In detail: do-it-yourself repair of propellers of outboard motors from a real master for the site my.housecope.com.
Brothers! On May, he did not have time to dodge the driftwood and as a result of the collision broke off half of the blade of the aluminum propeller. Motor Merck 90, a new screw costs about 6,000 rubles, so I thought about repairing a broken one, I rummaged on the Internet like a couple of offices in Moscow are engaged. Maybe someone tried to repair the screw or not get sick and buy a new one? I don’t feel sorry for the money, rather the question is interesting, for example, it can be cured and put as a backup
Recently there was a topic. It all depends on the cost of the work 🙂 And then I would only put such a screw in stock. So go to the store 🙁
I tried to weld such screws with argon outwardly, everything seems to be pretty good, but with a slight hit on any obstacle, it breaks at the place of welding. So it is repaired if the current is in reserve to reach the place. And I wouldn't even try.
Once, at a gathering of water motors, I drove across the ice fields of the Crimea with Whirlwind. I barely made it home, I almost became Chelyuskin, the wind moved the fields and really wiped them out, ice broke for an hour and a half. Having raised the motor, I saw that I had driven on one blade and did not notice, only the roots remained from the two blades. There was no vibration, it was gaining speed easier and there was no full speed.
MAK-360 wrote:
> I tried to weld such screws with argon outwardly everything is not bad
> like, but with a slight collision with any obstacle, it breaks down
> the place of welding. so that it is repaired if the current is in stock up to
> places to walk. And I wouldn't even try.
![]() |
Video (click to play). |
I approximately thought that half the cost of the new one would be given for work, but there would be little sense. I will post a photo of a feint who could not stand the battle with a snag))) Today I replaced it with a new one
\ Tried to weld such screws with argon outwardly, everything seems to be pretty good, but with a slight collision with any obstacle, it breaks at the place of welding. So repaired if the current is in stock to reach the place. And I wouldn't even try. \
So maybe you tried with such hands?
A normally repaired, step-by-step and balanced propeller runs no worse (and often better) than a store-bought one.
Here is the screw (Susa 140) before and after the repair, after the repair it has been running for the third season
This propeller (Yama 30), after repair, has already participated in several cross-country races and no one is in a hurry to return for revision.
There are many more photos with screws, in the worst condition before repair (or generally welded from a bare hub - these are mainly for racing) and have been running for several seasons. It all depends on the hands.
Date of registration: 22-June 14
The topic is about repairing your outboard propeller. Need some advice - ask our fishermen.
Request - in this thread, refrain from flooding. For those who want to “just talk”,at the bottom of each message there is a "Reply in flood" button.
For questions about the outboard motor, there is a whole "PLM" section.
By Boats - a boat section with a bunch of topics.
Choosing a screw for your PLM, subject - “Selection, replacement of a boat propeller ”.
Any flood in this thread will be deleted by the moderators, without explanations or warnings. Malicious flooders - risk getting banned.
But, despite the strictness of our Rules, I wish you pleasant communication. If you need help, please contact.
Date of registration: 30-November 15
- City: Novoaltaisk-beloyarsk
tell the guys how to correct the screw? if it is possible at all? bent on the river the vibration is terrible, on the bank corrected on a stump, visually it is very crooked. suza-9.9
Date of registration: 24-June 14
tell the guys how to correct the screw? if it is possible at all? bent on the river the vibration is terrible, on the bank corrected on a stump, visually it is very crooked. suza-9.9
Better to take a new one, I know a friend sent me to rule somewhere in St. Petersburg.
Never argue with idiots. You will sink to their level, where they will crush you with their experience!
Date of registration: 23-June 14
if it is possible at all? Perhaps, but you need special equipment and a stepping slide. It's easier to send Almaya to St. Petersburg. It will be better than the new one.
Date of registration: 22-June 14
I agree with Mitrich and Sergei.
I will add - an incorrectly straightened screw will quickly ruin the shaft or bearing (s) on the shaft - it will break like an unbalanced wheel disk.
Date of registration: 16-Jul 14

- City: Barnaul
- I can be useful: computers
tell the guys how to correct the screw? if it is possible at all? bent on the river the vibration is terrible, on the bank corrected on a stump, visually it is very crooked. suza-9.9
As a rule, one or two blades bend. If you see that it’s crooked, correct it. Choose the least damaged blade, make one not crooked, but the rest along it. And check everything else, shaft, plug caps, tank connectors. How many bent and knocked screws there were, there was never a particular vibration on motors up to 15 mares. The weights and sizes are not the same.
Peter, of course, is good, but in this category it is not very budgetary.
On the last fishing trip I hit a small piece of wood. The speed dropped by 2-3 km. Their. simia. At home in the garage I fixed the burrs on one blade, and on the next fishing trip I'll see what happened.
Post has been edited by stalex: 03 October 2016 - 20:06
I've been studying all my life. Hope the holidays are not coming soon.
Date of registration: 16-Jul 14

- City: Barnaul
- I can be useful: computers
I agree with Mitrich and Sergei.
I will add - an incorrectly straightened screw will quickly ruin the shaft or bearing (s) on the shaft - it will break like an unbalanced wheel disk.
But I disagree with either Engels or Kautsky ... (Heart of a Dog)
No, well, you can ruin everything with our men, but so that quickly the bearings, and even more the shaft, mulberries, I am categorically disagreeable.
If there is a strong vibration on the motor up to 15-18 forces on the tiller, then the difference in the curvature of the propeller blades can be seen even after 3-4 or even 5 stars. And if not with an “armed” look, then no questions at all.
As in the army: - albeit ugly, but uniform.
I've been studying all my life. Hope the holidays are not coming soon.
Date of registration: 19-July 14

- City: Malinbiao
- I can be useful: there is nothing to help
In the Flood, Truth is Born.
Date of registration: 16-Jul 14

- City: Barnaul
- I can be useful: computers
The node in this case is a reducer, the rest of the details of the node. To reduce the service life of the NODE, one of the parts must fail.
The shaft loses geometry immediately upon impact.
Then, the bent shaft breaks the oil seals, water gets into the gearbox, then the bearings run out, etc. increasingly.
The shaft was bent, there was water in the gearbox.
If the shaft is not bent, then even a “visual straightening on a hemp” to a more or less the same condition of the blades should not give a strong vibration. Of course, if the eye is not glass and your hands grow above the waist
I've been studying all my life. Hope the holidays are not coming soon.
Date of registration: 16-Jul 14

- City: Barnaul
- I can be useful: computers
You shouldn't be so, one thing is a burr, another is a change in the geometry of the screw. I think that of course the shaft will not break right away, but it will significantly reduce the service of this unit.
No, well, you can sit, cry, turn off the engine and go to the parking lot on the oars, turning on the alarm, of course, and call a mail courier on the sotik to urgently send the propeller to St. Petersburg
And you can, of course, assessing the nuisance, take measures for restoration and continue fishing.
Here everyone decides for himself
I've been studying all my life. Hope the holidays are not coming soon.
Date of registration: 29-June 14
Date of registration: 16-Jul 14

- City: Barnaul
- I can be useful: computers
And if the situation is even more deplorable - a broken blade - are there places where they know how to weld, or definitely for non-ferrous metal?
In Novosibirsk, I have repeatedly seen advertisements for the restoration of screws and gearboxes, the price tag in the advertisement is humane. I did not apply myself. And he didn’t call.
IMHO the ability to weld strongly depends on the material. But the question arises, has the broken piece survived?
If there is a need, you need to call to find out the technology, then decide
I've been studying all my life. Hope the holidays are not coming soon.
Date of registration: 23-June 14
“Visual straightening on the hemp” to more or less the same condition of the blades should not give a strong vibration. Tie the crap to smack, my screw, aligned far from the hemp, gave a decent vibration, visually everything was in order. Found a joint only on a stepping hill.
Date of registration: 30-September 14
Any cast part after impact will have a broken geometry, and straightening and welding is practically impossible. To fix defects on parts of complex geometry, which screw is needed at least a matrix for this screw, well, hands with experience gained by more than one product. Wow, not only make the same curve, on all blades, but also the angle of inclination, relative to the axis, and the step must be observed.
The question immediately arises, what is the difference between a proprietary screw and a copy? Probably, manufacturing accuracy and closeness to the ideal curve and efficiency close to ideal.
However, the option with hemp, in fishing conditions, is simply necessary to continue fishing and return to the base.
Do something useful in life, then it will become pleasant.
Pages 1 2 Next
You must login or register to post a response.
- Lensky
- Elder
- Inactive
- Where: Irkutsk region
- Registered: 10-02-2017
- Posts: 998
I have experience in restoring all the operating characteristics of the screws of imported motors. If the topic is interesting to someone, I can share my experience in detail.
..very
- Lensky
- Elder
- Inactive
- Where: Irkutsk region
- Registered: 10-02-2017
- Posts: 998
..the text is blurry
- Lensky
- Elder
- Inactive
- Where: Irkutsk region
- Registered: 10-02-2017
- Posts: 998
✔️ fas.st/1SYO-T - Huge selection of new screws and accessories
Subscribe to the main channel:
The rotated screw from the Yamaha 30 was reanimated. Drilled through the screw and inserted the pins that prevent the sleeve from turning. The damper remained rotated but locked firmly.
The method is not the most humane and correct, but very simple and cheap.
If you know how to fix such a screw, then write in the comments.
fucking goggles reducer in meat


If you get stranded or hit somewhere on a stone, immediately change the gearbox 🙂 So it's better to buy a new one

guy screw well tighten the shaeba presses on the damper, from time to time it is necessary to overtighten and that's it. so I turned a new screw.

did the same. I just cut the threads and planted them on an inseparable hermitic.

With a thread it will be clearly more reliable.

So did the pins survive or not?

We rode on the screw for about 20 minutes. Nothing criminal happened. Everything stands still. Lies as a spare.

Guys, these dampers can be ordered separately and re-pressed (it will take five minutes and not from some collective farm)

Silent block in the car market suitable

they just want to sell you bad

For example here and so on

Please tell me where to order. I dug the whole Internet and I can't find a fig. Also the screw is steel

Officials in the furnace! Divorce is important to them, not your well-being.
There are dampers separately, I bought for the screw from Toha and repressed it myself.

I ran into such a problem right now, tell me how long did it take?

Imagine I just did it differently. Where the nut splits the hole, I drilled the screw on both sides and stuck a through pin along the edges of the groove.

This is a spare screw. It took only about an hour. So the statistics are too small.

You have done something stupid, 1.Take Soviet outboard motors, the propeller is secured with brass or bronze pins, I will not talk about the strength of metals, in short, aluminum pins are not rolled in this mounting option. 2. The rubber-reinforced damper provides a reduction in radial-dynamic loads from the gearbox shaft, in other words, all dynamic discrepancies will come to the radial bearings of the gearbox shaft, resulting in the destruction of the gearbox.
3. Pouring such things with epoxy is also stupid, it's easier to cut threads in a screw and twist pins and put the threads on glue - then it will be dead.
4. Unfortunately, I did not quite understand from the video what exactly scrolled (outer diameter damper)?
5. Here, the same thing, only after 70 km, everything fell into disrepair

Aluminum pins are about nothing. Either steel (brass), or not at all. But it is better to somehow replace the damper.

Of course you are right, but I proceeded from considerations or throw it out or try to do so.
I did not have a goal to do it tightly. If I turn the aluminum pins, I will immediately throw out this screw.
I think everyone understands that any change to the factory design is done at your own peril and risk.
At the end of the month I will ride this propeller for a couple of days. And I'll write later what happened to him.

DIY boat propeller repair. Damper / coupling / bushing repair.
Or log in through one of these services
Comments can be posted only by registered users
Register a new account in our community. This is not difficult!
No registered user is viewing this page.
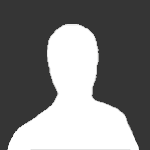
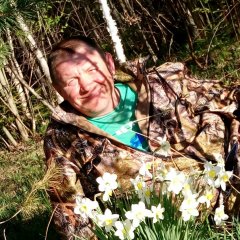
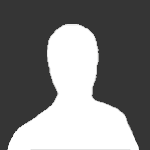
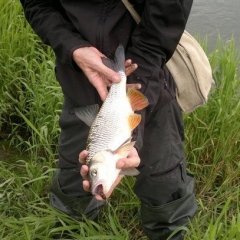
Temik »17 Apr 2014, 15:21
DOBRO »Apr 17, 2014 9:42 pm
Temik »Apr 17, 2014 10:37 pm
Temik »16 Jun 2014, 22:55
Temik "07 Jul 2014, 14:42
Added after 7 minutes 39 seconds:
Yes. The ring on the screw is also crooked and dangled like no one knows what!

Temik »09 Jul 2014, 00:14
Chief »10 Jul 2014, 09:34
Temik »10 Jul 2014, 11:12
And how much more money will it cost? Wasn't it easier to buy a new Chinese one?
I took a cast with cement mortar from one blade. Now I will adjust all the blades one at a time, from the beginning. Then cut and saw. Finish. The most interesting is what, how and for what. You have to learn from something.
Sagittarius "10 Jul 2014, 13:25
Temik "10 Jul 2014, 17:22
Solomonich »10 Jul 2014, 23:17
Babiyi »11 Jul 2014, 00:20
Don't tell me what and how I need to do, and I won't tell you where you need to go!
Temik »11 Jul 2014, 23:53
That I do not argue. I know. But I want to figure out the subtleties myself and learn. That's all for sure. Well, it's just interesting to me. Interesting and that's it. I want to try it myself. Understand your mistakes to draw conclusions and each time it gets better and better to make screws for yourself. That's how it is.

Added after 6 minutes 57 seconds:
DOBRO "12 Jul 2014, 17:39
Temik »14 Jul 2014, 12:13
Guest account "14 Jul 2014, 13:20
Tem, panimash what's the matter, I'll try to explain it easier.))
First, make a step slide so that you can see for yourself what you are doing.
All that you do is from idleness, but does not bring you closer to the correct screw.
Why.
The answer is simple - you do not know if the blade you took the impression is correct.
I personally had 1 perfectly correct screws, this is the one that Almay did not rule after the check. True, he still turned out to be a little jumbled, not the step as it is written on it, 15 is written, but really the cleanest 14. And Almay made me and my friends have more than fifty screws.
See what happens, just an example.
On the propeller, for example yours, the marking 9 14X3X14 is written, but in reality the blades can be at the base (hub) 1516 and end in 1413 and what happens from this. The beginning of the blade begins to spin, and the edges slow down, so the boat does not go. progressive), then the chance to go is real, but who knows without checking.
Therefore, if you want to achieve something, but you need to approach the issue with the utmost care.
But in my opinion, if you are not going to do this, then it is easier to send Lyokha to make the screw and let it be a little more expensive, it's not about the money, you already lost your fucking wish. and the dying of the oil seal, or the boat does not go.
Before Lyokha, I made screws for a rider known at one time in St. Petersburg, everything was hurt until he began to trust the apprentices. I gave the propeller to him, the result is the second place in its class at the “Ice Race”, the speed is 7879 km / h. instead of 7374 km / h.
Temik "14 Jul 2014, 13:32
Subject: Propellers, repair restoration ?! - Repair, revision, maintenance of floating crafts - Boats and boats - Transport (vehicles) - Main section - Forums of the Open Club Petersburg Hunter
"Whoever hunts and fishes will not get anything!" "From myself and for my brother!"
A properly restored screw is no worse than a new one. In addition, restoration is 3-4 times cheaper than a new screw (non-original). When you kill a screw 2-3 times over the summer, the savings are significant.
Believe me - it is possible in practice. Everything depends on the master.
If you need someone to fix the screw, knock on the PM, I'll give you the master's phone number.
I don't want to post it in the public domain.
If the wines are worth 20 thousand and wait a month. Then no alternatives. And for 2t.r it is easier to buy a new one.
If the screw costs 20 thousand and wait a month. Then no alternatives. And for 2t.r it is easier to buy a new one.
If you need someone to fix the screw, knock on the PM, I'll give you the master's phone number.
I don't want to post it in the public domain.
the only screw, its price is the same, there are no others.
Ah, Lesha "Almay"! Lives in Krasnoe Selo. He also has a workshop there.
The master is good, he does it with a soul. It does almost everything: welds on blades, balances, restores geometry, tilt angles, changes the pitch of the propeller, etc. I myself have repeatedly used his services. I know him from the RCC.
✔️ EVERYTHING for fishing:
Subscribe to the main channel:
The rotated screw from the Yamaha 30 was reanimated. Drilled through the screw and inserted the pins that prevent the sleeve from turning. The damper remained rotated but locked firmly.
The method is not the most humane and correct, but very simple and cheap.
If you know how to fix such a screw, then write in the comments.
Video Do-it-yourself repair of a propeller boat propeller. Damper / coupling / bushing repair. channel VeterNSK
The damper (bushing) of the standard (original) Suzuki DF-15 propeller turned. According to the Servesmen, a replaceable bushing is not included in spare parts. Throwing out a propeller with intact blades, the hand does not rise. Our country is full of Kulibins. This gives rise to the actual question: “Who treated the problem, how? “. Redoing under the key as an option, which is accompanied by drilling, I leave it as the very last.
This problem applies to other brands of engines as well.
I drilled a damper (rubber) in several places, filled it with glue, screwed in several self-tapping screws - Holds for 20 hours has passed. Now in stock, I use a high-speed one. Yamaha 8.
As I understand it, the rubber was drilled to reach the screw body and the cavity was filled with glue (what?). And where were the screws screwed in? If in the body of rubber to wedge, is it not better to use rods with glue? They will seal better than self-tapping screws.
Yes, I did that. He took molecular glue in a small tube. Maybe it should have been different?
Valera, think about it yourself. what is better to sell them - a screw or a bushing. Now, if they offered you a sleeve for 100 and a screw for 200 (based on prices, for example, according to my link), then it would be better for them to sell the sleeve. But smart people also sit there and understand. that you obviously can't buy a sleeve for 100.
Gena, and this is already called differently: mad: Therefore, I sent my question on the situation to not the last person of the service.
———- Added at 09:40 ———- Previous post was posted at 09:38 ———-
Managery delirium. the sleeve is sold and changed, only the cone needs to be carved for pressing ..
It is clear that the mandrel is needed, and also the question is about the restoration, because the damper also costs money. Here are the nuances of technology and balance (taking into account the revs) in order to restore the propeller not as a spare, but as a running propeller.
———- Added at 11:13 ———- Previous post was posted at 09:40 ———-
Yes, I did that. He took molecular glue in a small tube. Maybe it should have been different?
Well, in another way, in this version, it can only with self-tapping screws, as already mentioned, if they fill the role of spacers-seals. the self-tapping screw cuts the body practically without bursting the hole. I haven't seen the bushings of my screw. If there is a solid body, then yes, but if the outer surface has longitudinal ribs, then this can get into the cavity. Again, experiments with glue are needed to withstand the environment a habitat.
But this is theory (IMHO), and the practitioners are still silent.
Sobsno the best recovery technology :)
Screws and glue. I spent about 20 hours, now in stock. He, an infection, probably scrolls inside on a small diameter. If a large diameter was scrolled, then it would be possible to drill through the metal of the screw and screw it onto the rubber. Unless, of course, I'm not confusing.
The damper (bushing) of the standard (original) Suzuki DF-15 propeller turned. According to the Servesmen, a replaceable bushing is not included in spare parts. Throwing out a propeller with intact blades, the hand does not rise. Our country is full of Kulibins. This gives rise to the actual question: “Who treated the problem, how? “. Redoing under the key as an option, which is accompanied by drilling, I leave it as the very last.
This problem applies to other brands of engines as well.
At what service did they say that? Purely curious. I even have this in my warehouse. Someone ordered a long time ago and did not come to pick it up. Drive up, I'll give it up at the entrance, rarely demanded thing. Usually the screws cripple, but the dampers are alive.
Rummaging in the world wide web, on the issue of replacing the bushing, I came across useful information. Therefore, in the topic I changed the title simply to "screw repair".
So, repairing an aluminum screw:
0ixZmaENjHM
Steel screw repair:
eq9PwAgDroQ & feature = related
U6FZzVj8FgA & feature = related
Shl. The grandfather is more conscientious in doing than the young. Balancing is a necessary thing.
ZyZy. I took the bushing into my propeller. Some doubts are tormenting. It’s understandable to make a mandrel. There is a landing place, there will be no problems.
When pressing in, the bushing can skew with all the consequences. I think I need a guide.
Who did what or how? Do not want to spoil the sleeve.
Leafing through the chat room to find a topic for a person, I decided to collect the scattered into one (for convenience)
[Links to union members only.]
[Links to union members only.]
I remembered that I had not left information on the bushings, sorry.
Damper bushing screw Suzuki DF-15 (9,9)
original sleeve catalog number 58120-93701-000
Solas bushing catalog designation SA-RB
Both hubs fit Suzuki and Solas propellers
At one time, when King Hammurami was still living, he argued that the time spent fishing is not included in the total life span. This is also stated by many citizens who like to spend part of their free time fishing.
Typically, most anglers own a boat. Many boats, especially modern ones, are equipped with gasoline engines. And a boat without a motor, especially if you have to fish in the expanses of a large lake, becomes a burden that requires huge costs, strength and energy to move. And here you definitely need a motor: gasoline or electric - no difference.
And yet, special attention should be paid to the electric motor, because:
- electric ones do not require oil or gasoline for their work, which means there are no exhaust gases, which does not harm nature;
- electric motors are smaller, lighter and less space-consuming. This is especially true if you have to fish far away, and every kilogram of excess weight is always felt;
- they are much more profitable than their gasoline counterparts in economic terms;
- modern designs are assembled on modern parts developed using modern technologies, therefore, with a minimum weight, they have maximum power.
But these statements take place in the event that the boat owner already has an electric motor and has experienced such advantages to the fullest. But what if he is not there? So, you need to do it yourself.
Many adventurous boat owners use a drill or screwdriver that runs on batteries, as the industrial design of an electric motor is based on the same principle. The basic layout of such a unit is almost the same for all models and looks like this:
- the battery is the power source;
- the electric motor acts as a boat engine;
- a propeller with a gearbox is a working tool that ensures the movement of the boat on the water;
- control unit - consists of a handle for turning the direction of movement and changing the speed of rotation of the electric motor.
Almost all elements can be found in an electric drill or screwdriver. It should be borne in mind that industrial devices are hermetically sealed, which allows the main units to be in the water.
If you use an electric drill, then it is desirable that it is located away from water. This is the only problem, quite serious, that requires a technical solution. The slightest hit of water on the control unit can disable it, which will lead to the stop of the boat.
If you take an electric drill, you should always remember that its main value is the engine and the speed control unit (button). Choosing a drill or screwdriver comes with some advantages over buying an industrial outboard motor:
- for the price, this purchase will cost much less than buying a factory sample;
- according to the legislation, it is necessary to adhere to the requirements related to the power of the engines used in various bodies of water;
- the electric drill works from a battery or other power sources with suitable parameters;
- the electric drill is easy to repair, thanks to the availability of a sufficient number of spare parts on the market.
When choosing a drill, one should take into account the factor that it is mainly designed to work in a cyclic mode. If the drill will be installed on a boat, then you need to rely more on a continuous work cycle. This means that a reserve of power is needed, otherwise the drill will overheat.
In such cases, you should opt for a power of 150 W and more. The power reserve will allow you to work with a propeller with a diameter of 130-150 mm. In addition, it must be borne in mind that the total weight of the boat will correspond to 300 kg, not more. It can be considered that this is the limiting weight.
You should immediately pay attention to the fact that drills and screwdrivers are available for various operating voltages, such as 12 V, 14.5 V, 16 V, 18 V and 24 volts. Batteries are also available for the same voltage. And yet, the capacity of standard batteries that serve the operation of an electric drill or screwdriver in classic working conditions is not enough to ensure the necessary movement of the boat on the water. In this regard, it is better to pay attention to the car battery, which has a much higher capacity. And since a car battery gives out 12 V under a load, then a drill should also be chosen with an operating voltage of 12 V.
Naturally, you can make a battery of accumulators from a set of produced batteries for power tools for any voltage, but this can be much more expensive.
For such a device, you will need the following parts:
- electric drill for the motor;
- clamps for fastening the motor (drill). Both ready-made factory and handicraft are suitable;
- the gearbox from the grinder is suitable if the motor is installed on the transom of the boat;
- round tubes with a diameter of 20 mm and profiled tubes 20x20 mm. A rod and a mount for the motor (drill) will be made of them;
- a round bar of metal from which the motor shaft will be made, as well as sheet metal for the propeller.
To work, you may need the following tools:
- scissors for metal;
- a welding machine, although you can do without it;
- electric drill and a set of drills;
- grinder with cutting and grinding wheels;
- if the design provides for wood, then nails or screws (as well as wood).
The presence of a lifting mechanism radically simplifies the operation and maintenance of the entire system, especially since there are cases when it is necessary to urgently raise the propeller. As a rule, such a mechanism controls the position of the electric motor in all planes (vertical and horizontal).
Alternatively, the following design of such a mechanism can be proposed: the motor is attached to the transom of the boat with the help of clamps, which are rigidly fixed to the plate. The clamps are equipped with rings through which the tube is threaded, and the motor shaft is threaded to the axis welded in the center of the tube. The result is a very simple pivot joint that can provide normal motor control.
As far as is known, the drill is designed for drilling holes and has a high end RPM, which is not acceptable for a propeller that operates at a slower RPM. Therefore, in order to reduce the speed transmitted to the propeller, the installation of a gearbox is required. Sometimes you need 2 of them, depending on the design solutions. The upper gearbox should reduce the speed of the drill from 1500 to 200-300 revolutions, which will ensure the boat's normal running.
The lower gearbox serves for horizontal installation of the propeller. When using a reducer from a grinder, it is simply clamped in the drill chuck.
The manufacture of the propeller propeller begins with marking it on a piece of steel sheet. As mentioned above, its diameter should be no more than 130-150 mm. You can take a square of metal with dimensions of 200x200 mm and a thickness of 2.5-3.0 mm. It is better if it is stainless steel, although it is much more difficult to process. As a last resort, you can use an impeller from an air exhaust fan or the car's cooling system. At the same time, it should be borne in mind that the impeller profile is designed to work with air mass. In this regard, you will have to start making it yourself.
A hole is drilled in the center of the square for the landing screw. Slots are made along the diagonals so that the sheet remains intact in the center up to 25-30 mm. After that, they begin to form the shape of the blades. They usually have a rounded appearance. In this case, you need to ensure that the blades are of the same size, otherwise there will be vibrations. After that, the blades are slightly turned at a certain angle. In this case, the direction of rotation of the blade must be taken into account.
Since the manufacture takes place at home and, as they say, does not break off in the water, tests should be carried out. Any container of water that can hold the propeller is suitable for this. Naturally, the larger the capacity, the better. As a last resort, if possible, it is recommended to go out into nature, to a river or pond and try it in action, without installing it on a boat.
A directed jet of water should be observed and felt when the engine is running. In addition, there should be no severe vibrations. If the propeller does not work at full power, you can modify it by increasing the angle of inclination of the blades.
The engine control system is being finalized depending on the wishes of the boat owner. The main thing is to manage it conveniently. It is better to take the engine speed control button to a convenient place.
The calculations should include the following components:
- the mass of the boat in full gear;
- power consumption of the electric motor;
- current strength and operating voltage.
During the assembly process, you should take an electrical measuring device and make sure that the motor power and the load power match. The motor power must cover the load power. It is desirable that the engine power overlap the load power by at least 20%.
If the power of the engine matches the power consumed by the electric drill: if the power consumption calculated by the formula P = 12V x Ipot corresponds to the declared power of the engine (electric drill), then we can say that everything has been done correctly and the electric drill can be used as a motor for a boat. At the same time, one should not forget about 20% of the power reserve. You will need it in case of emergency.
In the process of establishing, it is better to experiment with the impeller in order to choose the correct configuration of the blades. As a rule, their shape significantly affects the economics of engine operation.
Some of the owners who decided to make their own electric motor for the boat use various 12V motors that are used on board the car.
Engines like these are great for these functions, if only because they are designed to run on a car battery. Despite this, they require some work.
Boat owners are constantly experimenting and finding amazing solutions. The high cost of industrial designs makes them do it. As a result, the idea was born to install a motor from a lawn mower on a boat. These are engines with a capacity of about 6 HP, which are designed for continuous operation under load in various conditions. A similar engine can be adapted to a boat if you use various spare parts intended for the repair of Soviet boat motors.
Some craftsmen easily adapted motors from Soviet chainsaws, as motors for boats. At one time, a huge number of chainsaws were released, the quality of which needs to be discussed separately. Despite this, installed on boats, some of the motors are still in use today. The main thing is to calculate everything correctly.
This is a very interesting question. The use of conventional AC motors has been talked about for a long time. Such motors do not have a brush mechanism, therefore, they are very easy to operate and operate.
But there are some factors to be considered here. The first factor is the presence of an alternating voltage of 220 V. Alternatively, it is possible to install an inverter that can convert a direct voltage of 12 V to an alternating voltage of 220 V.
The second component is safety, because the voltage of 220 V is very dangerous for humans, especially on water. This requires special measures. But if there is water all around, then it is difficult even to imagine what exactly these measures should consist of.
There is an almost ready-made option - this is the use of a motor from a trimmer or from a brushcutter. Here, almost everything is ready, it remains only to decide on the length of the device and install the propeller. There is no need for an upper gearbox and there is no need to modify the control system and the power supply system of the engine.
The main challenge is to properly attach such a device to the boat. It is especially true if you have an inflatable boat.
The manufacture of such structures is available only to those boat owners who are in constant creative search. On the other hand, most of the boats are owned by anglers who are constantly experimenting. Therefore, it will not be difficult for them to carry out their ideas.
![]() |
Video (click to play). |
Naturally, creative people or people who are not allowed by the family budget to purchase both a boat and a motor for it are engaged in the independent production of various structures. Therefore, some of the fishermen still paddle and do not regret it. They are only satisfied with the fact that they have a boat, since there is another category of anglers who do not have such a boat. They enjoy fishing from the shore and envy those fishermen who have a boat, albeit without a motor.