In detail: do-it-yourself repair of a vp44 injection pump from a real master for the site my.housecope.com.
Attention! Car service network of favorable prices. Camber check is FREE! No queues! Repair on the same day!
Download / Print topic
Download a theme in various formats, or view a printable version of the theme.
The injection pump number 059 130 106D was installed on cars:
Volkswagen Passat B5.5 / Volkswagen Passat B5.5 (3B3) 2001 - 2005
Volkswagen Passat Variant B5.5 / Volkswagen Passat Variant B5.5 (3B6) 2001 - 2005
Volkswagen Passat B5 / Volkswagen Passat B5 (3B2) 1997 - 2001
Volkswagen Passat Variant B5 / Volkswagen Passat Variant B5 (3B5) 1997 - 2001
Audi A4 B5 / Audi A4 B5 (8D2) 1995 - 2001
Audi A4 Avant B5 / Audi A4 Avant B5 (8D5) 1996 - 2002
Audi A6 C5 / Audi A6 (4B2) 1997 - 2005
Audi A6 Avant / Audi A6 Avant (4B5) 1998 - 2005
information is suitable for repairs and other cars.
Hello everyone! I decided to write a report on self-repair of the Bosch VP44 injection pump, number 059 130 106D, auto Audi A8 D2 2.5tdi V6, but this pump was not installed anywhere, Audi A4, A6, VW, BMW, Opel, often breaks down on trucks - so I think the information will not hurt.
I had no experience with high-pressure fuel pumps - so I bombarded specialists with questions on various forums - thanks to everyone who helped with advice!
A big role was played by the report of the owner of the Opel Vectra - Mitrofana (Thank you). The progress of the disassembly process is displayed there.
I want to tell you about my experience and my own “rakes” so that no one would jump on them again.
![]() |
Video (click to play). |
So, after pumping with a pear or something from the nozzle pipes, nothing presses when scrolling with the starter - it means you have problems with mechanics: the most likely option is damage to the membrane (or cutting rings), the second option is a defect in the booster pump ... You will see all this later in the photo.
Anyone who has everything working properly - here you can view the high-pressure fuel pump from all angles, incl. his most intimate places
To begin with, while the pump is on the machine, we set the timing and injection pump to the “base” position so that the hole for the stopper coincides with the hole on the pulley (we shine a flashlight), you can rotate the timing either by the crankshaft or by the camshaft (but with a force of no more than 75 Nm (! ), smoothly, with pauses, or with a gearbox, hanging out the muzzle, rotating the wheel. Then loosen the nut by 27mm of the gear wheel, put a clear mark on the shaft and the gear wheel. We may need it when reassembling. The tooth itself. The wheel sits firmly on the "cone "- even without a nut, it won't move a single gram, you don't need to press it yet, so far we only need a mark with an awl:
The decision on whether to compress it or not will be made later (so as not to do unnecessary work).
Then we unscrew the pump from the auto - we close the fitting with something and thoroughly rinse it with a “karcher”, then blow it in places with a carb cleaner and blow it with compressed air so that there is less dirt during disassembly:
We unscrew the "brains" and 2 e-mail. valve (details at Mitrofan), for this we need Torx 10,25,30 (later another T20 is possible). Before unscrewing, knock on the Torx with a small hammer, if it does not work, it is better to continue knocking, because when you break the edges, you will have to drill and drive in the “M” bit.
When pulling out the central valve (with a screwdriver as a lever), you need to make sure that it comes out without skewing, if it skews, push it back and again try supporting it from below.
Then we bring the gear wheel (which is still firmly sitting on the cone) to the mark into which the stopper is inserted (or, as for a collective farm, a 6mm drill), unscrew the T50 bolt, remove the washer under it and tighten it all the way, thereby blocking the movement of the shaft, the stopper take out:
In this case, the back will be in this position:
Further, to remove the distributor head according to Mitrofan, we burst and swing with screwdrivers, but I, so as not to spoil the al. the body simply rested with a screwdriver and knocked down with a hammer:
We remove the distribution head and see the very defect due to which the pressure disappeared - damage to the outer plastic part of the membrane:
If you saw such a picture (or just a crack), then there is no need to disassemble further - we change the membrane and rubber rings and put them back together.Membrane repair kit Bosch 1 467 045 032. But there are important nuances, read here
Since I did not immediately notice due to inexperience, I disassembled further:
Further, to remove the bearing according to Mitrofan, we pull it with a thick wire, I just spread the newspaper on the floor and hit it with the body - by inertia the bearing and 2 washers came out:
Then you need to unscrew the plug, wrap the top with paper or a rag and pull out with pliers:
With drifts or something handy, we turn the cam washer and the piston to the position at which the cool. the washer will move up (in the photo you need to turn it a little clockwise and it will rise):
After removing the cooler. washers - we take out the piston - this is how it looks from all sides (if it comes out badly, you can swing it with drifts for 2 holes, which are in the photo at the top left, but do not stick it deep into the hole):
Now we press the gear wheel off the shaft (while the shaft is "pressed in" Torx50, which was mentioned above, otherwise, when removed, the shaft will shoot like a bullet - both the shaft and the housing can be damaged). You will need a GOOD puller, the effort is HUGE, we put good pieces of rags under the puller's paws, so as not to leave “jammed”.
After pressing, we loosen T50 and take out the shaft.
... and the puck (what's underneath). The booster pump remains in the housing.
Now, using T20, unscrew the bolts (you need a long and thin T20, preferably):
It is desirable to “shake it out” by hitting the body on the newspaper - then it will fall out “assembled”. If you try to push from behind with your fingers, it will most likely fall out "in parts", this is bad:
As they say, it is undesirable to confuse the blades in places, otherwise they can wedge at revolutions.
Another photo of him:
It is serviceable, the only thing there is a small defect - chipping, but this is not criminal:
The booster pump was taken from the spare donor pump, it fell out “assembled”, we rinse very well. carba:
Then the empty body was washed with "Karcher" (without bringing it close to the channels), then och. Carba dried through channels and compressed air. Purity:
Install the booster pump (donor) in place:
We put the washer and insert the shaft (in the photo the washer hangs on the shaft):
The gear wheel is ready for installation:
Align it according to our scratch mark with the shaft, then rotate it until the hole for the stopper is aligned and block T50:
Slightly (!) Fill the tooth. the wheel onto the shaft, lightly tighten the nut by 27mm. We put catalogs and a tooth damper on the table. wheels to position the injection pump conveniently for further assembly.
In this case, the picture is as follows, the shaft is locked in the “basic” position:
The piston was taken from the donor pump, the scratches were slightly sanded with the P800, 1500, 2000 legs. It is advisable to grind the sleeve itself in the injection pump housing with P2000 (but this is before washing).
As you can see on the left - the piston ring interferes with the assembly - we just wrap the piston with plastic film, squeeze it with our fingers and put it on:
Place the piston so that the cam washer is “filled” into it (yellow arrow). The second point of connection is cool. washers - black arrow:
And here is the cam washer itself, these 2 pins must be “inserted” into the holes:
In this topic, a selection of links and information on repairing the VP44 pump installed on the ZD30 and many other engines will be collected.
Fast transitions
- Features of the VP44 pump
- VP44 issues
- Diagnostics
- How to properly pump (fill with fuel) an airborne injection pump
- How to get to the "mesh" in the injection pump
- Repair kit for injection pump VP44
- Removal and installation of injection pump
- Dismantling the injection pump
- Replacing the transistor
- useful links
Features of the VP44 pump
The VP44 injectors are designed with two springs, with the help of which two stages of needle lift are realized. In addition to the usual parameters typical for single-spring injectors (needle lift pressure, cutoff, fuel spray pattern, leakage), two-spring injectors have such parameters as needle lift pressure of the second stage and fuel consumption through the nozzle, which are determined only on a special stand ... In the malfunction of the injectors, the reason for the drop in engine power is often covered.
Booster pump, automatic injection timing, injection timing control valve and other problems
Malfunctions of the VP44 injection pump as part of the ZD30 are associated with these nodes, and the main problems leading to these malfunctions are as follows:
- air leaks in the fuel line
- poor permeability of the fuel line (clogged filter or paraffin wax)
- water in the fuel, poor fuel quality or poor quality fuel filter
- damage to the injection pump wiring
Thus, in Russian realities, at the inlet to the VP44 pump of the ZD30 engine, we have chronic air leaks, water and an increased load on the booster pump with a clogged filter or poor passability of the fuel line. Considering the fact that the lubrication of the mechanical parts and the cooling of the electronic part of the VP44 injection pump is carried out directly by the fuel supplied to it, the above factors are deadly for it. Water and air lead to accelerated wear of all mechanical components of the high pressure fuel pump, the first of which often dies out the booster pump.
Automatic injection advance.
As mentioned above, a situation often arises on the ZD30 when the booster pump may lack performance for a number of reasons (air, poor fuel permeability), as a result of which it is not able to provide the necessary pressure on the advance switch piston.
The automatic injection advance, in turn, is the lowest point of the pump, so water and dirt that enters it along with low-quality fuel can accumulate in it, as in a sump, which leads to accelerated wear of its piston (seizure, depletion), and in ultimately, and to its wedging. When the automatic injection advance is wedged in the early injection position, when a number of factors characteristic of the ZD30 coincide (an artificially lean mixture, coupled with an underestimation of the mass air flow sensor and, as a consequence, an increased boost pressure), it can lead to a violation of the thermal regime in the CGU (piston burnout, cylinder head crack ).
Fuel filling control valve (metering valve).
The problems with this valve are as follows:
- Wear, valve wedging and malfunction due to dirt and water in the fuel.
- Collapse of insulation, damage and short circuit of its external wiring.
- Turn-to-turn short circuit or breakage of the valve winding due to overheating.
- Failure of the control key due to a short circuit in the winding, wiring or insufficient cooling due to the presence of air in the fuel system
Prolonged presence of a large amount of air in the fuel or the operation of the pump when airing the fuel system can also lead to failure of the control key and inoperability of the valve. It is for this reason that you should not grease the starter for a long time, trying to start the engine with strong airing of the fuel system.
Injection timing control valve (advancing).
The problems with this valve are as follows:
- The valve is located at the bottom, so water and dirt in the fuel can accumulate in it, which can lead to malfunctioning.
- The valve wiring has an external location, therefore, in addition to the "fuel" factors, the valve is also affected by weather and temperature, as well as vibration and oil, which can get on the injection pump wiring from the ZD30 snotty intercooler. Exposure to changes in temperature and oil leads to damage (shedding) of the wire insulation and, as a result, to possible current leakage or short circuits. Continuous vibration can lead to internal fracture of the conductors, as a result of which the valve also ceases to function.
- Failure of the control key due to a short circuit in the wiring.
Features of ZD30 Nissan Patrol Y61.
Another problem is associated with the unsuccessful location of the intercooler on the ZD30, due to which it, unable to withstand vibration, begins to actively snot with oil, which flows onto the wiring and connectors of the injection pump, which, in turn, leads to the destruction of the insulation of the wires and glitches in the exchange of data ECM injection pump. You can learn more about the problem here.
Diagnostics
In the VP44 injection pump there are no sensors for the presence of water and air in the fuel, but indirectly, the problem with the quality of the fuel and the patency of the fuel line is diagnosed by the presence of error 77 (injection advance, synchronization system), the possible causes of which are poor performance of the injection pump pump of the injection pump due to its wear, poor the patency of the fuel line or the presence of air in it. If such an error appears regularly, first of all, you need to make sure of the quality of the fuel, change the fuel filter and exclude air leaks along the entire fuel line.
Errors 74 and 76 indicate problems with the injection timing control valve, when they appear, it is necessary to check the condition of the valve wiring, or even better, remove it, clean it and ring the winding to detect a crease. Error 76 can also indicate a failure of the transistor key of the injection timing control valve.
Errors 73 and 75 indicate problems with the injection pump wiring, when they appear, you need to check the condition of the injection pump wiring and take measures to protect it. The 73rd code may also appear when trying to start the engine with a low battery.
For more information on possible errors, their descriptions and diagnostic methods, click here.
How to properly pump (fill with fuel) an airborne injection pump
During the repair and maintenance of the fuel system, as well as as a result of leaks in the fuel line, the injection pump may become airy. Lubrication of the injection pump mechanisms and cooling of its ECU is carried out directly with fuel, therefore, before starting the engine, it is highly desirable to remove air and fill the injection pump with fuel.
A bypass valve is installed on the VP44 return connection, which does not allow pumping the high-pressure fuel pump by pumping fuel at the inlet. In order to pump the VP44, you need to fill it with fuel by pumping out air through the return connection.
To do this, unscrew the bolt with the bypass valve and temporarily turn the usual hollow bolt (banjo (banjo) -bolt) M14 instead.
The fuel supply to the high-pressure fuel pump is lowered into a container with fuel (through a filter), and a hand pump (pear) is connected to the return connection through a transparent hose to evacuate air.
The pump is pumped until fuel without air bubbles flows through the return hose.
Information provided by user GusevLebedev
How to get to the "mesh" in the injection pump
Disassembly:
- We take out the right battery.
- Disconnect the feed and return hoses to the injection pump from the fuel filter.
- Remove the fuel filter from the bracket and move it towards the engine shield.
- For convenience, you can remove the intercooler, but not necessary.
As a result, there will be access to the pressure reducing valve that regulates the internal pressure of the injection pump. Under this valve there is a strainer ("mesh"), which prevents the ingress of wear products of the booster pump and dirt into the mechanisms of the injection pump.
![]() |
Video (click to play). |
You can read more about the pressure reducing valve and the VP44 pump in the BOSCH tutorial
16700 VX100
16700 VX101
the numbers of our fuel pumps, they are interchangeable, although 101 has been going on since 06 and I would put it only with nozzles from the Zexel restyling 9430613801
Bosch F01G09X03S, they have more nozzles
REPAIR OF INPUTS, PURCHASE OF REPAIRED -
Injection pump VP44 - zd30
Began the second part by tradition, who wants to see the first
here is the topic of repair
the brains of the injection pump are not interchangeable, even if they are from a similar injection pump, the car will start, drive, but it will not develop full power
brains must be registered at the stand, brains can be registered three times, there are three paths for filling in information, it is non-retrievable and indelible
so after three times you need to buy new brains for the injection pump
On the advance valve (according to scheme 424), there is not a rare case of insulation crumbling followed by a short circuit (the Internet is full of information). At the same time, the car works but does not pull and error 77 appears. At least this is the case for me. To remove this valve, it is necessary to unscrew 2 bolts and remove the bracket (for cx 400) and, accordingly, 2 bolts on the valve itself. Without removing it is probably possible, but you will have to tinker. The 805 valve has short wires and is very difficult to slide into place.
By the way, regarding WD40, I personally have been using it in electrical equipment for a long time to process contacts and even high-voltage equipment (at work at 6 kV). Processed ignition distributor covers (distributor). As far as I know, this slurry contains oils with high hardenability that fill microcracks and prevent electrical breakdown. But now on the market (at least we have) there are many different options. In the photo under number 1, pure china and I would not risk it e-mail. to process. No. 2 is normal, and No. 3 went this way initially. Also in the photo is the set necessary for removing the injection pump valves
the bypass (pressure reducing) valve is located in the front of the injection pump on the right side in the direction of travel (fungus with cut flats, and in the middle there is an adjusting plug-piston.
The pressure regulating valve in the pump is located in the plug, which closes this hole. There is a piston, and a spring on top. In order to increase the pressure, you can not turn out the plug, there is something like a groove with a diameter of about 5 mm in it outside in the center, we take a barb and put it in the groove and put the rod in the bottom the rod compresses the spring pressure in the high pressure pump increases, sometimes it is necessary to Tap 1mm several times.
internal pressure of our injection pump VP44
740 rev - 7 atm (XX)
1000 rpm - 9 atm
1200 rpm - 11 atm
1500 rpm - 15 atm
2000 rpm - 18 atm
2500 rpm - 20 atm
3000 rpm - 21 atm
4000 rpm - 23 atm
The mesh is removed like this, you need a key, make a cut of 10mm in round timber by 12-14 (or with a key of 10 cut short), lift the intercooler and unscrew the valve and pull out the valve with a screw as in the photo.
to check the in-body pressure, it is necessary to unscrew the plug, insert a pressure gauge, it can be a hose with a threaded end, etc.
If, after a primitive check of the fuel pressure on the injectors, it does not start, then the transistor has burned out and also check the return flow, maybe when tightening the pipes it damaged the hoses, they seem to be normal, but in fact it’s dust, maybe the tee broke.
After airing it, until all four high-pressure pipes splatter the salar and it takes a long time to be oiled with a starter, you will not start.
A working pump produces 350-400 kgcm, a dead one 200, but even this pressure cannot be held by any rubber hose. The other thing is that everything is electrically implemented there. Try to pump it as it should, it may help.
RS My friend Zafir has a 2.2, and so he said that if the pump is pumped incorrectly, the injection pump is airing and that something in his electronic brain breaks down. I'll try to ask for more details.
So I was surprised at this pressure of 3-4 atmospheres.
The electrician controls the valve (its distribution), it works. When the transistor burned out, the fuel did not go at all. Now it splashes from the high-pressure fuel pump alternately by 10 centimeters and is the same, but through pipes 2 and 3 of the cylinder it barely pumps it to the nozzles.Here, from the pipes for 1 and 4 nozzles, when the nuts are loosened, it splashes well.
Tomorrow or the day after tomorrow, I'll try to drown out the return line altogether and pump it again - in fact, this is the last hope.
Well, if the motor is alive, then on two pots you should at least grab, smoke, etc.
Yes, I should. But if the pressure is not sufficient in the cylinders, it will not start. Probably because of this, it is, since there was no problem with the thrust of the engine itself.
... But if the pressure is not sufficient in the cylinders, it will not start.
It is necessary to try to start from the tug, of course, first completely de-air. Well, there it is based on the results.
The transistor has already changed before. Without it, the fuel did not pass from the high-pressure fuel pump at all. Now it spits well, but it doesn't seem to create a lot of pressure.
I will not start until it splashes from the high-pressure pipes. It is from the tubes that it splashes only from 1 and 4 cylinders, from 3 it drips a little, from the tube to 2 cylinders it does not come out at all. It seems to be the same with the high-pressure fuel pump.
I also recently changed the pipes on the return line.
In general, the questions remained the same. At least tell me if I am checking the pressure correctly, with the pipes unscrewed from the injection pump and a pressure gauge screwed to one of them through a rubber hose.
What transistor did you install? if you just replaced the transistor without finding the reason, then it will continue to burn.
What transistor did you install? if you just replaced the transistor without finding the reason, then it will continue to burn.
Which one I don’t remember exactly, after the repair I traveled for almost a year. Like IRLR2905, maybe IRL2505 - which one is more helpful.
The transistor controls the valve, without it, the fuel does not go at all. I have the same splashes, but the pressure is weak.
As the intense heat began, I began to podglyuchitsya. After stopping the engine, it will not start until you cool it down. It was enough to pour a glass of water onto the control unit, or wait a couple of hours.
Which one I don’t remember exactly, after the repair I traveled for almost a year. Like IRLR2905, maybe IRL2505 - which one is more helpful.
The transistor controls the valve, without it, the fuel does not go at all. I have the same splashes, but the pressure is weak.
As the intense heat began, I began to podglyuchitsya. After stopping the engine, it will not start until you cool it down. It was enough to pour a glass of water onto the control unit, or wait a couple of hours.
Did you put the transistor inside the injection pump or bring it out?
I understand that all four of you are sprinkling with the injection pump normally, you screw up the tubes with 1 and 4 it sprinkles well, but with 2 and 3 it is bad, maybe there is a problem in the tubes, is it clogged or something?
And also look at your problem here.
Do not disappear, unsubscribe.
If, after a primitive check of the fuel pressure on the injectors, it does not start, then the transistor has burned out and also check the return flow, maybe when tightening the pipes it damaged the hoses, they seem to be normal, but in fact it’s dust, maybe the tee broke.
After airing it, until all four high-pressure pipes splatter the salar and it takes a long time to be oiled with a starter, you will not start.
Likewise, fuel came from all pipes and start x. , managed to land Akum and spin while charging.
I soldered the transistor into a regular place without removing the pump, hanging upside down over the engine. If it bugs from overheating, then I will glue the radiator from the computer processor to the top cover, I think it should help.
You will change the filter, replace the rings on the quick-detachable fittings, usually there is a suction, outer diameter 12, thickness 1.8 or 2, I don’t remember exactly, you can buy it in auto markets.
You will change the filter, replace the rings on the quick-detachable fittings, usually there is a suction, outer diameter 12, thickness 1.8 or 2, I don’t remember exactly, you can buy it in auto markets.
If you have an all-metal filter, then do not worry about the rings, by the way, discard its number, and another reason for the transistor overheating is not a native filter, the Germans calculated the throughput of the native filter, and the non-native filter may have a lower throughput, the salary is not enough to heat up the injection pump and wear of the mechanical part, the second stuck ignition timing valve.
You should see a transparent hose, if you don't tighten it with clamps, it will let it through, replace it, look in other places for air leaks starting from the tank.
We do not have a check valve in the fuel system, there is only in the injection pump itself in the return pipe and an electronic one which is also in the injection pump, you can read about the operation of the injection pump in the books of Y. Shkolevsky, here.
.
I cut the wires on it and measured the resistance, it showed somewhere 0.1 ohm. I don’t know how much it should, but it seems suspiciously little.
.
I measured the resistance of 2 valves, one of them is now running my car - 0.147 Ohm.
I measured the resistance of 2 valves, one of them is now running my car - 0.147 Ohm.
Thank you. This now clarifies the situation more, the valve is most likely alive.
It clicks on the mechanic. You unscrew the spring and the fungus itself, screw it into place and start without wires, you have to jam it only with speed, but it will do for checking.
If we talk about the same thing. At the mechanic, he “starts” and muffles the car.
On the mechanics there is a little different - it just jamming. Here the system is more complicated; it also doses fuel in pulses. But the click should probably be the same as yours.
There is no more complex and critical unit in a diesel engine than the fuel injection system, more precisely, its main part - the high pressure fuel pump. Many mating parts, highly loaded units, the presence of a precision dosing system, make the repair of the injection pump a difficult task even in service conditions. It is all the more difficult to repair the high pressure fuel pump of a diesel engine with your own hands.
In automotive technology, almost everything is repaired, except, perhaps, individual oil seals and cuffs, the repair of which is impossible without special materials. The complexity of setting, diagnosing and repairing the injection pump requires the employee to have skills in working with precision mechanics.
It is simply impossible to adjust according to the factory parameters, without a special diagnostic stand for the repair of the injection pump. During the diagnostic study of the injection pump, it is necessary to check:
- cyclic supply of the high-pressure pump, in the entire range of revolutions of the injection pump shaft, at start-up, and after cutting off the fuel supply;
- stability of the developed pressure;
- uniformity of the injection pump delivery to the fuel injector.
Even having access to a diagnostic stand, and having studied the issue of repairing a high-pressure fuel pump using numerous videos, it is very difficult to qualitatively check and evaluate its work.
In heavy diesel engines, plunger, in-line injection pumps are used. In maintenance and repair, such devices are more difficult, since they require special equipment for its disassembly, therefore we will not consider such high pressure fuel pumps and their repair.
In a passenger diesel engine, a distribution type injection pump is almost always used. Unlike in-line pumps, in a distribution pump, the force is transmitted to the plunger using a profiled cam washer. The design of the injection pump turned out to be more compact, but it is hardly simpler to expect to carry out its repair on the knee.
The most famous and affordable is the Bosh VP44 injection pump. Often, the need to repair the pump internals arises when:
- poor traction and incomplete combustion of fuel even under ideal conditions - in the absence of load and a thoroughly warmed up engine;
- a sudden failure and stoppage of a diesel engine under load, which is called “death on takeoff”. Usually the scanner in such cases diagnoses the code P1630 and P1651.
- the appearance of a diesel fuel leak in the area of the gland seal of the central shaft of the injection pump.
Therefore, we will restrict ourselves to the issue of repairing the injection pump with our own hands by replacing the seals and eliminating the scoring of the working surfaces of the parts.
Before disassembling the pump drive shaft seal, try to move it radially. If play is felt with your hands, it is possible that the reason for the leakage of fuel is the wear of the working surface of the shaft or requires repair of the bearing.
A large number of split planes and mating surfaces of parts required the use of a large number of seals and glands. As a rule, they are made of quality material and last long enough until they are damaged during repair or maintenance. In this case, standard repair kits are used for DIY repair of Bosch injection pumps.
It is quite easy to replace the seal on the shaft position sensor and on the automatic injection timing during repairs.For a better fit, you can drip a few drops of spindle or engine oil onto new rings and rubber bands.
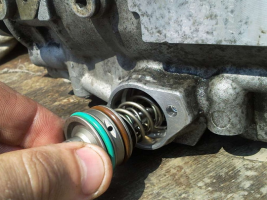

For preventive repair of a Bosch injection pump with your own hands, you will need to disassemble the pump in approximately the following order:
- remove the metering valve from the end of the injection pump. To do this, unscrew the four screws of the pressure plate, carefully release the cable of the injection advance valve. By removing the three screws securing the metering valve, you can carefully remove it from the seat;
- by unscrewing the fastener on the top cover, you can remove the control board and gain access to the electronics;
- we set the position of the shaft, as shown in the photo, remove the camera and get access to the insides of the injection pump;
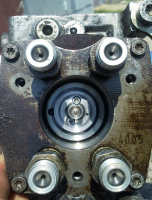
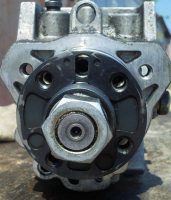
- after dismantling the bearing using a special puller, we get the opportunity to study the potential culprit for the poor performance of the injection pump - the piston of the injection advance unit. There is often surface wear and edge scuffing on the part. You can try to make repairs by polishing the surface, replacing the whole part is much more expensive.
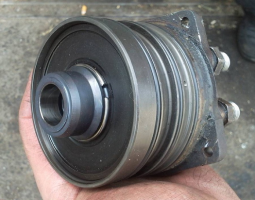
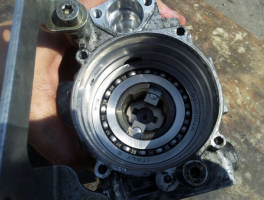
After the repair, the assembly is carried out in the reverse order with the washing of the parts with diesel fuel.
Often, in addition to scoring, on the surface of the pistons there is another reason why the injection pump does not develop the required pressure. This can be due to debris, films or wax build-up on the filter screen inside the pump. There is a mesh on the side of the inlet pipe. Rinsing the channels is a troublesome and ineffective business, it is easier to remove the mesh and blow it with compressed air.
Torn pieces of debris can jam the plunger piston or even break or break the pump drive shaft. Therefore, cleaning should be done very carefully to avoid contamination of the internal cavities of the pump.
Among the many reasons for the failure of the electronic "liver" of the injection pump, the most common is the breakage or burnout of the contacts of the control board and the failure of power transistors. If the knowledge and skills of working with electronic devices allow to carry out a "continuity" of the transistor performance and repair, it is worth trying to identify the cause and replace the culprit with a serviceable element.
To check the condition of the "culprit", you need to carefully open the black cover, which is tightly seated on the rubber seal with screws. It should be removed carefully so as not to damage the seal itself.
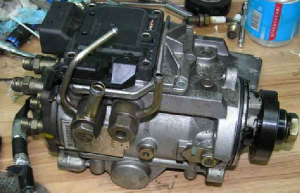
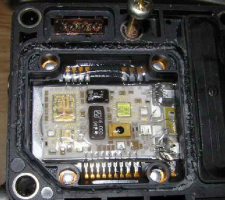

The reason for the failure of not only the transistor, but also the entire board could be air trapped in the cavity due to poor performance of the drainage system or the check valve. Often, they try to eliminate the airing by spinning up with a starter, hoping to pump diesel fuel into the high-pressure fuel pump in this way. At this moment, the transistor is open and loaded as much as possible, which leads to intense heating. In an air environment with poor heat dissipation, it will inevitably burn out. In some German cars there is a protection that prevents an attempt to start the engine in the absence of fuel in the highway. For this, a fuel sensor in the tank is used.
Failure of the transistor can be established by "dialing" a tester or by its appearance. The best option for repairing such a malfunction would be to replace the entire control board. Perhaps it is more expensive than soldering, but it will give guaranteed quality and stable operation of the injection pump after repair. As a last resort, give the board and the transistor for soldering to electronics specialists.
When installing and reassembling after repairs, check the tightness of all fasteners.
If during the audit you did not make rash and unreasonable replacements of parts, the assembled pump should work with approximately the same parameters as before. Bosch EPS-815 stand is used as a standard for testing and adjusting injection pump after overhaul.
The video shows how to raise the plunger pressure in a Bosch VE injection pump:
the advance piston was covered, error P1220.