In detail: hansa washing machine do-it-yourself repair from a real master for the site my.housecope.com.
This washing machine was purchased at the end of 2005 in Technoshock. Hansa Comfort 1000 spins at a speed of up to 1000 rpm, respectively Comfort 800 - 800 rpm. If memory serves, there was also a model with a spinning speed of 1200 rpm.
The error codes and the principle of repair are the same for the Comfort line. Therefore, below I will give a table with errors for Hansa washing machines
The error can be caused by the following reasons:
- the door is open;
- damaged wire connections from the controller to the door lock;
- the lock or limit switch is faulty
The error can be caused by the following reasons:
- low water pressure;
- partial blockage of water supply hoses or solenoid valves (also if they are faulty)
The error can be caused by the following reasons:
- low pressure or lack of water in the water supply;
- blockage of water supply hoses;
- faulty water supply valve;
- the water level sensor (pressure switch) is faulty;
- the electronic controller is faulty or the wiring between it and the level sensor or valve is damaged;
- blocking of the reset valve in the "off" position (in a washing machine with the Aqua Spray system)
The error can be caused by the following reasons:
- partial blockage of the drain pump filter (also if it is faulty);
- partial blockage of the drain hose
The error can be caused by the following reasons:
- the drain pump is blocked or faulty;
- complete blockage of the drain hose;
- the pressure switch or its wiring is faulty;
- blocking of the reset valve in the "on" position (in a washing machine with the Aqua Spray system)
![]() |
Video (click to play). |
The error can be caused by the following reasons:
- one or more water inlet valves are blocked in the "open" position;
- during the washing process, there was a significant increase in the water pressure in the water supply;
- defective pressure switch
The error can be caused by the following reasons:
- the drive motor (tachogenerator, thermal switch) is faulty;
- loose wiring between the drive motor and the controller board
The error can be caused by the following reasons:
- there was a leak of water into the pan of the washing machine, due to the depressurization of the tank, its connections or hoses;
- faulty float sensor AQUA STOP
For 8 years of operation, there were no particular complaints. Errors that were E01 due to a not tightly closed door, E05 due to the fact that he forgot to open the riser with cold water, E03 periodically due to contamination of the drain filter and E07 due to water getting into the pan of the washing machine inside.
It was the cause of error E07 that I eliminated in this photo report. The fact is that during periodic cleaning of the drain filter, it is necessary to drain off excess drains using a black hose in order to unscrew the lid. But since the hose is low enough, some of the effluent gets inside the machine. I have never had any depressurization of the tank.
So, when turned on, the machine issues code 07.
On the spot. You don't have to disassemble the washing machine, just wait a couple of three days for the water in the pan to dry.
To solve the problem, you need to remove the lower front cover, therefore the installed machine does not even need to be removed from the niche. It is necessary to unscrew only 2 self-tapping screws at the edges.
Then you need to pull the bottom cover towards you. The groove from which you need to pull the front cover is marked in blue.
Do not forget to take out the black hose marked with a blue arrow.
View of the washing machine with the bottom cover removed.
Julia wrote on 05/29/2018 [12:31]
The machine gives errors:
P007, E321.There are no such codes anywhere in the manual and description! It erases and cuts itself and corks, can do it at the beginning and at the end! All the masters looked and said with 100% certainty that it was Ten! We replaced it, but the problem persists.
Zoya wrote on 03/09/2018 [00:45]
Hello!
Comfort 800. It collects water and immediately drains it. But if you turn off, or rearrange the program, next time it may work fine
Alexander wrote on 12/04/2017 [17:06]
Nansa gives error E 22 and E 21, how to fix
Ivan wrote on 09/13/2017 [01:14]
In the beginning there was an error e07 how to fix it?
Natalia wrote on 03/07/2017 [20:54]
Hello! Does anyone have a faulty Hansa900 comfort clipper? Need a door from it. A neighbor tried to open the door and broke it. The machine generated error N7, but the “smart” neighbor continued to rape and try to open the washer. The result is that things go out in the machine for the 3rd day, the door is locked and broken so that it cannot be opened. Now just hack.
Dmitry wrote on 03/05/2017 [15:45]
Hansa optimum800 It draws water and turns off, the door lock indicator starts blinking and clicks are heard.
Victor wrote on 03/02/2017 [23:58]
Hello everyone! I would be grateful for your advice. Washing machine full size HANSA AWN 610 DR. The machine is new, in operation for 7 months. but purchased 1.5 years ago, so the warranty has passed. The cause of the malfunction is as follows, after 10-15 minutes. wash starts to squeak and stops, then scrolls 2-3 times and beeps again. + in addition, when you select a mode, the first mode is immediately remembered when you scroll the mode selection roller. The option is to set the desired mode, and then turn the plug into the socket. What could be the reason? Thank you all for your answer!
Tolyan wrote on 01/20/2017 [12:39]
Why isn't my washing machine picking up speed? Who can answer this question?
Sergey answers:
Does not gain momentum during spinning. There may be several reasons for this. The first is the uneven distribution of the laundry. In this case, the machine tries to balance and turns the drum in one direction or the other.
Another reason may lie in a malfunction of the triac of the drive motor.
It is also worth checking the condition of the brushes, perhaps they are almost worn out and require replacement.
Natalia wrote on 12/19/2016 [18:12]
how to assemble a hook to close the door at the hansa optima 800 washing machine
Anna wrote on 09.10.2016 [16:53]
Good day! After washing, there was water in the tank, everything was cleaned out of the filter, the water was knocked down. But it still gives an error E 01 and does not get cleaned. Help to solve the problem.
Few people complain about the quality of washing machines, which are produced under the Hansa brand, for several reasons. These washing machines are not as common as, for example, the brands LG, Samsung, Indesit or Hotpoint Ariston that have flooded the shelves of all stores, similar machines have appeared on the Russian market relatively recently, and their quality can be considered good. A logical conclusion suggests itself: if such machines were in every house, there would be much more repair practice.
At the moment, we can talk about typical malfunctions of Hansa washing machines, only according to the rather meager statistics that were provided to us by the largest service centers in the country. After analyzing this data, we identified the weak points of most models of machines from this company.
- The drain pump breaks down (and quite often).
- The drain filter and pipes are clogged with dirt and debris.
- The Aqua Spray system refuses to work.
- Closes the temperature sensor.
- Frequent freezes of the machine occur due to power surges.
For your information! In occasional cases, problems with the electronics and the leakage protection system appear; this system simply does not work correctly.
A clogged filter and hoses are at the top of Hans' washing machine breakdowns.There is nothing unusual about this, since it is one of the main problems of all automatic and semi-automatic washing machines. If the filter and drain hose of the Hans machine are dirty, you do not need to contact the master, repairs can be done by hand. Cleaning the filter of a washing machine is a fairly simple process, described in detail in the instruction manual.
It is also easy to clean the drain hose, here more problems arise during its installation / dismantling. It will not work just like that to unscrew the drain hose from the body of Hans' car; you will have to climb into the body. We do the following:
- unscrew the back wall of the washing machine;
- we find the clamps connecting the drainage hose to the pump and weaken them;
- we disconnect the drain hose and rinse it with water, in order to better remove dirt, you can use a drain cable;
- connect the drain hose and drain hose back and screw on the back of the machine.
Important! The drain hose must be cleaned even if Hans's washing machine is working properly; for prevention, the procedure is done about 1 time a year.
It is not difficult to clean the filters and hoses with your own hands, but what to do if the pump breaks. Specifically, in Hans' washing machines, the pump breaks down quite cleverly. The "symptoms" are as follows:
- at first, the machine sometimes freezes, while the water is not drained, but after restarting everything starts to work;
- after some time freezes become more frequent, especially after washing in hot water, restarting the program does not solve the problem, but after the water cools down, the machine continues to work properly;
- periodic freezes continue for quite a long time, after which the machine completely stops draining water.
What do these symptoms indicate? And they say about a malfunction of the pump impeller and urgent repair is needed. Is it possible to carry out such a repair with your own hands - quite, the main thing is to follow the instructions of the specialists.
- First, drain the water by unscrewing the drain filter plug (do not forget to place a suitable flat container under the machine).
- We remove the powder tray.
- We put the washing machine on its side.
- Unscrew the bottom, if your model does not have a bottom, this is even better.
- Disconnect all wires from the pump.
- Disconnect the impeller and check the interior of the pump for debris.
- We install a new original impeller.
- We connect the wires to the pump, tighten all the fasteners, put the machine on its legs, connect it to the communications and check the work.
For your information! Repairing the impeller of the pump of the Hans washing machine will cost you about 250 rubles, provided that all the work is done by hand. If you use the services of a master, then this is somewhere from 1,500 rubles and more.
Often, with Hans' washing machines, a problem arises in which they refuse to pour water into the tank, respectively, the washing does not start, and the system error E05 "pops up". In this case, it is most logical to start by checking the filler valve, because its task is to ensure that the tank is filled with water. We remove the top cover of the washing machine, inspect the filler valve, check the resistance with a multimeter and make sure that the valve is working normally. It would seem a dead end, but no!
The fact is that Hans' washing machines are equipped with the Aqua Spray system, the path of this system goes from the filler valve to the tank. Thanks to this system, jets of water forcefully spray the laundry in the drum, thanks to which the dirt stains are better removed. The disadvantage of the system is a rather complicated and in some places rather thin water supply path, which may well become clogged., which is what happens. The reason for this is the salts of heavy metals contained in the water, they are deposited in the tract, clogging it over time. How to carry out repairs yourself?
- We find the Aqua Spray system tract next to the filler valve.
- We unscrew the protective plugs.
- We take a bottle of water, pour water into the tract and check how well it goes into the tank.If the tank becomes clogged, the path will fill with water, and this will mean that it needs to be cleaned.
- We take a thin wire, clean the sharp edges with sandpaper and begin to clean the tract, periodically spilling it with clean warm water. You can pre-dissolve a little citric acid in water.
- As soon as the water passes freely, we assemble the machine, connect it and check it.
Most modern Hans washing machines are equipped with a surge protection system. The protection is mainly intended to save the control unit in case of short circuits and other problems with the electrical network. The idea of the manufacturer is good, but the execution let us down.
The Russian electrical network is far from perfect, drops happen often, but Hans' machine is sensitive to this. At best, at the slightest voltage drop, it will stop the washing program, at worst it will turn off, and the services of a specialist will be required to restore the “home assistant” to work.
Is it possible to carry out repairs by hand in this case? The answer is "no", in such a situation only a specialist will help. But you can prevent similar problems in the future if you connect your washing machine through a stabilizer. Modern stabilizers for washing machines will make the operation of equipment more reliable, moreover, several units of equipment can be connected to one stabilizer, which is also good.
Important! Choose wisely when choosing a stabilizer for your washing machine, because it is not a cheap but absolutely necessary purchase.
To summarize, we note that there are not so many weak points in Hans' washing machine, but those that do exist can manifest themselves in the form of a malfunction at the most inopportune moment. In some cases, it is quite difficult to diagnose such malfunctions, so you may need the help of a professional.
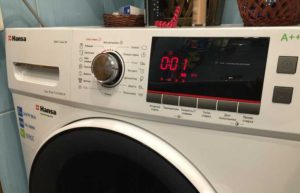
The existing ability to automatically check for failures that occur during the operation of the machine displays problems in the form of an error code. He will tell you where to look for the problem and what to do in a similar situation.
Consumers hardly ever complain about the brand's washing machines, and for good reason. The models are not very common when compared with Indesit, Ariston, Samsung, they appeared on the Russian markets not so long ago, they have good quality. Even a pattern appears - if everyone has such models, then the repair of Hansa washing machines will become more frequent.
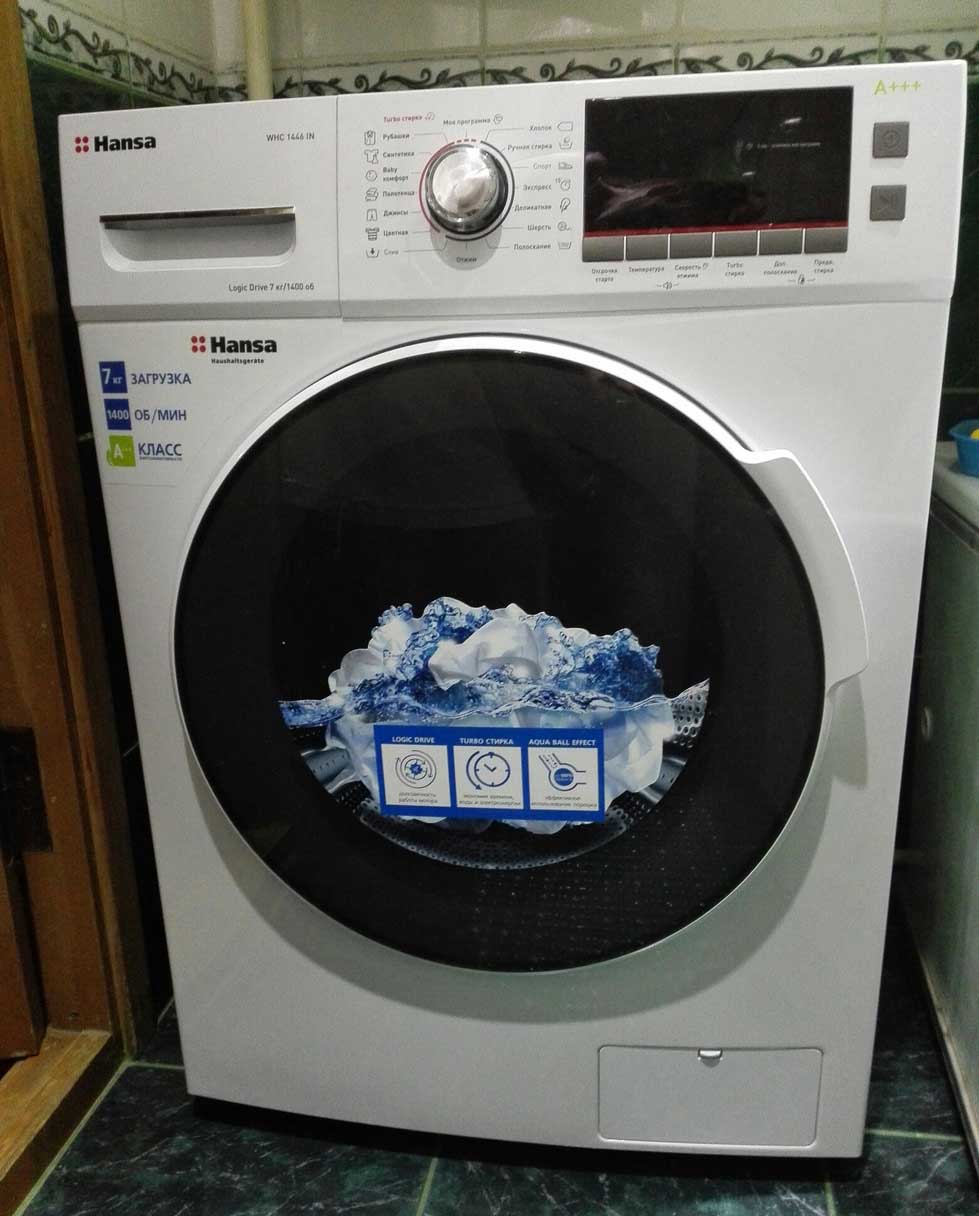
Today it is possible to talk about the most frequent failures of Hans washing machines, using rather scanty statistics provided by large repair service centers. After analyzing this information, we identified the vulnerabilities of machines from this manufacturer:
- quite often the pump that is responsible for draining the water fails;
- the filter and drain pipes are clogged;
- the AQUA-Spray system breaks down;
- short circuits occur in the temperature sensor;
- the machine often "freezes" due to a voltage drop in the electrical network.
Very rarely, but there are problems with the electronic control and the system that protects against water leaks.
In certain situations, it is quite possible to eliminate the failure of the machine with your own hands.
- Clogged filter, pump failure.
The first place in the rating of malfunctions of these machines belongs to the filter and hose clogged with debris. There is nothing strange in this, since such a reason really most often arises in automatic and semi-automatic washing machines. In such a situation, there is no need to call the wizard - you can fix everything yourself.
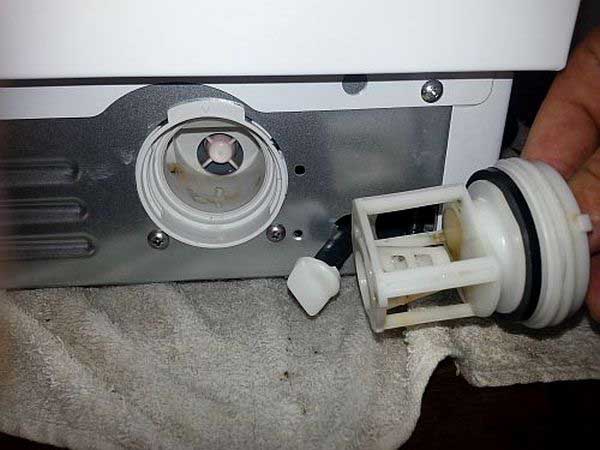
Cleaning the filter is an easy process that is detailed in the instruction manual. Removing the blockage in the hose will not cause difficulties, but you will have to tinker with its installation / dismantling. In order to unscrew the drain hose, you will have to climb into the unit body:
- you need to unscrew the back panel;
- find the connecting clamps for the hose and pump, release them;
- disconnect the drain hose, rinse it, clean it with a cable;
- connect and assemble in reverse order.
Remember that the hose should be cleaned, even for preventive purposes, once a year.
But the pump in a typewriter of this brand breaks down quite unusually:
- the machine starts to hang from time to time, the water does not drain, but when a reboot is performed, then everything starts to work normally;
- after a certain time freezes become more frequent, especially after washing with hot water. Restarting the program does not fix the problem, but when the water cools down, the machine continues to work normally;
- such problems arise for a long time, then the washing machine completely stops draining the water.
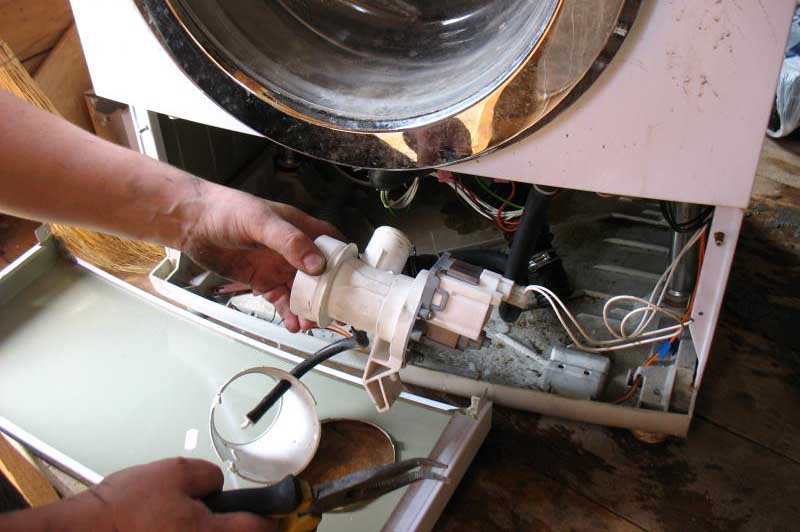
What conclusions can be drawn from such symptoms? Most likely, the impeller on the pump has failed, it is necessary to carry out repairs. Such work is quite within the power of every consumer, if all the recommendations of professional specialists are followed exactly. The list of works is as follows:
- first, the water is drained, for which it is necessary to unscrew the drain plug by placing a container under the machine;
- the detergent tray is removed;
- the washing machine turns over on its side;
- the bottom is unscrewed, if any;
- all wiring is disconnected from the pump;
- the impeller is removed, the pump is checked for clogging;
- a new impeller is being installed;
- the wiring is connected, the fasteners are tightened, the machine is installed on the legs, connected to the communications and checked for serviceability.
- Heating element failure.
Heating elements fail quite often. This can be caused by power surges. The element is damaged from a short circuit. In addition, due to the hardness of the water, scale forms on the heating element, it overheats and burns out.
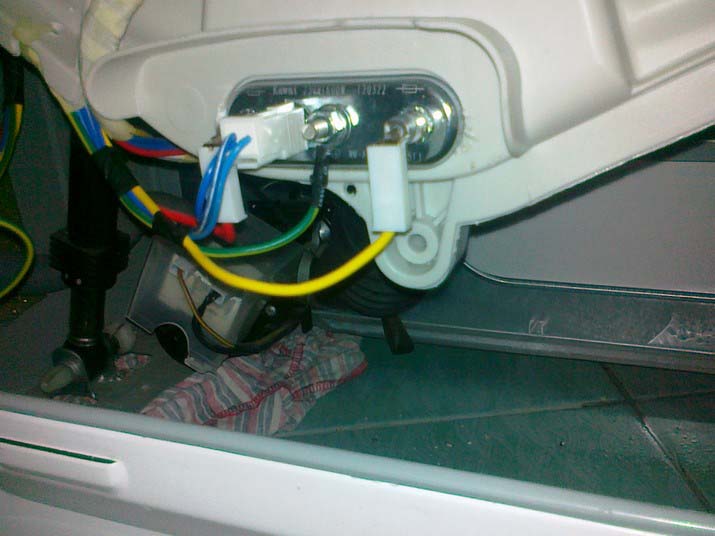
It is possible to determine the breakdown of the heater by its external signs. If, after turning on the machine, the machine in the panel is de-energized, the fuse blows out - look for the problem in the heating element. The second sign is that things are poorly washed, there is a musty smell, since the water does not heat up.
To replace the heating element, you will have to remove the front wall and follow these steps:
- at the base of the drum we find the heating element;
- disconnect all wires;
- we loosen the nut located in the center, push it inward, while squeezing the gasket;
- we remove the heating element, install a new analogue in its place.
- Failure of the Aqua-Spray system.
Often in such a machine there are problems in which they do not pump water into the tank, from which the washing process does not start, and the error code E 05 lights up on the screen.In this case, it is necessary to start the check from the inlet valve, since it is he who is responsible for pumping water ... Having removed the top panel, we check the valve, use a multimeter to measure the resistance values. If everything is in order, go to the AQUA-SPRAY system, which runs from the inlet valve to the tank. With its help, the water flows over the laundry with strong jets, from which stains are removed more efficiently. The disadvantage of the system is a complex and sometimes thin path for fluid supply, which can quickly become clogged with salts and metals in the water. What to do in such a situation?
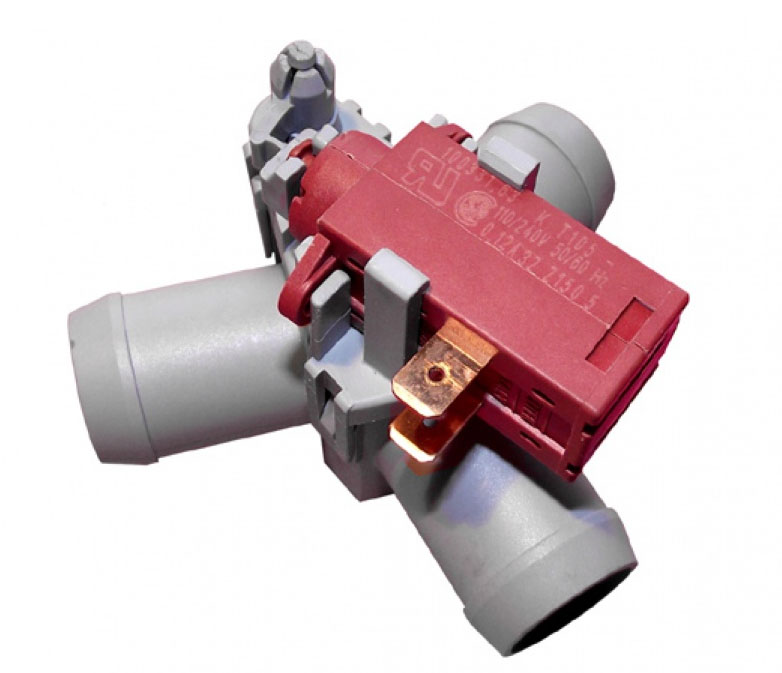
- find the path of this system near the inlet valve;
- remove the plugs;
- take a bottle of water, pour it into the tract, check how well it goes into the tank;
- if a blockage is found, we clean the tract with a thin wire, pouring warm water into it from time to time. It will be nice if you first dissolve citric acid in it;
- when the water begins to pass without interference, the machine can be assembled and a test run can be carried out.
- Problems with the electrical network.
Most models of washing machines have a surge protection system. The protection is intended for the safety of the unit responsible for the control if a short circuit or other problems with the electrical occurs. Initially conceived well, but the quality of the work was not up to par.
The machine still retained its sensitivity to voltage surges in the Russian power grid. At its best, it stops the program of work or simply turns off. But only a specialist can restore her working capacity. In such situations, performing repair work on your own is strictly contraindicated. But you can avoid such troubles in the future by connecting the washing machine through a stabilizing device.
Such a problem can be recognized by the characteristic grinding sound that occurs during washing. It is difficult to replace bearings in a typewriter, but it is possible to do such work with your own hands:
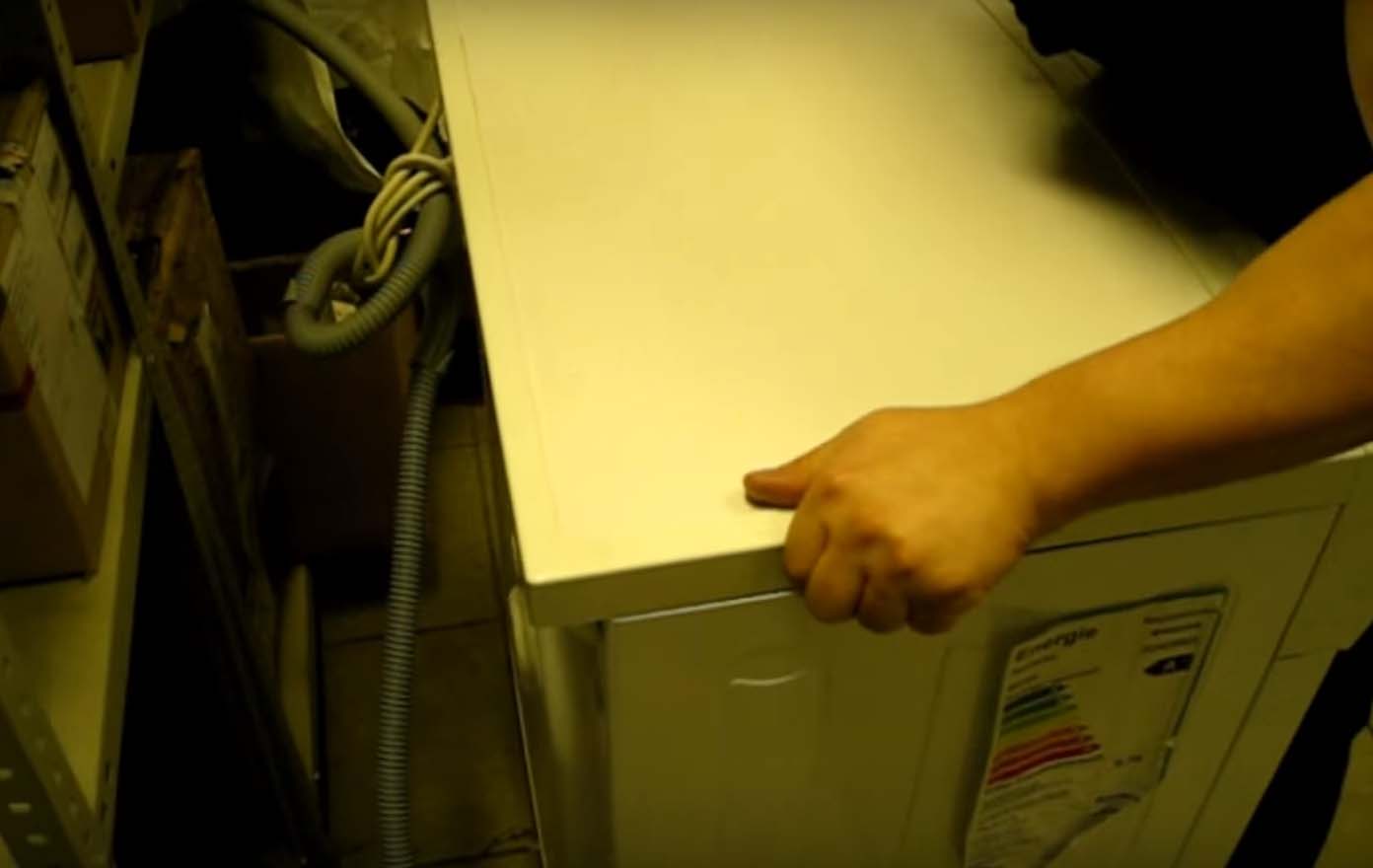
- unscrew the fasteners, remove the counterweights in front and on the sides;
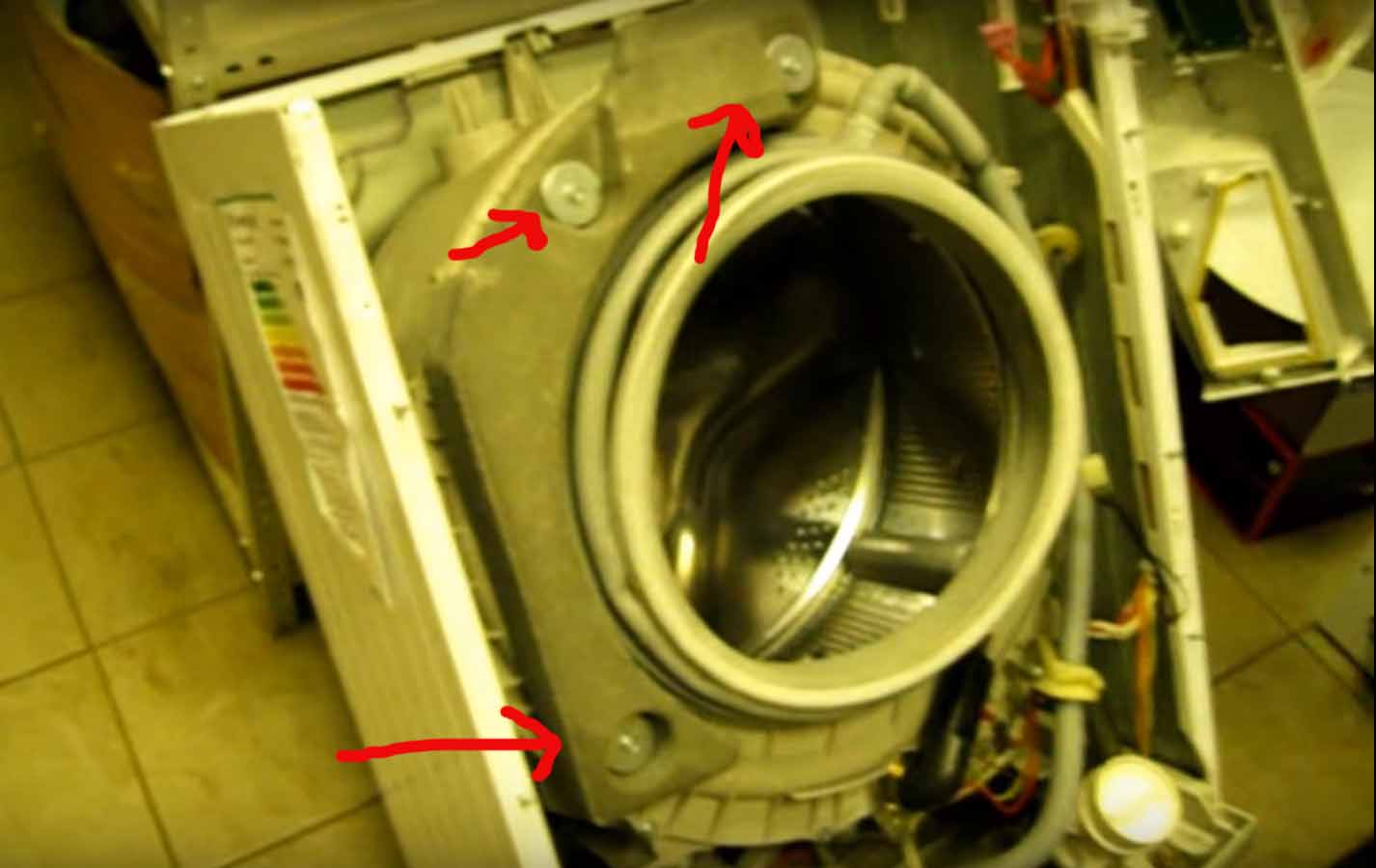
- disconnect the clamps holding the AQUA-SPRAY system path, move it away from the cuff;
- unclench the harnesses, unscrew the mounting bolts, remove the electric motor;
- loosening the clamps, remove the drain pipe;
- dismantle the tank from the shock absorber elements, lay it on a flat surface.
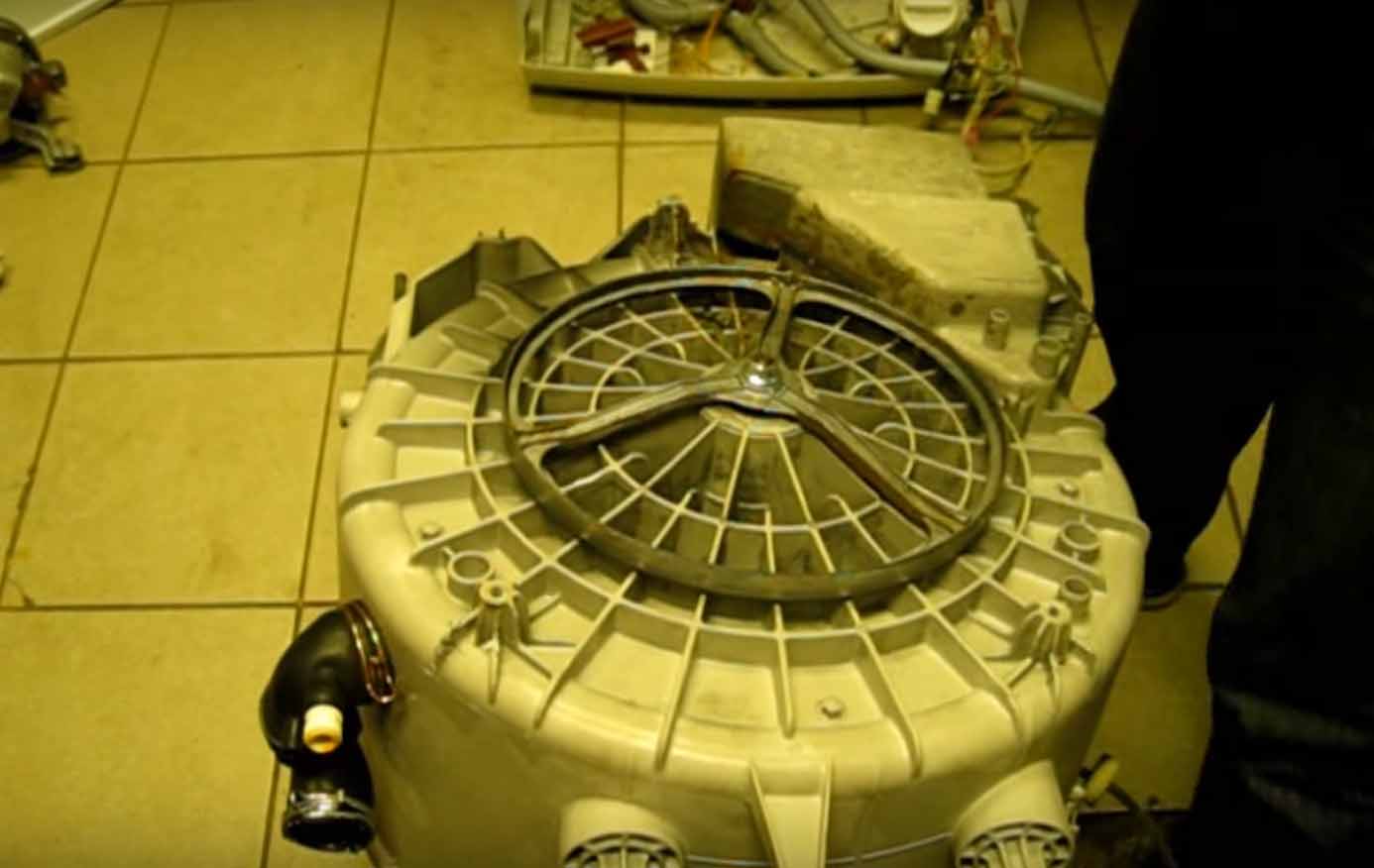
Now you have to disassemble the tank itself:
- unscrew the nuts, remove the pulley;
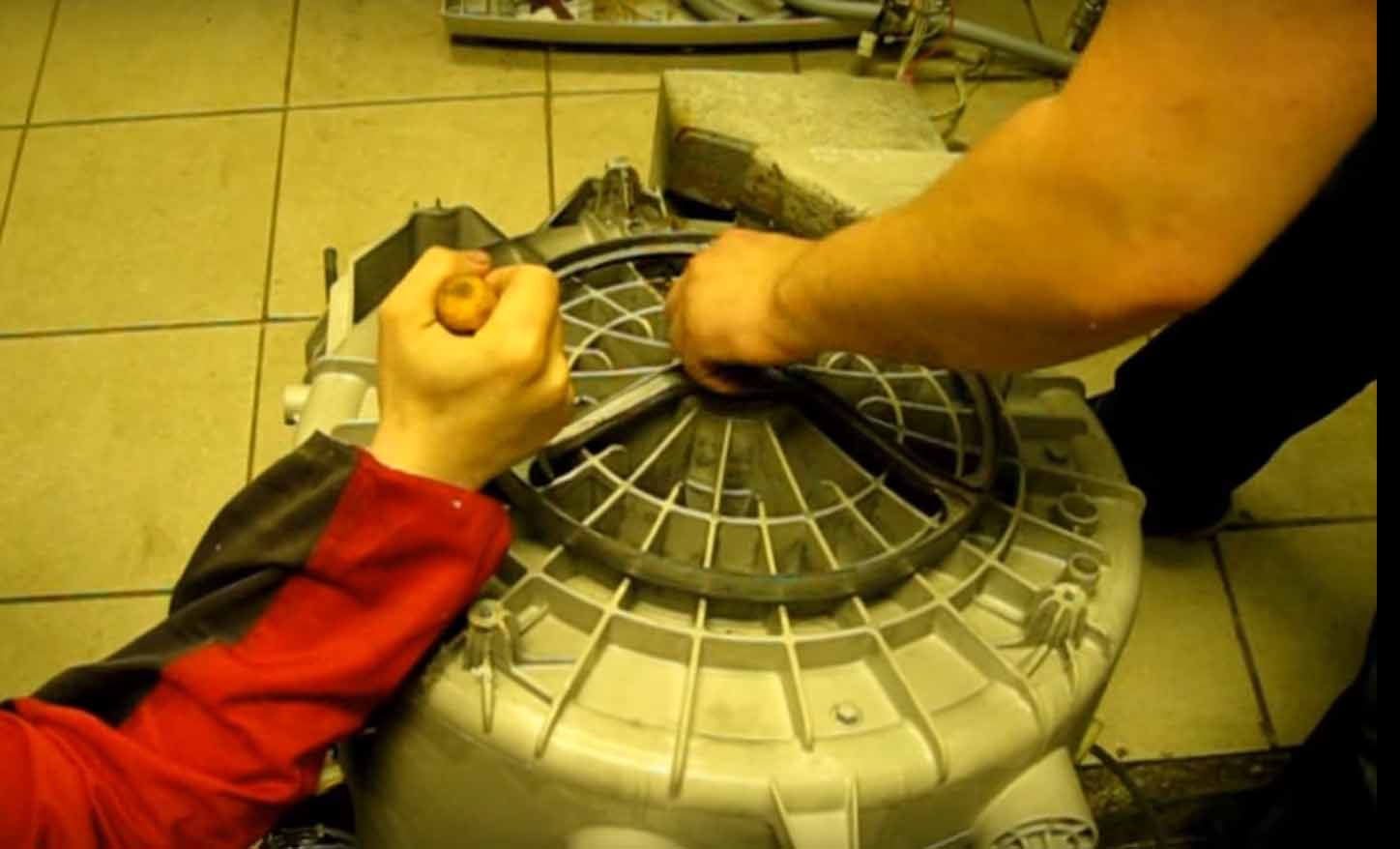
- turn the tank over, unscrew the nuts around the entire perimeter;
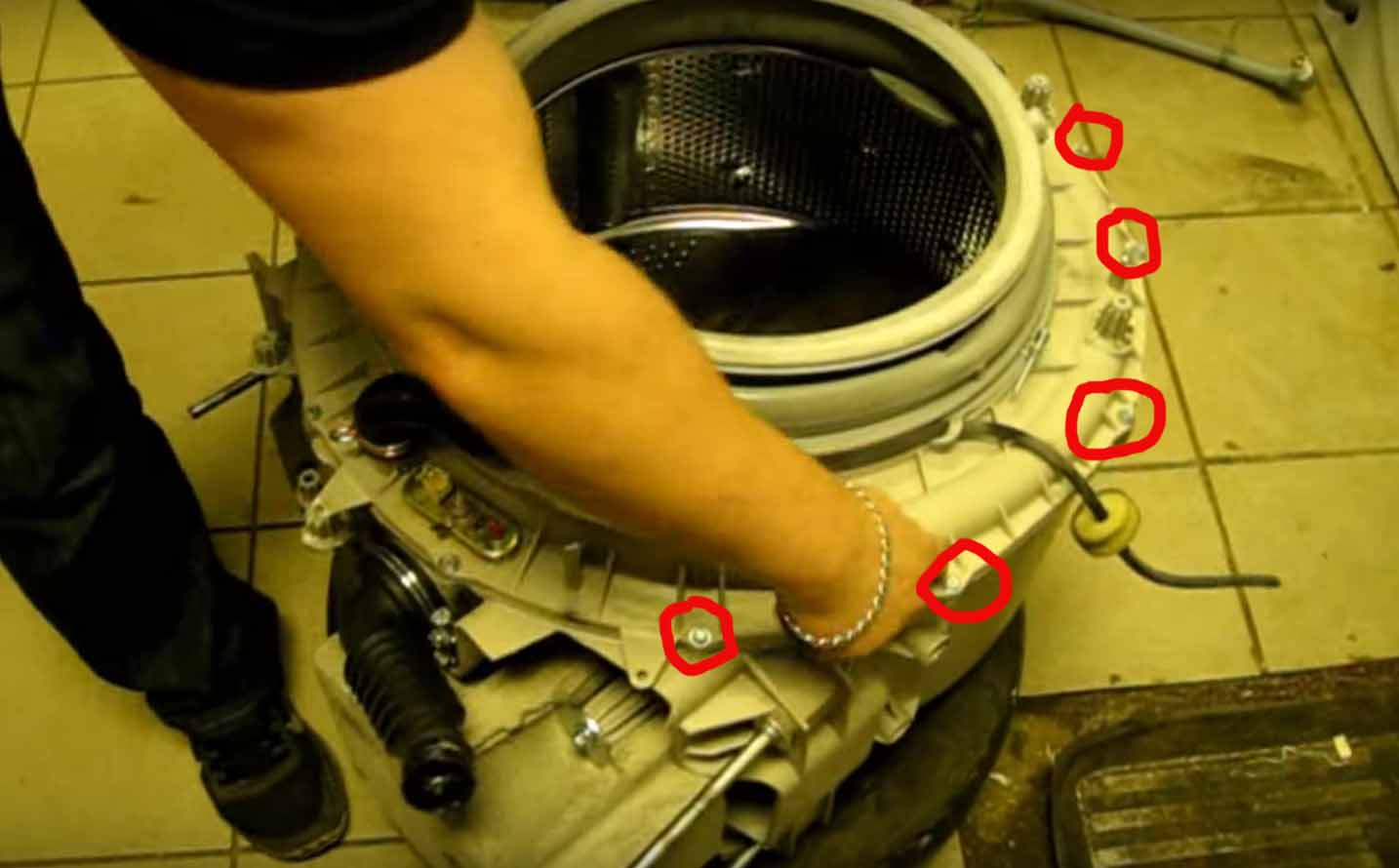
- remove the cover, push the bolt inward, take out the drum.
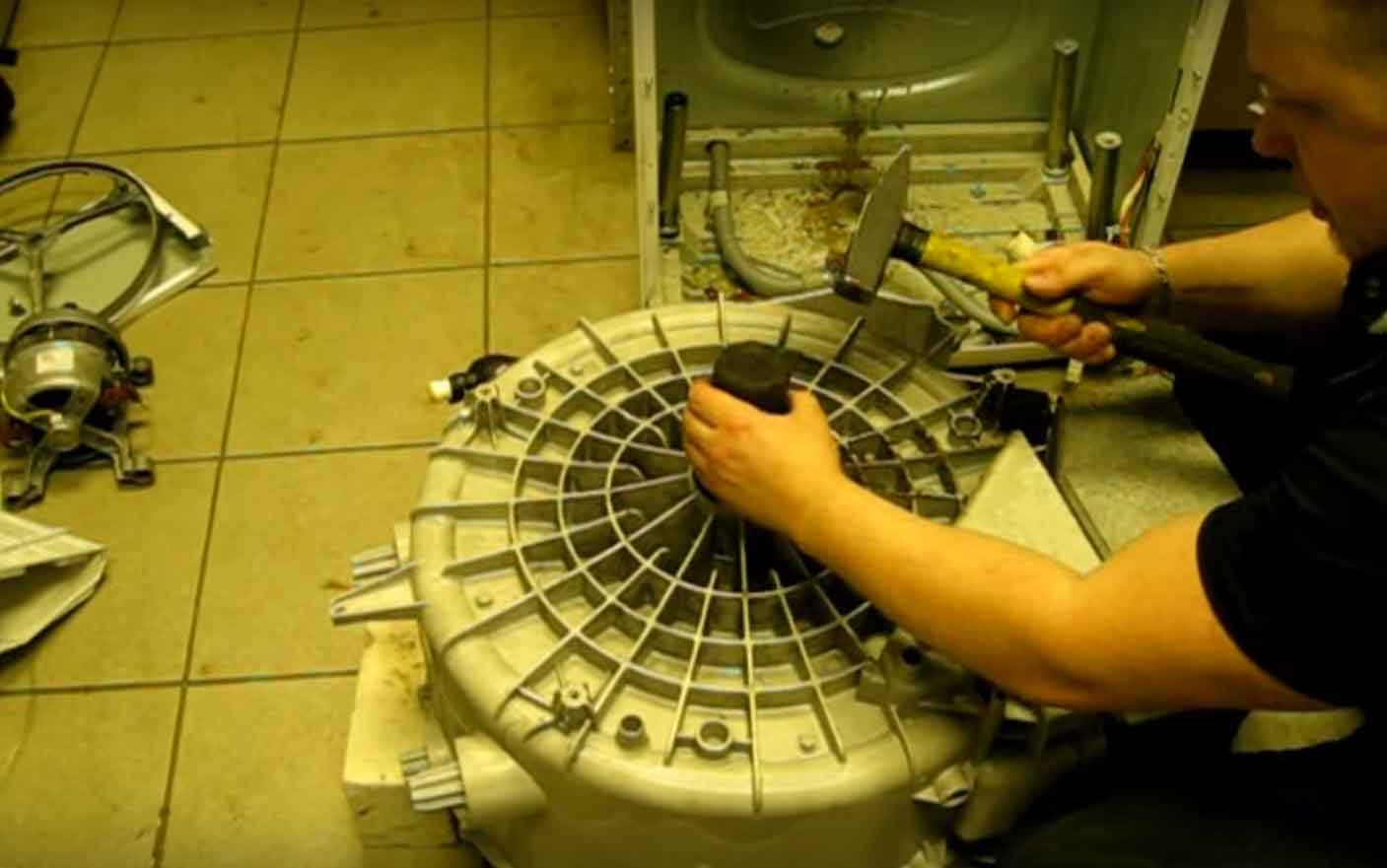
It remains to get the bearing and replace it. Now we assemble the unit in reverse order and check it in operation.
As a result, it should be noted that there are not so many weak points in the Hansa washing machine. But they are also capable of manifesting themselves as malfunctions at the most inopportune moment. In some situations, diagnosing such breakdowns is a rather difficult process, for this reason you will need the help of an experienced specialist from the service center.
The products of the Polish company Hansa entered the Russian market recently, but they have already managed to gain a good reputation.
Buyers of washing machines of this brand are attracted by their pleasant appearance, reasonable price and reliability of a sufficiently high level.
Nevertheless, some Hans models cause trouble to owners in the form of various kinds of breakdowns. Some of them can only be fixed at a service center, but many can be fixed at home. So, Hans' washing machine - DIY repair.
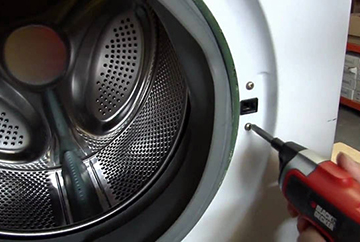
It is they who fail most often. The list of "unreliable" includes a drum and a pump, a drum flywheel and oil seals. The electronic modules of the unit also have complaints.
Often, machines fail due to clogging of the drain mechanism or the inlet filter. A suspicious noise indicates wear on the drive belt, brushes or bearings.
It happens that the electronic controller fails. The machine refuses to carry out the washing program, its drum begins to rotate only in one direction, the machine does not turn on or turns off spontaneously - this means that some kind of defect has formed in the memory of the device.
In some cases it is necessary to change the electronic board, and sometimes it is enough to reprogram it.
Eliminating problems with electronics is the work of specialists, at home you cannot cope with it.
Self-repairs lend themselves to malfunctions concerning the mechanical part of the machine.
- screwdrivers - cross and flat;
- wrenches (flat) - 19 and 8/10;
- pliers for unclamping clamps;
- pliers;
- nippers.
You will also need a special tool - a service hook.
If bearings are to be replaced, stock up on a set of end fittings, an extension cord for them, and a screwdriver. You will also need bearing pullers, a special lubricant - a waterproof bearing repair kit.
Elimination of any malfunction in the washing machine begins with its disassembly.
The first step is to remove the top panel. It is secured to the casing with Phillips screws. Having unscrewed them with a Phillips screwdriver, lift the rear side of the panel and slide it towards the rear of the car until it is completely free. After that, the part can be easily removed.
Further actions depend on what kind of damage is planned to be eliminated.
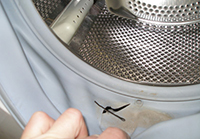
You can find all about the repair of Zanussi washing machines with your own hands here.
This information https://my.housecope.com/wp-content/uploads/ext/740/cancliz/mnogokvartirnyie-doma/santehnika/stiralnaya-mashina-ardo-remont-svoimi-rukami.html will help you deal with the main breakdowns of washing Ardo machines. You will learn what to do if the unit does not drain or heat the water, and also why the machine makes a lot of noise.
Following the top panel, the control panel is dismantled. It is held in place by two screws. To get to them, you need to remove the detergent dispenser hopper.
Having released the control panel, it is pushed outward and rotated almost 90 degrees (until it is completely disengaged from the locking latch). The next step is to turn the part 180 degrees and then hang it on the side wall of the machine casing using a service hook.
Replacing the heating element of the washing machine
Having unscrewed the fasteners, remove the plinth panel. It is held in place by two mounting screws. It is enough to unscrew them, and then pry the panel with some handy tool.
The wires are removed from the terminals of the heating element, the heating element fastening nut is unscrewed and carefully removed. Replacement is done upside-down.
In order not to damage the surface of the panels, only a plastic tool should be used as improvised means.
After the top panel is removed, you can disconnect the electrical wires from the terminals of the anti-interference filter. Then you need to unscrew a couple of screws securing the filter and remove it from the mounting slots.
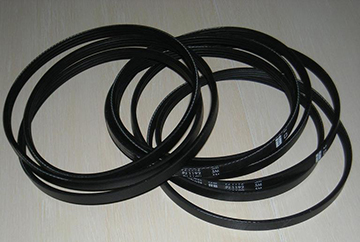
And then, turning the pulley, remove the old belt.
The new one is installed in the reverse order.
Replacing bearings in an automatic machine is one of the most difficult repair jobs. In this case, most of the unit is subject to disassembly:
- Remove the top panel.
- Remove the detergent drawer: it hides two screws that need to be removed.
- Then unscrew another pair of screws holding the aluminum strip (located under the top panel).
- Now you can disconnect the clamps from the tank and the cuvette hoses.
- Unscrew the two screws holding the lower casing (covering the pump filter) on the sides and remove it. Below it are the screws that hold the middle panel with the loading door in place.
- The clamp that presses the boot door collar to the cladding panel must also be dismantled.
- Remove the electrical connector from the UBL. Now you can unscrew all the remaining fasteners and remove the cladding panel along with the loading door.
Carefully put the panel with the hatch in a safe place during the repair: the hatch breaks easily if it falls.
The back of the drum from the pulley side
You got to the weighting compound. Using the socket on 13, unscrew the fasteners and remove it.
Your next steps:
- Using a socket head 8, unscrew all the bolts located around the perimeter of the front wall of the loading tank and remove it together with the hatch collar. The opened wires of the heating element can not be removed.
- Disconnect the spring that connects the back top of the tank to the back of the machine.
- Remove the pair of bolts securing the motor base. Then slide it back off the guides and it will fall down.
- It remains to disconnect the clamp connecting the pump and the lower corrugated pipe.
The tank, freed from all fasteners, can now be removed from the car. The shock absorbers on which it stands will remain in place, and the rubber grommets will come out with it.
All further work is carried out directly with the tank:
- Unscrew the nut holding the pulley with a 19 key. Remove the pulley from the shaft.
- We take out the shaft. If the bearings are in order, it can be removed easily. But if there is rust in the support nodes, this operation becomes problematic. Bronze drifts are used. It is more convenient to work together: one taps the shaft with a punch, the other pulls the drum.
- Having taken out the shaft, proceed to the extraction of the bearings.
The bearings are pressed in tightly, so there is a danger of leaving the outer race inside - the inner part of the large-diameter bearing may crumble when knocked out. Therefore, the outer bearing of the smaller diameter is knocked out first.
If removing the bearing assemblies is difficult, you can use WD grease.
It is best to buy a complete repair kit - it includes:
- a pair of bearings;
- stuffing box;
- device for the safe installation of units;
- special waterproof grease.
If you install the bearings skewed or bump them, they will soon need to be repaired again due to water getting into them.
At the end of the repair work, the machine is assembled in the reverse order. Make sure that the heating element fits into the socket specially designed for it, the sealing rubber is not pinched, and the spring at the back of the tank is set to its previous position.
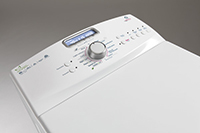
We will analyze the methods of eliminating the main breakdowns of Bosch washing machines in this article.
To disassemble Hansa washing machines, you need the following tools: a Phillips screwdriver, a flat screwdriver, a 19 flat wrench, an 8/10 flat wrench, pliers for unclamping the clamps, wire cutters, pliers, as well as a special tool - a service hook (Fig. 1).
Remove the top cover, for which, using a Phillips screwdriver, unscrew the two screws securing the cover to the case (Fig. 2).
Rice. 2. Removing the top cover fixing screws
After that, lifting the back of the top cover with one hand, slide it back with the other hand and separate it from the body (Fig. 3).
Rice. 3. Removing the top cover
Dismantle the control panel by removing the detergent dispenser hopper, and using a Phillips screwdriver, unscrew the two screws securing the control panel (Fig. 4).
Rice. 4. Removing the control panel mounting screws
Holding the control panel with your right hand, slide the panel outward with your left hand and turn it almost 90 ° until the panel (on the right side) is disengaged from the fastening latch (Fig. 5 and 6).
Rice. 5. Detaching the left side of the control panel
Rice. 6. Detaching the right side of the control panel
In this position, turn the control panel 180 ° parallel to the side wall of the washing machine and use the service hook to hang the panel on the side wall of the machine (Fig. 7).
Rice. 7. Hanging the control panel on the side of the machine
The longer end of the hook goes into the opening in the detergent hopper, and the shorter end hangs from the top edge of the side wall of the machine (fig. 8).
Rice. eight. Using the service hook to hang the control panel
Dismantle the plinth panel, for which, using a Phillips screwdriver, unscrew the two screws securing the plinth panel to the side walls of the machine, and then remove the panel (Fig. 9).
Rice. 9. Removing the plinth panel
The panel can be pry off with any tool, taking precautions not to damage the paint layer.
Having opened the door of the washing machine hatch, using a flat screwdriver, remove the clamp of the hatch seal (Fig. 10),
Rice. 10. Removing the clamp securing the hatch door seal
and then separate the hatch seal from. front panel (fig. 11).
Rice. eleven. Separating the hatch door seal from the front panel
Remove the front panel of the case, for which, using a Phillips screwdriver, unscrew the four screws securing the front panel to the side walls of the machine, and remove the panel together with the hatch (Fig. 12).
Rice. 12. Removing the front panel
Disconnect the wires from the door interlock (fig. 13).
Rice. thirteen. Disconnecting the wires from the sunroof locking device
Use pliers to loosen the spring clip on the tube connecting the Jet System control valve to the sunroof seal and remove the tube from the water injection fitting (figure 14).
Rice. 14. Disconnecting the tube from the water injection connection
Using pliers, loosen the spring clamp on the tube suitable for the level switch, remove the tube from the level switch fitting (Fig. 15),
Rice. 15. Disconnecting the tube from the level switch fitting
then pull it out of the hatch door seal (Fig. 16).
Rice. sixteen. Removing the tube from the manhole door seal
To dismantle the seal using a Phillips screwdriver, loosen the fastening clamp (Fig. 17),
Rice. 17. Removing the retaining clip
then, using a flat screwdriver, remove the clamp and separate the seal (Fig. 18).
Rice. eighteen. Removing the hatch door seal
The installation of the seal is carried out in the reverse order.
The seal should be put on in such a way that the triangular marker on it is on top and coincides with the same marker on the tank (fig. 19),
Rice. nineteen. The location of the markers when installing the hatch door seal
and the drain groove of the seal was located at the bottom.
When installing the seal, the screw of the fastening clamp must be installed so that its head is at the level of the threaded nipple on the tank (Fig. 20).
Rice. twenty. The location of the screw tightening the fastening clamp of the hatch seal
Using pliers, unhook the spring on which the tank is suspended (fig. 21).
Rice. 21. Uncoupling the tank suspension spring
Turning the pulley, remove the belt from it (fig. 22).
Rice. 22. Removing the drive belt
The belt is assembled in the reverse order. When putting on the belt, pay attention to the following: the belt must be put on the motor shaft so that one groove at the end of the shaft is free (Fig. 23 and 24).
Rice. 23. Correct position of the belt on the motor shaft
Rice. 24. Incorrect position of the belt on the motor shaft
Remove the top cover, tank suspension spring, drive belt.
Using a 19 wrench, unscrew the nut securing the pulley (Fig. 25) and remove the pulley.
Remove the basement panel. Remove the wires from the heating element terminals, unscrew the nut securing the heating element, and carefully remove the heating element (Fig. 26).
Remove the top cover, plinth, and drive belt. Unscrew the two screws securing the electric motor (fig. 27),
Rice. 27. Removing the screws holding the electric motor
and remove the engine (fig. 28).
Rice. 28. Removing the collector motor
Disconnect the electrical connectors of the electric motor (fig. 29).
Rice. 29. Disconnecting the electrical connectors of the electric motor
Remove the basement panel. Using a Phillips screwdriver, loosen the screw that secures the drain pump (fig. 30).
Rice. thirty. Unscrewing the screw that secures the drain pump
Having loosened the clamps with pliers, disconnect the pipes from the pump (Fig. 30).
Removing the wires from the pump terminals, remove the drain pump.
Rice. 31. Disconnecting the pipes from the drain pump
Remove the top cover. After opening the hatch door and holding the locking device with your hand from the inside, unscrew the two fastening screws.
Having disconnected the wires from the terminals of the blocking device, remove the device.
Remove the top cover. Remove the detergent hopper.Unscrew the screw securing the distributor from the control panel side (see fig. 4), and remove the distributor (fig. 32).
Rice. 32. Removing the detergent drawer
Remove tubes from the distributor fittings.
To replace the distributor cover, separate it with a flat screwdriver (fig. 33).
Rice. 33. Detergent dispenser lid compartment
On the inside of the lid you can see holes through which water enters the compartments of the detergent hopper (fig. 34).
Rice. 34. Holes in the lid of the detergent dispenser
Remove the top cover, disconnect the electrical wires from the terminals of the anti-interference filter (Fig. 35).
Rice. 35. Disconnecting the wires from the terminals of the anti-interference filter
After unscrewing the two screws securing the filter (Fig. 36), remove the filter from the seats.
Rice. 36. Removing the screws securing the anti-interference filter
Having disconnected the washing machine from the electrical and water supply networks, remove the water inlet hose and the top cover. Disconnect the wires from the EK terminals (Fig. 37).
Rice. 37. Disconnecting wires from the EK terminals
Remove the fixing clamps from the tubes suitable for the EC and remove the tubes from the EC fittings (Fig. 38).
Rice. 38. Disconnecting tubes from fittings EK
After unscrewing the screw securing the EC to the rear wall of the housing (Fig. 39), remove the EC.
Rice. 39... Removing the screw securing the EC to the rear wall of the case
Having opened the hatch door as much as possible, unscrew the two fastening screws and remove the door (fig. 40).
Rice. 40. Removing the hatch door
After unscrewing ten screws holding the hatch door edging (Fig. 41), separate the inner and outer edging and remove the glass.
Rice. 41. Removing the sunroof glass
Removing and putting aside the inner bezel with glass, remove the latch mechanism and handle (Fig. 42).
Rice. 42. Removing the hatch door latch mechanism
Having separated the inner edging from the glass, remove the hinge axis and remove the hinge (Fig. 43).
Rice. 43. Removing the hinge axis
Having removed and put aside the inner edging with glass, the latch mechanism and the handle are removed (see. rice. 42). Remove the two pins and the handle spring (fig. 44).
Rice. 44. Removing the hatch door handle
Having removed the plinth panel, disconnect the wires from the valve terminals and, removing the valve from the seat, disconnect three tubes that fit to it (Fig. 45).
Rice. 45. Removing the Jet System Control Valve
Remove the top cover, control panel, front and basement panels of the case.
Remove the wires from the terminals of the EK, drain pump, heating element, control valve and electric motor. Unscrew the screws that secure the housing support bracket. Loosen the clamp securing the seal to the front panel and separate the seal from the front panel. Release the cable ties from the cable ties. Disconnect the tank suspension spring. Loosen the screws holding the body to the base of the machine and remove the body. Disconnect all pipes from the tank.
Raise the tank in such a way as to separate it from the shock absorber rods, and fix the tank in a raised state. Remove the shock absorber from the rubber block at the base of the machine (fig. 46).
Rice. 46. Removing the shock absorber from the rubber block
To replace the rubber block, remove it from the shock absorber by prying it with a flat screwdriver (fig. 47).
Rice. 47. Removing the rubber block
Remove the top cover, control panel, front and basement panels of the case. Disconnect all pipes from the tank (fig. 48),
Rice. 48. Disconnecting the pipes from the washing machine tank
After unscrewing the mounting bolts, remove the front counterweight (fig. 49).
Rice. 49. Removing the front counterweight
Unscrew the 12 screws securing the front and back of the tank (fig. 50).
Rice. 50. Removing the screws securing the front and back of the tank
By unscrewing the two screws holding the body to the base of the machine (fig. 51), slide the body back.
Rice. 51. Removing the screws holding the housing to the base of the machine
Remove the drive belt and, by unscrewing the fastening nut, remove the pulley. Remove the drum (fig. 52).
Rice. 52. Removing the drum
Remove the top cover, control panel, front and basement panels of the case.
Remove the wires from the terminals of the EK, drain pump, heating element, control valve and electric motor. Unscrew the screws that secure the housing support bracket. Loosen the clamp securing the seal to the front panel and separate the seal from the front panel. Release the cable ties from the cable ties. Disconnect the tank suspension spring. Loosen the screws holding the body to the base of the machine and remove the body. Disconnect all pipes from the tank.
Remove the motor and counterweights.
Raise the tank up until it is separated from the shock absorber rods (Fig. 53).
To replace the rubber bushings of the shock absorbers, the tank is raised until it is separated from the shock absorber rods, after which, using a flat screwdriver, the rubber bushings are removed (Fig. 54).
Rice. 54. Removing the shock absorber rubber bushing
Remove the top cover, control panel, front and basement panels of the case. Disconnect the wires from the heating element terminals and remove the heating element. Remove the front counterweight, detach the front of the tank.
Having unscrewed two bolts, remove the heating element mounting bracket (Fig. 55).
Rice. 55. Dismantling the heating element mounting bracket
Remove the top cover. Remove the top counterweight by unscrewing the three mounting bolts.
Remove the top cover, control panel, front and basement panels of the case. Remove the front counterweight by unscrewing the three mounting bolts.
Remove the basement panel. Disconnect the drain pump and remove one of the pipes suitable for it. Remove the lower counterweight by unscrewing the three mounting bolts.
Remove the top cover. Disconnect the wires from the terminals of the anti-interference filter. Remove the power cord block from the socket (fig. 56).
Rice. 56. Replacing the power cord
N (neutral) - blue wire;
L (phase) - brown wire;
(ground) - yellow-green wire.
Remove the top cover, remove the hopper. Having wrung out the latch, at the same time push forward the front panel of the hopper (fig. 57). When reassembling, slide the panel from below until the latch clicks.
Rice. 57. Replacing the front panel of the detergent hopper
Remove the top cover, dismantle the level switch. After removing the retaining clip from the mounting bracket, replace the bracket (Fig. 58).
Rice. 58. Replacing the mounting bracket
Remove the top cover. Disconnect the power cord and wire harness. Remove the basement panel. Disconnect the wires from the terminals of the heating element, electric motor, control valve and drain pump. Take out the detergent hopper. Loosen the fixing screws of the detergent dispenser. Unscrew the screws that secure the support bracket.
Having loosened the fastening clamp, the hatch door seal is separated from the front panel of the case.
After unscrewing the fastening screws of the front panel of the case, remove it. Remove the wires from the terminals of the sunroof locking device. Disconnect the tank suspension spring.
Remove the screws that secure the case to the base. Separate the body (fig. 59). The shock absorbers with rubber blocks are removed.
Rice. 59. Dismantling the base
The article was prepared based on the materials of the "Repair & Service" magazine
Self-repairing equipment without the appropriate knowledge and experience may be more expensive than contacting a specialist. We recommend professional repair of Hansa washing machines in Moscow.
![]() |
Video (click to play). |