In detail: trimmer patriot 3045 DIY repair from a real master for the site my.housecope.com.
Hello everyone. This video is not educational. I don’t teach anyone how to assemble, repair and the rest. The situation has developed ...
Approximate management how to disassemble the trimmerto, for example, get to the starter or the ignition coil.
In this video, I'm repairing my Patriot trimmer. I will also tell you what kind of breakdowns happened to him, well, and my impressions after three years of work. We will also try to dig up young potatoes, see how much they have grown.
My libral1973 channel:
How to make a puller with your own hands:
Do-it-yourself mesh netting:
DIY LED floodlight:
DIY portable speaker:
DIY mini tractor:
DIY muffler:
How to adjust valve clearances:
Video Repairing a Patriot trimmer. Trimmer review, channel breakdown libral1973
Patriot PT Petrol Trimmer 3055 - a comfortable and productive tool for the treatment of areas with grass, requiring careful and precise cutting and trimming. The machine is used for quick mowing and trimming of grasses on backyard lawns, along flower beds, fences, walls, courts and lawns.
- Thanks to high quality construction two-stroke engine and its upper location in the structure, there is a low noise level of up to 70 dB.
- The fuel tank is made of transparent material, resistant to brutal environments.
- Automatic line feed.
- The width of the strip with a knife is up to 220 mm.
- Cutting the excess length of the fishing line is done with a special knife in a protective casing.
- The multi-stage air filter captures large, medium and small fractions of suspended dust and hard particles.
- The rod is detachable, comfortable for transportation and storage.
![]() |
Video (click to play). |
- In the manufacture of the device, modern materials and assembly technologies were used.
- A new anti-vibration system is provided.
- High performance is achieved by a shiny motor with durable and well-fitting parts.
- Conventional and mobile control system. A start button and a throttle lock are located on the handle of a bicycle shape in the reach zone, which allows work with a clear calculation and mobile control.
- A line of unique engine oils has been developed for the lubrication of drives.
- The ease of assembly and use of the tool is designed for an ordinary person without special technical knowledge and work experience.
- Non-hazardous operation. The protective cover protects the operator's hands from injury.
all the pros and cons of moto braids.
- The handle of the main rod is installed and fixed in such a way that the open part is located on the right side of the handle.
- The handle is not completely screwed in with the bolts, but taking into account the following adjustment.
- The control handle is installed with the throttle trigger to the trim head.
- The fastening screw is tightened with little effort. The cable clips are attached to the handle.
- The shoulder strap locks into place with a carabiner for a special attachment on the main shaft of the unit.
- A metal casing is screwed to the lower part of the bar at the base, and a plastic casing is attached to the top of the gearbox to enhance protection.
- Installed protective flange on the splined shaft of the gearbox with the coincidence of the technical grooves on the gearbox with flanged ones.
- A fixing rod or hexagon is inserted between the gearbox and the flange.
- The trimmer head is screwed in until it stops, counterclockwise.
- On the protective flange the cutting knife is installed.
- The knife is pressed with a washer and tightened with a nut until it stops against the clock.
If the knife is dull on one side, then turn it over and use the second sharpened side.
- Both parts of the boom are connected using the locking lever of the fastening system.
- Checking the correct assembly: the impossibility of opening without pressing the locking fasteners.
- The additional fastening of the coupling coupling is tightened up to the stop. This gives an advantage when using the machine for different jobs: the lower boom is set at fixed angles of 90 and 180 degrees.
- Gets dressed trimmer.
- The shoulder strap is adjusted to the individual characteristics of the operator's figure.
- The handle fastening bolts are tightened to the stop.
- Trimmer fuel mixes are made only with Genuine Patriot 2-stroke engine oils.
- Gasoline for filling the engine is used from the high-octane range, not lower than AI 92.
- The trimmer is equipped with a special canister for the fuel mixture with marks for dilution.
- Gasoline is poured into the container up to the appropriate mark.
- Two-stroke oil is poured into the gasoline, and not vice versa, up to the level mark
- The mixture is shaken several times until smooth.
- If the package does not include a special container, use a regular gasoline canister. Make a mixture in this ratio of gasoline / oil 32: 1.
- It is not recommended to prepare the mixture directly in the trimmer fuel tank.
Petrol trimmer starter repair may be required at the most inopportune moment. In this case, the problem can be solved in two ways: replace the broken part or change the entire unit. The latter option will cost more. To repair the device with your own hands, in most cases, you only need a screwdriver with the appropriate tip from the tools. Repair work does not take much time and does not require any special knowledge. It is enough to know the device, the principle of operation, the nuances of assembling and disassembling the starter on the trimmer in order to achieve the desired positive result.
Gas engine - this, in principle, is the main part of the brushcutter. Its power lies in the range of 0.5-2.5 hp. The movement from it is transferred to the shaft, which is inside the hollow rod, and then through a gearbox consisting of gears, already a fishing line or knife (working body).
The petrol brush also has the following elements:
- protective casing;
- lever;
- belt designed for the convenience of using the device;
- starter used to start a gasoline internal combustion engine.
All details of the brushcutter are presented in the photo below.
The trimmer starter is the integral part that starts the engine. He is shown separately in the two photos below.
Starter mechanisms of various models of petrol cutters work on the same principle: During the start of the internal combustion engine, the protrusions marked with 1 in the photo above engage with the pawls 3. When the engine starts to work, they return to their previous position due to the influence of centrifugal force. Wire 2 also plays a similar role.
The process of returning to the initial position of the elements of the mechanism occurs due to the presence of a spring wound around the axis. It unfolds when the rope is pulled. After releasing the cord, it is pulled in and wound up due to the coiling of the spring. During the start of the internal combustion engine, the petrol mowers, the starting mechanism turns its shaft until it starts to work (starts).
Today, gasoline brushcutters are equipped with starter mechanisms of two types:
The first option is much more common.
The trimmer starter can operate without breakdowns for a long time. It is impossible to clearly indicate the period of uptime.Everything is determined by the initial quality of the device and adherence to the rules for handling it.
It is not difficult to determine the cause of the breakdown of the triggering device. There are several main options:
- break of the cord (rope);
- when the spring breaks or disengages.
These details are shown in the photo below.
It may happen that the starter mechanism is accidentally broken. The consequences will be disastrous if the broken rope is wound around the flywheel of a working internal combustion engine: then the spring will burst, the pulley will break. But such cases, when a complete replacement of the starter unit is required, are extremely rare. In most cases, it is enough to install a new spring or replace the cord to fix the mechanism.
To repair the trimmer starter, you will first need to disassemble it and then assemble it. This process is not particularly difficult. For work you will need screwdriver with a tip of the desired shape.
Everything should be done carefully, observing safety precautions, mainly so that the spring does not injure the master in case of an accidental departure.
The launch mechanism is disassembled in order to install new parts instead of broken ones in the following sequence:
- unscrew the screw fixing the pulley with the starter cover with a screwdriver;
- take out the spring and antennae;
- carefully remove the pulley (you need to turn your head away or work, wearing glasses and gloves first);
- determine why the trigger is broken;
- if the spring has collapsed almost completely, then it is replaced;
- when the spring comes out of the hook, it is installed in its original place, bending the antennae in front of this (the photographs show the laying process);
- after the spring plate is installed inside the groove, twist it carefully.
To change the spring, you must work carefully and carefully: it can accidentally burst under the influence of the force caused by installing it in place. Even if you carefully remove the roller, the spring strip very quickly flies off the reel and can injure your hand with its sharp edges.
It is not always possible to immediately put the spring plate in its original place. It often slips, so attempts must be repeated until the desired result is achieved.
The assembly of the starter unit is carried out in a number of stages:
- the coil is turned over, setting it so that the spring bend fits exactly into the groove of the body, as in the photo below;
- two washers are placed, between which a spring is placed;
- put in place the cup with the antennae;
- tighten the screw (photos below).
When doing the above manipulations, it is imperative put two washers... If this is not done, then the spring will damage the plastic cup over time, and when it is pulled up, wedging will begin. Because of this, there is a feeling as if the spring has flown off. To eliminate this drawback, you need to install this part of a greater length or an additional washer.
When such parts are not available, you can just unscrew the screw, and the starter unit will start working without wedging. But this option is temporary - it is better to repair it with high quality as soon as possible.
After installing the spring, tighten it. To do this, perform the following actions:
- remove the handle from the starter cord;
- then the rope is inserted into the reel groove;
- tension the spring by rotating the coil in the opposite direction to the clockwise direction (winding);
- make the required number of revolutions specified in the operating instructions for the used trimmer model and corresponding to the length of the cord used;
- at the very end, the rope is threaded into the hole provided for this, located in the starter cover;
- put the handle in place, fixing it with a knot.
If after repair the spring continues to fly, then you can get rid of this in the following ways:
- squeeze a piece of the plate suitable in size into the groove at the location of the spring hook;
- drill holes on both sides of the groove in the spool, into which to insert the spring hook and fix it with a wire.
The torn rope is replaced in the following sequence:
- the old cord is removed;
- choose a rope that is suitable in size (thickness and length);
- passing it through a special hole in the coil, tie a knot;
- cocking the spring, producing the required number of revolutions;
- fix the handle.
It is better to stretch the spring plate with a partner so that the end of the cord does not reel into the starter mechanism.
Assembling the starter on the trimmer and winding the spring is not difficult, you just need to do it carefully and with care. For different models of petrol cutters, the breakdowns of the triggering mechanisms are the same, so they are repaired in the same way. However, there are some nuances associated with their design features.
Very often, complaints from owners of gasoline trimmers are associated with various kinds of carburetor malfunctions. Of course, in this case, it is best to seek help from specialists in this field, for whom the repair of carburetors of gasoline trimmers is an integral part of the profession. However, if you are still familiar with the basic principles of the trimmer carburetor, you can try to figure out the problem yourself, so as not to overpay money in the service, since sometimes the breakdown can be really frivolous.
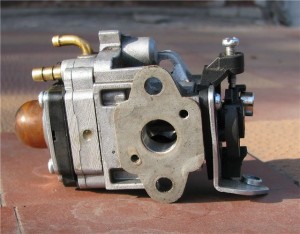
This article is just intended to help you deal with the problem.
Next, we will analyze the most common breakdowns and the reasons for their occurrence.
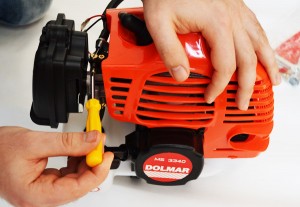
The first step is to generally inspect the carburetor and find out if there is any fuel leakage.
If it turns out that there are no problems with fuel, it is necessary to remove the carburetor from the engine and check the condition of the gasket located next to the carburetor.
If no malfunctions are observed here, you can try to check the carburetor for tightness.
To do this, you can purchase a special device, which is part of the tool kits for repairing the carburetor repair of mowers and representing a special pressure gauge that, in fact, checks the tightness.
If you don't want to spend money on its purchase, you can use a conventional medical tonometer, on which you just need to change the pressure gauge.
When using this device, pay attention to the indication.
If the pressure does not drop and remains the same for a long time, you can rest assured, as this indicates the tightness of the carburetor.
If the pressure begins to decrease after a certain time, then there are still problems.
They can be associated with damage to any parts of the carburetor.
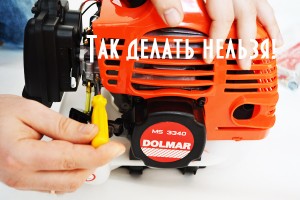
Before running to the nearest repair shop or specialty store selling trimers and spare parts, try to figure out the problem yourself. Sorry for the banality, but the brushcutter carburetor is not a spaceship of an extraterrestrial civilization, and it is quite possible to repair it with your own hands. To be confident in your actions, read the step-by-step instructions provided in this article.
A visual inspection of the carburetor will help detect fuel leakage and air leakage, but the main reasons for the failure of the device lie inside. Therefore, in order to determine and most importantly fix the breakdown, the carburetor must be disassembled.
It does not take much effort to disassemble the carburetor of the brushcutter.
It is enough to unscrew four screws on one side
and two on the other. This can be done using a conventional Phillips screwdriver. Unscrew the screws carefully and fold them to the side. They may be needed during assembly.It is advisable to cover the table with a white cloth before disassembling so that you can see everything, even the smallest details that may fall out during disassembly.
We start disassembling from the side of the fuel supply system.
We remove the primer - a pumping bubble, which is remarkable, it is simply impossible to install the carburetor parts incorrectly during assembly. Products have characteristic ebb and flow.
Now we remove the membrane. It is she who performs the function of pumping fuel into the carburetor.
When the membrane vibrates, the other side exerts pressure on the rocker of the mechanism and the needle rises, which, in turn, opens the hole and fuel is supplied.
Remove the carburetor cover with the injection mechanism.
Further, another membrane is installed. We carefully remove it.
There is another gasket under the membrane. We also carefully remove it, without damaging it in any way.
Next, we move on to dismantling the parts from the back of the carburetor. As mentioned earlier, we unscrew the two bolts. This is already an air supply system.
A valve is located here, which, when gas is added, opens and increases the flow of air into the engine.
After removing it, a bare body remains in the hands. The carburetor is disassembled.
Identification of faults and their elimination
Now it is worth paying attention to the problems that occur during the operation of the carburetor and how to fix them.
The first thing that happens is that the holes and jets in the fuel supply system are clogged with dirt. Filters installed in the tank and directly in the carburetor do not help. They still allow small particles to pass through, which cause brushcutter failure.
Now we need to get the needle.
To do this, unscrew the bolt on the mechanism, holding it with your finger. The fact is, there is a spring there and a careless action will lead to the fact that it is lost.
We take out the needle, see photo and spring.
How to purge. The most effective way is to use an ultrasonic bath.
It is filled with either a special liquid or gasoline, a carburetor is placed there and under the action of ultrasound, the so-called cavitation effect, the channels are cleaned of contamination.
The second option for cleaning is compressed air.
You can use the compressor available on the farm and clean the carburetor channels. However, this method is effective if the contamination is not very large.
If there is neither an ultrasonic bath nor a compressor at hand, then cleaning can be done in the third way using a special cylinder for cleaning the carburetor. They are sold in almost all car dealerships and supermarkets. The price is not high and is about $ 2-3. Enough of such a cylinder for 4 or 5 purges.
Now we need to blow through the channels in the body and carburetor cover. See photo.
Another particle of dirt can get stuck under the needle. See photo. This will also lead to brushcutter failure.
Important! When cleaning the carburetor, never use needles, pins or wires. Even the slightest scratch will damage the carburetor. It will have to be changed entirely.
It is located on the carburetor cover and is a fine metal mesh. Its pollution occurs very often. This is due to the deposition of oil, additives, dirt on it.
Sometimes, when disassembling on the nets, a certain film is found. Therefore, the carburetor does not have enough fuel and the brushcutter either does not start or works intermittently. The cleaning methods are identical to the first reason: an ultrasonic bath, a compressor or a spray bottle with a special solution. In addition, if the mesh is clogged thoroughly, you need to take a soft brush for watercolors, soak it in gasoline and rinse it carefully without damaging it.
They have the ability to wear out during operation. From prolonged use, they deform, stretch, lose elasticity, low-quality fuel corrodes them, and can no longer perform their functions well. This also applies to the needle itself.The fact is that it is covered with a thin layer of rubber, which wears out during operation and can no longer fit tightly into the hole. The brushcutter starts to work intermittently. To eliminate such a breakdown, it is necessary to replace all worn out parts. Where can I get them?
In specialized gardening equipment stores, a carburetor kit for a brush cutter of a certain model is sold. The cost of such a repair kit ranges from 40 to 60 hryvnia.
It includes two diaphragms, a gasket, a needle valve and a spring.
All wear parts of the carburetor can be replaced. Therefore, you should not rush and buy a new one, and you do not need to run to the workshop either, repairs are within the power of any brushcutter user. Professionals claim that the quality of the components in the repair kit even exceeds the characteristics of the native carburetor parts. Therefore, a well-repaired unit will perform better than a new one.
In addition, the bubble button for manual fuel pumping may fail. The impact of gasoline on it leads to the fact that during prolonged operation, the rubber corrodes and it begins to stick together or, under the influence of low temperatures, for example, during storage, it bursts. The button should also be replaced if necessary. In addition, its cost is small and will not affect the size of the repair budget in any way.
Based on the foregoing, it can be concluded that there are only three main carburetor malfunctions: clogging of channels, contamination of the fine filter and failure of components. In the first two cases, cleaning is enough, and in the third, a repair kit will help.
Assembling a brushcutter carburetor is a snap. All actions must be performed in reverse order:
Install a spring and a needle valve in the carburetor cover. Hold the spring with your finger and tighten the mounting bolt.
Screw the shutter of the air supply system to the product body with two screws.
Turn the carburetor over and go to the fuel system assembly. First you need to put the gasket.
Install the carburetor cover.
Install the main diaphragm.
Install the plate with the manual fuel pumping button and tighten the four screws.
The carburetor is assembled and ready for further use.
For the first time, repairing a brushcutter carburetor may seem like a complicated process, but if you have to disassemble it a second time, then this procedure will not cause much difficulty.
If you did not find any of the listed problems in your carburetor, it is recommended to contact a specialized service for help.
Adjustment carburetor petrol cutters you can do it yourself
The carburetor from the petrol cutter is a unit in the power system. In it, like all carburetors, there is a process of mixing air and fuel (gasoline) for the forthcoming supply to the engine cylinders.
In this process, the main thing is the correct proportion of fuel and air, which is why they regulate the carburetor.
Mesh filter. With this element, most often there are only two tasks:
In order to find out the cause of the breakdown, the fuel filter cap is unscrewed to remove the strainer. If dirt has simply accumulated on it, then flushing in gasoline or blowing will help.
If there is visible damage to the mesh filter, it is imperative to install a new one. There may also be damage to the fuel supply pipe (during repair, they practice checking this element).
Blowing out parts of a carburetor with a blockage with compressed air is an acceptable and comfortable repair practice.
The throttle body, the places where the carburetor parts are bundled, the inlet or outlet pipeline - all of these parts are subject to depressurization. You can probably check with a simple method - smear the problem area with soapy foam.
The diffuser is equipped with fuel channels. From them, fuel is drawn in with the help of a stream of air.
Outside the carburetor is installed:
- fuel pump;
- jet system;
- a system for adjusting the consistency of fuel with air;
The throttle valve determines the amount of air to be supplied, and the power of the motor directly depends on this.
Option correctness carburetor determined by the operation of the motor and by the color of the candle. Adjusted
Self-configuration carburetor on a Chinese trimmer, quickly and easily set up carburetor on the
Fuel is sucked into the carburetor system by a pump (its membrane). Then it goes through the choke in the carburetor. Then the liquid moves through the inlet and outlet valves of the pump. Filtered by the grid. It moves through the needle valve into the diaphragm chamber.
Phased operation of the device:
- Air supply to a tube with an air baffle (damper). The baffle regulates the intensity of the air flow.
- The fuel supply system is necessarily narrowed by the mixer to speed up the flow.
- Gasoline through the float chamber and the nozzle tube with a constriction. A float chamber adjusts the temporary volume of gasoline. In the float chamber, the pressure level is neutral, and in the tube with a constriction it is already small. Due to the pressure drop, the fuel seeps through the jet.
- The acceleration of the air flow facilitates the transfer of fuel (gasoline) and its atomization. Ultimately, an air-fuel mixture of the desired proportion or density appears.
- The air / fuel mixture seeps into the engine cylinder through the fuel pipe.
The level of air density in the system depends on the area of the open air damper. The wider the throttle is open, the greater the fuel consumption and power.
Simply put, adjusting the carburetor on a petrol cutter is the creation of a good fuel consistency due to the correct air supply.
The upcoming do-it-yourself adjustment of the carburetor of the petrol cutter is done with the adjusting screws. There are three of them:
Right (L) - adjustment of the fuel consistency for low revs.
It is necessary to find the highest idle speed. To do this, slowly unscrew the screw (L) to the right and to the left.
To adjust, turn the screw a quarter of a turn, certainly counterclockwise.
Lower (T) - is responsible for adjusting the engine at idle speed.
- clockwise - increase;
- counterclockwise - decrease.
For the correct adjustment of the idle speed specifically, it is characteristic:
- stable operation of a cold engine;
- not overestimated speed of a hot engine;
- a large reserve of turns for the trimmer head;
- stable operation of the engine when changing position (sharp lifting or lowering of the knife).
Left (H) - regulation of the mixture at high speeds. (The screw is adjusted last).
The left screw (H) determines the overall adjustment of maximum speed, engine power, temperature and gasoline consumption.
Setting up the carburetor of the brushcutter with the last screw is done as follows:
- Open the throttle to full, while at the same time give full throttle. Turn the screw clockwise until the revolutions drop (in this case, orientate by ear).
- Turn the screw counterclockwise as slowly as possible until the engine runs unevenly.
- Then turn back quite a bit, barely hearing a stable, even operation.
- For a more visual use of skills, it is more convenient to consider the work of an experienced user:
Interestingly, from the point of view of the author of the video, the setting (its correctness) is determined by the color of the candle, and not only by the speed and stability of the engine.
Support the project, share with your friends!
The clutch cup and clutch are similar to this photo.
Only registered users can reply to topics and conduct full-fledged communication.
That's not all. To unscrew the clutch, the shaft must be locked. To do this, you can use a rigid nylon cord: push it into the hole for the candle and clamp it with a piston - the shaft will be blocked. Just do not try to stop it with something metallic, otherwise you will damage the inner plane of the cylinder. Unfortunately, there is no photo of the disassembly of this unit.
Phone for masters:
+7 (915) 188-05-05
Also, you can enter the site using the following social networks (without filling in personal data):
Fill in the required fields in the form below and click the “Submit” button. Try to clearly and clearly state the essence of the issue and the purpose of the appeal. This will speed up the processing of your appeal. After receiving the letter, we will contact you in a convenient way, at a convenient time for you. Thank you for your interest in our site.
Petrol trimmers are perfect for clearing backyard weeds, as well as making hay. Yes, as grandfather's "Lithuanian" they also proved to be irreplaceable assistants. What to do in this case, when gasoline broke trimmer?
Petrol trimmers are perfect for clearing backyard weeds, as well as making hay. The cable on the patriot petrol trimmer broke. Yes, as grandfather's "Lithuanian" they also proved to be irreplaceable assistants. There is just one problem: even the ancient braids had to be repaired after the season.
It is known that prevention is much preferable to treatment, and therefore do not forget to take care of the instrument so that it does not need repairs. First of all, every 15 minutes of operation, you need to give the device at least ten minutes of rest. In addition, you do not need to cut grass higher than that specified in the instruction manual.
What to do if the petrol trimmer still breaks down? DIY repair is a good option! Let's make a reservation right away that we will talk more about engine malfunctions, since almost everyone can fix a broken rod. The lawn mower box is broken. Trimmer petrol rt 4355 disassembly grease. In extreme cases, you can simply secure it with some kind of tire and clamps.
Correctness of setting carburetor determined by engine operation and by the color of the spark plug. Adjusted.
Brushcutter carburetors can be bought here: How to adjust carburetorif configured.
Is the candle wet? Completely "showered" with a petrol-oil mixture? Your petrol trimmer we are trying to repair has carburetor adjustment problems. Easy start petrol trimmer. This often happens when non-specialists have tried to tune it.If you have no experience, we strongly advise you to contact the service center, since by your actions you may well burn out the entire piston system.
However, not everything is so bad: if you break the rules of a cold start, all the time trying to pump the fuel mixture, then this can easily lead to throwing.
It is a different matter when the candle is covered with a thick layer of black carbon. The bearing of the al ko lawn mower has broken. In this case petrol trimmer, the repair of which we are describing, was exposed to a poor-quality fuel mixture. Maybe the point is again in the incorrect adjustment of the carburetor, which produces a too saturated fuel mixture. The sterwins petrol lawn mower has broken drive. Just replace the candle.
Often, the lack of gasoline entering the combustion chamber is due to the fact that a lot of dirt has accumulated in the gas tank, which simply clogged the supply hose. Disconnect the fuel hose. If fuel does not flow from it, then a clogged fuel filter or breather is to blame. The latter can be cleaned with a needle, and it is advisable to completely change the former once every three months.
Among other things, the repair of petrol trimmers "Patriot»Often requires replacement of the air filter. When clogged, it prevents the formation of a normally rich fuel mixture.
And one more thing: often a muffler clogged with carbon deposits is to blame for everything. It must be dismantled, washed in kerosene or burned on a burner. This is especially often done by those for whom the repair of Husqvarna petrol trimmers is a daily job.
The starter is one of the main components of the brushcutter, which greatly facilitates starting the engine of the tool. Its breakdown can happen at the most inopportune time, which will certainly entail significant changes in the daily plans of the site owner. There are two ways to solve the problem: repair the trimmer starter with your own hands, or replace the entire assembly. The easiest way to troubleshoot a starting system is to completely replace it, but from a financial point of view, buying a new starter can seem far too heavy. For self-elimination of breakdowns, it is enough to prepare a screwdriver with an appropriate tip and familiarize yourself with the following recommendations.
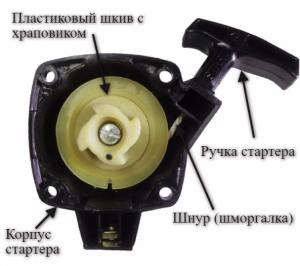
Petrol cutter starter with details
Like any garden or construction gasoline tool, the trimmer starter consists of a plastic case, into which a pulley with a pre-wound cord (shmorgalka) is installed. For the purpose of automatic twisting of the rope after a jerk by the starter, a ribbon spring made of alloy steel is fixed on the back of the pulley. A ratchet is mounted on the front of the pulley, by means of which the starter engages with the drive shaft of the trimmer motor. Depending on the manufacturer and the design of the brushcutter, the ratchet pulley can be either one piece or assembled from two separate parts.
The principle of operation of the trimmer starter practically does not differ, regardless of the model of the unit.
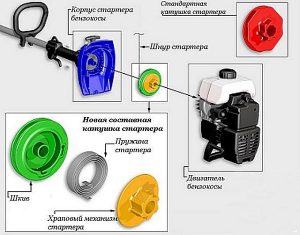
The main components of the trimmer starter
When jerking with the starter, the protrusions on the pulley come into engagement with the pawls, which, with a successful start of the internal combustion engine, under the influence of centrifugal forces, diverge in different directions. There are also models where the ratchet is spring-loaded from the side of the housing and when the pulley rotates backwards, the teeth of the engagement are removed from the motor shaft. Of course, with frequent and prolonged use of the trimmer, no one is safe from a break in the drive cord or wear of the tape spring. Therefore, in this case, you will need to repair the trimmer starter, which you can do yourself.
Currently, there are two main faults in the petrol trimmer starter:
- Breakage of the drive cord (shmorgalki);
- The belt spring breaks or is out of engagement with the pulley.
Trimmer band spring
In practice, there are cases when, for some reason, damage to the starter housing occurs and the torn cord is wound around the engine shaft, which will certainly lead to spring breakage and cracks on the housing. In this situation, local repair of the petrol cutter starter will be impossible and a complete replacement of the engine start unit will be required. In other cases, troubleshooting will be limited to replacing the spring or cord.
First of all, the repair process begins with removing the entire starter from the trimmer. This process is inherently straightforward and requires only the removal of a few screws with a suitable locksmith tool. It should be noted that when dismantling the petrol cutter start mechanism, it is necessary to observe safety precautions, since the ribbon spring in the compressed state has sufficient energy to injure a person.
This stage allows the wizard to establish the reasons for the failure of the launch unit, as well as to troubleshoot individual parts. Disassembly work should be carried out in the following sequence:
-
Unscrew the screws securing the pulley to the starter housing;
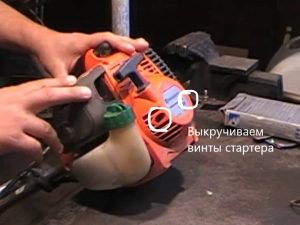
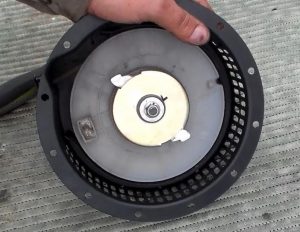
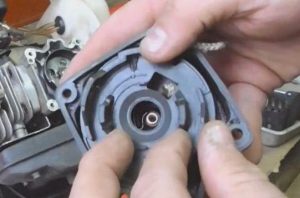
Removing the pulley from the brushcutter body
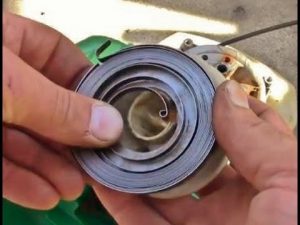
Spring removed from the starter coil
Many experts note that it is quite difficult to install the spring from the first time, therefore, when repairing a trimmer starter, the owner will need not only basic locksmith skills, but also patience.
Although the process of assembling the petrol cutter launch unit is carried out in the reverse order of disassembly, there are several nuances that should be paid special attention to:
-
The coil with the spring installed must be turned over and mounted in the groove of the starter body so that all the protrusions are in their original place.
Installing the trimmer coil in the starter housing
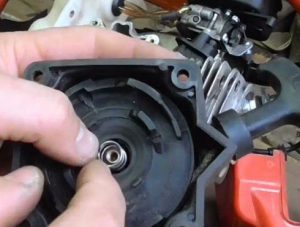
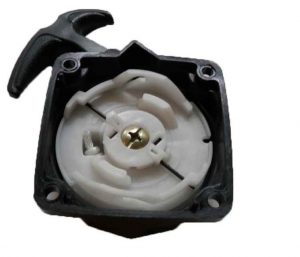
White cup with trimmer coil mustache
When assembling the starter, pay attention to the compression spring, which must be bounded on both sides by steel springs. If this is not done, then after the first season it will wipe the grooves in the pulley housing.
Trimmer Starter Spring Tension
After installing the starter, it is necessary to dismantle the rope handle and insert it into the reel groove. Further, against the direction of movement of the pulley when starting, it is necessary to make a certain number of revolutions specified in the instruction manual for the petrol trimmer. It is worth noting that the tension and further performance of the unit will depend on how to put the spring on the trimmer and what tension is made. At the final stage, we thread a rope into a special hole and fix it with a handle.
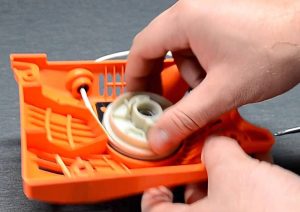
Installing the starter rope in the trimmer
![]() |
Video (click to play). |
At the very beginning, you need to remove the broken cord, choose a suitable length depending on the trimmer model. We pass it through a special hole in the pulley and at the other end we tie a knot in order to prevent the rope from jumping out of the trimmer start mechanism. Next, we erect the ribbon spring to the required number of revolutions and mount the handle.