In detail: do-it-yourself bumper amplifier repair from a real master for the site my.housecope.com.
Broken plastic bumper reinforcement
Restored reinforcement with sheet metal and self-tapping screws
Bumper lining crack
Aluminum beam and plastic bumper reinforcement
Beam with plastic reinforcement in foam
Plastic reinforcement cut
INFA for your judgment or sensible advice on further work on the cladding.
Broken plastic bumper reinforcement
Restored reinforcement with sheet metal and self-tapping screws
Bumper lining crack
Aluminum beam and plastic bumper reinforcement
Beam with plastic reinforcement in foam
Plastic reinforcement cut
INFA for your judgment or sensible advice on further work on the cladding.
well done Toko beam, I would put my own, this one is too flimsy, 300tyk is not very big money for a new beam
well done Toko beam, I would put my own, this one is too flimsy, 300tyk is not very big money for a new beam
Thank you for your rating. The profile of this beam is not visible in the photo, but it is in the shape of the letter N. The factory beam seemed to me even more flimsy than this aluminum profile. I work with metal myself and trust my eyes. On the brackets, cuts are made so that when hitting, the ini fold into a diamond (depreciation) and a beam in the form of such a profile (letter H) will also serve as a shock absorber. In theory
Forgot to write on the restoration of the bumper lining. After tightening the crack with a riveter, from the inside we solder small nails without a head with a soldering iron, and in those places where there are a lot of cracks or they branch out with a net we solder “rivet tails”. Next, we take a piece of plastic (preferably a piece of the same bumper) and use the dripping method or a soldering iron to melt the cracks from the inside. I did it with a soldering iron - slowly but neatly it turns out
![]() |
Video (click to play). |
- Thank you
- I do not like
Yes, I tried. Did you test the bumper repair place for durability? How does it hold? but it is somehow doubtful, you melted the cracks on one side, and not soldered the entire thickness of the bumper.
By the way, Sergey posted a video on bumper repair on the forum. 3M materials are used there - IMHO is more reliable. for example, the 8th bumper cannot be soldered (there is rubber in the plastic), but our bumpers are 2 orders of magnitude stronger.
I tested the bumper for strength :-) and twisted it and did a lot of other things with it while I was doing it :-) The cracks were drilled and there was no way for them to go further, also the cracks on the inside were dispersed with a soldering iron and sealed with the same plastic. plus nails soldered into plastic and on top there is another layer of fused plastic. I think the integrity of the bumper is sustained.
If it's not difficult to post a link to the video. it seems to be overcoated but I have not seen a video on this topic.
- Thank you
- I do not like

By the way, I rummaged through the favorites, there are still links, I don't know where to shove them. can make a special section "Video" on the forum? I hope one of the moderators will transfer it to the right place:
1. Video tutorial on repairing damaged car body parts.
A video tutorial with a detailed explanation of the theory and practice of abrasive processing, applying paint and varnish coatings.
2. Video tutorial on repairing bumpers.
A detailed video tutorial with a description of the repair technology, a description of the properties of the materials and tools used.
3. Video tutorial on tire fitting.
The video tutorial explains the technology of mounting and dismounting tires for cars and trucks.
4. Video tutorial on car interior repair.
Description of the technology and materials used in the repair of the passenger car interior.
5. Video tutorial on Airbrushing
6.Video tutorial on restoring the geometry of the car body.
7. Video tutorial on the technology of anti-corrosion treatment of cars.
vtomobilja.html
Video tutorial with a detailed explanation of the theory and practice of abrasive processing, applying paint and varnish coatings
-videourok.html
By the way, I rummaged through the favorites, there are still links, I don't know where to shove them. can make a special section "Video" on the forum? I hope one of the moderators will transfer it to the right place:
1. Video tutorial on repairing damaged car body parts.
A video tutorial with a detailed explanation of the theory and practice of abrasive processing, applying paint and varnish coatings.
2. Video tutorial on repairing bumpers.
A detailed video tutorial with a description of the repair technology, a description of the properties of the materials and tools used.
3. Video tutorial on tire fitting.
The video tutorial explains the technology of mounting and dismounting tires for cars and trucks.
4. Video tutorial on car interior repair.
Description of the technology and materials used in the repair of the passenger car interior.
5. Video tutorial on Airbrushing
6. Video tutorial on restoring the geometry of the car body.
7. Video tutorial on the technology of anti-corrosion treatment of cars.
vtomobilja.html
Video tutorial with a detailed explanation of the theory and practice of abrasive processing, applying paint and varnish coatings
-videourok.html
at home with a computer I'll look at the links :-) thanks :-) I think infa will come in handy :-)
Yes, I tried. Did you test the bumper repair place for durability? How does it hold? but it is somehow doubtful, you melted the cracks on one side, and not soldered the entire thickness of the bumper.
By the way, Sergey posted a video on bumper repair on the forum. 3M materials are used there - IMHO is more reliable. for example, the 8th bumper cannot be soldered (there is rubber in the plastic), but our bumpers are 2 orders of magnitude stronger.
About who is stronger.
In general, you can use chisel bumpers not only to clear snowdrifts and push everyone in the parking lot without fear, but they can demolish fences and dig up a vegetable garden - there its thickness will hurt half a centimeter.
But thanks for the info.
Hello everyone, I have a problem like this:
I decided to replace the bumper with 2115 for a start, the rear one, I installed everything and ran into one problem, the rear one is longer, so it is necessary to cut off the excess and fit under the 09 wing. I bought a hairdryer to melt I did a trial heating on a cut piece, but it does not melt, or rather melts but not as plastic but how rubber can it be a bumper like that? For some reason, I always thought that 2samaras had plastic bumpers.
As rubber is completely old, now they are doing plastic.
Repair of the bumper amplifier is one of the areas that has been successfully mastered by our masters, the cost of services is low. As a result of an accident, unsuccessful parking backward or forward, collision with an obstacle, the bumper and the amplifier part are most likely to suffer. We will undertake the repair operations and carry out a high-quality restoration.
- Local repair of the bumper amplifier from 365 rubles.
- Restoring the geometry of the bumper amplifier from 725 rubles.
- Repair of torn parts from 775 rubles.
It all depends on what problem you came to us with. If the matter is only in minor damage due to corrosion corroding metal, then we will clean and grind everything, cover the part with a protective compound, solder the missing length if necessary and install the amplifier in place.
If the damage is serious, the metal is deformed or even torn, it is necessary to restore the integrity of the part, return its original shape, which will be worked on by our specialists. Accurate straightening, welding, as a result of which almost invisible but strong seams are obtained, grinding - everything will be carried out in full accordance with the technology of car repair.
The amplifier for the front bumper, and even more so for the rear, today differs significantly from the first samples of the last century.Whether a car needs such a device, and which part of the body is better protected, will be discussed in this article.
A car bumper is a detail that has probably appeared since the self-propelled cart began to acquire the features of a full-fledged vehicle. The need for it arose for one simple reason: the still imperfect and fragile machines had not reached their perfection, and therefore often ran into various obstacles in the form of pedestals, pillars and fences.
In order to somehow mitigate the damage from the collision, the designers of the company Ford decided to weld a U-shaped metal beam in front, which protects the engine and wheels from impacts. They embodied their idea in 1930, releasing a car with the index Model A... In subsequent years, the company added its contribution to the development of bumpers. Packardby installing an ellipsoidal bumper with shock-absorbing properties on the vehicle. After that, the triumphal procession of this metal part began around the world.
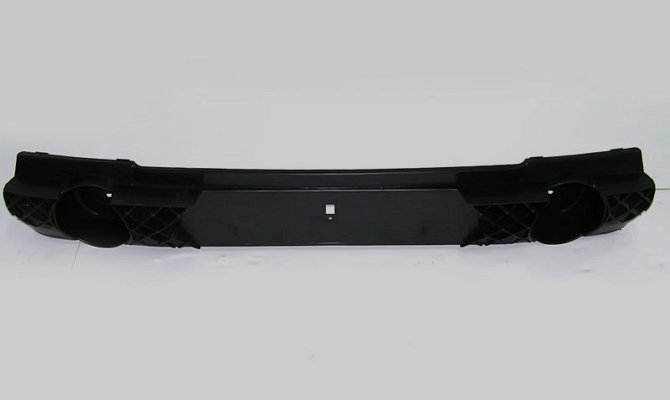
Shock absorbing metal part
In the process of evolution, the bumper has been modified and has now turned from a safety item to a decorative piece. Meanwhile, it has not become safer on the roads and the obstacles have not diminished. In order not to spoil the appearance of cars with a "prehistoric" metal channel, and also not to offend the creative feelings of designers, the designers invented an additional beam, which became the successor to the main part.
The bumper reinforcement is a metal piece that is rigidly attached to the underside of the bonnet under the main bumper. Under the hood, in this case, we mean the front part of the body with a motor. The amplifier gives additional strength to the structure itself. In addition to this function, on some car models, this part also serves as protection against mechanical damage to lighting fixtures.
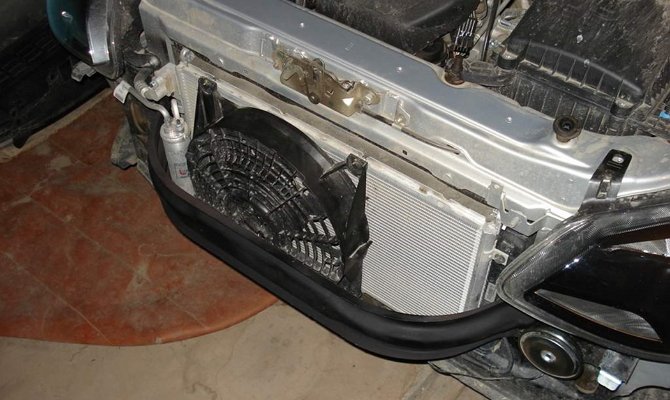
Amplifier under the hood of a car
Despite the fact that some motorists do not like to spend money on various improvements and consider this part superfluous, there are many “craftsmen” who made it themselves for their cars. Be that as it may, some car manufacturers believe that such a device is necessary, and therefore make amplifiers for both the front bumper and the rear. But are there any differences between them, let's try to figure it out.
When we mentioned some manufacturers, we did not indicate that, unfortunately (or fortunately), they are a minority. It is not known what the engineers were guided by, but many (and especially beginners) motorists, after several mini-accidents, understand the need to strengthen the fragile decorative panel. A few minor blows are enough as the bumper itself is covered with cracks and is in need of urgent repair, and expensive optics need to be replaced. If an amplifier is not provided in the design of the car, but you think that it will not interfere with you, contact the service, where they will help you choose a part that matches your bumper.
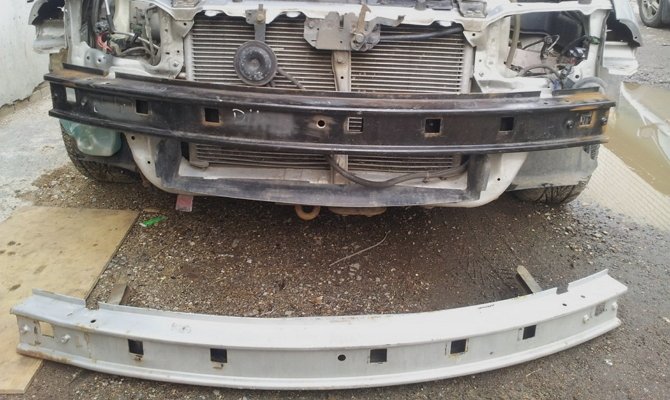
Detail for reinforcing a fragile decorative panel
The rear amplifier has a slightly different role: providing protection for the "rear" of the car. That is, the creation of a kind of buffer zone from impact. Not only from the impact of another vehicle, but also from collisions with obstacles when reversing, to protect against damage to the body, luggage compartment and, of course, things that are there. If we compare both amplifiers, then the functions for which they were created will be exactly the same: to protect the body and units from impacts, to strengthen the bumper, to create a springy effect during collisions. The only difference is probably in the shape of the part itself, but in the holes for the fasteners.
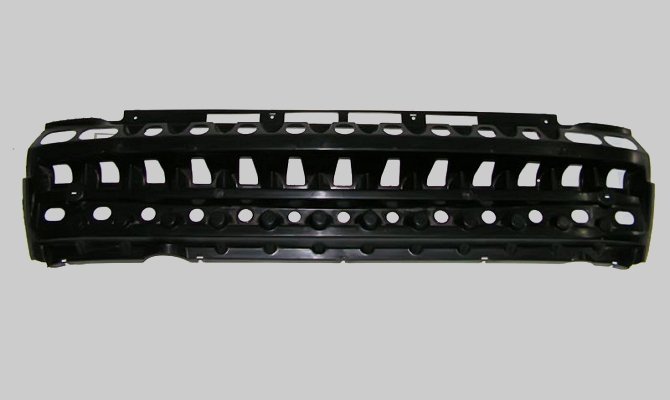
The debate about whether a bumper amplifier is needed or not began with the period of its appearance. Indeed, in addition to the pluses, there are also significant disadvantages.Probably the most unpleasant moment that makes car owners be careful and make a decision regarding the installation of an additional part is the behavior of the amplifier during a head-on collision. The fact is that in handicraft production, the metal structure is welded to the car body, and therefore does not soften, but enhances the negative impact during an impact... As a result, the damage becomes truly catastrophic. To prevent this from happening, do not rush to introduce innovations if the characteristics of the vehicle do not provide for such an upgrade.
It is rather difficult to give unequivocal advice whether a car needs amplifiers for the rear bumper or the front one. This is a personal matter and depends on what the car enthusiast considers to be safety. Probably, this option for tuning the bumper is just another requirement of the automotive fashion. Nevertheless, large automakers still make serial beams to increase the rigidity of a part that is only nominally called a bumper. For example, cars of factories are equipped with amplifiers. Toyota, Renault, Ford, Nissan.
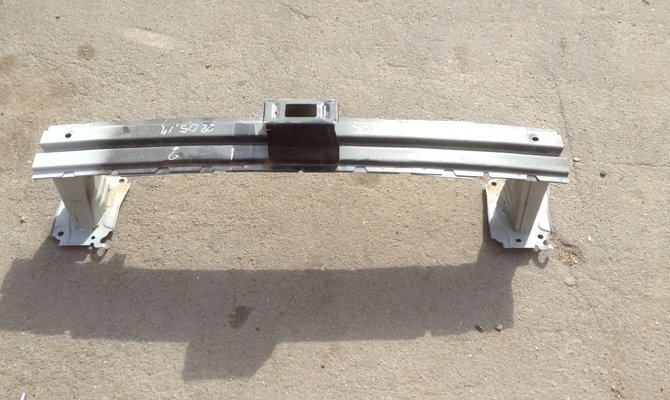
Standard beam for increased bumper stiffness
Naturally, the fastening to the body was also calculated by the designers. In the event of an accident, the bumper, due to the amplifier, either "dampens" the impact, or deforms, allowing minimal impact on the body and internal units.
Some car manufacturers install front and rear bumper reinforcements through shock absorbers to enhance the protective effect. If someone has the idea to, for example, build something similar on their Zhiguli 30 years ago, consider that simple copying, despite the best intentions, can be harmful. Any, even the smallest detail on the car is the fruit of the work of a large team of designers who performed calculations and tests, and its presence in the configuration is a justified necessity, and not a whim of this or that owner.

Installing the bumper reinforcement
Is it possible to repair this part? If the rear or front bumper reinforcement is not damaged too much (dent, slight deformation), then it is possible to fix it on the slipway. For more severe exposures, a complete replacement is recommended. The fact is that strength in places of metal deformation can no longer be expected: molecular bonds are broken, microcracks appear. The benefits of such an amplifier are minimal, practically zero.
heh, here half of the country drives on cuts and does not buzz, and you are worried about some kind of bumper amplifier)
but since you are worried, it means you are alive, it's already good)
let's have a discussion. and what is not a polytechnic - didn’t spoil the girls and didn’t drink cholet beer?)
what do you mean “wrong”? are there acceptable limits? strictly speaking, if you scratched the door, then also a replacement? yes, it will rust more strongly than with factory painting. but, I hope, when the door is scratched, the door does not change?
I understand that I am exaggerating, but it is only technically possible to feel the brink here, because they immediately quoted “taking into account the norms, rules and procedures for repairing vehicles established by vehicle manufacturers, certified repair technologies and economic feasibility“
the conclusion is simple that it, this detail, will not perform its function as if it will not perform its function - it is unmotivated, it is necessary to first describe the function, and only then determine the degree of loss of the ability to perform this function
The procedure is applicable to any car
Cracked bumper repair - Photo report.
This topic is for those who want to fix the bumper with their own hands. Cheap and reliable.
A piece of the bumper is broken off, and there are a bunch of cracks.
We remove from the car, twist the excess (In my case, the washer nozzle and the aluminum bumper amplifier)
If possible, we climb into the inner side of the bumper. A small piece is already sealed in the photo.
You will need a wire from an electrical cable 1-1.5 squares.We bend in such a way as to strengthen the cracked part.
Next, you need either a powerful soldering iron or a soldering iron made in 15 minutes heated by a gas torch.
We warm up and insert the wire into the bumper. We cut a new one.
The same procedure. We also go along the crack and solder the burst parts of the plastic.
Outside, we reinforce the missing piece of plastic with a mesh. And we also solder cracks, only more subtle than from the inside.
Next, apply a putty with fiberglass on 2 sides (main layer)
Grind with a coarse grinder 100 (you can use a grinder if you have one)
We apply again, already shaping and covering the grooves in the soldering points.
Then we apply a fine-grained putty and grind it with fine sandpaper.
And so we repeat until the surface is flat.
I didn't bother much, I just leveled it with 500-piece sandpaper, since I tinted the bumper with ordinary black paint. And for an ideal bumper you need to grind various scratches in many places. And then paint the whole thing entirely.
All this was done in 1 evening.
In the end, this is what happened:
Also a couple of pictures of the rear bumper. Only here I soldered the wire from the outside.
Often in the traffic flow you can find a car with a cracked or deformed buffer. What can you do, no one is safe from unsuccessful parking or a minor accident. However, this is not a reason to continue driving a car that has lost its "shiny" appearance - there is a practical experience of restoring the original state of this element.
The external plastic components are mainly made of thermoplastic plastics. The technology for restoring such products is based on welding, it is this technology that allows you to get rid of through cracks and even recreate broken fasteners. Actually, the procedure is not much more complicated than preparing and spray paint damaged area of the car body.
Some car enthusiasts assure us that we repair the bumper with our own hands using metal brackets. But the experienced car owner knows that like is treated like this, that is, repair plastic rods are used for soldering. Their composition, color and profile are different; the required core is selected according to the marking on the buffer.
Making the right choice means guaranteeing a high-quality repair, because the mismatch of materials will significantly reduce the life of the automotive element. To find out what the cracked bumper is made of, it is enough to carefully examine the inside of the part. Depending on the marking, the following conclusions are drawn:
- PP - polypropylene base.
- ABS (GF, PAG 6) are hard plastics.
- PUR - polyurethane.
Plastic welding requires high temperatures, for example, 400-450 ° C is suitable for propylene, and 500 ° C is necessary to restore an ABS structure. Many car owners will learn how to repair a bumper with their own hands in a video where craftsmen use an ordinary 100 W soldering iron.
You can also restore a damaged part using pieces from a bumper with a similar marking. They are cut into strips 8 mm wide for PUR, and 4-5 mm for polypropylene.
Almost any breakdowns are treated by welding, even broken parts are reanimated. However, no one canceled the economic feasibility of such work, because the restoration of numerous defects can hardly be called justified. The cost of a complete restoration and staining will be more expensive than a new buffer.
Certain tools are required to complete the repair. These can be both ordinary household appliances and professional tools. The ideal kit includes the following items:
- Orbital sander or sanding block.
- Grinding wheels of various grain sizes.
- Mini drill like Dremel or drill.
- Clamps and rubber spatula.
- Soldering iron and hair dryer.
- Metallic tape.
Of the materials for restoring a cracked buffer, you may need:
- Putty and primer.
- Brass mesh for crack reinforcement.
- A can of paint or a can of paint.
- Plastic repair rods of the required configuration and composition.
The damaged part must be dismantled in order to eliminate, firstly, excessive stress in the crack area. Those who have already done such work will say that now we clean the bumper and only then repair it with our own hands.
The cracked parts fit together. For reliability, they are fixed with metal tape from the outside of the part. If the breaks are quite significant, then clamps will be needed to clamp the edges of the cracks. Their number depends on the complexity of the repair.
When restoring PP-based parts, the reinforcing mesh is not used. The process begins with the fact that a nozzle with a nozzle with a diameter of 5-7 mm is installed on the hair dryer. In the future, work is carried out according to the following points:
- On the inside of the buffer along the crack joint, use a Dremel mini-drill to make a groove for the plastic rod.
- Using a hair dryer, melt and place the repair rod into the prepared groove.
- Clean the front part of the bumper with an orbital sander with P240 attachment and repeat the welding procedure similarly to the operation on the inside.
- Grind the cooled seam from the outside with a nozzle with the same grit P240, then remove dust from the surface.
- Even out irregularities with a special putty for plastic, try to keep the layer as small as possible.
- Dilute the primer with solvent 3: 1 and apply two coats to the degreased surface. Drying time for the first layer is 15 minutes.
- Apply a developing layer in a contrasting color, followed by sanding with a disc or sandpaper with grit P800 and P1000.
- Eliminate the detected defects with a nitro putty followed by sanding with P1000 sandpaper.
- Remove dust with a damp cloth and degrease the part, then paint plastic decorative paint with overlapping borders 50-100 mm. Apply the paint in 3-4 coats with intermediate drying cycles.
Anyone who is interested in how to properly repair a bumper in a video with their own hands should take into account an important detail. 30-40 minutes after applying the last layer of paint, the part should be varnished. Thus, we get a flawless appearance of the repaired part. Do not forget to follow a few simple rules:
- You should try to apply a minimum layer of putty.
- Take a temporary pause for complete hardening of the putty layer.
- To process the putty area with a grinding wheel or sandpaper with grit P800, and then - P1000.
- It is desirable to apply a developing layer of primer.
In the case of a polyurethane buffer, the preparatory stage in the form of grooving work is excluded. A brass reinforcing mesh is applied to the crack; steel is not recommended for use, because it is prone to corrosion. Alternatively, stapling staples can be used every 10-20 mm. They are recessed into the body of the part across the seam, it is imperative to make sure that the bracket does not go through the part.
Further, the repair technology does not differ from the restoration of a polypropylene part. Wire mesh or staplers should be sunk into the plastic. Only after that, the seam is filled with repair plastic and soldered from the opposite side. Some important points of technology should be taken into account:
- It is necessary to solder the mesh or staples carefully so as not to overheat the plastic, otherwise it may deform from the opposite side.
- For a complete DIY repair of a polyurethane bumper, the width of the reinforcing mesh should be 15-20 mm.
- It is better to press in the mesh or staples with a flat object.
- If the legs of the staples pierce the plastic through and through, then they should be shortened using side cutters.
- For the convenience of working with metal elements, you can use tweezers.
- To prevent the new enamel from peeling off, it is necessary to grind the paint over the entire plane of the part.
Puttying and painting are performed in the same way as described above - according to the traditional scheme. Repair work on the restoration of the buffer can be combined with painting the car , so the consumption of materials will be more rational. It is important to determine in advance the feasibility of carrying out restoration work. If there are significant costs in the future, then it is better to buy a new part.
The most dangerous time of the year for plastic body parts is winter. After all, slippery areas do not leave enough room for maneuvers and sometimes you have to ram drifts or something harder. In this case, the first affected area of the vehicle is the plastic bumper.
You shouldn't run to the nearest auto shop and buy a new expensive part. You can do bumper repairs with your own hands in your personal garage. The result will be decent, and the savings can be spent on something more enjoyable.
There are three unspoken classifications of damage to bumpers:
- A network of scratches. The option is considered the easiest, since it requires the least amount of investment in time and other resources. Often the work consists in sanding the damaged surface, treating it with a specialized spray to improve the adhesion properties, and then applying the paint layer.
- Chips, dents and cracks. Alignment is carried out using liquid plastic. Irregularities can also be tidied up with a putty. To eliminate such defects, an additional tool will be needed.
- Split bumper. This problem is solved on an individual basis. Repair of a car bumper in case of splits is carried out based on the degree of damage to the product.
Before starting work, you will need to stock up on the necessary tools.
It is unlikely that you can do without such a minimal list:
- soldering iron 40-60 W;
- tweezers with long thin legs;
- medium power construction hair dryer;
- orbital sander;
- coarse and fine-grained grinding wheels;
- Consumables.
For high-quality processing of a broken or damaged bumper, it is advisable to carry out repairs on the removed product.
Dismantling does not take much time, but it will save it during work. This relieves unnecessary stress in cracks at the attachment points to the car body.
It is advisable to wash the removed bumper from dirt and let it dry for further work. Further, the breakaway parts can be attached with adhesive tape by sticking the tape on the outside of the bumper. After that, you can heat up the soldering iron and start repairing the plastic bumper with your own hands.
The soldering of the fragments is carried out from the inside of the bumper. It is not visible from the outside, so you can conduct training on pairing elements. Significant flaws will be hidden from outsiders. During work from the back, you can feel the material, its reaction to a heated soldering iron and behavior in a softened state.
It is desirable to work smoothly, without a long delay in one place and abrupt transitions between the sections to be sealed. A perfect seam looks even, and the material does not deform in other areas that are not damaged.
In order for the soldering to stand for a long time without deformation, it is advisable to secure the additionally sealed cleavage line with metal staples using a furniture stapler.
The legs of the brackets must be selected so that they do not protrude from the back of the bumper when reinforcing.
To avoid burns, you must use tweezers.
The staples should be installed at a distance of up to 2 cm. All emerging cracks should be soldered. This will prevent new splits from occurring in the place of kinks during driving and vibration.
The staples must be closed against further corrosion. To do this, you will need to pull off a little plastic from adjacent areas and completely cover the metal parts. After carrying out such preliminary work, the form should return to its previous state.
We put a circle with P240 grain marking on the grinder. With its help we clean paint, varnish, irregularities and roughness. After that, we carry out soldering on the front side of the bumper, but only without using reinforcing brackets. We seal the cracks and cavities with too much plastic.
After cooling all surfaces with a grinder, we grind the seam. You should not seek to remove all the scuffs; it is enough to prepare the surface in a rough version, removing as much as possible irregularities and smoothing the protrusions. The soldering iron can penetrate deeply into the body of the bumper, you do not need to get carried away and reduce the thickness too much, since you need to repair the bumper carefully, leaving it with the maximum possible strength characteristics.
Sanding will electrify the surface of the bumper. After that, dust particles, villi and other small debris stick to it. You can get rid of this with compressed air. You can also wipe the surface with a clean cloth.
Working with an industrial hairdryer, leveling the surface, you need to know that from significant overheating, plastic can leak, the fibers will lose their original shape. Having finished with the alignment, you need to remove the caverns by treating the surface with a special putty on plastic.
The material is applied only to level out the formed pits, and the excess part must be wiped off. Having given time to the putty to polymerize, having received a solid material, we process the surface again with a grinder.
After finishing, all dust must be removed from the surface. Now you can apply the primer to the plastic. We dilute the mixture, guided by the recommendations from the instructions for use. Apply two layers in order of 15 minutes. Apply a layer of development from a spray can on the treated area.
This procedure is necessary to indicate pits, protrusions and other irregularities for grinding. After grinding, the development on the convex places will be removed, and in the depressions it will remain. At this stage, a nitro putty will help to get a flat surface. It is applied to cleaned and primed surfaces.
When the nitro putty hardening process is over, the surface is polished.
Now, for better adhesion of the enamel, a base coat can be applied. It binds plastic and paint at the molecular level.
After the base, you can enamel at least two layers, allowing the previous one to dry.
Then varnish is applied. The dried product can be neatly mounted on the vehicle. Only professionals will be able to notice traces of repair after such processing, and then only after a thorough examination.
Bumpers of modern cars are made mainly of plastic, they are damaged in a minor accident and collision is not an obstacle.
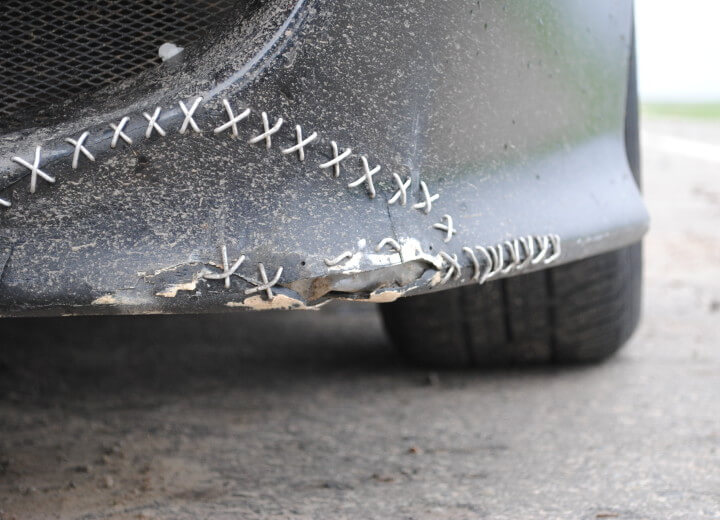
As you know, there are front and rear bumpers, and the front bumper (PB) is damaged much more often than the rear (ZB). PB needs repair if:
- the paintwork is damaged;
- scratches appear on the plastic element;
- bumper cracks have formed as a result of a collision with an obstacle or a minor accident.
If the impact to the front or rear of the car is severe, the bumper is most likely beyond repair. But in specialized car services, they often undertake the repair of a badly broken plastic bumper. The whole question is whether the restoration is worth the money, in some cases it is easier and cheaper to buy a new part.
The cost of repairing a PB or ST can be different, it depends on the level of the car service, the degree of damage to the part, the complexity of restoration. For example, in Moscow, the restoration of a bumper can cost from 2,500 rubles, and painting of one element will also cost from 5,000 rubles. There are auto repair shops that promise to repair the bumper from 500 rubles, to carry out repairs within one or two hours.Advertising is not worth it, most likely, car owners are deceived, or the repairs are performed here of poor quality.
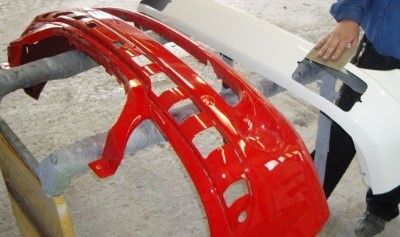
Repair of a front or rear bumper can be of varying complexity, there are main types of work that are carried out with body elements:
- sealing cracks;
- restoration of plastic fragments;
- repair of dents;
- preparation for painting (cleaning, sanding);
- primer;
- painting;
- restoration, repair of fasteners.
Restoring a plastic bumper requires care and accuracy, sufficient experience, and only a qualified master can do the job with high quality.
Repair of the PB becomes profitable if the bumper itself is rare, installed on an expensive car, on which the car owner does not want to install a cheap “non-original”. There are also tuning bumpers - they are expensive, and the industry does not produce non-original spare parts of this kind.
If the car is budgetary, and the owner of the car is "with hands", you can try to repair the PB yourself. Much depends on the degree of damage; you can also restore a slightly damaged body part with your own hands. Repair of the front bumper (with a crack) is carried out with the removal of the body part from the car, and to seal the crack, you need to connect the edges of the damaged area - make a reliable lock.
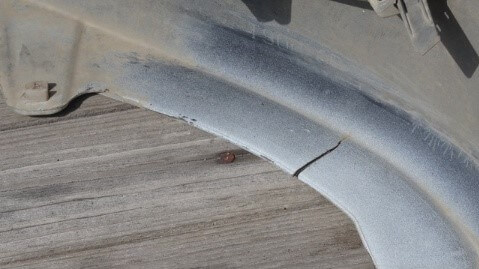
There are special repair kits on sale, for example, from 3M. The FPRM kit includes:
- two components of epoxy material (glue);
- reinforcing mesh;
- special tape.
We prepare the bumper for gluing as follows:
- the damaged area to be repaired is thoroughly washed with soapy water, we give time to the plastic to dry thoroughly;
- we grind the repaired area, remove the paintwork from it. We clean the paint so that adhesive tape can be glued to the area freed from it;
- we grind the edges of the crack at an angle of 45 degrees, they should be in the form of wedges. We process the surface first from the inside, and then from the outside, for this we use a grinder with a cleaning disc;
- we clean the treated surface with the composition 3M 08985, wait for the complete evaporation of the degreaser;
- we glue the scotch tape on the outside of the glued area;
- from the inside, we fix the reinforcing mesh;
- mix the epoxy components in a one-to-one ratio;
- apply the prepared composition on the reinforcing mesh, with a spatula, push it inward, it must close the crack;
- heat the crack with infrared drying (6-8 minutes). If there is no special drying device, let the glue dry at room temperature for about 30 minutes;
- remove the tape, degrease, process the front part with an adhesion activator;
- we prepare the composition for the front side;
- apply glue on the outside of the crack;
- let the parts dry again;
- we process the dried surface with abrasive wheels, first with a coarser abrasive (180), then with fine "sandpaper" (240, at the end of processing - 400);
- blow through the repaired area with compressed air, clean it with a compound from the set 3M 08985, wipe it with a dry cloth. The bumper is now ready for painting.
Damage to the bumper can be different - in one case it is just a crack, in the other, pieces of plastic fly off on impact. To seal a plastic element, you will need:
- construction hair dryer;
- angle grinder;
- pliers;
- screwdriver;
- soldering iron;
- sandpaper;
- spatulas.
The soldering iron must be powerful enough, preferably at least 100 watts.
If the pieces of the bumper are broken off and lost, initially we modify the damaged areas, give them a rectangular or triangular shape.
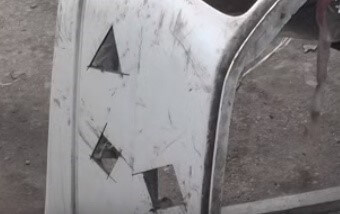
We carry out the work in the following order:
- from the inside and outside around the damage, we process the entire surface with a cleaning wheel - we clean off the paint;
- we remove all cracks in the paint to the base (to plastic);
- we prepare a nozzle for a hair dryer, it is needed so that hot air can be directed to the damaged area;
- we join the torn seam, melt and solder the pieces with a soldering iron. We grab the plastic with a soldering iron in several places - it is also necessary for the plastic to become homogeneous;
- we put on the nozzle on the hair dryer, with a hairdryer we evenly warm the plastic on both sides. It is important to keep an eye on the hair dryer, with a narrow nozzle it can overheat,
- after warming up, align the edges of the plastic;
- we solder the seam with a soldering iron thoroughly.
If you need to solder pieces of missing plastic to the bumper, it is advisable to take plastic of the same type, the marking is usually indicated on the inside of the plastic parts.
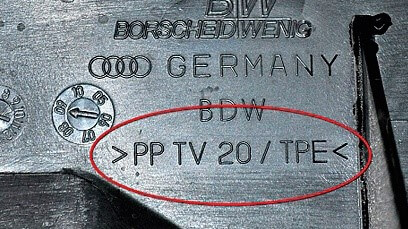
To solder the missing pieces into the bumper, proceed as follows:
- we take paper, apply it to the bumper, draw a circle around the damaged contour;
- we transfer the drawing from paper to plastic, cut out the necessary piece;
- install the cut-out piece in the bumper flush, solder along the edges with a soldering iron;
- So that the piece to be soldered does not move, we first grab it with a soldering iron from all sides.
If you cannot cut the desired piece to the exact size, you can cut off the plastic with a margin and solder it on the inside of the bumper. But this option is worse, since when soldering from the front part, a dimple is formed around the patch.
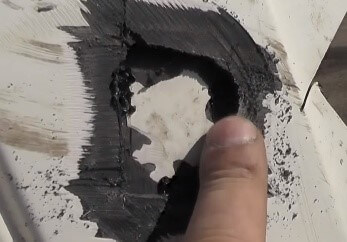
The surface can be leveled in two ways:
- melt everything outside with plastic;
- apply a layer of putty to the surface, then process it.
After soldering and applying putty, we process the surface, prime the bumper and paint.
![]() |
Video (click to play). |