In detail: do-it-yourself planer for body repair from a real master for the site my.housecope.com.
Body planer without blade AIST 67917105 rotary handle, length 350mm
Body planer with blade RHD TH01001
Set of ABREX Velcro abrasives (5pc) 70x198mm curved with dust extraction (22holes) B54R5620193
Velcro sanding set RM-90726 (6pr) in Russian Master case
Pneumatic grinding planer MIRKA OS 383 CV with dust extractor 190x70mm, stroke 3mm, 10000rpm, weight 2 kg
Pneumatic grinding planer RUPES SLP41A with dust extraction (14 holes) 400x70mm, stroke 4.8mm, 400l / min, 6bar
Velcro planer ABREX (70 x 198mm) without dust extraction medium sanding B58R7021198
Velcro planer ABREX (70 x 400mm) without dust extraction, long sanding / B56R0020740
Velcro planer FLEXIBLE ABREX (70 x 400mm) plastic sander 9021PV
Velcro planer FLEXIBLE RM-90672 (70 x 400mm) FLEXIBLE sanding soft Russian Master
Velcro planer with clamps RM-72000 (70x400mm) METAL for sanding on an aluminum base
OVAL Velcro planer (70x200mm) semicircular sanding 12-20 P
Adjustable Velcro planer ABREX (70 x 400mm) with dust extraction 14 holes
Adjustable Velcro planer (70 x 400mm) with dust extraction 53 holes
Velcro planer RM-90771 (70 x 125mm) PLASTIC sanding lightweight
Velcro planer RM-90788 (70 x 198mm) PLASTIC lightweight manual sanding block
Velcro planer RM-90795 (70 x 400mm) PLASTIC grinding sanding block
Velcro planer with dust extraction ABREX (70 x 125mm) 13 holes short sanding B58R7130125
Velcro planer with dust extraction ABREX (70 x 198mm) 22 holes medium sanding B58R7220198
Velcro planer with dust extraction ABREX (70 x 400mm) 14 holes long sanding B56R0021740
![]() |
Video (click to play). |
Velcro planer with dust extraction ABREX (70 x 400mm) 53 holes long sanding B56R0531740
Velcro planer with dust extraction Deerfos (70x125mm) with holes
Velcro planer with dust extraction Deerfos (70x200mm) with holes
Velcro planer with dust extraction Deerfos (70x400mm) with holes
Velcro planer with dust extraction PM-91808 (70 x 125mm) 13holes short grinding
Velcro planer with dust extraction PM-91815 (70 x 198mm) 22 holes medium grinding
Velcro planer with dust extraction PM-91822 (70 x 400mm) 53holes long sanding
Sanding block with Velcro 70x125mm WDK-431001 (hard + medium hard), double-sided
Sanding block with Velcro 70x125mm RM-90665 soft Russian Master
Sanding block with Velcro 70x125mm RM-90689 flexible Russian Master
Sanding block with Velcro 70x196mm RM-90696 flexible Russian Master
Sanding block with Velcro D150mm PM-90764 for grinding wheels
- records
11 - comment
53 - views
23 867
Published by Alexander Andreevich December 16, 2015
Continuing the conversation about curved surfaces, it makes sense to mention the issue of grinding and finishing. For flat surfaces, we use grinding planes or blocks; hard at the beginning and medium soft at the finish. Soft ones are used somewhat less often. For leveling grinding of curved surfaces, elastic planers are used. They are convenient to grind down bumps on arcs of convex and concave surfaces, to smooth them. Arches, curved walls and ceilings, car body parts. It looks like this:
I didn’t want to buy it, because I have to look for it, and it’s not cheap. So I made it myself: I took a piece of plexiglass and rubber from which they make soles and repair heels.
Peeled off the protector, glued it; around the perimeter sharpened evenly. In order not to drill the platform, I made adhesive fasteners for handles and clamps.
Choosing a tool for body polishing ">
Grinding has another name - matting (matting). Matting is the procedure for applying small scratches to the body of a car with abrasive materials. The purpose of the manipulation is to improve the adhesion of all subsequent layers (primer, paint, varnish, and so on).
If the matting area is negligible, use plain sandpaper or tape-bright. Large areas of the body are processed with a grinder.At the same time, there is a certain relationship between the grain size of the abrasive material and the subsequent work:
- reduction of gloss before painting - an abrasive from P120 to P180 is required;
- cleaning the surface to iron - P80.
All work on grinding the car must be carried out in a mask, since the process is associated with a lot of dust formation. The mask can be replaced with a respirator.
Matting the surface of the car body is carried out with a special tool - this is a plane or a grinder. There are many options for the latest devices, but an eccentric or orbital sander is considered universal. Its scope is extremely wide:
- cleaning the car surface from the old layer of varnish and paint;
- processing of transition zones before local painting of certain areas;
- alignment of areas after applying filler (putty).
For grinding large and flat surfaces with high rigidity, it is advisable to use a surface grinder.
It is unacceptable to use surface grinding technique on curved, curved and thin-walled surfaces, this can lead to deformation of parts!
For problem areas of the car that need sanding, it is best to use a plane.
Grinding with an orbital machine has a high-quality result if the following rules are observed:
- it is necessary to regularly check the serviceability of the components: the dust extraction hose and the vacuum pump;
- during matting, the sole of the machine must be tapped periodically so that abrasive particles do not get clogged inside;
- you should not put pressure on the grinder, grinding occurs under the own weight of the device itself;
- the heating of the surface of the car body must be controlled, if required - to arrange technological breaks in work.
Compliance with these simple points will allow you to perform grinding efficiently and quickly.
The plane is considered a hand tool for matting the car body. A fine grain skin is fixed on the device and the master begins to make smoothing movements along the surface in any order. The more varied the trajectory of movement, the higher the quality of the grinding.
When processing a car body, it is generally recommended to use sandpaper or scotch-bright with your hands. In this way, areas with complex relief are matted; movements should also not be of the same type.
Wet sanding of a car means constantly wetting the body with water. A damp sponge is used for these purposes. The water must be changed frequently to avoid heavy contamination. After sanding with water, the body surface must be washed and wiped dry with a lint-free cloth.
The polyester filler coat can only be sanded dry, because the filler is very hygroscopic.
If smudges or light shagreen appear on the car body, grinding will be much more effective when a few drops of liquid soap are added to the water.
Any body repair is focused on creating a perfectly smooth new car paintwork. A grinder will help to mechanize your work to prepare the work area. The principle of operation of the orbital device consists in combining the rotation of the sole and displacement of the orbit due to the eccentric to a diameter of 2 to 6 mm. The complex effect on the car body allows you to achieve a high abrasive result.
The basic configuration of any grinder implies the presence of either an electric drive or an air drive from a compressor. Many craftsmen prefer the first option because pneumatic equipment requires a large volume of air and a powerful compressor. The volume of the compressor is impressive, as is the power consumption.
Pneumatic orbital sanders are a popular product among auto repair shops; for home use, an electrically driven device is sufficient.
Orbital grinding technique is selected according to the following parameters:
- power consumption of electricity (200-600 W);
- rotation frequency indicators (revolutions per minute);
- the rhythm of vibration of the sole;
- the presence of the function of adjusting the stroke of the eccentric in mm;
- the diameter that the work sole has (12.5 or 15 cm);
- are there holes in the sole for dust extraction;
- weight of the device (1-2.5 kg).
The basic set of the grinder contains a 6-sided wrench, with which the sole is installed and removed. There is also a dust collector, sometimes a spare handle. Many models are equipped with a function for connecting to a vacuum cleaner.
To grind the car body, in addition to the orbital machine, the master will need consumables for it, namely, abrasive mugs.
Orbital grinding equipment costs differently, depending on the brand awareness of the manufacturer. So, for example, a Rupes SL 42 AE plane (Italy) can be bought for 26 thousand rubles. Less well-known manufacturers offer more modest prices. For example, a pneumatic polishing machine JAS-6531 from Jonnesway (Taiwan) costs 9.7 thousand rubles.
The plane for grinding cars is used in hard-to-reach places and on curved areas. It can be produced in two different versions:
- with Velcro for sanding paper;
- equipped with clamps.
In addition to the design features, an auto plane can be of any size. The cost of the simplest product is from 300 rubles.
A hand tool for matting a car body is considered not only a plane, but also a lot of other devices:
- a rubber pad for sanding is an elastic rubber block with special clips for attaching sandpaper. Such a block can be used for dry and wet surface cleaning;
- cork pad for sanding, weighs very little. It can also be used for dry and wet matting of a car body;
- pads with clips made of plastics. The bottom of the device is additionally reinforced with a rubber gasket, which prevents the sandpaper from slipping off the clamps;
- long sanding blocks of sizes 40 * 7 cm. ERSTA542 sanding strips are consumables for such an analog of a planer.
In addition to the listed devices, manufacturers of equipment for body auto repair are constantly updating their product line, delighting auto repairmen with new and useful developments. But, despite this, the plane and grinder remain the most popular grinding tools to this day.
Hello car enthusiast on the site
Today's article on the video of Vlad SchCh continues the theme of body repair - "Painting the car for a complete repaint from A to Z". Today the lesson is devoted to the selection of the necessary accessories (materials and tools) for working with putty surfaces. We will find out what types of sandpaper and bars of different shapes are needed for grinding car putty and how to combine it in practice.
It will also show how to work with a bar on different planes with the replacement of sandpaper of the required size.
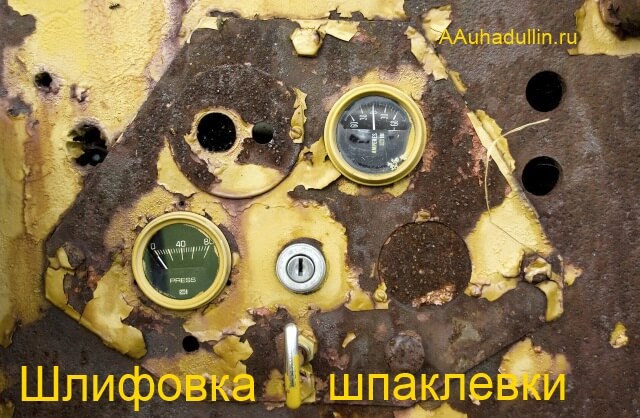
So, let's get down to do-it-yourself putty work. First of all, we will start with the wing arch and immediately figure out what we need for work.
This is a hard block of small size so that its plane overlaps the working area of the putty. The work may require other bars, this will be discussed during the video.
We also need several types of sandpaper for sanding the putty. First of all, we will use P80 sandpaper with a larger grain, which removes putty very well. It is needed to work with the top layer and we will work with it without strong pressure in order to knock down the putty a little.
Sandpaper P80 - we need it for sanding the first layers of putty, for the initial leveling of the material. Next, the number of sanding paper is used for grinding the putty P120, 150, 180.220, etc.- further grinding and preparation for the ground, each subsequent number removes a smaller layer of material and gives less risk.
After sanding paper P80, we will use the number P120 or P150. Generally speaking, it is recommended to work with this sandpaper, as the P80 is quite difficult to work with, because it is very rough and removes a fairly large layer of putty. With coarse grains, you can overdo it, and reach the metal, which will require reapplying the putty.
In addition, you need to remember that each paper leaves a risk, or in simple words, it's just a scratch. And this risk, a scratch must be removed with a subsequent finer-grain sandpaper.
The rule of 100 microns means that each subsequent number of sandpaper differs by no more than 100 gradation units, but we'd better take 50 units of difference or less. For example, a number of sanding paper numbers for grinding putty - P40 / 60/80/120/150/180/220/280/320 ...
Since the next sandpaper should erase the previous risk. You must always remember that finer sandpaper will go further and you do not need to remove a lot of putty! Basically, you just need to knock down the risk and leave some margin for working with fine grain.
How to properly grind planes and how to avoid possible mistakes was discussed in detail in the previous video (part # 8). If anyone has not watched, I advise you to familiarize yourself in order to better perceive the next stages of work.
This video (part # 9) will also talk about this, but not in such detail so as not to repeat it.
We take a block of sandpaper and begin to process the surfaces. Let's start working from the gas tank hatch, where there is a layer of putty applied on a flat surface. Master Vlad polishes the surface with the so-called herringbone, without applying much effort.
We do not completely grind this area with our own hands; in the video we can see that a small edging remains on the edge. We leave it to then align with the next number of sandpaper.
Next, we go to the arch itself, not forgetting that each plane is interconnected with another plane. You need to be careful when processing each and correctly display all planes.
Do not press very hard on the block, since a small layer of putty is applied to the end of the arch and you can easily get to the metal. Then we move on to the next plane, also without making great efforts with the hand.
Always pay more attention to the radius of the arch, as the appearance of the entire arch will depend on its appearance. In this case, the edge can be used to display the very plane of the radius of the arch. At the same time, when processing the arch along the radius, try not to "climb" on the upper plane, as there will be visible scratches on it.
Constantly control your work with your hand, which helps to "find" existing irregularities.
When processing the upper plane, the width of the bar does not fit everywhere on the surface and it is necessary in these places, to work only with the end of the bar. Since there are still small irregularities here, it is already necessary to take a sandpaper for grinding P150 putty in order to finally process the plane.
The video shows (see above) that there is an edging above this plane, and you need to work carefully so as not to damage it.
Next, we will continue grinding the wing on the "boot", the master clearly shows which part of the wing bears this name - this is the lower part of the wing, which passes into the threshold.
This part is quite difficult, since it also has a radius part, a plane and transitional hard-to-reach places. Therefore, to process this area, we need another block.
The block is already of a different shape and, most importantly, it is quite soft and there are radius curves on it, which is necessary for processing in such difficult places of the wing. Thanks to this shape of the bar, rounded parts of the metal can be processed.
On the block itself, we initially "glue" P80 sandpaper to remove the rough parts of the putty and get to work. Do not forget that you need to grind with some margin for processing with the next "skin" number.
At the end of the "boot", if putty was applied, then you need to work very carefully so as not to hurt the neighboring area. If the butt was not putty, then it is better not to touch it, so as not to remove the paint and "open" the bare metal when it is necessary to process it again.
Grind a straight plane with a herringbone, because if you grind in a straight line, you can leave a selection on the putty.
In our case, it is not worth removing a lot of putty, since there are still places where it will still need to be applied additionally. If anyone has watched the previous videos, they will remember that in this place there was a seam from welding and the place is quite difficult.
The video shows that small "bumps" have appeared along the edges of the plane, which means that a hole has formed in the center, respectively. Therefore, here you will need to apply a small additional layer of putty.
While we are finalizing the rest of the arch, we work very carefully, without much effort, especially at the ends.
Also, in places where the metal protrudes, this "shows" that there is a small hole and you will also need to apply a layer of putty. Therefore, in such places it makes no sense to further grind, since revision will be needed with the application of an additional layer of putty.
It should also be noted that when working with adjacent planes that border, and in our case, this is a door, you should always check the transition of the planes. This is done so that in these places everything is smooth and there are no pits or bumps.
In this case, you can finish with the arch, then it will already be processed with P150 sandpaper in order to remove the risks from the previous P80 paper.
Next, let's deal with the grinding of the putty on more or less even surfaces. In our example, in this area, the putty is green, since the material used is fiberglass.
The application of this putty was described in the previous video (see part # 8). There was a difficult area with an old putty applied by a previous master, and traces of rust on the plane. All this was completely removed and cleaned to pure metal.
There is a small radius on the wing itself, which must be taken into account when processing the putty.
Useful advice. If you work with any plane, for example, after an impact and do not know exactly how it should look “live”, then you can always look at this plane on the other side of the car body. Since both planes are mirrored, you can compare in order to understand how it will look after repair.
For grinding the putty, again a hard block and P80 sandpaper are taken. In this case, it is the P80 that suits perfectly. This is due to the fact that the filler with fiberglass itself has a rather rigid structure and, moreover, a rather thick layer is applied in this place.
Fiberglass putty is rather poorly sanded due to its rigid structure, for this reason it must be sanded with P80 / P120 sandpaper. It is not recommended to work with smaller skins, as this will be more problematic and ineffective.
Anyway, in the future, this area will need to be re-putty with a finishing putty.
As always, we work with a herringbone so as not to leave a selection on the processed plane. When working, always check the surface to be treated with your hand to feel any imperfections (pits, bumps), thereby controlling the process of work.
When a bump or visible hole appears, the sanding process in this place must be stopped, as additional application of putty will be required.
It is worth mentioning that when grinding the putty of any planes, they must be repeated with the movement of the bar.When there is a radius, it must be sanded with a repetition of the bending angle, if the plane is flat, it is leveled as a flat surface under a large block. This method is applicable to all planes, and is selected depending on the specific part that we want to get in the end.
So, the preliminary grinding of the part is finished and you can already see what the result is. Now you can clearly see all the pits, the existing cones and it is immediately clear what to do to level this area.
In the place of the wing, where the putty with fiberglass was applied, we will also apply a layer with fiberglass for now, as you can see still deep pores. We will cover the upper part of the wing, over the area with fiberglass with a universal putty. In this place, the irregularities are small and the universal putty will lay in a thin layer, which is what we need to remove the slight waviness of the part.
Next, let's move on to sanding the putty on flat surfaces. In our case, this will be shown on the example of a door.
As in the previous cases, take a hard block and initial P80 sandpaper for the first layers and light sanding of the work surface. Then we move on to P150 and further preparation under the ground. We work by hand, as usual, with a “fir-tree”.
At the same time, we try to work with our hand precisely on the putty itself, without hooking the non-putty section of the door. You can go slightly beyond the putty area for better leveling of the plane.
In this case, you need to ensure that you do not "climb" on the adjacent part. In our case, we opened the door so as not to touch the plane of the threshold during operation. If you grind with the door closed, then for reliability you need to close the adjacent area so as not to damage it.
Do not forget to leave a layer of putty under the next sandpaper P150. It can be seen that the ends remain and now we remove the transitions and align the plane. At the same time, this "sandpaper" can already handle the area somewhat wider than the putty plane, in our case it is possible to "reach" the very edge on the door.
Addition. Quite extensive planes, as in the example of this part - it is possible and necessary to grind under a longer bar if the plane to be leveled has large volumes and waviness.
We check it with our hand in the course of work, to determine the irregularities. It can be seen that the plane of the door has gone spots, which shows the alignment of the plane.
So, having finished processing the plane under the P150, it is clearly visible that the putty places were shaded and the hard boundaries of their transition were gone. Small pits and irregularities are now clearly visible.
Further, P220 or P240 sandpaper will be used for processing in order to interrupt the risk from the previous P150 and prepare the plane already for applying a primer.
On all parts where an additional layer of putty is required, it will be applied, processed and in the next parts of the video we will talk about preparing the surface for the ground.
So, in general, it was clear the principles of applying and grinding the putty, as well as what is needed for the work, what tools and materials need to be prepared.
Also, what should you pay attention to in order to properly grind the car putty on the parts. In the next video, we will analyze how to finally finish the planes for applying the primer and analyze the existing nuances.
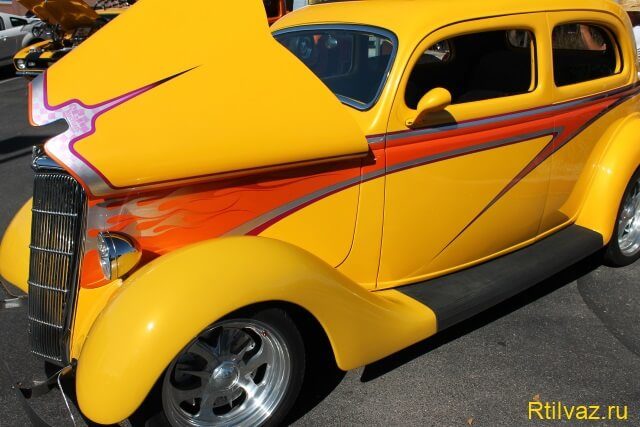
If you liked Vlad SchCh's video, then leave comments and like. And also if you have questions about the series, then ask in the comments, the questions will be answered.
Do not forget to look into the description, where there are a lot of videos, including the previous videos, regarding this project - "Preparing a car for a complete repainting from A to Z".
This concludes editing the article. Goodbye!
Grinding the car body is required to control and level the restored surface. To identify defects in the putty, before grinding, a special powder is applied to the working area, showing all the irregularities.Instead of powder, you can use graphite, crushed pencil, or carbon black. The application of the developing composition is carried out with a mesh.
ATTENTION! Found a completely simple way to reduce fuel consumption! Don't believe me? An auto mechanic with 15 years of experience also did not believe until he tried it. And now he saves 35,000 rubles a year on gasoline! Read more"
Grinding has another name - matting (matting). Matting is the procedure for applying small scratches to the body of a car with abrasive materials. The purpose of the manipulation is to improve the adhesion of all subsequent layers (primer, paint, varnish, and so on).
If the matting area is negligible, use plain sandpaper or tape-bright. Large areas of the body are processed with a grinder. At the same time, there is a certain relationship between the grain size of the abrasive material and the subsequent work:
- reduction of gloss before painting - an abrasive from P120 to P180 is required;
- cleaning the surface to iron - P80.
All work on grinding the car must be carried out in a mask, since the process is associated with a lot of dust formation. The mask can be replaced with a respirator.
Matting the surface of the car body is carried out with a special tool - this is a plane or a grinder. There are many options for the latest devices, but an eccentric or orbital sander is considered universal. Its scope is extremely wide:
- cleaning the car surface from the old layer of varnish and paint;
- processing of transition zones before local painting of certain areas;
- alignment of areas after applying filler (putty).
For grinding large and flat surfaces with high rigidity, it is advisable to use a surface grinder.
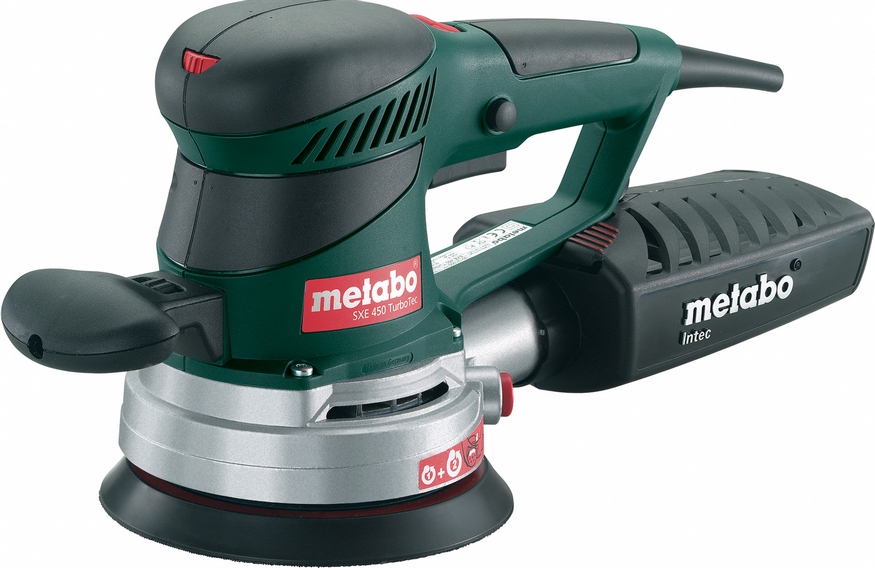
It is unacceptable to use surface grinding technique on curved, curved and thin-walled surfaces, this can lead to deformation of parts!
For problem areas of the car that need sanding, it is best to use a plane.
Grinding with an orbital machine has a high-quality result if the following rules are observed:
- it is necessary to regularly check the serviceability of the components: the dust extraction hose and the vacuum pump;
- during matting, the sole of the machine must be tapped periodically so that abrasive particles do not get clogged inside;
- you should not put pressure on the grinder, grinding occurs under the own weight of the device itself;
- the heating of the surface of the car body must be controlled, if required - to arrange technological breaks in work.
Compliance with these simple points will allow you to perform grinding efficiently and quickly.
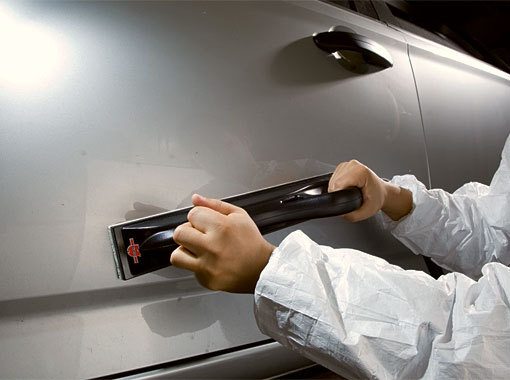
When processing a car body, it is generally recommended to use sandpaper or scotch-bright with your hands. In this way, areas with complex relief are matted; movements should also not be of the same type.
Wet sanding of a car means constantly wetting the body with water. A damp sponge is used for these purposes. The water must be changed frequently to avoid heavy contamination. After sanding with water, the body surface must be washed and wiped dry with a lint-free cloth.
The polyester filler coat can only be sanded dry, because the filler is very hygroscopic.
If smudges or light shagreen appear on the car body, grinding will be much more effective when a few drops of liquid soap are added to the water.
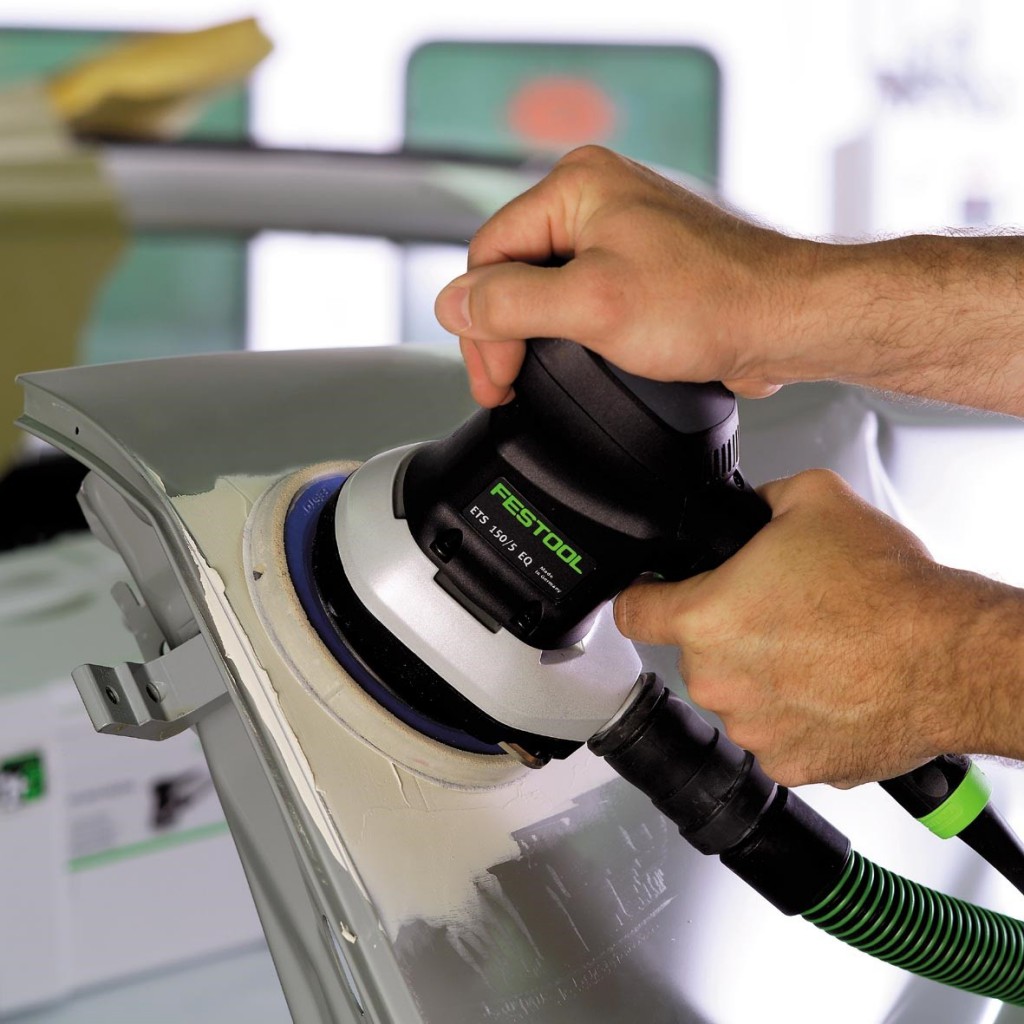
The basic configuration of any grinder implies the presence of either an electric drive or an air drive from a compressor. Many craftsmen prefer the first option, because pneumatic equipment requires a large volume of air and a powerful compressor. The volume of the compressor is impressive, as is the power consumption.
Pneumatic orbital sanders are a popular product among auto repair shops; for home use, an electrically driven device is sufficient.
Orbital grinding technique is selected according to the following parameters:
- power consumption of electricity (200-600 W);
- rotation frequency indicators (revolutions per minute);
- the rhythm of vibration of the sole;
- the presence of the function of adjusting the stroke of the eccentric in mm;
- the diameter that the work sole has (12.5 or 15 cm);
- are there holes in the sole for dust extraction;
- weight of the device (1-2.5 kg).
The basic set of the grinder contains a 6-sided wrench, with which the sole is installed and removed. There is also a dust collector, sometimes a spare handle. Many models are equipped with a function for connecting to a vacuum cleaner.
To grind the car body, in addition to the orbital machine, the master will need consumables for it, namely, abrasive mugs.
Orbital grinding equipment costs differently, depending on the brand awareness of the manufacturer. So, for example, a Rupes SL 42 AE plane (Italy) can be bought for 26 thousand rubles. Less well-known manufacturers offer more modest prices. For example, a pneumatic polishing machine JAS-6531 from Jonnesway (Taiwan) costs 9.7 thousand rubles.
The plane for grinding cars is used in hard-to-reach places and on curved areas. It can be produced in two different versions:
- with Velcro for sanding paper;
- equipped with clamps.
In addition to the design features, an auto plane can be of any size. The cost of the simplest product is from 300 rubles.
A hand tool for matting a car body is considered not only a plane, but also a lot of other devices:
- a rubber pad for sanding is an elastic rubber block with special clips for attaching sandpaper. Such a block can be used for dry and wet surface cleaning;
- cork pad for sanding, weighs very little. It can also be used for dry and wet matting of a car body;
- pads with clips made of plastics. The bottom of the device is additionally reinforced with a rubber gasket, which prevents the sandpaper from slipping off the clamps;
- long sanding blocks of sizes 40 * 7 cm. ERSTA542 sanding strips are consumables for such an analog of a planer.
In addition to the listed devices, manufacturers of equipment for body auto repair are constantly updating their product line, delighting auto repairmen with new and useful developments. But, despite this, the plane and grinder remain the most popular grinding tools to this day.
Forget about fines from cameras! An absolutely legal novelty - NANOFLENKA, which hides your numbers from IR cameras (which are in all cities). Read more about this at the link.
- Absolutely legal (Article 12.2.4).
- Hides from photo and video recording.
- Installs independently in 2 minutes.
- Not visible to the human eye, does not deteriorate due to the weather.
- 2 year warranty,
The preparation of the body part for repair is the most important starting point for achieving the best possible output quality. I hope no one will dispute this axiom?
So where should you start?
Take the front wing as an example.
To determine the nature of the damage and draw up the correct work plan, the suspected element should be properly washed. Moreover, after the water, wipe it with White Spirit and solvent. This action will give us a complete picture of the damage. It should be noted that behind a small defect in the wing (a scratch or a small dent), paint chips and other minor defects can also be observed. And, if it is destined to paint it, then it must be done with all dignity, regardless of different faces.
So, we found all the defects - what next? And, then we come to the conclusion that we will have to prime the entire element. Hence, the conclusion is that we remove all defects from the surface.
Let's imagine that we have a long scratch on the surface of the wing, forming a shallow dent, and several small scratches and chips.
What to do? - The age-old question of the Russian intelligentsia.

2. A scratch with a dent must be sanded down so that there are no sharp edges of chipped paint (If there is rust, remove it to zero). Do not be afraid to overwrite unnecessary things. We grind the scratch and its edges with an abrasive (sandpaper) P120. This is a fairly coarse abrasive grain, with which the best adhesion of the putty to the surface is achieved.
3. Next, we grind small scratches and chips. We expand them along the plane. So that there are no sharp corners and exfoliation from the surface.
4. Now, it's time to putty.
If you are not yet in the know, then great news for you - putty, it is not alone! She has many varieties. Let's start in order:


2. Filler with aluminum filler (coarse two-component filler-filler, for filling deep dents, as a primary layer). Excellent processing properties, low drying shrinkage.

3. "Universal" putty - (two-component), coarse enough to remove shallow dents and irregularities, usually yellowish in color.

4. Putty "Finishing", (two-component), usually white, perfectly processed. Apply over coarse filler for more precise alignment.

Having cleaned the repair surface with abrasive P120, we proceed to puttying. Do not forget to first degrease the repair surface. If traces of rust remain on the repair site, they should be treated with a "rust converter" according to the instructions on the bottle.
We knead the coarse putty with the hardener - stirring thoroughly so that there are no pink streaks (usually pink - hardener) and evenly fill the repair area with a spatula with light pressure. Do not try this procedure at one time. We applied, waited 10-15 minutes until the putty gets up. Usually, 3-4 kneading and greasing is required to achieve complete filling of the defective spot.
The next step is grinding.
We sand with an abrasive grain P120. Carefully, trying not to climb outside the repair area. (Otherwise, extra scratches - do you need it?)
To achieve safety, cover the repair area with masking tape, preferably in two or three layers. For better control, before sanding, I highly recommend wiping the surface to be treated (dried filler) with black developing powder. It will be easier to control defects (where putties should still be greased).

When sanding a part, pay attention to abrasions. If the metal has begun to protrude, then there is no point in rubbing further - you need to add putties (to fill the gap formed between the wiped areas).
Remember! The putty is much softer than paint (varnish), and even more so than metal, therefore it can be wiped off with a sandpaper faster and easier. Therefore, if metal begins to show through on the surface to be treated, stop sanding and add another layer of putty.

Do not forget to rub the surface to be treated with black developing powder.
Now! When it seems to us that everything is fine, we will apply the most finishing putty to the entire repair area with a rubber spatula (preferably white or transparent silicone - it does not leave traces of black rubber) (in the photo it is Nitrosoft). It dries quickly and fills all small pores on the treated surface, punctures, cavities and microcracks formed when the rough and finishing putty dries. But, this is not a "panacea", do not try to cover up the irregularities that are felt by the hand! For this there is - the finish line.
Note: Afraid of solvents!
This means that after using this putty, it is forbidden to use solvents for degreasing!

As a result, we must (and this is our main task) to get the perfect surface.
The next step is priming and painting.
![]() |
Video (click to play). |
When writing the article, photographs of materials from NOVOL, MIROX and BODY were used. This in no way means that there are no more other manufacturers and in no way is it an advertisement of these companies. Choose a line of manufacturers for you. I used only what came to hand.