltage drop at the input of the device. This is guaranteed to happen even if such a wire is too long.
If the length of the supply wire exceeds 40 meters, it is practically impossible to use an inverter for welding, which will be connected with its help. The voltage in the supply circuit can also drop if its contacts are burnt or oxidized. A frequent cause of electrode sticking is insufficiently high-quality preparation of the surfaces of the parts to be welded, which must be thoroughly cleaned not only from the existing contaminants, but also from the oxide film.
Selection of the cross-section of the welding cable
This situation often occurs in the event of overheating of the inverter device. At the same time, the control indicator on the panel of the device should light up. If the glow of the latter is hardly noticeable, and the inverter does not have a sound alert function, then the welder may simply not be aware of overheating. This state of the welding inverter is also typical when the welding wires are broken or spontaneously disconnected.
Spontaneous shutdown of the inverter during welding
Most often, this situation occurs when the supply of the supply voltage is turned off by circuit breakers whose operating parameters are incorrectly selected. When working with an inverter device, automatic machines designed for a current of at least 25 A must be installed in the electrical panel.
Most likely, this situation indicates that the voltage in the power supply network is too low.
Automatic shutdown of the inverter during prolonged welding
Most modern inverter machines are equipped with temperature sensors that automatically turn off the equipment when the temperature in its interior rises to a critical level. There is only one way out of this situation: give the welding machine a rest for 20-30 minutes, during which it will cool down.
If after testing it becomes clear that the cause of malfunctions in the operation of the inverter device lies in its inner part, you should disassemble the case and start examining the electronic filling. It is possible that the reason lies in poor-quality soldering of device parts or poorly connected wires.
A close inspection of the electronic circuits will reveal faulty parts that may be darkened, cracked, bloated, or have burnt contacts.
Burnt parts on the Fubac IN-160 inverter board (AC-DC regulator, 2NK90 transistor, 47 ohm resistor)
During repair, such parts must be removed from the boards (it is advisable to use a soldering iron with a suction for this), and then replaced with similar ones. If the marking on the defective elements is not readable, then special tables can be used to select them. After replacing defective parts, it is advisable to test the electronic boards using a tester. Moreover, this must be done if the inspection did not reveal the elements to be repaired.
A visual check of the electronic circuits of the inverter and their analysis with a tester should start with the power unit with transistors, since it is he who is the most vulnerable. If the transistors are faulty, then, most likely, the circuit that shakes them (driver) has also failed. The elements that make up such a circuit must also be checked first.
After checking the transistor unit, all other units are checked, for which a tester is also used. The surface of the printed circuit boards must be carefully examined to determine the presence of burnt areas and breaks on them. If any are found, then such places should be carefully cleaned and jumpers should be soldered on them.
If burnt or broken wires are found in the filling of the inverter, then during repair they must be replaced with similar ones in cross section. Although the diode bridges of the inverter rectifiers are reliable enough, they should also be ringed with a tester.
The most complex element of the inverter is the key control board, the operability of which depends on the operability of the entire device. Such a board for the presence of control signals that are fed to the gate buses of the key block is checked using an oscilloscope. The final stage in testing and repairing the electronic circuits of the inverter device should be to check the contacts of all existing connectors and clean them with a regular eraser.
Self-repair of an electronic device such as an inverter is quite difficult. It is almost impossible to learn how to repair this equipment just by watching a training video, for this you need to have certain knowledge and skills. If you have such knowledge and skills, then watching such a video will give you the opportunity to make up for the lack of experience.
It is well known that the repair of welding machines in the overwhelming majority of cases can be organized and carried out independently.The only exception is the restoration of the efficiency of the electronic inverter, the complexity of the circuit of which does not allow for full repairs at home.
Even an electrical engineer can be confused by just trying to turn off the protection of an inverter. So in this case, it is best to seek help from a specialized workshop.
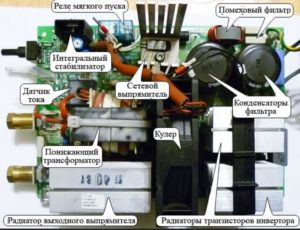
- the device does not turn on when connected to the mains and started;
- sticking of the electrode with a simultaneous hum in the area of the converter;
- spontaneous shutdown of the welding machine in case of overheating.
Repair always begins with an inspection of the welding machine, checking the supply voltage. It is not difficult to repair transformer welding machines, moreover, they are not picky to maintain. In inverter devices, it is more difficult to determine the breakdown, and repair at home is often impossible.
However, if handled correctly, inverters will last a long time and will not break down. Protect from dust, high humidity, frost, store in a dry place. There are the most typical malfunctions of welding machines, which can be eliminated by hand.
In this case, first of all, you need to make sure that there is voltage in the network and the integrity of the fuses installed in the transformer windings. If they are working properly, use the tester to ring the current windings and each of the rectifier diodes, thereby checking their performance.
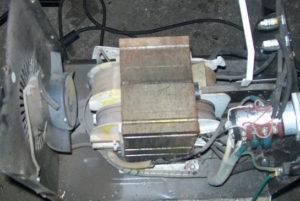
Sometimes the filter capacitor fails. In this case, the repair will consist in checking it and replacing it with a new part.
If all the elements of the circuit are working properly, it is necessary to deal with the mains voltage, which can be greatly underestimated and is simply not enough for the normal functioning of the welding machine.
Electrode sticking and arc interruption can be caused by a voltage drop due to a short circuit in the transformer windings, diode failure, or loose connection contacts. A breakdown of the capacitor filter or short circuiting of individual parts to the body of the welding machine is also possible.
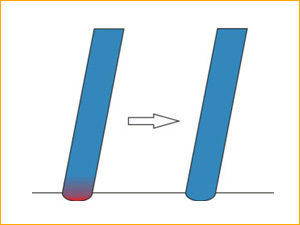
If sticking is accompanied by a strong hum of the transformer, this also indicates an overload in the load circuits of the device or a short circuit in the welding wires.
One of the repair options with the elimination of these effects can be the restoration of the insulation of the connecting cables, as well as the tightening of loose contacts and terminal blocks.
In some cases, repairs can be carried out independently if the device starts to shut down spontaneously. Most models of welding machines are equipped with a protective circuit (automatic) that is triggered in a critical situation, accompanied by a deviation from normal operation. One of the options for such protection involves blocking the operation of the device when the ventilation module is turned off.
After spontaneous shutdown of the welding machine, first of all, you should check the state of protection and try to return this element to working condition..
If the protective unit re-operates, it is necessary to proceed to troubleshooting according to one of the methods described above, associated with short circuits or malfunction of individual parts.
In this situation, first of all, you should make sure that the cooling unit of the unit is working properly, and that overheating of the internal spaces is excluded.
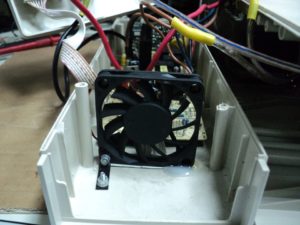
In the absence of internal protection, the circuit breaker can be installed in the electrical panel. To maintain the normal functioning of the welding unit, its settings must correspond to the selected modes.
So, some models of such machines (welding inverter, in particular), in accordance with the instructions, should work according to a schedule that assumes a break for 3-4 minutes after 7-8 minutes of continuous welding.
Before repairing an inverter welding machine with your own hands, it is advisable to familiarize yourself with the principle of operation, as well as with its electronic circuit. Their knowledge will allow you to quickly identify the causes of breakdowns and try to eliminate them in a timely manner.
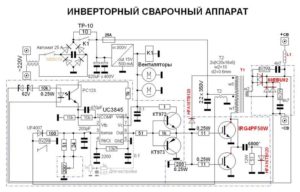
The use of an intermediate high-frequency signal makes it possible to obtain a compact impulse device that has the ability to effectively adjust the value of the output current.
Breakdowns of all welding inverters can be conditionally divided into the following types:
- malfunctions associated with errors in the choice of the welding mode;
- failures in operation due to the failure of the electronic (conversion) module or other parts of the device.
The method for detecting inverter malfunctions associated with malfunctions of the circuit involves the sequential execution of operations performed according to the principle "from simple damage to more complex breakdown." The nature and cause of breakdowns, as well as repair methods, can be found in more detail in the summary table.
It also contains data on the main parameters of welding, providing a trouble-free (without turning off the inverter) operation of the device.
Maintenance and repair of inverter-type welding machines is distinguished by a number of features associated with the complexity of the circuitry of these electronic units. To repair them, you will need certain knowledge, as well as the ability to handle measuring instruments such as a digital multimeter, an oscilloscope, and the like.
In the process of repairing an electronic circuit, first, a visual inspection of the boards is carried out in order to identify burnt or "suspicious" elements in the composition of individual functional modules.
If during the inspection no violations can be found, the troubleshooting continues by detecting violations in the operation of the electronic circuit (checking the voltage levels and the presence of a signal at its control points).
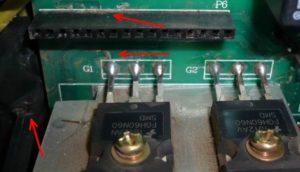
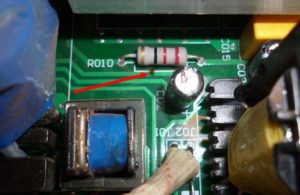
To do this, you will need an oscilloscope and a multimeter, which you should start working with only if you have full confidence in your abilities. If you have any doubts about your qualifications, the only correct solution would be to take (carry) the device to a specialized workshop.
Specialists in the repair of complex impulse devices will quickly find and eliminate the malfunction that has arisen, and at the same time will carry out maintenance of this unit.
If you decide to repair the board yourself, we recommend using the following advice from experienced specialists.
If burnt wires and parts are found during a visual inspection, they should be replaced with new ones, and at the same time all connectors should be plugged in, which will eliminate the option of losing contact in them.
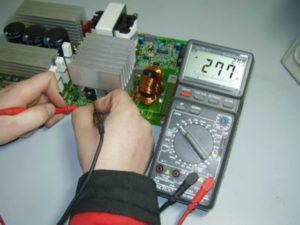
To do this, it is necessary to find sources in which the diagrams of voltages and currents are given, intended for a more complete understanding of the operation of this unit.
Based on these diagrams using an oscilloscope, you can sequentially check all the electronic circuits and identify the node in which the normal picture of the signal conversion is disturbed.
One of the most complex components of an inverter welding machine is considered to be an electronic key control board, which can be checked for serviceability using the same oscilloscope.
If you have doubts about the performance of this board, you can try to replace it with a serviceable one (from another working inverter) and try to start the welding machine again.
In case of a favorable outcome, it remains only to give your board for repair or replace it with a purchased new one. The same should be done when there is a suspicion that all other modules or blocks of the welding machine are in good working order.
In conclusion, we recall that the repair of any welding units (and inverters, in particular) is considered a rather complex procedure that requires certain skills and ability to handle complex measuring equipment.
![]() |
Video (click to play). |
If you have the slightest doubt about your professionalism, you should use the help of specialists and give them the opportunity to return the faulty device to work.