In detail: do-it-yourself repair of a vibration pump from a real master for the site my.housecope.com.
Submersible pumping equipment of models like Brook and Typhoon, Neptune and Malysh, Harvest and Chestnut, Bosna and Dzherelce, Strumok and Aquarius are popular among the inhabitants of the countryside. Comparatively (with foreign manufacturers), the low cost of domestically produced pressure equipment and a high degree of reliability (according to reviews) are attractive for owners of wells.
No less than reliability in terms of performance and price, summer residents are impressed by the possibility of self-repair and maintenance of pressure equipment. After all, the ability to quickly solve a problem with water on the site due to a pump breakdown without the involvement of third-party specialists is always a plus. And the man and the saved nerves, money and time of his household.
By and large, the design of all pumping equipment for private use is the same. The pump consists of:
- a case in which there is a hole for water intake;
- an electromagnet (dynamo);
- vibrator (electric motor).
What does a vibrating pump consist of?
For deep wells, pumps with an upper water intake hole are used, for shallow wells - with a bottom or side water intake. However, the lower water intake suffers from periodic captures of bottom impurities in the water from the well.
to the menu ↑
Since all vibration pumps operate on the principle of inertia, all work is reduced to creating vibrations in the fluid, which is driven by the diaphragm membrane and creates the difference between internal and external pressure. The difference in pressure created is responsible for pumping water.
![]() |
Video (click to play). |
Bending the diaphragm creates vibration. The more oscillatory movements the diaphragm creates, the more intensive the cooling of the motor with water should be. Therefore, it is forbidden to use pressure equipment without entering water.
Dynamka (as the people call it an electromagnet) is:
- steel core;
- two coils of enamelled copper wire.
To install the magnet, you need to fix the speaker and coils inside the case. To do this, we fill everything with epoxy compound, which works simultaneously as insulation and removes excess heat from the coils to the case for speedy cooling.
The composition of the compound necessarily contains epoxy, plus a hardener and a plasticizer (with the addition of quartz sand). Quartz in this case simply serves as an additional heat conductor.
The electric motor consists of an armature with a rod, on which a spring for shock absorption and a piston (rubber) are installed. The better the quality of the rubber from which the spring and piston are made, the more reliable and economical the pump.
The direction of the stem is provided by a rubber diaphragm. It divides the two working parts of the apparatus - (electrics and hydraulics) and is attached to the stem for a distance coupling. The most vulnerable place in the design of any pump is the rubber valve that closes the water intake openings.
The vibration of the diaphragm occurs due to the fact that when current enters the motor, the armature begins to be attracted to the magnet and is thrown back by the shock absorber at the moment of polarity reversal (polarity reversal).
The higher the frequency of the current, the more oscillations per second the diaphragm makes. Moreover, the piston also emits vibration of the same frequency.
The hydraulic chamber of the pump is the space occupied by the valve and piston. The piston vibrates, the water springs due to the air dissolved and not dissolved in the water, then contracting, then unclenching, and its excess is squeezed out of the hydraulic chamber into the pressure pipe, and then into the hose.The constant maximum amount of working fluid in the pressure vessel is provided by a valve that lets in and does not allow water to flow back.
Vibrating pump with bottom intake
The design with top water intake and bottom electric drive is a classic in the vibratory pump line-up. In them, the engine is better cooled, and with open suction openings, it can work without interruption for up to seven hours. Sometimes the kit contains an overheating sensor (thermal relay).
By the way, pay attention to the material from which the fastening cable is made. It is better that it was made of nylon. This cable, unlike steel, does not rub the lugs of the housing and provides additional protection in the event of damage to the current cable.
But, before proceeding to repair vibration pumps with your own hands, you should pay attention to two more things:
- the cross-section of the cable with the euro plug should not be less than the international standard 2x0.75 mm;
- hose with an internal passage diameter of at least 1.9 cm.
The ability to self-diagnose and repair will always come in handy. Therefore, whatever the reason for the failure of the pressure equipment (breakage of traction, short circuit or breakthrough of the valve), the pump will have to be disassembled first to inspect internal problems.
Unscrew the bolts that hold the body together, inspect the corrosion, the tightly seated bolts can be cut off with a grinder. Beat off the compound. Inspect the windings on the coils and clean all moving parts. The power coil, if it needs to be replaced, can be simply knocked out of the case. Use a tester to check the power cable, if everything is normal, you can put it back together.
Make sure that the water flow holes are well aligned with the rubber gasket. Tighten the mounting bolts so that the pump operates within the usual noise and vibration range.
to the menu ↑
If it was not possible to limit ourselves to the usual inspection and prevention, and the reason is in the carbonization of the cable or overheating of the case, lack of pressure or increased vibration, then you can repair your vibration pump using methods that are universal for any model of units.
As practice shows, a replaced hose or cable can easily reduce the pressure or the level of overheating. Replacing or repairing the magnet will help reduce vibration. Now, in more detail about each of the options for the emergence of problems.
to the menu ↑
The humming of the pump with a low pressure or lack of water can be caused by three possible reasons:
- the nuts of the rod attached to the shock absorber are loose;
- a worn-out valve burst;
- the stock broke.
Assembling the Vibratory Pump Trickle
Here only the problem cannot be solved if the stem is broken or deformed. There is nothing to replace it with. If the problem is in the nuts, tighten them all the way and fix the upper one well. It is from this nut that all the loosening goes. If you had to cut the bolts, replace them with the hex capscrews. About "replace the valve", I hope, they themselves understood - we just change it.
to the menu ↑
The cable is carbonized or knocks out plugs. There are two options: either the anchor winding has burned out, or the tester will show a malfunction of the cable itself. We change what is needed and should work.
If the cable cannot be changed, because the drive is filled with compound, then the wire will have to be extended by twisting.
to the menu ↑
Increased vibration or overheating occurs due to delamination of the magnetic part of the unit. The source of the problem is that the pump was running without water. How to reduce vibration?
You need to get out the magnet, cut through the grid of grooves with a grinder 2 millimeters deep and make the same grooves inside the case. We put the magnet on glue and sealant, let it dry and only after that we start assembling.
to the menu ↑
If the pump is operating normally, but the head could be clearly higher, then the reason is low pressure. To increase the pressure (if the reason is the vibrator - the gap is too small), you can use the washers mounted on it (up to 11 pieces, depending on the model of the device).
The main thing, when repairing a pump with your own hands, is to remember that replacement and adjustment of all its parts is carried out only when the device is completely de-energized.
to the menu ↑
Vibration pumps have a long history, so there are a huge number of their modifications. Each manufacturer introduces its own characteristics into the design of the product, but the time and operating conditions still lead to inevitable breakdown or complete failure.
The variety of breakdowns is great, but there are only a few major ones that significantly affect the quality and evenness of the pump. Having understood the principles of operation and the device, you can do a simple repair of a vibration pump with your own hands.
Vibration pumps are weaker than centrifugal pumps, less reliable, but have their positive aspects. They are much cheaper in cost and maintenance, and are easier to replace and repair. And they are also less selective in the quality of water and its content, therefore they have found their application in summer cottages and private lands for pumping water from a well and pumping it over short distances.
To perform any repair of a vibration pump, you need to know and navigate in its device. After all, knowing the principles of operation, it is possible to determine with great accuracy the causes of a malfunction only by the sound of work or by the actions performed.
What does a vibrating pump consist of?
The submersible pump with vibrating principle of operation is completed with the following elements:
- shockproof sealed housing;
- an electric motor driving the pump;
- working piston;
- high power electromagnet;
- additional replaceable structural elements: shock absorber, diaphragm, etc.
The operation of the electric pump is based on the action of an electromagnetic field, with the help of which the working piston is driven. Due to the pressure difference created by it, water enters the working chamber and is transferred to the connections of the branch pipe or hose of the water supply system.
to the menu ↑
Very often, submersible vibration pumps stop working, having a minor breakdown, which can be eliminated independently, and, sometimes, very quickly, without the intervention of paid specialists. Therefore, you should know how to determine the malfunction and how your own electrical appliance behaves at the same time.
A characteristic feature of the repair of the device is that after replacing the damaged elements, additional adjustment is required. For example, after replacing a rubber valve system, the pump does not deliver the rated power or even refuses to pump at all. In this case, a simple adjustment of the valves helps, setting them in the correct position, determining the correctness of their opening and closing.
to the menu ↑
Before the user is filled with decisiveness to disassemble a non-working product, a number of simple manipulations should be performed to establish a preliminary diagnosis:
- fix the pump in a container with water by releasing the outgoing pipe. Turning on the device in the power supply, check the voltage level, which should be in the range from 200 to 240 V.
- under normal conditions, turn off the pump and drain the water. Then blow with your mouth into the outlet. A correctly adjusted device lends itself to blowing, but with strong blowing it locks with the stroke of the working piston inside. Conversely, with the intake of air, the latter must pass freely inside.
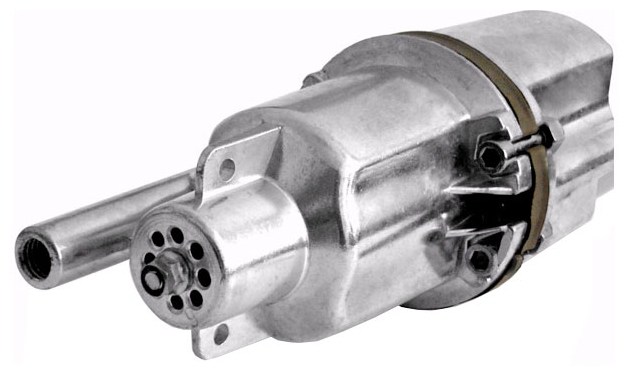
Vibrating pump with bottom intake
With an incorrect setting, when air is not blown through the pump, but passes through the suction, the pump can operate at a reduced voltage of less than 200 V.
Before starting active steps to disassemble the pump casing, you should leave marks at the joints for correct assembly in the future.
The principle of operation of pumping equipment dictates the control of three important parameters of reassembly in the specified order:
- Axial alignment of piston and seat.Sliding the inlet nozzle over the gasket makes it very difficult to achieve this when assembling the pump, but misalignment will prevent the pump from working in principle.
- The piston should be at some distance from its seat. The size of this gap should not exceed 0.5 mm, but be greater than 0. The gap can be adjusted using shims. The correct distance allows air to pass into the water outlet, and with a greater blowing force, the piston closes the channel.
- It is necessary to observe the parallelism of the piston disc with its seat - their axes must also be parallel.
- large clearance between piston sleeve and rod. Such a problem can not only affect the regulation, but also cause vibration of the operating unit. How to reduce a large gap? It is enough to replace either the bushing or the stem, and the popular method is to seal the stem with an improvised material, for example, foil.
- the stem is bent. In this case, the problem is unlikely to be corrected, but, perhaps, parallelism will be achieved by expanding the gasket to 180 0.
A correctly replaced structural element and a properly assembled submerged electric pump produces a jet of at least 30 cm in height and operates without interruption with a voltage of up to 240 V. Decreasing the voltage changes the sound of the pump and can reduce performance.
to the menu ↑
It greatly facilitates disassembly by placing the unit in a vice. Clamping the body protrusions with jaws, the tie bolts will give in faster, but they need to be loosened in turn and little by little. The collection after repair is carried out in the same way.
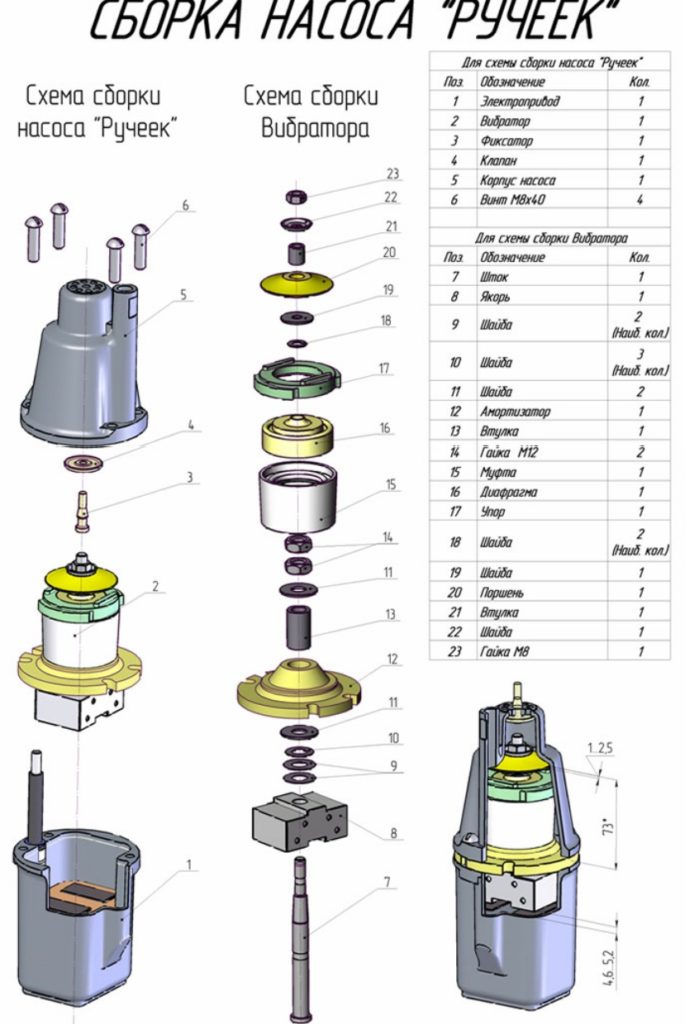
Assembling the Vibratory Pump Trickle
If the pump has been submerged for a long time, most likely, the tie bolts will not give way quickly - you should apply a penetrating lubricant and make slotted slots in the bolt heads. As a last resort, you should carefully cut off the bolt heads to disconnect the body parts of the device.
to the menu ↑
Let us consider in more detail the symptoms of malfunction of vibration pumps, how to identify and eliminate them with our own hands.
to the menu ↑
There may be several reasons for this pump behavior:
- The fastening nuts located on top of the shock absorber are loose. When unscrewing the nuts, the shock absorber can move slightly in relation to the rod and the movement of the rod will be idle. To eliminate the problem in the operation of the pump, fix the shock absorber, tighten the nuts to the stop and lock them in order to avoid repetition in the future.
- The rubber valve is mechanically damaged. The reason may be wear as a result of long work or the negative impact of abrasive particles pumped with water, or its banal breakthrough. The solution to this situation is to replace the worn out part.
- The worst variant of the resulting malfunction is a stem break. Repair or replacement of a rod with its deformations is practically impossible. With this development in business, buying a new pump will be the best way out of the situation.
When the pump is connected to the mains, the cable connection heats up and charred, knocks out the electrical plugs, the circuit breaker turns off.
Dismantling the vibration pump
This result is often due to two reasons:
- Defective power cable. To check, a tester is used, which will indicate the integrity of the connected wires and, accordingly, whether it is the reason for the operation of the electrical protection. Replacing the pump cable is possible, but not on all models. In some cases, the power cable is filled with an insulating compound and it is not possible to change it.
- Burnt armature winding. Repairing the winding requires special skills and knowledge, so it is impractical for an ordinary user to replace it. But nevertheless, its repair is possible by rewinding or by replacing it with a new one.
When the device is turned on, it must always be in the water, because the pumped liquid removes the heat it generates. In the absence of a cooler, the pump suddenly begins to heat up, which can lead to irreversible damage. The pump body expands and a special filling lags behind it, which holds the electromagnet. The "clanging" of the electromagnet becomes the basis of the vibration process. If the dry operation lasts long enough, then complete detachment of the magnet will inevitably occur and the piston will not be able to move.
A breakdown of this type is one of the most difficult, and doing it yourself requires a lot of patience.
First, the user disassembles the pump, separating the electrical part of the product. Then, tapping on the body, for sure, determines the looseness of the electromagnet. After removing the pump from the housing shell, it is necessary to cut small grooves in a chaotic order with a small grinder on the inner surface of the housing and on the unit itself.
It is recommended to replace the screws with new ones during assembly.
After the work done, it is necessary to cover the case with window sealant or high-quality strong glue and press in an electromagnet. After the structure has dried, it can be reassembled.
A thermostat built into the housing helps to avoid damage, which will cut off the power supply to the pump in case of strong heating or short circuit. Models equipped with such protection are more expensive, but last longer.
to the menu ↑
The pump operates in this mode due to the small clearance between the piston and its seat, unless there is another reason from the above.
An additional washer restores the work on the piston rod. Using washers, you can reduce or increase performance within the declared characteristics.
It should also be remembered that the pumping equipment is electrical and compliance with safety conditions with it is imperative.
to the menu ↑
Submersible vibration is very popular among gardeners and summer residents. pumps like "Kid", and other modifications that work on the same principle. They are inexpensive, productive, create a sufficiently high pressure and have a high pumpability (i.e., they can supply water over a sufficiently long distance). Unfortunately, these pumps are not very reliable. Moreover, their breakdowns are very diverse. Where the valves leak, where the thrust is cut off, problems with the pump winding, power magnet, short circuit or open circuit. There are quite a few simple malfunctions that are easily eliminated, but after repairs, for example, replacing rubber valves, the pump does not pump or pumps very weakly. Here you still need to correctly adjust and assemble the pump. To understand how to properly adjust the pump, we will consider the principle of operation and the important points of correct adjustment.
Working principle and design
Vibrating Submersible Pumps are inertial pumps. The operation of inertial pumps is based on the excitation of oscillatory processes in a liquid that contribute to its movement.
Design of all vibration pumps is of the same type. The pump consists of an electromagnet, a vibrator and a pump body.
The electromagnet consists of a U-shaped core assembled from sheet electrical steel and two coils wound with an enamelled copper wire.
The core with the coils is installed in the housing and sealed with epoxy. The compound serves to fix the core with coils in the housing, serves as an insulating material and provides heat removal from the coils to the housing, through which they are cooled.
The compound is prepared from epoxy resin, plasticizer, hardener and quartz sand, which improves thermal conductivity.
The vibrator consists of an anchor with a rod pressed into it. The rod has a rubber spring called a shock absorber. The parameters of the pump and its efficiency depend on the manufacturing quality of the shock absorber.
In the design of "Rucheyka" and "Baby", only natural rubber shock absorbers are used, which undergoes vulcanization for a long time.This ensures stable pump parameters.
A rubber diaphragm, installed at an appropriate distance from the shock absorber through a distance coupling, serves as an additional support for the rod and provides its direction. The diaphragm also separates the pressurized electric and hydraulic chambers. The stop provides compression and fixation of the diaphragm in the pump housing.
A rubber piston is attached to the end of the rod.
Finally, the final assembly is the pump casing with a valve that closes the inlets. There is also a 0.6-0.8 mm gap between the valve and the body, which ensures free flow of liquid in the absence of pressure.
The valve is also made of high quality rubber. It is the most vulnerable element in the pump and is the first to fail.
Vibrating pump great for irrigation systems, the construction of which was considered earlier.
How does a vibration pump work?
When the pump is connected to an electrical network with a current frequency of 50 Hz, the armature is attracted to the magnet. When the poles are magnetized, every half period, the shock absorber throws the armature back. That is, in one period of the current wave, for those who know electrical engineering, the armature is attracted 2 times. Accordingly, per second at a frequency of 50 Hz, the armature is attracted 100 times. The piston located on the same rod with the armature vibrates with the same frequency.
The volume in the pump casing, limited by the piston and the valve, forms the hydraulic chamber. Since the water pumped by the pumps is a two-component mixture containing dissolved and undissolved air, it has some elasticity - it is springy under mechanical action, which is what happens in the hydraulic chamber when the piston vibrates.
Water, like a spring, compresses and expands, and its surplus is pushed into the discharge pipe - in this way the pump pumps water. In this case, the valve allows water to enter and restricts the exit of water through the suction openings.
Pump modifications
Pump "Trickle" produced by JSC "Livgidromash" has a classic layout, i.e. the suction ports are at the top and the motor is at the bottom. This design has better cooling, eliminates the capture of impurities from the bottom. The pump can operate for a long time in a submerged state with the suction openings open to the air.
In this condition, according to international standards, the pump must work for 7 hours. Top suction pumps pass this test.
In critical cases, it is still worth purchasing pumps with a thermal relay, which will turn off the pump when it overheats. Overheating can occur in a limited amount or when the voltage rises above the permissible level. A pump with a thermostat will cost more.
Bavlenskiy plant "Electrodvigatel" satisfying the demand of discerning consumers, mastered the production of pumps "Kid" in several versions:
- "Kid" and "Kid K" - with the bottom arrangement of the suction holes (K - with thermal relay);
- "Kid M" - with the upper arrangement of the suction holes;
- "Malysh-3" - can be used in 3-inch wells, ie. wells equipped with a casing pipe with an inner diameter of 80 mm.
It is advisable to purchase pumps with a bottom arrangement of suction openings with a thermostat. Otherwise, they must not be left unattended. The popular opinion about the advantage of pumps with a lower water intake is that they can pump water from a shallower reservoir is controversial. The pump with top water intake can be positioned horizontally and will work perfectly.
The pumps must be equipped with a nylon cable for mounting and securing the pump. The nylon cable is not conductive and excludes electric shock in case of insulation breakdown. The use of a steel cable for securing leads to chafing of the lugs in the pump housing.
Although domestic pumps are produced according to the II class of protection against electric shock (- class II sign) and the insulation strength is tested with a voltage of 3750 V, it is better not to touch the electric pump connected to the network and not tempt fate.
If the wiring is equipped with grounding, then it is better to purchase pumps according to the 1st protection class, i.e. with euro plug. But these pumps are also more expensive.
PAY ATTENTION to fakes, when the pump is equipped with a Euro plug, and the wire is two-core, and even with a cross-section of 2x0.5mm, instead of the minimum allowable according to the international standard 2x0.75 mm.
Do not equip pumps with hoses with an internal bore less than 19 mm (3/4 ”). This leads to overloading of the pump and loss of performance.
Information on the parameters of vibration pumps from different manufacturers, indicated on the plates and in advertisements, is very contradictory.
Most domestic pumps are marked with a nominal head of 40 m at a nominal flow of -0.12 l / s (or 0.43 m3 / h).
On imported (Chinese) pumps, the maximum head is marked from 60 to 80 m. This is the head when the supply is completely shut off. In fact, all these pumps with a head of 40 m pump much less than the "Trickle" or "Malysh" pumps.
The maximum flow determined when vibration pumps are operating without pressure, depending on the adjustment, ranges from 1 to 1.5 m3 / h.
The power consumed by the pumps is indicated in the range from 180 to 300 W. In fact, the pumps adjusted to the rated parameters consume power from 190 to 220 W in the pressure range from 1 to 40 m. With increasing voltage, productivity, current and power increase. When the voltage is reduced to 200 V, performance is reduced by 25%. Thus, vibrating pumps can operate with voltage fluctuations inherent in rural areas and suburban areas.
The immersion depth indicated in the marking means to what level under the water layer the pump can submerge, in this case - 3 m.
Although the pump casing can withstand significantly higher pressure, they stopped at 3 meters. This is enough for the Bavlensk "Babies" and the Livensk "Brooks". If the pump is drowned deeper (up to 5-7 meters), there will be no problems.
During a short operation without immersion in water, the pump heats up and the aluminum housing expands out of proportion to the compound (epoxy filling of the magnet) and due to the lack of plasticity in the latter, the filling is detached from the pump housing. the situation is greatly aggravated by an increase in vibration during operation without water at all (during pumping out dry .. as a result, complete detachment of the magnet and the absence of a gap between the vibration piston and the magnet - no movement of the piston.
Treatment is simply impossible. it was performed in a car service on the occasion of being there
- first of all, we separate the electrical part (disassemble the vibration pump) by tapping with a hammer on the body, we are convinced that there is no fastening (the sound does not immediately feel the solidity of the contents) of the magnet .. we take it out of the body, make longitudinal and transverse grooves on it with a small grinder (depth less than 2- x millimeters), we make such grooves inside the case in a chaotic manner, then coat it with a thin layer of "glass" sealant (the one with which glasses are glued into foreign cars) - it is very durable and strong - ordinary sealants are up to it like the moon !! and press the magnet into the case using a press with a force of about 250-300 kilograms - (with less do not push in because of the viscosity of the sealant) I admit that instead of the sealant you can use some kind of adhesive, but I was at the auto service
hold until solidified and assemble in the reverse order ..
- First and foremost, if the valve and the piston are in good condition, this is the gap between the electromagnets of the coils and the piston, the gap should be 4-5 mm. If the gap is less, the coils will break if more the motor overheats.It is calculated as the difference between the depth of drowning of the iron of the coils in the body and the size of the protrusion of the iron of the piston above the rubberized flange-spring.
- The second valve should play freely on the stand, if you try to blow from the side of the water intake, the air should flow freely in both directions. The valve must not be damaged! It is advisable to unlock the rack from the outside with two nuts. This completes the valve.
- The third is the piston. It should also be free of mechanical damage and shape distortion, and be quite elastic. Rivet the nut with which it is fixed on the sleeve.
All this turned out to be very good, and the question lurked, why is it buzzing and not pumping? It turned out that inside the piston block, its sleeve (on which both the piston and part of the iron of the electromagnet sit) is screwed with a nut to a rubberized flange (such as a membrane-spring), and is disengaged with another nut. So, these two nuts completely unscrewed (((. In order to see this, it was only necessary to disassemble this unit, removing the piston, removing the gap adjustment washers, remove the thrust ring and pull off the rubber membrane (from the piston side!). Having removed the aluminum cylinder, firmly clamp the piston sleeve to the rubberized flange-spring, uncouple it, and collect everything back. We measure the gap, if it goes beyond 4-5 mm, then this sleeve has washers 0.5 mm thick, adding removing them from one side, we can change the gap in any direction.
We collect our happiness, special attention should be paid to the correct installation of the cover - the pipe through which the water comes out of the motor should be on the same side as the hole on the rubberized flange-spring))). We tighten, more precisely, we twist (collect) our miracle, and check. If the jet hits at least a meter (by immersing the motor in a full bucket of water, and plugging it into the mains), then everything is ok! If not, we disassemble, check everything over again.
A little from a lot of personal experience: the comrade from above said correctly about setting up the magnetic system, the gap is 4-5 mm. checked by a rod, the depth gauge rod to the end of the coils, and to the mating surface. then do the same on the moving system, the depth gauge rod on the rubber, but do not press, and on the end of the armature yoke. on the piston: it must be set as follows, the depth gauge rod to the edge of the piston contact, the end face to one of the four arms. we collect a movable system, a glass, rubber, a ring with four ears, we hold this ring as evenly as possible without distortions and presses, the depth gauge rod into it, the end to the edge of the piston, the data should converge with the body.
And in the end, the final assembly is the pump casing with a valve installed in it to close off the inlets. There is also a gap of 0.6-0.8 mm between the valve and the body, which ensures free flow of water in the absence of pressure.
Repair of household vibration submersible pumps of the brands "Malysh", "Trickle", "Neptune", "Urozhay", "Bosna", "Strumok", "Dzhereltse", etc. do it yourself
Despite all their positive qualities, submersible vibration pumps are not the most reliable and often break down for a variety of reasons. The cause of a pump malfunction can be problems with a power magnet or winding, an open traction, a broken valve, an open or short circuit. There are many simple malfunctions, which, it would seem, are not difficult to eliminate. Nevertheless, after repairing the pump, it can pump very weakly, or even stop pumping altogether. Therefore, it is very important to correctly assemble and adjust the pump. In order to understand how to set up and assemble the pump correctly, you need to know well the design and principle of operation of the pump, as well as some important points of its correct adjustment, which we will consider today ...
In order to correctly diagnose the pump malfunction and subsequently be able to troubleshoot the problem yourself, you should first study the principle of operation and the internal structure of the unit. This is especially true for those who are faced with such a problem for the first time as a breakdown of a vibration pump and have no idea how it can be repaired.
Let's take a closer look at these questions using an illustrative diagram.
The work of a submersible pump is based on the conversion of variable current strength into mechanical vibrations of the armature and piston, which contribute to the movement of water. The vibration of the piston pushes water out of the hydraulic chamber (the space between the piston and the valve) into the discharge port. The main components of the pump: housing, electromagnet and vibrator.
An electromagnet consists of a core and two coils wound with copper wire. Placed in the pump casing, it is filled with a compound, which serves not only to fix the magnetic system in the casing, but also as an insulating and heat dissipating material.
The vibrator consists of: an anchor, a rod, a shock absorber. The rod is pressed into the armature, the shock absorber is mounted on the rod and is a rubber membrane, the workmanship of which determines some parameters of the pump.
A rubber diaphragm, fixed by a stop, separates the hydraulic and electrical chambers of the pump, and also serves as a support for the stem, which determines its direction. There is a rubber piston at the top of the rod.
A rubber valve is located in the pump casing, which closes the outlet openings for water, but in the absence of pressure in the pump, it ensures its free flow.
1. Buzzing, but not pumping (or pumping very weakly)
To understand the reason, let's turn to the pump design (see diagram): on the rod 7 over the shock absorber 12 two nuts are screwed on 14... If their fastening is weakened, the shock absorber is also displaced, the pump starts to work "in vain".
To return the pump to normal operation, you need to disassemble it and tighten the nuts all the way, lock the top one. The sequence for disassembling the pump can be seen in the diagram above. Difficulties may arise with the tie screws (M8x40) on the cover if they are rusted and cannot be removed in the usual way. Alternatively, you can cut them off with a grinder, and during assembly, replace them with hex head cap screws.
Another reason could be damage to the valve due to heavy wear. Sand entering the pump accelerates this process, so the integrity of the rubber parts should be checked. In case of severe wear or rupture, the valve must be replaced.
A stem break is also one of the possible reasons, so it is worth checking its integrity. Replacing the stem if it is faulty or deformed is almost impossible.
2. When the pump is turned on, the plugs are knocked out, the cable is charred
The reason for this phenomenon may be a burnt out armature winding, or a cable malfunction. In the first case, the repair is impractical: the process of rewinding the armature requires certain knowledge, and the time and effort costs are not worth the result, since there is a high probability of re-closing. It is theoretically possible to make a winding for 36V by rewinding the coils in compliance with all parameters: wire thickness and grade; the number of turns calculated for a given voltage so that the power remains the same, etc. But it is easier to simply replace the winding with a new one.
We check the cable with a tester. Replacing the cable in the event of a malfunction is possible in some cases, since in "Malysh", for example, the wire in the case is filled with compound, only if necessary to increase its length, it can be increased by twisting.
3. Strong vibration and overheating of the pump
Even short-term operation of the pump without water causes overheating, which can lead to combustion of the pump. Due to overheating, the housing expands, the compound filling surrounding the magnet peels off from its surface, and vibration occurs. Operating without water for a longer time will result in complete detachment of the magnet. The gap between the magnet and the piston disappears, and movement of the piston becomes impossible.
You can bring the pump to its normal state and reduce the possibility of such a phenomenon in the future using the method described below (the method is rather complicated and not entirely accurate in the use of some materials and tools).
The pump should be disassembled by separating the electrical part. By tapping on the body, we determine that the magnet is not fixed inside. We release it from the case, after which with a grinder we cut grooves on it with a depth of almost 2 mm, in the longitudinal and transverse directions. On the inside of the housing, such grooves can be cut in a chaotic manner. After that, cover the body with sealant or glue and press the magnet inside. Once the sealant has cured, the pump can be reassembled.
However, there are models of pumps with suction openings located on top ("Trickle", manufactured by JSC "Livgidromash", and "Malysh M" from the "Electrodvigatel" plant). This design allows not only to exclude the intake of impurities from the bottom of the well, but also to improve the cooling of the pump, which makes it possible to safely operate the pump "dry" for up to 7 hours. The supply of a thermal relay pump (model "Kid K") increases its cost, but ensures its shutdown in case of voltage surges or overheating.
4. Low pressure, the pump does not pump well
This happens when there is insufficient clearance in the vibrator.
If the valves are in order, the nuts on the stem have not loosened and there is no break in the thrust, you can correct the situation by adding washers 11 (1mm each) per vibrator 2... By increasing the clearance in this way, you can increase the pressure and increase the pump stroke. It is worth remembering that during this procedure you need to adjust and check the pump, that is, determine the number of washers empirically until the desired result is achieved.
In this material, we examined the most common breakdowns in which you can repair the pump on your own. By the way, we talked about how to independently repair the pumping station here.
Repairs have been made, the pump is to be assembled, adjusted and checked. These actions require special attention and accuracy.
![]() |
Video (click to play). |
So, when assembling, you should first of all pay attention to the gap between the piston and the magnetic system of the pump, it should be about 4-5mm. Then we check the integrity of the valve, blow it from the water inlet side - the valve should allow air to pass through. The piston must also be tested for integrity, elasticity and deformation. The next step is to determine the gap between the body and the valve adjacent to the suction ports. The optimal value is 0.6-0.8 mm, the gap is needed for the free flow of water in the absence of pressure in the pump. Assembling the body, we match the symmetrical parts, aligning the hole for the water flow in the rubber gasket with the hole in the upper part of the body.